涡轮叶片精铸全过程
涡轮叶片熔模铸造工艺研究

万方数据
万方数据
涡轮叶片熔模铸造工艺研究
作者:刘彦昌, 李忠辉, 耿春旭
作者单位:刘彦昌(哈尔滨鑫润工业有限公司,哈尔滨,150040), 李忠辉,耿春旭(哈电集团秦皇岛重型装备有限公司,河北,秦皇岛,066206)
刊名:
机械工程师
英文刊名:MECHANICAL ENGINEER
年,卷(期):2008(8)
被引用次数:3次
参考文献(5条)
1.黄天佑;黄乃瑜;吕志刚消失模铸造技术 2004
2.梁光泽消失模铸造 1986
3.清华大学金属工艺学教研室金属工艺学实习教材 1994
4.李景波金属工艺学(热加工) 1998
5.邓文英;郭晓鹏金属工艺学 1999
引证文献(3条)
1.刘文娜.张凌峰.海潮.常涛岐.贺剑.王晓东精密铸造等轴晶涡轮叶片晶粒度控制方法[期刊论文]-特种铸造及有色合金 2010(2)
2.薄壁铸件的熔模铸造生产[期刊论文]-热加工工艺 2009(21)
3.孟庆武.耿林.祝立群.刘丽双镍基合金表面激光熔覆钴基合金涂层的耐磨性能[期刊论文]-金属热处理 2009(8)本文链接:/Periodical_jxgcs200808088.aspx。
航空发动机涡轮叶片精密成型技术分析

航空发动机涡轮叶片精密成型技术分析摘要:航空发动机技术复杂且难以制造。
世界上只有几个国家可以完成航空发动机的设计和制造。
中国不断发展航空发动机的设计和制造,以提高自身的制造水平。
空心涡轮叶片是高性能航空发动机的主要部件之一,制造困难长期以来一直给中国的制造公司带来麻烦。
通过分析空心涡轮叶片的结构特性,分析和解释空心涡轮叶片的精密成型技术。
关键词:空心涡轮叶片;精密成型技术;精密铸造前言空心涡轮叶片是高性能航空发动机的关键组件,由于对精度的要求和制造困难,我们无法批量生产空心涡轮叶片。
为了提高空心涡轮叶片的制造合格率,我们将从叶片精密铸造的“形状控制”和“可控制性”两个方面出发分析空心涡轮叶片的精密铸造工艺,以提高叶片精密铸造的质量。
需要1空心涡轮叶片的精密铸造技术现代飞机发动机正朝着高推进力和低油耗的方向发展。
为了实现这一目标,当今世界上的主流方法是提高航空发动机涡轮的进气温度。
发动机涡轮的当前入口温度已经很高。
随着温度的不断升高,发动机涡轮叶片的温度达到1880℃±50℃,为了解决这个问题,目前的涡轮叶片主要用于复合膜冷却的单晶空心涡轮叶片(称为空心涡轮叶片)。
由于结构的复杂性和材料的特殊性,熔模铸造工艺主要用于制造空心涡轮叶片,但由于精度低,产量低,该工艺存在使空心涡轮叶片具有高性能的问题。
有。
通常,当今的空心涡轮叶片精密铸造的产率约为10%,其中约90%的废叶片的形状和尺寸偏差约为50%,而重结晶缺陷约占25%。
主要原因是铸造缺陷。
为了提高空心涡轮叶片的制造成品率,有必要解决“形状控制”和“铸造控制”两个问题:精密铸造后的尺寸精度和复合材料性能。
空心涡轮叶片的工艺复杂且难以制造:粗略的制造过程如下:首先,使用模芯来完成空心涡轮叶片精密铸造所需的陶瓷芯,并且陶瓷芯是空心的填充零件。
用来。
随后,使用蜡模工艺在芯的外层上制备涡轮叶片蜡模,然后通过烧结注射成型和其他工艺来制造空心涡轮叶片粗糙毛坯。
航空发动机涡轮叶片精密成形技术分析

航空发动机涡轮叶片精密成形技术分析航空发动机作为飞机的动力系统,发挥着至关重要的作用。
而发动机的性能优劣直接影响着飞机的飞行性能和安全性。
在航空发动机中,涡轮叶片是发动机中最关键的部件之一,涡轮叶片的制作工艺与精度直接决定了发动机的性能。
涡轮叶片的精密成形技术显得尤为重要。
涡轮叶片是航空发动机中的一个重要零部件,它在发动机中扮演着承受高温高速气流的任务。
涡轮叶片需要具有极高的强度和耐热性。
涡轮叶片的表面粗糙度、气动性能也对发动机的性能有着直接的影响。
在涡轮叶片的制作工艺中,精密成形技术是至关重要的一环。
精密成形技术是一种应用于金属材料制造加工的高新技术,它包括了压铸、注塑、锻造、精密锻造等多种工艺。
而在航空发动机涡轮叶片的制作中,常用的精密成形技术主要有精密铸造和精密锻造两种。
下面将从这两种技术进行详细的分析。
一、精密铸造技术精密铸造技术是将金属材料通过在低温状态下的液态状态注入模具中,利用模具的结构将熔融金属冷却后形成所需形状的一种成形技术。
精密铸造技术制造的零件表面光洁度高,尺寸精度高,重量轻,成本低。
精密铸造技术在航空发动机涡轮叶片的制作中应用广泛。
在精密铸造技术中,铸造模具的结构设计和制造对于涡轮叶片的成型至关重要。
一方面,铸造模具的结构设计需要考虑到叶片的复杂形状和内部空腔,保证叶片的内部结构完整性;铸造模具的制造需要具备高精度加工和表面处理技术,以确保叶片的表面粗糙度和尺寸精度。
精密铸造技术制造的涡轮叶片表面光洁度高,可以减小叶片表面的阻力,提高叶片的气动性能;精密铸造技术还能够制造出形状复杂的内部空腔结构,提高叶片的强度和耐热性。
精密铸造技术在航空发动机涡轮叶片制作中有着重要的应用价值。
在不断发展的航空发动机领域,涡轮叶片的制作技术也在不断地进行创新与提升。
未来,随着材料工艺技术的不断进步,精密成形技术在涡轮叶片制作中将会有更加广泛和深入的应用,为航空发动机的性能提升和安全保障提供更加可靠的技术支持。
航空发动机涡轮叶片加工工艺流程
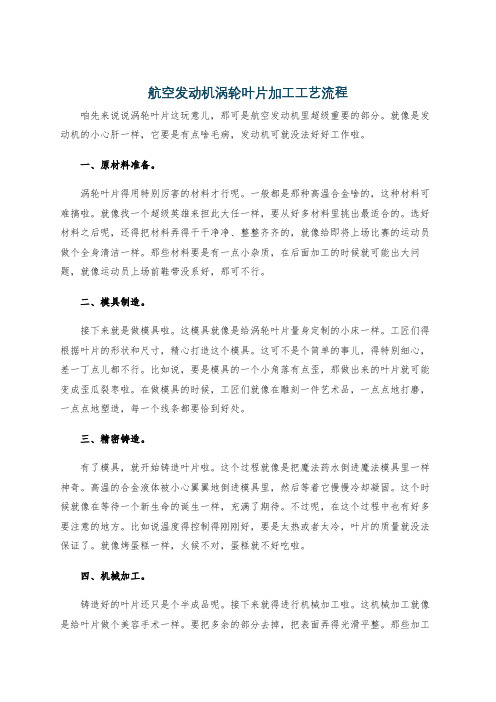
航空发动机涡轮叶片加工工艺流程咱先来说说涡轮叶片这玩意儿,那可是航空发动机里超级重要的部分。
就像是发动机的小心肝一样,它要是有点啥毛病,发动机可就没法好好工作啦。
一、原材料准备。
涡轮叶片得用特别厉害的材料才行呢。
一般都是那种高温合金啥的,这种材料可难搞啦。
就像找一个超级英雄来担此大任一样,要从好多材料里挑出最适合的。
选好材料之后呢,还得把材料弄得干干净净、整整齐齐的,就像给即将上场比赛的运动员做个全身清洁一样。
那些材料要是有一点小杂质,在后面加工的时候就可能出大问题,就像运动员上场前鞋带没系好,那可不行。
二、模具制造。
接下来就是做模具啦。
这模具就像是给涡轮叶片量身定制的小床一样。
工匠们得根据叶片的形状和尺寸,精心打造这个模具。
这可不是个简单的事儿,得特别细心,差一丁点儿都不行。
比如说,要是模具的一个小角落有点歪,那做出来的叶片就可能变成歪瓜裂枣啦。
在做模具的时候,工匠们就像在雕刻一件艺术品,一点点地打磨,一点点地塑造,每一个线条都要恰到好处。
三、精密铸造。
有了模具,就开始铸造叶片啦。
这个过程就像是把魔法药水倒进魔法模具里一样神奇。
高温的合金液体被小心翼翼地倒进模具里,然后等着它慢慢冷却凝固。
这个时候就像在等待一个新生命的诞生一样,充满了期待。
不过呢,在这个过程中也有好多要注意的地方。
比如说温度得控制得刚刚好,要是太热或者太冷,叶片的质量就没法保证了。
就像烤蛋糕一样,火候不对,蛋糕就不好吃啦。
四、机械加工。
铸造好的叶片还只是个半成品呢。
接下来就得进行机械加工啦。
这机械加工就像是给叶片做个美容手术一样。
要把多余的部分去掉,把表面弄得光滑平整。
那些加工的机器就像一个个小助手,工匠们指挥着它们,这儿切一点,那儿磨一下。
这个过程需要非常高的精度,因为涡轮叶片的形状很复杂,就像在给一个超级复杂的艺术品做最后的修饰一样,稍微一失手就可能毁了整个作品。
五、表面处理。
机械加工完了之后,还得对叶片的表面进行处理。
这就像是给叶片穿上一层漂亮的衣服一样。
涡轮叶片铸造流程
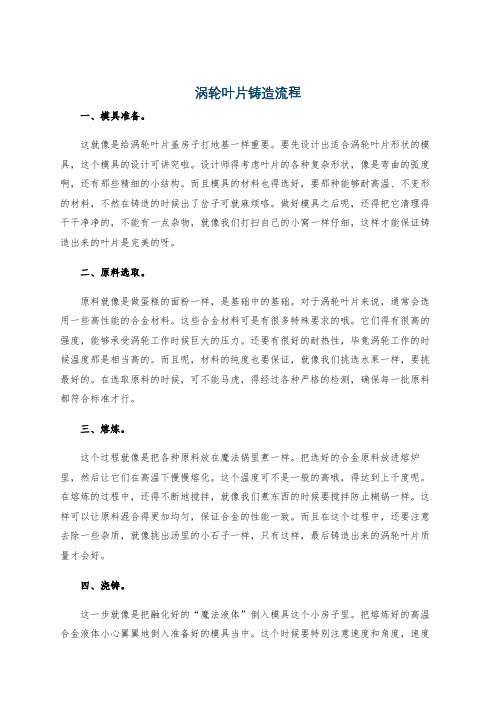
涡轮叶片铸造流程一、模具准备。
这就像是给涡轮叶片盖房子打地基一样重要。
要先设计出适合涡轮叶片形状的模具,这个模具的设计可讲究啦。
设计师得考虑叶片的各种复杂形状,像是弯曲的弧度啊,还有那些精细的小结构。
而且模具的材料也得选好,要那种能够耐高温、不变形的材料,不然在铸造的时候出了岔子可就麻烦咯。
做好模具之后呢,还得把它清理得干干净净的,不能有一点杂物,就像我们打扫自己的小窝一样仔细,这样才能保证铸造出来的叶片是完美的呀。
二、原料选取。
原料就像是做蛋糕的面粉一样,是基础中的基础。
对于涡轮叶片来说,通常会选用一些高性能的合金材料。
这些合金材料可是有很多特殊要求的哦。
它们得有很高的强度,能够承受涡轮工作时候巨大的压力。
还要有很好的耐热性,毕竟涡轮工作的时候温度那是相当高的。
而且呢,材料的纯度也要保证,就像我们挑选水果一样,要挑最好的。
在选取原料的时候,可不能马虎,得经过各种严格的检测,确保每一批原料都符合标准才行。
三、熔炼。
这个过程就像是把各种原料放在魔法锅里煮一样。
把选好的合金原料放进熔炉里,然后让它们在高温下慢慢熔化。
这个温度可不是一般的高哦,得达到上千度呢。
在熔炼的过程中,还得不断地搅拌,就像我们煮东西的时候要搅拌防止糊锅一样。
这样可以让原料混合得更加均匀,保证合金的性能一致。
而且在这个过程中,还要注意去除一些杂质,就像挑出汤里的小石子一样,只有这样,最后铸造出来的涡轮叶片质量才会好。
四、浇铸。
这一步就像是把融化好的“魔法液体”倒入模具这个小房子里。
把熔炼好的高温合金液体小心翼翼地倒入准备好的模具当中。
这个时候要特别注意速度和角度,速度不能太快也不能太慢,太快了可能会让液体溅出来或者产生气泡,太慢了又可能会让液体在倒入的过程中就开始凝固了。
角度也要合适,要确保液体能够均匀地填满整个模具。
就像我们倒水的时候一样,得小心翼翼的,不然就洒得到处都是啦。
五、冷却。
浇铸完之后,就进入冷却阶段啦。
这就像是让刚刚做好造型的蛋糕在冰箱里定型一样。
高铬铸钢叶轮铸造工艺流程

高铬铸钢叶轮铸造工艺流程1.高铬铸钢叶轮的铸造工艺需要经过严格的流程控制。
The casting process of high-chromium cast steel impeller requires strict process control.2.首先,准备合格的高铬铸钢材料。
First, prepare qualified high-chromium cast steel materials.3.将高铬铸钢材料加热至一定温度,以保证液态铸造的顺利进行。
Heat the high-chromium cast steel material to a certain temperature to ensure smooth liquid casting.4.在准备好的模具中,倒入高铬铸钢材料。
Pour the high-chromium cast steel material into the prepared mold.5.确保模具中的高铬铸钢材料填充均匀,没有气孔和夹杂。
Ensure that the high-chromium cast steel material in the mold is filled evenly, with no pores or inclusions.6.待高铬铸钢材料冷却凝固后,将模具拆除,取出铸件。
After the high-chromium cast steel material is cooled and solidified, remove the mold and take out the casting.7.对铸件进行修磨和清理,去除表面的毛刺和氧化物。
Grind and clean the casting to remove surface burrs and oxides.8.进行热处理,提高高铬铸钢的强度和硬度。
Carry out heat treatment to improve the strength and hardness of high-chromium cast steel.9.进行机加工,使高铬铸钢叶轮的尺寸和形状达到要求。
基于特征的涡轮叶片精铸模具加工工艺规程设计方法
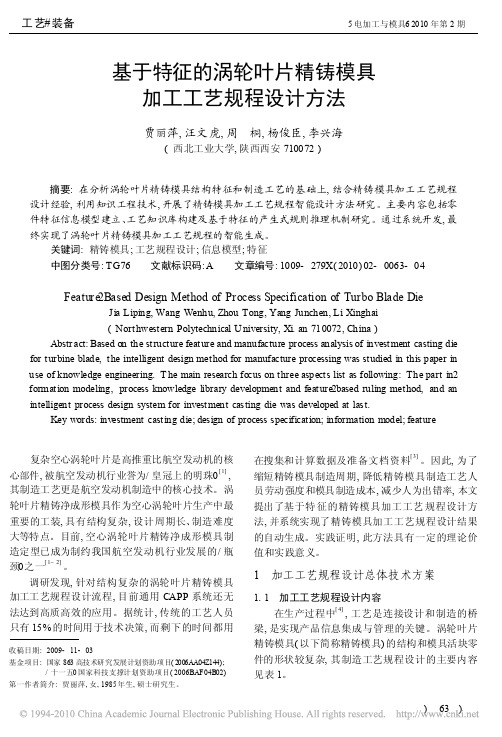
5 电加工与模具62010 年第 2 期
量推算出前一道工序的尺寸, 公差则按本道工序加 工方法的精度给出。
表 3 工艺规程实施方案
工艺路线
加工方案
制造资源
推理条件
基于零件原始 特征加工链
基于操作的排序
F {X1 , X2 , X 3, X4 , X5 }
F { Y1, Y2 , Y3, Y4, Y5}
/ 十一五0 国家科技支撑计划资助项目( 2006BAF04B02) 第一作者简介: 贾丽萍, 女, 1985 年生, 硕士研究生。
在搜集和计算数据及准备文档资料[ 3] 。因此, 为了 缩短精铸模具制造周期, 降低精铸模具制造工艺人 员劳动强度和模具制造成本, 减少人为出错率, 本文 提出了基于特 征的精铸模具加工工艺 规程设计方 法, 并系统实现了精铸模具加工工艺规程设计结果 的自动生成。实践证明, 此方法具有一定的理论价 值和实践意义。
制造资源包括机床、刀具、夹具、车间布局等一 切与资源环境相关的因素, 本文方法主要以机床选 择为例进行说明。机床的选择受所加工零件的表面 形状、尺寸精度及生产类型等因素影响。制造资源 选择的流程与加工方案选择的流程类似, 也是以 Y1 ~ Y5( 表 3) 作为已知条件, 调用工艺规则库中的规 则, 找到与该条件匹配的机床设备即可。表 3 所示 为工艺路线、加工方案及制造资源等工艺规程子任 务的实施方案。
粗车 粗车 ) 半精车
,
5
7~ 9
6. 3~ 1. 6
粗刨(粗铣) ) 精刨( 精铣)
6
7
3. 2~ 1. 6
未淬 硬平面
粗铣 ) 半精铣) 精铣
7
7~ 8
粗刨 ) 半精刨) 精刨
高压涡轮叶片定向凝固技术
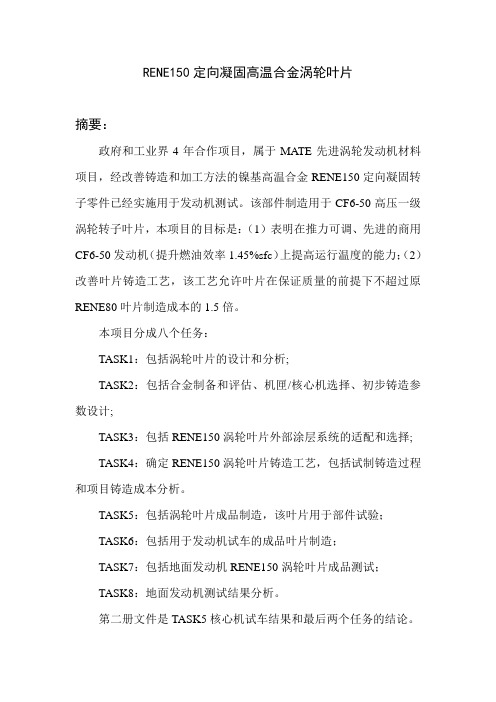
RENE150定向凝固高温合金涡轮叶片摘要:政府和工业界4年合作项目,属于MATE先进涡轮发动机材料项目,经改善铸造和加工方法的镍基高温合金RENE150定向凝固转子零件已经实施用于发动机测试。
该部件制造用于CF6-50高压一级涡轮转子叶片,本项目的目标是:(1)表明在推力可调、先进的商用CF6-50发动机(提升燃油效率1.45%sfc)上提高运行温度的能力;(2)改善叶片铸造工艺,该工艺允许叶片在保证质量的前提下不超过原RENE80叶片制造成本的1.5倍。
本项目分成八个任务:TASK1:包括涡轮叶片的设计和分析;TASK2:包括合金制备和评估、机匣/核心机选择、初步铸造参数设计;TASK3:包括RENE150涡轮叶片外部涂层系统的适配和选择;TASK4:确定RENE150涡轮叶片铸造工艺,包括试制铸造过程和项目铸造成本分析。
TASK5:包括涡轮叶片成品制造,该叶片用于部件试验;TASK6:包括用于发动机试车的成品叶片制造;TASK7:包括地面发动机RENE150涡轮叶片成品测试;TASK8:地面发动机测试结果分析。
第二册文件是TASK5核心机试车结果和最后两个任务的结论。
RENE150高压涡轮叶片已成功完成投产型DS铸造,有涂层和没有涂层两种叶片机械和物理性能符合设计要求,叶片已完成加速持久试车,结论在第二册中分别给出。
1 概述本项目的任务是扩大先进的DS涡轮叶片合金Rene150在CF6-50发动机HPT一级涡轮叶片的应用范围。
本次扩展应用将许可RENE150提升运行温度(超过RENE80)以期实现商用发动机CF6-50提升1.45%燃油效率。
本项目将通过改进铸造工艺,使得该叶片制造成本能够在不超过Rene80叶片1.5倍的前提下,完成批量生产。
项目开始阶段使用的是1977年9月的RENE150性能数据(见表1),初步设计分析确定RENE150材料应用于CF6-50叶片上时抗温度、载荷和应力的性能。
航空发动机涡轮叶片精密成形技术分析

航空发动机涡轮叶片精密成形技术分析Key words : hollow turbine;blade;precision forming technologyiprecision casting1空心涡轮叶片精铸技术高性能航空燃气涡轮发动机是精密器件,在飞机当中具有非常重要的作用,是飞机的心脏,也是导致我国航空业发展停滞不前的瓶颈之一。
伴随当前飞机设计指标逐步提升,航空发动机也需要逐步向低油耗、高推重比、大推力的方向发展,让涡轮前进口温度提高是保证推动力的一个重要方式,预计在推重比15 —级的航空发动机当中,涡轮前温度可能在1830〜1930摄氏度之间,因此一定要重视加强涡轮叶片的耐高温能力。
为了将这一问题解决。
当前的涡轮叶片主要使用的是复合气膜冷却单晶空心涡轮叶片,因为该设计材料较为特殊, 而且结构非常复杂。
在制备空心涡轮叶片的过程中,使用的工艺主要为熔模精铸工艺,但是这一工艺,具有成品率低、要求精度差等问题,造成我国在空心涡轮叶片生产方而出现了很多问题。
通常而言当前的空心涡轮叶片精铸成品率只有10%,而90%的废品叶片主要出现的问题是形位尺寸超差,另外一些是结晶缺陷。
为了让空心涡轮叶片的制造成品率提高,有效的解决。
形控”和'性控”两个问题,需要重视控制尺寸的精度,并且在完成精铸之后提高复合材料的性能。
空心涡轮叶片制造难度大,而且工序非常复杂,具体如下,首先需要注意合理的对模具成型工艺进行应用,将空心涡轮叶片精铸所需要的陶瓷型芯设计出来。
该陶瓷型芯是空心结构的重要填充物,接着通过蜡模工艺在型芯外层进行涡轮叶片蜡模的制备,而后进行烧结、浇铸、脱模等一系列工序,将空心涡轮叶片粗坯制备完成。
在完成粗坯的条件下进行后续操作,直到制备完整个空心涡轮叶片。
在传统空心涡轮叶片制备的时候使用的主要为复合材料,这种材料是等轴晶组织。
这种组织在高温条件下很容易受到损坏,而影响整个叶片制备的成品率。
伴随当前材料技术快速发展,叶片所使用的复合材料逐步以单晶为主。
复杂结构空心高压涡轮导向叶片精密铸造工艺

ZGZ-50kg真空感应炉 熔 炼 高 温 镍 基 合 金 (K441),合 金 成分见表1,将型壳预热到1 020 ℃,然后进行浇注 。 浇注 后对铸件进行清壳 ,然后进行脱芯处理和检测 。
表 1 高 温 镍 基 合 金 (K441)的 成 分
%
wB
C Cr W Mo Al Zr B S P Ni
管 目 前 陶 瓷 型 芯 已 基 本 满 足 国 内 的 需 求 ,但 与 发 达 国 家
相 比 还 有 相 当 的 差 距 ,特 别 是 在 复 杂 结 构 空 心 叶 片 用 陶
瓷型芯生产方面,无论 是 模 具 的 设 计 与 制 造,还 是 陶 芯
的制备与脱除等方面。
要生产的双联空心叶片铸造用陶瓷型芯制备非常
困难,采用普通型芯 制 备 方 法 很 难 制 备 该 类 陶 瓷 型 芯。
通过采用易脱除的硅基陶瓷型芯与石英管组合方式成
功 制 备 了 复 杂 结 构 陶 瓷 型 芯 ,利 用 该 型 芯 成 功 铸 造 了 满
足要求的复杂结构空心双联高压涡轮叶片。
收 稿 日 期 :2011-01-20 第一作者简介:刘鸣,男,1958年出生,高级工程师,沈阳中科三耐新材料股份有限公司,沈阳 市 浑 南 新 区 世 纪 路 8 号 8-3 (110179),电 话:15902402269, E-mail:aih580126@163.com
1 试验方法
采用 PWQW 型全 方 位 行 星 式 球 磨 机 对 基 体 SiO2 粉和矿化剂 Al2O3 粉 进 行 混 粉 处 理,混 料 时 间 为 10~ 20h;将石蜡与 蜂 蜡 的 混 合 物 在 油 浴 设 备 中 进 行 熔 化,
然后 加 入 混 合 好 的 陶 瓷 粉 并 搅 拌 均 匀,采 用 YT- 2XT50T 型 热 压 注 成 型 机 压 制 SiO2 基 主 陶 瓷 型 芯,主 陶 瓷 型 芯 烧 结 后 将 石 英 玻 璃 与 之 组 装 在 一 起 ,然 后 进 行
一种等轴晶涡轮工作叶片毛坯铸造方法[发明专利]
![一种等轴晶涡轮工作叶片毛坯铸造方法[发明专利]](https://img.taocdn.com/s3/m/2de9785769dc5022aaea00ff.png)
专利名称:一种等轴晶涡轮工作叶片毛坯铸造方法专利类型:发明专利
发明人:王丽萍,王铁军,王永明,冯文刚,白素春
申请号:CN201310195996.1
申请日:20130523
公开号:CN103252452A
公开日:
20130821
专利内容由知识产权出版社提供
摘要:一种等轴晶涡轮工作叶片毛坯铸造方法,其特征在于:首先,采用底注和顶注式浇注系统;成组铸造等轴晶涡轮工作叶片,每组4-20件工作叶片沿叶片圆周分布;然后在温度均匀一致、热量分布均匀的情况下,在每一个待浇筑叶片的叶背中间部位粘贴附带结构连接到直浇道上形成补缩冒口,并最终形成顶注、底注及侧注混合式浇注系统;最后,使用顶注、底注及侧注混合式浇注系统进行铸造得到等轴晶涡轮工作叶片铸件毛坯。
上述方法生产出的叶片铸件经Ⅹ射线检测,叶片内部的疏松缺陷完全消除,达到了技术标准的要求。
其解决了叶片内部的疏松缺陷,极大的提高了涡轮叶片的冶金质量及机械性能。
申请人:沈阳黎明航空发动机(集团)有限责任公司
地址:110043 辽宁省沈阳市大东区东塔街6号
国籍:CN
代理机构:沈阳晨创科技专利代理有限责任公司
代理人:樊南星
更多信息请下载全文后查看。
- 1、下载文档前请自行甄别文档内容的完整性,平台不提供额外的编辑、内容补充、找答案等附加服务。
- 2、"仅部分预览"的文档,不可在线预览部分如存在完整性等问题,可反馈申请退款(可完整预览的文档不适用该条件!)。
- 3、如文档侵犯您的权益,请联系客服反馈,我们会尽快为您处理(人工客服工作时间:9:00-18:30)。
涡轮叶片精铸全过程及其影响因素
无余量熔模精密铸造目前为涡轮叶片制造的最佳手段。
其工艺流程主要包括型芯模具的设计与制造、压制型芯、蜡模模具的设计与制造、装配注蜡、涂浆制壳、干燥型壳、脱蜡、烧结、浇注金属、脱壳脱芯、激光打孔等环节。
模具的设计定型:1、精铸模具型腔体设计,首先建立叶片零件模型,包括叶身、缘板、榫头伸根的内型特征,以此构建叶身实体。
此后进行叶片的多态模型转化,由叶片零件模型转化到型腔体模型。
2、型腔优化及精铸仿真,根据铸件的收缩原理采用反变形优化工艺方法对型腔进行放型最终得到模具型腔。
3、精铸模具结构设计与制造,确定核心包络块并设计叶片精铸模具模架,再由模具标准件经机械加工、表面处理、装配、检测、修模到定型。
模具结构的合理性和尺寸精度对于熔模精铸件十分重要。
设计制造高质量的内外型模具即精铸模具就成为精密熔模铸造技术的关键。
陶瓷型芯的制造:在叶片蜡型压制之前是需制作设计陶瓷型芯模具,并压制合格陶瓷型芯。
陶瓷型芯的制备包括浆料的配制、型芯压制、型芯素肧的修理、烧结、强化及其过程质量控制与检验等。
决定浆料性能的因素有陶瓷粉料的成分与颗粒形状、增塑剂的成分和性质、粉料和增塑剂的比例等。
陶瓷型芯的质量很大程度上取决于素胚的压制质量,压制压力、锁模压力、浆料温度、保压时间等是影响陶瓷型芯压制质量的主要原因。
蜡模的制造工艺:合格的蜡型是制备精密铸件的前提,压制蜡型时,将陶芯放入蜡型模具中,并依靠定位元件对其定位。
生产中大多采用压力把糊状模料压入压型的方法制造熔模。
压制蜡基模料时,分型剂可为机油、松节油等;分型剂层越薄越好,使熔模能更好地复制压型的表面,提高熔模的表面光洁度。
模料压制温度、压注压力、保压时间、压型温度、和模力、分型剂种类及其用量,以及制模和存放熔模的环境都会影响蜡模的质量。
熔模铸型的制造工艺:首先是熔模的组装,把形成铸件的熔模和形成浇冒口系统的熔模组合在一起,主要采用焊接法,用薄片状的烙铁,将熔模的连接部位熔化,使熔模焊在一起。
后再经过若干次涂料、挂砂,干燥硬化,密封加固,脱蜡,焙烧最终制成型壳。
型壳的性能与质量取决于面层与加固层材料的性能、相应涂挂工艺和过程控制。
合金浇铸工艺:高温合金熔模精密铸造广泛使用真空感应熔炼浇注。
影响其工艺的主要因素有母合金棒锭的质量,熔炼浇注用陶瓷制件的质量,浇注工艺参数(浇注温度、浇注速度、型壳温度、冷却速度)。
提高涡轮叶片精铸尺寸精度的工艺措施
影响涡轮叶片精铸尺寸精度的因素较多,例如模料的收缩、熔模的变形、型壳在加热和冷却过程中的线量变化、合金的收缩率以及在凝固过程中铸件的变形等。
采用模具型腔反变形补偿方法是提高涡轮叶片精铸尺寸精度的一个有效手段。
铸造中,浇注后叶片的尺寸变形最大,高温液态合金注入模壳后,随温度的降低,会产生收缩变形,同时会产生弯曲变形和弯扭变形。
为了有效地防止变形的产生,采用在传统的模具设计时考虑对收缩变形的补偿,通过数值模拟方法或者经验方法获得变形量,然后向与变形相反的方向预留一定的变形量,这样在变形后就会获得与设计模型一致的铸件。
由于涡轮叶片外形复杂,仅采用一次位移场补偿的方法,很难达到精度要求。
可以通过迭代法可以较为精确地逼近外形。