DFX面向产品生命周期的设计
DFX面向产品生命周期的设计详解

2011年7月
出现背景
自80年代以来, 市场竞争的国际化, 促使制 造业企业不断寻求产品开发的新思路、新 方法并应用于有竞争力的产品的开发
一个典型的例子是美国企业在承受着日本 70年代以后在汽车、半导体等行业逐步确 立的世界市场优势地位的压力下, 积极调整 产业结构, 学习和采用新的产品开发思想、 策略、方法, 如并行工程、虚拟制造、敏捷 制造、精良生产等等, 为美国经济在90年代 的振兴产生了重要的促进作用
DFA 面向装配的设计
最早,目前最成熟的DFX方法 旨在提高装配的方便性以减少装配时间、 成本的设计
DFA 面向装配的设计
原则:1.减少零件数 2.采用标准紧固件和其他标准零件 3.零件的方位保持不变 4.采用模块化的部件 5.设计可直接插入的零件 6.尽量减少调整的需要 7.适合自动生成线生产
DFX是Design for X的缩写。其中,X代表 产品生命周期或其中某一环节,也可以代 表产品竞争力或决定产品竞争力的因素 其中的Design不仅仅指产品的设计,也指 产品开发过程和系统的设计
DFX的内涵
DFX是一种哲理、方法、手段、工具 所有的产品开发人员都应该认识到, 在设计阶段尽 早地考虑产品全生命周期将有益于产品竞争力的 提高。 产品设计人员、产品开发管理人员应该积极应用 DFX方法于产品设计 借助计算机实现的DFX工具可以有效地辅助产品 设计人员按照DFX方法进行产品设计
DFS 面向维修的设计
售后服务是现代企业非常重视的环节之一。 产品的售后服务主要是指产品维修 维修总是伴随着拆卸和重装,产品维修性 主要取决于产品故障确定的容易程度、产 品的可拆卸性和可重装性,减少拆卸重装 的时间与成本是DFS的重要问题 维修性也取决于产品的可靠性,要尽量使 容易发生故障的零部件处于容易拆卸的位 置, 从而有利于维修时间与成本的减少
面向产品全生命周期的设计技术 DFx

面向产品全生命周期的设计技术,即DFx技术是一种集成化设计技术,其综合了计算机技术、制造技术、系统集成技术和管理技术,充分体现了系统化的思想。
利用DFx技术,可以在设计阶段尽早地考虑产品的性能、质量、可制造性、可装配性、可测试性、产品服务和价格等因素,对产品进行优化设计或再设计。
最常见的DFx技术有:面向装配的设计(Design for Assembly,DFA)、面向制造的设计(Design for Manufacturing,DFM)、面向性能的设计(Design for Compatibility,DFC)、面向方案的设计(Design for Variety,DFV)、绿色设计(Design for Green,DFG)和后勤设计(Design for Logistics,DFL)等。
面向装配的设计是一种针对零件配合关系进行分析的设计技术。
它为产品设计在早期提供一种确定装配所用的定量方法。
其原则包括最小零件数、最少接触面和易装配。
类似地,面向制造的设计则引入诸如零件最少原则和易制造原则等指导产品的设计。
在面向性能的设计中,设计团队从产品整个生命周期的角度审查有关产品的所有独立的规则集,从而完成产品界面及功能设计、零件特征设计、加工方法选用、工艺性设计和工艺方案的选择等。
面向方案的设计是为了从不同设计方案中选择花费最小的方案,它涉及产品设计方案的数量、产品设计阶段和产品设计更改的代价等因素。
绿色设计指在产品设计时从对环境的影响角度出发,考虑产品在全生命中的使用。
后勤设计是指设计人员在设计时利用不同的约束进行产品设计,如费用驱动约束、最小时间约束等。
第五章 设计过程质量管理

4.保障性
系统(装备)的设计特性和计划的保障资源满足平时和战时使用要求的 能力称为保障性。保障性是装备系统的固有属性,它包括两方面含义, 即与装备保障有关的设计特性和保障资源的充足和适用程度。 设计特性是指与保障有关的设计特性,如与可靠性和维修性等有关的, 以及保障资源要求装备所具有的设计特性。这些设计特性可以通过设 计直接影响装备的硬件和软件。如使设计的装备便于操作、检测、维 修、装卸、运输、消耗品(油、水、气、弹)补给等设计特性。从保障 性角度看,良好的保障设计特性是使装备具有可保障的特性或者说所 设计的装备是可保障的。 保障资源是保证装备完成平时和战时使用的人力和物力。从保障性的 角度看,充足的并与装备匹配完善的保障资源说明装备是能得到保障 的。 装备具有可保障的特性和能保障的特性才是具有完整保障性的装备。
12
5.可用性和可信性
可用性是在要求的外部资源得到保证的前提下,产品在规定的条 件下和规定的时刻或时间区间内处于可执行规定功能状态的能力。 它是产品可靠性、维修性和维修保障的综合反映,这里的可用性 定义是固有可用性的定义,外部资源(不包括维修资源)不影响产品 的可用性。反之,使用可用性则受外部资源的影响。可用性的概 率度量称为可用度。可用性通俗地说是“要用时就可用”。实际 上,可靠性和维修性都是为了使顾客手中的产品随时可用。可靠 性是从延长其正常工作时间来提高产品可用性,而维修性则是从 缩短因维修的停机时间来提高可用性。可用性是顾客对产品质量 的又一重要的需求。 可信性是一个集合性术语,用来表示可用性及其影响因素:可靠 性、维修性、维修保障。可信性仅用于非定量条款中的一般描述, 可信性的定性和定量具体要求是通过可用性、可靠性、维修性、 维修保障的定性和定量要求表达的。
通过DFX设计提高电子产品的质量与可靠性

・传 统 的设计流程
◆导入D x 的设计流程 F后
性 、高效性和经济 性 ,DM 目标是 F的
在保证产 品质量与可靠性的前提 下缩 短产品开发周期、降低产品成本 、提
高加工效 率 。DX 电子产 品设计 中 F在 的 出现有其深刻的历史背景 ,这是 由
于 电子产品竞争越来越激烈 ,公司必 须保证产 品能够快速 、高质 量的进入
二 、电子产 品设计 中采用D X 设计看成为一个孤立的任务,利用现 F 的意义
D X 目的是提倡在产 品的前期 F的 设计中考虑包括可制造性 、可装配性 代 化设计 工具和 DX F 分析工具 设计具 有 良好工程 特性 的产 品。图l 所示为 电子产 品传统 设计流程 与D x F 设计流
品的概念设计和详细设计阶段就综合
三、业界领先公 司的D X F 设计
成 功实施D X F 的一个关键 因素就
过程和系统设计时不但要考虑产品的 考虑到制造过程 中的工艺要求、测试
F 设计 团队进行沟通 。 功能和性 能要求,而且要 同时考虑产 要求 、组装的合理性 ,同时还考虑 到 是 要尽早 与DX 品整个生命周期相关的工程 因素,只 有具备 良好工程特性的产 品才是既满 足客户需求,又具备 良好 的质量、可 靠性与性价 比产品,这样的产品才 能 在市场得 到认可 。D M F 中最重要 F 是D X 的部 分,IM ) 就是 要考虑制造 的可 能 F 维修要求、售后服务要求、可靠性要 在项 目正式启动前就要经常进行工程
可 靠性 ( R la iiy 等 。DX 要 等相关 问题 。传 统的电子产品开发方 R e ib lt) F主 包 括 : 可 制 造 性 设 计 DM D sg 法通常是设 计一 生产制造一 销售 各 F : e in
DFX面向产品生命周期的设计

项目管理与实践
项目管理
将DFX的实施纳入项目管理范畴,制定详 细的项目计划和时间表,确保各项任务 按时完成。
VS
实践经验
借鉴和总结实践经验,不断完善DFX的实 施流程和方法,提高实施效果和产品质量 。
持续改进与优化
持续改进
在DFX实施过程中不断发现问题和不足,及时采取措施进行改进,提高DFX的成熟度和 可靠性。
dfx面向产品生命周期的 设计
• 引言 • DFX概述 • DFX在产品生命周期中的应用 • DFX实施的关键因素 • DFX实施案例分析 • DFX的未来发展与挑战
01
引言
主题简介
主题概述
dfx面向产品生命周期的设计是一种全面、集成的方法,旨在确保产品在整个生 命周期内具有最佳的性能、可靠性和可维护性。
人工智能与DFX
利用AI技术进行数据分析和预测,优化产品设计、生产和维护过 程。
数字化与DFX
借助数字化工具和平台,实现产品生命周期的全面数字化管理,提 高设计效率。
增材制造与DFX
利用增材制造技术,实现定制化、复杂化产品的快速设计和生产。
DFX在全球化环境中的挑战
跨文化沟通
在全球团队中,需克服语言和文化差异,确保信息准确传递和有效 协作。
03
DFX在产品生命周期中的应用
需求分析阶段的DFX应用
需求分析
DFX可以帮助团队更好地理解产品需求,包括功 能、性能、可靠性、可用性和可维护性等。
需求优先级排序
DFX可以协助团队对需求进行优先级排序,以便 在资源有限的情况下,优先满足最重要的需求。
需求变更管理
DFX可以帮助团队更好地管理需求变更,确保产 品设计的灵活性和可维护性。
设计中的DFX技术

包含三个成份的:
CAD和CAM数据库界面
工艺选择指南
工业工艺流程策划指南
计算机辅助工艺规划(computer aided process planning——CAPP)。
这些计算机辅助技术最初并不是专门为并
行工程开发地,而多数是在计算机集成制造系
统(CIMS)的发展过程中开发成的。
各种质量保证技术的有机结合
稳健设计与SPC
稳健设计用到的主要方法以统计理论为 基础。CE及先进的产品开发与生产模式对 质量保证的要求,使得稳健设计技术不断 发展,并为稳健设计技术的发展注入新的 活力。
稳健设计中主要涉及的方法
稳健设计的内容包括产品设计和工艺设计两个 方面,分系统设计、参数设计和容差设计三个阶 段,利用质量损失函数(Loss Function),即由于 参数的波动引起的费用损失来衡量质量,进而对 设计进行优化。
效方法。
DFX是TQM在并行工程中的体现。TQM的观 点认为,质量管理中的用户不仅是使用产品的最 终用户,在产品形成过程中的每个环节,下一环 节就是上一环节的用户,如产品设计是市场调研 的用户,工艺过程设计是产品设计的用户,制造/ 装配是工艺过程设计的用户,销售是制造/装配的 用户等。
而DFX正是体现产品设计过程中除满足 最终用户对产品质量的要求外,还应满足 其后续环节作为广义用户的要求。
由于各种质量保证和控制技术都是为适应某 特定过程或场合而设计的,在CE、AM等先进生产 系统和模式中,对质量保证和控制的集成性、并 行性和交叉性的要求,使得它们相互间独立运用 已变得不适应,只有集成及相互结合,才能发挥 积极作用。
一、QFD与田口方法的结合
QFD可用于田口设计中的系统设计,通过
QFD的顾客需求到工程特性及工程特性到零件技
面向“X”的设计DFX

第七章 面向“X”的设计DFX
§7.2 面向制造的设计
1 面向制造的设计的思想、原理
DFX是在产品的设计阶段就尽早地考虑与产品制造有关的约束(如可制造 性)、全面评价产品设计和工 艺设计,同时提供产品设计的 反馈信息,在设计过程中完成 可制造性预测,以使产品的结 构合理、制造简单、装配性好, 并实现全局优化从而缩短产品 的开发周期。
33
32
6/17/2020
第七章 面向“X”的设计DFX
§7.3 面向拆卸的设计
4 面向拆卸的设计评价
面向拆卸的设计评价是对设计方案进行评价--修改--再评价--再修 改直至满足设计要求的动态过程。 评价指标主要由两方面的指标组成: 与拆卸过程有关的指标: 拆卸费用、拆卸时间、拆卸过程的能量消耗和拆卸过程的环境影响。 与连接结构性有关的指标: ✓可达性 ✓标准化程度 ✓产品结构的复杂程度
15
6/17/2020
第七章 面向“X”的设计DFX
§7.2 面向制造的设计
5 减少装配成本
利用评分 DFA系数:理论装配最小时间与实际装配时间的比值 DFA系数=(理论最小部件数)*(3秒)/实际装配时间 组合部件 如果一个部件在理论上没有限定是独立的,那么就可以与其他一个或多个 部件合成一个部件。优点: ✓被组合的部件之间不需要装配 ✓组合件成本通常比组合前部件成本低 ✓在组合件中,被组合件的尺寸精度更高
27
6/17/2020
第七章 面向“X”的设计DFX
§7.3 面向拆卸的设计
2 面向拆卸的设计准则
拆卸工作量最少原则 简化产品结构和外形,减少零件材料种类;简化维护及拆卸回收工作,降 低对维护、拆卸回收人员的技术要求。 ✓明确所要拆卸的零部件 ✓功能集成 ✓减少材料种类 ✓有害才来哦的集成准则 ✓拆卸目标零件易于接近准则
DFX 案例整理ppt课件

DFM
DFA
DFC
D4
4
DFx同步工程
設計 週期
C0~C1 kick off
C2 Mock Up
驗證 週期 DFx1
DFx2
Review 重點
ID共用性及包裝標準化傳輸于PM/業務和客戶端定義.
設計端review.包含標準化,模組化,自動化及DFM 中功能性項目確認.
C3 EVT
DFx3
再次確認智能生產理念導入,模具品及制程能力確認.
C4 DVT
DFx4
FW及幾率性問題驗證.
C5 PVT
DFx5
Review DFM Check List,及光學項目的制程能力確認.
MP
入系統
沒有考慮 DFx
概念設計 詳細設計
樣機製作和設計修改
考慮DFx
縮短開發時間
QCDST
5
5
DFX管控制程分佈
標 準 化
2.光機內部光照區域禁用rubber等易揮發材質
目 的 避免因溫度或MTBF 燒機后揮發異物影響畫面品質.
圖示說明
畫面霧氣
Chip 表面 附著揮發物
OFF RAY PAD 材質: PPS
評 論 差異化材料使用到不同平臺,同樣做標準化
9
OFF RAY PLATE 材質:壓鑄+電槳陽極
9
Engine案例說明-DFM
1.檢驗標準統一分硬體和軟體 2.線外建議軟體的內容 3.確認適合可靠性驗證標準 4.適應自動化檢驗
1.包裝材料簡化標準 2.包裝后運輸方式確認 3.包裝端建議項目的簡化
6
40項 27項
53項 23項 11項
6
PCBA案例說明-DFM
《面向X的设计DFX》课件
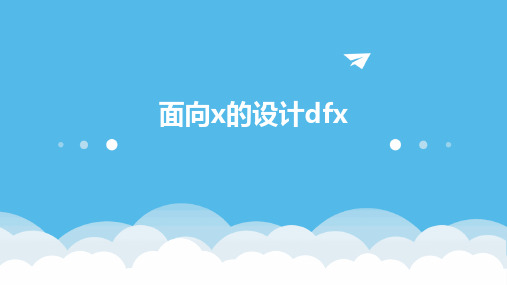
针对不同行业和领域的需求,DFX技 术将提供更加定制化的解决方案, 满足特定设计要求。
DFX在未来的应用场景
01
汽车制造
随着电动汽车和智能网联汽车 的发展,DFX将在电池管理、 车载电子、自动驾驶等方面发
挥重要作用。
02
航空航天
高性能计算和仿真技术的发展 ,使得DFX在航空发动机、先 进复合材料等领域的应用更加
通过提供清晰的用户界面、文档和指示,可以提高产品的易用性和用户满意度。
透明原则要求设计师注重与用户的沟通和反馈,了解用户需求和习惯,以便更好地 满足他们的期望。
反馈原则
反馈原则强调在产品设计中应 提供及时、准确和有用的反馈 信息,以便用户能够更好地理 解和使用产品。
反馈可以通过声音、视觉和触 觉等多种方式实现,例如语音 提示、指示灯和振动反馈等。
设计阶段
架构设计
根据需求规格说明书,设计系统的整体架构,包 括系统结构、模块划分、接口定义等。
详细设计
对各个模块进行详细设计,包括模块的功能、输 入输出、算法流程等。
接口设计
设计模块之间的通信接口,包括数据接口和功能 接口,确保模块之间的协调和交互。
测试阶段
单元测试
01
对每个模块进行单元测试,验证模块的功能和性能是否符合设
和稳定性。
成本问题
DFX技术的应用需要相应的软硬件投 入,成本较高,应通过优化技术方案
、降低成本等方式解决。
人才短缺
DFX技术涉及多个领域,需要跨学科 的复合型人才,应加强人才培养和引 进。
标准化与互操作性
不同DFX工具之间的标准化和互操作 性有待提高,应推动相关标准和规范 的制定与实施。
THANKS
DFX工艺设计方法介绍

• DFM:Design for Manufacture 可生产性设计 • DFR:Design for Reliability 为可靠性而设计 • DFA:Design for Assembly 可组装性设计 • DFT:Design for Testability 可测试性设计 • DFC: Design for Cost 成本设计 • DFE:Design for Environment 可环保设计 • DFD:Design for Diagnosis 可诊断分析设计
PCBA工艺设计关注重点
• DFF:Design for Fabrication of the PCB 为PCB可制造而设计
• DFS:Design for Serviceability 可服务设计 • DFP:Design for Procurement 可采购设计 • ……
DFX设计业界应用----思科
➢ 增加决策分析流程,指导项目组如何进行决策
➢ 从源头进行梳理,优化市场需求管理流程,强化产品战略部的市场需求管理、产品规 划的职能,逐步引导项目组建立以市场需求为核心的开发理念。
➢ 优化度量系统,根据组织业务需要,确定关键子过程,并对关键子过程进行度量,形 成度量指标
➢ 关键子过程增加准入/准出机制,建立过程符合度检查机制,加强对过程的监控,促进
DFX设计业界应用----IBM,华为等公司应用情况
➢ IBM于1992年首先将集成产品开发流程IPD(Integrated Product Development)付诸实践 ,实现了其将产品上市时间缩短一半,不影响开发结果的情况下,研发费用减少一半 的目标。
产品全生命周期设计

产品全生命周期设计产品全生命周期设计2011年07月13日产品全生命周期设计机械产品的全生命周期设计是多学科融合的综合科学,并涉及许多新兴学科和现代先进技术。
探讨了机械产品全生命周期设计概念和思想、主要研究内容和涉及的学科前沿课题。
全生命周期设计的提出和建立是现代设计理论发展的产物,也将是机械设计发展的必然方向。
1、全生命周期设计的基本概念1.1、全生命周期产品的全生命周期与产品的寿命是不同的概念。
产品的全生命周期包括产品的孕育期(产品市场需求的形成、产品规划、设计)、生产期(材料选择制备、产品制造、装配)、储运销售期(存储、包装、运输、销售、安装调试)、服役期(产品运行、检修、待工) 和转化再生期(产品报废、零部件再用、废件的再生制造、原材料回收再利用、废料降解处理等) 的整个闭环周期。
而产品的寿命往往指产品出厂或投入使用后至产品报废不再使用的一段区间, 仅是全生命周期内服役期的一部分。
由于传统的产品功能和性能主要在服役期实现, 传统设计主要为产品的运行功能设计和产品的使用寿命以及近年来日益重视的产品自然寿命设计。
基于产品的社会效应, 全生命周期包括对产品的社会需求的形成, 产品的设计、试验、定型, 产品的制造、使用、维修以及达到其经济使用寿命之后的回收利用和再生产的整个闭环周期。
如图1所示, 机械的全生命周期涵盖全寿命期, 全寿命期涵盖经济使用寿命和安全使用寿命。
图1 全生命周期与全寿命期作为全生命周期的一个重要转折点, 产品报废一般有3 种判据: 功能失效、安全失效、经济失效。
1.2、全生命周期设计所谓全生命周期设计, 就是面向产品全生命周期全过程的设计, 要考虑从产品的社会需求分析、产品概念的形成、知识及技术资源的调研、成本价格分析、详细机械设计、制造、装配、使用寿命、安全保障与维修计划, 直至产品报废与回收、再生利用的全过程, 全面优化产品的功能ö性能 (F)、生产效率(T )、品质ö质量(Q )、经济性(C)、环保性(E) 和能源ö资源利用率(R ) 等目标函数,求得其最佳平衡点。
DFX面向产品生命周期的设计1

并行工程——生命周期工程
? 集成地、并行地设计产品及其相关的各种过程(包括制 造与支持)
? 要求产品开发人员在设计一开始就考虑产品整个生命周 期中从概念形成到产品报废处理的所有因素
? 强调一切设计活动尽早开始,力争一次获得成功,关键 是产品及其相关过程设计工作的并行集成
11
串行工程与并行工程的对比
25
DFS 面向维修的设计
? 售后服务是现代企业非常重视的环节之一。产品的售后 服务主要是指产品维修
? DFX不仅用于改进产品本身,而且用于改进产品相关过 程(如装配和加工)和系统
17
? 以往当产品设计完毕, 再接着进行过程设计(体现 串行工程思想)
? DFX方法强调产品设计和过程设计的同时进行(体 现了并行工程思想)
18
典型的DFX方法
? DFA(Design for Assembly) 面向装配的设计 ? DFM(Design for Manufacture) 面向制造的设计 ? DFI(Design for Inspection) 面向检验的设计 ? DFS(Design for Service/Maintain/Repair) 面向
成本
23
DFI 面向检验的设计
? 着重考虑产品、过程、人的因素以便提高产品检验的方 便性
? 加工中的产品检验是为了提供快速精确的加工过程反馈 , 而维修中的产品检验则是为了快速而准确地确定产品结 构或功能的缺陷, 及时维修以保证产品使用的安全
24
DFI 面向检验的设计
? 产品检验方便性取决于色彩、零件内部可视性、结构等 等诸多因素
型 ? 60、70年代后,DFX研究得到重视
14
DFX的含义
? DFX是Design for X 的缩写。其中,X代表产品生命周期 或其中某一环节,也可以代表产品竞争力或决定产品竞 争力的因素
通过DFX设计提高电子产品的质量与可靠性

通过DFX设计提高电子产品的质量与可靠性1、 DFx简介DFX是Design for X(面向产品生命周期各环节的设计)的缩写,其中X代表产品生命周期的某一环节或特性,如可制造性(M-Manufacturability)、可装配性(A-Assembly)、可靠性(R- Reliability)等。
DFX主要包括:可制造性设计DFM: Design forManufacturability,可装配性设计DFA: Design forAssembly,可靠性设计DFR: Design forReliability,可服务性设计DFS: DesignforServiceability,可测试性设计DFT: Design for Test,面向环保的设计DFE: Design for Environment等。
DFX设计方法是世界上先进的新产品开发技术, 这项技术在欧美大型企业中应用非常广泛, 指在产品开发过程和系统设计时不但要考虑产品的功能和性能要求, 而且要同时考虑产品整个生命周期相关的工程因素,只有具备良好工程特性的产品才是既满足客户需求,又具备良好的质量、可靠性与性价比产品,这样的产品才能在市场得到认可。
DFM是DFX中最重要的部分,DFM就是要考虑制造的可能性、高效性和经济性,DFM的目标是在保证产品质量与可靠性的前提下缩短产品开发周期、降低产品成本、提高加工效率。
DFX在电子产品设计中的出现有其深刻的历史背景,这是由于电子产品竞争越来越激烈,公司必须保证产品能够快速、高质量的进入市场,适应电子产品短生命周期的要求。
2、电子产品设计中采用DFX的意义DFX的目的是提倡在产品的前期设计中考虑包括可制造性、可装配性等相关问题。
传统的电子产品开发方法通常是设计---生产制造---销售各个阶段串行完成。
由于设计阶段没有全面考虑制造要求,加之设计人员对工艺知识的欠缺,总会造成在产品生产时出现这样那样的问题,如元器件选择不当、PCB设计缺陷等,导致设计方案多次修改、PCB不断改板、生产多次验证等,使得产品开发周期延长、成本增加、质量和可靠性得不到有效保证。
设计中的DFX技术

在开发过程中大量应用的质量保证手段
占企业百分比 主要应用领域
质量功能配制 产品故障模式与影响分析
5 55
62 89 96 90 33 62 50 71 28 100 100 87 45 53 31 83
生产过程 开发过程
工艺故障模式与影响分析
故障树分析 实验设计 实验评估 统计工艺控制 质量圈 波卡—约基 产品评估 27
一种替代方法是预防检测和评价,即在缺陷 形成之前就进行检测和评价,对产生质量问题的 根源进行分析,找出造成质量问题的原因,对其 予以预防和消除。
二、在小批量产品制造中的应用
SPC一般建立在大量样本统计的基础上,然 而,当代企业和市场正在向着多品种小批量生产 的方向发展。 如何利用SPC理论对多品种小批量生产过程 的质量进行控制,成为SPC应用研究需要解决的 问题。 在这方面国内外已有相应研究。
包含三个成份的:
CAD和CAM数据库界面 工艺选择指南 工业工艺流程策划指南
计算机辅助工艺规划(computer aided process planning——CAPP)。
这些计算机辅助技术最初并不是专门为并 行工程开发地,而多数是在计算机集成制造系 统(CIMS)的发展过程中开发成的。
各种质量保证技术的有机结合
90
95
系统评估
优质企业 一般企业
85
产品开发中普遍采用的并行工程技术和方法
QFD
QFD、DFM和 PDCA QFD、产品FMEA 田口方法和DFM QFD、 PDCA和工序FMEA QFD、 工序FMEA、田口方法、过程能力 统计过程设计PDCA
确定要求
机械产品全生命周期设计方法概述
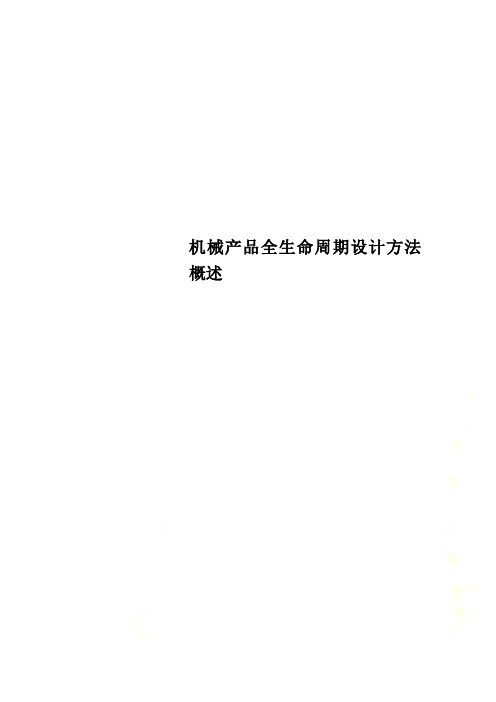
机械产品全生命周期设计方法概述产品全生命周期设计方法概述张翔胡冰乐郑金凤(福建农林大学机电工程学院,福建福州350002)摘要:介绍全生命周期设计的基本概念及其内容,还有全生命周期的相关技术。
产品的全生命周期设计融合多学科的内容, 并涉及许多新兴学科和现代先进技术。
给出了产品全生命周期设计实际应用中的相关要求。
关键词:全生命周期设计;绿色设计;并行设计;产品设计中图分类号:TH122 文献标识码:AProduct Life Cycle Design Method Overview ZHANG Xiang,HU Bing-le, ZHENG Jin-feng (College of Mechanical and Electronic Engineering, Fujian Agriculture and Forestry University, Fuzhou 350002, China) Abstract:Describes the whole basic concept of life cycle design and content, as well as full life-cycle of therelated technologies. The design of the product life-cycle integrate content of multi-disciplinary, and involve an abundance of emerging disciplines and modern advanced technology. Giving the relevant requirements of the product life cycle design in the practical applicationKey words:Full life cycle design; Green design;Concurrent design; Product Design1 引言进入廿十一世纪以来,随着全球经济的高速发展,人类在消耗自然资源、生产制造大量产品的同时,又在不断地加剧生态环境的恶化,地球日渐变暖、大气严重污染、陆地逐渐减少、水土大量流失、耕地瞬间沙化。
思维导图告诉你DFX,EVT,DVT,PVT,MP,DFLC
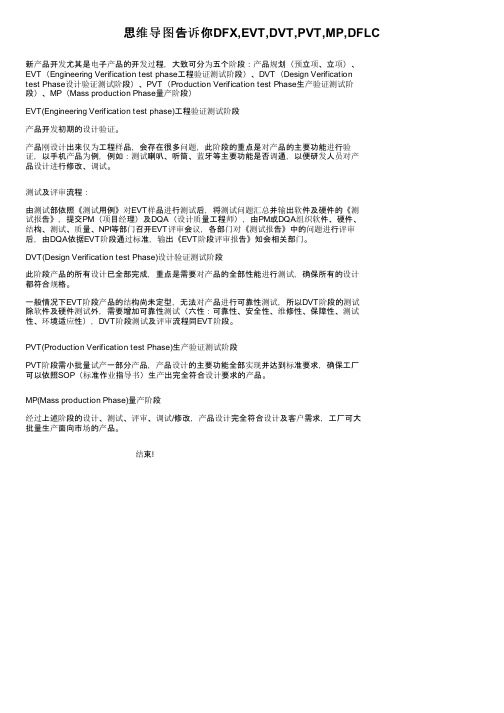
思维导图告诉你DFX,EVT,DVT,PVT,MP,DFLC 新产品开发尤其是电子产品的开发过程,大致可分为五个阶段:产品规划(预立项、立项)、EVT(Engineering Verification test phase工程验证测试阶段)、DVT(Design Verificationtest Phase设计验证测试阶段)、PVT(Production Verification test Phase生产验证测试阶段)、MP(Mass production Phase量产阶段)EVT(Engineering Verification test phase)工程验证测试阶段产品开发初期的设计验证。
产品刚设计出来仅为工程样品,会存在很多问题,此阶段的重点是对产品的主要功能进行验证,以手机产品为例,例如:测试喇叭、听筒、蓝牙等主要功能是否调通,以便研发人员对产品设计进行修改、调试。
测试及评审流程:由测试部依照《测试用例》对EVT样品进行测试后,将测试问题汇总并输出软件及硬件的《测试报告》,提交PM(项目经理)及DQA(设计质量工程师),由PM或DQA组织软件、硬件、结构、测试、质量、NPI等部门召开EVT评审会议,各部门对《测试报告》中的问题进行评审后,由DQA依据EVT阶段通过标准,输出《EVT阶段评审报告》知会相关部门。
DVT(Design Verification test Phase)设计验证测试阶段此阶段产品的所有设计已全部完成,重点是需要对产品的全部性能进行测试,确保所有的设计都符合规格。
一般情况下EVT阶段产品的结构尚未定型,无法对产品进行可靠性测试,所以DVT阶段的测试除软件及硬件测试外,需要增加可靠性测试(六性:可靠性、安全性、维修性、保障性、测试性、环境适应性),DVT阶段测试及评审流程同EVT阶段。
PVT(Production Verification test Phase)生产验证测试阶段PVT阶段需小批量试产一部分产品,产品设计的主要功能全部实现并达到标准要求,确保工厂可以依照SOP(标准作业指导书)生产出完全符合设计要求的产品。