叶片的加工方法
叶片曲面加工方法
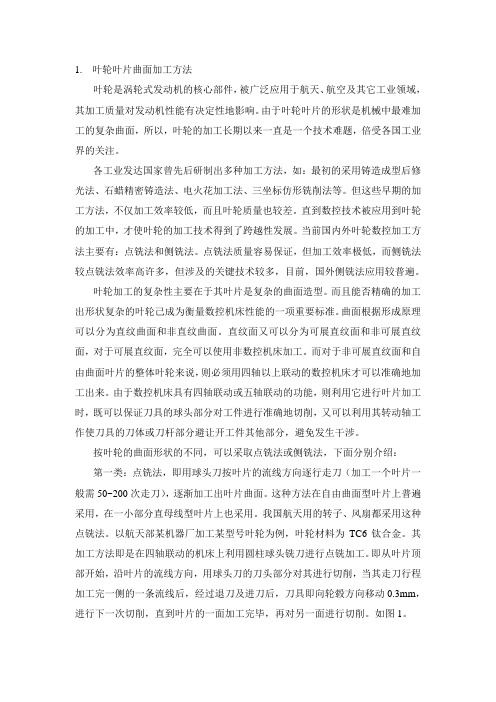
1.叶轮叶片曲面加工方法叶轮是涡轮式发动机的核心部件,被广泛应用于航天、航空及其它工业领域,其加工质量对发动机性能有决定性地影响。
由于叶轮叶片的形状是机械中最难加工的复杂曲面,所以,叶轮的加工长期以来一直是一个技术难题,倍受各国工业界的关注。
各工业发达国家曾先后研制出多种加工方法,如:最初的采用铸造成型后修光法、石蜡精密铸造法、电火花加工法、三坐标仿形铣削法等。
但这些早期的加工方法,不仅加工效率较低,而且叶轮质量也较差。
直到数控技术被应用到叶轮的加工中,才使叶轮的加工技术得到了跨越性发展。
当前国内外叶轮数控加工方法主要有:点铣法和侧铣法。
点铣法质量容易保证,但加工效率极低,而侧铣法较点铣法效率高许多,但涉及的关键技术较多,目前,国外侧铣法应用较普遍。
叶轮加工的复杂性主要在于其叶片是复杂的曲面造型。
而且能否精确的加工出形状复杂的叶轮己成为衡量数控机床性能的一项重要标准。
曲面根据形成原理可以分为直纹曲面和非直纹曲面。
直纹面又可以分为可展直纹面和非可展直纹面,对于可展直纹面,完全可以使用非数控机床加工。
而对于非可展直纹面和自由曲面叶片的整体叶轮来说,则必须用四轴以上联动的数控机床才可以准确地加工出来。
由于数控机床具有四轴联动或五轴联动的功能,则利用它进行叶片加工时,既可以保证刀具的球头部分对工件进行准确地切削,又可以利用其转动轴工作使刀具的刀体或刀杆部分避让开工件其他部分,避免发生干涉。
按叶轮的曲面形状的不同,可以采取点铣法或侧铣法,下面分别介绍:第一类:点铣法,即用球头刀按叶片的流线方向逐行走刀(加工一个叶片一般需50~200次走刀),逐渐加工出叶片曲面。
这种方法在自由曲面型叶片上普遍采用,在一小部分直母线型叶片上也采用。
我国航天用的转子、风扇都采用这种点铣法。
以航天部某机器厂加工某型号叶轮为例,叶轮材料为TC6钛合金。
其加工方法即是在四轴联动的机床上利用圆柱球头铣刀进行点铣加工。
即从叶片顶部开始,沿叶片的流线方向,用球头刀的刀头部分对其进行切削,当其走刀行程加工完一侧的一条流线后,经过退刀及进刀后,刀具即向轮毂方向移动0.3mm,进行下一次切削,直到叶片的一面加工完毕,再对另一面进行切削。
螺旋叶片加工工艺
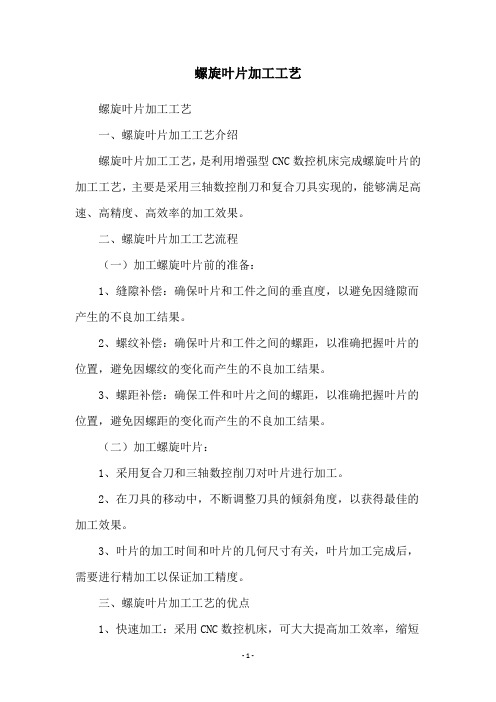
螺旋叶片加工工艺
螺旋叶片加工工艺
一、螺旋叶片加工工艺介绍
螺旋叶片加工工艺,是利用增强型CNC数控机床完成螺旋叶片的加工工艺,主要是采用三轴数控削刀和复合刀具实现的,能够满足高速、高精度、高效率的加工效果。
二、螺旋叶片加工工艺流程
(一)加工螺旋叶片前的准备:
1、缝隙补偿:确保叶片和工件之间的垂直度,以避免因缝隙而产生的不良加工结果。
2、螺纹补偿:确保叶片和工件之间的螺距,以准确把握叶片的位置,避免因螺纹的变化而产生的不良加工结果。
3、螺距补偿:确保工件和叶片之间的螺距,以准确把握叶片的位置,避免因螺距的变化而产生的不良加工结果。
(二)加工螺旋叶片:
1、采用复合刀和三轴数控削刀对叶片进行加工。
2、在刀具的移动中,不断调整刀具的倾斜角度,以获得最佳的加工效果。
3、叶片的加工时间和叶片的几何尺寸有关,叶片加工完成后,需要进行精加工以保证加工精度。
三、螺旋叶片加工工艺的优点
1、快速加工:采用CNC数控机床,可大大提高加工效率,缩短
加工时间。
2、精度高:采用CNC数控机床,可以满足极高的加工精度要求,优于手动加工的精度。
3、可靠性高:加工过程中能够自动监控,确保叶片的准确性和可靠性。
4、使用灵活:加工叶片的尺寸可以自由调节,加工效率高,适用于大批量生产,也可适用于小批量生产。
绞龙的叶片怎么加工?
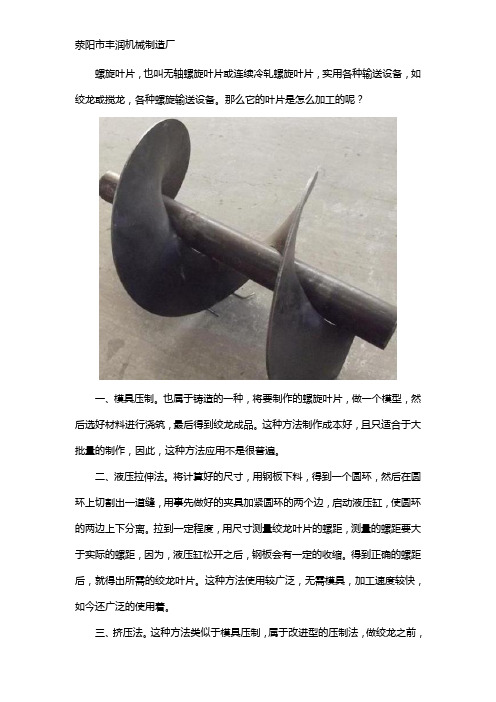
螺旋叶片,也叫无轴螺旋叶片或连续冷轧螺旋叶片,实用各种输送设备,如绞龙或搅龙,各种螺旋输送设备。
那么它的叶片是怎么加工的呢?
一、模具压制。
也属于铸造的一种,将要制作的螺旋叶片,做一个模型,然后选好材料进行浇筑,最后得到绞龙成品。
这种方法制作成本好,且只适合于大批量的制作,因此,这种方法应用不是很普遍。
二、液压拉伸法。
将计算好的尺寸,用钢板下料,得到一个圆环,然后在圆环上切割出一道缝,用事先做好的夹具加紧圆环的两个边,启动液压缸,使圆环的两边上下分离。
拉到一定程度,用尺寸测量绞龙叶片的螺距,测量的螺距要大于实际的螺距,因为,液压缸松开之后,钢板会有一定的收缩。
得到正确的螺距后,就得出所需的绞龙叶片。
这种方法使用较广泛,无需模具,加工速度较快,如今还广泛的使用着。
三、挤压法。
这种方法类似于模具压制,属于改进型的压制法,做绞龙之前,
需要做一套尺寸和成品一样的模具。
模具分为两个,形状和尺寸一样,分别安置于压力机的上下部,然后将下好料的圆环放置于模具上,启动压力机,使上下模具压在一起,钢板随之变形,形成螺旋状。
荥阳市丰润机械制造厂于2003月28日成立,以建筑机械而闻名全国的建筑之乡——荣阳,是一家专门从事建筑机械配件的生产,研发,营销,与服务的企业。
欢迎大家官方或致电咨询。
麻叶制作方法

麻叶制作方法
麻叶,又称大麻叶,是一种常见的植物叶子,具有丰富的营养
价值和药用价值。
麻叶可以用来制作各种美食和药品,具有清热解毒、消肿止痛等功效。
下面我们来介绍一下麻叶的制作方法。
首先,选择新鲜的麻叶。
新鲜的麻叶叶片完整,颜色鲜绿,质
地柔软,没有黄斑和病斑。
在采摘麻叶时,要选择天气晴朗、干燥
的日子,避免雨水或露水浸湿麻叶。
采摘下来的麻叶要立即进行加工,以保持其新鲜度和营养价值。
接下来,清洗麻叶。
将采摘下来的麻叶放入清水中浸泡,轻轻
搅动,使麻叶表面的杂质和尘土浮起,然后取出麻叶,用清水反复
漂洗,直至洗净。
洗净的麻叶放在通风处晾干,去除多余水分。
然后,进行晒干。
将洗净的麻叶摊放在通风干燥的地方,避免
阳光直射,以免麻叶失去颜色和营养。
麻叶晒干后,可以保存更久,也更方便后续的制作和使用。
最后,根据需要进行加工。
晒干的麻叶可以直接用于制作茶叶
或药材,也可以进行进一步加工,如制作麻叶包饭、麻叶包肉等美
食,或者制作麻叶药膏、麻叶药酒等药品。
加工方法因用途而异,可以根据具体需要选择适合的加工方法。
总之,麻叶的制作方法并不复杂,但需要注意选材、清洗、晒干和加工等环节,以确保麻叶的质量和营养价值。
希望以上介绍的方法对您有所帮助,祝您制作出美味可口的麻叶美食和药品。
一种涡轮叶片的加工方法

一种涡轮叶片的加工方法
涡轮叶片的加工方法有多种,以下是其中一种常见的方法:
1. 选择合适的材料:一般涡轮叶片使用的材料包括镍基合金、钛合金等,因此需要根据实际需求选择合适的材料。
2. 设计叶片形状:根据涡轮的设计需求,使用计算机辅助设计软件绘制叶片的三维模型。
3. 制作铸造模具:根据叶片的形状,制作用于铸造的模具,一般使用耐火材料,如石膏或砂土。
4. 铸造叶片:在模具中加入熔化的金属材料,如镍基合金,然后等待金属凝固形成叶片。
5. 清理和抛光:将铸造好的叶片进行清理和抛光,以去除表面的瑕疵和粗糙度,使得叶片表面光滑。
6. 动态平衡:根据叶片的形状和要求进行动态平衡调整,以确保叶片的旋转平衡和工作稳定性。
7. 检测和质量控制:使用非破坏性检测方法(如超声波检测)或其它方法对叶片进行质量检测,确保叶片的质量符合要求。
8. 表面处理:根据需要,对叶片表面进行进一步处理,如表面涂层或加工添加附属部件。
9. 最终修整:对加工完成的叶片进行最终调整和修整,确保叶片的形状和尺寸与设计要求相符。
10. 组装:将加工好的叶片与涡轮其他部件进行组装,完成涡轮的制造。
需要注意的是,涡轮叶片的加工方法还可以根据具体的工艺要求和设备条件进行调整和改进。
飞机发动机涡轮叶片的制备工艺研究
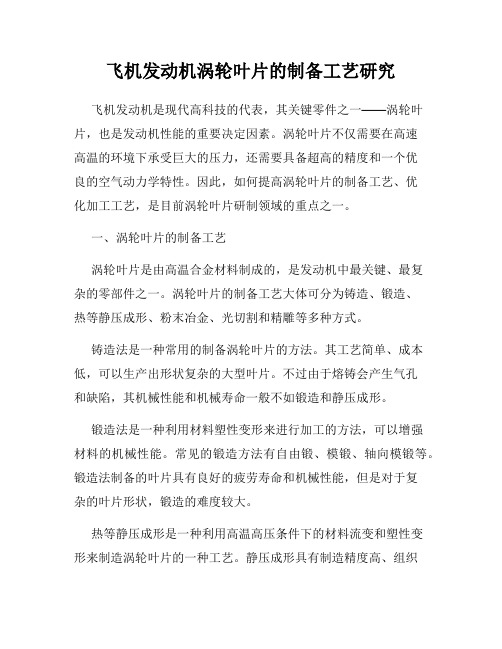
飞机发动机涡轮叶片的制备工艺研究飞机发动机是现代高科技的代表,其关键零件之一——涡轮叶片,也是发动机性能的重要决定因素。
涡轮叶片不仅需要在高速高温的环境下承受巨大的压力,还需要具备超高的精度和一个优良的空气动力学特性。
因此,如何提高涡轮叶片的制备工艺、优化加工工艺,是目前涡轮叶片研制领域的重点之一。
一、涡轮叶片的制备工艺涡轮叶片是由高温合金材料制成的,是发动机中最关键、最复杂的零部件之一。
涡轮叶片的制备工艺大体可分为铸造、锻造、热等静压成形、粉末冶金、光切割和精雕等多种方式。
铸造法是一种常用的制备涡轮叶片的方法。
其工艺简单、成本低,可以生产出形状复杂的大型叶片。
不过由于熔铸会产生气孔和缺陷,其机械性能和机械寿命一般不如锻造和静压成形。
锻造法是一种利用材料塑性变形来进行加工的方法,可以增强材料的机械性能。
常见的锻造方法有自由锻、模锻、轴向模锻等。
锻造法制备的叶片具有良好的疲劳寿命和机械性能,但是对于复杂的叶片形状,锻造的难度较大。
热等静压成形是一种利用高温高压条件下的材料流变和塑性变形来制造涡轮叶片的一种工艺。
静压成形具有制造精度高、组织致密、基体变形少、强度高、耐热性好等优点,是目前制备高端涡轮叶片的主流工艺。
粉末冶金法是将金属粉末经过压制、热处理等工序制成叶片。
其制造精度和自由锻造相当,优点在于不会出现缩孔、气孔等质量问题,适用于小型、多孔等叶片的制作。
光切割法是将纯度超过99.9%的高温合金薄片通过精密加工机床雕刻成复杂的叶片形状。
该法生产的叶片具有超高的制造精度和表面光滑度,并且不需要进行后续的热处理,广泛应用于发动机的高压压气机和低压涡轮中。
精雕法是将锻造或静压成形的大型叶片经过切割、穿孔、钻孔、铣孔、铺堆等工艺,制成小型叶片。
该法可加工出极为复杂的叶片形状,并可以利用基础模具制造多种类型的叶片。
二、涡轮叶片加工工艺优化制备涡轮叶片的过程中,加工工艺是影响叶片成品质量的重要因素之一。
通过对工艺参数、表面特征、材料特性等方面的优化,可以进一步提高叶片的质量和精度。
【免费下载】叶片的加工过程和工艺路线
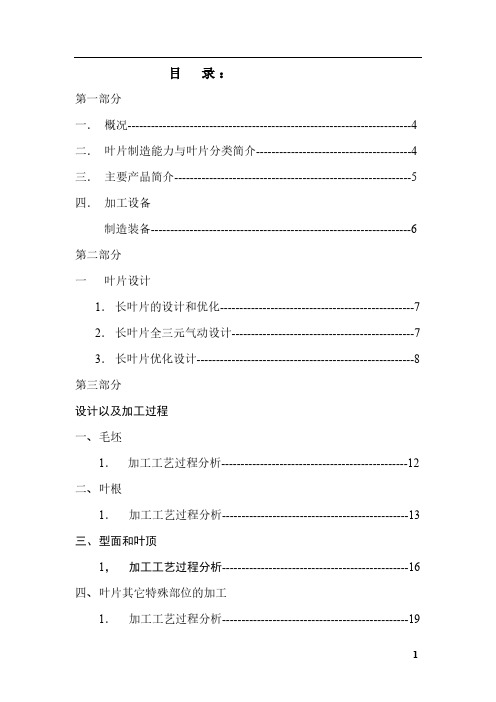
目 录:
第一部分 一. 概况-------------------------------------------------------------------------4 二. 叶片制造能力与叶片分类简介----------------------------------------4 三. 主要产品简介-------------------------------------------------------------5 四. 加工设备
3
大型汽轮机组叶片加工工艺分析和设计
第一部分
一. 概况
汽轮机单机功率越大,电站单位功率的投资成本越低,机组的经济性越高。 大的电网为了便于运行管理及环保,也要求增加单机功率。所以大功率汽轮机 已逐步成为大电网的主力机型。而开发大功率机组的关键之一就是排气面积大, 也就是更长的末级叶片。
我国每年 40%以上的煤用于发电,发电耗煤每年达到 5.7 亿吨。面对如此 巨大的燃料消耗,提高汽轮机机组的经济性将具有巨大的经济效益。由于末级 长叶片占整个汽轮机出力的 10%左右,它的气动性能直接影响整个机组的经济 性,因此,紧密结合各相关学科的发展,不断研制新的长叶片历来是汽轮机行 业开发的重点。
制造装备-------------------------------------------------------------------6 第二部分 一 叶片设计
1. 长叶片的设计和优化--------------------------------------------------7 2. 长叶片全三元气动设计-----------------------------------------------7 3. 长叶片优化设计--------------------------------------------------------8 第三部分 设计以及加工过程 一、毛坯 1. 加工工艺过程分析------------------------------------------------12 二、叶根 1. 加工工艺过程分析------------------------------------------------13 三、型面和叶顶 1, 加工工艺过程分析------------------------------------------------16 四、叶片其它特殊部位的加工 1. 加工工艺过程分析------------------------------------------------19
螺旋叶片加工工艺
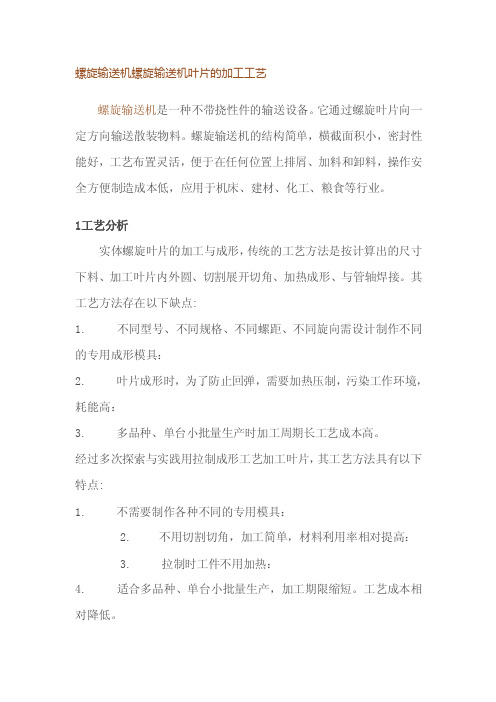
螺旋输送机螺旋输送机叶片的加工工艺螺旋输送机是一种不带挠性件的输送设备。
它通过螺旋叶片向一定方向输送散装物料。
螺旋输送机的结构简单,横截面积小,密封性能好,工艺布置灵活,便于在任何位置上排屑、加料和卸料,操作安全方便制造成本低,应用于机床、建材、化工、粮食等行业。
1工艺分析实体螺旋叶片的加工与成形,传统的工艺方法是按计算出的尺寸下料、加工叶片内外圆、切割展开切角、加热成形、与管轴焊接。
其工艺方法存在以下缺点:1.不同型号、不同规格、不同螺距、不同旋向需设计制作不同的专用成形模具:2.叶片成形时,为了防止回弹,需要加热压制,污染工作环境,耗能高:3.多品种、单台小批量生产时加工周期长工艺成本高。
经过多次探索与实践用拉制成形工艺加工叶片,其工艺方法具有以下特点:1.不需要制作各种不同的专用模具:2.不用切割切角,加工简单,材料利用率相对提高:3.拉制时工件不用加热:4.适合多品种、单台小批量生产,加工期限缩短。
工艺成本相对降低。
2拉制工艺1.首先根据实体螺旋图纸给出的螺旋体外径D、螺距t、叶片厚度δ,管轴直径d,计算出单件叶片的展开毛坯尺寸,内、外圆加上机械加工余量下料。
2.将单片坯料沿直径方向单面切开,按螺旋旋向将切口相互撬起,撬起里要大于3倍的叶片坯料厚度,按每节实体螺旋所需叶片数里为一组.相互焊接成一摄,压实并在外圆上局部相互点焊固定,一组叶片压实时,叶片内孔用一芯轴定位,以防叶片间相对错位。
3.焊接后的一组叶片按展开后的尺寸加工内孔及外圆,车削加工时,必须先加工内孔.后加工外圆。
加工外圆时一定要车掉外口上相互联接的点焊部分,否则叶片在拉制机上无法拉制成形。
4.将螺旋管轴套于车削加工后的叶片内孔上,首尾叶片分别紧固于拉制机夹持器上,然后开动拉制机。
将叶片拉开成形。
操作时应注意每片叶片的内缘线应与管轴外圆相互贴紧贴实。
这是因为叶片内孔与管轴外圆决定了叶片的螺距尺寸,当拉至螺距符合图纸尺寸时,将叶片与管轴点焊固定,卸离拉制机工作台后,分段焊接,整个拉制工作即告完成。
发动机叶片加工工序
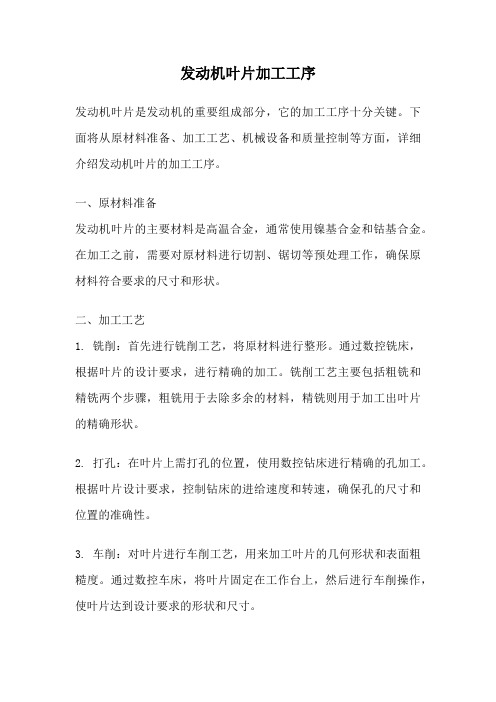
发动机叶片加工工序发动机叶片是发动机的重要组成部分,它的加工工序十分关键。
下面将从原材料准备、加工工艺、机械设备和质量控制等方面,详细介绍发动机叶片的加工工序。
一、原材料准备发动机叶片的主要材料是高温合金,通常使用镍基合金和钴基合金。
在加工之前,需要对原材料进行切割、锯切等预处理工作,确保原材料符合要求的尺寸和形状。
二、加工工艺1. 铣削:首先进行铣削工艺,将原材料进行整形。
通过数控铣床,根据叶片的设计要求,进行精确的加工。
铣削工艺主要包括粗铣和精铣两个步骤,粗铣用于去除多余的材料,精铣则用于加工出叶片的精确形状。
2. 打孔:在叶片上需打孔的位置,使用数控钻床进行精确的孔加工。
根据叶片设计要求,控制钻床的进给速度和转速,确保孔的尺寸和位置的准确性。
3. 车削:对叶片进行车削工艺,用来加工叶片的几何形状和表面粗糙度。
通过数控车床,将叶片固定在工作台上,然后进行车削操作,使叶片达到设计要求的形状和尺寸。
4. 磨削:在车削之后,对叶片进行磨削工艺,用来提高叶片的表面光洁度和精度。
通过磨床对叶片进行磨削,使其表面更加平整光滑,并且可以达到更高的尺寸精度。
三、机械设备发动机叶片的加工离不开各种机械设备的支持。
常用的机械设备包括数控铣床、数控钻床、数控车床、磨床等。
这些机械设备能够根据程序自动完成工件加工,提高生产效率和加工精度。
四、质量控制发动机叶片是发动机的核心部件之一,其加工质量直接影响到发动机的性能和可靠性。
因此,在加工过程中需要进行严格的质量控制。
常用的质量控制手段包括尺寸检测、外观检查和物理性能测试等。
通过这些手段,可以确保叶片的尺寸精度、外观质量和物理性能达到设计要求。
五、总结发动机叶片的加工工序是一个复杂而关键的过程。
通过对原材料的准备、加工工艺的选择、机械设备的使用和质量控制的实施,可以保证叶片的加工质量和性能要求。
发动机叶片的加工工序不仅需要高精度的机械设备的支持,还需要严格的质量控制和工艺操作的精细调控。
风电叶片成型工艺

风电叶片成型工艺风能作为一种绿色环保型能源是可再生能源中最具开发潜力的一种。
随着风电技术的进展与日趋成熟,机型已达到5MW以上,叶片长度超过60米。
叶片是风力发电机组关键部件之一,具有尺寸大,形状简单,精度要求高,对强度、刚度、和表面光滑度要求高等特点。
复合材料在风机叶片的制造中具备许多优势。
制造工艺主要有手糊成型、模压成型、预浸料成型、拉挤成型、纤维缠绕、树脂传递模塑以及真空灌注成型等工艺。
1、手糊工艺手糊是生产复合材料风机转子叶片的一种传统工艺。
在手糊工艺中,将纤维基材铺放于单模内,然后用滚子或毛刷涂敷玻璃布和树脂,常温固化后脱模。
手糊方法可用于低成本制造大型、外形简单制品。
由于它不必受加热及压力的影响。
使用简洁的设备和模具即可,另外相对于其他可行性方案成本更低廉。
手糊工艺生产风机叶片的主要缺点是产品质量对工人的操作娴熟程度及环境条件依靠性较大,生产效率低和产品质量匀称性波动较大,产品的动静平衡保证性差,废品率较高。
特殊是对高性能的简单气动外型和夹芯结构叶片,还需要粘接等二次加工,粘接工艺需要粘接平台或型架以确保粘接面的贴合,生产工艺更加简单和困难。
手糊工艺制造的风力发电机叶片在使用过程中消失问题往往是由于工艺过程中的含胶量不匀称、纤维/树脂浸润不良及固化不完全等引起的裂纹、断裂和叶片变形等。
手糊工艺往往还会伴有大量有害物质和溶剂的释放,有肯定的环境污染问题。
手糊是一种已被证明的生产复合材料叶片工艺方法,但由于其产量低及部件的不连续性以及很难实现结构简单,力学性能要求高的大型产品,促使人们将讨论重点转移至其他生产方法。
2、模压成型模压成型工艺首先将增加材料和树脂置于双瓣模具中,然后闭合模具,加热加压,然后脱模,进行后固化。
这项工艺的优点在于纤维含量高和孔隙率低,并且生产周期短,精确的尺寸公差及良好的表面处理。
然而,模压成型适用于生产简洁的复合材料制品如滑雪板,很难制造包括蒙皮、芯材和梁的叶片等简单外形部件。
发动机叶片加工工序

发动机叶片加工工序发动机叶片是发动机中的重要部件,其加工工序决定了叶片的质量和性能。
下面将介绍发动机叶片加工的工序和流程。
1. 铸造发动机叶片的制造通常从铸造开始。
首先,根据叶片的设计要求,制作出模具。
然后,在模具中注入熔化的金属材料,如铝合金或钛合金。
通过冷却和固化,获得所需形状的叶片。
2. 粗加工在铸造后,叶片需要进行粗加工。
首先,使用机械设备将叶片的外形进行修整和整形,以去除不必要的材料和缺陷。
然后,通过铣削、钻孔等工艺,对叶片进行必要的加工和修整,使其达到设计要求的尺寸和形状。
3. 热处理经过粗加工后,叶片需要进行热处理。
热处理是通过加热和冷却控制叶片的组织结构和性能。
通常,叶片会被加热到一定温度,然后快速冷却,以获得所需的硬度和强度。
热处理还可以消除叶片内部的应力,提高其耐久性和稳定性。
4. 精加工在热处理后,叶片需要进行精加工。
精加工是通过精密的加工设备和工艺,对叶片进行细致的加工和修整。
例如,使用CNC机床进行铣削、车削和钻孔,以及使用研磨和抛光工艺对叶片进行光洁度的提高。
精加工的目的是使叶片的尺寸和形状更加精确,并提高其表面质量。
5. 检测和质量控制在加工过程中,叶片需要进行检测和质量控制。
通过使用各种检测设备和工艺,如三坐标测量仪、金相显微镜、超声波探伤等,对叶片进行尺寸、形状、表面质量和材料性能的检测和评估。
只有通过严格的质量控制,确保叶片的质量达到设计要求,才能保证发动机的性能和可靠性。
6. 表面处理为了提高叶片的表面质量和耐腐蚀性,常常需要对叶片进行表面处理。
例如,通过电镀、喷涂或涂覆等工艺,对叶片进行防腐、增加润滑性和改善外观。
表面处理可以提高叶片的使用寿命和性能。
7. 组装经过以上工序的叶片将进行组装。
叶片将与其他发动机部件进行装配,形成完整的发动机装配体系。
在组装过程中,需要仔细对叶片进行安装和调整,确保叶片与其他部件的配合和运动的顺畅。
总结:发动机叶片加工是一个复杂而精细的工艺过程。
汽轮机的叶片加工工艺过程

汽轮机的叶片加工工艺过程
汽轮机的叶片加工工艺过程主要包括以下几个步骤:
1.叶片设计:根据汽轮机的使用要求,选择合适的叶片材料、形状和尺寸,并进行CAD图纸设计。
2.叶片制模:制作叶片模具,一般采用数控加工中心或电火花加工机完成。
3.叶片铸造:根据叶片模具进行熔炼和铸造,一般采用熔模法或精密铸造法完成。
4.叶片抛光:将铸造好的叶片进行表面抛光,使其表面光洁度达到要求。
5.叶片修整:对铸造完毕的叶片进行尺寸修整和检验,标记质量合格的叶片。
6.叶片装配:将质量合格的叶片与转子进行装配,用螺栓等固定在合适的位置,形成完整的汽轮机转子部件。
在这个过程中,需要使用一些特殊的工具和设备,如数控加工中心、电火花加工机、熔模炉、抛光机等。
在整个工艺过程中,需要高度的技术水平和严格的质量控制,以确保叶片的质量、性能和使用寿命符合要求。
风电叶片机加工工艺
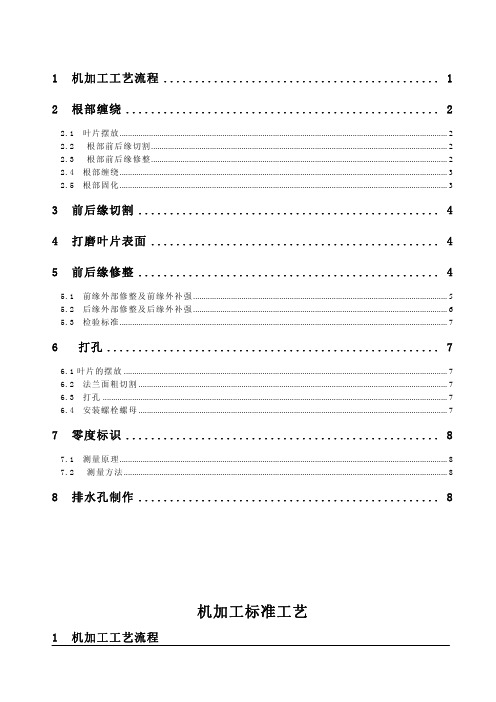
1 机加工工艺流程 (1)2 根部缠绕 (2)2.1叶片摆放 (2)2.2根部前后缘切割 (2)2.3根部前后缘修整 (2)2.4根部缠绕 (3)2.5根部固化 (3)3 前后缘切割 (4)4 打磨叶片表面 (4)5 前后缘修整 (4)5.1前缘外部修整及前缘外补强 (5)5.2后缘外部修整及后缘外补强 (6)5.3检验标准 (7)6 打孔 (7)6.1叶片的摆放 (7)6.2法兰面粗切割 (7)6.3打孔 (7)6.4安装螺栓螺母 (7)7 零度标识 (8)7.1测量原理 (8)7.2测量方法 (8)8 排水孔制作 (8)机加工标准工艺1 机加工工艺流程根部缠绕表面打磨前后缘切割前后缘外补强前后缘修整法兰面切割打孔安装螺栓螺母横向螺母孔封口铺层零刻度位置测量并标记2 根部缠绕2.1 叶片摆放将铺层车间运至机加工车间的叶片水平放置在支架上,SS面朝上。
支架位置为R1.2,R13.25,R26.75三处,支架支撑轮廓必须与叶片相应位置的外轮廓相贴合。
2.2 根部前后缘切割对于根部,理论上合模之后,PS面和SS面前缘应该完全重合,切割时应该从边缘上厚度突变的地方割下。
但是实际合模时,上下两个面有错位,因此应按照图2,使用电动切割机对前后缘R-0.05~R1.2范围进行粗切割,并为后续精细修整留出约10mm余量。
粗切割后,进行精切割。
用手感觉PS和SS面接缝处,感觉是否有错位。
如没有台阶,直接按照接两面的拐角切割;如有台阶,应该将台阶留下,按照最外面的一个拐角切割。
SS面PS面图2-前后缘粗切割2.3 根部前后缘修整完成切割后,撕掉根部脱模布。
如叶片的PS面和SS面有错位,使用气动打磨机将前后缘打磨圆滑,并将台阶内表面打磨粗糙。
扫去前缘上灰尘,用带粘性的纱布将其清理干净,在错位台阶内填入快配方胶粘剂,如图3。
待胶粘剂固化之后,用80目打磨片将前缘打磨圆滑。
如两面没有错位,直接将前后缘打磨圆滑。
图3—根部前后缘修整2.4 根部缠绕1) 将叶片转移至缠绕机支架上,竖直放置,支架位置为R1.2和R26.75两处。
中华叶片重加工工艺流程

中华叶片重加工工艺流程1.首先,将原始的中华叶片进行清洗和除杂处理。
First, the original Chinese blades need to be cleaned and rid of impurities.2.然后,对叶片进行粗加工,修整叶片的边缘。
Next, the blades need to be roughly processed, trimming the edges of the blades.3.接着,进行叶片的打磨,使叶片表面更加光滑。
Then, the blades need to be polished to make the surface smoother.4.之后,对叶片进行铣削,修整叶片的整体形状。
Afterwards, the blades need to be milled to refine the overall shape.5.进行热处理,增强叶片的硬度和韧性。
Carry out heat treatment to enhance the hardness and toughness of the blades.6.接下来,进行酸洗处理,去除叶片表面的铁锈和污渍。
Next, the blades need to be pickled to remove rust and stains from the surface.7.再进行喷砂处理,增加叶片的粗糙度和附着力。
Then, the blades need to be sandblasted to increase roughness and adhesion.8.进行防腐涂层处理,增加叶片的防腐性能。
Apply anti-corrosion coating to enhance the corrosion resistance of the blades.9.进行喷漆处理,增加叶片的美观度和表面硬度。
制造飞机叶片方法
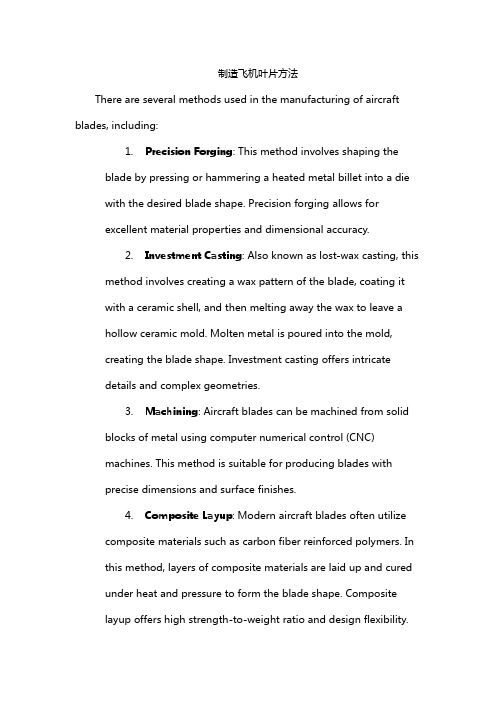
制造飞机叶片方法There are several methods used in the manufacturing of aircraft blades, including:1.Precision Forging: This method involves shaping theblade by pressing or hammering a heated metal billet into a diewith the desired blade shape. Precision forging allows forexcellent material properties and dimensional accuracy.2.Investment Casting: Also known as lost-wax casting, thismethod involves creating a wax pattern of the blade, coating itwith a ceramic shell, and then melting away the wax to leave ahollow ceramic mold. Molten metal is poured into the mold,creating the blade shape. Investment casting offers intricatedetails and complex geometries.3.Machining: Aircraft blades can be machined from solidblocks of metal using computer numerical control (CNC)machines. This method is suitable for producing blades withprecise dimensions and surface finishes.posite Layup: Modern aircraft blades often utilizecomposite materials such as carbon fiber reinforced polymers. Inthis method, layers of composite materials are laid up and curedunder heat and pressure to form the blade shape. Compositelayup offers high strength-to-weight ratio and design flexibility.5.Additive Manufacturing: Also known as 3D printing, additive manufacturing builds up the blade layer by layer from powdered metal or composite materials based on a digital design. This method allows for complex geometries and rapid prototyping.Chinese Description (中文说明):飞机叶片的制造方法包括:1.精密锻造:这种方法通过将加热的金属坯料在模具中锤打或压制成所需的叶片形状。
- 1、下载文档前请自行甄别文档内容的完整性,平台不提供额外的编辑、内容补充、找答案等附加服务。
- 2、"仅部分预览"的文档,不可在线预览部分如存在完整性等问题,可反馈申请退款(可完整预览的文档不适用该条件!)。
- 3、如文档侵犯您的权益,请联系客服反馈,我们会尽快为您处理(人工客服工作时间:9:00-18:30)。
第九章叶片的加工方法9.1 叶片的工艺特点叶片是透平机械的“心脏”,是透平机械中极为主要的零件。
透平是一种旋转式的流体动力机械,它直接起着将蒸汽或燃气的热能转变为机械能的作用。
叶片一般都处在高温,高压和腐蚀的介质下工作。
动叶片还以很高的速度转动。
在大型汽轮机中,叶片顶端的线速度已超过600 m/s,因此叶片还要承受很大的离心应力。
叶片不仅数量多,而且形状复杂,加工要求严格;叶片的加工工作量很大,约占汽轮机、燃气轮机总加工量的四分之一到三分之一。
叶片的加工质量直接影响到机组的运行效率和可靠行,而叶片的质量和寿命与叶片的加工方式有着密切的关系。
所以,叶片的加工方式对透平机械的工作质量及生产经济性有很大的影响。
这就是国内外透平机械行业为什么重视研究叶片加工的原因。
随着科学技术的发展,叶片的加工手段也是日新月异,先进的加工技术正在广泛采用。
叶片的主要特点是:材料中含有昂贵的高温合金元素;加工性能较差;结构复杂;精度和表面质量要求高;品种和数量都很多。
这就决定了叶片加工生产的发展方向是:组织专业化生产,采用少、无切削的先进的毛坯制造工艺,以提高产品质量,节约耐高温材料;采用自动化和半自动化的高效机床,组织流水生产的自动生产线,逐步采用数控和计算机技术加工。
叶片的种类繁多,但各类叶片均主要由两个主要部分组成,即汽道部分和装配面部分组成如图9.1。
因此叶片的加工也分为装配面的加工和汽道部分的加工。
装配面部分又叫叶根部分,它使叶片安全可靠地、准确合理地固定在叶轮上,以保证汽道部分的正常工作。
因此装配部分的结构和精度需按汽道部分的作用、尺寸、精度要求以及所受应力的性质和大小而定。
由于各类叶片汽道部分的作用、尺寸、形式和工作各不相同,所以装配部分的结构种类也很多。
有时由于密封、调频、减振和受力的要求,叶片往往还带有叶冠(或称围带)和拉筋(或称减震凸台)。
叶冠和拉筋也可归为装配面部分。
汽道部分又叫型线部分,它形成工作气流的通道,完成叶片应起的作用,因此汽道部分加工质量的好坏直接影响到机组的效率。
图9.1 叶片的组成9.2叶片的材料和毛坯9.2.1叶片材料由于透平叶片的工作条件和受力情况比较复杂,因此对叶片材料的要求也是多方面的,其中主要的要求概括如下:(1).具有足够的机械强度。
即在工作温度范围内具有足够的,稳定的机械强度(屈服极限和强度极限),并且在工作温度范围内这些机械强度具有稳定的数值。
在高温情况下(一般指450℃以上),具有足够的蠕变极限和持久强度极限。
(2).具有高的韧性和塑性以及高温下抗热脆性(高温下稳定的冲击韧性),避免叶片在载荷作用下产生脆性断裂。
(3).耐蚀性。
抵抗高温下气体中有害物质的腐蚀以及湿蒸汽和空气中氧的腐蚀能力。
(4).耐磨性。
抵抗湿蒸汽中水滴和燃气中固体物质的磨蚀。
叶冠汽道叶根凸台(5).具有良好的冷、热加工性能。
(6).具有良好的减振性。
叶片是处在交变载荷下工作,除要求有较高的疲劳极限外,还要求有良好的减震性能,即高的对数衰减率。
这样可以减小振动产生的交变应力,减小叶片疲劳断裂的可能性。
根据使用温度、使用温度和化学成份等,可以将叶片材料分为两类:(1).马氏体、马氏体-铁素体和铁素体钢。
这类钢的使用温度最高不超过580℃,可以作为汽轮机叶片材料。
(2).奥氏体钢、铁镍合金和镍基合金等。
着类钢的使用温度最高不超过700~750℃,可以作为燃气轮机叶片材料。
马氏体类钢包括1Cr13、2Cr13、Cr11MoV、Cr12WMoV等。
1Cr13和2Cr13马氏体不锈钢广泛被采用作为汽轮机叶片材料,他具有较好的耐腐蚀性和热强性,特别是它的减振性很好,其对数衰减率δ可达0.025。
按照其热强性,1Cr13钢可用于450℃~475℃;2Cr13钢可用于400℃~450℃。
2Cr13钢的含量较高,故室温强度和硬度较高。
常作汽轮机低压部分叶片,但2Cr13钢的抗水滴冲蚀性能不足,用来作末级叶片还需要进行表面硬化或镶焊硬质合金。
Cr11MoV和Cr12MoV是改形的12% Cr钢。
它保持原来1Cr13钢的优点,由于分别加入了强化元素钼、钒和钨,钼和钒使其热强性远比1Cr13钢高。
Cr11MoV可在温度550℃下使用;Cr12WMoV可在温度580℃下使用。
Cr12WMoV的屈服极限高,耐腐蚀性好,亦可作为大型汽轮机的长叶片材料。
马氏体类钢具有良好的减振性能,通常情况下其对数率减率δ在0.015~0.055范围内,它比奥氏体的δ大5~10倍。
9.2.1叶片的毛坯叶片的毛坯形式来划分可分为:模锻叶片毛坯,方刚叶片毛坯,精铸叶片毛坯。
下面我们详细分析三种毛坯的具体情况。
模锻叶片的毛坯:在成品的基础上叶身部分单面法向放量4~5mm,叶冠和叶根部分最小处单面法向放量7mm左右,叶根和叶冠基本上是锻成方形的,有时为了节约材料和机械加工成本则也锻出部分较为粗造的叶根、叶冠型线形状。
下图9.2为一模锻叶片的毛坯状态图。
图9.2 模锻叶片毛坯图方钢叶片的毛坯:当叶片结构简单,数量多、尺寸小的时候,则采用方钢叶片,方钢叶片的毛坯放量是在产品理论尺寸的基础上放量约5mm左右。
通常采用正六面体,有时为了节约材料和减少机械加工成本,将方钢毛坯锻成由几个六面体组成的形状。
图9.3所示为方钢叶片的毛坯图。
精铸叶片的毛坯:在我厂主要是针对汽轮机静叶片和特殊的空心叶片(为了冷却、减少应力、调频等目的而制成的具有内部空腔的透平叶片。
)。
毛坯放量是在理论叶身型线的基础上放量3~5mm。
图9.4所示为精铸叶片毛坯图。
图9.4 精铸叶片毛坯图9.3 叶片的机械加工工艺过程由于叶片的形式、结构、种类、大小等的差异比较大,因此加工方式、机床、工艺流程也不同。
但从总体上来说,按叶片的毛坯形式来划分可分为:方刚叶片加工工艺、模锻叶片加工工艺,精铸叶片加工工艺。
方刚叶片加工工艺主要是针对叶片汽(气)道长度在300mm以下的各种动叶片和静叶片。
模锻叶片加工工艺要是针对叶片汽(气)道长度在300mm以上的各种动叶片和静叶片。
精铸叶片加工工艺主要是针对一些静叶片和特殊叶片(如空心叶片)的加工方法。
9.3.1叶片的数控加工工艺由于本书是作为实习教材,则下面就以一个典型方刚动叶片为例如图9.5所示,介绍一下叶片的常规工艺和数控工艺的加工方法,该叶片叶根为菌形叶根,自带叶冠的预扭叶片,在加工过程中既有常规加工也有数控加工,叶片的常规加工主要是加工叶片的基准面和叶根型线,叶片的数控加工主要是加工叶片的装配面和汽道型线。
至于加工过程中或加工完成后对叶片的详细检查和测量方式则可以在实习的时候相互讨论或到叶片分厂加工车间参观学习,在工艺中只作简单说明。
9.3.1.1 叶片的数控加工工艺流程图 9.5 典型叶片成品(1)来料:该叶片毛坯来料为六面体的方钢,来料时必须按工艺上要求检查方钢尺寸的长、宽、高和直线度,并根据同一级不同的种类叶片分开装入专门的转运箱中方可投入生产车间。
(2)铣一平面(将作为叶片内背平面中的任一面):采用普通机床加工。
来料由于是方刚毛面,六个面均带有黑皮,当加工一个面后的测量也是比较粗糙的,因此通常在该工序中要求光出表面不见黑皮即可,并让加工部位的尺寸大于要求的尺寸,保证后工序有加工余量。
(3)在已加工面上做标记:采用标刻机在指定位置刻上产品的名称和流水作业号,叶片一但刻有编号后,既方便对叶片的识别也方便对叶片的追述。
(叶片在加工过程中需要按编号对尺寸等进行记录,叶片全部加工完成后如有出入可以追查问题出现的环节)(4)铣一侧面(将作为叶片进汽侧或出汽侧的任一平面):普通铣床。
(5)铣另一侧面:普通铣床(6)磨两侧面:磨床。
磨两侧面的作用主要是为了提高基准面的加工精度,因为后工序的加工都要以这两个面为基准。
(7)粗铣两端面:普通铣床。
(8)转移标记:标刻机。
前面将标记刻在平面上,后工序加工时会把刻有的标记铣刀掉,因此必须将标记转移到侧面上,该侧面将作为叶片的出汽侧。
(9)铣另一平面及修第一平面:普通铣床。
(10)精铣两端面:普通铣床。
至此将叶片的六个基准面加工完成。
此时叶片的形状如(图9.6)所示。
图9.6 方钢(11)打顶针孔:普通铣床。
叶片的汽道型线部分需要在数控机床上加工,加工时需要叶片作旋转运动,对于小叶片来讲叶片的变形不大,因此可以采用一端驱动而另一端用顶针顶住即可。
对于长叶片如果采用两端都驱动(即双驱)则可以不打顶针孔。
接下来由于此时叶片还处于长方体的状态,因此可以适当的对汽道部分进行去余量,此时去余量既方便叶片的测量也方边叶片的装夹。
(12)背弧出汽边倒角:普通铣床。
可采用专用工装(叶片过大时)或采用万能虎钳配合机床主轴旋转一定的角度加工。
(13)背弧进汽边倒角:普通铣床。
倒角完成后叶片的形状如图9.7所示。
图9.7 叶片倒角后的形状(14)粗精铣背平面及凸台、叶冠:数控机床。
该工序的加工根据编程者个人的习惯,分几道工序完成,为了提高加工效率加工中需要换几把刀才能完成加工任务。
工艺加工内容如图9.8中粗线部分所示。
加工中用了三把标准刀具,分别是:IG32、R28、D80。
IG32刀具用来粗加工,R28用来精加工叶顶,D80用来精加工叶根背平面和凸出部分。
刀具加工后的零件状态如图9.10所示。
加工中由于使用的是数控机床,因此尽量采用小余量高速切削加工。
加工中最后精铣叶冠的加工轨迹仿真如图9.9所示,图中左端的十字交叉线为加工中的坐标原点,在上方的长方形线框为抬刀平面,在右端的Z字形线为刀具轨迹线。
图9.8粗精铣背平面及凸台图9.9精铣叶冠刀具轨迹a.第一把刀加工后的状态b.第二把刀加工后的状态c.第三把刀加工后的状态图9.10 三把刀加工后的零件状态(15)叶根、叶冠内径向面去余量:这个加工根据产品图的情况分几个机床和几个工序来完成,加工机床有普通机床和数控机床配合使用。
最终将叶片的内径相面加工成如图9.11中上面部分所示的形状。
图9.11 叶根、叶冠内径向面去余量图9.12加工叶根型线图9.13叶根型线刀具(16)线切割叶根型线:线切割机。
加工形状如图9.12所示,要完成该工序的加工,在早期的加工中至少需要五道工序:预铣第一刀、预铣第二刀、预铣第三刀、粗铣、半精铣,粗铣和半精铣用成型铣刀加工。
采用线切割一道工序就加工到半精铣的位置。
(17)精铣叶根型线:平铣或圆盘铣床。
加工形状与线切割形状相同,只是该形状还必须绕叶轮中心旋转。
该工序的加工采用平铣则需采用蜗轮蜗杆连接的专用工装让叶片走圆弧运动,而成型刀具只作旋转运动,因为叶根型线与叶轮接触部位是圆弧面。
精铣叶根型线的刀具如图9.13所示。
如果采用圆盘铣则只需将叶片摆正即可。
(18)精铣叶根、叶冠内径向面及凹槽:数控机床。
加工部位及形状如图9.14中粗线所示。