制动轮砂型铸造工艺设计
砂型铸造及铸造工艺设计

砂型铸造及铸造工艺设计砂型铸造是一种常见的铸造工艺,它通过制作砂型并在其中注入熔化金属,使金属在砂型中凝固成型。
砂型铸造具有成本低、生产周期短、适用于各种金属材料等优点,因此在工业生产中得到广泛应用。
砂型铸造的工艺设计主要包括以下几个方面:模型制作、砂型制备、浇注系统设计、砂型充填与密实、凝固与固化、砂型剥离与修整等。
首先是模型制作。
模型是铸造过程中的主要参照物,它决定了最终铸件的形状和尺寸。
模型可以采用实物模型、木模、塑料模等材料制作。
在模型制作过程中,需要考虑到模型的缩短率,即模型尺寸与最终铸件尺寸之间的比例关系。
其次是砂型制备。
砂型是砂型铸造的核心部分,它承担着承载和固定熔化金属的功能。
砂型制备的关键在于砂型材料的选择和配比。
常用的砂型材料有硅砂、水玻璃、氯化钠等。
在制备砂型的过程中,需要考虑到砂型的强度、耐火性以及砂型表面的光洁度等因素。
浇注系统设计是保证铸件质量的重要环节。
浇注系统包括浇注口、浇注道和浇注杯等部分。
浇注系统的设计应考虑到金属液体的流动和凝固过程,以确保金属能够充分填充砂型,并且避免气体和杂质的混入。
砂型充填与密实是决定铸件质量的关键步骤。
在砂型充填过程中,需要确保熔化金属能够均匀地填充砂型,并且避免产生气孔和缩孔等缺陷。
砂型密实的方法包括振动、压实等。
振动可以提高砂型的密实度,压实则可以增加砂型的抗压强度。
凝固与固化是铸造过程中不可或缺的环节。
在凝固过程中,金属由液态逐渐转变为固态,并在这个过程中释放出大量的热量。
凝固过程的控制将直接影响到铸件的组织结构和性能。
固化过程的目的是使砂型的结构稳定,以便后续的剥离和修整。
最后是砂型剥离与修整。
在铸件凝固后,需要将砂型从铸件上剥离,并对铸件进行修整和清理。
砂型剥离的方法包括机械剥离、化学剥离等。
修整的目的是去除铸件上的毛刺、气孔等缺陷,使铸件达到设计要求的形状和尺寸。
总之,砂型铸造工艺设计的关键在于模型制作、砂型制备、浇注系统设计、砂型充填与密实、凝固与固化、砂型剥离与修整等方面的考虑。
制动盘铸造工艺的设计说明

1.结合所学知识,查找相应资料,对所给零件或铸件原铸造工艺进行分析(工艺图设计,参数选取,砂芯设计,冒口设计,模板设计等)谈谈你的体会,及对教材、课堂教学的建议。
2.查资料,完成所指定锻件的生产过程,锻件图设计、相应的计算过程、下料、加热、锻造及热处理工艺进行分析。
3.结合汽车零件生产。
阐述埋弧焊原理、工艺特点、质量保证措施。
1.结合所学知识,查找相应资料,对所给零件或铸件原铸造工艺进行分析(工艺图设计,参数选取,砂芯设计,冒口设计,模板设计等)。
1.1 制动盘铸造要求及现状一、生产技术状况:制动盘种类繁多,特点是壁薄,盘片及中心处由砂芯形成。
不同种类制动盘,在盘径、盘片厚度及两片间隙尺寸上存在差异,盘毂的厚度和高度也各不相同。
单层盘片的制动盘结构比较简单。
铸件重量多为6-18kg。
二、技术要求:铸件外轮廓全部加工,精加工后不得有任何缩松、气孔、砂眼等铸造缺陷。
金相组织为中等片状型,石墨型,组织均匀,断面敏感性小(特别是硬度差小)。
三、力学性能: σb ≥250MPa , HB180~240 , 相当于国际HT250 牌号。
四、有些外商对铸件的化学成分也作要求,本设计不作详细介绍。
1.2 设计内容用金属型覆砂技术克服上述局限性,解决当前所遇到的铸造问题,保证工艺出品率。
即在金属型与铸件外形间覆薄砂层,形成砂型胶。
优点是同时具备金属型和砂型铸造的特点,金属型与熔体不直接接触,冷却速度和金相组织易于控制,同时提高金属型寿命,铸件形状可较复杂。
铸件可保证致密无气孔、缩孔、缩松等缺陷,工艺出口率高。
2.1 设计任务要求名称:制动盘材料:HT220类型:成批生产本铸件属于盘状薄壁件,盘面上的风道利于空气对流,达到散热的目的。
如下图所示。
采用金属型覆砂工艺,需考虑金属型材料及芯砂材料。
2.2金属型材料选择根据以往金属型设计经验,选择常用的HT200作为金属型材料,参数如下:牌号:HT200标准:GB 9439-88特性:珠光体类型的灰铸铁。
第四章砂型铸造工艺设计

第四章砂型铸造工艺设计1.引言砂型铸造是一种常见的金属成型工艺,广泛应用于各种金属件的生产。
本章将介绍砂型铸造工艺的设计过程,包括模具设计、砂型制备、铸造工艺参数的确定等。
2.模具设计模具设计是砂型铸造工艺的基础,直接影响到铸件的质量和生产效率。
在模具设计中,需要考虑以下几个方面的因素:2.1铸件结构首先需要根据铸件的结构确定模具的形状和尺寸。
一般情况下,模具应该尽量符合铸件的外形,并考虑到铸件的收缩率和加工余量。
2.2浇注系统浇注系统是指从熔融金属到铸件腔室的流动路径。
浇注系统应该保证金属液能够均匀地填充整个铸件腔室,并避免产生气孔和夹杂物。
一般情况下,浇注系统包括浇口、浇杯、导流槽等。
2.3排气系统排气系统是指从砂型中排出空气和燃烧产物的通道。
排气系统应该保证空气能够顺利地从砂型中排出,避免产生气孔和夹杂物。
一般情况下,排气系统包括排气槽、排气孔等。
2.4垫块和芯垫块和芯是为了形成复杂形状的内部空间而使用的辅助构件。
垫块和芯应该和模具保持一定的间隙,并考虑到铸件的收缩率和加工余量。
3.砂型制备砂型制备是砂型铸造工艺的核心环节,直接影响到铸件的表面质量和尺寸精度。
在砂型制备中,需要注意以下几个方面的问题:3.1砂料的选择砂料的选择应该根据铸件的材质和尺寸来确定。
一般情况下,砂料应该具有一定的粘结力和抗压强度,并且易于流动和散落。
3.2砂型的填充砂型的填充应该保证砂料能够均匀地填充整个模具腔室,并且能够与铸件的表面接触紧密。
填充过程中需要注意控制填充速度和压实度,避免产生气孔和夹杂物。
3.3砂型的硬化砂型的硬化是指将填充好的砂料固化成为坚硬的砂型。
硬化过程中需要注意控制硬化时间和硬化温度,避免产生裂纹和变形。
4.铸造工艺参数的确定铸造工艺参数的确定是砂型铸造工艺的重要环节,直接影响到铸件的质量和生产效率。
在确定铸造工艺参数时,需要考虑以下几个方面的因素:4.1浇注温度浇注温度应该根据铸件的材质和尺寸来确定。
汽车制动卡钳的铸造工艺研究

汽车制动卡钳的铸造工艺研究摘要:汽车制动卡钳是汽车制动系统中重要的零部件之一,对于汽车的制动效果和安全性能起着至关重要的作用。
本文通过对汽车制动卡钳的铸造工艺进行研究,分析不同铸造工艺对制动卡钳性能的影响,寻找最优的铸造工艺参数,提高制动卡钳的质量和性能。
关键词:汽车制动卡钳;铸造工艺;性能;质量2.制动卡钳的铸造工艺汽车制动卡钳一般采用铸造工艺进行生产。
铸造工艺的选择直接影响到制动卡钳的质量和性能。
目前常见的铸造工艺有砂型铸造、金属型铸造和压铸等。
2.1 砂型铸造砂型铸造是一种常见的铸造工艺,其工艺简单、成本低,适用于生产中小型的制动卡钳。
砂型铸造的工艺流程主要包括模具制作、铸件装箱、砂型浇注、砂型凝固、模具分离和铸件修整等。
砂型铸造的产品密度和强度相对较低,容易产生气孔和夹杂物,影响制动卡钳的质量和性能。
2.3 压铸压铸是一种高效、高精度的铸造工艺,适用于生产复杂形状的制动卡钳。
压铸的工艺流程主要包括模具制作、熔化金属、液态金属注入、金属凝固和铸件冷却等。
压铸的产品密度和强度较高,具有优良的表面光洁度和尺寸精度。
3.铸造工艺对制动卡钳性能的影响不同的铸造工艺对制动卡钳的性能有不同的影响。
砂型铸造由于产品密度和强度较低,容易产生气孔和夹杂物,导致制动卡钳的强度和密封性能较差。
金属型铸造由于产品密度和强度较高,具有优良的尺寸精度和表面质量,能够满足制动卡钳的性能要求。
压铸由于产品密度和强度较高,并且能够实现复杂形状的制作,具有优良的表面光洁度和尺寸精度,能够满足高性能制动卡钳的要求。
4.最优铸造工艺参数的选择为了提高制动卡钳的质量和性能,可以通过选择最优的铸造工艺参数来进行优化。
最优的铸造工艺参数包括浇注温度、浇注速度、冷却时间等。
通过实验方法,对不同的工艺参数进行优化,可以得到最佳的制动卡钳铸造工艺参数,提高制动卡钳的质量和性能。
砂型铸造工艺及工装设计

砂型铸造工艺及工装设计一、工艺流程设计砂型铸造的工艺流程设计是整个工艺的基础,包括以下步骤:设计铸造模具:根据产品需求和工艺要求,设计铸造模具的结构和尺寸。
制作砂型:根据模具和产品需求,制作符合要求的砂型。
浇注:将熔融的金属液体注入砂型,填充模具的型腔。
冷却:让金属液体冷却凝固,形成铸件。
脱模:将凝固的铸件从砂型中脱出,完成整个铸造过程。
二、铸造模具设计铸造模具的设计是整个工艺的核心,直接影响产品的质量和工艺的效率。
设计时需考虑以下几点:模具材料选择:根据产品需求和工艺要求,选择合适的模具材料。
模具结构确定:根据产品形状和尺寸,设计模具的结构和形状。
模具尺寸精度:根据产品要求和工艺条件,确定模具的尺寸精度。
浇口设计:浇口是金属液体注入模具的通道,设计时需考虑浇口的尺寸、位置和形式。
排气口设计:排气口是排除模具内的空气和挥发物的通道,设计时需考虑排气口的位置和大小。
三、砂型制作工艺设计砂型制作是整个工艺的重要环节,其质量直接影响产品的质量和工艺的效率。
设计时需考虑以下几点:砂型材料选择:选择符合要求的砂型材料,如黄沙、石英砂等。
砂型紧实度控制:控制砂型的紧实度,以保证砂型的强度和稳定性。
砂型透气性控制:控制砂型的透气性,以保证浇注过程中金属液体能够顺利填充模具的型腔。
砂型表面处理:对砂型的表面进行处理,以提高产品的表面质量。
四、浇注系统设计浇注系统是金属液体注入模具的通道,其设计直接影响到金属液体的流动和填充效果。
设计时需考虑以下几点:浇注系统结构形式:根据产品要求和工艺条件,选择合适的浇注系统结构形式。
浇注系统尺寸精度:根据产品要求和工艺条件,确定浇注系统的尺寸精度。
浇注速度控制:控制浇注速度,以保证金属液体能够平稳、充足地填充模具的型腔。
浇口位置选择:根据产品形状和模具结构,选择合适的浇口位置。
溢流槽设计:溢流槽是收集多余金属液体的结构,设计时需考虑溢流槽的位置和大小。
过滤网设置:过滤网是过滤金属液体中的杂质和气泡的结构,设计时需考虑过滤网的形式和材料。
砂型铸造工艺设计

砂型铸造工艺设计砂型铸造是一种常用的金属铸造工艺,适用于生产各种大中小型铸件。
砂型铸造工艺设计的主要目的是确保铸件形状、尺寸和质量的准确性,同时提高生产效率和降低生产成本。
下面是一个砂型铸造工艺设计的示例。
首先,确定铸件的形状和尺寸。
这是工艺设计的基础,涉及到铸件的几何形状、尺寸和重量等参数。
根据铸件的设计图纸,确定铸件的准确尺寸。
然后,选择适当的砂型材料。
砂型材料是砂型铸造中非常重要的因素之一,直接影响到铸件表面质量和精度。
根据铸件的材料和需求,选择适当的砂型材料,如石英砂、粘土砂等。
接下来,设计合适的砂型。
砂型的设计涉及到铸件和模具的结构设计。
首先,根据铸件的形状、尺寸和结构特点,确定合适的砂型结构,包括上、下模、型芯等。
然后,结合砂型材料的特性,设计合理的砂型壁厚和腔型,以保证铸件表面的光洁度和尺寸精度。
在设计砂型的同时,需要考虑到浇注系统的设计。
浇注系统是指将熔化金属引导到砂型腔内的通道系统,包括浇杯、溢流槽、导流槽等。
合理设计浇注系统可以保证金属的顺利流入砂型腔,并且能够避免金属中的气体和杂质混入铸件中。
最后,进行铸造工艺参数的选择和优化。
包括浇注温度、浇注速度、浇注时间、浇注压力等。
通过合理选择和优化这些参数,可以在保证铸件质量的前提下提高生产效率,降低生产成本。
总之,砂型铸造工艺设计是铸造工艺中至关重要的一步,它直接影响到铸件的质量和生产效率。
只有通过科学合理地设计砂型铸造工艺,才能生产出满足要求的铸件。
砂型铸造工艺设计是铸造生产中重要的环节之一,对于确保铸件的质量、做工的精细度以及生产效率的提高具有重要意义。
在砂型铸造工艺设计过程中,不仅需要考虑铸件的形状尺寸和材料特性,还需要合理选择砂型材料、设计适当的砂型结构和浇注系统,优化铸造工艺参数等。
首先,砂型铸造工艺设计的第一步是确定铸件的形状和尺寸。
根据产品的设计图纸和要求,确定铸件的几何形状、尺寸和重量等参数。
这些参数的准确确定是工艺设计的基础,直接影响到最终铸件的形状和尺寸精度。
砂型铸造及铸造工艺设计
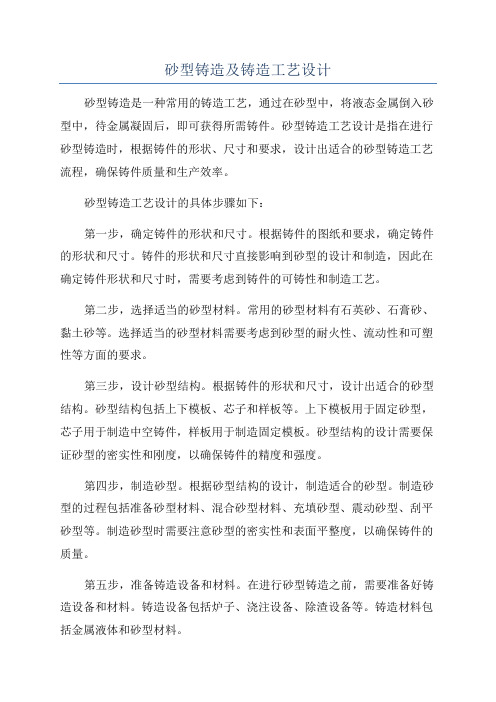
砂型铸造及铸造工艺设计砂型铸造是一种常用的铸造工艺,通过在砂型中,将液态金属倒入砂型中,待金属凝固后,即可获得所需铸件。
砂型铸造工艺设计是指在进行砂型铸造时,根据铸件的形状、尺寸和要求,设计出适合的砂型铸造工艺流程,确保铸件质量和生产效率。
砂型铸造工艺设计的具体步骤如下:第一步,确定铸件的形状和尺寸。
根据铸件的图纸和要求,确定铸件的形状和尺寸。
铸件的形状和尺寸直接影响到砂型的设计和制造,因此在确定铸件形状和尺寸时,需要考虑到铸件的可铸性和制造工艺。
第二步,选择适当的砂型材料。
常用的砂型材料有石英砂、石膏砂、黏土砂等。
选择适当的砂型材料需要考虑到砂型的耐火性、流动性和可塑性等方面的要求。
第三步,设计砂型结构。
根据铸件的形状和尺寸,设计出适合的砂型结构。
砂型结构包括上下模板、芯子和样板等。
上下模板用于固定砂型,芯子用于制造中空铸件,样板用于制造固定模板。
砂型结构的设计需要保证砂型的密实性和刚度,以确保铸件的精度和强度。
第四步,制造砂型。
根据砂型结构的设计,制造适合的砂型。
制造砂型的过程包括准备砂型材料、混合砂型材料、充填砂型、震动砂型、刮平砂型等。
制造砂型时需要注意砂型的密实性和表面平整度,以确保铸件的质量。
第五步,准备铸造设备和材料。
在进行砂型铸造之前,需要准备好铸造设备和材料。
铸造设备包括炉子、浇注设备、除渣设备等。
铸造材料包括金属液体和砂型材料。
第六步,进行砂型铸造。
在准备好铸造设备和材料之后,进行砂型铸造。
砂型铸造的过程包括熔炼金属、倒入砂型、待金属凝固、冷却铸件、取出铸件等。
在进行砂型铸造时,需要控制铸造温度、倒铸速度和铸造压力,以确保铸件的质量。
第七步,进行铸件的后处理。
在进行砂型铸造之后,需要对铸件进行后处理,包括去除砂型、修整表面、热处理等。
后处理的目的是提高铸件的机械性能和表面质量。
砂型铸造工艺设计需要综合考虑铸件的形状、尺寸和要求,选择适当的砂型材料和制造过程,并进行铸造和后处理。
制动轮砂型铸造工艺课程设计

机械制造课程设计题目:制动轮砂型铸造工艺课程设计目录一、零件工艺分析 (3)二、铸造工艺方案的设计 (4)2.1、确定铸造壁厚要求 (4)2.2、分型面及浇注位置的选择 (4)2.4、工艺参数的选择: (6)三、砂芯的设计 (8)四、浇注系统的设计 (10)五、冒口的设计 (11)参考文献 (12)一、零件工艺分析制动轮零件图如下:由零件图知,零件材料为铸钢,而铸钢的钢液的流动性较差,铸钢的体积收缩率和线收缩率大,易吸气氧化和粘砂,总体上,铸钢的铸造性能较差,易产生缩孔和裂纹等缺陷。
因此,铸钢件在铸造工艺上必须考虑到补缩问题,防止产生缩孔和裂纹等缺陷,设计铸型时,铸件壁厚要均匀,避免尖角和直角结构,宜采用顺序凝固工艺。
φ的中心线是主要的设计基准和加工基准。
同根据零件图分析,11010JSφ的圆端底面为重要的加工面,也是重要的设计基准。
时,415最终,通过零件分析,可以制动轮外形较为复杂,应采用砂型造型,且需要使用砂芯。
制动轮零件存有10个φ24的小孔,考虑到加工余量,不宜铸出,应采用机械加工方法成型;而中间的大孔φ100和φ180需要铸出。
二、铸造工艺方案的设计铸造工艺方案设计的内容主要有:选择铸件浇注位置及分型,选择铸确定铸造工艺参数等。
2.1、确定铸造壁厚要求为了避免浇不到、冷隔等缺陷,铸件不应太薄。
铸件的最小允许壁厚与铸造的流动性密切相关。
在普通砂型铸造的条件下,铸件最小允许壁厚见下表1(根据工程材料及成形工艺一书中表6-9)。
表1:铸件最小允许壁厚查得铸钢件在200~500mm的轮廓尺寸下,最小允许壁厚为10~12mm。
由零件图可知,零件中不存在壁厚小于设计要求的结构,在设计过程中,也没有出现壁厚小于最小壁厚要求的情况。
2.2、分型面及浇注位置的选择2.2.1 浇注位置的选择原则:1)重要加工面向下放原则:重要加工面或要求高的面,置于铸型下部或侧立;2)宽大平面向下放原则:将大平面朝下,以免出现气孔和夹砂。
砂型铸造工艺设计

三、砂型铸造工艺设计简介1. 铸造工艺图(1)浇注位置的确定(2)分型面的确定 (3)工艺参数的确定 (4)铸造工艺图绘制举例本节其它知识点:铸件图铸造工艺设计铸造工艺设计是根据铸件结构特点、技术要求、生产批量、生产条件等,确定铸造方案和工艺参数,绘制图标和标注符号、编制工艺和工艺规程等。
它是进行生产、管理、铸件验收和经济核算的依据。
铸造工艺设计主要内容是绘制铸造工艺图和铸件图。
1.铸造工艺图铸造工艺图是表示铸型分型面、浇冒系统、浇注位置、型芯结构尺寸、控制凝固措施(冷 铁、保温衬板)等内容的图样。
(1)浇注位置的确定浇注位置是浇注时铸件在铸型中所处的位置。
由于浇注时气体、熔渣、砂粒等杂质会上浮,使铸件上部易出现气孔、夹渣、夹砂等缺陷,而铸件下部质量较好。
确定浇注位置应遵循“三下一上”的原则。
1)主要工作面和重要面应朝下或置于侧壁。
床身的导轨面要求组织致密,耐磨,所以导轨面朝下是合理的。
气缸套要求质量均匀一致,浇注时应使其圆周表面处于侧壁2)宽大平面朝下大平面长时间受到金属液的烘烤容易掉砂,在平面上易产生夹砂、砂眼、气孔等缺陷,故铸件的大平面应尽量朝下,如划线平台的平面应朝下。
3)薄壁面朝下铸件薄壁处铸型型腔窄,冷速快,充型能力差,容易出现浇不到和冷隔的缺陷。
如电机端盖薄壁部位朝下,避免冷隔、浇不到等缺陷。
4)厚壁朝上将厚大部分放于上部,可使金属液按自下而上的顺序凝固,在最后凝固部分便于采用冒口补缩,以防止缩孔的产生。
如将缸头的较厚部位置于顶部,便于设置冒口补缩。
1)尽可能使铸件全部或主要部分置于同一砂箱中,以避免错型而造成尺寸偏差。
如左图所示:(a)不合理,铸件分别处于两个砂箱中。
(b)合理,铸件处于同一个砂箱中,既便于合型,又可避免错型。
2)尽可能使分型面为一平面。
如左图所示:(a)若采用俯视图弯曲对称面作为分型面,则需要采用挖砂或假箱造型,使铸造工艺复杂化。
(b)起重臂按图中所示分型面为一平面,可用分模造型、起模方便。
制动盘铸造工艺设计

1.结合所学知识,查找相应资料,对所给零件或铸件原铸造工艺进行分析(工艺图设计,参数选取,砂芯设计,冒口设计,模板设计等)谈谈你的体会,及对教材、课堂教学的建议。
2.查资料,完成所指定锻件的生产过程,锻件图设计、相应的计算过程、下料、加热、锻造及热处理工艺进行分析。
3.结合汽车零件生产。
阐述埋弧焊原理、工艺特点、质量保证措施。
1 •结合所学知识,查找相应资料,对所给零件或铸件原铸造工艺进行分析(工艺图设计,参数选取,砂芯设计,冒口设计,模板设计等)。
1.1制动盘铸造要求及现状一、生产技术状况:制动盘种类繁多,特点是壁薄,盘片及中心处由砂芯形成。
不同种类制动盘,在盘径、盘片厚度及两片间隙尺寸上存在差异,盘毂的厚度和高度也各不相同。
单层盘片的制动盘结构比较简单。
铸件重量多为6~18kgo二、技术要求:铸件外轮廓全部加工,精加工后不得有任何缩松、气孔、砂眼等铸造缺陷。
金相组织为中等片状型,石墨型,组织均匀,断面敏感性小(特别是硬度差小)。
三、力学性能:(T b >250MPa , HB180-240,相当于国际HT250牌号。
四、有些外商对铸件的化学成分也作要求,本设计不作详细介绍。
1.2设计内容用金属型覆砂技术克服上述局限性,解决当前所遇到的铸造问题,保证工艺出品率。
即在金属型与铸件外形间覆薄砂层,形成砂型胶。
优点是同时具备金属型和砂型铸造的特点,金属型与熔体不直接接触,冷却速度和金相组织易于控制,同时提高金属型寿命,铸件形状可较复杂。
铸件可保证致密无气孔、缩孔、缩松等缺陷,工艺出口率咼。
2.1设计任务要求名称:制动盘材料:HT220类型:成批生产本铸件属于盘状薄壁件,盘面上的风道利于空气对流,达到散热的冃的。
如下图所示。
采用金属型覆砂工艺,需考虑金属型材料及芯砂材料。
2.2金属型材料选择根据以往金属型设计经验,选择常用的HT200作为金属型材料,参数如下:牌号:HT200标准:GB 9439-88特性:珠光体类型的灰铸铁。
砂型铸造工艺设计步骤

砂型铸造工艺设计步骤1、设计铸件图根据零件图及相关技术要求设计铸件图,设计时涉及技术内容依次为零件铸造工艺性、铸件尺寸公差、机械加工余量、工艺肋、铸件最小铸出孔和槽。
2、设计铸造工艺图(1)铸造毛坯三维成形利用现代计算机辅助设计手段可以根据二维零件图绘制三维铸件实体,如果设计部门给出三维零件图,可在三维零件图基础上直接绘制三维铸件实体图。
通过三维实体图绘制,可以得到准确的铸造毛坯重量。
铸件形状复杂时,三维实体绘制显得更有必要。
(2)毛坯形体解析目的是多角度分析铸造毛坯空间形状和结构特点,发现铸件厚大断面和热节位置分布,计算毛坯分体几何模数(若工艺设计需要),为后续的铸造方案确定和工艺参数设计做准备。
(3)工艺方案和参数确定目的是确定铸件浇注位置、分型面、铸件线收缩率与模样放大率、起模斜度、非加工壁厚负余量、反变形量、工艺补正量、分型负数、浇冒口切割余量、铸件在砂型内冷却时间以及压铁重量计算和去压铁时间选择、起吊重量计算和铸件吊轴设计。
(4)砂芯设计目的是形成铸件内腔或复杂外轮廓形状,包括砂芯设置、砂芯固定、砂芯定位、芯头尺寸和间隙、砂芯负数、芯撑、芯骨以及砂芯排气、拼合与预装配设计。
(5)补缩系统设计目的是补充铸件凝固过程中的液态收缩,使铸造毛坯内部致密。
包括冒口配置、冒口补缩距离设计、补贴设计、冷铁设计以及冒口尺寸计算。
(6)出气孔设计目的是使铸件充型时型腔内气体(空气或铸型受热后产生的气体等)顺利排出,避免铸件内产生气孔缺陷。
(7)浇注系统设计目的是设计出合理的液态金属进入铸型型腔的通道。
(8)生成铸造工艺图(9)设计铸型装配图在成批生产的铸件或重要的单件上使用。
3、铸造工装设计在造型线上成批生产重要铸件时采用。
内容包括模样、模板、芯盒、砂箱以及其他工艺装备设计。
4、铸造工艺卡根据前述步骤产生的设计结果填写铸造工艺卡,用于指导工艺实施。
砂型铸造工艺方案设计与实践报告
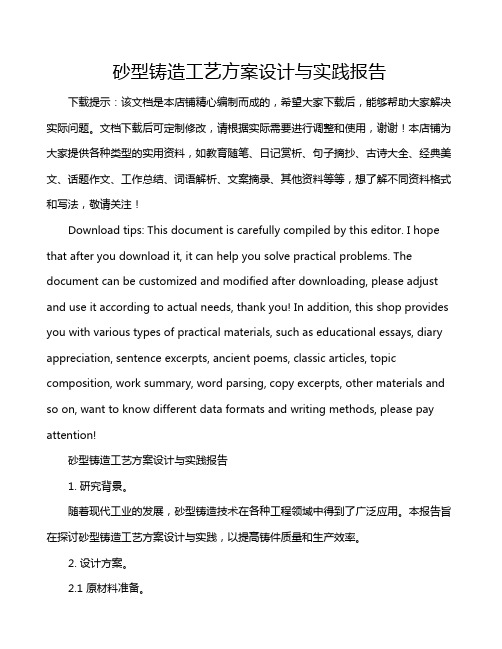
砂型铸造工艺方案设计与实践报告下载提示:该文档是本店铺精心编制而成的,希望大家下载后,能够帮助大家解决实际问题。
文档下载后可定制修改,请根据实际需要进行调整和使用,谢谢!本店铺为大家提供各种类型的实用资料,如教育随笔、日记赏析、句子摘抄、古诗大全、经典美文、话题作文、工作总结、词语解析、文案摘录、其他资料等等,想了解不同资料格式和写法,敬请关注!Download tips: This document is carefully compiled by this editor. I hope that after you download it, it can help you solve practical problems. The document can be customized and modified after downloading, please adjust and use it according to actual needs, thank you! In addition, this shop provides you with various types of practical materials, such as educational essays, diary appreciation, sentence excerpts, ancient poems, classic articles, topic composition, work summary, word parsing, copy excerpts, other materials and so on, want to know different data formats and writing methods, please pay attention!砂型铸造工艺方案设计与实践报告1. 研究背景。
《砂型铸造工艺设计》

整理课件
4、内浇道与铸件型腔连接位置的选择原则
• ①应使内浇道中的金属液畅通无阻地进入型腔,不正面 冲击铸型壁、砂芯或型腔中薄弱的突出部分。
• ②内浇道不应妨碍铸件收缩。如图4—16所示的圆环铸 件,其四个内浇道做成曲线形状,就不会阻碍铸件向中心 的收缩,避免了铸件的变形和裂纹。
• ③内浇道尽量不开设在铸件的重要部位。因内浇道附近 易局部过热而造成铸件晶粒粗大,并可能出现疏松,进而 影响铸件品质。
整理课件
(2) 分型面(中间)注入式浇注系统
内浇道开设在分型面上
优点:内浇道开设在分型面上,能方便地按需要进行布置, 有利于控制金属液的流量分布和铸型热量的分布。
应用:应用普遍,适用于中等质量、高度和壁厚的铸件。
整理课件
(3) 底注式浇注系统
内浇道开设在型腔底部
优点:金属液充型平稳,避免了金属液冲击型芯、飞溅和 氧化及由此引起的铸件缺陷;型内气体易于逐渐排出,整 个浇注系统充满较快,利于横浇道撇渣。 缺点:型腔底部金属液温度较高,而上部液面温度较低, 不利于冒口的补缩。
30~50 50
注: 若孔很深,孔径很小,一般不铸出; 不加工的特形孔,原则上应铸出; 非铁金属铸件上的孔,应尽量铸出。
整理课件
2.起模斜度
在造型和造芯时,为了顺利起模而不致损坏砂型和 砂芯,应该在模样或芯盒的起模方向上带有一定的斜度, 这个斜度称为起模斜度。
若铸件本身没有足够的结构斜度,就要在铸造工 艺设计时给出铸件的起模斜度。
整理课件
注:L-冒口的相对长度(相对延续率) 沿铸件长度方向各个冒口根部长度的总和与铸件被补缩 部分长度之比的百分数。
整理课件
第四节 液态成形工艺设计实例
汽车制动卡钳的铸造工艺研究
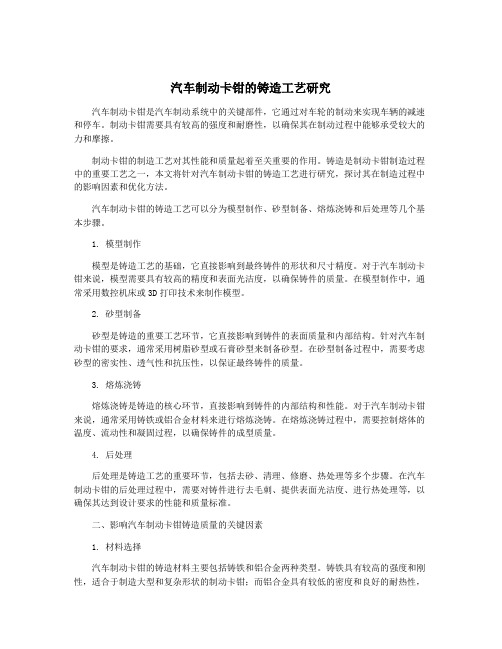
汽车制动卡钳的铸造工艺研究汽车制动卡钳是汽车制动系统中的关键部件,它通过对车轮的制动来实现车辆的减速和停车。
制动卡钳需要具有较高的强度和耐磨性,以确保其在制动过程中能够承受较大的力和摩擦。
制动卡钳的制造工艺对其性能和质量起着至关重要的作用。
铸造是制动卡钳制造过程中的重要工艺之一,本文将针对汽车制动卡钳的铸造工艺进行研究,探讨其在制造过程中的影响因素和优化方法。
汽车制动卡钳的铸造工艺可以分为模型制作、砂型制备、熔炼浇铸和后处理等几个基本步骤。
1. 模型制作模型是铸造工艺的基础,它直接影响到最终铸件的形状和尺寸精度。
对于汽车制动卡钳来说,模型需要具有较高的精度和表面光洁度,以确保铸件的质量。
在模型制作中,通常采用数控机床或3D打印技术来制作模型。
2. 砂型制备砂型是铸造的重要工艺环节,它直接影响到铸件的表面质量和内部结构。
针对汽车制动卡钳的要求,通常采用树脂砂型或石膏砂型来制备砂型。
在砂型制备过程中,需要考虑砂型的密实性、透气性和抗压性,以保证最终铸件的质量。
3. 熔炼浇铸熔炼浇铸是铸造的核心环节,直接影响到铸件的内部结构和性能。
对于汽车制动卡钳来说,通常采用铸铁或铝合金材料来进行熔炼浇铸。
在熔炼浇铸过程中,需要控制熔体的温度、流动性和凝固过程,以确保铸件的成型质量。
4. 后处理后处理是铸造工艺的重要环节,包括去砂、清理、修磨、热处理等多个步骤。
在汽车制动卡钳的后处理过程中,需要对铸件进行去毛刺、提供表面光洁度、进行热处理等,以确保其达到设计要求的性能和质量标准。
二、影响汽车制动卡钳铸造质量的关键因素1. 材料选择汽车制动卡钳的铸造材料主要包括铸铁和铝合金两种类型。
铸铁具有较高的强度和刚性,适合于制造大型和复杂形状的制动卡钳;而铝合金具有较低的密度和良好的耐热性,适合于制造轻量化和散热性能要求较高的制动卡钳。
材料的选择直接影响到铸件的性能和质量,需要根据具体的使用要求进行合理选择。
3. 浇注工艺浇注工艺是影响铸件内部结构和性能的关键环节。
灰铸铁汽车制动盘湿砂型铸造工艺的设计及数值模拟

第33卷 第3期 上 海 金 属 Vol .33,No .32011年5月 SHANGHA IMET ALS May,201131 作者简介:孙小亮,男,主要从事铌铸铁制动盘研究,Email:blues word123@灰铸铁汽车制动盘湿砂型铸造工艺的设计及数值模拟孙小亮 马志英 裴小虎 杨弋涛 华 勤 翟启杰(上海大学材料科学与工程学院,上海200072) 【摘要】 应用湿砂型铸造工艺制造灰铸铁汽车制动盘,上下型为对称结构,中间用砂芯分隔,一型6件,可以降低生产成本,大大提高生产效率。
并用ADSTEF AN 模拟软件对铸造过程进行数值模拟,从而优化设计工艺。
【关键词】 制动盘 潮膜砂铸造 数值模拟 优化工艺APP L I CATI ON OF SURGE CASTI NG SAN D M E M BRANE TECHNI QUE F OR GRE Y CAST I R ON BRAKE D I SC AN DPR OCESS NU M ERI CAL SI M U LATI ONSun Xiaoliang Ma Zhiying Pei Xiaohu Yang Yitao Hua Q in Zhai Q ijie (School of Materials Science and Engineering,Shanghai University ) 【Abstract 】 Green sand mold casting p r ocess was used t o manufacture grey cast ir on brake disc .The structure of high and l ow mould parts was sy mmetrical and sand cores were existed bet w een the m.A mold contained 6p ieces of casting,s o it could reduce the cost,and greatly i m p r ove the p r oducti on efficiency .ADSTEF AN si m ulati on s oft w are was used t o si m ulate the casting p r ocess,therefore t o op ti m ize the design and p r ocess .【Key W ords 】 B rake D isc,Surge Casting Sand Me mbrane,Numerical Si m ulati on,Pr ocess Op ti m izati on 制动盘是车辆制动系统中的关键部件,传统的制动盘材料为灰铸铁,具有良好的铸造成型性、加工性、耐磨耐热性、吸震性以及成本低廉等特点。
- 1、下载文档前请自行甄别文档内容的完整性,平台不提供额外的编辑、内容补充、找答案等附加服务。
- 2、"仅部分预览"的文档,不可在线预览部分如存在完整性等问题,可反馈申请退款(可完整预览的文档不适用该条件!)。
- 3、如文档侵犯您的权益,请联系客服反馈,我们会尽快为您处理(人工客服工作时间:9:00-18:30)。
铸造工艺设计
题目:“制动轮”砂型铸造工艺设计
目录
一、工艺分析 (1)
二、工艺方案的确定 (2)
1、毛坯的选择和铸造方法的确定 (2)
2、毛坯形状的确定 (2)
(1)铸件浇铸位置及分型面选择 (2)
(2)确定铸造工艺参数 (3)
(3)芯头设计 (4)
三、热处理工艺 (4)
1、去应力正火 (4)
2、淬火 (4)
3、回火 (4)
4、时效 (5)
四、浇注系统 (5)
制动轮制造工艺设计
一、工艺分析
该零件选用的材料为:ZG300 其工艺路线安排为:
铸造毛坯热处理加工机械加工去毛刺、修整,清洗、涂防锈油成品
二、工艺方案的确定
1、毛坯的选择和铸造方法的确定
毛坯按其制造形式分为六类:型材、铸件、锻件、焊接件、冲压件和其他。
每类又有若干种不同的制造方法。
零件的材料大致确定了毛坯的种类,而其力学性能的高低,也在一定程度上影响毛坯的种类,因为考虑到制动轮在使用中经常运动,承受较大的弯扭冲击载荷,所以选用铸件以保证零件的工作可靠。
因为零件的工作形状一般,故可以采用砂型铸造,并且从铸件精度,生产效率,劳动条件等方面考虑也是应该的!
2、毛坯形状的确定
毛坯形状应力求接近成品形状,以减少机械加工量。
(1)铸件浇铸位置及分型面选择
该铸件浇铸位置和分型面的确定方法,有两个方案可供选择。
方案1:分模造型,两半模样分开的平面就是分型面,分型面为 500外圆表面高度的一半处。
方案2:整模造型,分型面为零件的底面,浇铸位置为中间中心孔的位置。
根据对该零件两种造型方案的分析,考虑到铸件的重要加工面或主要工作面一般应处于底面或侧面,避免气孔、砂眼、疏松、缩孔等缺陷出现在工作面上;大平面尽可能朝下或用倾斜浇铸,避免夹砂或夹渣缺陷;铸件的薄壁部分放在下部或侧面,以免产生浇不足的情况。
而且应该选择最容易起模的方法,因此优先选择方案1。
(2)确定铸造工艺参数
(a)铸件孔的最小尺寸因为选择的是砂型铸造,且选择小批量生产,铸件的最小孔径尺寸为110mm。
(b)取铸件的最小壁厚为12mm。
(c)铸件的尺寸公差及加工余量由材料、制造方法和生产类型决定。
因为零件所用材料为铸钢,小批量生产时选择的毛坯铸造方法是砂型铸造,根据
GB/T11350-1989(如下图),铸件公差等级为IT13~15,取IT14,加工余量等级为J级。
a、总长为φ500h9mm圆周面双侧加工,机械加工余量为13mm,即该总长的基本尺寸为φ526h9mm。
b、上端面直径为φ110mm的圆锥孔圆周面双侧加工,机械加工余量为7mm,即该孔的基本尺寸为φ96mm
c、总长为φ190mm,圆周面双侧加工,机械加工余量为15mm,即该总长的基本尺寸
φ220mm。
d、总长为210mm的外端面单侧加工,机械加工余量为13,该总长的基本尺寸223mm。
e总长为167mm,212mm的外端面进行单侧加工其机械加工余量为13mm,该总长的基本尺寸180mm,225mm
e总长为12mm,42mm的机械加工余量为8.5mm,该总长的基本尺寸20.5mm ,50.5mm.
其他尺寸参照零件图查得。
(d)铸件的起模斜度
因为铸件在垂直于分型面的面上需有铸造斜度,且各面斜度数值尽可能一致,以便起模,查表得,高为210mm外表面的起模斜度为0度30分。
高为167mm外表面的起模斜度为0度25分。
高为99mm的两个内圆表面起模斜度1度45分。
表7.1.5 砂型铸造时模样外表面及内表面的起模
(e)铸件圆角半径
铸件壁部连接处的转角应有铸造圆角,铸造圆角半径一般取相交两壁平均厚度的1/3~1/2,计算后壁厚为42mm和20mm处的内外圆角半径圆整均为10mm,计算后壁厚为42mm 和15mm处的内圆角半径圆整为9mm。
(f)收缩率
为补偿铸件在冷却过程中产生的收缩,使冷却后的铸件符合图样的要求,需要放大模样的尺寸,放大量取决于铸件的尺寸和该合金的线收缩率。
铸钢件的铸造收缩率约取2%。
(3)芯头设计
1)按芯头位置分垂直和水平两类,根据设计的浇注系统知,芯头为立式芯头
2)立芯头的高度主要取决于直径大小,范围为15~150mm;
因为细长高芯子应有上、下芯头,且下面芯头的斜度小一点、高度大一点.
三、热处理工艺
1、去应力正火
去应力正火可得到细密、均匀的组织,可提高一般结构零件的力学性能,消除内应力。
将工件加热到临界温度以上,保持一定时间后在空中冷却。
2、淬火
提高工件的硬度、强度、耐磨性,提高工件的综合性能。
把工件加热到临界温度以上,保持一定时间后,于淬火剂(油、水或空气等)中急速冷却。
3、回火
减小或消除淬火内应力,防止工件在使用过程中产生变形或开裂;提高钢的韧性和塑性,适当调节材料的刚性和硬度;稳定组织,提高工件在使用过程中的尺寸稳定性。
把淬火后的工件加热到临界温度以下,保持一定时间后在空气、油或水中冷却。
4、时效
消除因热处理而产生的内应力,稳定工件的形状和尺寸;消除加工应力。
在常温或低温下长时间回火。
四、浇注系统
【浇注系统】是为填充型腔和冒口而开设于铸型中的一系列通道。
(1)浇注系统的类型按金属液导入型腔的位置,浇注系统可分为底注式、顶注式、中注式、阶梯式等,按照中注式的特点:横浇道和内浇道均开设在分型面上,易于操作,并
便于控制金属液的流量分布和铸型热分布。
用于重量中等、高度不大和壁厚也中等的件。
可知道零件图知应该选择中注式浇注系统。
(2)浇注系统的位置确定内浇道位置、数目和引入方向,确定直浇道位置和高度,确定各浇道截面的比例,并计算其各浇道组元的截面大小。
内浇道位置:因为制动轮为圆柱形套类零件,所以,内浇道应该尽量分布在砂型型腔的四周,故设计成环形分布的内浇道。
(如下图所示)其内浇道数目为3个,目的是为了让金属液可以快速和均匀的进入到砂型型腔内。
引入方向与,砂型型腔有一定的角度,而非直角,防止直冲砂型。
详细DWG图纸请JIA:三二③1爸爸五四0 六
全套资料低价拾元起
确定直浇道位置和高度:直浇道位置如下图所示,其高度为379mm,比型腔要高出84mm。
各浇道比例设计同样如下图所示。
直浇道截面:
S=3.14*25*25=1962.5(平方毫米)
内浇道截面:
S=(20+40)*10/2=300(平方毫米) 最后绘出的浇注系统如下图所示。