不良分析报告-8D-改善报告-
8d报告完整版范文3篇
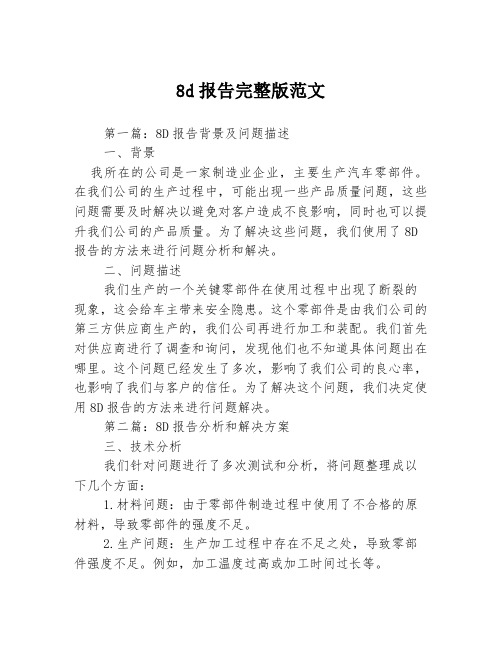
8d报告完整版范文第一篇:8D报告背景及问题描述一、背景我所在的公司是一家制造业企业,主要生产汽车零部件。
在我们公司的生产过程中,可能出现一些产品质量问题,这些问题需要及时解决以避免对客户造成不良影响,同时也可以提升我们公司的产品质量。
为了解决这些问题,我们使用了8D 报告的方法来进行问题分析和解决。
二、问题描述我们生产的一个关键零部件在使用过程中出现了断裂的现象,这会给车主带来安全隐患。
这个零部件是由我们公司的第三方供应商生产的,我们公司再进行加工和装配。
我们首先对供应商进行了调查和询问,发现他们也不知道具体问题出在哪里。
这个问题已经发生了多次,影响了我们公司的良心率,也影响了我们与客户的信任。
为了解决这个问题,我们决定使用8D报告的方法来进行问题解决。
第二篇:8D报告分析和解决方案三、技术分析我们针对问题进行了多次测试和分析,将问题整理成以下几个方面:1.材料问题:由于零部件制造过程中使用了不合格的原材料,导致零部件的强度不足。
2.生产问题:生产加工过程中存在不足之处,导致零部件强度不足。
例如,加工温度过高或加工时间过长等。
3.设计问题:设计过程中没有考虑到应力分布的均匀性,导致零部件在使用过程中容易产生应力过大的现象。
四、解决方案1.材料问题:我们将与供应商重新协商并重新规定原材料标准,以保证原材料的质量。
2.生产问题:我们将对生产过程进行检查和测试,改进加工温度和加工时间,并进一步探究生产中存在的不足之处,以最大程度地提高相关生产能力。
3.设计问题:我们会重新设计零部件,考虑应力分布的均匀性,并对原有零部件进行更加严格的测试和分析以验证新设计的可行性。
第三篇:8D报告措施计划和预防五、措施计划1.与供应商合作并重新规定原材料标准。
2.对生产过程进行检查和测试,并改进加工温度和加工时间。
3.重新设计零部件,考虑应力分布的均匀性,并进行严格的测试和分析。
4.对生产和供应链流程进行跟踪和监控,确保问题不再发生。
8D报告(8D-report) 螺纹孔不良

主题(Subject)问题类型(Rea For CA)零件编号(Parts NO.)报告日期(Date)部门(Dept):QE生产姓名(Name):徐凯程光君1NO.负责人1Gian 2徐凯1NO.负责人1宋海涛2程光君徐凯3程光君毛伟NO.确认人1毛伟2程光君3毛伟NO.负责人1宋海涛2杨磊12表单编号: 保存期限:三年2016/8/11螺纹孔加工增加对刀程式后CNC未发现有漏攻牙产品持续进行江苏精研科技股份有限公司日期E178-漏攻牙E178漏攻牙改善报告4、明确和核实根本原因(Discipline 4.Define and Verify Root Causes)Gian 客户反应7月份漏攻牙累计700pcs,8月份41pcs增加目视检验螺纹孔人员后未发现有漏攻牙产品流至QC段。
2016/8/11谷磊1、小组成员(Discipline 1.Team Members)纠正措施(permanent Corrective Actions)日期2016/8/11效果验证(Verification of Effectiveness)E1788/11全检16K产品未发现漏攻牙产品。
PM 李宁暂时补救的纠正措施(Immediate Containment Actions)FD在制品20K&待出货16K,使用M1.0螺纹规100%全检后安排检验人员100%目视螺纹出货。
CNC检验段和检包螺纹孔检验段增加1人目视100%检验螺纹孔。
2016/8/11备注(Memo)8、关闭报告(Discipline 8. CONGRATULATE YOUR TEAM)CNC机台增加对刀仪,并将丝锥加工对刀程式调整至螺纹孔加工完成后进行对刀,刀具断裂机台停机加工并报警提示,刀具完好则继续加工。
2016/8/11 纠正措施报告 (8D CAR)2、问题描述(Discipline 2. Problem Description)2016/8/10ME 3、临时措施(Discipline 3. Immediate Containment Actions)螺纹孔漏加工不良产生原因:加工过程中丝锥断裂机台程式未设定防呆措施导致漏攻牙产品混入正常品。
尺寸不良分析报告 8D报告
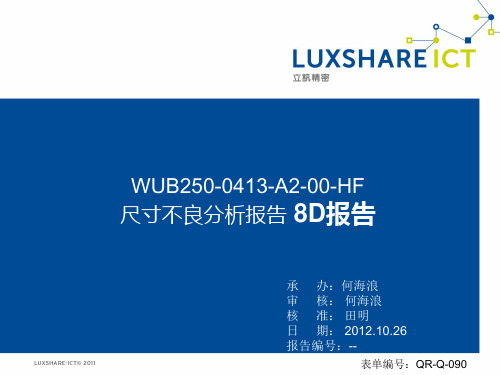
原因分析及验证
>总结: 针对客户反馈产品尺寸不良现象,我司通过对产品相关尺
寸,机械及电气性能(插拔力,插拔寿命,接触阻抗及与公座 对插灌胶)综合确认,以上结果符合产品要求,不会影响客 户使用与功能,因此请客户评估产品4.98尺寸超差帮忙消 化使用。
Thank You!
4.2
4.25
4.21
4.22
4.28 4.27 4.26 4.26 4.27 4.25 4.28 4.24 4.28 4.25
四.原因分析及验证
>.二.对客户反馈相关尺寸端子弹片高度测试确认,规格0.64+/-0.10实测0.62~0.70 符合产品尺寸要求
样品编号 Sample 1 Sample 2 Sample 3 Sample 4 Sample 5 Sample 6 Sample 7 Sample 8 Sample 9 Sample 10
USB 2.0 A TYPE尺寸测试数据
规格 0.64+/-0.10
0.63 0.64 0.63 0.67 0.65 0.70 0.62 0.64 0.63 0.66
实测数据
0.64
0.64
0.63
0.66
0.64
0.63
0.62
0.63
0.63
0.64
0.65
0.67
0.65
0.66
0.63
0.63
原因分析及验证
>五. 产品插拔力寿命测试确认,插入力35N MAX实测 33.02MAX 拔出力规格10Nmin 实测16.00MIN 。 寿命测试后接触阻抗规格30mΩMAX ,实测 11.1 mΩ ~18.1mΩ,寿命测试后产品插拔力及接触阻抗符合产品 要求,见以下测试报告
同方丝印不良8D改善报告

主题Caption 遥控器丝印字体不良*13PCS.供应商Supplier深圳金星精密技术有限公司客户Customer 沈阳同方物料编号S/N845-052-03B05/SY14008金星报告编号编号:B-QC-S-007CAP001第几次RO1成立小组Form theTeam张廷相、李冉、何奇祥、冯长庚、黄小燕,张家全,张昌南,张升东问题描述Problem description(5W2H) 1.When发生时间:2014年04月23日2.Where地点: 沈阳同方3.Who当事人: 金星生产部/品质部4.What问题主要内容: 同方客户在检验时发现遥控器不良(丝印字体模糊)占*13PCS.5.Why为何发生:1.面壳材料丝印来料问题;2.生产落机时漏检导致不良品流入客户。
6.How现时状态:遥控器不良问题,已确认属实;客户要求派人返工并提供改善报告。
过渡措施Containmen t action 1.Implementation of the actions/措施实施:1.培训生产线所有作业员,按照客户标准及作业标准书进行作业,IQPC进行巡检监督;发现不符合要求的工序立即纠正处理;2.生产QC在全检时特别留意外观丝印不良问题,由原来的两人检查丝印现增加到3人全检在经QC全检合格后方可流入下一道工序。
3.OQC将此类问题列入重点管控项目,重点检验,杜绝不良品流入客户。
2.Verification of the actions/结果确认:对25/4日生产1000PCS品质部进行确认全检1000PCS没有发现丝印不良,以上效果确认有效,可按此规定执行。
Rootcause 根本原因(4M1E) 寻找真正原因/Root causes find out:1.人(M):新进QC人员没有做重点培训,品质意识不足及QC漏检导致。
2.机(M);3.料(M):机壳来料丝印不良,品质员没有严格把好关导致。
4.法(M): 管理员监管不到位人为疏忽导致。
8D问题改善分析报告

第8讲分析问题的方法之二——PDCA手法与8D团队(下)8D团队改善之D4—D8的内涵8D团队改善的应用跨功能小组案例分析上一讲已经介绍了其中的D1和D2这两个部分,以下继续介绍其余六个部分。
8D团队改善之D3、D4和D58D改善之D3:临时措施1.为什么要采取临时措施在8D团队改善中,首先是成立一个跨功能的改善团体,然后按照客户的语言来描述问题。
定义和描述问题之后,并不是要急于分析、解决问题,而是要及时地采取临时性的措施,防止问题继续进一步严重。
临时性的措施不要求能根本性地解决问题,也不要求能面面俱到地处理问题,而是在情况紧急的形势下,果断地采取必要的手段和方法,防止问题的进一步扩大化,围堵、隔离和追踪问题。
因此,实施临时性措施的目的,是为了在根本性地彻底解决问题前,尽可能降低和补救由于问题发生所带来的一切损失。
2.围堵或隔离问题的措施为了达到阻止灾害进一步扩大化的目的,就需要想临时性的措施来围堵和隔离问题,进一步追踪灾害涉及的范围。
当出现的问题有可能危害到客户的利益时,应十分坦诚地与客户通报相关的信息,保证客户在面对可能出现的问题时有足够的反应时间。
这样,就能有效地将客户由此产生的不满意程度降到最低点。
围堵、隔离以及追踪问题可以采取多种多样的临时性措施。
例如,将出现问题的产品进行标识,防止不良品的进一步扩散;如果质量不合格的产品已经提供给了客户,则需要采取必要措施,必须将已售给客户的不良品用合格品换回或按原价退款给客户的办法全部收回。
8D改善之D4:界定根本原因在D3过程中,在探求根本原因之前,首先针对问题采取紧急的临时性措施进行防堵。
在防堵问题的同时,还需要同步进行清查搜寻的工作。
出现质量问题的产品,也是一笔珍贵的原始资料,其作用相当于实验过程中的小白鼠。
清查搜寻这些资料,有助于在D4过程中有效准确地界定问题发生的根本原因。
借助于搜寻所获得的样本资料,才能进行进一步的分析、研究,进而寻找出问题产生的根本原因。
螺丝不良 8D报告
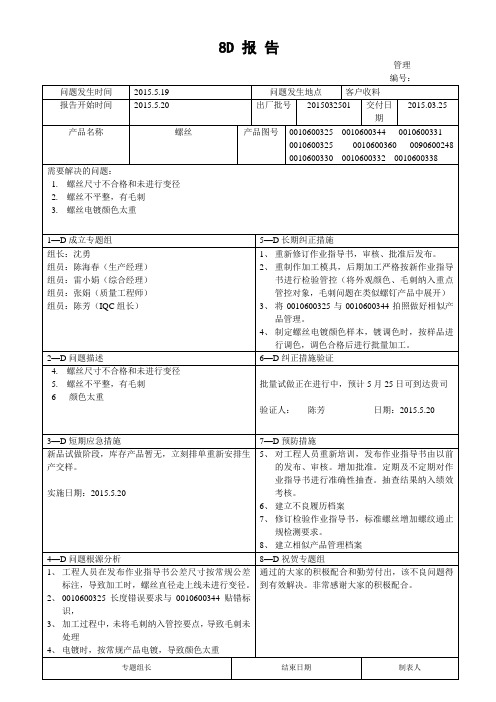
4、制定螺丝电镀颜色样本,镀调色时,按样品进行调色,调色合格后进行批量加工。
2—D问题描述
6—D纠正措施验证
4.螺丝尺寸不合格和未进行变径
5.螺丝不平整,有毛刺
6颜色太重
批量试做正在进行中,预计5月25日可到达贵司
验证人:陈芳日期:2015.5.20
需要解决的问题:
1.螺丝尺寸不合格和未进行变径
2.螺丝不平整,有毛刺
3.螺丝电镀颜色太重
1—D成立专题组
5—D长期纠正措施
组长:沈勇
组员:陈海春(生产经理)
组员:雷小娟(综合经理)
组员:张娟(质量工程师)
组员:陈芳(IQC组长)
1、重新修订作业指导书,审核、批准后发布。
2、重制作加工模具,后期加工严格按新作业指导书进行检验管控(将外观颜色、毛刺纳入重点管控对象,毛刺问题在类似螺钉产品中展开)
通过的大家的积极配合和勤劳付出,该不良问题得到有效解决。非常感谢大家的积极配合。
专题组长
结束日期
制表人
2015.5.20
陈芳
保管至无效YC-QD-QR18版本/修订A/0第页,共页
8D报告
管理编号:ຫໍສະໝຸດ 问题发生时间2015.5.19
问题发生地点
客户收料
报告开始时间
2015.5.20
出厂批号
2015032501
交付日期
2015.03.25
产品名称
螺丝
产品图号
001060032500106003440010600331
001060032500106003600090600248001060033000106003320010600338
电源不良8d分析报告
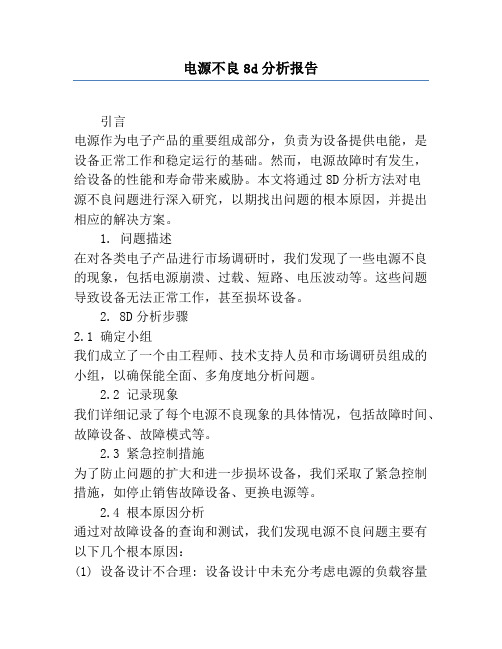
电源不良8d分析报告引言电源作为电子产品的重要组成部分,负责为设备提供电能,是设备正常工作和稳定运行的基础。
然而,电源故障时有发生,给设备的性能和寿命带来威胁。
本文将通过8D分析方法对电源不良问题进行深入研究,以期找出问题的根本原因,并提出相应的解决方案。
1. 问题描述在对各类电子产品进行市场调研时,我们发现了一些电源不良的现象,包括电源崩溃、过载、短路、电压波动等。
这些问题导致设备无法正常工作,甚至损坏设备。
2. 8D分析步骤2.1 确定小组我们成立了一个由工程师、技术支持人员和市场调研员组成的小组,以确保能全面、多角度地分析问题。
2.2 记录现象我们详细记录了每个电源不良现象的具体情况,包括故障时间、故障设备、故障模式等。
2.3 紧急控制措施为了防止问题的扩大和进一步损坏设备,我们采取了紧急控制措施,如停止销售故障设备、更换电源等。
2.4 根本原因分析通过对故障设备的查询和测试,我们发现电源不良问题主要有以下几个根本原因:(1) 设备设计不合理: 设备设计中未充分考虑电源的负载容量和电压波动等因素,导致电源无法稳定输出;(2) 材料质量问题: 电源中使用的电容、电阻等元器件存在质量问题,导致电源寿命短、易损坏;(3) 生产工艺不合理: 生产过程中存在不合理的焊接、组装等工艺操作,导致电源内部接触不良、焊接虚焊等问题。
2.5 制定纠正措施针对以上根本原因,我们制定了相应的纠正措施:(1) 设备设计优化: 在设备设计过程中加强功耗分析,合理选择电源元器件,确保电源的稳定输出;(2) 严格质量控制: 对电源元器件进行严格的质量检测,确保质量符合标准;(3) 完善生产工艺: 完善生产流程,加强焊接、组装等工艺操作的质量管理,降低接触不良和焊接虚焊的风险。
2.6 实施措施我们组织了相应的人员,对问题进行了改进。
在新批次的产品中引入了更稳定的电源设计,严格控制元器件的质量,并加强了生产工艺的管理。
2.7 验证措施效果在新批次产品的生产过程中,我们对电源进行了全面的验证和测试。
8D报告-8d报告

四. 8D步骤-D7效果确认及标准化
验证预防再发对策并监控长期的效果。 水平展开,以防同一问题及类似问题再 度发生。将相关对策形成书面文件(管 理制度、程序文件、作业指导书、表单、 技术文件、工程图纸等)。
四. 8D步骤-D7效果确认及标准化
效果确认 实事求是,以事实和数据为依据,对数据用统计工具处 理后得出相应的结论,不应未做对比分析即判定效果。
16.00% 14.00% 12.00% 10.00%
8.00% 6.00% 4.00% 2.00% 0.00%
slot1
slot2
slot3
slot4
slot5
改善前
改善后
数据点多按日期来建议走势图,数据点少可用上面的柱状图
数据来源: 时 间:
➢关键点一 :改善前后对比,数量及比例。 ➢关键点二: 结果收集的数据来源要说明。
TOYOTA 5-Why?
1W
WHY 问题
2W
WHY 中间原因
3W
WHY 中间原因
4W
WHY 中间原因
5-WHY分析案例1 状态1 一辆汽车出了故障不能行驶(WHY1)
状态2-原因1 引擎故障(WHY2)
状态3-原因2
火花塞不点火(WHY3)
状态4-原因3
3.措施 尽量具 体化。
四. 8D步骤—D6预防再发对策
计划和执行选取的预防再发对策。去除 临时行动。
需要考虑的问题:
1.确定并执行预 防再发对策, 并应注意持续 实施监控,以 确定根因已经 消除。
2.待步入生产阶 段,应即监视 纠正措施之长 期效果,并于 必要时采行补 救措施。
3.验证 预防再发 对策有效 后,可以 停止临时 措施。
8D报告模板

——需要有责任人和完成时间 ——需要有责任人和完成时间
96h
★说明: 原因和对策确定的原则:四不放过原则 ①原因未查清不放过 ②责任人未受到处理不放过 ③责任人和周围员工未受到教育不放过 ④制定切实可行的整改措施没有落实不放过
D6.验证纠正措施
Verify Corrective Actions
5D
24h
D3.应急措施
Containment Action(s)
风险批次
抽检排除风险
围堵措施
24h
结论
1、成品库数量及批次
抽检2K不良1k,风险极高 100%挑选使用
出厂
2、组测的数量及批次
抽检2K不良1k,风险极高 100%挑选使用
出厂
3、AA的数量及批次
正常可用
4、COB的数量及批次
正常可用
5、SMT的数量及批次
正常可用
6、原材料库的数量及批次
正常可用
7、客户端批次及数量
正常可用
8、检验点批次及数量
正常可用
小结:库存重检确认污点不良率较高,且大部分为浅污点软件不可抓,存在一定出货风险; 故厂内在制&库存品已安排全部隔离
D4.识别问题根因
Identify Root Cause of the Problem
1.1 分析流程如下: 1、头脑风暴确 定潜在原因(至 少10条)
核算质量成本
感谢您的聆听!
汇报人:XXX
结论:(措施是否有效实施)
D7.预防措施标准化
Preventive Action(s)
二、加入到LL中(必填,以附件格式插入报告中)
三、事件回溯(必填,以附件格式插入报告中) 将之前验证的3-5条发生原因和流出原因(检验工序的
产品外观不良8d报告围堵措施
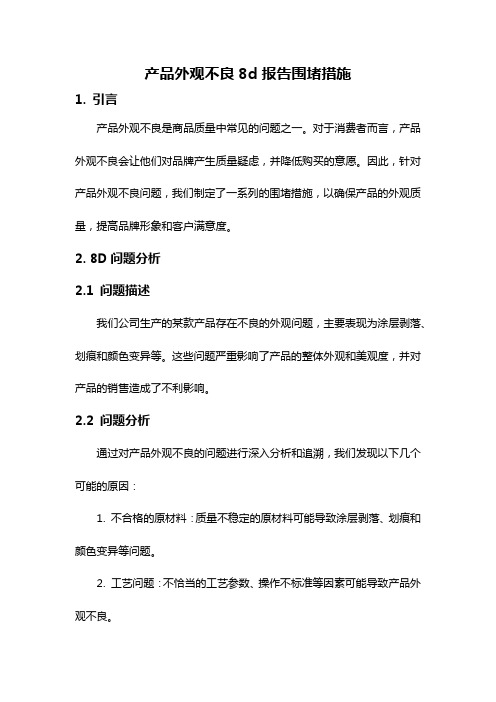
产品外观不良8d报告围堵措施1. 引言产品外观不良是商品质量中常见的问题之一。
对于消费者而言,产品外观不良会让他们对品牌产生质量疑虑,并降低购买的意愿。
因此,针对产品外观不良问题,我们制定了一系列的围堵措施,以确保产品的外观质量,提高品牌形象和客户满意度。
2. 8D问题分析2.1 问题描述我们公司生产的某款产品存在不良的外观问题,主要表现为涂层剥落、划痕和颜色变异等。
这些问题严重影响了产品的整体外观和美观度,并对产品的销售造成了不利影响。
2.2 问题分析通过对产品外观不良的问题进行深入分析和追溯,我们发现以下几个可能的原因:1. 不合格的原材料:质量不稳定的原材料可能导致涂层剥落、划痕和颜色变异等问题。
2. 工艺问题:不恰当的工艺参数、操作不标准等因素可能导致产品外观不良。
3. 供应链管理问题:供应商提供的原材料质量未经严格控制,无法保证每一批产品的一致性。
4. 质量检验不准确:质检流程的漏洞、检验人员的技能水平等因素可能导致产品外观问题未被及时发现。
3. 围堵措施3.1 质量控制体系完善为解决产品外观不良问题,我们需要建立一个完善的质量控制体系,确保产品在每个生产环节都能够进行严格的质量检验。
具体的围堵措施包括:- 优化供应链管理:与供应商建立合作伙伴关系,共同制定原材料质量管理要求,并对供应商进行定期的质量审核和评估。
- 建立严格的工艺标准:制定详细的工艺参数和操作规范,确保产品每个生产环节按照标准进行操作。
- 设备管理:对生产设备进行定期维护和保养,并进行设备的合理配置和更新,以确保操作的稳定性和可靠性。
3.2 质量培训与技能提升为了提升员工的质量意识和技能水平,我们需要进行全员培训和技能提升。
具体的围堵措施包括:- 培训计划:制定全员培训计划,包括质量管理、工艺操作和质检技巧等相关培训内容。
- 培训材料准备:准备培训材料和案例,以帮助员工更好地理解和掌握质量要求和操作规范。
- 绩效考核和奖励机制:建立与质量相关的绩效考核和奖励机制,激励员工积极参与质量管理和技能提升。
不良分析报告-8D-改善报告-

项目编号: 分析日期: 小组人员:
版本:R3
版本修订说明
版本 日期 修订者
修订说明
R1
12/2/10
ymz
R2
12/25/10
ymz
R3
8/18/11
YMZ
1.客诉开始进行第一次分析。
1.新识别不良 1.接到客户投诉,立即电话联系客户 2.增加问题发生的地点和反馈预防措施
Page 13
提供完整整改报告
把分析报告转换成8D格式或客户指定格式给到客 户。
1.每次沟通后要把进度邮件给到客户。 2.预防措施完成前,把样品给到客户确认。 3.把整改报告整理成8D格式给客户时,不可遗漏: 原因分析时的测试数据, 改善措施的关联图片, 验证报告&实验测试报告, 图纸,SIP,SOP等过程支持资料。
Confidential
Page 14
联系人 联系方式 沟通的内容 达成的共识 双方分歧点 下次沟通时间
第四次电话沟通
样品验证是否可以();批量交货()
Confidential
Page 15
Page 2
处理流程
1
接到客户投诉 /异常问题
确认不良现象 、比率,图片
电话和客 户沟通
2 隔离库存、wip
、供应商、客户
确定不良数量 及处理办法
确定短期措施(满 足客户需求)
3
原因分析
根本原因及改 善措施
结果验证计划
4 验证报告&实验
测试报告
合格样品 / 预 防措施
电话和客 户沟通
Confidential
本原因
备注
1
2 3 4 5
Confidential
产品折弯角度不良8D报告
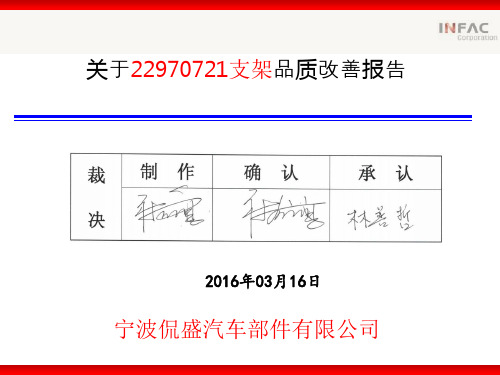
4. 根本原因 Supplier 分析结果: 2016-03-16 - 在V型压弯工序模具设计88.5度 (下限管理) SPEC:90 °± 2°(标准图未注,3D图基准) - - 追溯 批次: 20151226
负责
质量 技术 生产
角度偏小,造成装配不良
2. 措施现况.
5. 根本对策 改善日程 一. 临时措施: 选别 措施 区分 检查数 发生数 在操作 反送 废弃 1.客户端库存进行sorting.(6560) – 预计3.18 2016.3.16 完 2016.3.16 零部件 可疑批次 全部隔离返厂 工 程 ● 完成品 2.厂内库品调查:无库存. 主机厂 3.批次号为20151226 ,数量 8000 全部追回隔离. 2016.3.16 3. 发生现况 4.北京仓库0PCS 及因派克库存批号确认 .-进行 二. 根本措施: - 模具尺寸改善 :88.5°->89.5° (考虑钢板 因派克公司反馈产品角度偏小,装配不良 有部分回弹性) - 改善批次 20161005 (2016.1/5日) - 产品验证:89.7~90.1° OK
变更前 变更后
产品定位块干 涉取件
定位块高度价格 低设计成89.5°的原 因是 : 考虑钢板 折角度后 有一定 的回弹性,故角度 设定偏下
- 变更前折弯角度 是88.5 - 从模具中取件时定位块干涉
考虑产品取出适合性且角度中心 值管理 变更后 模具角度 89.5°
五、模具 改善前后产品检具验证对比结果。改善后按90± 1 °控制。
标准类 反映 图纸 P-FMEA 管理计划书 工作标准书 质量C/SHEET 设备日常检点表
二、制造工序排查分析
连续模生产流程
发生点 翻边、打弯、压筋 V型弯 折弯工序是在铁板上面 向下下压,形成内角度 90° 的模具 落料、冲孔、压字
不良分析报告-8D-改善报告-

页码
Confidential
Page 2
处理流程
接到客户投诉 /异常问题 确认不良现象 、比率,图片 电话和客 户沟通
1
2小时内完成 小时内完成
隔离库存、wip 、供应商、客户 确定不良数量 及处理办法 确定短期措施(满 足客户需求) 电话和客 户沟通
2
4小时内完成 小时内完成 3
原因分析 根本原因及改 善措施 结果验证计划 电话和客 户沟通
不良分析改善报告
项目编号: 项目编号: 分析日期: 分析日期: 小组人员: 小组人员:
版本: 版本: R3
版本修订说明
版本
R1 R2 R3
日期
12/2/10 12/25/10 8/18/11
修订者
ymz ymz YMZ
修订说明
1.客诉开始进行第一次分析。 1.新识别不良 1.接到客户投诉,立即电话联系客户 2.增加问题发生的地点和反馈的人
第三次电话沟通
联系人 联系方式 沟通的内容 达成的共识 双方分歧点 下次沟通时间
Confidential
Pag验证报告 实验测试报告
Confidential
Page 12
预防措施
供应商SOP更改内 更改内 供应商 容 供应商SIP更改内 更改内 供应商 容 公司图纸更改内容
Confidential
Page 5
临时措施
数量 供应商 WIP 库存 已经出货 不良品检 测方法 不良品分 选方法 处理方法
Confidential
Page 6
第二次电话沟通
联系人 联系方式 沟通的内容 达成的共识 双方分歧点 下次沟通时间
Confidential
Page 7
8D改善报告

执行人
确 认
完成日:
受影响品区域、数量Affected Product Area And Q'ty
年 月 日
处置方式Disposition:
4.原因分析(必要附图片说明)Root Cause(Put In Illustrated Picture If Necessary)
5.永久改善&预防措施Permanent Corrective&Preventive Action
执行人
确 认
完成日:
年 月 日执行人源自6.措施执行情况及效果Action Follow Up
验证人
结论Conclusion: 7.防止再发(Actions Taken to Prevent Recurrence)
确认日:
年 月 日
结案Close? Yes No
判定Confirmed By
审批Approved By
8D改善报告单
发行号: 客 户 流水号 产品规格 不良数量 订单号 接收日期
1.异常描述Non-conformance Details(必要附图片说明)
发文单位
拟制
审核
年 2.改善小组 (姓名、部门、备注事项)TEAM(Including Name,Department,Remarks)
月
日
3.应急措施Containment Action
日期Date: 8.同顾客达成最终协议(Completion agreed by Customer)
1)本单适用于客户投诉(如客户有要求可依客户版本).
备注:
2)本单流程:品管部门→品管部主管→改善小组→责任部门主管→执行人→小组判定→品管部主管审批.
连接器行业端子电镀不良8D报告案例样板

连接器行业端子电镀不良8D报告案例样板8D报告案例:连接器行业端子电镀不良1.情况描述:在连接器的生产过程中,发现一批端子的电镀存在不良情况。
问题主要集中在电镀层的厚度不均匀和存在气泡、麻点等缺陷。
该批次端子属于高精度产品,质量要求较高。
2.问题分析:2.1工艺参数分析:通过检查工艺参数记录发现,电镀温度、时间等参数都在正常范围内,且符合工艺规范。
因此,问题并不是由于工艺参数调整不当导致的。
2.2原材料分析:经过对原材料进行抽样分析,未发现原材料存在质量问题。
因此,问题并不是由于原材料问题导致的。
2.3设备状态分析:检查设备运行状态,包括电镀槽、电镀设备、输送带等。
未发现设备故障或异常情况。
因此,问题并不是由于设备问题导致的。
2.4操作人员分析:对操作人员进行培训,强调操作规范,并检查其操作流程。
发现一部分操作人员操作不规范,导致端子的镀层不均匀,存在气泡、麻点等缺陷。
因此,问题主要是由于操作人员操作不规范导致的。
3.问题解决:3.1培训操作人员:针对操作不规范的操作人员进行培训,并制定详细的操作规范,确保每个环节的操作正确执行。
3.2质量控制检查:增加质量控制检查的频率和强度,对端子进行严格的质量检查,保证产品质量符合要求。
3.3镀层监控:对电镀设备进行定期的维护和保养,确保电镀液的浓度和温度等参数稳定,并设置自动报警装置,确保电镀液参数异常时及时发现并处理。
4.效果验证:经过上述措施的实施,端子电镀不良情况得到有效改善。
经过多批次产品的质量检查,端子的电镀层厚度均匀,且无气泡、麻点等缺陷。
5.预防措施:5.1制定操作规范:对操作人员进行详细的培训,制定操作规范,确保每个环节的操作正确执行。
5.2强化质量控制:增加质量控制检查的频率和强度,对产品进行严格的质量检查,及时发现和纠正问题。
5.3定期维护设备:定期对电镀设备进行维护和保养,确保设备的稳定运行,避免设备故障对产品质量造成影响。
以上是连接器行业端子电镀不良的8D报告案例样板,详细阐述了问题的分析过程、解决措施以及效果验证和预防措施。
产品外观不良8d改善报告

产品外观不良8d改善报告> 项目名称:产品外观不良8D改善报告> 编号:XXXXXXX> 日期:XXXX年XX月XX日1. 引言在生产过程中,我们发现产品外观出现不良问题,这不仅给产品品质带来了负面影响,也对公司声誉造成了严重损失。
为了解决这个问题,我们进行了一系列的分析和改进措施,并制定了该8D改善报告。
2. 问题描述我们的产品外观出现不良的情况主要表现为以下几个方面:- 表面有明显划痕- 涂层出现脱落- 颜色不均匀这些问题不仅影响了产品的美观度,更可能导致一些功能上的缺陷,从而影响了产品的可靠性。
3. 根本原因分析通过对问题进行分析和探索,我们发现了造成产品外观不良的根本原因:- 生产设备的不稳定性- 生产工艺的缺陷- 操作人员技术水平不足4. 8D改善措施为了解决问题,我们采取了以下8D改善措施:4.1 D1:建立跨部门团队我们组建了包括生产、质检、工程等多个部门的跨部门团队,以协调和整合各个部门的资源,共同解决问题。
4.2 D2:问题确认和定义我们通过对不良产品进行全面检测和验证,确认了问题的具体表现和范围,并对问题进行了定义,确定了改善的目标。
4.3 D3:制定临时对策为了尽快解决当前的问题,我们采取了一些临时对策,例如进行现场培训和操作规程的修订,以提升操作人员的技术水平,减少不良问题的发生。
4.4 D4:根本原因分析我们通过对生产设备和工艺进行全面的调研和分析,找出了生产设备的不稳定性和生产工艺的缺陷这两个根本原因,并进行了深入的问题追溯。
4.5 D5:制定长期对策基于根本原因的分析,我们制定了长期的对策:- 更新和维护生产设备,确保设备的运行稳定性和效率- 优化生产工艺,改进涂层技术和颜色控制工艺- 加强对操作人员的培训和管理,提升技术水平和责任意识4.6 D6:执行对策我们按照制定的长期对策,进行了一系列的执行行动,包括设备维护、工艺改进和人员培训,以确保改善措施的落地和有效实施。
灯条不良8D分析及改善报告

ECHOM毅昌8D报告客户名称:发生时间:2018年03月25日报告人:罗亮单号:20180401001物料编码:0350TA002产品名称:灯条问题描述Describe the Issue3月25号客户反馈0350TA002灯条出现死灯、亮暗不均、色差等不良现象。
客户端退回13PCS灯条成品投诉LED死灯/LED微亮/LED色差不良。
(光电检查结果如下:死灯4条/微亮4条/色差4条/良品1条)3月29号我司人员去客户现场,3月30号出现1条死灯灯条,3月31号客户上线持续出现10根灯条死灯成立团队Setup one Team开发:林青云尹清海制造:罗亮、周玉龙、王际尧品质:卢群连暂定对策Containment Action1.客户端成品/库存品,此不良非批量异常,请贵司正常使用。
2.我司在线制作品,加强在线控制及过程中检验。
3.我司在分析收到不良品期间,客户持续发生同类问题,我司安排品质人员去客户现场处理原因分析Root Cause Analysis1、LENS刮花外观不良分析根据客户端反馈及在客户端现场确认,50TA产品在客户端一直出现LENS刮花的问题,经我司内部排查为包装使用的吸塑盒内腔尺寸较大,比灯条尺寸长60MM左右,灯条放在吸塑盒内科还有一定的活动空间,未能完全固定,导致在运输过程中透镜之间的相互摩擦,从而产生刮花不良。
为确定LENS刮花是由包材不合适,在运输过程中导致的。
抽取一箱包装好的材料做震荡测试,震荡测试后检测结果为,240条出现9条刮花不良现象,可确定LENS刮花不良是由包材不合适所致。
振动条件参数:1.加速度(196m/s24g)2.频率范围(100hz~2000hz)3.测试时间(X/Y/Z各轴向持续45min,共15次扫频循环)测试数量:测度前良品240PCS测试结果:测试后检查结果有9PCS为划伤不良:良品N:231r:9p:3.752、连接器脱落不良分析3月30号在客户车间现场对所有的已退不良品做点亮测试确认,38条共发现29条灯条条连接器不良连接器脱落,破损连接器不良根据焊点观察可以确认为两PIN端子的固定脚位焊盘较小,在插拔过程中容易导致连接器脱落,连接器胶壳破损。
不良8D报告

发生单位 发生时间提出单位/日期 要求反馈时间 编制: 日期: 2013-7-17组织整改单位 接收人/日期纠正和预防措施报告( 8D)报告书编号:Z204.03生产单位名称:科技粉末冶金有限公司 规格型号:HK0612A 零件名称: 油泵转子小组 成员 名单生产 采购 质量 技术白、姚 、营销 供方 财务 人力斌4 应急措施 /已采取什么措施防止不合格品流出?类别 措施//数量情况 负责人/日期6 永久对策:已采取什么措施防止以后生产不合格品?考虑:* 防错,试验,过程控制 措 施 负责人/日期1 问题详情级别/重要度: 产品尖锐部位缺料 受影响的数量:库存零 件原材料1 对此款产品易发生问题 的部位由成型管理人员做好宣 传,并此款产品由成型技术负责人做到定人,定岗,并做好 13-7-20 此款产品生产记录的不良品数据,以便追 朔。
2 知会相关各个部们的宣传,做到防控结合 姚叶花/13-7-19 白积珍/13-7-20 3 教育作业员切实安《成型生产作业指导书进行》 宁 / 4 、将该不良做成《过往不良履历》,并接示在生产 0 现场,教育培训作业员,防止类似不良再发; 8 5 、做成《外观全检作业指导书》,增加外观全检工序; . 0 2 . 2 0 13/7/20 亮 13/7/19 /13-7-21 /13-7-20是 再发?否 ∨半成品成 进行外观全检; 1485PCS 品 运输中产 品 顾客处产 挑选不良,不良品作退货报废处理 品 其他2 向类似产品的展开该问题在其他产品上发生过吗? 首批出货合格零件贴什么标签 ? 绿色或红色不干胶? 备注 /结果挑选,不良报废考虑* 其他零件 * 一般零件 * 其他型号半成品 * 其他型号成品 * 相关原材料 * 其他是 ∨否标记:黄卡标示牌;黄色纸张5 、产生原因分析:人:没有按要求全方位检查,成型收料不极时; 机: 料: 法3 流出原因的初步分析不合格产品应当在何处被发现? * 在制造工序中 * 在制造后(如最终检验) * 出货前 * 进料检测 没有被发现的原因:1 、成型工序作业员因收料步极时,产品脱模后在下滑轨道中产 品相互碰撞,导致不良产品流到下工序。
- 1、下载文档前请自行甄别文档内容的完整性,平台不提供额外的编辑、内容补充、找答案等附加服务。
- 2、"仅部分预览"的文档,不可在线预览部分如存在完整性等问题,可反馈申请退款(可完整预览的文档不适用该条件!)。
- 3、如文档侵犯您的权益,请联系客服反馈,我们会尽快为您处理(人工客服工作时间:9:00-18:30)。
数量
不良品分 选方法
临时措施
处理方法
精品课件
Page 6
联系人 联系方式 沟通的内容 达成的共识 双方分歧点 下次沟通时间
第二次电话沟通
精品课件
Page 7
序 号
可能原因
可能原因分析
验证方法(是否能 是否为根
复制不良)
本原因
备注
1
2 3 4 5
精品课件
Page 8
序 号
原因分析
1
2 3 4 5
不良分析改善报告
项目编号: 分析日期: 小组人员:
版本: R3
版本修订说明
版本 日期 修订者
修订说明
R1
12/2/10
ymz
R2
12/25/10
ymz
R3
8/18/11
YMZ
1.客诉开始进行第一次分析。
1.新识别不良 1.接到客户投诉,立即电话联系客户 2.增加问题发生的地点和反馈的人
页码
精品课件
精品课件
Page 12
供应商SOP更改内 容
供应商SIP更改内 容
公司图纸更改内容
公司SOP更改内容
公司SIP更改内容
精品课件
预防措施
Page 13
提供完整整改报告
把。
1.每次沟通后要把进度邮件给到客户。 2.预防措施完成前,把样品给到客户确认。 3.把整改报告整理成8D格式给客户时,不可遗漏: 原因分析时的测试数据, 改善措施的关联图片, 验证报告&实验测试报告, 图纸,SIP,SOP等过程支持资料。
电话和客 户沟通
4小时内完成
电话和客 户沟通
1.5天内完成
2天内完成
Page 3
不良现象 不良地点 不良影响 不良率
不良图片
问题描述
精品课件
Page 4
联系人 联系方式 沟通的内容 达成的共识 双方分歧点 下次沟通时间
第一次电话沟通
精品课件
Page 5
供应商 WIP 库存
已经出货
不良品检 测方法
Page 2
处理流程
1
接到客户投诉 /异常问题
确认不良现象 、比率,图片
电话和客 户沟通
2 隔离库存、wip
、供应商、客户
确定不良数量 及处理办法
确定短期措施(满 足客户需求)
3
原因分析
根本原因及改 善措施
结果验证计划
4 验证报告&实验
测试报告
合格样品 / 预 防措施
电话和客 户沟通
精品课件
2小时内完成
精品课件
Page 14
联系人 联系方式 沟通的内容 达成的共识 双方分歧点 下次沟通时间
第四次电话沟通
样品验证是否可以();批量交货()
精品课件
Page 15
根本原因及改善措施
应对措施
相关图片
精品课件
Page 9
结果验证计划
序
责任 预计完成 调整后完成日 实际完成
号
待办事项内容
人
日期
期
日期
状况
备注
1
2
3
4
5
精品课件
Page 10
联系人 联系方式 沟通的内容 达成的共识 双方分歧点 下次沟通时间
第三次电话沟通
精品课件
Page 11
验证报告&实验测试报告