油膜振荡
汽轮发电机机组油膜振荡综合诊断与处理建议
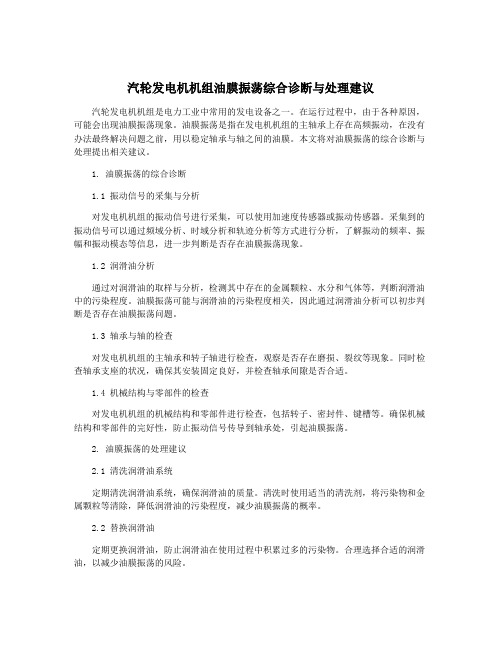
汽轮发电机机组油膜振荡综合诊断与处理建议汽轮发电机机组是电力工业中常用的发电设备之一。
在运行过程中,由于各种原因,可能会出现油膜振荡现象。
油膜振荡是指在发电机机组的主轴承上存在高频振动,在没有办法最终解决问题之前,用以稳定轴承与轴之间的油膜。
本文将对油膜振荡的综合诊断与处理提出相关建议。
1. 油膜振荡的综合诊断1.1 振动信号的采集与分析对发电机机组的振动信号进行采集,可以使用加速度传感器或振动传感器。
采集到的振动信号可以通过频域分析、时域分析和轨迹分析等方式进行分析,了解振动的频率、振幅和振动模态等信息,进一步判断是否存在油膜振荡现象。
1.2 润滑油分析通过对润滑油的取样与分析,检测其中存在的金属颗粒、水分和气体等,判断润滑油中的污染程度。
油膜振荡可能与润滑油的污染程度相关,因此通过润滑油分析可以初步判断是否存在油膜振荡问题。
1.3 轴承与轴的检查对发电机机组的主轴承和转子轴进行检查,观察是否存在磨损、裂纹等现象。
同时检查轴承支座的状况,确保其安装固定良好,并检查轴承间隙是否合适。
1.4 机械结构与零部件的检查对发电机机组的机械结构和零部件进行检查,包括转子、密封件、键槽等。
确保机械结构和零部件的完好性,防止振动信号传导到轴承处,引起油膜振荡。
2. 油膜振荡的处理建议2.1 清洗润滑油系统定期清洗润滑油系统,确保润滑油的质量。
清洗时使用适当的清洗剂,将污染物和金属颗粒等清除,降低润滑油的污染程度,减少油膜振荡的概率。
2.2 替换润滑油定期更换润滑油,防止润滑油在使用过程中积累过多的污染物。
合理选择合适的润滑油,以减少油膜振荡的风险。
2.3 修复或更换磨损严重的零部件对于存在磨损、裂纹等严重问题的零部件,应及时进行修复或更换,避免其对机组运行造成不利影响,减少油膜振荡的概率。
2.4 加装振动阻尼器在主轴承上加装振动阻尼器,以调节轴的振动,减少油膜振荡的发生。
振动阻尼器可以通过调整阻尼力大小来降低轴的振动幅度,从而改善油膜振荡现象。
油膜振荡产生的原因
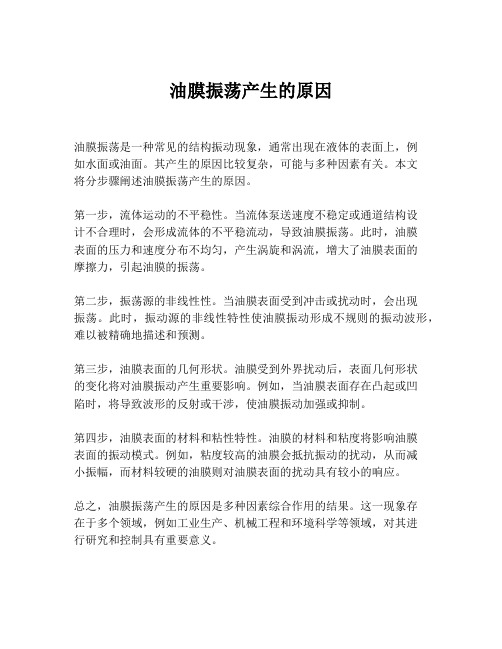
油膜振荡产生的原因
油膜振荡是一种常见的结构振动现象,通常出现在液体的表面上,例
如水面或油面。
其产生的原因比较复杂,可能与多种因素有关。
本文
将分步骤阐述油膜振荡产生的原因。
第一步,流体运动的不平稳性。
当流体泵送速度不稳定或通道结构设
计不合理时,会形成流体的不平稳流动,导致油膜振荡。
此时,油膜
表面的压力和速度分布不均匀,产生涡旋和涡流,增大了油膜表面的
摩擦力,引起油膜的振荡。
第二步,振荡源的非线性性。
当油膜表面受到冲击或扰动时,会出现
振荡。
此时,振动源的非线性特性使油膜振动形成不规则的振动波形,难以被精确地描述和预测。
第三步,油膜表面的几何形状。
油膜受到外界扰动后,表面几何形状
的变化将对油膜振动产生重要影响。
例如,当油膜表面存在凸起或凹
陷时,将导致波形的反射或干涉,使油膜振动加强或抑制。
第四步,油膜表面的材料和粘性特性。
油膜的材料和粘度将影响油膜
表面的振动模式。
例如,粘度较高的油膜会抵抗振动的扰动,从而减
小振幅,而材料较硬的油膜则对油膜表面的扰动具有较小的响应。
总之,油膜振荡产生的原因是多种因素综合作用的结果。
这一现象存
在于多个领域,例如工业生产、机械工程和环境科学等领域,对其进
行研究和控制具有重要意义。
油膜振荡报告
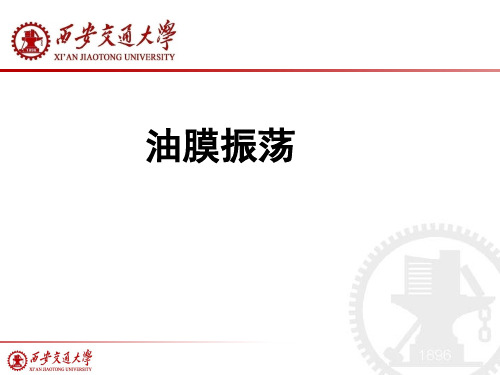
13
根据油流的连续条件分析油膜振荡
• 在△t时间内流进间隙(C+e)的油量为: • 在△t时间内流出间隙(C-e)的油量为:
t
t
R C e 2 R
2
C e
• 轴颈中心围绕O旋转时所造成空穴的体积为上图中月牙形部 分的体积,等于通过OO1线的直径所扫过的体积: e 2 R t 根据油腔中油流连续条件可得:
t R R C e t C e 2Re 2 2
2
流体涡动旋转速度等于轴 的旋转速度的一半
“半速涡动”现象
实际上,考虑到油膜速度并不按线性规律分布,而且由于润滑油在轴 承端面有泄露,一般涡动频率略小于轴颈转速的一半,约为轴颈转速 的0.40-0.49。
抑振措施 1、合理的选取轴承 轴承的选取主要是改变产生油膜压力的油 楔数目。 a、圆形轴瓦:一个 b、椭圆轴瓦:两个 c、多油楔轴承:大于两个
单油楔与多油楔轴承
2、避开共振区域 通过改变结构增加转子的固有频率,使转子 的工作转速低于2倍的临界转速。
3、采用稳定性很好的可倾轴瓦式轴承 当转子受到外界激励因素干扰,轴 颈暂时偏离原来位置时,各瓦块可按轴 颈偏移后的载荷方向自动调整位置, 使油膜合力与外载荷相平衡。
可倾轴瓦
4、其它措施 a、改变润滑油的粘度 b、减少轴承的长径比 c、增加供油压力
谢谢
化工学院
当涡动力超过油膜的阻尼,则使轴颈绕原平衡位置O′产 生涡动,这时涡动是发散的,轴颈运动是不稳定的。随着 转速的进一步提高,从而形成油膜振荡。
油膜涡动和油膜振荡
区别:油膜涡动(半速涡动)一般是在低转速下发生的, 而油膜振荡一般是在高转速下发生。
联系:油膜涡动一旦发生,不会随着转速的升高而消失, 会保持一定的振幅,涡动频率随转动频率的升高而增加, 始终保持一半的转速频率;在高转速下,油膜涡动的频率 会跟轴的固有频率发生共振。
油膜振荡是什么?发生油膜振荡为什么不能用提高转速的方法消除
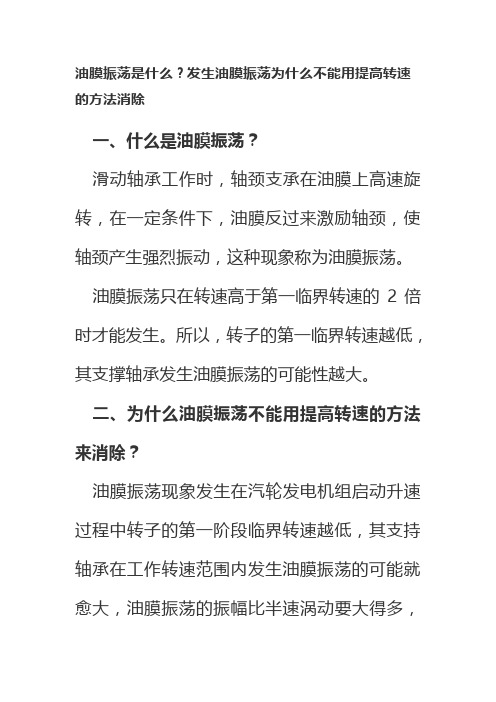
油膜振荡是什么?发生油膜振荡为什么不能用提高转速的方法消除
一、什么是油膜振荡?
滑动轴承工作时,轴颈支承在油膜上高速旋转,在一定条件下,油膜反过来激励轴颈,使轴颈产生强烈振动,这种现象称为油膜振荡。
油膜振荡只在转速高于第一临界转速的2倍时才能发生。
所以,转子的第一临界转速越低,其支撑轴承发生油膜振荡的可能性越大。
二、为什么油膜振荡不能用提高转速的方法来消除?
油膜振荡现象发生在汽轮发电机组启动升速过程中转子的第一阶段临界转速越低,其支持轴承在工作转速范围内发生油膜振荡的可能就愈大,油膜振荡的振幅比半速涡动要大得多,
转子跳动非常剧烈,而且往往不是一个轴承和相邻轴承,而是整个机组的所有轴承都出现强烈振动,在机组附近还可以听到“咯咯”的撞击声,油膜振荡一旦发生,转子始终保持着等于临界转速的涡动速度,而不再随转速的升高而升高,这一现象称为油膜振荡的惯性效应。
所以遇到油膜振荡发生时,不能像过临界转速那样,借提高转速冲过去的办法来消除。
汽轮发电机机组油膜振荡综合诊断与处理建议

汽轮发电机机组油膜振荡综合诊断与处理建议一、概述汽轮发电机机组作为发电厂的核心设备,其运行稳定性和可靠性对供电系统的正常运行至关重要。
而油膜振荡作为汽轮发电机机组常见的故障之一,一旦出现将严重影响设备的安全运行。
对汽轮发电机机组油膜振荡进行综合诊断与处理具有重要的意义。
二、油膜振荡的概念及危害油膜振荡是指在摩擦副间的油膜中因为受到外界激振或者系统本身的激振而发生振动的现象。
油膜振荡会导致机械部件磨损加剧、噪音增大、振动增大等问题,严重时还会造成设备损坏、停机甚至事故。
三、油膜振荡的诊断方法1. 实测法:通过振动仪、加速度传感器等设备对汽轮机设备进行实时监测,获得机组振动和频谱信息,判断是否存在油膜振荡现象。
2. 振动信号处理和分析法:通过对振动信号进行处理和分析,提取特征频点和特征值,判断是否存在油膜振荡现象。
3. 润滑油分析法:对发电机机组的润滑油进行分析,判断是否存在异常现象。
四、油膜振荡的处理建议1. 优化油膜结构:通过改进滑动轴承的结构、参数和材料,减少外激振和本振,提高滑动轴承的稳定性和可靠性。
2. 优化润滑系统:采用先进的油膜振动抑制技术,优化机组的润滑系统,提高摩擦副的稳定性和可靠性。
3. 控制外界激振:对机组的外界激振源进行控制和抑制,减少外界激振对机组的影响。
4. 提高润滑油质量:选择优质的润滑油品牌,保障机组的润滑油质量,减少润滑副的摩擦和磨损。
五、实际应用案例某电厂的汽轮发电机机组在运行中出现了油膜振荡的故障,严重影响了机组的安全运行。
经过综合诊断和处理,先后采取了优化油膜结构、改进润滑系统和控制外界激振等措施。
经过一段时间的试运行,汽轮发电机机组的油膜振荡问题得到了有效控制,机组的运行稳定性和可靠性得到了显著提高。
油膜振荡实验报告

一、实验目的本次实验旨在通过模拟油膜振荡现象,探究油膜振荡的产生机制、影响因素以及危害,为实际工程应用中预防和控制油膜振荡提供理论依据。
二、实验原理油膜振荡是指旋转轴颈在滑动轴承中带动润滑油高速流动,在一定条件下,高速油流反过来激励轴颈,产生一种强烈的自激振动现象。
其主要原因是在轴颈与轴瓦之间的间隙中形成的油膜,其承载力与外载荷平衡时,轴颈处于平衡位置;当转轴受到某种外来扰动时,轴颈中心就会在静平衡位置附近发生涡动,其振动频率约为转子回转频率的一半,称为半速涡动。
当转速达到比第一阶临界转速的2倍稍高以后,半速涡动的涡动速度与转轴的第一阶临界转速相重合,产生共振,振动幅度剧烈增加,称为油膜振荡。
三、实验仪器与材料1. 实验台:用于放置实验装置,确保实验过程稳定;2. 轴承:模拟实际工程中的轴承,提供支撑和承载;3. 轴颈:模拟实际工程中的轴颈,承受油膜振荡带来的振动;4. 润滑油:模拟实际工程中的润滑油,提供润滑和承载;5. 传感器:用于测量振动信号;6. 数据采集系统:用于实时采集振动数据;7. 电脑:用于数据处理和分析。
四、实验步骤1. 将轴承安装在实验台上,确保轴承与轴颈的配合精度;2. 将润滑油加入轴承中,确保油膜形成;3. 启动轴颈,逐渐提高转速,观察振动信号;4. 记录不同转速下的振动数据;5. 分析振动数据,判断是否存在油膜振荡现象;6. 通过改变轴承间隙、润滑油种类、转速等参数,研究油膜振荡的影响因素。
五、实验结果与分析1. 实验结果表明,当转速达到一定值时,振动信号出现约转速频率0.35~0.49倍的频率成分,表明半速涡动现象的存在;2. 当转速继续升高,半速涡动的频率成分保持不变,说明半速涡动现象稳定;3. 当转速达到比第一阶临界转速的2倍稍高时,振动幅度急剧增加,表明油膜振荡现象发生;4. 通过改变轴承间隙、润滑油种类、转速等参数,发现轴承间隙过小、润滑油粘度过高、转速过高等因素容易引发油膜振荡。
油膜振荡故障类型之一

油膜振荡故障类型之一
1.油膜振荡概念:转子轴颈在轴承内做高速旋转的同时,还环绕某一平衡中心做公转运动。
如果转子轴颈主要是由油膜力的激励作用引起的涡动,则轴颈的涡动角速度近似为转速的二分之一,所以称为“半速涡动”。
当转速升高到一阶临界转速的两倍附近时,涡动频率与转子一阶自振频率相重合,转子轴承系统将发生激烈的油膜共振,这种共振涡动就称为油膜振荡。
2.油膜涡动、油膜振荡的主要征兆与信号特征:
(1)油膜涡动实际振动频率要小于转频的一半,一般为0.43-0.48倍。
油膜振荡频率为转子系统的一阶自振频率。
(2)油膜振荡是一种自激振动,维持振动的能量由轴本身在旋转中产生,不受外部激振力的影响。
发生大振幅油膜振荡后,继续升高转速,振动频率不会变化,振幅也不会下降。
(3)发生油膜振荡时,轴心轨迹形状紊乱、发散。
(4)发生油膜振荡时,往往来势很猛,瞬时间振幅突然升高,引起轴承油膜破裂,会同时发生碰撞摩擦。
(5)当转子转速进入油膜共振区后,升高转速,振荡频率不变,振幅不下降。
但降低转速,振动也并不马上消失,油膜振荡消失的转速要低于它的起始转速。
3.油膜振荡频谱图
4.油膜振荡防治措施:
(1)避开油膜共振区域。
机器设计时避免转子工作转速在一阶临界转速的两倍附近运行。
(2)增加轴承比压。
增大轴颈偏心率,提高油膜的稳定性。
(4)减小轴承间隙。
(5)控制适当的轴瓦预负荷。
(6)选用抗振性好的轴承。
(7)调整油温。
适当升高油温,减小油的黏度,可以增加轴颈在轴承中的偏心率,有利于轴颈稳定。
汽轮发电机机组油膜振荡综合诊断与处理建议

汽轮发电机机组油膜振荡综合诊断与处理建议汽轮发电机机组是利用汽轮机驱动发电机产生电能的装置,其正常运转对于电力生产至关重要。
由于机组长期运行以及其他因素的影响,机组中的润滑油系统可能出现油膜振荡问题,严重影响机组的正常运行和寿命。
对于汽轮发电机机组油膜振荡问题的综合诊断和处理非常重要。
本文将从机组油膜振荡的原因、诊断方法和处理建议三个方面进行综合分析。
一、机组油膜振荡的原因1. 油膜振荡是由于机组运行时润滑油的振动引起的。
润滑油在机械部件表面形成一层薄膜,减少机械部件之间的摩擦和磨损,从而保证机组的正常运行。
但当润滑油的振动频率与机械部件的共振频率相近时,就会产生油膜振荡。
2. 机组设计不合理是油膜振荡的重要原因之一。
机组结构刚度不足、支座刚度不均匀、轴承刚度过大或过小等问题都可能导致油膜振荡的发生。
3. 机组运行过程中的机械故障也是油膜振荡的重要原因。
机械部件的磨损、轴承的损坏、齿轮间隙过大等问题都可能导致机组的振动频率发生变化,从而引发油膜振荡。
二、机组油膜振荡的诊断方法1. 观察机组的振动情况:通过安装振动传感器等设备,观察和记录机组的振动情况,特别是在运行过程中的振动频率和振幅的变化。
如果发现振动频率接近共振频率,说明存在油膜振荡的可能性。
2. 检测润滑油的振动:将机组的润滑油样品取出,使用振动传感器等设备检测润滑油的振动情况。
如果发现润滑油的振动频率与机组振动频率相近,说明存在油膜振荡问题。
3. 利用计算机模拟或仿真软件进行分析:将机组的结构和运行参数输入计算机模拟或仿真软件,通过计算和分析机组的共振频率和振动模态,判断是否存在油膜振荡。
三、机组油膜振荡的处理建议1. 对机组进行结构改造:根据机组的实际情况,对结构刚度不足、支座刚度不均匀等问题进行改造。
增加机组的刚度可以降低共振频率,从而减少油膜振荡的发生。
2. 更换合适的润滑油:选择合适的润滑油可以改善油膜振荡问题。
润滑油的黏度、粘度指数、摩擦系数等参数对油膜的形成和振动频率有一定的影响。
汽轮发电机机组油膜振荡综合诊断与处理建议
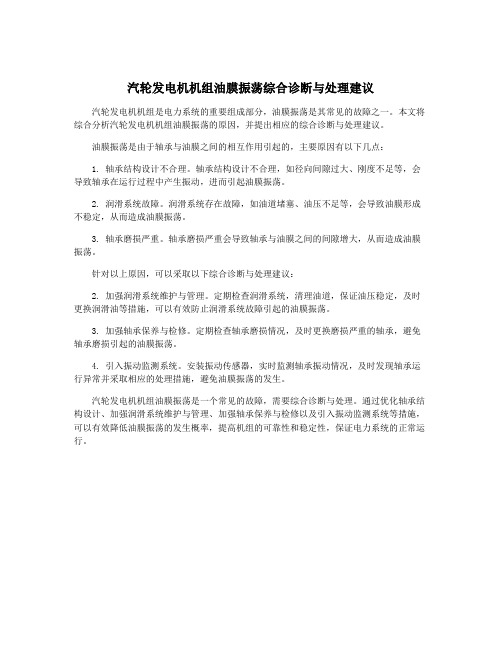
汽轮发电机机组油膜振荡综合诊断与处理建议
汽轮发电机机组是电力系统的重要组成部分,油膜振荡是其常见的故障之一。
本文将综合分析汽轮发电机机组油膜振荡的原因,并提出相应的综合诊断与处理建议。
油膜振荡是由于轴承与油膜之间的相互作用引起的,主要原因有以下几点:
1. 轴承结构设计不合理。
轴承结构设计不合理,如径向间隙过大、刚度不足等,会导致轴承在运行过程中产生振动,进而引起油膜振荡。
2. 润滑系统故障。
润滑系统存在故障,如油道堵塞、油压不足等,会导致油膜形成不稳定,从而造成油膜振荡。
3. 轴承磨损严重。
轴承磨损严重会导致轴承与油膜之间的间隙增大,从而造成油膜振荡。
针对以上原因,可以采取以下综合诊断与处理建议:
2. 加强润滑系统维护与管理。
定期检查润滑系统,清理油道,保证油压稳定,及时更换润滑油等措施,可以有效防止润滑系统故障引起的油膜振荡。
3. 加强轴承保养与检修。
定期检查轴承磨损情况,及时更换磨损严重的轴承,避免轴承磨损引起的油膜振荡。
4. 引入振动监测系统。
安装振动传感器,实时监测轴承振动情况,及时发现轴承运行异常并采取相应的处理措施,避免油膜振荡的发生。
汽轮发电机机组油膜振荡是一个常见的故障,需要综合诊断与处理。
通过优化轴承结构设计、加强润滑系统维护与管理、加强轴承保养与检修以及引入振动监测系统等措施,可以有效降低油膜振荡的发生概率,提高机组的可靠性和稳定性,保证电力系统的正常运行。
油膜振荡产生的原因
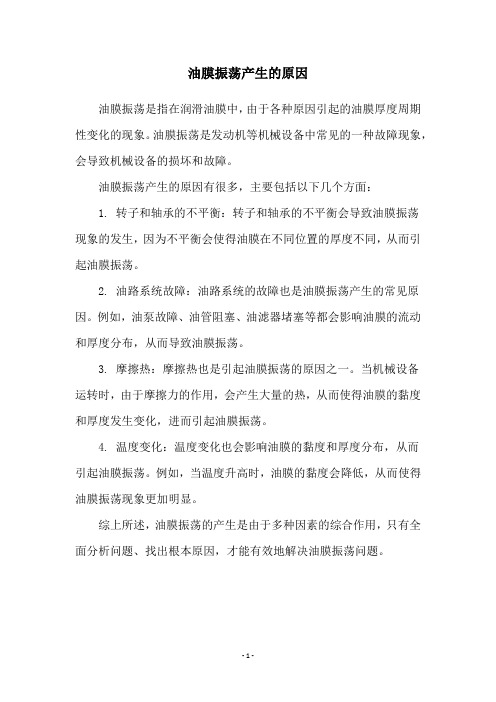
油膜振荡产生的原因
油膜振荡是指在润滑油膜中,由于各种原因引起的油膜厚度周期性变化的现象。
油膜振荡是发动机等机械设备中常见的一种故障现象,会导致机械设备的损坏和故障。
油膜振荡产生的原因有很多,主要包括以下几个方面:
1. 转子和轴承的不平衡:转子和轴承的不平衡会导致油膜振荡
现象的发生,因为不平衡会使得油膜在不同位置的厚度不同,从而引起油膜振荡。
2. 油路系统故障:油路系统的故障也是油膜振荡产生的常见原因。
例如,油泵故障、油管阻塞、油滤器堵塞等都会影响油膜的流动和厚度分布,从而导致油膜振荡。
3. 摩擦热:摩擦热也是引起油膜振荡的原因之一。
当机械设备
运转时,由于摩擦力的作用,会产生大量的热,从而使得油膜的黏度和厚度发生变化,进而引起油膜振荡。
4. 温度变化:温度变化也会影响油膜的黏度和厚度分布,从而
引起油膜振荡。
例如,当温度升高时,油膜的黏度会降低,从而使得油膜振荡现象更加明显。
综上所述,油膜振荡的产生是由于多种因素的综合作用,只有全面分析问题、找出根本原因,才能有效地解决油膜振荡问题。
- 1 -。
汽轮发电机机组油膜振荡综合诊断与处理建议

汽轮发电机机组油膜振荡综合诊断与处理建议汽轮发电机机组油膜振荡是指在润滑油膜的作用下,轴承产生的振动现象。
油膜振荡对机组的安全运行和设备的寿命造成了严重威胁,因此如何进行综合诊断和有效处理是非常重要的。
本文将对汽轮发电机机组油膜振荡的综合诊断与处理进行建议。
一、油膜振荡的诊断1. 振动检测振动检测是最直观的诊断手段,通过振动传感器对轴承振动情况进行监测。
正常情况下,振动应该是稳定的,若出现频繁的振动异常,则说明可能存在油膜振荡问题。
2. 油膜监测油膜监测是通过监测轴承的润滑油膜情况来判断是否存在振荡问题。
当润滑油膜不稳定时,往往会引起振动异常。
3. 温度检测由于油膜振荡会导致摩擦增加,从而使轴承温升,因此可以通过监测轴承温度来初步判断是否存在振荡问题。
4. 润滑油分析通过对润滑油的化学成分和污染物进行分析,可以了解润滑油是否存在异常情况,从而判断是否存在振荡问题。
二、油膜振荡的处理建议1. 调整轴承间隙轴承间隙对油膜的稳定起着至关重要的作用,因此可以通过调整轴承间隙来减轻油膜振荡的情况。
2. 改进润滑系统改进润滑系统可以采用更高性能的润滑油、改进润滑油供给系统等方式,从根本上解决油膜振荡的问题。
3. 增加油膜稳定性可以通过增加油膜的黏性或者加强润滑油的供给,来增加油膜的稳定性,减轻振荡的出现。
4. 检修轴承如果油膜振荡已经严重影响机组的运行,建议进行轴承的检修,彻底清洁和更换润滑油,并对轴承进行维护保养。
5. 定期维护及时清理设备表面和检查润滑油情况,可以防止因为摩擦增加而导致油膜振荡。
汽轮发电机机组油膜振荡是一种常见但危害严重的问题,需要及时进行综合诊断和处理。
合理的诊断手段和处理建议可以有效的帮助企业解决油膜振荡问题,提高机组的可靠性和安全性。
也需要加强对机组设备的定期维护和维修工作,减少油膜振荡的发生。
汽轮发电机机组油膜振荡综合诊断与处理建议

汽轮发电机机组油膜振荡综合诊断与处理建议汽轮发电机机组作为发电厂的重要设备之一,其稳定运行对于保障电网的稳定供电至关重要。
在机组运行过程中,油膜振荡问题常常会影响机组的运行稳定性,甚至对机组设备造成损害。
对于汽轮发电机机组油膜振荡问题的诊断与处理非常重要。
本文将针对这一问题进行综合诊断分析,并提出合理的处理建议。
一、油膜振荡的概念及影响油膜振荡是指在机械设备的润滑接触表面上,由于介质不均匀或运动状态不稳定产生的油膜振动现象。
在汽轮发电机机组中,油膜振荡主要出现在轴承、齿轮等润滑部位,严重影响设备的运行稳定性。
油膜振荡会导致机组发生噪音、振动增大,严重时还会出现局部过热或磨损等问题,严重影响机组的正常运行。
长期存在的油膜振荡问题还会缩短设备的使用寿命,增加维护成本,甚至引发设备故障,严重影响机组的安全运行。
二、油膜振荡的诊断方法1. 振动分析法通过振动传感器对机组设备进行实时振动监测,并对振动频率、振幅等进行分析,从而判断设备是否存在油膜振荡问题。
2. 润滑油分析法对机组设备的润滑油进行采样分析,通过油品的磨损颗粒、氧化物质等指标的检测,判断设备是否存在油膜振荡问题。
3. 温度监测法对机组设备的润滑部位进行温度监测,发现异常温升情况,从而判断设备是否存在油膜振荡问题。
4. 声学诊断法三、油膜振荡的处理建议1. 优化润滑系统对机组设备的润滑系统进行维护优化,包括润滑油的选择、供油方式、滤芯更换周期等,以保证润滑系统的稳定运行,减少油膜振荡的可能性。
2. 调整设备运行参数通过调整机组设备的运行参数,包括转速、负荷等,减小设备的运行振动,从而减少油膜振荡的发生。
3. 设备状态监测建立设备状态监测系统,实时监测机组设备的运行状态,及时发现油膜振荡问题的存在,并进行预警与处理。
4. 设备维护保养加强机组设备的维护保养工作,包括轴承润滑、齿轮清洗等,保证设备的运行状态良好,减少油膜振荡的发生。
5. 职工培训增加机组操作人员的油膜振荡问题的相关培训,提高操作人员对该问题的认识,加强对设备的监测与维护,减少油膜振荡的发生。
什么是油膜振荡?

油膜振荡发生在油润滑滑动轴承的旋转设备中,在转子正常工作时,轴径中心和轴承中心并不重合,而是存在一个偏心距e,当载荷不变、油膜稳定时,偏心距e保持不变,机组运行稳定,轴颈上的载荷W与油膜压力保持平衡,若外界给轴颈一扰动力,使轴心O1位置产生一位移△e而达到新位置,这时油膜压力由p变为p′,因而不再与此时的载荷W′(W′-W)平衡,两者的合力为F,其分力F1将推动轴颈回到起初的平衡位置O1,而在分力F2的作用下,轴颈除了以角速度ω作自转外,还将绕O1涡动(涡动方向与转动方向相同),其涡动速度约为角速度的一半,称为油膜涡动(半速涡动)。
油膜涡动产生后就不消失,随着工作转速的升高,其涡动频率也不断增强,振幅也不断增大,如果转子的转速继续升高到第一临界转速的2倍时,其涡动频率与一阶临界转速相同,产生共振,振幅突然骤增,振动非常剧烈,轴心轨迹突然变成扩散的不规则曲线,半频谐波振幅值就增加到接近或超过基频振幅,若继续提高转速,则转子的涡动频率保持不变,始终等于转子的一阶临界转速,这种现象称为油膜振荡。
发生油膜振荡现象:a.发生强烈振动时,振幅突然增加,声音异常。
b.振动频率为组合频率,次谐波非常丰富,并且与转子的一阶临界转速相等的频率的振幅接近或超过基频振幅;c.工作转速高于第一临界转速的2倍时才发生强烈振动,振荡频率等于转子的第一临界转速,并且不随工作转速的变化而变化,只有工作转速低于2倍第一临界转速后,剧烈振动才消失;d.轴心轨迹为发散的不规则形状,进动方向为正进动;e.轴承润滑油粘度变化对振动有明显的影响,降低润滑油粘度可以有效地抑制振动。
油膜振荡形成原因:油膜振荡是由半速涡动发展而成,即当转子转速升至两倍于第一临界转速时,涡动频率与转子固有频率重合,使转子----轴承系统发生共振性振荡而引起,如果能提高转子的第一临界转速,使其大于0.5倍工作转速,即可避免发生油膜振荡,但这显然无法实现。
只有通过加大轴承的载荷,使轴颈处于较大的偏心率下工作,提高轴瓦稳定性的办法解决。
汽轮发电机机组油膜振荡综合诊断与处理建议
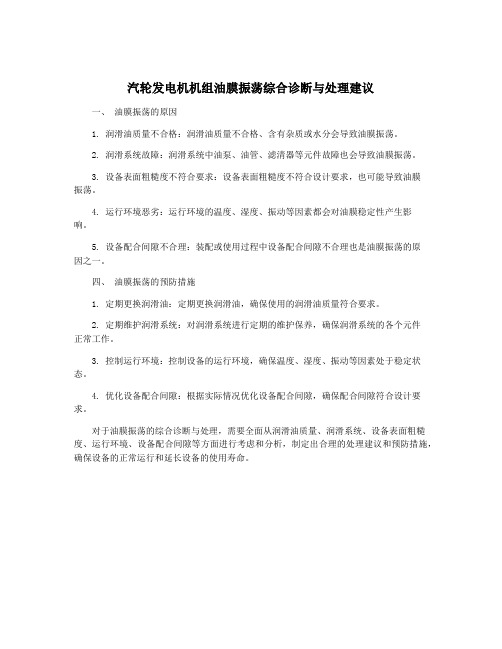
汽轮发电机机组油膜振荡综合诊断与处理建议
一、油膜振荡的原因
1. 润滑油质量不合格:润滑油质量不合格、含有杂质或水分会导致油膜振荡。
2. 润滑系统故障:润滑系统中油泵、油管、滤清器等元件故障也会导致油膜振荡。
3. 设备表面粗糙度不符合要求:设备表面粗糙度不符合设计要求,也可能导致油膜
振荡。
4. 运行环境恶劣:运行环境的温度、湿度、振动等因素都会对油膜稳定性产生影
响。
5. 设备配合间隙不合理:装配或使用过程中设备配合间隙不合理也是油膜振荡的原
因之一。
四、油膜振荡的预防措施
1. 定期更换润滑油:定期更换润滑油,确保使用的润滑油质量符合要求。
2. 定期维护润滑系统:对润滑系统进行定期的维护保养,确保润滑系统的各个元件
正常工作。
3. 控制运行环境:控制设备的运行环境,确保温度、湿度、振动等因素处于稳定状态。
4. 优化设备配合间隙:根据实际情况优化设备配合间隙,确保配合间隙符合设计要求。
对于油膜振荡的综合诊断与处理,需要全面从润滑油质量、润滑系统、设备表面粗糙度、运行环境、设备配合间隙等方面进行考虑和分析,制定出合理的处理建议和预防措施,确保设备的正常运行和延长设备的使用寿命。
汽轮发电机机组油膜振荡综合诊断与处理建议

汽轮发电机机组油膜振荡综合诊断与处理建议汽轮发电机机组油膜振荡是一种常见的故障,在机组正常运行过程中会导致机组振动异常,给设备安全和运行稳定性带来威胁。
为了正确诊断和处理该故障,以下给出一些综合诊断和处理建议:1. 振荡原因分析:首先需要确定振荡的具体原因。
可能的原因包括轴承故障、不平衡、轴封失效、内部结构松动等。
对不同可能原因的诊断可以采用振动分析、温度、压力、油液分析等方法。
2. 振荡的振动频率和幅值:确定振荡的频率和振幅,并与正常运行的数据进行比较。
这可以通过振动监测设备进行实时监测,并与设备的历史数据进行对比分析。
3. 检查轴承状态:轴承是汽轮发电机机组中常见的振动故障原因之一。
定期检查轴承的状态,包括测量轴承的轴向和径向游隙、凸轮磨损、轴承零部件的损坏等。
如果发现问题,及时更换或进行维修。
4. 平衡旋转部件:不平衡是导致振动的另一个常见原因。
对于汽轮发电机的转子,定期进行动平衡是必要的。
通过在适当的位置添加或移除质量,使旋转部件达到平衡。
5. 检查轴封状态:轴封失效可能导致油膜振荡。
需定期检查轴封的密封性能以及存在的磨损、裂缝或松动等问题。
如有必要,及时更换轴封。
6. 定期检查内部结构:震动和振荡可能由于内部结构的松动引起。
定期检查内部结构,包括螺栓紧固、接触面清洁和焊接连接等,确保机组内部结构稳定。
7. 机组维护和保养:定期维护和保养机组也是预防油膜振荡的重要措施。
包括更换油液、过滤器,清洗冷却器等。
对汽轮发电机机组油膜振荡的正确诊断和处理需要综合考虑多种因素,包括振动频率、振幅、轴承、不平衡、轴封和内部结构等。
建议采取定期检查和维护的措施,以保证机组的安全和稳定运行。
汽轮发电机机组油膜振荡综合诊断与处理建议

汽轮发电机机组油膜振荡综合诊断与处理建议
汽轮发电机机组在运行过程中,常常会出现油膜振荡问题,给机组的正常运行造成了一定的影响。
为了避免油膜振荡导致更严重的故障,本文将对油膜振荡进行综合诊断,并提出处理建议。
我们需要了解油膜振荡的原因。
油膜振荡是指油膜在运动时发生的不稳定振动现象,主要是由以下原因引起的:1)油膜本身的物理性质,比如粘度、流动性等;2)机组的结构特点,如叶片的形状、叶栅的间隙等;3)工作条件的变化,如压力的变化、速度的变化等。
在诊断油膜振荡时,我们可以采用以下方法:
1)观察振动信号:通过振动传感器采集振动信号,分析振动频谱和时域波形,判断是否存在油膜振荡现象。
2)检测油膜厚度:通过油膜测厚仪检测油膜的厚度,判断是否达到了引起振荡的临界值。
3)测量油膜温度:通过温度传感器测量油膜的温度,判断是否存在温度过高引起油膜振荡的情况。
针对油膜振荡问题,我们可以采取以下处理措施:
1)优化油品选择:选择合适的润滑油,具有较低的粘度和良好的流动性,以减少油膜振动的发生。
2)改进机组结构:对机组的叶片结构和叶栅间隙进行调整,使其满足油膜振荡的稳定条件。
3)调整工作条件:通过调整机组的工作条件,如压力、速度等,使其满足油膜振荡的稳定条件。
4)增加附件设备:在机组上增加振动控制装置,通过对油膜振动的监测和控制,减少振动的发生和传播。
对汽轮发电机机组油膜振荡问题的综合诊断建议是:通过观察振动信号、检测油膜厚度和测量油膜温度等方法,判断油膜振荡的发生情况;针对油膜振荡问题,可以优化油品选择、改进机组结构、调整工作条件和增加附件设备等措施。
通过这些处理措施,可以减少油膜振荡的发生,确保机组的正常运行。
汽轮发电机机组油膜振荡综合诊断与处理建议

汽轮发电机机组油膜振荡综合诊断与处理建议汽轮发电机机组是一种常见的发电设备,其正常运行对于电力系统的稳定运行至关重要。
汽轮发电机机组在长期运行过程中,会出现一些问题,例如油膜振荡,这会直接影响机组的稳定性和可靠性。
针对汽轮发电机机组油膜振荡问题,本文将进行综合诊断,并提出相应的处理建议。
一、油膜振荡的机理油膜振荡是指在发电机机组润滑系统中,由于油膜振动引起的系统异常振动现象。
这种振动通常由于机组内部的摩擦力变化或润滑不良引起,可能直接导致设备的损坏和故障。
在汽轮发电机机组中,油膜振荡通常与机组内部的转子、轴承和润滑系统有关。
二、油膜振荡的诊断方法1. 振动检测:通过安装振动传感器,在机组运行过程中对振动进行实时监测,可以发现油膜振荡的存在及程度。
2. 温度检测:通过在机组润滑系统各个关键部位安装温度传感器,监测润滑油的温度变化,可以及时发现异常和问题。
3. 润滑油分析:对机组润滑油进行定期取样,进行化验分析,可以发现油膜振荡导致的润滑油污染、老化等问题。
4. 轴承状态监测:通过安装轴承状态监测系统,对轴承运行状态进行实时监测,可以及时发现油膜振荡引起的轴承损坏和异常。
以上方法可以综合使用,对机组进行全方位的油膜振荡诊断,为后续处理提供准确的数据支持。
1. 润滑系统优化:对汽轮发电机机组的润滑系统进行优化,包括润滑油的选择、系统的清洗和油路的优化设计,以保证油膜的稳定性和良好润滑效果。
2. 减小负荷变化:尽量避免汽轮发电机机组的频繁启停和负荷变化,减小机组内部摩擦力的变化,降低油膜振荡的发生概率。
3. 加强轴承维护:定期对汽轮发电机机组的轴承进行检查和维护,包括润滑油更换、轴承清洗等工作,保证轴承的正常运行状态,减少由油膜振荡引起的轴承损伤。
4. 定期检测:建立定期的油膜振荡检测机制,及时发现问题并采取措施,以减小损失和降低维护成本。
5. 定期培训:针对发电机机组润滑系统的操作人员进行定期培训,提高其对润滑系统运行和维护的理解和认识,减少因操作不当引起的油膜振荡问题。
汽轮发电机机组油膜振荡综合诊断与处理建议

汽轮发电机机组油膜振荡综合诊断与处理建议汽轮发电机机组油膜振荡是指在涡轮机转子与轴承之间的油膜内,因非稳态激励或综合激励作用下,产生的以径向或轴向方向油膜相对运动引起的机械振荡现象。
汽轮发电机机组油膜振荡会导致振动过大,轴承磨损严重,甚至会引起机组故障,因此对其进行综合诊断与处理十分必要。
本文将对汽轮发电机机组油膜振荡的综合诊断与处理进行分析,并提出相关建议。
一、油膜振荡的诊断1. 振荡现象的观测通过震动测量仪器,对机组进行振动监测,获取振动的频率、幅值、相位等数据,分析振动的特点,确定振荡的种类和位置。
2. 涡轮转子的检查对涡轮转子的表面进行检查,观察是否有明显的磨损痕迹或异常。
同时检查轴承的磨损情况,观察轴承的运行情况是否正常。
3. 润滑油分析对机组的润滑油进行定期的取样检测,分析油品中的金属颗粒、杂质等成分,判断润滑油中的杂质是否超标,从而判断润滑油的清洁度和使用寿命。
4. 振动信号的分析通过振动信号的频谱分析,可以得到振动信号的频率分布情况,从而判断振动的来源和振动的特点。
5. 润滑油膜的模拟通过数值仿真或试验验证的方式,模拟涡轮机转子与轴承之间的油膜情况,分析润滑油膜的形成和运动情况,找出油膜振荡的原因。
二、油膜振荡的处理建议1. 油膜的优化设计通过对机组的润滑系统进行优化设计,可以改善油膜的形成和运动情况,减小油膜振荡的发生概率。
例如采用更优质的润滑油品,改进轴承结构,调整润滑系统的工作参数等方式。
2. 轴承的维护定期对轴承进行维护和保养,及时更换磨损严重的轴承,保证轴承的运行平稳。
采用高质量的润滑油品,保持润滑油的清洁度,延长轴承的使用寿命。
3. 振动的衰减采用合适的振动吸收装置,减小振动的幅值,降低振动对轴承的影响。
可以在轴承处增加减振垫或采用减振材料,减少振动的传递。
4. 故障的预警建立机组的故障预警系统,对机组的振动进行实时监测,并设置预警数值,一旦振动超出预警数值范围,及时报警并进行处理,避免机组发生严重故障。
汽轮发电机机组油膜振荡综合诊断与处理建议
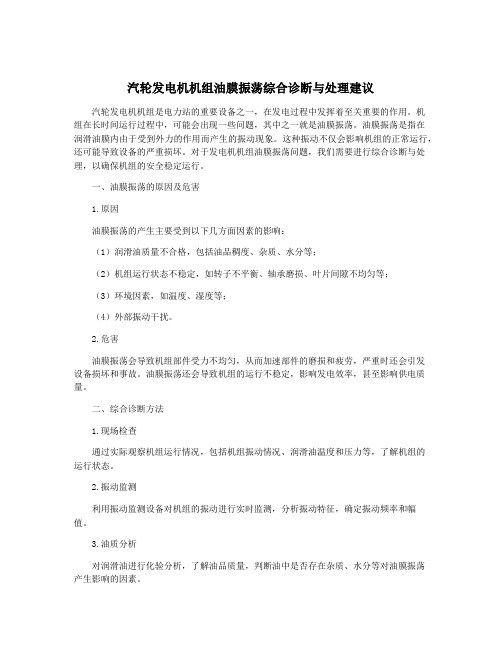
汽轮发电机机组油膜振荡综合诊断与处理建议汽轮发电机机组是电力站的重要设备之一,在发电过程中发挥着至关重要的作用。
机组在长时间运行过程中,可能会出现一些问题,其中之一就是油膜振荡。
油膜振荡是指在润滑油膜内由于受到外力的作用而产生的振动现象。
这种振动不仅会影响机组的正常运行,还可能导致设备的严重损坏。
对于发电机机组油膜振荡问题,我们需要进行综合诊断与处理,以确保机组的安全稳定运行。
一、油膜振荡的原因及危害1.原因油膜振荡的产生主要受到以下几方面因素的影响:(1)润滑油质量不合格,包括油品稠度、杂质、水分等;(2)机组运行状态不稳定,如转子不平衡、轴承磨损、叶片间隙不均匀等;(3)环境因素,如温度、湿度等;(4)外部振动干扰。
2.危害油膜振荡会导致机组部件受力不均匀,从而加速部件的磨损和疲劳,严重时还会引发设备损坏和事故。
油膜振荡还会导致机组的运行不稳定,影响发电效率,甚至影响供电质量。
二、综合诊断方法1.现场检查通过实际观察机组运行情况,包括机组振动情况、润滑油温度和压力等,了解机组的运行状态。
2.振动监测利用振动监测设备对机组的振动进行实时监测,分析振动特征,确定振动频率和幅值。
3.油质分析对润滑油进行化验分析,了解油品质量,判断油中是否存在杂质、水分等对油膜振荡产生影响的因素。
4.检测仪器检测利用检测仪器对叶片间隙、润滑油温度、压力等参数进行监测、测量,了解机组运行的关键参数。
5.数据分析通过以上多种手段获取的数据进行综合分析,找出引起油膜振荡的具体原因,为后续处理提供依据。
三、处理建议1.优化润滑油对润滑油进行更换或者升级,确保油质量符合要求,排除油品质量不良的影响。
2.检修设备对机组进行必要的检修和维护,如调整叶片间隙、更换磨损部件、平衡转子等,消除设备的运行不稳定因素。
3.环境控制调节机组周围的环境,如降低温度、湿度等,减少这些因素对机组产生的影响。
4.振动控制加强机组振动的监测和控制,及时发现振动异常并采取应对措施,减小振动对油膜的影响。
- 1、下载文档前请自行甄别文档内容的完整性,平台不提供额外的编辑、内容补充、找答案等附加服务。
- 2、"仅部分预览"的文档,不可在线预览部分如存在完整性等问题,可反馈申请退款(可完整预览的文档不适用该条件!)。
- 3、如文档侵犯您的权益,请联系客服反馈,我们会尽快为您处理(人工客服工作时间:9:00-18:30)。
油膜振荡的特征及判别方法山东工程学院曲庆文马浩柴山摘要:油膜振荡是大型机电设备出现故障较多的原因之一,本文主要对机电设备中出现油膜振荡的特征及判别方法加以总结论述,以便尽可能地避免油膜振荡的产生,提高机电设备的利用率和生产效率,减少设备的维修时间。
关键词:油膜振荡;设备故障;故障检测1 涡动转轴的涡动通常有惯性涡动、液力涡动和气隙涡动等[1]。
对于轴颈轴承受到动载荷时,轴颈会随着载荷的变化而移动位置。
移动产生惯性力,此时,惯性力也成为载荷,且为动载荷,取决于轴颈本身的移动。
轴颈轴承在外载荷作用下,轴颈中心相对于轴承中心偏移一定的位置而运转。
当施加一扰动力,轴颈中心将偏离原平衡位置。
若这样的扰动最终能回到原来的位置或在一个新的平衡点保持不变,即此轴承是稳定的;反之,是不稳定的。
后者的状态为轴颈中心绕着平衡位置运动,称为“涡动”。
涡动可能持续下去,也可能很快地导致轴颈和轴承套的接触,稳定性是轴颈轴承的重要性能之一,是由于惯性作用的主要例证。
惯性涡动是由于转子系统的不平衡重量引起的惯性离心力P强迫引起的涡动。
图1所示,矢量P与瞬时轴的动态挠度oH的夹角ψ表示惯性涡动的不同位置,夹角ψ随轴的转速n W变化。
对于小的n W值,ψ接近于零,当轴的转速小于临界转速时,ψ由零增加至90°,此时力P可以分解成作用在挠度方向oH上的力P r和垂直于OH的力P t。
P r与轴的弹性变形后生成的弹性力相平衡;而P t则没有与之平衡的固定力,于是被迫形成“同步涡动”。
当轴的转速达到临界转速n k时,涡动达到极值;若转速继续增加,超过临界转速n k后,涡动减小。
此时, P r与挠度方向相反,产生自动对中现象,这是柔性轴的特征。
图1 惯性涡动由此可知,涡动振幅oH与力P、角度ψ及接触介质有关。
液力涡动又称流体涡动,它是由于轴颈与轴瓦之间润滑油层中液动力所强迫造成的涡动。
图2是一经过理想动平衡(S=H)轴的径向轴颈,且有旋转速度n W。
若使该轴无任何横向力作用,那么轴颈位于轴承的中心位置即(H=o)。
当由于某种原因,轴颈中心作以半径为oH的圆旋转时,润滑层内产生不对称的压力场,它的合力在图中由R Q表示,同时,在轴颈上作用有与oH方向相同的离心力P。
此两个力合成为力Q,力Q可分解为与轴的弹性挠曲力平衡的力Q r和不平衡力Q t,此力将引起流体涡动。
图2 液力涡动原理对于流体涡动只能发生在流体润滑状态,且为弹性转子系统的不稳定时刻。
对于柔性轴工作的稳定性条件已由Hori推导出[1],他区分了两种流体涡动,即小的油膜振荡和大的油膜振荡。
对于最简单的涡动速度分析,设轴颈中心的涡动转速为Ω,润滑剂为常密度,若不考虑压力梯度的影响,根据流量平衡条件,由图3c可得,进入控制空间单位轴承宽度的体积流量和离开控制空间的体积流量分别为(Rωj-eΩ)(c+e)/2和(Rωj+eΩ)(c-e)/2,此二者之差应该等于轴颈移动造成的控制空间的容积增长率,即2ReΩ,则得图3 轴颈的涡动倾向(1)式中,R为轴承半径;e为偏心距;c为半径间隙。
从而解得Ω=ωj/(2+c/R)≈ωj/2 (2)由此,当轴颈偏离平衡位置,单从流量来考虑,涡动转速为自转转速的一半或稍小。
偏心率(偏心距与半径间隙之比)越小,上式越精确。
在偏心率大时,压力梯度的影响越来越显著,上式就不能用了。
由于偏心率增大有利于轴承的稳定性,所以上式在一般计算中是不能完全反映问题的。
2 油膜振荡机理研究的发展油膜振荡是由于滑动轴承中的油膜作用而引起的旋转轴的自激振荡,可产生与转轴达到临界转速时同等的振幅或更加激烈。
油膜振荡不仅会导致高速旋转机械的故障,有时也是造成轴承或整台机组破坏的原因。
在日本和中国都有过由于油膜振荡而出现机组破坏的实例。
油膜振荡从1925年由Newkirk B L和Taylor H D首先提出以来[2],经过了从认识到深化理解的长期发展过程,到目前已经基本成熟,能较深刻地揭示油膜振荡的本质。
1925年Newkirk和Taylor发现了由用滑动轴承支持的旋转轴,当转速达到转轴的临界转速的两倍以上时,基于某种边界条件,引起转轴的激烈甩动。
停止给油,转子甩动即停止,恢复给油,甩动即恢复。
从而发现甩动的原因来自于油膜。
且论述如下:(1) 油膜振荡发生于转轴两倍临界转速以上,其甩动方向与转轴旋转方向一致;(2) 油膜振荡的甩转角速度与转轴旋转角速度无关,约等于转轴临界转速时的角速度;(3) 油膜振荡与转轴在临界转速下产生的振动不同,一旦发生,转速增加也不会停止;(4) 缩短轴承宽度则不易发生油膜振荡;(5) 轴承的支承若做成自动调心式,在安装轴的两端轴承时使其有少量的不同心度,对于防止油膜振荡也有一定的作用。
1956年Newkirk B L和Lewis J F发表论文称,在工作转速达5倍临界转速时尚未产生油膜振荡。
同年,Pinkus O提到,在大量实验里证实了油膜振荡的“惯性效应”,即当没有油膜振荡时,即使提高转轴的转速也可维持原状;而当产生油膜振荡时,虽然降低转速,油膜振荡仍有继续下去的倾向。
同时,有人提出,当转轴工作转速低于不稳定转速时,若加以冲击也可能会出现激烈的油膜振荡现象。
在发生油膜振荡后对振幅的变化,Newkirk和Taylor则指出,油膜振荡一旦发生,伴随转轴转速的上升将愈为激烈,以后似乎没有稳定区;但也有人说,提高转速后振幅会减小。
日本油膜振荡学者堀幸夫在实验中也有类似的发现。
同时人们还提到在某些情况下转轴的稳定与不稳定状态被一段短暂的振荡所分开。
润滑油的粘度系数(或油温)对油膜振荡的影响也成为争论的问题。
多数学者认为油温愈高也即粘性愈小愈不容易引起油膜振荡,但也有相反意见。
Pinkus还特别提出温热的油和冷油对油膜振荡都具有稳定作用。
姚福生院士在东方汽轮机厂工作期间,处理汽轮机油膜振荡问题及在大量实验的基础上也观察到上述结果,对这些油膜振荡稍加处理就会立即消失,采用了提高轴承进油温度、改变轴承垂直和水平间隙、改变轴承宽度、改变轴承形式等手段。
总之,油膜振荡的产生与多种因素有关,概括起来如下[3~8]:(1) 轴系结构设计它影响转轴的刚度,也即影响临界转速;同时也影响转轴的载荷分布及轴的挠曲程度;转轴在工作过程中偏心率的大小将影响其临界转速,同时也影响轴承的工作条件,即轴承的工作性能。
(2) 轴承负载大型汽轮发电机组轴系安装时,是在转子不旋转的状态下,按制造厂家提供的挠度曲线和规范,调整轴承中心位置找正的。
但在运行过程中,由于机组的热变形,转子在油膜中浮起,以及真空度、地基不均匀下沉等因素的影响,轴系对中情况将发生变化,即标高产生起伏。
因此,在热态下,机组轴承的负荷将重新分配,有可能使个别轴承过载,出现温升过高和烧瓦,个别轴承的负荷偏低,产生油膜振荡或其它异常振动。
(3) 轴承进油温度油温对油膜振荡有很大的影响,当其它条件不变时,油温高则油的粘度低,最小油膜厚度变小,轴承的工作点、油膜刚度和阻尼系数都将发生变化。
一般情况下,油温高,最小油膜厚度小,偏心率大,轴承不易产生油膜振荡,即稳定转速提高的缘故。
(4) 轴瓦间隙轴瓦间隙影响轴承的稳定性,主要是由于影响轴承运行的最小间隙,最小间隙是稳定工作的重要依据。
最小间隙越小,轴承工作越稳定。
(5) 其它因素根据国内外文献及实验说明,轴承紧力、支承座、基础的刚度等对轴系稳定性也有影响。
定性地说,支承刚度、阻尼增大稳定性提高,特别是增大阻尼对提高稳定性有明显的作用,但目前还缺乏实验数据的支持。
3 油膜振荡的判别油膜振荡的性质与不平衡振动有本质的区别,油膜振荡现象有以下特征:(1) 油膜振荡在转子一阶临界转速的两倍以上转速时发生,一旦发生振荡,振幅急剧加大,即使再提高转速,振幅也不会下降,如图4所示。
强烈振动有时会导致烧瓦和轴系的破坏。
图4 油膜振荡(2) 油膜振荡时,轴心涡动频率通常为转子一阶固有频率,振型为一阶振型。
(3) 油膜振荡时,轴心涡动方向和转子旋转方向相同,为正向涡动。
而干摩擦引起的自激为反向涡动。
(4) 转速在一阶临界转速的两倍以下时可能产生半速涡动,涡动频率为转速的一半。
半速涡动的振幅较小,若再提高转速则会发展成为油膜振荡,如图5所示。
半速涡动通常在高速轻载轴承情况下发生。
图5 半速涡动油膜振荡(5) 油膜振荡具有惯性效应,升速时产生油膜振荡的转速与降速时油膜振荡消失的转速不相同,如图6所示。
图6 油膜振荡的惯性效应(6) 油膜振荡开始发生但还未发展为剧烈的自激振动时,轴心轨迹图形呈现紊乱状态,在一般情况下,正常工作时,轴心也是按一定的轨迹运动,其轨迹在小范围内变化。
当油膜振荡发生时,振动逐步剧烈,轨迹的变化范围剧烈增大,且呈紊乱状态。
(7) 油膜振荡时转轴将承受较大的交变应力,由油膜振荡产生的交变应力的频率是转轴旋转频率与轴心涡动频率的差。
油膜振荡可根据上述特征进行判断。
在实际中,以计算临界频率为依据,测量转轴的转速及振动或轴心轨迹,也可以测量轴上的作用力的变化,判断振动和轴心轨迹,预防油膜振荡发生,保证机器的正常运转。
由此可知,防止油膜振荡的措施可从以下几方面着手,即①增大轴承载荷;②降低润滑油粘度;③改变轴承间隙;④改变轴承的结构形式等。
4 结论以上对油膜涡动与油膜振荡的区别,在概念上的异同及它们的发展过程等作了论述。
由上可知,油膜振荡对机电设备的危害极大,是滑动轴承实际应用中必须考虑的问题,同时,油膜振荡的影响因素又很多,在机械的运转过程中,根据油膜振荡产生的现象,应通过测量振动和轴心轨迹来预测油膜振荡产生的可能性,以保证机器的正常运行。
SFCB如何提高旋转机械的稳定性Donald E. Bently Founder, Chairman, and CEOBently Nevada Corporation, and PresidentBently Rotor Dynamics Research Corporation e-mail: don@我们新的流体伺服可控轴承(ServoFluid?Control Bearing (SFCB))可以从根本上消除流体涡动。
油膜振荡及其它一些常见的失稳故障,只能部分地通过流体伺服可控轴承( SFCB)进行解决。
然庵种岢卸杂谙饫嗟氖裙收希喽杂诔9娴募际酰匀痪哂泻艽蟮挠攀疲以谝恍┯τ贸『现校梢蕴峁┮恢挚尚械慕饩龇桨浮N颐且丫诓煌幕魃希油暾难顾趸榈阶邮匝樘哉庵种岢邢卸驼竦吹男Ч辛耸匝楹脱菔荆馄恼麓蛹际跎虾褪隙哉庵衷鲅怪岢屑际跞绾翁岣呶榷ㄐ越辛司返乃得鳌1疚闹忻枋鑫榷ㄐ缘南喙毓绞怯? Don Bently 和 Agnes Muszynska提出并完善的。
流体伺服可控轴承(SFCB)工作的两个原理为了能理解SFCB如何工作,我们最好先看一下常规的流体动压和静压轴承是如何工作的。