管桁架工程施工方案
管桁架工程施工方案

管桁架工程施工方案一、项目概述管桁架工程是一种常见的建筑工程类型,其主要用途是在建筑物内部或外部支撑和连接管道、电缆、通讯线路等设备。
本文档将详细介绍管桁架工程的施工方案,包括施工前的准备工作、施工过程中的安全措施、施工后的验收和维护等内容。
二、施工前的准备工作1. 现场勘查:施工前需对现场进行详细勘查,了解工地环境、土壤情况、交通条件等,以确定施工方案的可行性。
2. 设计方案审核:审核设计方案,确保设计符合工程要求,并与设计单位进行沟通,明确施工细节和要求。
3. 材料采购:根据设计方案确定所需材料种类和数量,向合格的供应商采购材料,并保证材料质量合格。
4. 质量验收:对采购的材料进行验收,确保其符合国家相应标准,并做好验收记录。
三、施工过程中的安全措施1. 施工区域划分:在施工现场根据实际情况划定施工区域,并设置明显的警示标识,确保施工区域与周边区域分隔开,避免发生人员和设备的交叉作业。
2. 安全培训:施工前需对所有参与施工的人员进行安全培训,包括作业规范、个人防护措施等,提高员工的安全意识。
3. 安全防护设施:在施工现场设置合理的安全防护设施,如安全网、护栏等,保障施工人员的安全。
4. 现场监测:安排专人进行现场监测,及时处理施工中的安全隐患,确保施工安全。
四、施工过程1. 基础施工:首先进行管桁架工程的基础施工,包括挖掘基坑、浇筑混凝土等环节,确保基础稳固。
2. 框架安装:根据设计方案和施工图纸进行管桁架的组装,保证各个部件的连接稳固可靠。
3. 管道布置:根据要求进行管道的布置,保证管道的连通性和功能性。
4. 线路铺设:根据设计要求进行电缆和通讯线路的铺设,确保布线合理、整洁。
5. 焊接和固定:对于需要焊接的部分,采用合适的焊接工艺进行焊接,并在焊接完成后进行加固固定,保证连接牢固。
6. 质量验收:在施工过程中进行质量验收,确保工程质量符合设计要求。
五、施工后的验收和维护1. 施工完成后,对整个管桁架工程进行验收,保证工程质量符合设计要求。
管桁架安装吊装施工方案
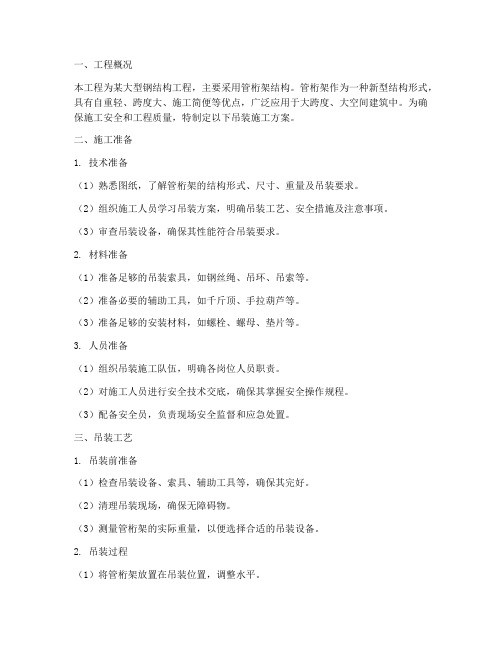
一、工程概况本工程为某大型钢结构工程,主要采用管桁架结构。
管桁架作为一种新型结构形式,具有自重轻、跨度大、施工简便等优点,广泛应用于大跨度、大空间建筑中。
为确保施工安全和工程质量,特制定以下吊装施工方案。
二、施工准备1. 技术准备(1)熟悉图纸,了解管桁架的结构形式、尺寸、重量及吊装要求。
(2)组织施工人员学习吊装方案,明确吊装工艺、安全措施及注意事项。
(3)审查吊装设备,确保其性能符合吊装要求。
2. 材料准备(1)准备足够的吊装索具,如钢丝绳、吊环、吊索等。
(2)准备必要的辅助工具,如千斤顶、手拉葫芦等。
(3)准备足够的安装材料,如螺栓、螺母、垫片等。
3. 人员准备(1)组织吊装施工队伍,明确各岗位人员职责。
(2)对施工人员进行安全技术交底,确保其掌握安全操作规程。
(3)配备安全员,负责现场安全监督和应急处置。
三、吊装工艺1. 吊装前准备(1)检查吊装设备、索具、辅助工具等,确保其完好。
(2)清理吊装现场,确保无障碍物。
(3)测量管桁架的实际重量,以便选择合适的吊装设备。
2. 吊装过程(1)将管桁架放置在吊装位置,调整水平。
(2)连接吊装索具,确保其牢固可靠。
(3)使用吊装设备将管桁架吊起,缓慢移动至指定位置。
(4)在吊装过程中,密切关注管桁架的变形和倾斜情况,及时调整。
(5)管桁架就位后,进行临时固定。
3. 吊装后处理(1)检查管桁架的变形和倾斜情况,确保其符合要求。
(2)拆除临时固定装置,确保管桁架稳定。
(3)对吊装索具进行清洗、保养。
四、安全措施1. 严格执行安全操作规程,确保吊装过程安全。
2. 吊装前对施工人员进行安全技术交底,提高安全意识。
3. 设立安全警示标志,提醒施工人员注意安全。
4. 配备安全员,负责现场安全监督和应急处置。
5. 定期检查吊装设备、索具等,确保其完好。
五、总结本施工方案针对管桁架安装吊装过程,从施工准备、吊装工艺、安全措施等方面进行了详细说明。
在实际施工过程中,应根据现场情况进行调整,确保施工安全和工程质量。
管桁架工程施工方案

管桁架工程施工方案一、工程概况1.1 项目名称:管桁架工程施工方案1.2 项目地址:XX省XX市XX县1.3 施工单位:XX建设工程有限公司1.4 设计单位:XX设计院1.5 施工内容:管桁架的设计、加工、安装等相关工作1.6 工程量及工程周期:总长2000m,预计工期120天二、施工原则2.1 安全第一:严格遵守相关安全规定,保障施工人员的人身安全。
2.2 质量为本:严格执行相关标准,确保施工质量符合要求。
2.3 绿色施工:在施工过程中尽量减少对环境的影响,积极推广绿色施工。
2.4 精细管理:加强组织协调,优化施工流程,确保工程顺利进行。
三、技术方案3.1 材料选择:选用优质钢材,确保管桁架的强度和稳定性。
3.2 设计方案:严格按照设计院的设计方案进行施工,做到无误差、无偏差。
3.3 施工工艺:采用模块化施工方式,加工和安装分段进行,以确保工程进度和质量。
四、施工组织4.1 组织架构:由施工单位建立施工组织架构,明确各岗位的职责和权利。
4.2 人员配备:按照工程量和工期合理配置施工人员,确保施工进度。
4.3 安全管理:设立专门的安全管理岗位,落实安全管理责任制,严格执行施工安全措施。
五、施工流程5.1 加工工序:首先进行管材的切割、焊接和加工,确保尺寸精准。
5.2 安装工序:根据设计方案进行桁架的分段安装,合理安排施工顺序。
六、质量管理6.1 设备检测:使用专业设备进行施工质量检测,确保材料和工程质量。
6.2 工艺控制:制定详细的工艺流程和控制点,确保每个环节的质量。
6.3 质量验收:在施工完成后进行专业的验收,确保工程符合相关标准和要求。
七、安全管理7.1 安全教育:对施工人员进行专业的安全教育和培训,提高安全意识。
7.2 安全防护:设置临时围挡和防护栏,防止高空坠物和其他事故。
7.3 应急预案:建立完善的应急预案和逃生通道,确保施工中的安全。
八、环境保护8.1 垃圾处理:加强施工现场的垃圾清理和分类处理,减少对环境的影响。
管桁架工程施工方案
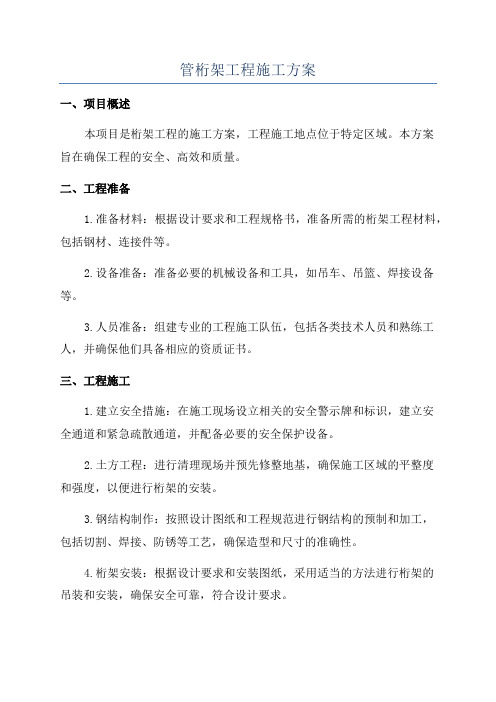
管桁架工程施工方案一、项目概述本项目是桁架工程的施工方案,工程施工地点位于特定区域。
本方案旨在确保工程的安全、高效和质量。
二、工程准备1.准备材料:根据设计要求和工程规格书,准备所需的桁架工程材料,包括钢材、连接件等。
2.设备准备:准备必要的机械设备和工具,如吊车、吊篮、焊接设备等。
3.人员准备:组建专业的工程施工队伍,包括各类技术人员和熟练工人,并确保他们具备相应的资质证书。
三、工程施工1.建立安全措施:在施工现场设立相关的安全警示牌和标识,建立安全通道和紧急疏散通道,并配备必要的安全保护设备。
2.土方工程:进行清理现场并预先修整地基,确保施工区域的平整度和强度,以便进行桁架的安装。
3.钢结构制作:按照设计图纸和工程规范进行钢结构的预制和加工,包括切割、焊接、防锈等工艺,确保造型和尺寸的准确性。
4.桁架安装:根据设计要求和安装图纸,采用适当的方法进行桁架的吊装和安装,确保安全可靠,符合设计要求。
5.桁架连接:进行桁架的连接和固定,采用合适的连接件和焊接工艺,确保连接牢固、稳定,并满足工程要求。
6.桁架调整:进行桁架的调整和校正,确保各节点的平直度和垂直度,使桁架的受力均匀和合理。
7.防腐处理:对已安装好的桁架进行防腐处理,采用合适的涂料或防腐剂,以延长桁架的使用寿命。
8.清理和整理:工程施工结束后,对施工现场进行清理和整理,包括清理垃圾、归还机械设备等。
四、质量控制1.材料检验:对采购的桁架材料进行必要的检验和试验,确保材料的质量和性能符合设计要求。
2.工艺控制:施工过程中严格按照工艺要求进行操作,确保焊缝的质量和连接的可靠性。
3.质量检测:对已安装好的桁架进行质量检测,包括尺寸、平直度、垂直度等,确保桁架的质量和几何参数符合要求。
4.环境保护:施工过程中注意环境保护,确保不产生污染物和噪音,减少对周边环境的影响。
五、安全措施1.安全检查:对施工现场进行定期安全检查和隐患排查,及时采取措施消除安全隐患。
中卫管桁架结构工程施工方案
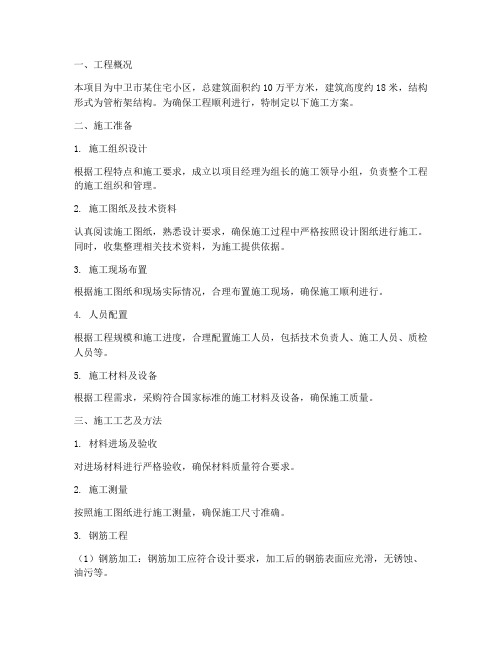
一、工程概况本项目为中卫市某住宅小区,总建筑面积约10万平方米,建筑高度约18米,结构形式为管桁架结构。
为确保工程顺利进行,特制定以下施工方案。
二、施工准备1. 施工组织设计根据工程特点和施工要求,成立以项目经理为组长的施工领导小组,负责整个工程的施工组织和管理。
2. 施工图纸及技术资料认真阅读施工图纸,熟悉设计要求,确保施工过程中严格按照设计图纸进行施工。
同时,收集整理相关技术资料,为施工提供依据。
3. 施工现场布置根据施工图纸和现场实际情况,合理布置施工现场,确保施工顺利进行。
4. 人员配置根据工程规模和施工进度,合理配置施工人员,包括技术负责人、施工人员、质检人员等。
5. 施工材料及设备根据工程需求,采购符合国家标准的施工材料及设备,确保施工质量。
三、施工工艺及方法1. 材料进场及验收对进场材料进行严格验收,确保材料质量符合要求。
2. 施工测量按照施工图纸进行施工测量,确保施工尺寸准确。
3. 钢筋工程(1)钢筋加工:钢筋加工应符合设计要求,加工后的钢筋表面应光滑,无锈蚀、油污等。
(2)钢筋绑扎:钢筋绑扎应牢固,绑扎间距符合规范要求。
4. 管桁架安装(1)管桁架制作:管桁架制作应严格按照设计要求,确保尺寸准确。
(2)管桁架运输:管桁架运输过程中,应采取有效措施防止变形。
(3)管桁架安装:安装前,对安装位置进行复核,确保安装准确。
安装过程中,采取分段吊装,逐步调整到位。
5. 模板工程(1)模板制作:模板制作应符合设计要求,确保模板尺寸准确、平整。
(2)模板安装:模板安装应牢固,接缝严密,防止漏浆。
6. 钢筋混凝土工程(1)混凝土搅拌:混凝土搅拌应符合设计要求,确保混凝土强度和耐久性。
(2)混凝土浇筑:混凝土浇筑应分层进行,确保混凝土密实。
四、质量控制及验收1. 施工过程中,严格执行国家及行业相关标准和规范。
2. 加强施工过程中的质量控制,确保施工质量。
3. 工程验收时,按照设计要求和验收标准进行验收,确保工程质量。
崇左管桁架工程施工(3篇)

第1篇随着我国经济的快速发展,城市化进程不断加快,建筑行业对新型建筑结构的需求日益增长。
管桁架作为一种新型建筑结构,以其自重轻、施工速度快、抗震性能好等优点,在建筑领域得到了广泛应用。
在崇左地区,管桁架工程已逐渐成为建筑行业的新宠。
本文将简要介绍崇左管桁架工程施工的相关内容。
一、工程概况崇左管桁架工程位于崇左市某住宅小区,总建筑面积约10万平方米。
该工程采用预制管桁架结构,建筑高度为18层,主体结构为框架-管桁架体系。
工程于2021年3月开工,预计2022年6月竣工。
二、施工准备1. 施工组织设计:根据工程特点,编制详细的施工组织设计,明确施工流程、施工工艺、施工质量要求等。
2. 材料准备:提前采购预制管桁架、钢筋、混凝土等主要材料,确保材料质量符合设计要求。
3. 机械设备准备:配置吊车、切割机、焊接机、测量仪器等机械设备,确保施工顺利进行。
4. 人员培训:对施工人员进行技术培训,提高施工人员的操作技能和安全意识。
三、施工工艺1. 预制管桁架安装:采用现场拼装的方式,将预制管桁架运输至施工现场,按照设计要求进行拼装。
拼装过程中,严格控制拼装精度,确保桁架整体稳定性。
2. 钢筋绑扎:在桁架拼装完成后,进行钢筋绑扎。
钢筋绑扎应符合设计要求,确保钢筋位置准确、间距均匀。
3. 混凝土浇筑:混凝土浇筑前,对模板进行清理、涂刷脱模剂,确保模板表面光滑。
混凝土浇筑过程中,采用分层浇筑、振捣密实的方法,确保混凝土质量。
4. 抗震加固:根据设计要求,对管桁架进行抗震加固处理,提高建筑物的抗震性能。
四、质量控制1. 材料质量:严格控制预制管桁架、钢筋、混凝土等材料的质量,确保材料符合设计要求。
2. 施工过程:严格按照施工工艺进行施工,确保施工质量。
3. 验收检测:施工过程中,定期进行验收检测,确保工程质量符合设计要求。
4. 成品保护:对已完成的构件进行成品保护,防止损坏。
五、安全措施1. 施工现场设置安全警示标志,提醒施工人员注意安全。
管桁架工程施工方案
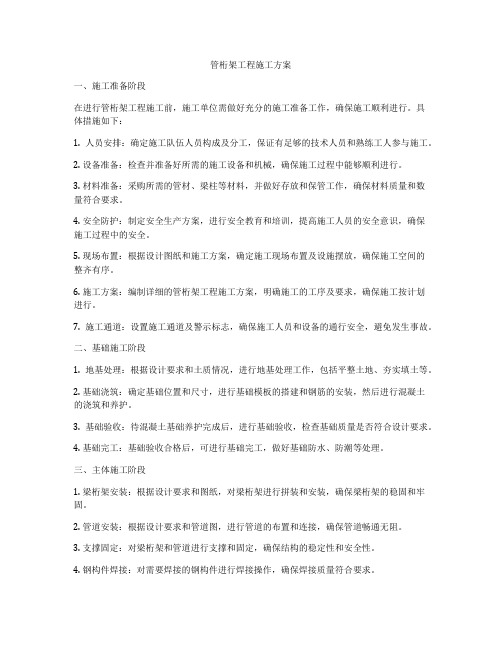
管桁架工程施工方案一、施工准备阶段在进行管桁架工程施工前,施工单位需做好充分的施工准备工作,确保施工顺利进行。
具体措施如下:1. 人员安排:确定施工队伍人员构成及分工,保证有足够的技术人员和熟练工人参与施工。
2. 设备准备:检查并准备好所需的施工设备和机械,确保施工过程中能够顺利进行。
3. 材料准备:采购所需的管材、梁柱等材料,并做好存放和保管工作,确保材料质量和数量符合要求。
4. 安全防护:制定安全生产方案,进行安全教育和培训,提高施工人员的安全意识,确保施工过程中的安全。
5. 现场布置:根据设计图纸和施工方案,确定施工现场布置及设施摆放,确保施工空间的整齐有序。
6. 施工方案:编制详细的管桁架工程施工方案,明确施工的工序及要求,确保施工按计划进行。
7. 施工通道:设置施工通道及警示标志,确保施工人员和设备的通行安全,避免发生事故。
二、基础施工阶段1. 地基处理:根据设计要求和土质情况,进行地基处理工作,包括平整土地、夯实填土等。
2. 基础浇筑:确定基础位置和尺寸,进行基础模板的搭建和钢筋的安装,然后进行混凝土的浇筑和养护。
3. 基础验收:待混凝土基础养护完成后,进行基础验收,检查基础质量是否符合设计要求。
4. 基础完工:基础验收合格后,可进行基础完工,做好基础防水、防潮等处理。
三、主体施工阶段1. 梁桁架安装:根据设计要求和图纸,对梁桁架进行拼装和安装,确保梁桁架的稳固和牢固。
2. 管道安装:根据设计要求和管道图,进行管道的布置和连接,确保管道畅通无阻。
3. 支撑固定:对梁桁架和管道进行支撑和固定,确保结构的稳定性和安全性。
4. 钢构件焊接:对需要焊接的钢构件进行焊接操作,确保焊接质量符合要求。
5. 设备安装:根据设计要求和设备安装图纸,对设备进行安装和调试,确保设备使用正常。
6. 防腐处理:对梁桁架和管道进行防腐处理,延长结构的使用寿命。
四、收尾阶段1. 施工清理:将施工现场进行清理整理,清除杂物和垃圾,确保施工现场的整洁。
柳州管桁架工程施工(3篇)

第1篇一、工程背景柳州市维义大桥位于市区北外环线上,是连接柳西、柳北片区的重要通道。
该桥为108米288米108米钢桁架拱桥,主桁由两片钢桁架拱组成,桥桁架部分最大板厚50mm,用钢量约为1万7千多吨。
为确保工程质量,我国中铁宝桥公司中标承担了该桥的管桁架工程施工。
二、施工方案1. 施工准备(1)技术准备:对施工图纸进行全面审查,熟悉设计要求,明确施工工艺和施工流程。
(2)材料准备:根据施工图纸和施工方案,采购所需的钢材、焊接材料、防腐材料等。
(3)设备准备:准备足够的起重设备、焊接设备、检测设备等。
2. 施工工艺(1)钢桁架拱制作:在工厂内进行钢桁架拱的制作,确保制作精度和质量。
(2)焊接:采用焊接技术将钢桁架拱的各个部件连接在一起,确保焊接质量。
(3)防腐处理:对焊接完成的钢桁架拱进行防腐处理,提高其使用寿命。
(4)运输:将制作完成的钢桁架拱运输至施工现场。
(5)安装:采用起重设备将钢桁架拱吊装至设计位置,确保安装精度。
3. 施工流程(1)现场施工准备:搭建临时设施,包括施工场地、材料堆场、施工人员宿舍等。
(2)钢桁架拱制作:在工厂内进行钢桁架拱的制作,确保制作精度和质量。
(3)焊接:对钢桁架拱进行焊接,确保焊接质量。
(4)防腐处理:对焊接完成的钢桁架拱进行防腐处理。
(5)运输:将制作完成的钢桁架拱运输至施工现场。
(6)安装:采用起重设备将钢桁架拱吊装至设计位置。
(7)验收:对安装完成的钢桁架拱进行验收,确保工程质量。
三、施工质量控制1. 材料质量控制:对钢材、焊接材料、防腐材料等进行严格检验,确保材料质量。
2. 施工过程控制:对焊接、防腐、运输、安装等施工过程进行严格把控,确保施工质量。
3. 质量检测:对钢桁架拱进行定期检测,确保其符合设计要求。
四、施工安全管理1. 人员安全:加强施工人员的安全教育,提高安全意识。
2. 设备安全:定期对起重设备、焊接设备等进行检查、维护,确保设备安全。
3. 施工现场安全:做好施工现场的安全防护措施,防止安全事故发生。
管桁架吊装施工方案(3篇)
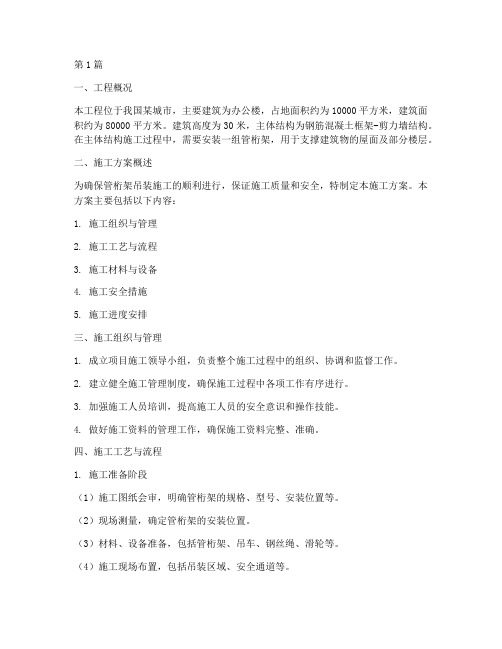
第1篇一、工程概况本工程位于我国某城市,主要建筑为办公楼,占地面积约为10000平方米,建筑面积约为80000平方米。
建筑高度为30米,主体结构为钢筋混凝土框架-剪力墙结构。
在主体结构施工过程中,需要安装一组管桁架,用于支撑建筑物的屋面及部分楼层。
二、施工方案概述为确保管桁架吊装施工的顺利进行,保证施工质量和安全,特制定本施工方案。
本方案主要包括以下内容:1. 施工组织与管理2. 施工工艺与流程3. 施工材料与设备4. 施工安全措施5. 施工进度安排三、施工组织与管理1. 成立项目施工领导小组,负责整个施工过程中的组织、协调和监督工作。
2. 建立健全施工管理制度,确保施工过程中各项工作有序进行。
3. 加强施工人员培训,提高施工人员的安全意识和操作技能。
4. 做好施工资料的管理工作,确保施工资料完整、准确。
四、施工工艺与流程1. 施工准备阶段(1)施工图纸会审,明确管桁架的规格、型号、安装位置等。
(2)现场测量,确定管桁架的安装位置。
(3)材料、设备准备,包括管桁架、吊车、钢丝绳、滑轮等。
(4)施工现场布置,包括吊装区域、安全通道等。
2. 管桁架吊装阶段(1)吊车就位,确保吊车位置满足吊装要求。
(2)钢丝绳连接,将管桁架与吊车连接。
(3)管桁架吊装,缓慢起吊,确保管桁架平稳移动。
(4)管桁架就位,调整位置,确保管桁架与预埋件对准。
(5)管桁架固定,采用螺栓或焊接方式将管桁架固定在预埋件上。
3. 施工验收阶段(1)对管桁架的安装位置、高度、倾斜度等进行检查。
(2)检查管桁架的连接情况,确保连接牢固。
(3)对管桁架进行外观检查,确保无变形、裂纹等现象。
五、施工材料与设备1. 材料要求(1)管桁架:采用Q345B钢材,厚度符合设计要求。
(2)预埋件:采用Q235B钢材,厚度符合设计要求。
(3)螺栓、焊接材料:符合国家标准。
2. 设备要求(1)吊车:选用符合吊装要求的吊车,如汽车吊、履带吊等。
(2)钢丝绳、滑轮:选用符合吊装要求的钢丝绳、滑轮。
大型管桁架工程施工方案
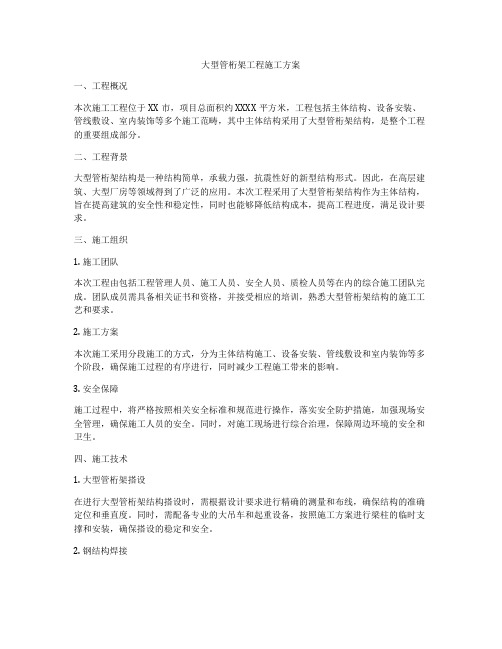
大型管桁架工程施工方案一、工程概况本次施工工程位于XX市,项目总面积约XXXX平方米,工程包括主体结构、设备安装、管线敷设、室内装饰等多个施工范畴,其中主体结构采用了大型管桁架结构,是整个工程的重要组成部分。
二、工程背景大型管桁架结构是一种结构简单,承载力强,抗震性好的新型结构形式。
因此,在高层建筑、大型厂房等领域得到了广泛的应用。
本次工程采用了大型管桁架结构作为主体结构,旨在提高建筑的安全性和稳定性,同时也能够降低结构成本,提高工程进度,满足设计要求。
三、施工组织1. 施工团队本次工程由包括工程管理人员、施工人员、安全人员、质检人员等在内的综合施工团队完成。
团队成员需具备相关证书和资格,并接受相应的培训,熟悉大型管桁架结构的施工工艺和要求。
2. 施工方案本次施工采用分段施工的方式,分为主体结构施工、设备安装、管线敷设和室内装饰等多个阶段,确保施工过程的有序进行,同时减少工程施工带来的影响。
3. 安全保障施工过程中,将严格按照相关安全标准和规范进行操作,落实安全防护措施,加强现场安全管理,确保施工人员的安全。
同时,对施工现场进行综合治理,保障周边环境的安全和卫生。
四、施工技术1. 大型管桁架搭设在进行大型管桁架结构搭设时,需根据设计要求进行精确的测量和布线,确保结构的准确定位和垂直度。
同时,需配备专业的大吊车和起重设备,按照施工方案进行梁柱的临时支撑和安装,确保搭设的稳定和安全。
2. 钢结构焊接大型管桁架结构采用了大量的钢结构,施工过程中需要进行大量的焊接作业。
因此,对焊工的技术要求较高,需要熟练掌握焊接技术,确保焊缝的质量和牢固度。
3. 混凝土浇筑对于混凝土的浇筑工艺,需精确控制浇筑的厚度和施工的时间,同时注意混凝土的养护和保温,确保混凝土的质量和强度。
4. 管线敷设在管线敷设过程中,需要精确布置管道位置,确保管线的连通和导向,同时要加强对管线的防腐处理和保护,确保管线的质量和使用寿命。
五、施工质量控制1. 施工验收每个工程节点完成后,需进行施工验收,确保工程质量符合设计要求。
预应力管桁架安装施工方案
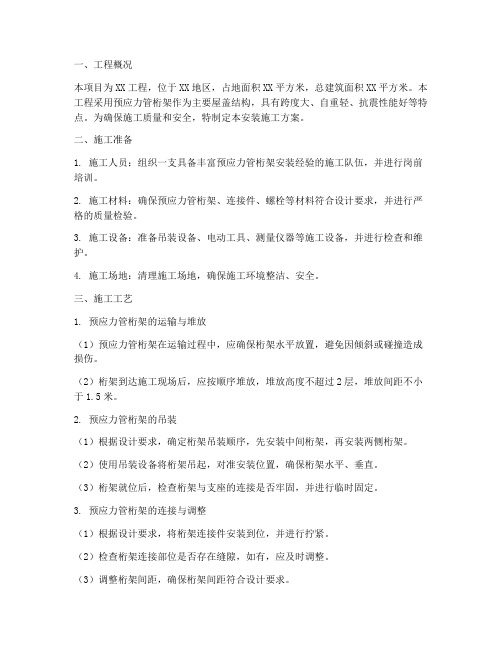
一、工程概况本项目为XX工程,位于XX地区,占地面积XX平方米,总建筑面积XX平方米。
本工程采用预应力管桁架作为主要屋盖结构,具有跨度大、自重轻、抗震性能好等特点。
为确保施工质量和安全,特制定本安装施工方案。
二、施工准备1. 施工人员:组织一支具备丰富预应力管桁架安装经验的施工队伍,并进行岗前培训。
2. 施工材料:确保预应力管桁架、连接件、螺栓等材料符合设计要求,并进行严格的质量检验。
3. 施工设备:准备吊装设备、电动工具、测量仪器等施工设备,并进行检查和维护。
4. 施工场地:清理施工场地,确保施工环境整洁、安全。
三、施工工艺1. 预应力管桁架的运输与堆放(1)预应力管桁架在运输过程中,应确保桁架水平放置,避免因倾斜或碰撞造成损伤。
(2)桁架到达施工现场后,应按顺序堆放,堆放高度不超过2层,堆放间距不小于1.5米。
2. 预应力管桁架的吊装(1)根据设计要求,确定桁架吊装顺序,先安装中间桁架,再安装两侧桁架。
(2)使用吊装设备将桁架吊起,对准安装位置,确保桁架水平、垂直。
(3)桁架就位后,检查桁架与支座的连接是否牢固,并进行临时固定。
3. 预应力管桁架的连接与调整(1)根据设计要求,将桁架连接件安装到位,并进行拧紧。
(2)检查桁架连接部位是否存在缝隙,如有,应及时调整。
(3)调整桁架间距,确保桁架间距符合设计要求。
4. 预应力管桁架的加固与检查(1)在桁架安装过程中,对关键部位进行加固,确保桁架稳定。
(2)安装完成后,对桁架进行检查,确保桁架安装质量。
四、施工注意事项1. 施工过程中,严格遵守安全操作规程,确保施工安全。
2. 施工人员应佩戴安全帽、安全带等防护用品。
3. 施工设备应定期检查和维护,确保设备正常运行。
4. 施工过程中,密切关注天气变化,如遇恶劣天气,应暂停施工。
五、施工进度安排根据工程进度要求,制定详细的施工进度计划,确保预应力管桁架安装工程按时完成。
六、质量保证措施1. 严格按照设计要求和质量标准进行施工,确保施工质量。
管桁架施工方案

管桁架施工方案1. 引言管桁架施工是一种常见的建筑施工方法,适用于搭建桥梁、高架路、建筑物外部支撑结构等场景。
本文将介绍管桁架施工方案的整体流程和关键步骤,以及施工中需要注意的事项。
2. 施工前准备在进行管桁架施工前,需要进行充分的准备工作,包括施工方案设计、材料准备和人员培训等。
2.1 施工方案设计施工方案设计是管桁架施工的重要环节,它包括桁架的设计和支撑结构的安排。
设计方案需要考虑施工场地的特点、所需承重以及施工的安全性。
通常需要由经验丰富的结构工程师来负责设计施工方案,并经过相关部门的审核。
2.2 材料准备管桁架施工所需的材料主要包括钢管、连接件和支撑材料等。
在施工前需要做好材料的采购工作,确保材料的质量和数量满足施工需求。
2.3 人员培训管桁架施工需要经验丰富的施工人员进行操作,并严格遵守相关的安全规范。
在施工前需要对施工人员进行培训,包括桁架的组装和拆卸方法、安全操作规程等。
3. 施工步骤管桁架施工的步骤可以分为桁架组装、架设和拆卸三个阶段。
3.1 桁架组装桁架组装是管桁架施工的第一步,主要包括钢管的切割和连接件的安装。
首先,根据设计方案将钢管切割成相应的长度。
然后,使用连接件将钢管连接成桁架的形状。
在组装过程中需要保证连接件的牢固和桁架的整体稳定。
3.2 架设桁架组装完成后,需要将其架设到预定的位置。
在架设过程中需要使用起重设备,确保桁架的安全和准确的定位。
同时,还需要注意施工现场的安全,保证施工人员的人身安全。
3.3 拆卸在管桁架施工完成后,需要对桁架进行拆卸。
拆卸过程中需要注意安全,避免桁架倒塌或损坏其他结构。
拆卸完成后,按照要求对桁架进行清理和储存,以备后续使用。
4. 施工注意事项在管桁架施工过程中,有一些注意事项需要施工人员和相关管理人员注意。
•安全第一:施工人员必须严格遵守安全操作规程,佩戴好安全帽、安全带等个人防护设备,并配备好必要的安全警示标识。
•合理计划:施工人员需要制定合理的施工计划,合理安排人员和设备,确保施工进度和质量。
平面管桁架工程施工方案

平面管桁架工程施工方案一、工程概述本工程为一栋多层建筑的平面管桁架结构施工工程,包括钢结构的设计、制作、安装及相关配套工程。
工程地点位于XX市某某区域,总建筑面积约为XXX平方米,主要用途为办公及商业综合楼。
本施工方案旨在保证工程的顺利进行,质量符合设计要求,安全保障到位,并且尽量节约成本,提高效率。
二、施工前准备1. 施工前,项目经理要对工程图纸、设计要求、相关规范进行仔细的研究和分析,确保施工方案符合相关要求。
2. 安排专业技术员对工程现场进行勘察,并制定详细的施工方案和施工组织设计。
3. 制定施工计划书,明确工程总量、施工流程、安全防护措施及工期计划。
三、施工工艺1. 施工组织在工程施工期间,应建立健全的施工组织,确保施工人员安全施工、合理操作。
2. 材料准备对于各项所需的施工材料,要提前进行采购计划,并在施工前对材料进行检查验收,确保质量合格。
3. 基础处理首先确保施工现场的地基承载力符合设计要求,进行相关的地基处理工程。
4. 结构加工对于钢材的切割、焊接等工艺应符合相关规范及施工图纸要求,确保工件尺寸精确、焊缝牢固。
5. 架设安装在进行结构架设安装工程时,要注重工艺流程的合理性,采用合适的吊装设备,确保架设的稳定性及垂直度。
6. 防腐处理在平面管桁架的制作和安装过程中,要对其进行防腐处理,以延长其使用寿命。
7. 安全保障在整个施工过程中,要严格遵守相关安全管理规定,加强安全教育,做好安全防护工作,确保施工人员的人身安全。
四、质量管理1. 在施工现场要严格控制工艺质量,对焊缝、尺寸、平直度等进行检查,确保质量合格。
2. 对各种接头及连接方式要进行检测、试验,并做好相应的记录。
3. 在施工过程中,要定期开展质量验收,确保质量符合设计要求。
五、环境保护1. 施工现场要做到垃圾分类、减少扬尘、控制噪音,以保护环境。
2. 对废弃物料要及时清理,妥善处理。
六、工程交付1. 在工程竣工前,要对整个工程项目进行综合验收,确保工程质量合格,符合设计要求。
管桁架工程施工方案

管桁架工程施工方案桁架工程施工方案一、施工前的准备工作1. 确定施工方案:根据设计方案和施工图纸,制定详细的施工方案,包括桁架的安装顺序、施工方法和施工工艺等。
2. 确定施工人员和机械设备:根据工程规模和施工难度,确定所需的施工人员和机械设备,并做好配备。
3. 现场勘查和准备:对施工现场进行勘查,了解地形、地质和环境等情况,做好相应的准备工作。
同时,对施工现场进行平整、清理和围栏设置等工作。
二、桁架的安装1. 安装基础:根据设计要求,在施工现场进行基础的施工,包括清理地面、浇筑混凝土和安装预埋件等。
2. 装配桁架材料:根据施工方案,按照桁架的安装顺序,进行桁架材料的装配工作。
要确保桁架的连接牢固、稳定。
3. 安装吊装设备:根据工程需要,安装吊装设备,以便进行桁架的吊装和安装。
4. 吊装和安装桁架:通过吊装设备将桁架吊装到指定位置,然后钢筋工人进行连接,焊接或螺栓紧固等工作,确保桁架的稳定和牢固。
三、施工过程中的安全措施1. 安全保护措施:在施工现场设置明显的安全警示标志和围栏,限制非施工人员进入施工区域。
同时,施工人员要穿戴好安全帽、防滑鞋、安全带等个人防护装备。
2. 安全教育和培训:对施工人员进行安全教育和培训,使其了解施工过程中的安全风险和措施,并具备应急处理能力。
3. 定期检查和维护:定期检查桁架安装情况,及时发现并处理隐患,确保桁架的安全可靠。
四、施工后的清理和验收1. 清理现场:施工完成后,对施工现场进行清理工作,包括废弃物的清运和设备的归还等。
2. 验收工作:由相关部门对桁架工程进行验收,确认其符合设计要求和相关标准。
3. 缺陷处理和保养:如有桁架缺陷,要及时进行处理和修复。
同时,制定桁架的定期保养计划,对其进行保养和维护,延长使用寿命。
综上所述,桁架工程施工方案包括施工前的准备工作、桁架的安装、施工过程中的安全措施和施工后的清理和验收等内容。
通过科学的施工方案和严格的施工管理,确保桁架工程的施工质量和安全性。
钢管桁架工程施工(3篇)

第1篇一、施工准备1. 施工图纸和资料:熟悉施工图纸,了解桁架结构的设计参数、尺寸、节点连接方式等。
收集相关资料,如施工规范、技术要求等。
2. 施工队伍:组建一支具备丰富经验和专业素质的施工队伍,包括施工管理人员、技术人员、施工工人等。
3. 施工材料:准备充足的钢管、扣件、连接件等施工材料,确保施工过程中材料的供应。
4. 施工设备:配备必要的施工设备,如吊车、切割机、焊接设备、测量仪器等。
二、施工流程1. 基础施工:根据设计要求,完成基础施工,确保基础坚实、平整。
2. 支模:按照桁架结构尺寸,搭建支模,确保模板的稳定性和精度。
3. 钢管切割:根据设计尺寸,对钢管进行切割,确保切割尺寸准确。
4. 钢管焊接:将切割好的钢管进行焊接,焊接过程中注意焊接质量,确保焊缝平整、牢固。
5. 桁架组装:将焊接好的钢管按照设计要求进行组装,注意节点连接的牢固性和精度。
6. 桁架吊装:利用吊车将桁架吊装至指定位置,注意吊装过程中的安全。
7. 桁架固定:将桁架固定在支模上,确保桁架的稳定性。
8. 拆模:待桁架达到设计强度后,拆除支模,注意拆除过程中的安全。
9. 验收:对桁架结构进行验收,确保桁架的尺寸、节点连接、焊接质量等符合设计要求。
三、施工注意事项1. 施工安全:施工过程中,严格执行安全操作规程,确保施工人员的安全。
2. 质量控制:严格控制施工质量,确保桁架结构的稳定性和安全性。
3. 环境保护:施工过程中,注意环境保护,减少施工对周围环境的影响。
4. 施工进度:合理安排施工进度,确保工程按期完成。
5. 施工协调:加强与相关部门的沟通协调,确保施工顺利进行。
总之,钢管桁架工程施工是一项复杂的系统工程,需要施工队伍具备较高的技术水平和丰富的施工经验。
在施工过程中,要严格按照设计要求和安全规范进行施工,确保工程质量、安全和进度。
第2篇一、施工准备1. 技术准备:熟悉设计图纸,了解桁架结构的特点和施工要求;对施工人员进行技术交底,确保施工人员掌握施工工艺和操作规范。
管网桁架工程施工方案

管网桁架工程施工方案一、施工前准备1. 地勘与勘察在施工前,需进行地勘与勘察工作,明确管网桁架工程的具体位置、地形地貌、地质情况等,为后续施工提供基础数据。
2. 材料采购与管理根据设计要求和实际需求,采购合格的构件材料,对采购的材料进行质量验收,做好材料的储存和管理工作,保证施工过程中的材料质量和供应。
3. 现场布置与准备根据设计图纸和施工计划,对施工现场进行布置和准备,包括搭建临时工棚、设置安全警示标识、确定施工用水和电源等。
4. 安全生产措施严格执行相关安全生产法规,做好安全防护措施,包括悬挂警示标语、设置安全警示牌、制定施工安全技术措施及应急预案等。
5. 施工图纸复核对施工图纸进行复核,确保施工过程中的图纸准确无误,达到设计要求。
二、施工流程1. 土方开挖根据设计要求,进行土方开挖工作,清理土壤表面杂物,保持开挖面的平整和稳固。
2. 基础浇筑根据设计要求,进行管网桁架基础的浇筑工作,确保基础的承载能力和稳定性。
3. 构件安装采用合理的安装顺序和施工方法,进行管网桁架构件的安装工作,确保构件的位置、间距和连接牢固可靠。
4. 钢结构防腐对已安装的钢结构进行防腐处理,保证钢结构的使用寿命和安全性。
对焊接工作进行验收,确保焊缝无裂纹、错位、气孔等质量问题,达到设计要求。
6. 安全监测在施工过程中进行安全监测,包括对承重构件、支撑结构等进行监测,及时发现并解决施工中存在的安全隐患。
7. 补救措施针对施工中出现的问题和质量不符合要求的情况,立即采取补救措施,确保施工质量和安全。
8. 完工验收对施工完成的管网桁架工程进行验收,确保工程质量和安全。
三、施工注意事项1. 施工组织建立合理的施工组织架构,明确责任分工,保证施工进度和质量。
2. 施工工艺根据设计要求和相关规范,采用合理的施工工艺,保证管网桁架工程的质量和安全。
3. 施工设备选择合适的施工设备和工具,做好设备的维护和保养工作,确保施工的顺利进行。
管道桁架施工方案

管道桁架施工方案管道桁架施工方案是在建筑物或工业设施中用于支撑和保护管道系统的重要工程。
以下是一个700字的管道桁架施工方案示例。
一、项目概述本项目为某工业设施的管道系统桁架施工,总长约为3000米。
本施工方案主要包括材料采购、现场准备、桁架安装、检测验收等步骤。
二、施工准备1. 管道桁架材料采购:根据设计图纸和工程要求,采购合适的桁架材料,包括钢管、角钢、螺栓等。
2. 施工团队组建:成立施工团队,包括技术人员、工程师和施工人员等,确保人员配备齐全。
3. 现场准备:清理施工现场,确保施工区域平整,清除障碍物,并做好安全防护措施。
三、桁架安装1. 桁架定位:根据设计要求和图纸标示,确定桁架的定位点和高度。
2. 桁架组装:根据设计图纸和施工计划,将所采购的材料进行组装,包括固定螺栓、焊接等工艺。
3. 桁架安装:将组装好的桁架安装到预定位置上,使用液压千斤顶等设备进行调整和定位。
4. 桁架固定:将桁架与建筑物的结构物进行连接,采用螺栓、焊接等方式进行固定,确保稳定性和安全性。
5. 桁架调整:在安装完毕后,对桁架进行调整和整体平衡处理,保证桁架的水平度和垂直度。
四、检测验收1. 非破坏性检测:对桁架进行非破坏性检测,包括超声波检测、射线检测等,确保桁架的质量和安全性。
2. 施工质量验收:按照设计图纸和施工标准进行验收,对桁架的组装、安装、固定等进行检查,确保质量合格。
3. 安全检查:对施工现场进行安全检查,确保施工过程中无安全事故发生,并采取必要的安全措施和应急预案。
五、总结本施工方案详细描述了管道桁架的施工步骤和要求,具备各项工作的组织、安全、质量等方面的保证措施。
施工过程中,应严格按照施工方案进行操作,确保施工质量和安全。
施工过程中若发现问题,应及时调整和解决,确保项目圆满完成。
管桁架工程施工方案

管桁架工程施工方案项目介绍本文档旨在提供管桁架工程施工方案的详细说明和步骤,以确保施工过程的高效性和安全性。
管桁架工程是一种结构系统,由钢管支撑桁架构成,用于承载和支撑各种建筑物的重量。
施工方案的制定和实施是确保项目顺利进行的关键。
1. 管桁架工程施工方案概述管桁架工程施工方案的概述包括以下几个方面:1.1 工程目标明确工程的目标和要求,包括承重、稳定性、施工时间等。
1.2 施工范围明确管桁架工程的施工范围,包括桁架的类型、结构形式、尺寸等。
1.3 施工条件评估施工现场的条件,包括地形、地质、气候等,以确定合适的施工方案。
1.4 施工流程制定施工的具体流程和步骤,确保施工顺利进行。
2. 施工准备工作在正式施工之前,需要进行一系列的准备工作,包括:2.1 施工人员组织确定施工团队的组成和职责分工,确保施工人员具备相关技术和经验。
2.2 施工设备和材料准备采购和准备必要的施工设备和材料,包括钢管、螺栓、焊接设备等。
2.3 施工现场准备做好施工现场的准备工作,包括清理、平整施工区域,确保施工的顺利进行。
2.4 安全措施规划针对施工过程中的安全风险,制定相应的安全措施和预防措施,确保施工人员的安全。
3. 施工步骤在完成准备工作后,按照以下步骤进行管桁架工程的施工:3.1 地基处理根据设计要求,在施工现场进行地基处理工作,确保地基的承载力和稳定性。
3.2 桁架组装根据设计图纸和方案,将预先制作好的桁架组装起来。
组装过程中要确保各组件的连接牢固稳定。
3.3 管道安装根据设计要求,安装管道系统。
此过程应注意管道的平整度和连接质量,确保管道的功能和安全性。
3.4 螺栓连接使用适当的螺栓将桁架各部分连接在一起,确保连接牢固,以增加结构的稳定性。
3.5 焊接处理对桁架进行必要的焊接处理,确保焊接接头的强度和质量。
3.6 安全检查在施工过程中需定期进行安全检查,确保施工人员的安全。
3.7 完工验收施工完成后进行完工验收,确保管桁架工程符合设计要求和规范标准。
管网桁架工程施工方案设计

一、工程概况1. 工程名称:XXX项目管网桁架工程2. 工程地点:XXX3. 工程规模:XXX4. 工程内容:管网桁架的安装、调试及验收二、编制依据1. 国家相关法律法规及标准规范2. 项目可行性研究报告及设计文件3. 施工合同及工程量清单4. 施工图纸及施工组织设计5. 有关施工技术资料三、施工方案1. 施工工艺(1)桁架安装1)桁架构件的加工与检验:桁架构件加工前,应按设计要求进行下料、焊接、矫正、涂装等工序,并严格按照相关标准进行检验。
2)桁架构件的运输与堆放:桁架构件在运输过程中应采取防潮、防锈措施,堆放时按规格分类堆放,并做好标识。
3)桁架安装:桁架安装前,应对安装现场进行清理,确保安装环境符合要求。
桁架安装时,应按照设计图纸和施工规范进行,确保桁架安装的准确性和牢固性。
(2)管道安装1)管道加工与检验:管道加工前,应按设计要求进行下料、焊接、涂装等工序,并严格按照相关标准进行检验。
2)管道运输与堆放:管道在运输过程中应采取防潮、防锈措施,堆放时按规格分类堆放,并做好标识。
3)管道安装:管道安装时,应按照设计图纸和施工规范进行,确保管道安装的准确性和牢固性。
2. 施工顺序(1)桁架安装:先安装桁架基础,然后安装桁架主体,最后进行桁架的连接与固定。
(2)管道安装:先安装管道基础,然后安装管道主体,最后进行管道的连接与固定。
3. 施工措施(1)加强施工人员的技术培训,提高施工人员的操作技能。
(2)严格按照施工规范进行施工,确保施工质量。
(3)加强施工现场的管理,确保施工安全。
(4)做好施工记录,确保施工过程的可追溯性。
四、施工进度计划1. 施工准备阶段:10天2. 桁架安装阶段:20天3. 管道安装阶段:15天4. 调试及验收阶段:5天五、质量保证措施1. 严格执行国家及行业标准,确保施工质量。
2. 加强施工过程中的质量检查,发现问题及时整改。
3. 做好施工记录,确保施工过程可追溯。
4. 加强对施工人员的质量意识教育,提高施工人员的质量意识。
管桁架工程施工方案
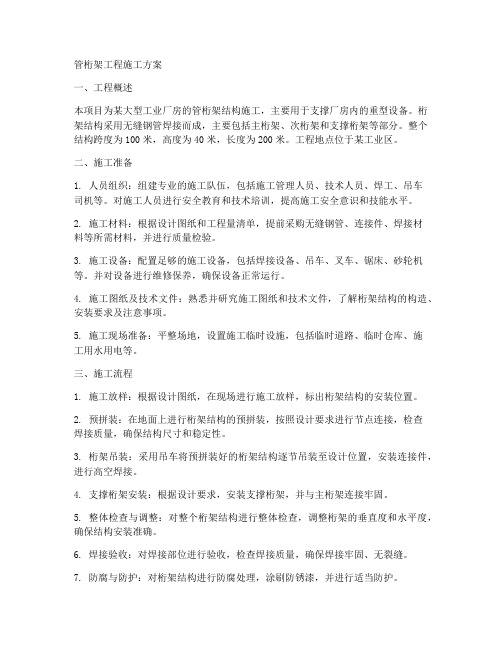
管桁架工程施工方案一、工程概述本项目为某大型工业厂房的管桁架结构施工,主要用于支撑厂房内的重型设备。
桁架结构采用无缝钢管焊接而成,主要包括主桁架、次桁架和支撑桁架等部分。
整个结构跨度为100米,高度为40米,长度为200米。
工程地点位于某工业区。
二、施工准备1. 人员组织:组建专业的施工队伍,包括施工管理人员、技术人员、焊工、吊车司机等。
对施工人员进行安全教育和技术培训,提高施工安全意识和技能水平。
2. 施工材料:根据设计图纸和工程量清单,提前采购无缝钢管、连接件、焊接材料等所需材料,并进行质量检验。
3. 施工设备:配置足够的施工设备,包括焊接设备、吊车、叉车、锯床、砂轮机等。
并对设备进行维修保养,确保设备正常运行。
4. 施工图纸及技术文件:熟悉并研究施工图纸和技术文件,了解桁架结构的构造、安装要求及注意事项。
5. 施工现场准备:平整场地,设置施工临时设施,包括临时道路、临时仓库、施工用水用电等。
三、施工流程1. 施工放样:根据设计图纸,在现场进行施工放样,标出桁架结构的安装位置。
2. 预拼装:在地面上进行桁架结构的预拼装,按照设计要求进行节点连接,检查焊接质量,确保结构尺寸和稳定性。
3. 桁架吊装:采用吊车将预拼装好的桁架结构逐节吊装至设计位置,安装连接件,进行高空焊接。
4. 支撑桁架安装:根据设计要求,安装支撑桁架,并与主桁架连接牢固。
5. 整体检查与调整:对整个桁架结构进行整体检查,调整桁架的垂直度和水平度,确保结构安装准确。
6. 焊接验收:对焊接部位进行验收,检查焊接质量,确保焊接牢固、无裂缝。
7. 防腐与防护:对桁架结构进行防腐处理,涂刷防锈漆,并进行适当防护。
四、施工注意事项1. 施工安全:加强施工现场的安全管理,严格遵守安全操作规程,确保施工人员的人身安全。
2. 质量控制:严格把控施工质量,确保桁架结构的安装尺寸、焊接质量符合设计要求。
3. 进度控制:合理安排施工进度,确保工程按时完成。
- 1、下载文档前请自行甄别文档内容的完整性,平台不提供额外的编辑、内容补充、找答案等附加服务。
- 2、"仅部分预览"的文档,不可在线预览部分如存在完整性等问题,可反馈申请退款(可完整预览的文档不适用该条件!)。
- 3、如文档侵犯您的权益,请联系客服反馈,我们会尽快为您处理(人工客服工作时间:9:00-18:30)。
工程施工程序6.1.1钢结构工程施工程序主线:6.1.2钢结构制作程序主线6.2钢结构制作方案钢构件的制作采用工厂配合现场的方式来完成,管桁架杆件在车间内完成制作,管桁架拼装在现场搭设拼装台架来完成。
管桁架支座、檩条支托、檩条、装饰架焊接H 型钢均在工厂制作完成后,运往施工现场。
屋面板拟在现场制作,将压瓦机运输到施工现场加工屋面板. 施工准备完工准备管桁架安装 管桁架钢管工厂下料 详细计划制定 管桁架现场拼装 管桁架钢管下料、抛丸除锈、底漆制作准备 檩条、屋面板制作 零、部、构、配件运输 现场拼装 檩条、屋面板制作屋面系统安装制作中应保持工厂与现场的制作联系。
6.2.1管桁架制作工艺流程:管桁架加工制作,工艺流程见图6.2.1-1。
图6.2.1-1工艺流程图退货或换货 合格 合格 不合格 不合格不合格 桁架分段单元拼装 检节点球、板和铸件加工 合格 节点焊接 检 不合格 油漆、标识弯管 检相贯线切割 管材验收 不合格 喷丸或喷砂机除锈 合格 检接管喷(刷)工厂底漆6.2.2制作准备6.2.2.1放样和号料是管桁架结构制作工艺中的第一道也是至关重要的一道工序,从事放样、号料的技术人员、操作工要求必须熟悉图纸,仔细了解技术要求,对图纸构件的尺寸和定位方向进行仔细核对。
6.2.2.2对于结构杆件空间关系复杂、连接节点呈空间定位、杆件之间或者杆件与相邻建筑体干涉较多的管桁架结构,宜采用三维实体放样,三维实体放样分为整体实体放样和节点局部实体放样,如图6.2.2-1、6.2.2-2所示。
图6.2.2-1整体实体放样图6.2.2-2节点实体放样6.2.2.3由放样图进行胎架平台制作时,胎架平台工艺补偿尺度一般不得超过2mm.6.2.2.4构件放样尺寸确定以后,为保证放样准确,应该进行自检,检查样板是否符合图纸要求,核对样板数量,并且报专职检验人员检验。
6.2.2.5下料加工之前,宜在计算机上进行电子图预拼装,当基于三维仿真实体模型条件下放样,可以直接进行数控切割。
6.2.3管桁架制作工艺细则6.2.3.1喷丸(砂)除锈1)管桁架的构件使用喷丸除锈、喷砂除锈,必须达到设计要求的除锈等级。
其除锈等级必须满足GB8923标准的规定。
2)抛丸除锈需达到Sa2.5级:完全除去黑皮、铁锈与其他外界异物,再经过吸尘机或压缩空气彻底清除灰尘与锈垢,仅允许少量点锈或丝锈存在,钢铁表面呈近似灰白色金属如Sa2.5及标准图片所示。
3)抛丸除锈要求:a.原材料、构件未经品质检验合格,不得作抛丸除锈处理。
b.钢珠规格须符合规定要求为16-40目(参见QC工程表)。
c.工作环境相对湿度超过85%,不得施工。
d.抛丸除锈后,若焊道上或其附近留有焊渣、油污等应予清除,清除部位应再作处理。
e.埋设于混凝土内的部份可不作防锈处理但应除去黑皮。
f.抛丸除锈完成后,应会同相关检验人员检验合格后,于4小时内喷涂第一道底漆。
6.2.3.2钢管对接1)管材对接,必须按JGJ81—2002标准规定进行焊接工艺评定,确定焊接材料、焊接方法以及焊接工艺参数,以保证接管的质量。
2)管材对接焊缝,通常采用加内衬管(板)(见图6.2.3.2-1)的等强度全熔透焊接以及加外套筒(见图6.2.3.2-2)和插入式的等强度角焊缝焊接,焊缝的质量等级必须达到设计图纸具体要求。
3)相同管材(同管径同壁厚)对接形式:图6.2.3.2-1 加内衬管(板)的单面焊示意图图6.2.3.2-2加外套筒角焊示意图4)不同管材对接形式分为:内径相同壁厚不同、外经相同壁厚不同和内径外经均不同三种情况。
不同管材对接,分别应采取下述措施达到管材之间的平缓过渡。
详见图6.2.3.2-3、图6.2.3.2-4、图6.2.3.2-5所示。
图6.2.3.2-3 内径相同壁厚不同管材对接示意图图6.2.3.2-4 外径相同壁厚不同管材对接示意图图图6.2.3.2-5内径外经均不同管材对接示意图5)管对接焊缝的坡口形式,在管壁厚度不大于6mm时,可用I形坡口,其坡口宽度应控制在4mm~8mm,见图5a。
在在管壁厚度大于6mm时,可用V形坡口,间隙应控制在2~5mm内,坡口角度α应根据管壁厚度和使用焊条或焊丝直径,在55°~80°内选择,见图 6.2.3.2-6内衬管一般选用壁厚4~10mm,长度40~60mm为宜。
图6.2.3.2-6 I形坡口管对接图图6.2.3.2-7 V形坡口管对接图7)管材焊接,可以采用二氧化碳气体焊和手工电弧焊。
接管焊缝应冷却到环境温度后进行外观检查,Q195、Q235、20#材质的管材应在焊接后焊缝自然冷却到环境温度;Q295、 Q345、16Mn材质的管材应在焊接完成24h后;Q390、Q420、Q460材质的管材应在焊接完成48h后,进行超声波探伤检查。
8)管材的最短接长为二倍D(管材外经)且不得小于600mm。
管材接管后,每10000mm的对接接头不得超过3个;每5000mm的对接接头不得超过2个;每3000mm的对接接头不得超过1个。
且对接接头处焊缝应与节点焊缝错开为1D并不得小于200mm的距离,如图6.2.3.2-7所示。
图6.2.3.2-7 对接接头焊缝与节点焊缝错开示意图9)相同管材(同管径同壁厚)对接,接口错边小于0.15t(t为壁厚)且小于等于3mm。
6.2.3.3相贯线加工工艺6.2.3.3.1数据计算采用先进的日本软件KASTL 以及AUTOCAD 制作拱、桁架、支撑的工作图,其中难点为中、前拱的工作图制作,制作时按设计图制成三维空间桁架,并利用计算机求出各分断处各点的三维坐标和腹杆的长度,以便现场拼装。
相贯线的加工主要采用原寸(放样)作业相贯杆件的切割采用数控管线切割机。
它能根据事先编制的放样程序在电脑控制下自动切割。
因此对相贯管件的切割来说,切割程序的编制极为重要。
使用整套的钢结构放样与材料管理集成软件(PIPE-COAST,WINCAD,WIN3D,A-BOX,NESCUT 等)并结合EXCEL 与AutoCAD 程序可实现这一目标。
具体的编制过程如下:在EXCEL 中输入节点坐标,做成一定的格式。
然后在AutoCAD 中调用自行开发的AUTOLISP 程序,生成以各节点坐标为端点的线框模型。
这是整个原寸放样工序的基础,要求输入电子表格的数据绝对正确,为此技术人员将对其进行反复检查。
线框模型建立后,转换成DXF(标准图形交换文件)文件输入WIN3D 设计软件中。
该软件用于三维结构分析的全32 位设计系统。
使用先进的计算机图形技术,使之在对空间结构的分析与计算上具有独特的优势。
经过WIN3D 计算所得的杆件角度、长度等参数输入PIPE-COAST 软件的“切割数据单”同时参照“制作要领书”,选择正确的加工设备、切割速度、坡口角度等各工艺元素。
并由专人负责对“切割数据单”做缜密、多道的检查,以保证在进入加工指令编制前所有数据正确无误。
PIPE-COAST 接受数据后,先生成单根管件的加工指令。
由于没有进行材料利用的优化处理,还不能直接交工厂加工。
为减少材料的损耗,同时进行材料的套料工作。
套料前先根据设计图将各部件的长度、数量和重量输入A-BOX 系统,由A-BOX系统生成工厂用“部材表”,同时也将所有数据输入NESCUT(材料优化软件)系统。
NESCUT 系统是一个优秀的材料优化软件,录入NESCUT 数据库的管件会自动地、以最优化的方式排于已有的原材料上。
其材料利用率可达95%以上,如果进行适当的人工干预,利用率更可达到98%。
根据NESCUT 的套料结果,将各单个管构件组合在一个原管上,组成“复合切割指令”。
即可将放样程序下发车间,分批实施切割加工。
6.2.3.3.2数控相贯线切割机切割通过试验事先确定各种规格杆件预留的焊接收缩量,在计算杆件钢管的断料长度时计入预留的焊接收缩量和钢管端面机械切削坡口的加工余量,输入程序。
依据数控数据,用HW.GGKW4-600 (六维)和LMGQ/P-A800(四维)相贯线切割机对每根管件进行相贯线的切割及相应接口处坡口的加工。
加工后的管件放入专用的贮存架上,以保护管件的加工面。
管件的检验方法为:原寸用塑料薄膜按1:1 作成检验型板,型板上标上管件的编号。
利用型板贴在相贯线管口,检验吻合程度。
管件精度偏差为正负1mm,以较高的切割精度来保证桁架的制造质量和尺寸精度。
1)杆件的下料采用数控相贯线切割机进行,其切割给位置、长度均可保证与施工详图一至。
2)其工艺顺序管件上机卡紧→数据输入→数据校对→管件切割→打坡口、清理切割面3)相贯线的切割,必须采用专用数控相贯线切割机进行。
管件在切割前,必须用墨线弹出基准线,作为相贯线切割的起止和管件拼装的定位线。
并保证相交管件的中心轴线交汇于一点。
如果管桁架中,斜腹杆中心线交汇于弦杆中心线的外侧(即正偏心)或内侧(负偏心),则应使交汇的偏心距最小,且应满足:-0.55d0≤e≤0.25 d0或-0.55h0≤e≤0.25 h0,如图6.2.3.3-1所示。
相贯线的切割,应按照先大管后小管、先主管后支管、先厚壁管后薄壁管的顺序进行。
图6.2.3.3-1斜腹杆、弦杆中心线的偏心示意图注:d0为圆管直径;h0为矩管高度;e为偏心距。
4)管件壁厚大于6mm,应按图6.2.3.3-2、图6.2.3.3-3、图6.2.3.3-4和表6.2.3.3的坡口要求,采用定角、定点、固定坡口的方式与相贯线配套切割相贯节点焊接坡口。
5)相贯线形式主要分为:a.二管相贯线垂直相交相贯线,如图6.2.3.3-2所示。
图6.2.3.3-2垂直相交相贯线示意图斜交相贯线,如图6.2.3.3-3所示。
图6.2.3.3-3 斜交相贯线示意图偏心相交相贯线,如图6.2.3.3-4所示。
图6.2.3.3-4 偏心相交相贯线示意图b.三管相交相贯线, 如图6.2.3.3-5所示。
图6.2.3.3-5 三管相交相贯线示意图c.多管相贯线, 如图6.2.3.3-6所示。
图6.2.3.3-6多管相贯线示意图d.与环管相贯线与外环管相贯线, 如图6.2.3.3-7所示。
图6.2.3.3-7外环管相贯线示意图与内环管相贯线, 如图6.2.3.3-8所示。
图6.2.3.3-8 内环管相贯线示意图4)若采用火焰或等离子数控相贯线切割机进行相贯线切割,切割后必须将相贯线周围残留熔渣清除干净,防止焊接缺陷产生。
5)管件切割时应根据不同的节点形式,参考下述规定预留焊接收缩余量:钢管球节点加衬管时,每条焊缝收缩余量应留 1.5~3.5mm,不加衬管时,每条焊缝收缩余量应留 1.0~2.0mm。
焊接钢板节点,每个节点焊缝收缩余量应留 2.0~3.0mm。
相贯节点,每条焊缝收缩余量应留1.0~2.0mm。