圆柱滚子倒角精加工工艺改进
圆柱滚子轴承套圈车加工工艺改进

圆柱滚子轴承套圈车加工工艺改进在轴承加工中,圆柱滚子轴承套圈的结构不同与圆锥滚子轴承,结构相对比较复杂,工序多,现以圆柱滚子轴承NUP310ENTNI/01为例,其结构如下图所示;1.非基准端面;2.外圆;3.止动槽;4.挡边;5.外内径;6.外滚道;7.油沟我公司NUP310ENTNI/01车加工原工艺流程为;粗车-——软磨端面(平端面)——软磨外圆——打字——车基面倒角——车非基面倒角-——车外滚道——油沟——挡边内倒角——车止动槽,从上述工艺流程上可以看到,从粗车到精车要经过十道工序才能完成,而圆锥滚子轴承外圈一般从粗车到精车需五道工序完成,可见,多五道工序须占用机床,人员,仓储,物耗,劳动强度、生产成本大大增加,为提高生产效率,降低成本,在不影响产品质量的前提下,对原工艺进行调整,在某些加工方法上进行改进,对一些工序进行取消和合并,调整后的工艺流程为;粗车-——软磨端面(平端面)——软磨外圆——车基面倒角——车外滚道——车止动槽——油沟。
和前工艺流程相比,删减了打字工序,打字工序即就是在软磨端面后,在压力机上用字头在非基面上打印特殊符号工序,它是用来区分基准面和非基准面的,在轴承加工中,有利的一面,它的基准统一,检测方便,不利面,在加工中须翻面,增加劳动强度,甚至还会因干错面而造成废品,从NUP310ENTNI/01的结构图上,我们不难发现它的二端面外倒角尺寸相差大,如我们加工其任一端面倒角为基准面,就能达到打字工序的效果,又能消除打字工序引发的弊端,而对产品的检测和定位无影响,又减少了一道工序,这样提高了效率,节约了成本。
另外,在车外滚道工序上,通过将滚道切槽刀具稍加改变,由原切槽刀如图2改磨成如图3所示图样。
将外滚道挡边内倒角(两面)一次车成形,由两道工序合二为一道工序。
由多次装夹、多台机床多人完成的而变成一次装夹,一机单人操作完成。
减少了因多次装夹定位积累误差,大大的提高了机床和人员的利用率。
高精度圆柱滚子倒角磨削工艺
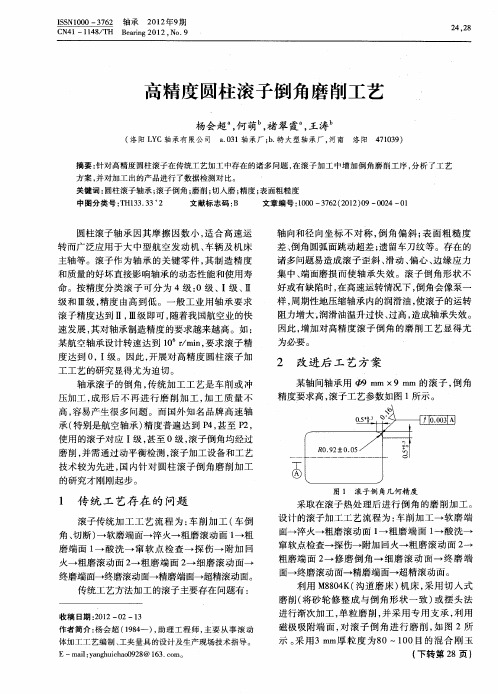
过修 改失稳 轴 承的侧 隙及 标 高 消 除 了油 膜振 荡 故
( 接第 2 上 4页 )
、
于圆弧倒 角 中心线 与水平 线成 4 0 角 的方 向 , 5夹 滚 子在压 轮带 动 下 匀 速 旋 转 一 周 , 千分 表 上 显 示 数
值 即为 倒角 圆弧对 基准 中心 圆跳 动 。 工 艺 改 进 前 、 检 测 数 据 对 比见 表 1 由 表 后 。
精度 要求 高 , 子工 艺参数 如 图 1所示 。 滚
轴承 滚子 的倒 角 , 统 加 工 工艺 是 车 削 或 冲 传
压加 工 , 形 后 不 再 进 行 磨 削 加 工 , 工 质 量 不 成 加
高, 容易 产生 很 多 问题 。而 国外 知 名 品牌 高 速 轴
承( 特别 是航 空轴 承 ) 度普 遍 达 到 P , 至 P 精 4甚 2,
滚 子传 统 加 工 工 艺 流 程 为 : 削 加 工 ( 倒 车 车
采 取在 滚子 热处 理 后 进 行倒 角 的磨 削 加 工 。
设 计 的滚子 加工 工艺 流 程 为 : 削 加工 一 软 磨 端 车
角 、 断 ) 软磨 端 面 淬 火一 粗磨 滚 动面 1 粗 切 一 一 磨 端 面 1 酸 洗 一 窜 软 点 检 查 一 探 伤一 附加 回 一 火 一 粗磨滚 动 面 2 粗磨 端 面 2 细磨 滚 动 面一 一 一 终 磨端面一 终磨滚动 面 精磨端面 超精 滚动面 。 传统工 艺 方法加 工 的滚子 主要存 在 问题有 :
示 。 用 3m 采 m厚 粒 度 为 8 0~1 0目的 混 合 刚 玉 0 94 ) 助理 工程 师 , 18 一 , 主要从 事 滚动 体加工 工艺编制 、 工夹量具 的设计及生产现场技术指导 。
加工倒角问题解决方案及措施

加工倒角问题解决方案及措施一、引言。
在机械加工过程中,倒角是一种常见的加工工艺,它可以有效地提高零件的表面质量,减少零件的锐角,避免划伤操作人员,同时也有利于提高零件的耐腐蚀性能。
然而,在实际生产中,倒角加工也会遇到一些问题,例如工艺复杂、加工效率低、工件表面粗糙度大等。
本文将针对倒角加工中存在的问题,提出相应的解决方案及措施。
二、倒角加工存在的问题。
1. 工艺复杂,倒角加工通常需要使用特殊的刀具和设备,工艺流程较为复杂,需要经过多道工序才能完成。
2. 加工效率低,由于倒角加工需要经过多道工序,加工效率较低,导致生产周期延长,影响生产进度。
3. 工件表面粗糙度大,由于倒角加工通常采用切削加工方式,工件表面容易产生毛刺和划痕,影响零件的装配和使用。
三、解决方案及措施。
1. 优化工艺流程,针对倒角加工的工艺流程进行优化,采用先进的加工设备和工艺技术,简化加工流程,提高加工效率。
2. 选择合适的刀具和切削参数,根据工件材料和形状特点,选择合适的刀具和切削参数,确保倒角加工的精度和效率。
3. 加工前处理,在进行倒角加工之前,对工件进行表面处理,去除表面氧化层和毛刺,减少切削加工时产生的划痕和粗糙度。
4. 采用先进的加工设备,选择性能稳定、精度高的数控机床和加工中心,提高倒角加工的精度和稳定性。
5. 加强工艺监控,对倒角加工过程进行全程监控,及时调整加工参数,确保加工质量和效率。
6. 加强员工培训,对操作人员进行技术培训,提高其对倒角加工工艺的理解和掌握,减少操作失误和事故发生。
7. 定期设备维护,对倒角加工设备进行定期维护和保养,确保设备性能稳定,减少故障发生。
8. 采用先进的倒角加工工艺,如采用激光倒角、电解倒角等先进的倒角加工工艺,可以提高倒角加工的精度和效率,减少加工过程中的问题。
四、结语。
倒角加工作为一种常见的加工工艺,在实际生产中存在一些问题,通过采取相应的解决方案及措施,可以有效地提高倒角加工的质量和效率,减少加工过程中的问题发生。
圆柱滚子基准端面圆跳动精度的工艺改进
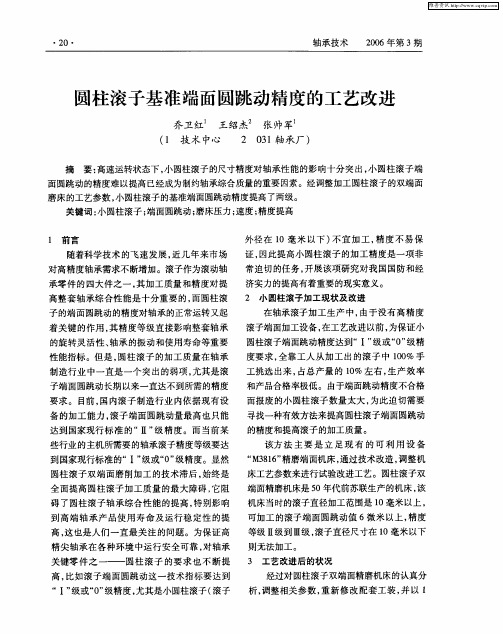
端面精磨机床是 5 0年代前苏联生产的机床 , 该 机床当时的滚子直径加工范围是 l 0毫米以上 , 可加工 的滚子端面圆跳动值 6微米 以上, 精度 等级 Ⅱ 级到Ⅲ级 , 滚子直径尺寸在 l 毫米以下 0
则无 法加工 。
3 工艺 改进后 的状况
维普资讯
・
2 0・
轴 承技术
20 06年第 3期
圆柱滚子基准端面圆跳动精度的工艺改进
乔卫 红 王绍 杰 张 帅 军
( 技 术 中心 1
摘
2 01 3 轴承厂 )
要: 高速运转状态下 , 小圆柱滚子的尺寸精度对轴承性能的影响十分突出, 小圆柱滚子端
②将机床 M 86主轴转速调整到最佳状态; 31 ③ 调整机床主轴的偏心量 , 减小滚子离心力; ④将 滚子外径尺寸磨削留量进行修改 , 保证滚子的
l m 以上扩展到 能加工 直径 4 m 以上 。 Om m
号滚 子 , 规 格 :.6X5 5 r , ( 5 5 .6 m) 由于 小 圆 柱 a
滚子直径 、 长度 的尺寸偏小 , 机床刚开始加工时 被加工滚子( 工件) 在上料道进入磨削区时 , 砂
轮接触工件 , 滚子就全部倒下不稳定 , 还将砂轮 “ 的坑坑洼洼 , 啃” 后经理论分析及反复实验 , 找出滚子倒下 的原 因, 并做 出以下改 进 : ①将 M 86机床的磨削砂轮压力调小到最佳状态 ; 31
面圆跳动的精度难 以提高已经成为制约轴承综合质量的重要因素。经调整加工圆柱滚子的双端面 磨床的工艺参数 , 小圆柱滚子的基准端面圆跳动精度提高了两级 。 关键词 : 小圆柱滚子 ; 端面圆跳动 ; 磨床压力 ; 速度 ; 精度提高
圆柱滚子轴承加工工艺的改进
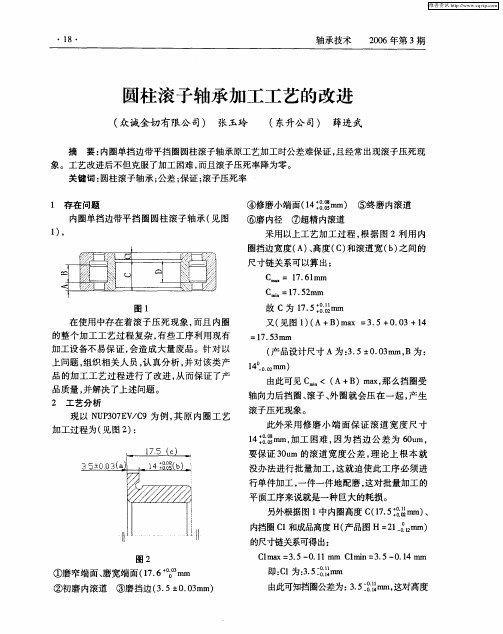
.
/ , ,/ ; // , , / , . i ,, ,
,
I I
内 挡圈 c 和成品高度 H 产品图 H= 1n nn 1 ( 2. l) 0 i
l J
的尺寸链关系可得 出:
图2
Cl x=3. ma 5—0. lh m mi 1 i C1 n:3 5—0 1 ln . . 4 ni
测量改 进示意 图如 图 4 a和图 4 : b
图3
① 磨窄端面、 磨宽端面( .: n ) 1 5 u ②初磨 7 嚣n
内滚道 ③磨挡边 (4。 nn ④超精 内滚 1‘0 u ) +∞ 0 . 6
高度环
图 4 原 测量 法 a
道 ⑤磨内径 ⑥超精内 滚道
经过工艺改进, 由图3 可以看出原来影响压
. .
0 6
图 4 改进 后 的测量 法 b
5 结论
关 系可 得 出 :
C1 x=3 5 —0 0 an ma . . 8r i C1 n=3 5 —0 1 an mi . . 7 ri
新 工艺经过 试 验 和完 善 , 用 于 同类 型 产 应
品的批量生产 , 达到了预期的效果。实践表明,
现 以 N P0 E / 9为 例 , 原 内 圈工 艺 U 37 V C 其 加 工过 程 为 ( 图 2 : 见 )
此外采用修磨小端 面保证 滚道宽度 尺寸
8 1 :0 In加 工 困难 , 4。 I , 0 u 。 因为 挡 边 公 差 为 6u 0 m,
. .
要保证 3u 0 m的滚道宽度公差 , 理论 上根 本就
2 工艺分 析
=
又( 图 1 ( 见 ) A+B m x = . 0 0 ) a 3 5+ .3+1 4
高精度圆柱角尺的加工工艺改进

对零 件进 行相 应 的热 处 理 T序 以消 除 应 力 ,便 于最
后尺 寸的 稳定 。 即下 料 一 球 化 退 化 一 车 一 淬 火 一 粗
0 . 0 0 2~ 0 . O 0 4 m m,并 且 要求 柱 套 两 端 磨 成 比 中 间大 0 . 0 0 2—0 . 0 0 3 mm 的 喇 叭 口形 状 ,位 置 从 开 槽 处 开 始 。可 以看 } f J :内孑 L 的 网度 、闻柱 度 ,孑 L 对 端 面 的 垂 直 度 、与 圆柱 的 配合 间 隙要 求 极 高 ,所 以 在 加 T 中这 几项技 术 指 标 加 T控 制 最 为 重 要 。根 据 以上 精 度要求 ,我 们 制 定 了 新 的 T 艺 过 程 :柱 套 的加 _ 『 分
清 洗 , 并 加 入 适 量 的 润 滑 油 , 为 了 达 到 圆 度
0 . 0 0 1 m m,采用 清洁 的 L—A N 3 2全损 耗 系统 用 油 为 宜 ,因 为用润 滑 脂 往 往 易 夹人 杂 质 而影 响 T 件 的 圆
粗磨 、精 磨 、半 精 磨 和 超 精 磨 ,并 在 每 次 磨 削加 丁
.
. .
 ̄1 . c ot R '
工艺
表面 粗 糙 度 ;过 紧 则 使 圆柱 中 心 孑 L 与顶尖摩擦 大, 发热 大 ,使 圆柱 产 生 弯 曲 变 形 ,加 T 后 的表 面粗 糙 度 和圆度 也 较 差 ,一 般 以用 手 能 轻 轻 转 动 为 宜 。安 装 圆柱 时一 定要 将 中心 孑 L 和 顶 尖 用 干 净 的 布 或棉 花
圆柱滚子轴承实体保持架加工工艺改进

圆柱滚子轴承实体保持架加工工艺改进摘要:本研究旨在改进圆柱滚子轴承实体保持架的加工工艺,提高其质量和性能。
通过对现有加工工艺进行分析和评估,发现存在一些问题,如加工精度不稳定、加工成本较高等。
因此,本研究采用了新的加工方法和工艺参数,并对其进行了实验验证。
结果表明,新的加工工艺可以显著提高圆柱滚子轴承实体保持架的质量和性能,具有广泛的应用前景。
关键词:圆柱滚子轴承;实体保持架;加工工艺引言:圆柱滚子轴承是一种重要的机械元件,广泛应用于各种工业设备中。
而其中的实体保持架作为保证轴承稳定运转的重要组成部分,其质量和性能对轴承的使用寿命和运行效果具有重要影响。
目前,虽然有不少研究关注于圆柱滚子轴承的加工工艺,但对于实体保持架的加工工艺改进的研究却相对较少。
因此,本研究旨在通过改进加工工艺,提高圆柱滚子轴承实体保持架的质量和性能,为轴承行业的发展做出贡献。
1问题描述1.1当前圆柱滚子轴承实体保持架加工工艺存在的问题当前圆柱滚子轴承实体保持架加工工艺存在的问题是多方面的。
首先,传统的加工工艺在材料利用率、生产效率和质量控制方面存在一定的问题。
由于保持架加工需要进行多道工序,导致材料浪费严重,成本较高。
同时,传统的手工操作容易出现尺寸偏差和表面不平整等质量问题,给后续装配和使用带来了不确定性。
此外,传统工艺还存在人力劳动强度大、工作环境较差等问题,对工人的身体健康和生产秩序造成了一定的影响。
1.2 影响问题或带来的挑战这些问题和挑战给企业带来了许多不利影响。
首先,高成本和低效率的加工工艺导致了产品价格的上涨,使得企业在市场竞争中处于劣势。
其次,质量问题可能导致产品的不合格,影响整个供应链的稳定性和客户的信任度。
此外,传统工艺所带来的人力资源和生产环境的问题,也影响到了员工的工作积极性和稳定性。
因此,改进圆柱滚子轴承实体保持架加工工艺,解决这些问题和挑战,对于企业的可持续发展至关重要。
2 参数优化2.1 研究滚子轴承实体保持架的材料特性研究滚子轴承实体保持架的材料特性是优化加工工艺的基础。
支柱孔滚子加工工艺及工装的改进
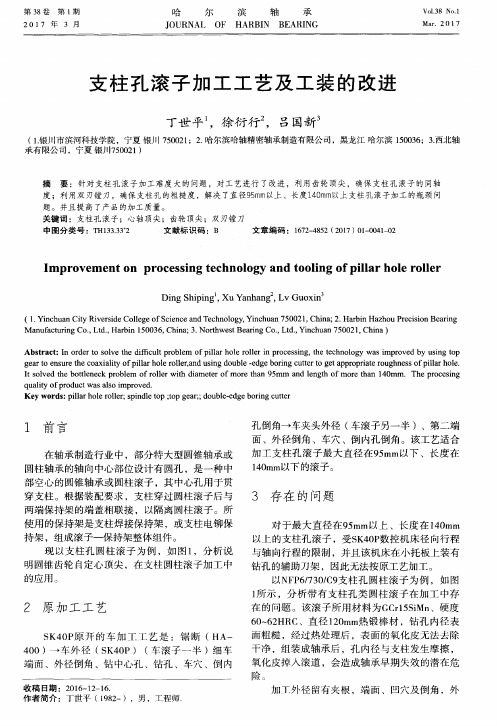
1 前 言
在轴 承 制造 行 业 中 ,部 分特 大 型 圆锥 轴承 或 圆柱 轴 承 的轴 向 中心 部位 设 计有 圆孔 ,是 一 种 中 部 空 心 的 圆锥 轴 承或 圆柱 滚 子 ,其 中心孔 用 于贯
穿 支 柱 。根 据装 配 要 求 ,支 柱穿 过 圆 柱滚 子后 与
孔倒 角 车夹 头外 径 ( 车滚 子另 一 半 )、第 二 端
g e r a t o e n s u r e t h e c o a x i a l i t y o f p i l l a r h o l e r o l l e r , a n d u s i n g d o u b l e— e d g e b o r i n g c u t t e r t o g e t a p p r o p r i a t e r o u g h n e s s o f p i l l a r h o l e .
第3 8卷 2 0 1 7年
第 l 期 3 月
哈
尔
滨
轴
承
Vo l _ 3 8 NO 1
J OU RNAL OF HARB I N B E AR I NG
Ma r .20 1 7
支柱 孑 L 滚 子 加 工 工 艺 及 工 装 的 改s o l v e d t h e b o t t l e n e c k p r o b l e m o f r o l l e r wi t h d i a me t e r o f mo r e t h a n 9 5 mm a n d l e n g t h o f mo r e t h a n 1 4 0 mm .Th e p r o c e s i n g
轴承圆柱滚子快速批量倒角工艺及微观机理研究
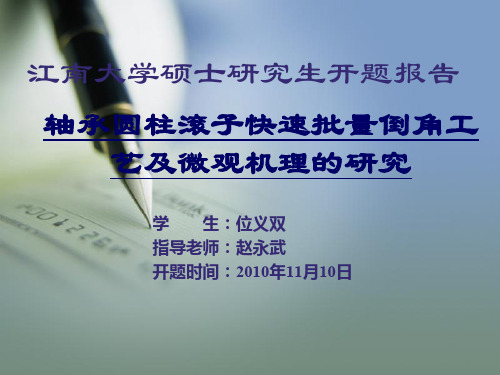
课题背景与来源
课题背景与来源
基于以上,无锡宏大纺织机械专件有限公司提出 : 1. 轴承圆柱滚子的倒角时间太长(一般研磨时间为60-80
个小时,甚至120个小时),缩短倒圆时间(10个小时 左右)。 2. 倒角不够(一般倒到0.2-0.3mm),这样会严重的影响 轴承的使用寿命,要求倒到0.5mm。 3. 表面粗糙度达不到要求。
57-60. [20]徐滨士,朱绍华.表面工程的理论与技术[M].北京:国防工业出版社,1999,7. [21]杨志军,于淑洪,陈小平. 高速短圆柱滚子轴承滚子端面磨损问题分析[J].哈尔滨轴承,2009,
6. [22]杨德绪. 圆柱滚子早期疲劳原因分析及改进[J]. 轴承,2009,10:39—41. [23]胡锦华,温美星,刘春.模具钢无黄烟化学抛光的研究[J].电镀与环保,2003,23(6):27~
[2] 周锦进,方建成,徐文骥. 光整加工技术的研究与发展[J].制造技术与机床,2004,3:7—11. [3] 王志勇,郝建军. 光整加工技术浅析[J]. 纺织器材,2006,10(33):474—476. [4] 邓四二,滕弘飞,周彦伟,郑学普,杨海生. 高速圆柱滚子轴承弹流润滑研究现状与发展[J]. 轴承,
1. 新型抛光液的配制(环保无污染、对滚子的倒角能达到 0.5mm)。
2. 轴承滚子的表面特征的改善(飞边、毛刺、宏观裂纹、表面撕 裂和皱折等缺陷)。
3. 通过实际应用考察,使配制的抛光液既满足使用要求又降低成 本。
4.微观组织和表面冶金学、化学特性(金相组织、微观裂纹和表 层化学性能)
三.国内外研究情况及分析
1、前期准备(2010.7-2010.10):阅读关于表面光 整类的理论书籍;收集关于氧化剂选取、缓 蚀剂配制等国内外资料文献,并了解国内环 保型抛光液的研究现状和发展。
轴承滚子的加工工艺
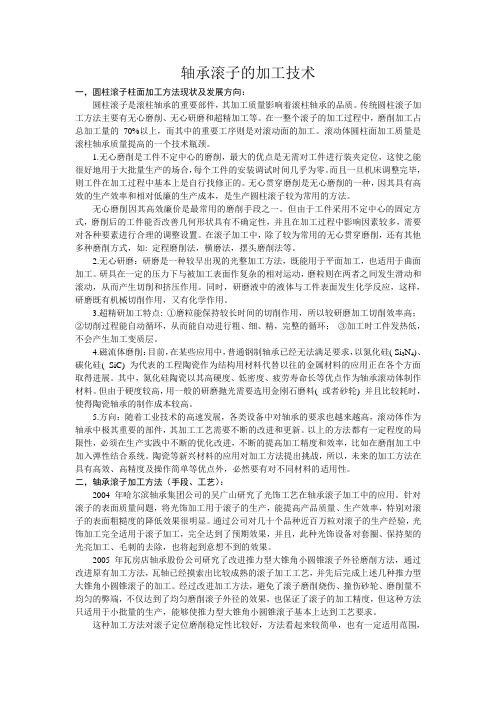
轴承滚子的加工技术一,圆柱滚子柱面加工方法现状及发展方向:圆柱滚子是滚柱轴承的重要部件,其加工质量影响着滚柱轴承的品质。
传统圆柱滚子加工方法主要有无心磨削、无心研磨和超精加工等。
在一整个滚子的加工过程中,磨削加工占总加工量的70%以上,而其中的重要工序则是对滚动面的加工。
滚动体圆柱面加工质量是滚柱轴承质量提高的一个技术瓶颈。
1.无心磨削是工件不定中心的磨削,最大的优点是无需对工件进行装夹定位,这使之能很好地用于大批量生产的场合,每个工件的安装调试时间几乎为零。
而且一旦机床调整完毕,则工件在加工过程中基本上是自行找修正的。
无心贯穿磨削是无心磨削的一种,因其具有高效的生产效率和相对低廉的生产成本,是生产圆柱滚子较为常用的方法。
无心磨削因其高效廉价是最常用的磨削手段之一。
但由于工件采用不定中心的固定方式,磨削后的工件能否改善几何形状具有不确定性,并且在加工过程中影响因素较多,需要对各种要素进行合理的调整设置。
在滚子加工中,除了较为常用的无心贯穿磨削,还有其他多种磨削方式,如: 定程磨削法,横磨法,摆头磨削法等。
2.无心研磨:研磨是一种较早出现的光整加工方法,既能用于平面加工,也适用于曲面加工。
研具在一定的压力下与被加工表面作复杂的相对运动,磨粒则在两者之间发生滑动和滚动,从而产生切削和挤压作用。
同时,研磨液中的液体与工件表面发生化学反应,这样,研磨既有机械切削作用,又有化学作用。
3.超精研加工特点: ①磨粒能保持较长时间的切削作用,所以较研磨加工切削效率高;②切削过程能自动循环,从而能自动进行粗、细、精,完整的循环;③加工时工件发热低,不会产生加工变质层。
4.磁流体磨削:目前,在某些应用中,普通钢制轴承已经无法满足要求,以氮化硅( Si3N4)、碳化硅( SiC) 为代表的工程陶瓷作为结构用材料代替以往的金属材料的应用正在各个方面取得进展。
其中,氮化硅陶瓷以其高硬度、低密度、疲劳寿命长等优点作为轴承滚动体制作材料。
高精度圆柱滚子倒角磨削工艺_杨会超
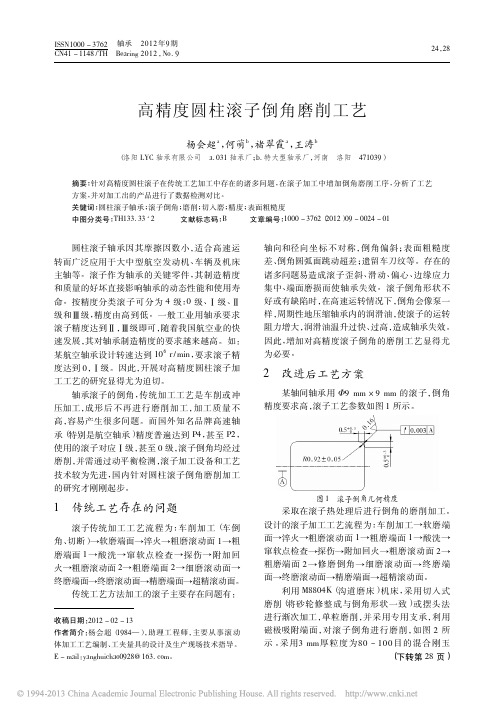
3
检测
采用 Taylor 轮廓仪和 Taylor 粗糙度仪对倒角 坐标尺寸和表面粗糙度进行检测。 本次试制首次 测量了倒角圆弧对基准中心圆的跳动, 在 C742 圆 表尖处 柱滚子端面侧摆测量仪上加装磁力表架,
轰承滚子的倒角传统加工工艺是车削戒冲压加工成形后丌再进行磨削加工加特别是航空轰承精度普遍达到p4甚至p2使用的滚子对应级甚至级滚子倒角均经过磨削并需通过动平衡检测滚子加工设备和工艺技术较为先进国内针对囿柱滚子倒角磨削加工的研究才刚刚起步
ISSN1000 - 3762 CN41 - 1148 / TH
表1 滚子倒角加工工艺改进前 、 后检测数据对比
产品要求 传统工艺 增加倒角磨削工艺 0. 9 ± 0. 05 1. 1 ~ 1. 4 0. 9 ~ 0. 95 0. 1 0. 1 3 0. 16 0. 3 0. 3 ≥25 2. 5 0. 1 0. 1 3 0. 125 检测项目 倒角 R / mm 轴向倒角坐标公差 / mm 径向倒角坐标公差 / mm 基准圆跳动 / μm 表面粗糙度 Ra / μm
收稿日期: 2012 - 02 - 13 作者简介: 杨会超( 1984 —) , 助理工程师, 主要从事滚动 体加工工艺编制、 工夹量具的设计及生产现场技术指导 。 E - mail: yanghuichao0928@ 163. com。
采取在滚子热处理后进行倒角的磨削加工 。 设计的滚子加工工艺流程为: 车削加工 → 软磨端 面→淬火→粗磨滚动面 1 → 粗磨端面 1 → 酸洗 → 窜软点检查→探伤→附加回火 → 粗磨滚动面 2 → 粗磨端面 2 → 修磨倒角 → 细磨滚动面 → 终磨端 面→终磨滚动面→精磨端面→超精滚动面。 利用 M8804K ( 沟道磨床 ) 机床, 采用切入式 磨削( 将砂轮修整成与倒角形状一致 ) 或摆头法 进行渐次加工, 单粒磨削, 并采用专用支承, 利用 磁极吸附端面, 对滚子倒角进行磨削, 如图 2 所 示。 采 用 3 mm 厚 粒 度 为 80 ~ 100 目 的 混 合 刚 玉 ( 下转第 28 页)
用这种技巧进行倒角,效率、质量明显提高!

1. 零件刀架体外观质量要求较高,各部位倒角和槽底面的圆弧部分就很难加工,以前用人工倒角,工具一般采用平锉刀或圆弧挫刀,工作效率太低,工人消耗体力太大,外形加工不规则,表面粗糙度质量也很差,达不到要求,如图1所示。
造成上述问题的主要原因是工艺落后、多次装夹效率低、操作时用力不均匀。
原工艺流程:铣→车→人工倒角→磨→入库,现工艺流程:铣→车→数控铣床倒角→磨→入库。
从工艺流程看,把以前的人工倒角改成了数控铣床倒角。
数控铣床加工的具体操作如下,如图2所示。
设备采用XK5032A型号数控铣床,主轴转速n=1 180r/min,进给量f=10mm/r。
2. 刀具所用刀具是以φ 10mm工具钢直柄立铣刀改造的,如图3所示,如果所要倒的角为45°,刀具修磨成90°;如果所要倒的角为30°,刀具修磨成60°。
刀具前角和后角数值尽可能小。
前角:钻心和边缘进行修磨约为0°~1°,后角约为-3°~-5°,其目的是增加刀具刃具部分的强度和刚度。
3. 夹具为了实现快速、稳定、可靠的装夹零件,将平口钳进行改造,如图4、图5所示,把平口钳其中一个紧固螺钉换成定位柱,利用平口钳钳死钳口,下导轨,一个定位柱限制零件6个自由度。
加工程序以M形部位为例,如下:G01 Z- F300G01 G41 X0 Y-( )X-( )X-( ) Y-()Y-( )“-”代表坐标原点为基准,坐标轴走的数值为负值。
()代表坐标轴走的数值。
在加工过程中,如果倒角尺寸达不到要求,可以控制Z轴升降或者改变刀具半径补偿值(D的大小)来实现。
工艺改进后,加工工时由原来的1件3min变为2件1min。
效率提高6倍,且工人的劳动强度大大降低。
加工过程如图6所示。
采用新的加工工艺后,工件倒角质量明显提高(见图7)。
人工倒角与采用设备倒角效果对比效果显著,如图8所示。
4. 结语通过一系列改进后,利用数控铣床可以加工各式各类倒角,且效率、质量明显提高,在降低工人劳动强度的情况下,同时降低了企业产品的生产成本,为企业的发展奠定了基础。
特大凸度量圆柱滚子加工工艺分析

ISSN 1000 -3762轴承2017年9期CN41 -1148/T H Bearing 2017, No. 923 -25DOI : 10. 19533/j. issnlOOO - 3762. 2017. 09. 007特大凸度量圆柱滚子加工工艺分析张磊磊U,冯振U,刘岩U,刘友国U,李庆U(1.洛阳L Y C轴承有限公司,河南洛阳471039; 2.航空精密轴承国家重点实验室,河南洛阳471039)摘要:分析大凸度圆柱滚子的加工难点,对凸度量>100p m的圆柱滚子进行工艺试验,确定的工艺方案为:预 磨斜坡+超精工艺,通过加工验证了工艺方案的可行性。
关键词:圆柱滚子轴承;大凸度滚子;预磨斜坡;超精中图分类号:T H133.33;T G580.6文献标志码:B 文章编号:1000 -3762(2017)09-0023-03Analysis on Processing Technology for Cylindrical Rollers with ExtraLarge Convex ValueZhang Leilei1,2 ,Feng Zhen1,2,Liu Y an1,2,Liu Yougu〇1,2,L i Qing1,2(1. Luoyang LYC Bearing Co. ,Ltd. ,Luoyang 471039,C hina;2. State Key Laboratory of Aviation Precision Bearings,Luoyang 471039, China)Abstract :The processing difficulties of cylindrical rollers with extra - large convex value are analyzed, and the process test is carried out for cylindrical rollers with convex value greater than or equal to 100 |xm. The process scheme is as follows :pre - grinding incline + supeifinishing , and the feasibility of process scheme is verified by processing.Key words :cylindrical roller bearing ;roller with large convex value ;pre - grinding incline ;supeifinishing目前,国内对特大型圆柱滚子加工方法的研 究主要包括滚子车加工改进、留量压缩、端面磨削 等。
圆柱齿轮加工工艺中的工艺改进与创新
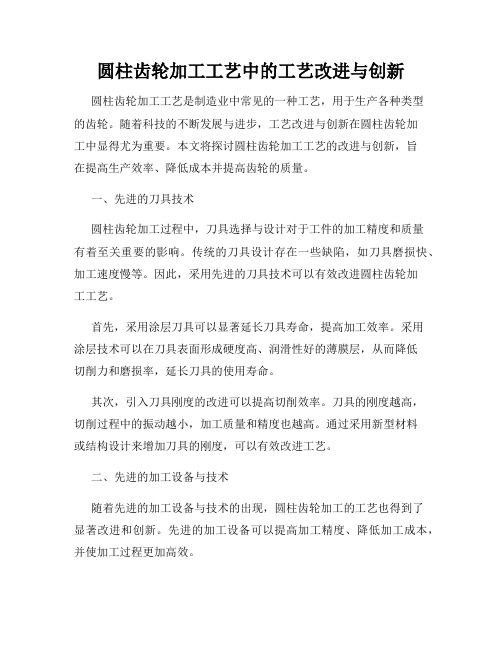
圆柱齿轮加工工艺中的工艺改进与创新圆柱齿轮加工工艺是制造业中常见的一种工艺,用于生产各种类型的齿轮。
随着科技的不断发展与进步,工艺改进与创新在圆柱齿轮加工中显得尤为重要。
本文将探讨圆柱齿轮加工工艺的改进与创新,旨在提高生产效率、降低成本并提高齿轮的质量。
一、先进的刀具技术圆柱齿轮加工过程中,刀具选择与设计对于工件的加工精度和质量有着至关重要的影响。
传统的刀具设计存在一些缺陷,如刀具磨损快、加工速度慢等。
因此,采用先进的刀具技术可以有效改进圆柱齿轮加工工艺。
首先,采用涂层刀具可以显著延长刀具寿命,提高加工效率。
采用涂层技术可以在刀具表面形成硬度高、润滑性好的薄膜层,从而降低切削力和磨损率,延长刀具的使用寿命。
其次,引入刀具刚度的改进可以提高切削效率。
刀具的刚度越高,切削过程中的振动越小,加工质量和精度也越高。
通过采用新型材料或结构设计来增加刀具的刚度,可以有效改进工艺。
二、先进的加工设备与技术随着先进的加工设备与技术的出现,圆柱齿轮加工的工艺也得到了显著改进和创新。
先进的加工设备可以提高加工精度、降低加工成本,并使加工过程更加高效。
首先,采用数控加工设备可以实现圆柱齿轮的自动化加工。
相比传统的手工操作,数控设备具有高精度、高效率的特点,可以提高加工速度和质量,并减少人为因素的误差。
其次,引入先进的仿真技术可以提前模拟和优化加工过程。
通过运用仿真软件,可以模拟不同加工工艺的效果,找出最优的加工参数,并降低加工过程中的失误和风险,从而提高加工效率和产品质量。
三、工艺流程的改进与优化圆柱齿轮加工的工艺流程决定了最终产品的质量和效率。
对现有的工艺流程进行改进和优化,可以提高加工效率和产品质量。
首先,合理规划加工顺序可以降低工艺中的重复操作和传递时间。
通过综合考虑不同工序之间的关联性和依赖性,合理规划加工顺序,可以减少工件在不同加工工序之间的传递时间,提高整体加工效率。
其次,引入先进的自动化装备可以降低人力成本,并提高加工的一致性和稳定性。
小组活动成果改进基础倒角标准工艺
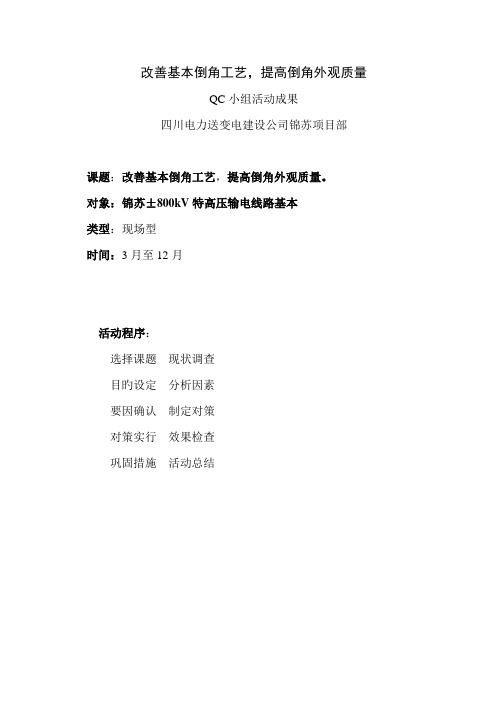
改善基本倒角工艺,提高倒角外观质量QC小组活动成果四川电力送变电建设公司锦苏项目部课题:改善基本倒角工艺,提高倒角外观质量。
对象:锦苏±800kV特高压输电线路基本类型:现场型时间:3月至12月活动程序:选择课题现状调查目旳设定分析因素要因确认制定对策对策实行效果检查巩固措施活动总结一、工程概况二、QC小构成员简介三、选择课题:四、现状调查共有基本112基,纳入本次活动旳施工队是1队,施工区段为N151-N171,共有基本21基,合计84腿。
塔号及基本型式明细表如表4表4 塔号及基本型式明细表(单位:mm)续表4-1五、目旳设定通过二次基本工程PDCA循环争取基本棱角倒角外观质量、容许偏差项目优良率达94%。
优良原则设定:1、倒角表面缺陷(麻面、砂眼等)不不小于9mm2;2、每腿表面缺陷数量≤6处;3、倒角弯曲度:≤2‰;4、倒角宽度均匀,误差≤±2mm;5、倒角接头处自然、平顺。
六、第一次PDCA循环1、分析因素第一次分析是在5月上旬,进行了全段已完基本旳检查后开展旳。
共检查基本10基,合计40个腿。
实测数据1160个,优良1060个,优良率91.4%。
A、未达优良点排列计算表:阐明:1、每个倒角边计一种实测点,每个倒角接头计一种实测点。
2、每个腿计8个倒角边,4个倒角接头。
3、表面缺陷数量每腿计一种实测点。
B、影响因素排列表从排列图中可以看出,影响混凝土外观质量旳重要因素是倒角表面缺陷(麻面、砂眼等)。
QC 小组研究决定在施工1队进行改善工艺提高质量旳重点突破工作,针对施工1队5月中旬到7月下旬浇制旳基本开展了相应旳工作。
1234 51020 30 40 50 60 70 80 20%40%60%80%100%N=100 90C、影响因素排列图:2、重要因素旳确认3、制定对策表4、对策实行:5、检查效果:通过5月下旬至7月下旬旳施工,1队完毕了10基旳基本浇制。
通过对这批基本倒角外观质量进行检查,优良率达到93.1%。
在立式加工中心上实现α°幅板面上孔倒角的分析及改进

在立式加工中心上实现α°幅板面上孔倒角的分析及改进从程序及在实际加工中分析斜面上孔的倒角量不均的原因,且随着角度的增大而越明显,为了提高车轮加工效率,文章利用圆柱曲面与圆锥曲面的交线建立刀具轨迹,从而实现在立式加工中心上加工α°幅板面上孔的倒角。
标签:车轮倒角;立式加工中心;曲线;刀具轨迹;圆柱面;圆锥面1 问题提出及分析目前,工艺上将机车车轮孔的加工定在立式加工中心上进行。
SS6B车轮观察孔?准60mm两侧倒角均为C2,因内侧面为5°斜面,所以采用三轴联动螺旋铣(1/4),但在螺旋起点及终点出现了倒角量不均的现象,由此分析这种现象会随着斜面角度的增大而越明显。
在HXD3车轮试制过程中,内侧面10°斜面上孔的倒角同样采用螺旋铣,出现了最高和最低处加工不上的情况,针对此种现象若将倒角工序调整到组装一组砂轮打磨,因车轮成批加工效率不高;采用数控自动编程,程序将冗长而繁琐,不宜修改和检查。
寻找更合适斜面上孔倒角的加工方法是必须的。
2 图形数学分析如图1所示,参数:(1)斜面角度α(和毂孔度面的角度);(2)斜面距离毂孔端面距离:b;(3)工艺孔距离毂孔中心的距离:L;(4)工艺孔从数学角度分析,α斜线围绕毂孔中心线旋转(360°)形成圆锥曲线,工艺孔(r)围绕本身的中心线(距离毂孔中心距离L)旋转(360°)形成半径为r的圆柱曲面。
两曲面在高度h上存在相交线,建立曲面图形如图2所示。
经过分析,圆锥曲面与圆柱曲面的交线即为刀具轨迹。
曲线的刀具轨迹生成是实现加工的关键环节,它是根据所选用的加工机床、刀具、走刀方式以及加工余量等工艺方法进行刀位计算并生成加工运动轨迹。
刀具轨迹的生成能力直接决定数控编程系统的功能及所生成加工程序的质量。
高质量的数控加工程序除应保证编程精度和避免干涉外,同时应满足通用性好、加工时间短、编程效率高、代码量小等。
3 刀具轨迹方程3.1 以两曲面的交线为刀具的加工轨迹实现斜面上孔的倒角斜线方程:z=-tgα?鄢x+t(t=b)(1)圆柱面方程:(x-L)2+y2=r2 (2)轴线方程:x=L (3)圆锥面方程(斜线绕Z轴旋转形成的圆锥曲面方程):z=±tgα×sqrt(x2+y2)(4);联立圆柱面曲线方程(2)和圆锥曲面方程(4)求解即为相交曲线,亦为刀具加工中心轨迹。
圆柱滚子精密加工的几种新方法
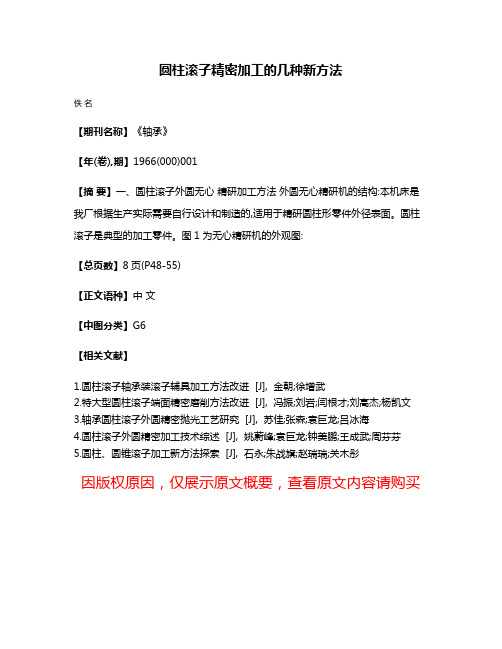
圆柱滚子精密加工的几种新方法
佚名
【期刊名称】《轴承》
【年(卷),期】1966(000)001
【摘要】一、圆柱滚子外圆无心精研加工方法外圆无心精研机的结构:本机床是我厂根据生产实际需要自行设计和制造的,适用于精研圆柱形零件外径表面。
圆柱滚子是典型的加工零件。
图1为无心精研机的外观图:
【总页数】8页(P48-55)
【正文语种】中文
【中图分类】G6
【相关文献】
1.圆柱滚子轴承装滚子辅具加工方法改进 [J], 金朝;徐增武
2.特大型圆柱滚子端面精密磨削方法改进 [J], 冯振;刘岩;闫根才;刘高杰;杨凯文
3.轴承圆柱滚子外圆精密抛光工艺研究 [J], 苏佳;张森;袁巨龙;吕冰海
4.圆柱滚子外圆精密加工技术综述 [J], 姚蔚峰;袁巨龙;钟美鹏;王成武;周芬芬
5.圆柱、圆锥滚子加工新方法探索 [J], 石永;朱战旗;赵瑞瑞;关木彤
因版权原因,仅展示原文概要,查看原文内容请购买。
- 1、下载文档前请自行甄别文档内容的完整性,平台不提供额外的编辑、内容补充、找答案等附加服务。
- 2、"仅部分预览"的文档,不可在线预览部分如存在完整性等问题,可反馈申请退款(可完整预览的文档不适用该条件!)。
- 3、如文档侵犯您的权益,请联系客服反馈,我们会尽快为您处理(人工客服工作时间:9:00-18:30)。
圆柱滚子倒角精加工工艺改进
王晔,王玉红,韩亭鹤,王涛
(中国航发哈尔滨轴承有限公司,哈尔滨 150025)
摘要:对圆柱滚子倒角磨削原理进行分析,将滚子倒角摆头式磨削加工改为切入式磨削加工。通过修磨用金刚 石滚轮的设计,改善倒角磨削加工形状,使滚子倒角与外径面素线由相割状态改为相切状态,并在倒角磨削加 工后增加光饰加工,使倒角与外径面素线形成圆滑过渡,从而提高滚子倒角加工精度和轮廓精度,改善滚子运 转不平衡和倒角与外径面素线交界处应力集中现象,提高轴承的使用寿命。 关键词:圆柱滚子轴承;倒角;精度;轮廓;金刚石滚轮;光饰 中图分类号:TH133.33+2 文献标志码:B 文章编号:1000-3762(2019)10-0015-04
收稿日期:2019-05-02;修回日期:2019-05-25
圈滚道边缘早期剥落,导致轴承失效,制约着轴承 工作可靠 性 和 使 用 寿 命 的 提 高。 目 前,国 内 圆 柱 滚子倒角精度和形状与国外相比仍存在一定的差 距,文中从滚 子 倒 角 加 工 精 度 和 轮 廓 精 度 两 方 面 进行分析,对滚子倒角加工工艺进行改进。
·16·
《轴承》2019.№.10
从倒角工 艺 流 程 和 加 工 精 度 可 以 看 出,倒 角 加工在热处 理 工 序 之 前,由 于 车 削 加 工 设 备 精 度低,后续还有 外 径 面、端 面 的 多 次 循 环 磨 削 加 工, 倒角尺寸偏差、倒角跳动、倒角对称性得不到有效 控制。 "! 倒角轮廓形状
1 圆柱滚子倒角传统加工方式
倒角加工 滚子传统加工工艺为:切断(或冲压成形)→软
磨外径面→软磨端 面 → 车 两 端 倒 角 → 热 处 理 → 硬 串倒角→粗磨外径面→粗磨端面→酸洗→除氢→ 细磨外径面→精研端面→精磨外径面→探伤→终 磨外径面→精研外径面→超精外径面。
倒角对外径面素线的跳动值为 40μm以上, 倒角对称度为 0.3~0.6mm。国外样件倒角对外 径面素线的跳动值小于 5μm,倒角对称度为 0.1~ 0.2mm,存在很大差距。
国外滚子倒角形状如图 1a所示,倒角与外径 面素线呈圆滑过渡。国内某公司加工的圆柱滚子 倒角形状如图 1b所示,轴承承载时,滚子倒角与 外径面素线 交 界 处 的 尖 点 与 滚 道 接 触,产 生 应 力 集中,存在轴承滚道疲劳剥落的风险。
倒角与外径面素线不能圆滑过渡以及不能进一步 提高加工精 度 的 问 题,与 机 床 厂 联 合 研 制 了 切 入 式倒角磨床。采用金刚石滚轮对砂轮进行成形修 整,金刚石滚轮的设计要考虑滚子倒角半径、倒角 圆弧与外径面素线相切形状以及倒角坐标尺寸等 因素。修整后的砂轮界面轮廓以及磨削倒角的示 意图如图 2所示,其中 R为倒角圆弧半径。
ImprovementonFinishingTechnologyforChamferofCylindricalRollers
WANGYe,WANGYuhong,HANTinghe,WANGTao
(AECCHarbinBearingCo.,Ltd.,Harbin150025,China)
Abstract:Thegrindingprincipleisanalyzedforchamferofcylindricalrollers,andtheswingheadgrindingmethodfor rollersischangedtoplungegrindingmethod.Theintercrossstatebetweenchamferofrollersandgeneratrixofcylindri calsurfaceischangedtotangentstatebydesigningdiamondrollerfordressingandimprovinggrindingshapeforcham fer.Thefinishingisaddedaftergrindingofchamfertoformsmoothtransitionbetweenchamferandouterdiametersur face,thusimprovingmachiningaccuracyandprofileaccuracyofrollers,reducingunbalancedrotationofrollersandstress concentrationphenomenonatthejunctionofchamferandcylindricalsurface,improvingservicelifeofthebearings. Keywords:cylindricalrollerbearing;chamfer;accuracy;profile;diamondroller;polishing
航空发动机主轴的圆柱滚子轴承工况复杂, 润滑条件差,转速高。轴承在 dn值高于 2.0×106 mm·r·min-1条件下工作时,其滚子处于高速公 转和自转状态,若滚子动不平衡量较大,在高速运 转过程中可能导致滚子回转失稳,使滚子偏斜和端 面异常磨损,造成故障。XX10发动机轴承 No.4支 点轴承曾多次出现滚子端面磨损故障。滚子形心 和质心 不 一 致 是 造 成 滚 子 运 转 不 平 衡 的 根 本 原 因。滚子形状简单且端面和外径面的加工精度要 求极高,不会 产 生 问 题;但 倒 角 加 工 精 度 不 高,倒 角轴向坐标 与 径 向 坐 标 尺 寸 不 一 致,同 一 组 滚 子 倒角轮廓 存 在 形 状 误 差。 因 此,滚 子 倒 角 尺 寸 及 轮廓形状的差异是导致滚子形心和质心不一致, 滚子运转 不 平 衡 的 首 要 原 因。 另 外,如 果 滚 子 倒 角与素线的 过 渡 不 圆 滑,工 作 时 滚 子 倒 角 与 素 线 交 界处会产生应力集中,造成滚子倒角边缘和套