模具N种顶出结构解说
(新)模具一般顶出机构设计_

第七章模具一般顶出机构设计一﹐推块顶出机构平板状带凸缘的塑件﹐如用推板顶出会粘附模具时﹐则应使用推顶出机构。
因推块是形腔的组成部分﹐所以它应具有较高的硬度和较低的表面粗糙度。
它的复位形式有两种:一种是依靠塑料压力﹐一种是采用复位杆。
二.利用成型零件顶出机构有些塑件由于结构形状和所用塑料关系﹐不宜采用顶杆﹐顶管﹐推板﹐推块等顶出机构﹐此时可采用成型镶件或凹模带出塑件。
前面讲的推块出属于成型镶块顶出机构。
三.多组件综合顶出机构它是指将前面所讲的几种顶出机构综合起来实现顶出的目的。
常用的有顶杆加顶板﹐顶管加顶板四.气压脱出机构使用气压脱模要设置压缩空气通路和气门﹐加工较简单﹐适用于轻的﹐薄的软性塑料脱模。
五.斜滑块脱出机构当塑件上具有与开模方向不同的内外侧孔或侧凹等阻碍塑件直接脱模时﹐必须采用斜滑块脱模机构。
即将成型侧孔或侧凹的零件做成活动的型芯。
在塑件脱模时先将活动型芯抽出﹐再从模中顶出塑件﹐完成活动型芯抽出和复位的机构叫做抽芯机构。
斜滑块抽芯机构的三种基本形式﹕1.抽芯方向与开模方向垂直2.抽芯方向与定模偏一定的角度3.抽芯方向与动模偏一定的角度斜滑块抽芯机构零件设计1.斜导柱(斜销)的设计1.1斜导柱长度和所需最小开模行程计算1.2斜导柱所受的弯曲力计算1.3斜导柱截面尺寸设计1.4斜导柱的斜角设计1.5斜导柱的安装固定形式及表面要求2.滑块的设计2.1型芯与滑块的连接形式2.2滑块的导滑形式2.3滑块的定位装置设计3.压紧楔块的设计3.1压楔块的形式3.2压楔块的楔角抽芯时的干涉现象及先复位机构设计常用的先复位机构有以下几种形式:1.楔形滑块先复位机构2.摆杆先复位机构3.杠杆先复位机构4.偏转杆先复位机构5.连杆先复位机构6.弹簧先复位机构斜导柱分型与抽芯机构的结构形式1.斜导柱在定模,滑块在动模的形式2.斜导柱在动模,滑块在定模的形式3.斜导柱与滑块同在定模的结构4.斜导柱同在动模的结构定距分型拉紧机构1弹簧螺钉式2摆钩式3滑板式4导柱式六.弯销分型与抽芯机构其原理和斜导柱抽芯机构一样,所不同的是在结构上以矩形断面的弯销代替了斜导柱.它的优点是斜角可以做大一些.七.斜导槽分型与抽芯机构。
塑胶模具设计原理:顶出系统

尺寸規格及材質
顶针布置 1、 在产品图上,首先在四边打顶针,然后在肋板两边打。 如肋深,则最好拆入子,在边上打肩销,宽度在1.2mm以上。 2、 在大平面上不用小顶针。直径不宜过细,需要足够刚度如不可加大,则做成台阶形。 Boss处用顶出套筒,如不,则必须在其附近打两枝顶针。 3、 顶出套筒尺寸确认,套筒厚度要有1mm以上内外径尺寸抓整数。 4、 顶针不宜设在产品最薄处,应在产品强度最大处布置,效果最好,不易顶白顶伤。 5、 顶针不可布置在滑块下面,必须时要加早回机构配合。顶针尽可能避免在高低面过渡的地方
四.顶板顶出: 如果塑件的沿周都要顶出的话,那就考虑用顶板顶出,另,一些特殊的产品表面不允许
有顶针的痕迹,也可以用顶板顶出的方式,顶板顶出制品受力 比较均匀,不易变形,一般适 用于盒盖类制品.推板内侧和胶位一般需留0.3mm的距离,在胶位不足的情况下,最小可 留到0.05mm,防止刮伤模仁,如图:
顶针的定位 当顶针的顶面为非平面或顶针面有成型胶位时,顶针的沉头部位就需要设计定位装置, 顶针转动或被装错.常用的定位装置有以下几种:
在较深的圆桶形胶位比较适用顶管顶出,司筒的固定方式于普通圆顶针一样,如成型的表面 为非平面,则司筒需加定位装置,方式参照原顶针的定位方式,司筒针定位于公模固定板,司筒 和司筒针前端前端采用精密配合防止制品毛边,后端应逃料0.1-0.2MM.以减少摩擦.具体参 数可参照顶针于模仁的配合.
塑胶模具设计原理 顶出系统
顶出系统
其中机械顶出为最 常用,分为顶针顶出,顶管顶出,顶块顶出及顶板顶出等.而顶针顶又为最常见,分为圆顶针 和扁顶针及异型顶针,此外根据顶出机构的不同还可分为 延时顶出,母模顶出,及二次顶 出等
模具系列7-模具顶出系统

一.使产品冷却固化后从模具上脱落的机构称为顶出系统,顶出系统要求安全可靠闭合时不能与其它机构发生干涉。
二.我们最常用的是机械顶出,其运用啤机机械力控制模具的闭合及顶出,另外还有气动顶出,液压顶出。
三.常用机械顶出类型A,圆顶针(推杆)<1>加工简便价格相对低廉,用得最广最多。
<2>分有托(双托)及无托(单托)我们厂通常直径2MM以下用有托(见图1)B,扁顶<1>加工比较复杂,要做镶件或者线割。
<2>主要用在深骨位置,透明产品上有骨位的地方,手机类骨状结构(见图2)<3>自制大扁顶(直顶),用在大面积深骨位置和透明类产品整个外形的顶出(见图3)C,司筒(推管)<1>价格相对比较高,主要用于空心柱子的顶出。
<2> A尺寸(司筒管壁厚)尽量取大否则易损坏, A≥0.8MM(见图4)<3>15MM以上的空心柱或者15MM以下但旁边不能下顶针的空心柱用司筒,透明类产品上有空心柱用司筒,细长圆形制品用司筒.<4>分有托及无托.<5>不能和顶棍孔干涉.<6>司筒针固定方式:我们厂规定用压板.没办法时可用基米镙丝.(见图4).D,推方(推块)<1>方式:a原身b镶件+顶针.<2>一般用在比较高并且其中间有大孔又不适合做推板的制品或制品后模边缘是大斜面或大弧面下顶针效果不好时,还有就是大面积深骨位置(和直顶相似)(见图5).E,推板<1>推呵(推后模料)深度较高或者产品内侧不能下顶针时(见图6)<2>推板和推呵相同,用有推板的模架.(桶状深长制品)四.注意事项A复位装置: 黄弹弓+回针B管位(定位),圆顶针或司筒上面不是平面的为了防转动而做定位装置,形式主要有两种(见图7)一种穿针,另一种把顶针头磨一角成”D”字形.我们厂要求所有顶针做”D”字头.(见图7b).C顶针处在大弧面或角度大的斜面上时要做”十”字防滑槽或晒格子纹(图8).D顶针等必须把产品顶离模具5~15MM,某些特别深的产品由于顶出行程的限制可以不用全部顶离模具,但其上面的骨位,柱位尽量顶离模具然后人工取出.E骨位,柱位及对内模有包紧力的地方(产品边缘等)是顶针布置集中区域F不能与其它机构干涉:离镶件,镶针边要有1~3MM;离运水要≥4MM;离镙丝牙≥2MM; 不能与推方相撞.G行位下面有顶针必须做先复位机构或做咭制.H有做”Z”形拉料的顶针其Z方向必须一致,方便取出(图9)I产品薄壁处不能下顶针(易顶高顶白)J注意某些禁设顶针区域(镜面要求,装配紧密,要滑动区等)K在产品有相互配合的地方下顶针,顶针要高出模面0.3~0.5MM.L原则上每套模具都要做顶针板限位块(一来防止弹弓过分压缩,二来防有托顶针避空不足撞断顶针)(见图10)五.顶针的一些下法A透明类常用垃圾水口顶出,它上面有筋骨考虑扁顶;上面有实心柱考虑圆顶;上面有空心柱考虑司筒;或者考虑整个外形的顶出.B主流道分流道处下圆顶C每一个或每一组潜水必须要有1支以上的水口针.D深实心柱子,下在其下面(图9b)短实心柱下在其旁边(图9C)E镶件,镶针旁边(图9def).F前模镶针碰后模顶针(图9gh)G骨位交叉位置(CASIO面,学习机面等(见图11).H围骨旁边(见图12).I深骨位旁边(见图13).J产品边缘.六.下顶针步骤A原则:圆顶优先,选大去小(面积足够)规格要少,分布平行—做到快速顶出,不顶白不顶高,顶针不倾斜不易断.B下法:,<1>对柱子先确认镶件还是司筒,镶针旁边要下顶针<2>深骨位置或凸凹台旁边下顶针或推方.<3>产品边缘下顶针.<4>对于对称产品可先下一边再镜像.<5>调整顶针位置达到均衡美观.。
最全的模具二次顶出

顶针二次脱模机构示例:⑴胶件如图&5・2所示,两骨间有半圆凹陷,被后模型腔包紧。
脱模机构如图8・5・3所示,第一次脱模使胶件脱出后模型腔,为强脱变形提供空间;第二次脱模,由顶针脱模,胶件半圆凹陷位强脱出型芯推块。
该机构运动过程:第一次脱模四块顶针板都运动,带着顶针、型芯推块同时运动,脱模距离/ h,使胶件脱出后模型腔,一次脱模完成。
当继续运动至摆块碰上限位面后,摆块摆动使上面两块针板快速运动,带动顶针脱出胶件,完成二次脱模。
此机构须注意:hl>h,H>lOmm1 hl1 (二次脱模运动距离)。
或者为获得可靠的脱模效果,分解胶件脱模阻力,经二次脱模动作,来完成胶件出模的 机构称二次脱模机构如图8.5.1所示。
图 8. 5.1^HUQnnHunfl沖一次脱快出内芯•为吹件從供父0空第:次脱模.胶件㈣凸位变形麻强脱出模胶件凹凸位被熨芯包醱方铁瞅位而图8・5.3由于潜浇道须设在斜顶行位块上,穿过斜顶块入胶,模具需实现浇道先脱出斜顶块,模具采用二次顶出机构如图8・5・6所示。
该机构第一次脱模时,拉料杆使浇道不动,顶针、斜顶脱出胶件M 距离.使胶件与潜浇道断开,潜浇道从斜顶行位块中变形后脱出,第一次脱模结束。
第二次脱模四块顶针板都动,顶出胶件.浇道脱出后模型腔。
需注意,为保证潜浇道脱出斜顶块,须M>S( 潜浇道长度)。
(2)胶件上入浇口、行位分模线如图8.5・5所示。
潜浇道放大图X-•步・卅鬼成1!丸$胆$・二次頂出上球疗成苦入干•怡了使具典成垛用赭戒农陵出冇氏*1 --延时頂出延时頂出是解决产品与浇口不能自动断开的问题(浇口形式。
搭接式或侧浇口)延时顶出只顶在流道上延时頂出,可以利用頂針的變化來完成。
适種艘形的頂針,是在一般的頂針下方,多加了 _段長度°延时頂出延时頂出 至於頂針採用兩截式頂 針,只是在於增加頂針的 強度,避免頂出時發生撓 曲變形。
採用這種頂針來完成兩 段式頂出,在模具結構上 是最簡單的,只要在頂針 板上動手腳就行了。
(完整版)塑胶模具顶出系统

1、顶针分类:1)圆顶针 ①单节式,直径在2以上;②双节式,直径在2以下;
2)扁顶针
形等等。
3)异形顶针:截面不为圆形也不为方形,为其它形状,如三角形,半圆
1)圆顶针:单节式,双节式。直径有很多,可以从0.5到很大。标准生产厂家可 以用0.1作为增量,也就是说直径可以从0.6、 0.7 、0.8 、0.9、 1 、1.1、1.2 、1.3 、1.4 等等。一般情况下,当直径小于2毫米时请尽可能采用双节式的圆顶针,有利于强度的提 高。
仁产生很大脫 模力.为使成品易于脫模使用顶出块配合 顶针的顶出结构,L段为逃料以减小顶出回位时与模仁 的磨损.
此側壁太深
• 7.5 顶出装置的种类四
• (2) 对于此类框架状成品,不易排顶针, 当顶出力不平衡时成品会变形,故采用整 整式顶出块.
7.7.1 顶板顶出 顶板顶出适用于筒形塑件,薄壁容器以及
7.8.2 气顶
密封圈
90° ~120
空 氣
7.9 急回机构一 在某些模具中,由于成品结构決定顶出装置与滑块等
抽芯机构发生干涉,导致无法順利合模,改善此种狀况必须 安装急回机构使顶出杆在合模时先回复原位 . 如图所示未装急回机构,滑块与顶管相撞导致無法合模
7.9 急回机构一 如图所示已装急回机构,顶管提前回位可順利合模
頂出或在较浅侧壁侧面進行咬花處理. 4. 顶针配置时在允许范围內直径应尽量加大且为標準 规格品. 5. 每一套模具顶针直径尺寸不宜太多种,以减少加工 时工时换刀时间及出错机率.
7.4 顶出位置之选择二
此處側壁較淺 均分在PL以上 易脫模
PL
此處側壁很深 均分在PL以下 不易脫模 PL
若脫模力不均衡 應考慮在此面作 咬花處理
(完整版)塑胶模具顶出系统

7.3 顶出行程之简介 7.3.1 顶出行程一般规
定被顶出的制品脫离模 5~10mm. 如右图所示
7.3.2 在成型一些形状简 单且脫模角度较大者的桶 形制品也可使顶出行程为 成品深度的2/3. 如右图所示
7.4 顶出位置之选择 一 1. 顶出机构的运动要准确,可靠,灵活,无卡死现象,机构 本身要有足夠的刚度和強度,足以克服脫模阻力. 2. 保证在顶出过程中塑件不变形,这是对顶出机构的最 基本的要求. 3. 冷却后由于塑料会对钢件产生收缩的应力,而有抱 紧的现象,在靠破孔两边成品肉厚強度最弱,应设置
7.9 急回机构二 7.9.1 利用弹簧片组合件急回机构
• 7.9 急回机构二 • 7.9.2 摇摆式急回机构
• 7.9 急回机构二 • 7.9.3 铰链式急回机构
7.10 顶针排布其它注意事項一 (1) 顶针布置时切不可与支撐柱、顶板导
柱、公模仁、公模板锁固螺钉及有拉回机构 之K.O孔相干涉.
前言 为了实现全自动化或者半自动化的机械生产,注塑模具的顶出系统在此作用上很重要. 顶出系统的构成:1、板子部分:模脚/下固定板/上下顶出板
2、固定螺丝部分:锁定模脚/上下顶出板 3、顶出设置:顶针/顶块/顶板/司筒 4、附助设置:KO孔
第一节 顶出样式 一、顶针顶出:材质,一般用好一点的材料:SKD61。
(2) 顶管布置时切不可与支撐柱、停止销、 K.O孔、上下顶板锁固螺钉, 公模板锁固螺钉 相干涉.
如下页:
7.10 顶针排布其它注意事顶二
回位杆 螺釘 彈簧
拉回機構 停止銷
頂管 螺釘 頂針
公模仁 公模板 支撐柱
頂出導杆 上頂出板 下頂出板 下固定板
各种罩壳形塑件的脫模顶出.这种顶出机构的 主要特点是顶出力均勻,平稳,顶出力大,塑件 不易变形,而且表面不留顶出痕跡,结构也比 顶管脫模机构简单,不需设置复位装置,合模
模具斜顶结构设计和顶出行程计算
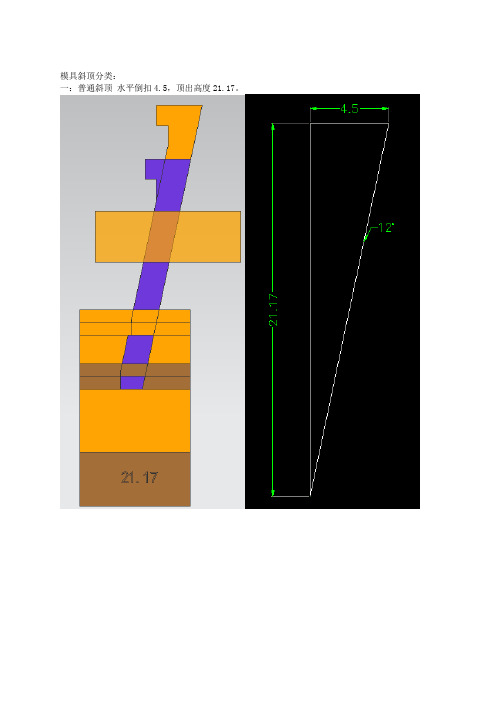
模具斜顶分类:
一:普通斜顶水平倒扣4.5,顶出高度21.17。
模具斜顶分类:
二. (1)斜斜顶(下落斜顶/下坡斜顶/延迟斜顶)水平倒扣4.5,顶出高度21.96
模具斜顶分类:
二. (2)斜斜顶(上坡斜顶/加速斜顶),水平倒,顶出行程20.37
模具斜顶分类:
三.(1)大角度斜顶—平行杆斜顶,计算方法和普通斜顶一样。
详解:产品倒扣较大,斜顶角度超过12°,斜顶多次斜向受力容易损坏,增加平行辅助杆。
可延伸为平行杆斜斜顶结构。
增加了平行杆的斜顶,斜顶座沿着平行杆运动,即:斜顶座也沿着倒扣轨迹运动,斜顶顶出距离和普通斜顶计算方法一样。
三.(2) 大角度交叉杆斜顶。
其他参数不变,分
解的角度5.51°
其他参数不变,分
解的角度5.61°
产品斜向倒扣角度比较大,控制斜斜顶运动轨迹的斜顶座角度太大,容易卡机构。
为了分解斜顶
座角度设置的辅助结构。
资料整理工程:赵小强 2019.11.20 上海立卡塑料托盘制造有限公司。
模具顶出方式的种类

顶出装置•成形品之顶出•有螺纹之成形品取出方法•点状浇口之主注到道一流道之顶出•两段顶出•顶出板超前退回机构为使射出成形能率及成形品质量提高﹐亦有必要施行自动运转﹐为此必需能使注道﹐流道及成形品自动而确实脱模﹒再者﹐少量生产之制品﹐型模制作日数及价格有所限制﹐亦由于成形品形状及浇口之种类不能自动脱模之场合﹐此际可决定成形品及注道﹐流道最容易脱模之顶出机构﹒同一形状之成形品亦由于材料种类及浇口形式之不同顶出方法亦随之异﹐必需将最适当之方法组合使用﹒成形品之顶出成形品顶出方法之决定﹐当然受成形品材料及形状等所左右﹐但原则上在成形品上制成缺口﹐阶层等﹐使能形成最确实之脱模﹐并且故障较少﹐再都故障发生之场合必需能简单补修﹒同一形状之成形品亦因由于外表﹐精度﹐成形性不同﹐而变化使用之顶出方法﹒顶出方法一般使用顶出梢(直梢﹐阶段梢)﹐筒套﹐刮料板﹐空气等﹐单独使用或组合使用﹐则视型模之寿命长短,型模加工之难易选定之﹒(1)顶出之种类1)顶出梢梢之加工最为容易﹐必需硬度之场合﹐施行淬火磨削等亦较其它方法为容易﹐可在成形品之任意位置上配置﹐为使用最多者﹒孔之加工容易﹐精度亦能达规定﹐滑动抵抗最小﹐契住发生少﹒因之型模寿命长﹐互换性使在破损之际﹐补修可以容易﹒然而在小面积上顶出﹐顶出应力集中于成形品之局部﹐杯类及箱形物品之退缩倾斜小﹐脱模抵抗大之成形品上﹐将发生压陷及顶穿等﹐此种场合﹐使用顶出梢大多不适当﹒2)方形或板状顶出梢板状顶出板等件之加工﹐热处理等并无困难点﹐但孔之加工困难﹐需要使用放电加工等特殊加工﹒将型范本及心型部份分割﹐形成组合型﹐加工变为容易﹐但制造工时增加﹐成形品由于有分割线﹐对透明件之外观有不良影响﹐亦有不允许之场合﹒再者﹐滑动抵抗亦较,圆梢为多﹐板之厚度较薄﹐容易引起弯折及挫屈﹐在可能限度中避免使用﹒3)套筒套筒之加工性比较良好﹐但套筒内径小而长度长者﹐加工较难﹐使用于肉薄件容易发生开裂﹒由于套筒之端面全面顶出﹐成形品顶出均一﹐能形成确实脱模﹐成形品开裂较少发生﹒4)刮料板刮料板及心型之加工并不比顶出梢为难﹐滑动面机械加工及配合则需要较多时间﹐滑动面契合部必需淬火﹐热处理为困难﹒再者﹐互换性亦趋向不良﹐修补必需较多人工﹒刮料板与心型配合面形状为圆形或方形者﹐机械加工及配合加工比较容易﹐但如为连续变化之曲线形者﹐则变为困难﹒再者﹐为使施行淬火后仍保有互换性﹐使用衬套嵌入﹐使补修容易﹐特别有数个型穴者﹐可仅将破损单件换调﹒刮料板与其它顶出方法比较﹐为顶出面积广大﹐成形品能确实脱模﹐对脱模抵抗较大之杯类及帽类之成形品脱模有效﹐广泛应用﹒再者﹐外观上几无顶出痕迹显示﹐此亦为优点之一﹒5)空气压出方法空气压出方法为设置阀等﹐将空气通入隙间﹐加工较为简单﹐对杯类及箱形等深度较大之成形品之脱模为极有效之方法﹒(2)顶出机构之实例图1为仅使用顶出梢之场合﹒顶出梢位置应配置于脱模抵抗强度较大之处﹐如脱模抵抗强度均一之场合﹐则应均等配置﹒图中所示之杯类及箱形成成形品﹐其侧面抵抗最大﹐最佳情形将顶出梢配置于此﹐再者﹐如于内侧面设置顶出梢场合﹐配置于侧壁附近较优于中央部份﹐否则将使顶出时容易引起开裂﹒图2为含有细而深之凸毂及加强肋之场合﹐使用顶出梢在其周围顶出﹐则发生开裂﹐容易使成形品破损报废﹐顶出梢必需设置于凸毂及加强肋底部﹐使能确实脱模﹒图3为阶层顶出梢之使例﹐由于无法使用细小顶出梢于小型成形品之场合﹐由于中段较粗﹐挫屈降低﹒图4为顶出梢与刮料板并用之一例﹐心型内面脱模抵抗较大部份﹐如仅用刮料板脱模﹐可能有列为断残留﹐为防止此种疵病发生﹐设置顶出梢﹐成为刮料板为主﹐顶出梢为补助之场合﹒此种场合﹐顶出梢设置于心型之内﹐形成心型冷却故障﹐使用小直径心型可作直接冷却﹐能消除此项缺点﹐必需考虑成形品之形状﹐使设置顶出梢之可能性消除﹐亦且能脱模﹒图5所示为部份之脱模抵抗较强(退缩倾斜少而深),如管状凸起场合﹐使用顶出梢在其周缘部及内面顶出时﹐成形品亦有开裂﹐皮用套筒顶出﹐以顶出梢为主﹐套筒为补助之机构﹒图6与图4﹒图5作相同之考虑﹐为刮料板及套筒并用之例﹒图7为深管状成形品之内外周具嵌入于可动侧之场合﹐在成形品端面使用用套筒顶出最为有效﹒图8示长套筒加工困难﹐短套套筒加工容易之例﹒一般情形﹐对盆形成形品顶出﹐大多使用图9之刮料板顶出﹐如使用图10所示之斜盆端顶出梢则加工简单﹒并且使用刮料板对心型冷却﹐亦如图4.图5之情形相同﹒有缺点存在﹒图11﹒图12为利用空气压出之情形﹒对大平面﹐深﹐肉薄之成形品(箱﹐杯等)使用刮料板顶出时﹐成形品可能引起挫屈﹐再者﹐成形品与心型间形成真空﹐使成形品破碎﹒使用于聚乙烯等软质材料场合破碎程度更为显著﹐此种场合使用空气压出最为有效﹐图11为仅使用空气者﹐图12为使用刮料板并在心型间有气压出方法之一例﹒有螺纹之成形品取出方法成形品有螺纹场合﹐脱模方法有下列三种﹒1) 型模螺纹部分模2)型模螺纹部置入嵌入件﹒3)成形品在型模螺纹部回转﹒(1)型模螺纹部分模此种方法适合于外螺纹(阳螺纹之型模构造﹐制造亦较简单﹐能确实脱模)﹒但成形品螺纹部有挤入分模线之废边产生﹐成形品之后加工﹐与契合件之配合形成故障﹒(2)型模螺纹部置入嵌入件型模构造不能使用分模及回转旋出者﹐型模构造简单之场合可使用置入嵌合件法﹒但使用此法时﹐成形品顶出后﹐必需将嵌入件取下﹐成形品为外螺纹之场合﹐由于收缩﹐取出容易﹐但如为内螺纹之场合﹐则置入之嵌入件与成形品之接角面积大﹐取出不易﹐由于成形品之材料及接触面积大取出困难﹒(3)成形品在型模螺纹部回转之场合一般盖件等为有内螺纹之成型品﹐大多使用回转自动旋出﹒此咱场合﹐成形品与型模任一件回转﹐并作退出运动﹐或一件仅作回转﹐他件退出运动﹐但对成形品必需有滑动定位(回转止动).成形品外周滑动定位﹐有点状浇口之型模﹐开模同时开始回转之场合﹐成形品与型模螺纹部之脱模﹐由于分模面之压开﹐分模面脱模抵抗大﹐成形品螺纹发生破断﹒为使能防止此项疵病﹐螺纹退出作用之速度﹐必需设计与分模线开模机构之速度相同﹒再者﹐在成形品螺纹部以外有脱模抵抗较强处所之场合﹐与回转开始之同时﹐必需有相同速度之顶出作用﹒回转伤虽在型模之固定侧及可动侧中俱可设置﹐但一般成形机设置于喷嘴及顶出机构之反对侧﹐由于注道﹐流道之配置及顶出关系﹐回转机构设置于可动侧﹐在型模构造上及成形能率上具属有利﹒1)成形品外周有滑动定位之场合图13为外点状浇口﹐图14为内点状浇口﹐俱使用特殊之顶出梢﹐刮料板等将其顶出﹐于开模间螺纹(a)回转纹数次后﹐在型穴中或心型上脱离﹐成形品自然落下﹒图15为成形品滑动定位及型模心型等位置于可动侧之场合﹐回转终了﹐成形品顶出H及h段﹐脱模落下﹒如图所示﹐H>h之场合﹐必需装置顶出梢(b)之顶出机构﹒图13~15所示适用于脱模时﹐浇口自动切断者﹐侧向浇口之场合﹐流道与成形品同时移动﹐必需设置同速之顶出机构﹒2)成形品内面有滑动定位之场合图16为内侧平面部有滑动定位﹐(a)一面回转﹐一面移动﹐当螺纹模之后﹐滑动定位仍然附着﹐必需另装除去装置﹐使成形件能自行落下﹒图17为内侧面有滑动定位之外螺纹场合﹐(a)回转﹐依成形品螺纹之螺距﹐将螺纹旋出﹐然后必需使用顶出梢(b)将其顶出﹒图18﹐图19内侧面有滑动定位﹐仅有(a)回转而(b)固定, 螺纹旋出脱模后,经由刮料板将其顶出. 刮料板之作用,有使用顶出梢, 弹簧等各种方法.3)成性形品端面有滑动定位之场合图20, 图21所示之成形品端面俱有滑动定位上, 为使其能自然落下, 必需另装顶出装置(a). 小型成形品而有侧向浇口之场合, 不能将成形品直接顶出, 需与流道一并顶出,再者无不需特别设置滑动定位, 可用浇口作为端面设置之滑动定位. 但对软质材料之场合, 如无相当大之浇口, 有剪断之可能.4)一面回转,一面作往复运动之小齿轮连结方法图22 示一面回转一面作往复运动之心型@与小齿轮直接连结, 图23示@与使用间接连结. 往复运动之滑动扺抵抗, 图23 者较小, 能圆滑作用,往复冲程较大, 图22中则强度较为良好, @中设质有心型梢之场合,与图22 所用者并物无差异.5)螺纹心型之驱动方法图24, 25利用开模冲程者.图26, 图27设置有油压及电动机等各别之动力者, 其优点为回转开始,停止等之时点能自由控制, 但必需有动力操纵装置. 成形品螺栓回转数多之场合, 图27 所示之驱动方法为最良好者.点状浇口之主注到道一流道之顶出侧向浇口在成形面中有流道一浇口之场合, 成形品可与之同时脱落,自然脱落容易,但点状浇口等场合, 自然脱落困难.图28 所示无流道剥离机构之场合, 必需以手工脱模. 型模构造最为简单, 但成形能率低, 少量生产以外场合不予使用.图29 为设置有流道刮料板, 但在剥离状态, 注道部分悬挂于流道刮料板孔中, 不能自然脱落, 此种情形应在A部设置顶出稍, 必要时使用空气压力将其压脱.图30 所示为较简单之构造,完成加工工数较少,流道长L比l为大,如l 深于以上场合,流道浮起时,形成嵌入于型范本策侧状态,不能自然脱落.再者,冷却时间长之场合,流道一部分弯折,一都度浮起之浇口部颁,仍将弹回退入于型范本侧.再者, A部颁有纵向庞旁边发生, 此等处所附着而不脱落. 此外, 成形品配置于注道之直下者, 注道定位稍不能装置, 使不适使用. 但无需使用弹簧及引长装置等装置, 并于开模同时, 浇口即可切断等利点.图31之优点及缺点大致相同,使图30中之A部不附着,流道之一部嵌入于型范本侧,亦能体度浮起脱落.但是注道顶出稍较可动侧装接板为长甚大,不能使用于无中心部顶出杆孔之成形机, 及中心顶出孔不够深之成形机上.图32 为钢笔套等细长成形品所用者, 在固定侧型模板内设置顶出板, 经由顶出梢将流道顶出, 此仅使用于限定之成形品形状.两段顶出(1)用途使用刮料板顶出场合, 刮料板内侧将成形品凸缘部顶出, 此部份仍与刮料板粘着, 必需更有任何方法将此自成形品上去除. 此种情形时, 为时能形成自动脱模, 必需有两段顶出机构.图33示刮料板与顶出梢之方法, 图34为将有凹陷之成形品, 使用两组出板, 作两段顶出, 使形成强制顶出之例.两段顶出之场合, 两组顶出冲程必需有所差异, 冲程大侧同同时或较迟作用.成性机顶出机构为压力缸及其附件, 以及定位杆及其附件, 前者之场合, 一方由固定侧, 使用螺杆,炼条及环等, 依开模冲程引长, 另一方由成形机之顶出机构作用, 能形成两段顶出作用.但后者场合, 两组必需由同一方向作两段顶出, 两组顶出机构必需有顶出冲程定时及冲程调节机构.(2)两段顶出之定位及冲程调节机构1)弹簧法图35为顶出之一方经由弹簧作用者,制造容易,安装位置小,为最简单之机构. 但不能承受过大之力,作用不确实.2)压力缸法图36 为使用压力缸代替弹簧, 作用确实, 定时能自由调节. 但安装位置较大, 成形机及型模较小时不能使用, 再者, 油压泵及空气压缩机必需有专用之控制设施.3)凸轮法图37示使用凸轮代替弹簧及压力缸, 作用确实,无须需其它附属设施.但由固定侧伸出之凸轮挺杆,必需安装对成形品取出无妨碍处所.4)夹颚法图38示(a), (b)两组顶出板, (a)组直接由(c)顶出, (a)组以夹颚(d)与(a)连结, 在作用行程中经(d)施行两段顶出.5)设置滑动件之顶出板图39为刮料板与顶出梢同时作用, (a)之直下方有滑动件, 由于此滑动件之移动, 顶出板在作用过程中, 刮料板停止作用,施行两段顶出.再者,(a)及(b)之接触面必需光滑.顶出板超前退回机构使用分模及侧向心型之型模中, 装有顶出梢者, 开模之际, 顶出梢必需在滑动件退回之前确实先行退回,否则两者发生冲突而破损.1)弹簧法图40为应用弹簧作顶出板之超前退回机构, 此种场合型模构造及加工最为简单, 装置位置亦小.但顶出梢者有发生住之场合, 使超前退回作用不确实, 滑动件与顶出梢冲突, 型模破损. 再者, 顶出冲程大者, 弹簧压缩比变大, 使用相当强度之弹簧, 顶出板在作用过程中亦不超前退回, 尽量避免作用.2)环节法图41示使用环节,作用确实,不致发生故障,但由固定侧伸出之作用杆(a)长度长,必需装置于成形品取出无妨碍之处所.3)游戏杆法图42示使用游戏杆之场合,起其优点及缺点与使用环节者相同.但当顶出板复归完了时,及必需解脱,.更需对定时调节注意.4)齿轮法图43所示使用齿轮之场合,作用确实,与环节法相同,有关成形品之取出考虑,必需与环节法及游戏杆法相同,与其它方法相异点为顶出板之作用,往复运动等由齿条实施,必需考虑顶出板顶出作用之稳定.5)油压缸法此种方法之机构之优点及缺点为:在两段顶出场合,作用确实,定时亦可自由调节; 缺点为装置复杂.。
经典模具结构原理动图,模具的滑块机构、顶出机构原理动图

经典模具结构原理动图,模具的滑块机构、顶出机构原理动图1. 二级推出机构2. 可折叠型芯-三维3. 可折叠型芯-平面4. 侧向分型与抽芯机构-滑块-15. 侧向分型与抽芯机构-滑块-26. 侧向分型与抽芯机构-滑块-37. 侧向分型与抽芯机构-滑块-48. 侧向分型与抽芯机构-滑块-59. 侧向分型与抽芯机构-滑块-610. 侧向分型与抽芯机构-滑块-711. 单分型面注射模示意图12. 双分型面注射模示意图13. 模架与镶件-C型14. 滑块脱模-外螺纹15. 推板推出16. 推杆推出-加强筋17. 推杆推出-斜面18. 推管顶出19. 推块推出-120. 推块推出-221. 延迟推出22. 圆推杆顶出23. 斜导柱侧抽芯-开模行程24. 单推板二次脱模机构-摆块拉板式25. 单推板二次脱模机构-弹簧式26. 单推板二次脱模机构-斜导柱-滑块式27. 弹簧先复位机构28. 定模设置推出机构的注射模示意图29. 分型面-垂直分型面30. 分型面-阶梯分型面31. 分型面-平面、曲面分型面32. 分型面-水平分型面33. 复位杆复位34. 改变合模线位置-范例35. 合模销定位36. 活动镶件示意图37. 浇口数量和位置对熔接痕的影响38. 开设冷料槽以增加熔接强度39. 气阀式引气-140. 气阀式引气-241. 气阀推出机构42. 推板脱模结构形式-143. 推板脱模结构形式-244. 推板脱模结构形式-345. 推板与型芯的配合形式46. 推杆推出机构形式-147. 推杆推出机构形式-2免责声明:本文系网络转载或改编,未找到原创作者,版权归原作者所有。
如涉及版权,请联系删除。
加入【制造交流圈】领5000个机械视频;领1000个机械动图,领5000个机械图纸;领上千G 机械资料,和机械老兵学机械。
模具顶出设计
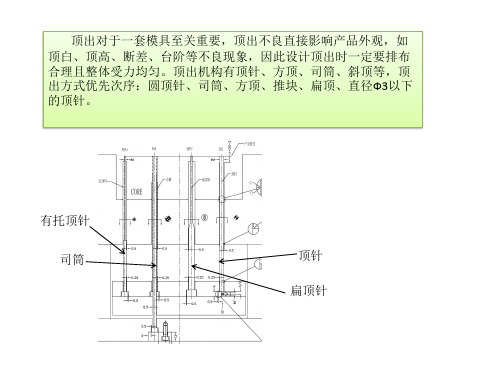
出模比较困难的地方,排放顶针时要注意产品的大小,尽量将产品 做大,规格做少,放在筋位旁的顶针要注意距离筋位1~2MM,直径 Ф3以下的顶针需用有托顶针,Ф4及以上顶针一般直接在深孔钻直 接加工到位。
方顶针一般用在产品有深筋位(20MM以上)不利于圆顶针顶出时, 一般加在筋位下部紧贴筋位侧壁,方顶顶出时一般会加防滑槽便于顶出, 在排位方顶时要注意放在筋位同侧,防止顶出时因产品收缩导致产品包 在方顶上造成产品难取。模仁上方顶孔需要先加工穿丝孔后线割加工到 位,订购方顶时要注意方顶托长防止顶出干涉。
司筒针
扁顶针具有深筋位无法下方顶时需在筋位下部下扁顶针,
因扁顶针强度较弱,尽量避免使用,订购扁顶针时托长要尽量 加长以增强其强度,但也要注意避空避免开模后顶出干涉。
当产品顶出只能在产品周边,且无法用推板顶出时用推块顶出, 推块四面拔1°~5°斜度,推块用螺丝与顶杆固定,顶杆材料为SKD61, 直接附螺牙图订购,推块一般用两个顶杆,起到防转作用,当只能用 一个顶杆时则要注意顶杆与推块之间加D型定位。推块订料时订一整 块料,先加工最后线割外形。
顶出对于一套模具至关重要,顶出不良直接影响产品外观,如
顶白、顶高、断差、台阶等不良现象,因此设计顶出时一定要排布 合理且整体受力均匀。顶出机构有顶针、方顶、司筒、斜顶等,顶 出方式优先次序:圆顶针、司筒、方顶、推块、扁顶、直径Ф3以下 的顶针。
有托顶针 司筒
顶针 顶针
圆顶针顶出是顶出系统最常用的机构,在设计顶出时,要注意
推块
当产品一圈深筋位且只能在内侧下顶出时,由于一圈若下
直顶会导致产品收缩后包在直顶上导致产品难取,此时需把直 顶改为小角度斜顶便于产品脱模,设计此类斜顶时要注意产品 收缩,斜顶行程要足够脱模,直顶基准平台比产品筋位端面要 高5MM左右以便保证筋位端面平整。
模具顶针结构
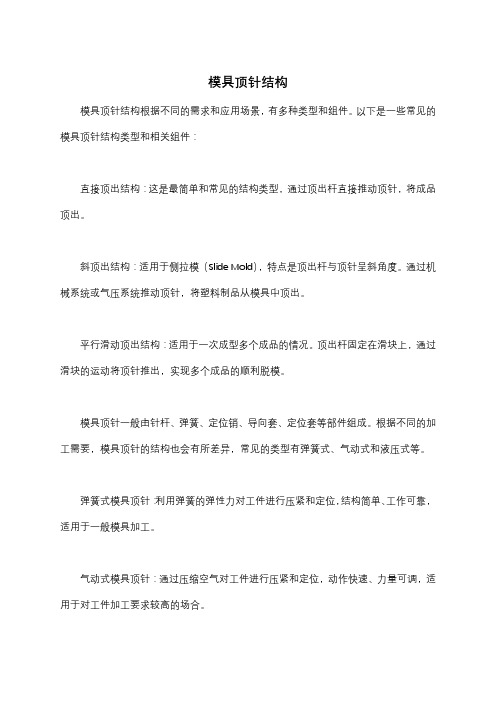
模具顶针结构
模具顶针结构根据不同的需求和应用场景,有多种类型和组件。
以下是一些常见的模具顶针结构类型和相关组件:
直接顶出结构:这是最简单和常见的结构类型,通过顶出杆直接推动顶针,将成品顶出。
斜顶出结构:适用于侧拉模(Slide Mold),特点是顶出杆与顶针呈斜角度。
通过机械系统或气压系统推动顶针,将塑料制品从模具中顶出。
平行滑动顶出结构:适用于一次成型多个成品的情况。
顶出杆固定在滑块上,通过滑块的运动将顶针推出,实现多个成品的顺利脱模。
模具顶针一般由针杆、弹簧、定位销、导向套、定位套等部件组成。
根据不同的加工需要,模具顶针的结构也会有所差异,常见的类型有弹簧式、气动式和液压式等。
弹簧式模具顶针:利用弹簧的弹性力对工件进行压紧和定位,结构简单、工作可靠,适用于一般模具加工。
气动式模具顶针:通过压缩空气对工件进行压紧和定位,动作快速、力量可调,适用于对工件加工要求较高的场合。
防粘夹顶针结构:包括模仁、上顶出板、下顶出板和常规顶针。
该结构还包括防粘夹顶针组件,包括防粘夹针杆和限位弹簧。
这种结构能够防止在脱模过程中顶针粘住或夹住产品,同时结构简单,制造成本低。
除了上述几种类型,还有圆顶针顶出、带托顶针顶出、扁顶针顶出、司筒针顶出、直顶(块)顶出、斜顶(块)顶出、推板顶出、气顶顶出、油缸顶出等几种形式。
每种形式都有其特定的适用场景和优缺点。
在实际应用中,需要根据产品特点和生产需求选择合适的模具顶针结构类型。
《模具顶出机构概要》课件
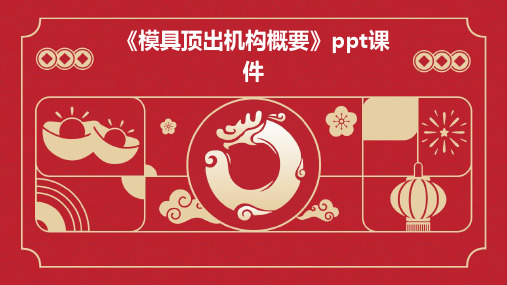
控制优化
引入智能控制技术,实现 顶出机构的自动化和智能 化控制,提高生产效率和 产品质量。
03 模具顶出机构的制造与装配
CHAPTER
制造工艺流程
粗加工
对模具顶出机构的各个零部件 进行粗加工,初步形成其基本 形状和结构。
精加工
对热处理后的零部件进行精加 工,使其达到设计图纸要求的 尺寸和精度。
备料
校核顶出机构强度和刚度
对顶出机构进行强度和刚度校核,确 保其在使用过程中具有足够的稳定性 和耐久性。
优化设计
根据校核结果,对顶出机构进行优化 设计,提高其性能和可靠性。
优化与改进
01
02
03
结构优化
通过改进顶出机构的结构 设计,提高其稳定性和可 靠性,减少故障率。
材料优化
选用高强度、耐磨、耐腐 蚀的材料,提高顶出机构 的使用寿命。
该机构采用伺服电机或步进电机驱动,具有高精度、高速度、高稳定性的特点。
通过采用先进的控制系统和传感器技术,可实现自动化生产,提高生产效率和产品 质量。
案例三:某大型注塑模具顶出机构
大型注塑模具顶出机构适用于 生产大型塑料制品,如家具、
建筑材料等。
该机构采用液压或气压驱动 ,具有大行程、大负载、高
稳定性的特点。
外观检测
对模具顶出机构的外观进行检 测,确保其表面光滑、无瑕疵 。
性能检测
对模具顶出机构进行性能检测 ,包括工作行程、推力、耐久 性等,确保其满足设计要求。
不合格品处理
对检测不合格的零部件进行返 工或报废处理,确保最终产品
的质量符合要求。
04 模具顶出机构的应用与案例分析
CHAPTER
应用领域与范围
汽车制造
模具顶出方式的种类

顶出装置•成形品之顶出•有螺纹之成形品取出方法•点状浇口之主注到道一流道之顶出•两段顶出•顶出板超前退回机构为使射出成形能率及成形品质量提高﹐亦有必要施行自动运转﹐为此必需能使注道﹐流道及成形品自动而确实脱模﹒再者﹐少量生产之制品﹐型模制作日数及价格有所限制﹐亦由于成形品形状及浇口之种类不能自动脱模之场合﹐此际可决定成形品及注道﹐流道最容易脱模之顶出机构﹒同一形状之成形品亦由于材料种类及浇口形式之不同顶出方法亦随之异﹐必需将最适当之方法组合使用﹒成形品之顶出成形品顶出方法之决定﹐当然受成形品材料及形状等所左右﹐但原则上在成形品上制成缺口﹐阶层等﹐使能形成最确实之脱模﹐并且故障较少﹐再都故障发生之场合必需能简单补修﹒同一形状之成形品亦因由于外表﹐精度﹐成形性不同﹐而变化使用之顶出方法﹒顶出方法一般使用顶出梢(直梢﹐阶段梢)﹐筒套﹐刮料板﹐空气等﹐单独使用或组合使用﹐则视型模之寿命长短,型模加工之难易选定之﹒(1)顶出之种类1)顶出梢梢之加工最为容易﹐必需硬度之场合﹐施行淬火磨削等亦较其它方法为容易﹐可在成形品之任意位置上配置﹐为使用最多者﹒孔之加工容易﹐精度亦能达规定﹐滑动抵抗最小﹐契住发生少﹒因之型模寿命长﹐互换性使在破损之际﹐补修可以容易﹒然而在小面积上顶出﹐顶出应力集中于成形品之局部﹐杯类及箱形物品之退缩倾斜小﹐脱模抵抗大之成形品上﹐将发生压陷及顶穿等﹐此种场合﹐使用顶出梢大多不适当﹒2)方形或板状顶出梢板状顶出板等件之加工﹐热处理等并无困难点﹐但孔之加工困难﹐需要使用放电加工等特殊加工﹒将型范本及心型部份分割﹐形成组合型﹐加工变为容易﹐但制造工时增加﹐成形品由于有分割线﹐对透明件之外观有不良影响﹐亦有不允许之场合﹒再者﹐滑动抵抗亦较,圆梢为多﹐板之厚度较薄﹐容易引起弯折及挫屈﹐在可能限度中避免使用﹒3)套筒套筒之加工性比较良好﹐但套筒内径小而长度长者﹐加工较难﹐使用于肉薄件容易发生开裂﹒由于套筒之端面全面顶出﹐成形品顶出均一﹐能形成确实脱模﹐成形品开裂较少发生﹒4)刮料板刮料板及心型之加工并不比顶出梢为难﹐滑动面机械加工及配合则需要较多时间﹐滑动面契合部必需淬火﹐热处理为困难﹒再者﹐互换性亦趋向不良﹐修补必需较多人工﹒刮料板与心型配合面形状为圆形或方形者﹐机械加工及配合加工比较容易﹐但如为连续变化之曲线形者﹐则变为困难﹒再者﹐为使施行淬火后仍保有互换性﹐使用衬套嵌入﹐使补修容易﹐特别有数个型穴者﹐可仅将破损单件换调﹒刮料板与其它顶出方法比较﹐为顶出面积广大﹐成形品能确实脱模﹐对脱模抵抗较大之杯类及帽类之成形品脱模有效﹐广泛应用﹒再者﹐外观上几无顶出痕迹显示﹐此亦为优点之一﹒5)空气压出方法空气压出方法为设置阀等﹐将空气通入隙间﹐加工较为简单﹐对杯类及箱形等深度较大之成形品之脱模为极有效之方法﹒(2)顶出机构之实例图1为仅使用顶出梢之场合﹒顶出梢位置应配置于脱模抵抗强度较大之处﹐如脱模抵抗强度均一之场合﹐则应均等配置﹒图中所示之杯类及箱形成成形品﹐其侧面抵抗最大﹐最佳情形将顶出梢配置于此﹐再者﹐如于内侧面设置顶出梢场合﹐配置于侧壁附近较优于中央部份﹐否则将使顶出时容易引起开裂﹒图2为含有细而深之凸毂及加强肋之场合﹐使用顶出梢在其周围顶出﹐则发生开裂﹐容易使成形品破损报废﹐顶出梢必需设置于凸毂及加强肋底部﹐使能确实脱模﹒图3为阶层顶出梢之使例﹐由于无法使用细小顶出梢于小型成形品之场合﹐由于中段较粗﹐挫屈降低﹒图4为顶出梢与刮料板并用之一例﹐心型内面脱模抵抗较大部份﹐如仅用刮料板脱模﹐可能有列为断残留﹐为防止此种疵病发生﹐设置顶出梢﹐成为刮料板为主﹐顶出梢为补助之场合﹒此种场合﹐顶出梢设置于心型之内﹐形成心型冷却故障﹐使用小直径心型可作直接冷却﹐能消除此项缺点﹐必需考虑成形品之形状﹐使设置顶出梢之可能性消除﹐亦且能脱模﹒图5所示为部份之脱模抵抗较强(退缩倾斜少而深),如管状凸起场合﹐使用顶出梢在其周缘部及内面顶出时﹐成形品亦有开裂﹐皮用套筒顶出﹐以顶出梢为主﹐套筒为补助之机构﹒图6与图4﹒图5作相同之考虑﹐为刮料板及套筒并用之例﹒图7为深管状成形品之内外周具嵌入于可动侧之场合﹐在成形品端面使用用套筒顶出最为有效﹒图8示长套筒加工困难﹐短套套筒加工容易之例﹒一般情形﹐对盆形成形品顶出﹐大多使用图9之刮料板顶出﹐如使用图10所示之斜盆端顶出梢则加工简单﹒并且使用刮料板对心型冷却﹐亦如图4.图5之情形相同﹒有缺点存在﹒图11﹒图12为利用空气压出之情形﹒对大平面﹐深﹐肉薄之成形品(箱﹐杯等)使用刮料板顶出时﹐成形品可能引起挫屈﹐再者﹐成形品与心型间形成真空﹐使成形品破碎﹒使用于聚乙烯等软质材料场合破碎程度更为显著﹐此种场合使用空气压出最为有效﹐图11为仅使用空气者﹐图12为使用刮料板并在心型间有气压出方法之一例﹒有螺纹之成形品取出方法成形品有螺纹场合﹐脱模方法有下列三种﹒1) 型模螺纹部分模2)型模螺纹部置入嵌入件﹒3)成形品在型模螺纹部回转﹒(1)型模螺纹部分模此种方法适合于外螺纹(阳螺纹之型模构造﹐制造亦较简单﹐能确实脱模)﹒但成形品螺纹部有挤入分模线之废边产生﹐成形品之后加工﹐与契合件之配合形成故障﹒(2)型模螺纹部置入嵌入件型模构造不能使用分模及回转旋出者﹐型模构造简单之场合可使用置入嵌合件法﹒但使用此法时﹐成形品顶出后﹐必需将嵌入件取下﹐成形品为外螺纹之场合﹐由于收缩﹐取出容易﹐但如为内螺纹之场合﹐则置入之嵌入件与成形品之接角面积大﹐取出不易﹐由于成形品之材料及接触面积大取出困难﹒(3)成形品在型模螺纹部回转之场合一般盖件等为有内螺纹之成型品﹐大多使用回转自动旋出﹒此咱场合﹐成形品与型模任一件回转﹐并作退出运动﹐或一件仅作回转﹐他件退出运动﹐但对成形品必需有滑动定位(回转止动).成形品外周滑动定位﹐有点状浇口之型模﹐开模同时开始回转之场合﹐成形品与型模螺纹部之脱模﹐由于分模面之压开﹐分模面脱模抵抗大﹐成形品螺纹发生破断﹒为使能防止此项疵病﹐螺纹退出作用之速度﹐必需设计与分模线开模机构之速度相同﹒再者﹐在成形品螺纹部以外有脱模抵抗较强处所之场合﹐与回转开始之同时﹐必需有相同速度之顶出作用﹒回转伤虽在型模之固定侧及可动侧中俱可设置﹐但一般成形机设置于喷嘴及顶出机构之反对侧﹐由于注道﹐流道之配置及顶出关系﹐回转机构设置于可动侧﹐在型模构造上及成形能率上具属有利﹒1)成形品外周有滑动定位之场合图13为外点状浇口﹐图14为内点状浇口﹐俱使用特殊之顶出梢﹐刮料板等将其顶出﹐于开模间螺纹(a)回转纹数次后﹐在型穴中或心型上脱离﹐成形品自然落下﹒图15为成形品滑动定位及型模心型等位置于可动侧之场合﹐回转终了﹐成形品顶出H及h段﹐脱模落下﹒如图所示﹐H>h之场合﹐必需装置顶出梢(b)之顶出机构﹒图13~15所示适用于脱模时﹐浇口自动切断者﹐侧向浇口之场合﹐流道与成形品同时移动﹐必需设置同速之顶出机构﹒2)成形品内面有滑动定位之场合图16为内侧平面部有滑动定位﹐(a)一面回转﹐一面移动﹐当螺纹模之后﹐滑动定位仍然附着﹐必需另装除去装置﹐使成形件能自行落下﹒图17为内侧面有滑动定位之外螺纹场合﹐(a)回转﹐依成形品螺纹之螺距﹐将螺纹旋出﹐然后必需使用顶出梢(b)将其顶出﹒图18﹐图19内侧面有滑动定位﹐仅有(a)回转而(b)固定, 螺纹旋出脱模后,经由刮料板将其顶出. 刮料板之作用,有使用顶出梢, 弹簧等各种方法.3)成性形品端面有滑动定位之场合图20, 图21所示之成形品端面俱有滑动定位上, 为使其能自然落下, 必需另装顶出装置(a). 小型成形品而有侧向浇口之场合, 不能将成形品直接顶出, 需与流道一并顶出,再者无不需特别设置滑动定位, 可用浇口作为端面设置之滑动定位. 但对软质材料之场合, 如无相当大之浇口, 有剪断之可能.4)一面回转,一面作往复运动之小齿轮连结方法图22 示一面回转一面作往复运动之心型@与小齿轮直接连结, 图23示@与使用间接连结. 往复运动之滑动扺抵抗, 图23 者较小, 能圆滑作用,往复冲程较大, 图22中则强度较为良好, @中设质有心型梢之场合,与图22 所用者并物无差异.5)螺纹心型之驱动方法图24, 25利用开模冲程者.图26, 图27设置有油压及电动机等各别之动力者, 其优点为回转开始,停止等之时点能自由控制, 但必需有动力操纵装置. 成形品螺栓回转数多之场合, 图27 所示之驱动方法为最良好者.点状浇口之主注到道一流道之顶出侧向浇口在成形面中有流道一浇口之场合, 成形品可与之同时脱落,自然脱落容易,但点状浇口等场合, 自然脱落困难.图28 所示无流道剥离机构之场合, 必需以手工脱模. 型模构造最为简单, 但成形能率低, 少量生产以外场合不予使用.图29 为设置有流道刮料板, 但在剥离状态, 注道部分悬挂于流道刮料板孔中, 不能自然脱落, 此种情形应在A部设置顶出稍, 必要时使用空气压力将其压脱.图30 所示为较简单之构造,完成加工工数较少,流道长L比l为大,如l 深于以上场合,流道浮起时,形成嵌入于型范本策侧状态,不能自然脱落.再者,冷却时间长之场合,流道一部分弯折,一都度浮起之浇口部颁,仍将弹回退入于型范本侧.再者, A部颁有纵向庞旁边发生, 此等处所附着而不脱落. 此外, 成形品配置于注道之直下者, 注道定位稍不能装置, 使不适使用. 但无需使用弹簧及引长装置等装置, 并于开模同时, 浇口即可切断等利点.图31之优点及缺点大致相同,使图30中之A部不附着,流道之一部嵌入于型范本侧,亦能体度浮起脱落.但是注道顶出稍较可动侧装接板为长甚大,不能使用于无中心部顶出杆孔之成形机, 及中心顶出孔不够深之成形机上.图32 为钢笔套等细长成形品所用者, 在固定侧型模板内设置顶出板, 经由顶出梢将流道顶出, 此仅使用于限定之成形品形状.两段顶出(1)用途使用刮料板顶出场合, 刮料板内侧将成形品凸缘部顶出, 此部份仍与刮料板粘着, 必需更有任何方法将此自成形品上去除. 此种情形时, 为时能形成自动脱模, 必需有两段顶出机构.图33示刮料板与顶出梢之方法, 图34为将有凹陷之成形品, 使用两组出板, 作两段顶出, 使形成强制顶出之例.两段顶出之场合, 两组顶出冲程必需有所差异, 冲程大侧同同时或较迟作用.成性机顶出机构为压力缸及其附件, 以及定位杆及其附件, 前者之场合, 一方由固定侧, 使用螺杆,炼条及环等, 依开模冲程引长, 另一方由成形机之顶出机构作用, 能形成两段顶出作用.但后者场合, 两组必需由同一方向作两段顶出, 两组顶出机构必需有顶出冲程定时及冲程调节机构.(2)两段顶出之定位及冲程调节机构1)弹簧法图35为顶出之一方经由弹簧作用者,制造容易,安装位置小,为最简单之机构. 但不能承受过大之力,作用不确实.2)压力缸法图36 为使用压力缸代替弹簧, 作用确实, 定时能自由调节. 但安装位置较大, 成形机及型模较小时不能使用, 再者, 油压泵及空气压缩机必需有专用之控制设施.3)凸轮法图37示使用凸轮代替弹簧及压力缸, 作用确实,无须需其它附属设施.但由固定侧伸出之凸轮挺杆,必需安装对成形品取出无妨碍处所.4)夹颚法图38示(a), (b)两组顶出板, (a)组直接由(c)顶出, (a)组以夹颚(d)与(a)连结, 在作用行程中经(d)施行两段顶出.5)设置滑动件之顶出板图39为刮料板与顶出梢同时作用, (a)之直下方有滑动件, 由于此滑动件之移动, 顶出板在作用过程中, 刮料板停止作用,施行两段顶出.再者,(a)及(b)之接触面必需光滑.顶出板超前退回机构使用分模及侧向心型之型模中, 装有顶出梢者, 开模之际, 顶出梢必需在滑动件退回之前确实先行退回,否则两者发生冲突而破损.1)弹簧法图40为应用弹簧作顶出板之超前退回机构, 此种场合型模构造及加工最为简单, 装置位置亦小.但顶出梢者有发生住之场合, 使超前退回作用不确实, 滑动件与顶出梢冲突, 型模破损. 再者, 顶出冲程大者, 弹簧压缩比变大, 使用相当强度之弹簧, 顶出板在作用过程中亦不超前退回, 尽量避免作用.2)环节法图41示使用环节,作用确实,不致发生故障,但由固定侧伸出之作用杆(a)长度长,必需装置于成形品取出无妨碍之处所.3)游戏杆法图42示使用游戏杆之场合,起其优点及缺点与使用环节者相同.但当顶出板复归完了时,及必需解脱,.更需对定时调节注意.4)齿轮法图43所示使用齿轮之场合,作用确实,与环节法相同,有关成形品之取出考虑,必需与环节法及游戏杆法相同,与其它方法相异点为顶出板之作用,往复运动等由齿条实施,必需考虑顶出板顶出作用之稳定.5)油压缸法此种方法之机构之优点及缺点为:在两段顶出场合,作用确实,定时亦可自由调节; 缺点为装置复杂.。
模具前模顶出的简易结构

模具前模顶出的简易结构
模具前模顶出的简易结构包括圆顶针顶出、带托顶针顶出、扁顶针顶出和司筒针顶出。
1. 圆顶针顶出:在所有的注塑模具中99%都会使用到圆顶针,根据模具设计的标准,选择国产正钢、MISUMI、HASCO、PUNCH的标准规格进行设计,区别在于每个厂家的挂台深度和挂台直径不同。
如果圆顶杆的直径不是以0和5的整数,可以在标准件厂家,指定参数进行订做。
如果前端有异形也可以给予3D形状进行订做。
顶针在顶出产品时,需要承受压缩压力,有可能会发生折断或者弯曲,所以顶针要保证足够的抗压强度和抗弯曲度。
顶针所使用的材料要保证在模具长时间顶出,强度一般都会好于于模仁的材料,通常使用SKH51、SKD61、SKD61+氮化、SKD61+预硬。
2. 带托顶针顶出。
3. 扁顶针顶出:根据产品形状,当产品的边缘位置或者很深的骨位无法放置圆顶针的时候,采用扁顶针顶出。
4. 司筒针顶出:司筒分为三部分组成:司筒针、推管、固定司筒针的压板(丝锥)。
模具顶出机构概要
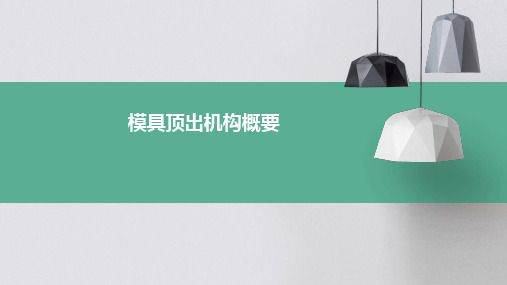
某铝合金门窗生产企业采用压铸模具生产铝合金型材,通过改进顶出机构,减少了残次品率。
冲压模具案例
某不锈钢厨具生产企业采用冲压模具生产厨具部件,优化顶出机构后,提高了生产效率和材料利 用率。
未来发展趋势
01
智能化
随着工业4.0和智能制造的推进,模具顶出机构的智能化将成为未来发
展的趋势。通过引入传感器、执行器和控制系统,实现顶出机构的自动
模具顶出机构概要
$number {01}
目 录
• 模具顶出机构简介 • 模具顶出机构设计 • 模具顶出机构制造工艺 • 模具顶出机构应用与案例 • 模具顶出机构常见问题与解决方
案
01
模具顶出机构简介
定义与作用
定义
模具顶出机构是指在塑胶模具中 ,将成型后的产品从模具型腔中 顶出的装置。
作用
在塑胶模具中,顶出机构的主要 作用是将成型后的产品从模具型 腔中顶出,以便进行后续的脱模 操作。
制造流程
设计
根据模具的需求和设计要求,进 行顶出机构的结构设计、尺寸计 算和零件排布。
热处理
对顶出机构的各个零件进行热处 理,以提高其机械性能和使用寿 命。
粗加工
对顶出机构的各个零件进行粗加 工,包括切割、打孔、铣削等, 以满足后续装配的需求。
精加工
对顶出机构的各个零件进行精加 工,包括研磨、抛光等,以获得 所需的尺寸和表面质量。
加强操作人员的培训和指导
确保操作人员熟悉模具的操作和维护要求,正确 使用和保养模具。
THANKS
模具顶出机构制造工艺
制造材料
1 3
钢材
钢材是制造模具顶出机构的主要材料,具有高强度、耐磨性 和耐腐蚀性。常用的钢材有碳素钢、合金钢和不锈钢等。
模具N种顶出结构解说
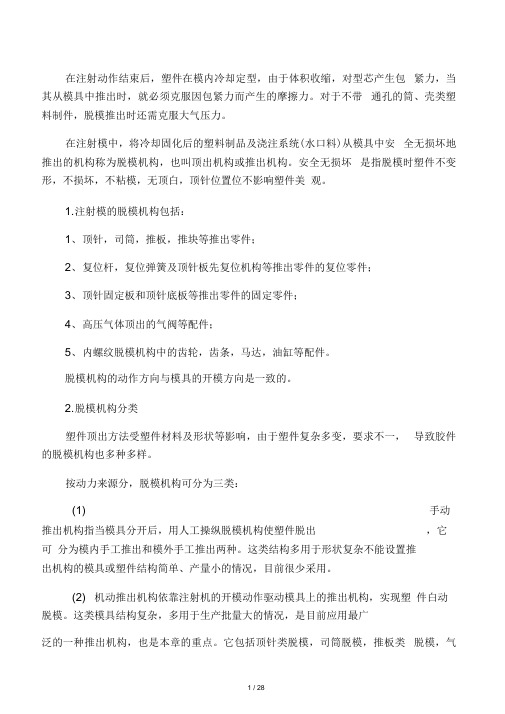
在注射动作结束后,塑件在模内冷却定型,由于体积收缩,对型芯产生包紧力,当其从模具中推出时,就必须克服因包紧力而产生的摩擦力。
对于不带通孔的筒、壳类塑料制件,脱模推出时还需克服大气压力。
在注射模中,将冷却固化后的塑料制品及浇注系统(水口料)从模具中安全无损坏地推出的机构称为脱模机构,也叫顶出机构或推出机构。
安全无损坏是指脱模时塑件不变形,不损坏,不粘模,无顶白,顶针位置位不影响塑件美观。
1. 注射模的脱模机构包括:1、顶针,司筒,推板,推块等推出零件;2、复位杆,复位弹簧及顶针板先复位机构等推出零件的复位零件;3、顶针固定板和顶针底板等推出零件的固定零件;4、高压气体顶出的气阀等配件;5、内螺纹脱模机构中的齿轮,齿条,马达,油缸等配件。
脱模机构的动作方向与模具的开模方向是一致的。
2. 脱模机构分类塑件顶出方法受塑件材料及形状等影响,由于塑件复杂多变,要求不一,导致胶件的脱模机构也多种多样。
按动力来源分,脱模机构可分为三类:(1) 手动推出机构指当模具分开后,用人工操纵脱模机构使塑件脱出,它可分为模内手工推出和模外手工推出两种。
这类结构多用于形状复杂不能设置推出机构的模具或塑件结构简单、产量小的情况,目前很少采用。
(2) 机动推出机构依靠注射机的开模动作驱动模具上的推出机构,实现塑件白动脱模。
这类模具结构复杂,多用于生产批量大的情况,是目前应用最广泛的一种推出机构,也是本章的重点。
它包括顶针类脱模,司筒脱模,推板类脱模,气动脱模,内螺纹脱模及复合脱模。
(3)液压和气动推出机构一般是指在注射机或模具上设有专用液压或气动装置,将塑件通过模具上的推出机构推出模外或将塑件吹出模外。
按照模具的结构特征分,脱模机构可分为:一次脱模机构、定模脱模机构、二次或多次脱模机构、浇注系统水口料的脱模机构、带螺纹塑件的脱模机构等。
3. 对脱模机构的要求模具打开时,塑件必须留在有顶出机构的半模上。
由于注射机的推杆在安装后模的一侧,所以注射模的顶出机构一般在后模。
单元2--模具顶出机构概要-new
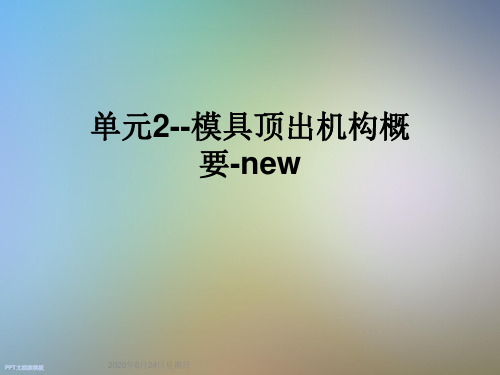
頂出機構運用-縲紋退出機構
•利用齒條與油壓缸退 出螺紋
•利用電動機與蝸輪退 出螺紋
cover圓銷鋼材探討
•Φ0.45m m
•Φ1.04m m
•cover 圓 銷
•cover
cover圓銷鋼材探討
•日本規格簡易認識法
•日本工業規格 (JIS) 所規定者,主要係由下列三部份構成(亦即金屬符號之命名方法)
•(1)在成品轂部頂出以避免成品破裂。 •(2)頂針過細時在中段加粗以避免挫屈。
•轂部頂 出
•中段加粗的頂 針
頂出機構運用-套筒之運用
•成品多半為環狀,頂出力量均勻,但長度長 者加工不易。
•套筒頂 出
•特殊套筒頂 出
頂出機構運用-脫料板頂出
•成品不易擺放頂針,或成品脫模力較大時。 •其頂出面積較大,但配合滑動面不易配合。
單元總結
••1.頂出法原則: •• 模具頂出的裝置很多,但均需注意到不使 成 • 形品產生破裂或擦傷,並能正確迅速脫模 與 • 減少故障並容易更換或修補。一般為頂出 銷、 • 套筒、脫料板、空氣壓等,單獨使用或組 合 • 使用,則視模具壽命長短,或加工難易而 定。
• 2.必須嚴格要求協力廠商,按照圖面材質及 硬 • 度施工,以符合原設計要求。
•(1)最前面的英文字母代表鋼材,如 S.....鋼
•(2)後面的英文字母代表合金成份 (構造用鋼)如CM.....鉻鉬鋼或鋼種名稱 (工具鋼)
• 如 K.....工具
•(3)最後阿拉伯數字代表含碳量(構造用鋼)或類別 (工具鋼)
• 例: 構造用鋼
•
S
CM
440
•
|
|
|
•
|
|
鋼種含碳量
- 1、下载文档前请自行甄别文档内容的完整性,平台不提供额外的编辑、内容补充、找答案等附加服务。
- 2、"仅部分预览"的文档,不可在线预览部分如存在完整性等问题,可反馈申请退款(可完整预览的文档不适用该条件!)。
- 3、如文档侵犯您的权益,请联系客服反馈,我们会尽快为您处理(人工客服工作时间:9:00-18:30)。
在注射动作结束后,塑件在模内冷却定型,由于体积收缩,对型芯产生包紧力,当其从模具中推出时,就必须克服因包紧力而产生的摩擦力。
对于不带通孔的筒、壳类塑料制件,脱模推出时还需克服大气压力。
在注射模中,将冷却固化后的塑料制品及浇注系统(水口料)从模具中安全无损坏地推出的机构称为脱模机构,也叫顶出机构或推出机构。
安全无损坏是指脱模时塑件不变形,不损坏,不粘模,无顶白,顶针位置位不影响塑件美观。
1. 注射模的脱模机构包括:1、顶针,司筒,推板,推块等推出零件;2、复位杆,复位弹簧及顶针板先复位机构等推出零件的复位零件;3、顶针固定板和顶针底板等推出零件的固定零件;4、高压气体顶出的气阀等配件;5、内螺纹脱模机构中的齿轮,齿条,马达,油缸等配件。
脱模机构的动作方向与模具的开模方向是一致的。
2. 脱模机构分类塑件顶出方法受塑件材料及形状等影响,由于塑件复杂多变,要求不一,导致胶件的脱模机构也多种多样。
按动力来源分,脱模机构可分为三类:(1)手动推出机构指当模具分开后,用人工操纵脱模机构使塑件脱出,它可分为模内手工推出和模外手工推出两种。
这类结构多用于形状复杂不能设置推出机构的模具或塑件结构简单、产量小的情况,目前很少采用。
(2)机动推出机构依靠注射机的开模动作驱动模具上的推出机构,实现塑件自动脱模。
这类模具结构复杂,多用于生产批量大的情况,是目前应用最广泛的一种推出机构,也是本章的重点。
它包括顶针类脱模,司筒脱模,推板类脱模,气动脱模,内螺纹脱模及复合脱模。
(3)液压和气动推出机构一般是指在注射机或模具上设有专用液压或气动装置,将塑件通过模具上的推出机构推出模外或将塑件吹出模外。
按照模具的结构特征分,脱模机构可分为:一次脱模机构、定模脱模机构、二次或多次脱模机构、浇注系统水口料的脱模机构、带螺纹塑件的脱模机构等。
3. 对脱模机构的要求模具打开时,塑件必须留在有顶出机构的半模上。
由于注射机的推杆在安装后模的一侧,所以注射模的顶出机构一般在后模。
这种模具结构简单,动作稳定可靠。
(特殊情况也用倒推模,此时塑件开模后必须留在前模。
塑件粘前模的原因大致如下:1、制品尺寸较大,形状如盒形,帽形或壳形,前模无进气装置,开模时前模型腔和制品间形成真空;2、分型面设计不合理,塑件对前模的粘附力大于对后模的沾附力;3、前模型腔抛光不够,或抛光方法不对(一定要沿出出模方向抛光);4、前模型腔脱模斜度太小;5、分型面在中间的板状或片状塑件(如唱片,碟子等),很易粘前模。
防止塑件在顶出时变形或损坏。
正确分析塑件对型芯的包紧力和对模腔的粘附力的大小及其所在部位,有针对性地选择合适的脱模方式,使顶出力施于塑件对模具包紧力大及能够承受顶出力的部位。
顶出时若型芯和塑件之间形成真空,没有必要的进气装置,也容易将塑件顶变形甚至破裂。
结构合理,工作稳定可靠。
顶出机构应顶出可靠,复位准确,运动灵活,制造方便,更换容易,且具有足够的强度和刚度。
顶出机构在顶出时要和模具发生摩擦,良好的顶出机构应使其磨损最小,寿命最高。
为减少顶针和司筒等磨损,宜增加顶针板导柱(EGP )。
顶针板导柱又叫中托边,其设计方法见第十二章《注射模具导向定位系统的设计》。
位置合理,顶出安全模具的顶针要设置于塑件包紧力最大的地方,且不能和冷却系统,侧向抽芯机构,撑柱,螺钉等发生干涉。
中间保持钢位3〜5mm。
顶出行程合理,制品可自由落下顶出机构必须将塑件完全推出,完全推出是指制品在重力作用下可自由落下。
顶出行程取决于制品的形状。
对于锥度很小或没有锥度的制品,顶出行程等于后模型芯的最大高度加5〜10mm的安全距离。
对于锥度很大的制品,顶出行程可以小些,一般取后模型芯高度的〜之间即可。
顶出行程受到模胚方铁高度的限制,方铁高度已随模胚标准化。
如果顶出行程很大,方铁不够高时,应在订购模胚时加高方铁高度,并在技术要求中写明。
4. 脱模机构的设计原则制品顶出是注射成型过程中的最后一个环节,顶出质量好坏将直接影响制品的质量,设计时应遵循以下原则。
1)顶针位置设计的一般原则:1、顶出要平衡,顶针必须均匀布置,以防顶出后胶件变形。
2、应注意塑件的美观性,尽量将顶针布置在产品装配后看不到的部位的地方,这一点对于透明制品尤其重要。
要知道,任何顶针都会在胶件上留下痕迹,而且随着顶针在生产过程中的不断磨损,这种痕迹会越来越明显。
3、顶针应落在最有利于成品出模,即脱模力最大的地方;顶出力必须施加于胶件的最底点,将胶件推出,而不是拉出。
见下图:4、顶出力必须作用在制品能承受最大顶出力的部位,即刚性好,强度最大的部位.如壁边,骨位、柱位下面,壳体侧壁,作用面积也尽可能大一些(即尽可能选直径大的顶针),以防塑件变形或损坏。
尽量避免受力点作用于制品薄平面上,防止制品破裂,穿孔,顶白等。
如筒形制品弃用顶针顶出而选择推板顶出。
5、为防止制品变形,受力点应尽量靠近型芯或难于脱模部位,如细小的柱位与骨位。
7、顶针尽量布置于胶件的拐角处。
8、顶针应尽可能对称布置。
9.在有滑块侧抽芯和斜滑块的模具中,顶针尽量布置于侧抽芯或斜滑块在分模面的投影面之外。
如无法避免,则要加顶针先复位机构。
顶针先复位机构图详见本章第节。
10、为方便水口脱落,在水口转角处应落水口顶针。
11、啤PP料及K料可采用垃圾钉顶出。
啤ABS等其它塑胶,当顶出力很小且成品上不允许留有顶针痕迹时,也可以采用垃圾钉顶出。
12、顶针应尽量落在较平的地方,如果落顶针处斜度较大,顶针应磨成阶梯状以增大顶出力,或在不影响功能的情况下加大箭脚或顶针柱。
13、局部胶位较深时,由于脱模力大,轻易顶白或顶穿,在不影响功能的前提下,顶针应傍骨,加头箭脚或出顶针柱。
傍骨或出顶针柱时,顶针一般用或,大件成品且胶位较厚时亦可采用顶针。
14、成品上有较深凹位时,一般在内骨底落或顶针出顶针柱或跟客户要求主骨两测傍骨出顶针柱。
15、螺丝柱、定位柱等深孔部位一般落司筒或在柱两侧傍骨出顶针柱。
实心柱底要落顶针,可以防止困气,也可以防止火花加工(EDM )时积碳。
16、顶针边离胶位边一般应有1—2mm 距离,当顶针傍柱位骨位顶出时,顶针边离胶位边不应超过2mm 距良,当顶针位钢料低于周边钢料时,顶针边离胶位边可以作到0.5mm 距离 ;17、PVC 料不宜顶垃圾钉及分流道不能直冲型腔。
但 PVC 等软胶的公仔模 (铍铜模、雕刻模 )一律采用顶垃圾钉的方式出模,顶针大小为或。
垃圾钉应落在 公仔较平整无花纹的部位,方便披水口,且顶出要平衡垃圾针要离开胶位边 2mm 以上。
18、顶针与撑头及运水之间最少要保证有 3—4mm 的钢位。
19、顶针图的标数采用坐标标注法,基准要和模具排位图的基准一致。
顶 针标数要准确且要拿整数,最多可给一位小数。
要小心顶针破边,一般顶针边 离胶位边应有 1—2mm 距离。
2)顶针大小设计的一般原则:3. 料,加工.(如5mm 舆6mm,可以的话选用其中一种)。
4.顶出零件和型芯的配合为间隙配合,配合公差为H7/f7。
配合长度10〜20mm 。
5. 每一套模具顶针直径尺寸不宜太多种,否则加工时需频频换刀,既浪费时 间也容易出错。
3)顶针数量设计的一般原则:顶针的数量往往取决于经验。
一般情况下,顶针数量越多,顶出效果就越 好,但不必要的顶针会提高模具的制作成本。
因此在保证胶件能可靠顶出的情 况下,应尽可能减少顶针的数量。
但对于经验不足的工程师,本人建议,在不1.因为下列理由,顶针外径应尽量取较大值 1)防止因射出压力而弯曲。
2)防止因脱模阻力而弯曲、破损。
3)防止白化。
2.在大平面上不宜用小顶针。
在不影响制品脱模和位置足够时应尽量采用同一型号大小顶针,以方便开影响外观及运水布置的情况下,顶针宁多勿少。
因为如果在试模时发现胶件顶白或变形,再增加顶针会非常麻烦。
但宁多勿少并非滥用,而是当你在X 根和X+1根之间犹豫不决时,你就用X+1根。
4)顶针设计的其它原则:1、能用顶针则不用司筒,能用圆顶针则不用扁顶针。
原因很简单,司筒和扁顶针制造成本高,且易磨损,寿命不如圆顶针,维修也不便。
2、当塑件上不允许有顶针印时,可在产品周边适当位置加辅助垃圾钉顶出6-9 所示)。
3、顶针与后模镶件的间隙应小于所啤塑料的溢边值。
各种塑料的溢边值见第一章《塑料及其注塑成型工艺》。
4、注意整体布局均匀,特殊情况要考虑采用多种顶出装置.如:斜顶,司筒针,推板,二次强行脱模,油缸拉动,气体顶出等复合脱模。
5、顶出件不能兼作型芯。
6、有方向性要求的顶针,司筒头要做(磨)单边或双边管位以防止转动。
7、当在斜面或曲面上配置时,顶针必须防转,且顶针顶端要加胶线防止出现顶滑现象。
8、避免因真空吸附而使胶件产生顶白、变形,可采用复合脱模或用透气钢排气,如顶杆与推板或顶杆与顶块脱模,顶杆适当加大配合间隙排气,必要时还可设置进气阀。
5.顶针脱模顶针包括圆顶针,扁顶针及异形顶针。
其中圆顶针推出时运动阻力小,推出动作灵活可靠,损坏后也便于更换,因此在生产中广泛应用。
圆顶针推出机构是整个推出机构中最简单、最常见的一种形式。
扁顶针截面是长方形,加工成本高,易磨损,维修不方便。
异形顶针是根据胶件推出位的形状而设计的,如三角形,弧形,半圆形等,因加工复杂,很少采用,此处不作探讨。
1)圆顶针圆顶针是最简单,最普通的顶出装置.圆顶针与顶针孔都易于加工,因此已被作为标准件广泛使用。
圆顶针有无托顶针和有托顶针二种。
顶针直径在©2.5以下而且位置足够时要做有托顶针,大于©2.5 都做无托顶针。
见图。
1、圆顶针优点是:(1)制造加工方便,成本底。
圆孔钻削加工,比起其它形状的线切割或电火花加工,要快捷方便得多。
另外,圆形顶针是标准件,购买很方便,相对于其它顶针,它的价钱最便宜。
(2)阻力小。
可以证明,面积相同的截面,以圆形截面的周长最短,因此摩擦阻力最小,磨损也最小。
3)维修方便。
圆形顶针尺寸规格多,有备件,更换方便。
2、圆顶针缺点:顶出位置有一定的局限性。
对于骨位,胶件边缘,及狭小的槽,布置圆顶针有较困难,若用小顶针,几乎没有作用。
3、圆顶针位置设计1)顶针布置顺序:四周、加强筋、Boss孔(套筒或两支顶针)。
顶针不能太靠边,要保持1.2mm 以上的钢位。
(2)对于表面不能有顶针印的产品,可在产品周边适当位置加辅助垃圾钉顶出(6-9 所示)(3)顶针尽可能避免设置在高低面过渡的地方;顶针尽量不要放在镶件拼接处,若无法避免,可将顶针对半做于二个镶件上,或在二镶件间镶圆套。
如下图。
4)顶针可以顶螺丝柱(Boss):低于20mm 以下的螺丝柱,如果旁边能够下顶针的话可以不用司筒,而在其附近对称加两支顶针。
见图。
5)顶针可以顶骨位:顶骨位的顶针一般用直径或者,但这样的话,骨位二边会增加一些胶位, 须征得客户同意,且要保证:①不影响产品的装配和使用功能;② 不能导致制品表面缩水,如图6-7 所示图加顶针。