高炉水渣脱水效果的分析
炼铁高炉总结反思
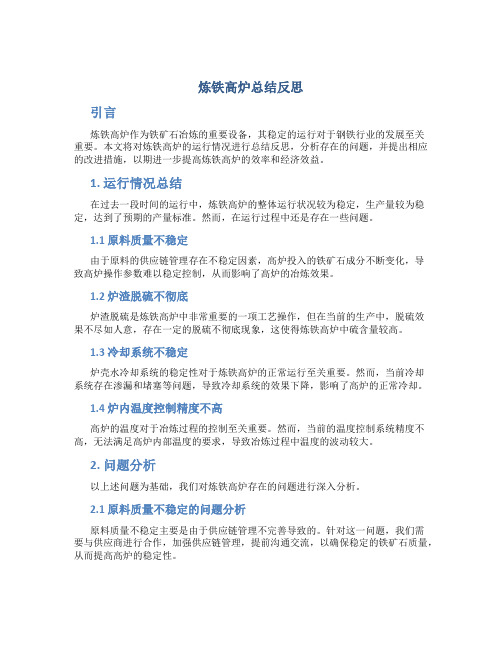
炼铁高炉总结反思引言炼铁高炉作为铁矿石冶炼的重要设备,其稳定的运行对于钢铁行业的发展至关重要。
本文将对炼铁高炉的运行情况进行总结反思,分析存在的问题,并提出相应的改进措施,以期进一步提高炼铁高炉的效率和经济效益。
1. 运行情况总结在过去一段时间的运行中,炼铁高炉的整体运行状况较为稳定,生产量较为稳定,达到了预期的产量标准。
然而,在运行过程中还是存在一些问题。
1.1 原料质量不稳定由于原料的供应链管理存在不稳定因素,高炉投入的铁矿石成分不断变化,导致高炉操作参数难以稳定控制,从而影响了高炉的冶炼效果。
1.2 炉渣脱硫不彻底炉渣脱硫是炼铁高炉中非常重要的一项工艺操作,但在当前的生产中,脱硫效果不尽如人意,存在一定的脱硫不彻底现象,这使得炼铁高炉中硫含量较高。
1.3 冷却系统不稳定炉壳水冷却系统的稳定性对于炼铁高炉的正常运行至关重要。
然而,当前冷却系统存在渗漏和堵塞等问题,导致冷却系统的效果下降,影响了高炉的正常冷却。
1.4 炉内温度控制精度不高高炉的温度对于冶炼过程的控制至关重要。
然而,当前的温度控制系统精度不高,无法满足高炉内部温度的要求,导致冶炼过程中温度的波动较大。
2. 问题分析以上述问题为基础,我们对炼铁高炉存在的问题进行深入分析。
2.1 原料质量不稳定的问题分析原料质量不稳定主要是由于供应链管理不完善导致的。
针对这一问题,我们需要与供应商进行合作,加强供应链管理,提前沟通交流,以确保稳定的铁矿石质量,从而提高高炉的稳定性。
2.2 炉渣脱硫不彻底的问题分析炉渣脱硫不彻底主要是由于脱硫工艺操作不当导致的。
我们需要加强脱硫工艺的研究与改进,优化脱硫剂的选择与添加方式,提高脱硫效果,减少炉内硫含量。
2.3 冷却系统不稳定的问题分析冷却系统不稳定主要是由于冷却系统的设计和维护不当导致的。
我们需要对冷却系统进行全面检查和维护,修复渗漏和堵塞问题,确保冷却系统的正常运行,提高高炉的冷却效果。
2.4 炉内温度控制精度不高的问题分析炉内温度控制精度不高主要是由于温度控制系统的精度不足导致的。
转鼓法高炉渣处理技术研究

转鼓法高炉渣处理技术研究张海斌1① 奉京蕾2(1:中钢设备有限公司 北京100080;2:北京国冶锐诚工程技术有限公司 北京100080)摘 要 研究转鼓法渣处理技术对高炉炉渣进行处理,能否达到节约用水的目的。
采用高炉水渣经粒化塔冲渣沟进入转鼓,通过转鼓进行渣水分离,通过增加熔渣沟长度、采用冲制箱极速水流水淬等方法转鼓分离高炉炉渣,并分析炉渣渣水比和吨耗水率,可以明显得出运用转鼓法高炉渣处理技术的项目,渣水比和吨耗水率都有明显优化,本项目通过改进转鼓法渣处理技术对高炉炉渣处理方法进行工艺技术研究,可以达到节约用水节约能源的目的,符合国家持续发展要求,供大家参考。
关键词 高炉;炉渣;转鼓法;渣处理中图法分类号 TF703.6 文献标识码 ADoi:10 3969/j issn 1001-1269 2024 02 010ResearchonBlastFurnaceSlagTreatmentTechnologybyRotaryDrumMethodZhangHaibin1 FengJinglei2(1:ChinaSteelEquipmentCo.,Ltd.,Beijing100080;2:ChinaMetallurgicalEngineeringTechnologyCo.,Ltd.,Beijing100080;)ABSTRACT Thepurposeofsavingwateristostudywhethertheslagtreatmenttechnologyofrotarydrummethodcanbeusedtotreattheblastfurnaceslag.Theblastfurnaceslagentersthedrumthroughtheslagflushingditchofthegranulationtower,andtheslag waterseparationiscarriedoutthroughthedrum,thentheblastfurnaceslagisseparatedfromtherotarydrumbyincreasingthelengthoftheslagditch,usingthemethodofextremelyfastwaterflowandwaterquenchingofthepunchingbox,andanalyzingtheslagwaterratioandtonwaterconsumptionrate,itcanbeclearlyconcludedthatthisprojectusingtherotarydrumblastfurnaceslagtreatmenttechnology,theslag waterratioandtonwaterconsumptionratehavebeensignificantlyoptimized.Thisprojectconductstechnicalresearchontheblastfurnaceslagtreatmentmethodbyimprovingthedrummethodslagtreatmenttechnology,toachievethepurposeofsavingwaterandenergy,whichmeetstherequirementsofnationalsustainabledevelopment,foryourreference.KEYWORDS Blastfurnace;Slag;Rotarydrum;Slagtreatment1 前言高炉熔渣是高炉炼铁的主要副产品之一,高炉熔渣的处理方法主要分为干渣和水渣两种,本文主要对高炉水渣进行研究。
论炉渣脱水综合利用技术改造的经济性

论炉渣脱水综合利用技术改造的经济性张家口发电厂除渣系统通过设备和工艺系统的技术改造,通过新增加#1-#4炉渣浆转排、脱水、浓缩澄清、回水复用系统,以及完善#5-#8炉渣脱水仓系统,基本实现向灰场的灰水零排放,脱水后的渣用汽车运至用户销售或灰场储存,以达到提高灰渣综合利用效益、节水节电、延长灰场的使用期限、改善灰场周围环境的综合目的。
标签:炉渣脱水综合利用技术改造节能降耗一、前言张家口发电厂有发电机组八台,总装机容量2560MW,年排总灰渣量110万t左右。
原除灰系统采用灰渣混除、水力输送方式,分别经各单元的灰浆泵直接排至灰场。
全部灰渣浆没有经过任何浓缩设施的处理,就直接排至灰场,灰渣浆输送浓度低,水电消耗量大,运行维护费用高;灰场污染严重,对灰场附近居民生活及生产影响比较大。
为解决除灰系统存在的问题,降低用水量,提高系统运行效益,改善周围环境,在对原除灰系统进行详细调研和全面测试基础上,提出了详细的改造方案,并得到大唐国际的批准。
改造后的除灰系统于2008年5月通过调试正式投入运行,实际运行表明,改造后的新系统达到了预期的最终目标,即:灰渣分除、干除灰、水除渣厂内脱水、销售剩余的灰渣运至灰场碾压储存,基本实现向灰场的灰水零排放。
经济效益和社会效益十分显著。
二、工艺系统改造及设备更新1.系统简介改造前,全厂除灰系统共分4个单元,每2台炉为1个单元。
总体来讲,除灰系统均为灰渣混除、水力输送至灰场方式。
#1-#4炉的除灰系统分为2个单元,其中:#1、#2炉为一单元,#3、#4炉为二单元,2个单元的除灰系统基本相同。
以一单元为例,工艺系统及配置的主要设备描述如下:#1、#2炉底各设2台捞渣机,渣经捞渣机后,沿渣沟自流出主厂房,至一单元灰浆泵房前池。
电除尘器的干灰通过灰斗下的搅拌器制成灰浆后进入灰沟,自流向一单元灰浆泵房前池,在入前池前与渣浆混合在一起,通过灰浆泵、管道,直接排至灰场。
灰浆泵采取2台串联为1组的运行方式,泵房内共设置3组,1组运行,另外2组备用,其中在第二级灰浆泵设液力偶合器调速(型号YOTGC750,输入转速1000r/min,功率范围150-440kw。
港陆高炉水渣“脱白”技术方案

港陆高炉水渣“脱白”技术方案港陆高炉水渣是一种含有高浓度铁的固体废弃物,通常会被用于做路面铺设。
但由于水渣中铁的含量非常高,所以造成了对环境的潜在威胁。
为了减轻对环境的影响,需要采用一种高效的处理技术,将水渣中的铁分离。
一种常用的方法是采用“脱白”技术,这种方法需要通过化学反应将水渣中的铁离子还原成固态铁,然后通过机械分离技术将固态铁分离出去。
下面是一个港陆高炉水渣“脱白”技术方案的详细介绍:1. 原材料准备首先需要准备好需要处理的港陆高炉水渣,这个需要确定处理的数量和质量,以便计算使用的化学药剂和工作时间。
2. 化学药剂配制脱白技术需要使用化学药剂来将水渣中的铁还原成固态铁。
常用的化学药剂有硫酸和氧化铁。
配制化学药剂的过程需要掌握正确的比例和浓度,以确保反应的有效性。
3. 反应槽设计反应槽是进行化学反应的关键设备。
设计反应槽需要考虑到反应温度、反应时间、反应物质的浓度等因素。
反应槽需要保持一定的压强和温度,并且需要配备搅拌装置以确保反应均匀。
此外,反应槽还需要设计成易于清洗和维护。
4. 反应过程将配制好的化学药剂倒入反应槽,并加入一定量的水渣。
在高温和高压的条件下,化学药剂会与水渣中的铁离子进行反应,将其还原成固态铁。
反应时间一般需要几小时到几天不等,具体取决于反应物质的浓度和反应槽的大小。
5. 固体分离反应结束后,需要将反应液中的固态铁分离出去。
这一步需要使用一定的机械设备以及过滤网等分离材料。
固态铁可以用于冶金行业或者建筑材料行业。
6. 残留液处理反应液中可能还存在一些化学药剂和其他杂质。
这些残留液需要进行处理,以避免对环境造成污染。
处理方法可以选择将残留液浓缩后进行焚烧处理,也可以选择将其作为无害化处理后的废水直接排放。
综上所述,港陆高炉水渣“脱白”技术方案是一种高效且环保的处理方法。
通过化学反应和机械分离等技术,可以将水渣中的铁分离出来,对环境造成的影响可以得到有效的减轻。
此外,该技术通过回收固态铁也具有一定的经济效益。
钢铁企业高炉冲渣水余热利用技术分析

钢铁企业高炉冲渣水余热利用技术分析摘要:随着社会经济快速发展,钢铁行业取得了巨大进步,这对于促进我国工业化水平提升起到了重要的推动作用。
但是钢铁企业在工业生产中的能耗较大,而且在生产过程中还会产生大量余热,如果不能合理利用,则会导致能源损耗严重,不利于保障企业的可持续发展。
对此,针对高炉冲渣水余热进行科学利用对于帮助钢铁企业降低能耗并实现能源节约,同时促进自身绿色环保发展具有重要意义。
本文主要分析了钢铁企业生产中高炉冲渣水余热的特点,并出了具体的余热利用技术,以期为钢铁企业余热科学利用提供指导。
关键词:钢铁企业;高炉冲渣水;余热利用在钢铁企业生产过程中,高炉冲渣水属于低温性的废热源,其具有温度稳定而且流量大的特点,如果将此项资源直接浪费掉,不仅会给钢铁企业造成极大损失,同时也会对周边环境造成极大污染。
为了更好地利用高炉冲渣水余热,就必须要积极探索其具备的特点,并基于此分析可利用的方向,从而提高余热利用效能,为钢铁企业带来更大经济效益,也为其后续高质量发展提供基础支持。
一、钢铁企业高炉冲渣水余热特点1、余热资源潜力大高炉冲渣水具有低温余热热点,虽然温度不高,但由于流量庞大,成为了重要的能源回收点[1]。
例如在一个年产铁量达250万吨的大型高炉中,每小时可产生高达2200立方米的循环冲渣热水,等量冲渣水热负荷估计达到40兆瓦,由此可见其巨大的能源回收潜力,若能高效利用低温余热,不仅能显著降低能源消耗,还能减轻环境热污染。
目前,冲渣热水通过冷却后循环使用或自然降温,其间大量热能未被充分利用,如果能开应用高效的热能回收和利用技术如热泵系统或低温余热发电技术等,可以有效转换热能为发电或供暖等其他用途,不仅对钢铁企业降低能源成本和提升环保水平有着重要意义,也对推动整个工业领域的绿色转型和可持续发展具有积极影响。
2、具有强腐蚀性在现代钢铁生产过程中,为应对日益严格的环保标准,许多钢铁厂开始循环利用各工序产生的含盐废水作为高炉冲渣用水,虽然有效减少了废水排放,但却使得冲渣水的腐蚀性显著增强。
“一键式”INBA冲渣在莱钢3200m3高炉上的研究与应用

“一键式”INBA冲渣在莱钢3200m3高炉上的研究与应用摘要:INBA渣处理技术是引进卢森堡Paul Wurth(PW)公司的一种新型高炉熔渣处理工艺,可以将高炉炉渣转为高品位的水泥原材料,实现炉渣的再生利用,是集经济效益、社会效益与环保效益于一体的高炉水渣处理新技术。
关键词:一键式冲渣;脱水转鼓;自控技术;环保节能概述高炉炉渣是高炉炼铁的主要副产品之一。
在传统的高炉冶炼工艺中,未经过处理的炉渣一般作为废弃物运出厂区废弃,不仅浪费资源,而且污染环境。
所以选择一种运行可靠、配套合理、综合经济效益好的炉渣处理系统妥善处理炉渣,充分开发炉渣的经济价值是极为重要的。
现代渣处理主要是采用水力冲渣的方式将高炉炼铁产生的热态炉渣冲制成水渣的一种技术。
这样不仅可以解决高炉炉渣产生的环境污染问题,更重要的是,水渣还可以作为生产水泥、混凝土、隔热填料、矿渣微粉等的主要原料,可获得可观的经济效益。
1.研究内容INBA系统具有设备复杂、布置紧凑、工艺成熟的特点,因此对自动化程度要求非常高。
为了使这项技术能取得良好的运用效果,本文结合工艺和实践,实现将INBA渣处理法应用于莱钢3200m3高炉的目标,对系统实现综合自动控制,主要研究系统全自动控制——“一键式”INBA冲渣的实现,并自动计算渣流量,技术上主要根据现场实际实现脱水转鼓变频、变频冷却泵的自动调速,使水渣能够高效、方便的粒化、脱水、冷却、运输,在控制上给操作人员带来极大的方便,使系统达到节约用水,环保的目的。
系统主要分为三大部分:皮带连锁启停,水循环连锁以及脱水转鼓控制。
(1)按照工艺,程序要实现渣运输皮带逆启顺停的控制。
(2)INBA水循环系统主要分为粒化水路、冷凝水路以及再循环水路,要分别实现系统的单机控制与自动启停,实现INBA主循环,即转鼓皮带、转鼓电机、再循环泵、粒化泵、冷却泵、冷却塔等设备的“一键式”连锁自动控制。
另外,INBA渣处理的冷凝系统和皮带也实现了“一键式”操作。
高炉炼铁四种炉渣处理工艺

高炉炼铁四种炉渣处理工艺现代高炉炼铁生产中,比较成熟的炉渣的处理工艺有圆盘法、图拉法、因巴伐及明特克法四种。
其中图拉法是将炉渣机械破碎后,再进行水淬,其它三类是将炉渣直接水淬。
1.圆盘法(RD)圆盘法最显著的特点是:圆盘脱水器转速较慢,因此圆盘的脱水时间长,水渣含水率低(≤10%),回水质量好,无尾渣处理。
设备上冲制箱可调节冲渣的角度,可使粒化更充分,避免了传统水淬渣易爆炸的问题。
此外对处理的渣要求较低,对渣带铁不限制、无需设干渣坑;同时处理的效果较好,可以解决漂浮在沉淀池表明上的浮渣及泡沫渣。
圆盘法利用圆盘脱水,作业率高、处理能力大、布置紧凑,可以实现整个流程机械化、自动化,其次,检修、维护简便,维护成本低。
市场前景看好。
2.图拉法(TYNA)图拉法最显著的特点是彻底解决了传统水淬渣易爆的问题,安全性高。
熔渣处理过程在封闭的状态下进行,环保;利用转鼓脱水,循环水量少、能耗低;此外对处理的渣要求也较低,当带铁高达40%时,仍可安全生产。
图拉法存在的两个主要缺陷是:1)返渣率高,使水系统磨损严重。
2)配套要求高,会出现不完整情况下,循环水量激增,脱水器设备尺寸欠妥。
3.因巴法(INBA)因巴法布置紧凑、占地面积小,可实现整个流程机械化、自动化,水渣质量好;冲渣水系统闭路循环,无外加水悬浮物,泵和管路的磨损小;此外该法的另一个优点是能彻底解决烟尘、蒸汽对环境的污染,达到零排放。
因巴法是利用转鼓脱水的工艺。
图拉法存在的三个主要缺陷是:1)引进技术,投资费最大。
2)转鼓滤网使用过短;转鼓容易停转。
3)粒化泵容易卡死,产生事故。
4.明特克法(MTC)明特克法采用提升脱水,是国内拥有自主知识产权的工艺方法,其设备投资省,备件消耗少,运行成本低;占地面积小,布置灵活;脱水效果较好,水渣含水率低(≤15%);系统采用变频系统控制;冲渣水为净水闭路循环使用,该法存在的主要问题是:1)浮渣无法解决,循环水含渣率高,使水系统设备管路磨损严重。
炼铁高炉水渣循环再利用技术研究综述

炼铁高炉水渣循环再利用技术研究综述摘要:作为钢铁生产中的重要环节,高炉炼铁的实际情况受到关注,其主要是由古代竖炉炼铁发展改进而来,主要目标是将自然界的铁矿石还原成生铁。
虽然世界各国研发了多种多样的炼铁法,但是高炉炼铁技术仍然受到关注,其凭借着简单工艺、良好的技术经济指标等成为首选。
本文将对高炉炼铁展开分析,了解水渣循环再利用的技术,旨在提供借鉴。
关键词:高炉炼铁;水渣;循环再利用;技术研究钢铁在楼层建造和铁路建设中均扮演着重要角色,属于不可或缺的资源。
在钢铁制造中,一般涉及到两个基本流程,其中之一就是高炉炼铁,这是我国重点使用的炼铁工艺。
近些年,随着该项技术的蓬勃发展,自动化、高效化和大型化趋势明显,低污染、低消耗、低成本成为了主要目标。
在高炉炼铁中,除了关注实际效率外,还要重视水渣的妥善处理,应通过可靠手段将其变废为宝。
一、炼铁高炉水渣概述水渣主要是指炼铁高炉矿渣,在高温熔融状态下,经过水的急速冷却而形成粒化泡沫形状。
水渣呈现乳白色,质轻且松脆,多孔、易磨成细粉。
水渣一般涵盖着渣池水淬和炉前水淬两种方式,可以被当做建材运用至生产水泥和混凝土的过程中。
在石灰、石膏等的作用下,水渣能够充当优质的水泥原料,最终制成石灰矿渣水泥和石膏矿渣水泥等,属于相对环保的原材料。
对于水渣循环再利用时,应该明确其基本特点,还要根据具体的情况加以总结,让相关的技术展示出自身价值,保证为循环再利用提供支撑条件。
以首钢京唐公司为例,其自主建设了矿渣超细粉生产线,可以将高炉炼铁中产生的水渣进一步加工,使其变为矿渣超细粉。
现阶段运用到的矿渣超细粉已成功运用到京沪高铁、承唐高速等重点工程。
二、炼铁高炉水渣循环再利用意义水渣也被称作炼铁高炉矿渣,属于高炉炼铁的副产品,在水泥行业叫矿粉,重点涵盖着渣池水淬和炉前水淬两种方式【1】。
因其危害性突出,所以在实际处理的过程中需要消耗大量的人力物力及财力资源,难以在看到效益成果。
现阶段,水渣的作用被发掘,其在多个行业展示出自身影响力,如经过磨粉机的处理,可以搭配石灰或者是石膏等激发剂生成性能优良的水泥原料。
高炉冲渣水余热利用现状分析
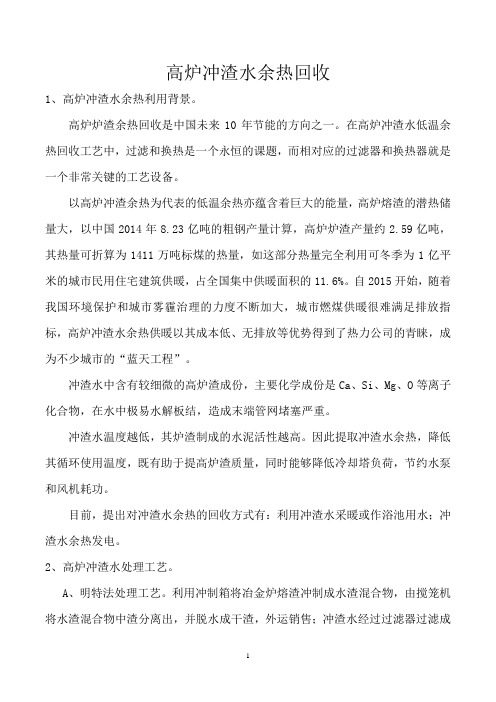
高炉冲渣水余热回收1、高炉冲渣水余热利用背景。
高炉炉渣余热回收是中国未来10年节能的方向之一。
在高炉冲渣水低温余热回收工艺中,过滤和换热是一个永恒的课题,而相对应的过滤器和换热器就是一个非常关键的工艺设备。
以高炉冲渣余热为代表的低温余热亦蕴含着巨大的能量,高炉熔渣的潜热储量大,以中国2014年8.23亿吨的粗钢产量计算,高炉炉渣产量约2.59亿吨,其热量可折算为1411万吨标煤的热量,如这部分热量完全利用可冬季为1亿平米的城市民用住宅建筑供暖,占全国集中供暖面积的11.6%。
自2015开始,随着我国环境保护和城市雾霾治理的力度不断加大,城市燃煤供暖很难满足排放指标,高炉冲渣水余热供暖以其成本低、无排放等优势得到了热力公司的青睐,成为不少城市的“蓝天工程”。
冲渣水中含有较细微的高炉渣成份,主要化学成份是Ca、Si、Mg、O等离子化合物,在水中极易水解板结,造成末端管网堵塞严重。
冲渣水温度越低,其炉渣制成的水泥活性越高。
因此提取冲渣水余热,降低其循环使用温度,既有助于提高炉渣质量,同时能够降低冷却塔负荷,节约水泵和风机耗功。
目前,提出对冲渣水余热的回收方式有:利用冲渣水采暖或作浴池用水;冲渣水余热发电。
2、高炉冲渣水处理工艺。
A、明特法处理工艺。
利用冲制箱将冶金炉熔渣冲制成水渣混合物,由搅笼机将水渣混合物中渣分离出,并脱水成干渣,外运销售;冲渣水经过过滤器过滤成干净水,由冲渣泵循环供冲制箱冲渣使用。
明特法水渣处理系统作为第三代水渣处理技术(即水渣领域的最新技术),其主要特点是彻底克服渣池法(第一代水渣处理技术:平流法、侧滤法、底滤法)、转鼓法(第二代水渣处理技术:INBA、图拉法)的不足,以全自动化方式对水渣进行处理。
即通过操作员的一个按钮动作,使水渣的分离自动完成,实现从设备出来的渣为干渣;出来的水为干净水,直接循环使用。
B、嘉恒法处理工艺。
由高炉放出的高温熔渣经熔渣沟流到出铁厂平台边缘的冲制箱前方,被冲制箱喷出的急速水流水淬,形成渣水混合物。
炉渣脱水器溢水原因分析及治理
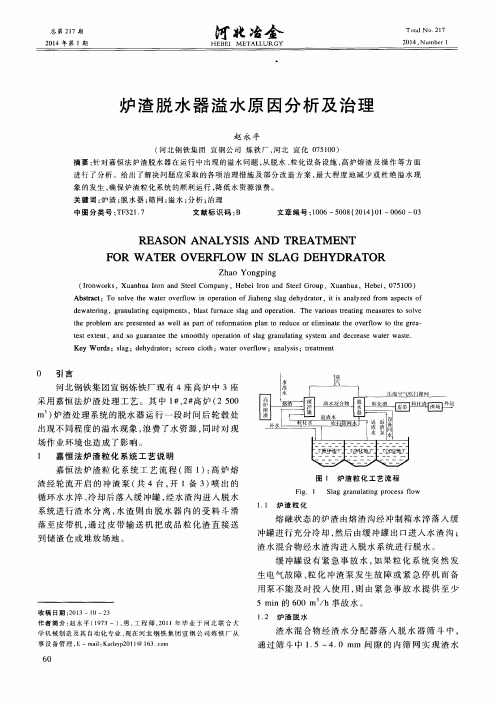
t e s t e x t e nt ,a n d S O g u a r a nt e e t h e s mo ot h l y op e r a t i o n o f s l a g g r a n u l a t i ng s y s t e m a n d d e c r e a s e wa t e r wa s t e . Ke y W o r d s: s l a g;d e hy d r a t o r ;s c r e e n c l o t h;w a t e r o ve r lo f w ;a na l y s i s;t r e a t me nt
Abs t r a c t :To s ol v e t h e wa t e r o ve r lo f w i n o p e r a t i o n o f J i a h e n g s l a g d e h yd r a t or ,i t i s a na l yz ed f r o m a s pe c t s of de wa t e r i ng,g r a n ul a t i ng e q u i p me n t s,bl a s t f u r na c e s l a g a nd o pe r a t i on . Th e va r i o us t r e a t i n g me a s u r e s t O s ol ve
1 嘉恒 法 炉渣粒 化 系统 工艺说 明
嘉 恒法 炉渣粒 化 系统 工 艺 流 程 ( 图 1 ) : 高 炉 熔 渣 经轮 流开 启 的 冲渣 泵 ( 共 4台 , 开 1备 3 ) 喷 出 的 循 环水 水淬 、 冷却 后落 入缓 冲罐 , 经水 渣 沟进入 脱 水 系统进 行渣 水分 离 , 水 渣 则 由脱 水器 内 的受 料 斗 滑
高炉渣处理技术的现状和新的发展趋势 好文
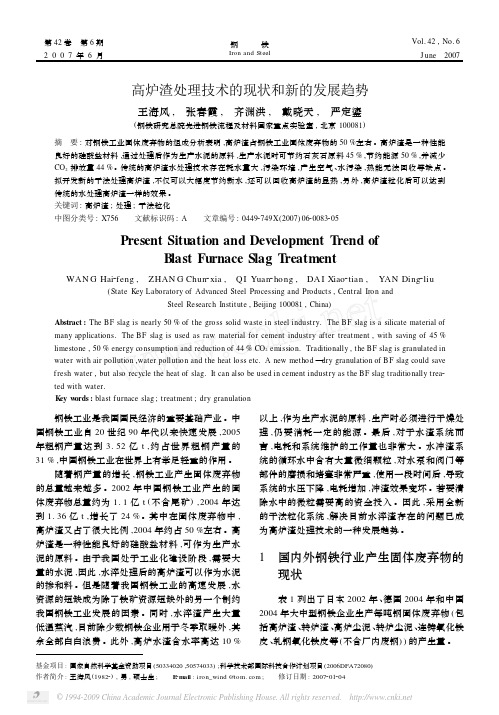
第42卷 第6期 2007年6月钢铁Iron and Steel Vol.42,No.6J une 2007高炉渣处理技术的现状和新的发展趋势王海风, 张春霞, 齐渊洪, 戴晓天, 严定鎏(钢铁研究总院先进钢铁流程及材料国家重点实验室,北京100081)摘 要:对钢铁工业固体废弃物的组成分析表明,高炉渣占钢铁工业固体废弃物的50%左右。
高炉渣是一种性能良好的硅酸盐材料,通过处理后作为生产水泥的原料,生产水泥时可节约石灰石原料45%,节约能源50%,并减少CO 2排放量44%。
传统的高炉渣水处理技术存在耗水量大,污染环境,产生空气、水污染,热能无法回收等缺点。
拟开发新的干法处理高炉渣,不仅可以大幅度节约新水,还可以回收高炉渣的显热,另外,高炉渣粒化后可以达到传统的水处理高炉渣一样的效果。
关键词:高炉渣;处理;干法粒化中图分类号:X756 文献标识码:A 文章编号:04492749X (2007)0620083205Present Situ ation and Development T rend ofB last Furnace Slag T reatmentWAN G Hai 2feng , ZHAN G Chun 2xia , Q I Yuan 2ho ng , DA I Xiao 2tian , YAN Ding 2liu(State Key Laboratory of Advanced Steel Processing and Products ,Central Iron andSteel Research Institute ,Beijing 100081,China )Abstract :The BF slag is nearly 50%of the gross solid waste in steel industry.The BF slag is a silicate material of many applications.The BF slag is used as raw material for cement industry after treatment ,with saving of 45%limestone ,50%energy consumption and reduction of 44%CO 2emission.Traditionally ,the BF slag is granulated in water with air pollution ,water pollution and the heat loss etc.A new method —dry granulation of BF slag could save fresh water ,but also recycle the heat of slag.It can also be used in cement industry as the BF slag traditionally trea 2ted with water.K ey w ords :blast f urnace slag ;treatment ;dry granulation基金项目:国家自然科学基金资助项目(50334020,50574033);科学技术部国际科技合作计划项目(2006DFA72080)作者简介:王海风(19822),男,硕士生; E 2m ail :iron_wind @ ; 修订日期:2007201204 钢铁工业是我国国民经济的重要基础产业。
高炉炉渣处理方法(二篇)

高炉炉渣处理方法1.概述:高炉熔渣处理方法主要分为出干渣和水淬渣,由于干渣处理环境污染较为严重,且资源利用率低,现在已很少使用,一般只在事故处理时,设置干渣坑或渣罐出渣;目前,高炉熔渣处理主要采用水淬渣工艺,水渣可以作为水泥原料,或用于制造渣砖、轻质混凝土砌块,使资源得到合理的利用。
1.1水淬渣的按其形成过程,可以分为两大类:A:高炉熔渣直接水淬工艺。
脱水方法主要有渣池法或底滤法、因巴法、拉萨法及笼法等。
其主要工艺过程是高炉熔渣渣流被高压水水淬,然后进行渣水输送和渣水分离。
B:高炉熔渣先机械破碎后水淬工艺。
主要代表为图拉法和HK法等。
其主要工艺过程是高炉熔渣流首先被机械破碎,在抛射到空中时进行水淬粒化,然后进行渣水分离和输送。
1.2按水渣的脱水方式可分为:A:转鼓脱水法。
经水淬或机械粒化后的水渣流到转鼓脱水器进行脱水,前者为INBA法(因巴法),后者为TYNA法(图拉法);图拉法在我国已获得国家发明专利,专利名称为冶金熔渣粒化装置,专利权人为中冶集团包头钢铁设计研究总院,为俄罗斯人与中国人共同发明。
B:渣池过滤法:渣水混合物流人沉渣池,采用抓斗吊车抓渣,渣池内的水则通过渣池底部或侧部的过滤层进行排水。
底滤式加反冲洗装置,一般称为OCP法,即底滤法;C:脱水槽式:水淬后的渣浆经渣浆泵输送到脱水槽内进行脱水。
这种方法就是通常所说的RASA法,即拉萨法;D:提升脱水式:高炉熔渣渣流首先被机械破碎,进行水淬后,在池内用提升脱水实现渣水分离,提升脱水器可采用螺旋输送机和斗式提升机。
前者即通常所说的笼法,后者称为HK法。
下面分别介绍各种高炉熔渣处理方法的工艺流程和技术特点,TYNA法(图拉法)将作为重点介绍。
2.各种水渣处理方法的工艺流程及特点:2.1OCP法(底滤法)高炉熔渣在冲制箱内由多孔喷头喷出的高压水进行水淬,水淬渣流经粒化槽,然后进入沉渣池,沉渣池中的水渣由抓斗吊抓出堆放于渣场继续脱水。
沉渣池内的水及悬浮物通过分配渠流入过滤池,过滤池内设有砾石过滤层,过滤后的水经由集水管由泵加压后送入冷却塔冷却,循环使用,水量损失由新水补充。
高炉水渣脱水效果的分析
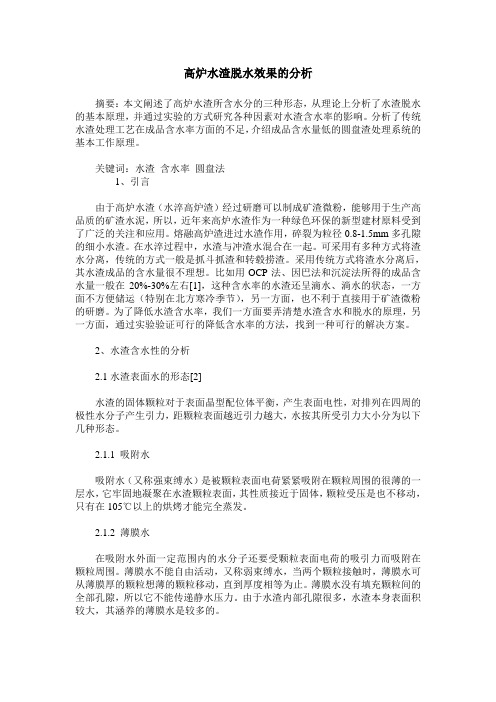
高炉水渣脱水效果的分析摘要:本文阐述了高炉水渣所含水分的三种形态,从理论上分析了水渣脱水的基本原理,并通过实验的方式研究各种因素对水渣含水率的影响。
分析了传统水渣处理工艺在成品含水率方面的不足,介绍成品含水量低的圆盘渣处理系统的基本工作原理。
关键词:水渣含水率圆盘法1、引言由于高炉水渣(水淬高炉渣)经过研磨可以制成矿渣微粉,能够用于生产高品质的矿渣水泥,所以,近年来高炉水渣作为一种绿色环保的新型建材原料受到了广泛的关注和应用。
熔融高炉渣进过水渣作用,碎裂为粒径0.8-1.5mm多孔隙的细小水渣。
在水淬过程中,水渣与冲渣水混合在一起。
可采用有多种方式将渣水分离,传统的方式一般是抓斗抓渣和转毂捞渣。
采用传统方式将渣水分离后,其水渣成品的含水量很不理想。
比如用OCP法、因巴法和沉淀法所得的成品含水量一般在20%-30%左右[1],这种含水率的水渣还呈滴水、淌水的状态,一方面不方便储运(特别在北方寒冷季节),另一方面,也不利于直接用于矿渣微粉的研磨。
为了降低水渣含水率,我们一方面要弄清楚水渣含水和脱水的原理,另一方面,通过实验验证可行的降低含水率的方法,找到一种可行的解决方案。
2、水渣含水性的分析2.1水渣表面水的形态[2]水渣的固体颗粒对于表面晶型配位体平衡,产生表面电性,对排列在四周的极性水分子产生引力,距颗粒表面越近引力越大,水按其所受引力大小分为以下几种形态。
2.1.1 吸附水吸附水(又称强束缚水)是被颗粒表面电荷紧紧吸附在颗粒周围的很薄的一层水,它牢固地凝聚在水渣颗粒表面,其性质接近于固体,颗粒受压是也不移动,只有在105℃以上的烘烤才能完全蒸发。
2.1.2 薄膜水在吸附水外面一定范围内的水分子还要受颗粒表面电荷的吸引力而吸附在颗粒周围。
薄膜水不能自由活动,又称弱束缚水,当两个颗粒接触时,薄膜水可从薄膜厚的颗粒想薄的颗粒移动,直到厚度相等为止。
薄膜水没有填充颗粒间的全部孔隙,所以它不能传递静水压力。
高炉脱水工程案例

高炉脱水工程案例话说有这么一个高炉厂啊,那高炉就像一个大胃王,每天不停地“吃”各种原料,然后产出铁水。
但是呢,这里面有个麻烦事儿,就是原料里老是带着不少水分。
这水分要是不处理好啊,就像在高炉里捣乱的小怪兽。
这个高炉厂的老板可头疼了,因为水分多了之后,高炉里面就容易出各种状况。
比如说,热量会被水分偷走不少,这就像你冬天本来想好好烤火,结果旁边放了一堆湿漉漉的木头,火怎么也旺不起来一样。
而且,水分多了还可能让高炉里面的气体流动变得乱七八糟的,就像在马路上突然来了一群乱走的小动物,交通堵塞了。
于是,他们决定搞个高炉脱水工程。
这工程刚开始的时候啊,就像一场没有硝烟的战争拉开了序幕。
工程师们先对高炉的原料供应系统进行了全面的“体检”。
他们发现,那些从外面运进来的矿石啊、焦炭啊,就像刚从水里捞出来似的,湿哒哒的。
这些原料在传送带上的时候,有的地方甚至还在滴答滴答地滴水呢。
然后呢,他们就想出了第一个妙招——加热烘干。
在原料进入高炉之前,专门设置了一个长长的烘干通道,就像给原料们建了一个超级大的桑拿房。
通道里面有好多加热装置,一打开,那温度就蹭蹭往上升。
原料们在这个“桑拿房”里慢慢地被烘干,那些水分就像受不了高温的小虫子,纷纷逃跑了。
这还不够呢。
因为有的水分很狡猾,藏在原料的小缝隙里,加热也不容易把它们全赶出来。
所以啊,工程师们又上了新的武器——离心脱水机。
这东西就像一个超级大力士,把原料一股脑儿地放进去,然后高速旋转起来。
这一转啊,原料里的水分就被甩了出来,就像你甩干毛巾一样。
在这个过程中,还发生了一些有趣的小插曲。
有一次,离心脱水机突然发出了奇怪的声音,就像一个人在咳嗽一样。
工程师们赶紧围过去查看,原来是有一块比较大的矿石卡在里面了,差点没把这个“大力士”给累坏。
经过一番抢修,这个脱水机又欢快地转了起来。
经过这一系列的脱水措施之后啊,效果那是相当明显。
高炉就像换了一个新的环境一样,工作起来可带劲了。
热量能更好地发挥作用了,铁水的产量也慢慢地提高了。
炼钢高炉冲渣水余热
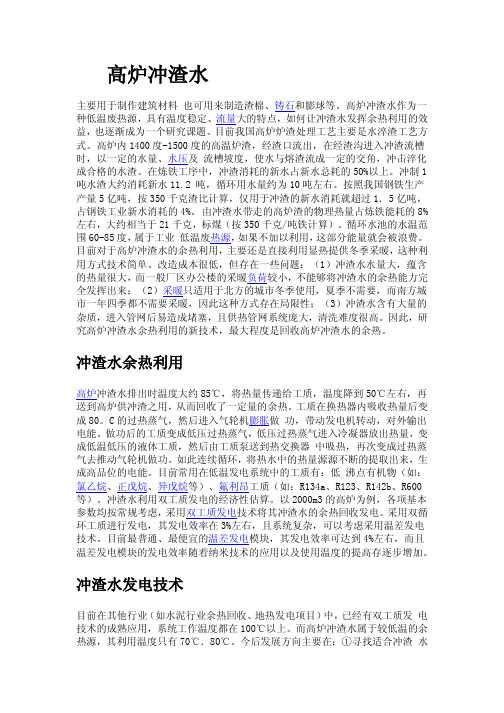
高炉冲渣水主要用于制作建筑材料也可用来制造渣棉、铸石和膨球等。
高炉冲渣水作为一种低温废热源,具有温度稳定、流量大的特点,如何让冲渣水发挥余热利用的效益,也逐渐成为一个研究课题。
目前我国高炉炉渣处理工艺主要是水淬渣工艺方式。
高炉内1400度-1500度的高温炉渣,经渣口流出,在经渣沟进入冲渣流槽时,以一定的水量、水压及流槽坡度,使水与熔渣流成一定的交角,冲击淬化成合格的水渣。
在炼铁工序中,冲渣消耗的新水占新水总耗的50%以上。
冲制1吨水渣大约消耗新水11.2 吨,循环用水量约为10吨左右。
按照我国钢铁生产产量5亿吨,按350千克渣比计算,仅用于冲渣的新水消耗就超过1.5亿吨,占钢铁工业新水消耗的4%。
由冲渣水带走的高炉渣的物理热量占炼铁能耗的8%左右,大约相当于21千克,标煤(按350千克/吨铁计算)。
循环水池的水温范围60-85度,属于工业低温废热源,如果不加以利用,这部分能量就会被浪费。
目前对于高炉冲渣水的余热利用,主要还是直接利用显热提供冬季采暖,这种利用方式技术简单、改造成本很低,但存在一些问题:(1)冲渣水水量大,蕴含的热量很大,而一般厂区办公楼的采暖负荷较小,不能够将冲渣水的余热能力完全发挥出来;(2)采暖只适用于北方的城市冬季使用,夏季不需要,而南方城市一年四季都不需要采暖,因此这种方式存在局限性;(3)冲渣水含有大量的杂质,进入管网后易造成堵塞,且供热管网系统庞大,清洗难度很高。
因此,研究高炉冲渣水余热利用的新技术,最大程度是回收高炉冲渣水的余热。
冲渣水余热利用高炉冲渣水排出时温度大约85℃,将热量传递给工质,温度降到50℃左右,再送到高炉供冲渣之用,从而回收了一定量的余热。
工质在换热器内吸收热量后变成80。
C的过热蒸气,然后进入气轮机膨胀做功,带动发电机转动,对外输出电能。
做功后的工质变成低压过热蒸气,低压过热蒸气进入冷凝器放出热量,变成低温低压的液体工质,然后由工质泵送到热交换器中吸热,再次变成过热蒸气去推动气轮机做功。
港陆高炉水渣“脱白”技术方案
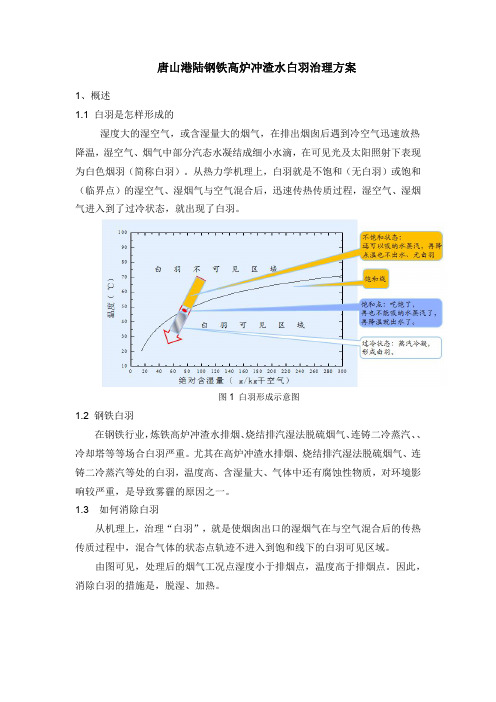
为了确保冲渣点不外溢蒸汽,冲渣点需保持微负压,因此系统配置引风机, 引风机电机采用变频电机,可根据湿空气量的变化变频运行,实现节能。引风机 安装在水冷换热器和混合换热器之间。引风机采用防腐蚀材质。 4.5.2 热风炉废气管道系统
热风炉废气温度在 140-150℃,采用碳钢卷焊管道,采用外保温。 在废气管道上设置废气引风机,电机采用变频电机,可根据系统加热的需 要调节废气量,并降低运行电耗。 4.5.3 混合气体管道系统 从混合换热器到现有的水渣烟囱间的混合气体,温度为超过饱和温度,不会 有凝结水析出,因此该管道采用碳钢卷焊管道,为了减少管道内气体降温,拟采 用外保温。 4.5.4 冷却水管道系统 水冷换热器的外部冷却水管道采用碳钢无缝钢管。 4.6 系统控制 高炉水渣白羽治理系统的治理,受到水渣蒸汽的温度、湿度等内因,大气温 度、湿度等外因的制约,同时外部冷却水、废热温度和量的影响,是一个多因素 相互干扰的过程,内在模型较为复杂。 该系统的自控控制拟采取以下措施,确保白羽治理的效果,并做到成本最优。
电机功率 m³/h 45 65 30 30 45 45
6、投资估算
6# 750 1.15
4.3.2 冷却水条件
最大渣量 t/min 1.3 1.75 1.0 1.0 1.3 1.3
冲渣水量 m³/h 1736 2264 1800 1800 1750 1750
冲渣水温 ℃
60-69
冲渣后 水温℃ 70-100
冲渣点蒸 汽温度℃ 40-100
采暖季时冷却水采用现有的采暖水,供回水温度为 44℃/67℃,采暖水量需 要根据现有采暖水系统的质量平衡、热量平衡评估。
无法直接利用)。
4、高炉水渣消除白羽方案
4.1 目标及系统能力
高炉冲渣乏汽脱白技术在钢铁企业应用

高炉冲渣乏汽脱白技术在钢铁企业应用发布时间:2021-03-15T03:21:51.872Z 来源:《中国科技人才》2021年第4期作者:师小文[导读] 既节约了能源介质(不用煤气加热)又可降低温度,且能消除白烟,完全可以达到现有环保排放标准,获得了良好的环境效益,值得广泛推广。
陕西龙门钢铁有限责任公司规划发展部陕西韩城 715405摘要:高炉冲渣乏汽脱白技术在某钢铁企业实地应用,既解决了对周边环境产生较大的感官污染,减少凝结水资源的浪费,消除白羽现象,大大减轻高炉水渣系统引起的腐蚀现状,实施后空冷消白效果明显,既节约了能源介质(不用煤气加热)又可降低温度,且能消除白烟,完全可以达到现有环保排放标准,获得了良好的环境效益,值得广泛推广。
关键词:高炉冲渣;乏汽脱白回收1现状某钢铁企业炼铁厂3#高炉炉炉渣处理采用炉前水冲渣的方式(茵芭(INBA)法)。
茵芭(INBA)法是卢森堡PW公司的专利炉渣处理工艺,水淬后的渣水混合物经水渣槽流入脱水转鼓,脱水后的水渣经过转鼓内、外的胶带机运到成品水渣仓内进一步脱水。
滤出的水经冷却塔冷却后进入冷却水池,冷却后的冲渣水经泵送往冲渣箱循环使用。
利用冲渣水将一千多度的炉渣降温,渣水混合时瞬间产生大量的水蒸汽,这些水蒸汽在自生动力与烟囱的吸力下排入大气,形成很大的白烟,并且为间断性排放,外排蒸汽量大,排放时浓烟滚滚,形成严重的白色烟羽,冬季尤为严重。
既对周边环境产生较大的感官污染,同时又耗去较多的水资源。
高炉冶炼过程中,水淬后的渣水混合物经水渣槽流入脱水转鼓,脱水后的水渣经过转鼓内、外的胶带机运到成品水渣仓内进一步脱水。
滤出的水经冷却塔冷却后进入冷却水池,冷却后的冲渣水经泵送往冲渣箱循环使用。
利用冲渣水将一千多度的炉渣降温,渣水混合时瞬间产生大量的水蒸汽,这些水蒸汽在自生动力与烟囱的吸力下排入大气,形成很大的白烟,并且为间断性排放,外排蒸汽量大,排放时浓烟滚滚,形成严重的白色烟羽,冬季尤为严重。
- 1、下载文档前请自行甄别文档内容的完整性,平台不提供额外的编辑、内容补充、找答案等附加服务。
- 2、"仅部分预览"的文档,不可在线预览部分如存在完整性等问题,可反馈申请退款(可完整预览的文档不适用该条件!)。
- 3、如文档侵犯您的权益,请联系客服反馈,我们会尽快为您处理(人工客服工作时间:9:00-18:30)。
高炉水渣脱水效果的分析
摘要:本文阐述了高炉水渣所含水分的三种形态,从理论上分析了水渣脱水的基本原理,并通过实验的方式研究各种因素对水渣含水率的影响。
分析了传统水渣处理工艺在成品含水率方面的不足,介绍成品含水量低的圆盘渣处理系统的基本工作原理。
关键词:水渣含水率圆盘法
1、引言
由于高炉水渣(水淬高炉渣)经过研磨可以制成矿渣微粉,能够用于生产高品质的矿渣水泥,所以,近年来高炉水渣作为一种绿色环保的新型建材原料受到了广泛的关注和应用。
熔融高炉渣进过水渣作用,碎裂为粒径0.8-1.5mm多孔隙的细小水渣。
在水淬过程中,水渣与冲渣水混合在一起。
可采用有多种方式将渣水分离,传统的方式一般是抓斗抓渣和转毂捞渣。
采用传统方式将渣水分离后,其水渣成品的含水量很不理想。
比如用OCP法、因巴法和沉淀法所得的成品含水量一般在20%-30%左右[1],这种含水率的水渣还呈滴水、淌水的状态,一方面不方便储运(特别在北方寒冷季节),另一方面,也不利于直接用于矿渣微粉的研磨。
为了降低水渣含水率,我们一方面要弄清楚水渣含水和脱水的原理,另一方面,通过实验验证可行的降低含水率的方法,找到一种可行的解决方案。
2、水渣含水性的分析
2.1水渣表面水的形态[2]
水渣的固体颗粒对于表面晶型配位体平衡,产生表面电性,对排列在四周的极性水分子产生引力,距颗粒表面越近引力越大,水按其所受引力大小分为以下几种形态。
2.1.1 吸附水
吸附水(又称强束缚水)是被颗粒表面电荷紧紧吸附在颗粒周围的很薄的一层水,它牢固地凝聚在水渣颗粒表面,其性质接近于固体,颗粒受压是也不移动,只有在105℃以上的烘烤才能完全蒸发。
2.1.2 薄膜水
在吸附水外面一定范围内的水分子还要受颗粒表面电荷的吸引力而吸附在颗粒周围。
薄膜水不能自由活动,又称弱束缚水,当两个颗粒接触时,薄膜水可从薄膜厚的颗粒想薄的颗粒移动,直到厚度相等为止。
薄膜水没有填充颗粒间的全部孔隙,所以它不能传递静水压力。
由于水渣内部孔隙很多,水渣本身表面积较大,其涵养的薄膜水是较多的。
2.1.3 自由水
自由水是存在于颗粒表面电荷引力作用范围之外的水,能在颗粒间自由流动,并传递水压力,在重力作用下向下流动,又称重力水;在水体表面手表面张力支持的水称毛细水。
毛细水有一定的高度,随着水体表面的下降而下降。
2.2 水渣脱水的理论依据
上述三种水的形态,前两种被束缚在水渣颗粒表面,统称为粘结水。
两两水渣颗粒表面的束缚水之间又通过范德华力作用是颗粒间相互束缚,这种束缚力使颗粒结团,并由一定的强度。
若烘干到105℃脱去束缚水,水渣则会成为松散的颗粒。
因此,水渣脱水的对象不是束缚水而是重力水。
至于毛细水,它不发生在水体内部,只发生在水体表面以上的孔隙中,距水体有一定高度,岁水体的下降而下降,随水体的消失而消失。
因此,也可以看作是重力水的特殊形式,一般不做考虑。
根据以往水渣含水率试验,当水渣的重力水全部脱去时,依水渣粒径大小和孔隙多少,其含水率约为8%.因此,对水渣进行较好的重力脱水就能达到水渣含水率小于15%的工艺要求,那么影响水渣重力脱水的因素可用达西定律表示:
q=KWh/l=KIW (1)
式中:q—单位时间渗透量;K—渗透系数;W—渗流面积;h—水头高度;l—渗流路程;I—水力坡度。
由于对于不同介质的渗流过程,影响渗流速度的参量是渗透系数K,那么,
K=kρg/η(2)
式中:k—孔隙介质的渗透率;ρ—流体密度;g—重力加速度;η—流体的粘滞性系数。
结合式(1)及式(2),可以看出对于相同性状的水渣颗粒要增加其渗流速度的因素有增大渗流面积,增加重力加速度(但在大规模工业生产中采用离心的方法产生更大的加速度将耗费大量能源,因此工业生产中对此不予考虑),以及减小流体的粘滞性系数,即考虑增加流体温度。
脱水量Q可用以下公式表示:
Q=
式中,t—水渣脱水时间。
可以看出水渣的脱水量(直接决定水渣的最终含水量)与脱水时间t密切相关。
3、水渣重力脱水试验
为验证渣水温度以及水渣脱水时间对水渣最终含水率的影响,设计了一个脱水实验。
该实验采用的水渣粒径为1-1.2mm具有较强代表性,但实验的最终结果仅代表该种水渣的脱水特性,对于其它水渣的脱水过程有定性参考价值,不能作为精确定量分析。
3.1 实验器材
3个渣桶Ø1000×3200mm,底部为条形筛网,筛网间隙3.8mm,筛条宽度4mm,在油桶垂直方向开三个洞,分别是距离底部200mm、1500mm和2800mm处,大小Ø40mm;冲渣水池及配套电葫芦及抓斗;取样钢管一根;油桶内刻度标杆一根。
3.2 实验过程
在3个渣桶中堆积高度为3m高的同质水渣,分别浸泡于20℃、50℃和95℃的水中5分钟后悬挂脱水,每隔五分钟从三个取样孔取样测定水渣含水率并求平均值,依据得出的每组温度下水渣各个时间的含水率与脱水时间的绘制“含水率—时间”曲线图。
3.3 试验结果
实验结果如图1。
图1
实验表明:①进入渣桶的渣水混合物的初始温度越高,其脱水速度越快。
这是因为随着温度的升高,水的表面张力减小、粘滞性也降低了。
②脱水时间越长水渣含水率越小,同时随着脱水时间延长脱水速率越慢。
脱水5分钟以内,水渣含水率远高于15%,脱水超过25分钟,脱水效果好。
4、对传统水渣处理设备的改进
4.1 传统水渣处理设备含水率剖析
诸如抓斗抓水渣以及采用转毂法捞渣等方式进行渣水分离时,水渣在空中依靠重力脱水的时间一般不会超过1分钟,脱水时间过短,参照实验的数据,即使水温很高,其脱水效果也远达不到15%的标准。
如果刻意延长其在空中沥水的时间,则会严重影响传统处理方式的处理能力。
因此,在传统的渣处理工艺中,其脱水过程的脱水时间和水渣含水率有着不可调和的矛盾。
那么也就是说要达到更好的水渣含水率必须要延长脱水时间并同时保证设备的处理能力。
4.2 圆盘法渣处理系统
圆盘法渣处理系统的脱水器如图2所示。
图2
一个圆盘由若干个料斗组成(示例中为12个),每个料斗具有以吨记的承载能力,其底部为筛网,料斗在受料处接纳渣水混合物,旋转近一圈后在卸料处卸料,圆盘每小时旋转0.5-1圈,水渣的脱水时间可以超过30分钟,这样就保证了水渣有着足够的脱水时间,保证了成品水渣含水率的合格。
同时由于圆盘单个料斗的处理能力大,保证了整个圆盘在慢转速下的处理能力。
5、结语
高炉水渣的脱水效果受多种因素影响,其中受脱水时间和渣水温度影响最大。
在现有的渣处理工艺中渣水混合物的温度多为70℃以上,要改善脱水效果主要考虑延长脱水时间。
圆盘法渣处理系统很好地解决了传统渣处理系统在渣水分离过程中水渣脱水时间和系统处理能力矛盾问题,保证了成品水渣超低的含水率,是一种极具优势的渣处理系统,值得推广应用。
参考文献
[1]田彦生,张振瑞.高炉轮法粒化渣处理工艺及设备[J].冶金设备,2000(1):38.
[2]梁定伟,编.水力学基础[M].武汉:中国地质大学出版社,1998.。