数控车床可靠性数据的采集及数据库建立
数控机床数据采集
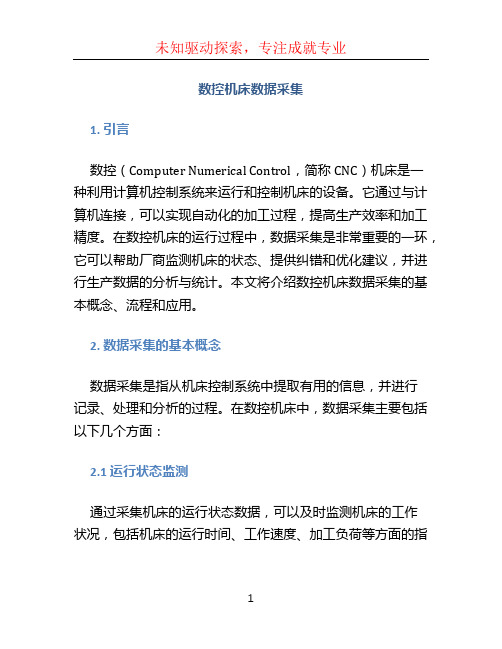
数控机床数据采集1. 引言数控(Computer Numerical Control,简称CNC)机床是一种利用计算机控制系统来运行和控制机床的设备。
它通过与计算机连接,可以实现自动化的加工过程,提高生产效率和加工精度。
在数控机床的运行过程中,数据采集是非常重要的一环,它可以帮助厂商监测机床的状态、提供纠错和优化建议,并进行生产数据的分析与统计。
本文将介绍数控机床数据采集的基本概念、流程和应用。
2. 数据采集的基本概念数据采集是指从机床控制系统中提取有用的信息,并进行记录、处理和分析的过程。
在数控机床中,数据采集主要包括以下几个方面:2.1 运行状态监测通过采集机床的运行状态数据,可以及时监测机床的工作状况,包括机床的运行时间、工作速度、加工负荷等方面的指标。
这些数据可以用来判断机床的性能是否正常,是否需要进行维护和保养。
2.2 故障诊断与纠错数据采集还可以用于故障诊断与纠错。
通过采集机床运行过程中的异常数据和错误信息,可以判断出可能存在的问题,并进行相应的调整和修复。
这可以提高机床的稳定性和可靠性,减少故障停机时间。
2.3 生产数据分析与统计对机床生产过程中的数据进行分析和统计,可以得到生产过程的特征和规律。
这有助于优化生产过程,提高生产效率和产品质量。
同时,也可以根据数据分析的结果进行生产计划的调整和优化,以满足不同的订单需求。
3. 数据采集的流程数控机床数据采集的流程主要包括数据获取、数据传输、数据处理和数据存储等多个环节。
下面将对每个环节进行详细介绍。
3.1 数据获取数据获取是指从数控机床中提取数据的过程。
数控机床的控制系统通常会提供各种接口和协议,用于与外部设备进行数据交换。
可以通过这些接口将数据传输到数据采集设备上。
数据获取的方式可以是实时采集,也可以是定期采集,根据实际需求进行选择。
3.2 数据传输数据传输是指将采集到的数据传输到数据处理设备的过程。
数据传输可以通过有线或无线方式进行,常见的有以太网、USB和Wi-Fi等。
数控车床的可靠性分析

时 由于数控 车床 的故 障而造 成 的停 机 以及维 修费 用又 给数控 车床 用户带 来 了极大 的 困惑 。这样数 控 车床 的 可靠性 问题 就摆在 了机 床制 造商 和用户 的面 前 , 靠性 已成 为 数控 车 床 的制 造商 和用 户 使 用频 率 车床 的可靠性 是指 在规定 的条 件下 和规定 的时 间 内 , 数控 车 床稳 定 完成 其 功 能 的程 度或 性 质 。它
分为 固有 可靠性 和工作 可靠 性两种 。其 中固有可靠 性是 指 数控 车 床 的设计 制 造 者按 照 可靠 性 规 划 , 原 材 从 料和零 部件 的选用 , 过设计 、 经 制造 、 验 , 到数控 车 床 出产 的各个 阶段 所确 立 的可靠性 。工 作可 靠性 是指 试 直 已生产 的数 控车床 经过 包装 、 运输 、 存储 、 安装 、 使用 、 修等 因素影 响 的可靠性 。 维 C K 25 A 37 V型数控 车床 采用 了华 中数控 系统 , 是一 种真 正意 义上 的 国产数 控 车床 , 的研 发 和应 用对 提 它
数 控 车床又称 为 C C车 床 , N 即计算机 数字 控制 车床 , 目前 国内使用 量最 大 , 盖面 最广 的一种 数控 机 是 覆 床 , 占数 控 机床 总 数 的 2 % 。数控 车 床是 数 控机 床 的 主要 品种 之一 , 在数 控 机床 中 占有 非 常重 要 的位 约 5 它 置 , 十年来 一直 受 到世界 各 国的普遍 重视并 得 到 了迅 速 的发 展 。数控 车床 是一种 高精 度 、 几 高效率 的 自动化
数控机床数据采集
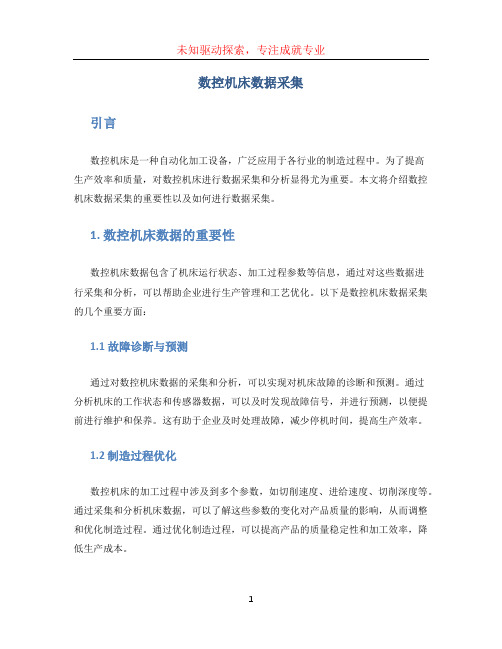
数控机床数据采集引言数控机床是一种自动化加工设备,广泛应用于各行业的制造过程中。
为了提高生产效率和质量,对数控机床进行数据采集和分析显得尤为重要。
本文将介绍数控机床数据采集的重要性以及如何进行数据采集。
1. 数控机床数据的重要性数控机床数据包含了机床运行状态、加工过程参数等信息,通过对这些数据进行采集和分析,可以帮助企业进行生产管理和工艺优化。
以下是数控机床数据采集的几个重要方面:1.1 故障诊断与预测通过对数控机床数据的采集和分析,可以实现对机床故障的诊断和预测。
通过分析机床的工作状态和传感器数据,可以及时发现故障信号,并进行预测,以便提前进行维护和保养。
这有助于企业及时处理故障,减少停机时间,提高生产效率。
1.2 制造过程优化数控机床的加工过程中涉及到多个参数,如切削速度、进给速度、切削深度等。
通过采集和分析机床数据,可以了解这些参数的变化对产品质量的影响,从而调整和优化制造过程。
通过优化制造过程,可以提高产品的质量稳定性和加工效率,降低生产成本。
1.3 能源消耗管理数控机床在运行过程中会消耗大量能源,如电力和冷却水。
通过采集和分析机床的能源消耗数据,可以了解机床的能源利用情况,并对能耗进行管理和优化。
通过降低能耗,可以减少企业的生产成本,提高资源利用效率。
2. 数控机床数据采集方法在进行数控机床数据采集时,需要选取合适的采集方法和设备。
以下介绍几种常见的数控机床数据采集方法:2.1 传感器数据采集传感器是实现数控机床数据采集的重要设备。
通过安装传感器在机床上,可以实时采集机床运行状态、加工参数等数据。
常见的传感器包括温度传感器、压力传感器、力传感器等。
这些传感器可以将采集到的数据通过信号传输给数据采集器进行存储和处理。
2.2 机床控制系统数据采集数控机床自身已经具备了控制系统,这些控制系统通常会记录机床的运行状态和加工参数。
可以通过与机床控制系统进行通信,将数据采集到外部的数据采集器中。
这种方法不需要额外的传感器设备,对于已经安装了数控控制系统的机床来说较为方便。
FANUC数控系统的机床数据采集

标签:分类:机床数据采集及监控发那科fanuc数据采集0i16i .'.一,・:一,・18i•报警数据:NC报警,PLC报警状态和PLC报警号所有数据均实时后台采集,不用任何人工干预。
针对具备以太网通信功能的西门子802系列数控系统,制造数据管理系统MDC可采集到大量的数据,其数据量与SINUMERIK 840D系列相当。
例如,典型的数据包括:•操作方式数据:手动JOG、乂口人、自动等•程序运行状态(运行,停止,暂停等)•主轴数据:主轴转速、主轴倍率,主轴负载,主轴运转状态•进给数据:进给速度、进给倍率轴数据:•轴坐标(机床坐标系、工件坐标系统),轴负载•加工数据:当前执行的程序名称、程序路径;当前使用的刀具•报警数据:报警代码、报警信息内容、报警时间所有数据均实时后台采集,不用任何人工干预。
MDC系统充分利用机床已有的硬件资源,实现机床通信资源的共享。
如MDC和DNC系统可共用数控系统的网卡或者串口通信端口进行数据采集和程序传输的功能。
例如西门子802D/C/S系统、FANUC 0i系统共用一个串口实现MDC/DNC两个系统的功能需要。
MDC系统的特点:以通用以太网为骨干网络,减低硬件投入,增强了数据通讯能力,奠定车间与工业以太网的发展相适应能力。
基于以太网络的模式从而充分利用车间现有网络,可完全与DNC网络兼容。
2)灵活的数据采集方式由于如今金属加工工业的数控机床数量较大,采用单一系统或单一机床的企业很少,对于大多数企业,其机床种类比较多,新旧不一,因此如果采用某一种数据采集方式则缺乏灵活性,从而使得能采集的数据不能最大化。
而根据车间现场具体设备情况采用相应的数据采集方式,既能获得最大的数据量,又能有效的控制成本投入,取得最佳的性价比。
制造数据管理系统MDC常见的采用如下方式:•软件通讯方式(TCP/IP、串口通讯等)•工业总线方式(如PROFIBUS、MODBUS, CAN总线等)•硬件方式(数据采集模块)•终端数据采集3)丰富的采集数据量从简单的开关量到复杂的模拟量和字符串,制造数据涵盖车间现场需求的各个方面。
DNC数控机床联网数据采集解决方案

DNC数控机床联网、数据采集解决方案苏州摩恩信息技术有限公司1.DNC的概念DNC(Distributed Numerical Control)称为分布式数控,是数控机床联网专业术语。
DNC数控机床联网解决方案对车间的加工设备进行有效的整合,提高了设备的利用率,减少了机床的辅助时间;实现车间的资源与信息透明化,降低了管理成本及管理难度,解决了过去对设备无法掌控的被动局面。
帮助企业有效的优化生产、提高人员工作效率、增强各部门间的协同能力,最终实现企业经济效益的同比显著增长。
2.DNC数控机床联网解决方案DNC服务器是负责与通讯相关的所有活动的中央数据应用程序,它主要和机床的串口/网口进行通讯,处理机床发送的命令,自动查找匹配的数控程序发送给机床,服务器端实现无人值守,加强了编程部门和车间设备的连接,使您不再使用CF卡或者U盘满车间跑,逐个机床拷贝程序,编程员只要将编制好的数控程序放在指定的目录即可,操作员只要在机床面板上直接调用相关的数控程序即可,一切变得如此简单。
DNC服务器功能介绍:1) 一台DNC服务器可管理256 台机床。
更新许可证即可增加机床。
2) 批量从机床到电脑上传数控程序和批量从电脑到机床下载数控程序。
3) 自动备份,当机床上传的文件与服务器重复时,自动备份。
方便数控程序管理。
4) 操作人员在机床控制面板前就可以完成各种操作,包括查看电脑目录中的数控程序、大小、修改时间等,完成程序的发送与接收,进行双向通讯,无需来回跑动。
5) 所有联网机床可以同时进行双向通讯,互不干扰,支持同时做DNC在线加工。
6) 远程查看服务器程序目录,只要在机床上发个命令就可以查看服务器上目录下面的程序名,程序大小,最后修改日期等。
7) 循环呼叫,在进行批量DNC加工时,实用改功能只要呼叫一次程序即可,换工件后直接进行加工。
8) 呼叫批处理,通过该功能,用户可以直接在机床端,通过修改控制程序中的一行程序,调用电脑上的一批NC程序。
数控机床状态和数据实时采集及分析

数控机床状态和数据实时采集及分析在制造企业数字化工厂的方案设计中,SFC底层数据管理对企业工厂信息化平台的支撑是必不可少的。
对于已经具备ERP/MRPⅡ/MES/PDM等上层管理系统的企业来说,迫切需要实时了解车间底层详细的设备状态信息,而盖勒普MDC系统是绝佳的选择。
MDC是一套用来实时采集、并报表化和图表化车间生产过程详细制造数据的软硬件解决方案(Manufacturing Data Collection & Status Management,简称MDC)。
在上世纪90年代初,盖勒普最早把MDC以精益制造管理理念及解决方案引入中国,基于全球20多年的技术沉淀和国内近14年的本地应用,真正助力中国离散制造企业的数字化制造集成生产管理落地。
盖勒普MDC通过多种灵活的方法获取生产现场的实时数据,结合近100种专用计算、分析和统计方法,直观反映当前或过去某段时间的生产状况,帮助企业生产部门通过反馈信息做出科学和有效的决策。
作为生产管理平台(SFC)的重要系统之一,与ERP\MES等系统可实现高效集成。
MDC可以解决如下问题:1.当前设备是正在加工中、故障还是空闲?2.设备停机的原因是什么?3.设备停机时间内耗费的成本是多少?4.产量是由于哪些原因下降?5.谁在进行零件的生产?哪一班组?生产绩效?6.生产设备是怎样被利用的?7.哪些生产环节可以被改善?8.工厂设备现有的生产能力是多少?等等以上所有问题的答案都可以在任何一台MDC系统终端上显示。
此外,MDC系统还能够直观反映当前或过去某段时间的设备状态,使企业对工厂的设备状况一目了然。
MDC 主要功能如下:一、强大的设备状态采集盖勒普MDC系统提供了与各类设备PLC通讯的数据采集接口,支持Siemens、Fanuc、Heidenhain、Hurco、Mazak、Okuma、Mitsubishi等基本上所有型号的控制系统。
对于非数控设备也提供了多种采集方案,针对焊接机、热处理炉、注塑机、温控及测试测量设备等都可以实现组态联网。
工程机械可靠性数据管理系统设计
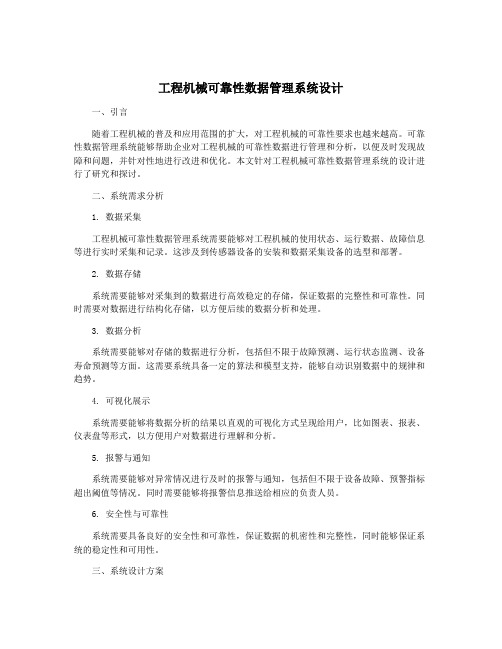
工程机械可靠性数据管理系统设计一、引言随着工程机械的普及和应用范围的扩大,对工程机械的可靠性要求也越来越高。
可靠性数据管理系统能够帮助企业对工程机械的可靠性数据进行管理和分析,以便及时发现故障和问题,并针对性地进行改进和优化。
本文针对工程机械可靠性数据管理系统的设计进行了研究和探讨。
二、系统需求分析1. 数据采集工程机械可靠性数据管理系统需要能够对工程机械的使用状态、运行数据、故障信息等进行实时采集和记录。
这涉及到传感器设备的安装和数据采集设备的选型和部署。
2. 数据存储系统需要能够对采集到的数据进行高效稳定的存储,保证数据的完整性和可靠性。
同时需要对数据进行结构化存储,以方便后续的数据分析和处理。
3. 数据分析系统需要能够对存储的数据进行分析,包括但不限于故障预测、运行状态监测、设备寿命预测等方面。
这需要系统具备一定的算法和模型支持,能够自动识别数据中的规律和趋势。
4. 可视化展示系统需要能够将数据分析的结果以直观的可视化方式呈现给用户,比如图表、报表、仪表盘等形式,以方便用户对数据进行理解和分析。
5. 报警与通知系统需要能够对异常情况进行及时的报警与通知,包括但不限于设备故障、预警指标超出阈值等情况。
同时需要能够将报警信息推送给相应的负责人员。
6. 安全性与可靠性系统需要具备良好的安全性和可靠性,保证数据的机密性和完整性,同时能够保证系统的稳定性和可用性。
三、系统设计方案1. 数据采集采用现场总线技术,结合传感器和数据采集设备,对工程机械的各项数据进行实时采集和传输。
同时通过物联网技术,实现设备信息的远程监控和管理。
3. 数据分析引入机器学习和深度学习算法,对工程机械的数据进行分析和挖掘,以发现数据中的规律和趋势,并进行故障预测和设备寿命预测。
同时采用数据仓库和数据挖掘技术,对历史数据进行分析和挖掘。
4. 可视化展示采用专业的数据可视化工具,对数据分析的结果进行可视化展示,以方便用户对数据进行理解和分析。
数控机床生产数据信息采集控制系统设计

数控机床生产数据信息采集控制系统设计数控机床生产数据信息采集控制系统设计近年来,随着制造业的迅速发展,数控机床在工业生产中发挥着越来越重要的作用。
作为一种高精度、高效率的加工设备,数控机床可以实现复杂零部件的高精度加工,并且具有良好的稳定性和可靠性。
为了实现数控机床的自动化生产和提高生产效率,设计一套可靠的生产数据信息采集控制系统变得尤为重要。
本文将探讨数控机床生产数据信息采集控制系统的设计与实现。
首先,我们需要明确系统的设计目标,即实时采集数控机床的生产数据信息,提供可视化的生产监控界面,并实现对数控机床的远程控制。
其次,我们需要设计合适的硬件装置和传感器,用于采集数控机床的各项参数数据,如工作温度、转速、加工时间等。
同时,还需要利用现代通讯技术,建立数控机床与数据采集控制系统之间的通讯连接。
在系统软件设计方面,我们需要开发一套用户友好的界面,以便操作员能够直观地了解数控机床的工作状态和生产情况。
通过实时监控和分析数据,我们可以及时发现数控机床的故障和异常情况,从而采取相应的措施进行维修和调整。
此外,为了提高生产效率,我们还可以通过远程控制系统对数控机床进行参数调整和优化,从而实现自动化生产。
在实际应用中,我们可以将生产数据信息采集控制系统与企业的生产管理系统相结合,实现生产数据的实时传输和共享。
通过对生产数据的分析和挖掘,企业可以实现生产过程的优化,提高设备利用率和生产效率。
另外,数控机床生产数据信息采集控制系统还可以与企业的质量管理系统相连,实现对生产过程中各项质量参数的自动监控,确保产品的质量稳定性。
在系统的实施过程中,我们需要充分考虑到数控机床和生产数据信息采集控制系统之间的兼容性和稳定性。
首先,我们需要选择合适的通讯协议和接口,并进行充分的测试和验证。
其次,还需要针对不同类型的数控机床进行定制化的设计和开发。
最后,我们需要进行全面的系统测试和调试,确保系统的稳定运行。
在项目的实施过程中,我们还需要加强与数控机床生产厂家的合作,实现系统的无缝对接和信息共享。
数控机床可靠性信息系统信息建模

收稿日期:2005-01-05基金项目:山东省优秀青年科学家奖励基金资助项目(2001493-01BS36)作者简介:张强(1966-),男,吉林长春人,副教授,工学博士.主要研究方向为数控技术、可靠性工程和物流技术等.E -mail:z hangqiangd@文章编号:1672-3961(2005)04-0014-05数控机床可靠性信息系统信息建模张 强1,艾 兴1,贾亚洲2(1.山东大学 机械工程学院, 山东 济南 250061; 2.吉林大学 机械工程学院, 吉林 长春 130000)摘要:可靠性信息建模是开发数控机床可靠性信息系统的关键.提出了一种数控机床可靠性信息建模的新方法)))功能元法,定义了功能元法的基本概念和基本理论,得出了基于功能元法的数控机床功能信息抽象方法和故障模式及原因等可靠性信息抽象方法,应用于某国产数控车床故障模式与影响分析(FME A)的信息建模.结果表明:该方法适用于对不同种类数控机床进行不同深度可靠性分析的信息建模.以此方法开发的数控机床信息系统已应用于国产数控车床、数控冲床、数控轴承磨床、线切割机床等的可靠性增长,数控机床的平均无故障时间显著提高.关键词:可靠性;功能元法;数控机床;建模中图分类号:TH164 文献标识号:AStudy on reliability information system modeling of CNC machine toolsZHANG Qiang 1, AI Xing 1, JI A Ya -zhou2(1.School of Mechanical Engineering, Shandong University, Jinan 250061, China;2.School of Mechanical Engineering, Jilin University, Changchun 130000, China)Abstract :Considering reliability information modeling as a key technology in C NC(Computerized Numerical Control)machine tool reliability information syste m,the function ele ment method,a kind of new CNC machine tool reliability information modeling method,is proposed.Basic conception and theory on function element method is defined.And information abstraction methods,such as CNC machine tool function method based on function element method and reliability method related to failure model and cause,are obtained.And FE MA information model applied in a certain home -made C NC lathe machine is introduced as well.The results ind-i cate that this method are suitable for the modeling of various kinds of CNC machine tools.C NC machine infor -mation syste m based on this method has been applied to improve reliability of home -made CNC lathe,C NC punch,C NC bearing grinding machine,linear cutting machine,and etc.Mean Time Between Failure (MT -BF)of a certain home -made CNC lathe is increased re markably.Key words :reliability;function element method;C NC machine tool;modeling0 引言数控机床是先进制造技术的基础装备,其技术水平是衡量一个国家工业现代化水平的重要标志.数控机床的可靠性是广大机床用户和社会在机床众多技术指标中特别关注的质量特性,它是机床质量的核心和关键,国家在/九五0和/十五0期间都把可靠性作为/数控机床产业化工程0中的关键技术组织攻关研究.数控机床种类繁多,同一类型的数控机床第35卷 第4期 Vol.35 No.4 山 东 大 学 学 报 (工 学 版)JO URN AL OF SHAND ONG UNIV ER SITY (ENGINEERIN G SCIENCE)2005年8月Aug.2005也存在较大的差别,为建立通用的数控机床可靠性数据库系统,必须对数控机床进行抽象,建立其信息模型.对数控机床可靠性的研究表明,有相当部分的故障发生在子系统之间的联系上,传统的故障分析方法,或是忽略了这部分故障,或是把它们归结到比较相近的子系统中,往往掩盖了故障发生的实质.另外,由于收集的可靠性数据较少,初期进行可靠性分析时,主要是对较大子系统进行粗略分析,随着可靠性数据的增加,可靠性分析将深入到更小的环节,可见数控机床可靠性分析具有明显的层次性.根据以上特点,提出了数控机床可靠性信息建模的新方法)))功能元法.研究建立功能元法的基本理论,并结合实例提出基于功能元法的数控机床可靠性信息系统建模方法=1~4>.1功能元法的基本概念1.1功能元数控机床是由多个具有特定功能的子系统组成,并通过它们之间的有机联系构成的系统.系统的组成可用具有特定功能的实体和实体间的联系概括.功能元:具有特定功能的可靠性分析的最小实体或实体间的联系定义为可靠性分析功能元,简称功能元.功能元分为实体型功能元和联系型功能元2种.最小实体是指为进行可靠性分析划分的最小功能实体,根据研究的深度具体界定.实体型功能元i 简记为I i,联系型功能元j简记为J j.为了相互区别,对每一个功能元人为地赋予一个唯一性标识号)))功能元编号.功能元名和描述值构成了功能元的2个基本要素.1.2功能元组若干个功能元的集合称为功能元组.功能元组名表示功能元组的意义.功能元组有唯一性标识)))功能元组号,以区分不同的功能元组.在数控机床可靠性分析中,功能元组是上一层可靠性分析的实体型功能元.功能元组是某系统的功能信息的全部或局部.单个功能元是功能元组的特例.记功能元组k为G k.若I i(或J j)是G k里的一个功能元,则称I i(或J j)属于G k,记为I i I G k(或J j I G k).数控机床功能元组可定义为G k={I m,I i,I mm,J n,J j,J n n}.1.3功能结构树采用如图1所示的树状分层结构来描述数控机床功能信息之间的结构关系,即功能结构树.功能结构树上的节点为功能元和功能元组,功能元又分为实体型功能元和联系型功能元.所有功能元组均是实体型的功能元组.树的顶功能元组表示需分析的数控机床系统,功能元组分枝表示数控机床的子系统、子功能单元和子部件,功能元分枝表示该功能元组所包含的功能元.图中的实线为路径,表示从某节点到其后另一节点的功能结构关系.在同一条路径上,相邻层次节点为父子关系.没有父节点的节点为根节点,没有子节点的节点为叶节点.数控机床系统为父节点,而功能元为功能结构树的叶节点.图1功能结构树Fi g.1Tree of function and structure1.4功能元法及其特点(1)功能元法以功能元为基本实体进行数控机床功能信息建模和可靠性分析的方法称为功能元法.功能元法中的数控机床功能信息建模是建立数控机床功能信息抽象模型,为可靠性分析提供数控机床产品的分析基础;可靠性分析是在数控机床功能信息抽象模型的基础上,以功能元为基本实体进行的.(2)功能元法的特点功能元法的优点是能建立高度通用、柔性强、易于重新配置的数控机床可靠性信息系统的框架结构.由于数控机床种类繁多,实现功能千差万别,很难使数控机床可靠性信息系统做到完全意义上的通用,功能元法避免了可靠性分析对数控机床具体功能和功能实现的理解,用户可在数控机床产品可靠性分析的不同阶段,自由地决定分析的层次,通过实例化配置实现再开发.2功能元法的基本理论下面将从以下几个方面探讨功能元法的基本理论:数控机床功能信息模型及其描述方法,功能,可靠性信息的包容原则等.功能信息模型均采用第4期张强,等:数控机床可靠性信息系统信息建模15IDEF1X 方法表示.2.1 数控机床功能信息模型及其描述方法(1)功能信息模型与功能结构树相对应,建立功能元组多层嵌套的数控机床功能信息模型,如图2所示.数控机床的功能可抽象为最高层的功能元组,其父功能元组号为空,功能元组号为数控机床的标识号,功能元组名称为数控机床的名称(包括型号如XXX 数控车床,其中XXX 表示数控车床的型号).数控机床的部件和子系统均可抽象为子功能元组.各部件和子系统之间的联系均可抽象为联系型功能元.每个功能元组根据其实际意义还可能有多个子功能元组./组-功能元0实体模型表示数控机床功能元组或子系统功能元组包括的功能元.实体中的/功能元组号0为对应的功能元组的编号;/组-功能元号0为该功能元的编号;/功能元号0为规定功能元的统一的编号.图2 数控机床的功能信息模型Fi g.2 Function information model of machine tools(2)数控机床功能信息模型的描述方法采用数据库来描述数控机床的功能信息.数控机床功能元组号的格式为Txx(Txx ,,(Y P Xxx)),xx 为两位的数字(00-99),编号中的T 表示功能元组,X 表示实体功能元,Y 表示联系功能元.表1为数控冲床功能信息描述实例.表1 数控冲床的功能信息描述T ab.1 Description of CNC machine tool .s functions 功能元(组)名称功能元(组)号数控机床功能元(组)描述数控冲床T01数控,冲床,板料送料机构T01T01按规定的程序拖动扳料X 轴传动系统T01T01T01按规定的程序拖动扳料沿X 轴运动伺服单元T01T01T01T01交流伺服控制伺服电机T01T01T01T01X01交流伺服电机Z 轴传动系统T01T01T02按规定的程序拖动扳料沿Z 轴运动夹钳T01T01T03夹持扳料2.2 数控机床功能信息的包容原则在图1所示的功能结构树中,功能信息之间存在包容的关系:上层功能元组信息包容下层所属各功能元和功能元组的功能信息.功能信息的包容可以减少信息的冗余,反映功能信息的一致性.数控机床的功能包容所有子系统的功能,同样也包容所有子系统的故障模式.例如,数控冲床送料机构功能包容X 轴传动系统、Z 轴传动系统、夹钳的功能,送料机构故障模式也包容其故障模式.3 数控机床功能信息抽象以功能元为基本实体进行数控机床功能信息建模,对数控机床进行功能抽象,建立功能信息模型.数控车床由C NC 系统、Z 进给系统、X 进给系统、转塔刀架等子系统组成.X 进给系统由伺服单元、进给拖板、导轨等构成,可得其功能结构树,如图3所示.图4为数控车床的功能信息模型实例./数控机床-子系统0实体中,子系统指各层次的功能元组,当子系统为第1层时,父系统编号为数控车床的编号;当子系统为第2层以下层次时,父系统编号为其上一层子系统的编号.在/数控机床-功能元0实体中,数控机床-功能元号为该型号数控车床所有功能元的统一编号;数控机床-系统编号为功能元所属系统的编号;功能元号为规定功能元的统一的编号.图3 数控车床的功能结构图Fig.3 Structure of the CNC machi ne tool .s function图4 数控车床的功能信息模型实例Fi g.4 Instance of the CNC machine tool .sfunction information model16山 东 大 学 学 报 (工 学 版)第35卷4 数控机床可靠性信息抽象在采用FMEA 方法进行数控机床产品的可靠性分析时,首先确定故障发生的部位,由于可靠性分析是基于数控机床产品进行的,故障部位可根据实际情况由规定的分解重组的层次的功能元组和功能元确定.为使数控机床可靠性信息系统具有FMEA 的功能,基于数控机床功能模型,建立了数控机床可靠性信息模型.图5为以数控车床为例的基于功能模型的数控机床可靠性信息模型.图5 基于功能法的数控车床可靠性信息模型Fig.5 The reliabili ty information model of C NCmachi ne tool based on function -method由图5可见,功能元与故障模式和故障模式与故障原因均是一对多的关系.实体中的故障模式号和故障原因号为数控机床可靠性信息系统的统一编号,而数控车床-故障模式号和数控车床-故障原因号为某型号数控车床可靠性信息的统一编号.5 应用实例运用功能元法的理论和方法,基于文献=1>提出的控制模型,开发了文献=2>描述的框架结构的数控机床可靠性信息系统,并应用于国产数控车床、数控冲床、数控轴承磨床、线切割机床等的可靠性增长.在国家/九五0和/十五0攻关项目中,首先对在全国使用的32台某系列国产普及型数控车床的故障数据进行了两年的跟踪记录,获得了较为丰富准确的可靠性数据.机床故障间隔时间分布规律符合威布尔分布,平均无故障时间260h,远低于600~700h 的国际先进水平.为实现对数控车床的F ME A 分析,首先从上而下建立如图3所示的功能结构树,并从下而上分析可能出现的故障的模式、原因和影响,通过图6所示可靠性建模等用户实例配置模块,实现机床功能和可靠性信息的抽象.图6 可靠性建模模块Fig.6 Reliabili ty model通过对该数控车床第一层功能结构树各功能元组故障的分析,CNC 系统发生故障最频繁.通过分析可建立如图7所示数控车床C NC 系统的功能结构树.分析各功能元的故障模式、原因和影响见表2.按照功能元法的包容原则,由功能元FME A 分析的结果可进行C NC 系统和各层次子系统的FMEA,如表3所示.根据试验数据统计,C NC 系统故障主要集中在硬件部分,硬件部分故障又主要是主板经常烧坏,说明数控系统硬件部分存在较大问题.图7 数控车床C NC 系统的功能结构图Fig.7 Structure of the CNC system function根据FMEA 的结果,提出了该系列数控车床改进的具体措施,并建立了可靠性设计、可靠性制造、采购等规范.改进后,通过对15台机床的跟踪,平均无故障时间超过480h,接近了国际先进水平.第4期张 强,等:数控机床可靠性信息系统信息建模17表2数控车床CNC系统硬件系统功能元组FMEATab.2Function element.s FME A of CNC hard ware system功能元模式原因局部影响最终影响主板主板故障元件损坏、线路故障、干扰系统失常系统失常显示器显示器损坏元器件损坏、线路故障不显示无法监控系统控制面板元器件损坏元件损坏、线路故障无法控制系统无法控制系统内存参数丢电池损坏、线路故障控制参数丢系统失常内存功能紊乱干扰、参数错、元器件损坏内存失常系统失常,,表3数控车床CNC系统FMEATab.3CNC system FMEA of the CNC machine tool功能元(组)模式原因局部影响最终影响系统硬件元器件损坏元件损坏、线路故障硬件功能失常系统失常参数丢电池损坏、线路故障控制参数丢系统失常内存功能紊乱干扰、参数错、元件损坏内存失常系统失常通讯故障元件损坏P路故障P干扰P接插件接触不良无法实现与功能模块的通讯不能实现特定功能系统软件软件功能失常干扰\系统程序坏\参数错系统功能失常系统失常误报警干扰、参数错系统功能失常系统失常6结论功能元法基本概念和理论的提出和应用,建立了可靠性分析与数控机床产品的柔性联系,提高了数控机床可靠性信息系统的通用性和柔性,并为数控机床可靠性分析的标准化提供了理论和技术保障,有利于可靠性技术的推广应用.基于功能元法开发的数控机床信息系统已应用于国产数控车床、数控冲床、数控轴承磨床、线切割机床等的可靠性增长.某国产普及型数控车床应用结果表明:该方法适用于对不同种类数控机床进行不同深度可靠性分析的信息建模,数控车床的平均无故障时间由260h提高到480h以上,接近国际先进水平.参考文献:[1]张强,吴耀华,贾亚洲.面向并行工程数控机床可靠性控制模型[J].机械工程学报,2001,37(7):24-27.ZHANG Q,WU Y H,JIA Y C machine tool.s reliability controll model for concurrent engineering[J].Chinese Journal of Mechanical Eng i neering,2001,37(7):24-27.[2]ZHANG Q,LIU S J,DUAN C Y,et al.The architecture ofreliability information system for CNC machine tool in concurrent engineering[J].Materials Science Forum,2004, 471-472.[3]何国伟.可信性工程[M].北京:中国标准出版社,1997.HE G W.Reliability engineering[M].Beiji ng:China Standards Press,1997.[4]WANG Y Q,SHEN G X,JIA Y Z.Multidimensional forcespectra of CNC machine tools and their applications,part two: reliability design of elemen ts[J].International Journal of Fati gue,2003,25(5):447-452.(编辑:陈燕)18山东大学学报(工学版)第35卷。
数控冲床的数据采集与分析技术研究

数控冲床的数据采集与分析技术研究近年来,数控冲床作为一种重要设备,广泛应用于各个行业中的制造业,其高效性和精确性受到了广大企业的青睐。
为了提高冲床的生产效率和质量,数据采集与分析技术在数控冲床的研究中显得尤为重要。
一、数据采集技术1. 传感器技术数据采集的关键是实时获取各个部位的运行数据,而传感器技术无疑是实现这一目标的有效手段之一。
通过在数控冲床的关键节点上安装传感器,可以实时采集到设备的运行状态数据,如冲床的位移、速度、压力、温度等。
这些数据的采集能够为后续的数据分析提供有力支持。
2. 数据存储技术为了保证数据的完整性和可靠性,需要将采集到的数据进行存储。
单一和简单的数据存储方式已经不能满足现代工业生产的需要,因此,需要采用高效、可靠的数据存储技术。
目前,常用的数据存储方式有数据库和云端存储。
数据库可以提供快速的数据存取、查询和分析功能,而云端存储则能够保证数据的安全性和可用性。
3. 数据传输技术为了实现数据的实时采集和远程监控,需要采用数据传输技术将采集到的数据从设备传输到监控中心。
常用的数据传输技术有有线通信和无线通信两种方式。
有线通信方式包括以太网、Modbus等,可以实现稳定可靠的数据传输;无线通信方式包括WIFI、蓝牙、4G等,可以实现无线远程监控。
二、数据分析技术1. 数据预处理技术冲床数据的采集过程中可能会受到各种噪声的干扰,为了保证采集的数据质量,需要进行数据预处理。
常用的数据预处理技术包括滤波、去噪、降噪等。
通过对采集到的原始数据进行预处理,可以提高数据的准确性和可靠性。
2. 数据挖掘技术数据挖掘技术是针对大规模数据进行分析和发现隐藏在其中的有价值信息的一种技术。
在数控冲床的数据分析中,可以应用数据挖掘技术来挖掘出隐藏在数据背后的规律或趋势,从而帮助企业优化生产流程、提高生产效率。
3. 数据可视化技术数据可视化技术可以将复杂的数据以直观、易懂的形式展示出来,帮助决策者直观地了解数控冲床的运行状态。
数控机床的数据采集与分析方法

数控机床的数据采集与分析方法随着信息技术的发展,数据采集和分析在数控机床的制造和维护中起着至关重要的作用。
数据采集可以帮助生产厂家实时监测机床的运行状态、性能指标和生产情况,而数据分析则可以帮助厂家优化生产过程、提高机床的使用效率和预测故障。
一、数据采集方法1. 传感器采集:数控机床普遍配备了各种类型的传感器,如温度传感器、压力传感器、振动传感器等,用于采集机床不同部件的运行情况。
通过传感器采集到的数据可以及时反馈到系统中,帮助监测机床的工作状态。
2. 数字控制系统采集:数控机床的数字控制系统可以采集到各种运行参数和状态信息,如主轴转速、进给速度、切削力、功率消耗等。
这些数据可以通过数字接口传输到外部计算机系统,以供进一步分析和利用。
3. 人工采集:除了传感器和数字控制系统采集的数据,操作人员也可以通过观察和记录的方式采集一些关键数据,如故障发生时间、生产数量、停机时间等。
二、数据分析方法1. 统计分析:通过对采集到的数据进行统计分析,可以发现机床的运行模式和规律,如设备的平均运行时间、故障发生的频率和位置等。
这些统计结果可以帮助厂家对设备的使用情况进行评估,制定更合理的生产计划。
2. 故障诊断:利用机床采集到的数据,结合故障数据库和专家经验,可以对机床的故障进行诊断。
通过分析故障发生时的数据特征,可以快速定位故障原因,减少停机时间和维修成本。
3. 运行参数优化:利用数据分析的方法,可以分析机床在不同参数设置下的性能表现,如主轴转速、进给速度等。
通过对数据的分析,可以找到最佳的参数组合,实现机床的最佳运行状态,提高生产效率和产品质量。
4. 预测维护:利用历史数据和机器学习算法,可以建立机床的故障预测模型。
通过对机床运行数据的分析,可以提前预警设备可能发生的故障,并采取相应措施,避免设备停机和生产中断。
5. 能耗分析:通过采集机床的能耗数据,可以对机床的能源利用情况进行分析。
通过找到能耗高的设备和环节,可以进行合理的优化和节能措施,降低生产成本和环境污染。
工业制造数控机床联网及数据采集管理系统PPT课件
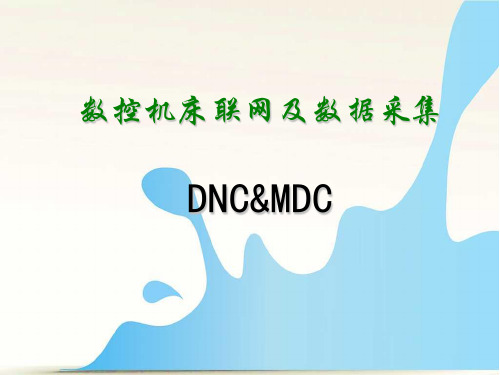
MDC-采集方式
2、硬件采集
(1)采集信息: 开机时间、运行时间、待机时间、主轴功率。 在条件允许情况下,通过修改PLC可额外采集到运行模式、产量、倍
率等信息。 (2)采集条件: 具备开放的PLC并有扩展的接线端子等。
MOXA ioLogik E1200系列
电流传感器
MDC-系统集成
DNC系统与其他系统集成主要是MDC与MES集成,当然也有和其他软件 的集成。主要集成方式如下:
1、客户端主界面
MDC-功能介绍
2、实时状态图
MDC-功能介绍
3、生产信息表
MDC-功能介绍
4、设备日志表
MDC-功能介绍
5、多台状态对比
MDC-功能介绍
6、单台状态对比
MDC-功能介绍
7、状态分布
MDC-功能介绍
8、效率分析
9、工艺曲线
MDC-功能介绍
MDC-功能介绍
10、报警查询
设备/产品/人员
资源状态 生产进度 质量数据
不能自动、实时、准确、稳定的获取底层资源状态数据, MES难以真正发挥作用!
数控机床联网采集是智能制造的 重要基础
智能制造
深度感知、智慧决策、精准控制、自动执行
设备互联(DNC),建立实时信息通道是智能制造的基础!
程序传输
实时 采控
云端 分析
智能 制造
解决方案
MDC-功能介绍
11、产量统计
MDC-功能介绍
12、效能报表
MDC-功能介绍
13、服务端主界面
MDC-功能介绍
14、机床参数维护
MDC-采集方式
1、网卡采集
FANUC 0i-MD采集界面
SIEMENS840D采集界面
机床行业数据采集解决方案
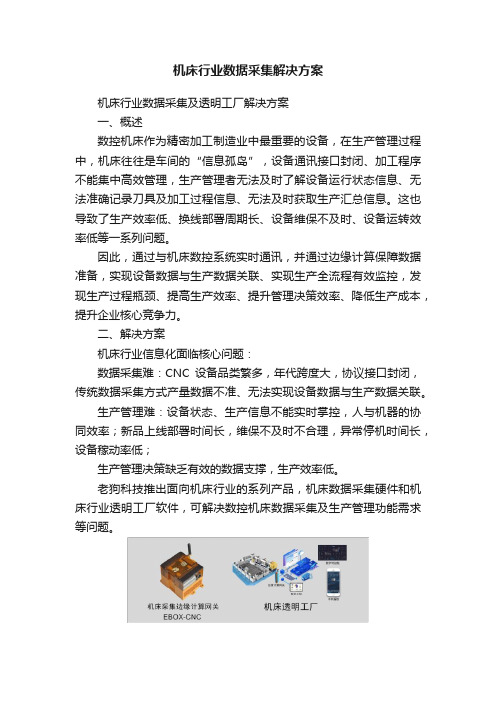
机床行业数据采集解决方案机床行业数据采集及透明工厂解决方案一、概述数控机床作为精密加工制造业中最重要的设备,在生产管理过程中,机床往往是车间的“信息孤岛”,设备通讯接口封闭、加工程序不能集中高效管理,生产管理者无法及时了解设备运行状态信息、无法准确记录刀具及加工过程信息、无法及时获取生产汇总信息。
这也导致了生产效率低、换线部署周期长、设备维保不及时、设备运转效率低等一系列问题。
因此,通过与机床数控系统实时通讯,并通过边缘计算保障数据准备,实现设备数据与生产数据关联、实现生产全流程有效监控,发现生产过程瓶颈、提高生产效率、提升管理决策效率、降低生产成本,提升企业核心竞争力。
二、解决方案机床行业信息化面临核心问题:数据采集难:CNC设备品类繁多,年代跨度大,协议接口封闭,传统数据采集方式产量数据不准、无法实现设备数据与生产数据关联。
生产管理难:设备状态、生产信息不能实时掌控,人与机器的协同效率;新品上线部署时间长,维保不及时不合理,异常停机时间长,设备稼动率低;生产管理决策缺乏有效的数据支撑,生产效率低。
老狗科技推出面向机床行业的系列产品,机床数据采集硬件和机床行业透明工厂软件,可解决数控机床数据采集及生产管理功能需求等问题。
2.1 数据采集:机床采集边缘计算网关2.1.1优势1)无需授权协议即插即用、兼容100%老旧CNC及周边设备;2)支持边缘计算,采集数据更加准确、并可挖掘更多可用数据价值;3)支持CNC程序下发;4)数据分频传输,数据高效应用,减轻服务器后台数据处理负荷;5)兼容性好,可接入CNC周边设备,包括CNC能耗、压铸机、切割机等。
2.1.2 支持品牌型号兼容常见机床的通讯协议,如西门子、FANUC、三菱、广数、HASS、兄弟、华中数控、赫克等品牌。
2.2 解决方案:机床行业透明工厂“机床行业透明工厂”,通过边缘计算网关与数控系统进行实时通讯,结合极简工业全新的生产管理工具,为客户提供从机床数据采集、边缘计算分析、数据应用到数字驾驶舱、透明工厂的一站式解决方案。
工程机械可靠性数据管理系统设计
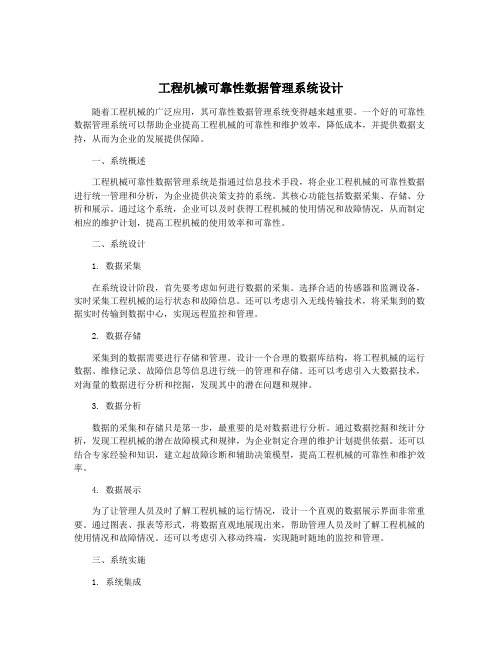
工程机械可靠性数据管理系统设计随着工程机械的广泛应用,其可靠性数据管理系统变得越来越重要。
一个好的可靠性数据管理系统可以帮助企业提高工程机械的可靠性和维护效率,降低成本,并提供数据支持,从而为企业的发展提供保障。
一、系统概述工程机械可靠性数据管理系统是指通过信息技术手段,将企业工程机械的可靠性数据进行统一管理和分析,为企业提供决策支持的系统。
其核心功能包括数据采集、存储、分析和展示。
通过这个系统,企业可以及时获得工程机械的使用情况和故障情况,从而制定相应的维护计划,提高工程机械的使用效率和可靠性。
二、系统设计1. 数据采集在系统设计阶段,首先要考虑如何进行数据的采集。
选择合适的传感器和监测设备,实时采集工程机械的运行状态和故障信息。
还可以考虑引入无线传输技术,将采集到的数据实时传输到数据中心,实现远程监控和管理。
2. 数据存储采集到的数据需要进行存储和管理。
设计一个合理的数据库结构,将工程机械的运行数据、维修记录、故障信息等信息进行统一的管理和存储。
还可以考虑引入大数据技术,对海量的数据进行分析和挖掘,发现其中的潜在问题和规律。
3. 数据分析数据的采集和存储只是第一步,最重要的是对数据进行分析。
通过数据挖掘和统计分析,发现工程机械的潜在故障模式和规律,为企业制定合理的维护计划提供依据。
还可以结合专家经验和知识,建立起故障诊断和辅助决策模型,提高工程机械的可靠性和维护效率。
4. 数据展示为了让管理人员及时了解工程机械的运行情况,设计一个直观的数据展示界面非常重要。
通过图表、报表等形式,将数据直观地展现出来,帮助管理人员及时了解工程机械的使用情况和故障情况。
还可以考虑引入移动终端,实现随时随地的监控和管理。
三、系统实施1. 系统集成系统设计完成后,需要进行系统集成和实施。
选择合适的硬件设备和软件平台,进行系统的建设和部署。
与现有的企业信息系统进行对接,实现数据的共享和集成,提高系统的整体效益。
2. 人员培训一个好的系统需要有专业的人员进行运维和管理。
CNC机床加工中的数据采集与分析技术

CNC机床加工中的数据采集与分析技术随着工业自动化的快速发展,计算机数控(CNC)机床在现代制造业中扮演着重要的角色。
CNC机床通过精确控制和操作工件的切削工具,实现高效、精密的加工任务。
在CNC机床加工过程中,数据的采集与分析技术的应用变得越来越重要。
本文将探讨CNC机床加工中的数据采集与分析技术的意义、方法和应用。
一、数据采集的意义数据采集是指通过传感器、监测装置等手段,收集CNC机床加工过程中所产生的各类数据。
这些数据包括切削力、温度、振动、工件位置等。
数据采集的意义在于:1. 提高加工质量和效率:通过及时采集和分析数据,可以对CNC 机床加工过程中的异常情况进行监测和预警,及时调整参数和控制策略,从而提高加工质量和效率。
2. 实现智能化管理:数据采集为CNC机床加工提供了大量的实时信息,通过对这些信息的分析和挖掘,可以实现智能化管理和优化,提高生产效益。
3. 提高设备可靠性和维护效率:通过对CNC机床加工数据的采集和分析,可以了解设备的工作状态和磨损程度,及时排除故障和进行维护,延长设备的使用寿命。
二、数据采集的方法数据采集可以通过多种方式实现,常用的方法包括:1. 传感器采集:通过安装感应器,如应力传感器、温度传感器等,在CNC机床的关键部位进行数据采集。
传感器将实时监测的信号转换为电信号,再通过数据采集系统进行数字化处理,并传输到数据存储设备中。
2. 数据总线采集:采用数据总线技术,将CNC机床的各个部分连接到同一个网络中,实现数据的实时传输和共享。
通过总线接口,可以从机床的各个组成部分,如电机、控制器、传感器等,采集各种数据。
3. 人工采集:除了自动化的数据采集方式外,人工采集也是一种常用的方法。
在CNC机床加工过程中,操作人员可以手动记录关键数据,如刀具磨损情况、加工参数等。
三、数据分析的技术数据采集只是第一步,对采集到的数据进行分析是实现加工优化和设备管理的关键。
下面介绍几种常用的数据分析技术:1. 统计分析:通过统计方法对采集到的数据进行处理,获得加工过程中的平均值、标准差、极差等参数,帮助判断加工的稳定性和可靠性。
数控车床可靠性数据的采集及数据库建立

序号
名称
类型 宽度 序号
名称
类型 宽度
1 机床编码 字符 8 10 修复日期 日期 8 2 机床型号 字符 8 11 故障时间 数字 8. 3 3 机床名称 字符 40 12 修复时间 数字 8. 3 4 使用厂家 字符 40 13 维修时间 数字 8. 3 5 制造厂家 字符 40 14 维修工时 数字 8. 3 6 故障现象 字符 40 15 故障模式 字符 40 7 故障原因 字符 40 16 故障部位 字符 40 8 处理方法 字符 40 17 累积时间 数字 10. 3 9 故障日期 日期 8 18 故障编码 字符 8
可靠性分析是以大量的现场数据为基础的, 只有 在拥有真实、可靠数据的基础上, 我们才能进行故障分 析、可靠性设计等, 才能对机床的设计、使用、维修等提 出合理的改进意见。可靠性数据的积累是一个长期的、 艰巨的过程。在此过程中必须对数据进行有效的组织 和管理, 而这是手工难以完成的, 必须借助于计算机数 据库技术。数据库可以理解为在一个或多个单位中, 为 多个用户服务的、在计算机上可运行的、具有一定结构 的数据集合。目前较流行的数据库类型有三种: 层次 型、网络型和关系型。我们使用关系型数据库管理系统 FOXPRO, 建立了数控车床可靠性数据库。
NC CNC 系统 G 气动系统 E 电源 Q 整体防护 N 不明
H 机械手 A A 轴进给系统
PC PL C 系统 L 润滑系统 P 外接口
V 电器系统
故障 部位: 发生 故障的子 系统及部 件, 以代码 表
示。具体代码见表 4; 维修工时: 维修时所耗费的工时( 单位: 工时) ; 累积时间: 从试验开始到本次故障总的工作时间
36 定向不准 37 坐标原点漂移 38 噪声超标 39 温升过高 40 气、液控制失灵 41 液、气、油渗漏 42 液、气、油堵塞不畅 43 液、气、油元部件损坏 44 密封件损坏 45 护板、护罩损坏 46 防护门开关损坏 47 数控系统不能正常工作 48 主机未按程序指令执行 49 程序、参数记忆功能紊乱 50 数据传输错误 51 元器件功能丧失 52 元器件误动作 53 元器件损坏 54 元器件参数漂移 55 电机起动不起来 56 电机不能正常工作 57 电机过载 58 电机损坏 59 误报警 60 线路、电缆接触不良 61 线路、电缆断路 62 线路、电缆短路 63 熔断器损坏 64 传感部件失灵 65 易损件超期损坏 66 转塔转位不灵活 67 空气开关跳 68 CNC 参数错 69 其它
- 1、下载文档前请自行甄别文档内容的完整性,平台不提供额外的编辑、内容补充、找答案等附加服务。
- 2、"仅部分预览"的文档,不可在线预览部分如存在完整性等问题,可反馈申请退款(可完整预览的文档不适用该条件!)。
- 3、如文档侵犯您的权益,请联系客服反馈,我们会尽快为您处理(人工客服工作时间:9:00-18:30)。
数控车床可靠性数据的采集及数据库建立1 前言数控机床是现代制造技术的基础装备,其技术水平高低是衡量一个国家的工业现代化水平的重要标志。
数控机床的可靠性是机床质量的关键。
目前国产数控机床的可靠性水平与国外相比明显偏低,严重影响了国产数控机床的竞争能力,提高国产数控机床的可靠性已成为当务之急。
可靠性分析是以大量的现场数据为基础的,借助有计划、有目的地收集产品寿命周期各阶段的数据,进行分析,发现产品可靠性的薄弱环节,改进设计,从而提高产品质量,所以可靠性数据的收集和分析在可靠性工程中具有重要地位。
然而这方面正是国内可靠性研究中的一个薄弱环节。
在1996年7月1日至1996年12月31日期间,我们收集了一汽集团长春齿轮厂的42台CNC车床的可靠性数据,并初步建立了数控车床可靠性数据库。
以此为例说明数控机床可靠性数据的采集方法及数据库的建立方法。
2 可靠性试验方案的确定可靠性试验是取得可靠性数据的主要方法之一,它是进行可靠性设计和分析的基础。
近30年来,可靠性试验方法取得很大发展。
可靠性试验既费时又费钱。
对于数控车床而言,主要考虑试验场所和试验样本两方面。
按试验场所,可靠性试验分为现场试验和实验室试验两种。
数控车床由于结构复杂,使用条件中的不确定因素很多,故选用现场试验方法能够采集到真实的可靠性情况。
在现场试验中数据可靠性问题是一个关键问题。
事先必须制订完善的采集计划,事后应对数据进行处理,以排除不合理因素。
可靠性试验按样本大小可以分成全数试验和抽样试验两类。
对于数控车床这种批量产品不可能进行全数试验,只能采用抽样定时截尾的试验方法。
为了使收集到的数据具有代表性,并且便于数据收集,在选取试验样本时,应选取尽量多的数控车床作为抽样样本,所选取的设备应该比较集中。
因此本文选择了数控车床使用量大且设备比较集中的一汽集团长春齿轮厂作为试验基地,将其42台CNC车床作为样本,进行了半年跟踪调查。
3 可靠性数据的采集根据《数控车床可靠性评定方法》,即标准JB/GQ1153-90数控车床的故障判据为:1.由于数控车床的质量缺陷,在规定条件下、规定时间内不能完成规定功能的事件便成为故障。
2.在用户正常使用之前的早期故障,由于是在规定的截取范围以外,所以不计为故障。
3.与整机功能暂时无关或影响较小的局部微小故障不计为故障。
4.不按规定操作使用而引起的误用故障不计为故障。
在进行数据采集之前,必须首先明确数控车床故障模式。
我们在参考《数控车床可靠性评定方法》的同时,根据数控车床的本身特点和使用中的实际情况,制定了数控车床故障模式表(表1)。
根据所确定的试验方案,按如下步骤进行数据采集:表 1数控车床故障模式表序号故障模式序号故障模式序号故障模式1 2 3 4 5 6 7 8 91011121314151617181920212223运动部件爬行运动部件抖动运动部件异响运动部件制动失灵运动部件间隙过大运动部件窜动运动部件过紧运动部件卡死运动部件变速失灵运动部件超速运动部件掉档振动影响工件质量机电互锁机构失灵锁紧部件失灵紧固件松动预紧机构松动定位装置失灵夹紧装置失灵夹紧装置提前夹紧夹紧装置提前松开夹紧装置夹不紧夹紧装置松不开零、部件损坏2425262728293031323334353637383940414243444546零、部件变形零、部件松动零、部件脱落轴承损坏转位无动作转位不到位转位超程几何精度超标定位精度超标工作精度超标性能参数下降回零不准定向不准坐标原点漂移噪声超标温升过高气、液控制失灵液、气、油渗漏液、气、油堵塞不畅液、气、油元部件损坏密封件损坏护板、护罩损坏防护门开关损坏4748495051525354555657585960616263646566676869数控系统不能正常工作主机未按程序指令执行程序、参数记忆功能紊乱数据传输错误元器件功能丧失元器件误动作元器件损坏元器件参数漂移电机起动不起来电机不能正常工作电机过载电机损坏误报警线路、电缆接触不良线路、电缆断路线路、电缆短路熔断器损坏传感部件失灵易损件超期损坏转塔转位不灵活空气开关跳CNC参数错其它参考《数控车床可靠性评定方法》,我们编制了《数控车床故障分析报告》(表2),分别对每台受试车床进行跟踪。
表2 数控车床故障分析报告车间班组年月日设备编号设备役龄设备型号设备名称故障序号工作环境故障现象故障原因处理方法起始时间日时分共计台时终止时间日时分工时2修理工34维修组长56设备使用人7《数控车床故障分析报告》填写说明:从试验开始起,记录被试车床故障,发生一次故障,填写一份故障分析报告。
按照故障发生时间顺序填写故障序号。
要求填表人签字,用户单位加盖公章,以保证数据真实、可靠。
与协作厂家定好执行计划,由厂家派专人负责填写故障分析报告。
一旦故障发生,立即根据故障判据和故障类型填写报告,恢复后应继续观察。
每隔一定时间进行中途检查,了解现场情况,并就具体问题进行指导。
由现场试验中得到的主要数据项如表2所示。
这样就可以根据需要建立数控车床的可靠性数据库,以满足不同的数据分析要求。
4 数控车床可靠性数据库的建立可靠性分析是以大量的现场数据为基础的,只有在拥有真实、可靠数据的基础上,我们才能进行故障分析、可靠性设计等,才能对机床的设计、使用、维修等提出合理的改进意见。
可靠性数据的积累是一个长期的、艰巨的过程。
在此过程中必须对数据进行有效的组织和管理,而这是手工难以完成的,必须借助于计算机数据库技术。
数据库可以理解为在一个或多个单位中,为多个用户服务的、在计算机上可运行的、具有一定结构的数据集合。
目前较流行的数据库类型有三种:层次型、网络型和关系型。
我们使用关系型数据库管理系统FOXPRO,建立了数控车床可靠性数据库。
建立数控车床可靠性数据库主要目的如下:为数控车床的可靠性指标评估提供重要信息;为故障分析,可靠性设计提供基础数据;为改进数控车床的可维修性,提高数控车床的使用有效度提供信息;建立数控车床的故障档案,以便进行比较和预测。
数控车床可靠性数据库的数据结构如表3所示。
为满足数据分析的需要,它所包含的字段名称与表2中各记录项目名称有所不同。
现对部分字段作如下解释。
故障日期:数控车床发生故障时的具体日期(年/月/日);修复日期:数控车床恢复正常工作时的具体日期(年/月/日);故障时间:发生故障时的具体时间(单位:h);修复时间:机床恢复正常工作时的具体时间(单位:h);维修时间:指纯修理时间(单位:台时);表 4子系名称代码名称代码名称统及部件代码代码S1XBFWTJS2Y主传动系统X向进给系统B轴进给系统伺服控制单元冷却系统工作台卡盘及夹具主轴组件Y向进给系统CDKCTVMZNCGC轴进给系统液压系统排屑系统交换工作台电器系统转塔(刀库)Z向进给系统CNC系统气动系统EQNHAPCLPR电源整体防护不明机械手A轴进给系统PLC系统润滑系统外接口其它故障部位:发生故障的子系统及部件,以代码表示。
具体代码见表4;维修工时:维修时所耗费的工时(单位:工时);累积时间:从试验开始到本次故障总的工作时间(单位:h);故障编码:即故障分析报告中的故障序号;机床编码;由8位数字组成,具体如右图所示:按照上述数据结构和内部编码方法,建立数据库文件DA TABAS.DBF。
由数据库文件DA TABAS.DBF生成如下索引文件:IDXTOOL.IDX、IDXFACT.IDX、IDXUSE.IDX、IDXMODE.IDX、IDXPOS.IDX等。
利用这些索引文件,我们可以对数据库中的数据,分别按照机床、制造厂、使用厂、故障模式、故障部位等字段进行检索或数据重组,以满足不同目的的数据分析要求。