天车简单故障处理
天车操作发生故障的处理流程

天车操作发生故障的处理流程下载温馨提示:该文档是我店铺精心编制而成,希望大家下载以后,能够帮助大家解决实际的问题。
文档下载后可定制随意修改,请根据实际需要进行相应的调整和使用,谢谢!并且,本店铺为大家提供各种各样类型的实用资料,如教育随笔、日记赏析、句子摘抄、古诗大全、经典美文、话题作文、工作总结、词语解析、文案摘录、其他资料等等,如想了解不同资料格式和写法,敬请关注!Download tips: This document is carefully compiled by theeditor. I hope that after you download them,they can help yousolve practical problems. The document can be customized andmodified after downloading,please adjust and use it according toactual needs, thank you!In addition, our shop provides you with various types ofpractical materials,such as educational essays, diaryappreciation,sentence excerpts,ancient poems,classic articles,topic composition,work summary,word parsing,copy excerpts,other materials and so on,want to know different data formats andwriting methods,please pay attention!处理天车操作发生故障的流程如下:1. 立即停车在天车操作过程中,一旦发现任何故障迹象,应立即按下停车按钮,使天车停止运行。
天车机械常见问题及排除方法

安全意识教育与培训
开展安全意识教育
通过开展安全意识教育活动,提高操作人员的安全意识,使其认 识到安全的重要性。
定期进行安全培训
定期组织安全培训活动,包括理论知识和实际操作技能的培训,确 保操作人员具备足够的安全知识和技能。
建立安全责任制度
建立安全责任制度,明确各级管理人员和操作人员的安全职责,形 成全员参与的安全管理格局。
线路故障
由于线路老化、连接不良等原因,可能导致线路 短路、断路或接触不良。
控制系统故障
如PLC、变频器等控制系统可能出现故障,导致天 车无法正常工作。
机械系统问题
传动系统故障
如减速机、链条等传动部件可能因润滑不良、安装不 当等原因出现故障。
轨道问题
轨道不直、轨道接头错位等可能导致天车运行不稳或 卡滞。
机械系统故障排除
总结词
机械系统故障通常表现为运动部件异常、结 构件损坏等,需定期维护和检查。
检查传动装置
检查传动带、链条、齿轮等是否正常工作, 有无松动或磨损。
检查结构件
检查天车的梁、轨道、轴承等结构件是否完 好,有无变形或损坏。
检查运动部件
检查滑轮、车轮、吊钩等运动部件是否正常, 有无卡滞或异常声响。
天车机械的种类与用途
种类
天车机械的种类繁多,根据其用途和 结构可分为桥式、门式、单梁式、双 梁式、悬臂式等多种类型。
用途
天车机械广泛应用于钢铁、化工、电 力、造船、港口等行业的物料搬运和 设备安装,是现代化工业生产中不可 或缺的重要设备。
天车机械的发展历程
初期阶段
天车机械的雏形可以追溯到古代 的起重设备和建筑机械,如杠杆、 滑轮等。
车轮问题
车轮磨损、轮缘断裂等可能导致天车运行不稳或掉道。
450T天车故障查找及处置办法

450T天车故障查找及处置办法一、急停一、急停灯亮包括以下几种情形:一、急停按钮被压下。
全车一共6。
有PLC柜内急停、东电气梁内急停、西电气梁内急停、主小车急停、副小车急停、司机室内急停。
二、整机急停。
共五种情形。
包括:主起升整机急停(K01)副起升整机急停(K04)能够在触摸屏的监控总揽和各机构状态上查询相应机构的状态和急停状态。
3、各机构控制回路跳闸。
主如果辅助配电柜的F21——主起升控制回路F22——主小车控制回路F23——副小车控制回路F24——大车控制回路F25——副起升控制回路4、主起升或副起升的重锤出现故障。
五、主、副起升逆变器出现FXXX的形式,即逆变器出现故障。
在司机室压复位按钮进行复位或压变频器操作面板上的P键进行复位。
六、整车掉电。
二、大车无法运行1、如果两个方向都不能走,查看门是不是关好。
若是门开关没有关好,则将门从头关上;若是是门开关损坏,则将门开关的限位进行强制。
将大车/副起升连锁柜的K1六、K17、K1八、K19进行强制。
二、查看大车轨道限位和激光防碰撞装置(一个方向不能走)。
激光防撞限位:强制大车/副起升连锁柜的K7、K八、K 九、K11。
用手挡一下。
大车轨道限位:强制大车副起升连锁柜的K13(东减速继电器)K14(西减速继电器)K28和K29(东停止继电器)K30和K31(西停止继电器)3、查看大车逆变器1#和2#是不是报FXXX故障。
如在司机室压故障复位按钮进行复位。
若是故障无法复位当即将大车装置选择开关进行切换,选1号单机或2号单机,然后进行复位。
(若无法复位,且变频器报F149时为抱闸反馈故障)4、查看大车副起升切换柜(东梁)的电机电源Q一、Q2是不是跳闸和2号大车逆变柜(西梁)的电机电源Q一、Q2是不是跳闸。
五、查看大车抱闸电源开关Q71,Q一、Q二、Q4、Q5是不是跳闸。
能够从触摸屏的大车机构上看到。
位于大车副起升连锁柜(东梁)6、查看大车手柄接线是不是是松动(动手柄并观看相应的限位)。
天车常见故障处理方法大全
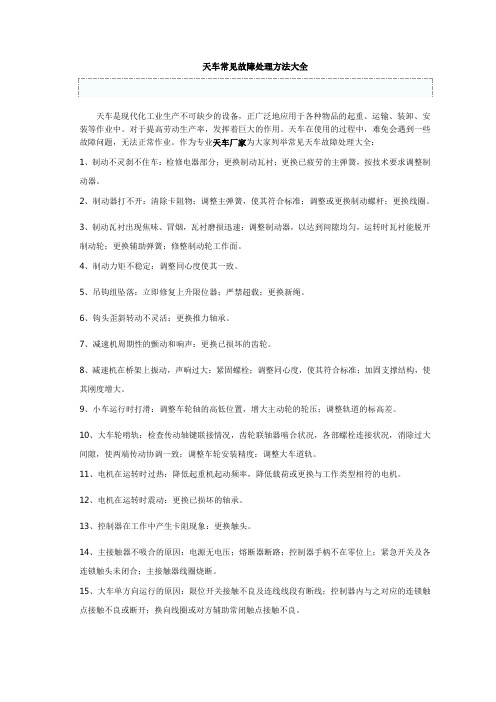
天车常见故障处理方法大全天车是现代化工业生产不可缺少的设备,正广泛地应用于各种物品的起重、运输、装卸、安装等作业中。
对于提高劳动生产率,发挥着巨大的作用。
天车在使用的过程中,难免会遇到一些故障问题,无法正常作业。
作为专业天车厂家为大家列举常见天车故障处理大全:1、制动不灵刹不住车:检修电器部分;更换制动瓦衬;更换已疲劳的主弹簧,按技术要求调整制动器。
2、制动器打不开:清除卡阻物;调整主弹簧,使其符合标准;调整或更换制动螺杆;更换线圈。
3、制动瓦衬出现焦味、冒烟,瓦衬磨损迅速:调整制动器,以达到间隙均匀,运转时瓦衬能脱开制动轮;更换辅助弹簧;修整制动轮工作面。
4、制动力矩不稳定:调整同心度使其一致。
5、吊钩组坠落:立即修复上升限位器;严禁超载;更换新绳。
6、钩头歪斜转动不灵活:更换推力轴承。
7、减速机周期性的颤动和响声:更换已损坏的齿轮。
8、减速机在桥架上振动,声响过大:紧固螺栓;调整同心度,使其符合标准;加固支撑结构,使其刚度增大。
9、小车运行时打滑:调整车轮轴的高低位置,增大主动轮的轮压;调整轨道的标高差。
10、大车轮啃轨:检查传动轴键联接情况,齿轮联轴器啮合状况,各部螺栓连接状况,消除过大间隙,使两端传动协调一致;调整车轮安装精度:调整大车道轨。
11、电机在运转时过热:降低起重机起动频率,降低载荷或更换与工作类型相符的电机。
12、电机在运转时震动:更换已损坏的轴承。
13、控制器在工作中产生卡阻现象:更换触头。
14、主接触器不吸合的原因:电源无电压;熔断器断路;控制器手柄不在零位上;紧急开关及各连锁触头未闭合;主接触器线圈烧断。
15、大车单方向运行的原因:限位开关接触不良及连线线段有断线;控制器内与之对应的连锁触点接触不良或断开;换向线圈或对方辅助常闭触点接触不良。
16、副钩不能上升的原因:上升限位开关断开;触点接触不良;滑线断线。
天车故障应急救援预案

天车故障应急救援预案一、预案目的为确保天车在作业过程中出现故障时,能够迅速、有效地进行应急处理,保障人员安全和财产损失降到最低,制定本预案。
二、预案适用范围本预案适用于公司内所有天车作业过程中出现的故障应急处理。
三、预案内容1. 天车故障类型及应急措施(1)溜钩失控应急程序:- 立即鸣长铃警示地面人员,让地面人员避让。
- 操作人员保持冷静,一手操作大车或小车运行机构控制器避开地面人员,另一手迅速点动一次该机构控制器判断故障原因。
- 若属机械原因偶尔卡住或电器触头粘接,一般情况下点动一次,该机构即可恢复正常。
- 若仍然无法将重物坠落现象消除,按以下程序操作:机械原因所致:迅速将该机构控制器打到下降方向的最后一档,用电动机发出功能控制重物快速下降,坠落现象,并在吊钩上升下降允许范围内反复操作上升和下降控制器,同时另一只手还要操作大小车移动运行机构控制器,就近的选择一个平整安全的地方将重物放到地面,然后检查并排除故障。
注意在操作过程中不宜过快,谨防因操作过快引起反接电流过大造成天车或配电室电器跳闸。
电气原因所致:立即将所控制器操作手柄放回零位停稳天车后,迅速按下紧急开关,切断天车主电源,并拉下总电源开关,重物坠落现象即可消失。
重物停止坠落后立即汇报维修人员和当班班长协商处理,若需长时间处理故障重物仍在空中时应用工具松开吊钩制动器缓慢将重物放至地面。
(2)天车控制手柄失灵应急程序:- 利用紧急开关断开电源保修。
- 司机和指挥人员禁止走开现场,要戒备任何人禁止经过危险区,等电力恢复或设施办理完后将吊运的重物放好后才能走开。
(3)天车在吊运重物时发生故障,不可以起落应急程序:- 立刻派人查察电源能否跳闸;如电源无故障,应联系维修工进行维修。
- 维修前应先搭乘液压起落台升至电动葫芦旁,松开行走抱闸手动将主钩挪动到适合地点,松开主钩抱闸迟缓落下重物后,再进行维修。
(4)天车发生故障没法行走时应急程序:- 天车司机和维修工上下天车时一定搭乘液压起落台。
天车故障手册

《天车故障手册》要求:针对故障现象,找出发生故障的原因,知道如何排除及方法。
一、大车单方向运行的故障排除:1、限位开关接触不良及连线线段有断线。
1、找出断线位置,消除接触不良。
2、控制器内与之对应的连锁触点接触不2、检修触点。
良或断开。
3、换向线圈或对方辅助常闭触点接触不3、更换线圈,检修触点。
良。
二、付钩不能上升的故障排除;1、上升限位开关断开。
1、检修限位开关。
2、控制器3、5触点接触不良,元件接2、检修触点,测量连线排除断线。
触不良。
3、滑线(29#)断线。
3、检查连线情况,找出断点加以修复。
(培训中大家独立画出主钩操作回路电路图)作业与习题:1、桥架型起重机是取物装置悬挂在可沿桥架运行的起重小车或运行式葫芦上的起重机。
()2、桥架型起重机就是桥式起重机。
()3、桥式起重机是桥架两端通过运行装置直接支承在高架轨道上的桥架型起重机。
()4、门式起重机是桥架通过两侧支腿支承在地面轨道或地基上的桥架型起重机。
()5、吊钩起重机与抓斗起重机和电磁起重机的起升机构、运行机构都不同。
()三、付钩不能下降的故障排除:1、控制器内3、5方向联锁触点接触不良1、检修触点、线辫,用万用表测连线。
或连线断。
2、主接触器辅助触点1、3接触不良。
2、检修触点。
3、保险1R断或松动。
3、更换排除。
四、上升接触器不吸合的故障排除:1、限位或连线断。
1、找出断点位置排除。
2、控制器内K6触点接触不良。
2、检修触点加以修复。
3、下降与4Y接触器辅助常闭触点不通。
3、检修接触器与触点,消除问题。
4、线圈损坏或无电压。
4、更换线圈,测量电压。
5、它们之间的连线断。
5、用万用表找出断线点排除。
作业与习题:6、按照取物装置不同,桥式起重机可分为通用起重机和冶金桥式起重机两大类。
()7、桥式起重机主要由金属结构(桥梁)、小车、大车运行机构和电气四大部分组成。
()8、单钩桥式起重机是通用桥式起重机的基本类型,其他各种桥式起重机是由此派生出来的。
天车常见故障处理与日常维护
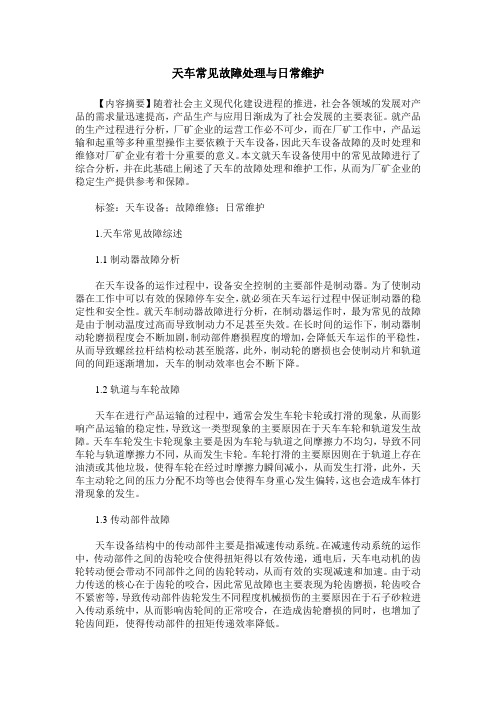
天车常见故障处理与日常维护【内容摘要】随着社会主义现代化建设进程的推进,社会各领域的发展对产品的需求量迅速提高,产品生产与应用日渐成为了社会发展的主要表征。
就产品的生产过程进行分析,厂矿企业的运营工作必不可少,而在厂矿工作中,产品运输和起重等多种重型操作主要依赖于天车设备,因此天车设备故障的及时处理和维修对厂矿企业有着十分重要的意义。
本文就天车设备使用中的常见故障进行了综合分析,并在此基础上阐述了天车的故障处理和维护工作,从而为厂矿企业的稳定生产提供参考和保障。
标签:天车设备;故障维修;日常维护1.天车常见故障综述1.1制动器故障分析在天车设备的运作过程中,设备安全控制的主要部件是制动器。
为了使制动器在工作中可以有效的保障停车安全,就必须在天车运行过程中保证制动器的稳定性和安全性。
就天车制动器故障进行分析,在制动器运作时,最为常见的故障是由于制动温度过高而导致制动力不足甚至失效。
在长时间的运作下,制动器制动轮磨损程度会不断加剧,制动部件磨损程度的增加,会降低天车运作的平稳性,从而导致螺丝拉杆结构松动甚至脱落,此外,制动轮的磨损也会使制动片和轨道间的间距逐渐增加,天车的制动效率也会不断下降。
1.2轨道与车轮故障天车在进行产品运输的过程中,通常会发生车轮卡轮或打滑的现象,从而影响产品运输的稳定性,导致这一类型现象的主要原因在于天车车轮和轨道发生故障。
天车车轮发生卡轮现象主要是因为车轮与轨道之间摩擦力不均匀,导致不同车轮与轨道摩擦力不同,从而发生卡轮。
车轮打滑的主要原因则在于轨道上存在油渍或其他垃圾,使得车轮在经过时摩擦力瞬间减小,从而发生打滑,此外,天车主动轮之间的压力分配不均等也会使得车身重心发生偏转,这也会造成车体打滑现象的发生。
1.3传动部件故障天车设备结构中的传动部件主要是指减速传动系统。
在减速传动系统的运作中,传动部件之间的齿轮咬合使得扭矩得以有效传递,通电后,天车电动机的齿轮转动便会带动不同部件之间的齿轮转动,从而有效的实现减速和加速。
各种天车的故障及排除方法

各种天车的故障及排除方法天车是一种重型起重设备,常见的故障包括电气故障、机械故障、液压故障等。
下面将分别介绍各种天车的常见故障及排除方法。
1.电气故障:-电机无法正常启动:可能是供电不足或者电机损坏。
检查供电线路和开关,确认供电是否正常,并检查电机绕组是否有断路或短路现象。
-开关失灵:检查开关是否损坏或老化,并进行更换。
-控制器故障:检查控制器上的电路板和元件,排除故障,如有需要,更换控制器。
-停机按钮无法解锁:可能是按钮卡住或者按钮本身故障,检查按钮是否松动或损坏,并进行维修或更换。
2.机械故障:-传动装置故障:检查传动链条、齿轮、轴承等,是否有磨损、断裂或损坏的情况,及时更换损坏部件。
-起重机滑车滑轮故障:滑车滑轮可能由于磨损或故障导致起重机无法正常工作。
检查滑车滑轮并更换为新的滑轮。
-行走机构故障:检查行走机构的轮胎、链条、传动齿轮等是否有损坏或磨损现象,及时进行修复或更换。
-行车轨道故障:检查行车轨道是否有损坏或松动的情况,如有需要,修复或更换轨道。
3.液压故障:-液压油温过高:可能是液压系统中油量不足或油质质量差,检查液压系统的油量和油质,及时添加或更换液压油。
-液压系统泄漏:泄漏可能由于密封件老化或损坏导致,检查液压系统的密封件,并进行更换。
-液压缸无法正常收放:检查液压缸和液压泵的工作状态,如有需要,修复或更换液压缸或液压泵。
以上只是天车常见的几种故障及排除方法,实际上,天车的故障种类繁多,解决方法也需要根据具体情况进行选择。
为了防止故障的发生,我们还需要定期对天车进行检查和维护,如保持润滑、检查电气线路、清除灰尘等。
此外,操作人员应该经过专业培训,熟悉天车的使用方法和注意事项,提高操作技能,确保工作安全。
天车轨道常见故障
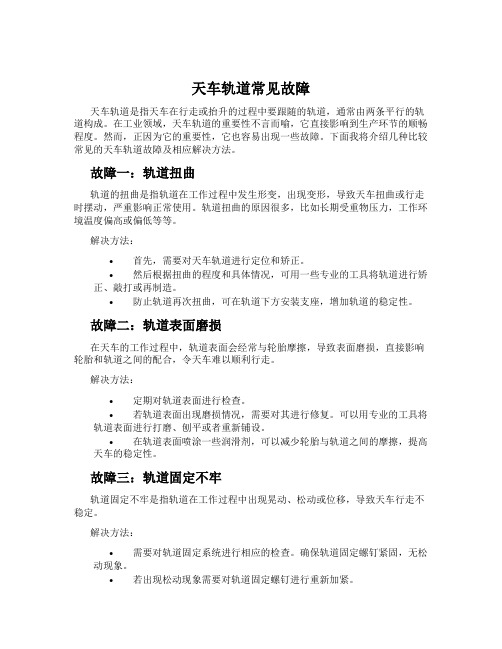
天车轨道常见故障天车轨道是指天车在行走或抬升的过程中要跟随的轨道,通常由两条平行的轨道构成。
在工业领域,天车轨道的重要性不言而喻,它直接影响到生产环节的顺畅程度。
然而,正因为它的重要性,它也容易出现一些故障。
下面我将介绍几种比较常见的天车轨道故障及相应解决方法。
故障一:轨道扭曲轨道的扭曲是指轨道在工作过程中发生形变,出现变形,导致天车扭曲或行走时摆动,严重影响正常使用。
轨道扭曲的原因很多,比如长期受重物压力,工作环境温度偏高或偏低等等。
解决方法:•首先,需要对天车轨道进行定位和矫正。
•然后根据扭曲的程度和具体情况,可用一些专业的工具将轨道进行矫正、敲打或再制造。
•防止轨道再次扭曲,可在轨道下方安装支座,增加轨道的稳定性。
故障二:轨道表面磨损在天车的工作过程中,轨道表面会经常与轮胎摩擦,导致表面磨损,直接影响轮胎和轨道之间的配合,令天车难以顺利行走。
解决方法:•定期对轨道表面进行检查。
•若轨道表面出现磨损情况,需要对其进行修复。
可以用专业的工具将轨道表面进行打磨、刨平或者重新铺设。
•在轨道表面喷涂一些润滑剂,可以减少轮胎与轨道之间的摩擦,提高天车的稳定性。
故障三:轨道固定不牢轨道固定不牢是指轨道在工作过程中出现晃动、松动或位移,导致天车行走不稳定。
解决方法:•需要对轨道固定系统进行相应的检查。
确保轨道固定螺钉紧固,无松动现象。
•若出现松动现象需要对轨道固定螺钉进行重新加紧。
•对于因为强烈振动造成的轨道松动或位移现象,需要对其跨度和支座进行重新调整。
故障四:轮胎与轨道之间卡滞若轨道表面存在沙粒、油污或其他杂质,或者轮胎在行走过程中出现卡滞状况,也会导致天车行走不顺畅,进而影响到生产效率。
解决方法:•对轨道表面进行清洁,去除表面污垢及其他杂质。
•定期对轮胎进行清洁与保养,确保其摩擦表面处于一种良好的状态。
•若出现轮胎卡滞现象,可根据具体情况进行轮胎更换或者是修复,以恢复天车正常运行。
结论天车轨道的稳定性对工业生产的影响非常大,其正常运行和维护都需要引起充分重视。
天车常见故障及排除方法

滑轮
1.滑轮绳槽磨损不匀
2.滑轮心轴磨损量达工程直径的
3%~5%
3.滑轮转不动
4.滑轮倾斜、松动
5.滑轮裂纹或轮缘断裂
1.材质不均匀、安装不合要求,绳和轮接触不良
2.心轴损坏
3.心轴和钢丝绳磨损加剧
4.轴上定位件松动,或钢丝绳
跳槽
5.滑轮损坏
1.轮槽壁磨损量达原厚的
2)触头污脏
1)调整压力
2)排除或更换
4.主接触器不能接通
1)闸刀开关没合上,紧急开关没合上
2)仓口开关没合上
3)控制器手柄没放回零位
4)控制电路熔断器烧断
5)线路无电
1) 2)闭合开关
3)手柄回零
4)检查或者更换熔断器
5)检查线路有无电压
5.起重机运行中经常
掉闸
1)触头压力不足
2)触头烧损
3)触头污脏
齿面有缺陷、轮齿不是沿全齿面接触,而是在一角上接触
更换齿轮
4.壳体,特别是安装轴承
处发热
1)轴承破碎
2)轴颈卡住
3)轮齿磨损
4)缺少润滑油
1)、2)更换齿轮
3)修整齿轮
4)更换润滑油
5.剖分面漏油
1)密封失效
2)箱体变形
3)剖分面不平
4) ;连接螺栓松动
1)更换密封件
2)检修箱体剖分面,变形严重则换
叠片式吊钩(板钩)
1.吊钩变形
2.表面有疲劳裂纹
3.销轴磨损量超过工程直径的
3%~5%
4.耳环有裂纹或毛刺
5.耳环衬套磨损量达原厚的50%
1.长期过载,容易折钩
2.超期、超载、吊钩损坏
天车的现场处置方案
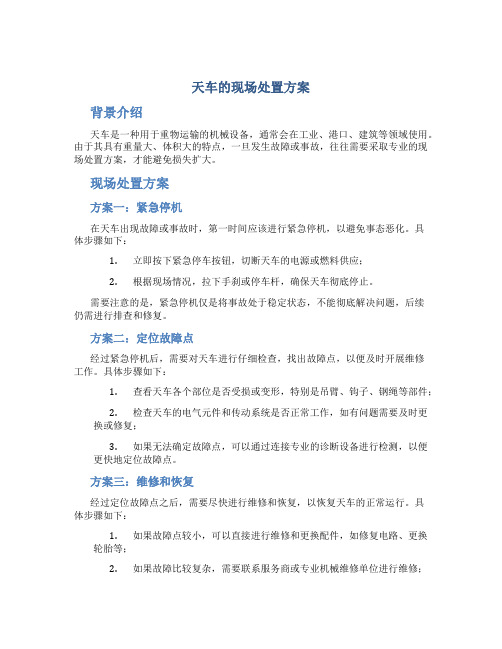
天车的现场处置方案背景介绍天车是一种用于重物运输的机械设备,通常会在工业、港口、建筑等领域使用。
由于其具有重量大、体积大的特点,一旦发生故障或事故,往往需要采取专业的现场处置方案,才能避免损失扩大。
现场处置方案方案一:紧急停机在天车出现故障或事故时,第一时间应该进行紧急停机,以避免事态恶化。
具体步骤如下:1.立即按下紧急停车按钮,切断天车的电源或燃料供应;2.根据现场情况,拉下手刹或停车杆,确保天车彻底停止。
需要注意的是,紧急停机仅是将事故处于稳定状态,不能彻底解决问题,后续仍需进行排查和修复。
方案二:定位故障点经过紧急停机后,需要对天车进行仔细检查,找出故障点,以便及时开展维修工作。
具体步骤如下:1.查看天车各个部位是否受损或变形,特别是吊臂、钩子、钢绳等部件;2.检查天车的电气元件和传动系统是否正常工作,如有问题需要及时更换或修复;3.如果无法确定故障点,可以通过连接专业的诊断设备进行检测,以便更快地定位故障点。
方案三:维修和恢复经过定位故障点之后,需要尽快进行维修和恢复,以恢复天车的正常运行。
具体步骤如下:1.如果故障点较小,可以直接进行维修和更换配件,如修复电路、更换轮胎等;2.如果故障比较复杂,需要联系服务商或专业机械维修单位进行维修;3.在维修过程中,需要注意事项有:使用正确的工具和设备,严格遵守安全操作规程,确保维修人员的人身安全。
结论天车在工业、港口、建筑等领域应用广泛,但其出现故障或事故时,会对生产和生命财产造成巨大的损失。
因此,我们需要在日常维护和使用中,严格遵守相关规程和操作要求,以最大程度地减少故障和事故的发生。
一旦出现故障或事故,也需要及时采取专业的处置方案,以避免损失扩大。
天车常见故障处理方法大全
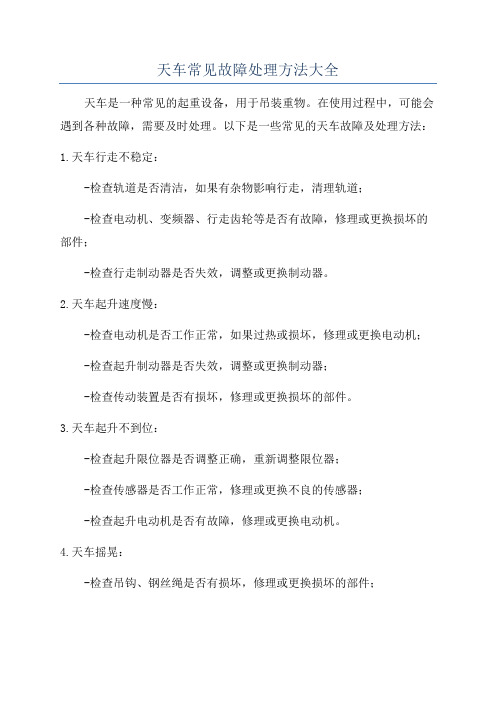
天车常见故障处理方法大全天车是一种常见的起重设备,用于吊装重物。
在使用过程中,可能会遇到各种故障,需要及时处理。
以下是一些常见的天车故障及处理方法:1.天车行走不稳定:-检查轨道是否清洁,如果有杂物影响行走,清理轨道;-检查电动机、变频器、行走齿轮等是否有故障,修理或更换损坏的部件;-检查行走制动器是否失效,调整或更换制动器。
2.天车起升速度慢:-检查电动机是否工作正常,如果过热或损坏,修理或更换电动机;-检查起升制动器是否失效,调整或更换制动器;-检查传动装置是否有损坏,修理或更换损坏的部件。
3.天车起升不到位:-检查起升限位器是否调整正确,重新调整限位器;-检查传感器是否工作正常,修理或更换不良的传感器;-检查起升电动机是否有故障,修理或更换电动机。
4.天车摇晃:-检查吊钩、钢丝绳是否有损坏,修理或更换损坏的部件;-检查大车和小车上的摇动缓冲器是否工作正常,修理或更换不良的缓冲器;-检查电动机、变频器是否有故障,修理或更换损坏的部件。
5.天车制动失效:-检查刹车片是否磨损,修理或更换损坏的刹车片;-检查制动器油缸是否泄漏,修理或更换泄漏的油缸;-检查制动器是否调整正确,重新调整制动器。
6.天车电源故障:-检查电源线路是否有故障,修理或更换受损的电线;-检查电源接触器和断路器是否工作正常,修理或更换不良的部件;7.天车电气元件故障:-检查继电器和开关是否工作正常,修理或更换不良的部件;-检查电线连接是否松动,重新固定电线连接;-检查电气元件是否有烧损,修理或更换受损的元件。
8.天车遥控器失效:-检查遥控器电池是否电量不足,更换电池;-检查遥控器是否进水或摔坏,修理或更换损坏的部件;-检查遥控器与接收器之间的信号是否受干扰,调整信号接收器的位置。
此外,为了预防天车故障的发生,还应定期对天车进行检查和维护,包括:-检查润滑油是否充足,及时添加或更换润滑油;-检查紧固螺栓是否松动,紧固螺栓;-检查电气元件是否有积水和灰尘,清理电气元件;-检查导向轮是否磨损,修理或更换损坏的导向轮。
各种天车的故障及排除方法

各种天车的故障及排除方法第七章各种故障产生的原因及排除方法天车的启动、制动、转向等动作极为频繁,在工作过中经常受到冲击和振动,因此,天车经常会出现各种机械、电气等方面的故障。
作为天车司机,不仅要熟练地掌握天车的操作技术,还要了解各种故障产生的原因及排除方法。
§7—1 常见的机械故障产生的原因及排除方法一、主梁下挠天车的主梁结构必须具有足够的强度、刚度及稳定性,这是保证各运行机构正常工作的首要条件。
因此,一般在天车主梁的设计、制造中规定要有一定的上拱度。
其目的是减少天车在额定的负载作用下所产生的下挠度,使小车轨道有最小的倾斜度,从而减少小车在运行时的附加阻力和自动滑移。
所谓上拱度,就是主梁向上拱起的程度,,一般上拱度为跨度的1/1000。
而天车在使用一段时问后,主梁上的上拱度逐渐减小。
随着使用时间的不断延长,主梁就由上拱度逐渐过渡到下挠。
所谓下挠,就是主梁的向下弯曲程度。
主梁产生下挠有两种情况:一种是弹性变形,一种是永久变形。
前者要及时进行修复,后者就不仅是下挠修复问题了,而是要立即进行加固修复。
究竟下挠到什么程度才需要修复,其允许值参考表7一l和表7—2。
表7—1 新双梁天车的允许挠度mm┏━━━━━━━┳━━━━━━━━━━━━━━━┓┃国家名称┃新双梁天车的允许挠度(F) ┃┣━━━━━━━╋━━━━━━━━━━━━━━━┫┃中国┃≤LK/700 ┃┣━━━━━━━╋━━━━━━━━━━━━━━━┫┃前苏联┃≤Lk{700 ┃┣━━━━━━━╋━━━━━━━━━━━━━━━┫┃日本┃≤LK/800 ┃┣━━━━━━━╋━━━━━━━━━━━━━━━┫┃英国┃≤LK/900 ┃┣━━━━━━━╋━━━━━━━━━━━━━━━┫┃美国┃O·0125~O.015IN/FT跨度┃┗━━━━━━━┻━━━━━━━━━━━━━━━┛我国还规定:单梁天车主梁的允许挠度F≤LK/500MM:手动单梁天车主梁的允许挠度F≤LK/400rnm。
天车常见机械故障处理措施

技术与检测Һ㊀天车常见机械故障处理措施张君雄摘㊀要:天车是厂矿起重㊁运输和各种作业中最重要㊁最常用的设备ꎮ文章结合天车运行中的几个常见故障ꎬ对故障的主要原因进行了分析和探讨ꎮ并提出了预防天车常见故障的处理方法ꎮ关键词:天车ꎻ机械ꎻ故障ꎻ措施一㊁常见问题(一)肯轨车轮肯轨是指轮缘与轨道发展严重抵触ꎬ在行驶过程中可以产生影响噪声或感觉ꎮ如果手推车的轮子保持在一个重要方向ꎬ应该进行重新开始调整轮子或两个自动轮或夹紧轮的水平偏转ꎮ如果发生偏转方向就是没有能力达到完全相反的方向ꎬ很可能是通过两个电机和制动器不同步ꎮ如果城市轨道保持在一定行程ꎬ轨道安装方式可能我们会有一些误差ꎻ如果中国轨道停留在行程中ꎬ则轨道跨度有问题ꎮ(二)主动车轮打滑主动车轮滑动检查车轮的滚动表面ꎬ以查看它们是否在同一平面上ꎮ如果它们不在同一平面上ꎬ应填充和调整角度轴承盒ꎮ如果赛道上有油ꎬ可以在赛道上撒下细砂等东西ꎬ增加摩擦系数ꎬ然后调整制动时刻ꎬ避免过度制动ꎮ(三)安全开关失灵它主要是由开关内部卡住或移位形成的物体ꎮ调校及使用时ꎬ请注意以下事项:吊装限位安全开关应确保吊钩升起时停电时吊车最高点与相关物体之间的距离不小于200毫米ꎮ更换或磨损钢丝绳后ꎬ重新调整安全开关ꎮ试试在每班开始时使用一次ꎬ检查开关的可靠性ꎮ二㊁减速器齿轮对于天车车辆运行的过程当中ꎬ减速器齿轮是非常重要的部件之一ꎬ它通过常规的动力传输ꎬ将运行机器达到速度的标准ꎬ在动力的传输过程当中ꎬ齿轮会出现磨损和断裂的可能ꎬ侧翼胶水和齿面磨损ꎮ齿轮故障原因是:短期过载或冲击载荷ꎬ反复变化形成疲劳断裂ꎻ牙齿的外观不润滑ꎬ有凸起形成应力集中ꎬ或平滑剂不干净ꎻ高温引起的平滑问题ꎻ磨损是由进入耐磨外部的硬颗粒引起的ꎮ三㊁卷筒及钢丝绳压板在天车运行过程当中ꎬ卷筒是重要的受力部分ꎬ它所常见的是薄壁㊁孔洞㊁裂纹等现象ꎮ这些问题毛病的缘由是滚筒和钢丝绳之间的接触社会互相学习挤压和摩擦ꎮ当滚筒变薄到一定水平时ꎬ由于企业无法理解接受钢丝绳施加的压力ꎬ就会发展产生影响裂纹ꎮ为了可以防止滚筒的机械毛病ꎬ依据不同国家法律规范ꎬ当磨损到达20%或呈现裂纹时ꎬ应及时改换滚筒壁ꎮ应留意学生操作技术环境的卫生服务以及工作线圈和钢丝绳的光滑ꎮ四㊁制动器制动器是起重机的重要安全部件ꎬ具有防止悬架坠落和停车的功能ꎮ定期检查和维护制动器ꎮ第一先检查铰链是否磨损ꎬ关键的固定装置是否安装到位ꎻ运行的装置是否正常ꎻ液压系统能否正常运作ꎻ制动轮与制动带两者的串联是否流畅和平滑ꎬ无磨损现象ꎮ基于以上检查的情况ꎬ再进一步的确定是否运行ꎬ确保刹车的灵敏性ꎬ不能带着机械方面的问题进行运行ꎬ定期一起保持刹车打开ꎮ是否能够支撑设备的正常运行ꎬ一定要经常调整制动体的工作要求ꎮ五㊁车轮与轨道天车运行过程中车轮和履带常见的障碍物有车轮咬死㊁小车高度不均匀和打滑ꎮ吃刀的原因有很多ꎬ吃刀的方式也有很多ꎮ轻啃路面影响天车寿命ꎬ重啃路面造成严重伤亡ꎮ所以特种设备管理人员要注意吃路的满意度ꎮ啃道的问题出现的根源是安装过程中误差和不均匀之间的联系不恰当所产生的ꎬ以及大车传动系统中零件磨损较严重和齿轮之间的咬合不稳定所造成的传动动力不足ꎮ台车车轮出现问题的原因有下面几个方面:主要原因是安装过程中导致误差范围错位而导致ꎬ台车在设计中如果重量不符合规定ꎬ使用需要综合分析台车高度参差不齐的问题ꎬ合理规定台车高度的问题ꎮ六㊁处理措施(一)制动无效ꎬ制动力矩小ꎬ升降机构打滑ꎻ在作业组织中ꎬ车辆发生打滑ꎮ原因分析和处理方法将在后面介绍: (1)制动轮表面有运行产生的污垢ꎬ积累后导致运行时的摩擦系数减小ꎬ最终使得制动轮抱死的情况出现ꎮ这种情况可以通过使用汽油来清洗处理ꎮ(2)制动片磨损较为严重ꎬ导致铆钉在外暴露ꎬ铆钉如果在外和制动轮进行摩擦ꎬ这样就造成了制动力矩的减小ꎬ并且也造成了齿轮外表的变化ꎮ这种情况的出现就需要更换制动片ꎮ(3)主动弹簧的安装不正确ꎬ会使得弹簧的拉力无法发挥原先的性质ꎮ这种情况的出现就需要首先从制动器开始调节ꎬ使得弹簧拉力增大ꎮ(二)刹车出现问题不能正常打开ꎬ或者是制动器无法正常运行ꎬ解决的方法如下:(1)主弹簧的拉力过大ꎬ会导致电磁铁的拉力小于其主弹簧的拉力ꎬ导致闸门不能正常打开ꎮ解决方法为合理调节制动器ꎬ以至于主弹簧的拉力减小ꎮ(2)刹车杆传动系统卡死ꎬ传动时刹车释放力受阻ꎬ无法接通刹车ꎮ检查传动系统并清除堵塞ꎮ(3)制动器的制动螺钉弯曲ꎬ导致螺钉不能接触到磁铁的中心部位ꎬ因而不能顺利的开启闸门ꎬ使得制动器脱离ꎬ解决的方法就是拆下来螺钉或者更新ꎮ(三)制动时ꎬ制动衬片受热ꎬ 熏 烧ꎬ使衬片磨损很快ꎮ(1)制动蹄衬片与制动轮两者中的距离控制的不合理ꎬ导致间隔过于狭小ꎬ最后导致接触面摩擦ꎮ从运行的初期阶段就调节制动轮和制动蹄的距离ꎬ以便在操作过程中衬片和制动轮均匀地完全分离ꎮ(2)短距离的制动器弹簧不起作用ꎬ使得闸瓦不能顺利开启ꎬ从而使得其一直附着在制动轮上面ꎮ更换辅助拉簧ꎬ并从头调整制动器ꎮ(3)闸瓦和制动轮由于运行的轴心不对应ꎬ导致运行过程中两者无法分离开来ꎬ产生摩擦生热ꎮ从头开始安装制动器ꎬ以满足同心度要求ꎮ七㊁结语综上所述ꎬ文章主要分析了天车在常见的机械工程中出现的故障以及处理的措施研究ꎬ总结了部分出现问题的根源以及提出了相应的解决措施ꎬ在机械工程工作当中ꎬ需要相关工作人员对机械的专业性再加强技术培养ꎬ避免机械故障的出现ꎬ保证天车的正常运行ꎬ提高工程效率ꎮ参考文献:[1]褚新荣.浅谈冶金行业中桥式起重机的常见问题及解决方案[J].中国军转民ꎬ2010(2).作者简介:张君雄ꎬ河钢唐钢物流分公司ꎮ391。
天车维修常见故障排除方法
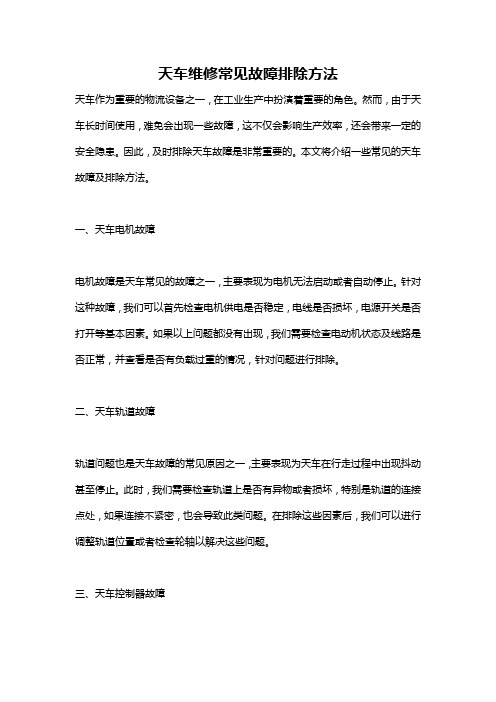
天车维修常见故障排除方法天车作为重要的物流设备之一,在工业生产中扮演着重要的角色。
然而,由于天车长时间使用,难免会出现一些故障,这不仅会影响生产效率,还会带来一定的安全隐患。
因此,及时排除天车故障是非常重要的。
本文将介绍一些常见的天车故障及排除方法。
一、天车电机故障电机故障是天车常见的故障之一,主要表现为电机无法启动或者自动停止。
针对这种故障,我们可以首先检查电机供电是否稳定,电线是否损坏,电源开关是否打开等基本因素。
如果以上问题都没有出现,我们需要检查电动机状态及线路是否正常,并查看是否有负载过重的情况,针对问题进行排除。
二、天车轨道故障轨道问题也是天车故障的常见原因之一,主要表现为天车在行走过程中出现抖动甚至停止。
此时,我们需要检查轨道上是否有异物或者损坏,特别是轨道的连接点处,如果连接不紧密,也会导致此类问题。
在排除这些因素后,我们可以进行调整轨道位置或者检查轮轴以解决这些问题。
三、天车控制器故障控制器故障也是天车常见的故障之一,表现为天车无法移动或者操纵性变差。
针对这种问题,我们可以先查看控制器面板上是否有报警信息。
如果有,我们需要根据报警信息排除故障。
如果没有报警信息,我们可以检查控制器的电源线、信号线、控制器板上的端子等,是否松动或损坏。
如果这些都没有问题,我们则需要检查控制器本身是否被烧坏了,需要及时进行更换维修。
四、天车行走轮故障行走轮故障也是一个十分常见的问题,主要表现为天车行走时发出异响或者摩擦不畅。
此时,我们首先需要检查行走轮上是否有异物或者松动等物质影响,如果轮子损坏,则需要及时更换。
此外,我们还需检查马达和减速器是否工作正常,如果有问题需要及时更换维修。
五、天车行走距离不匀有时候我们会发现天车在行走的过程中,行走距离出现不匀的情况。
此时,我们需要检查天车行走轨道是否平衡,轨道宽度是否相对一致,行走轮上的摩擦是否均匀等问题。
如果以上问题都没有出现,则需要检查控制器是否设置正确,在设定参数合理的情况下,通过调整轮轴、减速器等零部件以解决行走距离不匀的问题。
天车常见电气故障及排除方法

天车常见电气故障及排除方法
天车常见电气故障及排除方法:
1. 天车不启动或启动困难:检查电源是否正常,检查控制柜电
源模块是否工作正常,检查电器设备接线是否松动或接触不良。
2. 天车起重机制不能正常工作:检查起重机制断路器、熔断器
是否正常,检查电机电缆是否接触不良或损坏,检查起重机制限位器
是否调整正确。
3. 天车行走速度不稳定或不能正常行走:检查驱动传动链条是
否有松动或损坏,检查轮轴承是否良好,检查行走电机是否正常工作。
4. 天车变频器故障:检查变频器安装是否牢固、电缆接触是否
良好,检查是否存在过压或过流现象。
5. 天车控制系统故障:检查控制柜是否工作正常,检查控制器
接线是否松动或接触不良,检查传感器是否有效。
6. 天车紧急停车系统故障:检查紧急停车开关是否正常工作,
检查机械制动器是否损坏,检查紧急停车电路是否完好。
以上是天车常见电气故障及排除方法,操作时需谨慎,确保操作
人员安全。
若以上方法均不能排除故障,需及时联系相关专业人员。
天车常见机械故障处理措施

天车常见机械故障处理措施天车常见机械故障处理措施【摘要】天车是厂矿企业中最主要、最常用的起重、运输及其多种操作的重要设备。
本文结合天车运行中几种常见的故障情况,分析探讨故障的主要原因,并提出预防天车常见故障的处理措施。
【关键词】天车机械故障处理天车是桥架在高架轨道上运行的一种桥架型天车,被广泛地应用在室内外仓库、厂房、码头和露天贮料场等处。
天车的机械系统一般由桥架、装有升降机构和运行机构的小车、大车运行机构等组成。
这些机构主要有大梁、断梁、轨道、车轮、减速机、卷筒、滑轮、联轴器等部件组成。
天车在企业生产过程中带来高效、经济的同时,也经常发生故障和事故给企业和职工造成重大经济损失和人身伤害。
在发生故障时往往会引发一些重大事故的发生,会造成设备毁坏、人身伤亡等重大事故发生。
下面就几种常见的故障进行分析,并提出处理措施。
一、减速器齿轮减速器是桥式天车的重要传动部件,通过齿轮啮合对扭矩进行传递,把电动机的高速运转调到需要的转速,在传递扭矩过程中齿轮会出现轮齿折断、齿面点蚀、齿面胶和、齿面磨损等机械故障,造成齿轮的故障原因有:短时间过载或受到冲击载荷,多次重复弯曲引起的疲劳折断;齿面不光滑,有凸起点产生应力集中,或润滑剂不清洁;由于温度过高引起润滑失效;由于硬的颗粒进入摩擦面引起磨损。
预防措施有:天车不能起载使用,启动、制动要缓慢、平稳,非特定情况下禁止突然打反车;更换润滑剂要及时,并把壳体清洁干净,同时要选择适当型号的润滑剂;要经常检查润滑油是否清洁;发现润滑不清洁要及时更换。
二、卷筒及钢丝绳压板卷筒是天车重要的受力部件,在使用过程中会出现筒壁减薄、孔洞及断裂故障。
造成这些故障的原因是卷筒和钢丝绳接触相互挤压和摩擦。
当卷筒减薄到一定的程度时,因承受不住钢丝绳施加的压力而断裂。
为防止卷筒这种机械事故的发生,按照国家标准,卷筒的筒壁磨损达到原来的20%或出现裂纹时应及时进行更换。
同时要注意操作环境卫生和对卷筒、钢丝绳的润滑。
天车常见电气故障及排除方法
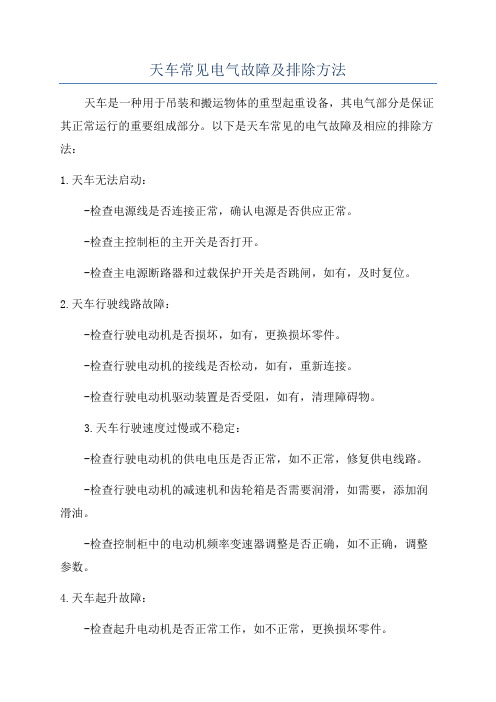
天车常见电气故障及排除方法天车是一种用于吊装和搬运物体的重型起重设备,其电气部分是保证其正常运行的重要组成部分。
以下是天车常见的电气故障及相应的排除方法:1.天车无法启动:-检查电源线是否连接正常,确认电源是否供应正常。
-检查主控制柜的主开关是否打开。
-检查主电源断路器和过载保护开关是否跳闸,如有,及时复位。
2.天车行驶线路故障:-检查行驶电动机是否损坏,如有,更换损坏零件。
-检查行驶电动机的接线是否松动,如有,重新连接。
-检查行驶电动机驱动装置是否受阻,如有,清理障碍物。
3.天车行驶速度过慢或不稳定:-检查行驶电动机的供电电压是否正常,如不正常,修复供电线路。
-检查行驶电动机的减速机和齿轮箱是否需要润滑,如需要,添加润滑油。
-检查控制柜中的电动机频率变速器调整是否正确,如不正确,调整参数。
4.天车起升故障:-检查起升电动机是否正常工作,如不正常,更换损坏零件。
-检查起升电动机的供电电压是否正常,如不正常,修复供电线路。
-检查起升电动机的制动器是否正常放松,如不正常,修复或更换制动器。
5.天车遥控器无法正常操作:-检查遥控器电池是否耗尽,如耗尽,更换电池。
-检查遥控器与接收器之间的信号连接是否正常,如不正常,重新连接或更换零件。
-检查遥控器上的按钮是否坏了,如坏了,更换遥控器或修复按钮。
6.天车电缆故障:-检查天车电缆是否出现断线、破损或接线松动,如有,及时修复或更换。
-检查天车电缆的绝缘是否损坏,如损坏,更换绝缘材料。
7.天车限位开关故障:-检查限位开关是否被堵塞或损坏,如被堵塞,清理障碍物;如损坏,更换限位开关。
-检查限位开关的接线是否正确,如不正确,重新连接或更换零件。
以上是天车常见的电气故障及相应的排除方法,对于天车的维护保养和日常操作中遇到的电气故障,及时采取相应的排除方法可以确保天车的正常运行和延长设备寿命。
- 1、下载文档前请自行甄别文档内容的完整性,平台不提供额外的编辑、内容补充、找答案等附加服务。
- 2、"仅部分预览"的文档,不可在线预览部分如存在完整性等问题,可反馈申请退款(可完整预览的文档不适用该条件!)。
- 3、如文档侵犯您的权益,请联系客服反馈,我们会尽快为您处理(人工客服工作时间:9:00-18:30)。
盛年不重来,一日难再晨。
及时宜自勉,岁月不待人。
天车工简单故障的处理
一、钢丝绳的检查与维护
1、随着钢绳的使用日久,钢绳中的一部分钢丝将受到磨损或折断。
钢丝绳能否继
续安全使用,是由钢绳每一节距内钢丝的断裂数目来决定的。
钢丝绳的一个节距,指每股钢丝绳缠绕一周的轴向距离,对于符合GB1102-74《园股钢丝绳》标准的钢丝绳,在断丝与磨损的指标上可按照下述要求检查报废。
a 钢丝绳报废断丝数表
b钢丝绳有锈蚀或磨损时,应将上表定的报废断丝数按下表折减,并按折减后的断丝数报废
折减系数表
2、钢丝绳的维护:定期检查测量;按周期润滑。
二、吊钩的检查与维护
1、表面出现任何裂纹,破口或发裂(严禁焊补使用);
2、危险断面磨损达原尺寸的10%;
3、开口度比原尺寸增加15%;
4、扭转变形超过10°;
5、危险断面或吊钩颈部产生塑性变形;
6、螺母,吊钩横梁出现任何裂纹和变形;
7、吊钩的维护:定期检查测量;吊钩不允许维修,发生上述任何一种问题只能报废。
三、制动装置的检查与维护
1 制动轮出现下列情况之一时应报废:
(1)裂纹
(2)起升机构的制动轮,轮缘厚度磨损达原厚度的40%;
(3)运行机构的制动轮,轮缘厚度磨损达原厚度的50%;
(4)轮面凹凸不平度达1.5mm时,如能修理,修复后轮缘厚度应符合上述两条的要求。
2 液压推杆制动器
液压推杆制动器是由驱动电机及器身(离心泵)两部分组成。
器身部分
由缸盖、缸体、活塞、推杆、叶轮及转轴组成,在器身外壳底部有两搭
子供安装在制动器上用,上端有与两推杆相连接的梁及连杆,供安装在
制动器上时做杠杆用。
当电动机通电时,带动叶轮旋转,在活塞内产生
压力,在压力影响下将油液从活塞的上部流到活塞的低部,活塞上下的
油液产生一个压差,此压差迫使活塞及固定在它上面的推杆及梁一同上
升压缩圆柱弹簧,这样就完全打开了制动器。
当电动机断电后,叶轮停止旋转,活塞在受压力及本身重量作用下,向
下降落,制动器便起刹车作用。
3 液压推杆制动器的安装及调试:
制动器是在起升机构卷筒等零部件安装后,再装上去的,安装时,应使
制动带在制动器松开状态下平行于制动轮,当制动器在制动状态下应使
制动带整个表面贴在制动轮上,制动带与制动轮的贴合面积应不小于总
面积的70%,制动轮的工作表面勿粘油腻,调试合格后,把制动器底座
与车架焊牢。
制动带未磨损前,制动带与制动轮间的允许打开间隙见下表:
在试车前,必须给液压推动器注入清洁和不得有任何污浊物及机械杂质
的液压油,根据使用环境温度推荐用油如下表:
油液应加足,到观察孔中流出油液时为止。
4 液压推杆制动器的调整
a 制动器工作行程调整:在保证闸瓦最小退距的情况下,推动器的工作行程越小愈理想,因此需要调节其安装高度H1,使H1尺寸符合下表要求:
b 根据使用情况,适当改变主弹簧的安装长度,以获得各种适应的制动力矩,
检查制动力矩,起升机构的制动器,必须可靠的支持额定起重量的1.25倍。
c 制动器装有自动调整间隙装置,随着制动带的磨损,制动瓦退矩始终保持一定数值,勿需另外调整。
d 固定制动瓦螺母时,不宜过紧,也不宜过松,以不使制动瓦自由转动为宜。
5 使用液压推杆制动器的注意事项
起升机构的制动器由行车操作人员每班检查一次,运行机构的制动器不少于2-3天检查一次。
点检维护人员点检时应着重检查以下各项:
(a)铰链关节处是否有卡住现象。
(b)制动器的构件运行是否正常,调整螺母是否坚固,自动调整退矩的滚子是否被油腻阻塞。
(c)电力液压推动器的工作是否正常,液压油是否足量。
有无漏油和渗油现象,引入电线的绝缘是否良好。
(d)推动器的工作行程H1 不得小于表列之H1 的最小尺寸,如超出要求,需立即进行调整,否则失去作用。
(e)制动瓦是否正确地靠在制动轮上,摩擦表面的状态是否完好,有无油腻脏物痕迹,当制动带的厚度磨损达到原厚度50%时,则应更换制动带。
四、大小车车轮的检查与维护
答:1 出现下列情况之一时,应报废:
(1)轮缘崩裂;
(2)轮缘厚度磨损达原厚度的30%;
(3)轮缘厚度弯曲变形达原厚度的20%;
(4)轮缘两个主动车轮的工作直径在不均匀磨损后所造成的相互偏差不得超过其公称直径的1/600,如果超过此值,应重新车光,但如果重车后车
轮直径较原公称直径小10mm时,车轮应更换;
(5)当运行速度低于50m/min时,椭圆度达1mm,当运行速度高于50m/min 时,椭圆度达0.5mm;
2、车轮的维护:每班目视检查;
五、经常发生的故障的原因及排除方法。