钢铁行业节能降耗改造技术方案7页
钢铁行业节能降耗改造技术方案

钢铁行业节能降耗改造技术方案一、序言钢铁行业是工业领域的耗能大户,也是我国节能减排潜力最大的行业之一。
“十一五”期间,钢铁行业一方面频频被“点名”,成为全社会节能减排的重点和难点领域;另一方面,钢铁行业节能减排取得的成效,也为全社会推进节能减排做出了巨大贡献。
去年9 月国家已经出台《钢铁行业生产经营规范条件》,对钢铁企业的环境保护、能源消耗和资源回收利用、工艺装备等方面做出了具体的要求。
《条件》明确提出,对于不具备规范条件的企业需按照规范条件要求进行整改,整改后仍达不到要求的企业应逐步退出钢铁生产。
对不符合规范条件的企业,有关部门不予核准或备案新的项目、不予配置新的矿山资源和土地、不予新发放产品生产许可证、不予提供信贷支持。
与“十一五”相比,“十二五”期间,国家的环保法律法规将更加严格,节能减排任务更艰巨,钢铁行业的压力也更大。
在“十二五”规划纲要提出的钢铁行业发展重点方向中,与节能减排相关的内容占据了大多数:支持非高炉炼铁、洁净钢生产、资源综合利用等技术开发;重点推广能源管控系统技术和高温高压干熄焦、余热综合利用、烧结烟气脱硫等节能减排技术。
二、高炉冲渣水余热利用目前,钢铁产业余热余能的回收利用率相当低,其中,高温余热比较容易回收,目前在节能降耗的技术改造中已大部分得到回收;但低温余热的回收却几乎为零,如高炉冲渣水的余热,大多被浪费掉。
应该指出,低温余热约占总余热的35%,因此,钢铁产业的低温余热存在着巨大的回收潜力。
钢铁厂在高炉炼铁工艺中,产生的炉渣温度大约为1000C。
目前,大多数炼铁企业的处理方法是:将此炉渣在冲渣箱内由冲渣泵提供的高速水流急冷冲成水渣并粒化,以供生产水泥之用。
一般每吨铁排出约0.3t 渣,每吨渣可产生80〜95C, 5〜10t的冲渣水。
为了保证冲渣水的循环利用效果,需要将这部分冲渣水在沉淀过滤后引入空冷塔,降温到50C以下再次循环冲渣。
这样就使得很大一部分热量在空冷塔中流失,既造成了能源的浪费,又对环境造成了热污染。
炼铁厂节能减排技术改造工程技术方案
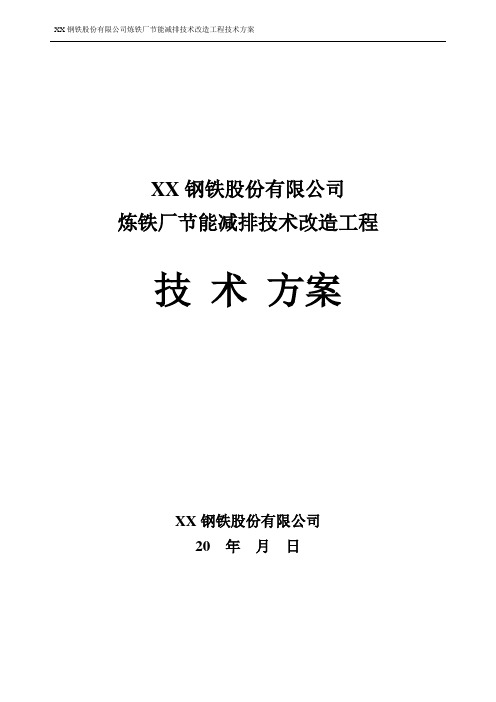
XX钢铁股份有限公司炼铁厂节能减排技术改造工程技术方案XX钢铁股份有限公司20 年月日1.项目名称XX钢铁股份有限公司炼铁厂节能减排技术改造工程2.项目规模本工程设计规模为1座1050m3 高炉及相应配套的公用和辅助设施。
年产生铁100万吨。
3.项目范围(1)炼铁工艺贮矿(焦)槽系统、皮带上料系统、炉顶系统、高炉本体、风口平台,出铁场、炉渣处理系统、热风炉系统、粗煤气系统、煤粉制备、喷吹系统。
(2)储运设施焦碳、烧结矿、球团矿、块矿及杂矿从矿焦槽前最近转运站(注:不含该转运站)运受料,然后运至高炉贮矿槽内;喷煤用原煤运输,并设置自动清除式除铁器。
(3)热力设施高炉鼓风机站、煤粉制备及本高炉区域内有关压缩空气、蒸汽等热力管网。
(4)燃气设施煤气净化、TRT余压发电以及高炉煤气、焦炉煤气、氧气、氮气等高炉区域内的燃气管线。
(5)给排水设施高炉中心循环水泵站、水冲渣浊环水系统及高炉区域内生产、消防给排水系统,生活给水及生活污水排水系统,雨水排水系统。
注:以上各种介质交接点在红线范围外1 m。
(6)采暖、通风、除尘设施设置完善的采暖、通风、空调、除尘设施。
(7)供配电高炉及其配套设施的供配电.(8)三电自动化控制系统配套的三电一体化自动化控制系统(电气传动、仪表、计算机、工业电视监控等)。
(9)电讯(10)总图运输铁路、道路、平土排水及综合管线。
4.高炉主要技术经济指标高炉主要经济技术指标序号指标名称单位数值备注1 公称容积m310502 利用系数t / m3d 2.61 365天年平均3 综合燃料比kg / t 530焦比kg/t 380煤比kg/t 1504 热风温度o C 12005 熟料率% 90其中:烧结矿% 70球团矿% 20块矿% 106 入炉矿石综合品位% 577 炉顶压力MPa 0.16~0.208 富氧率% 0-39 渣铁比kg / t 35010 年工作日 d 353 2.70 t / m3d 5.主要设计原则1)先进、实用、可靠、经济、环保;2)优化设计、技术装备达到同级高炉先进水平;3)采用精料、高温、高压、富氧、大喷煤的冶炼工艺,实现高产、优质、低耗的目的。
钢铁行业节能减排方向和措施方案
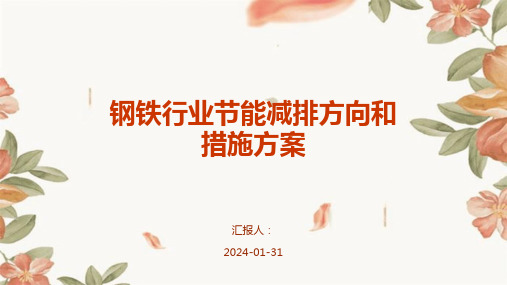
智能化生产管理与优化调度
推广智能化生产管理系统
01
实现生产计划、调度、监控等智能化管理,提高生产效率。
发展能源管理中心
02
实现能源数据采集、分析、优化调度等功能,提高能源利用效
率。
推广自动化控制技术
03
如自动化炼钢、自动化轧钢等,减少人工干预,提高生产稳定
性和效率。
绿色产品认证
推动钢铁产品绿色认证,提高产 品环保性能,满足市场需求。
01
节能减排技术应用
推广高效节能技术,如高炉煤气 余压发电、干熄焦等,降低能源 消耗。
02
03
04
资源综合利用
加强废弃物和副产品的回收利用 ,提高资源利用效率,降低生产 成本。
未来发展趋势预测及挑战分析
低碳化发展
随着全球气候变化问题日益严峻,钢铁行业 将面临更严格的碳排放限制,推动低碳化发
持续改进路径及创新点挖掘
技术改造升级
推广应用高效节能、环保治理新技术,提高能源利用效率和环保 治理水平。
管理优化创新
引入精益管理、能源管理等先进理念和方法,提升企业管理效能。
创新点挖掘
鼓励企业开展技术创新、管理创新等活动,培育节能减排新动力。
国内外经验借鉴与合作交流
国内经验借鉴
学习国内先进企业的节能减排经验,推广成功案例和 做法。
国际合作交流
加强与国际钢铁行业组织、企业的交流合作,引进国 际先进技术和管理经验。
政策对接与资源整合
密切关注国内外政策动态,整合内外部资源,为企业 节能减排提供有力支持。
05
总结与展望:推动钢铁行业绿色发 展
项目成果总结及亮点展示
钢铁厂节能环保措施方案

钢铁厂节能环保措施方案背景钢铁厂作为重工业的代表,是国家经济发展和军事建设的重要支撑。
同时,钢铁生产也是能源消耗和环境污染较为严重的行业之一。
为了实现经济效益和生态环境的可持续发展,钢铁厂需要采取节能环保措施。
节能措施1.引进先进节能技术。
钢铁厂可以引进节能型高炉、热风炉和高温烟气余热利用等先进技术。
通过这些技术的应用,可以降低单位产品的能耗。
2.实行系统能源管理。
钢铁厂可以建立能源管理中心,通过对能源的策划、监测、调度和优化,实现节能减排的目的。
3.优化能源结构。
钢铁厂可以将煤改气、煤改电,同时利用生物质能源、风能、太阳能等清洁能源,优化能源结构,降低能耗。
环保措施1.建立废气、废水处理系统。
钢铁厂通过建立废气、废水处理系统,对生产过程中产生的废气、废水进行处理,实现排放的标准化和减少对环境的影响。
2.推广循环经济。
钢铁厂可以采用“废渣变宝”、“废渣变土”等循环经济模式,将废渣转化为资源,实现资源的高效利用,既减少废物排放,又降低了生产成本。
3.建立环境监测系统。
钢铁厂应建立环境监测中心,对生产过程中的废气、废水、废渣等对环境的影响进行在线监测和数据分析,并及时进行调整和优化,保证环境排放达到标准化要求。
未来展望钢铁厂作为重工业的代表,在经济发展和环境保护之间需要寻找合理的平衡点。
随着社会的发展和技术的进步,钢铁厂在节能环保领域仍有许多发展空间。
未来,钢铁厂应不断引入新技术、新材料,提高自身的节能环保水平,逐渐实现从传统能源向清洁能源的转变。
钢铁行业节能工作方案

钢铁行业节能工作方案
钢铁行业作为重要的基础产业,其高耗能、高排放的特点使其成为节能减排的重要领域。
为此,钢铁行业需要制定一系列的节能工作方案,以提高产品生产效率,降低能耗和排放量,实现可持续发展。
以下是一些可以采取的具体措施:
1. 完善能源管理体系:建立科学的节能指标体系,制定能源消耗监测和管理办法,建立能源消耗数据管理系统,实现对能源消耗情况的精确监控和评估。
2. 推广先进的设备和工艺:引进并推广运用先进的钢铁生产设备和技术,如高效炼钢技术、能量回收技术、先进的热处理工艺等,以降低能耗、提高产品质量和产能。
3. 加强能源利用和回收利用:改造和升级炉况设备,提高热能利用效率;开展钢铁渣的资源化利用,建立钢铁渣综合利用系统,实现渣料的有效回收和再利用。
4. 优化生产过程管理:通过优化生产流程,减少生产中的能源浪费和损失,合理调度生产计划,降低能源供应和消耗的峰谷差异。
5. 建立节能意识教育和培训体系:加强员工的节能意识教育和培训,提高员工节能意识和能力,促使其充分参与到节能工作中。
6. 完善能源管理政策和措施:加强对钢铁行业的节能管理政策,
通过制定税收、奖励和惩罚等措施,激励企业主动进行节能减排,推动全行业的节能工作。
综上所述,通过完善能源管理体系、推广先进设备和工艺、加强能源利用和回收利用、优化生产过程管理、建立节能意识教育和培训体系、完善能源管理政策和措施等措施,钢铁行业可以实现节能减排,促进可持续发展。
钢铁行业节能降耗改造技术方案

钢铁行业节能降耗改造技术方案钢铁行业是社会经济发展的基础产业之一,但同时也是能源消耗和环境污染相对较大的行业。
为了实现可持续发展和降低能源消耗、减少环境污染,钢铁行业需要进行节能降耗改造。
以下是钢铁行业节能降耗改造技术方案。
1.高效炼钢技术:采用高效炼钢技术,如湿法炼钢技术、氧气后燃技术等,可以提高钢铁生产效率,并降低能源消耗和环境污染。
2.能源回收利用技术:通过对高温烟气、废水、废渣等进行能源回收利用,如余热回收利用、生物气的产生与利用、炉渣综合利用等,可以降低能源消耗,提高资源利用率。
3.熔炼废钢技术:钢铁行业可以大量采用回炉精炼技术,通过对废钢的高温熔炼,可以降低原料消耗,减少能源消耗,同时还可以减少废钢的堆放和对环境的污染。
4.绿色烧结技术:烧结是钢铁生产过程中不可或缺的环节,采用绿色烧结技术可以降低燃料消耗和烟气排放。
绿色烧结技术包括脱硫烧结、沸腾床烧结等,可以提高烧结矿的质量,减少烧结废气的排放。
5.节能炉窑技术:采用高炉煤气发电技术、烧结废气余热发电技术等,可以将炉窑产生的余热直接转化为电力,提高能源利用效率。
6.环保净化技术:钢铁生产过程中产生的废气、废水、废渣等需要进行净化处理。
采用湿法除尘技术、脱硫脱氮技术、深度处理废水技术等,可以降低大气污染物和水污染物的排放,保护环境。
7.节能监测与管理系统:建立钢铁行业节能监测与管理系统,通过对能源消耗、产能利用率等进行实时监测和数据分析,提出改进建议,实现能源的合理利用和节约。
除了以上技术方案,钢铁行业还可以加强与科研机构和高校的合作,加大对节能降耗技术的研发力度。
同时,政府可以出台相关政策和标准,加大对节能降耗改造的支持和奖励力度,鼓励企业进行节能降耗改造。
总之,钢铁行业的节能降耗改造技术方案包括高效炼钢技术、能源回收利用技术、熔炼废钢技术、绿色烧结技术、节能炉窑技术、环保净化技术和节能监测与管理系统等。
通过采取这些技术方案,可以降低能源消耗,减少环境污染,实现钢铁行业的可持续发展。
钢铁厂施工技术的能源消耗优化方案

钢铁厂施工技术的能源消耗优化方案一、引言随着工业的快速发展,钢铁行业成为推动国民经济增长的重要支柱产业。
然而,钢铁生产过程中的能源消耗却不可忽视,对环境造成了较大的影响。
因此,本文旨在提出钢铁厂施工技术的能源消耗优化方案,以帮助钢铁厂提高能源利用效率,减少对环境的负面影响。
二、燃料选择优化燃料的选择对钢铁生产过程能源消耗的优化起着至关重要的作用。
首先,钢铁厂可以考虑采用替代燃料,如生物质燃料、煤矸石等,以减少对化石燃料的过度依赖。
其次,钢铁厂在选择燃料时应充分考虑其能量密度、成本以及环境效益,以达到能源消耗和环境影响的双重平衡。
三、高效供能设备的使用在钢铁厂的施工过程中,采用高效供能设备是减少能源消耗的重要手段。
例如,引入节能型电机、高效热能回收系统等设备,以提高能源利用率。
此外,采用智能化监控系统,对设备运行进行优化管理,进一步提高生产效率,减少能源浪费。
四、工艺流程的优化优化钢铁厂施工的工艺流程是降低能源消耗的关键因素之一。
通过对现有工艺流程进行改进和优化,可以降低能源消耗,并提高生产效率。
例如,优化高炉炼铁工艺,减少渣的产生,提高炉渣综合利用率;调整钢铁冶炼工艺中的工艺参数,以减少废气、废水的排放。
五、节能意识的培养在钢铁厂的施工过程中,培养员工的节能意识是实现能源消耗优化的重要环节。
钢铁企业应加强对员工的节能培训,提高员工的节能意识,促使员工在施工过程中采取节能措施。
此外,建立激励机制,对于在节能方面有突出贡献的员工予以奖励,进一步推动节能减排工作。
六、技术创新的推动技术创新是钢铁厂施工技术能源消耗优化的重要保障。
钢铁企业应加大对新技术的研发和应用,如智能控制技术、绿色制造技术等,以实现生产过程的能源消耗降低和生产效率提高。
同时,加强与科研院校和专业研究机构的合作,共同推动钢铁行业技术创新工作。
七、结论综上所述,钢铁厂施工技术的能源消耗优化方案是实现钢铁产业可持续发展的重要途径。
通过燃料选择优化、高效供能设备的使用、工艺流程的优化、节能意识的培养和技术创新的推动,钢铁企业可以降低能源消耗,提高效率,减少对环境的负面影响。
炼钢厂节能降耗措施

炼钢厂节能降耗措施
炼钢厂可以采取以下节能降耗措施:
1. 优化生产工艺:通过改进生产工艺,减少能源消耗和浪费。
2. 设备升级与维护:定期对设备进行维护和升级,提高设备的运行效率,降低能耗。
3. 能源管理系统:建立能源管理系统,实时监控能源消耗情况,及时发现并解决能源浪费问题。
4. 员工培训:加强员工节能意识培训,提高员工的节能意识和技能。
5. 余能回收利用:利用炼钢过程中产生的余能,如废气、废渣等,进行回收利用,降低能源消耗。
6. 照明系统优化:采用高效节能的照明灯具,合理布置照明系统,减少照明能耗。
7. 原料优化:选择低能耗、高品质的原料,降低生产成本和能源消耗。
8. 能源合同管理:与能源服务公司合作,进行能源合同管理,优化能源使用效率,降低能源成本。
这些措施可以帮助炼钢厂降低能源消耗,提高生产效率,实现可持续发展。
具体实施应根据炼钢厂的实际情况进行调整和优化。
- 1、下载文档前请自行甄别文档内容的完整性,平台不提供额外的编辑、内容补充、找答案等附加服务。
- 2、"仅部分预览"的文档,不可在线预览部分如存在完整性等问题,可反馈申请退款(可完整预览的文档不适用该条件!)。
- 3、如文档侵犯您的权益,请联系客服反馈,我们会尽快为您处理(人工客服工作时间:9:00-18:30)。
钢铁行业节能降耗改造技术方案
一、序言
钢铁行业是工业领域的耗能大户,也是我国节能减排潜力最大的行业之一。
“十一五”期间,钢铁行业一方面频频被“点名”,成为全社会节能减排的重点和难点领域;另一方面,钢铁行业节能减排取得的成效,也为全社会推进节能减排做出了巨大贡献。
去年9月国家已经出台《钢铁行业生产经营规范条件》,对钢铁企业的环境保护、能源消耗和资源回收利用、工艺装备等方面做出了具体的要求。
《条件》明确提出,对于不具备规范条件的企业需按照规范条件要求进行整改,整改后仍达不到要求的企业应逐步退出钢铁生产。
对不符合规范条件的企业,有关部门不予核准或备案新的项目、不予配置新的矿山资源和土地、不予新发放产品生产许可证、不予提供信贷支持。
与“十一五”相比,“十二五”期间,国家的环保法律法规将更加严格,节能减排任务更艰巨,钢铁行业的压力也更大。
在“十二五”规划纲要提出的钢铁行业发展重点方向中,与节能减排相关的内容占据了大多数:支持非高炉炼铁、洁净钢生产、资源综合利用等技术开发;重点推广能源管控系统技术和高温高压干熄焦、余热综合利用、烧结烟气脱硫等节能减排技术。
二、高炉冲渣水余热利用
目前,钢铁产业余热余能的回收利用率相当低,其中,高温余热比较容易回收,目前在节能降耗的技术改造中已大部分得到回收;但低温余热的回收却几乎为零,如高炉冲渣水的余热,大多被浪费掉。
应该指出,低温余热约占总余热的35%,因此,钢铁产业的低温余热存在着巨大的回收潜力。
钢铁厂在高炉炼铁工艺中,产生的炉渣温度大约为1000℃。
目前,大多数炼铁企业的处理方法是:将此炉渣在冲渣箱内由冲渣泵提供的高速水流急冷冲成水渣并粒化,以供生产水泥之用。
一般每吨铁排出约0.3t 渣,每吨渣可产生80~95℃,5~10t 的冲渣水。
为了保证冲渣水的循环利用效果,需要将这部分冲渣水在沉淀过滤后引入空冷塔,降温到50℃以下再次循环冲渣。
这样就使得很大一部分热量在空冷塔中流失,既造成了能源的浪费,又对环境造成了热污染。
若能合理利用这些余热,既可节约能源、减少运行成本,又可保护环境、减少热污染。
热泵的利用是解决这一问题的有效途径。
热泵作为一种有效的节能技术,正在成为利用低品位能量的有效工具。
根据驱动能源的不同,热泵还可分为电力驱动的蒸汽压缩式热泵、蒸汽或废热驱动的吸收式热泵和热力驱动的蒸汽喷射式热泵三大类。
利用高温热源,将低温热源(如废热)提高到某一中间温度而加以利用的热泵称为第一类热泵,如家用热泵式空调等;利用大量中间温度的废热和该废热源与低温热源的热势差,来制取热量少但温度高于中温废热的热水或蒸汽的热泵为第二类热泵,如热泵干燥机等。
钢铁
企业的许多工序中产生大量低品位余热,所以,吸收式热泵特别是第二类热泵在冶金企业中有很大的应用潜力。
1.制取高温水或低压蒸汽
将高炉冲渣水沉淀过滤后,进行水水热交换,再通过吸收式热泵机组,利用冲渣水中大量的中温热源为热能驱动,用大量中温热源和低温热源的热势差,制取高温水或者低压蒸汽,将部分中低热能转移到更高温位,从而提高了热源的利用品位,同时也对冲渣水进行了冷却。
制取的蒸汽可用于厂区或厂区周边建筑供热、洗浴或为锅炉补水。
以年产值10万吨钢铁的某钢铁厂为例,其每年产生180000吨90℃冲渣水。
通过吸收式热泵将冲渣水降温至60℃,则可获得
62.8MW热量,相当于燃烧1046吨标准煤产生的热量。
2.制取工艺冷却水
钢铁企业在生产过程中有许多部门需要制取低温冷媒水用于工艺冷却和空调制冷,如轧钢厂、焦炉煤气净化工艺、主电室、电气控制室、电子计算机房、操作台、仪表放、各办公楼、居住区等。
从冷却要求来说,有的可以用较高温度的冷却水,而又的冷却过程必须使用较低温度的冷却水,这部分低温冷却水就需要通过制冷机组制取。
可以使用吸收式热泵机组,利用高炉冲渣水进行制冷。
首钢是国内第一家利用高炉冲渣水进行制冷的钢铁企业。
在满足多个部门空调用冷量的同时,充分利用了余热资源达到了节能降耗的目的。
吸收式热泵制冷流程图
以制取5000kW冷量为例,如使用电压缩制冷机组,电压缩机组能效比COP按3.0计算,按小时满负荷费用计算,耗电量为5000kW/3.0=1666.7kWh。
每千瓦时电费按0.55元计算,则电压缩制冷机组每小时运行费用为916.7元。
选用双效吸收式热泵制冷时,按小时满负荷费用计算,消耗蒸汽量6.25t/h,蒸汽价格80元/吨,则每小时500元。
可以看出吸收式热泵制冷费用是电制冷的54.5%。
3.发电
冲渣水余热回收发电系统的一般思路是:该系统主要由循环工质蒸汽发生器、动力机、工质循环增压泵和发电机组成。
循环工质进入余热蒸汽发生器中吸收冲渣水热量汽化为工质蒸汽。
工质蒸汽进入动力机中,推动动力机转动,并带动发电机产生电能。
其中动力机本身具有减温减压的功能。
液态工质在增压泵的作用下进入余热蒸汽发生器中再次吸收热量,循环往复。
每吨90℃热水可发电1.5kWh,折标煤0.6kg,80℃热水可发电1kWh,折标煤0.4kg。
以年产值10万吨钢铁的某钢铁厂为例,其每年产生180000吨90℃冲渣水,冲渣水经过冷却塔冷却后循环利用,年耗水量约为19000吨。
将冲渣水余热用来发电,则年发电量为270000 kWh,年节省标煤108吨,节水19000吨。
三.烟气余热回收
烧结工序的能耗约占冶金总能耗的12%。
而其排放的余热约占总能耗热能的49%。
回收和利用这些余热,显然极为重要,余热回收主要在烧结矿成品显热及冷却机的排气显热两个方面。
目前热管技
术主要应用在冷却机的排气显热回收上。
烧结机生产时,热烧结矿从烧结机的尾部落下经破碎后,通过振动筛分经溜槽落到冷却机传送带上,在溜槽部分热矿料温度可达700~800℃,此时以辐射形式向外散热为主,落到冷却带上后料温仍在600℃以上。
一般在烧结冷却机下布置有数台冷却风机,通过轴流风机或鼓风机,使冷却风强制穿过料矿层,经料矿加热后,在第一风罩内冷却风温提高到350~400℃,在第二风罩内冷却风温提高到250~300℃,这两个风罩内的冷却风都可以利用其余热。
烟气热回收主要目的是利用热管设备吸收锅炉余热产出过热蒸汽。
主要设备包括:蒸汽过热器、高温热管式蒸发器、高压蒸汽包、热管式省煤器、低温热管式蒸发器、低压蒸汽包、除氧器、分汽缸、连排扩容器、定排扩容器、取样器、水箱循环管路及电控系统等组成。
蒸汽过热器采用翅片列管式,其余换热设备全部采用重力热管式,高温区采用高温热管式蒸发器,中温区采用热管式省煤器,低温区采用低温热管式蒸发器。
热管设备全部采用环翅片钢——水热管,热管与水平呈15°夹角倾斜布置,烟气下进上出、垂直烟道。
热管技术介绍:热管是一种具有特高导热性能的新颖传热元件。
热管是由钢、铜、铝管内灌充导热介质,抽成一定的真空后密封而成,管内的工作介质由多种无机活性金属及其化合物混合而成,具有超强的热活性和热敏感性,遇热而吸,遇冷而放。
以首钢京唐钢铁厂烧结车间为例,年产1015.3万吨烧结矿,年回收蒸汽约为77.6万吨。
四.变频技术的利用
在工厂电力拖动自动控制系统领域中,作为传动源的异步电动机担负着重要的角色,变频器的高静、动态性能、宽调速范围及无级调速方式等特点远远胜过直流电动机调速。
变频技术是应交流电动机无级调速的需要而产生的。
变频器是通过对电力半导体器件(如IGBT)等的通断控制,将电压和频率固定不变的交流电工频电源,变换为电压和频率可变的交流电的电能控制装置,为了产生可变的电压和频率,该设备首先要把三相或单相交流电变换为直流电(DC)。
然后再把直流电(DC)变换为三相或单相交流电(AC),我们把实现这种转换的装置称为“变频器”(inverter)。
对于交—直—交型的变频器来说,为了产生可变的电压和频率。
首先要把工频(50Hz或60Hz)的交流电源,变换为直流电(DC)再转换成各种频率(0Hz ~50Hz、0Hz ~60Hz 及0Hz ~400Hz )的交流电,最终实现对电机的调速运行。
变频调速是异步电动机变压变频调速系统的简称,即改变电机供电电源的电压和频率,以改变旋转磁场的旋转速度,从而使电机的转速得到改变。
变频调速的功能特点是明显的,改变电动机转速即可达到改变流量、压力的目的,又可使输入功率成三次方减少。
可见节电效果相当显著。
对部分功率有富裕的水
泵而言,应用变频调速还可以起到节水作用,从而避免了“大马拉小车”的弊端。
可对钢铁厂除尘风机、水泵、烧结风机系统等设备进行变频节电改造,使其达到最佳运行状态,同时节省其运行费用。