多段炉与斯列普炉活化装置系统综合比较
东北大学智慧树知到“能源与动力工程”《工业炉热工及构造(录题)》网课测试题答案4

东北大学智慧树知到“能源与动力工程”《工业炉热工及构造(录题)》网课测试题答案(图片大小可自由调整)第1卷一.综合考核(共15题)1.热滑轨是在钢坯与水管之间起一种“隔绝作用”,以()黑印温度,减少黑印的温差,甚至基本上消除黑印。
A.降低B.提高C.保持D.减少2.二段制度炉子分为两段,即加热段和预热段。
()A.正确B.错误3.在炉气充满炉膛的条件下,适当地增加炉膛高度,还可增加炉内气层厚度,提高1这也使C值增大,不利于传热。
()A.正确B.错误4.一般加热炉的热平衡分为二个区域:炉膛区域,预热装置区域炉子热平衡。
()A.正确B.错误5.炉子生产率它是指单位时间内炉子的产量,用P表示。
()A.正确B.错误6.在其它条件一定的情况下,平均辐射温压∆T4的数值愈大,传给炉料的热量愈多,炉子生产率愈高。
()A.正确B.错误7.准确控制金属的加热温度,使其超过所要求的加热温度,这样就可以减少金属烧损。
()A.正确B.错误8.炉子热工系统是火焰炉的最基本的组成部分,它包括炉子的工作室、供热系统、排烟系统以及冷却系统。
()A.正确B.错误9.供热制度:指炉内的燃料燃烧的情况,它和炉温分布是互为因果的。
()A.正确B.错误10.设计和修筑炉子基础时混凝土任何部分的温度不允许超过()℃。
A.300°B.400°C.200°D.150°11.炉温制度和供热制度总是结合起来考虑的,把它们的总和叫作“预热制度”。
()A.正确B.错误12.一般加热炉分为两个区域:预热装置区域和整个炉子平衡。
()A.正确B.错误13.钢的氧化和脱碳是同时发生的,随着氧化铁皮的生成,钢的脱碳将()或抑制。
A.提高B.不变C.减弱14.连续加热炉的炉膛内部宽度决定于料坯的()和料坯在炉内的排数。
A.炉子消耗的热量B.炉子的生产率C.长度15.火焰炉炉膛热工作的基本方程式的解析式是联立炉膛热平衡和热交换方面的过程中得到的,它包括炉子热效率或有效热方程式和炉膛废气出口温度方程式。
多段炉与回转炉全面对比分析(1)
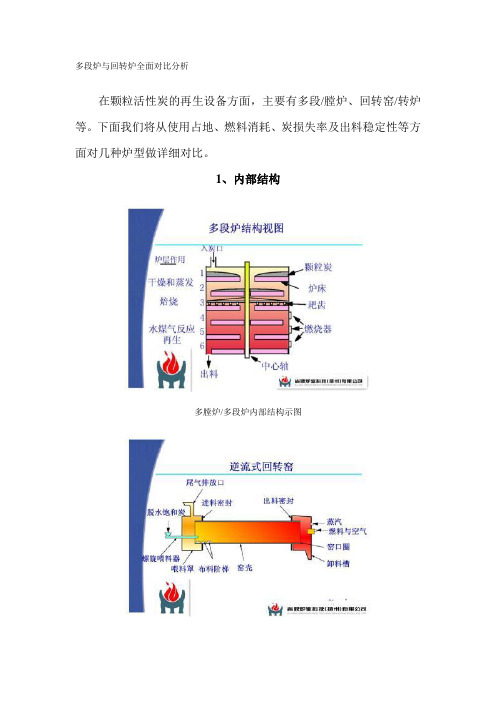
多段炉与回转炉全面对比分析在颗粒活性炭的再生设备方面,主要有多段/膛炉、回转窑/转炉等。
下面我们将从使用占地、燃料消耗、炭损失率及出料稳定性等方面对几种炉型做详细对比。
1、内部结构多膛炉/多段炉内部结构示图气固相物料逆向接触式/逆流式回转窑/转炉结构示图气固相物料同向接触式/顺流(并流、平行)式回转窑/转炉结构示图2、设备的运行和使用情况2.1占地回转窑对于工厂用地,建筑用地及附属结构所需用地要大于多段炉。
2.2燃料消耗多段炉内衬砖后面的隔热材料的使用能够减少热量的损失,而类似的隔热材料是不能够用于回转窑上的,另外回转窑表面积大,热量损失大。
炉型能量消耗(KJ/KG炭)多段炉5815至10467回转窑8141至186082.3炭损失率回转窑因其内部环境的不稳定性容易造成损失率高于多段炉,并且各个批次的物料情况也波动较大。
2.4 多段炉热再生活性炭之优势(1)可对再生工艺参数进行严格控制,尤其在炉膛气氛——蒸汽比率和燃气用量——的控制方面更是如此;(2)可降低由气化反应引起的炭损耗率,该项损失率一般在3%到5%范围内,比其它类型的再生炉炭损失率(一般在5%到10%范围内)要低得多;(3)可降低因机械磨耗导致的炭损失率;(4)单位产品的能耗较低,通常在1380 到2500kcal/kg再生炭范围内;(5)固相活性炭与气相活化剂的相接触几率高(反应速率快),故炉子的最小设计容量比率可允许降低到35%的水平,装置系统更加紧凑;(6)结构简单、坚固,使用寿命长,保养维修容易;(7)运转操作简单,最适合自动化,易于管理;(8)装置系统占地面积小;(9)对负荷波动安定性好。
(10)值守工人少(1到2人)(11)热值利用高。
定点供热高效利用热能,可满足氧化性、还原性及中性气氛需要。
(12)多段炉炉床采用异形耐火砖铺设,相互锁紧,稳定性高,不脱落。
回转窑因空腔内无支撑耐火砖或耐火金属之结构,在高温且重力作用下易出现坍塌、断裂的情况,且修复处易出现反复脱落情况。
催化裂化装置产汽系统及余热锅炉技术特点概述

催化裂化装置产汽系统及余热锅炉技术特点概述催化裂化是一种重要的炼油工艺,通过将重质石油馏分裂解成较轻的产品,如汽油和柴油等,以满足市场需求。
在催化裂化装置中,产汽系统及余热锅炉是其重要组成部分,其技术特点对于提高催化裂化装置的生产效率和能源利用率至关重要。
本文将对催化裂化装置产汽系统及余热锅炉的技术特点进行概述,以期为相关行业提供参考。
一、催化裂化装置产汽系统的技术特点1. 多级产汽系统设计催化裂化装置中的多级产汽系统是为了最大限度地利用热能,提高能源利用效率。
通常采用的是高温高压的产汽方式,将裂化反应过程中产生的热能转化为高温高压的蒸汽,用于提供装置运行所需的动力和热能。
多级产汽系统能够有效地增加蒸汽的压力和温度,提高其能量利用率,从而降低了生产成本,提高了装置的经济效益。
2. 蒸汽余热回收催化裂化装置中,裂化反应过程会产生大量的余热,这些余热如果不能得到合理的利用将会造成能源的浪费。
对于产汽系统而言,余热回收是其重要的技术特点之一。
通过余热锅炉将裂化反应产生的余热进行回收利用,将余热转化为蒸汽,从而进一步提高了热能的利用率,降低了能源消耗,减少了环境污染。
3. 自动控制与安全保护产汽系统作为催化裂化装置的重要组成部分,其自动控制与安全保护技术是至关重要的。
通过自动控制系统对产汽系统的运行参数进行实时监控和调节,确保系统的稳定运行和高效工作。
配备完善的安全保护系统,对于产汽系统的各个部分进行全方位的监测和保护,有效预防了可能发生的事故和故障,保障了装置的安全运行。
二、余热锅炉的技术特点1. 高效换热余热锅炉是一种利用余热进行能量回收的设备,其技术特点之一是高效换热。
通过采用先进的换热器件和换热技术,余热锅炉能够将裂化反应产生的余热充分利用,实现热能的高效转化。
2. 多种余热回收方式余热锅炉的技术特点还体现在其多种余热回收方式上。
根据裂化装置产生的余热特点和需要利用的热能形式,余热锅炉可以采用不同的回收方式,如蒸汽余热回收、热油余热回收、热水余热回收等,以实现余热的高效回收利用。
多段炉的构造运行原理及应用

应用于活性炭制造过程的炭化、 水蒸气活化工序的优点
7
活性炭制造工艺流程简介
一.
活性炭是对一系列具有高孔隙率碳质材料的通用性称谓,它无法采 用结构式进行描述,也不能进行化学式量分析。活性炭的孔容积一般 被定义为高于0.2mL/g,且其内表面积一般大于400m2/g(采用氮吸附 BET法进行检测)。活性炭的孔隙宽度变化范围从3埃米到几千埃米, 其孔隙在传统上一般按照直径进行分类:大孔(500到20000埃米)、 过渡孔(中孔,100到500埃米)、微孔(8到100埃米)。从横截面角 度观察,孔隙的形状表现为圆筒状或矩形,但同时还表现为各种不规 则的形状,也存在“束颈型”或“瓶颈型”孔隙。
10
1.什么是传统机械按键设计?
传统的机械按键设计是需要手动按压按键触动PCBA上的开关按键来 实现功能的一种设计方式。
传统机械按键结构层图:
按键
PCBA
开关键
传统机械按键设计要点:
1.合理的选择按键的类型,尽量选 择平头类的按键,以防按键下陷。
2.开关按键和塑胶按键设计间隙建 议留0.05~0.1mm,以防按键死键。 3.要考虑成型工艺,合理计算累积 公差,以防按键手感不良。
运行原理及应用尚鼎炉业科技扬州有限公司多段耙式炉之构造特性多段耙式炉之构造特性构造多段耙式炉之构造特性如上图所示在钢板制圆筒型炉体内以耐火材做壁炉施工并区隔为多段每段炉床隔段分别于炉床周围及中央设置处理物排出口处理物由安装于低速运转053rpm中心轴搅拌臂之搅拌齿由炉床上外侧向内侧如图二及于下一段由炉床内侧往外侧如图三交互排出处理物与燃烧物体经排出口完全对流接触设置于炉中央之空心中心轴及搅拌臂由专用轴冷风车之冷风强制
在理想温度(Uniform temperature)置留时间(RESIDENCE TIME)平均 厚度(Uniform Depth) 使其反应完全(Uniform Reactively) ,在回转炉 (Rotary Kiln)是不能达到的。
斯列普火化炉烘炉经验技巧总结
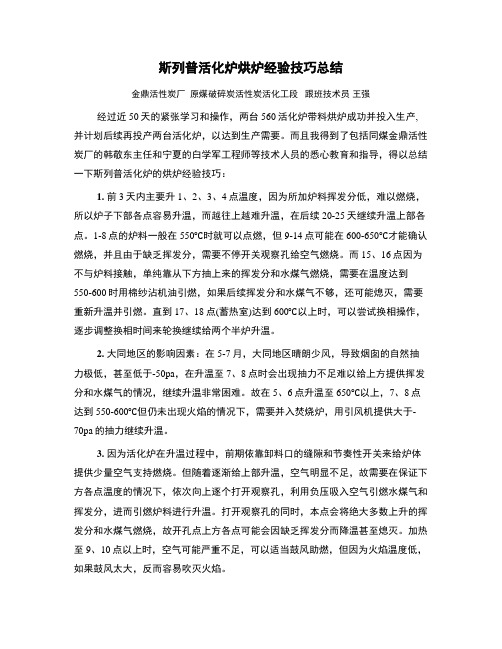
斯列普活化炉烘炉经验技巧总结金鼎活性炭厂原煤破碎炭活性炭活化工段跟班技术员王强经过近50天的紧张学习和操作,两台560活化炉带料烘炉成功并投入生产,并计划后续再投产两台活化炉,以达到生产需要。
而且我得到了包括同煤金鼎活性炭厂的韩敬东主任和宁夏的白学军工程师等技术人员的悉心教育和指导,得以总结一下斯列普活化炉的烘炉经验技巧:1.前3天内主要升1、2、3、4点温度,因为所加炉料挥发分低,难以燃烧,所以炉子下部各点容易升温,而越往上越难升温,在后续20-25天继续升温上部各点。
1-8点的炉料一般在550℃时就可以点燃,但9-14点可能在600-650℃才能确认燃烧,并且由于缺乏挥发分,需要不停开关观察孔给空气燃烧。
而15、16点因为不与炉料接触,单纯靠从下方抽上来的挥发分和水煤气燃烧,需要在温度达到550-600时用棉纱沾机油引燃,如果后续挥发分和水煤气不够,还可能熄灭,需要重新升温并引燃。
直到17、18点(蓄热室)达到600℃以上时,可以尝试换相操作,逐步调整换相时间来轮换继续给两个半炉升温。
2.大同地区的影响因素:在5-7月,大同地区晴朗少风,导致烟囱的自然抽力极低,甚至低于-50pa,在升温至7、8点时会出现抽力不足难以给上方提供挥发分和水煤气的情况,继续升温非常困难。
故在5、6点升温至650℃以上,7、8点达到550-600℃但仍未出现火焰的情况下,需要并入焚烧炉,用引风机提供大于-70pa的抽力继续升温。
3.因为活化炉在升温过程中,前期依靠卸料口的缝隙和节奏性开关来给炉体提供少量空气支持燃烧。
但随着逐渐给上部升温,空气明显不足,故需要在保证下方各点温度的情况下,依次向上逐个打开观察孔,利用负压吸入空气引燃水煤气和挥发分,进而引燃炉料进行升温。
打开观察孔的同时,本点会将绝大多数上升的挥发分和水煤气燃烧,故开孔点上方各点可能会因缺乏挥发分而降温甚至熄灭。
加热至9、10点以上时,空气可能严重不足,可以适当鼓风助燃,但因为火焰温度低,如果鼓风太大,反而容易吹灭火焰。
催化裂化装置产汽系统及余热锅炉技术特点概述

催化裂化装置产汽系统及余热锅炉技术特点概述随着工业化进程的不断推进,石油化工行业的发展也愈发迅猛。
炼油业作为石油化工产业中最重要的产业之一,对能源资源的利用和环境保护提出了更高的要求。
在炼油过程中,催化裂化装置产汽系统及余热锅炉技术扮演着重要的角色。
在这篇文章中,我们将概述催化裂化装置产汽系统及余热锅炉技术的特点和应用。
一、催化裂化装置产汽系统1.技术原理催化裂化是一种重要的炼油工艺,在炼油过程中通过催化剂将重质原油分解成轻质油品的方法。
催化裂化装置产汽系统是催化裂化装置中的一个重要组成部分,其主要作用是产生高温高压的蒸汽,为催化裂化反应提供所需的热量和压力。
2.技术特点(1)高效节能:催化裂化装置产汽系统采用先进的节能技术,能够充分利用燃料燃烧产生的热能,实现高效节能。
(2)稳定可靠:产汽系统运行稳定,设备可靠,能够满足催化裂化装置在不同工况下的运行需求。
(3)自动化控制:采用先进的自动化控制系统,实现对产汽系统的精准控制,提高生产效率,降低人工操作成本。
(4)环保节能:产汽系统能够充分利用余热资源,减少能源消耗,降低对环境的影响。
3.应用领域催化裂化装置产汽系统广泛应用于炼油、化工等行业,为生产提供所需的蒸汽能源,是炼油生产过程中不可或缺的重要设备。
二、余热锅炉技术余热锅炉是一种利用工业生产过程中废热资源的能源回收设备,其原理是将工业生产过程中产生的高温废热转化为蒸汽或热水,用于供暖或生产过程中的热能需求。
(1)废热回收:余热锅炉技术能够有效回收工业生产过程中产生的废热能源,提高能源利用效率。
(2)灵活多样:余热锅炉技术可以根据不同的工业生产过程和废热特点进行定制设计,满足不同用户的热能需求。
(3)环保节能:余热锅炉技术能有效减少工业生产过程中的能源消耗,降低排放,具有显著的环保效益。
(4)经济效益:余热锅炉技术的应用能够有效降低企业的能源成本,改善生产效率,提高企业的经济效益。
余热锅炉技术广泛应用于炼油、化工、钢铁、造纸等行业,为工业生产提供经济、环保的热能解决方案。
2022年-2023年公用设备工程师之专业知识(动力专业)练习题(二)及答案

2022年-2023年公用设备工程师之专业知识(动力专业)练习题(二)及答案单选题(共40题)1、干背式锅炉和湿背式锅炉的区别在于( )。
A.干背式锅炉的烟气为干的,而湿背式锅炉的烟气是湿的B.干背式锅炉的烟室布置在烟气的第一、二回程之间,而湿背式锅炉的烟室布置在第二、三回程之间C.炉胆后部的折烟室是否布置于锅水中D.烟气温度低时用干背式锅炉,烟气温度高时用湿背式锅炉【答案】 C2、下列说法中正确的为( )。
A.采用制冷剂直接膨胀式空气冷却器时,可用氨作制冷剂B.采用制冷剂直接膨胀式空气冷却器时,宜用氨作制冷剂C.采用制冷剂直接膨胀式空气冷却器时,应用氨作制冷剂D.采用制冷剂直接膨胀式空气冷却器时,不得用氨作制冷剂【答案】 D3、工业锅炉供热系统热介质包括蒸汽和热水两种,下列选项不属于以蒸汽为供热介质优点的是( )。
A.可以同时满足蒸汽用户和热水用户的需要B.供热介质温度高,可减少用户的散热器面积C.热水蓄热能力强,热稳定性好D.可采用热电联产供热方案,提高供热的经济效益【答案】 C4、未经处理的天然水或城镇供水网的自来水称为( )。
A.锅水B.补给水C.原水D.给水【答案】 C5、热力除氧是根据( )的基本原理。
A.阿基米德定律和道尔顿定律B.道尔顿定律和亨利定律C.道尔顿定律和自控定律D.自动定律和阿基米德定律【答案】 B6、对于液化石油气供应基地、气化站、混气站内的生产区内的规划,以下叙述正确的为( )。
A.可随意种植不易造成液化石油气积存的植物B.严禁种植易造成液化石油气积存的植物C.可种植各类植物D.可种植乔木【答案】 B7、以下不属于活塞式压缩机的是( )。
A.鼓风机B.单作用式压缩机C.转子式压缩机D.双作用式压缩机【答案】 C8、关于管道固定支架,下列说法错误的是( )。
A.管段的热伸长量不得超过补偿器的允许补偿量B.固定支架所能承受的允许推力值不得超过管段因膨胀产生的推力C.不宜使管道产生纵向弯曲D.管道固定支架是用来承受管道因热胀冷缩而产生的推力【答案】 B9、提高汽轮机单机最大功率的途径不包括( )。
能源科学技术:生物质能技术试题预测三

能源科学技术:生物质能技术试题预测三1、问答题简述世界生物柴油生产现状及发展趋势。
正确答案:世界各国,尤其是发达国家,都在致力于开发高效、无污染的生物质能利用技术。
欧洲已成为全球生化柴油的主要生产地。
美国、意大(江南博哥)利、法国已相继建成生物柴油生产装置数百座。
截止2007年,中国有大小生物柴油生产厂2000多家。
生物柴油的需求量在不断增加,预计到2012年,中国生物柴油的需求量将达到2000万吨/年,按国家再生能源中长期规划,那时的产能是20万吨/年。
需求与产量的反差,将会是形成产品供不应求的局面。
向基地化和规模化方向发展,实行集约经营,形成产业化.目前,原料短缺是制约生物柴油产业化发展的重要瓶颈。
2、问答题生物柴油标准分析的指标有哪些?正确答案:①闪点:表示油品蒸发性和着火危险性的指标,生物柴油的闪点一般高于110℃,远高于石化柴油(70℃),因此在储存、运输和使用中安全性很高。
闪点和生物柴油中甲醇含量有关。
由于甲醇和碱性催化剂多溶解在极性甘油中,当甘油从生物柴油中分离出来时,大多数醇和催化剂也被去除。
残留在生物柴油中的甲醇很少,一般不会影响到燃料的性能,但低闪点存在潜在的安全隐患。
②含水量:水可以导致生物柴油氧化,和游离脂肪酸生成酸性溶液,促进燃料中微生物的生长,腐蚀金属,以及产生沉淀。
生物柴油中水以两种形式存在:溶解水和悬浮液滴,其中悬浮液滴影响较大,水在生物柴油中较易溶解,一般要求生物柴油中水分不大于500mg/kg。
③灰分含量:灰分可导致喷射器、燃烧泵、活塞的磨损以及滤网堵塞和发动机沉积。
灰分含量和生物柴油中残留催化剂有关。
欧美标准中都要求灰分含量不超过0.02%④甘油含量:甘油含量过高可导致喷射器沉积,阻塞供油系统,引起黑烟生成。
根据我国标准,使用GC检测(ASTMD6584)最终的生物柴油产品总甘油质量分数不能高于0.24%。
甘油本身不能溶解于生物柴油中,因此,绝大多数甘油通过沉淀或离心很容易被分离出来,只有很少量的游离甘油以悬浮液滴或微溶态的形式残留在生物柴油中。
煤基活性炭生产用斯列普活化炉生产工艺探讨
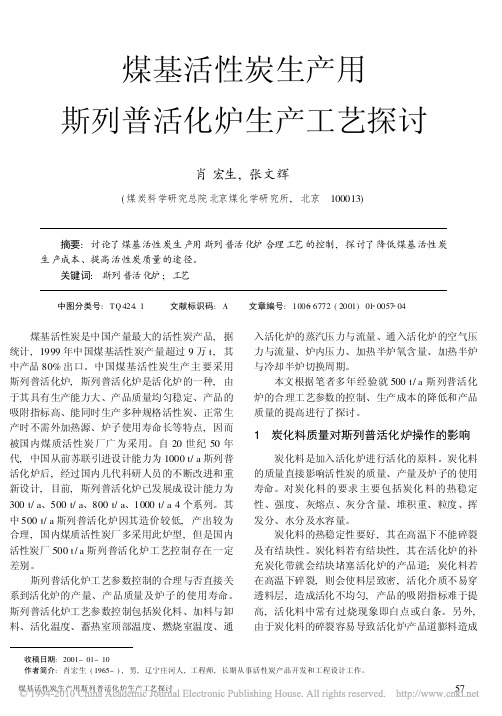
煤基活性炭生产用斯列普活化炉生产工艺探讨肖宏生,张文辉(煤炭科学研究总院北京煤化学研究所,北京 100013)摘要:讨论了煤基活性炭生产用斯列普活化炉合理工艺的控制,探讨了降低煤基活性炭生产成本、提高活性炭质量的途径。
关键词:斯列普活化炉;工艺中图分类号:T Q 424 1 文献标识码:A文章编号:1006 6772(2001)01 0057 04收稿日期:2001-01-10作者简介:肖宏生(1965-),男,辽宁庄河人,工程师,长期从事活性炭产品开发和工程设计工作。
煤基活性炭是中国产量最大的活性炭产品,据统计,1999年中国煤基活性炭产量超过9万t,其中产品80%出口。
中国煤基活性炭生产主要采用斯列普活化炉,斯列普活化炉是活化炉的一种,由于其具有生产能力大、产品质量均匀稳定、产品的吸附指标高、能同时生产多种规格活性炭、正常生产时不需外加热源、炉子使用寿命长等特点,因而被国内煤质活性炭厂广为采用。
自20世纪50年代,中国从前苏联引进设计能力为1000t/a 斯列普活化炉后,经过国内几代科研人员的不断改进和重新设计,目前,斯列普活化炉已发展成设计能力为300t/a 、500t/a 、800t/a 、1000t/a 4个系列。
其中500t/a 斯列普活化炉因其造价较低,产出较为合理,国内煤质活性炭厂多采用此炉型,但是国内活性炭厂500t/a 斯列普活化炉工艺控制存在一定差别。
斯列普活化炉工艺参数控制的合理与否直接关系到活化炉的产量、产品质量及炉子的使用寿命。
斯列普活化炉工艺参数控制包括炭化料、加料与卸料、活化温度、蓄热室顶部温度、燃烧室温度、通入活化炉的蒸汽压力与流量、通入活化炉的空气压力与流量、炉内压力、加热半炉氧含量、加热半炉与冷却半炉切换周期。
本文根据笔者多年经验就500t/a 斯列普活化炉的合理工艺参数的控制、生产成本的降低和产品质量的提高进行了探讨。
1 炭化料质量对斯列普活化炉操作的影响炭化料是加入活化炉进行活化的原料。
斯列普活化炉尾气回收利用及脱硫净化排放
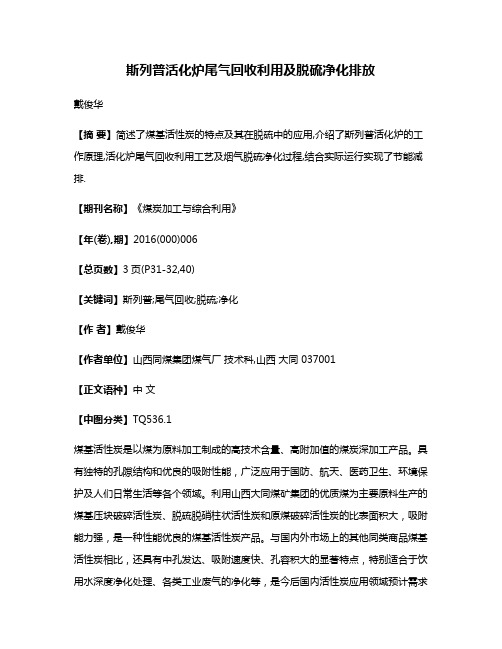
斯列普活化炉尾气回收利用及脱硫净化排放戴俊华【摘要】简述了煤基活性炭的特点及其在脱硫中的应用,介绍了斯列普活化炉的工作原理,活化炉尾气回收利用工艺及烟气脱硫净化过程,结合实际运行实现了节能减排.【期刊名称】《煤炭加工与综合利用》【年(卷),期】2016(000)006【总页数】3页(P31-32,40)【关键词】斯列普;尾气回收;脱硫;净化【作者】戴俊华【作者单位】山西同煤集团煤气厂技术科,山西大同 037001【正文语种】中文【中图分类】TQ536.1煤基活性炭是以煤为原料加工制成的高技术含量、高附加值的煤炭深加工产品。
具有独特的孔隙结构和优良的吸附性能,广泛应用于国防、航天、医药卫生、环境保护及人们日常生活等各个领域。
利用山西大同煤矿集团的优质煤为主要原料生产的煤基压块破碎活性炭、脱硫脱硝柱状活性炭和原煤破碎活性炭的比表面积大,吸附能力强,是一种性能优良的煤基活性炭产品。
与国内外市场上的其他同类商品煤基活性炭相比,还具有中孔发达、吸附速度快、孔容积大的显著特点,特别适合于饮用水深度净化处理、各类工业废气的净化等,是今后国内活性炭应用领域预计需求增长最快的活性炭产品品种,也是世界目前需求量最大,今后几年增长速度最快的活性炭产品品种,具有广阔的市场前景和很强的市场竞争力。
斯列普炉是我国于20世纪50年代从前苏联引进的活化设备,经过国内几代科研人员的不断改进和完善,工艺技术已非常成熟。
大同地区的活化炉由左右半炉和对应的左右蓄热室组成,每个半炉和对应的蓄热室之间由上连烟道相通,左右半炉之间由下连烟道(燃烧室)相连。
蓄热室底部是普异砖砌成的璇砖结构,上面摆放几十层格子砖用于过热蒸汽及蓄热。
若左半炉为冷却半炉,右半炉为加热半炉,则蒸汽从左蓄热室底部通入,然后在蓄热室内上升,与上部被炽热的格子砖进行热交换,使水蒸汽温度由130 ℃提高到1 000 ℃左右。
此时,水蒸气成为过热水蒸气,经左蓄热室顶部上连烟道进入左半炉炉体内;经上近烟道、上远烟道、中部烟道、下远烟道、下近烟道自上而下曲折运动。
斯列普活化炉生产过程控制系统的应用研究的开题报告

斯列普活化炉生产过程控制系统的应用研究的开题报告一、选题背景斯列普活化炉是一种将低活度放射性废物经过处理后,使其达到稳定、长期安全处置要求的设备。
在斯列普活化炉生产过程中,需要对其进行严格的控制,以保证生产过程的稳定性和安全性。
目前,斯列普活化炉生产过程控制系统的应用研究尚处于起步阶段,需要深入开展研究,探索如何有效地对斯列普活化炉生产过程进行控制,保障生产过程的稳定和安全。
二、选题意义斯列普活化炉生产过程控制系统的应用研究对于提高斯列普活化炉生产工艺的效率和质量,保障人员安全和防治环境污染具有重要的意义。
研究的成果可以为斯列普活化炉生产企业的高效、安全、环保生产提供技术支撑和参考,还能为相关科研机构和院校的教学和科研工作提供学术研究价值。
三、研究内容和方法本研究主要内容包括:1. 对斯列普活化炉生产过程的控制需求进行深入分析。
2. 研究斯列普活化炉生产过程中控制系统的基本原理和技术支持。
3. 设计和开发斯列普活化炉生产过程控制系统的软件和硬件。
4. 对斯列普活化炉生产过程控制系统进行测试和优化验证。
本研究采用的研究方法包括文献调研、实验分析、案例研究和数据分析等方法,通过深入研究斯列普活化炉生产过程,探索控制系统的设计原则和实现方法,最终对控制系统进行测试验证和优化,以达到提高斯列普活化炉生产效率、保障生产安全的目的。
四、预期成果通过本研究,预计可以得到以下成果:1. 对斯列普活化炉生产过程的控制需求有深入的了解。
2. 研发并实现斯列普活化炉生产过程的控制系统。
3. 掌握斯列普活化炉生产过程的控制原理和技术。
4. 提供斯列普活化炉生产过程控制系统的完整解决方案。
五、研究的难点和挑战斯列普活化炉生产过程控制系统的应用研究中存在创新性、复杂性和高风险性等多方面的难点和挑战:1. 研究控制系统的方案设计和基本原理时需要攻克技术难题。
2. 研发出的控制系统需要具有稳定的性能表现和高可靠性。
3. 研究控制系统需要考虑各种情况的复杂因素,包括安全性和环保等方面。
斯列普活化炉产品质量控制浅析

【 键 词 】 斯 列普 活化 炉 ; 关 产品 质 量 ; 制 控
【 中图分类号 】 F 7 . 【 23 2 文献标识码 】 A
I 文章编号】 l0 — 7 X 20 )l0 1— 2 0 3 7 3 l0 9O 一 16 0
设计 更加 合 理 . 国 内粒状 活性 炭 生 产 中得 到 广 泛 应 用 , 在 它具 有适 用 于各 种 炭 的 生产 , 活化 工 艺条 件 稳 定 , 产品 质 量 寿 命 长的 优 点 , 厂 的 斯 列普 炉运 行 将 至5 , 定 良好 , 激 烈 的 市 场 竞争 中发挥 质 量控 制优 势 , 我 年稳 在 生产 出优 质 低耗 的
F b2 ( e .0) 9
斯列普活化炉产品质量控制浅析
石 头 鲎
f 同煤 矿 集 团 有 限 责 任 公 司煤 气 厂 ,J 大 l 两 犬 同 J 0 7 0) 3 00
【 摘
要 】 我 国 的 活性 炭 工 业初 创 于2 0世 纪 5 0年 代 ,94年 我 国 从原 苏联 引进 斯 列 普 炉 , 入 9 年 代 , 炉 型 的 15 进 0 此
务于生 产 。
加 热 源 , 要 是靠 炭 化 料 中挥 发 份 逸 出 , 主 以及 活 化 反
应 产生 的 可燃 气体 的燃 烧来 提 供热 量 挥发 份低 , 产 品 的烧 失加 大 , 率 降 低 挥 发 份 高 , 造 成 产 品烧 效 会
结 , 塞产 品道 。 堵 4 )炭化 料反 应 性要 好 :炭化 料 的反 应性 也 叫 活
流 整 丁 活
如 下 : 化料 粒径 2 3nn 生 产 碘 吸附 值 l0 0 m / 炭 ~ l , l 0 g g 的 产品 , 产量 31炭 化料 粒 径 3 6i ]生 产 碘 吸 附值 : ~ n, c n
东北大学智慧树知到“能源与动力工程”《工业锅炉(录题)》网课测试题答案5

东北大学智慧树知到“能源与动力工程”《工业锅炉(录题)》网课测试题答案(图片大小可自由调整)第1卷一.综合考核(共15题)1.以下表示正确的是()。
A.Q2-有效利用热量B.Q2-排烟热损失C.Q3-固体未完全燃烧损失D.Q4-散热损失2.属于干背式锅炉的优点是什么?()A.结构简单B.制造方便C.结构复杂D.制造繁琐3.蒸汽中携带的杂质包括()。
A.气体杂质B.非气体杂质C.固体杂质D.液体杂质4.锅炉蒸发管内的流型主要分()。
A.泡状流B.弹状流C.环状流D.雾状流5.以下()属于煤。
A.无烟煤B.烟煤C.褐煤D.柴油6.砖砌烟道拱顶型式分为()。
A.大圆弧拱顶B.半圆弧拱顶C.小圆弧拱顶D.以上都不是7.单个颗粒的质量与其体积的比值称为()。
A.堆积密度B.颗粒密度C.堆积空隙率D.以上都不是8.冷凝式锅炉特点:()A.水蒸气释放汽化潜热B.降低排烟温度C.减小排烟热损失D.提高锅炉的热效率9.热风加热炉分为()。
A.直接混合型热风炉B.间接换热的换热设备C.蓄热式热风加热设备D.以上都是10.空气干燥基的用途:()A.确定煤中的真实水分B.反映煤的燃烧特性C.确定煤中的真实灰分D.锅炉的设计计算和运行11.大型电站锅炉的对流受热面是指对流换热为主的()。
A.对流过热器和再热器B.省煤器和空气预热器C.直流锅炉过渡区D.辐射份额较大的屏式受热面12.弹性变形的极限点称为弹性极限。
()A.正确B.错误13.如果完全由三原子气体组成的火焰肉眼是看不见的,称之为“发光火焰”。
()A.正确B.错误14.原则上锅炉负荷减小时应先()。
A.减少引风量B.减少送风量C.减少燃料量D.减少给水量15.下列()属于燃料层不移动的固定火床炉。
A.抛煤机炉B.倾斜推饲炉C.振动炉排炉D.链条炉第2卷一.综合考核(共15题)1.无烟煤和烟煤相比,其qV值应取小些,截面热负荷qF应取()。
A.大些B.小些C.相同D.以上都不是2.床料或物料流化时动力流体的速度称为临界流化风速。
斯列普炉活性炭制造控制系统的研究与改进

斯列普炉活性炭制造控制系统的研究与改进
王振;虎恩典;单壮;兰永平;王大鹏
【期刊名称】《工业控制计算机》
【年(卷),期】2024(37)4
【摘要】对斯列普活化炉原理及其工作流程进行了基本介绍。
利用西门子S7-200 SMART系列PLC实现了对斯列普活化炉的换火和卸料工序的逻辑和定时控制,并通过以太网与上位机触摸屏进行通信。
与传统的斯列普活化炉控制系统相比,对温度和压力采集模块进行了技术上的改进,将原来的使用S7-200 SMART模拟量输入模组采集数据的方法改为利用数据采集卡采集温度和压力,并通过RS 485总线将数据传送到上位机触摸屏上,进行数据的显示。
对换火程序进行改进,使得换火动作在外部检测元件发生故障时仍能继续执行。
该系统具有控制性能可靠、可视性好等优点,与传统的控制系统相比,在保证产品质量的前提下,可以大大降低生产成本。
【总页数】3页(P38-40)
【作者】王振;虎恩典;单壮;兰永平;王大鹏
【作者单位】北方民族大学电气信息工程学院
【正文语种】中文
【中图分类】TP2
【相关文献】
1.煤基活性炭生产用斯列普活化炉生产工艺探讨
2.斯列普活化炉的改进
3.对斯列普活化炉蒸汽入炉及前后挡板密封方式的研究
4.一种利用斯列普活化炉尾气加热烘干炉的方法
5.斯列普活化炉尾气余热利用技术研究与应用
因版权原因,仅展示原文概要,查看原文内容请购买。
一段与两段UOP工艺技术的加氢裂化装置异同点比较
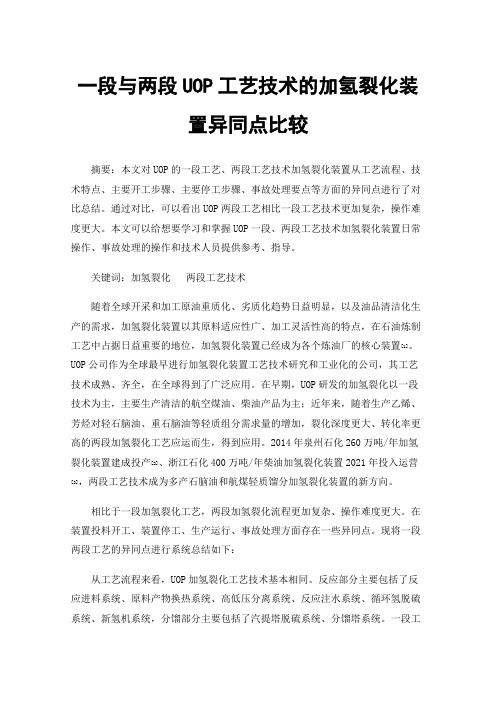
一段与两段UOP工艺技术的加氢裂化装置异同点比较摘要:本文对UOP的一段工艺、两段工艺技术加氢裂化装置从工艺流程、技术特点、主要开工步骤、主要停工步骤、事故处理要点等方面的异同点进行了对比总结。
通过对比,可以看出UOP两段工艺相比一段工艺技术更加复杂,操作难度更大。
本文可以给想要学习和掌握UOP一段、两段工艺技术加氢裂化装置日常操作、事故处理的操作和技术人员提供参考、指导。
关键词:加氢裂化两段工艺技术随着全球开采和加工原油重质化、劣质化趋势日益明显,以及油品清洁化生产的需求,加氢裂化装置以其原料适应性广、加工灵活性高的特点,在石油炼制工艺中占据日益重要的地位,加氢裂化装置已经成为各个炼油厂的核心装置[1]。
UOP公司作为全球最早进行加氢裂化装置工艺技术研究和工业化的公司,其工艺技术成熟、齐全,在全球得到了广泛应用。
在早期,UOP研发的加氢裂化以一段技术为主,主要生产清洁的航空煤油、柴油产品为主;近年来,随着生产乙烯、芳烃对轻石脑油、重石脑油等轻质组分需求量的增加,裂化深度更大、转化率更高的两段加氢裂化工艺应运而生,得到应用。
2014年泉州石化260万吨/年加氢裂化装置建成投产[2]、浙江石化400万吨/年柴油加氢裂化装置2021年投入运营[3],两段工艺技术成为多产石脑油和航煤轻质馏分加氢裂化装置的新方向。
相比于一段加氢裂化工艺,两段加氢裂化流程更加复杂、操作难度更大。
在装置投料开工、装置停工、生产运行、事故处理方面存在一些异同点。
现将一段两段工艺的异同点进行系统总结如下:从工艺流程来看,UOP加氢裂化工艺技术基本相同。
反应部分主要包括了反应进料系统、原料产物换热系统、高低压分离系统、反应注水系统、循环氢脱硫系统、新氢机系统,分馏部分主要包括了汽提塔脱硫系统、分馏塔系统。
一段工艺主要流程:原料经过反应进料泵升压后和循环氢进入高压换热器与反应产物换热再进入反应加热炉进一步升温,进入反应器进行精制和裂化反应,反应产物流经高压换热器换热降温后进入高低压分离器进行油气分离,油相进入分馏系统分馏切割成石脑油、航煤、柴油、尾油组分。
斯列普活化炉的改进

斯列普活化炉的改进
严国辉
【期刊名称】《煤炭加工与综合利用》
【年(卷),期】2003(000)002
【摘要】针对目前广泛应用的斯列普活化炉的结构特点,根据多年的实践经验,从炉芯砖结构、炉体结构、砌筑方式、混合气体流程等方面对斯列普活化炉进行了改进.改进后的斯列普活化炉产量大幅度提高,活性炭产品质量稳定,取得了极好的经济效益.
【总页数】2页(P32-33)
【作者】严国辉
【作者单位】宁夏煤业集团有限责任公司,项目管理部,宁夏,银川,750000
【正文语种】中文
【中图分类】TQ424.1
【相关文献】
1.斯列普活化炉尾气回收利用及脱硫净化排放 [J], 戴俊华
2.对斯列普活化炉蒸汽入炉及前后挡板密封方式的研究 [J], 韩锡政
3.斯列普式活化炉活化工艺探讨 [J], 刘泽
4.一种利用斯列普活化炉尾气加热烘干炉的方法 [J], 王晖
5.斯列普活化炉尾气的回收利用 [J], 张俊龙
因版权原因,仅展示原文概要,查看原文内容请购买。
斯列普活化炉使用流程

斯列普活化炉使用流程 The manuscript was revised on the evening of 2021斯列普活化炉使用流程物料流程:物料进入加料槽后,借重力作用沿着产品道缓慢下行,依次经过预热带、补充炭化带、活化带、冷却带,完成全部活化过程,最后由下部卸料器卸出。
炭化预热段利用炉内热量预热除去水分。
在补充炭化段,炭化料被高温活化气体间接加热使炭的温度不断提高进行补充炭化。
在活化段,活化道与活化气体道垂直方向相通,炭与活化气体直接接触进行活化。
在冷却段,用循环水对活化料进行冷却(或采用风冷),这样所得到的活化料温度可以降到60℃以下,便于物料运输和直接进行筛分包装。
气体流程:是左半炉烟道闸阀关闭,右半炉烟道闸阀开启,水蒸汽从左半炉蓄热室底部进入,经格子砖加热到变成高温蒸汽,从上连烟道进入,蒸汽与物料反应后产生的水煤气与残余蒸汽依次经过左半炉上、中下烟道进入右半炉。
在右半炉内混合气体经过下、中部及上烟道及上连烟道进入右半炉蓄热室顶部,然后通过格子砖往下流动,同时加热格子砖,尾气冷却,进入烟道排出完成循环。
第二次循环与上述循环相反。
第一、二次循环每半小时切换一次,从而使活化过程连续不断地进行。
工艺标准(1)加料时间间隔8小时,为保证活化炉安全,入炉料各项指标必须合格,每次须将加产品道内料槽加满耙平,料层下沉深度不得超过60厘米,加料后将水封槽注满水。
(2)出料时间间隔:根据下达的生产指标调整。
(3)工艺温度:1—10点: 930℃—950℃11—12点: 920℃—930℃(4)蓄热室温度:顶部950℃—1050℃,底部300℃—400℃。
(5)进炉蒸汽压力:336型炉大于cm2,588型炉大于 kg/cm2。
(6)进炉蒸汽流量:336型炉大于1500kg/h, 588型炉大于3000 kg/h。
(7)进炉空气压力:300-700Pa。
(8)炉内压力:冷却半炉:70-100Pa,加热半炉50-70Pa。
- 1、下载文档前请自行甄别文档内容的完整性,平台不提供额外的编辑、内容补充、找答案等附加服务。
- 2、"仅部分预览"的文档,不可在线预览部分如存在完整性等问题,可反馈申请退款(可完整预览的文档不适用该条件!)。
- 3、如文档侵犯您的权益,请联系客服反馈,我们会尽快为您处理(人工客服工作时间:9:00-18:30)。
多段炉与斯列普炉活化装置系统综合比较吉建斌康德朗(尚鼎炉业科技(扬州)有限公司,扬州市邗江开发区)摘要:本文试图根据实际经验及文献数据对煤基颗粒活性炭制造业常见的两种活化装置——多段炉及斯列普炉——及其技术系统进行全面的应用性能及应用效果比较。
进入综合比较范围的两种活化炉装置系统均涵盖活化设备本体、蒸汽生产设备、尾气处理装置及其他的必要、主要附属设备等。
涉及的工艺物料包括炭化料、水蒸气活化剂、一次风及二次风、燃料、尾气和/或烟气、活化料等。
重点比较的项目包括设备结构及运行原理、工艺特点及生产效率、关键性工艺参数等。
通过综合比较和分析之后即可知悉多段炉活化装置系统成为发达国家活性炭制造业主流炉型的根本原因。
关键词:煤基颗粒活性炭,多段炉,斯列普炉,活化前言煤基颗粒活性炭制造业使用的活化设备有斯列普炉、多段炉(耙式炉)、转炉、管式炉、流化床炉等类型,以前两种最为常见。
东亚地区的煤基活性炭厂多采用斯列普活化炉,而欧洲和美洲的煤基活性炭厂则习惯采用多段炉活化装置。
图1为两种炉型的现场照片。
(a) 多段炉活化装置(由BSP Thermal Systems, Inc.提供)(b) 斯列普炉活化装置图1. 多段炉与斯列普炉装置系统的外观斯列普活化炉装置于1950年代被引入我国活性炭制造业,经过40多年的发展,目前仍为我国煤基活性炭制造业的主力生产装置类型。
斯列普炉多按设计年产能力进行细分(在宁夏产区则多按设计产能炉型对应的产品道总数量来细分),常见的有300吨炉、500吨炉、1000吨炉型,近年新开发了2000吨和3000吨炉型,最常用的是1000吨/年产能(产品道总数为576)的斯列普活化炉(下文中简写为SLIP)。
多段炉(Multiple Hearth Furnace,简称MHF)在我国活性炭制造业多被称为“耙式炉”,这种工业炉装置最早是由美国的Nichols公司设计制造的。
Nichols公司于1939年设计了第一台外径0.9米、层数为10层的MHF设备,应用于Freeport硫磺公司的实验室研究;同年设计建造了一台外径达6.78米、16层的MHF用于处理铁矾土和赤铁矿,产能为每天4000吨。
之后,外形尺寸为1.4×10、6.78×17、2.59×12和7.85×17(均为“外径尺寸×层数”)的MHF相继投入使用。
从1950年始,MHF开始用于活性炭行业,最早是用于木炭制造,其后用于煤基颗粒活性炭生产,后来发展成为欧美国家活性炭制造和再生的主力炉型之一。
经过60多年发展之后,煤基活性炭制造用的MHF装置已实现标准化和系列化,适用的规模生产的常见炉型按照最大外径尺寸顺序依次为2.5米,2.8米,3.9米,4.8米,5.1米,5.7米,6.5米,和7.8米共8种,可用于实验室试验用的炉型有外径1.1米,1.4米,1.8米和2.1米四种炉型。
其中的5.1米和6.5米外径炉型在煤基活性炭制造业最为常见,而7.8米炉型在新兴国家是最受欢迎的型号。
我国活性炭制造业最早于1980年代引进一台外径较小的MHF装置,之后于2001年由大同市三星力源炭素有限公司引进一套外径7.8米、10层结构的MHF装置用来炭化并活化加工原煤直接破碎活性炭产品。
目前上述两套装置因各种原因已停用。
目前已建成并将于今年试生产的MHF活化装置系统是由神华新疆能源有限责任公司于2009年引进、2011年建成的两套同型号MHF装置系统,单台装置的外径为7.8米、17层结构,总设计能力为年产2万吨煤基压块颗粒活性炭产品。
1. MHF与SLIP活化装置的结构特点及运行原理1.1 MHF装置的结构特点及运行原理如图2所示,MHF装置本体是由钢质外壳及耐火材料衬层、耐火砖砌筑的球面形自支撑结构的炉床层及落料孔、物料“搅拌”机构(中轴、耙臂、耙齿及电机驱动单元部件等)、燃烧机、附属的管线及仪器仪表和传感器等构件组成。
(a) 剖面示意图(Industrial Furnace Company, Inc.供)(b) 立体布置图(CMI NESA供)(c) 结构及运行机制示意图(尚鼎炉业科技)图2. 多段炉结构及运行原理示意图MHF是由几个至十几个在水平方向平行叠加的球面形炉床组成,在顶端炉层接受给入的固体原料。
带有耙齿的耙臂在每一炉床耙动固体原料,从外向内按照螺旋形路径推动固体料(称为“内耙炉床”),从设置在近中心处的落料孔掉落到下一炉床。
在相邻设置的下一层炉床,耙臂按照螺旋形路径从内向外推动固体料到炉壁(称为“外耙炉床”),通过设置在近炉壁位置的一系列落料孔落入下一层炉床。
固体物料以这种方式不断向多段炉的下方运动,最终从最底层炉床中排出。
由空气冷却的中心轴在炉底设置的电机、减速机、伞形齿轮的驱动下带动轴上固定安装的耙臂(一般每层安装四支耙臂)以0.5至3.0rpm转速回转,耙臂每隔一段间距即安装一只垂直向下的耙齿,并与耙臂成一定角度,以使耙齿按照螺旋形路径耙动固体料,使固体物料在炉床上移动并通过所有炉床。
在这一过程中,固体物料通过耙齿的连续搅动和扰动,其料层的表面被不断地“更新”并与气相进行接触。
由燃料燃烧或炉内化学反应产生的高温气体则以逆向流动的方式向上流动到各炉膛上部,最终从顶层炉膛流出、进入后继的尾气处理/热能回收利用技术系统。
概括地说,多段炉是这样的一种设备:它通过热量和质量的传递(即气体和固体之间的热传递),使气体和固体呈逆向通过一系列的炉床结构;在每一层炉床上,气体以错流、逆流等流动方式在折皱的薄层固体上流动并向固体物料的内表面扩散,这些薄层固体周期性地被中轴、耙臂和耙齿组成的搅拌机构所搅动,以使固体不停地混合、摊开,并使其强制进入下一层炉床继续反应,直至达到设定的停留时间为止。
采用水蒸气为活化剂的煤基活性炭MHF活化装置系统的工艺流程见图3。
温度低于300℃(若采用耐热钢材质的炭化料输送及给料装置且不产生安全问题时,允许进一步提高炭化料的进炉温度)的炭化料用螺旋给料机和气密加料阀连续加入最高一层炉膛(第一层炉床),炭化料被从下方炉床流动过来的高温气体加热至800℃以上,从第二层炉床开始,每层均加设有两台或三台燃烧机和蒸汽喷嘴、二次风喷嘴,炉膛温度被精确控制在预设的活化温度±(5∼10)℃范围内并开始进行活化,最底层炉床不加设燃烧机和二次风喷嘴,为冷却床层。
活化时间通过中轴转速进行调节。
从MHF装置中连续卸出的活化料进入强制夹套式冷却机(冷媒为水),设计合理时从强制冷却机卸出的活化料温度可低于50℃,允许直接进入后继的筛选包装工序。
碳与水蒸气反应后生成的可燃气体成分与二次风(中轴冷却产生的热风回用为二次风及一次风)含有的氧在炉膛空间内发生部分“层燃”以补充活化过程所需的部分热能,过量加入的水蒸气及未燃的反应生成气体(以一氧化碳和氢气为主)、不参与反应的氮气成分、燃烧后产生的二氧化碳和水蒸气等混合气流通过炉床的落料孔向上流动,在第一层炉床与炭化料受热逸出的气相有机物、和少量在炭化料表面粘附的、在第一层炉床内即脱落进入气相的固体粉尘、以及在活化过程中因机械磨耗产生的固体粉尘物完全混合后由尾气排出口及排放管离开MHF本体,进入后燃室。
在正常运行状态下,燃烧机仅消耗少量燃料(燃油或燃气)即可维持炉温。
同时,通过在线监控系统自动控制炉内的剩余氧含量不超过0.5∼1.0%。
后燃室中设置一台燃烧机,并使用中轴冷却产生的热风做助燃空气(一次风),设计足够的尾气停留时间(1.5∼2秒钟),使活化尾气中的可燃物质如一氧化碳、氢气、有机挥发物、碳质粉尘等彻底氧化,产生的高温烟气(温度高达950至1200℃)离开后燃室后进入余热回收蒸汽锅炉装置系统生产活化炉所需的工艺过热蒸汽,当MHF被用于制造烟煤基、褐煤基和无烟煤基颗粒活性炭产品时,MHF装置系统余热回收生产的过热蒸汽仅有1/3能被活化过程消耗,其余的2/3可用来发电或做为生产线其他装置所需的工艺蒸汽原料使用。
经过余热锅炉之后,烟气温度下降至150℃以内,可根据原煤含硫的情况决定是否设置脱硫装置,若需要设置的话,可采用洗气器进行脱硫并除尘,之后的烟气由烟囱排空。
图3. 煤基活性炭的MHF蒸汽活化装置系统工艺流程图(Hankin Environmental Systems, Inc.提供)1.2 SLIP炉的结构特点及运行原理SLIP活化炉属于竖式工业炉的一种,几乎全部使用各种形状的耐火砖和耐火材料进行砌筑,仅在外围构件中使用少量金属器件。
其结构示意图见图4。
1-产品道2-冷却带3-鞍形耐火砖4-下远烟道5-红砖墙6-烟道盖板7-硅酸铝纤维毡8-标准耐火砖9-加料槽10-水封11-上远烟道12-补充炭化带13-上连烟道口14-上近烟道15-中部烟道16-下连烟道17-下近烟道18-活化带图4. SLIP活化炉结构示意图(1)SLIP活化炉从上到下分为四个功能区段,即加热段、炭化段、燃烧室和冷却段。
1000吨级(通称)SLIP炉各个功能区段的尺寸和操作温度分别为:预热带高度为1650mm(利用炉子的辐射热和传导热,炭化料温度由常温缓慢升至约550℃);补充炭化带高度860mm(利用高温蒸汽或烟道气的间接加热,炭化料温度由550℃升高到约850℃,停留时间约6小时);活化带高3900mm(灼热的炭与高温水蒸汽或高温烟道气直接接触,温度控制在880~960℃,停留时间约30小时);冷却带高800mm(利用炉壁散热使灼热的炭自然冷却至300℃以下,停留时间约5小时)。
在每台SLIP炉内正中间位置用644mm或348mm耐火砖墙将炉子分成左右两半炉,两半炉靠下连烟道连通,上部由两个上连烟道分别与左右蓄热室连通。
SLIP炉由总计17种异形耐火砖砌筑炉芯,以形成符合设计预定尺寸的产品道和气道。
水封槽砌成八个独立的料槽,理论上一台SLIP活化炉可同时生产八种不同尺寸规格的产品(在生产实践中,一台炉子极少被同时用来生产超过两种以上尺寸规格的活化料)。
炉芯与前后炉墙之间各有一侧烟道,侧烟道又被烟道盖板分隔成上下部分,从上到下形成——上近、上远、中部、下远、下近烟道。
在上远、中部、下远烟道内均设有空气格栅入口以便从外部通入适量均匀的空气燃烧放热。
连接两半炉的下连烟道顶部也设计有进风口以保证两个下近烟道的温度。
经蓄热室的两上连烟道各设计有均布的进风口,保证加热时提高炉气温度,以便于排出烟气时回收更多的热量。
蓄热室是SLIP炉的节能和第一级环保装置,也是该炉设计的特点和要点之一,它可充分利用排气中热能,使炉子本身达到热平衡状态,并使活化用的水蒸汽从加入时的130∼150℃提高到1000∼1100℃,加强了活化作用。
炉内助燃用的空气由送风机和空气管输入,空气量通过蝶阀和插板调节。