用于发动机生产的切削液冷却过滤研究
一种机床用冷却液过滤装置改进设计
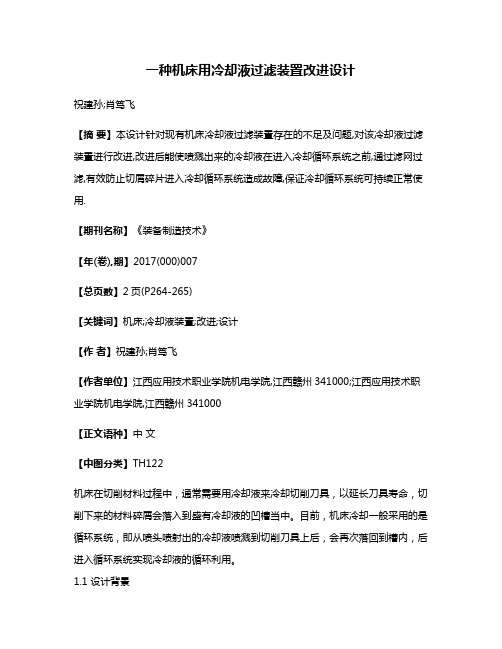
一种机床用冷却液过滤装置改进设计祝建孙;肖笃飞【摘要】本设计针对现有机床冷却液过滤装置存在的不足及问题,对该冷却液过滤装置进行改进,改进后能使喷溅出来的冷却液在进入冷却循环系统之前,通过滤网过滤,有效防止切屑碎片进入冷却循环系统造成故障,保证冷却循环系统可持续正常使用.【期刊名称】《装备制造技术》【年(卷),期】2017(000)007【总页数】2页(P264-265)【关键词】机床;冷却液装置;改进;设计【作者】祝建孙;肖笃飞【作者单位】江西应用技术职业学院机电学院,江西赣州341000;江西应用技术职业学院机电学院,江西赣州341000【正文语种】中文【中图分类】TH122机床在切削材料过程中,通常需要用冷却液来冷却切削刀具,以延长刀具寿命,切削下来的材料碎屑会落入到盛有冷却液的凹槽当中。
目前,机床冷却一般采用的是循环系统,即从喷头喷射出的冷却液喷溅到切削刀具上后,会再次落回到槽内,后进入循环系统实现冷却液的循环利用。
1.1 设计背景机床冷却液在循环利用的过程中,部分细小的切削材料碎屑易随冷却液进入到循环系统中,而造成冷却循环系统的堵塞。
本文改进设计针对机床切削材料碎屑易随冷却液进入循环系统,造成系统堵塞这一问题,设计出了一种新的机床冷却液过滤装置,使其能有效防止切屑碎片堵塞冷却循环系统,避免冷却循环系统陷入故障影响机床使用。
1.2 冷却液过滤装置的结构设计过滤装置结构如图1所示,其中,包括一腔体1,其底部为一斜面结构2,该斜面结构2一侧设有可使腔体1保持和地面水平的支脚3;在腔体1上端通过一个和腔体1内部相连通的第一凹槽4卡接有一铺设有过滤网5的套筒6,在套筒6上通过一长杆9连接有一手柄10;第一凹槽4一侧设有和腔体1内部相连通的第二凹槽7,在第二凹槽7上卡设有弹性固定圈8.本文提供的机床冷却液过滤装置设计方案中(见图1),包括一腔体,所述腔体底部为斜面结构,且斜面一侧设有可使腔体保持和水平地面的支脚;腔体上端通过一个和腔体内部相连通的第一凹槽卡接有一个铺设了过滤网的套筒;套筒上通过一长杆连接有一手柄。
常见切削液过滤系统的形式
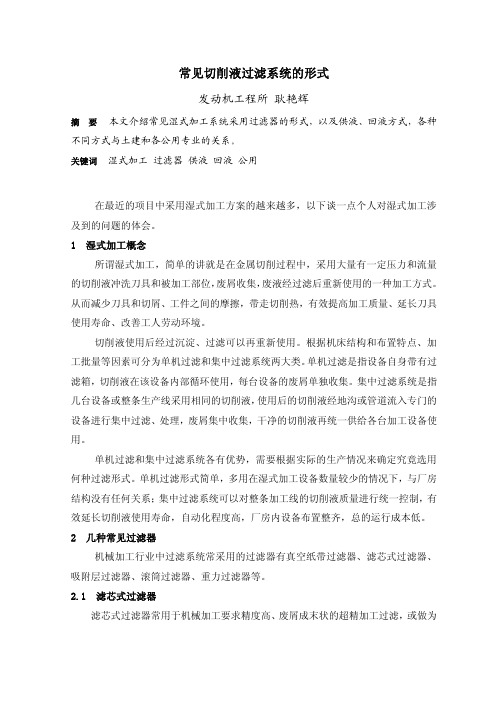
常见切削液过滤系统的形式发动机工程所 耿艳辉摘 要本文介绍常见湿式加工系统采用过滤器的形式,以及供液、回液方式,各种不同方式与土建和各公用专业的关系。
关键词 湿式加工 过滤器 供液 回液 公用在最近的项目中采用湿式加工方案的越来越多,以下谈一点个人对湿式加工涉及到的问题的体会。
1 湿式加工概念所谓湿式加工,简单的讲就是在金属切削过程中,采用大量有一定压力和流量的切削液冲洗刀具和被加工部位,废屑收集,废液经过滤后重新使用的一种加工方式。
从而减少刀具和切屑、工件之间的摩擦,带走切削热,有效提高加工质量、延长刀具使用寿命、改善工人劳动环境。
切削液使用后经过沉淀、过滤可以再重新使用。
根据机床结构和布置特点、加工批量等因素可分为单机过滤和集中过滤系统两大类。
单机过滤是指设备自身带有过滤箱,切削液在该设备内部循环使用,每台设备的废屑单独收集。
集中过滤系统是指几台设备或整条生产线采用相同的切削液,使用后的切削液经地沟或管道流入专门的设备进行集中过滤、处理,废屑集中收集,干净的切削液再统一供给各台加工设备使用。
单机过滤和集中过滤系统各有优势,需要根据实际的生产情况来确定究竟选用何种过滤形式。
单机过滤形式简单,多用在湿式加工设备数量较少的情况下,与厂房结构没有任何关系;集中过滤系统可以对整条加工线的切削液质量进行统一控制,有效延长切削液使用寿命,自动化程度高,厂房内设备布置整齐,总的运行成本低。
2 几种常见过滤器机械加工行业中过滤系统常采用的过滤器有真空纸带过滤器、滤芯式过滤器、吸附层过滤器、滚筒过滤器、重力过滤器等。
2.1 滤芯式过滤器滤芯式过滤器常用于机械加工要求精度高、废屑成末状的超精加工过滤,或做为二级过滤提高过滤精度时使用。
过滤精度1至3μ,单个滤芯的过滤能力为0.8l/min。
废液从滤芯外表面进入,杂质被隔离在滤芯表面,杂质越积越厚,当滤芯无法正常工作时,从滤芯内部向外吹压缩空气,清除杂质,重新开始过滤。
一种机床切削冷却液的循环制冷过滤系统[发明专利]
![一种机床切削冷却液的循环制冷过滤系统[发明专利]](https://img.taocdn.com/s3/m/fd4bc0e56c85ec3a86c2c566.png)
专利名称:一种机床切削冷却液的循环制冷过滤系统专利类型:发明专利
发明人:李依然
申请号:CN202011309673.7
申请日:20201120
公开号:CN112548670A
公开日:
20210326
专利内容由知识产权出版社提供
摘要:本发明公开了一种机床切削冷却液的循环制冷过滤系统,属于机床领域,本发明在切削冷却液输出过程中,通过制冷滤球与切削冷却液形成反向对流,相互接触,不仅与冷却液进行换热过程,实现对冷却液的降温处理,同时在对流过程中,制冷滤球还对冷却液中的切削碎屑进行了过滤吸附处理,切削碎屑被截留在制冷滤球内部,并且,随着换热过程的进行,制冷滤球的温度逐渐升高,其内部发生形变,一方面对已吸附的切削碎屑实现了压缩控制,减少切削碎屑的再次流失,另一方面扩大了切削液流动通道,使切削液顺利流动,方便制冷滤球进行回收,进行切削碎屑清理和再次制冷处理,通过制冷滤球的循环回流,实现了对切削冷却液的持续降温和过滤处理。
申请人:李依然
地址:400900 重庆市大足区三驱镇双吉村2组12号
国籍:CN
更多信息请下载全文后查看。
切削液的过滤
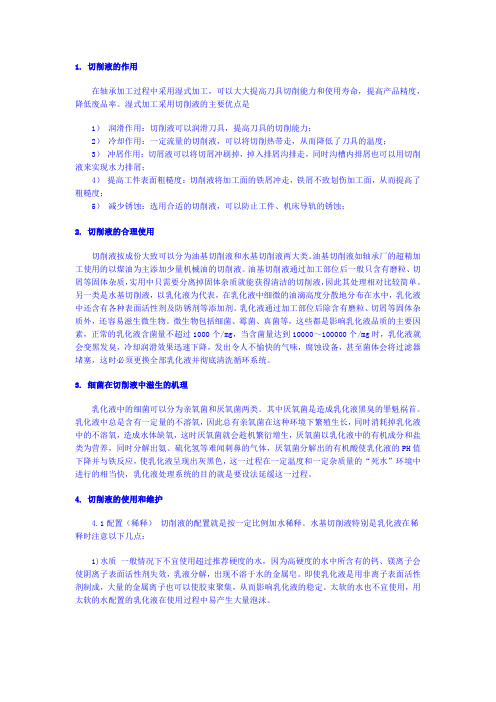
1. 切削液的作用在轴承加工过程中采用湿式加工,可以大大提高刀具切削能力和使用寿命,提高产品精度,降低废品率。
湿式加工采用切削液的主要优点是1)润滑作用:切削液可以润滑刀具,提高刀具的切削能力;2)冷却作用:一定流量的切削液,可以将切削热带走,从而降低了刀具的温度;3)冲屑作用:切屑液可以将切屑冲刷掉,掉入排屑沟排走,同时沟槽内排屑也可以用切削液来实现水力排屑;4)提高工件表面粗糙度:切削液将加工面的铁屑冲走,铁屑不致划伤加工面,从而提高了粗糙度;5)减少锈蚀:选用合适的切削液,可以防止工件、机床导轨的锈蚀;2. 切削液的合理使用切削液按成份大致可以分为油基切削液和水基切削液两大类。
油基切削液如轴承厂的超精加工使用的以煤油为主添加少量机械油的切削液。
油基切削液通过加工部位后一般只含有磨粒、切屑等固体杂质,实用中只需要分离掉固体杂质就能获得清洁的切削液,因此其处理相对比较简单。
另一类是水基切削液,以乳化液为代表,在乳化液中细微的油滴高度分散地分布在水中,乳化液中还含有各种表面活性剂及防锈剂等添加剂。
乳化液通过加工部位后除含有磨粒、切屑等固体杂质外,还容易滋生微生物。
微生物包括细菌、霉菌、真菌等,这些都是影响乳化液品质的主要因素,正常的乳化液含菌量不超过1000个/mg,当含菌量达到10000~100000个/mg时,乳化液就会变黑发臭,冷却润滑效果迅速下降,发出令人不愉快的气味,腐蚀设备,甚至菌体会将过滤器堵塞,这时必须更换全部乳化液并彻底清洗循环系统。
3. 细菌在切削液中滋生的机理乳化液中的细菌可以分为亲氧菌和厌氧菌两类。
其中厌氧菌是造成乳化液黑臭的罪魁祸首。
乳化液中总是含有一定量的不溶氧,因此总有亲氧菌在这种环境下繁殖生长,同时消耗掉乳化液中的不溶氧,造成水体缺氧,这时厌氧菌就会趁机繁衍增生,厌氧菌以乳化液中的有机成分和盐类为营养,同时分解出氨、硫化氢等难闻刺鼻的气体,厌氧菌分解出的有机酸使乳化液的PH值下降并与铁反应,使乳化液呈现出灰黑色,这一过程在一定温度和一定杂质量的“死水”环境中进行的相当快,乳化液处理系统的目的就是要设法延缓这一过程。
一种机械加工用冷却液过滤装置[发明专利]
![一种机械加工用冷却液过滤装置[发明专利]](https://img.taocdn.com/s3/m/f313ea8d27d3240c8547ef4a.png)
专利名称:一种机械加工用冷却液过滤装置专利类型:发明专利
发明人:杨晓成
申请号:CN202010980769.X
申请日:20200917
公开号:CN112090146A
公开日:
20201218
专利内容由知识产权出版社提供
摘要:本发明属于机械加工技术领域,尤其是一种机械加工用冷却液过滤装置,针对滤网过滤进行简单处理,清洗过滤的效果一般,无法达到重复利用的清洁度要求问题,现提出以下方案,包括箱体,所述箱体底部外壁固定连接有多个支脚,所述支脚底部固定连接有减震胶垫,所述箱体顶部固定连接有进液管,所述箱体内部设置有离心仓,所述离心仓设置为圆柱状。
本发明中,通过设置电机转动转动轴,带动转动轴顶部的离心仓转动,从而使从进液管进入到离心仓内的冷却液进行转动离心运动,通过设置半径依次减小的导流块对冷却液进行分流,使冷却液均匀被过滤板上离心过滤,实现了冷却液高效多级处理的工作机理,使装置具有很高的工作效率。
申请人:杨晓成
地址:310027 浙江省杭州市浙大路38号浙江大学机械工程学院
国籍:CN
更多信息请下载全文后查看。
一种机械加工用冷却液过滤装置[实用新型专利]
![一种机械加工用冷却液过滤装置[实用新型专利]](https://img.taocdn.com/s3/m/a9d4ae2e5fbfc77da369b121.png)
专利名称:一种机械加工用冷却液过滤装置专利类型:实用新型专利
发明人:何君怡
申请号:CN201820620042.9
申请日:20180427
公开号:CN208260329U
公开日:
20181221
专利内容由知识产权出版社提供
摘要:本实用新型公开了一种机械加工用冷却液过滤装置,包括保护壳、过滤箱、离心筒、定时开关,所述保护壳的底部设置有支撑腿,所述保护壳的前方安装有所述定时开关,所述定时开关的侧面设置有按钮,所述保护壳的侧面设置有收集箱,所述保护壳的内部设置有所述过滤箱,所述过滤箱的上方设置有漏网,所述漏网的侧面安装有马达,所述漏网的下面设置有过滤板,所述过滤箱的侧面设置有出水管道。
有益效果在于:本实用新型通过多次过滤提高了冷却液的回收效率,过滤的杂质进行回收处理,更加环保高效,避免了对环境的污染,提高了设备的实用性,进而降低了机械零件的生产成本。
申请人:连江极智工业设计有限公司
地址:350500 福建省福州市连江县凤城镇丹凤东路15号丹凤花园15#704
国籍:CN
更多信息请下载全文后查看。
用于发动机生产的切削液冷却过滤研究

用于发动机生产的切削液冷却过滤研究动力总成的生产往往由大量金属切削机床组成,如发动机缸体、缸盖、变速箱壳体等,此类零件的加工大多选用湿式加工,即加工过程中需要使用切削液进行冷却。
切削液和切屑是机加工车间的主要污染源之一,减少切削液用量并妥善处理,不仅是目前流行的清洁生产的需要,同时也是节能减排、降本增效的必然选择。
汽车生产是大批量生产模式的典型代表,动力总成车间加工中心密集、节拍快,要求使用高效的冷却过滤处理系统,同时毛坯材料较单一(多为铸铝、铸铁材质),为切削液统一集中处理提供了可能性。
集中冷却过滤系统高效节能环保,正在被国内外车企越来越广泛地采用,如何正确使用以发挥其最大效能就显得迫在眉睫。
本文以加工中心中使用的切削液为例,重点研究切削液的处理方式。
切削液与处理方式1.切削液的作用切削液分为切削油和水溶性切削液两大类,水溶性切削液又分为全合成、半合成和乳化型三小类,加工中心一般使用乳化型的水溶性切削液。
金属加工中切削液主要起冷却、润滑排屑、防锈和清洗的作用,金属切削时由于金属变形和摩擦,产生大量的热量,如不及时将热量带走将导致热量积聚在刀具上,影响刀具切削性能。
切削时同时产生大量切屑,如不及时将切屑从切削区移开,将划伤加工表面,甚至导致刀具粘结,因此需要带屑清洗。
铁件周围存在大量水汽,在局部高温的作用下,工件极易生锈,此时切削液还起到防锈的作用。
2.切削液过滤物化指标由于切削液关乎加工质量和稳定性、刀具寿命,因此经净化后的切削液需要实时监测,满足要求后才能继续使用。
对过滤后的净液监测项很多,主要有浓度、pH值、过滤精度等,具体参数见表1。
3.处理方式切削液过滤形式分为四大类:沉淀过滤、缝隙过滤、离心过滤和磁性过滤,加工中心一般使用缝隙过滤和离心过滤两种方式,其原理如图1所示。
其中缝隙过滤的使用介质种类有许多种,常见过滤介质有滤网、滤纸、过滤芯、过滤筒、过滤袋和纤维粉等。
图1 过滤原理过滤介质的选择非常重要,过滤介质的选取需要根据过滤精度和流量来确定,由于直接关乎后期使用效果,所以选择时需要根据实际情况合理选用。
- 1、下载文档前请自行甄别文档内容的完整性,平台不提供额外的编辑、内容补充、找答案等附加服务。
- 2、"仅部分预览"的文档,不可在线预览部分如存在完整性等问题,可反馈申请退款(可完整预览的文档不适用该条件!)。
- 3、如文档侵犯您的权益,请联系客服反馈,我们会尽快为您处理(人工客服工作时间:9:00-18:30)。
用于发动机生产的切削液冷却过滤研究动力总成的生产往往由大量金属切削机床组成,如发动机缸体、缸盖、变速箱壳体等,此类零件的加工大多选用湿式加工,即加工过程中需要使用切削液进行冷却。
切削液和切屑是机加工车间的主要污染源之一,减少切削液用量并妥善处理,不仅是目前流行的清洁生产的需要,同时也是节能减排、降本增效的必然选择。
汽车生产是大批量生产模式的典型代表,动力总成车间加工中心密集、节拍快,要求使用高效的冷却过滤处理系统,同时毛坯材料较单一(多为铸铝、铸铁材质),为切削液统一集中处理提供了可能性。
集中冷却过滤系统高效节能环保,正在被国内外车企越来越广泛地采用,如何正确使用以发挥其最大效能就显得迫在眉睫。
本文以加工中心中使用的切削液为例,重点研究切削液的处理方式。
切削液与处理方式1.切削液的作用切削液分为切削油和水溶性切削液两大类,水溶性切削液又分为全合成、半合成和乳化型三小类,加工中心一般使用乳化型的水溶性切削液。
金属加工中切削液主要起冷却、润滑排屑、防锈和清洗的作用,金属切削时由于金属变形和摩擦,产生大量的热量,如不及时将热量带走将导致热量积聚在刀具上,影响刀具切削性能。
切削时同时产生大量切屑,如不及时将切屑从切削区移开,将划伤加工表面,甚至导致刀具粘结,因此需要带屑清洗。
铁件周围存在大量水汽,在局部高温的作用下,工件极易生锈,此时切削液还起到防锈的作用。
2.切削液过滤物化指标由于切削液关乎加工质量和稳定性、刀具寿命,因此经净化后的切削液需要实时监测,满足要求后才能继续使用。
对过滤后的净液监测项很多,主要有浓度、pH值、过滤精度等,具体参数见表1。
3.处理方式切削液过滤形式分为四大类:沉淀过滤、缝隙过滤、离心过滤和磁性过滤,加工中心一般使用缝隙过滤和离心过滤两种方式,其原理如图1所示。
其中缝隙过滤的使用介质种类有许多种,常见过滤介质有滤网、滤纸、过滤芯、过滤筒、过滤袋和纤维粉等。
图1 过滤原理过滤介质的选择非常重要,过滤介质的选取需要根据过滤精度和流量来确定,由于直接关乎后期使用效果,所以选择时需要根据实际情况合理选用。
不同类型的机床产生的切屑形状不同,如加工中心一般产生较大颗粒切屑,可采重力过滤进行初级过滤;而磨床类产生的粉末较细,小颗粒可通过过滤介质,容易产生淤泥,如图2所示,考虑采用磁性过滤装置或过滤筒增加反冲功能。
缸体、缸盖一般为铸铝或铸铁材料,一般采用沉淀的方法将大颗粒切屑沉降到液箱底部,再用刮屑板将其提升出液面,再采用滤纸过滤小颗粒杂质。
图2 金属污泥冷却过滤系统如上所述,脏液中含有大量杂质,需要通过选用合理的、性价比高的过滤方案。
根据冷却过滤系统规模大小及供应机床台数,可分为单机型和集中型两种。
1.单机冷却过滤系统加工中心一般配有单机刮屑链和冷却过滤单元,如图3所示,对脏液进行过滤冷却,循环使用。
大颗粒切屑通过刮屑链送往积屑小车,脏液收集后利用液体的重力通过滤纸进行过滤,该系统具有成本低,布局灵活,独立性强等优点,但缺点同样明显,如切削液寿命短、污染环境、维护工作量大等。
图3 单机冷却过滤系统对于大型封闭式恒温工厂,清洁度和温控要求高,而单机冷却液箱是敞开式结构,热量直接散发在车间,使车间闷热,对工作环境影响比较大。
同时受限于布局,液箱容积往往仅数立方米,消泡性和散热性差,切削液容易发生泡沫溢出和渗漏。
实际使用中,由于需要逐台控制检测,带来很多负面效应,如频繁地加液、换液导致冷却箱周围湿滑,存在安全隐患。
每台加工中心都配备过滤冷却装置,过于分散,无法对切屑进行深入处理,特别对于大型工厂,切削液维护和废物处理工作量巨大。
正是以上缺点,限制了单机冷却过滤的使用范围。
2.集中冷却过滤系统单机冷却过滤系统无法满足大型工厂的使用要求,自动化程度高、节能环保的集中冷却过滤系统越来越广泛地被采用,特别适用于发动机、变速器工厂。
(1)系统组成集中冷却过滤系统由过滤系统、供回液系统、增氧系统、除油系统以及管路冲刷系统等部分组成。
过滤系统解决方案有很多种,各有千秋,但基本思路一致。
大体思路为大颗粒切屑依靠重力沉淀分离,由泵组或重力在过滤单元两侧产生压力差,切削液通过,杂质无法通过,从而获得净液。
不同的过滤单元,使用场合、效果不尽相同,具体组合方案有多种,如表2所示。
目前我公司新工厂缸体、缸盖线采用了一种星形过滤单元:金属滤网内注入乳状纤维,俗称预涂粉(预涂粉由纤维粉加液搅拌而成),由专门的装置注入过滤单元,如图4所示,液体通过预涂粉之间的缝隙过滤,它是缝隙式过滤的一种。
预涂粉使用寿命结束后,过滤压力增大,控制系统侦测到出液管负压增大后,可由机械装置将过滤单元提起,由振动的方法将失效的块状预涂粉从滤网上剥离,通过刮屑链排出系统,当重新注入预涂粉后,过滤单元恢复工作。
该结构消除了滤纸结构破损后导致过滤失效的隐患,且过滤精度高,可达30μm,同时消除高污染性的废弃滤纸,可减小成本压力。
图4 星形过滤单元结构供回液系统由液箱(沉淀液箱、脏液箱、净液箱)、供回液泵、热量交换器等组成。
液箱布置形式有地上和地下两种,地上式的采用液箱与管路全部位于地面之上,而地下水池式将回液沟槽与液箱置于地面之下,该方案可很好的利用厂房地下空间。
供液泵可选用变频泵或者恒频泵,由于机床用液量不是固定的,存在波动,而机床对供液压力要求恒定,故优先采用变频泵,其具有节能环保、噪音低等优点。
根据泵的安装位置不同,分为正压过滤与负压过滤两种,负压过滤将过滤泵与供液泵合二为一,结构简单且节能。
热量交换器是保证切削液温度的第一层保障,为了保证切削液的应有性能和加工精度,需要使切削液的温度恒定在22℃左右。
夏天可以用厂房外的冷却水对切削液进行降温;冬天切削液温度较低,又需要对切削液进行加热处理,因此热交换器非常重要。
增氧系统是为了增加切削液中的氧气含量,抑制切削液中的厌氧菌生长,防止细菌分解切削液成分;同时细菌生长易造成切削液霉变,产生异味,污染环境,该系统可延长切削液寿命,降低成本,地下式液箱尤其需要注意增氧。
除油系统的作用是将混入切削液中的杂质油(机床导轨、丝杠润滑油,液压油,工件防锈油)分离开来,防止污油影响切削液品质。
集中冷却系统一般采用多级过滤,沉淀液箱根据两者不同比重进行油水分离,再利用撇油器对浮油进行捕获。
管路冲刷系统是为消除切屑在管路拐弯处或流速缓慢处的堆积而设计的,一般采用从净液管路中取切削液进行冲刷的方法,从而保证切屑可全部流回液箱,防止堆积堵塞。
另外对于铸铁件机加线,当液箱采用地上式时,脏液提升泵需要将混有铁屑的切削液泵回液箱,泵的叶轮需要考虑断屑与抽屑功能。
(2)工作原理集中冷却过滤系统示意图如图5所示,其工作原理为机床使用过的切削液经回液泵回沉淀箱,大颗粒的切屑在此沉淀,经刮屑链排到系统外部,浮油漂浮在液面上,可通过撇油器进行捕获、清理,切削液经沉淀箱下方连通器孔进入脏液箱,在供液泵产生的负压下经过星形过滤单元,得到净液。
其中一部分净液泵入净液箱备用,其余净液经热交换系统向机床供液。
当其中某一过滤单元发生堵塞或者预涂粉失效时,将从净液箱中抽取液体来补充,同时过滤单元自动进行清洁,清洁完毕后重新供液。
图5 集中冷却过滤系统示意图(3)集中冷却过滤系统优缺点集中冷却过滤具有许多特点,如大循环、大流量、大行程,散热快;与单机过滤冷却系统相比,切削液寿命提高了三倍左右;可采用PLC控制,自动化程度高,使用周期长,维护简单,切屑便于集中处理(压块、甩干等),密封性好,夏天空气中不会有异味,有利于环境清洁;切削液易于控制维护,只需要在净液出口处进行抽检控制;通过热交换系统可实现恒温控制,同时如厂房内外冷却水进行冷却,可将热量带到厂房外部,降低了夏天厂房内的温度,增加舒适度;过滤精度高,过滤精度高可延长刀具使用寿命,降低工件表面粗糙度数值。
可加装撇油器,消除切削液中的污油,提高切削液使用寿命;便于废水集中处理,通过管道可将废水直接排到污水处理站进行清理。
但同时也存在诸多缺点,如布线复杂,建设周期长,施工难度大,一次性投资大,一旦发生故障可能造成整线停机,风险大;如果采用空中回液,需要采用回液泵进行提升,由于泵的搅动易造成切削液起泡,对切削液的消泡性提出了更高的要求。
集中冷却过滤与单机冷却过滤的优缺点具体可见表3所示。
集中冷却过滤单机冷却过滤优点1、冷却液为同一品牌、浓度、过滤精度等 2、改善工作环境 3、能够集中处理切屑和固体杂质 4、统一管理,有利于延长冷却液的寿命,减少废液排放1、可选用多个品牌的冷却液 2、根据加工工艺不同,每序可以配不同浓度的冷却液 3、生产线工艺布置灵活,后期易改造 4、独立性好,避免互相干扰缺点1、机床位置固定,且增加了切削液受污染的可能性 2、独立性差,易造成过滤系统及生产线机床的集体停机 3、易引起泡沫问题,对切削液的品质要求高1、消泡性及散热性差 2、切屑处理系统繁多,且切屑处理复杂 3、点检、维护复杂 4、环境污染严重3.冷却过滤选用原则及成功案例对于小型工厂内分散布置的加工中心,适宜采用单机冷却过滤系统。
对于大型动力总成零件工厂,如发动机缸体、缸盖、框架和变速箱壳体等,由于产量大,机床数量多,且切削液型号相同,故可采用大型的集中冷却过滤系统。
集中冷却过滤系统可以大幅提高切削液寿命,降低生产成本,实现清洁生产,改善员工工作环境,因此该系统具有先进性与环保性的特点。
过滤机的基本参数主要有过滤精度、过滤介质的尺寸、流量、箱体尺寸和出屑量。
如我公司某缸体生产线,年产能30万台,机床切削液的过滤精度要求高(外冷100μm/内冷30μm), 流量需求较大(8000L/min),故采用了集中冷却过滤系统。
具体方案为地上式液箱,空中回液,外冷过滤单元采用星形过滤单元,机床主轴内冷采用单独的离心式过滤,以保证内冷过滤要求;液箱容积一般为每分钟需求流量的10倍左右,液箱的容积最终确定为120m3。
该系统经过近一年的使用,充分发挥了集中处理高效节能、保护环境、运营成本低的优点。
总结切削液作为动力总成工厂一种非常重要的消耗品,不仅用量大,而且容易污染环境,因此有必要对其进行深入研究。
本文围绕切削液的净化过滤处理,对过滤方式、过滤介质和过滤系统尺寸选取进行了研究,得出大型机加工车间适宜采用集中冷却系统的结论。
同时结合我公司长期使用经验,将先进的切削液处理理念进行推广,为汽车企业切削液处理提供优秀的解决方案,从而振兴我国装备制造业。