工业自动控制系统可靠性分析
自动化控制系统在电气工程中的可靠性与安全性分析

自动化控制系统在电气工程中的可靠性与安全性分析自动化控制系统在电气工程中扮演着至关重要的角色。
它们能够有效地监测、控制和管理各种电气设备和过程,提高工作效率和生产质量。
然而,如何确保这些系统的可靠性和安全性一直是电气工程师们面临的一个重要挑战。
本文将对自动化控制系统的可靠性和安全性进行分析,并介绍一些提高这些方面的常用方法。
1. 可靠性分析自动化控制系统的可靠性是指其在一定时间内正常运行的概率。
可靠性分析是通过评估系统的故障率、失效模式和维修时间等指标来衡量系统的可靠性水平。
常用的可靠性评估方法包括故障树分析(FTA)和可靠性块图(RBD)等。
1.1 故障树分析(FTA)故障树分析是一种定性的方法,用于确定导致系统故障的原因和可能发生的失效路径。
它通过使用逻辑门和事件组合来建立故障树模型,进而计算系统的可靠性。
故障树分析能够帮助工程师们理解系统的可靠性短板,并采取相应的改进措施。
1.2 可靠性块图(RBD)可靠性块图是一种定量的可靠性评估方法,通过建立系统组成部分之间的关系来分析系统的可靠性。
可靠性块图将系统的各个组成模块表示为块,并通过概率计算方法来确定整个系统的可靠性。
通过使用可靠性块图,工程师们可以对系统的可靠性进行细致的量化分析。
2. 安全性分析自动化控制系统的安全性是指系统在正常运行状态下,不会对人员、设备或环境造成任何危害的程度。
安全性分析的目的是识别和评估潜在的风险,并采取措施来降低这些风险。
2.1 风险评估风险评估是一种系统性的方法,用于识别和分析系统中的潜在风险。
它通过评估各种可能的风险因素,如人为错误、设备故障和自然灾害等,从而确定其对系统安全性的潜在影响。
风险评估能够帮助工程师们制定有效的风险控制策略,确保系统的安全性。
2.2 安全措施为了提高自动化控制系统的安全性,工程师们可以采取一系列的安全措施。
例如,使用备份系统和冗余设计来降低系统故障的影响;建立严格的访问控制和身份验证机制,防止未经授权的访问;定期进行系统维护和更新,修复可能存在的漏洞等。
系统可靠性预计分析报告

系统可靠性预计分析报告一、引言在当今复杂的技术环境中,系统的可靠性成为了至关重要的因素。
无论是工业生产中的自动化控制系统,还是日常生活中的电子设备,系统的可靠性直接影响着其性能和用户体验。
为了确保系统能够在规定的条件下和规定的时间内完成预期的功能,进行系统可靠性预计分析是必不可少的环节。
二、系统概述本次分析的系统是一个系统名称,该系统主要用于系统的主要用途。
系统由以下几个主要部分组成:1、部件 1 名称:负责部件 1 的主要功能。
2、部件 2 名称:承担部件 2 的主要功能。
3、部件 3 名称:执行部件 3 的主要功能。
三、可靠性预计方法在本次系统可靠性预计分析中,我们采用了以下几种常见的方法:1、故障模式与影响分析(FMEA)通过对系统各部件可能出现的故障模式进行分析,评估其对系统整体性能的影响,从而确定系统的薄弱环节。
2、可靠性框图(RBD)将系统的各个部件以框图的形式表示,并根据部件之间的逻辑关系计算系统的可靠性指标。
3、蒙特卡罗模拟利用随机数生成和统计分析的方法,对系统的可靠性进行多次模拟,以获取更准确的可靠性估计。
四、部件可靠性数据收集为了进行准确的可靠性预计,我们收集了系统各部件的可靠性相关数据,包括:1、故障率数据:从供应商提供的技术文档、行业标准以及类似系统的历史数据中获取部件的故障率信息。
2、维修时间数据:了解部件发生故障后的平均维修时间,以评估系统的可用性。
3、工作环境数据:考虑系统运行的环境条件,如温度、湿度、振动等,对部件可靠性的影响。
五、系统可靠性模型建立基于收集到的部件可靠性数据和所选择的可靠性预计方法,我们建立了系统的可靠性模型。
以可靠性框图为例,系统的整体可靠性可以表示为各个部件可靠性的组合。
假设系统由三个串联的部件 A、B、C组成,其可靠性分别为 R_A、R_B、R_C,则系统的可靠性 R_sys =R_A × R_B × R_C 。
六、可靠性预计结果经过计算和分析,得到了系统的以下可靠性预计结果:1、系统的平均故障间隔时间(MTBF)为具体数值小时,这意味着系统在平均情况下,每隔具体数值小时可能会发生一次故障。
自动化控制系统可靠性分析

自动化控制系统可靠性分析自动化控制系统是现代工业中不可或缺的组成部分,它可以实现生产过程的自动控制和监控,提高生产效率和产品质量。
然而,在使用过程中,系统的可靠性往往成为一个关键问题。
本文将对自动化控制系统的可靠性进行分析,并探讨提高系统可靠性的方法。
一、自动化控制系统可靠性的定义和评价指标可靠性是指系统在给定的时间范围内能够正常工作的能力。
在自动化控制系统中,可靠性的评价指标主要包括可用性、故障率和平均修复时间。
1. 可用性:可用性是指系统在给定时间内处于可工作状态的比例。
它可以通过以下公式计算:可用性 = 工作时间 / (工作时间 + 故障时间)2. 故障率:故障率是指在单位时间内系统发生故障的概率。
它可以通过以下公式计算:故障率 = 发生故障的次数 / 工作时间3. 平均修复时间:平均修复时间是指系统发生故障后修复故障所需的平均时间。
二、自动化控制系统可靠性分析的方法自动化控制系统可靠性分析的方法通常包括故障树分析、故障模式与影响分析、可靠性块图等。
1. 故障树分析:故障树分析是将系统的故障表现和故障原因进行逻辑关系的可视化表示。
通过构建故障树,可以识别系统中的潜在故障模式和导致故障的原因,从而提高系统的可靠性。
2. 故障模式与影响分析:故障模式与影响分析是对系统可能发生的故障模式及其对系统性能的影响进行分析。
通过分析故障模式和影响,可以确定系统中容易发生故障的部件和系统的薄弱环节,从而采取相应的措施来提高系统的可靠性。
3. 可靠性块图:可靠性块图是一种将系统的不同部件和元素通过可靠性块的形式进行组合以评估系统整体可靠性的方法。
通过分析系统中不同部件的可靠性指标和相互之间的关系,可以计算系统整体的可靠性,并确定影响系统可靠性的关键部件。
三、提高自动化控制系统可靠性的方法为了提高自动化控制系统的可靠性,可以采取以下方法:1. 设计合理的冗余系统:冗余系统是指在系统中引入冗余元件或功能,以提高系统对故障的容忍能力。
自动化控制系统的可靠性与维护性研究
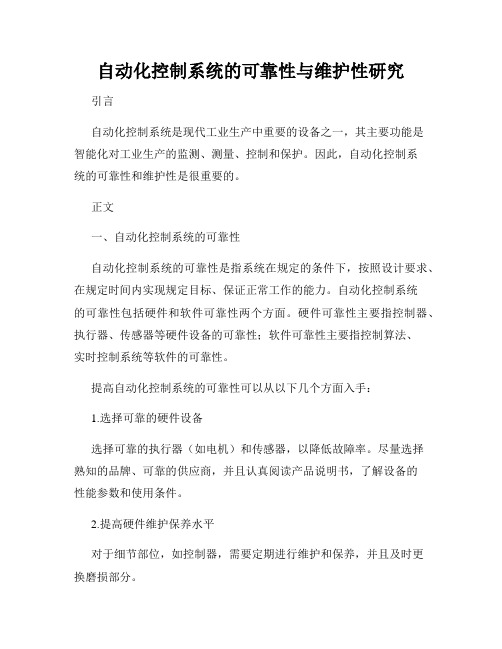
自动化控制系统的可靠性与维护性研究引言自动化控制系统是现代工业生产中重要的设备之一,其主要功能是智能化对工业生产的监测、测量、控制和保护。
因此,自动化控制系统的可靠性和维护性是很重要的。
正文一、自动化控制系统的可靠性自动化控制系统的可靠性是指系统在规定的条件下,按照设计要求、在规定时间内实现规定目标、保证正常工作的能力。
自动化控制系统的可靠性包括硬件和软件可靠性两个方面。
硬件可靠性主要指控制器、执行器、传感器等硬件设备的可靠性;软件可靠性主要指控制算法、实时控制系统等软件的可靠性。
提高自动化控制系统的可靠性可以从以下几个方面入手:1.选择可靠的硬件设备选择可靠的执行器(如电机)和传感器,以降低故障率。
尽量选择熟知的品牌、可靠的供应商,并且认真阅读产品说明书,了解设备的性能参数和使用条件。
2.提高硬件维护保养水平对于细节部位,如控制器,需要定期进行维护和保养,并且及时更换磨损部分。
3.优化自动化控制系统的控制策略将传感器和执行器合理的配置在系统中,使其满足系统要求,使系统运行得更加平滑高效。
二、自动化控制系统的维护性自动化控制系统的维护性是指系统在规定的条件下,按照设计要求、在规定时间内实现规定目标、保证正常工作的能力。
与自动化控制系统的可靠性相比,该项涉及到系统的快速恢复和维护。
提高自动化控制系统的维护性可以从以下几个方面入手:1.清洁保养各设备交流电器件、控制器和仪器仪表各有不同,具体清洁保养方式请参考相应的说明书。
及时更换各类容易磨损的零件,例如传动皮带、轴承、螺丝等等。
2.防止进入杂质各种进入设备中的杂物包括油污、灰尘等,它们会堵塞风扇及进口,并对设备内部造成损坏。
因此,要定期将设备内部进行清洁。
3.检查电路及仪表定期进行设备内部部件的检查,包括电线、插头、电线板等等。
对于机器故障,首先要检查一些常见故障,例如过热或者开关不工作等问题。
结论自动化控制系统的可靠性和维护性是现代工业生产不可或缺的一部分。
浅谈PLC控制系统的可靠性措施
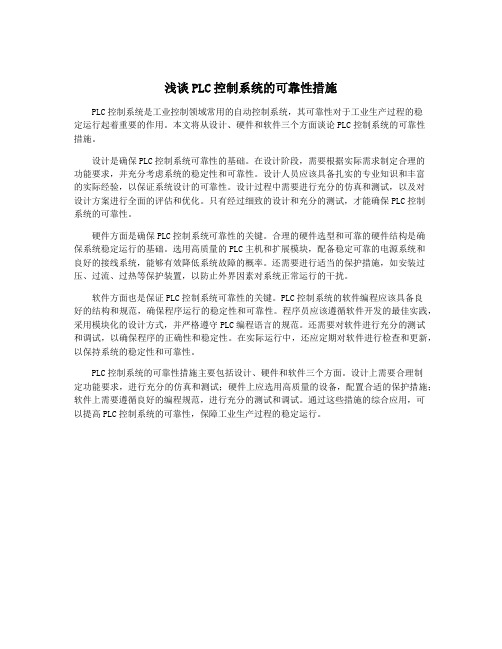
浅谈PLC控制系统的可靠性措施PLC控制系统是工业控制领域常用的自动控制系统,其可靠性对于工业生产过程的稳定运行起着重要的作用。
本文将从设计、硬件和软件三个方面谈论PLC控制系统的可靠性措施。
设计是确保PLC控制系统可靠性的基础。
在设计阶段,需要根据实际需求制定合理的功能要求,并充分考虑系统的稳定性和可靠性。
设计人员应该具备扎实的专业知识和丰富的实际经验,以保证系统设计的可靠性。
设计过程中需要进行充分的仿真和测试,以及对设计方案进行全面的评估和优化。
只有经过细致的设计和充分的测试,才能确保PLC控制系统的可靠性。
硬件方面是确保PLC控制系统可靠性的关键。
合理的硬件选型和可靠的硬件结构是确保系统稳定运行的基础。
选用高质量的PLC主机和扩展模块,配备稳定可靠的电源系统和良好的接线系统,能够有效降低系统故障的概率。
还需要进行适当的保护措施,如安装过压、过流、过热等保护装置,以防止外界因素对系统正常运行的干扰。
软件方面也是保证PLC控制系统可靠性的关键。
PLC控制系统的软件编程应该具备良好的结构和规范,确保程序运行的稳定性和可靠性。
程序员应该遵循软件开发的最佳实践,采用模块化的设计方式,并严格遵守PLC编程语言的规范。
还需要对软件进行充分的测试和调试,以确保程序的正确性和稳定性。
在实际运行中,还应定期对软件进行检查和更新,以保持系统的稳定性和可靠性。
PLC控制系统的可靠性措施主要包括设计、硬件和软件三个方面。
设计上需要合理制定功能要求,进行充分的仿真和测试;硬件上应选用高质量的设备,配置合适的保护措施;软件上需要遵循良好的编程规范,进行充分的测试和调试。
通过这些措施的综合应用,可以提高PLC控制系统的可靠性,保障工业生产过程的稳定运行。
自动化系统的可靠性与安全性分析

自动化系统的可靠性与安全性分析随着科技的不断进步,自动化系统在各个领域得到了广泛的应用,如工业生产、交通运输、医疗保健等。
然而,这些自动化系统虽然提高了效率和准确性,但同时也面临着可靠性和安全性的挑战。
本文将对自动化系统的可靠性与安全性进行分析。
一、可靠性分析可靠性是指自动化系统在一定时间内完成任务的概率。
自动化系统的可靠性直接影响到生产效率和用户满意度。
在进行可靠性分析时,需要考虑以下几个方面:1. 硬件可靠性:自动化系统的硬件部分包括传感器、执行器、控制器等。
硬件故障可能导致系统无法正常工作。
因此,对于硬件的可靠性分析需要考虑其平均故障时间(MTTF)、平均修复时间(MTTR)等指标。
2. 软件可靠性:自动化系统的软件部分需要确保程序的正确性和稳定性。
软件故障可能导致系统崩溃或出现错误操作。
因此,对于软件的可靠性分析需要进行代码检查、测试和验证,确保程序的质量。
3. 数据可靠性:自动化系统需要处理大量的数据,包括传感器采集的数据、用户输入的数据等。
数据的准确性和完整性对于系统的可靠性至关重要。
因此,对于数据的可靠性分析需要考虑数据采集的准确性、数据传输的可靠性以及数据备份和恢复策略等。
二、安全性分析安全性是指自动化系统抵抗各种威胁和攻击的能力。
自动化系统的安全性关乎到用户的隐私和财产安全。
在进行安全性分析时,需要考虑以下几个方面:1. 身份认证与访问控制:自动化系统需要确保只有经过授权的用户才能进行访问和操作。
因此,需要进行身份认证和访问控制的设计和实施,包括用户账号管理、密码策略、角色权限管理等。
2. 数据保护与加密:自动化系统处理的数据可能包含敏感信息,如个人身份信息、商业机密等。
因此,需要对数据进行保护和加密,确保数据在传输和存储过程中的安全性。
3. 应急响应与恢复:自动化系统可能面临各种威胁和攻击,如病毒感染、网络攻击等。
因此,需要建立健全的应急响应和恢复机制,包括实时监测、入侵检测、应急演练等,及时应对和恢复系统的安全事件。
控制系统的可靠性与安全性分析方法
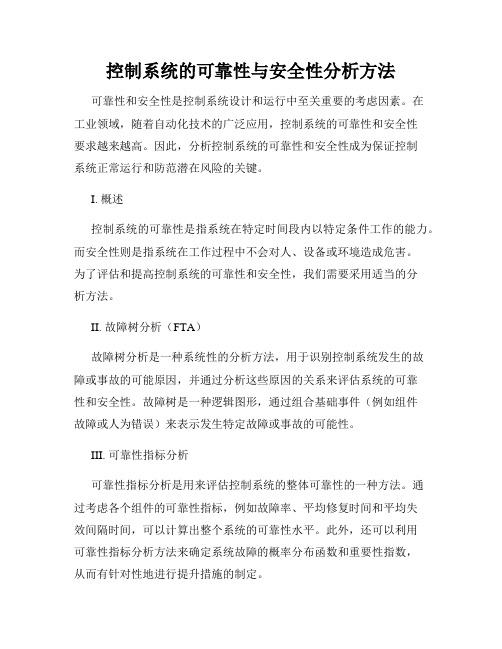
控制系统的可靠性与安全性分析方法可靠性和安全性是控制系统设计和运行中至关重要的考虑因素。
在工业领域,随着自动化技术的广泛应用,控制系统的可靠性和安全性要求越来越高。
因此,分析控制系统的可靠性和安全性成为保证控制系统正常运行和防范潜在风险的关键。
I. 概述控制系统的可靠性是指系统在特定时间段内以特定条件工作的能力。
而安全性则是指系统在工作过程中不会对人、设备或环境造成危害。
为了评估和提高控制系统的可靠性和安全性,我们需要采用适当的分析方法。
II. 故障树分析(FTA)故障树分析是一种系统性的分析方法,用于识别控制系统发生的故障或事故的可能原因,并通过分析这些原因的关系来评估系统的可靠性和安全性。
故障树是一种逻辑图形,通过组合基础事件(例如组件故障或人为错误)来表示发生特定故障或事故的可能性。
III. 可靠性指标分析可靠性指标分析是用来评估控制系统的整体可靠性的一种方法。
通过考虑各个组件的可靠性指标,例如故障率、平均修复时间和平均失效间隔时间,可以计算出整个系统的可靠性水平。
此外,还可以利用可靠性指标分析方法来确定系统故障的概率分布函数和重要性指数,从而有针对性地进行提升措施的制定。
IV. 安全性评估方法在控制系统设计和运行过程中,安全性评估是至关重要的。
一种常用的安全性评估方法是风险评估和风险分析。
通过识别可能的风险和事故,并评估其潜在的影响和发生概率,可以采取相应的措施来降低风险。
此外,还可以使用安全完整性级别(SIL)评估方法对控制系统进行定量的安全性评估,以确保系统满足特定的安全性要求。
V. 故障模式与效果分析(FMEA)故障模式与效果分析是一种通过识别系统中的潜在故障模式,并分析其可能的影响来评估系统可靠性和安全性的方法。
通过定性和定量分析系统中故障模式的发生概率和影响程度,可以制定相应的预防和纠正措施来提高系统的可靠性和安全性。
VI. 系统安全保障措施除了分析方法之外,还需要采取适当的安全保障措施来提高控制系统的可靠性和安全性。
工业控制系统的安全性分析与改进

工业控制系统的安全性分析与改进随着社会的不断发展和科技的不断进步,工业控制系统被广泛应用于各个领域,尤其是在工业自动化控制和智能制造方面,它的作用越来越重要。
然而,工业控制系统的安全问题也越来越引起人们的关注。
毫无疑问,工业控制系统的安全对于工业生产的安全、稳定及可靠性至关重要,不仅关乎企业的经济效益和声誉,更关系到人民生命财产的安全和利益。
一、工业控制系统的安全性分析1.工业控制系统存在的问题工业控制系统中常见的问题包括设备老化、软件漏洞、通信安全漏洞、人为操作等。
其中,软件漏洞是工业控制系统最为严重的安全问题之一。
因为工业控制系统数据都是通过软件进行处理,如果软件出现漏洞,将极大地威胁工业控制系统的安全。
此外,工业控制系统还存在人为操作不规范、数据泄露、通信信息被窃取等问题。
2.工业控制系统的安全威胁工业控制系统的安全威胁可分为两类:内部威胁和外部威胁。
内部威胁主要来自于不良员工的行为,如未经授权的系统访问、窃取密码、篡改数据等。
外部威胁则主要来自于黑客攻击、病毒木马、网络钓鱼等手段所导致的信息泄露或工业控制系统遭遇瘫痪,最终影响工业生产及基础设施运转。
3.工业控制系统安全措施为了确保工业控制系统的安全,必须采取一系列的安全措施。
首先要注重对系统硬件、软件的及时更新和维护,升级系统安全漏洞的补丁和防护机制。
其次,对于敏感数据的存储和交换要采用加密技术。
此外,为了增强工业控制系统的安全性,还需细致的人员培训、规章制度的制定和正确的操作习惯的培养等。
二、工业控制系统的安全性改进1.加强硬件和软件的维护为了确保工业控制系统正常与安全稳定运行,必须加强硬件和软件系统的维护,及时更新补丁、升级版本。
与此同时,实施定期的巡查和维护,保证系统能够持续运行,提高系统的稳定性和可靠性。
2.加强访问控制和权限管理为了确保工业控制系统的安全,首要的措施是加强访问控制和权限管理。
在该系统中,只有具备系统操作的员工才有权访问其内部数据和资源。
工业自动化控制系统的可靠性分析

工业自动化控制系统的可靠性分析一、引言工业自动化控制系统在现代工业生产中扮演着至关重要的角色。
然而,由于其复杂性和高度耦合的特点,这些系统在运行过程中可能会出现各种故障,影响到生产效率和安全性。
因此,对工业自动化控制系统的可靠性进行分析和评估显得尤为重要。
本文将探讨工业自动化控制系统的可靠性分析方法以及如何提升其可靠性。
二、工业自动化控制系统概述工业自动化控制系统是指利用计算机技术、传感器、执行器等设备对工业过程进行自动化控制的系统。
它由硬件设备和软件程序组成,用于实现工业过程的监测和控制。
常见的工业自动化控制系统包括PLC(可编程逻辑控制器)系统、DCS(分布式控制系统)以及SCADA(监控与数据采集系统)等。
三、可靠性分析的重要性工业自动化控制系统的可靠性分析可以帮助工程师深入了解系统的故障模式和影响因素,从而制定相应的预防和恢复策略。
通过对系统进行全面的可靠性分析,可以降低系统故障的频率和持续时间,提高系统的可靠性和稳定性,从而确保工业生产的连续性和效率。
四、可靠性分析方法1. 故障树分析(FTA)故障树分析是一种定性和定量分析故障发生的概率及其可能的影响的方法。
它通过将故障现象分解为各个可能性的基本事件,并使用逻辑门进行组合,最终确定系统失效的概率。
FTA可以帮助工程师识别系统中的故障路径,并提供改进和优化的建议。
2. 事件树分析(ETA)事件树分析是一种定性和定量分析故障发生的可能性和其后果的方法。
与故障树分析不同,事件树分析从故障的结果开始,逆向分析导致该结果的可能的事件序列。
通过事件树分析,工程师可以评估各个事件发生的概率,以及系统遭受损失的可能性,为风险管理提供参考。
3. 可靠性指标分析可靠性指标分析是根据系统的故障和修复数据,计算系统的可靠性指标,如平均无故障时间(MTTF)、平均修复时间(MTTR)、可靠性指数(RI)等。
这些指标可以定量评估系统的可靠性水平,为故障排除和维修工作提供依据。
自动化控制系统的可靠性与稳定性

自动化控制系统的可靠性与稳定性自动化控制系统在现代工业中起着至关重要的作用。
为了确保自动化控制系统的正常运行,我们需要关注其可靠性与稳定性。
本文将探讨自动化控制系统的可靠性与稳定性,并提供一些提高其可靠性与稳定性的方法。
一、自动化控制系统的可靠性可靠性是指系统在给定时间内正常运行的能力。
自动化控制系统的可靠性取决于多个因素。
1.1 硬件可靠性自动化控制系统的硬件部分包括传感器、执行器等,其可靠性直接影响整个系统的可靠性。
确保使用高质量的硬件设备,并进行定期的维护和检修,可以提高系统的可靠性。
1.2 软件可靠性自动化控制系统的软件部分负责控制和决策,因此软件的可靠性也是至关重要的。
在软件开发过程中,需要进行充分的测试和验证,确保软件的正确性和稳定性。
此外,定期进行软件的更新和升级,可以修复潜在的错误和漏洞,提高系统的可靠性。
1.3 环境因素自动化控制系统常常运行在各种环境条件下,例如高温、湿度等。
这些环境因素有时候可能会对系统的性能产生负面影响。
因此,在系统设计和安装阶段需要考虑环境因素,并采取相应的措施来保护系统,确保其稳定运行。
二、自动化控制系统的稳定性稳定性是指系统在给定条件下保持稳定运行的能力。
自动化控制系统的稳定性取决于以下方面。
2.1 控制算法自动化控制系统的稳定性主要依赖于其控制算法。
选择合适的控制算法对于确保系统的稳定性非常重要。
常见的控制算法包括PID控制、模糊控制等。
在选择控制算法时,需要考虑系统的动态特性,并进行合理的参数调节,以确保系统的稳定性。
2.2 反馈机制自动化控制系统通常采用反馈机制来实现对系统状态的监测和调节。
反馈机制可以及时探测到系统状态的变化,并通过相应的控制手段进行调节,从而维持系统的稳定运行。
合理设计反馈机制,确保其敏捷性和准确性,对提高系统的稳定性非常重要。
2.3 重构系统在某些情况下,自动化控制系统可能会遭遇故障或失效。
为了保证系统的连续运行和稳定性,可以采取重构系统的策略。
自动控制系统的安全性与可靠性分析
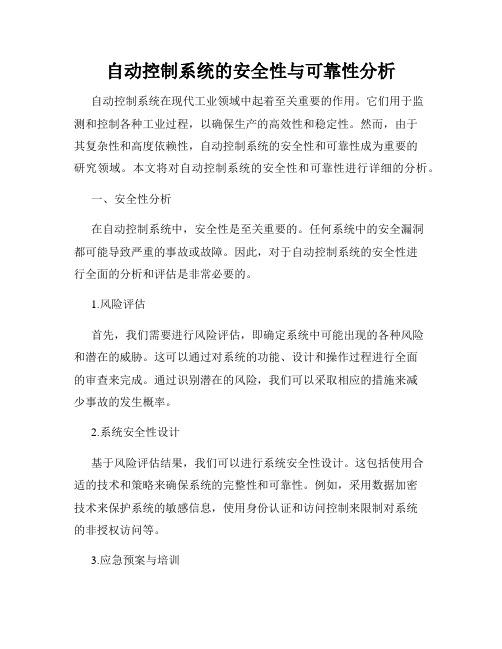
自动控制系统的安全性与可靠性分析自动控制系统在现代工业领域中起着至关重要的作用。
它们用于监测和控制各种工业过程,以确保生产的高效性和稳定性。
然而,由于其复杂性和高度依赖性,自动控制系统的安全性和可靠性成为重要的研究领域。
本文将对自动控制系统的安全性和可靠性进行详细的分析。
一、安全性分析在自动控制系统中,安全性是至关重要的。
任何系统中的安全漏洞都可能导致严重的事故或故障。
因此,对于自动控制系统的安全性进行全面的分析和评估是非常必要的。
1.风险评估首先,我们需要进行风险评估,即确定系统中可能出现的各种风险和潜在的威胁。
这可以通过对系统的功能、设计和操作过程进行全面的审查来完成。
通过识别潜在的风险,我们可以采取相应的措施来减少事故的发生概率。
2.系统安全性设计基于风险评估结果,我们可以进行系统安全性设计。
这包括使用合适的技术和策略来确保系统的完整性和可靠性。
例如,采用数据加密技术来保护系统的敏感信息,使用身份认证和访问控制来限制对系统的非授权访问等。
3.应急预案与培训除了系统安全性设计,制定应急预案也非常重要。
在系统发生故障或事故时,应急预案可以帮助我们迅速采取措施以最小化损失。
同时,为系统操作员和维护人员提供培训以增强其对系统安全性的认识和应对能力。
二、可靠性分析除了安全性,自动控制系统的可靠性也是一个关键的参数。
可靠性表示系统在规定的时间内,以规定的准确度和可用性来执行其功能或任务的能力。
1.可靠性评估可靠性评估是判断系统性能和可靠性的主要方法之一。
通过对系统的各个组件和子系统进行评估,我们可以确定系统在给定条件下的可靠性水平。
这涉及到对系统的故障率、失效模式分析、故障诊断和纠正等方面的研究。
2.容错设计为增强自动控制系统的可靠性,容错设计是一个常用的策略。
容错设计可以使系统在故障情况下保持部分功能,并能够进行相应的故障诊断和修复。
例如,使用冗余组件来代替可能发生故障的组件,以确保系统的连续运行。
浅谈PLC控制系统的可靠性措施
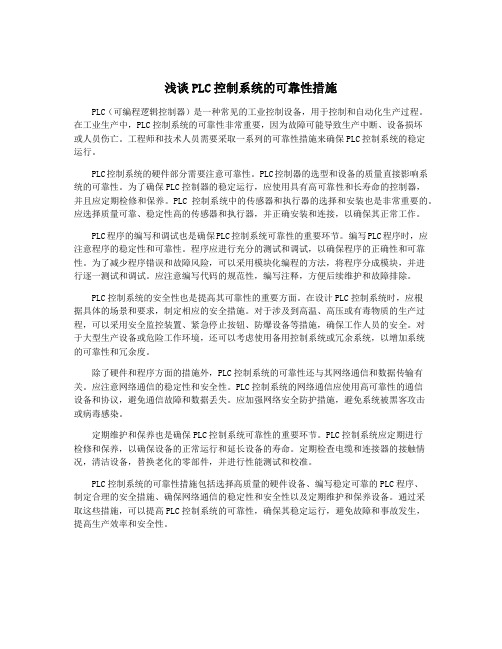
浅谈PLC控制系统的可靠性措施PLC(可编程逻辑控制器)是一种常见的工业控制设备,用于控制和自动化生产过程。
在工业生产中,PLC控制系统的可靠性非常重要,因为故障可能导致生产中断、设备损坏或人员伤亡。
工程师和技术人员需要采取一系列的可靠性措施来确保PLC控制系统的稳定运行。
PLC控制系统的硬件部分需要注意可靠性。
PLC控制器的选型和设备的质量直接影响系统的可靠性。
为了确保PLC控制器的稳定运行,应使用具有高可靠性和长寿命的控制器,并且应定期检修和保养。
PLC控制系统中的传感器和执行器的选择和安装也是非常重要的。
应选择质量可靠、稳定性高的传感器和执行器,并正确安装和连接,以确保其正常工作。
PLC程序的编写和调试也是确保PLC控制系统可靠性的重要环节。
编写PLC程序时,应注意程序的稳定性和可靠性。
程序应进行充分的测试和调试,以确保程序的正确性和可靠性。
为了减少程序错误和故障风险,可以采用模块化编程的方法,将程序分成模块,并进行逐一测试和调试。
应注意编写代码的规范性,编写注释,方便后续维护和故障排除。
PLC控制系统的安全性也是提高其可靠性的重要方面。
在设计PLC控制系统时,应根据具体的场景和要求,制定相应的安全措施。
对于涉及到高温、高压或有毒物质的生产过程,可以采用安全监控装置、紧急停止按钮、防爆设备等措施,确保工作人员的安全。
对于大型生产设备或危险工作环境,还可以考虑使用备用控制系统或冗余系统,以增加系统的可靠性和冗余度。
除了硬件和程序方面的措施外,PLC控制系统的可靠性还与其网络通信和数据传输有关。
应注意网络通信的稳定性和安全性。
PLC控制系统的网络通信应使用高可靠性的通信设备和协议,避免通信故障和数据丢失。
应加强网络安全防护措施,避免系统被黑客攻击或病毒感染。
定期维护和保养也是确保PLC控制系统可靠性的重要环节。
PLC控制系统应定期进行检修和保养,以确保设备的正常运行和延长设备的寿命。
定期检查电缆和连接器的接触情况,清洁设备,替换老化的零部件,并进行性能测试和校准。
浅谈PLC控制系统的可靠性措施

浅谈PLC控制系统的可靠性措施PLC控制系统是现代工业中常见的自动控制系统,它可以用来控制各种不同的生产设备和工业过程。
由于PLC控制系统的可靠性对于工业生产的稳定运行至关重要,因此采取了一系列的可靠性措施来确保PLC控制系统的稳定运行。
本文将就PLC控制系统的可靠性措施进行浅谈,以帮助读者更好地了解和应用PLC控制系统。
PLC控制系统的可靠性措施包括对硬件和软件两方面的管理。
在硬件方面,对PLC控制器的选型和安装至关重要。
首先需要选择具有较高性能和可靠性的PLC控制器,如西门子、施耐德等知名品牌。
在安装过程中需要保证PLC控制器的稳定性,避免外部干扰和物理损坏。
在使用过程中需要定期进行检查和维护,保证硬件设备的长期稳定运行。
对于PLC控制系统的软件管理也十分重要。
在编写PLC程序时,需要采用结构化编程方法,避免使用过多的跳转和循环,以提高程序的可读性和稳定性。
在编写程序时需要充分考虑各种异常情况的处理,确保程序在出现异常情况时能够正确地进行处理,并保证系统的安全运行。
需要定期对程序进行版本管理和备份,以防止程序丢失或损坏。
PLC控制系统的可靠性措施还包括对通信网络的管理。
在现代工业中,很多PLC控制系统都需要与其他设备进行通信,因此对通信网络的管理至关重要。
在设计通信网络时需要考虑网络的稳定性和抗干扰能力,避免因网络问题导致控制系统失效。
同时需要采取相应的安全措施,对网络进行加密和隔离,以确保数据的安全传输。
对于PLC控制系统的可靠性还需要进行可靠性分析和风险评估。
通过对系统的可靠性进行分析,可以找出系统中存在的潜在问题和风险,及时进行改进和处理,以提高系统的可靠性和稳定性。
同时还需要定期进行系统的故障模拟和应急演练,以确保系统在出现故障时能够迅速进行处理并恢复正常运行。
PLC控制系统的可靠性措施需要从硬件、软件、通信网络和风险评估等多个方面来进行管理和控制。
只有通过全面的管理和措施,才能确保PLC控制系统的稳定运行,为工业生产提供可靠的自动控制保障。
SCADA系统中的数据安全与可靠性分析

SCADA系统中的数据安全与可靠性分析一、引言随着信息化技术的不断发展,工业控制系统已逐渐从传统的机械传动方式向数字化、网络化方向发展。
工业控制系统(SCADA)是其中之一,它是工业自动化领域的重要组成部分,广泛应用于工业过程控制、制造业、电力、水利等领域。
在这个过程中,SCADA系统的数据安全与可靠性已成为处理厂商和用户关注的焦点。
本文将通过对SCADA系统中的数据安全与可靠性分析,探讨如何提高SCADA系统的可靠性和安全性,为工控系统的安全发展提供参考。
二、SCADA系统的工作原理及特点SCADA系统是由人机界面、通讯传输装置和监控设备组成的。
通常,它采集各种工业过程的数据,以实现监测、控制和自动化管理。
SCADA系统通常被分为多个子系统,如监视子系统、控制子系统、数据采集子系统、用户终端子系统等。
SCADA系统的工作原理基于现场设备的采集、传输和处理各种工艺数据。
SCADA系统还可以将工艺数据发送给下游或上游的生产系统,以实现更好的生产过程控制。
SCADA系统有以下几个特点:1、可编程: SCADA系统采用程序控制,能够根据控制任务的变化,对系统进行实时调整,实现自动化管理。
2、网络化:SCADA系统建立在网络上,以实现数据的远程传输。
3、安全性要求高:SCADA系统中重要的数据和程序需要高度保密和安全,防止被非法访问破坏。
4、集中式管理:SCNADA系统采集数据和处理数据,同时,也是一个数据管理系统,实现了集中式管理。
三、SCADA系统中的数据安全问题SCADA系统中的数据安全问题一直是大家关注的焦点。
在工业控制领域,网络和数据安全问题是屡遭攻击的对象。
恶意软件、网络病毒、黑客、勒索软件等攻击手段影响工业控制系统的稳定性,给安全生产和生产管理带来了严重的影响。
SCADA系统中的数据安全主要面临以下几个问题:1、信息泄露:SCADA系统中的数据,如果被非法访问,有可能泄漏给不属于该系统的人。
控制器的安全性和可靠性测试报告分析
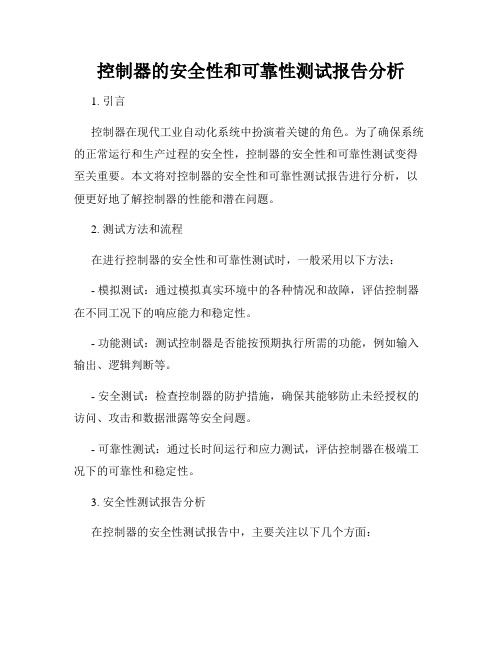
控制器的安全性和可靠性测试报告分析1. 引言控制器在现代工业自动化系统中扮演着关键的角色。
为了确保系统的正常运行和生产过程的安全性,控制器的安全性和可靠性测试变得至关重要。
本文将对控制器的安全性和可靠性测试报告进行分析,以便更好地了解控制器的性能和潜在问题。
2. 测试方法和流程在进行控制器的安全性和可靠性测试时,一般采用以下方法:- 模拟测试:通过模拟真实环境中的各种情况和故障,评估控制器在不同工况下的响应能力和稳定性。
- 功能测试:测试控制器是否能按预期执行所需的功能,例如输入输出、逻辑判断等。
- 安全测试:检查控制器的防护措施,确保其能够防止未经授权的访问、攻击和数据泄露等安全问题。
- 可靠性测试:通过长时间运行和应力测试,评估控制器在极端工况下的可靠性和稳定性。
3. 安全性测试报告分析在控制器的安全性测试报告中,主要关注以下几个方面:- 防护措施评估:测试报告应包括对控制器的防护措施进行评估,包括密码保护、用户权限管理、网络安全等方面。
- 安全漏洞发现:报告中应详细记录已发现的安全漏洞,并给出相应的建议和修复方案,以保护系统免受潜在威胁。
- 潜在风险分析:测试报告应分析已发现的潜在安全风险,对可能导致系统故障或被攻击的因素进行评估和预警。
4. 可靠性测试报告分析在控制器的可靠性测试报告中,应关注以下几个方面:- 响应性能评估:测试报告中应包括对控制器响应时间的评估,以确保其能够在预定时间范围内对输入信号做出合理响应。
- 稳定性分析:报告中应详细记录控制器在长时间运行和不同应力环境下的表现,并分析导致不稳定的原因,提供相应的解决方案。
- 故障率评估:通过长时间运行和故障注入测试,评估控制器的故障率,并提供相应的改进建议。
5. 结论通过对控制器的安全性和可靠性测试报告进行分析,可以全面了解控制器的性能和存在的问题。
同时,评估报告中的建议和修复方案,并采取相应的措施,以提高控制器的安全性和可靠性,确保系统的正常运行和生产过程的安全性。
工业自动化系统的可靠性分析与优化
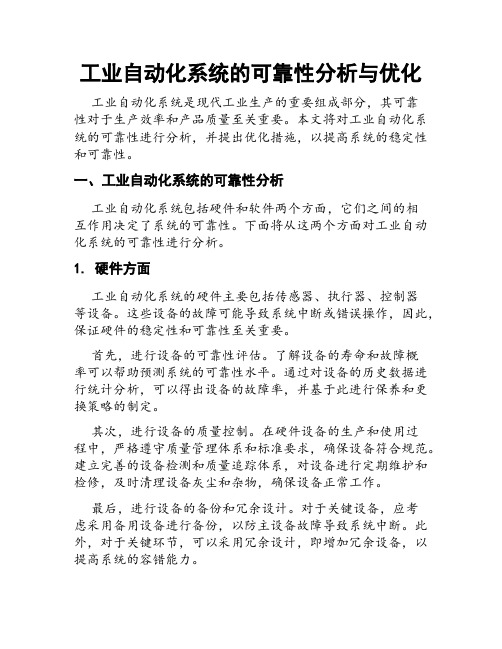
工业自动化系统的可靠性分析与优化工业自动化系统是现代工业生产的重要组成部分,其可靠性对于生产效率和产品质量至关重要。
本文将对工业自动化系统的可靠性进行分析,并提出优化措施,以提高系统的稳定性和可靠性。
一、工业自动化系统的可靠性分析工业自动化系统包括硬件和软件两个方面,它们之间的相互作用决定了系统的可靠性。
下面将从这两个方面对工业自动化系统的可靠性进行分析。
1. 硬件方面工业自动化系统的硬件主要包括传感器、执行器、控制器等设备。
这些设备的故障可能导致系统中断或错误操作,因此,保证硬件的稳定性和可靠性至关重要。
首先,进行设备的可靠性评估。
了解设备的寿命和故障概率可以帮助预测系统的可靠性水平。
通过对设备的历史数据进行统计分析,可以得出设备的故障率,并基于此进行保养和更换策略的制定。
其次,进行设备的质量控制。
在硬件设备的生产和使用过程中,严格遵守质量管理体系和标准要求,确保设备符合规范。
建立完善的设备检测和质量追踪体系,对设备进行定期维护和检修,及时清理设备灰尘和杂物,确保设备正常工作。
最后,进行设备的备份和冗余设计。
对于关键设备,应考虑采用备用设备进行备份,以防主设备故障导致系统中断。
此外,对于关键环节,可以采用冗余设计,即增加冗余设备,以提高系统的容错能力。
2. 软件方面工业自动化系统的软件负责控制和运行系统,正确的软件逻辑和稳定的运行环境对系统的可靠性至关重要。
以下是软件方面的可靠性分析方法。
首先,进行软件质量评估。
对工业自动化系统中使用的软件进行全面评估,包括设计和编程规范的合规性、代码的可读性和可维护性等。
通过软件测试和静态分析工具,检查软件是否存在潜在的错误和漏洞,并及时进行修复和更新。
其次,进行软件的备份和灾备设计。
对于关键软件,应备份至可靠的存储介质中,以保证软件的可恢复性。
此外,建立完善的灾备计划,包括应急预案和数据备份策略,以应对可能发生的系统故障和损坏。
最后,进行软件的更新和升级。
自动化控制系统的安全性分析
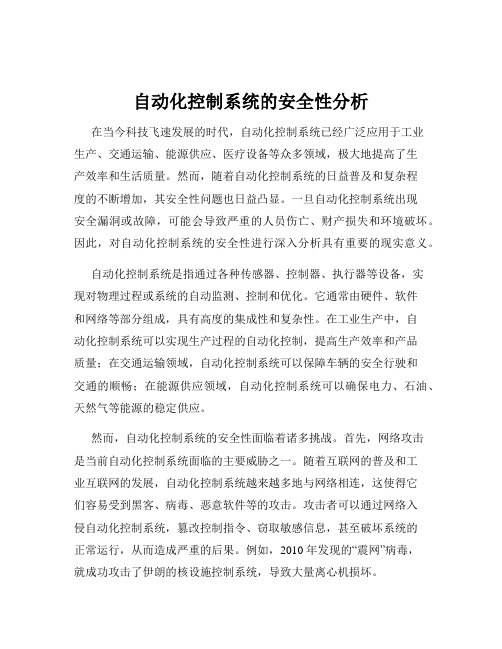
自动化控制系统的安全性分析在当今科技飞速发展的时代,自动化控制系统已经广泛应用于工业生产、交通运输、能源供应、医疗设备等众多领域,极大地提高了生产效率和生活质量。
然而,随着自动化控制系统的日益普及和复杂程度的不断增加,其安全性问题也日益凸显。
一旦自动化控制系统出现安全漏洞或故障,可能会导致严重的人员伤亡、财产损失和环境破坏。
因此,对自动化控制系统的安全性进行深入分析具有重要的现实意义。
自动化控制系统是指通过各种传感器、控制器、执行器等设备,实现对物理过程或系统的自动监测、控制和优化。
它通常由硬件、软件和网络等部分组成,具有高度的集成性和复杂性。
在工业生产中,自动化控制系统可以实现生产过程的自动化控制,提高生产效率和产品质量;在交通运输领域,自动化控制系统可以保障车辆的安全行驶和交通的顺畅;在能源供应领域,自动化控制系统可以确保电力、石油、天然气等能源的稳定供应。
然而,自动化控制系统的安全性面临着诸多挑战。
首先,网络攻击是当前自动化控制系统面临的主要威胁之一。
随着互联网的普及和工业互联网的发展,自动化控制系统越来越多地与网络相连,这使得它们容易受到黑客、病毒、恶意软件等的攻击。
攻击者可以通过网络入侵自动化控制系统,篡改控制指令、窃取敏感信息,甚至破坏系统的正常运行,从而造成严重的后果。
例如,2010 年发现的“震网”病毒,就成功攻击了伊朗的核设施控制系统,导致大量离心机损坏。
其次,硬件故障和软件漏洞也是自动化控制系统安全性的重要隐患。
由于自动化控制系统中的硬件设备和软件系统长期运行,可能会出现老化、磨损、故障等问题。
同时,软件系统在设计和开发过程中可能存在漏洞,这些漏洞如果被攻击者利用,也会对系统的安全性造成威胁。
此外,人为因素也是影响自动化控制系统安全性的一个不可忽视的因素。
操作人员的误操作、违规操作、安全意识淡薄等都可能导致系统出现安全事故。
为了保障自动化控制系统的安全性,我们需要采取一系列的措施。
控制系统的可靠性分析与设计

控制系统的可靠性分析与设计在现代社会中,各行各业都离不开控制系统的应用。
而作为一种重要的机电一体化技术,控制系统的可靠性对于系统的稳定运行和安全性至关重要。
本文将对控制系统的可靠性进行分析与设计,并探讨其中的关键要素。
一、控制系统可靠性的概念与意义控制系统可靠性是指系统在规定时间内按照要求进行连续稳定运行的能力。
作为一个综合性指标,控制系统的可靠性直接影响到系统的性能、安全性和经济性。
而在现实生活中,各种不可预测的外界因素和内部故障将不可避免地导致控制系统的故障和失效,因此,提高控制系统的可靠性就显得尤为重要。
二、控制系统可靠性分析的关键要素1. 故障模式与故障树分析故障模式分析是对控制系统可能发生的故障进行分类和描述,能够提供重要的故障特征信息。
而故障树分析则是通过将系统故障事件按照逻辑关系构成树状图,分析故障的因果关系,找出系统故障的根因,从而为系统的可靠性改进提供依据。
2. 故障诊断与容错技术故障诊断是指通过对控制系统中故障的检测和判断,找出故障出现的位置和原因。
而容错技术则是指通过设计系统的容错机制,即使在部分故障发生时,系统仍能够维持基本的功能和性能。
3. 可靠性评估与预测可靠性评估是对控制系统进行性能测试和参数检验,以确定系统的可靠性水平。
而可靠性预测则是通过对系统各部件寿命和故障率等数据的统计和分析,对系统未来的可靠性进行预测。
4. 备份与冗余设计备份与冗余设计是通过增加系统的冗余部件或备用系统,以提高系统的可靠性和容错性。
例如,采用双机热备份、多路冗余等技术手段,能够实现系统在部分故障发生时的无缝切换和自动恢复。
三、控制系统可靠性设计的方法与技术1. 可靠性设计的目标与约束在进行控制系统可靠性设计时,需要明确系统的可靠性目标和约束条件。
例如,需要确定系统的可靠性水平、运行时间和故障率要求等。
2. 故障防御与容错设计故障防御是通过合理的设计和布局,减少故障的发生和扩散。
例如,采用合适的工艺和材料,加强故障检测与报警,设置故障处理和排除机制等手段。
浅谈PLC控制系统的可靠性措施

浅谈PLC控制系统的可靠性措施PLC控制系统在工业自动化领域中起着至关重要的作用,其可靠性对于保证工程的正常运行至关重要。
为了确保PLC控制系统的可靠性,可以采取以下措施:选择合适的PLC设备和组件。
选择可靠的PLC设备是确保PLC控制系统可靠性的基础。
在选择设备时,要考虑其品牌、质量和性能等因素。
还要选择可靠的组件,如输入输出模块、传感器、执行器等,确保它们的稳定性和长寿命。
进行充分的可靠性测试。
在PLC控制系统开发和安装完成后,要进行充分的可靠性测试,包括功能测试、性能测试和稳定性测试等。
通过测试,可以发现潜在的故障和问题,并及时解决,确保系统的可靠性。
采用冗余设计。
冗余设计是提高PLC控制系统可靠性的重要手段之一。
可以采用冗余PLC控制器、冗余输入输出模块和冗余通信模块等。
当一个设备或模块出现故障时,可以自动切换到备份设备或模块,保证系统的连续运行。
第四,进行定期的维护和检修。
定期的维护和检修是确保PLC控制系统可靠性的重要手段。
包括对设备和组件的清洁、检查和测试等。
还要注意设备和组件的更新和更换,及时采用新的技术和设备,提高系统的可靠性。
第五,建立完善的备份和恢复机制。
在PLC控制系统中,要建立完善的备份和恢复机制,包括数据备份和程序备份等。
在系统发生故障或数据丢失时,可以快速恢复系统,保证生产的连续性和稳定性。
加强人员培训和管理。
人员是PLC控制系统运行的决定因素之一。
必须加强对工作人员的培训和管理,提高他们的技术水平和操作能力。
还要建立健全的安全管理制度,规范操作行为,确保系统的安全可靠运行。
对于提高PLC控制系统的可靠性,可以采取多种措施,如选择合适的设备和组件、进行可靠性测试、采用冗余设计、定期的维护和检修、建立备份和恢复机制,以及加强人员培训和管理等,从而确保PLC控制系统的稳定运行,提高工程的可靠性和安全性。
系统可靠性预计分析报告
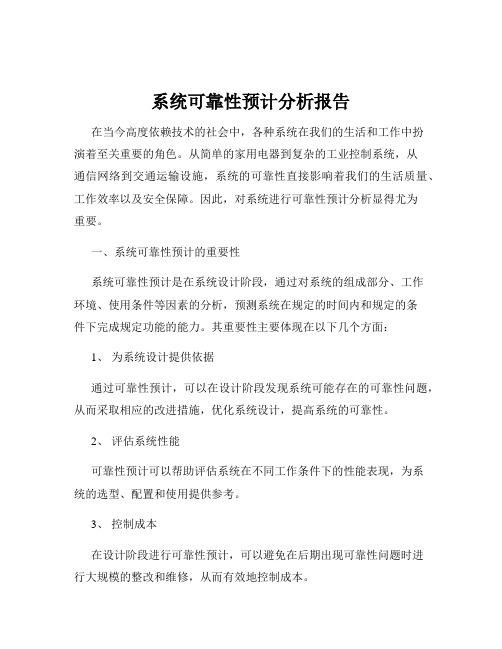
系统可靠性预计分析报告在当今高度依赖技术的社会中,各种系统在我们的生活和工作中扮演着至关重要的角色。
从简单的家用电器到复杂的工业控制系统,从通信网络到交通运输设施,系统的可靠性直接影响着我们的生活质量、工作效率以及安全保障。
因此,对系统进行可靠性预计分析显得尤为重要。
一、系统可靠性预计的重要性系统可靠性预计是在系统设计阶段,通过对系统的组成部分、工作环境、使用条件等因素的分析,预测系统在规定的时间内和规定的条件下完成规定功能的能力。
其重要性主要体现在以下几个方面:1、为系统设计提供依据通过可靠性预计,可以在设计阶段发现系统可能存在的可靠性问题,从而采取相应的改进措施,优化系统设计,提高系统的可靠性。
2、评估系统性能可靠性预计可以帮助评估系统在不同工作条件下的性能表现,为系统的选型、配置和使用提供参考。
3、控制成本在设计阶段进行可靠性预计,可以避免在后期出现可靠性问题时进行大规模的整改和维修,从而有效地控制成本。
4、提高用户满意度可靠的系统能够满足用户的需求,减少故障和停机时间,提高用户的满意度和忠诚度。
二、系统可靠性预计的方法目前,常用的系统可靠性预计方法主要有以下几种:1、元器件计数法这种方法适用于初步设计阶段,通过对系统中各类元器件的数量和质量等级进行统计,结合相应的可靠性数据手册,计算系统的基本可靠性指标。
2、应力分析法应力分析法相对较为复杂,需要考虑元器件的工作应力(如温度、湿度、电压等)对可靠性的影响。
通过建立数学模型,分析应力与可靠性之间的关系,从而更准确地预计系统的可靠性。
3、故障模式影响及危害性分析(FMECA)FMECA 是一种自下而上的分析方法,通过对系统中各个元器件和组件的故障模式、故障影响以及危害程度进行分析,评估系统的可靠性,并提出改进措施。
4、可靠性框图法可靠性框图法通过绘制系统的功能框图,将系统分解为若干个相互独立的子系统或组件,然后根据它们之间的逻辑关系计算系统的可靠性指标。
- 1、下载文档前请自行甄别文档内容的完整性,平台不提供额外的编辑、内容补充、找答案等附加服务。
- 2、"仅部分预览"的文档,不可在线预览部分如存在完整性等问题,可反馈申请退款(可完整预览的文档不适用该条件!)。
- 3、如文档侵犯您的权益,请联系客服反馈,我们会尽快为您处理(人工客服工作时间:9:00-18:30)。
工业自动控制系统可靠性分析
作者:靳永全
来源:《中国科技博览》2012年第32期
[摘要]:分析了影响工业自动控制系统可靠性的因素,从硬件、软件及编程组态方面,提出了提高可靠性的措施;硬件方面从一次元件及接地方面进行了论述;软件方面包括:I/O信号的处理、程序设计及监视报警等。
中图分类号:TG453+.9 文献标识码:TG 文章编号:1009-914X(2012)32- 0389 -01
1、引言
自动控制系统现在广泛应用于工业生产中,其本身主要由四部分组成:控制器、被控对象、执行机构和变送器,其中任何一个环节的任何一个部件出现故障,都会影响到系统的正常工作。
因此针对这些环节进行分析,采取相应的措施可有效提高自动控制系统的可靠性。
2、影响自动控制系统可靠性的因素
自动控制系统本身具有较高的可靠性,其影响因素主要来至于外部,一方面来自于输入输出信号,另一方面来至于就地一次元件;另外逻辑组态的缺陷同样会影响控制系统的可靠性。
2.1 输入输出信号对系统可靠性的影响
控制系统输入输出信号的正确性直接影响到系统的可靠性,如果输入到控制系统的信号不正确,系统将无法确定当前系统及设备状况,甚至给监控人员错误的信息,从而做出不正确的决策,造成故障,影响系统的可靠性。
而造成输入输出信号的错误主要有以下几方面的因素:
2.1.1辐射的干扰
控制系统输入信号的辐射干扰主要由电力网络、雷电、无线电广播、高频设备等产生的。
辐射干扰对控制系统的影响主要有两个方面,一方面是对控制系统内部的辐射,由控制系统内部电路感应而产生干扰;另一个方面是对控制系统通信网络的辐射,由通迅及信号线路引入到控制系统而产生干扰。
辐射干扰主要与电磁场的强度特别是频率有关,通常采用屏蔽或信号隔离的方法,减小干扰的影响,提高系统的可靠性。
2.1.2来自接地系统的干扰
正确的接地可有效避免信号的干扰,提高信号的正确性。
如果接地不当,不仅不能减少干扰,反而会影响信号的精度,甚至引入错误的信号。
控制系统的接地主要有系统接地、设备接
地、屏蔽接地及保护接地。
不同的接地系统对接地阻值及接地方式有不同的要求。
不正确的接地,可能在各接地系统间产生环路电流,影响系统的正常工作。
此外,屏蔽层、接地线及大地间可能构成回路,在磁场的作用下,在屏蔽层内产生感应电流,通过屏蔽层与芯线之间的耦合,干扰信号回路。
2.2来自就地一次元件的影响
接入到控制系统的信号包括数字量信号及模拟量信号,如果开关量信号的触点接触不良,触点发生抖动,控制系统就会收到错误的信号;同样现场变送器等一次模拟量元件出现故障,接线松动,变送器本身控制单元出现问题都会使送入控制系统的模拟量信号偏离实际值,使控制系统产生错误的判断而发出错误的指令,影响系统的稳定性。
2.3执行机构误动或拒动的影响
控制系统发出指令传递到就地执行机构,由于执行机构本身的缺陷或故障,造成控制器指令并未能得以正确执行,影响系统的可靠性。
例如就地电动执行器机械卡涩,电磁阀故障或气动执行器运行不到位,都影响到控制指令的正确执行,甚至给系统带来故障,造成重大损失。
3、提高控制系统可靠性的措施
在现代工业控制系统中,采取了许多提高系统可靠性的措施。
这些技术措施一般都基于四种策略:一是使系统本身不易发生故障,即所谓的故障预防;二是在系统发生故障时尽可能的减少故障所造成的影响,即所谓的故障保安或故障弱化;三是在系统发生故障时,能够让系统继续运行,即所谓的故障容错;四是在系统发生故障时,可以在运行情况下进行维修,即所谓的在线维修。
3.1提高控制系统可靠性的硬件措施
3.1.1有效控制干扰信号的影响
对于影响控制系统可靠性的干扰信号,主要应从以下几个方面进行控制:首先对信号电缆要采用带屏蔽层的信号电缆,信号电缆要与动力电缆分层敷设,不要在同一电缆槽盒内敷设,尤其不要与大功率动力电缆同层敷设;其次电缆屏蔽层要单点接地,不要两点或多点接地,避免由于接地点间电位不同产生感应电流,影响测量信号的正确性;第三信号电缆及元器件要尽量避开强磁场区间。
在广州某玻璃厂脱硫系统的调试期间,曾发生过大功率动力电缆与控制电缆同槽敷设,造成PLC控制系统故障的缺陷。
最后将动力电缆从控制电缆槽盒内抽出,重新单独敷设后,缺陷得到彻底消除。
3.1.2完善接地系统
对电子电路来说,接地是防止辐射干扰的有效方法。
控制系统中的地线分为屏蔽地、保护地、系统地等几种,这些地线应分开布置。
对于接地系统是采用单点接地还是多点接地,应按如下原则设置:信号频率低于1MHz时,布线和元器件间的电感影响较小,而接地电路形成的环流影响较大,因而单元回路间宜采用单点接地;信号频率大于10MHz时,宜采用多点接地。
3.1.3提高就地一次元件信号的正确性
一次元件本身运行是否稳定,直接影响到控制系统的可靠性。
因此要从几个方面确保就地一次元件的稳定性能:第一,选用质量好的就地一次元件,从根本上减少就地一次元件的故障率;第二,就地变送器、执行器本体要可靠接地;第三,加强对就地一次元件的维护,如对取样装置要定期进行清理,保持采样管路的畅通;对执行机构,要定期加油润滑,保证执行机构动作灵活、无卡涩;第四,对就地一次元件还应做好防雨措施,避免雨水侵蚀而引起一次元件的故障。
对于一些重要的信号,可采用多个测量元件,对同一测量点同时进行监测,减小信号的误差。
如锅炉炉膛负压等就利用这种方式,提高信号的可靠性。
这也体现了在线维修的控制策略,若其中一个测量元件出现故障,其它几个元件仍能确保系统正常运行的需要,同时可对故障元件进行维修。
3.2提高控制系统可靠性的软件措施
控制系统软件的可靠性同样非常重要,如果软件的可靠性不高,不仅会影响系统的正常工作,甚至会导致系统瘫痪。
近年来,随着自动化程度的提高,软件的可靠性越来越多的引起人们的重视。
3.2.1采用软件自身的某些功能,提高输入信号的可靠性
对于输入信号,利用组态软件的滤波功能,对输入信号进行滤波处理,以消除输入信号偶发性的波动;对于信号开路或短路的故障,利用软件自身的质量判断功能,判断输入信号质量的好坏,对系统认为是坏点的信号,进行合理组态,减少系统误动的可能性。
对输入信号及就地一次元件应根据具体情况设计多级报警系统,根据报警级别的不同,做出不同的处理。
如对引风机轴承温度,我们一般设置两级报警,当轴承温度达到高1值时,系统就会发出声光报警,提醒操作人员注意,以便及时采取措施;而当轴承温度达到高2值时,控制系统就会按照预定的控制逻辑,停运风机,以免造成设备的损坏。
3.2.3提高软件的容错性
为了提高控制系统的可靠性,逻辑组态时要考虑到信号出错时,系统能够识别错误信号,并能排除错误信号。
对重要的信号,可结合工艺情况,进行合理性判断,排除工艺条件下不可能产生的错误信号。
如进行液位控制,由于储罐的尺寸是已知的,进液或出液的阀门开度和压力是已知的,在一定时间里罐内液体变化高度大约在什么范围是知道的,如果这时液位计送给控制系统的数据和估算液位高度相差较大,判断可能是液位计故障,通过故障报警系统通知操作人员检查该液位计。
在程序设计时采用上述方法,可大大提高了输入信号的正确性,确保系统的稳定运行。
4、结束语
控制系统的可靠性受多种因素的影响,不仅与本身的性能有关,而且与现场环境、安装质量、软件编程组态等有很大关系。
从硬件设备上有效提高设备的抗干扰能力,从软件编程组态上提高软件的容错能力是提高控制系统可靠性的重要手段。
参考文献
武红军可编程控制器入门与应用实例(西门子S7-200系列)(第2版),中国电力出版社,2010;。