《冷冲压工艺与模具设计》模块三U形件弯曲模课件
合集下载
冷冲压工艺与模具设计教学课件

F KLt b
对在曲柄压力机上用薄料(t<1.5mm)对小 工件(面积 <2000mm2)压肋或压肋兼有校形工 序时的变形力按式计算。
F KAt2
K-系数,取0.7~1; L-加强肋长度(mm); t-材料料厚(mm); b —材料的抗拉强度(Mpa); A-局部成形面积;
二、压凸包
D 4 dp
握胀形模的结构及工作原理。
教学要求: 掌握常见胀形模的工作过程,能够根据模具
设计手册,进行胀形模的设计。
胀形:利用模具使坯料局部塑性变形,材料变薄, 表面积增大的冲压方法。
5.1.1 胀形成形的特点和分类 外部材料不进入变形区,变形区材料受双向
拉应力,产生拉伸变形,材料变薄。
当坯料外径与成形直径的比值D/d>3时, 其成形完全依赖于直径为d的圆周以内金属厚度 的变薄实现表面积的增大而成形。
(4)翻边力的计算
翻边力一般不大,非圆孔翻边力比圆孔翻边力小
圆柱形凸模:
F=1.1 (D-d0 )ts
圆锥形(球形)凸模:
F=1.2 tDms
(m=0.05~0.25)
5.2.2 外缘翻边 沿毛坯的曲边,使材料的拉伸或压缩,形成
高度不大的竖边。
1.分类 (1)外凸外缘翻边:属压缩类翻边,近似于局
课后思考
1、胀形的变形特点怎样?为什么采用胀形 工序加工的零件表面质量好?
2、什么叫胀形?胀形方法一般有哪几种? 各有什么特点?
3、胀形模的主要结构特点是什么?
5.2 翻边
学习目标: 能够掌握翻边的概念、成形特点及分类,掌
握翻边模的结构及工作原理。
教学要求: 掌握常见翻边模的工作过程,能够根据模具
胀形和液压胀形。
《冷冲压工艺及模具设计》U形件弯曲模PPT共92页
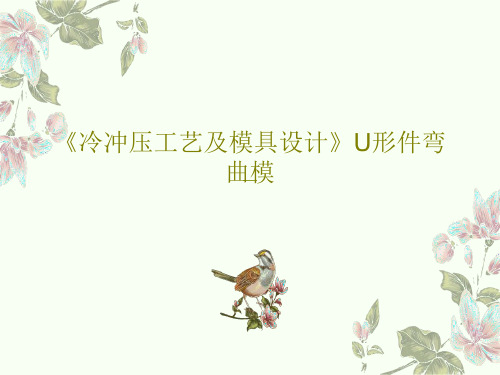
31、只有永远躺在泥坑里的人,才不会再掉进坑里。——黑格尔 32、希望的灯一旦熄灭,生活刹那间变成了一片黑暗。——普列姆昌德 33、希望是人生的乳母。——科策布 34、形成天才的决定因素应该是勤奋。——郭沫若 35、学到很多东西的诀窍,就件弯 曲模
16、自己选择的路、跪着也要把它走 完。 17、一般情况下)不想三年以后的事, 只想现 在的事 。现在 有成就 ,以后 才能更 辉煌。
18、敢于向黑暗宣战的人,心里必须 充满光 明。 19、学习的关键--重复。
20、懦弱的人只会裹足不前,莽撞的 人只能 引为烧 身,只 有真正 勇敢的 人才能 所向披 靡。
《冷冲模工艺与设计》课件——课题三十:弯曲工艺
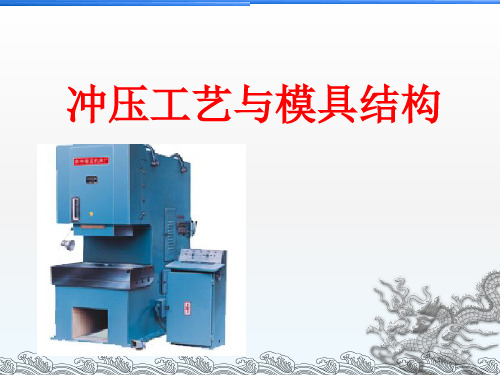
主要考虑的因素: (1)最小相对弯曲半径 (2)弯曲件的形状 (3)弯曲直边高度(图3-33) (4)弯曲件孔边距离(图3-34 、图3-35 )
(5)防止弯曲根部裂纹的工件结构(图3-36) (6)增添连接带和定位工艺孔(图3-37 ) (7)弯曲件尺寸的标注(图3-38 )
图3-33 弯曲件的直边高度
图3-34 弯曲件的孔边距
图3-35 防止孔变形的措施
图3-36 防止弯曲根部裂纹
图3-37 增添连接带和定位工艺孔的弯曲件
图3-38 尺寸标注与工艺的关系
3.弯曲件的精度 弯曲件的精度受坯料定位、偏移、翘曲和回弹等因素的影
响,弯曲的工序数目越多,精度也越低。
冲掌握弯曲件的工艺分析。
能力目标: 1、提高对弯曲件工艺分析的能力,提高工件质量, 减少废品率。
良好弯曲工艺的优点:能提高工件质量,减少废品率,而且 能简化工艺和模具结构,降低材料消耗。 1.弯曲件的材料
要求:具有良好的塑性,屈强比(s/b)小,屈服点与弹性模 量的比值(s/E)小。 2.弯曲件的结构
(5)防止弯曲根部裂纹的工件结构(图3-36) (6)增添连接带和定位工艺孔(图3-37 ) (7)弯曲件尺寸的标注(图3-38 )
图3-33 弯曲件的直边高度
图3-34 弯曲件的孔边距
图3-35 防止孔变形的措施
图3-36 防止弯曲根部裂纹
图3-37 增添连接带和定位工艺孔的弯曲件
图3-38 尺寸标注与工艺的关系
3.弯曲件的精度 弯曲件的精度受坯料定位、偏移、翘曲和回弹等因素的影
响,弯曲的工序数目越多,精度也越低。
冲掌握弯曲件的工艺分析。
能力目标: 1、提高对弯曲件工艺分析的能力,提高工件质量, 减少废品率。
良好弯曲工艺的优点:能提高工件质量,减少废品率,而且 能简化工艺和模具结构,降低材料消耗。 1.弯曲件的材料
要求:具有良好的塑性,屈强比(s/b)小,屈服点与弹性模 量的比值(s/E)小。 2.弯曲件的结构
电子课件-《冷冲压模具制作》-B01-2679 冷冲压模具制作 模块三
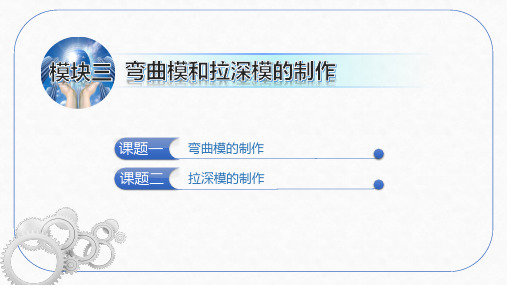
圆筒拉深模
(1) 凸模的加工
凸模
(2) 凹模的加工 图所示为拉深模凹模零件图,该零件属于圆盘零件,车削加工,加工过程 中需要车削心轴辅助装夹工件。M8 螺纹孔、ϕ8mm 销钉孔均留在装配过程中 加工。
凹模
(3) 凸模固定板的加工 图所示为拉深模的凸模固定板零件图,都属于圆盘零件。在加工过程中应 根据零件圆孔尺寸,加工心轴辅助装夹工件。M8 螺纹孔、ϕ11mm 螺纹过孔、 ϕ8mm 销钉孔均留在装配过程中加工。
(3) 拉深凸模的出气孔尺寸 凸模通气孔,以防止当工件脱离凸模时在凸模端头与工件底部之间形成真 空,增加额外的卸件力,严重时会损伤工件。
3. 工作原理
表为圆筒拉深模一次成形的整个加工过程,包含制件定位、压料、冲压成
形等过程。
圆筒拉深模加工过程
圆筒拉深模加工过程
二、拉深模零件加工、装配与调试
1. 拉深模零件加工 图所示的圆筒拉深模各零件均为回转件,主要采用车削加工工艺制作而成。
凸模固定板
(4) 压料板的加工 图所示为拉深模的压料板零件图,属于圆盘零件。在加工过程中应根据零 件圆孔尺寸,加工心轴辅助装夹工件。M8 螺纹孔留在装配过程中加工。
压料板
(5) 上模座的加工 图所示为拉深模的上模座零件图,属于圆盘零件。在加工过程中应根据零件 圆孔尺寸,加工心轴辅助装夹工件。ϕ8mm 销孔、ϕ12mm 螺钉安装孔、ϕ9mm 螺钉安装孔留在装配过程中加工。
上模座
(6) 下模座的加工 图所示为拉深模的下模座零件图,属于圆盘零件。在加工过程中应根据零件 圆孔尺寸,加工心轴辅助装夹工件。ϕ9 螺钉安装孔留在装配过程中加工。
下模座
(7) 模柄的加工 图所示为模柄零件图。
模柄
2. 拉深模装配与调试 (1) 下模装配
(1) 凸模的加工
凸模
(2) 凹模的加工 图所示为拉深模凹模零件图,该零件属于圆盘零件,车削加工,加工过程 中需要车削心轴辅助装夹工件。M8 螺纹孔、ϕ8mm 销钉孔均留在装配过程中 加工。
凹模
(3) 凸模固定板的加工 图所示为拉深模的凸模固定板零件图,都属于圆盘零件。在加工过程中应 根据零件圆孔尺寸,加工心轴辅助装夹工件。M8 螺纹孔、ϕ11mm 螺纹过孔、 ϕ8mm 销钉孔均留在装配过程中加工。
(3) 拉深凸模的出气孔尺寸 凸模通气孔,以防止当工件脱离凸模时在凸模端头与工件底部之间形成真 空,增加额外的卸件力,严重时会损伤工件。
3. 工作原理
表为圆筒拉深模一次成形的整个加工过程,包含制件定位、压料、冲压成
形等过程。
圆筒拉深模加工过程
圆筒拉深模加工过程
二、拉深模零件加工、装配与调试
1. 拉深模零件加工 图所示的圆筒拉深模各零件均为回转件,主要采用车削加工工艺制作而成。
凸模固定板
(4) 压料板的加工 图所示为拉深模的压料板零件图,属于圆盘零件。在加工过程中应根据零 件圆孔尺寸,加工心轴辅助装夹工件。M8 螺纹孔留在装配过程中加工。
压料板
(5) 上模座的加工 图所示为拉深模的上模座零件图,属于圆盘零件。在加工过程中应根据零件 圆孔尺寸,加工心轴辅助装夹工件。ϕ8mm 销孔、ϕ12mm 螺钉安装孔、ϕ9mm 螺钉安装孔留在装配过程中加工。
上模座
(6) 下模座的加工 图所示为拉深模的下模座零件图,属于圆盘零件。在加工过程中应根据零件 圆孔尺寸,加工心轴辅助装夹工件。ϕ9 螺钉安装孔留在装配过程中加工。
下模座
(7) 模柄的加工 图所示为模柄零件图。
模柄
2. 拉深模装配与调试 (1) 下模装配
冷冲压工艺与模具设计
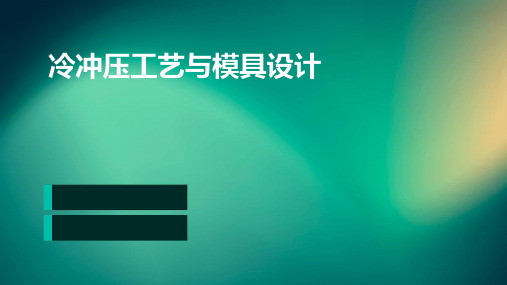
多工位级进模是一种高效率的冲模,可在一 副模具上完成多个工件的加工。设计时需考 虑工件的排列方式、送料方式、定位精度等 因素,确保生产效率和产品质量。
典型复合模和多工位级进模结构分析
典型复合模结构分析
以落料、冲孔复合模为例,其结构包括上模 、下模和导柱导套等部分。上模装有冲孔凸 模和落料凹模,下模装有卸料板、导料板和 定位销等。工作时,上模下行完成冲孔和落 料工序,废料从卸料板排出。
冷冲压工艺与模具设计
contents
目录
• 冷冲压工艺概述 • 冷冲压模具设计基础 • 冲裁工艺与模具设计 • 弯曲工艺与模具设计 • 拉深工艺与模具设计 • 其他冷冲压工艺与模具设计
01 冷冲压工艺概述
冷冲压定义及特点
冷冲压定义
冷冲压是在常温下利用冲模在压力机 上对材料施加压力,使其产生分离或 变形,从而获得一定形状、尺寸和性 能的产品零件的加工方法。
工序的冲裁模。生产效率高,但结构复杂,制造难度较大,适用于形状
复杂、精度要求高的零件生产。
Байду номын сангаас
04 弯曲工艺与模具设计
弯曲变形过程分析
01
02
03
弹性变形阶段
凸模开始接触坯料并下压, 坯料发生弹性压缩和弯曲。
塑性变形阶段
随着凸模继续下压,坯料 产生塑性变形,弯曲程度 逐渐增大。
校正阶段
弯曲变形完成后,凸模回 程,弯曲件在弹性恢复作 用下得到校正。
复合式拉深模
03
结合多种模具结构的特点,实现多工位连续拉深,提高生产效
率和产品质量。
06 其他冷冲压工艺与模具设 计
成形工艺原理及分类
成形工艺原理
冷冲压成形工艺是利用模具使金属板 材在室温下产生塑性变形,从而获得 所需形状、尺寸和性能的零件的加工 方法。
模块三U型弯曲模PPT课件
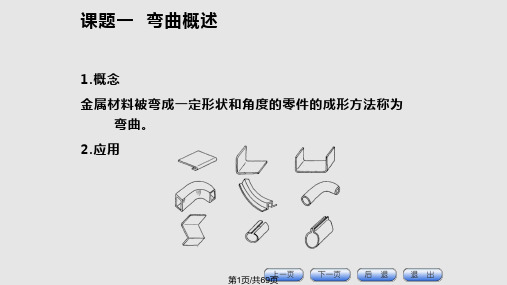
(1)最小相对弯曲半径
概念:
在自由弯曲保证坯料最外层纤维不发生
破裂的前提下,所能获得的弯曲件内表面最小圆
角半径与弯曲材料厚度的比rm值in / t
,称为最
小相对弯曲半径。
意义:外
aa 00
oo
(r1
)
r1
(r t) (r t / 2) t / 2
rt/2
rt/2
2
1 r
1
t
第9页/共69页
(2)最小弯曲半径的影响因素
1)材料的塑性和热处理状态 :材料塑性越好,最小相 对弯曲半径可越小。 2)坯料的边缘及表面状态 :应将毛刺和其他缺陷置于 弯曲内侧。
3)弯曲方向 :弯曲方向与纤 维方向垂直时,对弯曲有利。
4)弯曲角a :弯曲角a越大, 最小相对弯曲半径越小。
第10页/共69页
(3)防止弯裂的措施 • 退火、加热弯曲 • 消除冲裁毛刺 • 两次弯曲(先加大弯曲半径,退火后再按工件
1)
第14页/共69页
三、减小回弹的措施
1)改进零件的设计
第15页/共69页
2)从弯曲工艺上采取措施 如采用校正弯曲、拉弯等工艺以减小回弹值。
拉弯用模
第16页/共69页
3)从模具结构上采取措施
补偿回弹的方法
改变凸模形状减小回弹
增加拉应变减小回弹
端部加压减小回弹 第17页/共69页
四、弯曲时的偏移
第32页/共69页
二. 校正弯曲时的弯曲力
F校 Ap
F校 ——校正弯曲应力; A ——校正部分投影面积; p ——单位面积校正力。
三. 顶件力或压料力
若弯曲模设有顶件装置或压料装置,其顶件力 FD(或
压料力 FY )可近似取自由弯曲力的30~80%, 即
《冷冲模工艺与设计》课件——课题二十九:弯曲模的典型结构

图3-8 U形件弯曲模
图3-9 弯曲角小于90°的U形件弯曲模
3、Z形件弯曲模 (图3-11) 由于Z形件两直边折弯方向相反,所以弯曲模必须有两个方
向弯曲的动作。
图3-11 Z形件弯曲模
4、
形件弯曲模
形零件,也称为四角弯曲件。可以一次弯曲成形,
也可以分两次弯曲成形。
图3-13 四角弯曲件一次弯曲成形模具
图3-15 两次弯曲复合的
形件弯曲模
图3-14
形件分步弯曲模
5、圆形件弯曲模 1) 直径d≥5mm的先弯成 U形,再弯成圆形(图3-17)。 2)圆筒直径d≥20mm的先将毛坯弯成波浪状,然后再弯成圆筒形, (图3-18、图3-19)。
图3-18 大圆两次弯曲模
图3-17 小圆弯曲模
图3-19 摆块式圆形件一次弯曲成形模
冲压工艺与模具结构课题二十九:弯曲源自的典型结构(2)知识目标:
1、掌握单工序弯曲模、连续弯曲模和复合弯曲模的典 型结构和工作原理。
能力目标: 1、能够根据弯曲模的结构图说出模具零件的名称和 模具的工作原理。
弯曲模按其工序组合形式分类可以分为单工序弯曲模、复合 弯曲模和连续弯曲模。 3.2.1单工序弯曲模 1、V形件弯曲模 (图3-7) 特点:是结构简单、通用性好,但是精度不高 弯曲方法:带有定位尖(图3-6b),顶杆(图3-6c)、 V形顶块(图 3-6d)
弯曲模结构要点: ① 弯曲毛坯的定位要准 确、可靠,尽可能水平放 置。 ② 毛坯的安放和制件的 取出要方便、安全,操作 简单。 ③ 模具结构尽量简单并 且便于调整修理。
图3-23 复合弯曲模
6、铰链件弯曲模 (图3-20、图3-21) 铰链件通常是将毛坯头部预压弯后才能卷圆。
模具设计第3章弯曲工艺与弯曲模课件

b/t>3宽板弯曲,横断面几乎 不变
b/t<3窄板弯曲,断面产生了 畸变 ,外窄内宽
3.1.4 弯曲件的结构工艺性
弯曲件的结构工艺性是指弯曲零件的形状、 尺寸、精度、材料以及技术要求等是否符合弯 曲加工的工艺要求。具有良好工艺性的弯曲件, 能简化弯曲的工艺过程及模具结构,提高工件 的质量。
1. 弯曲件的形状 弯曲件形状对称,对应r 相等
播放动画
1-顶杆 2-定位钉 3-模柄 4-凸模 5-凹模 6-下模座
3. L形件弯曲 适用于两直边长度相差较大的单角弯曲件
a)竖边无校正
b)竖边可校正
L形件弯曲
4.复杂零件 多次V形弯曲制造复杂零件举例
3.2.2 U形件弯曲模
1.U形件弯曲模的一般结构形式
U 形 件 弯 曲 模
1.凸模 2.凹模 3.弹簧 4.凸模活动镶块 5.凹模活动镶块 6.定位销 7.转轴 8.顶板 9.凹模活动镶块
弯曲半径r>0.5t: 按中性层不变原理,坯料总长度应等于弯曲 件直线部分和圆弧段长度之和,即:
提问:下面的弯曲件展开长度如何计算?
L
l1
l2
l3
π α1 180
(r1
xt
)
π α2 180
S / E 越大,回弹越大。
E1>E2
1 2
.
1 2
图a)
E3=E4
3 4
3 4
图b)
材料的力学性能对回弹值的影响 1、3-退火软钢 2-软锰黄铜 4-经冷变形硬化的软钢
应尽量选择屈服极限小、n值小的材料以获得 形状规则、尺寸精确的弯曲件。
(2)相对弯曲半径r/t r/t越小,变形程度越大,回弹量减小。
例:1mm厚铝板、65Mn板,弯曲时易裂,退火后 再弯,则弯曲正常。
b/t<3窄板弯曲,断面产生了 畸变 ,外窄内宽
3.1.4 弯曲件的结构工艺性
弯曲件的结构工艺性是指弯曲零件的形状、 尺寸、精度、材料以及技术要求等是否符合弯 曲加工的工艺要求。具有良好工艺性的弯曲件, 能简化弯曲的工艺过程及模具结构,提高工件 的质量。
1. 弯曲件的形状 弯曲件形状对称,对应r 相等
播放动画
1-顶杆 2-定位钉 3-模柄 4-凸模 5-凹模 6-下模座
3. L形件弯曲 适用于两直边长度相差较大的单角弯曲件
a)竖边无校正
b)竖边可校正
L形件弯曲
4.复杂零件 多次V形弯曲制造复杂零件举例
3.2.2 U形件弯曲模
1.U形件弯曲模的一般结构形式
U 形 件 弯 曲 模
1.凸模 2.凹模 3.弹簧 4.凸模活动镶块 5.凹模活动镶块 6.定位销 7.转轴 8.顶板 9.凹模活动镶块
弯曲半径r>0.5t: 按中性层不变原理,坯料总长度应等于弯曲 件直线部分和圆弧段长度之和,即:
提问:下面的弯曲件展开长度如何计算?
L
l1
l2
l3
π α1 180
(r1
xt
)
π α2 180
S / E 越大,回弹越大。
E1>E2
1 2
.
1 2
图a)
E3=E4
3 4
3 4
图b)
材料的力学性能对回弹值的影响 1、3-退火软钢 2-软锰黄铜 4-经冷变形硬化的软钢
应尽量选择屈服极限小、n值小的材料以获得 形状规则、尺寸精确的弯曲件。
(2)相对弯曲半径r/t r/t越小,变形程度越大,回弹量减小。
例:1mm厚铝板、65Mn板,弯曲时易裂,退火后 再弯,则弯曲正常。
冷冲压工艺与模具设计之U形件弯曲模(ppt 91页)
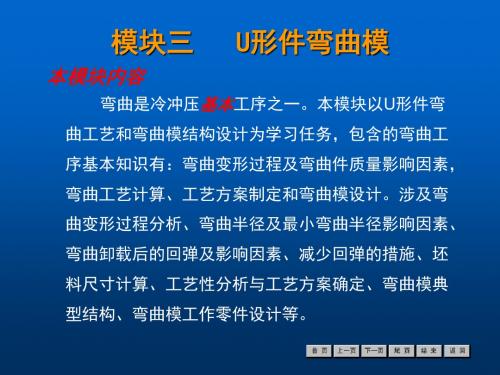
b ——材料的抗拉强度;
K——安全系数,一般取K=1.3。
二 校正弯曲时的弯曲力
F校 Ap
式中: F校 ——校正弯曲应力; A——校正部分投影面积; P——单位面积校正力,其值见表3-9。
三 顶件力或压料力
若弯曲模设有顶件装置或压料装置,其顶件力 FD (或压料力 FY )可近似取自由弯曲力的30%~80%。即
对于形状比较复杂或精度要求高的弯曲件,在利用下述
公式初步计算坯料长度后,还需反复试弯不断修正,才能最
后确定坯料的形状及尺寸。
1.圆角半径r>0.5t的弯曲件
按中性层展开的原理,坯 料总长度应等于弯曲件直线部 分和圆弧部分长度之和,即
L z l1 l2 18 0 l1 l2 18 (r 0 x)t
模块三 U形件弯曲模
本模块内容
弯曲是冷冲压基本工序之一。本模块以U形件弯
曲工艺和弯曲模结构设计为学习任务,包含的弯曲工 序基本知识有:弯曲变形过程及弯曲件质量影响因素, 弯曲工艺计算、工艺方案制定和弯曲模设计。涉及弯 曲变形过程分析、弯曲半径及最小弯曲半径影响因素、 弯曲卸载后的回弹及影响因素、减少回弹的措施、坯 料尺寸计算、工艺性分析与工艺方案确定、弯曲模典 型结构、弯曲模工作零件设计等。
也不宜过大,因为过大时,受到回弹的影响,弯曲角度与 弯曲半径的精度都不易保证。
三 弯曲件的结构
2.弯曲件的形状
一般要求弯曲件形状对称,弯曲半径左右一致,则弯曲 时坯料受力平衡而无滑动。
三 弯曲件的结构
3.弯曲件高度
弯曲件的直边高度不 宜过小,其值应为
h>r+2t
三 弯曲件的结构
4.防止弯曲根部裂纹的工件结构 在局部弯曲某一段边缘时,为避免弯曲根部撕裂,应
K——安全系数,一般取K=1.3。
二 校正弯曲时的弯曲力
F校 Ap
式中: F校 ——校正弯曲应力; A——校正部分投影面积; P——单位面积校正力,其值见表3-9。
三 顶件力或压料力
若弯曲模设有顶件装置或压料装置,其顶件力 FD (或压料力 FY )可近似取自由弯曲力的30%~80%。即
对于形状比较复杂或精度要求高的弯曲件,在利用下述
公式初步计算坯料长度后,还需反复试弯不断修正,才能最
后确定坯料的形状及尺寸。
1.圆角半径r>0.5t的弯曲件
按中性层展开的原理,坯 料总长度应等于弯曲件直线部 分和圆弧部分长度之和,即
L z l1 l2 18 0 l1 l2 18 (r 0 x)t
模块三 U形件弯曲模
本模块内容
弯曲是冷冲压基本工序之一。本模块以U形件弯
曲工艺和弯曲模结构设计为学习任务,包含的弯曲工 序基本知识有:弯曲变形过程及弯曲件质量影响因素, 弯曲工艺计算、工艺方案制定和弯曲模设计。涉及弯 曲变形过程分析、弯曲半径及最小弯曲半径影响因素、 弯曲卸载后的回弹及影响因素、减少回弹的措施、坯 料尺寸计算、工艺性分析与工艺方案确定、弯曲模典 型结构、弯曲模工作零件设计等。
也不宜过大,因为过大时,受到回弹的影响,弯曲角度与 弯曲半径的精度都不易保证。
三 弯曲件的结构
2.弯曲件的形状
一般要求弯曲件形状对称,弯曲半径左右一致,则弯曲 时坯料受力平衡而无滑动。
三 弯曲件的结构
3.弯曲件高度
弯曲件的直边高度不 宜过小,其值应为
h>r+2t
三 弯曲件的结构
4.防止弯曲根部裂纹的工件结构 在局部弯曲某一段边缘时,为避免弯曲根部撕裂,应
3冷冲压工艺与模具设计第三章
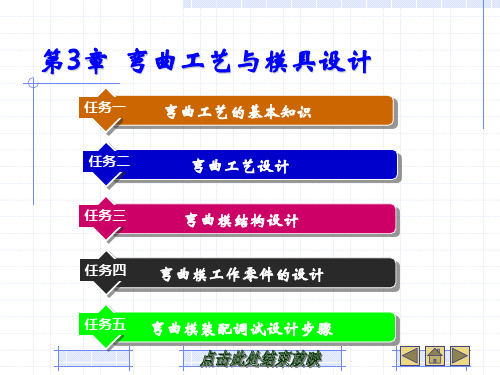
阶段二 弯曲时凸模与凹模宽度尺寸
根据工件尺寸的标注方式不同
,凸模与凹模的宽度尺寸可按表 3-12所列公式进行计算。
阶段三 弯曲时模具圆角半径与凹模深 度
1、凸模圆角半径rp 2、凹模圆角半径rd 3、凹模深度
任务五 弯曲模的装配调试与设计步骤
阶段一 弯曲模的装配与调试 阶段二 弯曲模的设计步骤与实例
阶段一 弯曲模的装配与调试
1、弯曲模的装配 弯曲模的装配方法基本上与冲
裁模相同,即确定装配基准件和 装配顺序,并按基准件装配有关 部件,即上模、下模、压料装置 、顶件装置及模具间隙的初调。
2、弯曲模的调试
弯曲模装配后需要安装在压力 机上试冲,并根据试冲得到的情 况进行调整或修正。弯曲模在试 冲过程中的常见问题、产生原因 及调整方法见表3-14。
则弯曲角变化量为Δα=α-αp
则弯曲半径变化量为Δr=r-rp
2、影响回弹的因素 (1)材料的力学性能 (2)相对弯曲半径r/t (3)弯曲工件的形状 (4)模具间隙 (5)弯曲力
3、回弹值的确定
(1)大变形自由弯曲(r/t>5)时,由于 弯曲半径的变化不大,可忽略不计,只考 虑角度的回弹。当弯曲角度不为90º时,回 弹角应作如下修改:
阶段三 最小弯曲半径
1、影响最小弯曲半径rmin的因素 (1)材料的力学性能 (2)材料表面和侧面的质量 (3)弯曲线的方向 (4)弯曲中心角α
2、最小弯曲半径rmin的数值 各种金属材料在不同状态下的最小弯曲半径的
数值,参见表3-1 3、提高弯曲极限变形程度的方法 (1)经冷变形硬化的材料,可采用热处理的方 法恢复其塑性,再进行弯曲。
(4)防止弯曲根部裂纹的工件结构
(5)弯曲件孔边距离 当t<2mm时,l≥t 当t≥2mm时,l≥2t
相关主题