磷化底漆配方
磷化液配方及制作方法
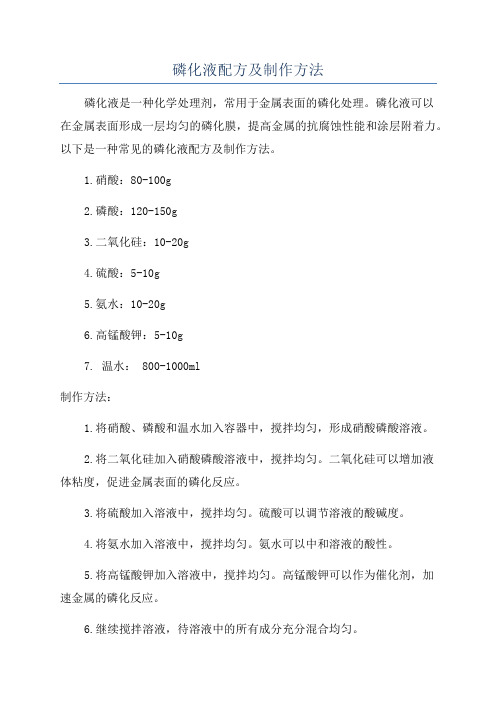
磷化液配方及制作方法磷化液是一种化学处理剂,常用于金属表面的磷化处理。
磷化液可以在金属表面形成一层均匀的磷化膜,提高金属的抗腐蚀性能和涂层附着力。
以下是一种常见的磷化液配方及制作方法。
1.硝酸:80-100g2.磷酸:120-150g3.二氧化硅:10-20g4.硫酸:5-10g5.氨水:10-20g6.高锰酸钾:5-10g7. 温水: 800-1000ml制作方法:1.将硝酸、磷酸和温水加入容器中,搅拌均匀,形成硝酸磷酸溶液。
2.将二氧化硅加入硝酸磷酸溶液中,搅拌均匀。
二氧化硅可以增加液体粘度,促进金属表面的磷化反应。
3.将硫酸加入溶液中,搅拌均匀。
硫酸可以调节溶液的酸碱度。
4.将氨水加入溶液中,搅拌均匀。
氨水可以中和溶液的酸性。
5.将高锰酸钾加入溶液中,搅拌均匀。
高锰酸钾可以作为催化剂,加速金属的磷化反应。
6.继续搅拌溶液,待溶液中的所有成分充分混合均匀。
7.将制作好的磷化液过滤,去除悬浮颗粒和杂质,得到清澈的磷化液。
使用磷化液时,应注意以下事项:1.磷化液的pH值通常在1-3之间,酸性较强,请在操作时佩戴防护手套、护目镜和防护服,避免溅入皮肤和眼睛。
2.使用磷化液时,应先清洗金属表面的油污和氧化物,确保表面干净。
3.将金属置于磷化液中浸泡一段时间,通常为10-30分钟,可以根据具体情况调整。
4.浸泡时间过长可能导致磷化膜过厚,降低涂层附着力;浸泡时间过短可能导致磷化膜过薄,影响金属的抗腐蚀性能。
5.浸泡结束后,用清水冲洗金属表面,去除多余的磷化液,然后干燥金属。
总之,磷化液的制作方法相对简单,但在使用时需要注意安全和正确操作步骤,以确保磷化效果和金属表面的质量。
磷化液配方总
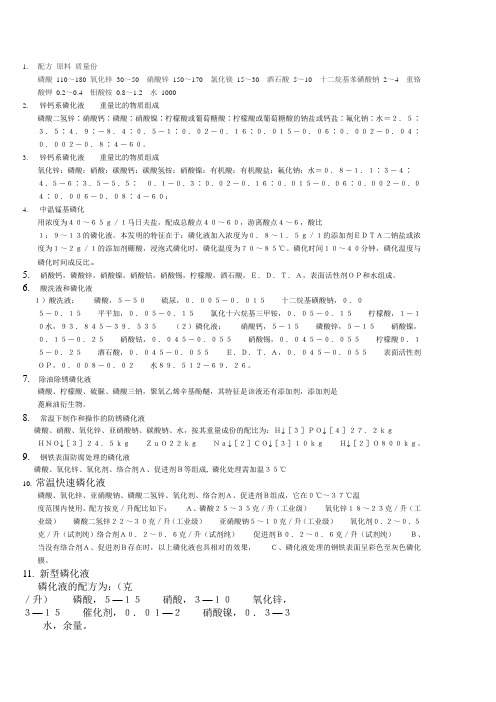
1.配方原料质量份磷酸110~180 氧化锌30~50 硝酸锌150~170 氯化镁15~30 酒石酸5~10 十二烷基苯磺酸钠2~4 重铬酸钾0.2~0.4 钼酸铵0.8~1.2 水10002. 锌钙系磷化液重量比的物质组成磷酸二氢锌∶硝酸钙∶磷酸∶硝酸镍∶柠檬酸或葡萄糖酸∶柠檬酸或葡萄糖酸的钠盐或钙盐∶氟化钠∶水=2.5∶3.5∶4.9∶-8.4∶0.5-1∶0.02-0.16∶0.015-0.06∶0.002-0.04∶0.002-0.8∶4-60。
3. 锌钙系磷化液重量比的物质组成氧化锌:磷酸:硝酸:碳酸钙:碳酸氢铵:硝酸镍:有机酸:有机酸盐:氟化钠:水=0.8-1.1∶3-4∶4.5-6∶3.5-5.5∶0.1-0.3∶0.02-0.16∶0.015-0.06∶0.002-0.04∶0.006-0.08∶4-60;4. 中温锰基磷化用浓度为40~65g/1马日夫盐,配成总酸点40~60,游离酸点4~6,酸比1:9~13的磷化液。
本发明的特征在于:磷化液加入浓度为0.8~1.5g/1的添加剂EDTA二钠盐或浓度为1~2g/1的添加剂硼酸,浸泡式磷化时,磷化温度为70~85℃。
磷化时间10~40分钟,磷化温度与磷化时间成反比。
5. 硝酸钙,磷酸锌,硝酸镍,硝酸钴,硝酸锡,柠檬酸,酒石酸,E.D.T.A,表面活性剂OP和水组成。
6. 酸洗液和磷化液1)酸洗液:磷酸,5-50硫尿,0.005-0.015十二烷基磺酸钠,0.05-0.15平平加,0.05-0.15氯化十六烷基三甲铵,0.05-0.15柠檬酸,1-10水,93.845-39.535(2)磷化液:硝酸钙,5-15磷酸锌,5-15硝酸镍,0.15-0.25硝酸钴,0.045-0.055硝酸锡,0.045-0.055柠檬酸0.15-0.25酒石酸,0.045-0.055E.D.T.A,0.045-0.055表面活性剂OP,0.008-0.02水89.512-69.26。
(完整版)磷化处理技术+配方
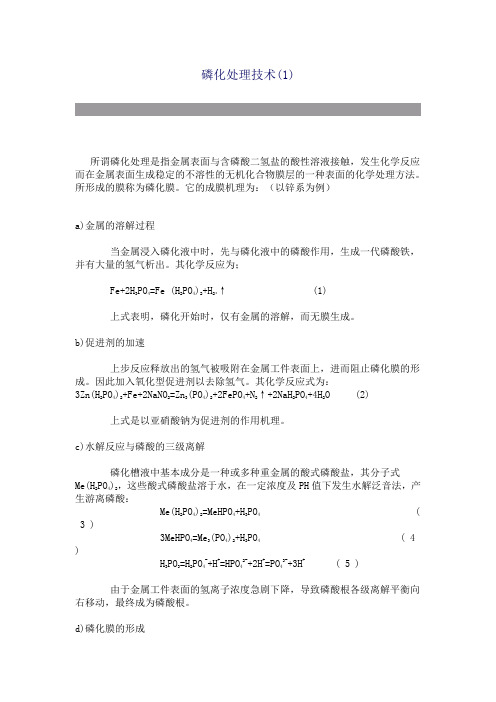
磷化处理技术(1)所谓磷化处理是指金属表面与含磷酸二氢盐的酸性溶液接触,发生化学反应而在金属表面生成稳定的不溶性的无机化合物膜层的一种表面的化学处理方法。
所形成的膜称为磷化膜。
它的成膜机理为:(以锌系为例)a)金属的溶解过程当金属浸入磷化液中时,先与磷化液中的磷酸作用,生成一代磷酸铁,并有大量的氢气析出。
其化学反应为;Fe+2H3PO4=Fe (H2PO4)2+H2•↑ (1)上式表明,磷化开始时,仅有金属的溶解,而无膜生成。
b)促进剂的加速上步反应释放出的氢气被吸附在金属工件表面上,进而阻止磷化膜的形成。
因此加入氧化型促进剂以去除氢气。
其化学反应式为:3Zn(H2PO4)2+Fe+2NaNO2=Zn3(PO4)2+2FePO4+N2↑+2NaH2PO4+4H2O (2) 上式是以亚硝酸钠为促进剂的作用机理。
c)水解反应与磷酸的三级离解磷化槽液中基本成分是一种或多种重金属的酸式磷酸盐,其分子式Me(H2PO4)2,这些酸式磷酸盐溶于水,在一定浓度及PH值下发生水解泛音法,产生游离磷酸:Me(H2PO4)2=MeHPO4+H3PO4(3 )3MeHPO4=Me3(PO4)2+H3PO4( 4)H3PO3=H2PO4-+H+=HPO42-+2H+=PO43-+3H+( 5 )由于金属工件表面的氢离子浓度急剧下降,导致磷酸根各级离解平衡向右移动,最终成为磷酸根。
d)磷化膜的形成当金属表面离解出的三价磷酸根与磷化槽液中的(工件表面)的金属离子(如锌离子、钙离子、锰离子、二价铁离子)达到饱和时,即结晶沉积在金属工件表面上,晶粒持续增长,直至在金属工件表面上生成连续的不溶于水的黏结牢固的磷化膜。
2Zn2++Fe2++2PO43-+4H2O→Zn2Fe (PO4)2•4H2O↓ ( 6 )3Zn2++2PO42-+4H2O=Zn3(PO4)2•4H2O ↓( 7 )金属工件溶解出的二价铁离子一部分作为磷化膜的组成部分被消耗掉,而残留在磷化槽液中的二价铁离子,则氧化成三价铁离子,发生(2)式的化学反应,形成的磷化沉渣其主要成分是磷酸亚铁,也有少量的Me3(PO4)2。
磷化液配方

磷化液配方与配制磷化是金属材料防腐蚀的重要方法之一,其目的在于给基体金属提供防腐蚀保护,用于喷漆前打底、提高覆膜层的附着力与防腐蚀能力及在金属加工中起减摩润滑作用等。
按用途可分为三类:涂装性磷化;冷挤压润滑磷化;装饰性磷化。
按所用的磷酸盐分类有:磷酸锌系、磷酸锌钙系、磷酸铁系、磷酸锌锰系、磷酸锰系。
根据磷化温度分类有:高温(80°C 以上)磷化、中温(50~70°C)磷化、低温磷化(40°C左右)和常温磷化(10~30°C)。
除了能产生灰色到黑色磷化膜外,还可以做黑色磷化。
目前,有关黑色磷化技术可以分成两种类型。
一种是改造原磷化液的配方,使磷化膜的颜色变为黑色;另外一种是将常温发黑和磷化分两步对钢铁进行表面处理。
即先用常温发黑工艺对钢铁进行发黑,得到较好的黑色外观,再进行磷化处理以提高表面膜的附着力和耐蚀性。
微谱技术长期做磷化液配方还原,磷化液配方分析,对其组分做定性定量分析,产品性能改进等——微谱分析法提供了“金属表面处理剂”行业的综合技术解决方案。
常温磷化液配方(质量份)原料1号2号原料1号2号磷酸 4 3 硼氟酸钠0.8 0.5氧化锌0.55 0.5 氯酸钠 2.5 2.5硝酸锌 1.5 1 柠檬酸 2 1硝酸镍 3 3.5 软化水加至100硝酸锰 3.5 3制备方法首先将氧化锌用少量混合湿润,加入磷酸,溶解完全后,再加入其他原料,搅拌均匀即可。
原料配伍本品各组分质量份配比范围为:磷酸2~4、氧化锌0.4~0.6、硝酸锌0.5~1.5、硝酸镍3~5、硝酸锰2~4、硼氟酸钠0.2~1、氯酸钠2~3、柠檬酸0.5~2、软化水加至100本品由于加入了复合加速剂和复合钝化剂——硝酸镍、硝酸锰、硼氟酸钠和氯酸钠,使磷化膜与工件的结合速度快,结合更牢固。
使磷化液磷化速度加快,并使成膜和强度大。
产品特性本品方法简单,被处理工件先要经预处理、脱脂、表调等工艺,使用工件表面无油、无锈及赃物,采用浸渍或喷淋方法施工,在常温下处理3~5min,无需加热,节省能源,操作方便。
磷化液配制方法
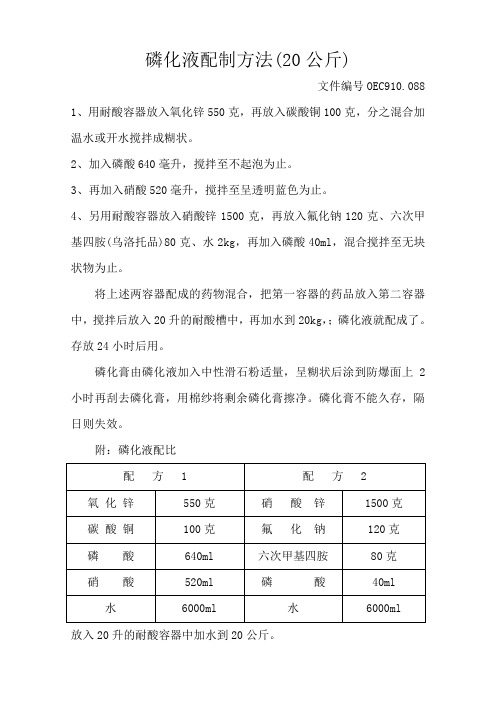
磷化液配制方法(20公斤)文件编号OEC910.088 1、用耐酸容器放入氧化锌550克,再放入碳酸铜100克,分之混合加温水或开水搅拌成糊状。
2、加入磷酸640毫升,搅拌至不起泡为止。
3、再加入硝酸520毫升,搅拌至呈透明蓝色为止。
4、另用耐酸容器放入硝酸锌1500克,再放入氟化钠120克、六次甲基四胺(乌洛托品)80克、水2kg,再加入磷酸40ml,混合搅拌至无块状物为止。
将上述两容器配成的药物混合,把第一容器的药品放入第二容器中,搅拌后放入20升的耐酸槽中,再加水到20kg,;磷化液就配成了。
存放24小时后用。
磷化膏由磷化液加入中性滑石粉适量,呈糊状后涂到防爆面上2小时再刮去磷化膏,用棉纱将剩余磷化膏擦净。
磷化膏不能久存,隔日则失效。
附:磷化液配比放入20升的耐酸容器中加水到20公斤。
磷化操作工艺说明1、用醇酸稀料或酒精清洗隔爆面上的油脂、污物。
2、用细纱布把隔爆面去锈,再用干净的棉纱擦干净,不得用化学的方法使隔爆面漏出金属光泽。
3、按冷磷化处理工艺守则文件编号OEC910.088配置的磷化液与滑石粉搅拌均匀,成为磷化涂膏。
4、涂膏前,隔爆面必须干燥,光泽干净。
5、将磷化膏均匀的涂在隔爆面上,厚度为2-4毫米,不得漏出金属表面,室温在30℃左右时,磷化时间为半小时,室温在20℃左右时,时间为5-10小时,室温在0度左右时,时间为20小时,涂膏时速度要快。
6、磷化膏不能长时间存放,超过24小时后,则失效。
7、金属表面涂膏后,用非金属刮刀除去涂膏,再用水冲洗干净,使金属表面出现一层棕色而均匀的磷化膜。
8、为了提高抗腐能力,可再涂上一层微薄的防锈油,如:石油碳酸钡,凡士林等油脂,若采用机油与石油碳酸钡各50%的混合液防锈效果更好。
常温磷化液的配方
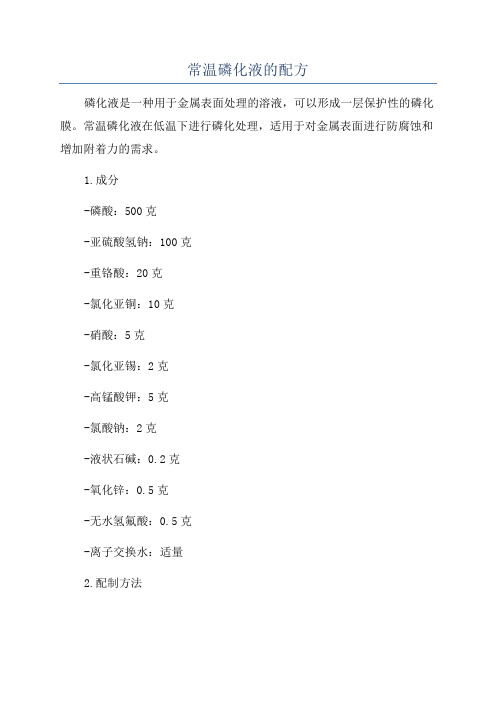
常温磷化液的配方
磷化液是一种用于金属表面处理的溶液,可以形成一层保护性的磷化膜。
常温磷化液在低温下进行磷化处理,适用于对金属表面进行防腐蚀和增加附着力的需求。
1.成分
-磷酸:500克
-亚硫酸氢钠:100克
-重铬酸:20克
-氯化亚铜:10克
-硝酸:5克
-氯化亚锡:2克
-高锰酸钾:5克
-氯酸钠:2克
-液状石碱:0.2克
-氧化锌:0.5克
-无水氢氟酸:0.5克
-离子交换水:适量
2.配制方法
1)首先用离子交换水稀释磷酸,将500克磷酸稀释至1000毫升,搅拌均匀。
2)将亚硫酸氢钠加入到磷酸溶液中,搅拌溶解。
3)在容器中加入重铬酸、氯化亚铜、硝酸、氯化亚锡、高锰酸钾、氯酸钠和液状石碱,搅拌均匀。
4)在溶液中加入氧化锌搅拌溶解。
5)最后,在溶液中加入少量无水氢氟酸,搅拌均匀。
3.使用方法
1)首先,将金属零件清洗干净,去除表面的油脂和污垢。
2)将金属零件完全浸泡在配制好的磷化液中,保持一定时间。
浸泡时间的长短取决于所需的磷化层厚度。
3)期间可以加热溶液,加快反应速度。
加热时需要注意控制温度,防止溶液过热。
4)磷化结束后,将金属零件从磷化液中取出,用清水彻底冲洗干净。
5)最后,将金属零件晾干或用热风吹干。
环氧玻璃鳞片漆组成及配方

环氧玻璃鳞片漆组成及配方
优质玻璃鳞片防腐漆;由合成树脂+增塑剂+触角剂+偶联剂、玻璃鳞片+颜料+溶剂组成;重庆环氧玻璃鳞片漆——科@冠玻璃鳞片在涂层中作用(抗渗透作用);玻璃鳞片化学成分;玻璃鳞片主要成分是二氧化硅;耐酸耐碱玻璃Na2OK29.6%;含sio264.6%;为了提高玻璃鳞片的增水性;悬浮性和分散性;增加与树脂的粘接力;采用偶联剂对玻璃鳞片表面进行处理。
组成:以环氧树脂、煤焦沥青、玻璃鳞片、有机溶剂、固化剂等配置而成;是双组分自干型重防腐涂料。
性能与用途:漆膜硬度高、附着力强;耐磨,抗冲击,具有良好的防腐蚀性能。
耐水性和防锈性比环氧玻璃鳞片涂料更好,价格便宜。
适用于对防腐蚀、耐磨蚀要求较高的环境;甲:乙=20:3;现用现配;4h完成。
施工时对金属表面处理干净;涂2道漆;没道漆膜干后厚度80-100um;
技术指标:。
重庆乙烯磷化底漆
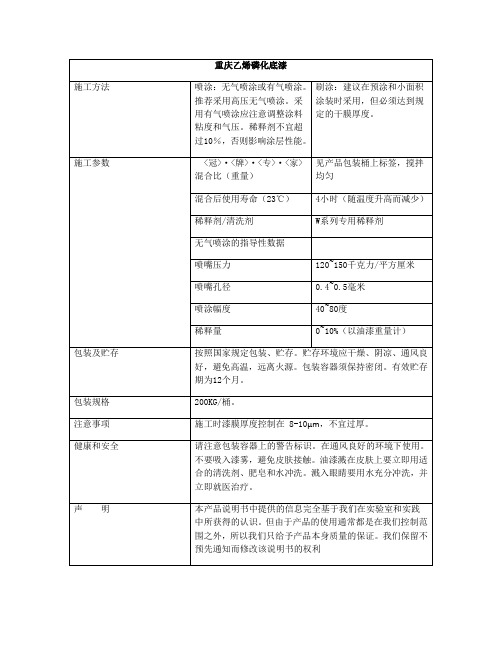
施工参数
按照国家规定包装、贮存。贮存环境应干燥、阴凉、通风良 好,避免高温,远离火源。包装容器须保持密闭。有效贮存 期为12个月。 200KG/桶。 施工时漆膜厚度控制在 8-10μm,不宜过厚。 请注意包装容器上的警告标识。在通风良好的环境下使用。 不要吸入漆雾,避免皮肤接触。油漆溅在皮肤上要立即用适 合的清洗剂、肥皂和水冲洗。溅入眼睛要用水充分冲洗,并 立即就医治疗。 本产品说明书中提供的信息完全基于我们在实验室和实践 中所获得的认识。但由于产品的使用通常都是在我们控制范 围之外,所以我们只给予产品本身质量的保证。我们保留不 预先通知而修改该说明书的权利
重庆乙烯磷化底漆 施工方法 喷涂:无气喷涂或有气喷涂。 刷涂:建议在预涂和小面积 推荐采用高压无气喷涂。采 涂装时采用,但必须达到规 用有气喷涂应注意调整涂料 定的干膜厚度。 粘度和气压。稀释剂不宜超 过10%,否则影响涂层性能。 <冠>·<牌>·<专>·<家> 混合比(重量) 混合后使用寿命(23℃) 稀释剂/清洗剂 无气喷涂的指导性数据 喷嘴压力 喷嘴孔径 喷涂幅度 稀释量 包装及贮存 120~150千克力/平方厘米 0.4~0.5毫米 40~80度 0~10%(以油漆重量计) 见产品包装桶上标签,搅拌 均匀 4小时(随温度升高而减少) W系列专用稀释剂
包装规格 注意事项 健康和安全声明
磷化、脱脂原理和经验配方
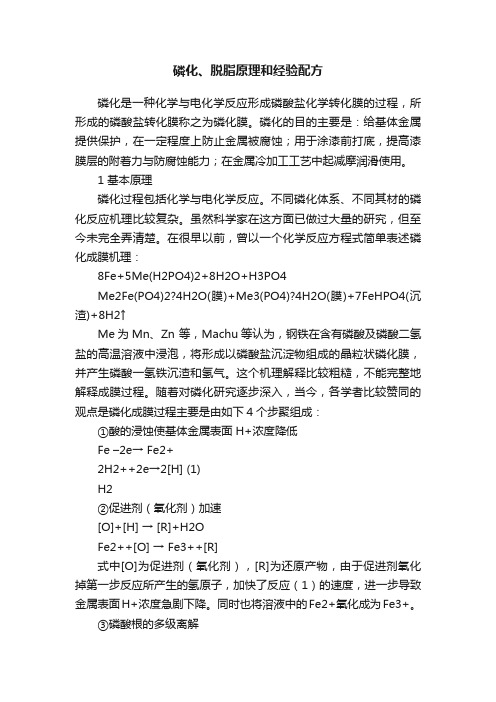
磷化、脱脂原理和经验配方磷化是一种化学与电化学反应形成磷酸盐化学转化膜的过程,所形成的磷酸盐转化膜称之为磷化膜。
磷化的目的主要是:给基体金属提供保护,在一定程度上防止金属被腐蚀;用于涂漆前打底,提高漆膜层的附着力与防腐蚀能力;在金属冷加工工艺中起减摩润滑使用。
1 基本原理磷化过程包括化学与电化学反应。
不同磷化体系、不同其材的磷化反应机理比较复杂。
虽然科学家在这方面已做过大量的研究,但至今未完全弄清楚。
在很早以前,曾以一个化学反应方程式简单表述磷化成膜机理:8Fe+5Me(H2PO4)2+8H2O+H3PO4Me2Fe(PO4)2?4H2O(膜)+Me3(PO4)?4H2O(膜)+7FeHPO4(沉渣)+8H2↑Me为Mn、Zn 等,Machu等认为,钢铁在含有磷酸及磷酸二氢盐的高温溶液中浸泡,将形成以磷酸盐沉淀物组成的晶粒状磷化膜,并产生磷酸一氢铁沉渣和氢气。
这个机理解释比较粗糙,不能完整地解释成膜过程。
随着对磷化研究逐步深入,当今,各学者比较赞同的观点是磷化成膜过程主要是由如下4个步聚组成:①酸的浸蚀使基体金属表面H+浓度降低Fe –2e→ Fe2+2H2++2e→2[H] (1)H2②促进剂(氧化剂)加速[O]+[H] → [R]+H2OFe2++[O] → Fe3++[R]式中[O]为促进剂(氧化剂),[R]为还原产物,由于促进剂氧化掉第一步反应所产生的氢原子,加快了反应(1)的速度,进一步导致金属表面H+浓度急剧下降。
同时也将溶液中的Fe2+氧化成为Fe3+。
③磷酸根的多级离解H3PO4+H2PO4-+H+ +HPO42-+2H+ +PO43-+3H-(3)由于金属表面的H+浓度急剧下降,导致磷酸根各级离解平衡向右移动,最终为PO43-。
④磷酸盐沉淀结晶成为磷化膜当金属表面离解出的PO43-与溶液中(金属界面)的金属离子(如Zn2+、Mn2+、Ca2+、Fe2+)达到溶度积常数K sp时,就会形成磷酸盐沉淀Zn2++Fe2++PO43-+H2O→Zn2Fe(PO4)2?4H2O↓ (4)3Zn2++2PO43-+4H2O=Zn3(PO4)2?4H2O↓ (5)磷酸盐沉淀与水分子一起形成磷化晶核,晶核继续长大成为磷化晶粒,无数个晶粒紧密堆集形而上学成磷化膜。
磷化液基本原理、种类介绍及配方参考

磷化液基本原理、种类介绍及配方参考磷化液基本原理、种类介绍及配方参考导读:本文详细介绍了磷化液简介,基本原理,分类,参考配方等,本文中的配方数据经过修改,如需更详细资料,可咨询我们的技术工程师。
一、磷化液的简介磷化是金属与磷酸或酸性磷酸盐反应形成磷酸盐保护膜的化学反应过程。
磷化反应是一种典型的局部多相反应,本质上属于电化学反应。
当金属浸入到含有磷酸盐的溶液中,在其表面形成许多微腐蚀电池,发生轻微浸蚀。
在溶液-金属界面处,酸浓度降低,所形成金属磷酸盐化学转化膜称之为磷化膜。
磷化主要用于金属材料的防腐蚀,给机体金属提供腐蚀保护,用于喷漆前打底,提高覆膜层的附着力和防腐蚀能力以及在金属加工中起到减磨润滑作用。
磷化膜的外观是均匀致密的,主要呈现浅灰、深灰、灰黑等色;其结构主要呈现斜方晶体、圆柱形晶体、四方面心晶体、混合晶体以及无定型结晶等形态。
磷化膜具有多孔性,极大地提高了金属的表面积,从而在很大程度上提高了金属表面与涂层之间的附着力,但是磷化膜的耐热性、耐酸碱性、导热性和导电性等性能都较差。
磷化液一般由磷化开槽剂(磷化建浴剂)、磷化补充剂、磷化调整剂、磷化促进剂几部分组成,其中开槽剂和补充剂为主要组成成分:开槽剂是首次建槽使用,补充剂是建槽之后的补充使用;磷化调整剂是调节磷化液的总酸和游离酸,以达到合适的酸比;磷化促进剂是一种氧化剂,主要去极化作用,促进磷化的反应速度。
磷化工艺操作简单,成本低廉,经过磷化处理的工件,原来的物理机械性能如强度、硬度等保持不变,而被处理的金属表面,由于形成均匀致密的磷化膜,其金属表面的性能大大提高。
因此金属的磷化处理工艺在工业上得到了广泛应用,尤其是在金属表面涂装领域。
禾川化学技术团队具有丰富的分析研发经验,引进国外配方破译技术,专业从事磷化液产品的技术开发,经过多年的技术积累,可以运用尖端的科学仪器、完善的标准图谱库、强大原材料库,彻底解决表面处理企业生产研发过程中遇到的难题,利用其八大服务优势,最终实现企业产品性能改进及新产品研发。
锌系磷化液配方及各组分详细说明

1943年,Jernstedt,G.W.发表论文,讲述磷酸肽微小的胶体颗粒吸附在金属表面上能作为晶核促进磷化膜的生长。磷化前的这种活化细化了结晶的结构,也改善了膜层的性能。
1氧化锌
别名 锌白 分子式 ZnO 分子量 81.37 白色六角晶系结晶或粉末。无味、质细腻。相对密度5.606。熔点1975℃。不溶于水,溶于酸和氢氧化钠,属两性氧化物。
在空气中吸收二氧化碳和水生成碳酸锌呈黄色。
生产磷化液时,通常使用含量99.7以上的氧化锌。
ZnO + 2H3PO4 = Zn(H2PO4)2 + H2O
氟硼酸钠
别名 四氟硼酸钠 分子式 NaBF4 分子量 109.811 白色或无色结晶。相对密度 2.47.熔点384℃(分解)。易溶于水。遇硫酸分解。有毒。
氟硅酸钠
分子式 Na2SiF6 分子量 188.06 无色六方结晶。相对密度2.679.有吸潮性。在酸中的溶解度比水中大。在碱液中分解。灼热到300℃以上分解。有毒。
硝酸铁一般在刚配槽时起到熟化磷化液的作用,尤其溶液中氟离子含量少、游离酸低时,加入少量硝酸铁可避免最初的磷化膜发黄、粗晶,后期由于钢铁工件硫酸铜)
硫酸铜
化学式 CuSO4·5H2O 分子量 249.68 亮蓝色三斜晶系结晶或粉末。相对密度2.284.易溶于水。110℃失去四个结晶水,150℃以上将失去全部结晶水,成为强烈吸湿性白色粉末状无水硫酸铜。在干燥空气中慢慢风化,变为白色粉状物。有毒。
ZnO + 2HNO3 = Zn(NO3)2 + H2O
金属磷化发黑技术
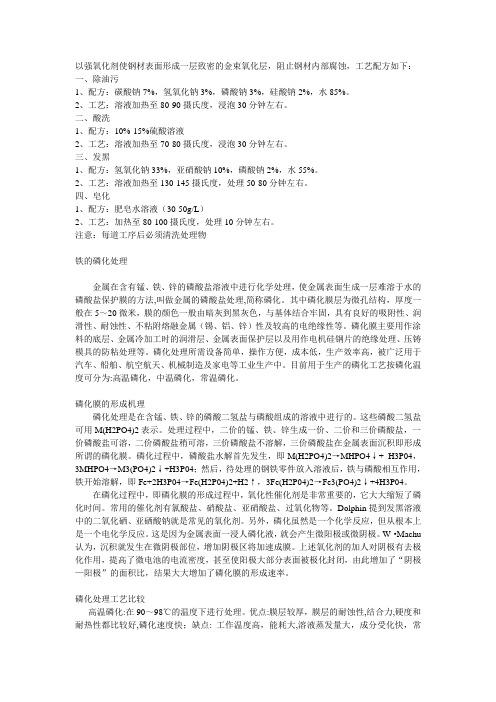
以强氧化剂使钢材表面形成一层致密的金束氧化层,阻止钢材内部腐蚀,工艺配方如下:一、除油污1、配方:碳酸钠7%,氢氧化钠3%,磷酸钠3%,硅酸钠2%,水85%。
2、工艺:溶液加热至80-90摄氏度,浸泡30分钟左右。
二、酸洗1、配方:10%-15%硫酸溶液2、工艺:溶液加热至70-80摄氏度,浸泡30分钟左右。
三、发黑1、配方:氢氧化钠33%,亚硝酸钠10%,磷酸钠2%,水55%。
2、工艺:溶液加热至130-145摄氏度,处理50-80分钟左右。
四、皂化1、配方:肥皂水溶液(30-50g/L)2、工艺:加热至80-100摄氏度,处理10分钟左右。
注意:每道工序后必须清洗处理物铁的磷化处理金属在含有锰、铁、锌的磷酸盐溶液中进行化学处理,使金属表面生成一层难溶于水的磷酸盐保护膜的方法,叫做金属的磷酸盐处理,简称磷化。
其中磷化膜层为微孔结构,厚度一般在5~20微米,膜的颜色一般由暗灰到黑灰色,与基体结合牢固,具有良好的吸附性、润滑性、耐蚀性、不粘附熔融金属(锡、铝、锌)性及较高的电绝缘性等。
磷化膜主要用作涂料的底层、金属冷加工时的润滑层、金属表面保护层以及用作电机硅钢片的绝缘处理、压铸模具的防粘处理等。
磷化处理所需设备简单,操作方便,成本低,生产效率高,被广泛用于汽车、船舶、航空航天、机械制造及家电等工业生产中。
目前用于生产的磷化工艺按磷化温度可分为:高温磷化,中温磷化,常温磷化。
磷化膜的形成机理磷化处理是在含锰、铁、锌的磷酸二氢盐与磷酸组成的溶液中进行的。
这些磷酸二氢盐可用M(H2PO4)2表示。
处理过程中,二价的锰、铁、锌生成一价、二价和三价磷酸盐,一价磷酸盐可溶,二价磷酸盐稍可溶,三价磷酸盐不溶解,三价磷酸盐在金属表面沉积即形成所谓的磷化膜。
磷化过程中,磷酸盐水解首先发生,即M(H2PO4)2→MHPO4↓+ H3P04,3MHPO4→M3(PO4)2↓+H3P04;然后,待处理的钢铁零件放入溶液后,铁与磷酸相互作用,铁开始溶解,即Fe+2H3P04→Fe(H2P04)2+H2↑,3Fe(H2P04)2→Fe3(PO4)2↓+4H3P04。
二合一磷化液配方

二合一磷化液配方
1.配方原料:
-磷酸:30-50克
-锌磷酸:30-50克
-硝酸:5-10克
-阻挡剂:1-3克
-助溶剂:2-5克
-表面活性剂:1-3克
-稳定剂:0.5-1克
-水:适量
2.配方步骤:
-步骤1:将磷酸和锌磷酸按比例加入适量的水中,搅拌均匀,形成磷酸锌溶液。
-步骤2:将硝酸溶解于适量的水中,然后将其缓慢加入磷酸锌溶液中,同时搅拌均匀。
这一步骤可以调节磷化液的酸度和活性。
-步骤3:将阻挡剂、助溶剂和表面活性剂依次加入溶液中,搅拌均匀。
阻挡剂可以降低磷化液对金属的腐蚀性,助溶剂可以帮助配方物质更好地溶解,表面活性剂可以提高涂层的均匀性和附着力。
-步骤4:最后加入稳定剂,用于延长磷化液的使用寿命和稳定性。
搅拌均匀后,磷化液配方制备完成。
3.应用方法:
-将待处理的金属表面彻底清洗,并确保表面没有油脂和杂质。
-将磷化液倒入合适的容器中,将金属制品浸入磷化液中。
-控制磷化液的温度和处理时间,一般情况下,温度在50-70摄氏度,处理时间为15-30分钟。
-将处理后的金属制品取出,用清水冲洗干净。
-在需要时,可以将磷化液后进行涂层处理,以提高防腐性和美观度。
磷化液配方组成磷化液成分分析关键技术及生产基本工艺

磷化液配方组成磷化液成分分析关键技术及生产基本工艺磷化液是一种常用的表面处理剂,主要用于金属材料的防锈和增强的化学转化涂层的形成。
磷化液的组成和配方对于其处理效果和使用性能有着重要影响。
下面将介绍磷化液的配方组成、成分分析关键技术以及生产基本工艺。
1.磷化液的配方组成一般而言,磷化液的主要成分由以下几个方面组成:(1)酸性成分:酸性成分是磷化液的主要组成部分,常用的酸性成分包括磷酸、硫酸、盐酸等。
酸性成分起到溶解金属表面氧化物和清洁金属表面的作用,使金属表面裸露出新鲜的金属。
(2)磷酸盐:磷酸盐是磷化液中的重要成分,它能和金属表面形成磷化层,提高金属的防锈性能。
常用的磷酸盐有磷酸二氢钠、磷酸钠等。
(3)辅助成分:辅助成分在磷化液中起到调节酸性和增强磷化效果的作用。
常用的辅助成分有过硫酸钠、硝酸、硼酸、草酸等。
2.磷化液成分分析关键技术对于磷化液的成分分析,常用的方法有以下几种:(1)pH检测:pH值检测可以帮助我们确定磷化液的酸碱性质,从而了解磷化液中的酸性成分含量。
(2)离子色谱法:离子色谱法可以检测磷化液中的阴离子组成,如磷酸盐、硫酸盐等。
通过分析阴离子的浓度可以确定磷酸盐的含量。
(3)原子吸收光谱法:原子吸收光谱法可以检测磷化液中的金属离子元素含量,如铁、锌、钠等。
通过分析金属离子的含量可以评估磷化液的质量。
磷化液的生产工艺一般包括以下几个步骤:(1)原料配料:按照磷化液的配方要求,将各种原料按照一定比例进行配料。
在配料过程中要注意安全操作,避免接触皮肤和吸入刺激性气体。
(2)溶解混合:将配料好的原料加入合适的容器中,向其中加入适量的水,通过搅拌等方式将原料溶解和混合均匀。
(3)pH调节:根据配方中的酸碱性要求,使用适量的酸碱物质进行pH值调节,使磷化液达到要求的酸碱度。
(4)过滤净化:通过过滤装置对磷化液进行过滤,去除杂质和固体颗粒,提高磷化液的质量。
(5)包装贮存:将生产好的磷化液装入适当容器中,密封存放于阴凉干燥的地方,以保证磷化液的稳定性和使用寿命。
磷化底漆
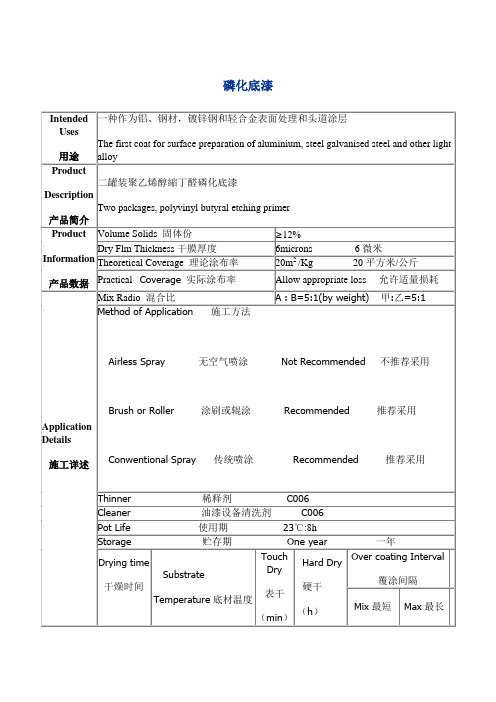
二罐装聚乙烯醇縮丁醛磷化底漆
Two packages, polyvinyl butyral etching primer
Product
Information
产品数据
Volume Solids固体份
≥12%
Dry Flm Thickness干膜厚度
6microns 6微米
Theoretical Coverage理论涂布率
20m2/Kg 20平方米/公斤
PracticalCoverage实际涂布率
Allow appropriate loss允许适量损耗
Application Details
施工详述
Mix Radio混合比
A : B=5:1(by weight)甲:乙=5:1
Method of Application施工方法
技术要求及表面处理
Clean all grease according to SSPC-SP1 by solvent cleaning
Ensure that the area is clean, dry and free from metallic corrosion.
根据SSPC-SP1用溶剂清洗表面去除油脂。
保证该区域清洁干燥无金属腐蚀物
Limitations
限制
Avoid excessively thick film in application the dry-film thickness should be no more than 12um
避免施工漆膜过厚,其干膜厚度不超过12微米,乙组份含有磷酸
Enough ventilation is necessary at application sites. In order to remove any danger of explosion, must keep the ratio of gas / air is less than 10 %, Usually 200 m3of ventilation quantity per 1 Kg solvent (according to the solvent) is necessary, it canMaintain the minimum explosive limit. Take effective precautions to prevent skin and eye contact with the coating (such as the use of overalls, gloves, goggles, face shields and protective oil coating and so on). If paint gets in touch with skin,If accidental skin contact with the product, please use fresh water and soap or an appropriate industrial cleaning agents thoroughly cleansed. In case of eyes being contaminated, rinse with fresh water for 10 min at least and give medical treatment immediately.During painting, it is recommended to wear face shields to prevent inhalation of paint mist and harmful gases.Especially in poorly ventilated environment, it is more necessary.Finally, be handled with care so as not to waste paint barrels of pollution of the environment.
X06-01 乙烯磷化底漆(分装)
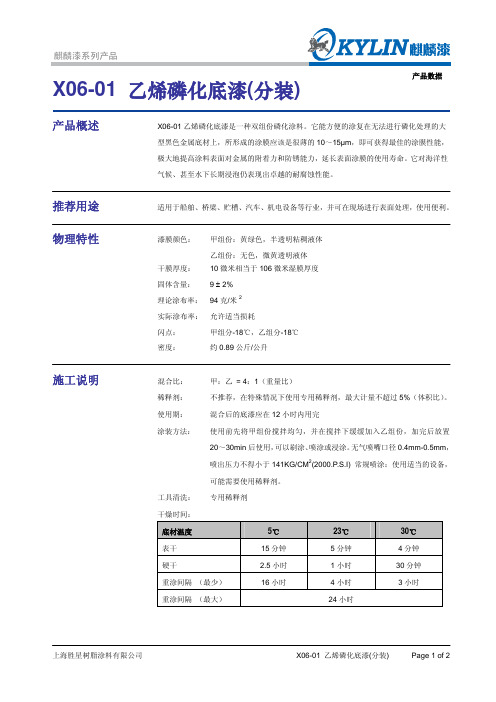
产品数据X06-01 乙烯磷化底漆(分装)产品概述X06-01乙烯磷化底漆是一种双组份磷化涂料。
它能方便的涂复在无法进行磷化处理的大型黑色金属底材上,所形成的涂膜应该是很薄的10~15µm,即可获得最佳的涂膜性能,极大地提高涂料表面对金属的附着力和防锈能力,延长表面涂膜的使用寿命。
它对海洋性气候、甚至水下长期浸泡仍表现出卓越的耐腐蚀性能。
推荐用途适用于船舶、桥梁、贮槽、汽车、机电设备等行业,并可在现场进行表面处理,使用便利。
物理特性漆膜颜色:甲组份:黄绿色,半透明粘稠液体乙组份:无色,微黄透明液体干膜厚度: 10微米相当于106微米湿膜厚度± 2%固体含量: 9理论涂布率: 94克/米2实际涂布率:允许适当损耗闪点:甲组分-18℃,乙组分-18℃密度:约0.89公斤/公升施工说明混合比:甲:乙 = 4:1(重量比)稀释剂:不推荐,在特殊情况下使用专用稀释剂,最大计量不超过5%(体积比)。
使用期:混合后的底漆应在12小时内用完涂装方法:使用前先将甲组份搅拌均匀,并在搅拌下缓缓加入乙组份,加完后放置20~30min后使用,可以刷涂、喷涂或浸涂。
无气喷嘴口径0.4mm-0.5mm,喷出压力不得小于141KG/CM2(2000.P.S.I) 常规喷涂:使用适当的设备,可能需要使用稀释剂。
工具清洗:专用稀释剂干燥时间:底材温度5℃23℃30℃表干15分钟5分钟4分钟硬干 2.5小时1小时30分钟重涂间隔(最少)16小时4小时3小时重涂间隔(最大) 24小时配套用漆请咨询上海胜星树脂涂料有限公司。
表面处理所有表面应当清洁、干燥且无污物,表面应当按照ISO8504进行评估和处理。
裸钢清洁度:喷砂处理至Sa2.5(ISO 8501-1:1988)。
粗糙度:使用合适的冲砂和抛丸材料处理到30 – 75微米(ISO 8503-2)。
涂有车间底漆的钢材清洁、干燥、完好经认可的车间底漆。
涂有油漆的表面清洁、干燥、和完好经认可的兼容底漆。