高速切割的关键技术
先进制造技术复习题
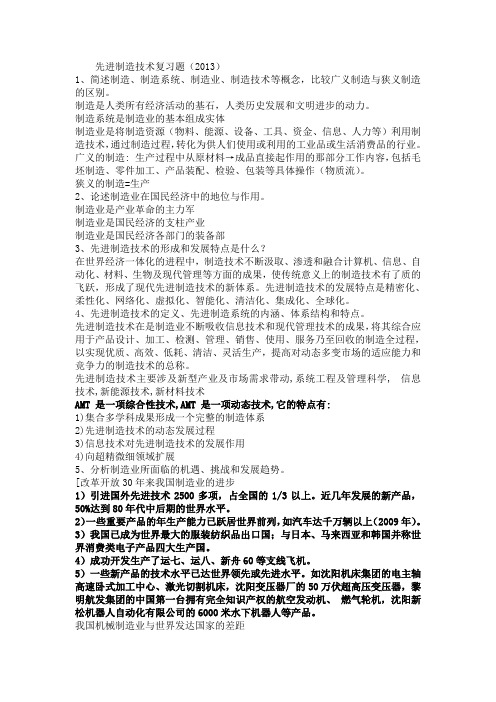
先进制造技术复习题(2013)1、简述制造、制造系统、制造业、制造技术等概念,比较广义制造与狭义制造的区别。
制造是人类所有经济活动的基石,人类历史发展和文明进步的动力。
制造系统是制造业的基本组成实体制造业是将制造资源(物料、能源、设备、工具、资金、信息、人力等)利用制造技术,通过制造过程,转化为供人们使用或利用的工业品或生活消费品的行业。
广义的制造: 生产过程中从原材料→成品直接起作用的那部分工作内容,包括毛坯制造、零件加工、产品装配、检验、包装等具体操作(物质流)。
狭义的制造=生产2、论述制造业在国民经济中的地位与作用。
制造业是产业革命的主力军制造业是国民经济的支柱产业制造业是国民经济各部门的装备部3、先进制造技术的形成和发展特点是什么?在世界经济一体化的进程中,制造技术不断汲取、渗透和融合计算机、信息、自动化、材料、生物及现代管理等方面的成果,使传统意义上的制造技术有了质的飞跃,形成了现代先进制造技术的新体系。
先进制造技术的发展特点是精密化、柔性化、网络化、虚拟化、智能化、清洁化、集成化、全球化。
4、先进制造技术的定义、先进制造系统的内涵、体系结构和特点。
先进制造技术在是制造业不断吸收信息技术和现代管理技术的成果,将其综合应用于产品设计、加工、检测、管理、销售、使用、服务乃至回收的制造全过程,以实现优质、高效、低耗、清洁、灵活生产,提高对动态多变市场的适应能力和竞争力的制造技术的总称。
先进制造技术主要涉及新型产业及市场需求带动,系统工程及管理科学,信息技术,新能源技术,新材料技术AMT 是一项综合性技术,AMT是一项动态技术,它的特点有:1)集合多学科成果形成一个完整的制造体系2)先进制造技术的动态发展过程3)信息技术对先进制造技术的发展作用4)向超精微细领域扩展5、分析制造业所面临的机遇、挑战和发展趋势。
[改革开放30年来我国制造业的进步1)引进国外先进技术2500多项,占全国的1/3以上。
切割技术在航空航天领域中的应用有哪些?

切割技术在航空航天领域中的应用有哪些?一、涡轮叶片切割技术涡轮叶片是航空发动机中关键的零部件,其制造质量直接影响着发动机的性能和可靠性。
传统的涡轮叶片制造工艺复杂、成本高,而采用切割技术可以使涡轮叶片制造更加高效和精确。
具体应用包括:1. 高精度切割:利用激光切割或电火花切割等技术对涡轮叶片进行高精度的切割,保证叶片的尺寸和形状的一致性,提高发动机的工作效率。
2. 自动化切割:采用机器人或自动化设备对涡轮叶片进行切割,使切割过程更加快速和精确,降低人为操作造成的误差,并提高生产效率。
3. 切割质量检测:通过光学检测、射线检测等技术对涡轮叶片的切割质量进行检测,保证叶片的质量和可靠性,提高发动机的寿命。
二、航空结构切割技术在航空制造中,常常需要对航空结构进行切割加工以满足设计和装配要求。
切割技术可以有效地对航空结构进行加工和切割,提高生产效率和产品质量。
相关应用包括:1. 自动化切割:采用机器人、数控切割机等自动化设备对航空结构进行切割加工,提高生产效率和产品质量。
2. 高精度切割:利用激光切割、水刀切割等高精度切割技术对航空结构进行加工,保证切割尺寸的精确性和一致性。
3. 表面质量控制:通过优化切割工艺、选用合适的切割工具和加工参数,控制航空结构切割表面的质量,减少切割残留物和毛刺,提高航空结构的整体性能。
三、复合材料切割技术复合材料在航空航天领域中得到了广泛应用,而复合材料的切割加工对产品的质量和性能有着重要影响。
切割技术可以使复合材料的切割加工更加高效和精确。
具体应用包括:1. 高速切割:采用高速切割工具和刀具对复合材料进行切割加工,提高生产效率和切割质量。
2. 质量控制:通过优化切割工艺、选择合适的切割工具和加工参数,控制复合材料切割的质量,减少切割残留物和毛刺,提高产品的质量和性能。
3. 切割损伤控制:针对复合材料的特殊性,采用适当的切割技术和工艺,在切割过程中有效控制切割损伤,提高产品的使用寿命和可靠性。
武汉理工大学先进制造工艺技术及其装备期末复习题

先进制造工艺技术及其装备复习题复制题目后,按住CtrI+F键查找相应题目答案(超越高度)一、多选(共计25分,每题2.5分,每题答案完全一样得满分,少选、多选、错选均不得分。
)1、工业机器人的发展趋势有()。
A.机器人的智能化B.机器人的多机协调化C.机器人的标准化D.机器人的模块化正确答案:【A;B;C;D】2、制造与制造业的作用有()。
A.创造价值,生产物质财富和新的知识B.为国民经济各个部门包括国防和科学技术的进步提供先进的手段和装备C.是国民经济和综合国力的支柱产业D.是国民经济和综合国力的唯一指标正确答案:【A;B;C】3、先进制造技术的发展特点()。
A.小批量一少品种大批量一多品种变批量B.从劳动密集型一设备密集型一信息密集型一知识密集型变化。
C.手工一机械化一单机自动化一刚性流水自动线一柔性自动线一智能自动化。
D.蒸汽时代一电气时代一信息时代正确答案:【A;B;C】4、电火花加工、电解加工相比,超声波加工的加工精度高,加工表而质量好,但加工金属材料时效率低()A.B.正确答案:【正确】5、机器人的控制系统由机器人本体和伺服控制器组成。
A.B.正确答案:【正确】6、国际生产工程研究学会(CIRP)定义:”制造是一个涉及制造工业中产品设计、物料选择、()市场销售和服务的一系列相关活动和工作的总称”。
A.生产计划B.生产过程C.质量保证D.经营管理正确答案:【A;B;C;D】7、光刻加工的主要阶段有()oA.涂胶B.曝光C.显影D.坚膜正确答案:【A;B;C;D】8、制造与制造业的作用有()。
A.创造价值,生产物质财富和新的知识B.为国民经济各个部门包括国防和科学技术的进步提供先进的手段和装备C.是国民经济和综合国力的支柱产业D,是国民经济和综合国力的唯一指标正确答案:【A;B;C】9、福特首先推行所有零件都按照一定的公差要求来加工(零件互换技术),实现了以刚性自动化为特征的大量生产方式,它对()都产生了重大的作用。
高速搅拌切割制粒过程及影响因素简介

高速搅拌切割制粒过程及影响因素简介文章标题:高速搅拌切割制粒过程及影响因素简介概述:高速搅拌切割制粒是一种常见的固体制粒方法,它可以将粉末、颗粒或浆料转化为均匀的颗粒状物料。
在这个过程中,搅拌切割设备通过高速旋转刀片将原料分散并切割成均匀的颗粒。
本文将对高速搅拌切割制粒过程以及影响因素进行简要介绍,并分享一些个人观点和理解。
一、高速搅拌切割制粒过程:1. 设备介绍:高速搅拌切割制粒常用的设备包括高剪切搅拌机、高剪切混合机或高剪切切割机。
这些设备通常由旋转刀片、筒体和驱动装置组成。
在制粒过程中,原料通过进料口加入搅拌切割设备,旋转刀片高速旋转时,将原料分散并切割,形成均匀颗粒。
2. 切割原理:高速切割刀片的旋转速度和形状对制粒效果起着重要作用。
刀片旋转时,带动原料发生剪切和抛撒,进而将颗粒状物料切割成均匀颗粒。
切割过程中,刀片与原料之间的相对速度越大,切割作用就越明显。
刀片的形状也能够影响颗粒大小和形态。
3. 切割条件:高速搅拌切割制粒的切割条件包括刀片速度、刀片形状、搅拌速度、搅拌时间等。
不同的切割条件将导致不同的制粒效果。
刀片速度越高,制粒效果越好;刀片形状对颗粒形态有一定的影响;搅拌速度和时间决定了切割时间和强度,进而影响颗粒的大小和分布。
二、影响因素:1. 原料特性:原料的物理性质、颗粒大小和分布、含水量等都会影响高速搅拌切割制粒的效果。
物理性质包括粉末流动性、颗粒形状等,这些特性将影响切割和分散性能。
较大的颗粒可能需要更长的切割时间来获得均匀的颗粒。
含水量的变化也可能导致制粒效果的不稳定性。
2. 设备参数:高速搅拌切割设备的参数,如刀片速度、刀片形状、搅拌速度和时间等,决定了切割的强度和时间。
这些参数的选择与原料的特性有关,通过合理调控这些参数,可以获得所需的颗粒特性。
3. 外部环境:制粒过程中的外部环境也会对制粒效果产生一定影响。
湿度、温度、压力等因素都可能影响粉末的流动性、粘附性和切割效果。
高功率薄片超快激光器关键技术与产业化
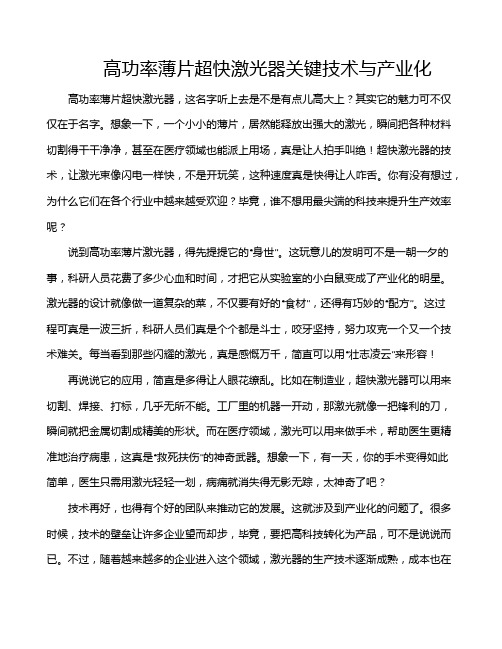
高功率薄片超快激光器关键技术与产业化高功率薄片超快激光器,这名字听上去是不是有点儿高大上?其实它的魅力可不仅仅在于名字。
想象一下,一个小小的薄片,居然能释放出强大的激光,瞬间把各种材料切割得干干净净,甚至在医疗领域也能派上用场,真是让人拍手叫绝!超快激光器的技术,让激光束像闪电一样快,不是开玩笑,这种速度真是快得让人咋舌。
你有没有想过,为什么它们在各个行业中越来越受欢迎?毕竟,谁不想用最尖端的科技来提升生产效率呢?说到高功率薄片激光器,得先提提它的“身世”。
这玩意儿的发明可不是一朝一夕的事,科研人员花费了多少心血和时间,才把它从实验室的小白鼠变成了产业化的明星。
激光器的设计就像做一道复杂的菜,不仅要有好的“食材”,还得有巧妙的“配方”。
这过程可真是一波三折,科研人员们真是个个都是斗士,咬牙坚持,努力攻克一个又一个技术难关。
每当看到那些闪耀的激光,真是感慨万千,简直可以用“壮志凌云”来形容!再说说它的应用,简直是多得让人眼花缭乱。
比如在制造业,超快激光器可以用来切割、焊接、打标,几乎无所不能。
工厂里的机器一开动,那激光就像一把锋利的刀,瞬间就把金属切割成精美的形状。
而在医疗领域,激光可以用来做手术,帮助医生更精准地治疗病患,这真是“救死扶伤”的神奇武器。
想象一下,有一天,你的手术变得如此简单,医生只需用激光轻轻一划,病痛就消失得无影无踪,太神奇了吧?技术再好,也得有个好的团队来推动它的发展。
这就涉及到产业化的问题了。
很多时候,技术的壁垒让许多企业望而却步,毕竟,要把高科技转化为产品,可不是说说而已。
不过,随着越来越多的企业进入这个领域,激光器的生产技术逐渐成熟,成本也在下降。
这对于整个行业来说,简直是个好消息!你想想,如果价格变得亲民,谁不愿意买呢?让更多人享受到高科技的红利,简直是“双赢”啊!可别以为光有技术和团队就够了,市场的需求同样重要。
随着各行各业对高效、精准的要求越来越高,超快激光器的市场前景就像一片广阔的蓝天,潜力无限。
超高压磨料射流切割系统及其关键技术研究
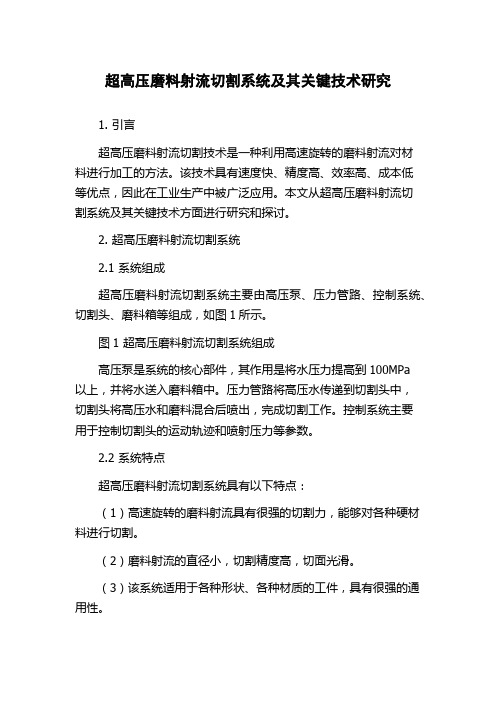
超高压磨料射流切割系统及其关键技术研究1. 引言超高压磨料射流切割技术是一种利用高速旋转的磨料射流对材料进行加工的方法。
该技术具有速度快、精度高、效率高、成本低等优点,因此在工业生产中被广泛应用。
本文从超高压磨料射流切割系统及其关键技术方面进行研究和探讨。
2. 超高压磨料射流切割系统2.1 系统组成超高压磨料射流切割系统主要由高压泵、压力管路、控制系统、切割头、磨料箱等组成,如图1所示。
图1 超高压磨料射流切割系统组成高压泵是系统的核心部件,其作用是将水压力提高到100MPa以上,并将水送入磨料箱中。
压力管路将高压水传递到切割头中,切割头将高压水和磨料混合后喷出,完成切割工作。
控制系统主要用于控制切割头的运动轨迹和喷射压力等参数。
2.2 系统特点超高压磨料射流切割系统具有以下特点:(1)高速旋转的磨料射流具有很强的切割力,能够对各种硬材料进行切割。
(2)磨料射流的直径小,切割精度高,切面光滑。
(3)该系统适用于各种形状、各种材质的工件,具有很强的通用性。
(4)系统操作简单,成本低,可广泛应用于工业生产中。
3. 关键技术3.1 磨料磨料是超高压磨料射流切割中十分重要的一环,磨料的选择直接影响到切割质量和效率。
常见的磨料有金刚石、碳化硅、氧化铝等。
金刚石磨料切割效率较高,但成本较高;碳化硅磨料成本相对较低,在对非金属材料进行切割时表现较优;氧化铝磨料在对钢材等金属材料进行切割时效果较好。
3.2 磨料喷嘴磨料喷嘴是将高压水和磨料混合后喷出的关键部件。
其喷嘴口径、喷嘴设计、内壁涂层等都会影响到磨料射流的稳定性和喷射效果。
喷嘴口径越小,磨料射流的速度越高,能够获得更高的切割效率;喷嘴设计直接影响到磨料射流的稳定性和方向性,设计合理的喷嘴能够使切割面光滑,减少破碎和毛刺等缺陷。
3.3 切割头切割头是喷出高压水和磨料的部件,其结构和材料也对切割效果有影响。
切割头必须具有高压耐受性和磨损性,常见的切割头材料有钨钢、陶瓷等。
消防强切工作原理

消防强切工作原理
消防强切是指针对火场中的金属门窗、墙壁等建筑材料进行快速切割,以便顺利开展灭火救援行动的技术手段。
消防强切工作原理主要是通过电动工具的高速旋转切割轮,将旋转切割轮带动的高速运动刀片,对金属材料进行锯切或切割,从而达到快速破拆门窗、打开通道、疏散人员等目的。
消防强切工作原理的关键在于切割轮的选择和运用。
消防强切用的切割轮通常由石英、树脂等材料制成,这种切割轮具有高强度、高硬度和高耐磨性,能够适应高强度的工作环境。
消防人员在进行消防强切操作时,需要根据切割材料的硬度和厚度,合理选择切割轮的种类和规格,以确保切割效果和速度。
消防强切工作原理的另一个关键在于操作技巧的掌握。
消防人员在进行消防强切操作时,需要注意安全操作规范,保持良好的操作姿势和稳定的切割姿态。
在切割过程中,需要根据实际情况进行角度调整和切割方向的转换,以确保切割效果和切割速度。
同时,还需要注意对周围环境的保护,避免对人员和物品造成不必要的损害。
总之,消防强切工作原理在消防救援工作中具有非常重要的作用,能够有效地帮助消防人员打开通道、疏散人员、扑灭火灾等,提高救援效率和成功率。
因此,消防人员在工作中需要熟练掌握消防强切技术,确保在紧急情况下能够快速、安全地完成任务。
- 1 -。
高速加工机床及其关键技术
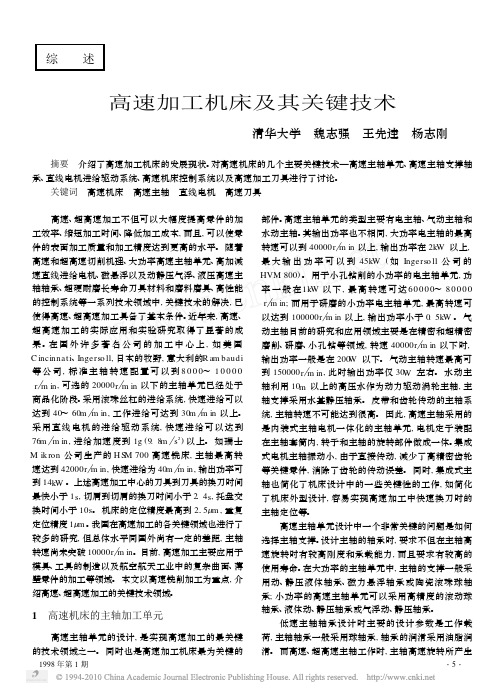
综 述高速加工机床及其关键技术清华大学 魏志强 王先逵 杨志刚 摘要 介绍了高速加工机床的发展现状。
对高速机床的几个主要关键技术—高速主轴单元、高速主轴支撑轴承、直线电机进给驱动系统、高速机床控制系统以及高速加工刀具进行了讨论。
关键词 高速机床 高速主轴 直线电机 高速刀具 高速、超高速加工不但可以大幅度提高零件的加工效率、缩短加工时间、降低加工成本,而且,可以使零件的表面加工质量和加工精度达到更高的水平。
随着高速和超高速切削机理、大功率高速主轴单元、高加减速直线进给电机、磁悬浮以及动静压气浮、液压高速主轴轴承、超硬耐磨长寿命刀具材料和磨料磨具、高性能的控制系统等一系列技术领域中,关键技术的解决,已使得高速、超高速加工具备了基本条件。
近年来,高速、超高速加工的实际应用和实验研究取得了显著的成果。
在国外许多著名公司的加工中心上,如美国C incinnati、Ingerso ll,日本的牧野,意大利的R am baudi 等公司,标准主轴转速配置可以到8000~10000 r m in,可选的20000r m in以下的主轴单元已经处于商品化阶段。
采用滚珠丝杠的进给系统,快速进给可以达到40~60m m in,工作进给可达到30m m in以上。
采用直线电机的进给驱动系统,快速进给可以达到76m m in,进给加速度到1g(9.8m s2)以上。
如瑞士M ik ron公司生产的H S M700高速铣床,主轴最高转速达到42000r m in,快速进给为40m m in,输出功率可到14k W。
上述高速加工中心的刀具到刀具的换刀时间最快小于1s,切屑到切屑的换刀时间小于2.4s,托盘交换时间小于10s。
机床的定位精度最高到215Λm,重复定位精度1Λm。
我国在高速加工的各关键领域也进行了较多的研究,但总体水平同国外尚有一定的差距,主轴转速尚未突破10000r m in。
目前,高速加工主要应用于模具、工具的制造以及航空航天工业中的复杂曲面、薄壁零件的加工等领域。
提高食品加工效率与质量的关键技术与设备介绍

提高食品加工效率与质量的关键技术与设备介绍提高食品加工效率与质量的关键技术与设备介绍摘要:随着社会经济的快速发展,食品产业成为经济发展的重要支柱产业之一。
然而,食品加工业面临着诸多挑战,包括提高加工效率、保障食品质量和提高产品的竞争力等。
本文将介绍几种关键的技术和设备,帮助提高食品加工效率和质量。
一、自动化技术自动化技术是提高食品加工效率的重要手段之一。
传统食品加工过程中需要大量的人力和时间,而自动化技术可以将这些过程自动化完成,大大提高生产效率。
例如,自动化包装机可以将食品制品进行分装、封装和贴标,并自动调整每个包装的重量和尺寸,使得包装过程快速而准确。
此外,自动化技术还可以通过控制系统监测和调节温度、湿度和时间等因素,保证食品加工过程的稳定性和一致性。
二、物联网和大数据技术物联网和大数据技术可以帮助食品加工企业实现智能化管理和优化生产。
物联网技术将传感器和设备与互联网连接,实现即时监测和数据采集。
大数据技术可以对采集的数据进行分析和挖掘,提取有价值的信息,并进行预测和决策。
例如,通过物联网技术,可以实时监测食品加工生产线的运行状态和设备的工作情况,及时发现问题并进行处理,提高生产的稳定性和可靠性。
大数据技术可以分析食品加工过程中的关键参数,并与质量检测数据进行对比,找出影响食品质量的关键因素,并采取相应的措施进行改进。
三、高效能设备高效能设备是提高食品加工效率和质量的基础。
例如,高速切削机可以提高切割效率,减少切割损失。
高速分离机可以将固液混合物高效分离,提高生产效率。
高压灭菌设备可以在较短的时间内对食品进行杀菌处理,减少细菌和病毒的污染。
此外,还有高效能的搅拌设备、混合设备和喷涂设备等,可以满足不同食品加工过程中的需求,提高生产效率和产品质量。
四、智能控制系统智能控制系统可以监测和控制食品加工过程中的多个参数,使之在合理的范围内波动,保证食品的质量。
例如,智能温控系统可以根据食品的特性和质量要求,自动调节加热和冷却设备的温度,保证食品在合适的温度下加工和储存。
气体高速切割的原理
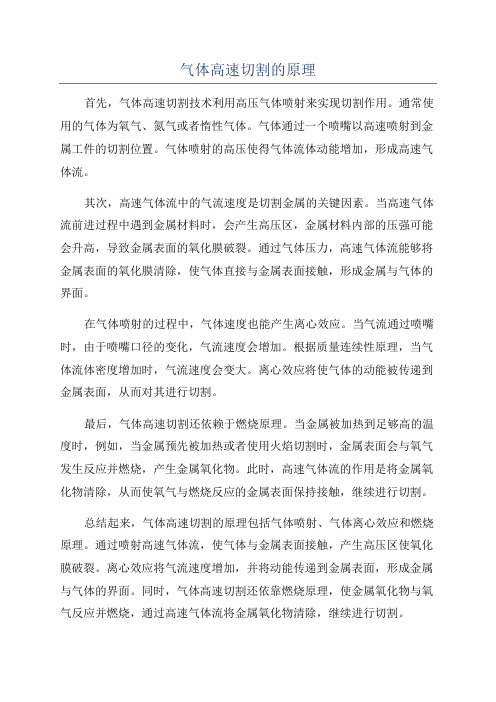
气体高速切割的原理
首先,气体高速切割技术利用高压气体喷射来实现切割作用。
通常使用的气体为氧气、氮气或者惰性气体。
气体通过一个喷嘴以高速喷射到金属工件的切割位置。
气体喷射的高压使得气体流体动能增加,形成高速气体流。
其次,高速气体流中的气流速度是切割金属的关键因素。
当高速气体流前进过程中遇到金属材料时,会产生高压区,金属材料内部的压强可能会升高,导致金属表面的氧化膜破裂。
通过气体压力,高速气体流能够将金属表面的氧化膜清除,使气体直接与金属表面接触,形成金属与气体的界面。
在气体喷射的过程中,气体速度也能产生离心效应。
当气流通过喷嘴时,由于喷嘴口径的变化,气流速度会增加。
根据质量连续性原理,当气体流体密度增加时,气流速度会变大。
离心效应将使气体的动能被传递到金属表面,从而对其进行切割。
最后,气体高速切割还依赖于燃烧原理。
当金属被加热到足够高的温度时,例如,当金属预先被加热或者使用火焰切割时,金属表面会与氧气发生反应并燃烧,产生金属氧化物。
此时,高速气体流的作用是将金属氧化物清除,从而使氧气与燃烧反应的金属表面保持接触,继续进行切割。
总结起来,气体高速切割的原理包括气体喷射、气体离心效应和燃烧原理。
通过喷射高速气体流,使气体与金属表面接触,产生高压区使氧化膜破裂。
离心效应将气流速度增加,并将动能传递到金属表面,形成金属与气体的界面。
同时,气体高速切割还依靠燃烧原理,使金属氧化物与氧气反应并燃烧,通过高速气体流将金属氧化物清除,继续进行切割。
先进制造技术知识点总结

第一章概述1、先进制造技术的特点:先进性、广泛性、实用性、集成性、系统性、动态性。
2、先进制造技术分为三个技术群:主体技术群、支撑技术群、制造技术环境。
3、主体技术:面向制造的设计技术群(1)产品、工艺设计(2)快速成形技术(3)并行工程制造工艺技术群:(1)材料生产工艺(2)加工工艺(3)连接与装配(4)测试和检测(5)环保技术(6)维修技术(7)其他支撑技术:(1)信息技术(2)标准和框架(3)机床和工具技术(4)传感器和控制技术4、先进制造技术研究的四大领域:(1)现代设计技术(2)先进制造工艺技术(3)制造自动化技术(4)系统管理技术4、美国的先进制造技术发展概况 P10美国先进制造技术发展概况:美国政府在 20 世纪 90 年代初提出了一系列制造业的振兴计划,其中包括“先进制造技术计划”和“制造技术中心计划”。
先进制造技术计划美国的发展目标:1、为美国人创造更过高技术、高工资的就业机会,促进美国经济增长。
2、不断提高能源效益,减少污染,创造更加清洁的环境。
3、使美国的私人制造业在世界市场上更具有竞争力,保持美国的竞争地位。
4、使教育系统对每位学生进行更有挑战性的教育。
5、鼓励科技界把确保国家安全以及提高全民生活质量作为核心目标三个重点领域的研究:1、成为下一代的“智能”制造系统2、为产品、工艺过程和整个企业的设计提供集成的工具3、基础设施建设第二章柔性制造系统(FMS)技术1、柔性制造系统(FMS)的特点:(1)主要特点:柔性和自动化(2)设备利用率高,占地面积小(3)减少直接劳动工人数(4)产品质量高而稳定(5)减少在制品库存量(6)投资高、风险大,开发周期长,管理水平要求高2、FMS与传统的单一品种自动生产线(即刚性自动生产线,其物流设备和加工工艺是相对固定的,只能加工一个零件,或加工几个相互类似的零件)缺点:改变加工产品的品种,刚性自动线做较大改动,投资和时间方面耗资大,难以男足市场要求。
高速飞剪在轧钢中的应用及改进
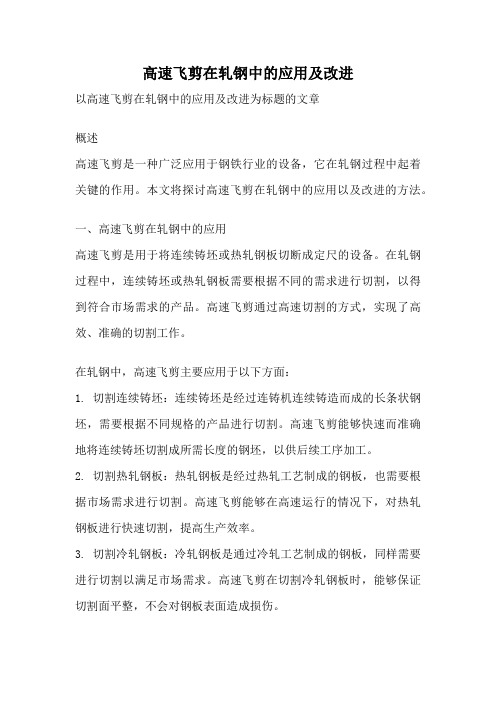
高速飞剪在轧钢中的应用及改进以高速飞剪在轧钢中的应用及改进为标题的文章概述高速飞剪是一种广泛应用于钢铁行业的设备,它在轧钢过程中起着关键的作用。
本文将探讨高速飞剪在轧钢中的应用以及改进的方法。
一、高速飞剪在轧钢中的应用高速飞剪是用于将连续铸坯或热轧钢板切断成定尺的设备。
在轧钢过程中,连续铸坯或热轧钢板需要根据不同的需求进行切割,以得到符合市场需求的产品。
高速飞剪通过高速切割的方式,实现了高效、准确的切割工作。
在轧钢中,高速飞剪主要应用于以下方面:1. 切割连续铸坯:连续铸坯是经过连铸机连续铸造而成的长条状钢坯,需要根据不同规格的产品进行切割。
高速飞剪能够快速而准确地将连续铸坯切割成所需长度的钢坯,以供后续工序加工。
2. 切割热轧钢板:热轧钢板是经过热轧工艺制成的钢板,也需要根据市场需求进行切割。
高速飞剪能够在高速运行的情况下,对热轧钢板进行快速切割,提高生产效率。
3. 切割冷轧钢板:冷轧钢板是通过冷轧工艺制成的钢板,同样需要进行切割以满足市场需求。
高速飞剪在切割冷轧钢板时,能够保证切割面平整,不会对钢板表面造成损伤。
二、高速飞剪在轧钢中的改进为了进一步提高高速飞剪的切割质量和生产效率,钢铁行业进行了一系列的改进措施。
1. 提高切割速度:通过优化刀具材料和刀具设计,提高切割速度是提高生产效率的关键。
采用高硬度、高耐磨的材料制作刀具,能够提高切割速度并延长刀具的使用寿命。
2. 精确控制切割长度:采用先进的控制系统,能够实现对切割长度的精确控制。
通过精确控制切割长度,能够减少钢材的浪费,提高生产效率和经济效益。
3. 自动化操作:引入自动化技术,实现高速飞剪的自动化操作。
通过自动化操作,能够减少人力投入,提高生产效率,并降低操作过程中的人为误差。
4. 质量监测与控制:引入在线检测系统,对切割后的钢材进行质量监测与控制。
通过实时监测和调整切割参数,能够提高切割质量,减少次品率。
三、结论高速飞剪在轧钢中的应用十分广泛,它能够高效、准确地将连续铸坯或热轧钢板切割成所需长度的钢材。
线切割原理
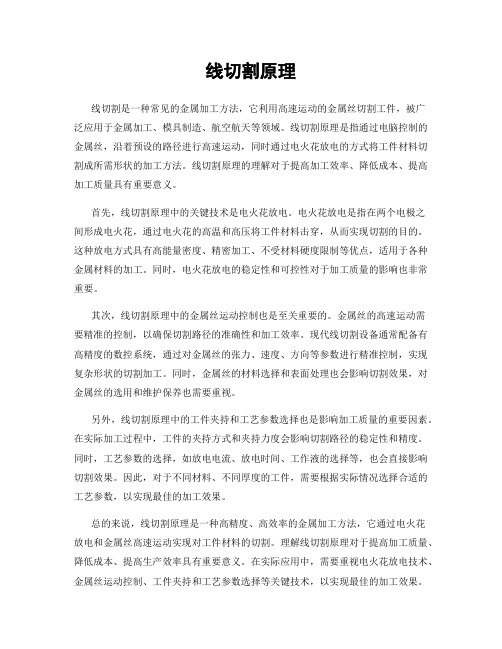
线切割原理线切割是一种常见的金属加工方法,它利用高速运动的金属丝切割工件,被广泛应用于金属加工、模具制造、航空航天等领域。
线切割原理是指通过电脑控制的金属丝,沿着预设的路径进行高速运动,同时通过电火花放电的方式将工件材料切割成所需形状的加工方法。
线切割原理的理解对于提高加工效率、降低成本、提高加工质量具有重要意义。
首先,线切割原理中的关键技术是电火花放电。
电火花放电是指在两个电极之间形成电火花,通过电火花的高温和高压将工件材料击穿,从而实现切割的目的。
这种放电方式具有高能量密度、精密加工、不受材料硬度限制等优点,适用于各种金属材料的加工。
同时,电火花放电的稳定性和可控性对于加工质量的影响也非常重要。
其次,线切割原理中的金属丝运动控制也是至关重要的。
金属丝的高速运动需要精准的控制,以确保切割路径的准确性和加工效率。
现代线切割设备通常配备有高精度的数控系统,通过对金属丝的张力、速度、方向等参数进行精准控制,实现复杂形状的切割加工。
同时,金属丝的材料选择和表面处理也会影响切割效果,对金属丝的选用和维护保养也需要重视。
另外,线切割原理中的工件夹持和工艺参数选择也是影响加工质量的重要因素。
在实际加工过程中,工件的夹持方式和夹持力度会影响切割路径的稳定性和精度。
同时,工艺参数的选择,如放电电流、放电时间、工作液的选择等,也会直接影响切割效果。
因此,对于不同材料、不同厚度的工件,需要根据实际情况选择合适的工艺参数,以实现最佳的加工效果。
总的来说,线切割原理是一种高精度、高效率的金属加工方法,它通过电火花放电和金属丝高速运动实现对工件材料的切割。
理解线切割原理对于提高加工质量、降低成本、提高生产效率具有重要意义。
在实际应用中,需要重视电火花放电技术、金属丝运动控制、工件夹持和工艺参数选择等关键技术,以实现最佳的加工效果。
随着科技的不断进步,线切割技术也在不断创新和发展,为各行业的金属加工提供了更多的可能性。
数控超高压水射流切割技术的特点及其应用_陈光明

1 超高压水射流切割机工作原理 高压水射流加工技术的基本工作原理是运用液体
增压原 理 , 通 过 特 定 的 转 能 装 置 (增 压 器 或 高 压
泵 ) , 将动力源 (电动机 ) 的机械能转换成水的压力
Keywords: Cutting; W ater jet technology; Abrasive; H igh p ressure; NC
0 前言 近几十年来 , 随着科学技术的不断发现 , 人们给
液滴赋予了比自由落体运动大得多的打击能量 , 使漫 长的滴水穿石现象在瞬间便可完成 , 这就是水射流 。 为了提高效率 , 人们将水加以高压 , 并使之以直径较 小的喷嘴中喷出 , 形成一束高速 、连续或间断的水流 束 , 这便是高压水射流 。水射流加工 (W ater Jet Cut2 ting) 又称水喷射加工 , 是利用高压高速水流对工件 的冲击作用来去除材料的 , 俗称 “水刀加工 ”, 即是 利用超高压 (达数百 MPa) 水射流对各种材料进行 切割 、穿孔和工件表层材料去除等加工 。
能 , 具有巨大压力能的水在通过小孔喷嘴后 , 再将压
力能转变成动能 , 从而形成高速水射流 , 喷射到工件
表面 , 当水射流冲击被切工件时 , 动能又重新转变成
作用于材料上的压力能 , 若压力能超过材料的破坏强
度时 , 即可切断材料 , 达到去除材料的加工目的 。因
而高压水射流又常被称为高速水射流 。
从结构形式上分 , 可有多种形式 , 如 : 2— 3 个 数控轴的龙门式结构和悬臂式结构 , 这种结构多用于 切割板材 ; 5—6 个数控轴的机器人结构 , 这种结构 多用于切割汽车内饰件和轿车的内衬等 。
高速切削技术的发展现状
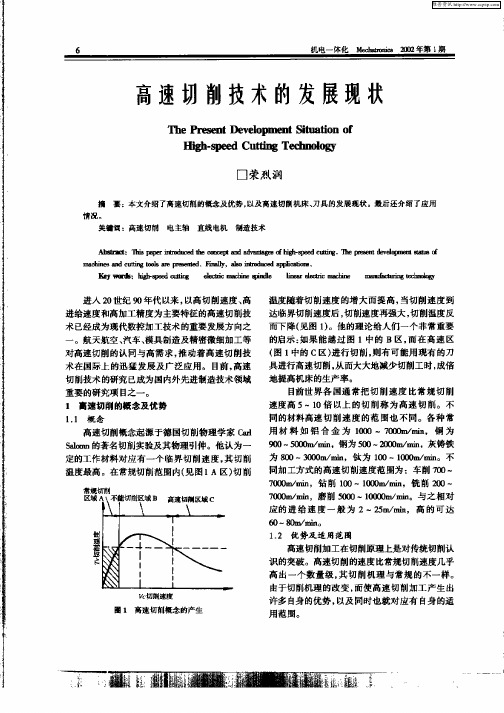
温度随着切削速度 的增大而提高 , 当切削速度到 达临界切削速度后 , 切削速度再强大 , 切削温度反
。
而下降( 见图 1。他的理论给人们一个非常重要 ) 的启示 : 如果能越过图 1中的 B区, 而在高速 区
( 1 图 中的 c区) 进行切削 , 则有可能用现有 的刀 具进行高速切削 , 而大大地减少切削工时, 从 成倍 地提高机床的生产率 。 目前世界各 国通 常把切削速度 比常规 切削 速度高 5 0倍 以上 的切 削称 为高速切 削。不 —1 同的材料高速 切削速度 的范 围也不 同。各 种常 用材 料 如 铝 台 金 为 10 0 0—7 0m rn 00 / i,铜 为 a 90 .0m mn 0一 0/t  ̄ ,钢为 5O 20m rn 0 一 00 / i a ,灰铸铁 为 8O一30m ri,钛 为 10—10m mn 0 00 / n a 0 00 / i。不 同加工方式的高速切削速度范围为 :车削 70 0—
tpr teue h m e r cdte∞啦e n c h d ad丑 删a o 咿 fi h
m cie dc ahns a 吨 协 m a
I . i l , l nr ue e Fn l as tdcd叩 c 啊 . d ay oi o 自
K
:l 删
瞳n e c Ig i l  ̄cm A  ̄印I l e wh ne d
关键技术也正在不断革新 。它包括以下几项 :
2 1 高速 主 轴 .
高速主轴是高速切削机床的搀 部件 , 随着对 主轴转 速要 求的不断提高 ( 主轴转 速在 l0 一 O呻 2 00 ,i 的数控加 工中心越来越普及 )传 统 0 0I加n ,
的齿轮一 皮带变速主传动 系统由于本身的振动、
高性能仪器设备的关键技术
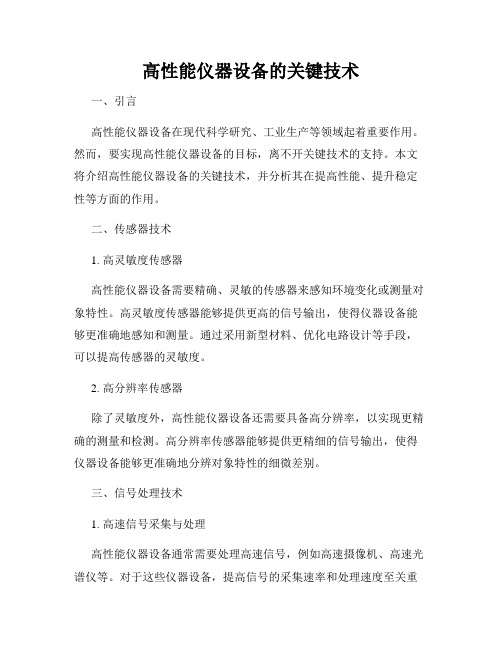
高性能仪器设备的关键技术一、引言高性能仪器设备在现代科学研究、工业生产等领域起着重要作用。
然而,要实现高性能仪器设备的目标,离不开关键技术的支持。
本文将介绍高性能仪器设备的关键技术,并分析其在提高性能、提升稳定性等方面的作用。
二、传感器技术1. 高灵敏度传感器高性能仪器设备需要精确、灵敏的传感器来感知环境变化或测量对象特性。
高灵敏度传感器能够提供更高的信号输出,使得仪器设备能够更准确地感知和测量。
通过采用新型材料、优化电路设计等手段,可以提高传感器的灵敏度。
2. 高分辨率传感器除了灵敏度外,高性能仪器设备还需要具备高分辨率,以实现更精确的测量和检测。
高分辨率传感器能够提供更精细的信号输出,使得仪器设备能够更准确地分辨对象特性的细微差别。
三、信号处理技术1. 高速信号采集与处理高性能仪器设备通常需要处理高速信号,例如高速摄像机、高速光谱仪等。
对于这些仪器设备,提高信号的采集速率和处理速度至关重要。
采用高速ADC(模数转换器)等设备,结合优化的数字信号处理算法,可以实现高速信号的准确采集和实时处理。
2. 低噪声信号处理高性能仪器设备的性能要求对噪声的抑制非常高。
噪声会影响信号的准确性和稳定性,因此需要采用低噪声放大器、滤波器等设备来降低噪声的影响。
此外,通过数字滤波算法等技术,可以进一步减小噪声对信号的影响。
四、控制技术1. 高精度运动控制对于高性能仪器设备中的运动部件,要求具备高精度的运动控制能力。
通过采用精密的电机和传动装置,并结合高精度的运动控制算法,可以实现仪器设备的高速、高精度运动。
2. 高稳定性控制高性能仪器设备往往需要在长时间内保持稳定工作。
因此,控制系统需要具备高稳定性,并且能够自动补偿温度、压力等环境变化对控制精度的影响。
通过采用温度补偿、自适应控制等技术,可以提高仪器设备的稳定性。
五、材料与制造技术1. 特种材料应用高性能仪器设备需要采用特种材料来满足其高性能的要求。
例如,特种合金可以提供更高的机械强度和耐腐蚀性;特种陶瓷材料可以提供更高的绝缘性能和耐高温性能。
切割技术的精度要求是多少?
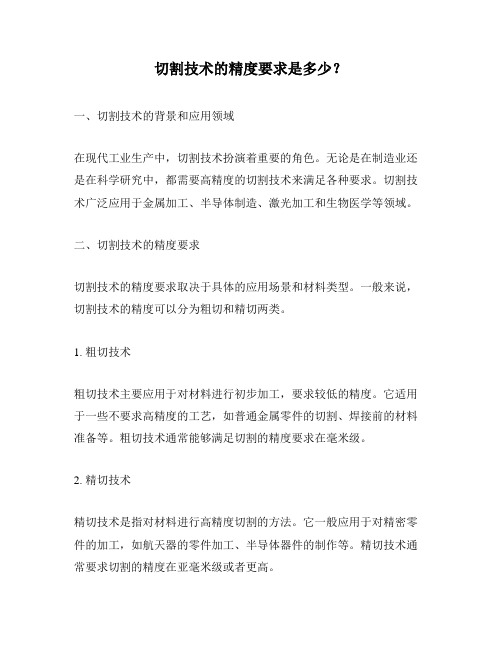
切割技术的精度要求是多少?一、切割技术的背景和应用领域在现代工业生产中,切割技术扮演着重要的角色。
无论是在制造业还是在科学研究中,都需要高精度的切割技术来满足各种要求。
切割技术广泛应用于金属加工、半导体制造、激光加工和生物医学等领域。
二、切割技术的精度要求切割技术的精度要求取决于具体的应用场景和材料类型。
一般来说,切割技术的精度可以分为粗切和精切两类。
1. 粗切技术粗切技术主要应用于对材料进行初步加工,要求较低的精度。
它适用于一些不要求高精度的工艺,如普通金属零件的切割、焊接前的材料准备等。
粗切技术通常能够满足切割的精度要求在毫米级。
2. 精切技术精切技术是指对材料进行高精度切割的方法。
它一般应用于对精密零件的加工,如航天器的零件加工、半导体器件的制作等。
精切技术通常要求切割的精度在亚毫米级或者更高。
三、切割技术的影响因素切割技术的精度受到多个因素的影响,主要包括以下几个方面:1. 切割设备的质量和性能切割设备的质量和性能直接决定了切割的精度。
一台高品质的切割设备能够提供更加稳定和准确的切割结果。
2. 材料的物理特性不同材料具有不同的物理特性,对切割的精度和难度有一定影响。
一些脆性材料在切割时容易产生裂纹和毛边,因此需要更高的精度要求。
3. 操作人员的技能水平操作人员的技能水平对切割的精度起着至关重要的作用。
熟练的操作人员能够根据具体情况调整切割参数,以保证切割的精度。
四、切割技术的发展趋势随着科技的不断发展,切割技术也在不断演进。
未来的切割技术将朝着更高的精度、更快的速度和更多样化的切割能力发展。
1. 激光切割技术激光切割技术由于其非接触式、高精度和高速度的特点,被广泛应用于金属、塑料和纺织品等材料的切割。
未来随着激光技术的进一步发展,激光切割技术的精度将进一步提升。
2. 纳米切割技术纳米切割技术是指对纳米级材料进行精密切割的技术。
随着纳米科技的快速发展,纳米切割技术将在纳米器件的制备和纳米加工领域发挥重要作用。
高速加工技术的关键技术及应用

高速加工技术的关键技术及应用高速加工技术是一种在短时间内高效精确地完成加工任务的技术。
它的应用领域广泛,包括航空航天、汽车制造、电子通讯、模具制造等。
高速加工技术的关键技术主要包括五轴加工、超声波加工、高速切割技术等。
首先,五轴加工技术是高速加工技术的重要组成部分。
五轴加工技术是利用五轴数控机床实现多个方向的加工能力,使工件可以在不同方向上进行切削,从而提高加工效率和加工质量。
这项技术可以实现更复杂的加工任务,如曲线曲面的加工、倒角和开槽等。
五轴加工技术的应用领域广泛,包括航空航天、汽车制造、模具制造等。
其次,超声波加工技术也是高速加工技术的一项重要技术。
超声波加工技术利用超声波振动产生高频微小振动,通过磨料和工件之间的相互磨擦来实现加工效果。
这种加工技术在硬脆材料的加工中具有独特的优势,如陶瓷、半导体材料等。
超声波加工技术的应用能够提高加工精度和加工质量,尤其适用于微细加工和高难度加工。
另外,高速切割技术也是高速加工技术的一种重要技术。
高速切割技术是通过快速旋转的刀具对工件进行切割,具有高效、准确和快速的特点。
高速切割技术的应用非常广泛,包括机械加工、模具制造、汽车制造等。
这种技术能够有效地提高加工效率和降低加工成本,同时还能够实现对各种材料的高精度切割。
除了以上所述的关键技术,高速加工技术还需要配合一系列的辅助技术和设备,例如智能化控制技术、刀具材料技术、冷却系统技术等。
这些技术的综合应用可以进一步提高高速加工技术的效率和精度。
高速加工技术的应用非常广泛。
在航空航天领域,高速加工技术可以用于制造飞机零部件、发动机叶片等高精度零件。
在汽车制造领域,高速加工技术可以用于制造发动机缸体、汽缸套等零部件。
在电子通讯领域,高速加工技术可以用于制造PCB电路板、高频电子元件等。
在模具制造领域,高速加工技术可以用于制造塑料模具、铝合金模具等。
总而言之,高速加工技术的关键技术包括五轴加工、超声波加工、高速切割技术等。
关键工序复杂环节的技术要求措施
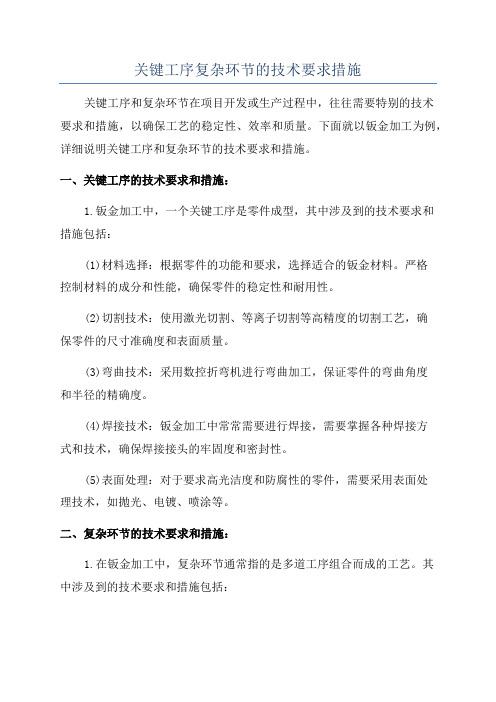
关键工序复杂环节的技术要求措施关键工序和复杂环节在项目开发或生产过程中,往往需要特别的技术要求和措施,以确保工艺的稳定性、效率和质量。
下面就以钣金加工为例,详细说明关键工序和复杂环节的技术要求和措施。
一、关键工序的技术要求和措施:1.钣金加工中,一个关键工序是零件成型,其中涉及到的技术要求和措施包括:(1)材料选择:根据零件的功能和要求,选择适合的钣金材料。
严格控制材料的成分和性能,确保零件的稳定性和耐用性。
(2)切割技术:使用激光切割、等离子切割等高精度的切割工艺,确保零件的尺寸准确度和表面质量。
(3)弯曲技术:采用数控折弯机进行弯曲加工,保证零件的弯曲角度和半径的精确度。
(4)焊接技术:钣金加工中常常需要进行焊接,需要掌握各种焊接方式和技术,确保焊接接头的牢固度和密封性。
(5)表面处理:对于要求高光洁度和防腐性的零件,需要采用表面处理技术,如抛光、电镀、喷涂等。
二、复杂环节的技术要求和措施:1.在钣金加工中,复杂环节通常指的是多道工序组合而成的工艺。
其中涉及到的技术要求和措施包括:(1)工艺规划:合理规划工序的先后顺序,确保每一道工序都能够顺利进行并完成。
(2)设备选择:根据复杂环节的要求,选择合适的设备和工具,如多功能联动机床、自动化钣金加工生产线等。
(3)质量控制:设立严格的质量控制标准,加强对每一道工序的检查和监控,及时发现和解决问题,确保复杂环节的顺利进行。
(4)技术人员培训:钣金加工中,技术人员的专业水平和工艺技能直接关系到复杂环节的成功与否。
因此,加强技术人员的培训和学习,提高他们的技术水平和应变能力。
以上是关键工序和复杂环节的技术要求和措施的一些例子。
实际上,在不同的项目或生产过程中,关键工序和复杂环节的技术要求和措施会有所不同。
因此,在实施过程中,需要根据具体情况进行调整和完善,以确保项目或生产能够高效、稳定地进行。
- 1、下载文档前请自行甄别文档内容的完整性,平台不提供额外的编辑、内容补充、找答案等附加服务。
- 2、"仅部分预览"的文档,不可在线预览部分如存在完整性等问题,可反馈申请退款(可完整预览的文档不适用该条件!)。
- 3、如文档侵犯您的权益,请联系客服反馈,我们会尽快为您处理(人工客服工作时间:9:00-18:30)。
高速切割的关键技术学院:动力与机械学院班级:机械一班(09621)姓名:丰德海学号:200930139014摘要: 高速切削是切削加工的发展方向,现已成为切削加工的主流。
包括高速软切削、高速硬切削、高速干切削和大进给切削等,高速切削是一个相对概念,如何定义尚无共识,切削速度为普通切削5-10倍的切削,刀具转速10000-20000rpm的切削,1978年切削委员会规定的500-7500m/min 的切削,通常为高速切削。
高速切削不只是切削速度的提高,它的发展和推广应用(包括机床和刀具技术的全面发展和提高)将带动整体制造业水平和效益的进步与提高。
关键词:高速切割,关键,技术,发展,前景。
正文:高速切削是一项复杂的系统工程。
高速切削不只是切削速度的提高,它的发展涉及到机床、刀具、工艺和材料等诸多领域的技术配合和技术创新。
实现高速切削的最关键技术是研究开发性能优良的高速切削机床, 自20世纪80年代中期以来, 开发高速切削机床便成为国际机床工业技术发展的主流。
1 高速加工对机床的特殊要求高速切削加工的特殊性对实施高速切削加工的机床提出新的要求:(1)要有一个适合高速运转的主轴单元及其驱(2)要有一个快速反应的进给系统单元部件和数控伺服驱动系统。
(3)要有一个高效、快速的冷却系统。
(4)高刚性的床体结构。
(5)安全装置和实时监控系统。
(6)要有方便可靠的换刀装置。
(7)优良的热态特性和静、动态特性。
2 高速切削机床的关键技术2.1 高速主轴高速数控机床的工作性能, 首先取决于高速主轴的性能。
数控机床的高速主轴单元包括主轴动力源、主轴、轴承和机架等几个部分, 它影响加工系统的精度、稳定性及应用范围, 其动力性能及稳定性对高速加工起着关键的作用。
目前高速切削机床的主轴主要为陶瓷滚珠轴承电动主轴。
机床主轴由内装式电动机直接驱动,从而把机床主传动链的长度缩短为零,实现机床的“零传动”,俗称“电主轴”。
电主轴是一种智能型功能部件,不但转速高、功率大,还有一系列控制主轴温升与振动等机床运行参数的功能,以确保其高速运转的可靠性与安全性。
目前电主轴主要采用交流异步感应电动机(高频),国内外专业的电主轴制造厂已可供应几百种规格的电主轴。
其套筒直径从32mm至320mm、转速从10000r/min到150000r/min,功率从0.5kW到80kW、转矩从0.1N•m 到300N•m。
2. 2 高速精密轴承高速轴承是高速切削机床的核心,是决定高速主轴寿命和负载容量的最关键部件。
2. 2. 1 磁悬浮轴承它是用电磁力将主轴无机械接触地悬浮起来,其转速可达45000rPmin ,功率为20kW,精度高,易实现实时诊断和在线监控,是理想的支承元件,但其价格较高。
2. 2. 2 液体动静压轴承采用流体动、静力相结合的办法,使主轴在油膜支撑中旋转,具有径、轴向跳动小、刚性好、阻尼特性好,适于粗、精加工,寿命长的优点。
但其无通用性,维护保养较困难。
2. 2. 3 混合陶瓷轴承用氮化硅制的滚珠与钢制轨道相组合,是目前在高速切削机床主轴上使用最多的支承元件,在高速转动时离心力小,刚性好,温度低,寿命长,功率可达80kW,转速高达150000rPmin ,它的标准化程度高,便于维护,价格低。
2.3 高精度快速进给系统高速切削是高切削速度、高进给率和小切削量的组合,进给速度为传统的5~10倍。
这就要求机床进给系统高进给速度、良好的加减速特性、高精度、快响应、宽调速范围、低速大转矩。
要实行这样并准确控制这样高的进给速度,对机床导轨、滚珠丝杠、伺服系统、工作台结构提出了新的要求。
高速机床普通采用线性滚动导轨代替了传统的滑动导轨,其移动速度、摩擦阻力、动态响应特性和阻尼效果都不同于传统的滑动导轨,其特有的双V型导轨结构大大提高了机床的抗扭能力,同时其磨损近乎为零,导轨精度和寿命都比以往提高几倍,配合以数字伺服电机,其进给和快速进给从过去的6m/min提高到了现在的20~60m/min。
传统的直线电动机驱动机构,由旋转电动机、齿轮箱或联轴器、丝杠和驱动螺母、丝杠支座轴承等构成的驱动系统,影响和限制了机床的性能。
例如:电动机最大转速的限制;高加速度下电动机轴产生的扭曲变形和位置误差;丝杠本身受临界转速、间隙、扭曲、螺距误差、摩擦等影响,且其振动衰减时间很长;齿轮箱增加系统惯性,产生间隙。
而直线电动机。
驱动机构则没有上述缺点,能达到快速移动(可以达到120m/min 甚至200m/min的速度)和较短的位置稳定时间,且能进一步减少机床不进行实际切削加工的非生产时间。
由于直线电动机驱动机构仅由两个互不接触部件组成,没有低效率的中间传动部件,也无机械滞后以及螺距误差,从而可达到高的效率,且其精度完全取决于反馈系统和轴承。
当用全数字伺服系统驱动直线电动机时,可达到高刚度和高固有频率,从而达到极好的伺服性能。
高速伺服系统已经发展成数字化、智能化,软件化,高速切削机床已开始使用全数字交流伺服电机和控制技术。
2.4 高速伺服系统为了实现高速切削加工,机床不但要有高速主轴,还要有高速的伺服系统,这不仅是为了提高生产效率,也是维持高速切削中刀具正常工作的必要条件,否则会造成刀个的急剧磨损与升温,破坏工件加工的表面质量。
2.4. 1 直线电机伺服系统直线电机是使电能直接转变成直线机械运动的一种推力装置,将机床进给传动链的长度缩短为零,它的动态响应性能敏捷、传动刚度高、精度高、加减速度大,行程不受限制、噪音低、成本较高,在加速度大于1g 的情况下,是伺服系统的唯一选择。
2.4. 2 滚珠丝杠驱动装置滚珠丝杠仍是高速伺服系统的主要驱动装置,用AC 伺服电机直接驱动,并采用液压轴承,进给速度可达40~60m/min ,其加速度可超过0. 6g ,成本较低,仅为直线电机的1/2. 5。
2.5 高性能的数控系统数控系统的选用要注意是否具有如下的高速加工功能:①进给速度、加减速度的控制,前馈控制,前瞻控制,冲击控制;②各种螺距补偿、反向间隙补偿、弯曲度补偿、温度补偿、跨象限补偿等;③大容量存储器,以适应复杂形状加工的需要;④程序的快速输入和处理。
高性能的数控系统组成目前常用的高性能数控系统有FANUC的16i、SIEMENS的840D和HEIDENHAIN的TNC430等,它们的脉冲当量已达纳米级。
2.6 高速切削机床本体结构的要求高速切削机床要求机床本体具有很好的静刚度、动刚度和热刚度特性等, 尤其对动态特性有很高的要求。
在设计时, 从机床结构动态特性、固有频率的角度, 进行有限元分析或利用"多体系统"进行动态仿真, 设计出最优的床身结构。
目前大多采用落地式床身, 整体铸铁结构, 龙门框架的主轴立柱, 并在立柱上增加适当的加强筋, 使机床结构具有良好的静、动态刚度和稳定性, 且有很好的吸振性。
也可采用基于S tew art平台的并联机床的床身结构, 以减轻重量, 增加刚度。
近年来高速机床的床身和立柱材料采用了聚合物混凝土或称人造花岗石, 这种材料的阻尼特性为铸铁的7~ 10倍, 而比重只有铸铁的三分之一, 是制造高速机床支承件较为适宜的材料。
3 高速切削机床发展历史与现状3.1 国外20世纪80年代,世界机床制造强国德国、日本就在政府强有力的资助下,联合众多机床制造企业,共同攻关,进行高速切削机床各相关硬件与软件的开发,并迅速实现高速切削机床的商品化。
1993年,汉诺威国际机床博览会上展出了德国制造的世界上第一台用直线电动机驱动工作台的高速加工中心,由此拉开了高速进给的序幕,高速切削技术从此快速走向成熟应用阶段。
目前,德国的高速立式铣削加工中心实用化的主轴转速已经达到60 000r/min,快速进给速度X 、Y 、Z 轴均为60m/m i n,加速度为2.5g ,重复定位精度±1μ m。
在研制高速切削机床的同时,德国还在高速切削工艺方面进行深入研究,在有色金属、复合材料、铸铁及模具钢等高速切削机理研究方面形成系统理论,以加工效率、加工精度和加工零件表面完整性为目标,对高速切削工艺进行优化,对指导高速切削生产起到很大作用。
日本于1996年研制出第一台卧式高速切削加工中心,主轴转速30 000r/min,最大进给速度80m/min,加速度为2g ,重复定位精度±1μ m。
同时在高速切削工艺方面进行了深入研究,包括高速切削工艺数据库、高速切削刀具磨损破损机理、切屑控制、高速切削过程C A D/C A M系统开发及质量控制等,从而加速高速切削技术产业化进程,在国际机床界产生重大影响。
近几年国外高速加工机床发展迅速,美国、法国、瑞士、英国、加拿大、意大利等国家相继开发出了各自的高速切削机床。
3.2 国内我国在20世纪90年代初开始有关高速切削机床及工艺的研究。
研究内容包括水泥床身、超高速主轴系统、全陶瓷轴承及磁悬浮轴承、快速进给系统、有色金属及铸铁超高速切削机理与适应刀具等方面。
通过科技工作者的艰苦工作,各项关键技术都取得了显著进展。
然而,由于种种原因,一些高速加工技术基础共性技术研究没有得到优化、集成和推广应用,未能形成系统理论,与国外发达国家差距明显。
在市场经济引进技术设备的带动下,我国高速机床技术有了长足进步。
现在国内10 000~15 000r/min的立式加工中心、18 000r/min的卧式加工中心、 3 500~4 000r/min的数控车床和车削中心已批量生产,切削速度达8 000r/min的数控车床也已问世。
高速机床的高档数控系统和开放式数控系统正在深入研究中,但目前主要还是依赖进口。
目前国内正逐步开始推广应用高速切削技术,主要是应用在航空航天、模具和汽车工业,加工铝合金和铸铁较多,采用的刀具以进口为主。
我国现在的国情是,在航空、汽车和模具等生产部门,已进口相当规模的高速切削机床,而且进口高速切削机床数量还在进一步上升。
4 结束语高速切削加工技术是一项全新的、正在发展中的先进实用技术,在理论和技术各方面还有大量研究、开发工作要做。
我国高速切削加工技术的开发和应用还处于初步阶段,但国内已进口了大批高速加工设备,也开发了多种高速加工机床,只要我们充分认识高速切削加工技术的优越性,完全有可能把我国切削加工水平推进到一个新高度。
参考文献[1]张伯霖.高速切削技术及应用.机械工业出版社,2003.4[2]艾兴,刘战强,赵军,邓建新,宋世学.高速切削刀具材料的进展和未来.制造技术与机床 ,2001.8[3]刘文化.高速加工机床的发展历史与现状.金属加工, 2010.12[4]王正君,史津平,周小玉.高速超高速切削及高速机床.机床与液压,2001.1[5]胡秋.高速机床关键技术及其发展趋势.机床与液压, 2001.8[6]徐彪,李长光.高速切削的技术装备.电子机械工程,2002.Vol.18 No.6[7]孙全平,廖文和.高速切削的现状及其关键技术.淮阴工学院学报,Feb. 2002 Vol.11 No.1[8]吴明友.高速切削机床.煤矿机械,2006.6[9]张宁菊.高速切削机床的关键技术.机床与液压,2005.11[10]周华, 石彦华.高速切削机床的关键技术及其应用.现代制造工程,2008.8[11]朱从容,顾平灿.高速切削技术及高速切削机床.精密制造与自动化,2002.3。