框架中桥施工组织设计毕业论文正文
桥梁施工组织设计-毕业设计定稿

京张7 号大桥施工组织设计2011年6月目录引言 (1)第一章、编制依据和原则 (2)一、编制范围 (2)二、编制依据 (2)三、编制原则 (2)第二章、工程概况介绍 (3)一、地理位置 (3)二、气候及水文条件 (3)三、地质条件 (3)四、技术标准 (4)第三章、施工方案的确定及部署 (4)一、施工流的确定 (4)二、施工组织及顺序的确定 (4)三、施工方案的确定 (6)第四章、施工场地布置及施工准备 (18)第五章、劳动人员准备 (19)第六章、施工总进度计划 (20)第七章、施工总平面布置 (20)第八章、保证工期的主要技术措施 (21)第九章、季节性施工措施 (22)第十章、质量保证体系 (23)第十一章、安全生产保证措施 (23)第十二章、年、季度用款计划安排 (24)第十三章、文明施工措施及环境保护 (24)第十四章、技术管理措施 (25)第十五章、新技术的研究与推广应用 (26)第十六章、施工降低工程成本的措施 (26)结论 (27)参考文献 (27)致谢 (28)引言随着桥梁工程技术的发展,科学、合理的施工组织设计对于桥梁工程施工的指导作用愈发重要。
施工组织设计是以整个建设项目为对象,根据设计图纸以及其他有关资料和现场施工条件编制的用以指导工地各项施工准备和施工活动的技术经济文件。
该设计影响着整个工程的质量、进度、经济效益等。
因此,施工组织设计要合理的运用人力、物力、财力等资源,即结合工程实际情况,以承包合同、设计图纸以及国家相关法律法规为依据;在保证质量和安全的前提下,秉承技术先进、经济合理的原则,使桥梁施工活动全过程科学化、系统化、规范化,从而使桥梁施工各方都能获得最大的利益。
本施工组织设计是公路桥梁施工组织设计(京张7号大桥施工组织设计),该设计的编制依据招标文件、设计图纸、各种规范、国家政策及当地法规等。
其编制包括:工程概况和特点分析;施工部署和主要工程项目施工方案;施工进度计划;施工资源需求量;施工总平面图;各种施工保证措施等,认真地编制好施工组织设计,同时对这些错综复杂的活动进行组织和协调,对保证施工的顺利进行具有重要意义。
施工组织设计毕业论文范文

施工组织设计毕业论文范文施工组织设计毕业论文范文:一场“工地风云”在这个充满阳光的春天,我们的大学生活即将画上一个圆满的句号。
在这个特殊的时刻,我们要用一篇毕业论文来纪念这段美好的时光。
这篇论文的主题是施工组织设计,它就像是一场“工地风云”,让我们一起揭开它的神秘面纱吧!我们要了解什么是施工组织设计。
简单来说,施工组织设计就是对建筑工程项目的施工过程进行合理的规划和安排,以确保工程顺利进行。
在这场“工地风云”中,我们需要运用各种技巧和方法,让这场演出变得更加精彩。
我们要明确论文的结构。
按照题目要求,我们可以采用1,1.1,1.2,2,2.1,2.2,3,3.1,3.2等大纲结构。
这样既能保证文章的条理性,又能让我们更好地组织语言。
接下来,我们要进行文献综述。
在这部分,我们要对施工组织设计的相关理论和方法进行梳理和总结。
我们可以通过查阅大量的书籍、论文和报告来获取这些信息。
在这个过程中,我们要学会筛选和整理资料,以便为后续的分析和讨论做好准备。
在文献综述的基础上,我们要进行案例分析。
在这部分,我们可以选择一个典型的建筑工程项目作为案例,对其施工组织设计进行详细的分析和评价。
通过对案例的研究,我们可以更好地理解施工组织设计的原理和方法,同时也能提高我们的实际操作能力。
我们还要进行相关的实验和模拟。
在这个过程中,我们可以运用现代科技手段,如计算机仿真、虚拟现实等,来模拟施工现场的情况。
通过实验和模拟,我们可以更加直观地了解施工组织设计的效果,为实际工程提供有益的参考。
我们要撰写论文的结论部分。
在这个部分,我们要对我们的研究结果进行总结和归纳,同时也可以提出一些改进和完善的建议。
在这个过程中,我们要注意保持谦虚谨慎的态度,不断反思和学习。
这篇毕业论文就像是一场“工地风云”,让我们在学习和实践中不断成长和进步。
在这个过程中,我们要学会运用各种技巧和方法,让这场演出变得更加精彩。
相信通过我们的努力,一定能够圆满完成这场“工地风云”,为我们的人生画上一个圆满的句号!。
某工程框架完整施工组织设计
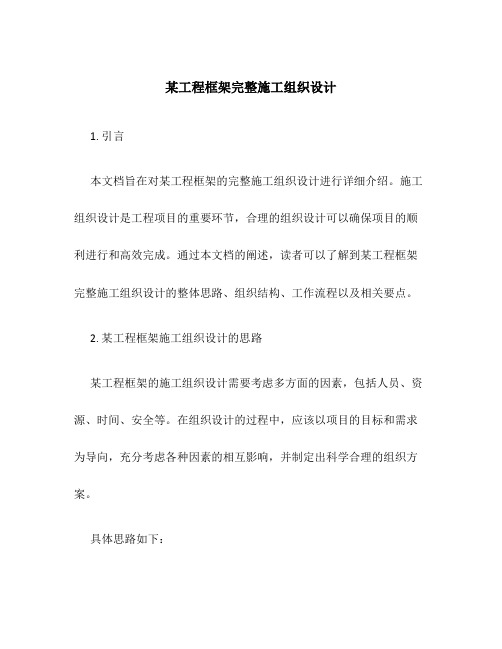
某工程框架完整施工组织设计1. 引言本文档旨在对某工程框架的完整施工组织设计进行详细介绍。
施工组织设计是工程项目的重要环节,合理的组织设计可以确保项目的顺利进行和高效完成。
通过本文档的阐述,读者可以了解到某工程框架完整施工组织设计的整体思路、组织结构、工作流程以及相关要点。
2. 某工程框架施工组织设计的思路某工程框架的施工组织设计需要考虑多方面的因素,包括人员、资源、时间、安全等。
在组织设计的过程中,应该以项目的目标和需求为导向,充分考虑各种因素的相互影响,并制定出科学合理的组织方案。
具体思路如下:2.1 项目目标和需求分析在开始施工组织设计前,应对项目的目标和需求进行全面的分析和评估。
了解项目的规模、技术要求、时间周期等信息,为后续的组织设计提供基础数据。
2.2 确定组织结构根据项目的特点和规模,确定适合的组织结构。
组织结构应该明确各个部门的职责和权限,确保项目各项工作能够有序进行。
2.3 制定工作流程根据项目的工程内容和施工阶段,制定相应的工作流程。
工作流程应该清晰明确,包括工作任务的划分、工作内容的流程化、工作人员的配备等。
2.4 安全管理安全是任何工程项目的重要因素,应在施工组织设计中充分考虑。
制定科学的安全管理措施,确保施工过程中的安全。
3. 某工程框架施工组织设计的组织结构某工程框架的施工组织结构如下图所示:# TODO: 插入组织结构图该组织结构包括了项目经理、工程师、施工队长、监理人员等角色,他们各司其职,协同工作,确保工程项目的顺利进行。
4. 某工程框架施工组织设计的工作流程某工程框架的施工工作流程如下:4.1 施工准备阶段•完善项目准备工作,包括项目资料整理、人员配备、施工设备准备等。
•制定施工方案和工作计划,明确工作任务和时间节点。
4.2 施工实施阶段•根据工作计划组织人员和设备,按照施工方案进行工作。
•监督施工现场,确保施工质量和进度。
4.3 施工总结阶段•对施工过程进行总结和评估,发现问题并进行改进。
中桥施工方案(3篇)

第1篇一、项目背景随着我国经济的快速发展,交通基础设施建设日益重要。
桥梁作为交通基础设施的重要组成部分,其施工质量直接关系到交通的安全与畅通。
本方案针对一座中型桥梁的施工进行详细规划,以确保工程顺利进行,达到预期目标。
二、工程概况1. 工程名称:XX中桥2. 工程地点:XX市XX区XX街道3. 桥梁长度:80米4. 桥梁宽度:15米5. 桥梁结构:预应力混凝土T型梁6. 设计荷载:公路-Ⅰ级7. 施工工期:12个月三、施工组织机构1. 施工项目经理部(1)项目经理:全面负责项目的施工管理工作。
(2)项目副经理:协助项目经理工作,负责项目的质量、安全、进度、成本等管理工作。
(3)项目总工:负责项目的工程技术管理工作。
(4)各专业工程师:负责各自专业领域的工程技术管理工作。
2. 施工班组(1)钢筋班组:负责钢筋加工、绑扎、焊接等工作。
(2)模板班组:负责模板制作、安装、拆除等工作。
(3)混凝土班组:负责混凝土的拌制、运输、浇筑、养护等工作。
(4)起重班组:负责桥梁施工中的起重作业。
(5)测量班组:负责桥梁施工中的测量工作。
四、施工工艺1. 施工准备(1)现场勘查:对施工现场进行勘查,了解地质、水文、交通等情况。
(2)施工图纸会审:组织相关人员对施工图纸进行会审,确保施工图纸的准确性。
(3)材料、设备准备:根据施工进度,提前准备所需材料、设备。
(4)施工方案编制:根据施工图纸、现场情况及施工要求,编制施工方案。
2. 施工过程(1)基础施工1)桩基础施工:采用旋挖钻机进行桩基础施工,确保桩位准确、垂直度满足要求。
2)承台施工:采用现浇混凝土进行承台施工,确保承台强度、刚度满足要求。
(2)桥墩施工1)桥墩基础施工:采用现浇混凝土进行桥墩基础施工,确保基础强度、刚度满足要求。
2)桥墩身施工:采用现浇混凝土进行桥墩身施工,确保桥墩身强度、刚度满足要求。
(3)桥台施工1)桥台基础施工:采用现浇混凝土进行桥台基础施工,确保基础强度、刚度满足要求。
道路桥梁工程技术毕业设计(论文)-大桥施工组织设计
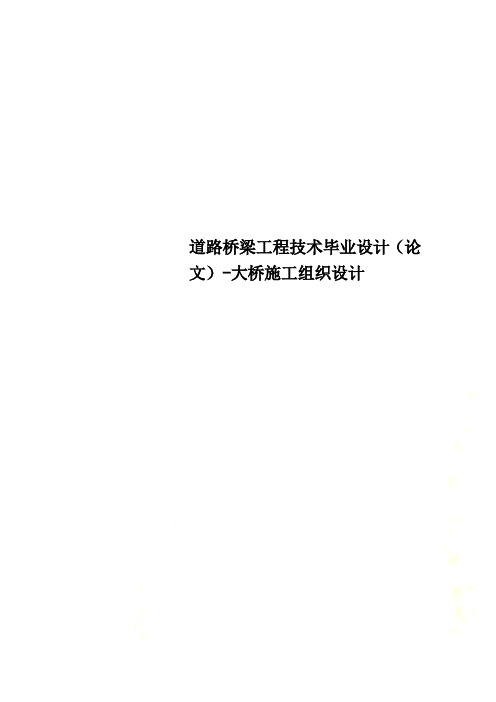
道路桥梁工程技术毕业设计(论文)-大桥施工组织设计存档号:_ _ 学号:200801031075石家庄铁路职业技术学院毕业设计系部:交通系姓名:专业: 道路桥梁工程技术指导教师Ⅰ:指导教师Ⅱ:二零一一年六月石家庄铁路职业技术学院毕业论文任务书学生用表指导教师签名:年月目录目录 (1)摘要 (3)第一章编制依据及原则 (1)1.编制依据 (1)2.编制原则 (1)第二章工程概况及主要工程数量表 (2)2.1工程简介 (2)2.2水文、地质及气象 (2)2.2.1水文 (2)2.2.2工程地质 (2)2.2.3气象情况 (3)2.3主要工程数量表 (3)第三章施工总体规划 (4)3.1施工组织机构及施工队伍分布 (4)3.2总体布局及施工统筹 (5)3.2.1钢筋加工场 (5)3.2.2混凝土供应 (5)3.2.3技术准备 (5)3.2.4施工测量 (5)3.2.5相关单位协调 (5)3.3过渡方案 (5)3.3.1施工便道 (5)3.3.2跨河、跨沟 (7)3.4施工用电、用水及通讯 (7)3.4.1施工用电 (7)3.4.2施工、生活用水 (7)3.4.3施工通讯 (8)3.5主要施工机械 (8)第四章总体施工方案及各分项工程施工方案、工艺 (8)4.1总体施工方案 (8)4.1.1桩基施工 (8)4.1.2承台施工 (8)4.1.3墩身施工 (9)4.1.4桥台施工 (9)4.2各分项工程施工方案、工艺 (9)4.2.1桩基施工 (9)4.2.2承台施工 (15)4.2.3墩身施工 (18)4.3.4附属工程施工 (21)4.3.5综合接地系统 (21)第五章施工进度计划 (22)5.1总工期安排 (22)5.2本桥工程进度计划 (22)5.3本桥资金使用计划 (25)第六章工期目标及保证措施................................................................................................................... - 25 -6.1工期目标 (25)6.2工期保证措施 (28)6.2.1组织保证措施 (28)6.2.2制度保证措施 (28)6.2.3技术保证措施 (28)6.2.4物资保证措施 (28)6.2.5后勤保证措施 (29)第七章质量目标及保证措施................................................................................................................. - 29 -7.1质量目标 (30)7.2质量体系组织机构 (30)7.2.1质量保证体系 (30)7.2.2质量体系组织机构设置 (33)7.3质量保证措施 (34)7.4质量管理制度 (34)7.4.1施工测量复核制度 (34)7.4.2施工图现场核对制度 (34)7.4.3施工技术交底制度 (35)7.4.5成品、半成品保护制度 (37)7.4.6特殊工种、关键岗位持证上岗制度 (37)7.4.7质量责任制、质量事故报告和责任追究制度 (39)7.4.8施工工艺流程设计及工艺试验制度 (40)7.4.9质量信息管理制度 (41)7.4.10基础技术资料管理制度 (41)第八章安全及环保............................................................................................................................... - 42 -8.1安全保证体系及措施 (42)8.1.1安全管理组织机构 (43)8.1.2安全保证体系 (43)8.1.2.1建立安全生产责任制 (43)8.1.3安全生产保证措施 (46)8.1.4其他安全措施 (49)8.2环保、水保、文物保护措施 (50)8.2.1环境保护方针与目标 (50)8.2.2环境保护体系 (51)8.2.3施工环保、水土保持措施 (52)8.2.4文物保护措施 (54)8.2.5临时工程的使用与恢复 (55)第九章全文总结及工程展望............................................................................................................... - 55 -9.1主要结论 (55)9.2工程展望 (57)参考文献 .................................................................................................................................................. - 58 -致谢 .................................................................................................................................................... - 59 -摘要设计是根据设计任务书的要求,现行的国家有关方针政策,以及国家和铁道部有关法律、规范、验标、施工指南和铁道部最新规章制度等,对何村大桥桥进行方案比选和设计的。
框架结构施工组织设计(共10篇)
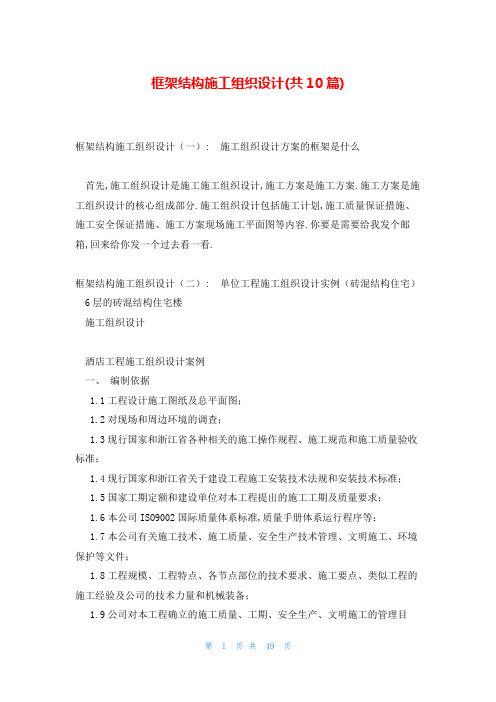
框架结构施工组织设计(共10篇)框架结构施工组织设计(一): 施工组织设计方案的框架是什么首先,施工组织设计是施工施工组织设计,施工方案是施工方案.施工方案是施工组织设计的核心组成部分.施工组织设计包括施工计划,施工质量保证措施、施工安全保证措施、施工方案现场施工平面图等内容.你要是需要给我发个邮箱,回来给你发一个过去看一看.框架结构施工组织设计(二): 单位工程施工组织设计实例(砖混结构住宅) 6层的砖混结构住宅楼施工组织设计酒店工程施工组织设计案例一、编制依据1.1工程设计施工图纸及总平面图;1.2对现场和周边环境的调查;1.3现行国家和浙江省各种相关的施工操作规程、施工规范和施工质量验收标准;1.4现行国家和浙江省关于建设工程施工安装技术法规和安装技术标准;1.5国家工期定额和建设单位对本工程提出的施工工期及质量要求;1.6本公司ISO9002国际质量体系标准,质量手册体系运行程序等;1.7本公司有关施工技术、施工质量、安全生产技术管理、文明施工、环境保护等文件;1.8工程规模、工程特点、各节点部位的技术要求、施工要点、类似工程的施工经验及公司的技术力量和机械装备;1.9公司对本工程确立的施工质量、工期、安全生产、文明施工的管理目标.二、工程概况2.1工程地点及地貌大酒店工程位于 ,紧靠南龙公路,交通十分便利,三通一平己经完成,场地比较开阔.2.2建筑形式本酒店平面几何形状为“角尺”形,东西向长度为40.27米,南北向长度为38.08米;东侧面房为框架结构,西侧面房为混合结构,共计层数为五层.框架部分层高为3.8米,混合结构部分层高为3.2米,室内外高差为0.6米,总高度为89米(室外地坪至檐口标高);建筑面积为7899.78平方米.2.3工程结构本工程分为东侧房和西侧房两部份,东侧房为四层框架结构,西侧房为五层混合结构,设计抗震设防烈度为7级,建筑场地类别按三类.行的话留个邮箱给我我发给你框架结构施工组织设计(三): 框架结构设计步骤是什么了较长,建议你复制下来放电脑上慢慢看,应该能帮到你!框架结构设计步骤及要点1. 结构设计说明主要是设计依据,抗震等级,人防等级,地基情况及承载力,防潮抗渗做法,活荷载值,材料等级,施工中的注意事项,选用详图,通用详图或节点,以及在施工图中未画出而通过说明来表达的信息.如混凝土的含碱量不得超过3kg/m3等等.2. 各层的结构布置图,包括:(1).预制板的布置(板的选用、板缝尺寸及配筋).标注预制板的块数和类型时, 不要采用对角线的形式.因为此种方法易造成线的交叉, 宜采用水平线或垂直线的方法, 相同类型的房间直接标房间类型号.应全楼统一编号,可减少设计工作量,也方便施工人员看图.板缝尽量为40, 此种板缝可不配筋或加一根筋.布板时从房间里面往外布板, 尽量采用宽板, 现浇板带留在靠窗处, 现浇板带宽最好≥200(考虑水暖的立管穿板).如果构造上要求有整浇层时, 板缝应大于60.整浇层厚50, 配双向φ[email protected], 混凝土C20.纯框架结构一般不需要加整浇层.构造柱处不得布预制板.地下车库由于防火要求不可用预制板.框架结构不宜使用长向板,否则长向板与框架梁平行相接处易出现裂缝.建议使用PMCAD的人工布板功能布预制板,自动布板可能不能满足用户的施工图要求,仅能满足定义荷载传递路线的要求.(2).现浇板的配筋(板上、下钢筋,板厚尺寸).板厚一般取120、140、160、180四种尺寸或120、150、180三种尺寸.尽量用二级钢包括直径φ10(目前供货较少)的二级钢,直径≥12的受力钢筋,除吊钩外,不得采用一级钢.钢筋宜大直径大间距,但间距不大于200,间距尽量用200.(一般跨度小于6.6米的板的裂缝均可满足要求).跨度小于2米的板上部钢筋不必断开,钢筋也可不画,仅说明钢筋为双向双排钢筋多少上下钢筋间距宜相等,直径可不同,但钢筋直径类型也不宜过多.顶层及考虑抗裂时板上筋可不断,或50%连通,较大处附加钢筋,拉通筋均应按受拉搭接钢筋.板配筋相同时,仅标出板号即可.一般可将板的下部筋相同和部分上部筋相同的板编为一个板号,将不相同的上部筋画在图上.当板的形状不同但配筋相同时也可编为一个板号.应全楼统一编号.当考虑穿电线管时,板厚≥120,不采用薄板加垫层的做法.电的管井电线引出处的板,因电线管过多有可能要加大板厚至180(考虑四层32的钢管叠加).宜尽量用大跨度板,不在房间内(尤其是住宅)加次梁.说明分布筋为φ[email protect ed]板顶标高不同时,板的上筋应分开或倾斜通过.现浇挑板阳角加辐射状附加筋(包括内墙上的阳角).现浇挑板阴角的板下宜加斜筋.顶层应建议甲方采用现浇楼板,以利防水,并加强结构的整体性及方便装饰性挑沿的稳定.外露的挑沿、雨罩、挑廊应每隔10~15米设一10mm的缝,钢筋不断.尽量采用现浇板,不采用予制板加整浇层方案.卫生间做法可为70厚+10高差(取消垫层).8米以下的板均可以采用非预应力板.L、T或十字形建筑平面的阴角处附近的板应现浇并加厚,双向双排配筋,并附加45度的4根16的抗拉筋.现浇板的配筋建议采用PMCAD软件自动生成,一可加快速度,二来尽量减小笔误.自动生成楼板配筋时建议不对钢筋编号,因工程较大时可能编出上百个钢筋号,查找困难,如果要编号,编号不应出房间.配筋计算时,可考虑塑性内力重分布,将板上筋乘以0.8~0.9的折减系数,将板下筋乘以1.1~1.2的放大系数.值得注意的是,按弹性计算的双向板钢筋是板某几处的最大值,按此配筋是偏于保守的,不必再人为放大.支承在外圈框架梁上的板负筋不宜过大,否则将对梁产生过大的附加扭距.一般:板厚>150时采用φ[email protected];否则用φ[emai l protected]生成的板配筋图应注意以下几点:1.单向板是按塑性计算的,而双向板按弹性计算,宜改成一种计算方法.2.当厚板与薄板相接时,薄板支座按固定端考虑是适当的,但厚板就不合适,宜减小厚板支座配筋,增大跨中配筋.3.非矩形板宜减小支座配筋,增大跨中配筋.4.房间边数过多或凹形板应采用有限元程序验算其配筋.PMCAD生成的板配筋图为PM.T.板一般可按塑性计算,尤其是基础底板和人防结构.但结构自防水、不允许出现裂缝和对防水要求严格的建筑, 如坡、平屋顶、橱厕、配电间等应采用弹性计算.室内轻隔墙下一般不应加粗钢筋,一是轻隔墙有可能移位,二是板整体受力,应整体提高板的配筋.只有垂直单向板长边的不可能移位的隔墙,如厕所与其他房间的隔墙下才可以加粗钢筋.坡屋顶板为偏拉构件,应双向双排配筋.(3).关于过梁布置及轻隔墙.现在框架填充墙一般为轻墙,过梁一般不采用预制混凝土过梁,而是现浇梁带.应注明采用的轻墙的做法及图集,如北京地区的京94SJ19,并注明过梁的补充筋.当过梁与柱或构造柱相接时,柱应甩筋,过梁现浇.不建议采用加气混凝土做围护墙,装修难做并不能用在厕所处.(4).雨蓬、阳台、挑檐布置和其剖面详图.注意:雨棚和阳台的竖板现浇时,最小厚度应为80,否则难以施工.竖筋应放在板中部.当做双排筋时,高度900时,最小板厚120.阳台的竖板应尽量现浇,预制挡板的相交处极易裂缝.雨棚和阳台上有斜的装饰板时,板的钢筋放斜板的上面,并通过水平挑板的下部锚入墙体圈梁(即挑板双层布筋).两侧的封板可采用泰柏板封堵,钢筋与泰柏板的钢丝焊接,不必采用混凝土结构.挑板挑出长度大于2米时宜配置板下构造筋,较长外露挑板(包括竖板)宜配温度筋.挑板内跨板上筋长度应大于等于挑板出挑长度,尤其是挑板端部有集中荷载时.内挑板端部宜加小竖沿,防止清扫时灰尘落下.当顶层阳台的雨搭为无组织排水时,雨搭出挑长度应大于其下阳台出挑长度100,顶层阳台必须设雨搭.挑板配筋应有余地,并应采用大直径大间距钢筋,给工人以下脚的地方,防止踩弯.挑板内跨板跨度较小,跨中可能出现负弯距,应将挑板支座的负筋伸过全跨.挑板端部板上筋通常兜一圈向上,但当钢筋直径大于等于12时是难以施工的,应另加筋.(5).楼梯布置.采用X型斜线表示楼梯间,并注明楼梯间另详.尽量用板式楼梯,方便设计及施工,也较美观.(6).板顶标高.可在图名下说明大多数的板厚及板顶标高,厨厕及其它特殊处在其房间上另外标明.(7).梁布置及其编号,也可按层编号,如L-1-XX,1指1层,XX为梁的编号.柱布置及编号.(8).板上开洞(厨、厕、电气及设备)洞口尺寸及其附加筋,附加筋不必一定锚入板支座,从洞边锚入La即可.板上开洞的附加筋,如果洞口处板仅有正弯距,可只在板下加筋;否则应在板上下均加附加筋.留筋后浇的板宜用虚线表示其范围,并注明用提高一级的膨胀混凝土浇筑.未浇筑前应采取有效支承措施.住宅跃层楼梯在楼板上所开大洞,周边不宜加梁,应采用有限元程序计算板的内力和配筋.板适当加厚, 洞边加暗梁.(9).屋面上人孔、通气孔位置及详图.(10).在平面图上不能表达清楚的细节要加剖面,可在建筑墙体剖面做法的基础上,对应画结构详图.3. 基础平面图及详图:(1).在柱下扩展基础宽度较宽(大于4米)或地基不均匀及地基较软时宜采用柱下条基.并应考虑节点处基础底面积双向重复使用的不利因素,适当加宽基础.(2).当基础下有防空洞或枯井等时,可做一大厚板将其跨过.(3).混凝土基础下应做垫层.当有防水层时,应考虑防水层厚度.(4).建筑地段较好,基础埋深大于3米时,应建议甲方做地下室.地下室底板,当地基承载力满足设计要求时,可不再外伸以利于防水.每隔30~40米设一后浇带,并注明两个月后用微膨胀混凝土浇注.设置地下室可降低地基的附加应力,提高地基的承载力(尤其是在周围有建筑时有用),减少地震作用对上部结构的影响.不应设局部地下室,且地下室应有相同的埋深.可在筏板区格中间挖空垫聚苯来调整高低层的不均匀沉降.(5).地下室外墙为混凝土时,相应的楼层处梁和基础梁可取消.(6).抗震缝、伸缩缝在地面以下可不设缝,连接处应加强.但沉降缝两侧墙体基础一定要分开.(7).新建建筑物基础不宜深于周围已有基础.如深于原有基础,其基础间的净距应不少于基础之间的高差的1.5至2倍,否则应打抗滑移桩,防止原有建筑的破坏.建筑层数相差较大时,应在层数较低的基础方格中心的区域内垫焦碴来调整基底附加应力.(8).独立基础偏心不能过大,必要时可与相近的柱做成柱下条基.柱下条形基础的底板偏心不能过大,必要时可作成三面支承一面自由板(类似筏基中间开洞).两根柱的柱下条基的荷载重心和基础底版的形心宜重合,基础底板可做成梯形或台阶形,或调整挑梁两端的出挑长度.(9).采用独立柱基时,独立基础受弯配筋不必满足最小配筋率要求,除非此基础非常重要,但配筋也不得过小.独立基础是介于钢筋混凝土和素混凝土之间的结构.面积不大的独立基础宜采用锥型基础,方便施工.(10).独立基础的拉梁宜通长配筋,其下应垫焦碴.拉梁顶标高宜较高,否则底层墙体过高.(11).底层内隔墙一般不用做基础,可将地面的混凝土垫层局部加厚.(12).考虑到一般建筑沉降为锅底形、结构的整体弯曲和上部结构和基础的协同作用,顶、底板钢筋应拉通(多层的负筋可截断1/2或1/3),且纵向基础梁的底筋也应拉通.(13).基础平面图上应加沉降观测点.(14).基础底板混凝土不宜大于C30,一是没用,二是容易出现裂缝.(15).可用JCCAD软件自动生成基础布置和基础详图.生成的基础平面图名为JCPM.T,生成的基础详图名为JCXT.T.(16).基础底面积不应因地震附加力而过分加大,否则地震下安全了而常规情况下反而沉降差异较大,本末倒置.请参照《建筑地基基础设计规范GB50007-2023》和各地方的地基基础规程.4. 暖沟图及基础留洞图:(1).沟盖板在遇到电线管时下降(500),室外暖沟上一般有400厚的覆土.(2).注明暖沟两侧墙体的厚度及材料作法.暖沟较深时应验算强度.(3).洞口大于400时应加过梁,暖沟应加通气孔.(4).基础埋深较浅时暖沟入口底及基础留洞有可能比基础还低,此时基础应局部降低.(5).湿陷性黄土地区或膨胀土地区暖沟做法不同于一般地区.应按湿陷性黄土地区或膨胀土地区的特殊要求设计.(6).暖沟一般做成1200宽,1000的在维修时偏小.5. 楼梯详图:(1).应注意:梯梁至下面的梯板高度是否够,以免碰头,尤其是建筑入口处.(2).梯段高度高差不宜大于20,以免易摔跤(3).两倍的梯段高度加梯段长度约等于600.幼儿园楼梯踏步宜120高.(4).楼梯折板、折梁阴角在下时纵筋应断开,并锚入受压区内La,折梁还应加附加箍筋(5).楼梯的建筑做法一般与楼面做法不同,注意楼梯板标高与楼面板的衔接.(6).楼梯梯段板计算方法:当休息平台板厚为80~100,梯段板厚100~130,梯段板跨度小于4米时,应采用1/10的计算系数,并上下配筋相同;当休息平台板厚为80~100,梯段板厚160~200,梯段板跨度约6米左右时,应采用1/8的计算系数,板上配筋可取跨中的1/3~1/4,并且不得过大.此两种计算方法是偏于保守的.任何时候休息平台与梯段板平行方向的上筋均应拉通,并应与梯段板的配筋相应.梯段板板厚一般取1/25~1/30跨度.(7).注意当板式楼梯跨度大于5米时,挠度不容易满足.应注明加大反拱或增大配筋.(8).当休息平台板为悬挑板时,其内部的楼梯梯段板负筋应大于休息平台板的板上筋,长度也应大于平台板筋.(9).楼层处的休息平台板的配筋应与楼层板统一考虑配筋,主要是板的负筋.6. 梁详图:(1).梁上有次梁处(包括挑梁端部)应附加箍筋和吊筋,宜优先采用附加箍筋.梁上小柱和水箱下, 架在板上的梁, 不必加附加筋.可在结构设计总说明处画一节点,有次梁处两侧各加三根主梁箍筋,荷载较大处详施工图.(2).当外部梁跨度相差不大时,梁高宜等高,尤其是外部的框架梁.当梁底距外窗顶尺寸较小时,宜加大梁高做至窗顶.外部框架梁尽量做成外皮与柱外皮齐平.梁也可偏出柱边一较小尺寸.梁与柱的偏心可大于1/4柱宽,并宜小于1/3柱宽.(3).折梁阴角在下时纵筋应断开,并锚入受压区内La,还应加附加箍筋(4).梁上有次梁时,应避免次梁搭接在主梁的支座附近,否则应考虑由次梁引起的主梁抗扭,或增加构造抗扭纵筋和箍筋.(此条是从弹性计算角度出发).当采用现浇板时,抗扭问题并不严重.(5).原则上梁纵筋宜小直径小间距,有利于抗裂,但应注意钢筋间距要满足要求,并与梁的断面相应.箍筋按规定在梁端头加密.布筋时应将纵筋等距,箍筋肢距可不等.小断面的连续梁或框架梁,上、下部纵筋均应采用同直径的,尽量不在支座搭接.(6).端部与框架梁相交或弹性支承在墙体上的次梁,梁端支座可按简支考虑,但梁端箍筋应加密.(7).考虑抗扭的梁,纵筋间距不应大于300和梁宽,即要求加腰筋,并且纵筋和腰筋锚入支座内La.箍筋要求同抗震设防时的要求.(8).反梁的板吊在梁底下,板荷载宜由箍筋承受,或适当增大箍筋.梁支承偏心布置的墙时宜做下挑沿.(9).挑梁宜作成等截面(大挑梁外露者除外).与挑板不同,挑梁的自重占总荷载的比例很小,作成变截面不能有效减轻自重.变截面挑梁的箍筋,每个都不一样,难以施工.变截面梁的挠度也大于等截面梁.挑梁端部有次梁时,注意要附加箍筋或吊筋.一般挑梁根部不必附加斜筋,除非受剪承载力不足.对于大挑梁,梁的下部宜配置受压钢筋以减小挠度.挑梁配筋应留有余地.(10).梁上开洞时,不但要计算洞口加筋,更应验算梁洞口下偏拉部分的裂缝宽度.梁从构造上能保证不发生冲切破坏和斜截面受弯破坏.(11).梁净高大于500时,宜加腰筋,间距200,否则易出现垂直裂缝.(12).挑梁出挑长度小于梁高时,应按牛腿计算或按深梁构造配筋.(13).尽量避免长高比小于4的短梁,采用时箍筋应全梁加密,梁上筋通长,梁纵筋不宜过大.(14).扁梁宽度不必过大,只要钢筋能正常摆下及受剪满足即可.因为在挠度计算时,梁宽对刚度影响不大,加宽一倍,挠度减小20%左右.相对来讲,增大钢筋更经济,钢筋加大一倍,挠度减小60%左右,同时梁的上筋应大部分通长布置,以减小混凝土徐变对挠度的增大,如果上筋不小于下筋,挠度减小20%.(15).框架梁高取1/10~1/15跨度,扁梁宽可取到柱宽的两倍.扁梁的箍筋应延伸至另一方向的梁边.(16).当一宽框架梁托两排间距较小的柱时,可加一刚性挑梁,两个柱支承在刚性挑梁的端头.(17).梁宽大于350时,应采用四肢箍.7. 柱详图:(1).地上为圆柱时,地下部分应改为方柱,方便施工.圆柱纵筋根数最少为8根,箍筋用螺旋箍,并注明端部应有一圈半的水平段.方柱箍筋应使用井字箍,并按规范加密.角柱、楼梯间柱应增大纵筋并全柱高加密箍筋.幼儿园不宜用方柱.(2).原则上柱的纵筋宜大直径大间距,但间距不宜大于200.(3).柱内埋管,由于梁的纵筋锚入柱内,一般情况下仅在柱的四角才有条件埋设较粗的管.管截面面积占柱截面4%以下时,可不必验算.柱内不得穿暖气管.(4).柱断面不宜小于450X450,混凝土不宜小于C25,否则梁纵筋锚入柱内的水平段不容易满足0.45La的要求,不满足时应加横筋.异型柱结构,梁纵筋一排根数不宜过多,柱端部纵筋不宜过密,否则节点混凝土浇筑困难.当有部分矩形柱部分异型柱时,应注意异型柱的刚度要和矩形柱相接近,不要相差太大.(5).柱应尽量采用高强度混凝土来满足轴压比的限制,减小断面尺寸.(6).尽量避免短柱,短柱箍筋应全高加密,短柱纵筋不宜过大.(7).考虑到竖向地震作用,柱子的轴压比及配筋宜留有余地.(8).独立柱上或柱的中部(半层处)有挑梁时,挑梁长度应有限制.在用PKPM软件计算梁柱时,应尽量采用TAT或SATWE三维软件.相对平面框架PK来讲,第一,计算结果更接近实际受力状态,如地震力或风力是按抗侧移刚度分配,而不是按框架的楼面从属面积,还如从框架柱出挑的梁和从次梁出挑的梁,因次梁的支座(框架梁)发生下沉变形,内力重分布,从框架柱出挑的挑梁配筋将较大.第二,快速方便,三维软件整体计算,不必生成单榀框架,再人工归并,可整楼归并.第三,TAT或SATWE还可以进行井式梁的计算,由于PKPM软件计算梁时仅按矩形计算,而井式梁的断面较小,有可能超筋,此时可取出弯距再按T型梁补充计算,不必直接加大梁高.在绘制施工图时,较大直径的钢筋连接宜用机械连接取代焊接,造价相差不大,但机械连接可靠并易于检查.机械连接接头位置可任意,但一次截断的钢筋不大于50%,接头位置应错开70d.8. 重点注意或设计原则:(1).抗震验算时不同的楼盖及布置(整体性)决定了采用刚性、刚柔、柔性理论计算.抗震验算时应特别注意场地土类别.8度超过5层有条件时,尽量加剪力墙,可大大改善结构的抗震性能.框架结构应设计成双向梁柱刚接体系,但也允许部分的框架梁搭在另一框架梁上.应加强垂直地震作用的设计,从震害分析,规范给出的垂直地震作用明显不足.(2).雨蓬不得从填充墙内出挑.大跨度雨蓬、阳台等处梁应考虑抗扭.考虑抗扭时,扭矩为梁中心线处板的负弯距乘以跨度的一半.(3).框架梁、柱的混凝土等级宜相差一级.(4).由于某些原因造成梁或过梁等截面较大时,应验算构件的最小配筋率.(5).出屋面的楼电梯间不得采用砖混结构.(6).框架结构中的电梯井壁宜采用粘土砖砌筑,但不能采用砖墙承重.应采用每层的梁承托每层的墙体重量.梯井四角加构造柱,层高较高时宜在门洞上方位置加圈梁.因楼电梯间位置较偏,梯井采用混凝土墙时刚度很大,其它地方不加剪力墙,对梯井和整体结构都十分不利.(7).建筑长度宜满足伸缩缝要求,否则应采取措施.如:增大配筋率,通长配筋,改善保温,铺设架空层,加后浇带等.(8).柱子轴压比宜满足规范要求.(9).当采用井字梁时,梁的自重大于板自重,梁自重不可忽略不计.周边一般加大截面的边梁.(10).过街楼处的梁上筋应通长,按偏拉构件设计.(11).电线管集中穿板处,板应验算抗剪强度或开洞形成管井.电线管竖向穿梁处应验算梁的抗剪强度.(12).构件不得向电梯井内伸出, 否则应验算是否能装下.电梯井处柱可外移或做成L型柱.(13).验算水箱下、电梯机房及设备下结构强度.水箱不得与主体结构做在一起.(14).当地下水位很高时,暖沟应做防水.一般可做U型混凝土暖沟,暖气管通过防水套管进入室内暖沟.有地下室时,混凝土应抗渗,等级S6或S8,混凝土等级应大于等于C25,混凝土内应掺入膨胀剂.混凝土外墙应注明水平施工缝做法,一般加金属止水片,较薄的混凝土墙做企口较难.(15).采用扁梁时,应注意验算变形.(16).突出屋面的楼电梯间的柱为梁托柱时应向下延伸一层,不宜直接锚入顶层梁内,并且托梁上铁应适当拉通.错层部位应采取加强措施.女儿墙内加构造柱,顶部加压顶.出入口处的女儿墙不管多高,均加构造柱,并应加密.错层处可加一大截面梁,上下层板均锚入此梁.(17).等基底附加压力时基础沉降并不同.(18).应避免将大梁穿过较大房间,在住宅中严禁梁穿房间.(19).当建筑布局很不规则时,结构设计应根据建筑布局做出合理的结构布置,并采取相应的构造措施.如建筑方案为两端较大体量的建筑中间用很小的结构相连时(哑铃状),此时中间很小的结构的板应按偏拉和偏压考虑.板厚应加厚,并双层配筋.(20).较大跨度的挑梁下柱子内跨梁传来的荷载将大于梁荷载的一半.挑板道理相同.(21).挑梁、板的上部筋,伸入顶层支座后水平段即可满足锚固要求时,因钢筋上部均为保护层,应适当增大锚固长度或增加一10d的垂直段.。
框架结构施工组织设计

框架结构施工组织设计一、项目概况本项目是一座框架结构的建筑工程,总建筑面积为xxx平方米,由x层框架结构组成。
项目位于xx地区,交通便利,施工条件良好。
本项目的目标是按照相关设计要求和质量标准,按时完成工程,并确保施工安全。
二、组织设计原则1.安全第一:施工组织设计要以安全为前提,确保所有参与施工的人员和设备都能在安全的条件下进行工作。
2.效率优先:施工过程中要高效利用资源,合理安排工作流程,确保按期完成工程。
3.质量为本:施工组织设计要严格按照设计要求和质量标准进行,保证施工质量,防止质量问题。
三、施工组织结构1.总经理:负责整个项目的管理和决策,并与业主和监理进行沟通。
2.工程经理:负责项目的具体组织和实施,并协调各个施工分包单位。
3.技术总监:负责项目技术指导和工艺控制,在施工过程中解决技术问题。
4.施工队长:负责具体施工作业,协调作业人员和材料供应,保证施工进度和质量。
5.安全主管:负责施工现场的安全管理,制定安全防护措施,并进行安全培训和检查。
6.质量主管:负责质量管理工作,制定质量控制计划,对施工质量进行监督和验收。
四、施工组织工作内容1.招投标准备:包括编制投标书和项目概况,确定施工方法和施工计划。
2.施工准备:包括施工场地的搭建和布置,设备和材料的采购,制定施工管理制度和安全计划等。
3.施工过程控制:包括工程量的测量和计量,施工进度的控制,质量和安全的监督,施工记录的整理和归档。
4.施工质量控制:包括施工工艺和工序的控制,材料的验收和使用,施工质量的检验和验收。
5.施工安全管理:包括施工现场的安全防护措施,人员的培训和带领,安全事故的预防和处理。
6.进度控制和协调:包括施工进度的计划和控制,工序和工艺的协调,与相关单位的沟通和协商。
五、工作流程1.招投标阶段:编制投标书,确定施工方法和施工计划,与业主进行沟通,确定中标。
2.施工准备阶段:搭建施工场地,采购设备和材料,制定管理制度和安全计划。
框架结构施工组织设计(毕业设计)

目录第一章编制说明和编制依据 (1)1.1编制说明 (1)1.2 编制依据 (1)第二章工程概况 (3)2.1工程主要概况 (3)2.2设计概况 (3)2.2.1建筑设计 (3)2.2.2结构设计 (4)2.3 施工条件 (5)2.4 施工特点 (5)第三章施工组织管理和机构设置 (6)3.1 施工组织管理 (6)3.2 项目组织机构设置及职责 (7)第四章施工部署及施工总平面布置 (9)4.1 施工部署 (9)4.1.1 任务划分 (9)4.1.2 施工组织计划 (9)4.2 施工准备 (9)4.2.1 技术准备 (9)4.2.2 施工现场及生产准备 (9)4.3 总平面布置 (10)4.3.1 施工道路 (10)4.3.2 施工场地 (10)4.3.3 混凝土搅拌站 (10)4.3.4 垂直运输 (10)4.3.5 周转材料堆场 (10)4.3.6 钢筋、木材加工厂和生活办公用房等其他布置见施工总平面布置图 (10)4.4 总平面管理 (11)4.5 施工总平面布置图 (11)第五章主要分部分项工程施工方法 (12)5.1施工准备 (12)5.2施工测量 (12)5.2.1 施测程序及安排 (12)5.2.2施工测量的基本要求 (12)5.2.3工程定位与控制网测设 (14)5.2.4基础测量 (16)5.2.5 主体结构施工测量 (17)5.2.6沉降观测 (20)5.2.7工程重点部位的测量控制方法 (21)5.2.8质量保证措施 (21)5.2.9施测安全及仪器管理 (22)5.3土方开挖与回填工程 (22)5.3.1施工准备 (22)5.3.2质量要求 (24)5.3.3操作工艺 (25)5.4地基处理工程 (27)5.4.1施工工艺 (27)5.5基础工程 (29)5.5.1 施工准备 (30)5.5.2 工艺流程 (30)5.5.3 施工方法(钢筋、模板、砼具体施工方法详见分项技术交底) (31)5.5.4 基础施工要点 (31)5.5.5 质量标准及要求 (33)5.5.6 安全生产,文明施工 (34)5.5.7冬雨季施工的安全和防火 (35)5.6钢筋工程 (36)5.6.2施工布署 (37)5.6.3操作工艺 (37)5.6.4质量验收标准 (39)5.6.5成品保护 (39)5.6.6注意事项 (40)5.7模板工程 (40)5.7.1模板的配备与安装 (40)5.7.2模板体系技术措施 (42)5.7.3支模质量要求及验收标准 (42)5.7.4模板的拆除 (43)5.8混凝土工程 (43)5.8.1砼的浇筑前的准备: (44)5.8.2操作工艺: (44)5.8.3质量标准: (47)5.8.4施工注意事项: (47)5.8.5砼的取样: (48)5.9脚手架工程 (49)5.9.1脚手架搭设材料要求 (49)5.9.2脚手架搭设技术措施 (49)5.9.3脚手架检查和验收 (51)5.9.4脚手架使用、维护、保养技术措施 (52)5.9.5脚手架搭设时注意事项 (52)5.9.5脚手架拆除: (52)5.9.6安全措施 (53)5.10砌筑工程 (54)5.10.1 材料要求 (54)5.10.2 技术要求 (54)5.10.3 施工工艺顺序 (55)5.10.4 施工准备 (55)5.10.6 质量标准 (59)5.11屋面工程 (59)5.11.1操作工艺: (59)5.11.2施工准备工作: (59)5.11.3 材料要求 (59)5.11.4主要施工工艺 (60)5.11.5 质量保证 (62)5.12内外墙面装饰工程 (63)5.12.1 施工准备 (63)5.12.2水泥砂浆找平层 (63)5.12.3地砖面层 (64)5.12.4有防水要求的卫生间 (65)5.12.5 楼梯 (66)5.12.6 质量标准及注意事项 (66)5.12.7 质量保证 (68)5.12.8 成品保护 (68)5.13门窗工程 (69)5.13.1门窗的安装 (69)5.13.2 质量要求 (69)5.13.3 门窗的一般规定 (70)第六章施工进度计划 (72)6.1 工程总控制进度计划 (72)6.2 施工进度计划 (72)6.2.1 地基处理阶段 (72)6.2.2 基础施工阶段 (72)6.2.3 主体结构施工阶段 (72)6.2.4 屋面施工阶段 (72)6.2.5 装饰施工阶段 (73)6.2.6 清理竣工阶段 (73)第七章技术管理措施 (74)7.1测量管理措施 (74)7.2 试验管理措施 (74)7.3 资料管理措施 (75)7.4 其他技术管理措施 (75)第八章质量管理措施 (76)8.1 质量方针和目标 (76)8.1.1 质量方针: (76)8.1.2 质量目标 (76)8.2 质量管理控制措施 (76)8.3 质量技术控制措施 (77)第九章现场管理措施 (80)9.1 安全生产保证措施 (80)9.1.1建立健全安全生产责任制 (80)9.1.2 加强安全教育 (80)9.1.3加强安全检查 (81)9.2文明施工保证措施 (85)9.3 成品保护措施 (85)9.4 雨季施工措施 (86)9.5 冬季施工 (87)9.6 防火措施 (87)第十章工期保证措施 (88)第十一章环境保护保证措施 (88)第一章编制说明和编制依据1.1编制说明对承建本工程,该公司具有极大的热忱,对与建设单位的合作充满诚挚的意愿。
框架结构施工组织设计(完整)

框架结构施工组织设计(完整)范本1:一、前言1.1 编制目的本文档旨在规范框架结构施工组织设计的编制过程,确定施工组织设计的内容和要求,确保施工过程顺利进行。
1.2 适合范围本文档适合于各类建造工程的框架结构施工组织设计。
二、施工组织设计概述2.1 设计依据2.1.1 相关法律法规:包括《建设工程法》、《建造法》等相关法律法规。
2.1.2 工程技术标准:根据国家有关框架结构工程的技术标准进行设计。
2.1.3 合同文件:根据合同文件中的施工要求进行设计。
2.2 设计2.2.1 编制施工组织设计方案:根据项目情况,编制适合的施工组织设计方案。
2.2.2 具体施工组织设计:对施工方案进行具体细化,编制施工组织设计图纸和文字说明。
三、施工组织设计详细内容3.1 工程概况3.1.1 工程名称:填写框架结构施工项目名称。
3.1.2 工程地点:填写框架结构施工项目所在地。
3.1.3 工程规模:填写框架结构施工项目的规模。
3.2 施工组织设计原则3.2.1 安全第一原则:确保施工过程中的安全。
3.2.2 经济合理原则:合理利用资源,降低施工成本。
3.2.3 质量可控原则:确保施工质量符合要求。
3.3 施工组织设计方案3.3.1 施工组织总体方案3.3.1.1 施工组织总体布置:包括施工区域划分、施工设备布置等。
3.3.1.2 施工组织总体进度计划:制定施工总体进度计划,明确工期要求。
3.3.1.3 劳动力与材料计划:确定施工所需的劳动力和材料数量。
3.3.2 分部份项工程施工组织设计3.3.2.1 分部份项工程施工组织布置:对各个分部份项工程进行施工组织布置。
3.3.2.2 分部份项工程施工进度计划:制定各个分部份项工程的施工进度计划。
四、附件本文档涉及的附件包括施工组织设计图纸、施工进度计划等。
五、法律名词及注释1. 建设工程法:是中华人民共和国于1998年制定通过的法律,用以规范和促进建设工程的合理、有序、安全、经济、社会效益最大化的建设。
工程施工组织设计毕业论文
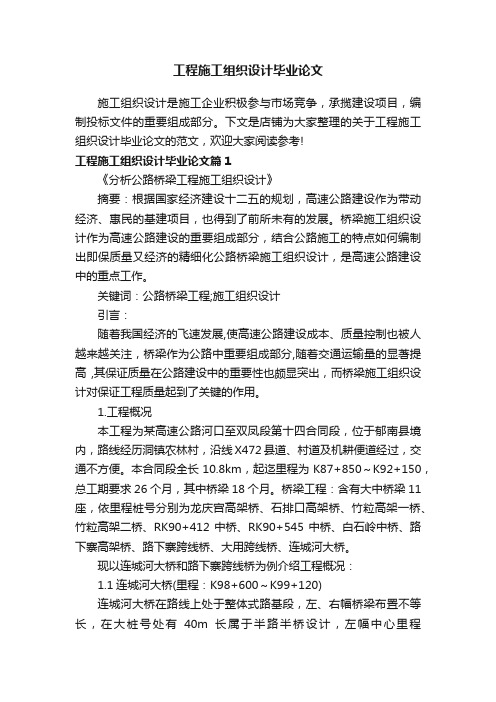
工程施工组织设计毕业论文施工组织设计是施工企业积极参与市场竞争,承揽建设项目,编制投标文件的重要组成部分。
下文是店铺为大家整理的关于工程施工组织设计毕业论文的范文,欢迎大家阅读参考!工程施工组织设计毕业论文篇1《分析公路桥梁工程施工组织设计》摘要:根据国家经济建设十二五的规划,高速公路建设作为带动经济、惠民的基建项目,也得到了前所未有的发展。
桥梁施工组织设计作为高速公路建设的重要组成部分,结合公路施工的特点如何编制出即保质量又经济的精细化公路桥梁施工组织设计,是高速公路建设中的重点工作。
关键词:公路桥梁工程;施工组织设计引言:随着我国经济的飞速发展,使高速公路建设成本、质量控制也被人越来越关注,桥梁作为公路中重要组成部分,随着交通运输量的显著提高,其保证质量在公路建设中的重要性也颇显突出,而桥梁施工组织设计对保证工程质量起到了关键的作用。
1.工程概况本工程为某高速公路河口至双凤段第十四合同段,位于郁南县境内,路线经历洞镇农林村,沿线X472县道、村道及机耕便道经过,交通不方便。
本合同段全长10.8km,起迄里程为K87+850~K92+150,总工期要求26个月,其中桥梁18个月。
桥梁工程:含有大中桥梁11座,依里程桩号分别为龙庆宫高架桥、石排口高架桥、竹粒高架一桥、竹粒高架二桥、RK90+412中桥、RK90+545中桥、白石岭中桥、路下寨高架桥、路下寨跨线桥、大用跨线桥、连城河大桥。
现以连城河大桥和路下寨跨线桥为例介绍工程概况:1.1连城河大桥(里程:K98+600~K99+120)连城河大桥在路线上处于整体式路基段,左、右幅桥梁布置不等长,在大桩号处有40m长属于半路半桥设计,左幅中心里程K98+840,桥跨组合12×40,桥长481.2m,右幅中心里程K98+855,桥跨组合13×40,桥长521.2m,上部构造为预应力砼先简支后连续刚构T梁。
桩基桩直径为φ150cm、φ180cm、φ200cm,桩长为16 m~44m,桩基性质属嵌岩桩与摩擦桩,桩基共56根。
桥梁毕业设计论文(施工组织设计)

大连理工大学城市学院本科毕业设计(论文)学院(系):建筑工程学院专业:工程管理学生姓名:朱鹏飞学号: 200832194指导教师:苗毓海评阅教师:刘伟完成日期: 2012年05月10日大连理工大学程城市学院Dalian University of Technology City Institute大连理工大学城市学院本科毕业设计(论文)题目名称兰渝铁路LYS-14标段施工组织设计总计毕业设计(论文) 73 页表格 8 表附图 15 幅摘要本工程是位于重庆市市站前北侧,由中铁十局投资建设的。
该工程是由中铁设计研究院设计。
本工程为节能设计,外墙60厚XPS挤塑保温,室内外高差600mm,屋面为SBS防水,窗为单层双玻塑钢推拉窗,室内门为双面胶合板门,砖混结构墙体采用承重多孔砖砌筑,基础为毛石基础,MU40毛石M10水泥砂浆。
在毕业实践中,通过在施工现场的见习,通过对工程施工资料的研读对工程的概况有了基本的了解,根据对此工程项目的学习,进行的此次施工组织设计,其内容包括编制依据工程概况主要分部分项工程的施工方法施工进度计划施工现场平面布置图项目现场及安全管理措施冬雨期的施工措施主要机械设备和劳动力资源量。
关键词:兰渝铁路连续梁保证施工安全落实责任优质工程AbstractThis project is located in Chongqing city on the north side of the building, by Zhongtie limited investment in building. This project is by the Zhongtie Architectural Design Institute of design. This project for the energy saving design of60XPS Extrusion insulation, wall thickness, the height difference of indoor and outdoor600mm, SBS waterproof roof, window for single double glass plastic-steel push-and-pull window, door for double-sided plywood door, wall of brick and concrete structure by bearing porous brick masonry, foundation stone MU40M10foundation, cement mortar rubble.In the graduation practice, through the practice in construction site, the construction of the project of reading materials and have a basic understanding of the project, according to the study, Venus in the construction organization design, which includes the basis project overview the main sub-segment of the construction methods of construction plan of the construction site layout figure project site and safety management measures for winter construction measures of period of main mechanical equipmentand laborKey Words:T h e r a i l w a y o f L a n z h o u t o C h o n g q i n g c o n t i n u o u s b e a m G u a r a n t e e d T h e C o n s t r u c t i o n S e c u r i t y A s s i g n R e s p o n s i b i l i t i e s h i g h g r a d e p r o j e c t目录大连理工大学城市学院 (1)本科毕业设计(论文) (1)摘要 (I)ABSTRACT........................................... I I 1 编制依据及原则.. (1)1.1编制依据 (1)1.2编制原则 (1)2 工程概况 (3)2.1工程概述 (3)2.2工程范围及主要技术标准 (3)2.3自然地理特征 (4)2.4主要工程数量 (5)2.5当地可供利用的资源 (7)2.6主要工程特点 (8)3 施工组织机构及施工任务划分 (10)3.1施工组织机构 (10)3.2施工队伍部署及任务划分 (13)3.3项目管理目标 (13)3.3.1 工期目标 (13)3.3.2 质量目标 (13)3.3.3 安全目标 (14)3.3.4 文明施工及环境保护目标 (14)3.4施工总体平面布置及规划 (14)3.4.1 总体平面布置原则 (14)3.4.2 施工总体平面布置 (15)3.4.3 临时工程及临时设施 (15)4.各种资源需要量计划及施工准备 (19)4.1人员组织 (19)4.2测量仪器及精度 (19)4.3资料收集及引用标准 (19)4.4重点工程建立独立平面、高程控制网 (21)4.5施工过程控制测量 (22)4.6竣工测量阶段 (23)4.7桥梁墩台基础沉降控制 (23)5施工方案 (25)5.1工程概况 (25)5.2设计概况 (25)5.2.1 施工组织安排及施工单元划分 (26)6 施工平面布置 (28)6.1劳动力安排 (29)7 施工进度安排 (30)7.1资源配置计划 (31)8 施工方法及工艺 (33)8.1栈桥施工 (33)8.2水中墩钻孔桩施工 (34)8.3水中墩承台施工 (38)8.4下料 (39)8.5HDPE圆管焊接 (41)8.6质量要求 (48)9 连续梁及斜拉桥箱梁施工方法、工艺及相应措施 (49)9.1悬臂浇筑连续梁施工方法 (49)9.2合拢段及体系转换施工 (60)9.3施工控制措施 (63)10 后期维护及各种突发方案应急处理 (65)10.1桥梁墩台基础沉降控制 (65)10.2桥梁主体结构的耐久性 (65)10.3加强安全工作、作好应急准备 (66)10.4事故应急处理程序 (66)11 冬雨季施工 (68)11.1雨季施工应急预案 (68)11.2冬季施工应急预案 (68)12 施工机械安全保证措施 (70)致谢 (71)参考文献 (73)1 编制依据及原则1.1 编制依据(1)新建兰州至重庆铁路兰州东至夏官营、广元至重庆段土建工程和兰州东至重庆铺架工程L YS-14标段投标施组、初步设计图、已到位的施工图等。
框架中桥专项施工方案

一、项目背景随着我国城市化进程的加快,桥梁工程作为城市基础设施的重要组成部分,其建设规模和施工技术不断提高。
本方案针对框架中桥的专项施工进行编制,以确保工程质量和施工安全。
二、工程概况本工程为一座框架中桥,位于某城市主干道,全长80米,桥宽24米,主桥采用预应力混凝土框架结构,引桥采用预应力混凝土空心板结构。
桥墩采用钢筋混凝土圆形实体墩,桥台采用钢筋混凝土U型桥台。
三、施工组织1. 施工准备(1)人员准备:成立项目经理部,配备专业技术人员、施工人员、质检人员等,明确各岗位职责。
(2)材料准备:按照设计要求,准备足够的钢筋、混凝土、模板、砂石等原材料。
(3)设备准备:配置必要的施工机械设备,如混凝土搅拌站、泵车、吊车、振动器等。
2. 施工工艺(1)基础施工:采用钻孔灌注桩基础,桩径为1.2米,桩长根据地质条件确定。
(2)桥墩施工:采用圆形实体墩,墩身采用现浇混凝土,模板采用钢模板。
(3)桥台施工:采用U型桥台,桥台基础采用钻孔灌注桩,桥台身采用现浇混凝土。
(4)主桥施工:采用预应力混凝土框架结构,先施工桥面板,然后施工梁体。
(5)引桥施工:采用预应力混凝土空心板结构,先施工桥面板,然后施工梁体。
3. 施工进度安排根据工程量和施工难度,制定合理的施工进度计划,确保工程按期完成。
四、质量控制1. 材料质量控制:严格筛选原材料,确保质量符合设计要求。
2. 施工过程控制:严格执行施工规范,确保施工质量。
3. 质量检验:按照相关规范进行检验,确保工程质量合格。
五、安全管理1. 人员安全:加强安全教育,提高作业人员的安全意识。
2. 施工安全:制定安全措施,确保施工安全。
3. 设备安全:定期检查和维护设备,确保设备安全运行。
六、环境保护1. 噪音控制:合理安排施工时间,减少噪音对周边环境的影响。
2. 污染控制:对施工废水、废气进行处理,减少对环境的影响。
3. 固废处理:对施工产生的固体废弃物进行分类处理,减少对环境的影响。
框架结构施工组织设计范本
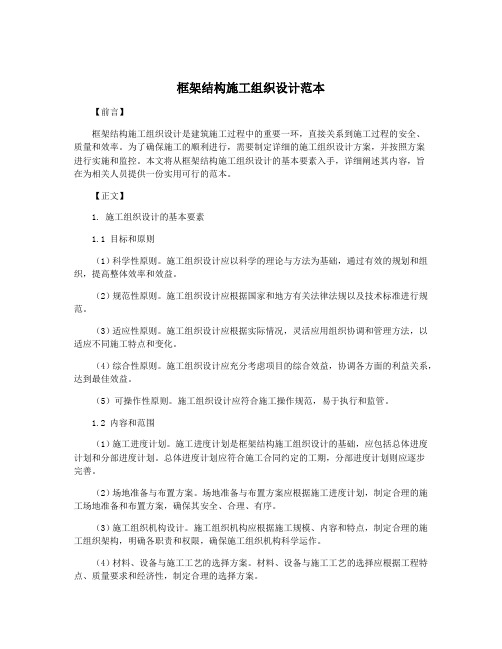
框架结构施工组织设计范本【前言】框架结构施工组织设计是建筑施工过程中的重要一环,直接关系到施工过程的安全、质量和效率。
为了确保施工的顺利进行,需要制定详细的施工组织设计方案,并按照方案进行实施和监控。
本文将从框架结构施工组织设计的基本要素入手,详细阐述其内容,旨在为相关人员提供一份实用可行的范本。
【正文】1. 施工组织设计的基本要素1.1 目标和原则(1)科学性原则。
施工组织设计应以科学的理论与方法为基础,通过有效的规划和组织,提高整体效率和效益。
(2)规范性原则。
施工组织设计应根据国家和地方有关法律法规以及技术标准进行规范。
(3)适应性原则。
施工组织设计应根据实际情况,灵活应用组织协调和管理方法,以适应不同施工特点和变化。
(4)综合性原则。
施工组织设计应充分考虑项目的综合效益,协调各方面的利益关系,达到最佳效益。
(5)可操作性原则。
施工组织设计应符合施工操作规范,易于执行和监管。
1.2 内容和范围(1)施工进度计划。
施工进度计划是框架结构施工组织设计的基础,应包括总体进度计划和分部进度计划。
总体进度计划应符合施工合同约定的工期,分部进度计划则应逐步完善。
(2)场地准备与布置方案。
场地准备与布置方案应根据施工进度计划,制定合理的施工场地准备和布置方案,确保其安全、合理、有序。
(3)施工组织机构设计。
施工组织机构应根据施工规模、内容和特点,制定合理的施工组织架构,明确各职责和权限,确保施工组织机构科学运作。
(4)材料、设备与施工工艺的选择方案。
材料、设备与施工工艺的选择应根据工程特点、质量要求和经济性,制定合理的选择方案。
(5)现场安全、环境保护和文明施工方案。
现场安全、环境保护和文明施工方案应根据法律法规,严格控制施工现场的安全和环境,同时保持文明施工。
1.3 编制要求(1)施工组织设计应根据施工合同的具体要求和施工现场的实际情况,结合项目管理的要求进行编制。
(2)施工组织设计应经过相关专业人员的审核和批准,并及时更新和调整。
路桥工程施工组织毕业设计
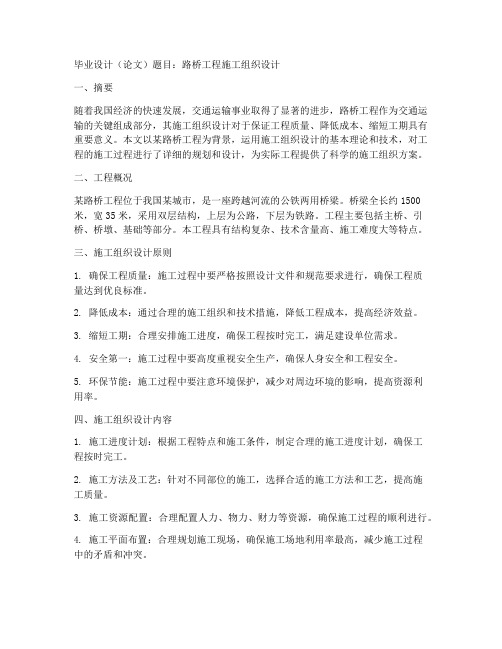
毕业设计(论文)题目:路桥工程施工组织设计一、摘要随着我国经济的快速发展,交通运输事业取得了显著的进步,路桥工程作为交通运输的关键组成部分,其施工组织设计对于保证工程质量、降低成本、缩短工期具有重要意义。
本文以某路桥工程为背景,运用施工组织设计的基本理论和技术,对工程的施工过程进行了详细的规划和设计,为实际工程提供了科学的施工组织方案。
二、工程概况某路桥工程位于我国某城市,是一座跨越河流的公铁两用桥梁。
桥梁全长约1500米,宽35米,采用双层结构,上层为公路,下层为铁路。
工程主要包括主桥、引桥、桥墩、基础等部分。
本工程具有结构复杂、技术含量高、施工难度大等特点。
三、施工组织设计原则1. 确保工程质量:施工过程中要严格按照设计文件和规范要求进行,确保工程质量达到优良标准。
2. 降低成本:通过合理的施工组织和技术措施,降低工程成本,提高经济效益。
3. 缩短工期:合理安排施工进度,确保工程按时完工,满足建设单位需求。
4. 安全第一:施工过程中要高度重视安全生产,确保人身安全和工程安全。
5. 环保节能:施工过程中要注意环境保护,减少对周边环境的影响,提高资源利用率。
四、施工组织设计内容1. 施工进度计划:根据工程特点和施工条件,制定合理的施工进度计划,确保工程按时完工。
2. 施工方法及工艺:针对不同部位的施工,选择合适的施工方法和工艺,提高施工质量。
3. 施工资源配置:合理配置人力、物力、财力等资源,确保施工过程的顺利进行。
4. 施工平面布置:合理规划施工现场,确保施工场地利用率最高,减少施工过程中的矛盾和冲突。
5. 施工安全管理:建立健全安全生产责任制,加强施工现场的安全管理,预防安全事故的发生。
6. 施工质量控制:通过严格的质量管理体系和措施,确保工程质量达到优良标准。
7. 施工环境保护:采取有效措施,减少施工过程中的环境污染,保护生态环境。
五、结论本文以某路桥工程为背景,运用施工组织设计的基本理论和技术,对工程的施工过程进行了详细的规划和设计。
施工组织设计毕业论文范文

施工组织设计毕业论文范文摘要:本文通过对具体工程名称施工组织设计的详细阐述,对施工过程中的各项工作进行了全面规划和安排,旨在保证工程质量、缩短工期、降低成本,提高施工效率和经济效益。
关键词:施工组织设计;工程进度;质量控制;资源配置一、工程概述具体工程名称位于具体地点,总建筑面积为X平方米,结构形式为结构类型。
本工程包括具体的工程内容,如基础工程、主体结构、装饰装修等。
二、施工部署(一)施工目标1、质量目标:确保工程质量达到具体的质量标准,如优良、合格等。
2、工期目标:计划在开始日期开工,在结束日期竣工,总工期为X天。
3、安全目标:杜绝重大伤亡事故,轻伤事故发生率控制在X%以内。
(二)施工组织机构成立项目经理部,下设工程技术部、质量安全部、物资设备部、综合办公室等部门,各部门分工明确,密切配合。
(三)施工顺序按照先地下、后地上,先主体、后装饰的原则组织施工。
三、施工进度计划(一)编制依据1、工程合同要求的工期。
2、施工图纸及相关技术规范。
3、施工条件和资源供应情况。
(二)进度计划安排1、基础工程:具体工期。
2、主体结构:具体工期。
3、装饰装修:具体工期。
(三)进度计划的保证措施1、组织措施:建立健全进度控制的组织体系,落实各部门的职责。
2、技术措施:优化施工方案,采用先进的施工技术和工艺。
3、经济措施:实行进度奖惩制度,提高施工人员的积极性。
四、施工准备(一)技术准备1、熟悉施工图纸,进行图纸会审。
2、编制施工组织设计和专项施工方案。
(二)现场准备1、平整施工场地,修筑临时道路和排水设施。
2、搭建临时办公和生活设施。
(三)资源准备1、劳动力准备:根据施工进度计划,组织劳动力进场。
2、材料准备:制定材料采购计划,确保材料按时供应。
3、机械设备准备:根据施工需要,调配机械设备。
五、主要分部分项工程施工方法(一)基础工程1、土方工程:采用机械开挖,人工清底的方式。
2、基础钢筋工程:严格按照设计要求进行钢筋的加工和绑扎。
桥工程施工组织设计(3篇)

第1篇一、工程概况本工程为某市某区某桥工程,位于市区中心区域,是一座重要的交通枢纽。
桥梁全长约500米,主桥跨度为80米,采用预应力混凝土结构。
工程包括主桥、引桥、桥台、桥墩、排水系统等部分。
工程总投资约1.2亿元,预计工期为24个月。
二、施工组织设计原则1. 安全第一、预防为主:坚持安全生产,确保施工过程中人员安全、设备安全、环境安全。
2. 质量第一:严格按照设计要求和规范标准进行施工,确保工程质量。
3. 科学组织、合理施工:根据工程特点,科学制定施工方案,合理安排施工顺序,确保工程进度。
4. 节约成本、提高效益:合理利用资源,降低施工成本,提高工程效益。
三、施工方案1. 施工方法- 主桥施工:采用预制梁板吊装法,先进行桩基施工,然后进行承台、墩身施工,最后进行梁板预制及吊装。
- 引桥施工:采用现浇法,先进行桩基施工,然后进行承台、墩身施工,最后进行现浇梁板。
- 桥台、桥墩施工:采用现浇法,先进行桩基施工,然后进行承台、墩身施工。
2. 施工顺序- 桩基施工:先进行主桥桩基施工,然后进行引桥桩基施工。
- 承台、墩身施工:先进行主桥承台、墩身施工,然后进行引桥承台、墩身施工。
- 梁板预制及吊装:先进行主桥梁板预制及吊装,然后进行引桥梁板预制及吊装。
- 桥面系施工:先进行桥面防水层施工,然后进行桥面铺装。
3. 施工机械设备- 桩基施工:采用旋挖钻机、搅拌桩机等。
- 承台、墩身施工:采用混凝土搅拌站、混凝土输送泵、模板等。
- 梁板预制及吊装:采用预制梁板生产线、吊车等。
- 桥面系施工:采用摊铺机、压路机等。
四、施工进度计划1. 桩基施工:预计3个月完成。
2. 承台、墩身施工:预计5个月完成。
3. 梁板预制及吊装:预计4个月完成。
4. 桥面系施工:预计2个月完成。
五、施工管理措施1. 安全管理:建立健全安全管理制度,加强安全教育培训,严格执行安全操作规程,确保施工安全。
2. 质量管理:建立健全质量管理体系,加强质量监控,严格执行质量标准,确保工程质量。
最新毕业论文范例土木工程施工组织设计

最新毕业论文范例土木工程施工组织设计摘要:本文以大型桥梁施工为背景,针对土木工程施工过程中的组织设计问题进行研究。
首先,通过对相关文献进行综述,探讨了土木工程施工的特点和组织设计的重要性。
然后,结合实际案例,以一座大型桥梁项目为例,详细介绍了施工组织设计的具体内容和步骤。
最后,通过对案例分析和实践经验总结,提出了一些建议,用于指导未来类似项目的施工组织设计。
关键词:土木工程;施工组织设计;大型桥梁;案例分析;实践经验1.引言土木工程施工组织设计是确保施工项目顺利进行的关键环节。
合理的组织设计可以提高工程效率并保障施工质量。
随着大型桥梁项目的不断增多,其施工组织设计问题也日益显现。
针对这一问题,本文通过对相关文献的综述和实际案例的分析,探讨了大型桥梁施工组织设计的重要性以及具体的设计方法。
2.土木工程施工组织设计的特点土木工程施工组织设计的特点主要包括施工规模大、施工时间紧迫、工程复杂度高等。
这些特点对施工组织设计提出了更高的要求,需要考虑到人力资源、机械设备、材料供应等多方面因素。
因此,合理的组织设计必不可少。
3.大型桥梁施工组织设计的案例分析以大型桥梁项目为例,对其施工组织进行详细的设计。
首先,分析施工工艺和方法,确定主要工序和工作流程。
然后,制定施工计划并合理分配资源,确保各项工作按计划进行。
同时,制定安全管理方案,确保施工过程中的安全性。
最后,进行施工组织的综合设计,包括人员结构、协作方式、沟通渠道等方面。
4.大型桥梁施工组织设计的实践经验总结通过对案例的实践和经验总结,得出以下几点经验:一是要充分考虑环境因素,如气候条件和地质状况等,制定相应的施工组织措施。
二是要合理分配资源,包括人力、机械和材料等,并进行合理的调度和管理。
三是要注重安全管理,制定科学的安全措施,并提供必要的培训和指导。
四是要加强沟通和协作,建立良好的工作氛围和团队合作精神。
5.结论本文以大型桥梁施工为背景,研究了土木工程施工组织设计的问题。
版新建铁路工程框构中桥施工组织设计方案
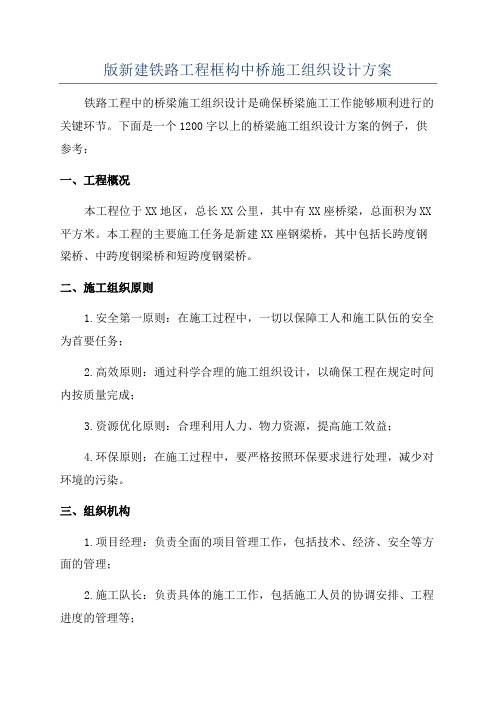
版新建铁路工程框构中桥施工组织设计方案铁路工程中的桥梁施工组织设计是确保桥梁施工工作能够顺利进行的关键环节。
下面是一个1200字以上的桥梁施工组织设计方案的例子,供参考:一、工程概况本工程位于XX地区,总长XX公里,其中有XX座桥梁,总面积为XX 平方米。
本工程的主要施工任务是新建XX座钢梁桥,其中包括长跨度钢梁桥、中跨度钢梁桥和短跨度钢梁桥。
二、施工组织原则1.安全第一原则:在施工过程中,一切以保障工人和施工队伍的安全为首要任务;2.高效原则:通过科学合理的施工组织设计,以确保工程在规定时间内按质量完成;3.资源优化原则:合理利用人力、物力资源,提高施工效益;4.环保原则:在施工过程中,要严格按照环保要求进行处理,减少对环境的污染。
三、组织机构1.项目经理:负责全面的项目管理工作,包括技术、经济、安全等方面的管理;2.施工队长:负责具体的施工工作,包括施工人员的协调安排、工程进度的管理等;3.专业技术人员:包括结构设计师、施工技术员等,负责工程的技术指导和质量控制;4.施工人员:包括钢筋工、焊工、起重工等,负责具体的施工工作。
四、施工工艺与方法1.打地基:根据桥梁的设计要求,采用适当的地基处理方法,确保桥梁的稳固性;2.施工桩基:根据桥梁的设计要求安排施工机组进行施工桩基工作,包括打桩、灌注桩等;3.浇筑墩台:按照桥梁设计要求,采用模板浇筑墩台,利用起重机进行安装;4.安装梁体:根据桥梁设计要求,通过临时架设进行钢梁的安装;5.桥面铺装:施工完成后,进行桥面的铺装和护栏的安装。
五、安全措施1.建立安全生产责任制度,明确每个人的安全责任;2.配备专职安全员,全面负责工地安全工作的监督和管理;3.定期进行安全教育培训,提高施工人员的安全意识和技能;4.设置明显的施工警示标识,确保施工区域的安全;5.配备完善的安全设施,如防护网、安全带、灭火器等。
六、施工进度计划1.按照桥梁设计要求和施工工艺,制定详细的施工进度计划;2.确定每个施工工序的时间节点,合理安排施工工作;3.配合设计单位和监理单位的工作,及时解决施工过程中的问题;4.按照施工进度计划,进行工程的验收和交付。
施工组织设计毕业论文范文

施工组织设计毕业论文范文1.项目背景及目标该项目城市商业中心建设项目,总建筑面积达到10万平方米。
项目目标是在保证工程质量的前提下,按时按质完成建设任务,为城市商业发展做出贡献。
2.施工组织设计内容2.1工程组织架构根据项目规模和工程性质,确定了项目总经理、技术负责人、施工员、质量员等工程组织人员,并明确了各自职责和权限。
同时,制定了施工组织管理办法,明确了组织架构中各层级之间的协作关系和沟通渠道,以保证信息畅通和工作顺畅进行。
2.2施工作业计划根据项目工程量和工期,制定了详细的施工作业计划。
首先,对项目进行了分区划分,确定了各个施工区域。
然后,在施工前进行了详细工序划分和时间节点安排,制定了施工任务分解图。
最后,根据施工任务分解图,制定了施工进度计划,并对关键节点进行了重点监控。
2.3施工资源配置根据工期和工程量,合理配置了施工人员和设备资源。
在施工人员方面,根据专业和工种要求,招聘了具备相应资质和经验的施工人员,并进行了培训。
在设备方面,根据工序要求和工期安排,按时调配了所需设备,确保施工过程中的资源供应充足。
2.4安全管理措施在施工组织设计中,安全管理是不可忽视的重要部分。
根据建筑工程安全操作规范,对施工过程中可能存在的安全风险进行了评估,并采取相应措施进行预防和控制。
例如,设置了安全警示标志,配备了安全防护装备,并组织了安全教育培训等措施。
3.施工组织设计的效果评估在实际施工过程中,施工组织设计的效果要进行及时评估和调整。
通过对施工现场进行巡查、检查和整改,及时发现问题并加以解决。
同时,与项目管理人员、业主代表进行定期沟通,了解他们的意见和建议,并及时进行调整和改进。
4.施工组织设计的优化方向在施工组织设计中,应不断寻求优化的方向。
一方面,要利用现代信息技术手段,提高施工组织管理的智能化水平,以提高工作效率和质量。
另一方面,要加强员工培训和技术交流,提高团队整体素质和协作能力,以提高施工组织设计的综合效能。
- 1、下载文档前请自行甄别文档内容的完整性,平台不提供额外的编辑、内容补充、找答案等附加服务。
- 2、"仅部分预览"的文档,不可在线预览部分如存在完整性等问题,可反馈申请退款(可完整预览的文档不适用该条件!)。
- 3、如文档侵犯您的权益,请联系客服反馈,我们会尽快为您处理(人工客服工作时间:9:00-18:30)。
1、编制依据1.1新建南京枢纽大胜关长江大桥南京南站及相关工程施工图DK1019+040.696 站东路框架中桥施工图。
1.2国家及相关部委颁布的法律、法规和铁道部颁布的现行设计规范、铁路工程质量验收标准及其它有关文件资料。
《客运专线铁路桥涵工程施工质量验收暂行标准》〔铁建设(2005)160号〕《铁路混凝土工程施工质量验收补充标准》〔铁建设(2005)160号〕《铁路桥涵工程施工质量验收标准》(TB10415-2003)〔J286-2004〕《铁路桥涵施工规范》(TB10203-2002)〔J162-2002〕《新建时速200公里客货共线铁路工程施工质量验收暂行标准》〔铁建设(2004)8号〕《铁路混凝土工程施工技术指南》(TZ210-2005)《新建时速200~250公里客运专线铁路设计暂行规定》〔铁建设(2005)140号〕《新建时速300~350公里客运专线铁路设计暂行规定》〔铁建设(2007)47号〕《铁路混凝土结构耐久性设计暂行规定》(铁建设[2005]157号)1.3工地现场调查、采集、咨询所获取的资料。
1.4我单位类似工程施工积累的施工经验及设备。
2、工程概况2.1 工程简述本桥位于南京南站,因跨越规划站东路[《铁路南京南站地区综合规划》(2008.1终稿)]而设置, 本桥跨越京沪高速、宁杭城际、仙西联络线等,京沪高速正线及道路交角为90°,跨越京沪高速及宁杭城际及仙西联络线框架中间以挡墙相接,出入口设一字挡墙,本桥设计为1-(9+16+16+9)四孔分离框架桥,中间两孔为机动车道(双向四车道),两边孔为非机动车道及人行道。
2.2 设计规模本桥设计宽度58.86m,全长182.74m,中心里程为DK1019+040.696,顶板厚0.7m(边孔)、1.2m(中孔);净高8.8m(边孔)、6.3m(中孔);底板厚1m(边孔)、1.6m(中孔);桥基础采用C30混凝土厚0.9m,级配碎石垫层厚0.2m,其中京沪正线、沪汉蓉场基底加固采用CFG桩,桩中心间距按照顺桥向×横桥向=1.6m×1.6m设计施工,正方形布置,桩长有9.5m、11m、20m、21m、21.5m五种,桩底均置于W3层内0.5m。
本桥共有翼墙4个,框架14节。
其中京沪场翼墙2个,框架3节,长度分别为9.485m+15.424m+16m+11.522m+9.485m,宁杭城际及仙西联络线共有翼墙2个,框架11节,长度分别为:9.561m+8.413m+10m+15m+15m+1 5m+15m+15m+10m+10m+15m+11.138m+9.561m。
2.3 主要工程数量框架桥主要工程数量表2.4主要技术标准2.4.1双线,正线间距5.0m,其余线路线间距6.0m,到发线及联络线间距随曲线变化。
2.4.2设计荷载和设计速度:京沪正线桥:按ZK荷载设计、ZK荷载检算。
设计时速350km/h。
轨道结构形式:有碴轨道。
沪汉蓉正线桥:按ZK荷载设计、“中-荷载”检算。
设计时速250km/h。
轨道结构形式:有碴轨道。
宁安场正线桥:按ZK荷载设计、“中-荷载”检算。
设计时速250km/h。
轨道结构形式:有碴轨道。
2.5工程地质:(0) 人工填土;(1)-2 alQ4粉质黏土,软塑,σ0 =120KPa;(1) alQ4粉质黏土,硬塑,σ0 =180KPa;(2) alQ3粉质黏土,硬塑,σ0 =200KPa;(2)-3 alQ3粉质黏土夹角砾土,σ0 =250KPa;(3)-1 泥质砂岩,全风化,σ0 =250KPa;(3)-2 泥质砂岩,强风化,σ0 =350KPa;(3)-3 泥质砂岩,弱风化,σ0 =450KPa。
2.6临时工程及“三通一平”2.6.1施工准备自六月上旬进点以来,我项目部已组织各部门深入现场进行了全面调查和研究。
在交通运输、材料供应、供水供电、施工方案等诸方面已有所规划和准备。
2.6.2施工便道根据现场工地调查,在京沪场左线左侧地界外修筑了一条长800m的施工主便道,并及搅拌站和钢筋场地之间修筑贯通便道700m。
所有的施工便道按照宽6m路面结构,厚0.8m设计(能够满足50t车辆运输要求),便道采用挖掘机配合推土机修筑。
便道设向外单面排水坡,在外侧设0.4m×0.5m的排水土沟。
每150m 设置会车避让台一处,其尺寸为长15m,宽4m。
2.6.3道路交通、场地平整本管段沿线两侧多为农田,住房,交通较为便利,乡道、村道纵横穿越,可以直接利用乡村通道运输物资及机械。
施工用场地主要利用铁路征地,钢筋场地设在京沪场左侧地界外临时征地,场地长100m,宽50m。
临时场地先采用建筑垃圾进行填筑并压实厚0.5m,顶铺0.1m瓜子片整平。
钢筋棚、木工棚、活动房的建筑垃圾顶面浇筑0.25m厚C20混凝土。
2.6.4施工用电根据现场实际情况,施工前期共安装2台发电机(1台500KVA、1台630KVA),一台设于京沪线DK1019+250处线路左侧地界外,并用380V的高压线引入搅拌站内;一座设于沪汉蓉场及宁安场之间DK1019+300处;因中铁十三局前期已经在南京南站施工,业主共建立了8个变压器,通过业主及十三局协商进行电力调配,到2009年1月31日划给我部3台630KVA的变压器。
所有的电力同时延高架桥架设约2km长的低压线路,供东咽喉各墩台使用。
2.6.5征地拆迁本框架桥牵涉到拆迁的自然村为大张里自然村,需要拆迁共约有20户左右,征地拆迁任务非常大,作为前期工作的重点并以书记为组长成立了征地拆迁小组。
2.6.6施工用水因本管段没有大型的自然水源,施工用水采用接自来水和打井相结合,并对水质进行化验,沿线纵向布置地下水管并接通到桥范围内。
水井设1口,直径0.5m,深不小于100m,设在混凝土搅拌站西侧围墙外10m处,用于搅拌站内及框架桥的施工用水。
2.6.7电力、通讯项目部办公处均引入程控电话及传真机,并配备移动电话。
各办公室安装宽带网线,通过互联网其他项目队、设计、监理、业主和地方政府相连,实现信息双向沟通。
2.6.8混凝土供应本管段布置混凝土搅拌站1座(120m3/h搅拌机2台),位置设于DK1019+130~DK1019+300段,长170m,宽100m,利用京沪场及沪汉蓉场之间的空地及该段的沪汉蓉场,混凝土总生产能力240 m3/h,均采用电子自动计量系统,经标定后使用,拌和站内设砂、碎石料仓以及水泥、粉煤灰、矿粉罐以及外加剂罐,另备配电房、工具库、料库、发电机房、值班室等临时设施。
混凝土砂石料场采用25cm厚的C20混凝土硬化,采用混凝土墙作为隔仓,分类存放。
混凝土搅拌站采用强制式混凝土搅拌机(自动计量)进行拌合。
2.7工期目标计划工期:2008年9月10日开工,2009年1月31日站前工程竣工。
施工工期144天。
2.8质量目标达到国家和铁道部现行的质量和验收标准和设计要求,一次验收合格率达到100%,力争国家和铁道部优质工程奖。
2.9安全目标坚持“安全第一,预防为主”的方针,建立健全安全管理组织机构,完善安全生产保证体系。
杜绝较大(及以上)施工安全事故;杜绝较大(及以上)道路交通责任事故;杜绝较大(及以上)火灾事故;控制和减少一般责任事故;创建安全生产标准工地。
2.10环保、水保目标严格按国家、铁道部和地方政府有关规定及设计要求做好环保、水保的标准,在施工过程中严格按照批准的环保、水保方案实施,确保工程所处的环境不受污染和通过国家验收。
工地生产、生活设施清洁文明。
施工产生的噪音控制在《铁路边界噪声限值标准及其测量方法》(GB12525-90)的限值内。
泥浆及废水、废弃物、弃土等实行有效控制,不对环境造成污染。
2.11职业健康安全目标从业人员上岗职业健康体检率100%;有毒有害作业场所监测率100%;从业人员职业健康普及率100%;无职业病发生;特殊工种持证上岗率100%;2.12文明施工目标按国家和地方有关规定执行,做到依法施工,文明施工,杜绝违法施工、野蛮施工事件发生。
做到现场布局合理,施工组织有序,材料堆码整齐,设备停放有序,标识标志醒目,环境整洁干净,实现施工现场标准化、规范化管理。
创建南京南站文明工地。
3、组织机构3.1现场组织机构为了更好的组织生产,执行国家有关政策,根据南京南站工程特点及甲方对工期的要求,按照各个工序交叉施工的总体安排进行人员组织,按专业化、机械化作业的原则配备施工队伍。
成立中铁四局集团京沪高铁南京南站项目经理部第三项目队,实行项目法管理,设队长、书记、副队长、总工程师各一名,下设工程部、物设部、安质部、财务部、工经部、综合办公室、试验室、搅拌站计五部二室一站。
详见项目队的组织机构图如下:4、施工工期安排4.1总工期安排根据总工期、建设指挥部的要求及现场实际情况(只安排了1-6框架节。
7-14框架节位于房区,暂定2008年11月1日可以开工),本框架桥定于2008年9月10日开工,2009年1月31日竣工,总工期144天。
4.2主体工程工期安排 4.2.1京沪场(第1-3节)京沪场共有承台12块,底板12块,边墙身15堵,顶板12孔。
计划承台配置2套模板,按照2天/个,共计需要12天;底板配置3套模板,按照4天/个,共需要16天;墙身配置1套模板(5个边墙为一套),按照5天/1块,共需要15天;顶板配置2套模板和膺架,按照15天/4孔,根据交叉作业,共需要20天。
京沪场1-3节框架工期安排表4.2.2沪汉蓉场(4-6节)沪汉蓉场共有承台12块,底板12块,边墙身15块,顶板12孔。
计划安排同京沪场1-3节。
沪汉蓉场4-6节框架工期安排表4.2.3沪汉蓉场(7-9节)沪汉蓉场共有承台12块,底板12块,边墙身15堵,顶板12孔。
计划安排同京沪场1-3节。
沪汉蓉场7-9节框架工期安排表4.2.4宁安场(10-14节)宁安场共有承台20块,底板20块,边墙身25块,顶板20孔。
计划承台配置2套模板,按照2天/个,共计需要20天;底板配置3套模板,按照4天/个,共需要27天;墙身配置1套模板(5个边墙为一套),按照1天/1块,共需要25天;顶板配置2套模板和膺架,按照10天/4孔,根据交叉作业,共需要25天。
宁安场10-14节框架工期安排表5、施工的内容及影响5.1施工内容:场地布置、土方开挖、地基加固、基础垫层、承台混凝土、框架制作及其养护、防水层施工、出入口翼墙施工、附属工程施工。
5.2施工影响:根据施工图纸及现场调查,框架桥部分处在大张里自然村范围内,施工前必须对部分房屋进行拆除,因地方拆迁不到位造成该框架桥只能施工京沪场的①~③框架节和宁杭城际的④~⑥框架节,其余部分等房屋拆迁完才能够施工。