化学镍金常见缺陷分析
化金常见异常及改善
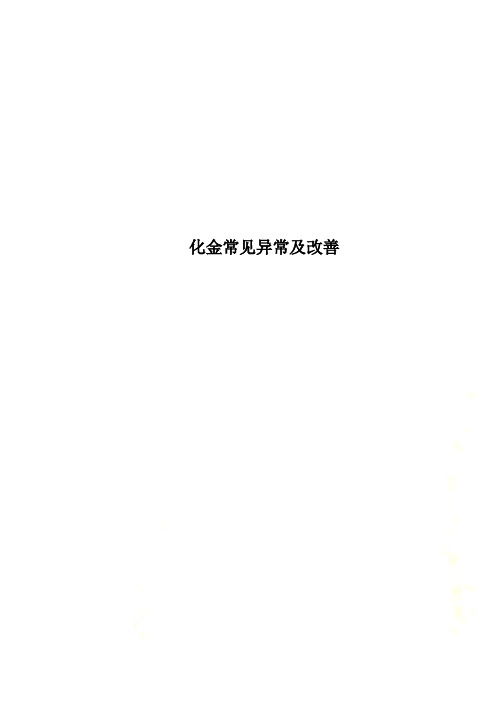
化金常见异常及改善常见问题的原因及处理方案1.漏镀产生原因及解决方案A、镍缸方面①.镍缸拖缸效果差,未能很好激发其活性:重新拖缸,拖缸时镍缸温度提升至82-85℃之间或负载加大或时间延长则可解决。
②.镍缸温度低于75℃或PH值低于4.0:检查温度和PH值,使其不脱离控制范围。
③.镍缸D剂含量过高:正确使用D剂,停产1天以上则额外补加1ml/L,平时按正常比例补加。
④.镍缸打气过强:适当调整其打气流量。
⑤.镍缸空载时间过长或负载不够:保证生产连续性,负载不足加挂拖缸板共镀。
⑥.镍缸加热管漏电:将漏电加热管换掉;B、活化方面①.活化Pd2+浓度低:添加钯水提高Pd2+浓度;②.活化温度太低(低於20℃):加强检测频率,留意温控效果。
③.活化CU2+高,已到后期:更换新活化。
④.活化处理时间过短:正确掌握活化处理时间。
C、板子方面①.线路图形设计不合理,存在电位差,生产时产生化学电池效应出现漏镀:前处理磨板时仅磨板不过微蚀,适当延长活化时间并提高镍缸的活性。
②.阻焊油塞孔未塞满填平,生产中水洗不足,造成药水污染铜面:加大水洗流量。
③.板面铜层显影不净或毒钯处理时遭硫化物污染:检查前工序,毒钯处理应当在蚀刻后退锡前进行,生产此种板需加强磨刷和水平微蚀。
④.板面铜层退锡不净:重新剥锡至铜面干净。
⑤.挠性板溢胶:检查压合工序,控制压合品质。
D、其他方面①.板子活化后在空气中裸露太久钯钝化:防止板子裸露空气中,天车故障及时将板移入对应水洗槽。
②.活化后酸洗或水洗太久,促使钯剥离或铜面遭氧化:活化后酸洗和水洗总时间保持在3分钟以内。
③.新配后浸酸温度太高使钯剥离:新配后浸需将温度下降到30℃以下才可生产。
2.渗镀产生原因及预防改善对策A、活化时间过长或活化水洗不足:致使镀镍时出现长胖现象,严重的则表现为跨镀。
预防及改善:①.活化时间控制在工艺范围内。
②.加大活化后水洗流量,并且活化后水洗每班更新一次。
若中途停纯水则需停止生产,待有纯水后再生产。
如何改善化学镀镍的耐腐蚀性能

如何改善化学镀镍的耐腐蚀性能化学镀技术能广为应用的原因之一是镀层具有优越的耐蚀性能,它是阴极性镀层,所以镀层厚度及完整性是保护基材效果好坏的关键,否则反而加快基材的腐蚀,这点必须充分予以重视。
Ni-P镀层耐蚀性能与磷量密切相关,高磷镀层耐蚀性能优越源于它的非晶态结构。
非晶态与晶态的本质区别在它们的原子排列是否周期性,由于固体化学键的作用从短程看二者都是有序的,非晶的特性是不存在长程有序,无平移周期性。
这种原子排列的长程无序,使非常均匀的Ni-P固溶体组织中不存在晶界、位错、孪晶或其他缺陷。
另外,非晶态镀层表面钝化膜性质也因为基体的特征,其组织也是高度均匀的非晶结构,无位错、层错等缺陷,韧性也好,不容易发生机械损伤。
与晶态合金对比,非晶态合金钝化膜形成速度快,破损后能立即修复而具有良好的保护性。
研究发现Ni-P合金在酸性介质中形成的钝化膜是磷化物膜,其保护能力比纯镍钝化膜强。
例如,Ni-P合金在稀盐酸中腐蚀,磷量低是磷促进镍的活性溶解。
小于8%P的镀层表面有黑灰色的腐蚀产物,用俄歇电子谱仪测定表面一定深度处发现Ni、P及O三种元素,光电子能谱仪进一步证实它是镍的磷酸盐膜。
但大于8%P的高磷镀层腐蚀后表面呈灰白色,一般尚能保持光洁,俄歇电子谱仪观测到约10Å深处有Ni、O,是氧化镍层,依次在20Å处是Ni、P及O共存,是磷酸盐层,内层则为富P的Ni、P层,P量约占20(重量)%,大体对应Ni2P。
含P≥8%的非晶态Ni-P镀层在HCl、FeCl3等介质中腐蚀后X射线从产物中检查出Ni2P。
光电子能谱定量分析发现腐蚀前Ni/P=3.4,腐蚀后Ni/P=1.2,即有磷在表面富集现象。
腐蚀过程的热效应也会使亚稳的非晶态结构晶化,形成Ni2P或NixPy。
Ni-8%P镀层在H2SO4中腐蚀后光电子能谱除了发现NixPy峰外,还发现PO43-。
非晶态Ni-P层表面形成的磷化物膜阻挡了腐蚀继续进行而提高了它的耐蚀性,但这层磷化物膜易被氧化性酸如HNO3溶解,所以Ni-P层不耐氧化性介质的腐蚀。
化金常见异常及改善
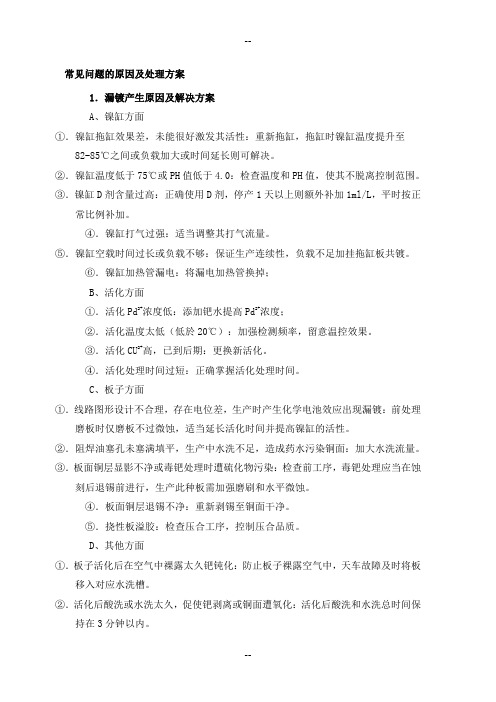
常见问题的原因及处理方案1.漏镀产生原因及解决方案A、镍缸方面①.镍缸拖缸效果差,未能很好激发其活性:重新拖缸,拖缸时镍缸温度提升至82-85℃之间或负载加大或时间延长则可解决。
②.镍缸温度低于75℃或PH值低于4.0:检查温度和PH值,使其不脱离控制范围。
③.镍缸D剂含量过高:正确使用D剂,停产1天以上则额外补加1ml/L,平时按正常比例补加。
④.镍缸打气过强:适当调整其打气流量。
⑤.镍缸空载时间过长或负载不够:保证生产连续性,负载不足加挂拖缸板共镀。
⑥.镍缸加热管漏电:将漏电加热管换掉;B、活化方面①.活化Pd2+浓度低:添加钯水提高Pd2+浓度;②.活化温度太低(低於20℃):加强检测频率,留意温控效果。
③.活化CU2+高,已到后期:更换新活化。
④.活化处理时间过短:正确掌握活化处理时间。
C、板子方面①.线路图形设计不合理,存在电位差,生产时产生化学电池效应出现漏镀:前处理磨板时仅磨板不过微蚀,适当延长活化时间并提高镍缸的活性。
②.阻焊油塞孔未塞满填平,生产中水洗不足,造成药水污染铜面:加大水洗流量。
③.板面铜层显影不净或毒钯处理时遭硫化物污染:检查前工序,毒钯处理应当在蚀刻后退锡前进行,生产此种板需加强磨刷和水平微蚀。
④.板面铜层退锡不净:重新剥锡至铜面干净。
⑤.挠性板溢胶:检查压合工序,控制压合品质。
D、其他方面①.板子活化后在空气中裸露太久钯钝化:防止板子裸露空气中,天车故障及时将板移入对应水洗槽。
②.活化后酸洗或水洗太久,促使钯剥离或铜面遭氧化:活化后酸洗和水洗总时间保持在3分钟以内。
③.新配后浸酸温度太高使钯剥离:新配后浸需将温度下降到30℃以下才可生产。
2.渗镀产生原因及预防改善对策A、活化时间过长或活化水洗不足:致使镀镍时出现长胖现象,严重的则表现为跨镀。
预防及改善:①.活化时间控制在工艺范围内。
②.加大活化后水洗流量,并且活化后水洗每班更新一次。
若中途停纯水则需停止生产,待有纯水后再生产。
《金属热处理缺陷分析及案例》完整版
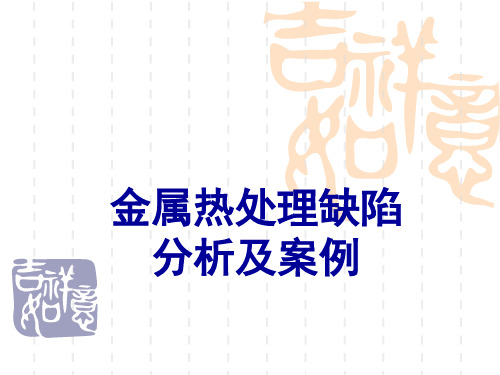
聚二醇(PAG)。
▪ F、其它措施: ▪ 及时回火。局部包扎。 ▪ (六)、其它热处理裂纹: ▪ 回火裂纹:多出现于高速钢或高合金工
具钢。 ▪ 冷处理裂纹:高速钢刀具、工模具冷至
-80度以下的淬火处理时易出现裂纹。 ▪ 时效裂纹:高温合金多。 ▪ 磨削裂纹:出现于淬硬工具钢或经渗碳、
▪ 经渗碳、碳氮共渗的零件,表层产生 很大的压应力、心部产生很大的拉应 力。
三、残余应力对力学性能的影响:
▪ 1、残余拉应力导致硬度降低,压应力则提 高硬度值。
▪ 2、残余应力增大,磨损增大。 ▪ 3、疲劳失效: ▪ (1)、失效过程:裂纹萌生→裂纹扩展。 ▪ (2)、残余压应力提高工件的疲劳强度。 ▪ 4、残余拉应力增大了应力腐蚀开裂的敏感
金属热处理缺陷 分析及案例
授课内容:
▪ 第一部分: ▪ 常见热处理缺陷的特征、产生原因、
危害性和预防措施。 ▪ 第二部分: ▪ 热处理质量全面控制体系。 ▪ 第三部分: ▪ 典型热处理缺陷案例分析。 ▪ 第四部分: ▪ 总结复习
▪第一部分
▪热处理缺陷特征、原因 及防止措施
第一章、热处理缺Biblioteka 概述:▪ A、冶金因素: ▪ (1)材料质量:冶金缺陷扩展成淬火裂纹。 ▪ (2)、化学成分:①、碳量超高,倾向越大。
②、合金元素:双向作用。 ▪ (3)、原始组织:粗大组织或魏氏组织倾向
大。球状组织倾向小。
B、零件尺寸和结构:
▪ (1)、截面尺寸过大或过小不易淬 裂。
▪ (2)、截面突变处:淬裂倾向大。
▪ (一)、含义:
▪ 指在热处理生产过程中产生 的使零件失去使用价值或不符合 技术条件要求的各种不足,以及 使热处理以后的后序工序工艺性 能变坏或降低使用性能的热处理 隐患。
化学镀镍层的外观及镀层成分的分析方法

化学镀镍层的外观及镀层成分的分析方法化学镀镍层的外观及镀层成分的分析方法镀态下的主要表面的外观可为光亮、半光亮或无光泽。
除另有规定,当用目视检查时,表面应均匀,不应有麻点、裂纹、起泡、分层或结瘤等缺陷。
若用户规定了化学镀镍磷合金镀层的化学成分,应逐项分析,并提供其化学成分的数据。
其测定方法如下:(1)试样的制备在遮盖了一面的铝箔上沉积20~50um厚的镀层,除去遮盖层后将其浸入10%的氢氧化钠溶液中溶解,除净铝箔,可获分析用镀层试样。
另一种制备的方法是:在清洁的不锈钢片上沉积20~50um厚镀层,由于镀层与不锈钢表面结合强度较差,可剥取片状镀层试样。
(2)镍含量的测定(丁二酮肟重量法)原理将试样溶解于硝酸中,加入柠檬酸与存在的铁络合,中和,并用丁二酮肟使镍生成沉淀,然后过滤、干燥、称重。
试剂①(1:1)硝酸溶液;②丁二酮肟1%异丙醇或甲醇溶液;③柠檬酸;④(1:1)按水,密度大约为0.88g/mL的浓按水,用等体操作的蒸馏水稀释。
设备砂芯玻璃坩埚。
烘箱,能够保持温度为110±2℃。
方法步骤称取大约0.1g试样,精确至0.0001g,移至400mL的烧杯中。
将试样溶于20mL硝酸溶液,加热溶液至沸腾使二氧化氮挥发,冷却至室温,用水稀释至150mL,加入1g柠檬酸,再加氨水调整溶液PH值至8~9。
将溶液加热至60~70℃,并且在搅拌下加入30mL丁二酮肟溶液,混合后在60~70℃保温1h干燥,在干燥中冷却至室温;称量精确至0.001g。
结果表示镍含量按下列公式计算,以质量百分数表示Ni%=20.32(m2-m1)/m式中m——试样质量(g)m1——坩埙的质量(g)m2——坩埚和沉淀的质量(g)。
(3)磷含量的测定(分光光度法)原理将试样溶于硝酸中,用高锰酸钾氧化磷,并用亚硝酸钠溶解二氧化锰沉淀,再与钼酸铵或钒酸铵反应呈蓝色,在波长大约为420nm对该显色的络合物进行吸光度测量。
试剂①硝酸溶液,40%(V/V),将2份体积硝酸与3份体积的水混合而成;②亚硝酸溶液NaNO220g/L③高锰酸钾溶液KmnO47.6g/L④钼酸盐—钒酸盐溶液在热水中分别溶解20g钼酸铵和1g钒酸铵,将两种溶液混合,加入200mL硝酸(密度大约1.42g/mL)并用水稀释至1000mL,混合均匀。
化学镍金常见缺陷分析汇总

化学镍金常见缺陷分析:1漏镀1.1.1 主要原因:体系活性(镍缸及钯缸)相对不足,铅锡等铜面污染。
1.1.2问题分析:漏镀的原因在于镍缸活性不满足该Pad位反应势能,导致沉镍化学反应中途停止,或者根本没有沉积金属镍漏镀的特点是:如果一个Pad位漏镀与其相连的所有Pad位都漏镀;出现漏镀问题,首先须区分是否由于污染板面所致。
若是,将该板进行水平微蚀或采用磨板方式除去污染。
影响体系活性的最主要原因是镍缸稳定剂的浓度,但由于难以操作控制,一般不采用降低稳定剂浓度解决该问题。
影响体系活性的主要原因镍缸温度,升高温度一定有利于漏镀的改善。
如果不考虑对部分环境以及内部稳定性,无限度的升高镍缸温度,应该能解决漏镀问题。
影响体系活性的次要因素是活化浓度,温度和时间。
延长活化的时间或提高活化浓度和温度,一定有利于漏镀的改善。
由于活化的温度和浓度太高会影响钯缸的稳定性,而且会影响其他制板的生产,所以,在这些次要因素中,延长时间是首选改善措施。
镍缸的PH值、次磷酸钠以及镍缸负载都会影响镍缸活性,但其影响程度较小,而且过程缓慢,所以不宜作为解决漏镀的主要方法。
1.2 渗镀1.2.1 主要原因体系活性太高,外界污染或前工序残渣;1.2.2问题分析渗镀的主要成因在于镍缸活性过高,导致选择性太差,不但使铜面发生化学沉积,同时其他区域(如基材、绿油侧边等)也发生化学沉积,造成不该出现沉积的地方沉积化学镍金。
出现渗镀问题,首先须区分是否由外界污染或残渣(如铜、绿油等)所致。
若是,将该板进行水平微蚀或其他的方法去除。
升高稳定剂浓度是改善体系活性太高的最直接的方法,但是,用漏镀问题改善一样,因难以操作控制而不宜采用。
降低镍缸温度是改善渗镀的最有效的方法,理论上无限度的降低温度,可以彻底解决渗镀问题。
降低钯缸温度和浓度,以及减少钯缸处理时间,可以降低体系活性,有效地改善渗镀的问题。
镍缸的PH值,次磷酸钠以及镍缸负载,降低其控制范围有利于渗镀的改善,但因其影响较小而且过程缓慢,不宜作为改善渗镀问题的主要方法。
化学镍金之镍腐蚀标准及改善

化学镍金之镍腐蚀标准及改善在化学沉镍金表面处理工艺中,镍层作为金层和铜层之间的过渡层,起到阻挡铜和金相互扩散的作用,同时还起到焊接基底层的作用。
而镍腐蚀是化学沉镍金工艺一直以来面临的一个品质问题,镍腐蚀的存在会导致PCB的可焊性下降,造成焊点强度变差,甚至掉元器件等情况,降低了PCBA 产品的可靠性。
对于化学镍金工艺来说,其本质是一个置换反应,由于置换反应获得的金层为疏松多孔结构,且金原子体积大,在浸金反应后期,虽然金层厚度不再增加,但金原子间隙下的镍层仍然可以继续被置换。
镍过度置换产生的镍离子往往积累在金层下面,被氧化后就生成黑色氧化物,这也就是所谓的黑盘(镍腐蚀)。
镍氧化物浸润能力很差,因而黑盘对镍金层的可焊性会产生致命影响。
1.可焊性不良及元器件掉落现象沉金镍腐蚀的存在会导致PCB焊盘缩锡、PTH孔孔环发黑等现象,如下图1所示。
2.镍腐蚀现象观察及评判标准(1)焊盘表面观察通过扫描电镜观察缩锡焊盘及发黑焊环表面的微观形貌,可观察到晶格处在大量黑色纹路,即存在镍腐蚀现象。
(2)剥金后镍层水平观察采用无氰剥金药水将焊盘表面的金层剥离掉,观察剥金后的镍层表面形貌,可以观察到镍层表面存在大量黑点和裂纹,即为镍腐蚀。
(3)垂直切片镍层截面观察观察镍层截面处的形貌,可以观察到连续的镍腐蚀,进一步确认该可焊性不良板存在镍腐蚀现象。
镍腐蚀标准:(1)连续性的镍腐蚀不接受;(2)镍腐蚀深度≤1/3镍厚可接受;(3)局部单点接受判定:深度≤40%镍厚且10μm范围内点数≤2。
可知图4中的镍腐蚀不可接受。
(4)镍腐蚀对IMC的影响镍腐蚀处IMC生长不连续,导致可焊性不良,如图5所示。
3.可焊性验证为验证焊盘可焊性不良的根本原因,现对酸洗前后的PCB焊盘进行可焊性验证,结果如图6所示。
PCB裸板直接浸锡存在上锡不良的现象;经稀盐酸清洗后,上锡饱满。
稀盐酸清洗可以有效去除因镍腐蚀导致的镍面氧化层,改善了镍层的焊接性能,因此,经稀盐酸清洗后,PCB可焊性良好。
图形电路化学镍金镀层品质缺陷与分析
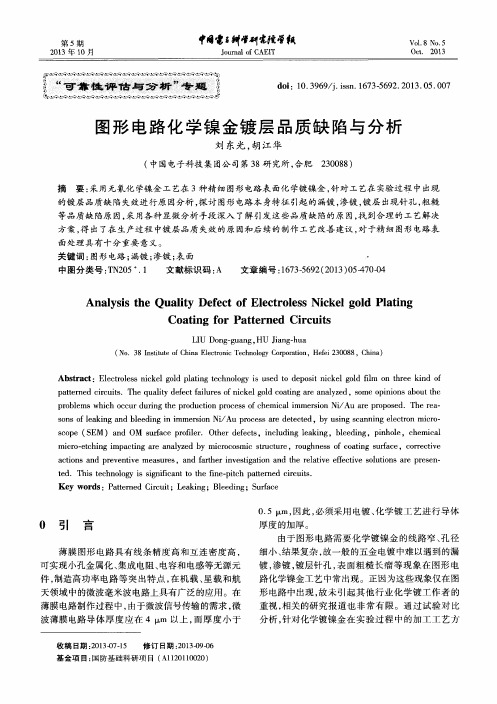
s c o p e( S E M)a n d O M s u r f a c e p r o i f l e r .O t h e r d e f e c t s ,i n c l u d i n g l e a k i n g , b l e e d i n g ,p i n h o l e ,c h e m i c a l
pa t t e r n e d c i r c u i t s .Th e q ua l i t y de f e c t f a i l u r e s o f ni c k e l g o l d c o a t i n g a r e a n a l y z e d,s o me o p i n i o n s a b o u t t h e pr o b l e ms wh i c h o c c ur d u r i n g t he p r o d uc t i o n p r o c e s s o f c h e mi c a l i mme r s i o n Ni /Au a r e p r o p o s e d.Th e r e a - s o n s o f l e a k i n g a n d b l e e d i n g i n i mme r s i o n Ni / Au p r o c e s s a r e d e t e c t e d,b y us i n g s c a n n i n g e l e c t r o n mi c r o -
Co a t i ng f o r Pa t t e r ne d Ci r c ui t s
L I U Do n g — g u a n g , HU J i a n g — h u a
PCB化学镍金ENIG板焊接不良和回流焊不良的分析、区分——PCB测试手段综合运用实例探讨
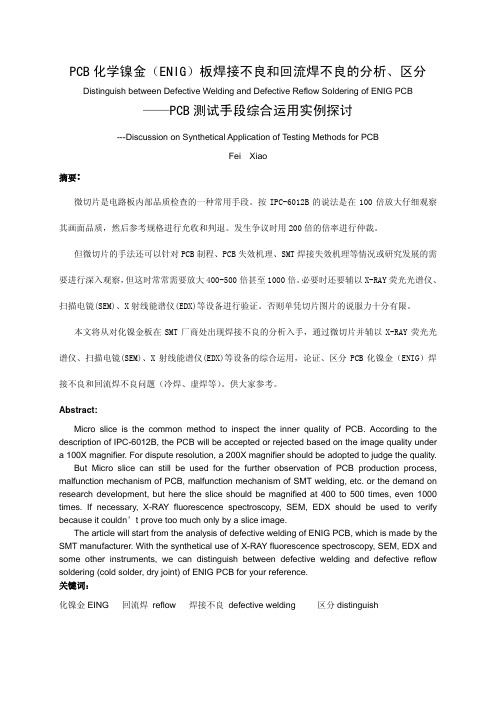
保温区时,使 PCB 和元器件得到充分的预热,以防 PCB 突然进入焊接高温区而损坏 PCB
和元器件;在助焊剂活化区,焊膏中的助焊剂润湿焊盘、元件焊端,并清洗氧化层;当
PCB 进入焊接区时,温度迅速上升使焊膏达到熔化状态,液态焊锡润湿 PCB 的焊盘、元
件焊端,同时发生扩散、溶解、冶金结合,漫流或回流混合形成焊锡接点;PCB 进入冷
程中会迅速溶入锡体之中。所以黄金本身并未参与焊点的组织,其唯一的功用就是在保 护化镍层免于生锈或钝化,否则将不能形成IMC也无法焊牢。金层越厚熔入焊点的量也 将越多,反而会造成脆化以致焊点强度越糟也越不可靠。而焊接温度不足也会对焊接造 成非常大的影响。相关问题大致请见下表:
常见问题一览表
问题
问题产生分析
才较坚强和可靠。焊接良好的焊点切片将清楚的看到均匀的IMC层。如果焊接时焊接热
量不充足,虽然已经形成NixSny的IMC层,但由于热量不足会直接影响AuxSny的形成和Au 的扩散速度,导致Au未必完全熔入焊锡,那么此时的焊点强度将大打折扣。一旦收到外
力将很容易裂开。 所以由上可见:ENIG可焊层所形成的焊点是生长在镍层上,而浸金的薄层在焊接过
But Micro slice can still be used for the further observation of PCB production process, malfunction mechanism of PCB, malfunction mechanism of SMT welding, etc. or the demand on research development, but here the slice should be magnified at 400 to 500 times, even 1000 times. If necessary, X-RAY fluorescence spectroscopy, SEM, EDX should be used to verify because it couldn’t prove too much only by a slice image.
化学镀镍配方分,化学镀镍配方分析技术及生产工艺

化学镀镍配方成分分析,镀镍原理及工艺技术导读:本文详细介绍了化学镍的研究背景,分类,原理及工艺等,本文中的配方数据经过修改,如需更详细资料,可咨询我们的技术工程师。
禾川化学引进国外配方破译技术,专业从事化学镍成分分析、配方还原、研发外包服务,为化学镍相关企业提供一整套配方技术解决方案。
一、背景化学镀镍也叫做无电解镀镍,是在含有特定金属盐和还原剂的溶液中进行自催化反应,析出金属并在基材表面沉积形成表面金属镀层的一种优良的成膜技术。
化学镀镍工艺简便,成本低廉,镀层厚度均匀,可大面积涂覆,镀层可焊姓良好,若配合适当的前处理工艺,可以在高强铝合金和超细晶铝合金等材料上获得性能良好的镀层,因此在表面工程和精细加工领域得到了广泛应用。
禾川化学技术团队具有丰富的分析研发经验,经过多年的技术积累,可以运用尖端的科学仪器、完善的标准图谱库、强大原材料库,彻底解决众多化工企业生产研发过程中遇到的难题,利用其八大服务优势,最终实现企业产品性能改进及新产品研发。
样品分析检测流程:样品确认—物理表征前处理—大型仪器分析—工程师解谱—分析结果验证—后续技术服务。
有任何配方技术难题,可即刻联系禾川化学技术团队,我们将为企业提供一站式配方技术解决方案!二、化学镀工艺化学镀工艺流程为:试样打磨-清洗-封孔-布轮抛光-化学除油-水洗-硝酸除锈-水洗-活化-化学镀-水洗-钝化-水洗-热水封闭-吹干。
图1 化学镀的工艺流程图三、化学镀镍分类化学镀镍的分类方法种类多种多样,采用不同的分类规则就有不同的分类法。
四、化学镀镍原理目前以次亚磷酸盐为还原剂的化学镀镍的自催化沉积反应,已经提出的理论有羟基-镍离子配位理论、氢化物理论、电化学理论和原子氢态理论等,其中以原子氢态理论得到最为广泛的认同。
该理论认为还原镍的物质实质上就是原子氢。
在以次亚磷酸盐为还原剂还原Ni2+时,可以以下式子表示其总反应:3NaH2PO2+3H2O+NiSO4→3NaH2PO3+H2SO4+2H2+Ni(1)也可表达为:Ni2++H2PO2-+H2O→H2PO3-+2H++Ni(2)其过程可分为以下四步:首先,加热化学沉积镍-磷合金镀液,此时镀液并未马上反应,而是金属首先进行催化,H2PO2-在水溶液中发生脱氧生成了H2PO3-,同时释放出原子态活性氢。
ElectrolessNickelandImmersionGold简称ENIG化镍沉金
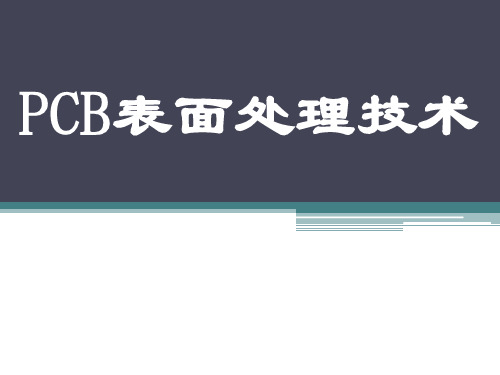
• 应用:客户指定。在高频信号中,沉Ag板电性能良好。欧美不少用户要求作
沉Ag板。 9
3.5 电镀镍金
• 流程:除油-微蚀-酸洗-纯水洗-镀镍-纯水洗-镀金-回收金-水洗 • 镀层类型:
⑴镀硬金。
用在:PCB插头,按键上。 特点:·耐磨,接触良好,有硬度(120-190㎏/㎜²﹚ ·镍打底,Ni层厚度3-5微米;金厚度:0.1,0.25,0.5,0.8,1.0…微米。 ·金镀层含有钴(Co,0.5%﹚,或Ni锑等金属。 ⑵镀软金。 纯金,24K金。 用途:焊接用。
2
2. 0、 PCB无铅化
(1)、ROHS禁令: 禁6种物质:Pb,Hg,Cr6+ (六价铬),PBB(多溴联苯),PBDE(多溴联苯乙醚)。 其中一种就是铅。 (2)、铅的毒性: 智力下降,失眠,恶梦,无力,腹胀痛,头痛,食欲不振。 典型有害影响:贫血,中枢神经系统紊乱。 (3)、何为无铅? ·物质含量中的Pb≤1000ppm,即0.1%,为无铅。 ·只要不是故意在焊料中加铅就应是无铅。
·图形镀Ni/Au。板子在图形线路上镀Ni/Au,镍金作抗蚀层。蚀刻图形后,线路、
孔、焊盘覆盖Ni/Au。但图形线路和板边上镀金浪费,在金面上印阻焊剂附着力难 以保证。目前使用的产品已不多。
(6)、无铅焊料的配方。
4
·美国熔焊: 95.9 Sn-3.9 Ag- 0.6Cu 波焊:99.3 Sn-0.7 Cu ·欧盟:95.5 Sn-3.8 Ag-0.7 Cu ·日本:96.5 Sn-3.0 Ag-0.5 Cu ,即305配方(3.0%银,0.5%铜,其余为 锡,称之为305)。 ·上述配方,共熔点是217℃。比传统的铅锡合金183℃熔点提高了34℃。 ·无铅喷锡工艺,温度为265-270℃。有时候,板子喷得不平整,不合格,返 工1-2次,引起板子分层起泡,或阻焊剂起泡,板子报废。 ·据说,目前用得最广泛的是305焊料配方。SMT装配时用305,PCB厂喷锡往往 不使用305焊料。 “这是一筐烂苹果中找到的一个好苹果”学者这样评说。 ·在PCB厂作无铅喷锡,基于305焊料在使用过程中,Cu含量不断升高污染锡缸, 引起SMT装配时,锡面流动性差,散锡性不理想。在PCB厂作无铅喷锡,较多的 使用是这样的焊料:SCN,或SN100C,其焊料成份是:Sn-0.7Cu-0.05Ni(或锗 Ge替代Ni,0.05%Ge)。(Ni含量为0.02-0.05%)。 ·在Sn-0.7 Cu-0.05 Ni的焊料配方中,镍的存在减缓了铜在界面金属化合物 (IMC)的扩散速度。锗Ge的存在,目的是形成一层保护性的氧化膜。 5 ·当熔融焊料中Cu含量≥3%,涂覆的焊料层会发生粗糙,脆裂等问题。
电镀缺陷一览表
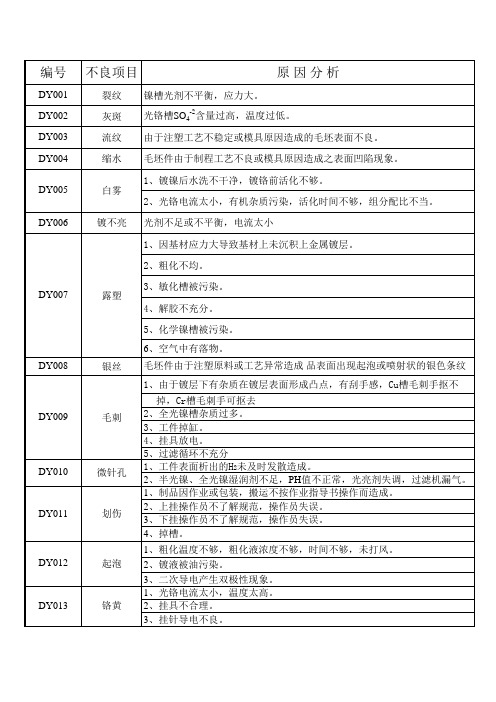
DY014
DY015 DY016
污点 凸点
DY017
麻点
DY018
漏镀铜
DY019
漏镀镍
DY020
变形
2、粗化温度过高。 3、毛胚存在应力。 4、毛胚结构不合理。 1、槽液受污染。 2、水洗不干净所致。 3、制程在空气中暴露时间过长,灰尘附着。
DY021
星尘
DY022 DY023 DY024 DY025
镀不亮
光剂不足或不平衡,电流太小 1、因基材应力大导致基材上未沉积上金属镀层。 2、粗化不均。
DY007
露塑
3、敏化槽被污染。 4、解胶不充分。 5、化学镍槽被污染。 6、空气中有落物。
DY008
银丝
毛坯件由于注塑原料或工艺异常造成 品表面出现起泡或喷射状的银色条纹 1、由于镀层下有杂质在镀层表面形成凸点,有刮手感,Cu槽毛刺手抠不 掉,Cr槽毛刺手可抠去 2、全光镍槽杂质过多。 3、工件掉缸。 4、挂具放电。 5、过滤循环不充分 1、工件表面析出的H2未及时发散造成。 2、半光镍、全光镍湿润剂不足,PH值不正常,光亮剂失调,过滤机漏气。 1、制品因作业或包装,搬运不按作业指导书操作而造成。 2、上挂操作员不了解规范,操作员失误。 3、下挂操作员不了解规范,操作员失误。 4、掉槽。 1、粗化温度不够,粗化液浓度不够,时间不够,未打风。 2、镀液被油污染。 3、二次导电产生双极性现象。 1、光铬电流太小,温度太高。 2、挂具不合理。 3、挂针导电不良。
水渍 熔接线 脱皮 靠胶
水洗工序的水质差。 注塑工艺造成,熔融塑胶的接合线。 1、酸活化浓度不够,时间不够。 挂具设计不当,操作有误。
编号
DY001 DY002 DY003 DY004 DY005 DY006
半导体晶圆化学镍金UBM工艺与设备-刘勇

8 (总第 179 期)Dec. 2009
EPE 电 子 工 业 专 用 设备 Equipment for Electronic Products Manufacturing
·封装工艺与设备·
1 钝化层清洗洗 4 退锌
5 二次浸锌
2 铝层蚀刻 3 一次浸锌 6 化学镀镍
备的化学槽体采用 PVDF 材料,管道采用 Teflon 材 料,泵体、阀门、管道等也采用防腐耐温部件。需要 有金属构件的部件也要用 Teflon 材料包裹。
步骤 1-5 属于前处理工艺,前处理的质量和效 果直接影响到化学镍 / 金 UBM 的质量和化学镍槽 的使用寿命,在整个工艺中应引起足够的重视。
3.2 设备的结构布局 根据化学镍 / 金 UBM 的工艺流程确定设备的
结构和布局,包括钝化层清洗槽,铝层蚀刻槽,浸锌 槽,褪锌槽,化学镍槽,浸金槽。产品进出每一个化 学槽都要经过一水洗槽,将晶圆上的残留药液冲洗 干净,防止化学槽间的交叉污染。产品自上料区由 自动机械手抓取,按照设定的工艺程序,自动进出 每个化学槽体。图 3 为一半导体晶圆化学镍 / 金 UBM 自动生产线。
3.1 设备材料的选择 考虑到化学镀镍的自催化特性和半导体晶圆
的生产要求,选择的材料应符合的要求:(1) 耐强酸 碱腐蚀;(2) 在 100 ℃内不老化变形;(3) 材料表面 光滑平整,无毛刺,粗糙的表面容易引起化学镍的 沉积,同时也不利于槽体的清洗;(4) 材料本身不具 有对化学镀镍产生催化的成分。根据以上要求,设
求及设备内部结构。 在 200 mm 的半导体晶圆上成功制作 5 μm 化学镍 / 金 UBM 和 18 μm 化学
镍金凸点。 在光学显微镜、表面轮廓仪和 SEM 下检测了化学镍 / 金镀层的表面形貌。 通过 EDX
化学镀镍的常见故障
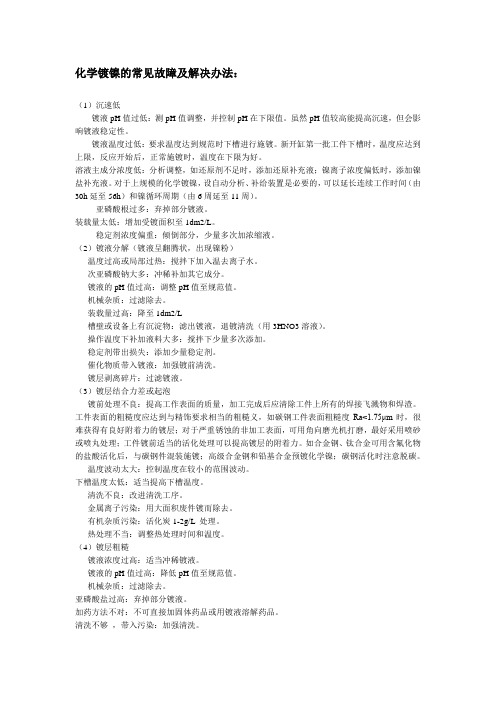
化学镀镍的常见故障及解决办法:(1)沉速低镀液pH值过低:测pH值调整,并控制pH在下限值。
虽然pH值较高能提高沉速,但会影响镀液稳定性。
镀液温度过低:要求温度达到规范时下槽进行施镀。
新开缸第一批工件下槽时,温度应达到上限,反应开始后,正常施镀时,温度在下限为好。
溶液主成分浓度低:分析调整,如还原剂不足时,添加还原补充液;镍离子浓度偏低时,添加镍盐补充液。
对于上规模的化学镀镍,设自动分析、补给装置是必要的,可以延长连续工作时间(由30h延至56h)和镍循环周期(由6周延至11周)。
亚磷酸根过多:弃掉部分镀液。
装载量太低:增加受镀面积至1dm2/L。
稳定剂浓度偏重:倾倒部分,少量多次加浓缩液。
(2)镀液分解(镀液呈翻腾状,出现镍粉)温度过高或局部过热:搅拌下加入温去离子水。
次亚磷酸钠大多:冲稀补加其它成分。
镀液的pH值过高:调整pH值至规范值。
机械杂质:过滤除去。
装载量过高:降至1dm2/L槽壁或设备上有沉淀物:滤出镀液,退镀清洗(用3HNO3溶液)。
操作温度下补加液料大多:搅拌下少量多次添加。
稳定剂带出损失:添加少量稳定剂。
催化物质带入镀液:加强镀前清洗。
镀层剥离碎片:过滤镀液。
(3)镀层结合力差或起泡镀前处理不良:提高工作表面的质量,加工完成后应清除工件上所有的焊接飞溅物和焊渣。
工件表面的粗糙度应达到与精饰要求相当的粗糙义,如碳钢工件表面粗糙度Ra<1.75μm时,很难获得有良好附着力的镀层;对于严重锈蚀的非加工表面,可用角向磨光机打磨,最好采用喷砂或喷丸处理;工件镀前适当的活化处理可以提高镀层的附着力。
如合金钢、钛合金可用含氟化物的盐酸活化后,与碳钢件混装施镀;高级合金钢和铅基合金预镀化学镍;碳钢活化时注意脱碳。
温度波动太大:控制温度在较小的范围波动。
下槽温度太低:适当提高下槽温度。
清洗不良:改进清洗工序。
金属离子污染:用大面积废件镀而除去。
有机杂质污染:活化炭1-2g/L 处理。
热处理不当:调整热处理时间和温度。
封孔剂应用于化学镀镍金中改善腐蚀的研究

封孔剂应用于化学镀篠金中改善腐蚀的研究邱成伟李小海唐鹏王晓槟(惠州中京电子科技有限公司,广东惠州519029)摘要随着印制电路板不断向轻、薄、短小高密度方向发展,其中化铢浸金是一种能满足大多数的组装要求的可行的表面涂层。
在生产过程中出现一种异常现象,沉金后如何减少操腐蚀反应速率,降低或消除沉金板金面异色、焊接不良等缺陷的产生比例,采用有机小分子填充沉金镀层微孔,防止沉金后工序各类水、酸、碱等物质的渗入,隔绝金-線原电池效应的反应环境,达到改善沉金金面异色、焊接不良等异常的目的,经过多方验证测试,该方法效果良好。
关键词镰腐蚀;填充;沉攥金中图分类号:TN41文献标识码:A文章编号:1009-0096(2019)10-0036-05Study on the improving corrosion in electroless nickel and goldby using pore-sealing agentQiu Chengwei Li Xiaohai Tang Peng Wang XiaobinAbstract As the printed circuit board is to develop in the direction of light,thin,short and high density,the chemical nickel gold leaching is a kind of process which can satisfy the requirement of most of the assembly of the feasible surface coating.But a kind of abnormal phenomenon appeared in the process of production.How to reduce the nickel corrosion reaction rate after heavy gold,how to reduce or eliminate the heavy gold sheet metal surface defects such as different colors,poor welding cases by using organic small molecular filling heavy gold coating micropore,preventing heavy gold after process of all kinds of materials such as water,acid and alkali infiltration,cutting off the gold-nickel galvanic effect of the reaction of the environment,so as to achieve the purpose of improving the abnormal color of gold surface and bad welding,etc.Key words Nickel Etching;Filling and Precipitation.0刖百近年来,随着电子设备线路设计日趋复杂,以及电子产业无铅化的大背景下,化学镀镰/金工艺得到国内外的迅速推广。
化学镀镍金常见问题分析
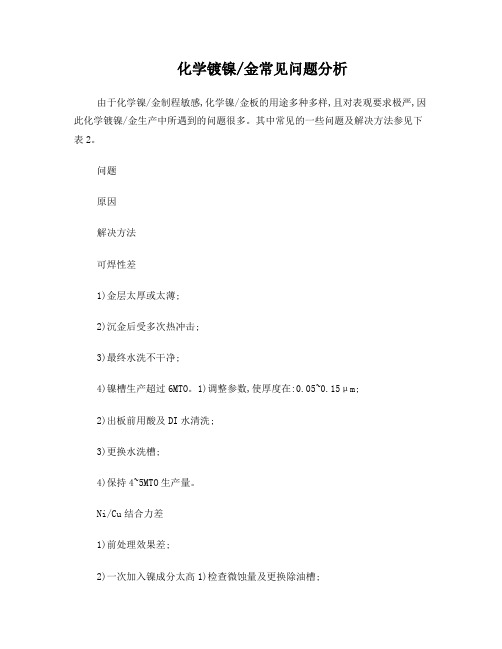
化学镀镍/金常见问题分析由于化学镍/金制程敏感,化学镍/金板的用途多种多样,且对表观要求极严,因此化学镀镍/金生产中所遇到的问题很多。
其中常见的一些问题及解决方法参见下表2。
问题原因解决方法可焊性差1)金层太厚或太薄;2)沉金后受多次热冲击;3)最终水洗不干净;4)镍槽生产超过6MTO。
1)调整参数,使厚度在:0.05~0.15μm;2)出板前用酸及DI水清洗;3)更换水洗槽;4)保持4~5MTO生产量。
Ni/Cu结合力差1)前处理效果差;2)一次加入镍成分太高1)检查微蚀量及更换除油槽;2)用光板拖缸20~30minAu/Ni结合力差1)金层腐蚀;2)金槽、镍槽之间水洗PH>83)镍面钝化1)升高金槽PH值;2)检查水的质量;3)控制镀镍后沉金前打气及停留时间漏镀1)活化时间不足;2)镍槽活性不足1)提高活化时间;2)使用校正液,提高镍槽活性渗镀1)蚀刻后残铜;2)活化后镍槽前水洗不足;3)活化剂温度过高;4)钯浓度太高;5)活化时间过长;6)镍槽活性太强1)反馈前工序解决;2)延时水洗或加大空气搅拌;3)降低温度至控制范围;4)降低浓度至控制范围;5)降低活化时间;6)适当使用稳定剂镍厚偏低1)PH 太低;2)温度太低;3)拖缸不足;4)镍槽生产超6MTO 1)调高PH值;2)调高温度;3)用光板拖缸20~30min;4)更换镍槽金厚偏低1)镍层磷含量高;2)金槽温度太低;3)金槽PH值太高;4)开新槽时起始剂不足1)提高镍槽活性;2)提高温度;3)降低PH值;4)适当加入起始剂渗镀问题改善办法随着电子产业的高速发展,PCB布线越来越精密,多数PCB厂家都采用干膜来完成图形转移,干膜的使用也越来越普及,但我在售后服务的过程中,仍遇到很多客户在使用干膜时产生很多误区,现总结出来,以便借鉴。
一,干膜掩孔出现破孔很多厂家认为,出现破孔后,应当加大贴膜温度和压力,以增强其结合力,其实这种观点是不正确的,因为温度和压力过高后,抗蚀层的溶剂过度挥发,使干膜变脆变薄,显影时极易被冲破孔,我们始终要保持干膜的韧性,所以,出现破孔后,我们可以从以下几点做改善:1,降低贴膜温度及压力2,改善钻孔披锋3,提高曝光能量4,降低显影压力5,贴膜后停放时间不能太长,以免导致拐角部位半流体状的药膜在压力的作用下扩散变薄6,贴膜过程中干膜不要张得太紧二,干膜电镀时出现渗镀之所以渗镀,说明干膜与覆铜箔板粘结不牢,使镀液深入,而造成“负相”部分镀层变厚,多数PCB厂家发生渗镀都是由以下几点造成:1,曝光能量偏高或偏低在紫外光照射下,吸收了光能量的光引发剂分解成游离基引发单体进行光聚合反应,形成不溶于稀碱的溶液的体型分子。
常见金相组织缺陷与失效介绍
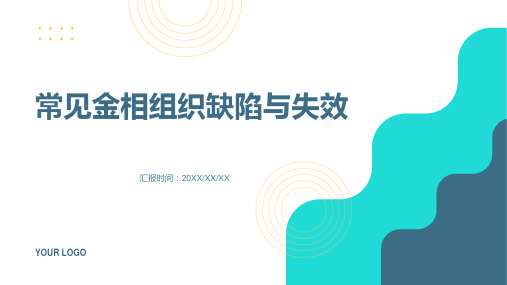
缺陷与失效分析
缺陷类型:气孔、夹杂、裂纹、磨损等 失效原因:设计不合理、材料选择不当、加工工艺问题等 失效后果:影响产品性能、缩短使用寿命、造成安全隐患等 预防措施:优化设计、选用合适材料、改进加工工艺等
解决方案
优化材料选择:选择合适的材料,避免缺 陷产生
改进工艺:优化生产工艺,减少缺陷产生
加强检测:提高检测频率和质量,及时发 现缺陷
材料缺陷:如夹杂物、气孔、裂纹等 加工工艺不当:如热处理不当、锻造不当等 设计不合理:如结构不合理、应力集中等 使用环境恶劣:如高温、高压、腐蚀等 维护保养不当:如润滑不足、磨损严重等
失效机理
疲劳失效:循环载荷作用下,材料疲劳 损伤累积导致断裂
断裂失效:材料内部缺陷或应力集中导 致断裂
腐蚀失效:环境因素导致材料表面腐蚀, 降低机械性能
气压:气 压变化可 能导致材 料变形或 破裂
辐射:辐 射可能导 致材料老 化或失效
化学物质: 接触有害 化学物质 可能导致 材料腐蚀 或变质
生物因素: 生物侵蚀 可能导致 材料损坏 或失效
金相组织缺陷检测方法
宏观检测
肉眼观察:直接观察样品表面,发 现明显缺陷
低倍显微镜观察:使用低倍显微镜 观察样品表面,发现更细微的缺陷
变形预防:合理设计、正确选材、控制热处理工艺等
金相组织缺陷原因
原材料问题
原材料质量不 合格:如杂质、 气孔、裂纹等
原材料加工工 艺不当:如热 处理、锻造、 焊接等工艺不
当
原材料选择不 当:如选材不 当、材料搭配
不当等
原材料储存不 当:如储存环 境不当、储存
时间过长等
工艺问题
材料选择不当:材料 性能与使用环境不匹 配
影响金板可焊性原因--SMT生产方面

PTH孔表面焊盘总是无法形成良好的焊点,去返工修正时,焊盘就露黑色,然后再也焊不上去了,划掉黑色层,却又可以焊了,沉镍金PCB板一般只能经受两次高温焊接(一次回流、一次波峰焊)。
再修补的话,表面的沉金就很容易脱落,露出里面的镍(呈现黑色),而镍氧化后的可焊性差,因此很难焊接。
刮掉这层黑色的镍,就露出了里面的铜,所以又能焊接了。
金是被锡溶解的,不是因为高温!锡最终在镍在形成良好的焊点,前提是镍没有氧化!但镍氧化后是沉不上金的!金的掉落并不是因为高温,而是因为与锡发生反应,但沉金的确实只能经过两次焊接的,否则会有质量问题;镍很容易氧化,当然在沉金时是没有氧化的,但经过加工(特别是高温加工)后,如果暴露在空气中,将很快就被氧化了,氧化的镍是不可能进行焊接加工的黑焊盘的检测方式有2种:拉力测试和酸性试验。
黑色氧化物质是Ni2O3。
为化金镀层。
但是当把此小扳子焊接在大扳子上面时发现有较多假焊,甚至拒焊情况。
针对此情况我们有把此位置钢板开孔加大,锡量加大的同时减少了此不良情况,但不良依然存在,一般不良率为2%。
我们初步分析:一.为镀Ni层P含量不较低,在焊接时产生应力较大的IMC,导致IMC以及Nip3熔入锡液中导致拒焊现象(李宁成博士曾经在自己的文章里面这样阐述过)二.PCB 板厂商偷工减料在镀金时镀金量不够,导致可焊性下降。
事实上板面化学沉镍金所形成的焊点,其对零件之焊接强度几乎全都建立在镍层表面上,金层之目的只是让镍层在空气中受到保护不致钝化或氧化,维持起码的可焊性。
因为金层不适合焊接,其焊点强度也非常不好。
在高温焊接的瞬间,金早已与锡组成不同形式的“介面合金共化物”(如:AuSn,AuSn2,AuSn4等)而逸在走,因而真正的焊点基础都是着落在镍面上,焊点的强弱与金无关。
也就是说焊料中的纯锡会与镍形成Ni3Sn4的“介面合金共化物”。
薄薄的金层会在很短时间内快速散走,溜入到大量的焊料中。
金层根本无法形成可靠的焊点,而且金层越厚溶入焊料中也越多,反而使整体焊点强度为之变脆变弱。
PCB_金手指和沉镀金工艺详解

机理—阴极:Ni2++2eNi 阳极: Ni-2eNi2+
VIASYSTEMS ASIA
化学镍金
1.2 无电镍 A、一般无电镍分为“置换式”与“自我催化式”,其配
方极多,但不论何者仍以高温镀层品质较佳。 B、镍盐为硫酸镍。
VIASYSTEMS ASIA
化学镍金
1.2 无电镍
C、还原剂有次磷酸盐类(Hypophosphite)/甲醛( Formaldehyde)/氨(Hydrazine)/硼氩化合物( Borohydride)/硼氢化合物(Amine Borane)。
VIASYSTEMS ASIA
化学镍金
主要反应为: [H2PO2]- +H2O→H+ + [HPO3]2- +2H(Cat)------------(1) Ni2+ + 2H(Cat) →Ni + 2H+-------------------------------(2) [H2PO2]- + H(Cat) → H2O +OH- + P-------------------(3) [H2PO2]- + H2O → H+ + [HPO3]2- +H2-----------------(4)
VIASYSTEMS ASIA
Gold Finger - 金手指
B、镀金 1.高电流区烧焦 原因:金浓度不够;比重太低;搅拌不够;镀金液被镍铜污染。
- 1、下载文档前请自行甄别文档内容的完整性,平台不提供额外的编辑、内容补充、找答案等附加服务。
- 2、"仅部分预览"的文档,不可在线预览部分如存在完整性等问题,可反馈申请退款(可完整预览的文档不适用该条件!)。
- 3、如文档侵犯您的权益,请联系客服反馈,我们会尽快为您处理(人工客服工作时间:9:00-18:30)。
化学镍金常见缺陷分析
:
1漏镀
1.1.1 主要原因:体系活性(镍缸及钯缸)相对不足,铅锡等铜面污染。
漏镀的原因在于镍缸活性不满足该Pad位反应势能,导致沉镍化学反应中途停止,或者根本没有沉积金属镍
漏镀的特点是:如果一个Pad位漏镀与其相连的所有Pad位都漏镀;出现漏镀问题,首先须区分是否由于污染板面所致。
若是,将该板进行水平微蚀或采用磨板方式除去污染。
影响体系活性的最主要原因是镍缸稳定剂的浓度,但由于难以操作控制,一般不采用降低稳定剂浓度解决该问题。
影响体系活性的主要原因镍缸温度,升高温度一定有利于漏镀的改善。
如果不考虑对部分环境以及内部稳定性,无限度的升高镍缸温度,应该能解决漏镀问题。
影响体系活性的次要因素是活化浓度,温度和时间。
延长活化的时间或提高活化浓度和温度,一定有利于漏镀的改善。
由于活化的温度和浓度太高会影响钯缸的稳定性,而且会影响其他制板的生产,所以,在这些次要因素中,延长时间是首选改善措施。
镍缸的PH值、次磷酸钠以及镍缸负载都会影响镍缸活性,但其影响程度较小,而且过程缓慢,所以不宜作为解决漏镀的主要方法。
1.2 渗
镀
1.2.1 主要原因
体系活性太高,外界污染或前工序残渣;
渗镀的主要成因在于镍缸活性过高,导致选择性太差,不但使铜面发生化学沉积,同时其他区域(如基材、绿油侧边等)也发生化学沉积,造成不该出现沉积的地方沉积化学镍金。
出现渗镀问题,首先须区分是否由外界污染或残渣(如铜、绿油等)所致。
若是,将该板进行水平微蚀或其他的方法去除。
升高稳定剂浓度是改善体系活性太高的最直接的方法,但是,用漏镀问题改善一样,因难以操作控制而不宜采用。
降低镍缸温度是改善渗镀的最有效的方法,理论上无限度的降低温度,可以彻底解决渗镀问题。
降低钯缸温度和浓度,以及减少钯缸处理时间,可以降低体系活性,有效地改善渗镀的问题。
镍缸的PH值,次磷酸钠以及镍缸负载,降低其控制范围有利于渗镀的改善,但因其影响较小而且过程缓慢,不宜作为改善渗镀问题的主要方法。
因操作不当导致钯缸或镍缸产生悬浮颗粒弥漫槽液,则应采取过滤或更新槽液来解决!
1.3 甩金
,镍缸或金缸杂质太多
金层因镍层发生分离,镍层与金层的结合力很差,镍面出现异常的造成甩金,镍面出现钝化是造成甩金的主要原因,沉镍后暴露时间过长和水洗时间过长,都会造成镍面钝化面导致结合力不良,当然,水洗的水质出现异常,也有可能导致镍层钝化
至于镍缸或金缸是否为甩金出现的主要原因,可在实验室烧杯中做对比实验来确定,若是,则更换槽液。
1.4甩镍
1.4.1 主要原因:铜面不洁或活化钯层表面钝化,镍缸中加速剂失衡。
1.4.2 问题分析:
镍缸以前制程不良或不能除去铜面杂物(包括绿油残渣),镍层与铜面结合力就会受到影响,从而就导致甩镍。
出现甩镍问题,首先须检查做过程中板面状况,区分铜面杂物还是活化后钯层表面钝化,若是后者,则追踪是否活化后空气中太长还是水洗时间太长。
如果铜面杂物引起甩镍,则检查前处理水平微蚀是否正常,同时须检查前处理之前铜面是否正常,另外,前处理中硫脲药液残留铜面,轻则出现沉镍金色粗糙,重则甩镍。
镍缸中加速剂(如Na2S2O3)太多则会导致镍沉积松散,造成镍层剥落,此时多伴镍面哑色出现(失去光泽),出现这种情况,用拖缸板(镍板)消耗掉多余加速剂,即可重新进行生产。
1.5 非导通孔上金
1.5.1 主要原因:直接电镀或化学沉铜残留的钯太多,或镍缸活性太高
1.6 金面粗糙
,铜面不洁,镍缸药水失衡
1.6.2 问题分析:
电镀产生的铜面粗糙,只能在电镀通过调整光剂或电流密度来改善,至于沉金线,水平微蚀也不能明显改变其粗糙程度;
对于铜面不洁则考虑用磨板或水平微蚀的方式加以改善,可以做到解决铜面不洁造成的金面粗糙。
镍缸药水失衡也会导致沉积松散或粗糙,影响沉积粗糙的主要原因是加速剂太高或稳定剂太少,至于改善对策,则可在实验烧杯加入稳定剂,按1m/L,2ml/L,3m/L做对比实验。
这时就会发现镍面逐渐变得光亮,找出适当的比例将稳定剂加入镍缸即可试板和重新生产。
需要注意的是,药水往往是加药过程中出现偏差,中要纠正错误偏差,调整稳定剂并不是一危险操作:
1.7角位平镀﹝启镀不良﹞
镍缸温度局部过高
镍缸稳定剂浓度过高,加速剂量不够
1.7.2 问题分析:
角位平镀是指化学沉镍过程中,出现Pad的角位不沉积镍的现象,它通常具有方向性的特征,例如圆型Pad则出现同一方向的月芽形不上镍,方型Pad则出现一边完好,对边严重不上镍,两个侧边逐渐变差。
对于镍缸循环局部过快,往往是镍缸药液循环设计不合理或出水管变形造成,它特点是镍缸某个角落固定出现该问题,当然,不合理的打气冲击板面出会导致该问题的出现。
对于镍缸温度局部过热,往往出现在副溢流的镍缸设计,当水位不足的时候,副缸温度往往比主缸高出5℃以上,溢流的热水流量在偏小的同时,往往只扩散在主缸的顶层,造成生产板顶部出现角位平镀的现象。
对于镍缸稳定剂浓度过高,只要不是来料(供应药水)出现太大的质量问题,通过补加适量的加速剂或拖缸,均能解决该问题的出现。
1.8金面颜色不良
,金层厚度严重不足,金缸使用寿命太长或水洗不净。
1.8.2 问题分析
金面颜色不良主要有两种形式,一种是由于金缸稳定剂(络合剂)太多或金层厚度严重不足而形式的金面颜色发白,另一种是由于金缸使用寿命太长或水洗不净造成金面氧化。
当金缸稳定剂补充过多时,往往会出现金面发白而金厚正常的现象,此状况多发生在新开缸初期。
遇到这种情况,只要不拘于化验分析的控制范围,几次补药,颜色就会逐渐转为金黄色。
当然,将金缸温度升高,也会一定程度的改善金面颜色。
对于金层厚度严重不是导致的颜色发白,主要是金缸温度低于下限太多或金盐浓度严重不足,使金层不能将镍的颜色完全覆盖,以至出现白色
对于沉金缸后的水洗过程,残留药水会对金面造成污染,尤其是回收缸,浸洗时间控制在半分钟左右为佳,金面污染的制板,当经过干燥后,金面就会出现棕色的斑痕,用酸洗或普通橡皮擦少除去。
当金缸使用寿命太长,槽液积聚的杂质就会越来越多,金面棕色斑痕就容易出现,所以沉金后水洗一定严重控制,尤其是回收缸药水浓度不能太高。
1.9渗漏镀(这是指渗镀和漏镀在同一块板上同时出现)
1.9.1 问题分析:
渗镀和漏是沉镍金工序最常见问题,首先区分是否外界污染或残留渣(包括残铜)导致问题出现,若是,则采用磨板或水中微蚀的方式去除。
对于漏镀和渗镀在同一块板上同时出现,这说明体态活性不能满足该制板的需求,升高活性,会加剧渗镀的出现,而降低活性则又会导致漏镀的加剧,所以改善对策出现从渗镀、漏镀的特性调整钯缸和镍缸。
首先漏镀的成因在于镍缸选择性太强,导致活性效果不佳的Pad位沉镍化学反应中途停止或镍根本不能沉积,所以唯一能做的就是大幅度提高活化效果(不考虑调节加速剂和稳定剂浓度)缩小Pad位间活化效果差异,方能调整镍缸的空间。
渗镀的成因在于镍缸的选择性太差,降低镍缸的温度可解决该问题出现,一般来讲,将活化时间延长一倍,适应时可以考虑升高活化缸温度(最好不要超过30℃)Pd2+浓度也可以考虑升高10-20PPM,同时将镍缸温度降低到适当值则可解决漏镀和渗镀同时出现的问题。
解决渗镀和漏镀的方法表面看起来好像很矛盾,其实从化学反应原理去看待,则不难理解。
首先,拉的两个问题同时存在,说明单从镍缸入手根本没有调整的空间,其次,活化缸是Pd2+和Cu的置换反应,其反应初期各Pad位有Pd的沉积,随着Pd层的加厚,化学反应速度逐渐减慢,沉钯快的Pad位(Pd较厚)反应趋于停止,而沉钯快的Pad位仍然继续沉积,因而就缩小了各Pad间的活化效果的差异,为解决该矛盾的问题提供调整空间。
化学Ni/Au 问题与对策。