化学镍金制程分析
化学镍金工艺制程简介及生产注意事项及改善方案

化学镍槽基本结构
防析出保护装置 排气管 通孔挡板 低压空气 阴极棒(不锈钢) 此阴极棒必须与槽壁绝缘。 通孔挡板 蒸汽
过
流
溢
滤 罐
槽
副
主槽
不锈钢加热管路
主槽空气搅拌出口 槽 管路与加热 不锈钢 不锈钢 加热区空气搅拌口
镍槽的防析出保护装置
× ×
× ×
※ 须定期测量实际保护电压值; 须定期测量实际保护电压值; ※ 检查阴极棒是否松动接触到槽壁以及接线是否接触良好。 检查阴极棒是否松动接触到槽壁以及接线是否接触良好。
阳极反应 阴极反应
17
置换金反应
离子化趋势 Ni > Au
Ni/P Ni
Ni → Ni2+ + 2e- Ni2+ +螯合剂 → Ni错离子 Au(CN)2 - + e - → Au + 2 CN -
18
现场生产注意事项
1. 化学镍槽生产中注意事项 2. 沉镍金前、后处理注意事项 沉镍金前、 3. 微蚀量的测定方法 4. 各水洗槽空气搅拌注意事项 5. 药水分析添加记录及点检表的填写 6. 来料检验和终检
15 min 15min
30min
60min
15
化学镍操作参数
操作參數
鎳濃度 溫度 pH ↗ ↗ ↗
磷含量
析出速度
還原劑(次磷酸鈉)濃度 ↗ 浴負載(> 1.0 dm /L) 浴負載(< 0.3 dm /L) 攪拌(循環泵浦) 浴壽命M.T.O.
2 2
↗ ↘ ↗ ↗
16
浸镀金
主成份 (1) 金氰化钾KAu(CN)2 (2)有机酸 功能 (3) 螯合剂 (1)提供Au(CN)2— 错离子来源,.在镍面置换 (离子化趋势Ni > Au)沉积出金层. (2)防止镍表面产生钝态并与溶出的Ni2+结合成错离子. (3)抑制金属污染物(减少游离态的Ni2+, Cu2+等). Ni →Ni2++ 2eAu(CN)2-+e-→ Au + 2 CNNi + (Au(CN)2)- → Ni2+ + Au + 2 CN-
化学镍金工艺介绍

化学镍金工艺应知应会
苏州市三生电子有限公司
前言
1、制程介绍 2、药水简介 3、制程管制 4、异常改善 5、保养事项
苏州市三生电子有限公司
制程特征 1、在阻焊之后进行选择性镀镍/金,采取挂篮式作业,无须通电 2、单一表面处理即可满足多种组装城城需求,具有可焊接、可接触导通、
可打线、可散热等功能 3、板面平整、SMD焊垫平坦,适合于密距窄垫的锡膏熔焊。
内置干燥剂。
镍与铜镀层密著不良原因 Nhomakorabea对策绿油残渣附着于铜面
显影后水洗不良
检讨前制程与加强清洁剂,微蚀,磨刷或喷砂 同上
绿油溶入镀液 铜表面氧化没完全去除
1、更换镀液 2、检讨绿油特性,后烧烤条件及前处理流程
加强前处理流程(磨刷是、清洁剂、微蚀等)
微蚀或活化后水洗时间过长
缩短水洗时间 增加水洗槽进水量
前处理机台保养
• 水洗槽定期清洗 • 传送滚轮定期清洗 • 滤芯、滤网定期清洗或更换 • 传动轴上油 • 喷嘴清洗,水洗,风刀 • 药水成份分析补充或更换 • 刷轮定期更换
化金线保养
• 水洗槽清洗 • 管路定期清洗:进水管,过滤筒,循环管等 • 滤芯定期更换 • 机台上油:天车,机械摇摆 • 气压缸:主体清洁,空气管检查 • 药水分析补充更换 • 镍槽防析出装置检查 • 添加系统检查清洁 • 排气设备检查 • 挂架保养或更新 • 硝酸槽及管路管阀检查
• 谢谢
活化
• 主成份 硫酸钯 硫酸 • 作用 1、在铜面置换(离子化趋势Cu>Pd)上一层钯,以作为化
学镍反应之触媒
• 反应 • 阳极反应 Cu--Cu2+ + 2e-(E0 = -0.34V) • 阴极反应 Pd2+ +2e- → Pd(E0=0.98V) • 全反应 Cu + Pd2+ → Cu2+ + Pd
化学镍金工艺原理.

1.概述化学镍金又叫沉镍金,业界常称为无电镍金(Elestrolss Nickel ImnersionGold又称为沉镍浸金。
PCB化学镍金是指在裸铜表面上化学镀镍,然后化学浸金的一种可焊性表面涂覆工艺,它既有良好的接触导通性,具有良好的装配焊接性能,同时它还可以同其他表面涂覆工艺配合使用,随着日新日异的电子业的发展,化学镍金工艺所显现的作用越来越重要。
2.化学镍金工艺原理2.1 化学镍金催化原理2.1.1催化作为化学镍金的沉积,必须在催化状态下,才能发生选择性沉积,VⅢ族元素以及Au等多金属都可以为化学镍金的催化晶体,铜原子由于不具备化学镍金沉积的催化晶种的特性,所以通过置换反应可使铜面沉积所需要的催化晶种;PCB业界大都使用PdSO4或PdCl2作为化学镍前的活化剂,在活化制程中,化学镍反应如下:Pd2++Cu Cu2++Pd 2.2化学镍原理2.2.1 在Pd(或其他催化晶体的催化作用下,Ni2+被NaH2PO2还原沉积在将铜表面,当Ni沉积覆盖Pd催化晶体时,自催化反应继续进行,直到所需的Ni层厚度2.2.2化学反应在催化条件下,化学反应产生的Ni沉积的同时,不但随着氢析出,而且产生H 2的溢出主反应:Ni2++2H2PO2-+2H2O Ni+2HPO32-+4H++H2副反应:4H2PO2- 2HPO32-+2P+2H2O+H22.2.3 反应机理H2PO2-+H2O H++HPO32-+2HNi2++2H Ni+2H2 H2PO2-+H H2O+OH-+PH 2PO2-+H2O H++HPO32-+H22.2.4作用化学镍的厚度一般控制在3-5um,其作用同金手指电镍一样不但对铜面进行有效保护,防止铜的迁移,而且备一定硬度和耐磨性能,同时拥有良好的平整度,在镀镍浸金保护后,不但可以取代拔插频繁的金手指用途(如电脑的内存条,同时还可避免金手指附近的导电处斜边时所遗留裸铜切口2.3 浸金原理2.3.1浸金是指在活性镍表面,通过化学置换反应沉积薄金化应式:2Au(CH2-+Ni 2Au+Ni2++4CN-2.3.2 作用浸金的厚度一般控制在0.03-0.1um,其对镍面有良好的保护作用,而且具备很好的接触导通性能,很多需按键接触的电子器械(如手机、电子字典都采用化学浸金来保护镍面3.化学Ni/Au的工艺流程3.1 工艺流程简介作为化学镍金流程,只要具备6个工作站就可满足生产要求3-7分钟 1-2分钟 0.5-4.5分钟 2-6分钟除油微蚀活化预浸沉Au沉Ni20-30分钟 7-11分钟3.2 工艺控制3.2.1除油缸一般情况下,PCB沉镍金采用酸性除油剂处理制板,其作用在于除掉铜面的轻度油脂及氧化物,达到清洁及增加湿润效果的目的,它应当具备不伤SOiderMask(绿油以及低泡型易水洗的特点。
化镍金生产流程及工艺简介

化镍金生产流程及工艺简介目前PCB业界流行的表面处理制程有喷锡、抗氧化(OSP)、电镍金、化镍金、化银、化锡等几种。
化镍金(ENIG=electroless nickel and immersion gold)制程主要应用于笔记本电脑主板、各种电脑内存条、声卡、显卡、路由器、手机板、数码相机主板、各种存储块以及摄相机等高难度线路板的制造。
化镍金制程优点1、表面平坦;2、可焊接,可打线;3、可接触导通;4、可散热(高温不氧化);5、可耐多次回流焊。
几种PCB表面处理对比化镍金流程简介1、一般化镍金流程:水平前处理→上料→除油→水洗→水洗→微蚀→水洗→水洗→酸洗→纯水洗→纯水洗→预浸→活化→纯水洗→纯水洗→纯水洗→化学镍→纯水洗→纯水洗→化金→回收→纯水洗→纯水洗→下料→洗板→检板2、厚化金流程水平前处理→上料→除油→水洗→水洗→微蚀→水洗→水洗→酸洗→纯水洗→纯水洗→预浸→活化→纯水洗→纯水洗→纯水洗→化学镍→纯水洗→纯水洗→预浸金→厚化金→回收→纯水洗→纯水洗→下料→洗板→检板化镍金各工序原理及说明1、水平前处理通过水平前处理将铜面的过度氧化及污染,以机械法和化学法相结合的方法去除,协助清洁能力不太强的除油槽,使后续的沉镍金得以顺利进行。
常见的方法有微蚀+尼龙磨刷,微蚀+喷砂,纯微蚀水平前处理等等。
2、除油去除铜面轻微氧化及污染,降低槽液的表面张力,使药水在对象表面扩张,达到浸润的效果。
除油剂一般为有机酸型,容易滋生霉菌,保养时要注意槽壁的清洗。
由于含有界面活性剂,因此其后的第一道水洗不开打气或轻微开打气,槽液本身更无需空气搅拌,防止气泡过多不易清洗。
除油槽液要求充分的循环过滤,避免出现浑浊现象。
CuO +2 H+ →Cu2++ H2O3、微蚀去除铜面氧化,使铜表面微粗化,并化学镍层保持良好的结合力。
NaS2O8 + H2O → Na2SO4 + H2SO5H2SO5 + H2O → H2S O4 + H2O2H2O2 + Cu → CuO + H2OCuO + H2SO4 → CuSO4 + H2O为了保持比较稳定的微蚀速率,溶液中的铜离子一般要求控制在3-20g/l,因此在配新槽时需要保留1/5-1/3的母液,或添加适量的硫酸铜。
化学镍金工艺探讨

∙化学镍金工艺探讨∙化学镍金镀层集可焊接、可接触导通,可打线、可散热等功能于一身,是PCB板面单一处理却具有多用途的湿制程。
目前尚无其它的工艺可与之抗衡。
但该制程不好做已时日已久,问题常常出现且不易重工,问题的解决须从源头开始。
对此,本人将工作过程中遇到的品质问题同业界前辈探讨一下。
首先从化学镍金的反应机理入手。
一、化镍镍盐:以硫酸镍为主,也有氯化镍、乙酸镍还原剂:次磷酸二氢钠,NaH2PO2反应机理:说明:①次磷酸二氢钠的次磷酸根离子水解并氧化成磷酸根,同时放出两个活性氢原子吸附在铜底钯面上。
②镍离子在活化钯面上迅速还原镀出镍金属。
③小部分次磷酸根在催化氢的刺激下,产生磷原子并沉积在镍层中。
④部分次磷酸根在催化环境下,自己也会氧化并生成氢气从镍面上向外冒出。
∙二、化金当PCB板面镀好镍层放入金槽后,其镍面即受到槽液的攻击而溶出镍离子,所抛出的两个电子被金氰离子获得而在镍面上沉积出金层。
反应机理:Ni→Ni2+2eAu(CN)2-+e→Au+2CN-由此可知,一个镍原子溶解可获得两个金原子的沉积,又因金层上有许多疏瓦,故表面虽已盖满了金层,但仍可让疏孔的镍面溶解而继续镀出金层,只是速度越来越慢而已。
其次,化学镍金各流程的管控。
一、前处理。
1.刷磨:使用高目数的尼龙刷(1000-1200目)对板面进行轻刷(刷磨电流2.0±0.2A)除去访垢和氧化物.在刷磨后接板时必须戴干净的手套避免接触成型线内的待镀区,以免后续做板出来后板面上有花斑。
2.去脂:去徐油脂及有机物,只能采用非离子型遥介面活性剂,仅具润湿效果而已,不能用太强的板子型活性剂,以防止防焊漆表面或基材上带有静电而上镍或损伤水性碱液显影的防焊漆而溶出碳份污染槽液。
3.微蚀:通常只咬铜30-40µm即可,如果发现有星点露铜现名象,很可能为湿膜制程之显影不洁或显影后水洗不净造成。
此时可适当延长微蚀时间以便除之。
4.酸洗:去除微蚀生成的铜盐。
化学镍金常见缺陷分析汇总

化学镍金常见缺陷分析:1漏镀1.1.1 主要原因:体系活性(镍缸及钯缸)相对不足,铅锡等铜面污染。
1.1.2问题分析:漏镀的原因在于镍缸活性不满足该Pad位反应势能,导致沉镍化学反应中途停止,或者根本没有沉积金属镍漏镀的特点是:如果一个Pad位漏镀与其相连的所有Pad位都漏镀;出现漏镀问题,首先须区分是否由于污染板面所致。
若是,将该板进行水平微蚀或采用磨板方式除去污染。
影响体系活性的最主要原因是镍缸稳定剂的浓度,但由于难以操作控制,一般不采用降低稳定剂浓度解决该问题。
影响体系活性的主要原因镍缸温度,升高温度一定有利于漏镀的改善。
如果不考虑对部分环境以及内部稳定性,无限度的升高镍缸温度,应该能解决漏镀问题。
影响体系活性的次要因素是活化浓度,温度和时间。
延长活化的时间或提高活化浓度和温度,一定有利于漏镀的改善。
由于活化的温度和浓度太高会影响钯缸的稳定性,而且会影响其他制板的生产,所以,在这些次要因素中,延长时间是首选改善措施。
镍缸的PH值、次磷酸钠以及镍缸负载都会影响镍缸活性,但其影响程度较小,而且过程缓慢,所以不宜作为解决漏镀的主要方法。
1.2 渗镀1.2.1 主要原因体系活性太高,外界污染或前工序残渣;1.2.2问题分析渗镀的主要成因在于镍缸活性过高,导致选择性太差,不但使铜面发生化学沉积,同时其他区域(如基材、绿油侧边等)也发生化学沉积,造成不该出现沉积的地方沉积化学镍金。
出现渗镀问题,首先须区分是否由外界污染或残渣(如铜、绿油等)所致。
若是,将该板进行水平微蚀或其他的方法去除。
升高稳定剂浓度是改善体系活性太高的最直接的方法,但是,用漏镀问题改善一样,因难以操作控制而不宜采用。
降低镍缸温度是改善渗镀的最有效的方法,理论上无限度的降低温度,可以彻底解决渗镀问题。
降低钯缸温度和浓度,以及减少钯缸处理时间,可以降低体系活性,有效地改善渗镀的问题。
镍缸的PH值,次磷酸钠以及镍缸负载,降低其控制范围有利于渗镀的改善,但因其影响较小而且过程缓慢,不宜作为改善渗镀问题的主要方法。
表面处理之化学镍金制程讲解.

程
控制范围 80-120ml/L 清洁无杂质 清洁无杂质 80-120g/L 2-5% 清洁无杂质 8-12% 清洁无杂质 80-120ml/L 建浴用
控 制------操作及控制参数表
温度 35±5℃ 室温 45±5℃ 27±2℃ 室温 室温 室温 室温 时间 1-3min 60-90sec 60sec 1-2min 30-60sec 30-60sec 30-60sec 30-60sec 添加溢流表 20ml/m2 8L/min 不需 30g/m2 5L/min 20ml/m2 5L/min 20ml/m2 更槽频率 Cu2+>7g/L 一次/日 一次/班 Cu2+>15g/L 一次/日 一次/3日 一次/日 一次/日 分析频率 一次/班 不需 不需 一次/班 不需 一次/日 不需 一次/日 机器动作 振动 空气搅拌 不需 空气搅拌 空气搅拌 不需 空气搅拌 不障名称 可能原因分析 1.Ni2+含量太低. 2.NaH2PO2太低. 3.PH值太低. 4.温度太低. 5.循环不够. 1.脱脂时间不够. 2.水洗不良. 3.前处理不够. 4.反应过剧(镍缸). 5空气.搅拌中有杂质. 解决方法 1.分析调整. 2.分析调整20-25g/L. 3.分析调整4.6-5.2. 4.温度升至81±3℃. 5.检查阀门、管道、过滤机. 1.加长脱脂时间200-300秒内. 2.加长水洗时间,保持清洁. 3.加强前处理磨刷次数. 4.降低镍缸活性. 5.每周清洁空气滤芯. 1.分析调整到50±5ppm. 2.分析调整到100±20ml/L. 3.显示温度与实际温度相符 (25±3℃). 4.检查时间并相应延长. 5.水洗时间不可太长,相应调整. 6.提升镍槽活性. 预防措施 1.检查自动添加机管道,各藥水是否添加正 常,并要求化验校正,操作员必须每小时巡 查1次自动添加机. 2.温度显示值与实际值必须相等. 3.检查循环装置是否有堵塞现象. 1.检查更换频率及添加量. 2.按照要求更换并保持溢流. 3.有来料之污染程度进行调节. 4.调整药水时注意做到少量多次添加. 5.保持滤芯及管道之清洁度. 1.按照生产面积定时定量添加. 2.化验后稀释,检查预浸滴水时间. 3.每日测量并校正,标准25-28℃为佳. 4.发现此类问题时,活化时间可延长到34min. 5.保持水洗清洁度,以免Pd后钝化. 6.镍沉积速率保持在6-8u″为佳. 1.加强进料检验及点检各槽是否在管控范围. 2.以磨刷速度和压力进行调节. 3.在未作业时间加以循环过滤,温度在70℃ 以下. 4.从前处理着手,检验铜面光亮无点状粗糙 为佳. 5.按照生产面积定时定量添加,并要求化验 准确. 沉积速率 太低
化学镍金工艺原理.

1.概述化学镍金又叫沉镍金,业界常称为无电镍金(Elestrolss Nickel Imnersion Gold又称为沉镍浸金。
PCB化学镍金是指在裸铜表面上化学镀镍,然后化学浸金的一种可焊性表面涂覆工艺,它既有良好的接触导通性,具有良好的装配焊接性能,同时它还可以同其他表面涂覆工艺配合使用,随着日新日异的电子业的发展,化学镍金工艺所显现的作用越来越重要。
2.化学镍金工艺原理2.1 化学镍金催化原理2.1.1催化作为化学镍金的沉积,必须在催化状态下,才能发生选择性沉积,VⅢ族元素以及Au等多金属都可以为化学镍金的催化晶体,铜原子由于不具备化学镍金沉积的催化晶种的特性,所以通过置换反应可使铜面沉积所需要的催化晶种;PCB业界大都使用PdSO4或PdCl2作为化学镍前的活化剂,在活化制程中,化学镍反应如下:Pd2++Cu Cu2++Pd 2.2化学镍原理2.2.1 在Pd(或其他催化晶体的催化作用下,Ni2+被NaH2PO2还原沉积在将铜表面,当Ni沉积覆盖Pd催化晶体时,自催化反应继续进行,直到所需的Ni层厚度2.2.2化学反应在催化条件下,化学反应产生的Ni沉积的同时,不但随着氢析出,而且产生H 2的溢出主反应:Ni2++2H2PO2-+2H2O Ni+2HPO32-+4H++H2副反应:4H2PO2- 2HPO32-+2P+2H2O+H22.2.3 反应机理H2PO2-+H2O H++HPO32-+2HNi2++2H Ni+2H2 H2PO2-+H H2O+OH-+PH 2PO2-+H2O H++HPO32-+H22.2.4作用化学镍的厚度一般控制在3-5um,其作用同金手指电镍一样不但对铜面进行有效保护,防止铜的迁移,而且备一定硬度和耐磨性能,同时拥有良好的平整度,在镀镍浸金保护后,不但可以取代拔插频繁的金手指用途(如电脑的内存条,同时还可避免金手指附近的导电处斜边时所遗留裸铜切口2.3 浸金原理2.3.1浸金是指在活性镍表面,通过化学置换反应沉积薄金化应式:2Au(CH2-+Ni 2Au+Ni2++4CN-2.3.2 作用浸金的厚度一般控制在0.03-0.1um,其对镍面有良好的保护作用,而且具备很好的接触导通性能,很多需按键接触的电子器械(如手机、电子字典都采用化学浸金来保护镍面3.化学Ni/Au的工艺流程3.1 工艺流程简介作为化学镍金流程,只要具备6个工作站就可满足生产要求3-7分钟 1-2分钟 0.5-4.5分钟 2-6分钟除油微蚀活化预浸沉Au沉Ni20-30分钟 7-11分钟3.2 工艺控制3.2.1除油缸一般情况下,PCB沉镍金采用酸性除油剂处理制板,其作用在于除掉铜面的轻度油脂及氧化物,达到清洁及增加湿润效果的目的,它应当具备不伤SOiderMask(绿油以及低泡型易水洗的特点。
化学镍金制程分析
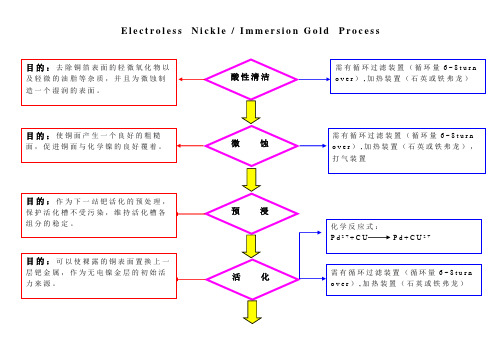
E l e c t r o l e s s N i c k l e/I m m e r s i o n G o l d P r o c e s s■化学镀镍/金可焊性控制1金层厚度对可焊性和腐蚀的影响在化学镀镍/金上,不管是施行锡膏熔焊或随后的波峰焊,由于金层很薄,在高温接触的一瞬间,金迅速与锡形成“界面合金共化物”(如A u S n、A u S n2、A u S n3等)而熔入锡中。
故所形成的焊点,实际上是着落在镍表面上,并形成良好的N i-S n合金共化物N i3S n4,而表现固着强度。
换言之,焊接是发生在镍面上,金层只是为了保护镍面,防止其钝化(氧化)。
因此,若金层太厚,会使进入焊锡的金量增多,一旦超过3%,焊点将变脆性反而降低其粘接强度μμμm时,镍层里发生强烈的不可控制的腐蚀。
2镍层中磷含量的影响化学镀镍层的品质决定于磷含量的大小。
磷含量较高时,可焊性好,同时其抗蚀性也好,一般可控制在7~9%。
当镍面镀金后,因N i-A u层A u层薄、疏松、孔隙多,在潮湿的空气中,N i为负极,A u为正极,由于电子迁移产生化学电池式腐蚀,又称焦凡尼式腐蚀,造成镍面氧化生锈。
严重时,还会在第二次波峰焊之后发生潜伏在内的黑色镍锈,导致可焊性劣化与焊点强度不足。
原因是A u面上的助焊剂或酸类物质通过孔隙渗入镍层。
如果此时镍层中磷含量适当(最佳7%),情况会改善。
3镍槽液老化的影响镍槽反应副产物磷酸钠(根)造成槽液“老化”,污染溶液。
镍层中磷含量也随之升高。
老化的槽液中,阻焊膜渗出的有机物量增高,沉积速度减慢,镀层可焊性变坏。
这就需要更换槽液,一般在金属追加量达4~5M T O时,应更换。
4P H值的影响过高的P H,使镀层中磷含量下降,镀层抗蚀性不良,焊接性变坏。
对于安美特公司之A u r o t e c h(酸性)镀镍/金体系,一般要求P H不超过 5.3,必要时可通过稀硫酸降低P H。
5稳定剂的影响稳定剂可阻止在阻焊C u焊垫之间的基材上析出镍。
化镍浸金制程

槽等使用强氧化剂的槽位,实务 上常暂时以手动加减震荡的方式 来厘清是否为震荡不足才造成的 种种问题。
6.2、金机红斑或变色 从热力学的角度来看金氧 化的自由能为正值(△ G>0),理 论上金面氧化反应属于非自发反 应,但实务上仍不时惊传有金面 氧化异色的特例发生,经实际了 解下才发现大都是金面沾附的异 物发生了变色或氧化,为了防止 此一问题发生,浸金槽的作业条 件与管控、化镍金后水洗的质量 与如何降低化镍金成品表面污染 的风险管理变的相当重要。如下
115
图 6 此二图分别为白雾区域(左图)与正常区域(右图)经剥金后以 SEM 1500x 拍摄之镍面,明显看出白 雾区域耐蚀性较差,薄金置换后腐蚀的情性严重,一般也常伴随白雾区域之金厚度较厚的现像。
本解决之道是在有机材料的选择 与其曝光聚合的条件上多下苦 功。
样具备这些功能的电镍金 (Electroplating Nickel and
G o l d ),E N I G 则有以下特徵: a. 无须通电,不需拉导线至每一 待镀 P a d ,不会因电流分布 (Current distribution)造成镀
二、 流程系列 Flow System(流程图 A)
表1 一般化镍浸金板之品检项目
a. 去除铜面氧化层。 b. 减少 S/M 前处理刷磨造 成的沟痕深度。 (过深的刷痕常成为浸金攻 击镍层的帮凶) 3.4、酸洗 Acid dip 浸泡 3~5%(v/v)的稀硫 酸以去除蚀后的铜面氧化物。 3.5、预浸 Pre-dip 本槽的稀酸浓度与活化槽 相同,浸泡之后不经水洗直接进 入活化槽,以维持活化槽中的酸 度,并使铜面在新鲜状态(无氧 化物)下,进入活化槽。 3.6、活化 Activation 3.6.1 功能:由于铜面无法 直接动化学镍的沈积反应,所以 必须在铜面置换上一层钯(Pd), 以作为化学镍反应之触媒(做为 促使次磷酸根氧化的氧化剂)。利 用 Cu>Pd 的离子化趋势,Cu 溶解 后放出的电子使钯离子还原为金 属态。
化学镍金流程及注意
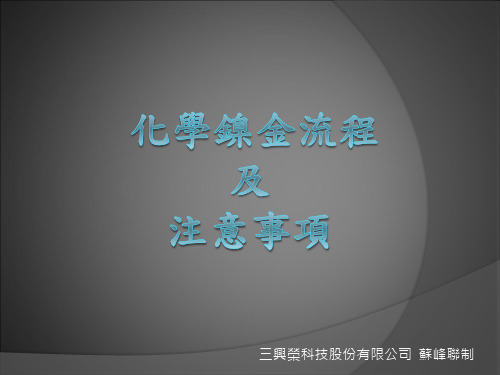
操作條件:濃度Pd 20ppm 範圍10~30ppm/L 時間1~2min 溫度25±5º C 注意事項:1.溫度對鈀附著影響甚大低於15℃時,易造 成鈀附著不足,形成無鍍層現象;高於 35℃時,鈀的附著量過多,易造成bridge ,並使無電解鎳浴的安定性變差。 2.在溫度固定下如藥液管控超出範圍之外, 就會産生酸度高,鈀濃度低,會造成SKIP (無電解鎳無法析出);相反的,酸濃度 低,鈀濃度高會造BRIDGE (擴散架橋)。
FPF-MC 建浴用(含錯化劑、還原劑、促進劑)。 FPF-1C 建浴補充用(每1L含100g鎳鹽)。 FPF-2CL 補充用(含還原劑、促進劑、安定劑、濕 潤劑)。 FPF-3C補充用(含PH調整劑)。 FPF-5建浴用,界面活性调整剂
錯 化 劑:防止PH迅速下降的緩衝劑,避免鎳離子與 亞磷酸根離子生成沈澱。 還 原 劑:Na(H2PO2)(磷的供應源)。
溫度較高
提升沈積速率 加快槽壁上鍍
溫度較低
降低沈積速率 無反應
易鎳厚不足 無鍍層
以上各項參數需控制于範圍內,其鎳:磷含量 最好控制于1:4~5,面積爲0.2dm2~0.8 dm2最爲
適當。
注意事項:1. FPF-3C主要爲調整PH值,若直接加入易 生成Ni(OH)2 之沈澱造成不良的産生,所 以需將其稀釋2倍後在攪拌處,徐徐加入 2.降低PH值可用H2SO4。 3.放入面積0.5dm2之裸銅板進行起鍍(dummy) 新建浴時間需1hr, 後起鍍30min即可。 4.須有陰極析出防止裝置,其控制電壓爲 1~2V,電流密度應在0.2~0.5A
參數變化的影響之性質:
補
充: (標準-分析)*槽體積/68.3 1.每添加100g K Au(CN)2時,約補充 1000ml GOLD—AD。 2. PH 下降時,可用試藥特級NH4OH調升 (添加時以純水稀釋1:1),調降時以試 藥特級的檸檬酸20%溶液調整。 注意事項:1.AD添加達3MTO 及鎳離子達800~1000PPM 時,應重新建浴。 2.因以高溫作業,其藥水蒸發量較大,需補 充純水。
化学镍金的工艺

化学镍金的工艺化学镍金的工艺Tags: 化学镍金,印制电路板, 积分Counts:907 次本文在简单介绍印制板化学镀镍金工艺原理的基础上,对化学镍金之工艺流程、化学镍金之工艺控制、化学镍金之可焊性控制及工序常见问题分析进行了较为详细的论述。
在一个印制电路板的制造工艺流程中,产品最终之表面可焊性处理,对最终产品的装配和使用起着至关重要的作用。
综观当今国内外,针对印制电路板最终表面可焊性涂覆表面处理的方式,主要包括以下几种:Electroless Nickel and Immersion Gold形电镀铜的常见缺陷及故障排除。
1.前言由于行业竞争的激烈,印制板的制造商不断降低成本提高产品质量,追求零缺陷,以质优价廉取胜。
而客户对印制板的要求也没有单纯停留在对产品性能的可靠性上,同时对产品的外观也提出了更严格的要求。
而图形电镀铜作为化学沉铜的加厚层或其它涂覆层的底层,其质量与成品的关系可谓休戚相关“一荣俱荣,一损俱损”。
所以图形电镀铜上的任何缺陷如镀层粗糙、麻点针孔、凹坑、手印等的存在,严重影响成品的外观,透过涂覆其上的阻碍或铅锡镀层或是镍金层,都能清楚的显露出来。
本文主要叙述图形电镀铜常见的系列故障及缺陷,并针对这些缺陷进行跟踪调查、模拟实验,找出产生缺陷的成因,制定切实的纠正措施,保证生产的正常进行。
2.缺陷特点及成因2.1 镀层麻点图形电镀铜上出现麻点,在板中间较为突出,退完铅锡后铜面不平整,外观欠佳。
刷板清洁处理后表面麻点仍然存在,但已基本磨平不如退完锡后明显。
此现象出现后首先想到电镀铜溶液问题,因为出现故障的前一天(4月2日)刚对溶液进行活性炭处理,步骤如下:1)在搅拌条下件下加入2升H2O22)充分搅拌后将溶液转至一个备用槽中,加入4kg活性碳细粉,并加入空气搅拌2小时,之后关闭搅拌,让溶液沉降。
从调查中发现,生产线考虑到次日有快板,当晚将溶液从备用槽中转回工作槽。
未经过充分过滤沉降活性炭,而转移溶液时未经循环过滤泵(慢)直接从工作槽的输出管理返回(管道粗,快)。
表面处理之化学镍金制程讲解
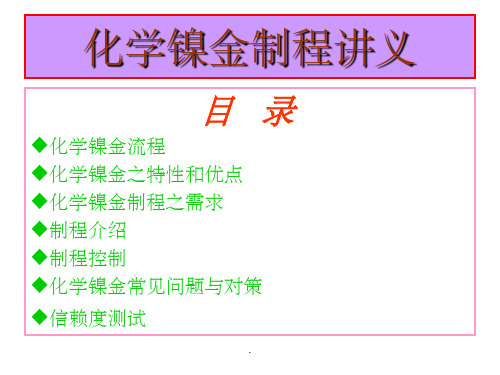
8L/min
30-60sec
20ml/m2
30-60sec
8L/min 以UPC-M(10%)
控制速率为69u″/min
1L/5m2 1L/5m2 0.8L/5m2
按要求厚度而 定
100g金盐 /100m2
30-60sec 30-60sec
60sec
.
8L/min 5L/min 不需
一次/日 一次/3日 一次/日 UPC-1(5%)配制
控 制------操作及控制参数表
温度 35±5℃
室温 45±5℃ 27±2℃
室温 室温 室温 室温
27±2℃ 室温 室温 室温
81±3℃
87±5℃ 室温 室温
45±5℃
时间 1-3min 60-90sec 60sec
1-2min
30-60sec 30-60sec 30-60sec 30-60sec
.
制 程 控 制------配槽用量
槽名
项目
配槽浓度
添加次序
备注
除油
DI.H2O
1
2
DI.H2O
80%
1
微蚀
SPS
பைடு நூலகம்
100g/L
2
AR.H2SO4
2-3%
3
酸洗
DI.H2O
90%
1
AR.H2SO4
10%
2
预浸
DI.H2O
1
2
活化
DI.H2O
1
2
DI.H2O
1
化镍槽
2
3
DI.H2O
1
化金槽
2
KAu(CN)2
不需 不需 不需
016化学镍金作业指导书解析

莆田市佳宜电子文件编号JY-WI-016作业指导书版本 2.0标题: 化学镍金操作指引页码1/11一、目的:标准操作,维护品质.二、适用范围:适用于生产各种需要沉镍金的产品三、设备、工具及物料化学镍金线、清洗机、铁氟龙线.珠粒、周转盆、水盆、产品、化学镍金系列药水、手指套四、作业环境:温度:室温。
地面要求:无积水、无杂物空气要求:空气流通良好,无刺激性气味五、职责:工程部负责标准制作,生产部负责按标准要求操作,品管部负责监控。
六、内容6.1.工艺流程刷板→检查→预备工作→穿板→酸洗→双水洗→微蚀→双水洗→预浸→活化→双水洗→后浸→水洗→化镍→双水洗→化金→金回收→水洗→热水洗→卸板→放入水盆→烘干检查→生产完后关机6.2 刷板:刷轮 800#,1000#,每天进展刷幅测试,刷幅要求 0.8-1.2CM.6.3检查:全检铜刷板,板面无压坑,皱折,胶点,油污,手指印的合格,否则为不合格。
合格板才能进入沉金,不合格退回上工序或处理成为合格板。
6.4预备工作:1、设备点检〔具体见点检表〕2、更换每个药水缸后的第一道水洗,并将水加满3、补加各药缸液位,翻开加热器及过滤泵,通知化验室对药水进展分析且准时补加4、检查各药缸温度是否在工艺范围内.6.5穿板:穿板时必需将手指全部戴上手指套,穿板张数一挂不超过20PNL,且必需用珠粒隔开6.6检查:检查是否穿好。
制定日期核准日期6.7酸洗:除去板面氧化。
A.工艺参数操作条件范围推举值硫酸4-6%5%温度28-32℃30℃时间1-3min 2min分析频率 1 次/2 天B.配制 150 升槽液的程序:①开缸体积150L 开缸浓度:硫酸5%。
②清洗干净缸体,缸体内不能有任何灰尘杂物。
③向槽里参加 1/2 缸体的去离子水。
④参加 7.5L 硫酸。
⑤用去离子水补充到操作体积并开启过滤泵混匀。
⑥加热至要求值,分析补加。
C.酸洗缸保养:①每生产100±10m2补加一次,每次补加 0.5L 硫酸。
化学镍金工艺探讨
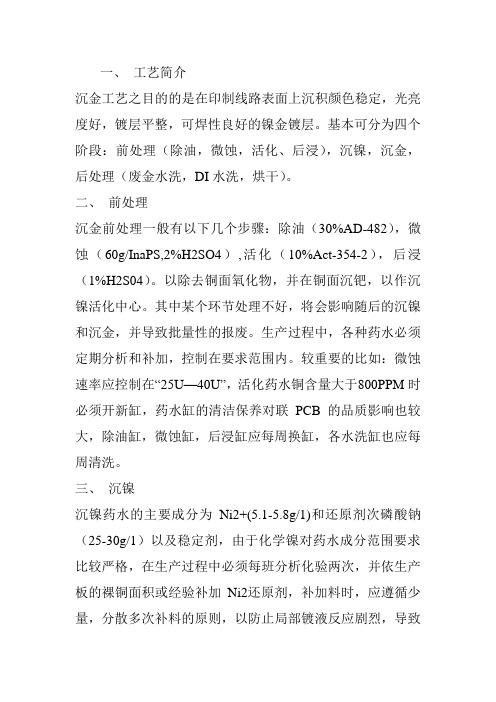
一、工艺简介沉金工艺之目的的是在印制线路表面上沉积颜色稳定,光亮度好,镀层平整,可焊性良好的镍金镀层。
基本可分为四个阶段:前处理(除油,微蚀,活化、后浸),沉镍,沉金,后处理(废金水洗,DI水洗,烘干)。
二、前处理沉金前处理一般有以下几个步骤:除油(30%AD-482),微蚀(60g/InaPS,2%H2SO4),活化(10%Act-354-2),后浸(1%H2S04)。
以除去铜面氧化物,并在铜面沉钯,以作沉镍活化中心。
其中某个环节处理不好,将会影响随后的沉镍和沉金,并导致批量性的报废。
生产过程中,各种药水必须定期分析和补加,控制在要求范围内。
较重要的比如:微蚀速率应控制在“25U—40U”,活化药水铜含量大于800PPM时必须开新缸,药水缸的清洁保养对联PCB的品质影响也较大,除油缸,微蚀缸,后浸缸应每周换缸,各水洗缸也应每周清洗。
三、沉镍沉镍药水的主要成分为Ni2+(5.1-5.8g/1)和还原剂次磷酸钠(25-30g/1)以及稳定剂,由于化学镍对药水成分范围要求比较严格,在生产过程中必须每班分析化验两次,并依生产板的裸铜面积或经验补加Ni2还原剂,补加料时,应遵循少量,分散多次补料的原则,以防止局部镀液反应剧烈,导致镀液加速老化,PH值,镀液温度对镍厚影响比较大,镍药水温度抄袭控制在85℃-90℃。
PH在5.3-5.7,镍缸不生产时,应将镍缸温度降低至70℃左右,以减缓镀液老化,化学镍镀液对杂质比较敏感,很多化学成分对化学镍有害,可分为以下几类:抑制剂:包括Pb.Sn..Hg.Ti.Bi(低熔点的重金属),有机杂质包括S2,硝酸及阴离子润湿剂。
所有这些物质都会降低活性,导致化学镀速度降低并漏镀,严惩时,会导致化学镀镍工艺完全停止。
有机杂质:包括:除以上所提到的有机的稳定剂以外,还有塑料剂以及来自于设备和焊锡的杂质。
尽管可通过连续镀清除一部分杂质,但不能完全清除。
不稳定剂:包括Pd和少量的铜,这两种成分造在化学镍不稳定,使镀层粗糙,而且过多地镀在槽壁及加热器上。
- 1、下载文档前请自行甄别文档内容的完整性,平台不提供额外的编辑、内容补充、找答案等附加服务。
- 2、"仅部分预览"的文档,不可在线预览部分如存在完整性等问题,可反馈申请退款(可完整预览的文档不适用该条件!)。
- 3、如文档侵犯您的权益,请联系客服反馈,我们会尽快为您处理(人工客服工作时间:9:00-18:30)。
E l e c t r o l e s s N i c k l e/I m m e r s i o n G o l d P r o c e s s
■化学镀镍/金可焊性控制
1金层厚度对可焊性和腐蚀的影响
在化学镀镍/金上,不管是施行锡膏熔焊或随后的波峰焊,由于金层很薄,在高温接触的一瞬间,金迅速与锡形成“界面合金共化物”(如A u S n、A u S n2、A u S n3等)而熔入锡中。
故所形成的焊点,实际上是着落在镍表面上,
并形成良好的N i-S n合金共化物N i3S n4,而表现固着强度。
换言之,焊接是发生在镍面上,金层只是为了保护镍面,防止其钝化(氧化)。
因此,若金层太厚,会使进入焊锡的金量增多,一旦超过3%,焊点将变脆性反而降低其粘接强度。
据资料报导,当浸镀金层厚度达0.1μm时,没有或很少有选择性腐蚀;金层厚度达0.2μm时,镍层发生腐蚀;当金层厚度超过0.3μm时,镍层里发生强烈的不可控制的腐蚀。
2镍层中磷含量的影响
化学镀镍层的品质决定于磷含量的大小。
磷含量较高时,可焊性好,同时其抗蚀性也好,一般可控制在7~9%。
当镍面镀金后,因N i-A u层A u层薄、疏松、孔隙多,在潮湿的空气中,N i为负极,A u为正极,由于电子迁移产生化
学电池式腐蚀,又称焦凡尼式腐蚀,造成镍面氧化生锈。
严重时,还会在第二次波峰焊之后发生潜伏在内的黑色镍锈,导致可焊性劣化与焊点强度不足。
原因是A u面上的助焊剂或酸类物质通过孔隙渗入镍层。
如果此时镍层中磷含量适当(最佳7%),情况会改善。
3镍槽液老化的影响
镍槽反应副产物磷酸钠(根)造成槽液“老化”,污染溶液。
镍层中磷含量也随之升高。
老化的槽液中,阻焊膜渗出的有机物量增高,沉积速度减慢,镀层可焊性变坏。
这就需要更换槽液,一般在金属追加量达4~5M T O时,应更
换。
4P H值的影响
过高的P H,使镀层中磷含量下降,镀层抗蚀性不良,焊接性变坏。
对于安美特公司之A u r o t e c h(酸性)镀
镍/金体系,一般要求P H不超过 5.3,必要时可通过稀硫酸降低P H。
5稳定剂的影响
稳定剂可阻止在阻焊C u焊垫之间的基材上析出镍。
但必须注意,太多时不但减低镍的沉积速度,还会危害到镍面的可焊性。
6不适当加工工艺的影响
为了减少N i/A u所受污染,烘烤型字符印刷应安排在N i/A u工艺之前。
光固型字符油墨不宜稀释,并且也应安排在N i/A u工艺之前进行。
做好N i/A u之后,不宜返工,也不宜进行任何酸洗,因为这些做法都会使镍层埋伏下氧化的危险,危及可焊性和焊点强度。
7两次焊接的影响
对低档卡板只做一次焊接,一般不会有问题。
但如笔记型电脑的主板、手机或P C等高档板,一般需两次焊接。
第一次焊接后,助焊剂残余会浸蚀镍层。
第二次焊接的高温会促使氧化甚至变黑,其固有强度变坏,无法通过振动试验。
遇到这种情况,只能从槽液管理上入手进行改进,使镀镍层具有更好的抗蚀性能。
6化学镀镍/金与其它表面镍金工艺
化学镀镍/金除了通常所指之化学镀薄金外,应打金线等需求,又派生出化学厚金工艺;出于耐磨导电等性能要求,也派生出化学镀镍金后的电镀厚金工艺;针对H D I板B G A位拉力要求,也派生出选择性沉金工艺。
■化学厚金工艺
1)工艺流程
除油®水洗®微蚀®水洗®预浸®活化®水洗®沉镍®水洗®化学薄金®回收®水洗®化学厚金®回收®水洗®干板
2)化学厚金之特点
化学厚金是指在还原条件下,金离子被还原为金单质(还原剂同化学镀薄金),均匀沉积在化学薄金上面,在自催化作用下,达到所需要的厚度。
一般情况下,印制板化学厚金的金厚控制在20μi n左右。
某些情况下,也有超过30μi n金厚的。
3)工艺控制
化学厚金最重要的是成本问题,所以,反应速度的控制尤为重要。
络合剂、还原剂、稳定剂以及温度,是影响反应速度的重要因素。
■沉金金手指电镀工艺
1)工艺流程
阻焊膜®沉镍金®干板®包胶纸®电镀金®去胶纸
其中,电镀金为如下工艺流程:
酸洗®水洗®刷磨®水洗®活化®水洗®镀金®回收®水洗®干板
2)沉金金手指电镀的特点
沉金金手指这种类型的板,在制作过程中,先将整板的露铜部分,包括金手指部分进行化学镀镍金。
然后,单独将金手指按客户要求之厚度进行电镀金。
这种工艺流程简单,性能可靠,既能满足客户元件粘贴要求,又能满足插接性能。
3)工艺控制
包蓝胶纸时,一定要防止药水渗漏,避免金药水污染。
此外,电镀厚金前,一定要将被镀表面磨刷干净,否则会引起分层。
刷磨时,不可吝啬沉金层的浪费,刷磨效果越好,电镀金层的结合力越牢固。
■选择性沉金工艺
1)工艺流程
阻焊膜®干菲林®曝光®显影®干板®沉镍金®褪菲林®干板®有机保焊涂敷
2)选择性沉金的特点
选择性沉金既具有元件粘贴平整的特点,又具有良好的装配焊接性能。
同时,针对H D I板B G A位等小型P a d位采用有机保焊涂覆(如C u106),避免因P a d位太小而造成镍金拉力不足的缺点。
而且,选择性沉金的成本低于整板沉金,是一种很有发展潜力的工艺。
3)工艺控制
干菲林是专用于沉镍金的类型,它不但应具有耐高温药液能力,且须具备良好的掩孔能力。
由于沉镍金疏孔的局限性,其表面对微蚀药水非常敏感,极易造成镍层腐蚀。
所以,在有机保焊涂覆制程中,微蚀率应在保证铜面清洁的前提下,控制的越低越好。
能够采用贴红胶纸的制板,最好能象喷锡板那样,贴红胶纸加以保护。