挤出成型工艺确认表
挤出成型操作人员资格确认表
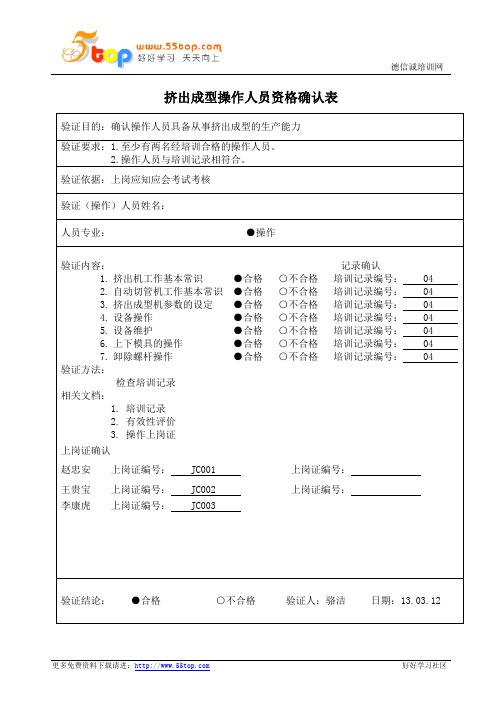
王贵宝上岗证编号:JC002上岗证编号:
李康虎上岗证编号:JC003
验证结论:●合格○不合格验证人:骆洁日期:13.03.12
审核结论:●合格○不合格审核人:陈宝荣日期:13.03.13
3.挤出成型机参数的设定●合格○不合格培训记录编号:04
4.设备操作●合格○不合格培训记录编号:04
5.设备维护●合格○不合格培训记录编号:04
6.上下模具的操作●合格○不合格培训记录编号:04
7.卸除螺杆操作●合格○不合格培训记录编号:04
验证方法:
检查培训记录
相关文档:
1.培训记录
2.有效性评价
挤出成型操作人员资格确认表
验证目的:确认操作人员具备从事挤出成型的生产能力
验证要求:1.至少有两名经培训合格的操作人员。
2.操作人员与培训记录相符合。
验证依据:上岗应知应会考试考核
验证(操作)人员姓名:
人员专业:●操作
验证内容:记录确认
1.挤出机工作基本常识●合格○不合格培训记录编号:04
2.自动切管机工作基本常识●合格○不合格培训记录编号:04
挤出成型工艺确认表
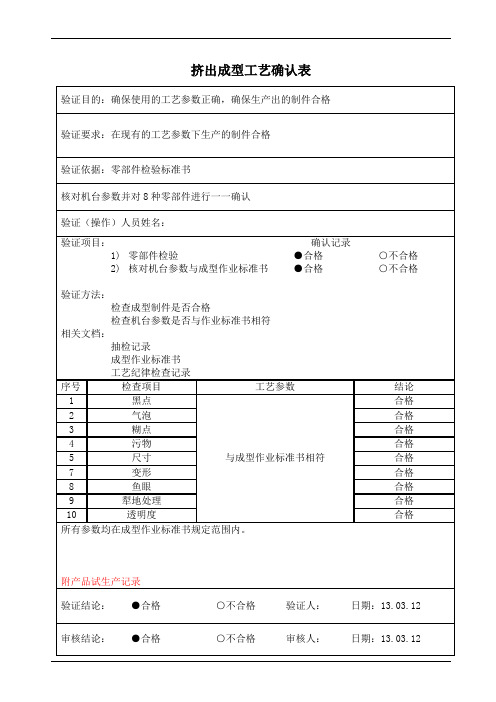
检查成型制件是否合格
检查机台参数是否与作业标准书相符
相关文档:
抽检记录
成型作业标准书
工艺纪律检查记录
序号
检查项目
工艺参数
结论
1
黑点
与成型作业标准书相符
合格
2
气泡
合格
3
糊点
合格
4
污物合格5ຫໍສະໝຸດ 尺寸合格7
变形
合格
8
鱼眼
合格
9
犁地处理
合格
10
透明度
合格
所有参数均在成型作业标准书规定范围内。
附产品试生产记录
验证结论:●合格○不合格验证人:日期:13.03.12
挤出成型工艺确认表
验证目的:确保使用的工艺参数正确,确保生产出的制件合格
验证要求:在现有的工艺参数下生产的制件合格
验证依据:零部件检验标准书
核对机台参数并对8种零部件进行一一确认
验证(操作)人员姓名:
验证项目:确认记录
1)零部件检验●合格○不合格
2)核对机台参数与成型作业标准书●合格○不合格
验证方法:
挤出模具安装试运行确认表
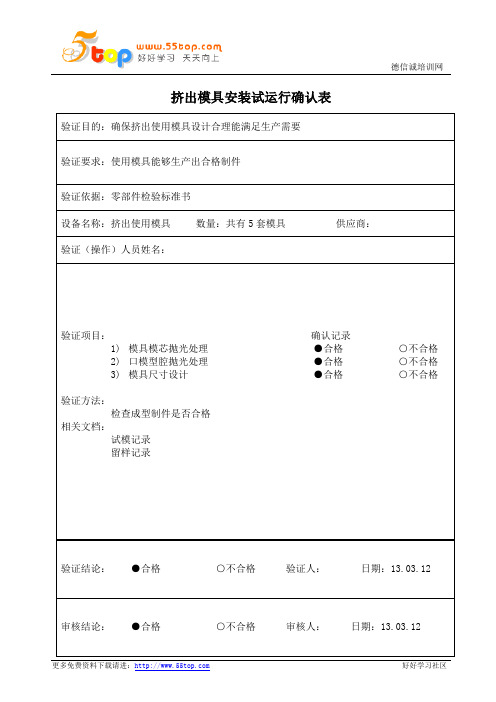
验证目的:确挤出使用模具设计合理能满足生产需要
验证要求:使用模具能够生产出合格制件
验证依据:零部件检验标准书
设备名称:挤出使用模具数量:共有5套模具供应商:
验证(操作)人员姓名:
验证项目:确认记录
1)模具模芯抛光处理●合格○不合格
2)口模型腔抛光处理●合格○不合格
3)模具尺寸设计●合格○不合格
验证方法:
检查成型制件是否合格
相关文档:
试模记录
留样记录
验证结论:●合格○不合格验证人:日期:13.03.12
审核结论:●合格○不合格审核人:日期:13.03.12
挤出机挤管过程确认方案

插管车间挤出机挤管过程确认方案目录1 目的 (3)2 范围 (3)3 确认依据 (3)4 设备概述 (3)5 确认小组组成 (5)6 重新确认的条件 (5)7 确认方案 (5)7.1 IQ方案 (6)7.2 OQ方案 (8)7.3 PQ方案 (11)1 目的通过实施挤出机的挤出过程确认,从而保证挤出机搬迁后能够持续稳定地生产出符合既定要求的产品。
2 范围2.1确认的产品: 见附录12.2 设备:挤管设备与模具信息见附录13 确认依据3.1机器的操作说明书、工作原理和安装图纸;3.2 参考文件ISO 5361 Anaesthetic and respiratory equipment-Tracheal tubes and connectors,IDT.YY0337.1-2002气管插管-第1部分:常用型插管及接头ISO 5366-1 Anaesthetic and respiratory equipment-Tracheal tubes-Part 1:tubes and connectors for use in adults, IDT.YY 0338.1-2002气管切开插管-第一部分:成人用插管及接头YY 0338.2-2002气管切开插管-第二部分:小儿用气管切开插管EN ISO 8336 Suction catheter for use in the respiratory tractYY 0339-2009 呼吸道用吸引导管过程确认指导-GHTF过程确认指南4 设备概述4.1 基本工作原理该挤出系统分螺杆挤出、牵引和切割三个大的工作模块,基本工作程序为:当机器的安装调试准备工作就绪,接通供气和冷水系统,把原料注满相应料斗内(造影线的原料注入辅机料斗内),接通电源、打开开关进行预热,待到达加热时间后,启动主、辅机的挤出机马达,让螺杆慢慢旋转。
储存在漏斗内的原料,被旋转的螺杆推送到机筒内,用加热的方法使原料逐渐熔融为流动状态,在经机头的引导,形成管状流出。
挤出成型产品配方和工艺流程

挤出成型产品配方和工艺流程挤出成型是一种常见的制造工艺,在生产过程中可以生产各种形状和尺寸的产品。
本文将介绍挤出成型产品的配方和工艺流程,以帮助工厂提高生产效率和产品质量。
配方挤出成型产品的配方是制造过程中至关重要的一环。
一般来说,挤出成型产品的配方包括原材料、添加剂以及辅助剂三个主要部分。
原材料主要指的是基础材料,比如塑料颗粒、橡胶等;添加剂用于改善产品的性能,比如增强材料、阻燃剂等;辅助剂则用于调节产品的流动性、颜色等。
在确定配方时,需要考虑产品的用途、性能要求以及成本等因素。
合理的配方可以确保产品质量稳定,生产成本降低。
工艺流程挤出成型的工艺流程一般包括原料预处理、挤出成型和后处理三个主要阶段。
1.原料预处理: 在这个阶段,需要对原料进行预处理,包括原料混合、加热融化等。
确保原料的质量和均匀性对最终产品的质量至关重要。
同时,还需要根据产品要求添加相应的添加剂和辅助剂。
2.挤出成型: 在挤出机中,原料被加热至熔化状态后,通过螺杆将熔化的原料挤出成型。
挤出机的温度、挤压速度和压力等参数需要根据产品的要求进行调节,确保产品的成型质量和外观。
3.后处理: 成型后的产品需要经过冷却、切割、拉伸等后处理工艺。
通过这些步骤可以使产品的尺寸、外观等达到设计要求。
在整个工艺流程中,操作员需要不断监控和调节各道工序的参数,确保产品的质量稳定。
同时,定期对挤出机及相关设备进行维护保养,延长设备的使用寿命。
结语挤出成型产品的配方和工艺流程对产品的质量和生产效率具有重要影响。
通过优化配方和工艺流程,可以提高产品的品质,降低生产成本。
工厂在实际生产中应根据具体情况,不断改进和优化,提升企业竞争力。
挤出成型确认验证实施方案
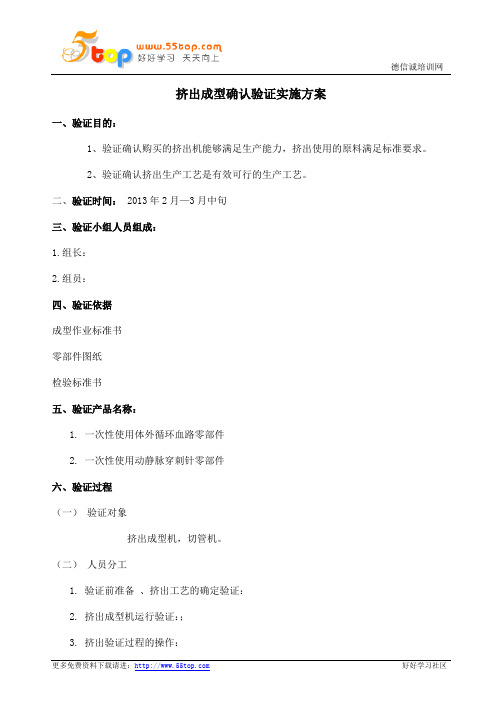
挤出成型确认验证实施方案
一、验证目的:
1、验证确认购买的挤出机能够满足生产能力,挤出使用的原料满足标准要求。
2、验证确认挤出生产工艺是有效可行的生产工艺。
二、验证时间: 2013年2月—3月中旬
三、验证小组人员组成:
1.组长:
2.组员:
四、验证依据
成型作业标准书
零部件图纸
检验标准书
五、验证产品名称:
1.一次性使用体外循环血路零部件
2.一次性使用动静脉穿刺针零部件
六、验证过程
(一)验证对象
挤出成型机,切管机。
(二)人员分工
1.验证前准备、挤出工艺的确定验证:
2.挤出成型机运行验证:;
3.挤出验证过程的操作:
4.验证过程中的审核:
5.验证报告、作业文件的批准:。
挤出成型工艺及挤出模

三、典型挤出机头结构
1、管材挤出成型机头
三、典型挤出机头结构
1、管材挤出成型机头
2、棒材挤出成型机头
2、棒材挤出成型机头
2、棒材挤出成型机头
3、吹塑薄膜挤出成型机头
3、吹塑薄膜挤出成型机头
3、吹塑薄膜挤出成型机头
3、吹塑薄膜挤出成型机头
4、电线电缆挤出成型机头
4、电线电缆挤出成型机头
(3)塑件的定型与冷却 管材的定径方法:定径套、定径环、定径板
3、挤出成型工艺
(3)塑件的定型与冷却
3、挤出成型工艺
(4)塑件的牵引Biblioteka 卷曲和切割 在冷却得同时,连续均匀地将塑件引出。
牵引速度略大于挤出速度
不同的塑件,牵引速度不同。
4、挤出成型工艺条件
(1)温度 加料段的温度不宜过高,压缩段和均化段的温度可高一些。
5、温度调节系统:使挤出成型设备具有一定温度。
6、定径套:对塑件进行冷却定型,以获得完好的塑件。
定型模:让从口模中挤出的塑料的既定形状稳定下来
三、典型挤出机头结构
1、管材挤出成型机头
(1)直通式
三、典型挤出机头结构
1、管材挤出成型机头
(2)直角式
三、典型挤出机头结构
1、管材挤出成型机头
(3)旁侧式
二、挤出成型模具的组成及分类
挤出机头:挤出塑料制件成型的主要部件产生必要的成型压力。
1、口模和芯棒:相当于型腔和型芯,用于成型塑件的内外表面。
2、过滤网和过滤板:将塑料熔体的螺旋运动转变为直线运动,并过滤杂 质。
3、分流器和分流器支架:使塑料熔体平稳地进入成型区,同时进一步加 热和塑化。
4、机头体:组装并支承机头的各个零部件。
挤出成型工艺

02 挤出成型设备
(1)主机: ·单螺杆挤出机
·双螺杆挤出机
02 挤出成型设备
(2)机头:机头的型孔(口模)决定制品断面的形状,不 同的制品可以更换
03 挤出成型工艺优、缺点
优点:1、能加工绝大多数热塑性复合材料及部分热固性复合材料; 2、生产过程连续,自动化程度高,生产效率高; 3、工艺易掌握及产品质量稳定等; 4、生产线占地面积小,且生产环境清洁。 缺点:只能生产线型制品。
原材料(FRTP粒料)
03
03 原材料
树脂
增强纤维
树脂:绝大部分热塑性塑料及部分热固性塑料, 如PVC、PS、ABS、PC、PE、PP、PA、环氧 树脂、酚醛树脂及丙烯酸树脂
增强纤维:玻璃纤维
长纤维:纤维长度等于粒料长度(3mm~13mm ) 树脂及助剂 增强粒料 增强纤维 短纤维 :纤维和树脂无规混合(0.25mm~0.5mm)
挤出成型工艺
组员:刘畅 郝均雨 陈兵
目录
CONTENTS
01 03
挤出成型原理
02 工艺流程、设备及优、缺点
原材料
04 主要应用
挤出成型原理
01
01 挤出成型原理
将塑料加热呈粘流状态,加 压使之通过口模,而成为截 面与口模形状相仿的连续体, 再通过冷却,使其具有一定
几何形状和尺寸的塑料由粘
流态变为高弹态,最后定型 为玻璃态,得到所需要的制 品。
纤维平行于粒料长度排列;
04
主要应用
04 主要应用 01 生产制备管材
04 主要应用 02 生产制备棒材
04 主要应用 03 生产制备异型断面型材
04 主要应用 04
其他应用(板材、塑料薄膜、打包带、网材等)
挤出成型工艺参数包括温度

挤出成型工艺参数包括温度、压力、挤出速率和牵引速度等。
1. 温度温度是挤出成型得以顺利进行的重要条件之一。
从粉状或粒状的固态物料开始,高温制品从机头中挤出,经历了一个复杂的温度变化过程。
严格来讲,挤出成型温度应指塑料熔体的温度,但该温度却在很大程度上取决于料筒和螺杆的温度,一小部分来自在料筒中混合时产生的摩擦热,所以经常用料筒温度近似表示成型温度。
由于料筒和塑料温度在螺杆各段是有差异的,为了使塑料在料筒中输送、熔融、均化和挤出的过程顺利进行,以便高效率地生产高质量制件,关键问题是控制好料筒各段温度,料筒温度的调节是靠挤出机的加热冷却系统和温度控制系统来实现的。
机头温度必须控制在塑料热分解温度以下,而口模处的温度可比机头温度稍低一些,但应保证塑料熔体具有良好的流动性。
此外,成型过程中温度的波动和温差,将使塑件产生残余应力、各点强度不均匀和表面灰暗无光泽等缺陷。
产生这种波动和温差的因素很多,如加热、冷却系统不稳定,螺杆转速变化等,但以螺杆设计和选用的好坏影响最大。
表9-1是几种塑料挤出成型管材、片材和板材及薄膜等的温度参数。
2. 压力在挤出过程中,由于料流的阻力,螺杆槽深度的变化,以及过滤网、过滤板和口模等产生阻碍,因而沿料筒轴线方向,在塑料内部产生一定的压力。
这种压力是塑料变为均匀熔体并得到致密塑件的重要条件之一。
增加机头压力可以提高挤出熔体的混合均匀性和稳定性,提高产品致密度,但机头压力过大将影响产量。
和温度一样,压力随时间的变化也会产生周期性波动,这种波动对塑件质量同样有不利影响,螺杆转速的变化,加热、冷却系统的不稳定都是产生压力波动的原因。
为了减少压力波动,应合理控制螺杆转速,保证加热和冷却装置的温度控制精度。
3. 挤出速率挤出速率(亦称挤出速度)是单位时间内挤出机口模挤出的塑料质量(单位为kg/h)或长度(单位为m/min)。
挤出速度的大小表征着挤出生产能力的高低。
影响挤出速度的因素很多,如机头、螺杆和料筒的结构、螺杆转速、加热冷却系统结构和塑料的特性等。
图1: 挤出成型工艺流程图

3
挥其效能,减少促进剂用量,加快硫化反应速度,缩短硫化时间。 防焦剂:硫化延缓剂,其作用是防止或延缓胶料发生焦烧。 防老剂:延缓或抑制老化过程,从而延长橡胶及其制品的贮存期和使用寿命。 增塑剂:使生胶软化,增加胶料的可塑性,以便于成型加工,减少动力消耗;浸润炭黑等粉状配合剂,使其
易于在胶料中分散,缩短混炼时间,提高混炼效果;提高制品的柔软性和耐寒性;增进胶料的自粘性和粘性。 填充剂:可以分为补强填充剂和惰性填充剂两大类。惰性填充剂又称为增量剂、增容剂,对橡胶的补强效果
床。大部分熔融发生在相对长的压缩段中,需要减少槽深以改善熔融效率。计量段浅槽能合理地均化熔体,熔体 来自熔融区的部分熔态区域,能够给这些部分熔态区带来更均匀的温度。 2. 画出挤出成型工艺的流程图
见图 1。
图 1: 挤出成型工艺流程图
3. 注射机由哪几大部分组成? 这几大部分中,赋予制品一定形状与尺寸的工具称为什么? 主要由哪些部分组成, 各自包含哪些零件? 由注射系统、锁模系统、液压系统及注射模具等几部分组成。 利用本身特定形状,使塑料 (或聚合物) 成型为具有一定形状和尺寸的制品的工具称模具。 注射模具主要由浇注系统、成型零件和结构零件三大部分所组成;成型部件:成型部件是指构成型腔和制品
NPD 函数 Gk(t)
∑k Gk(t) = gj(t)
j=0
一个完整的混合物特征应该叙述为:次要组分的每个粒子、块或斑点的尺寸、形状、取向以及空间位置。三
维浓度分布函数可以提供一个稍不完整的特征。然而,对于许多应用,并不需要如此完整的混合物特征叙述;在
实践中,简单方法即可满足需求。例如,与标准样板进行颜色对比,以定性分析其均匀度,或测量某种典型的
生胶在常温下大多处于高弹态,生胶的这一宝贵性质却给制品的生产带来极大的困难,在加工过程中,各种 配合剂便无法在生胶中分散均匀,而大部分的机械能也会消耗在橡胶的弹性变形上。因此,为了满足各种成型加 工工艺的要求,必须使生胶由强韧的弹性状态变成柔软而具有可塑性的状态,这种增加橡胶可塑性的工艺过程 称为塑炼。
挤出成型工艺介绍工艺
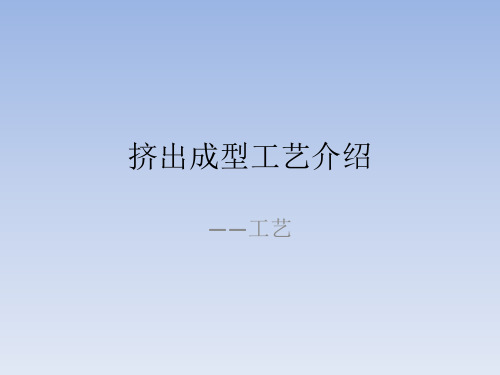
三、工艺控制
三、工艺控制
2、螺杆冷却 用单螺杆挤出机生产板、片材时,对于与螺杆表面摩擦因数较大的物料
或较易熔融并使固体输送段很短的物料,应采用螺杆冷却方法以提高固体输送速 率。 3、牵引速度
挤板、片材过程中,为了避免板、片材“冷拉”导致的表面不平整,内 应力集中等缺陷,应保持牵引速度与挤出的线速度基本相等,但是比三辊压光机 快5%——10%左右。 4、板片厚度控制
三、工艺控制
1、挤出温度 ①挤出温度应根据挤出物料的加工流变特性、热分解性能和板、片材使
用性能综合确定。挤出温度一般分6——10段控制,挤出料筒温度控制在满足均 匀塑化物料的前提下应尽可能低,机头温度除了考虑挤出产量外,还要考虑制品 表面质量要求及与结晶、取向有关的物理力学性能要求,一般比挤出料筒温度高 5——10。
对大型挤出机头,应选用内外加热装置,提高口模温度均匀性和加热效 率。
一、工艺参数设定原则
3、挤出机冷却 为了防止挤出机加料斗底部处物料因过热软化而“架桥”,导致加料不
顺畅,一般挤出机加料斗底部均设置冷却水通道,生产前应接通冷却水冷却。对 与单螺杆挤出机,可采用螺杆内部冷却方法,提高固体输送速率。 4、挤出速度
——工艺
目录
一、工艺参数设定原则 二、片材工艺流程及装置 三、工艺控制 四、常见缺陷
一、工艺参数设定原则
1、机身温度 对与普通的单组份热塑性塑料固体原料的挤出成形,挤出机机身温度设
定原则为: ①机身设定的最高温度略高于塑料的黏流温度(或熔点); ②机身设定的最低温度应至少低于塑料软化点10; ③单螺杆挤出机机身设定的最高温度与最低温度的差值不大于80; ④机身温度字加料端到熔料出口逐渐升高或与螺杆计量段对应区温度相近; ⑤在满足熔化物料的前提下,机身温度应尽可能低。
塑料成型工艺第六章-挤出成型

适用的树脂材料: 绝大部分热塑性塑料及部分热固性塑料,如
PVC、PS、ABS、PC、PE、PP、PA、丙烯酸 树脂、环氧树脂、酚醛树脂及密胺树脂等 应用:
塑料薄膜、网材、带包覆层的产品、截面一定、 长度连续的管材、板材、片材、棒材、打包带、 单丝和异型材等等,还可用于粉末造粒、染色、 树脂掺和等。
面灰暗无光泽等。
努力方向是尽可能减少或消除这种波动和温差。
产生这种波动和温差的原因:
如加热冷却系统不稳定,螺杆转数的变化等, 但 以螺杆设计的好坏影响最大。
普通三段螺杆存在的问题
1.熔融效率低 熔融段熔体与固体床共同存在于一个螺槽中,减
小了料筒壁与固体床的接触面积;固体床随着熔融 解体,部分碎片进入熔体中,很难从剪切获得热量, 这样,固体床不能彻底熔融;另外,已熔物料与料 筒壁接触,从料筒壁和熔膜处获取热量,温度继续 升高过热。 2.压力、温度和产量波动大
的物料量或塑件长度。它表示挤出能力的高低。 4.牵引速度
牵引速度与挤出速度相当,可略大于挤出速度。 牵引— 比— 牵引速度与挤出速度的比值,其值 等于或大于1。
§6.3 挤出管材成型工艺
一、挤出管材工艺控制要点
1.温度的控制
挤出成型温度是促使成型物料塑化和塑料熔体流动的 必要条件。对物料的塑化及制品的质量和产量有着十分 重要的影响。
分离型(屏障型)螺杆
原理:在螺杆熔融段再附加一条螺纹,将原来一 个螺纹所形成的螺槽分为两个,将已熔物料和未 熔物料尽早分离,促进未熔料尽快熔融。
销钉型螺杆 物料流经过销钉时,销钉将固体料或未彻底熔 融的料分成许多细小料流,这些料流在两排销钉 间较宽位置又汇合,经过多次汇合分离,物料塑 化质量得以提高。
料筒外部加热器提供的热量。
挤出生产质量记录表
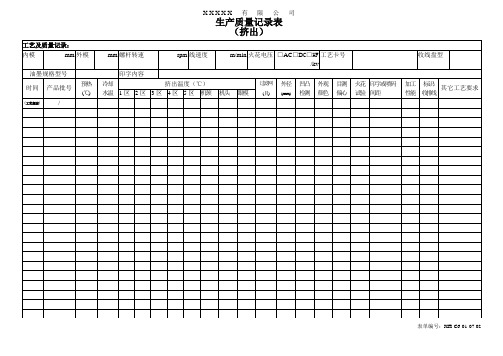
收排线
其它工艺要求
1区
2区
3区
4区
5区
机颈
机头
眼模
(工艺规定)
/
表单编号:XH-C6-01-07.02
常熟市鑫华电子科技有限公司
生产质量记录表
(挤出)
□绝缘□内护套 □外护套 □其他
日期/班次:ห้องสมุดไป่ตู้台号:生产令:规格型号:完成数量:km
物料及批号记录:
物料(制品)编号及批号
送检批号
上工序半制品明细
分批原因
本工序明细
异常说明
不良处理记录
备注
1)“印字”、“外观颜色”、“火花试验”、“目测偏心”、“加工性能”、“标识\收排线”栏目中,合格填“○”,不合格填“×”,如为喷码,需在相应栏目填写实际测量长度,其他项目应填写具体数据。偏心如有检测时,应填写具体数据。
2)当有不合格时,应在“不良处理记录”栏中记录具体的处理方法/结果,或记录对应的MRB编号,以证明不合格(品)被有效控制。
3)首检以在“时间”栏中记录的“时间”前面加“△”表示。
4)“分批原因”栏中只需记录“A”或“B”或“C”,其中:A表示“换导体”,B表示“换颜色”,C表示“其它原因”;当记录“C”时,应作“异常说明”。
表单编号:XH-C6-01-07.02
操作工:审核:
X X X X X有限公司
生产质量记录表
(挤出)
工艺及质量记录:
内模
mm
外模
mm
螺杆转速
rpm
线速度
m/min
火花电压
□AC□DC□HF
/kv
工艺卡号
收线盘型
油墨规格型号
印字内容
- 1、下载文档前请自行甄别文档内容的完整性,平台不提供额外的编辑、内容补充、找答案等附加服务。
- 2、"仅部分预览"的文档,不可在线预览部分如存在完整性等问题,可反馈申请退款(可完整预览的文档不适用该条件!)。
- 3、如文档侵犯您的权益,请联系客服反馈,我们会尽快为您处理(人工客服工作时间:9:00-18:30)。
检查机台参数是否与作业标准书相符
相关文档:
抽检记录
成型作业标准书
工艺纪律检查记录
序号
检查项目
工艺参数
结论
1
黑点
与成型作业标准书相符
合格
2
气泡
合格
3
糊点
合格
4
污物
合格
5
尺寸
合格
7
变形
合格
8
鱼眼
合格
9
犁地处理
合格
10
透明度
合格
所有参数均在成型作业标准书规定范围内。
附产品试生产记录
验证结论:●合格○不合格验证人:日期:13.03.12
审核结论:●合格○不合格审核人:日期:13.03.12
挤出成型工艺确认表
验证目的:确保使用的工艺参数正确,确保生产出的制件合格
验证要求:在现有的工艺参数下生产的制件合格
验证依据:零部件检验标准书
核对机台参数并对8种零部件进行一一确认
验证(操作)人员姓名:
验证项目:确认记录
1)零部件检验●合格○ቤተ መጻሕፍቲ ባይዱ合格
2)核对机台参数与成型作业标准书●合格○不合格
验证方法: