采用西门子PLC控制的自动化生产线案例
西门子PLC编程实例|自动分拣生产线控制系统

西门子PLC编程实例|自动分拣生产线控制系统
控制要求
1.按下启动按钮(不带复位),系统开始动作,启动指示灯亮。
2.按下停止按钮(不带复位),系统暂停,此时若再按下启动按钮,系统自动动作,停止指示灯亮。
3.按下急停按钮(带复位),系统全部停止。
若再按下启动按钮,系统重新开始动作。
系统操作流程
1.按下启动按钮,当送料气缸在缩回的位置时,该电磁阀得电,将仓内的零件推出,当气缸达到完全伸出的位置时,该电磁阀失电,送料动作完成。
2.送料动作完成后,皮带通过变频器启动。
3.通过安装在皮带上的各种检测传感器(金属、颜色),将不同零件区分开。
4.黑色(非金属)的零件到达槽3时,其对应的槽3气缸将它推出。
5.白色(非金属)的零件到达槽2时,其对应的槽2气缸将它推出。
6.蓝色(非金属)的零件到达槽1时,其对应的槽1气缸将它推出。
7.金属零件到达皮带终端的到位开关时,机械手立即上升,上升到机械手的上限位时,右移:右移到右限位时,下降:下降到下限位时,夹住金属零件,然后上升:上升到上限位时,左移:左移到左限位时,下降:下降到下限位时,放开零件:放开零件后,上升:上升到上限位时,右移:右移到右限位时,完成金属零件的放置。
每当放好一个零件后,送料气缸动作,推出下一个零件,系统循环动作。
I/O分配
PLC接线图
梯形图
今天的介绍就到这里了,感兴趣的朋友可以试着用顺序控制指令的编程方法实现这一控制!
本文转自锦绣添香,版权归原作者,侵删。
PLC在生产线控制中的应用案例分享

PLC在生产线控制中的应用案例分享PLC(可编程逻辑控制器)是一种常见的工业自动化设备,广泛应用于各种生产线的控制系统中。
本文将分享几个PLC在生产线控制中的应用案例,旨在探讨PLC的功能和应用,以及它们在提高生产效率和质量方面的作用。
案例一:汽车生产线在汽车生产线上,PLC扮演着关键的角色。
它通过接收传感器和外部设备的输入信号,对各个工作站的运行进行控制和调度。
通过编程,PLC可以对不同的操作进行精确的定时和顺序控制,确保每个工作站都按照正确的步骤进行,并与其他工作站协调合作。
举个例子,在汽车装配线上,PLC可以控制机械臂的动作和位置,确保零部件的准确提取和装配。
它还可以监控传送带的速度和方向,及时调整生产节奏,以适应不同车型和订单的要求。
通过PLC的应用,汽车生产线可以实现高效、精确和稳定的生产,大大提升了生产效率和产品质量。
案例二:食品加工生产线在食品加工行业,PLC也发挥着重要的作用。
以饼干生产线为例,PLC可以控制不同工作站的温度、时间和速度等参数,实现对各个工艺环节的精确控制。
例如,在饼干生产的烘烤环节,PLC可以根据产品种类和要求,控制烤箱的温度和气流方向,确保饼干可以均匀烘烤,达到理想的口感和外观。
此外,PLC还可以监测并记录生产数据,如温度、湿度、压力等,以便质量控制人员进行分析和追溯。
案例三:包装生产线在包装行业,在PLC的应用下,生产线的包装过程可以更加高效、准确和可靠。
例如,在瓶装水生产线上,PLC可以控制灌装机的流量和速度,确保每个瓶子都按照预定的容量装满水。
它还可以监控瓶子的位置和运行速度,及时进行调整,避免瓶子的堵塞和脱落。
此外,PLC还可以与其他包装设备如贴标机、封口机等进行联动控制,实现自动化生产和包装过程。
综上所述,PLC在生产线控制中的应用案例丰富多样。
它的高可编程性和灵活性使得PLC适用于各种不同的生产线和行业。
通过合理的编程和控制,PLC能够提高生产效率、降低成本、提升产品质量,并且具备良好的稳定性和可靠性。
西门子PCS7自控系统UCC日产万吨生产线应用案例
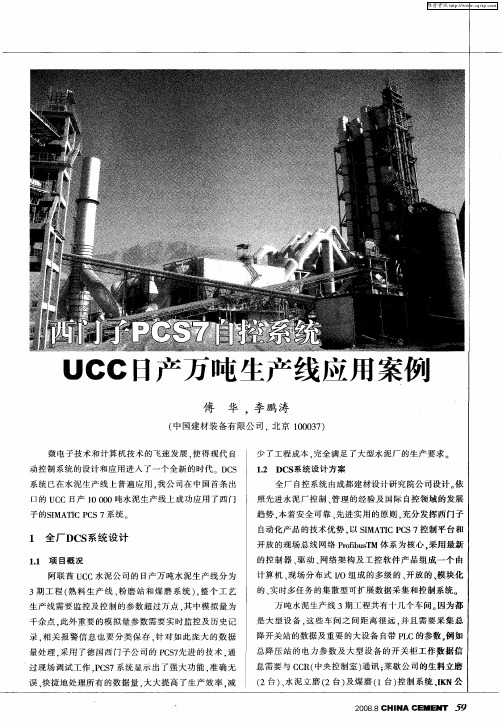
子 的SMA I C 统 I T C P S7系
少 了工程成本 . 完全满足 了大 型水泥厂 的生产要求 。
1 全 厂DCS 系统 设 计
11 项 目概 况 .
开放的现场总线 网络 P b sM体 系为核心 . uT 采用最新
的控制器 、 动 、 络架构 及工控 软件产 品组成一 个 由 驱 网
阿联酋 U C水泥公 司的 日产 万吨水泥生产线分 为 C 3期工程 ( 料生产 线 、 磨站 和煤磨 系统 )整 个工 艺 熟 粉 , 生产线需要 监控及控制 的参数超 过万点 . 中模拟量 为 其
据 . 将就 近的开关 在控制站 的重要大 型设备 自带 P C通过点 对点方 式或 L
是 总 线 方 式 与 该 控 制 站 D S通 讯 .然 后 将 每 个 现 场 控 C
视频 图像监控技术等关键 技术 . 以定义 为集 成现场工 可
业总线 的高速 以太 网多媒体计 算机信 息管理 、控制 系
1 DCS 统 设 计 方 案 . 2 系
全 厂 自控 系 统 由成 都建 材 设 计 研 究 院公 司设 计 。 依 照先 进 水 泥 厂 控 制 、 理 的经 验及 国 际 自控 领 域 的发 展 管
趋势, 本着安全 可靠 、 先进实用 的原则 , 充分发挥西 门子
自动化 产 品 的 技 术 优 势 . SMA I C 制 平 台 和 以 I TCP S7控
2 0 8CH I 0 8. NA CEM EN T
录. 相关 报警信 息也要 分类保存 。 针对如 此庞大 的数据
PLC在制造业中的自动化改造案例分析
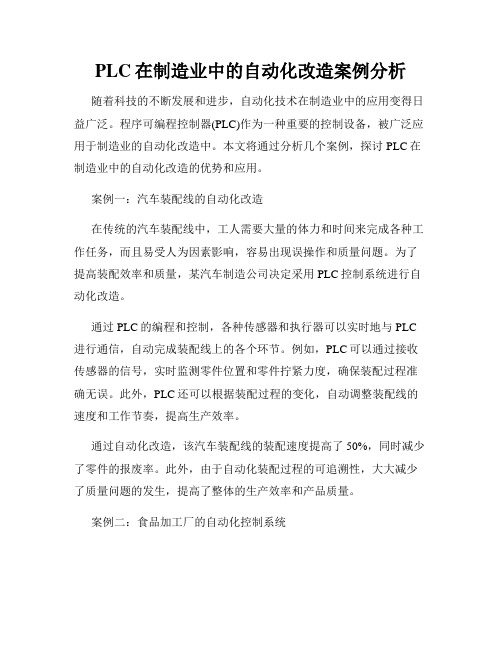
PLC在制造业中的自动化改造案例分析随着科技的不断发展和进步,自动化技术在制造业中的应用变得日益广泛。
程序可编程控制器(PLC)作为一种重要的控制设备,被广泛应用于制造业的自动化改造中。
本文将通过分析几个案例,探讨PLC在制造业中的自动化改造的优势和应用。
案例一:汽车装配线的自动化改造在传统的汽车装配线中,工人需要大量的体力和时间来完成各种工作任务,而且易受人为因素影响,容易出现误操作和质量问题。
为了提高装配效率和质量,某汽车制造公司决定采用PLC控制系统进行自动化改造。
通过PLC的编程和控制,各种传感器和执行器可以实时地与PLC 进行通信,自动完成装配线上的各个环节。
例如,PLC可以通过接收传感器的信号,实时监测零件位置和零件拧紧力度,确保装配过程准确无误。
此外,PLC还可以根据装配过程的变化,自动调整装配线的速度和工作节奏,提高生产效率。
通过自动化改造,该汽车装配线的装配速度提高了50%,同时减少了零件的报废率。
此外,由于自动化装配过程的可追溯性,大大减少了质量问题的发生,提高了整体的生产效率和产品质量。
案例二:食品加工厂的自动化控制系统在一个食品加工厂中,涉及到许多复杂的生产工艺和控制任务,需要大量的人力投入和精确的控制。
为了提高生产效率和减少人为因素对产品质量的影响,该加工厂引入了PLC控制系统进行自动化改造。
通过PLC的编程和控制,生产工艺的各个环节可以实现自动化控制。
例如,通过接收传感器的信号,PLC可以对温度、压力、流量等参数进行实时监测和控制,确保每个工艺环节的精确执行。
此外,PLC可以根据不同产品的需求,自动调整生产线的工作模式和参数设置,提高生产效率和产品质量。
通过自动化改造,该食品加工厂的生产能力提高了30%,同时大大减少了产品的浪费和损耗。
此外,由于自动化控制系统的精确性和稳定性,产品的质量得到了有效的保障。
整个加工过程更加高效、安全和可靠。
案例三:电子设备生产线的自动化优化在一个电子设备生产厂中,原本采用传统的人工操作方式,容易出现操作疏漏和质量问题。
基于西门子PLCS7-200的自动化电镀生产线控制设计
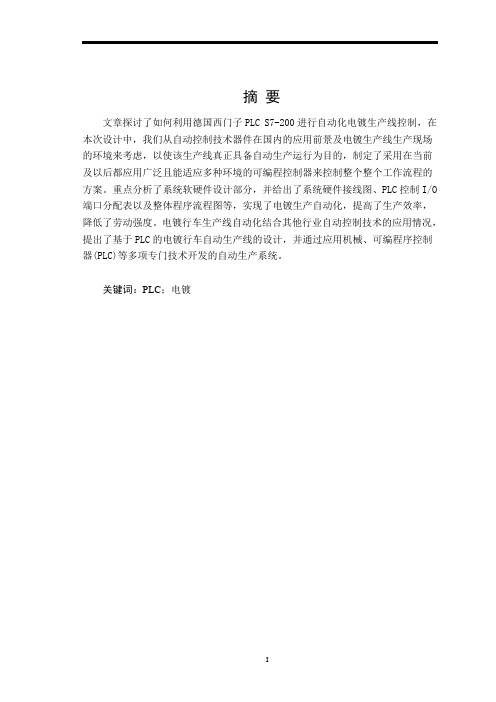
摘要文章探讨了如何利用德国西门子PLC S7-200进行自动化电镀生产线控制,在本次设计中,我们从自动控制技术器件在国内的应用前景及电镀生产线生产现场的环境来考虑,以使该生产线真正具备自动生产运行为目的,制定了采用在当前及以后都应用广泛且能适应多种环境的可编程控制器来控制整个整个工作流程的方案。
重点分析了系统软硬件设计部分,并给出了系统硬件接线图、PLC控制I/O 端口分配表以及整体程序流程图等,实现了电镀生产自动化,提高了生产效率,降低了劳动强度。
电镀行车生产线自动化结合其他行业自动控制技术的应用情况,提出了基于PLC的电镀行车自动生产线的设计,并通过应用机械、可编程序控制器(PLC)等多项专门技术开发的自动生产系统。
关键词:PLC;电镀目录第1章绪论 (1)1.1电镀生产线的控制系统概述与选题背景意义 (1)1.1.1基于PLC电镀生产线的控制系统的概述 (1)1.1.2课题的选题背景及意义 (1)1.2PLC的发展和历史趋势 (2)1.3PLC的分类 (2)1.4PLC系统组成及各部分的功能 (3)1.5PLC的基本工作原理 (3)第2章课程设计的方案 (5)第3章硬件设计 (6)3.1PLC机型选择 (6)3.2I/O分配表及其端子接线图 (6)3.3主电路的设计 (8)第4章软件设计 (10)4.1软件的组成及作用 (10)4.1.1PLC内部资源 (10)4.1.2PLC编程语言 (10)4.2电镀生产线的工作流程图 (12)第5章系统测试与分析/实验数据及分析 (17)第6章课程设计总结............................... 错误!未定义书签。
参考文献.. (20)第1章绪论1.1电镀生产线的控制系统概述与选题背景意义1.1.1基于PLC电镀生产线的控制系统的概述电镀行车生产线自动化的程度在德国、意大利、美国等国家的发展水平已经较高,而在我国尚处在发展阶段。
西门子S7-200型PLC在YL-335A自动化生产线中机械手臂的设计与应用
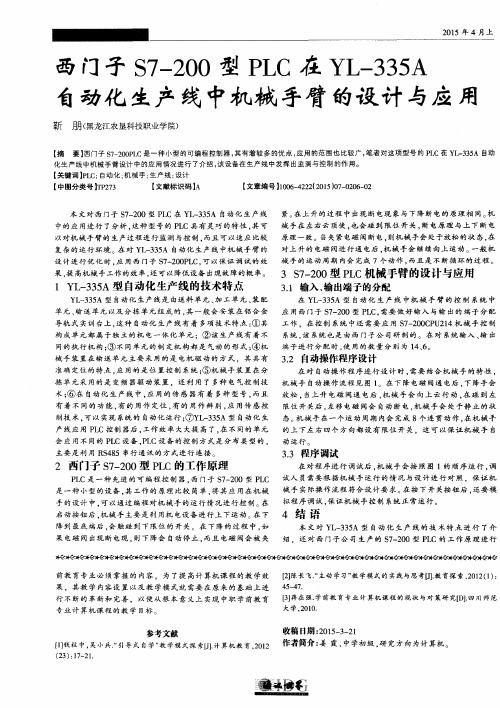
主 要 是 利 用 R¥ 4 8 5串行 通 讯 的 方 式进 行 连 接
的 上 下 左 右 四 个 方 向 都设 有 限 位 开 关 ,这 可 以保 证 机 械 手 自
3 . 3 程序 调试
3 . 2 自动操作程序设计
在 对 自动 操 作 程 序 进 行 设 计 时 , 需要结合机械手的特性 ,
拣 单 元 采 用 的 是 变 频 器 驱动 装 置 .还 利 用 了 多 种 电 气控 制技 机 械 手 自动 操 作 流 程 见 图 1 。在 下 降 电磁 阀 通 电后 , 下 降手 会
本 文 对 西 门子 S 7 — 2 0 0型 P L C在 Y L 一 3 3 5 A 自动 化 生 产 线
紧。 在 上 升 的过 程 中 出现 断 电现 象与 下 降 断 电 的 原理 相 同 。 机
中 的应 用进 行 了分 析 。 这种型号的 P L C具 有 灵 巧 的特 性 , 其 可 械 手在 左 右 云顶 使 , 也会碰到限位开关 , 断电原理与上下断 电 复 杂 的运 行 环 境 。在 对 Y L 一 3 3 5 A 自动 化 生 产 线 中机 械 手 臂 的
术; ( 9在 自动 化 生 产 线 中 , 应 用 的 传 感 器有 着 多种 型 号 , 而 且 放 松 , 当 上 升 电磁 阀通 电后 , 机械 手会 向上云行动 , 在碰 到 左 有 着 不 同的 功 能 . 有的用作定位 , 有 的用作辨别 , 应 用传 感 控 限 位 开 关后 。 左 移 电磁 阀会 自动 断 电 . 机 械 手 会 处 于静 止 的状
3 . 1 输入 、 输 出端予 的分配
采用西门子PLC控制的自动化生产线案例

采用西门子PLC控制的自动化生产线案例一、引言上海大众汽车有限公司引进的德国SCHULER 6000KN大型自动化冲压线主要用来生产PASSA T轿车4门2盖等中型冲压件,平均冲次可达6.7次/分钟。
SCHULER冲压线主要由6个压机单元和6个机械化单元组成,压机单元主要用来进行料片冲压,机械化单元主要采用吸盘方式进行料片拆垛、压机之间料片传送等任务。
SCHULER自动化压机线的控制设备采用先进的西门子控制设备,整个自动化控制网络分为两级,第一级为基础自动化网络,它主要包括现场层SIEMENS 可编程控制器SIMA TIC H1网络和操作员工作站WINCC网络;第二级为服务器控制管理层网络。
SCHULER压机线的整个工业控制网络系统较为复杂,由环形拓扑结构、星形拓扑结构、总线形拓扑结构三种拓扑结构类型的工业控制网络组合而成。
二、基础自动化网络2.1 现场层网络SCHULER 压机线现场层控制采用PLC和PROFIBUS现场总线控制。
每个压机单元和机械化单元各采用独立的PLC控制,PLC采用西门子S5-115U可编程控制器,整条压机线共使用了12个PLC进行控制。
2.1.1 PLC H1 网络服务器与现场层PLC通讯采用SIMA TIC H1以太网络,CSMA/CD协议,光缆介质,通信速率为10Mbps,环形拓扑结构。
每单元PLC都配置有CP1430通讯模块,通过相应的OLM(光电转换模块)上网通讯,服务器内置CP1413通讯模块通过第一单元OLM模块与PLC H1网通讯。
在此服务器起到参数的上传/下送作用,它与PLC之间的数据交换通过DDF(动态数据交换)来进行。
使用光纤网不仅满足了高速大容量的数据交换,也大大增强了抗外界电磁场干扰以及抗泄漏的性能,环形结构的好处是一旦光纤网链路发生断裂,仍可保持通信;此外,它完全与电位无关地运行,不必花费昂贵的等电位连接费用,且大大增强了网络的可靠性。
2.1.2 PROFIBUS 总线PLC与现场设备的通迅采用西门子公司的PROFIBUS-DP现场总线,PROFIBUS-DP总线是一种全分布式现场总线型现场控制网络,它通过ET200分布式输入/输出系统与现场设备之间实现双向串行多节点数字通信。
基于西门子S7-200自动生产线分拣站的控制
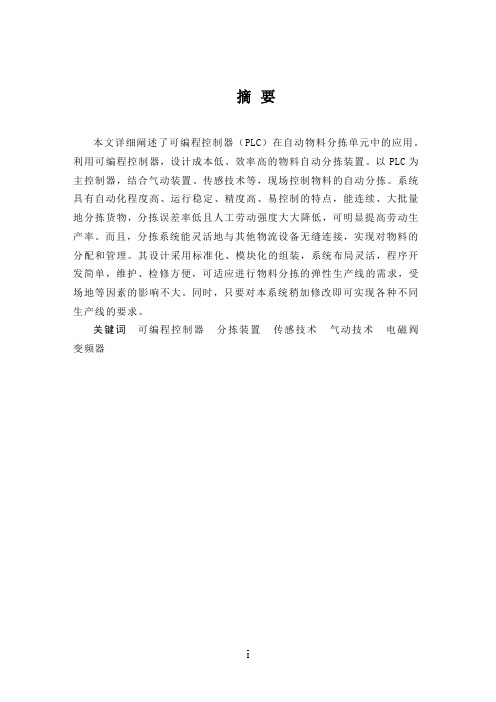
摘要本文详细阐述了可编程控制器(PLC)在自动物料分拣单元中的应用。
利用可编程控制器,设计成本低、效率高的物料自动分拣装置。
以PLC为主控制器,结合气动装置、传感技术等,现场控制物料的自动分拣。
系统具有自动化程度高、运行稳定、精度高、易控制的特点,能连续、大批量地分拣货物,分拣误差率低且人工劳动强度大大降低,可明显提高劳动生产率。
而且,分拣系统能灵活地与其他物流设备无缝连接,实现对物料的分配和管理。
其设计采用标准化、模块化的组装,系统布局灵活,程序开发简单,维护、检修方便,可适应进行物料分拣的弹性生产线的需求,受场地等因素的影响不大。
同时,只要对本系统稍加修改即可实现各种不同生产线的要求。
关键词可编程控制器分拣装置传感技术气动技术电磁阀变频器ABSTRACTThe design of an automatic sorting device with low cost and high efficiency is presented in the paper which regards programmable logic controller (PLC) as the master controller and combines pneumatic device sensing technology and other technology to implement automatic selecting of the products. The device is characteristic of high automation, steady running, high precision and easy control .It can be continuous, large quantities of goods are sorted, sorting error rate low ,greatly reduce labour intensity, can significantly increase labour productivity. Furthermore, the sorting system would be flexibly and seamlessly connect to other logistics equipment. The design use standardized and modular assembly, a flexible system layout, simple program development and easy maintenance. It adapts to elasticity production line for materials sorting. The system affected by the venue and other factors with little impact. Meanwhile it can fulfil different requirement according to different situations with little modifications.Keywords PLC, sorting device, sensing technology, pneumatic technology, solenoid pilot actuated valve, frequency converters,目录第1章概论 (1)1.1课题研究的背景 (1)1.2自动分拣系统发展的现状 (2)1.3YL-335A自动化生产线实训考核装备概述 (2)1.3.1 YL-335A的基本组成 (2)1.3.2. YL-335A各工作单元的基本功能 (3)1.3.3. YL-335A 的特点 (4)1.3.4 YL-335A的PLC网络控制方案 (4)1.3.5 YL-335A的公共模块和器件 (5)第2章分拣单元的结构与控制 (7)2.1分拣单元的结构组成 (7)2.1.1传送和分拣机构 (8)2.1.2 传动机构 (10)2.1.3 电磁阀组 (11)2.2分拣单元的工作原理 (12)2.3气动控制回路 (12)2.4分拣单元的电气接线 (13)2.5PLC的I/O接线 (14)2.6西门子MM420变频器简介 (15)2.6.1 MM420 变频器的BOP 操作面板 (17)2.6.2 MM420 变频器的参数设置 (18)第3章分拣单元的编程. (21)3.1分拣单元的编程要点 (21)3.2分拣单元变频器的参数设置及梯形图 (21)3.2.1变频器固定频率调速 (21)3.2.2变频器模拟输入变速调速 (23)3.2.3在PLC网络控制下的分拣单元程序 (24)3.2.4运行结果 (27)结束语 (27)参考文献 (28)第1章概论在高新技术不断迅速发展及企业现代化生产规模的不断扩大和深化的今天,不断更新和研发自动化生产线非常重要。
plc程序联动控制程序案例
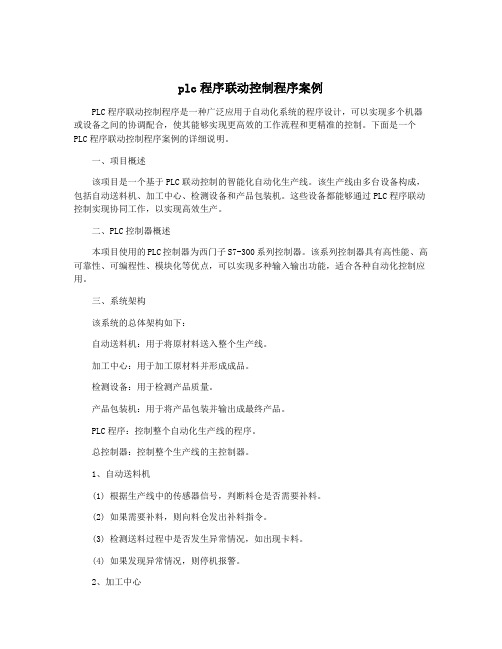
plc程序联动控制程序案例PLC程序联动控制程序是一种广泛应用于自动化系统的程序设计,可以实现多个机器或设备之间的协调配合,使其能够实现更高效的工作流程和更精准的控制。
下面是一个PLC程序联动控制程序案例的详细说明。
一、项目概述该项目是一个基于PLC联动控制的智能化自动化生产线。
该生产线由多台设备构成,包括自动送料机、加工中心、检测设备和产品包装机。
这些设备都能够通过PLC程序联动控制实现协同工作,以实现高效生产。
二、PLC控制器概述本项目使用的PLC控制器为西门子S7-300系列控制器。
该系列控制器具有高性能、高可靠性、可编程性、模块化等优点,可以实现多种输入输出功能,适合各种自动化控制应用。
三、系统架构该系统的总体架构如下:自动送料机:用于将原材料送入整个生产线。
加工中心:用于加工原材料并形成成品。
检测设备:用于检测产品质量。
产品包装机:用于将产品包装并输出成最终产品。
PLC程序:控制整个自动化生产线的程序。
总控制器:控制整个生产线的主控制器。
1、自动送料机(1) 根据生产线中的传感器信号,判断料仓是否需要补料。
(2) 如果需要补料,则向料仓发出补料指令。
(3) 检测送料过程中是否发生异常情况,如出现卡料。
(4) 如果发现异常情况,则停机报警。
2、加工中心(1) 读取自动送料机送进来的原材料信号。
(2) 根据自动送料机的信号,判断需要加工的零件类型和数量。
(3) 根据生产计划和零件特性,进行自动加工。
(4) 检测零件加工质量。
(5) 如果发现质量问题,则停工处理。
3、检测设备(1) 检测成品的各项指标,如尺寸、材质、工艺标准等。
(2) 如果发现不合格品,则将其送回加工中心或直接处理。
4、产品包装机(1) 将生产线出产的成品进行包装。
(2) 对包装产品进行检测,防止出现漏装、错装等质量问题。
5、PLC程序(1) 根据生产计划以及生产线中的传感器信号,完成整个生产线的自动化控制。
(2) 管理设备之间的数据传递、信息反馈和异常处理问题。
基于西门子PLC的纯净水自动化生产线系统
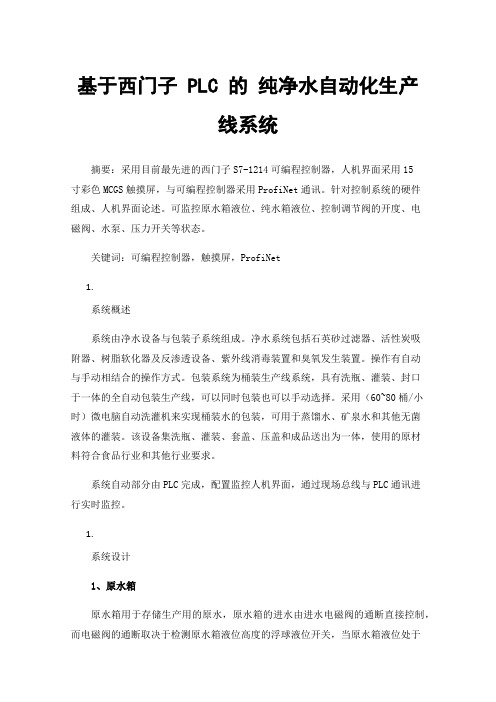
基于西门子 PLC 的纯净水自动化生产线系统摘要:采用目前最先进的西门子S7-1214可编程控制器,人机界面采用15寸彩色MCGS触摸屏,与可编程控制器采用ProfiNet通讯。
针对控制系统的硬件组成、人机界面论述。
可监控原水箱液位、纯水箱液位、控制调节阀的开度、电磁阀、水泵、压力开关等状态。
关键词:可编程控制器,触摸屏,ProfiNet1.系统概述系统由净水设备与包装子系统组成。
净水系统包括石英砂过滤器、活性炭吸附器、树脂软化器及反渗透设备、紫外线消毒装置和臭氧发生装置。
操作有自动与手动相结合的操作方式。
包装系统为桶装生产线系统,具有洗瓶、灌装、封口于一体的全自动包装生产线,可以同时包装也可以手动选择。
采用(60~80桶/小时)微电脑自动洗灌机来实现桶装水的包装,可用于蒸馏水、矿泉水和其他无菌液体的灌装。
该设备集洗瓶、灌装、套盖、压盖和成品送出为一体,使用的原材料符合食品行业和其他行业要求。
系统自动部分由PLC完成,配置监控人机界面,通过现场总线与PLC通讯进行实时监控。
1.系统设计1、原水箱原水箱用于存储生产用的原水,原水箱的进水由进水电磁阀的通断直接控制,而电磁阀的通断取决于检测原水箱液位高度的浮球液位开关,当原水箱液位处于低水位时,低水位信号反馈到控制中心PLC,然后PLC驱动打开进水电磁阀,使原水进入水箱补水;当原水箱液位处于高水位时,同样浮球开关反馈高水位信号到PLC,PLC使进水电磁阀关闭,避免原水溢出水箱。
另外,原水箱还配有投入式液位传感器,输出4-20MA电流信号,传感器量程0-1.5米,此传感器用于检测实时水箱液位高度,配合显示仪表或上位机软件可直观显示当前液位高度。
2、增压泵系统采用380V 0.55KW 卧式增压泵用于给过石英砂过滤器、活性炭吸附器、树脂软化器等过滤器提供压力。
3、电动调节阀电动调节阀用于调节原水流量,从而调节产水速率。
电动调节阀可接受外部4-20ma电流信号作为开度控制信号,也可反馈4-20ma电流信号到PLC,作为位置反馈。
基于s7-1200系列PLC自动化生产线设计
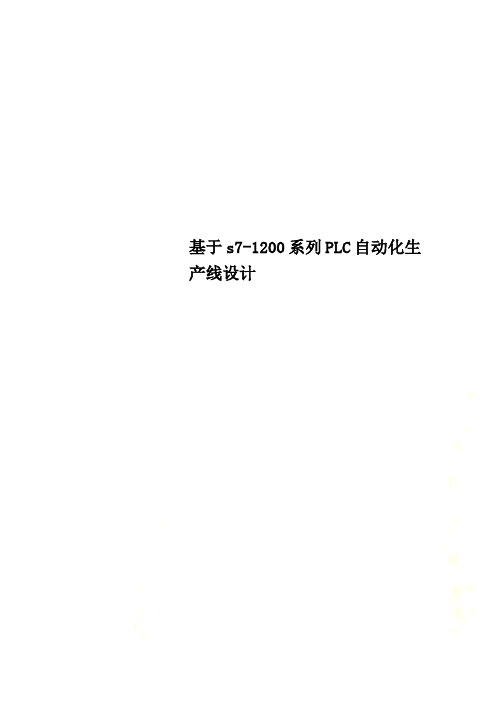
基于s7-1200系列PLC自动化生产线设计广州城建职业学院毕业设计题目_基于S7-1200 PLC自动化生产线控制系统的设计_ 所在系机电与信息工程学院____专业班级 14机电一体化2班____学生姓名 _程广通_____ _学生学号__1409010202_指导老师曾一新 _____ _ __广州城建职业学院教务处制基于S7-1200 PLC自动化生产线控制系统的设计14机电一体化2班程广通指导老师:曾一新摘要基于S7-1200 PLC自动化生产线控制系统是加工、组装的一套结合工业案例,按工业标准设计,集成主流、常用工业控制设备的教学仪器。
该系统设备采用西门子应用于制造行业中的SIMATIC S7-1200为核心,配合工业总线通讯接口,集成变频器、人机界面、通信网络、多种传感器(颜色、姿势、材质辨别等),实现自动化技术相关专业中PLC应用技术教学、训练和考核。
设备包含:自动送料功能模块、传送带功能模块、自动检测功能模块、气动、电动机械手功能模块、PLC与变频器控制系统、直流调速模块、步进驱动模块、报警功能模块、人机界面PLC网络通讯系统、气动控制系统等,构成自动分拣与姿势调整的主从工作站。
关键词S7-1200;西门子;PLC;自动化生产线目录引言 (6)第一章基于S7-1200PLC自动化生产线控制系统的概述 (7)一、自动化生产线控制系统的现状与发展 (7)二、自动化生产线控制系统的组成 (8)三、自动化生产线控制系统运行模式分析 (9)第二章 PLC结构和工作原理及相关知识介绍 (10)一、PLC组成与基本结构 (10)二、 PLC的系统结构 (10)三、 PLC的基本工作原理 (12)四、西门子S7-1200系列PLC功能特点 (13)五、开放式用户通信简介............................ 错误!未定义书签。
六、步进电机的结构及原理 (17)七、西门子MM420变频器介绍控制 (18)第三章基于S7-1200PLC自动化生产线控制系统方案设计 (22)一、系统的工作原理 (22)二、设计分析 (23)三、可行性分析 (25)四、可行性试验 (25)五、PLC的选择 (26)第四章PLC的硬件和硬件组态设置 (28)一、步进电机驱动器设置 (28)二、变频器参数设置 (29)三、硬件组态 (31)第五章系统硬件开发设 (36)一、硬件系统的结构 (36)二、控制系统I/O地址分配 (37)第六章系统软件控制设计 (39)一、控制要求 (39)二、梯形图编程流程图 (44)小结 (49)参考文献 (50)引言本论文是考虑到目前的自动化生产线发展的实际情况,现代化的自动生产设备是现今生产中最为普遍的生产方式,以及最有发展前景的生产方式,由本论文作者结合相关资料编写的一遍毕业论文。
自动生产线两层式升降电梯PLC系统设计(西门子plc200)

毕业论文(设计)自动生产线两层式升降电梯PLC系统设计(西门子plc200)系别:机电工程系专业:机电一体化技术班级:学号:学生姓名:指导教师:目录1.绪论 (1)1.1研究自动生产线两层式升降电梯控制系统的意义 (1)1.2自动生产线两层式升降电梯控制系统的研究思路和主要内容 (1)2.自动升降电梯机械系统和自动控制系统概述 (2)2.1自动升降电梯机械系统的组成 (2)2.2自动升降电梯自动控制系统的组成 (4)3.自动升降电梯系统的工作原理和控制要求 (5)4.自动升降电梯系统的PLC型号的确定 (6)4.1基本模块的选择 (6)4.2扩展模块的选择 (7)5.自动升降电梯PLC控制系统程序设计 (8)5.1自动升降电梯PLC控制系统的I/O地址分配 (8)5.2自动升降电梯PLC控制系统的外围接线图 (9)5.3自动升降电梯PLC控制系统的状态流程图 (9)5.4自动升降电梯PLC控制系统的梯形图程序 (10)5.5自动升降电梯PLC控制系统的程序模拟及调试 (17)5.5.1仿真软件介绍 (17)5.5.2 调试的过程说明和结果分析 (19)6.总结和展望 (20)6.1论文的主要研究成果和不足 (20)6.2进一步研究的方向 (20)7.致谢 (21)参考文献: (22)绪论自动生产线两层式升降电梯控制系统设计摘要: 文章主要介绍的是自动生产线两层式升降电梯的PLC控制系统设计。
它详细地阐述了系统组成、系统工作原理、系统的PLC梯形图程序设计以及利用模拟软件进行程序的调试过程。
该系统控制原理简单、操作方便、自动化程度较高且稳定性强,对于工厂的不间断生产作业有很强的实用性。
关键词: 升降电梯 PLC 自动生产线1.绪论1.1研究自动生产线两层式升降电梯控制系统的意义自动生产线两层式升降电梯的控制系统用PLC控制有很高的稳定性和可操作性,高的稳定性正是工厂不间断生产所要求的,可操作性为当生产有新的任务要求时可以重新设计或手动操作以达到不同的任务要求,操作方便。
PLC在生产线控制中的应用案例

PLC在生产线控制中的应用案例PLC 在生产线控制中的应用案例在现代工业领域,自动化生产线已经成为提高效率和降低成本的重要手段之一。
而可编程逻辑控制器(PLC)作为控制自动化生产线的核心设备之一,因其稳定可靠、灵活扩展等特点而被广泛应用于各个行业。
本文将介绍一个在生产线控制中应用 PLC 的实际案例,展示其在提高生产效率和质量控制方面的优势。
案例描述:某家汽车零部件制造工厂生产线上,存在着多个工序需要协同工作。
在传统的生产方式下,各个工序之间需要人工干预来完成工作任务,无法实现高效自动化的流程控制,导致生产效率低下和质量难以控制。
为解决这个问题,工厂决定引入 PLC 控制系统。
方案实施:1. 系统模块设计:针对生产线上的各个工序和对应的设备,设计了相应的控制模块,并将其连接到 PLC 控制器上。
这些模块包括传感器模块、执行模块、输入输出模块等。
传感器模块用于采集实时的工艺参数,执行模块用于控制各个执行器的动作,输入输出模块用于与外部设备进行交互。
2. 逻辑程序编写:基于生产线上的工艺流程和控制要求,编写了 PLC 的逻辑程序。
逻辑程序定义了各个工序之间的协同关系和相应的控制逻辑。
通过编写适当的程序语句和流程控制指令,实现了自动化生产线上的流程控制。
此外,逻辑程序还包括了错误处理和异常情况的处理等机制,以确保生产线的稳定运行。
3. 联机调试和优化:在完成逻辑程序编写后,对PLC 控制系统进行了联机调试和优化。
通过与实际生产线的协同工作,检验了程序的正确性和稳定性,并对其中存在的问题进行了调整和改进。
在调试过程中,利用 PLC 提供的实时监控和诊断功能,及时发现并解决了潜在的故障和异常情况。
4. 实施效果:引入PLC 控制系统后,工厂的生产线控制方面出现了显著的改善。
首先,生产效率大大提高,因为各个工序之间能够无缝衔接,减少了人为操作和等待时间。
其次,生产质量得到了有效控制,因为 PLC 控制系统具备高精度和高稳定性,能够做到精确的动作控制和工艺参数监控。
自动化生产线装配与调试技术-——基于西门子S7-200系列PLC项目四
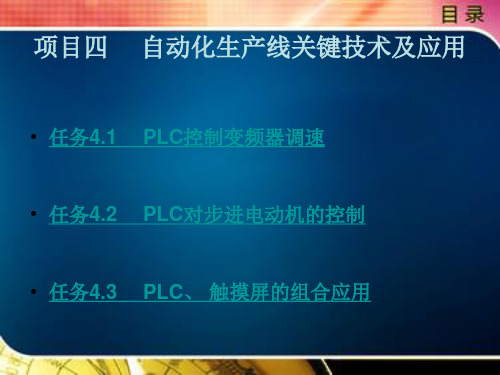
上一页 下一页 返回
任务4.1 PLC控制变频器调速
• 4.1.2 MM440 变频器与PLC的多段速控制设 置训练
• 任务提出 • 由于现场工艺上的要求, 很多生产机械在不同的转速下运行。 为方便
这种负载, 大多数 变频器均提供了多挡频率控制功能。 用户可以通过 几个开关的通、 断组合来选择不同的运行 频率, 实现在不同转速下运 行的目的。 • 任务分析 • 多段速功能也称作固定频率, 就是设置参数P1000=3的条件下, 用开关 量端子选择固 定频率的组合, 实现电动机多段速度运行。 可通过如下 三种方法实现多段速控制。 • 1. 直接选择 (P0701-P0706=15) 在这种操作方式下, 一个数字输入选 择一个固定频率, 端子与参数设置对应见表4-1。
上一页 下一页 返回
任务4.2 PLC 对步进电动机的控制
• (2) PTO的种类及特点。 • PTO功能可输出多个脉冲串, 现用脉冲串输出完成时, 新的脉冲串输出
自动化生产线装配与调试技术-——基于西门子S7-200系列PLC项目三
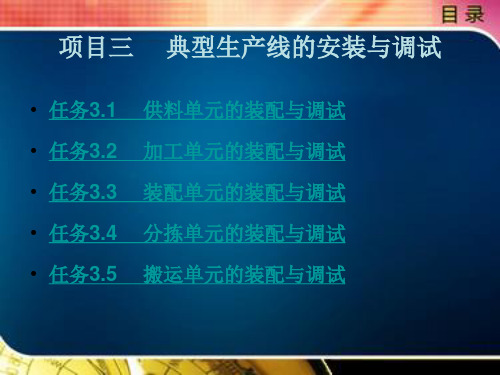
• 3. 3. 2 装配单元的电气连接及编程
• 1. 装配单元PLC 电气电路 • 装配单元PLC 电气电路如图3 -11 所示。
下一页 返回
任务3. 3 装配单元的装配与调试
梯形图程序。 • 3. 下载程序及调试 • 将编写好的程序下载至PLC 中运行, 调试通过, 完成控制任务, 并记录
下实验操作过程。
上一页 下一页 返回
任务3.1 供料单元的装配与调试
• 3. 1. 4 供料单元PLC 程序
• 主程序:
上一页 下一页 返回
任务3.1 供料单元的装配与调试
上一页 下一页 返回
项目三 典型生产线的安装与调试
• 任务3.1 供料单元的装配与调试 • 任务3.2 加工单元的装配与调试 • 任务3.3 装配单元的装配与调试 • 任务3.4 分拣单元的装配与调试 • 任务3.5 搬运单元的装配与调试
任务3.1 供料单元的装配与调试
• 3. 1. 1 供料单元的气动控制回路分析及仿真
• (3) 启动前, 供料单元不在初始位置或无法回复至初始位置时, 警示灯 红灯亮, 则系统不允许供料单元启动。
• (4) 当供料单元缺少物料超过3 s 后, 缺料警示灯黄灯亮起, 当无物料3 s 后, 警示灯红灯亮起。
• 2. 编写工序图, 编写程序梯形图 • 根据上述控制任务要求, 先编写供料单元工序图, 再编写相应的PLC
1 ~ 4 号和上排1 ~4 号端子短接经过带保险的端子与+24 V 相连。上 排5 ~19 号端子短接与0 V 相连, 如图3 -7 所示。
基于s7-1200系列PLC自动化生产线设计

广州城建职业学院毕业设计题目_基于S7-1200 PLC自动化生产线控制系统的设计_ 所在系机电与信息工程学院____专业班级 14机电一体化2班____学生姓名 _程广通_____ _学生学号__1409010202_指导老师曾一新 _____ _ __广州城建职业学院教务处制基于S7-1200 PLC自动化生产线控制系统的设计14机电一体化2班程广通指导老师:曾一新摘要基于S7-1200 PLC自动化生产线控制系统是加工、组装的一套结合工业案例,按工业标准设计,集成主流、常用工业控制设备的教学仪器。
该系统设备采用西门子应用于制造行业中的SIMATIC S7-1200为核心,配合工业总线通讯接口,集成变频器、人机界面、通信网络、多种传感器(颜色、姿势、材质辨别等),实现自动化技术相关专业中PLC应用技术教学、训练和考核。
设备包含:自动送料功能模块、传送带功能模块、自动检测功能模块、气动、电动机械手功能模块、PLC与变频器控制系统、直流调速模块、步进驱动模块、报警功能模块、人机界面PLC网络通讯系统、气动控制系统等,构成自动分拣与姿势调整的主从工作站。
关键词S7-1200;西门子;PLC;自动化生产线目录引言 (5)第一章基于S7-1200PLC自动化生产线控制系统的概述 (6)一、自动化生产线控制系统的现状与发展 (6)二、自动化生产线控制系统的组成 (7)三、自动化生产线控制系统运行模式分析 (7)第二章PLC结构和工作原理及相关知识介绍 (8)一、PLC组成与基本结构 (8)二、PLC的系统结构 (8)三、PLC的基本工作原理 (9)四、西门子S7-1200系列PLC功能特点 (9)五、开放式用户通信简介 (11)六、步进电机的结构及原理 (12)七、西门子MM420变频器介绍控制 (13)第三章基于S7-1200PLC自动化生产线控制系统方案设计 (16)一、系统的工作原理 (16)二、设计分析 (16)三、可行性分析 (17)四、可行性试验 (17)五、PLC的选择 (18)第四章PLC的硬件和硬件组态设置 (20)一、步进电机驱动器设置 (20)二、变频器参数设置 (20)三、硬件组态 (22)第五章系统硬件开发设 (26)一、硬件系统的结构 (26)二、控制系统I/O地址分配 (26)第六章系统软件控制设计 (28)一、控制要求 (28)二、梯形图编程流程图 (31)小结 (35)参考文献 (36)引言本论文是考虑到目前的自动化生产线发展的实际情况,现代化的自动生产设备是现今生产中最为普遍的生产方式,以及最有发展前景的生产方式,由本论文作者结合相关资料编写的一遍毕业论文。
自动化生产线装配与调试技术-——基于西门子S7-200系列PLC项目五

任务5.1 自动化生产线单元调试
• (1) 查接线。 • 要逐点进行, 要确保正确无误。可不带电核对, 那就是查线, 较麻烦。
也可带电查, 加上信号后, 看电控系统的动作情况是否符合设计的目的。 • (2) 检查模拟量输入输出。 • 看输入输出模块是否正确, 工作是否正常。必要时, 还可用标准仪器检
项目五 自动化生产线调试及维护
• 任务5.1 自动化生产线单元调试 • 任务5.2 自动化生产线总体调试操作
任务5.1 自动化生产线单元调试
• 对自动化生产线的调试, 是在完成自动化生产设备硬件安装后, 为了自 动化生产设备能够按照设计, 正常地完成设备自动化所需要的后期检 测及调整。同时, 自动生产线工作频繁, 为了保证生产线正常使用, 必 须进行维护保养。
上一页 下一页 返回
任务5. 2 自动化生产线总体调试操作
• 1. PPI 通信概述 • PPI 协议是S7 -200 系列PLC 最基本的通信方式, 通过自身的端口
(PORT0 或PORT1)就可实现通信。PPI 是一种主- 从协议通信, 主从站在一个令牌环网中, 主站发送要求到从站设备, 从站设备响应, 从 站不发送信息, 只是等待主站的要求并对要求做出响应。主站靠一个 PPI 协议管理的共享连接来与从站通信。PPI 并不限制与任意一个从 站通信的主站数量, 但在一个网络中, 主站个数不能超过32。如果在 用户程序中使用PPI 主站模式, 可以使用网络读写指令来读写从站信 息。 • 2. PPI 通信实现步骤 • (1) 设置通信端口参数。 • 对网络上的每一台PLC, 应设置其系统块中的通信端口参数。对用作 PPI 通信的端口(PORT0 或PORT1), 指定其PLC 地址(站号) 和波特 率。设置后把系统块下载到PLC。具体操作如下:
- 1、下载文档前请自行甄别文档内容的完整性,平台不提供额外的编辑、内容补充、找答案等附加服务。
- 2、"仅部分预览"的文档,不可在线预览部分如存在完整性等问题,可反馈申请退款(可完整预览的文档不适用该条件!)。
- 3、如文档侵犯您的权益,请联系客服反馈,我们会尽快为您处理(人工客服工作时间:9:00-18:30)。
一、引言上海大众汽车有限公司引进的德国SCHULER 6000KN大型自动化冲压线主要用来生产PASSAT轿车4门2盖等中型冲压件,平均冲次可达6.7次/分钟。
SCHULER冲压线主要由6个压机单元和6个机械化单元组成,压机单元主要用来进行料片冲压,机械化单元主要采用吸盘方式进行料片拆垛、压机之间料片传送等任务。
SCHULER自动化压机线的控制设备采用先进的西门子控制设备,整个自动化控制网络分为两级,第一级为基础自动化网络,它主要包括现场层SIEMENS 可编程控制器SIMATIC H1网络和操作员工作站WINCC网络;第二级为服务器控制管理层网络。
SCHULER压机线的整个工业控制网络系统较为复杂,由环形拓扑结构、星形拓扑结构、总线形拓扑结构三种拓扑结构类型的工业控制网络组合而成。
二、基础自动化网络2.1 现场层网络SCHULER 压机线现场层控制采用PLC和PROFIBUS现场总线控制。
每个压机单元和机械化单元各采用独立的PLC控制,PLC采用西门子S5-115U可编程控制器,整条压机线共使用了12个PLC进行控制。
2.1.1 PLC H1 网络服务器与现场层PLC通讯采用SIMATIC H1以太网络,CSMA/CD协议,光缆介质,通信速率为10Mbps,环形拓扑结构。
每单元PLC都配置有CP1430通讯模块,通过相应的OLM(光电转换模块)上网通讯,服务器内置CP1413通讯模块通过第一单元OLM模块与PLC H1网通讯。
在此服务器起到参数的上传/下送作用,它与PLC之间的数据交换通过DDF(动态数据交换)来进行。
使用光纤网不仅满足了高速大容量的数据交换,也大大增强了抗外界电磁场干扰以及抗泄漏的性能,环形结构的好处是一旦光纤网链路发生断裂,仍可保持通信;此外,它完全与电位无关地运行,不必花费昂贵的等电位连接费用,且大大增强了网络的可靠性。
2.1.2 PROFIBUS 总线PLC与现场设备的通迅采用西门子公司的PROFIBUS-DP现场总线,PROFIBUS-DP总线是一种全分布式现场总线型现场控制网络,它通过ET200分布式输入/输出系统与现场设备之间实现双向串行多节点数字通信。
单个分散的现场设备通过PROFIBUS总线连接成可以相互沟通信息、共同完成控制任务的网络系统和控制系统,形成控制功能彻底下放到现场的全分布网络集成式新型控制系统,它大大简化了现场布线并节省了安装费用。
ET200分布式输入/输出系统采用主栈和从栈结构, 主栈在总线上向从栈发送数据并向从栈索取数据, 从栈只有当主栈发出请求时才能与主栈进行数据交换。
在本控制系统的PROFIBUS现场总线中,内置总线接口控制板IM308-C的PLC作为总线的主栈,ET200 输入/输出模块作为总线的从栈,总线传输介质为屏蔽双绞线,PLC 通过PROFIBUS-DP实现对现场设备的控制。
2.2 操作员工作站WinCC网络操作员工作站通信网络采用10BASE-T以太网,TCP/IP开放协议,光缆介质,通信速率为10Mbps ,环形拓扑结构,具体配置为:每个压机单元各附有前后2个操作员工作站,SCHULER自动化压机线共有12个操作员工作站,工作站内置3COM网卡通过TPTR(以太网接口)及相应的OLM(光电转换模块)模块与以太网通讯,第一单元的OLM模块通过双绞线与HUB(中央集线器)相连,服务器内置3COM网卡与HUB相连,从而实现服务器与操作员工作站以太网络的通讯。
2.2.1 WinCC 组态软件操作员站的人机界面的画面组态采用西门子公司的SIMA TIC WinCC 4 .0工控组态软件。
SIMA TIC WinCC(Windows Control Center)是西门子公司开发的全32位的分布自动化控制组态软件,WinCC 作为一个监控组态软件具有强大功能以及高度开放性,可使用户设计出界面良好的、功能完善的监控系统;且由于它能在Windows标准环境下利用各Windows 的便利功能,可大为缩短开发生成过程软件包的时间。
WinCC软件主要包括数据采集和数据管理2个基本功能。
数据采集是指从现场采集数据并进行相应处理,采集主要由作为现场控制站的PLC完成。
数据管理是把从现场得到的数据进行处理后并把它送到服务器的数据库以及由数据库访问函数读取数据然后再送到应用中去。
2.2.2 WinCC网络在本系统中,服务器作为WinCC的Server,也作为SQL(结构化查询语言)Server(数据库服务器),它包括有运行数据库和工程数据库。
现场数据经PLC通过服务器送到WinCC 中进行采集和管理,经处理后,送到服务器的运行数据库;所有的模具及生产数据都储存在SQL服务器的工程数据库中,SQL服务器经过以太网连接到生产线的WinCC操作员站上,模具生产数据和现场数据在服务器或操作员站上以图形方式显示出来,实现监控。
在生产时,模具作业在选定后,WinCC操作站收到从SQL服务器来的模具生产所需要的生产数据,然后启动生产过程。
数据库总计可存有1000套模具数据,随时可以检索。
操作人员通过分别设在冲压线6个压机单元上的12个操作员站的WinCC人机界面可以监视每个压机单元及机械化单元的工作状态及故障报警显示,并可进行模具数据转换及生产数据设定等操作。
三、控制管理层网络压机线服务器通过10BASE-T中央集线器(HUB)与路由器(ROUTER)及操作员站以太网和PMS(压机生产管理系统)连成控制管理层星形网络。
3.1 网络操作平台服务器与操作员站采用服务器/客户机网络结构进行通讯。
服务器的操作平台是WinNT Server 4.0中文操作系统,操作员站的操作平台是Win NT Workstation 4 .0中文操作系统。
WinNT操作平台具有安全性、可靠性、多任务性等特点,并具有较好的软件兼容性,支持绝大多数Windows应用软件,为用户的工作提供很大的便利。
3.2 网络安全技术服务器作为SCHULER压机控制网络的中枢,服务器安全对保障整个压机线工业网络安全具有十分重要的意义,服务器采用硬件RAID(磁盘阵列)技术。
2.2.2 WinCC网络在本系统中,服务器作为WinCC的Server,也作为SQL(结构化查询语言)Server(数据库服务器),它包括有运行数据库和工程数据库。
现场数据经PLC通过服务器送到WinCC 中进行采集和管理,经处理后,送到服务器的运行数据库;所有的模具及生产数据都储存在SQL服务器的工程数据库中,SQL服务器经过以太网连接到生产线的WinCC操作员站上,模具生产数据和现场数据在服务器或操作员站上以图形方式显示出来,实现监控。
在生产时,模具作业在选定后,WinCC操作站收到从SQL服务器来的模具生产所需要的生产数据,然后启动生产过程。
数据库总计可存有1000套模具数据,随时可以检索。
操作人员通过分别设在冲压线6个压机单元上的12个操作员站的WinCC人机界面可以监视每个压机单元及机械化单元的工作状态及故障报警显示,并可进行模具数据转换及生产数据设定等操作。
三、控制管理层网络压机线服务器通过10BASE-T中央集线器(HUB)与路由器(ROUTER)及操作员站以太网和PMS(压机生产管理系统)连成控制管理层星形网络。
3.1 网络操作平台服务器与操作员站采用服务器/客户机网络结构进行通讯。
服务器的操作平台是WinNT Server 4.0中文操作系统,操作员站的操作平台是Win NT Workstation 4 .0中文操作系统。
WinNT操作平台具有安全性、可靠性、多任务性等特点,并具有较好的软件兼容性,支持绝大多数Windows应用软件,为用户的工作提供很大的便利。
3.2 网络安全技术服务器作为SCHULER压机控制网络的中枢,服务器安全对保障整个压机线工业网络安全具有十分重要的意义,服务器采用硬件RAID(磁盘阵列)技术。
2.2.2 WinCC网络在本系统中,服务器作为WinCC的Server,也作为SQL(结构化查询语言)Server(数据库服务器),它包括有运行数据库和工程数据库。
现场数据经PLC通过服务器送到WinCC 中进行采集和管理,经处理后,送到服务器的运行数据库;所有的模具及生产数据都储存在SQL服务器的工程数据库中,SQL服务器经过以太网连接到生产线的WinCC操作员站上,模具生产数据和现场数据在服务器或操作员站上以图形方式显示出来,实现监控。
在生产时,模具作业在选定后,WinCC操作站收到从SQL服务器来的模具生产所需要的生产数据,然后启动生产过程。
数据库总计可存有1000套模具数据,随时可以检索。
操作人员通过分别设在冲压线6个压机单元上的12个操作员站的WinCC人机界面可以监视每个压机单元及机械化单元的工作状态及故障报警显示,并可进行模具数据转换及生产数据设定等操作。
三、控制管理层网络压机线服务器通过10BASE-T中央集线器(HUB)与路由器(ROUTER)及操作员站以太网和PMS(压机生产管理系统)连成控制管理层星形网络。
3.1 网络操作平台服务器与操作员站采用服务器/客户机网络结构进行通讯。
服务器的操作平台是WinNT Server 4.0中文操作系统,操作员站的操作平台是Win NT Workstation 4 .0中文操作系统。
WinNT操作平台具有安全性、可靠性、多任务性等特点,并具有较好的软件兼容性,支持绝大多数Windows应用软件,为用户的工作提供很大的便利。
3.2 网络安全技术服务器作为SCHULER压机控制网络的中枢,服务器安全对保障整个压机线工业网络安全具有十分重要的意义,服务器采用硬件RAID(磁盘阵列)技术。
服务器采用DPT-RS3W RAID(磁盘阵列)站,外置的RAID硬盘柜把所有的RAID处理智能化统一到嵌在外置磁盘子系统的控制器中,全部的子系统通过一个SCSI 控制器联到主机上,RAID磁盘柜包括有3个硬盘:2个为镜像硬盘,1个为热备份硬盘。
在服务器系统采用磁盘镜像(RAID 1)技术, 服务器在处理数据时,同样的数据写在两个镜像硬盘中, 虽然数据冗余性较高,但由于并行处理两个磁盘,数据传输速率高,并提供了数据的高可信度;若工作中,一个硬盘在工作中发生故障,热备份硬盘会自动替换坏的硬盘,并且数据立刻从镜像硬盘拷贝到热备份硬盘上,系统在热备份硬盘上自动进行重建,从而磁盘阵列得到恢复,这样就大大提高了服务器网络系统运行的安全性,保障了生产的正常进行。
3.3 PMS系统为了更好实现对压机线的生产控制,压机线安装PMS系统(Rress Management System 压机生产管理系统),用于跟踪压机的生产情况及制定生产计划,系统通过CP1413网卡与PLC H1网络进行通讯,从PLC中获得数据进行数据采集,并将获得信息自动进行统计归类,从而获得压机线产量、生产时间、故障内容及时间的内容,为车间生产调度和管理提供参考。