炼油化工生产装置工程设计节能技术要求
浅析石化装置蒸汽管网的优化和节能技术

浅析石化装置蒸汽管网的优化和节能技术石化装置是石油化工行业的重要组成部分,是炼油厂和化工厂生产原料和产品的核心设备。
在石化装置中,蒸汽管网是一个至关重要的系统,它提供了供能、加热、冷却、压力和其他功能,是整个石化装置运行的动力源。
蒸汽管网的优化和节能技术对于石化装置的运行效率和生产成本具有重要意义。
一、蒸汽管网的优化1. 管网布局优化蒸汽管网的布局是影响其运行效率的关键因素之一。
合理的管网布局可以降低管道的阻力,减少能量损耗,提高管网的运行效率。
在设计蒸汽管网时,应该充分考虑设备位置、管道直径和长度等因素,合理规划管网的布局,减少管道弯头和支架的使用,使蒸汽流动更加顺畅。
2. 管道材质优化蒸汽管网的管道材质直接影响其运行效率和使用寿命。
选择合适的管道材质可以减少管道的阻力和损耗,降低维护成本。
在选择管道材质时,应该考虑其耐压性能、耐腐蚀性能和导热性能,根据具体的运行条件和要求选择合适的材质。
蒸汽管网中的管道系统包括管道、阀门、附件、管道支架等组成部分。
合理设计和选择这些组成部分可以降低管道的阻力和损耗,提高管网的运行效率。
在设计管道系统时,应该充分考虑流体的流动特性和运行要求,选择合适的阀门和附件,设计合理的支架结构,减少管道的挠曲和变形。
二、蒸汽管网的节能技术1. 蒸汽回收技术蒸汽回收技术是一种有效的节能技术,通过回收蒸汽的热量,将其用于加热和其他用途,可以降低蒸汽的消耗量,减少能源的浪费。
在蒸汽管网中,可以通过安装蒸汽回收装置,将冷凝后的蒸汽重新利用,提高能源利用率,降低生产成本。
2. 蒸汽动力系统优化蒸汽动力系统是石化装置中的重要能源消耗设备,通过优化蒸汽动力系统的设计和运行参数,可以降低蒸汽的消耗量,提高能源利用率。
在蒸汽动力系统中,可以通过优化锅炉燃烧控制、提高锅炉热效率、优化蒸汽轮机运行参数等方式,实现节能减排的目标。
3. 蒸汽管网智能控制蒸汽管网智能控制技术是一种先进的节能技术,通过实时监测和控制管网的运行参数,可以有效地提高管网的运行效率和稳定性,降低能源消耗。
石油化工装置节能优化分析及措施
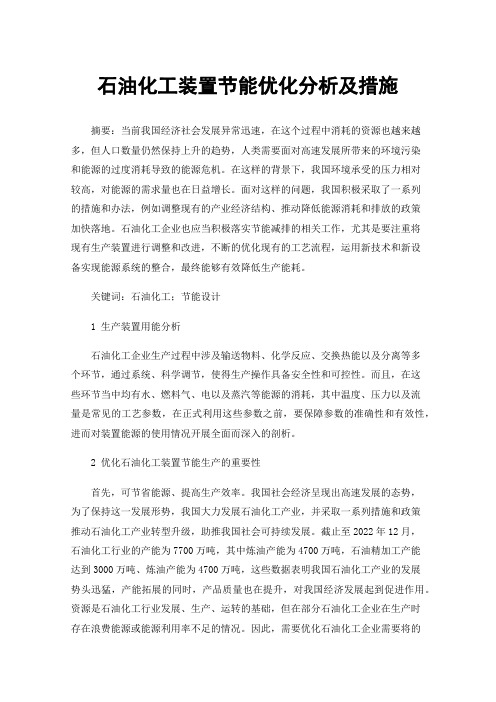
石油化工装置节能优化分析及措施摘要:当前我国经济社会发展异常迅速,在这个过程中消耗的资源也越来越多,但人口数量仍然保持上升的趋势,人类需要面对高速发展所带来的环境污染和能源的过度消耗导致的能源危机。
在这样的背景下,我国环境承受的压力相对较高,对能源的需求量也在日益增长。
面对这样的问题,我国积极采取了一系列的措施和办法,例如调整现有的产业经济结构、推动降低能源消耗和排放的政策加快落地。
石油化工企业也应当积极落实节能减排的相关工作,尤其是要注重将现有生产装置进行调整和改进,不断的优化现有的工艺流程,运用新技术和新设备实现能源系统的整合,最终能够有效降低生产能耗。
关键词:石油化工;节能设计1 生产装置用能分析石油化工企业生产过程中涉及输送物料、化学反应、交换热能以及分离等多个环节,通过系统、科学调节,使得生产操作具备安全性和可控性。
而且,在这些环节当中均有水、燃料气、电以及蒸汽等能源的消耗,其中温度、压力以及流量是常见的工艺参数,在正式利用这些参数之前,要保障参数的准确性和有效性,进而对装置能源的使用情况开展全面而深入的剖析。
2 优化石油化工装置节能生产的重要性首先,可节省能源、提高生产效率。
我国社会经济呈现出高速发展的态势,为了保持这一发展形势,我国大力发展石油化工产业,并采取一系列措施和政策推动石油化工产业转型升级,助推我国社会可持续发展。
截止至2022年12月,石油化工行业的产能为7700万吨,其中炼油产能为4700万吨,石油精加工产能达到3000万吨、炼油产能为4700万吨,这些数据表明我国石油化工产业的发展势头迅猛,产能拓展的同时,产品质量也在提升,对我国经济发展起到促进作用。
资源是石油化工行业发展、生产、运转的基础,但在部分石油化工企业在生产时存在浪费能源或能源利用率不足的情况。
因此,需要优化石油化工企业需要将的装置,使得石油化工装置在降低能源损耗的同时,也能够提高生产的效率,降低生产成本,将节省出来的资金投入到提高生产质量中。
炼油常减压装置特点及节能新技术

炼油常减压装置特点及节能新技术摘要:常减压装置能够回收余热、降低过剩空气系数,本文对如何控制常减压装置的能耗展开研究,分析常减压装置的特性,然后分析当前可以采取的技术措施。
通过研究帮助工厂解决常减压装置的运行能耗问题,提升综合效益。
关键词:常减压装置;特点;技术;应用引言:现代炼油厂为了保证工作的顺利进行,会使用常减压装置开展工作。
但是常减压装置同样有耗能较大的问题,为了保证生产的顺利进行,需要使用有效的技术,控制常减压装置的能耗。
1炼油常减压装置特性分析1.1加强烟气余热回收使用常减压装置能够回收炼油厂的烟气余热,常减压装置的余热回收系统会包括高温段空气预热器、低温段空气预热器两种装置,在高温段使用了高效的导热元件是,低温段使用双向板翅预热器[1]。
通过使用这些装置,常减压装置能够有效控制烟气余热所导致的露点腐蚀问题,控制烟气温度在130℃的安全范围以内。
通过使用常减压装置,其中的余热回收系统可以有效利用炼油系统的余热,解决温度浪费问题,并降低炼油系统的能耗临。
目前一般使用冷凝技术进行烟气的低温余热回收,可以有效提升热炉的热反应效率。
1.2减少过剩空气炼油厂工作中,如果剩余的空气系数比较小,加热炉内部的燃烧就会缺少足够的空气,很难满足加热炼油的要求,不仅会造成工作效率降低,还会释放出比较多的废物,对环境造成比较严重的损害。
但是如果盲目提升空气系数,过剩的空气就会将炉内多余的热量带走,同样会导致炼油设备热强度不能达标的问题,还会严重影响系统的热传递效率,也会缩短锅炉的使用寿命,以及造成空气污染。
为了解决上述问题,在目前的炼油工作中会使用常减压设备将空气系数控制在合理的范围内。
工作人员在点燃火嘴含氧量会比较高,常减压设备也会同时对气压进行调节,让设备的火焰能始终处于燃烧的状态下,并保证锅炉温度保持正常,工作人员通过随时控制常减压设备可以进行工作方式的调节,让炉内的空气系数保持最佳的运行状态。
1.3能源消耗大在目前的炼油厂生产中,常减压设备的装置会占据比较大的能源消耗,普遍超过了30%,在很多炼油厂重,常减压设备已经成为了最为主要的生产成本要素。
化工工艺节能降耗技术措施

化工工艺节能降耗技术措施随着全球环境问题的日益严峻,化工行业也面临越来越严格的环保要求。
为了实现可持续发展,化工生产必须实现节能降耗。
以下是一些化工工艺节能降耗技术措施:1、改进化工工艺流程化工工艺流程的优化是降低能耗和生产成本的一项重要举措。
通过改进化工工艺流程,化工厂可以降低原材料消耗、排放废水废气以及节省能源。
其中,更加高效的反应技术和分离技术有助于提高化工生产的能源利用效率。
此外,化工厂还可以采用智能化控制和监控技术对生产过程进行实时监控和调整,从而实现生产过程的优化控制。
2、改造设施和设备化工厂设施和设备升级换代是提高化工生产的能源利用效率的另一种途径。
化工厂可以对设备进行改造,采用更加节能的技术。
例如,采用高效节能的电机和变频器,减少输送和循环泵的能耗,以及采用节能型热交换器等。
此外,化工厂还可以通过重新设计设施和建筑结构,改进传统的制造方式以及推广建筑节能技术等来实现节能降耗。
3、开发新型节能产品和材料新型节能产品和材料的研发与应用是化工生产实现节能降耗目的的另一种途径。
例如,采用高效的产物回收材料,如烷基化洗油等可有效减少废料和污染物产生。
此外,利用新型高效催化剂、催化反应条件设计的提高等,也是提高化工生产能源利用效率的重要手段。
另外,新型的绿色材料也有望在化工生产中得到广泛应用,换用生态友好型材料与节能材料会减少化工生产中的资源流失、环境污染等问题。
4、减少废弃物的产生和处理降低化工生产中废料的产生和处理,同样也是实现化工生产节能怀进的重要策略。
去除无用废料后,可将大量资源和能源释放出来,例如,在炼油生产过程中,减少或避免燃烧过程中废气的产生,可有效节约能源和减少污染物的产生。
此外,化工厂在余热利用方面的进展也是一个不可忽视的方向。
未被充分利用的高温排放在经过一系列的废热回收喜误处理技术后,可以有效地将废热再利用于化工厂的自身生产过程、再生产品制造过程、城市供热系统等。
这不仅能够循环利用资源,减少废弃物的产生,而且还有助于降低化工生产成本。
炼化企业节能降耗技术措施探讨

炼化企业节能降耗技术措施探讨摘要:随着全球人口的不断增加和工业生产方式的不断进步,传统的炼化生产方式无论是在技术层面,还是在成本层面都越来越难以适应炼化行业的发展要求。
因此,本文就针对炼化企业的节能降耗进行分析,为炼化企业的良好发展提供保障。
关键词:炼化企业;节能降耗;技术措施一、炼油化工概述炼化企业主要通过对原油进行加工炼制生产汽油、柴油等石油产品获取利润。
通常而言,炼油企业在钻井平台获取原油后,处于石油化工生产的第二阶段。
在炼油化工过程中,炼化企业会以蒸馏的方式对原油进行精炼,将处于极端环境中的原油分离成不同的烃类。
在炼化企业炼制原油,使原油组分分离后,炼化企业可以生产各类石油产品,如汽油、柴油、煤油、润滑剂、沥青等,再将这类石油化工产品售卖至各个行业,可以发挥极大的用途。
以润滑剂为例,在蒸馏过后,润滑剂可以即刻向工厂出售,其他产品也可在精炼后向其余厂家售卖,一家大型炼化企业每日可对数十万桶原油进行加工处理,生产上万吨石油化工产品。
在整个炼化过程中,通常将炼油环节视为“下游”部门,原油产地,即油田则被视为“上游”部门。
同时,“下游”这一术语还与炼油环节在石油化工产品价值链中的作用相关,除了对原油进行精炼之外,炼化企业还要与相关企业、政府部门等石油产品需求者进行沟通。
美国能源情报署(EIA)相关研究表明,截至目前,全球每日约有1亿桶原油经过炼化企业加工,生产汽油、馏分燃料等石油化工产品数百万吨,即便如此,却仍然难以满足全球范围内对石油化工产品的大量需求,炼化企业还需进一步提升其生产效率。
二、“双碳”目标下炼化企业面临的形势(一)市场驱动炼油向化工转型国内成品油市场受“双碳”政策影响,产品结构不断调整。
同时,受节能减排技术不断提高及替代能源快速发展的影响,成品油需求量增速逐渐放缓。
据预测,我国汽油需求将于“十四五”末期达到峰值,煤油需求在2040年前后达到峰值,柴油消费已处于达峰后期。
我国化工产品需求量增长空间巨大,预计2035年后达峰。
炼油化工企业节能降耗技术分析
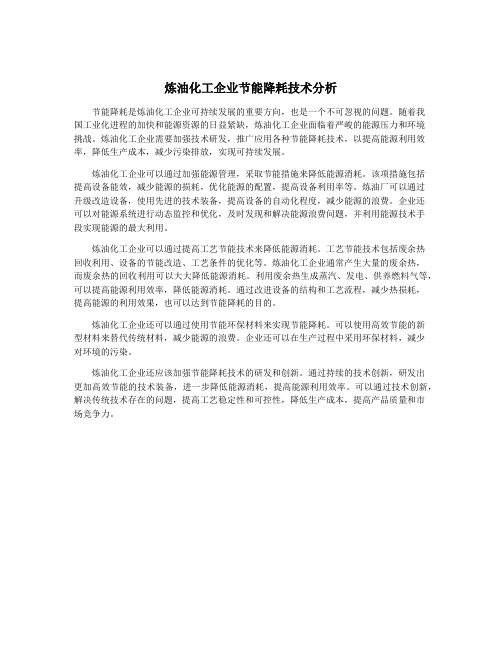
炼油化工企业节能降耗技术分析节能降耗是炼油化工企业可持续发展的重要方向,也是一个不可忽视的问题。
随着我国工业化进程的加快和能源资源的日益紧缺,炼油化工企业面临着严峻的能源压力和环境挑战。
炼油化工企业需要加强技术研发,推广应用各种节能降耗技术,以提高能源利用效率,降低生产成本,减少污染排放,实现可持续发展。
炼油化工企业可以通过加强能源管理,采取节能措施来降低能源消耗。
该项措施包括提高设备能效,减少能源的损耗,优化能源的配置,提高设备利用率等。
炼油厂可以通过升级改造设备,使用先进的技术装备,提高设备的自动化程度,减少能源的浪费。
企业还可以对能源系统进行动态监控和优化,及时发现和解决能源浪费问题,并利用能源技术手段实现能源的最大利用。
炼油化工企业可以通过提高工艺节能技术来降低能源消耗。
工艺节能技术包括废余热回收利用、设备的节能改造、工艺条件的优化等。
炼油化工企业通常产生大量的废余热,而废余热的回收利用可以大大降低能源消耗。
利用废余热生成蒸汽、发电、供养燃料气等,可以提高能源利用效率,降低能源消耗。
通过改进设备的结构和工艺流程,减少热损耗,提高能源的利用效果,也可以达到节能降耗的目的。
炼油化工企业还可以通过使用节能环保材料来实现节能降耗。
可以使用高效节能的新型材料来替代传统材料,减少能源的浪费。
企业还可以在生产过程中采用环保材料,减少对环境的污染。
炼油化工企业还应该加强节能降耗技术的研发和创新。
通过持续的技术创新,研发出更加高效节能的技术装备,进一步降低能源消耗,提高能源利用效率。
可以通过技术创新,解决传统技术存在的问题,提高工艺稳定性和可控性,降低生产成本,提高产品质量和市场竞争力。
炼油化工企业节能降耗技术分析

炼油化工企业节能降耗技术分析炼油化工企业是我国经济中的重要产业,但在生产过程中,能源消耗占据了相当大的比重。
为了实现可持续发展,提高能源利用效率是非常重要的。
节能降耗技术在炼油化工企业中的应用,有助于减少能源消耗、改善生产效率,降低污染排放,提高企业核心竞争力。
1. 废热利用技术炼油化工过程中的废热含量很高,如果能利用这些废热,将能够大幅度减少能源消耗。
目前,常用的废热利用技术包括:余热锅炉、余热回收系统、蒸汽排烟器、热泵等。
废热锅炉是企业中较为常见的废热利用设备,它能够将废热转化为蒸汽、热水等热能,再把它们送回生产过程中重复利用。
2. 节能设备炼油化工生产过程中,大量机械设备需要用电来驱动。
而节能设备的应用能够大幅度降低用电量,达到节能的效果。
例如,智能逆变器、伺服电机等,能够根据设备的负荷情况,调整驱动电力的大小,从而达到省电、减少能源消耗的效果。
此外,选择高效率的设备也是企业实现节能降耗的有效途径。
3. 低温分馏技术传统的分馏技术,大多是采用高温方式将原油或石化产品分离出各种成分。
而低温分馏技术则可以在低温下进行分离,这样能够达到节能降耗的效果。
低温分馏技术包括:冷凝回收技术、凝汽吸收技术、气液膜分离技术等,这些技术能够将重复利用的材料进行分离和回收,减少废料和排放,完成节能降耗目标。
4. 空气压缩节能技术炼油化工企业中广泛使用的空气压缩机消耗较多的电力,同时也会产生大量的热能。
空气压缩节能技术可以在压缩空气的同时,回收并再利用压缩时产生的热能,节约电力消耗。
比如空气动力润滑系统、变频控制技术、精细化压缩技术等,这些技术既能提高空气压缩效率,又可以实现能源的回收利用。
总的来说,炼油化工企业的节能降耗是一项长期、系统性的工程。
企业需要在产品技术上不断创新,完善生产流程,降低能源和资源的消耗,同时加强员工教育,提高对节能降耗的认识,全员参与,共同推进节能降耗工作的开展。
炼油化工企业的节能降耗技术
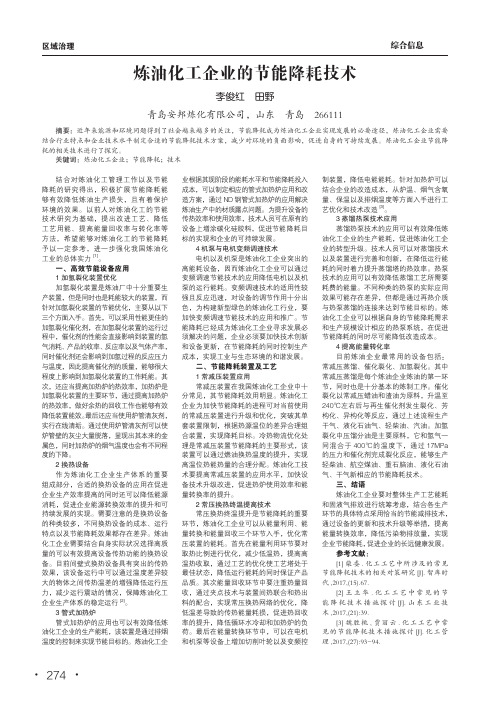
区域治理综合信息炼油化工企业的节能降耗技术李俊红 田野青岛安邦炼化有限公司,山东 青岛 266111摘要:近年来能源和环境问题得到了社会越来越多的关注,节能降耗成为炼油化工企业实现发展的必要途径,炼油化工企业需要结合行业特点和企业技术水平制定合适的节能降耗技术方案,减少对环境的负面影响,促进自身的可持续发展。
炼油化工企业节能降耗的相关技术进行了探究。
关键词:炼油化工企业;节能降耗;技术结合对炼油化工管理工作以及节能降耗的研究得出,积极扩展节能降耗能够有效降低炼油生产损失,且有着保护环境的效果。
以前人对炼油化工的节能技术研究为基础,提出改进工艺、降低工艺用能、提高能量回收率与转化率等方法,希望能够对炼油化工的节能降耗予以一定参考,进一步强化我国炼油化工业的总体实力[1]。
一、高效节能设备应用1加氢裂化装置优化加氢裂化装置是炼油厂中十分重要生产装置,但是同时也是耗能较大的装置,而针对加氢裂化装置的节能优化,主要从以下三个方面入手。
首先,可以采用性能更佳的加氢裂化催化剂,在加氢裂化装置的运行过程中,催化剂的性能会直接影响到装置的氢气消耗、产品的收率、反应率以及气体产率,同时催化剂还会影响到加氢过程的反应压力与温度,因此提高催化剂的质量,能够很大程度上影响到加氢裂化装置的工作耗能。
其次,还应当提高加热炉的热效率,加热炉是加氢裂化装置的主要环节,通过提高加热炉的热效率,做好余热的回收工作也能够有效降低装置能效。
最后还应当使用炉管清灰剂,实行在线清垢。
通过使用炉管清灰剂可以使炉管壁的灰尘大量脱落,显现出其本来的金属色,同时加热炉的烟气温度也会有不同程度的下降。
2换热设备作为炼油化工企业生产体系的重要组成部分,合适的换热设备的应用在促进企业生产效率提高的同时还可以降低能源消耗,促进企业能源转换效率的提升和可持续发展的实现。
需要注意的是换热设备的种类较多,不同换热设备的成本、运行特点以及节能降耗效果都存在差异。
化工装置工艺节能技术和综合能耗计算
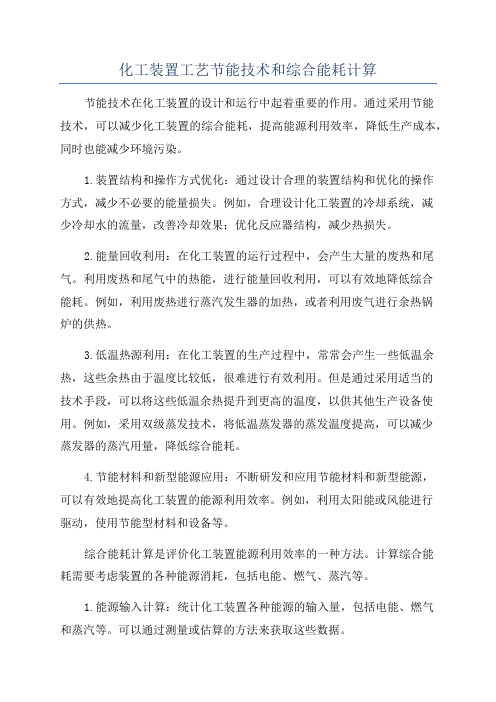
化工装置工艺节能技术和综合能耗计算节能技术在化工装置的设计和运行中起着重要的作用。
通过采用节能技术,可以减少化工装置的综合能耗,提高能源利用效率,降低生产成本,同时也能减少环境污染。
1.装置结构和操作方式优化:通过设计合理的装置结构和优化的操作方式,减少不必要的能量损失。
例如,合理设计化工装置的冷却系统,减少冷却水的流量,改善冷却效果;优化反应器结构,减少热损失。
2.能量回收利用:在化工装置的运行过程中,会产生大量的废热和尾气。
利用废热和尾气中的热能,进行能量回收利用,可以有效地降低综合能耗。
例如,利用废热进行蒸汽发生器的加热,或者利用废气进行余热锅炉的供热。
3.低温热源利用:在化工装置的生产过程中,常常会产生一些低温余热,这些余热由于温度比较低,很难进行有效利用。
但是通过采用适当的技术手段,可以将这些低温余热提升到更高的温度,以供其他生产设备使用。
例如,采用双级蒸发技术,将低温蒸发器的蒸发温度提高,可以减少蒸发器的蒸汽用量,降低综合能耗。
4.节能材料和新型能源应用:不断研发和应用节能材料和新型能源,可以有效地提高化工装置的能源利用效率。
例如,利用太阳能或风能进行驱动,使用节能型材料和设备等。
综合能耗计算是评价化工装置能源利用效率的一种方法。
计算综合能耗需要考虑装置的各种能源消耗,包括电能、燃气、蒸汽等。
1.能源输入计算:统计化工装置各种能源的输入量,包括电能、燃气和蒸汽等。
可以通过测量或估算的方法来获取这些数据。
2.能源产出计算:统计化工装置各种产品的产量,并计算其对应的能量产出。
例如,对于炼油装置,可以统计原油加工量和各种产品的产量,并计算原油和产品之间的能量差。
3.能源消耗计算:根据能源输入和能源产出的数据,计算化工装置的能源消耗量。
通常可以采用能效指标来表示能源利用效率,例如能源消耗量与产量之比。
4.综合能耗计算:将化工装置各个部分的能源消耗累加,得到整个装置的综合能耗。
可以通过比较不同装置的综合能耗来评价其能源利用效率。
炼油化工企业节能降耗技术分析

炼油化工企业节能降耗技术分析【摘要】炼油化工企业在当今环境保护意识日益增强的背景下,节能降耗技术显得尤为重要。
本文分析了当前炼油化工企业的现状,以及节能和降耗技术的应用情况。
针对设备更新改造和管理措施方面,提出了一些有效的建议。
通过对炼油化工企业节能降耗技术的重要性进行探讨,展望了未来技术应用的前景。
最后总结强调了节能降耗技术在炼油化工企业中的重要性,并提出了一些建议,以期更好地推动炼油化工企业节能降耗技术的发展。
通过这些措施,可以更好地实现能源利用的最大化,降低企业的生产成本,同时也为环境保护作出积极的贡献。
【关键词】炼油化工企业、节能、降耗、技术分析、现状、节能技术、降耗技术、设备更新、改造、管理措施、重要性、展望、建议、总结。
1. 引言1.1 炼油化工企业节能降耗技术分析炼油化工企业是能源消耗的重要行业,其生产过程中需要大量的能源支持。
随着能源资源日益紧张和环境污染日益严重,炼油化工企业必须重视节能降耗技术的应用。
节能降耗不仅可以减少企业的能源消耗和生产成本,也可以减少对环境的污染,符合可持续发展的要求。
炼油化工企业的节能技术包括了从原料选择、生产工艺优化到设备更新改造等多个方面。
优化生产工艺和设备更新改造是节能降耗的重要手段。
通过采用先进的生产工艺和高效的设备,可以最大程度地提高能源利用效率,降低能源消耗。
管理措施也是炼油化工企业节能降耗的重要一环。
建立健全的能源管理体系,加强对能源消耗情况的监测和分析,制定科学的节能降耗措施,对实施效果进行评估和调整,可以帮助企业有效地实现节能降耗目标。
炼油化工企业节能降耗技术的应用是非常重要的。
未来,随着技术的不断进步和政策的支持,炼油化工企业在节能降耗方面将迎来更好的发展前景。
为此,企业需要加大技术创新力度,不断提升节能降耗水平,以实现可持续发展的目标。
2. 正文2.1 现状分析炼油化工企业是能源消耗大、排放量高的行业,面临着严峻的能源和环境压力。
炼油化工厂节能技术
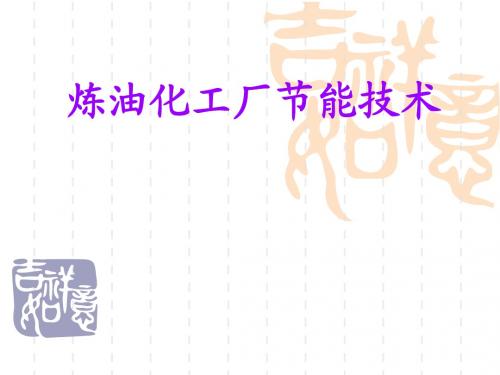
能量升级利用技术
炼油化工厂中,在装置进行工艺和换热网络优化 后,仍有许多低温热排出系统。这些低温热的回收 利用是石油化工厂深化节能的一个重要方面。 对于炼油厂,空冷、水冷余热大多分布在 90~200℃之间,约占总余热量的55.4%。
对于化工厂,空冷、水冷余热大多分布在 60~90℃区间,约占总余热的70%。而这些低温热 量回收利用的好坏对“三环节能量流结构理论”,把整个 系统分为能量转换环节、能量利用环节和能量回收 环节,其中利用环节是核心。工艺总用能是整个过 程系统的核心能量指标
通过优化运行实现炼油厂节能降耗的技术思路:在 四个层面展开:优化工艺装置内部;装置间热联合; 低温热优化利用,优化蒸汽动力系统,火用经济调 优。
三、提高能量回收率,减少排弃能量及火用损
1.减少散热量 2.优化换热系统减少传热 火用损 3.降低冷却排弃能
四、提高能量转换环节效率,减少装置供入能耗
1.停用或合用加热炉 2.提高加热炉效率 3.采用自动调速设施 4.合理选择蒸汽动力的驱动方式 5.催化裂化再生器排烟能量的回收利用
优化运行节能降耗的主要技术
单位:MJ/t原油 (万kcal/t原油)
ηU = 86.91% ;
ηT=9.73% ; ηR =64.5% ;
EN=1178.6MJ/t
图4-5 某炼厂联合装置常减压1980年7月能流图
综上所述,石油化工节能技术改进是有规 律可循的,以用能分析三环节模型为基础的节能 改进方法,反映了这种客观规律及节能改进各用
过程工艺的系统节能思路
工艺装置 装置间热联合 低温热利用 蒸汽动力系统 火用经济学的技术经济分析 实施下一个循环 优化过程完成
2、通过运行优化的节能技术应用
工艺装置内部的运行优化:
炼油化工企业节能降耗技术分析

炼油化工企业节能降耗技术分析炼油化工企业是国民经济的重要组成部分,其生产活动对能源资源的消耗非常大,因此如何提高能源利用效率,降低能源消耗,是炼油化工企业一直在探讨和努力的问题。
为了实现可持续发展,保护环境,节能降耗已经成为炼油化工企业的必然选择。
本文将就炼油化工企业节能降耗技术进行分析,并结合实际案例进行说明。
一、炼油化工企业能耗现状炼油化工企业在生产过程中,主要能源消耗集中在原料加工、反应分离、产品制造等生产环节,同时还伴随着供热供冷、输送系统等辅助设施的能源消耗。
根据国家统计局数据显示,2019年中国炼油化工行业规模以上企业能源消耗总量为4.18亿吨标准煤,约占全国工业总能源消耗的12.9%。
与此炼油化工企业在生产过程中也面临着原料资源的浪费和排放污染的问题。
由于传统生产方式存在能源浪费、排放多等问题,才有必要采取相应措施,以实现节能降耗。
二、节能降耗技术分析1. 节能技术(1)高效换热技术炼油化工企业在高温高压条件下进行加工反应,需消耗大量热能。
采用高效换热技术,可以有效提高能量利用率。
采用先进的换热设备,如板式换热器、壳管式换热器等,能够实现热量的充分利用,减少低温废热的损失,从而降低能源消耗。
(2)蒸汽系统优化蒸汽是炼油化工企业生产过程中常用的热能介质。
蒸汽系统的运行状态直接关系到能源的利用效率。
采用蒸汽系统优化技术,可以通过合理的管道设计、减少蒸汽泄漏、提高蒸汽的回收利用率等手段,降低燃料消耗,提高热能利用效率。
(3)节能调度管理通过对设备的能耗进行综合分析和调度,合理调配生产过程中的能量消耗,做到能量平衡,避免资源浪费。
采用先进的监测和控制系统,实现对能耗的实时监测和调整,最大限度地降低能源消耗。
2. 减排技术(1)脱硫脱硝技术炼油化工企业在生产过程中会产生大量的氧化硫和氮氧化物等废气排放,对环境造成污染。
采用脱硫脱硝技术,可以有效降低废气中有害物质的排放,减少对环境的影响。
(2)废水处理技术炼油化工企业生产过程中会产生大量的废水,包括含油废水、含盐废水、高浓度废水等,严重影响水资源的环境质量。
炼油化工工程项目规范

炼油化工工程项目规范征求意见稿目次1 总则 (1)2 基本规定 (2)2.1目标与功能 (2)2.2通用要求 (3)2.3环境保护 (5)2.4职业安全卫生 (6)3 选址布局与总平面布置 (9)4 生产装置及系统单元 (14)4.1一般规定 (14)4.2装置布置及管道 (14)4.3泄压排放系统 (18)4.4控制系统 (18)4.5给排水系统 (19)4.6电气系统 (19)4.7热力系统 (21)4.8其他 (21)5 储运设施 (22)5.1罐区一般规定 (22)5.2可燃液体储罐区 (22)5.3液化烃、可燃气体、助燃气体储罐罐区 (24)5.4可燃液体、液化烃装卸车设施 (25)6 辅助生产设施 (26)6.1一般规定 (26)6.2中心控制室 (27)6.3中心化验室与环境监测站 (28)6.4厂房与仓库 (28)6.5三废处理设施 (28)7 应急救援设施 (30)7.1消防系统 (30)7.2消防站及气体防护站 (32)7.3应急救援物资及人员防护装备 (32)1 总则1.0.1 为在炼油化工工程项目建设中保障人身健康和生命财产安全、工程安全、生态环境安全、促进能源资源节约利用以及满足经济社会管理等基本需要,制定本规范。
1.0.2 以石油、天然气、煤及其产品为原料,生产、储运各种炼油化工产品的工程项目规划、建设、维修及拆除,必须执行本规范。
本规范未做规定的应符合国家现行有关通用规范的规定。
1.0.3 工程建设所采用的技术方法和措施是否符合本规范要求,由相关责任主体判定。
其中,创新性的技术方法和措施,应进行论证并符合本规范中有关性能的要求。
2 基本规定2.1 目标与功能2.1.1 炼油化工工程项目应符合下列目标要求:1 符合国家技术经济发展战略与能源发展规划;2 保障人身健康和生命财产安全,保障社会公共安全,将个人风险和社会风险控制在可接受范围内;3 以本质安全为主导,将事故风险控制到尽可能低的合理水平;4 维护生态环境安全,促进清洁生产,有效控制大气、水体、土壤、噪声等污染,符合污染物排放和环境质量要求;5 合理利用资源,促进低碳循环经济和可持续发展。
炼油化工企业节能降耗技术分析

炼油化工企业节能降耗技术分析
炼油化工企业作为重要的能源制造业企业,对能源的消耗量较大,因此要想降低能源消耗,提高能源利用效率,必须要采用一些节能降耗技术。
本文将重点分析炼油化工企业常用的节能降耗技术。
炼油化工企业可以通过采用先进的设备和工艺技术来实现节能降耗。
采用反应器内换热器技术能够将高温产物中的热能转移到需要加热的介质中,提高能源利用效率。
还可以采用节能热交换装置来实现热能的回收利用,例如利用废热锅炉等设备进行余热回收,降低能源消耗。
炼油化工企业还可以通过优化流程和管理来实现节能降耗。
合理调整生产流程,减少能源的损耗,提高生产效率。
加强能源管理,建立能源指标制度,定期检查和评估能源消耗情况,以及制定合理的能源管理措施,都能够有效地降低能源消耗。
炼油化工企业可以通过开展节能技术研究和推广应用来实现节能降耗。
开展新型催化剂和催化剂再生技术研究,提高催化剂的利用率和寿命,降低炼油和化工过程中的能源消耗。
加强技术交流和合作,推广应用节能技术,促进企业之间的经验分享,也能够带动整个行业的能源消耗降低。
炼油化工企业还可以通过利用清洁能源来实现节能降耗。
使用天然气取代传统的燃煤和重油,可以降低炉膛内的燃烧温度,减少氮氧化物的生成,达到降低能源消耗的目的。
可以逐步推广使用太阳能、风能等可再生能源,减少对传统能源的依赖。
炼油化工企业节能降耗技术可以从设备和工艺技术优化、流程和管理优化、节能技术研究和推广应用以及利用清洁能源等方面入手。
通过采取这些措施,可以有效地降低炼油化工企业的能源消耗,提高能源利用效率,实现可持续发展。
石油化工行业节能与环保技术研究和应用

石油化工行业节能与环保技术研究和应用石油化工行业是支持现代产业和人们生活的关键性行业之一,其产品覆盖能源、金属、建材、化工、环保等各个领域。
然而,在实现高速发展的同时,石油化工行业也面临着严峻的环境和资源压力。
为了舒缓环境压力,发展石油化工行业节能和环保技术,成为了现代社会的迫切需要。
一、节能技术研究和应用节能在石油化工行业中的重要性不言而喻,通过采用节能技术来减少能源消耗,不仅能够降低企业的能耗成本,还能降低企业排放的温室气体,起到环保的作用。
1. 设备节能技术在生产设备方面,石化企业可以采用多种节能技术,以减少能源消耗。
其中,提高设备的自动化水平,是实现节能的重要手段。
比如,在生产过程中,可以采用自动监测、预测和控制技术,实现对生产设备进行全面、实时、精准的控制和调整,从而有效提高生产效率,达到节能的目的。
此外,还可以采用优化设计技术,提高设备的节能性能。
比如,在承受高温高压环境的条件下,通过提高设备的密封性和耐腐蚀性等重要性能指标,有效减少设备的能源消耗,实现节能的目的。
2. 生产工艺节能技术除了设备方面,石油化工企业还可以通过改进和优化生产工艺来实现节能。
比如,在炼油和化工生产中,采用高效节能的蒸汽回收技术,可以有效地降低能源消耗。
此外,还可以根据生产的具体情况,采用污水回用技术、废气再利用技术等,实现废弃物资源化,达到节能的目的。
此外,在催化剂的制备和运用过程中,也可以通过优化催化材料的结构、表面性质等方面的设计和改进,提高催化剂的活性和选择性,实现更高的生产效率和更好的环保效果。
二、环保技术的研究和应用石油化工企业的生产过程中,排放物质污染和能源的浪费问题都非常严重。
为了打破这种局面,石油化工企业必须采取环保技术,把环境保护凸显在企业的经营管理中。
1. 先进控制技术在石油化工生产过程中,为达到最佳的生产效率和最好的环境保护效果,可以采用先进的控制技术,如模型预测控制技术(MPC)和建模控制技术等。
炼油厂常减压装置节能新技术措施分析

炼油厂常减压装置节能新技术措施分析炼油厂常减压装置是石油化工生产中的重要设备,用于对裂化汽油、重油等石油产品进行降压处理,以满足生产和加工的需要。
在炼油厂常减压装置的操作过程中,能耗问题一直是一个亟待解决的难题,炼油厂常减压装置的节能新技术措施显得十分重要。
本文将对炼油厂常减压装置的节能新技术措施进行深入分析,以期为炼油厂的节能工作提供有益的参考。
一、加强装置的热力系统优化在炼油厂常减压装置的运行过程中,热力系统是一个非常重要的方面。
热力系统的效率直接关系到能源的利用程度,加强装置的热力系统优化是一个非常重要的节能技术措施。
在优化热力系统方面,可以采取以下措施:1. 合理设计热力系统结构合理设计热力系统的结构,包括进料、出料、介质循环等部分,以确保热能传递的高效率和稳定性。
2. 优化换热设备优化换热设备的设计和工艺,采用高效、节能的换热器,提高换热效率,减少能源损耗。
3. 提高热力系统的控制精度提高热力系统的控制精度,采用先进的自动控制技术,实现热力系统的智能化运行,减少人为干预,提高能源利用效率。
二、采用先进的节能设备在炼油厂常减压装置的操作过程中,各种设备都会消耗大量的能源,采用先进的节能设备是一个非常重要的节能新技术措施。
在采用先进的节能设备方面,可以从以下几个方面进行改进:1. 采用高效的压缩机采用高效的压缩机设备,能够有效地提高设备的压缩效率,减少能源损耗。
1. 优化操作参数通过优化操作参数,调整装置的运行方式,提高系统的整体效率,减少能源损耗。
2. 改进产品分离工艺改进炼油厂常减压装置的产品分离工艺,提高产品的分离效率,减少能源消耗。
3. 加强系统的监控与管理加强系统的监控与管理,实施全面的巡检和检修,及时发现并解决设备运行中存在的问题,确保系统的稳定运行。
四、提高员工的技术水平1. 开展技术培训开展特色化的技术培训,提高员工的技术水平,使其能够更好地掌握先进的节能技术知识和应用技能。
节能标准信息
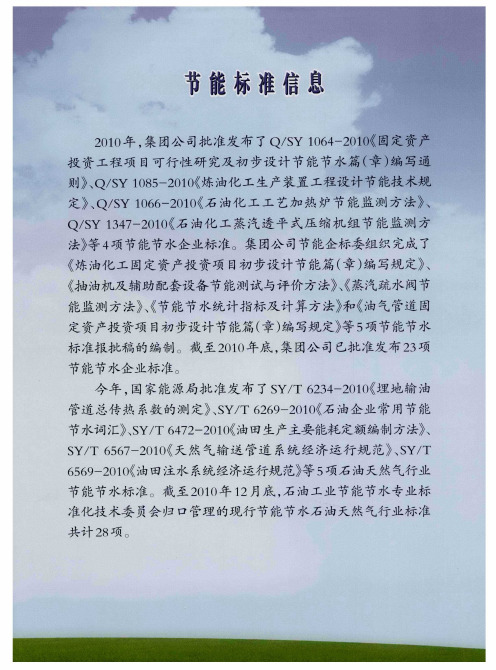
21年 , 00 集团公 司批准发布 了Q/Y 16— 00 固定资产 S 04 21{
投 资工程 项 目可行 性研 究及初 步设 计 节能 节水篇 ( ) 写通 章 编
则》 Q/Y l8 — O 炼 油化 工 生产装置 工程设计 节能技 术规 、 S O 5 2 l ̄ O
节 能 节 水标 准 。截 至 2 1 年 1 月底 , 油 工 业 节 能 节 水 专 业标 0 0 2 石 准化 技 术委 员会 归 口管理 的现 行 节 能 节水 石 油天 然 气行 业标 准
共计 2 项 , 8 、
节水词汇》s T6 7 — (( 油田生产主要 能耗 定额编制方法》 、Y/ 42 2 1《 )) 、
s / 57 2 l ( Y T 66 — o o  ̄然 气输 送 管道 系统 经 济运行 规 范》 s / 、Y T
66— OO5 59 2 l(  ̄田注水 系统经济运行规 范》 5 等 项石 油天然气行业
定》 Q/Y 16 — 00 . 、 S 0 6 2 1 (  ̄油化 工 工 艺加 热 炉 节能监 测 方法》 、 Q/Y 14 — 00 2 油化 3 蒸 汽透 平 式 压 缩机 组 节能监 测 方 S 3 7 2 1 {  ̄ -
法》 4 等 项节能节水企业标 准。集 团公 司节能企标委组 织完成 了
标 准报 批 稿 的编 制 。截 至 2 1 年 底 , 团公 司 已批 准 发 布 2 项 00 集 3
节能节水企业标 准。
今年 , 国家能 源局批 准发 布 了S / 2 4 2 1《 地输 油 Y T 6 3 — 00 埋
管道 总传Байду номын сангаас热 系数 的测 定》 s T 6 6 — 0 ; 、Y/ 2 9 2 1 ̄ 油企 业常用节能 0
石油化工行业绿色生产及节能减排策略

石油化工行业绿色生产及节能减排策略第一章石油化工行业绿色生产概述 (3)1.1 绿色生产理念 (3)1.2 绿色生产的重要性 (3)1.2.1 提高资源利用效率 (3)1.2.2 降低环境污染 (3)1.2.3 促进可持续发展 (3)1.2.4 增强国际竞争力 (3)1.3 绿色生产的发展趋势 (4)1.3.1 生产过程清洁化 (4)1.3.2 产品绿色化 (4)1.3.3 循环经济发展 (4)1.3.4 政策法规引导 (4)第二章石油化工行业节能减排现状分析 (4)2.1 节能减排政策法规 (4)2.2 节能减排技术现状 (5)2.3 节能减排存在的问题 (5)第三章生产过程优化与节能减排 (5)3.1 生产工艺改进 (5)3.2 设备优化与升级 (6)3.3 生产过程智能化 (6)第四章清洁生产与节能减排 (7)4.1 清洁生产技术 (7)4.2 清洁生产案例分析 (7)4.3 清洁生产推广策略 (7)第五章节能技术与应用 (8)5.1 能源回收与利用 (8)5.1.1 热能回收 (8)5.1.2 压能回收 (8)5.1.3 电能回收 (8)5.2 节能设备与产品 (8)5.2.1 节能电机 (8)5.2.2 节能泵与压缩机 (9)5.2.3 节能型变压器 (9)5.3 节能技术在石油化工行业的应用 (9)5.3.1 炼油工艺优化 (9)5.3.2 化工生产过程优化 (9)5.3.3 能源管理系统 (9)5.3.4 余热利用 (9)第六章节水技术与应用 (9)6.1 水资源循环利用 (9)6.1.1 概述 (9)6.1.3 水资源循环利用策略 (10)6.2 节水设备与产品 (10)6.2.1 概述 (10)6.2.2 节水设备 (10)6.2.3 节水产品 (10)6.3 节水技术在石油化工行业的应用 (10)6.3.1 概述 (10)6.3.2 应用实例 (11)6.3.3 应用效果 (11)第七章减排技术与应用 (11)7.1 污染物排放控制 (11)7.1.1 概述 (11)7.1.2 排放标准与法规 (11)7.1.3 排放控制技术 (11)7.2 污染物处理技术 (12)7.2.1 概述 (12)7.2.2 水污染物处理技术 (12)7.2.3 大气污染物处理技术 (12)7.3 减排技术在石油化工行业的应用 (12)7.3.1 生产工艺优化 (12)7.3.2 设备改进与更新 (12)7.3.3 资源循环利用 (12)7.3.4 智能化管理与监控 (12)7.3.5 技术创新与研发 (12)第八章企业管理与节能减排 (13)8.1 企业管理理念更新 (13)8.2 企业内部节能减排措施 (13)8.3 企业节能减排激励机制 (13)第九章政策法规与节能减排 (14)9.1 政策法规在节能减排中的作用 (14)9.1.1 引言 (14)9.1.2 政策法规的引导作用 (14)9.1.3 政策法规的激励作用 (14)9.1.4 政策法规的约束作用 (14)9.2 政策法规体系完善 (14)9.2.1 完善政策法规体系的重要性 (14)9.2.2 政策法规体系的完善方向 (14)9.3 政策法规执行与监督 (15)9.3.1 政策法规执行的保障措施 (15)9.3.2 政策法规监督的实施 (15)第十章石油化工行业绿色生产及节能减排未来发展 (15)10.1 绿色生产技术创新 (15)10.1.1 绿色原料替代 (15)10.1.3 末端治理技术创新 (16)10.2 节能减排技术发展趋势 (16)10.2.1 节能技术优化 (16)10.2.2 减排技术发展 (16)10.2.3 综合利用能源 (16)10.3 绿色生产与节能减排国际合作与交流 (16)10.3.1 技术交流与合作 (16)10.3.2 政策法规交流 (16)10.3.3 人才培养与交流 (16)第一章石油化工行业绿色生产概述1.1 绿色生产理念绿色生产理念是一种以保护环境、节约资源、降低污染为核心的生产方式。
炼油化工企业节能降耗技术分析

炼油化工企业节能降耗技术分析炼油化工企业是工业生产中的重要部门之一,它们对能源的需求较大,因此节能降耗对企业的发展至关重要。
随着国内外市场的竞争越来越激烈,企业如何有效地进行节能降耗已成为当前炼油化工企业的一项重要课题。
本文将从节能降耗的重要性、技术分析和实施路径等方面进行探讨。
一、节能降耗的重要性1. 节约资源,减少成本炼油化工企业在生产过程中需要大量的能源资源,随着资源的日益枯竭和环境问题的日益加剧,如何合理利用资源成为了一个亟待解决的问题。
通过引入节能降耗技术,企业可以减少能源的消耗,降低生产成本。
2. 提高竞争力在竞争激烈的市场环境下,企业如果能够有效地节能降耗,就能提高生产效率,降低生产成本,提高产品质量,从而提高企业的竞争力,占据更大的市场份额。
3. 减少环境污染炼油化工企业在生产过程中会产生大量的废气、废水等环境污染物,而这些污染物的排放会严重危害周围环境和人们的健康。
通过采用节能降耗技术,不仅可以减少对环境的损害,还可以提高企业的社会形象。
二、技术分析1. 节能设备的引入炼油化工企业在生产过程中可以通过引入一些节能设备,如高效燃烧设备、节能照明系统等,来提高生产效率,减少能源的消耗。
2. 工艺优化改造通过对生产工艺流程的分析和改造,可以减少能源的浪费,提高生产效率。
对设备的升级改造、工艺流程的优化,都可以有效地降低能源的消耗。
3. 废热利用技术炼油化工企业在生产过程中会产生大量的废热,而这些废热如果能够得到合理利用,将可以为企业节约大量的能源成本。
目前,废热利用技术已经比较成熟,企业可以对废热进行有效地回收利用。
4. 节能监控系统通过引入节能监控系统,可以对生产过程进行实时监控,发现和解决能源的浪费问题,从而达到节能降耗的目的。
三、实施路径1. 制定节能降耗规划企业在进行节能降耗时,首先需要制定一份详细的节能降耗规划,明确目标和路线图,为后续的实施工作提供指导和保障。
2. 引入专业技术团队在实施节能降耗工作时,企业可以引入专业的节能降耗技术团队,他们可以根据企业的实际情况,量身定制节能降耗方案,提供技术支持和指导。
化工装置工艺节能技术和综合能耗计算
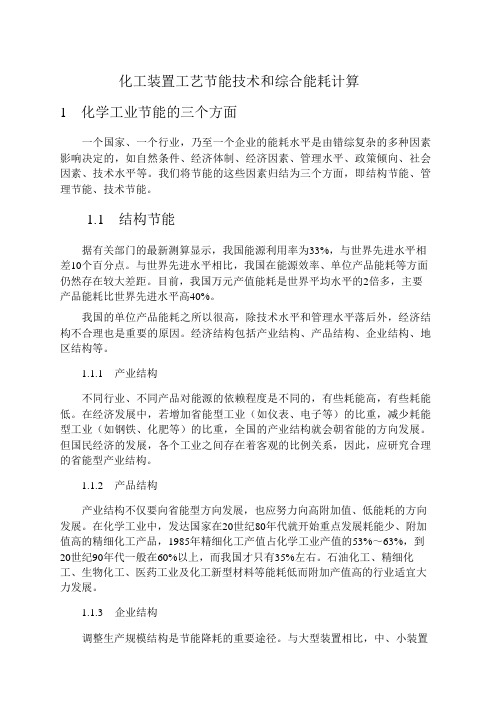
化工装置工艺节能技术和综合能耗计算1化学工业节能的三个方面一个国家、一个行业,乃至一个企业的能耗水平是由错综复杂的多种因素影响决定的,如自然条件、经济体制、经济因素、管理水平、政策倾向、社会因素、技术水平等。
我们将节能的这些因素归结为三个方面,即结构节能、管理节能、技术节能。
1.1结构节能据有关部门的最新测算显示,我国能源利用率为33%,与世界先进水平相差10个百分点。
与世界先进水平相比,我国在能源效率、单位产品能耗等方面仍然存在较大差距。
目前,我国万元产值能耗是世界平均水平的2倍多,主要产品能耗比世界先进水平高40%。
我国的单位产品能耗之所以很高,除技术水平和管理水平落后外,经济结构不合理也是重要的原因。
经济结构包括产业结构、产品结构、企业结构、地区结构等。
1.1.1产业结构不同行业、不同产品对能源的依赖程度是不同的,有些耗能高,有些耗能低。
在经济发展中,若增加省能型工业(如仪表、电子等)的比重,减少耗能型工业(如钢铁、化肥等)的比重,全国的产业结构就会朝省能的方向发展。
但国民经济的发展,各个工业之间存在着客观的比例关系,因此,应研究合理的省能型产业结构。
1.1.2产品结构产业结构不仅要向省能型方向发展,也应努力向高附加值、低能耗的方向发展。
在化学工业中,发达国家在20世纪80年代就开始重点发展耗能少、附加值高的精细化工产品,1985年精细化工产值占化学工业产值的53%~63%,到20世纪90年代一般在60%以上,而我国才只有35%左右。
石油化工、精细化工、生物化工、医药工业及化工新型材料等能耗低而附加产值高的行业适宜大力发展。
1.1.3企业结构调整生产规模结构是节能降耗的重要途径。
与大型装置相比,中、小装置一般能耗较高,经济效益较差。
所以应该有计划、有步骤地调整企业的组织结构,新建化工装置应当选择经济规模较大的大型企业(装置),缺乏竞争力的小企业(装置)应关、停、并、转。
1.1.4地区结构地区结构(资源配置)的调整主要是指资源的优化配置,调整部分耗能型工业的地区结构。
- 1、下载文档前请自行甄别文档内容的完整性,平台不提供额外的编辑、内容补充、找答案等附加服务。
- 2、"仅部分预览"的文档,不可在线预览部分如存在完整性等问题,可反馈申请退款(可完整预览的文档不适用该条件!)。
- 3、如文档侵犯您的权益,请联系客服反馈,我们会尽快为您处理(人工客服工作时间:9:00-18:30)。
炼油化工生产装置工程设计节能技术要求
中国石油天然气集团公司企业标准(Q/CNPC 85-2003)
1范围
本标准规定了炼油化工生产装置工程设计的主要节能措施和技术要求。
本标准适用于新建、改建和扩建炼油化工生产装置的工程设计。
2规范性引用文件
下列文件中的条款通过本标准的引用而成为本标准的条款。
凡是注日期的引用文件,其随后所有的修改单(不包括
勘误的内容)或修订版均不适用于本标准,然而,鼓励根据本标准达成协议的各方研究是否可使用这些文件的最新版本。
凡是不注日期的引用文件,其最新版本适用于本标准。
SH 3010石油化工设备和管道隔热技术规范
SH 3035石油化工企业工艺装置管径选择导则
SH/T 3110石油化工设计能量消耗计算方法
SH/T 3121炼油装置工艺设计规范
Q/CNPC 64固定资产投资工程项目可行性研究报告及初步设计节能篇(章)编写通则
3通则
3.1烁油化工生严装置的设计应执行《中国节能技术政策大纲中国石油天然气集团公司实施细则(炼油和石油化工部分)》,高效、合理利用能源。
3.2可行性研究报告和基础设计(初步设计)文件中,应有节能篇(章)。
节能篇(章)应按Q/CNPC 64的规定编写。
3.3在炼油化工生产装置可行性研究、基础设计(初步设计)和详细设计(施工图设计)中,应根据工艺过程特点,对原料资源、工艺流程、操作条件和自动控制方案进行系统节能优化,选用先进、成熟、可靠的节能新工艺、新技术、新设备、新材料(包括新催化剂、新溶剂等),以提高工艺过程中能源的转换和利用效率,减少能源消耗。
3.4应合理确定装置和单系列设备的生产能力,使其达到经济规模。
3.5引进装置或设备,应综合考虑技术条件、经济效益和能耗水平。
3.6炼油化工装置的能耗计算应符合SH/T 3110的规定。
炼油装置能耗值参见SH/T 3121。
3.7在炼油化工生产装置的工程设计中执行本标准时,应符合现行有关强制性标准规范的要求。
3.8设备布置应结合工艺流程进行设计,合理利用物料的压力能或位能输送物料,并有利于热能和位能的充分利用。
3.9应根据SH 3035合理选择各种管道的管径。
3.10在满足生产及安装要求的前提下,应选用阻力降较小的阀门、管件等。
3.11应选用结构先进、质量可靠的蒸汽疏水阀。
3.12各种设备、管道及其附件的隔热设计,应根据SH
3010合理确定隔热材料的结构和经济厚度,以减少设备和管道的热量或冷量的损失。
3.13应采取措施回收蒸汽凝结水,提高回收率。
蒸汽凝结水应尽量在装置内充分利用,送出装置的蒸汽凝结水温度宜为75℃一85℃。
3.14应合理进行管道的伴热设计。
伴热介质应考虑就近利用热水、回收的蒸汽凝结水和有余热的物料,尽量节省蒸汽。
3.15采暖系统应采用热水作热媒。
3.16供电电源和配电系统的设计应进行多方案比较,做到安全可靠、节约能源、技术先进、经济合理。
3.17在保证照明标准的前提下,照明设计应采用节能型灯具。
4生产流程
4.1工艺路线的选择应进行能耗和技术经济比较。
4.2装置和单系列设备生产能力的确定,在满足产品方案的要求和用户要求的操作弹性下,尽可能减少富裕量。
4.3在满足国家、行业和用户要求的前提下,应合理确定产品(包括中间产品)的质量指标。
4.4设备的生产能力应与装置年操作时数、操作方式、检修周期相适应。
4.5应做好装置的物料平衡和能量平衡设计,合理地按品位高低分级利用能源。
4.6选择合理的工艺操作参数(如温度、压力、流量、配比等),优化工艺过程,并回收利用工艺过程中释放的余热、余压和排放的可燃气体。
4.7在自动控制方案设计中,除满足生产要求外,还应根据节能的要求,合理配置各种监控、调节及计量等仪表设施。
4.8进出装置的物料、燃料、水、电力、蒸汽等能源和载能工质应设置计量仪表。
主要产生或消耗能源的设备,应单独设置计量仪表。
4.9应根据能量平衡的需要设置必要的仪表测试接口。
4.10工艺流程设计应结合单元过程组合,避免或减少重复操作(如加热、冷却、升压、降压、相变、混合等)。
4.11应采用清洁牛产工艺,减少废气、废水、废渣排放量。
5反应单元
5.1采用先进节能的反应器,选择高效催化剂,提高转化率和产率,减少副反应。
5.2充分回收利用反应热加热工艺物料、副产蒸汽或预热锅炉给水等。
5.3合理选择反应器的供热、取热方式和介质。
5.4技术可行时,应将反应和其它过程(也包括其它反应过程)组合起来。
5.5应尽可能避免采用间歇反应方案。
5.6间歇反应应尽可能使反应器的进料、出料及反应产物的分离、提纯等过程采用连续操作。
5.7需要采用搅拌的反应,应合理设计搅拌方式及相应几何、操作参数。
6分离单元
6.1确定方案时,应进行能耗比较,合理确定分离方式、分离顺序、操作参数、产品质量和收率。
6.2应优先采用新型、高效塔盘或填料。
6.3塔系统宜采用进料预热、中间再沸器、中间冷凝(冷却)器等措施。
6.4采用适宜回流比。
6.5选择合适的进料位置。
6.6合理选择传热、传质形式和换热介质。
6.,合理选择吸收剂、萃取剂,并确定适宜的吸收剂量或溶剂比。
6.8对于沸点相近的物系分离,如无合适的低品位热能可用时,宜采用热泵精馏。
7换热系统
7.1宜采用先进技术和软件进行优化设计。
7.2应合理选择工艺单元之间、工艺装置之间、工艺装置与公用工程单元之间、工艺装置与贮运单元之间的热联合方案,充分利用热能。
7.3合理确定传热介质的流速,特别是提高控制传热一侧的流速,合理选择热端和冷端的温差。
7.4换热系统中的冷却和加热介质,应按能量品位合理利用。
7.5传热面积不宜有过大的预留系数。
7.6宜采用新型、高效的换热设备。
7.7宜采用先进的换热器防垢技术和清洗技术。
7.8工艺介质进冷却器的温度不宜高于120'C。
在经济合理的条件下,宜采用低温热能利用设施。
8泵和压缩机
8.1应选用高效、节能的机泵,严禁选用国家规定淘汰产品。
8.2应使选用的机泵在正常负荷下处于性能曲线的高效区。
8.3驱动机应与机泵相匹配。
电动机所需功率的安全系数应按表1选取。
若选用汽轮机作驱动机,汽轮机应满足机泵在额定工况下所需的功率,所留安全裕量不大于10%。
8.4驱动机选型,宜结合厂区的汽源和电源等条件统筹考虑。
8.5汽轮机型式的选择,应根据厂区蒸汽平衡确定,尽量多选用背压式汽轮机。
8.6电动机额定电压应按功率大小选用。
当功率大于或等于160kW时,宜用6kV或10kV;当功率小于160kW时,宜用38 0V。
8.7对负荷变化较大的电机,在经济合理的条件下,宜采用调速技术。
9工业炉
9.1确定合理的加热炉热效率。
按常年连续运行设计的管式炉,热效率值不应低于表2的指标。
当装置内设有多台热负荷较小的加热炉时,可采用联合余热回收系统,以提高加热炉的热效率。
9.2选择工业炉燃料时,在满足工业炉要求的前提下,根据炉型特点尽可能采用从工艺装置回收的可作为燃料的油
和气。
9.3在经济合理与技术可行的前提下,工业炉的烟气余热应充分利用,尽可能地降低排烟温度。
9.4工业炉燃烧器的类型,应根据炉型、燃料种类和燃烧方式选择,宜选用新型节能燃烧器。
9.5工业炉砌体外部均应安装表面钢板。
在保证安全操作的前提下,应控制炉体上各种门、孔的数量,减少漏风,
保证合理的空气系数并保护炉墙。
9.6炉墙结构材料和厚度应经济合理。
在环境温度为25℃和无风的条件下,工业炉本体和空气预热系统的外表面的
设计温度不宜高于60℃。
无余热回收系统的工业炉散热损失应控制在2%以下,有余热回收系统时散热损失应控制在3
%以下。
9.7宜利用工业炉自身烟气的低温热或工艺余热等预热工业炉燃烧用空气。
9.8在保证燃料充分燃烧的基础上,宜采用降低空气系数和减少雾化蒸汽量等节能措施。
9.9宜采用多种形式的扩面管(如钉头管)和各种除灰技术等措施改善传热。
9.10宜采用新型、高效隔热材料,减少散热损失。
原文地址:/tech/84936.html。