MT磁粉检验操作工艺规程
8-10磁粉探伤MT检验工艺卡

表面准备
Suface Prepared
□磨削Grinding
□机械加工Machining
表面状态
Surface Condition
□焊接As Welded
□修磨As Ground
□机加工As Machined
工作表面温度
Part Surf. Temp
°F
℃
工件表面粗糙度
Part Surf. Fin.
仪器型号/编号
Equip./Type No.
磁场指示器编号
Indicator No.
磁粉类型
M.P. Type
□干式Dry□萤光Fluor.
□湿式Wet□非萤光Und
磁粉颜色M.P. Color
载体Vehicles
□水Water□油Oil
磁悬液的浓度测定Concentration of Suspension
光强
Light intensity
Lx
磁化技术Mag. Technique□连续法Continuous□剩磁法Residual
磁化方法
Mag. Method
□磁锥法Prod□纵向磁化法Longl. Mag.
□磁轭法Yoke□周向磁化法Circ. Mag.
Project Name
图号/位号
Dwg./Item No.
检验范围
Extent of MT
□全部Full
□局部Spot
材质及厚度
Mat'l & T
检验阶段
Test Stage
□焊后As-welded□机加工前Before Machining
□热处理后After P.W.H.T.□返修后After Repair
磁粉检测的工艺规程
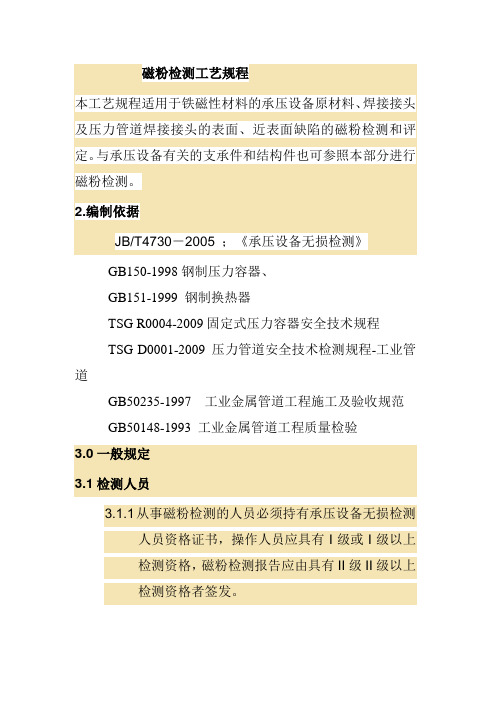
磁粉检测工艺规程本工艺规程适用于铁磁性材料的承压设备原材料、焊接接头及压力管道焊接接头的表面、近表面缺陷的磁粉检测和评定。
与承压设备有关的支承件和结构件也可参照本部分进行磁粉检测。
2.编制依据JB/T4730-2005 ;《承压设备无损检测》GB150-1998钢制压力容器、GB151-1999 钢制换热器TSG R0004-2009固定式压力容器安全技术规程TSG D0001-2009 压力管道安全技术检测规程-工业管道GB50235-1997 工业金属管道工程施工及验收规范GB50148-1993 工业金属管道工程质量检验3.0一般规定3.1检测人员3.1.1从事磁粉检测的人员必须持有承压设备无损检测人员资格证书,操作人员应具有I级或I级以上检测资格,磁粉检测报告应由具有II级II级以上检测资格者签发。
3.1.2色盲、色弱及矫正视力低于1.0者不得从事磁分检测工作。
3.2检测设备和材料3.2.1检测设备3.2.1.1磁粉检测设备应经检定合格并在检定有效期内使用。
3.2.1.2磁粉检测作业前,检测设备应经调试合格。
当磁轭式检测设备磁轭间距为最大时,交流电磁轭至少应有45N的提升力;直流电磁轭至少应有177N的提升力;交叉磁轭至少应有118N的提升力(磁极与试件表面间隙为0.5mm)3.2.1.3采用剩磁法检测时,交流探伤机应配备断电相位控制器。
3.2.1.4黑光辐照度及波长当采用荧光磁粉检测时,使用黑光灯在工件表面的黑光辐照度应大于或等于1000μW/cm2,黑光的波长约为320nm~400nm,中心波长约365nm 。
黑光源应符合GB/T16673的规定。
3.2.1.5退磁装置应能保证工件退磁后表面剩磁小于或等于0.3mT(240A/m) 。
3.2.1.6磁场强度计、标准试片、磁场指示器、黑光灯等辅助器材应满足磁粉检测的需要。
3.2.2检测材料3.2.2.1磁粉检测材料应有产品合格证或质量证明书,并应符合以下要求:3.2.2.2磁粉应具有高导磁率、低矫顽力和低剩磁,磁粉之间不应相互吸引;3.2.2.3磁粉粒度均匀,颜色与检测工件应有较高的对比度。
作业指导书 (MT)

承压设备磁粉检测通用工艺规程1范围1.1本规程规定了承压设备焊缝及其原材料、机加工部件磁粉检测方法及质量分级要求。
1.2 本规程适用于铁磁性材料制板材、复合板材、管材、管件和锻件等表面或近表面缺陷的检测,以及铁磁性材料对接接头、T 型焊接接头和角接接头等表面或近表面缺陷的检测,不适用于非铁磁性材料的检测。
1.3 承压设备有关的支承件和结构件,也可参照本部分进行磁粉检测。
1.4引用标准1.4.1 NB/T47013.1-2015《承压设备无损检测.第1部分:通用要求》1.4.2 NB/T47013.4-2015《承压设备无损检测.第4部分:磁粉检测》2 检测人员2.1 磁粉检测人员应按国家特种设备无损检测人员考核的相关规定取得相应的资格(MT-III、II、I级)后,才能从事与该方法和该资格级别相应的无损检测工作。
2.2磁粉检测人员应具有一定的金属材料、焊接及热处理、设备制造安装等基本知识。
2.2 磁粉检测人员的未经矫正或经矫正的近(距)视力和远(距)视力应不低于5.0(小数记录值为1.0), 测试方法应符合GB 11533的规定。
且应每年检查一次视力。
不得有色盲。
2.3 MT-II级或以上人员出具磁粉检测报告。
3磁粉检测程序磁粉检测程序如下:a)预处理;b)磁化;c)施加磁粉或磁悬液;d)磁痕的观察与记录;e)缺陷评级;f)退磁;g)后处理。
4检测工艺文件4.1 检测工艺文件包括工艺规程和操作指导书4.2工艺规程除满足NB/T47013.1 的要求外,还应规定下列相关因素的具体范围或要求;当相关因素的一项或几项发生变化并超出规定时,应重新编制或修订工艺规程。
a)被检测对象(材质、形状、尺寸等);b)磁化方法;c)检测用仪器设备;d)磁化电流类型及其参数;e)表面状态;f)磁粉(类型、颜色、供应商);g)磁粉施加方法;h)最低光照强度;i)非磁性表面反差增强剂(使用时);j)黑光辐照度(使用时)。
设备检测(VT、TM、MT、PT、硬度)

设备检测(VT、TM、MT、PT、硬度)作者:赣C者(qq:416978041)一、VT(目视检测)1、VT常常用于目视检查焊缝,焊缝本身有工艺评定标准,都是可以通过目测和直接测量尺寸来做初步检验,发现咬边等不合格的外观缺陷,就要先打磨或者修整,之后才做其他深入的仪器检测。
例如焊接件表面和铸件表面较多VT做的比较多,而锻件就很少,并且其检查标准是基本相符的。
2、检测步骤:用刷子除去内部的结晶(杂质)及锈迹。
仔细的观察设备内部,不能放过任何一个角落,光线不足时应使用白光手电筒照射,查看是否有裂缝,有穿孔的情况,有明显腐蚀的痕迹要用显眼的记号笔标出,并拍照记录,以便下一步做更详细的检测;换热器的管板是重点检查的区域,比较明显的穿孔,裂缝通过VT能够看出,特别是每根列管和管板之间的焊缝一般出现问题的概率大。
3、注意事项:检查过程中要仔细,避免漏掉每一个角落。
二、TM(厚度测定)1、仪器:超声波测厚仪(TT140,北京时代)测厚仪标定:按开机键(OFF/ON)后,在测厚仪的顶部的圆形标定铁块上涂上耦合剂,按下ZERO按钮,将测定探头按压在标定铁块上,显示屏上数字显示为4.0mm,标定结束。
2、注意事项:1)、若被测设备为不锈钢,则要用相应的不锈钢标定块标定;2)、耦合剂涂抹的原则是使探头与被测物之间紧密接触,不能留有空气,因为超声波不能在空气中传导,因此耦合剂的涂抹量自己把握。
3、测定方法:用砂轮机除去测定点的涂漆,使之平滑。
在测定点上涂抹耦合剂,将测厚仪(已标定)的探头按压在被测点上,若屏幕上的数值跳动,有必要稍微移动探头并将探头紧贴设备,直到屏幕左下角显“”标志并数值稳定,屏幕上显示的值即为测定值。
发现数值的问题较大应重复多次测量求均值。
4、测定点的确定:厚度的测定并不是随便在设备上找几个点测定,而是找有代表性或者是容易发生腐蚀的地方进行测定,***换热器设备一般测定的点为筒体的两端,上下封头,进出物料的法兰,都是测定这些位置的同一截面的四个方向,示意图如下:***二冷冷凝器检查规格图:测定的部位为图中的①②③④的东南西北四个方向,a、c、d上下东西(或者南北)四个方向。
(完整版)磁粉探伤工艺规程-2017

磁粉探伤工艺规程编制:年月日审核:年月日批准:年月日1 目的和范围1.1 目的:使产品磁粉探伤作业质量符合质量要求,并处于受控状态。
1.2 范围:本规程适用于检验钢质模锻件及其加工件表面及近表面的裂纹和其它缺陷。
2 岗位任职条件2.1 必须具有高中、技校、中专及以上学历,视力(包括矫正视力)达到1.0以上,无色盲;熟练掌握磁粉探伤基本知识,热爱本职工作。
2.2 必须经过铁道部门无损检测鉴定考核委员会组织的磁粉探伤专门培训,并取得铁道部门无损检测人员考核委员会颁发的Ⅱ级及以上级别的磁粉探伤技术资格证书。
3 工具、量具、工装设备及材料4 环境条件4.1 探伤作业场地应远离翻砂、锻打、电焊、潮湿、粉尘场所,地面须经硬化;室内温度达到10—30℃。
4.2 探伤作业场地应整洁明亮,采用荧光磁粉探伤时,观察磁痕显示处紫外灯的辐照度不得低于1500μW/cm2。
4.3磁粉探伤机所用电源必须与大型机械、动力电源分开。
4.4 探伤作业场地应设有工件存放架或箱,待探、待处理、合格的零件应隔离放置,并设有明显的标识。
5 检验规则5.1新造工件的磁粉探伤应在最终热处理工序或机加工工序之后进行。
最终热处理工序之前的磁粉探伤结果不能作为产品交验的依据。
检修工件的磁粉探伤应在分解抛丸除锈工序之后进行。
5.2工件探伤部位表面经过处理应达到规定清洁度,探伤部位应光滑平整,不得存在油污、尘垢、锈蚀、氧化皮等影响磁化及磁痕识别的物质。
5.3 探伤部位经过修磨或机械加工后,必须进行复探。
5.4探伤后,探伤部位再次经过热处理的工件,热处理后探伤部位必须进行全面复探。
5.5探伤后,探伤部位再次经过机加工的工件加工后探伤部位必须进行全面复探。
6 探伤方法6.1 工件磁粉探伤采用湿法连续法。
悬液应比磁化提前结束,或在施加磁悬液结束后,再进行一至两次磁化。
7 作业程序及标准7.1 开工前的准备7.1.1上岗前要充分休息,上岗应按规定穿戴好劳保防护用品,准备好工具。
焊缝mt检验规程
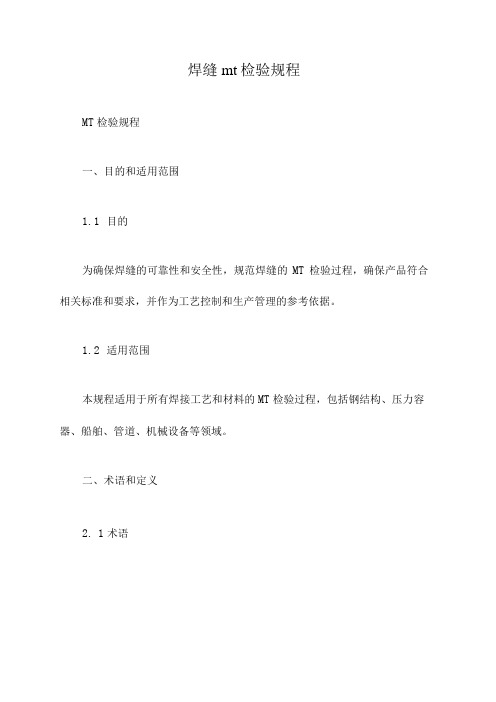
焊缝mt检验规程MT检验规程一、目的和适用范围1.1目的为确保焊缝的可靠性和安全性,规范焊缝的MT检验过程,确保产品符合相关标准和要求,并作为工艺控制和生产管理的参考依据。
1.2适用范围本规程适用于所有焊接工艺和材料的MT检验过程,包括钢结构、压力容器、船舶、管道、机械设备等领域。
二、术语和定义2.1术语MT检验:磁粉检验,是通过涂敷自然或人造磁场,使磁性颗粒在缺陷表面聚集,通过视觉或光学放大器观察和判断缺陷是否存在和类型的一种检验方法。
焊缝:两个或多个材料通过焊接形成的接头。
磁粉:一种铁氧体磁性粉末,由氧化铁或氧化铁与镁的混合物构成。
缺陷:焊缝中的不良部位,如气孔、夹杂、裂纹等。
检验人员:经过培训和资格认证的MT检验操作人员。
2.2定义磁粉检验是通过磁粉检验设备,使用磁粉涂敷在焊缝表面,在外加磁场作用下,能使缺陷表面的磁粉成为一定形式的图案,通过观察和测量这些图案来判断缺陷的存在和类型。
三、检验准备在进行MT检验之前,应进行如下准备工作:3.1设备及材料3.1.1磁粉检验设备,包括磁场发生器、磁探头和磁粉喷涂枪等。
3.1.2磁粉,包括干式和湿式磁粉。
4.1.3支持设备,包括卷尺、标记笔、毛刷和清洁毛巾等。
5.1.4消耗品,包括磁粉检验用刷子、洗刷剂和消毒抹布等。
6.2检验场所3.2.1检验场所应具备足够的空间,确保操作者的安全和操作的便利性。
3.2.2检验场所应保持清洁,并防止灰尘、油脂、水汽等影响检验结果的因素。
3.3检验前的焊缝准备3.3.1焊缝表面应清洁干净,无杂质和磨损。
3.3.2焊缝表面应去除任何可能干扰检验结果的涂层、油漆和锈垢等。
3.3.3焊缝表面应标识清楚,以便区分和追踪。
四、检验步骤4.1选择磁粉在进行MT检验前,应根据实际情况选择合适的磁粉。
干式磁粉适用于垂直和上部焊缝,湿式磁粉适用于水平和下部焊缝。
4.2磁粉涂敷4.2.1在涂敷前,应将磁粉搅拌均匀。
4.2.2在焊缝表面涂敷一层薄薄的磁粉。
典型焊接接头磁粉检测技术教案
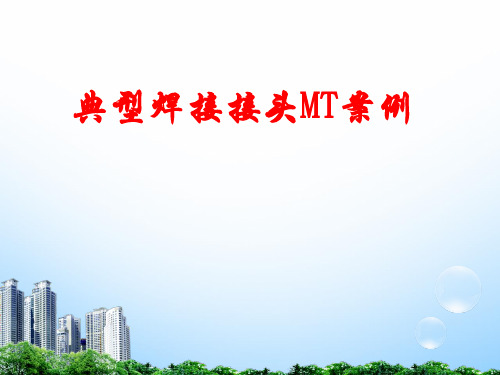
工 序
工序名称
操作要求及主要工艺参数
1 预清理
采用砂轮打磨等方式,清除焊缝及边缘处飞溅焊渣,并 保证被检区域光滑。
采用磁轭法磁化, 先磁轭平行焊缝磁化,磁轭间距为
2
磁 化
磁化顺序与 磁化次数
100mm。两次之间重叠10mm,对整条焊缝磁化完成后, 再用磁轭垂直焊缝磁化,磁轭间距200mm,每次磁化 焊缝的有效长度100mm,两次之间重叠10mm,依次完 成整条焊缝磁化。
请按照NB/T47013.4-2015,Ⅰ级合格,编写磁 粉检测操作指导书。
可选用的设备有:CEE-1000型磁轭探伤仪、 CXE-2000型旋转磁场探伤仪、CJX-1000型交流磁 粉探伤仪、CYD-3000移动式磁粉探伤机、CEW3000型整流磁粉探伤仪及磁粉、载液和其他相关 器材。
图14 液化石油气储罐
触头法的电极应控制在75mm~200mm之间。但 触头连线间距应L≥75mm,两次磁化间的两触头 间距b≤L/2。触头法磁化电流值I按NB/T47013.4 表4计算,触头法检测平板对接焊缝如图4和5所 示;检测T型焊缝如图6所示;检测管板焊缝如图 7所示;检测角焊缝如图8所示。
表4 触头法磁化电流值
灵敏度校核
所有磁化方式其磁化规范最终以A1:30/100试片确定, 放置在焊缝热影响区灵敏度最弱处。
磁悬液要求 3 及施加方式
磁悬液配好后,应采用梨形沉淀管测定磁悬液浓度,保 证浓度在要求范围内。正式检测前,应在被检表面进行 水断实验,合格后再进行检测。喷洒时自高而低,自上 而下分进行磁化。
检验时机 检验在磁痕形成后立即进行。
术
工 艺 参
磁悬液沉淀 浓度
0.10.4mL/100m
磁粉检测工艺规程
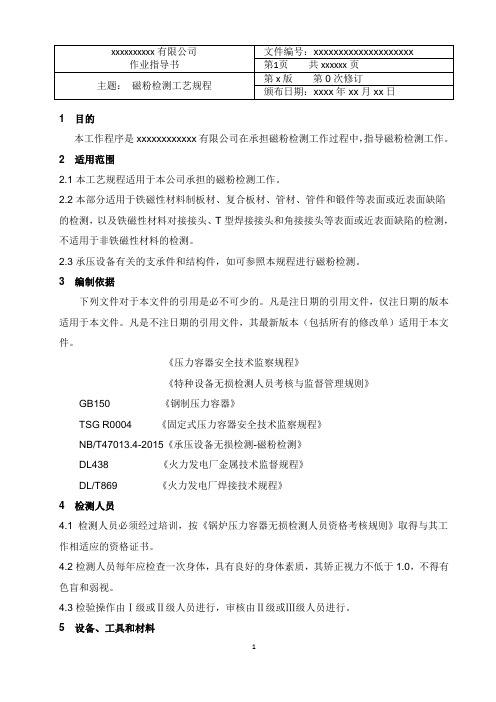
1 目的本工作程序是xxxxxxxxxxxx有限公司在承担磁粉检测工作过程中,指导磁粉检测工作。
2 适用范围2.1本工艺规程适用于本公司承担的磁粉检测工作。
2.2本部分适用于铁磁性材料制板材、复合板材、管材、管件和锻件等表面或近表面缺陷的检测,以及铁磁性材料对接接头、T型焊接接头和角接接头等表面或近表面缺陷的检测,不适用于非铁磁性材料的检测。
2.3承压设备有关的支承件和结构件,如可参照本规程进行磁粉检测。
3 编制依据下列文件对于本文件的引用是必不可少的。
凡是注日期的引用文件,仅注日期的版本适用于本文件。
凡是不注日期的引用文件,其最新版本(包括所有的修改单)适用于本文件。
《压力容器安全技术监察规程》《特种设备无损检测人员考核与监督管理规则》GB150 《钢制压力容器》TSG R0004 《固定式压力容器安全技术监察规程》NB/T47013.4-2015《承压设备无损检测-磁粉检测》DL438 《火力发电厂金属技术监督规程》DL/T869 《火力发电厂焊接技术规程》4 检测人员4.1 检测人员必须经过培训,按《锅炉压力容器无损检测人员资格考核规则》取得与其工作相适应的资格证书。
4.2检测人员每年应检查一次身体,具有良好的身体素质,其矫正视力不低于1.0,不得有色盲和弱视。
4.3检验操作由Ⅰ级或Ⅱ级人员进行,审核由Ⅱ级或Ⅲ级人员进行。
5 设备、工具和材料5.1 磁化设备5.1.1磁化设备见表5.1表5.15.1.2 提升力当使用磁轭最大间距时,交流电磁轭至少应有45N的提升力;直流电(包括整流电)磁轭或永磁轭至少应有177N的提升力;交叉磁轭至少应有118N的提升力(磁极与试件表面间隙为小于等于0.5mm)。
5.1.3磁化设备的选择5.1.3.1对于表面开口型缺陷宜选用能提供交流电的磁化设备。
5.1.3.2对于近表面缺陷及埋藏缺陷,宜选用能提供直流电的磁化设备。
5.2辅助器材5.2.1辅助器材a)A型、C型、标准试块和磁场指示器;b)磁悬液浓度沉淀管;c)2倍~10倍放大镜;d)光照度计:光照度计用于测量被检工件表面的可见光照度。
AWS D1.1磁粉MT检测工艺规程

目的在不损伤被检物使用性能情况下而主要用于探测材料、构件、焊缝或设备等被检物的各种内部缺陷(如:夹渣、裂纹、未焊透等)并判断其位置大小、形状和种类,从而判定被检物的质量状况和质量等级。
1、适用范围本程序适于直流、交流、交叉电磁轭,运用湿式连续磁化法,检验铁磁材料及其制品(熔化焊缝等)表面或近表面的裂纹和其他缺陷。
2、人员要求无损探伤人员资质审定需符合 SNT-TC-1A 的要求,或 ISO9712 的要求。
3、职责质检科负责焊缝磁粉探伤的实施。
4、依据本程序按照:ASTM E709磁粉检验的标准推荐操作方法、AWS D1.1(钢结构焊接规范)编制5、使用仪器及辅助材料5.1 交流电磁轭磁粉探伤机(CDX-III 射阳探伤机厂 B310S 美国派克)5.2 标准试片(A型标准试片)表1 A型标准试片5.3磁粉(MT-BW灌装黑水磁悬液)应当是无毒的,并应与被检工件表面有较高的对比度。
具有高导磁率和低顽磁性的细铁磁粉,其尺寸和形状必须易于形成磁粉显示。
所用的磁粉颜色应尽可能与被检表面有明显的对比度。
必要时可在被检部位喷刷一层反差增强剂(喷涂厚度应尽量薄),以增加对比度。
白色反差剂(FA-5型)应与黑色磁粉同时使用,不能腐蚀或对被检工件产生有害影响。
6、磁粉探伤检测程序6.1 应当首先完成被检焊缝或坡口的外观检查,被检表面可以是焊后或热轧之后的状态。
表面的不规则状态不得影响检测结果的正确性和完整性,否则应做适当的修理。
如打磨、使用清洁剂、有机溶剂、渗透清洗剂等。
6.2 检验过程中要保证电磁轭与构件接触良好,持续通电时间不得超过2min。
磁悬液要在磁化过程中施加,施加磁悬液不得影响已形成的缺陷磁痕。
磁化时间为大于等于3 秒,为保证磁化效果,应至少反复磁化两次或以上。
磁轭的磁极间距最为75~150mm,可以根据被检表面的状况进行调整。
每次检验都应保证足够的重叠。
电磁轭每次移动的覆盖区应不少于25mm。
为检验各方向的缺陷,应至少采用两次不同方向的磁化,或采用旋转磁场和复合磁化方法。
MT工艺

验收等级-验收标准也叫验评标准中规定验收等级, 而方法标准中一般不规定验收等级。如压力容器 安全技术监察规程,GB150 f) 检测程序;
g) 检测部位示意图; h) 编制(级别)和审核(级别)人 ;(编制(Ⅱ 或Ⅲ)审核(Ⅱ或Ⅲ)
三、工艺卡类型
工艺卡一般有两种格式,一种是:特种设备磁粉检测
11)光纤及检测环境: 使用荧光磁粉时,暗区的“环境光照度应小于20lx”,“黑光
辐照度应不小于1000μ W/cm2”。使用非荧光磁粉检测时, “可见光照度应大于或等于1000lx”;当现场采用便携式设备 检测时,由于条件所限制无法满足要求,可见光照度可适当降 低,但“不得低于500 lx”。 12)缺陷磁痕记录方式: 用“照相”、“贴印”、“录像”或“临摹草图”等任意一种。 13)磁化方法: 根据工件尺寸、结构、外形和欲发现缺陷的方向,选择“磁轭 法”、“交叉磁轭法”、“轴向通电法”、“触头法”、“线 圈法”、“中心导体法”等方法中的一种或几种的组合来进行 检测。
因线圈法又有低、中、高填充因素的三种公式,故计算填充因
素。S1/S2=(D1/D2)2= ( 500 / 48 )2= 10.422=108.5> 10。 因而属于低填充因素。但低填充因素又分偏心放置和中心放置。 这两种放置没有硬性规定,均可,但一般优先选用偏心,因为 磁场强度大,所需磁化电流小。 先看偏心放置: 偏心放置公式:首先计算 L/D=310/48= 6.46> 2,可直接采用 公式 45000 I
举例1
对在用高压压力容器设备法兰螺栓进行疲劳裂纹磁粉检测,
螺栓材质为35CrMoA,规格M48×310,按JB4730-2005 标准Ⅰ级验收,请自行选定最佳磁化方法、磁粉探伤设备 和器材后,制定螺栓磁粉探伤工艺卡(可选用的设备和器 材有:CYE—1A磁轭式磁粉探伤仪、CDE—ⅡE旋转磁场 磁粉探伤仪、CY—1000触点式磁粉探伤仪、CEW12000 固定式磁粉探伤仪、线圈(长500mm,10匝,内径 500mm)、黑光灯、A型、C型试片、磁粉、载液等)。
无损检测MT三级(Ⅲ级)工艺编制及优化

MTⅢ级工艺编制及优化1 磁粉探伤工艺方法分类及选择1.1 磁粉探伤工艺方法的分类:1.1.1 按施加磁粉的载体分两种:干法(荧光、非荧光)、湿法(荧光、非荧光)。
1.1.2 按施加磁粉的时机分两种:连续法、剩磁法。
1.1.3 按磁化方法分六种:轴向通电法、触头法、线圈法、磁轭法、中心导体法、交叉磁轭法。
1.2 磁粉探伤工艺方法的一般选择原则:1.2.1 连续法和剩磁法都可进行探伤时,优先选择连续法。
1.2.2 对于湿法和干法,优先选择湿法。
1.2.3对于按磁化方法分类的六种探伤方法,优先选用要根据工件的形状、尺寸、探伤操作的困难程度进行。
2 磁粉探伤工艺方法具体介绍2.1 连续法:2.1.1 概念:在磁化的同时,施加磁粉或磁悬液。
2.1.2 适用范围:①形状复杂的工件;②剩磁Br (或矫顽力Hc)较低的工件;③检测灵敏度要求较高的工件;④表面覆盖层无法除掉(涂层厚度均匀不超过0.05mm)的工件。
2.1.3操作要点:①先用磁悬液润湿工件表面;②磁化过程中施加磁悬液,磁化时间1S-3S;③磁化停止前完成施加操作并形成磁痕,时间至少1S;④至少反复磁化两次。
2.1.4优点:1)适用于任何铁磁性材料。
(2)具有最高的检测灵敏度。
(3)可用于多向磁化。
(4)交流磁化不受断电相位的影响。
(5)能发现近表面缺陷。
(6)可用于湿法和干法检验。
2.1.5局限性:(1)效率低。
(2)易产生非相关显示。
(3)目视可达性差。
2.2 剩磁法:2.2.1 概念:停止磁化后,施加磁粉或磁悬液。
2.2.2 适用范围:①矫顽力Hc在1000A/m以上,并保持剩磁Br在0.8T以上的工件,一般如经过热处理的高碳钢和合金结构钢(淬火、回火、渗碳、渗氮、局部正火);低碳钢、处于退火状态或热变形后的钢材都不能采用剩磁法;②成批的中小型零件进行磁粉检测时;③因工件几何形状限制连续法难以检验的部位。
2.2.3操作要点:①磁化结束后施加磁悬液;②磁化后检验完成前,任何磁性物体不得接触被检工件;③磁化时间一般控制在0.25-1S;④浇磁悬液2 –3遍,或浸入磁悬液中10—20S,保证充分润湿;⑤交流磁化时,必须配备断电相位控制器。
(完整)焊接磁粉检验规程

焊接磁粉检验规程1.适用范围1)本规程按ISO23278和ISO17638编制完成;2)本规程规定了磁粉检测方法及质量分级要求;3)本规程适用于铁磁性原材料、零部件和焊接接头表面、近表面缺欠的检测,不适用于不锈钢和其他非铁磁性材料的检测.2.参考标准1)ISO17638《焊接无损检测-磁粉检测》2) ISO23278《焊接无损检测-磁粉检测-可接受等级》3) ISO9712《无损检测人员的资格鉴定及认证推荐方法》3.人员1)Ⅰ级磁粉无损检测人员a)可在Ⅱ、Ⅲ级人员指导下进行无损检测操作;b)按照检测规程的要求,正确记录检测数据,整理检测记录.2)Ⅱ级磁粉无损检测人员a)可编制一般的无损检测程序b)按照无损检测工艺规程独立进行检测操作,评定检测结果,签发检测报告.3)Ⅲ级磁粉无损检测人员负责验证和批准无损检测规程、报告。
4)无损检测人员应按规定定期进行资格换证。
4.磁粉检测原理铁磁性材料和工件被磁化后,由于不连续性的存在,使工件表面和近表面的磁力线发生局部畸变而产生漏磁场,吸附施加在工件表面的磁性,形成在合适光照下目视可见的磁痕,从而显示出不连续的位置、形状和大小。
5.磁化设备校验1)校验周期磁粉检测设备至少每年校验一次;设备进行过重要电源修理,周期大修或损坏时,必须得到校验.如果设备已一年或一年以上未使用,则在第一次使用之前必须校验。
2)磁轭提升力的校验当使用磁轭最大间距时,交流电磁轭至少应有45N的提升力;直流电磁轭至少应有177N 的提升力;交叉磁轭至少应有118N的提升力。
6.磁粉、载体和磁悬液1)磁粉磁粉应具有高导磁率、低矫顽力和低剩磁,并应与被检工件表面颜色有较高的对比度。
2)载体本规程采用湿法,湿法采用水作为分散媒介。
3)磁悬液a)磁悬液浓度应按制造厂推荐,对循环使用的磁悬液,每天开始工作前,应进行磁悬液浓度测定;b)除制造厂另有规定外,非荧光磁粉磁悬液配制浓度应为10~25g/L,荧光磁粉应为0.5~3.0g/L。
磁粉检测通用工艺规程

1. 范围适用于铁磁性材料制承压设备的原材料、零部件和焊接接头表面近表面缺陷的检测。
2.引用标准法规GB/T16673-1996 无损检测用黑光源辐射的测量JB/T4730-2005 承压设备无损检测JB/T6063-1992 磁粉探伤用磁粉JB/T6065-2004 无损检测磁粉检测用试片JB/T8290-1998 磁粉探伤机3. 检测人员3.1、磁粉检测人员上岗前, 应按照《特种设备无损检测人员考核与监督管理规则》的要求, 取得磁粉检测资格, 且只能从事相应资格的检测工作。
3.2、磁粉检测人员的矫正视力应不低于5.0, 并每年检查一次, 不得有色盲。
4. 检测设备、器材和材料4.1.设备磁粉检测设备应符合JB/T8290的规定。
4.1.1.当磁轭间距最大时, 交流电磁轭的提升力≮44N, 直流电磁轭的提升力≮177N.4.1.2、剩磁法检测时, 交流探伤机必配备断电相位控制器。
4.1.3、荧光磁粉检测时, 黑光灯在工作表面的照度≥1000μw/ , 黑光的波长λ=320nm~400nm,中心波长λ≈365nm。
黑光源应符合GB/T16673的规定。
4.1.4.退磁装置应保证退磁后表面剩磁≤0.3mT4.2.辅助器材一般包括下列器材:a)A1型、C型、D型和M1型试片, 磁场指示器;b)磁场强度计及毫特斯拉计;c)磁悬液浓度沉淀管;d)2~10倍放大镜;d)白光照度计;f)黑光灯;g)黑光辐照计。
4.3.磁粉、载液、磁悬液4.3.1、磁粉应具有高磁导率、低矫顽力和低剩磁, 并与工件表面的颜色对比度要较高。
其他要求应符合GB/T6063的规定。
4.3.2、载液为水时, 应加入防锈剂、表面活性剂及清洗剂。
载液为油时, 其运动粘度在38℃时应小于或等于3.0 /s, 使用温度小于或等于5.0 /s, 闪点不低于94℃, 且无荧光和异味。
4.3.3.磁悬液浓度范围应符合表1的规定。
测定前应充分搅匀。
表1 磁悬液浓度4.4.标准试块4.4.1、一般应选用A1-30/100, 检测狭小部位可选用C-15/50。
MT工作规范

1.0目的1.1本规程确定了依照API 20B标准,用湿荧光法进行磁粉探伤检测的方法,人员要求以及接受标准(参考API 6A),本规程也适用于按照相关规范的要求进行产品磁粉探伤测试。
1.2本规程概述了依据ASTM E709 对铁磁材料进行表面及近表面的缺欠的连续法磁粉探伤。
2.0 参考资料a) ASTM E709–磁粉检验指导标准b) API 6A-井口和采油树设备规范c) SNT-TC-1A –美国无损检测协会推荐的操作规程3.0 磁粉检验流程—湿荧光法3.1 安全与环境3.1.1 使用者/承包人在特定的安全,健康和环境方针的指导下安全操作是使用者/承包人的责任。
3.1.2 磁粉和浓缩磁粉的安全操作应由供货商的材料安全数据单(MSDS)控制,使用者和承包人在特定安全,健康和环境方针的指导下,应依照本规程负责对任何与程序相关的浪费或危害环境的做法进行控制.3.2 人员资格3.2.1 依据以下规范,进行检测、说明及对结果作出评价、记录的人员应具备至少 II 级资格证明,在有资格证明的II 级或III 级人员直接监督下, I 级人员才可以做检查测试3.2.2 依据以下规范,所有进行按本程序检测的人员都要求进行每年的视力测试及三年一次的辨色测试:3.3 设备、材料要求与校准3.3.1 设备和材料要求3.3.1.1带接触板和线圈或便携磁极(至少 4500 安培)的水平湿磁粉探伤机,设备应包括所有电子仪器、机械装置以及满足本规程要求的必要附件。
3.3.1.2 可使用交流,整流(全波或半波)或直流电源,设备应具备不同电流控制能力,并可以为周和/或纵向磁性产生所需电流。
3.3.1.4 使用磁粉以油或水介质的溶液。
3.3.1.5 黑光灯 (紫外线灯)应具备最小光强为1000μW/cm2,并且不能产生超过2尺烛光(约20Lux)的可见光。
3.3.1.6 暗区或暗室:推荐的检测区范围内的可见光强度不应超过2 尺烛光(约20Lux)3.3.1.7 线圈,电缆和导棒:可以使用铜或铝制的尺寸为2/0 或4/0 的电缆。
磁粉检测工艺-2014
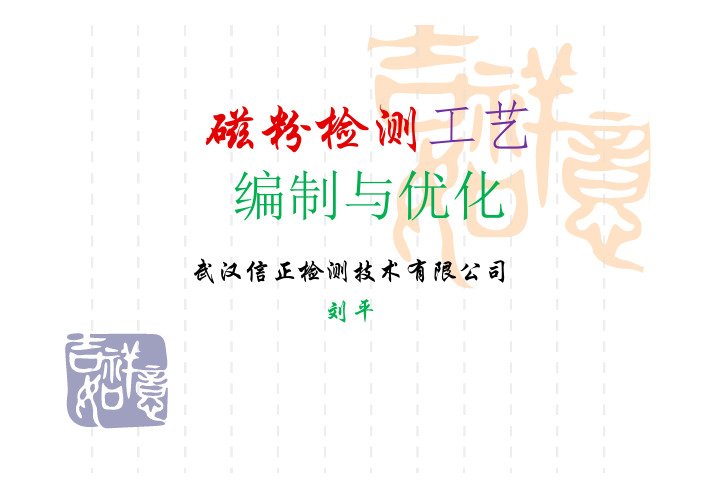
2、该工件外表面角焊缝如采用触头法检测,是 否需按法兰厚度来选择磁化电流?为什么? 答:该角焊缝工件属于不等厚结构,采用触头 法检测时,不用按法兰厚度来选择磁化电流, 因为在法兰中电流的绝大部分是沿与薄板厚度 相近的表层中流过,所以应按薄板厚度确定磁 化规范,即(3.5~4.5)倍触头间距。同时应 根据标准试片实测结果来校正。
产品名称 材料牌号 探伤设备 检验方法 磁化电流 磁化规范 磁粉、载液、磁悬 液配制浓度 紫外光辐照度或试 件表面光照度 探伤方法标准 不允许缺陷 磁化方法示意草图:
产品规格 检测部位 表面预清理要求 标准试片 磁化方法 磁化时间 磁悬液施加方法及 操作要求 缺陷记录方式 质量验收等级
磁化操作附加说明:
3 MT工艺编制并优化的实例
3.1例题一: 对在用高压压力容器设备法兰螺栓进行疲劳裂纹 磁 粉 检 测 , 螺 栓 材 质 为 35CrMoA , 规 格 M48×310,按JB4730.4-2005标准Ⅰ级验收, 请自行选定最佳磁化方法、磁粉探伤设备和器 材后,制定螺栓磁粉探伤工艺卡.(可选用的设 备和器材有: CYE—1A 磁轭式磁粉探伤仪、 CDE—ⅡE旋转磁场磁粉探伤仪、CY—1000触 点式磁粉探伤仪、 CEW12000 固定式磁粉探伤 仪、线圈(长 500mm , 10 匝,内径 500mm )、 紫外灯、A型、C型试片、磁粉、载液等)。
换热器管箱 Q235B 表面检验合格后 CYE-1A、CY-1000磁探机 交流、连续法 1、I=3.5-4.5倍触头间距 2、 ≥45N 黑磁粉、水悬液 1.2~2.4ml/100ml 试件表面光照度≥1000lx JB4730.4-2005
产品规格(mm) 检测部位 表面预清理要求 标准试片 磁化方法 磁化时间 磁悬液施加 方法及操作要求 缺陷记录方式 质量验收等级
特种设备无损检测(NDT)磁粉检测(MT)工艺编制及优化

MT工艺编制及优化1 磁粉探伤工艺方法分类及选择1.1 磁粉探伤工艺方法的分类:1.1.1 按施加磁粉的载体分两种:干法(荧光、非荧光)、湿法(荧光、非荧光)。
1.1.2 按施加磁粉的时机分两种:连续法、剩磁法。
1.1.3 按磁化方法分六种:轴向通电法、触头法、线圈法、磁轭法、中心导体法、交叉磁轭法。
1.2 磁粉探伤工艺方法的一般选择原则:1.2.1 连续法和剩磁法都可进行探伤时,优先选择连续法。
1.2.2 对于湿法和干法,优先选择湿法。
1.2.3对于按磁化方法分类的六种探伤方法,优先选用要根据工件的形状、尺寸、探伤操作的困难程度进行。
2 磁粉探伤工艺方法具体介绍2.1 连续法:2.1.1 概念:在磁化的同时,施加磁粉或磁悬液。
2.1.2 适用范围:①形状复杂的工件;②剩磁Br (或矫顽力Hc)较低的工件;③检测灵敏度要求较高的工件;④表面覆盖层无法除掉(涂层厚度均匀不超过0.05mm)的工件。
2.1.3操作要点:①先用磁悬液润湿工件表面;②磁化过程中施加磁悬液,磁化时间1S-3S;③磁化停止前完成施加操作并形成磁痕,时间至少1S;④至少反复磁化两次。
2.1.4优点:1)适用于任何铁磁性材料。
(2)具有最高的检测灵敏度。
(3)可用于多向磁化。
(4)交流磁化不受断电相位的影响。
(5)能发现近表面缺陷。
(6)可用于湿法和干法检验。
2.1.5局限性:(1)效率低。
(2)易产生非相关显示。
(3)目视可达性差。
2.2 剩磁法:2.2.1 概念:停止磁化后,施加磁粉或磁悬液。
2.2.2 适用范围:①矫顽力Hc在1000A/m以上,并保持剩磁Br在0.8T以上的工件,一般如经过热处理的高碳钢和合金结构钢(淬火、回火、渗碳、渗氮、局部正火);低碳钢、处于退火状态或热变形后的钢材都不能采用剩磁法;②成批的中小型零件进行磁粉检测时;③因工件几何形状限制连续法难以检验的部位。
2.2.3操作要点:①磁化结束后施加磁悬液;②磁化后检验完成前,任何磁性物体不得接触被检工件;③磁化时间一般控制在0.25-1S;④浇磁悬液2 –3遍,或浸入磁悬液中10—20S,保证充分润湿;⑤交流磁化时,必须配备断电相位控制器。
磁粉检测通用工艺规程 nb t47013
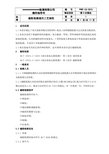
1 适用范围1.1本部分规定了承压设备焊缝及其原材料、机加工部件磁粉检测方法及质量分级要求。
1.2本部分适用于铁磁性材料制板材、复合板材、管材、管件和锻件等表面或近表面缺陷的检测,以及铁磁性材料对接接头、T型焊接接头和角接接头等表面或近表面缺陷的检测,不适用于非铁磁性材料的检测。
1.3承压设备有关的支承件和结构件,也可参照本部分进行磁粉检测。
2 编制依据NB/T 47013.1—2015《承压设备无损检测》第1部分通用要求NB/T 47013.4—2015《承压设备无损检测》第4部分磁粉检测3 一般要求3.1 检测人员3.1.1从事磁粉检测的人员应按照国家特种设备无损检测人员考核的相关规定取得相应无损检测人员资格。
3.1.2磁粉检测人员的未经矫正或经矫正的近(小数)视力和远(距)视力应不低于5.0(小数记录值为1.0),测试方法应符合GB 11533的规定;并一年检查一次,不得有色盲。
3.2 磁粉检测程序磁粉检测程序如下:⑴预处理;⑵磁化;⑶施加磁粉或磁悬液;⑷磁痕的观察与记录;⑸缺陷评级;⑹退磁;⑺后处理。
3.3 磁粉检测设备3.3.1 设备磁粉检测设备应符合JB/T 8290的规定。
3.3.2 提升力当使用磁轭最大间距时,交流电磁轭至少应有45N的提升力;直流电(包括整流电)磁轭或永久性磁轭至少应有177N的提升力;交叉磁轭至少应有118N的提升力(磁极与试件表面间隙为小于等于0.5mm)。
3.3.3 断电相位控制器采用剩磁法检测时,交流探伤机应配备断电相位控制器。
3.3.4黑光灯当采用荧光磁粉检测时,使用的黑光灯在工件表面的辐照强度应大于或等于1OOOμW/cm2,其波长应为315nm-400nm,峰值波长约为365nm。
黑光源应符合GB/T 5097的规定。
3.3.5黑光辐光照度计黑光辐光照度计用于测量黑光的辐照度,其测量的波长范围应至少在315nm-400nm内,峰值波长约为365nm。
MT操作及判定

1.简述及相关标准磁粉探伤是通过对铁磁材料进行磁化所产生的漏磁场,来发现其表面或近表面缺陷的无损检测方法。
国标:NB/T47013.4-2015;美标:ASTM E1444/E709、ASME V第7章;欧标:EN 99342.磁粉探伤的基本原理磁粉探伤是通过磁粉在缺陷附近漏磁场中的堆积以检测铁磁性材料表面或近表面处缺陷的一种无损检测方法。
磁粉探伤的基本原理:将待测物体置于强磁场中或通以大电流使之磁化,若物体表面或表面附近有缺陷(裂纹、折叠、夹杂物等)存在,由于它们是非铁磁性的,对磁力线通过的阻力很大,磁力线在这些缺陷附近会产生漏磁。
当将导磁性良好的磁粉(通常为磁性氧化铁粉)施加在物体上时,缺陷附近的漏磁场就会吸住磁粉,堆集形成可见的磁粉迹痕,从而把缺陷显示出来,如图1所示。
(a)(b)图1 磁粉探伤原理示意图(a) 表面缺陷(b) 近表面缺陷3、磁化方法与设备3.1 磁轭法在压力容器制造和在用检验中,以焊缝检测为主,一般采用便携式电磁轭,因其结构简单、重量轻、使用方便。
磁轭法适用于大型工件的局部检测,如对接焊缝、角焊缝、筒体钢板母材及坡口等的检测。
其特点是设备简单、操作方便。
NB/T47013 标准规定磁轭法的磁化规范可根据灵敏度试片或提升力来确定。
对于磁轭,当使用电磁轭最大间距时,交流电磁轭至少应有44N 的提升力。
3.2 设备1)马蹄形磁粉探伤仪:无锡市捷成检测设备制造有限公司 XMTY——II 型2)反差增强剂:上海新美达探伤器材有限公司 FA-53)黑油磁悬液:上海新美达探伤器材有限公司 MT-BO4.磁粉探伤的工艺根据被探件的材料、形状、尺寸及需检查缺陷的性质、部位、方向和形状等的不同,所采用的磁粉探伤方法也不尽相同,但其探伤步骤大体如下:1、探伤前的准备校验探伤设备的灵敏度,除去被探伤件表面的油污、铁锈、氧化皮等。
2、磁化(1)确定探伤方法对高碳钢或经热处理(淬火、回火、渗碳、渗氮)的结构钢零件用剩磁法探伤;对低碳钢、软钢用连续法。
磁粉检测规程
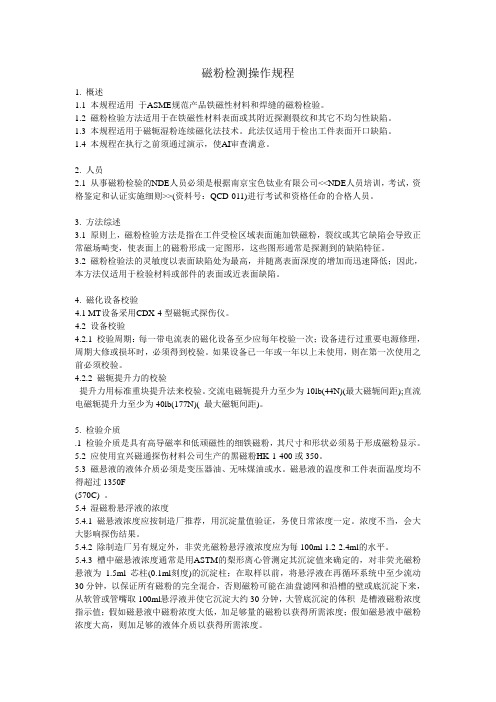
磁粉检测操作规程1. 概述1.1 本规程适用于ASME规范产品铁磁性材料和焊缝的磁粉检验。
1.2 磁粉检验方法适用于在铁磁性材料表面或其附近探测裂纹和其它不均匀性缺陷。
1.3 本规程适用于磁轭湿粉连续磁化法技术。
此法仅适用于检出工件表面开口缺陷。
1.4 本规程在执行之前须通过演示,使AI审查满意。
2. 人员2.1 从事磁粉检验的NDE人员必须是根据南京宝色钛业有限公司<<NDE人员培训,考试,资格鉴定和认证实施细则>>(资料号:QCD-011)进行考试和资格任命的合格人员。
3. 方法综述3.1 原则上,磁粉检验方法是指在工件受检区域表面施加铁磁粉,裂纹或其它缺陷会导致正常磁场畸变,使表面上的磁粉形成一定图形,这些图形通常是探测到的缺陷特征。
3.2 磁粉检验法的灵敏度以表面缺陷处为最高,并随离表面深度的增加而迅速降低;因此,本方法仅适用于检验材料或部件的表面或近表面缺陷。
4. 磁化设备校验4.1 MT设备采用CDX-4型磁轭式探伤仪。
4.2 设备校验4.2.1 校验周期:每一带电流表的磁化设备至少应每年校验一次;设备进行过重要电源修理,周期大修或损坏时,必须得到校验。
如果设备已一年或一年以上未使用,则在第一次使用之前必须校验。
4.2.2 磁轭提升力的校验提升力用标准重块提升法来校验。
交流电磁轭提升力至少为10lb(44N)(最大磁轭间距);直流电磁轭提升力至少为40lb(177N)( 最大磁轭间距)。
5. 检验介质.1 检验介质是具有高导磁率和低顽磁性的细铁磁粉,其尺寸和形状必须易于形成磁粉显示。
5.2 应使用宜兴磁通探伤材料公司生产的黑磁粉HK-1-400或350。
5.3 磁悬液的液体介质必须是变压器油、无味煤油或水。
磁悬液的温度和工件表面温度均不得超过1350F(570C) 。
5.4 湿磁粉悬浮液的浓度5.4.1 磁悬液浓度应按制造厂推荐,用沉淀量值验证,务使日常浓度一定。
- 1、下载文档前请自行甄别文档内容的完整性,平台不提供额外的编辑、内容补充、找答案等附加服务。
- 2、"仅部分预览"的文档,不可在线预览部分如存在完整性等问题,可反馈申请退款(可完整预览的文档不适用该条件!)。
- 3、如文档侵犯您的权益,请联系客服反馈,我们会尽快为您处理(人工客服工作时间:9:00-18:30)。
磁粉检验操作工艺规程
1. 概述
1.1 本规程适用于ASME规产品铁磁性材料和焊缝的磁粉检验。
1.2 磁粉检验法适用于铁磁性材料表面或其附近探测裂纹和其它不均匀性缺陷。
1.3 本规程适用于磁轭湿粉连续磁化法。
此法仅适用检出工件表面开口缺陷。
1.4 本规程在执行之前须通过演示,使AI审查满意。
2. 人员
2.1 从事磁粉检验的NDE人员必须是根据宝色钛业<<NDE人员培训,考试,资格鉴定和认证实施细则>>(资料号:QCD-011)进行考试和资格任命的合格人员。
3. 方法综述
3.1 原则上,磁粉检验方法是指在工件受检区域表面施加铁磁粉,裂纹或其它缺陷会导致正常磁场畸变,使表面上的磁粉形成一定图形,这些图形通常是探测到的缺陷特征。
3.2 磁粉检验法的灵敏度以表面缺陷处为最高,并随离表面深度的增加而迅速降低;因此,本方法仅适用于检验材料或部件的表面或近表面缺陷。
4. 磁化设备校验
4.1 MT设备采用CDX-4型磁轭式探伤仪。
4.2 设备校验
4.2.1 校验周期:每一带电流表的磁化设备至少应每年校验一次;设备进行过重要电源修理,周期大修或损坏时,必须得到校验。
如果设备已一年或一年以上未使用,则在第一次使用之前必须校验。
4.2.2 磁轭提升力的校验
提升力用标准重块提升法来校验。
交流电磁轭提升力至少为10lb(44N)(最大磁轭间距);直流电磁轭提升力至少为40lb(177N-18kg)( 最大磁轭间距)。
5. 检验介质
.1 检验介质是具有高导磁率和低顽磁性的细铁磁粉,其尺寸和形状必须易于形成磁粉显示。
5.2 应使用宜兴磁通探伤材料公司生产的黑磁粉HK-1-400或350。
5.3 磁悬液的液体介质必须是变压器油、无味煤油或水。
磁悬液的温度和工件表面温度均不得超过1350F(57℃) 。
5.4 湿磁粉悬浮液的浓度
5.4.1 磁悬液浓度应按制造厂推荐,用沉淀量值验证,务使日常浓度一定。
浓度不当,会大大影响探伤结果。
5.4.2 除制造厂另有规定外,非荧光磁粉悬浮液浓度应为每100ml 1.2-2.4ml 的水平。
5.4.3 槽中磁悬液浓度通常是用ASTM的梨形离心管测定其沉淀值来确定的,对非荧光磁粉悬液为1.5ml 芯柱(0.1ml刻度)的沉淀柱;在取样以前,将悬浮液在再循环系统中至少流动30分钟,以保证所有磁粉的完全混合,否则磁粉可能在油盘滤网和沿槽的壁或底沉淀下来,从软管或管嘴取100ml悬浮液并使它沉淀大约30分钟,大管底沉淀的体积是槽液磁粉浓度指示值;假如磁悬液中磁粉浓度大低,加足够量的磁粉以获得所需浓度;假如磁悬液中磁粉浓度大高,则加足够的液体介质以获得所需浓度。
5.4.4 假如沉淀磁粉表现为松散的团块,而不是紧密的敷层,则应作第二次取样试验,如果还是团块,说明磁粉可能已被磁化,这时需更换悬浮液。
6. 磁化过程
6.1 磁轭法
6.1.1 可采用直流的、交流的电磁轭或永久磁轭、来磁化一个局部区域、形成一个纵向磁场。
6.1.2 交流电磁轭的提升力应至少在两极间距离最大时为10磅(4.5公斤)。
6.1.3 经验磁轭式磁场强度可测量它的提升力来确定。
6.1.4根据经验磁轭式磁场强度可测量它的提升力来确定。
6.1.4 磁化方向
每一区域应至少进行两次分别检验。
在第二次检验中,磁通线的方向应大致与第一次检验区域所采用的方向相垂直。
6.1.5受检区域应限制在两磁极连线的双侧,相当于1/4最大磁极间距的围,磁极间距每次至少有1英寸(25毫米)的搭接。
7.磁场强度
7.1使用专用的碳钢/铜板磁场指示器来校验零件表面的磁场强度和方向是否满足要求。
如果铜板边有清晰的磁粉线条,则表明磁场强度是足够的。
8.检验要求
8.1表面制备
8.1.1经焊接、轧制、铸造、锻造等加工的零件,一般会取得满意的效果。
然而,表面不平(不均匀)会掩饰缺陷的显示,则这些地方要通过打磨或机加工进行表面制备。
8.1.2在磁粉检验之前,被检验的表面及其附近至少1英寸(25mm)的区域应实干燥的,并且没有任何污垢、纤维屑、锈皮、焊剂和焊接飞溅、油污或其他能妨碍检验的外来物。
8.1.3可使用去污剂、有机溶剂、除绣剂、除绣液、去漆剂、蒸气除油、喷沙或超声波清洗等方法达到清洁的目的。
8.1.4如果在被检验部件表面存在漆层等覆盖物,必须进行演示实验,使缺陷能透过覆盖层最厚处显示出来。
使用磁轭法时,应按ASME法规第Ⅴ卷第7章强制性附录Ⅰ之要求,验证涂层厚度的影响。
8.2 除非图纸或其他技术文件中另有规定,任何零件均应在完工的表面状态,或最终机加工状态,或最终热处理状态下进行磁粉探伤。
8.3 零件上的小开口、槽或孔,应在检验前堵塞好以防磁粉进入。
8.4 检验时应有足够的重叠(至少10%),保证受检零件在规定的灵敏度下能得到100%的履盖。
8.5 受检工件上经返修的区域,应按原来的检验程序重新检验。
8.6 受检工件表面的观察亮度必须至少为50fc(500lx)。
9. 显示评定及合格标准
9.1 磁粉显现评定
磁粉保留一段时间回显示出磁线,并不是所有显示出来的都是缺陷,因受检表面粗燥(如在热影响区边缘),导磁发生变化等原因,会产生类似于缺陷的显示。
只有被确认为机械缺陷的显示,且显示的尺寸大于1/16英寸(1.5mm)时才被认为有效显示;
a. 线形显示是指其长度超过宽度3倍的显示。
b. 圆形显示是指一个圆形和椭圆的长度小于或等于宽度的3倍的显示。
c. 可疑的、有争议的显示均应重新检验以决定它们是否为有效显示。
d. 主要区域被积聚的不连续的磁粉遮盖不允许的,对这些区域应重新检验。
9.2合格标准(根据ASME第Ⅷ卷第一分册附录6)
除特殊材料指定使用更严格的标准外,通常应采用如下合格标准。
所有受检表面不允许有如下缺陷显示:
a. 有效的线形显示;
b. 尺寸大于3/16英寸(5mm)有效的面形显示;
c. 一条直线上边缘间隔等于或小于1/16in.(1.5mm)的4个或更多的有效的圆形显示。
d.缺陷显示可能大于缺陷本身,但是以显示尺寸作为合格评价的基础。
10. 退磁
当剩磁对零件附加工或使用有影响时,该零件在磁粉检验后应及时进行退磁。
11. 清洁
磁粉材料会妨碍后继加工或使用时,检验后应进行清理。
12. 记录和报告
12.1 操作员必须记录检验详情和结果,必要时要用胶带纸、照相或其他方法作永久性记录。
12.2 NDE报告应由操作者编制,由NDE Ⅱ级或Ⅲ级探伤员审核,并经指定的NDE Ⅲ级人员批准,然后提交AI认可。