铸造理论
铸造工艺基础知识及理论

铸造工艺基础知识及理论目录一、基础概念 (2)1.1 铸造的定义与意义 (3)1.2 铸造工艺的种类与应用 (4)二、铸造材料 (6)三、铸造设备 (7)3.1 熔炼设备 (9)3.2 锻造设备 (10)3.3 后处理设备 (11)四、铸造工艺过程 (12)五、铸造工艺设计 (13)5.1 工艺方案的确定 (15)5.2 工艺参数的选择 (16)5.3 工艺文件的编制 (18)六、铸造质量与控制 (20)6.1 铸造缺陷的产生原因及防止措施 (22)6.2 铸造质量检测方法与标准 (23)七、铸造生产与环境 (24)7.1 铸造生产的环保要求 (26)7.2 环保设备的应用与管理 (27)八、现代铸造技术的发展趋势 (28)8.1 快速凝固与近净形铸造技术 (30)8.2 数字化与智能化铸造技术 (31)8.3 生物铸造与绿色铸造技术 (33)一、基础概念铸造工艺是指将熔炼好的液态金属浇入铸型,待其凝固后获得所需形状和性能的金属制品的过程。
它是制造业中非常重要的工艺之一,广泛应用于汽车、航空、建筑、电子等领域。
铸造工艺的基础知识主要包括液态金属的性质、铸型(即模具)的设计与制造、浇注系统、凝固过程以及后处理等。
这些知识是理解和掌握铸造工艺的基本前提。
液态金属的性质:液态金属在铸造过程中的流动性、填充能力、冷却速度等对其最终的产品质量有着决定性的影响。
了解液态金属的成分、温度、粘度等基本性质对于铸造工艺的设计和实践都是非常重要的。
铸型的设计与制造:铸型是形成金属制品形状和内部结构的重要工具。
铸型的设计需要考虑到金属液的流动性和凝固特性,以及制品的精度和表面质量要求。
铸型的制造也需要选用合适的材料,并经过精密加工才能达到设计要求。
浇注系统:浇注系统是连接铸型和液态金属的通道,包括浇口杯、直浇道、横浇道和内浇道等部分。
合理的浇注系统设计可以确保金属液均匀地注入铸型,并有利于热量和气体的排出,从而提高制品的质量和生产效率。
铸造工高级理论试题及答案
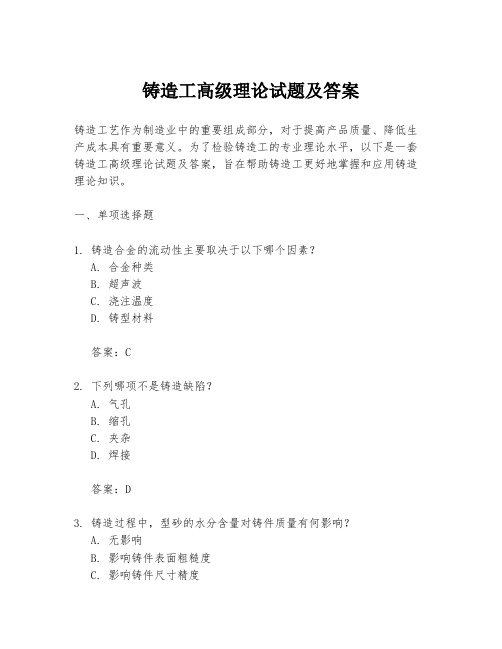
铸造工高级理论试题及答案铸造工艺作为制造业中的重要组成部分,对于提高产品质量、降低生产成本具有重要意义。
为了检验铸造工的专业理论水平,以下是一套铸造工高级理论试题及答案,旨在帮助铸造工更好地掌握和应用铸造理论知识。
一、单项选择题1. 铸造合金的流动性主要取决于以下哪个因素?A. 合金种类B. 超声波C. 浇注温度D. 铸型材料答案:C2. 下列哪项不是铸造缺陷?A. 气孔B. 缩孔C. 夹杂D. 焊接答案:D3. 铸造过程中,型砂的水分含量对铸件质量有何影响?A. 无影响B. 影响铸件表面粗糙度C. 影响铸件尺寸精度D. 影响铸件的内部结构答案:C4. 金属型铸造与砂型铸造相比,其主要优点是什么?A. 成本低B. 精度高C. 易于大规模生产D. 材料利用率高答案:B5. 压力铸造与重力铸造的主要区别在于?A. 铸件材料B. 铸型材料C. 浇注方式D. 冷却速度答案:C二、判断题1. 铸造过程中,提高浇注温度可以提高铸件的表面质量。
(对/错)答案:对2. 所有铸造合金都可以通过改变成分来提高其流动性。
(对/错)答案:错3. 铸造缺陷的产生与铸造工艺无关,完全取决于材料本身。
(对/错)答案:错4. 金属型铸造适用于大批量生产。
(对/错)答案:对5. 铸造过程中,型砂的紧实度越高,铸件的尺寸精度越高。
(对/错)答案:错三、简答题1. 简述铸造工艺中“缩孔”和“缩松”的区别。
答案:缩孔是指铸件在凝固过程中,由于收缩而在铸件内部或表面形成的孔洞,通常呈现为宏观可见的圆形或椭圆形空洞。
而缩松则是铸件内部的微小孔洞,通常不可见,是由于铸件最后凝固部分的收缩未能得到充分的金属液补充而形成。
缩松通常通过超声检测或射线检测来发现。
2. 论述影响铸件冷却速度的因素。
答案:铸件的冷却速度受多种因素影响,主要包括:- 铸件材料:不同材料的热传导性能不同,影响冷却速度。
- 铸件壁厚:壁厚越大,热量传递到外部的难度越高,冷却速度越慢。
铸造工理论知识复习题(2)
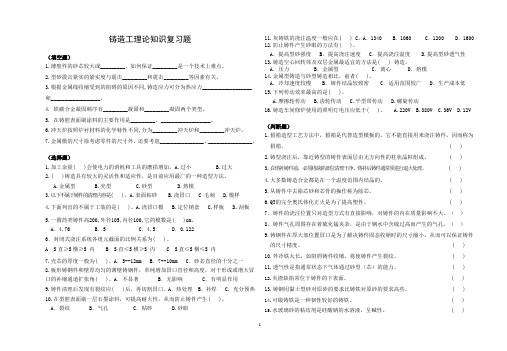
铸造工理论知识复习题(填空题)1.薄壁件的砂芯较大或_________,如何保证_________是一个技术上难点。
2.型砂震击紧实的紧实度与震击_________和震击_________等因素有关。
3.根据金属线收缩受到的阻碍的原因不同,铸造应力可分为热应力__________________和__________________。
4. 铁碳合金凝固顺序有_________凝固和_________凝固两个类型。
5. 在铸腔表面刷涂料的主要作用是_________、__________________。
6.冲天炉按照炉衬材料的化学特性不同,分为_________冲天炉和_________冲天炉。
7.金属模的尺寸除考虑零件的尺寸外,还要考虑________________、________________。
(选择题)1.加工余量( )会使电力的消耗和工具的磨损增加。
A.过小 B.过大2.( )铸造具有较大的灵活性和适应性,是目前应用最广的一种造型方法。
A.金属型B.壳型C.砂型D.熔模3.以下不属于铸件的清理内容是( )。
A.表面粘砂 B.浇冒口 C 毛刺 D.模样4.下面列出的不属于工装的是( )。
A.浇冒口模 B.定位销套 C.样板 D.刮板5.一圆筒类铸件高200,外径105,内径100,它的模数是( )cm。
A.4.76 B.5 C.4.5 D.0.1226.封闭式浇注系统各组元截面的比例关系为( )。
A S直≥S横≥S 内B S直≤S横≥S 内C S直≤S横≤S 内7.壳芯的厚度一般为( )。
A.5--12mm B.7--10mm C.砂芯直径的十分之一8.板形铸钢件和壁厚均匀的薄壁铸钢件,单纯增加冒口直径和高度,对于形成或增大冒口的补缩通道扩张角( )。
A.不显著 B.无影响 C.有明显作用9.铸件清理后发现有裂纹应( )后,再切割冒口。
A.热处理 B.补焊 C.充分预热10.在型腔表面刷一层石墨涂料,可提高耐火性,从而防止铸件产生( )。
铸造工艺理论基础测验题
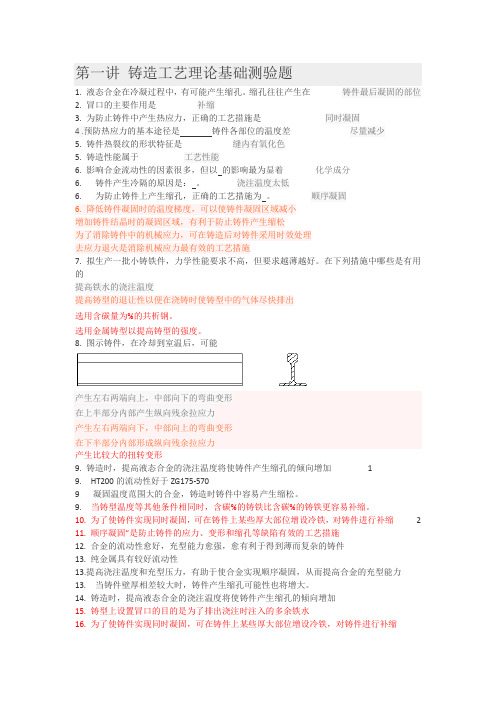
第一讲铸造工艺理论基础测验题1. 液态合金在冷凝过程中,有可能产生缩孔。
缩孔往往产生在铸件最后凝固的部位2. 冒口的主要作用是补缩3. 为防止铸件中产生热应力,正确的工艺措施是同时凝固4 .预防热应力的基本途径是铸件各部位的温度差尽量减少5. 铸件热裂纹的形状特征是缝内有氧化色5. 铸造性能属于工艺性能6. 影响合金流动性的因素很多,但以的影响最为显着化学成分6. 铸件产生冷隔的原因是:。
浇注温度太低6. 为防止铸件上产生缩孔,正确的工艺措施为。
顺序凝固6. 降低铸件凝固时的温度梯度,可以使铸件凝固区域减小增加铸件结晶时的凝固区域,有利于防止铸件产生缩松为了消除铸件中的机械应力,可在铸造后对铸件采用时效处理去应力退火是消除机械应力最有效的工艺措施7. 拟生产一批小铸铁件,力学性能要求不高,但要求越薄越好。
在下列措施中哪些是有用的提高铁水的浇注温度提高铸型的退让性以便在浇铸时使铸型中的气体尽快排出选用含碳量为%的共析钢。
选用金属铸型以提高铸型的强度。
8. 图示铸件,在冷却到室温后,可能产生左右两端向上,中部向下的弯曲变形在上半部分内部产生纵向残余拉应力产生左右两端向下,中部向上的弯曲变形在下半部分内部形成纵向残余拉应力产生比较大的扭转变形9. 铸造时,提高液态合金的浇注温度将使铸件产生缩孔的倾向增加19. HT200的流动性好于ZG175-5709 凝固温度范围大的合金,铸造时铸件中容易产生缩松。
9. 当铸型温度等其他条件相同时,含碳%的铸铁比含碳%的铸铁更容易补缩。
10. 为了使铸件实现同时凝固,可在铸件上某些厚大部位增设冷铁,对铸件进行补缩211. 顺序凝固”是防止铸件的应力、变形和缩孔等缺陷有效的工艺措施12. 合金的流动性愈好,充型能力愈强,愈有利于得到薄而复杂的铸件13. 纯金属具有较好流动性13.提高浇注温度和充型压力,有助于使合金实现顺序凝固,从而提高合金的充型能力13. 当铸件壁厚相差较大时,铸件产生缩孔可能性也将增大。
熔炼、铸造和均质的基础理论

有色金属熔炼和铸造一. 基本原理1.熔炼和铸造的定义:熔炼的含义:就是将各种胚锭通过加温重熔的方法,实现由固态向液态转变的同时,进行合金化的过程.在熔炼的过程中,将实现净化除杂的目的.铸造的含义:将符合铸锭要求的金属熔体通过转注工具浇入到具有一定形状的铸模 中,使熔体在重力场或外力场的作用下充满模腔,冷却并凝固成型的工艺过程.它不仅要实现外部定型,而且还要实现对内部的微观组织结构的调控.二. 铝及其合金的熔炼1.熔炼的传热过程铝的熔点虽然很低(660℃),但由于熔化潜热(395.56kJ/kg)、固态热容(1.1386kJ/kg. ℃)和液态热容(1.046kJ/kg. ℃)都较高,而铝的黑度是铜铁的1/4,所以铝熔炼耗能大,很难实现理想的热效率。
热的传递方式有三种,传导、对流和辐射。
要提高金属的受热量,一方面提高炉温,这对炉体和熔体都不利,另一方面铝的黑度小,故提高辐射传热也是有限的,因此只能着眼于增大对流的传热系数(αc),它与气流速度的关系:αc=5.3+3.6v[kJ/(m2 h.℃)] V<5m/s时αc=647+v0.78 [kJ/(m2 h.℃)] V>5m/s时可见提高燃烧的气流速度是有效的。
2.合金元素的溶解和蒸发熔炼温度下(700℃)几种元素在铝中的扩散系数为(cm2/s):Ti:0.66,Mo:1.38(760℃),Co:0.79,Ni:1.44,Si:14.4,通常情况下,与铝形成易熔共晶的元素,一般较易熔解,与铝形成包晶转变的,特别是熔点相差大的元素较难于溶解。
在相同溶解条件下,一般蒸气压高的元素容易挥发,可把常用的铝合金分为两组:Cu、Cr、Fe、Ni、Ti、Si、V、Zr等元素的蒸气压比铝的小,蒸发慢,Mn、Li、Mg、Zn、Na、Cd等元素蒸气压比铝的大,容易蒸发,在熔炼过程中损失较大。
3.熔炼的吸气过程铝—氧反应金属以熔融态或半熔融态暴露于炉气中并与之相互作用时间越长,往往造成金属大量吸气,氧化和形成其它非金属夹杂,其反应分为:吸附、界面反应和熔解(扩散)。
铸造涂料理论
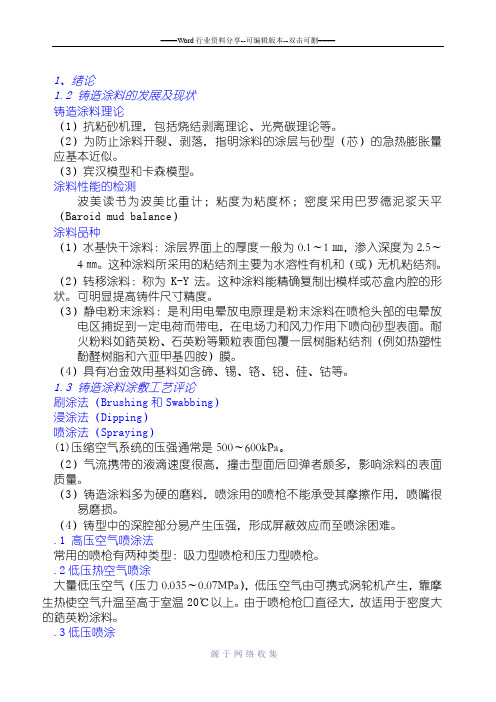
1、绪论1.2 铸造涂料的发展及现状铸造涂料理论(1)抗粘砂机理,包括烧结剥离理论、光亮碳理论等。
(2)为防止涂料开裂、剥落,指明涂料的涂层与砂型(芯)的急热膨胀量应基本近似。
(3)宾汉模型和卡森模型。
涂料性能的检测波美读书为波美比重计;粘度为粘度杯;密度采用巴罗德泥浆天平(Baroid mud balance)涂料品种(1)水基快干涂料:涂层界面上的厚度一般为0.1~1㎜,渗入深度为2.5~4㎜。
这种涂料所采用的粘结剂主要为水溶性有机和(或)无机粘结剂。
(2)转移涂料:称为K-Y法。
这种涂料能精确复制出模样或芯盒内腔的形状。
可明显提高铸件尺寸精度。
(3)静电粉末涂料:是利用电晕放电原理是粉末涂料在喷枪头部的电晕放电区捕捉到一定电荷而带电,在电场力和风力作用下喷向砂型表面。
耐火粉料如鋯英粉、石英粉等颗粒表面包覆一层树脂粘结剂(例如热塑性酚醛树脂和六亚甲基四胺)膜。
(4)具有冶金效用基料如含碲、锡、铬、铝、硅、钴等。
1.3 铸造涂料涂敷工艺评论刷涂法(Brushing和Swabbing)浸涂法(Dipping)喷涂法(Spraying)(1)压缩空气系统的压强通常是500~600kPa。
(2)气流携带的液滴速度很高,撞击型面后回弹者颇多,影响涂料的表面质量。
(3)铸造涂料多为硬的磨料,喷涂用的喷枪不能承受其摩擦作用,喷嘴很易磨损。
(4)铸型中的深腔部分易产生压强,形成屏蔽效应而至喷涂困难。
.1 高压空气喷涂法常用的喷枪有两种类型:吸力型喷枪和压力型喷枪。
.2低压热空气喷涂大量低压空气(压力0.035~0.07MPa),低压空气由可携式涡轮机产生,靠摩生热使空气升温至高于室温20℃以上。
由于喷枪枪口直径大,故适用于密度大的鋯英粉涂料。
.3低压喷涂该搅拌器靠气动马达驱动,用于近距离(300~380㎜)、大流量喷涂。
.4高压无空气喷涂这种工艺是用液体压力喷出涂料。
将涂料贮存在高压容器中,通过喷枪上的特殊喷嘴,涂料分散成小滴。
铝合金压铸理论计算

=
10 ms
充填速 率Q
(l/s) x
= 10 冲头截 面积
(cm2)
= 8.51852 l/s X 10
=
28.2743 cm2
流道截面积 AGl
充填速 率Qx = 1000 流道速 度 VGL
进料口总截面积 AA
充填速 率Qx = 1000
进料口 速度 VA
= 8.51852 l/s X 1000 = 15 m/s
冷室压铸机模具进料口尺寸理论计算
表
产品编号/名称 产品材料 产品重量 (单腔) 渣包重量 (单腔) 型腔数目 进料口速度(见表三) 最小壁厚 充填时间(见表一)
XXXXXXXX
Aluminum
200 g
30 g
1
n
40 m/s
1.5 mm
10 ms
机器型 号冲头直 径冲头截 面材积料密 度铸造压 力是(否见机表 械是载否荷耐 气是密否/电大 镀/喷
LK 160
T
Φ 60 mm
28.2743339 cgm/c2
2.7
m3
500 bar
Y
充填重量 充填体积 充填速率 (Q)
冲头速率
(产品重
量+
渣包重
量)
X型
腔数目
= (n)
= 200 g + 30 g X
1 (n)
=
充填重 =量
材料密 度
=
230 g
=
g/cΒιβλιοθήκη 2.7 m3充填体 =积
充填时 间
= 85.1852 cm3
1
=
212.96296 mm2
表一:产品充填时间与最小壁厚对照表
铸造技师理论考试试题汇总
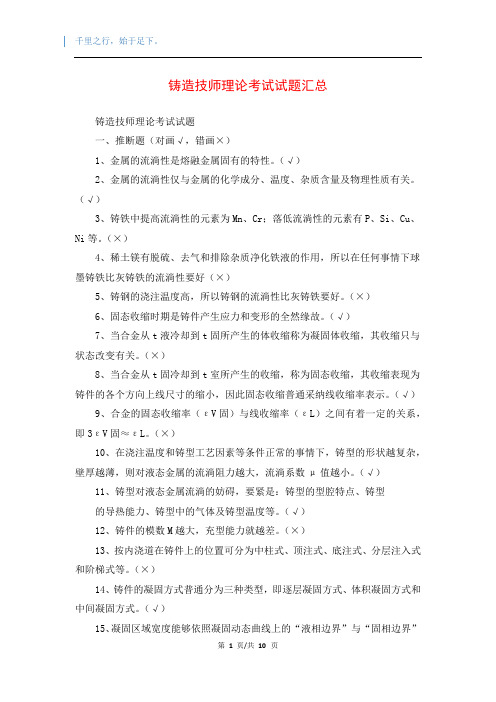
铸造技师理论考试试题汇总铸造技师理论考试试题一、推断题(对画√,错画×)1、金属的流淌性是熔融金属固有的特性。
(√)2、金属的流淌性仅与金属的化学成分、温度、杂质含量及物理性质有关。
(√)3、铸铁中提高流淌性的元素为Mn、Cr;落低流淌性的元素有P、Si、Cu、Ni等。
(×)4、稀土镁有脱硫、去气和排除杂质净化铁液的作用,所以在任何事情下球墨铸铁比灰铸铁的流淌性要好(×)5、铸钢的浇注温度高,所以铸钢的流淌性比灰铸铁要好。
(×)6、固态收缩时期是铸件产生应力和变形的全然缘故。
(√)7、当合金从t液冷却到t固所产生的体收缩称为凝固体收缩,其收缩只与状态改变有关。
(×)8、当合金从t固冷却到t室所产生的收缩,称为固态收缩,其收缩表现为铸件的各个方向上线尺寸的缩小,因此固态收缩普通采纳线收缩率表示。
(√) 9、合金的固态收缩率(εV固)与线收缩率(εL)之间有着一定的关系,即3εV固≈εL。
(×)10、在浇注温度和铸型工艺因素等条件正常的事情下,铸型的形状越复杂,壁厚越薄,则对液态金属的流淌阻力越大,流淌系数μ值越小。
(√)11、铸型对液态金属流淌的妨碍,要紧是:铸型的型腔特点、铸型的导热能力、铸型中的气体及铸型温度等。
(√)12、铸件的模数M越大,充型能力就越差。
(×)13、按内浇道在铸件上的位置可分为中柱式、顶注式、底注式、分层注入式和阶梯式等。
(×)14、铸件的凝固方式普通分为三种类型,即逐层凝固方式、体积凝固方式和中间凝固方式。
(√)15、凝固区域宽度能够依照凝固动态曲线上的“液相边界”与“固相边界”之间的横向距离直截了当举行推断。
(×)16、在实际生产中,铸件的收缩受到外界阻力的妨碍,对同一合金而言,受阻收缩率大于自由收缩率。
(×)17、铸造应力按期产生的缘故分为三种:热应力、相变应力和收缩应力。
铸件形成理论基础

第一章能量起伏:金属晶体结构中每个原子的振动能量不是均等的,一些原子的能量超过原子的平均能量,有些原子的能量则远小于平均能量,这种能量的不均匀性称为“能量起伏”近程有序排列:金属液体则由许多原子集团所组成,在原子集团内保持固体的排列特征,而在原子集团之间的结合处则受到很大破坏。
这种仅在原子集团内的有序排列称为近程有序排列。
浓度起伏:不同原子间结合力存在差别,在金属液原子团簇之间存在着成分差异。
这种成分的不均匀性称为浓度起伏。
实际金属的液态结构实际金属中总存在大量杂质和溶质原子,所以其液态除了存在能量起伏和结构起伏以外,还存在浓度起伏。
实际液态金属在微观上是由存在能量起伏、结构起伏和成分起伏的游动原子集团、空穴和许多固态、气态或液态的化合物组成的混浊液体;从化学键上看,除了基体金属与其合金元素组成的金属键之外,还存在其他多种类型的化学键。
影响表面张力的因素1)熔点:高熔点的物质,其原子间结合力大,其表面张力也大。
2)温度:大多数金属和合金,温度升高,表面张力降低。
3)溶质:向系统中加入削弱原子间结合力的组元,会使表面内能和表面张力降低。
第二章液态金属的充型能力一、水力学特点1、液态金属在砂型流动时具有的特性:①粘性液体流动②多相流动③不稳定流动④紊流流动⑤在‘多孔管’中流动2、什么是液态金属充填铸型能力答:液态金属充满铸型型腔,获得形状完整、轮廓清晰的能力。
3、影响液态金属充型能力的因素:①取决于金属本身的流动性②受外界影响(铸型性质、杂质含量、)4、充型能力不好的缺陷:浇不足、冷隔5、用浇注“流动性试样”方法衡量流动性、试样类型有:螺旋形、球形、真空试样。
四、液态金属充型能力的计算l=v τ gH v 2μ=五、影响充型能力的因素和措施因素:金属性质方面:(①密度②比热③导热系数④结晶潜热⑤动力粘度)铸型性质方面:(①铸型蓄热系数②铸型密度③铸型比热④铸型温度⑤铸型发气性和透气性)浇注条件方面:(①浇注温度②液态金属静压头③外力场)铸件结构方面:(①铸件的折算率 ②压头损失)凝固过程中释放的潜热越多,则凝固进行的越缓慢,流动性就越好措施:金属性质:(①正确选择合金成分②合理的熔炼工艺)铸型性质:(①选择蓄热系数低的铸型材料②预热铸型③适当降低型砂中的含水量和发气 ④量提高砂型的透气性)浇注方面:(①合理提高提高浇注温度②增加金属液静压头③选择恰当的浇注系统结构)铸件结构:(选择适当的浇注位置)第三章 铸件的凝固一:凝固动态曲线(书本76页)二:铸件的凝固方式(书本77-78页):1、逐层凝固方式2、体积凝固方式3、中间凝固方式铸件的凝固方式取决于凝固区域的宽度。
铸件形成理论习题答案
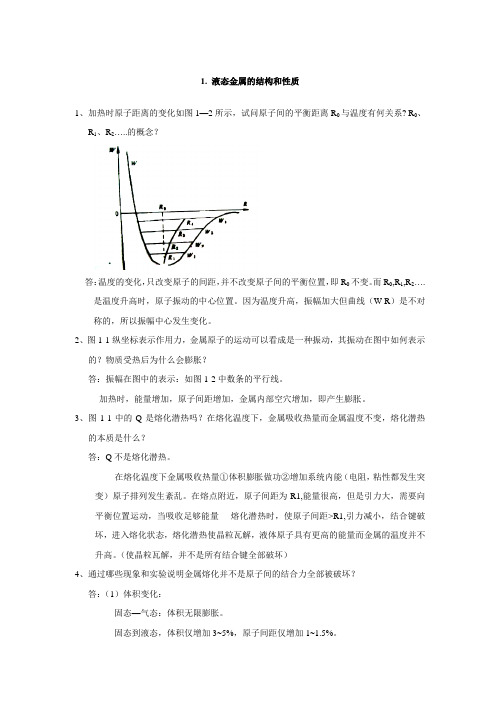
1. 液态金属的结构和性质1、加热时原子距离的变化如图1—2所示,试问原子间的平衡距离R0与温度有何关系? R0、R1、R2…..的概念?答:温度的变化,只改变原子的间距,并不改变原子间的平衡位置,即R0不变。
而R0,R1,R2….是温度升高时,原子振动的中心位置。
因为温度升高,振幅加大但曲线(W-R)是不对称的,所以振幅中心发生变化。
2、图1-1纵坐标表示作用力,金属原子的运动可以看成是一种振动,其振动在图中如何表示的?物质受热后为什么会膨胀?答:振幅在图中的表示:如图1-2中数条的平行线。
加热时,能量增加,原子间距增加,金属内部空穴增加,即产生膨胀。
3、图1-1中的Q是熔化潜热吗?在熔化温度下,金属吸收热量而金属温度不变,熔化潜热的本质是什么?答:Q不是熔化潜热。
在熔化温度下金属吸收热量①体积膨胀做功②增加系统内能(电阻,粘性都发生突变)原子排列发生紊乱。
在熔点附近,原子间距为R1,能量很高,但是引力大,需要向平衡位置运动,当吸收足够能量----熔化潜热时,使原子间距>R1,引力减小,结合键破坏,进入熔化状态,熔化潜热使晶粒瓦解,液体原子具有更高的能量而金属的温度并不升高。
(使晶粒瓦解,并不是所有结合键全部破坏)4、通过哪些现象和实验说明金属熔化并不是原子间的结合力全部被破坏?答:(1)体积变化:固态—气态:体积无限膨胀。
固态到液态,体积仅增加3~5%,原子间距仅增加1~1.5%。
(2)熵值变化:△Sm/△S 仅为0.13~0.54% (3)熔化潜热:原子结合键只破坏了百分之几(4)X 线衍射分析:液态金属原子分布曲线波动于平衡密度曲线上下第一峰位置和固态衍射线极为相近,其配位数也相近,第二峰值亦近似。
距离再大,则与固态衍射线远了,液态金属中原子的排列在几个原子间距的范围内,与其固态的排列方式基本一致。
5、纯金属和实际金属在结构上有何异同?试分析铸铁的液态结构。
答:纯金属的液态结构:接近熔点的液态金属是由和原子晶体显微晶体和“空穴”组成。
铸造基本知识及理论

程中,其体积或尺寸缩减的现象。
分类:分为三类,液态收缩、凝固收缩和固态收缩。
浇注温度
铸 液态收缩
件 温
开始凝固温度
体
度 降
凝固收缩
积 收
低
缩
凝固终止温度
固态收缩
室温
线收缩
收缩率:
体积收缩是指单位体积的收缩量(体积收缩率)。 线收缩是指单位长度上的收缩量(线收缩率)。
体积收缩率:
V
V0 V1 100% V1
2、型砂的影响: 1)原砂、粘结剂和稀释剂的成分配比; 型砂
原砂
稀释剂
粘结剂
石
铬
锆
英
铁
英
砂
矿
砂
砂
水
粘
水
树
溶
玻
剂
土
璃
脂
2)原砂的形状、粒度状况
一般认为:粒度在小尺寸范围呈正态分布,有利于
砂型强度的提高,但透气性较差。
➢
工 艺 过 程
特点及应用:
1、不受铸件材质、尺寸、质量和生产批量的限制; 2、属于一次性铸造成形,造型工作量大; 3、铸件精度和表面质量差; 4、砂型铸造缺陷多,废品率高,机械性能较差; 5、设备简单、投资少,价格低廉,应用广泛。
连续铸造:
➢ 定义:是指将熔融金属连续不断地浇注到被成为结晶
器的特殊容器中,凝固的铸件不断从结晶器的另一端被引 出,从而获得任意长度的等横截面铸件的铸造方法。
➢ 工艺过程:如右图所示。
➢ 特点和应用:
1、冷却速度快,组织致密, 机械性能好;
2、工艺简单,生产效率高; 3、适于横截面一定的钢材、
铝材和铸铁管等铸件的生产。
阶 段 主要影响因素
铸件形成理论复习提纲
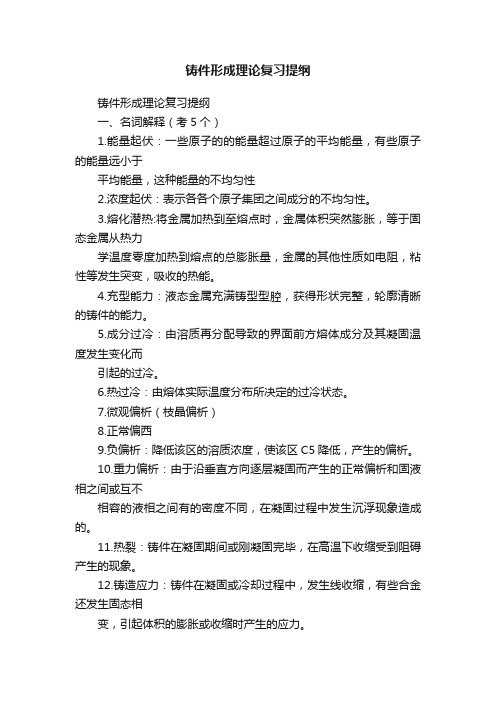
铸件形成理论复习提纲铸件形成理论复习提纲一、名词解释(考5个)1.能量起伏:一些原子的的能量超过原子的平均能量,有些原子的能量远小于平均能量,这种能量的不均匀性2.浓度起伏:表示各各个原子集团之间成分的不均匀性。
3.熔化潜热:将金属加热到至熔点时,金属体积突然膨胀,等于固态金属从热力学温度零度加热到熔点的总膨胀量,金属的其他性质如电阻,粘性等发生突变,吸收的热能。
4.充型能力:液态金属充满铸型型腔,获得形状完整,轮廓清晰的铸件的能力。
5.成分过冷:由溶质再分配导致的界面前方熔体成分及其凝固温度发生变化而引起的过冷。
6.热过冷:由熔体实际温度分布所决定的过冷状态。
7.微观偏析(枝晶偏析)8.正常偏西9.负偏析:降低该区的溶质浓度,使该区C5降低,产生的偏析。
10.重力偏析:由于沿垂直方向逐层凝固而产生的正常偏析和固液相之间或互不相容的液相之间有的密度不同,在凝固过程中发生沉浮现象造成的。
11.热裂:铸件在凝固期间或刚凝固完毕,在高温下收缩受到阻碍产生的现象。
12.铸造应力:铸件在凝固或冷却过程中,发生线收缩,有些合金还发生固态相变,引起体积的膨胀或收缩时产生的应力。
13.冷裂:铸件应力超出合金强度极限而产生的现象。
14.顺序凝固:铸件结构各部分,按照远离冒口的部分最先凝固,然后是靠近冒口部位,最后是冒口本身凝固的次序进行的凝固方式15.同时凝固:铸件各部分之间没有温差或温差尽量小,使各部分同时进行凝固的方式。
16.析出性气孔:金属液在凝固过程中,因气体溶解度下降而析出气体,形成气泡未能排除而产生的气孔。
17.反应性气孔:金属液与铸型之间,金属与熔渣之间或金属液内部某些元素、化合物之间发生化学反应所产生的气孔。
二、填空题(不限于这些)1.减小或消除残余应力的方法有人工、自然、共振时放。
2.润湿角是衡量界面张力的标志,润湿角≥90o,表明液体不能润湿体。
3.晶体结晶时,有时会以枝晶生长方式进行。
此时固液界面前液体中的温度梯度小于0 。
铝合金铸造基础知识课堂PPT

冷芯制芯
冷芯制芯:
将树脂砂填入冷芯模,而后吹气硬化制成坭芯。 根据使用的粘结剂和所吹气体及其作用的不同,而 有三乙胺法、SO2法、酯硬化法、低毒和无毒气体 促硬制芯法。
三乙胺法:一般用干燥的压缩空气或氮气作液态硬 化剂(三乙胺)的载体气体,稀释到约5%浓度,形 成三乙胺气雾,向冷芯模中填入树脂砂后再吹入三 乙胺气雾,树脂砂便能在数秒至数十秒内硬化制成 所需要强度的坭芯。
36
壳芯制芯
壳芯:进排气道
37
壳芯制芯
壳芯制芯的优点: ➢混制好的覆膜砂可以较长期贮存(三个月以上); ➢能获得尺寸精确的坭芯; ➢坭芯的强度高、质量轻、易搬运; ➢可用细的原砂得到光洁的铸件表面; ➢覆膜砂消耗量小。
38
壳芯制芯
壳芯制芯的缺点: (一)壳芯表面易疏松 覆膜砂流动性差; 排气不当,在深凹处疏松和缺肉的,多是排气不好; 射砂压力太低; 射砂时间太短; 覆膜砂所使用的原砂太粗。
42
冷芯制芯
冷芯:冒口芯
43
冷芯制芯
冷芯制芯的冷芯树脂(粘结剂)由两部分组成,组 分Ⅰ是酚醛树脂,组分Ⅱ是聚异氰酸酯。
硬化反应:
酚醛树脂+聚异氰酸酯 三乙胺 尿烷
采用三乙胺法制芯时,原砂采用干净的AFS的细度 50-60的硅砂。
原砂必须干燥,水分超过0.1%(质量分数)就会减 少树脂砂的可使用时间,降低坭芯的抗拉强度,也 会增加铸件针孔缺陷。
第三章 铝液的熔化 及精炼处理
47
熔炼炉的操作
➢第一节 熔炼炉的简介 ➢第二节 铝合金熔炼理论知识
48
熔炼炉的简介 熔炼炉的分类:
熔炼炉
火焰炉
感应炉
电阻炉
49
熔炼炉的简介
铸造理论基础

33
§1-4 液态金属结晶的基本原理 一、液态金属的结晶过程
2.液态金属的结晶过程 晶核形成
界面 长大 热力学能障
能量障碍
动力学能障
材料成型与控制工程专业
34
§1-4 液态金属结晶的基本原理 二、生核过程
1.生核分类 均质生核(自 发生核)
分 类
非均质生核(异质 生核)
界面:
1280 ~ 1180
15
§1-2 液态金属的充型能力 三、影响充型能力的因素及提高充型能力的措施
•3浇注条件 2)充型压头
液态金属在流动方向上所受的压力 越大,充型能力就越好; 不良后果?
采取措施:
1)增加金属静压头h;
2)其它方式如压铸等; 3)浇注系统的结构
材料成型与控制工程专业
16
§1-2 液态金属的充型能力 三、影响充型能力的因素及提高充型能力的措施
•2铸型方面 3)铸型中气体 发气能力:在金属液与铸型之间形成气膜, 可减小流动的摩擦阻力,有利于充型
减小反压力途径:
1)减少砂型的发气性(适当降低含水量和发气物 质含量);
2)提高砂型透气性(扎通气孔,设冒口等)
材料成型与控制工程专业
14
§1-2 液态金属的充型能力 三、影响充型能力的因素及提高充型能力的措施
材料成型与控制工程专业
37
§1-4 液态金属结晶的基本原理 二、生核过程
局限性: 克服高能量障碍,所需的过冷度是很大的。 ΔT=(0.18-0.2)T熔 如:纯Al T熔=660℃,ΔT=195℃;
但实际上金属结晶时的过冷度一般只有十几摄氏度或 几分之一摄氏度,远小于均质生核所需的过冷度。
铸造技术及计算公式理论东芝机械株式会社著

3. 澆鑄是一種鑄造法 合金溶湯(熱溶液)凝固之前,高速將模穴內的空氣替換溶湯,以高壓使其凝固的方法。
澆鑄法
模具 產品形状 鑄造方案
4. 鑄造產品
外觀完好、尺寸精度高的產品。
鑄造機 鑄造条件
材料
合金特性 溶解 溶湯(熱溶液)處理
模具 柱塞直徑 : 產品肉厚 : 產品重量 : 投影面積 : 材料: 溶湯温度 :
× ACC壓力 × 0.9
アキュムレータ圧力ドロップ
(2)昇壓時間
必須在鋁溶湯在穴內凝固前加壓。 昇壓時間=0.01 × 產品肉厚 (tm) × 產品肉厚 (tm)
蓄壓器的壓力在95㎏/㎝2 ~135㎏/㎝2之間,可經由氮氣 排出來做調整。 TOSCAST的話,鑄造壓力可透過輸入方式來進行。
(3) 射出力
低速速度太快時
柱塞
低速速度適當時
柱塞
(1) 料管填充率
料管充填率指的是溶湯注入時料管內的溶湯比率。
料管填充率 =
鑄入重量 柱塞剖面積×空打行程×溶湯比重
×100 %
(2)低速速度
低速速度是在料管內沒有空氣進入的範圍下進行加速。
低速速度的標準
0.7 × 柱塞直徑 低速速度 =
料管填充率
低速速度
低速區間中沒有速度變化。
時間 *低速啟動是在沒有啟動衝擊的狀態下 至順利地啟動至低速速度為止。
铸造工艺基础知识及理论

4
铸造材料
1
工艺基础 工艺性能
2
铸件生产
铸造工艺
3 工艺方法
1. 金属液态成形(铸造)工艺基础
什么是金属的液态成形:
将熔炼好的液态金属浇入与零件形 状相适应的铸型空腔中,待其冷却凝固, 以获得毛坯或零件的工艺方法,亦称铸造.
金属的液态成形的方法:
金属的液态成形是制造毛坯、零件的重要方法之一。按铸型材 料的不同,金属液态成形可分为砂型铸造和特种铸造(包括压力铸 造、金属型铸造等).其中砂型铸造是最基本的液态成形方法,所生 产的铸件要占铸件总量的80%以上.特种铸造较适用于大批量生产, 应用范围逐渐增加。
松
的 方
方法
合理布置内浇道及确定浇铸工艺。
法
合理应用冒口、冷铁和补贴等工艺措施。
3. 铸件的生产工艺
整模造型
分模造型
手工造型
砂型铸造
活块造型 三箱造型
液
挖砂造型
态
机器造型
刮板造型
成
铸造工艺图的绘制
型
砂型铸造的工艺设计
分型面的选择
工
工艺参数的确定 浇注位置的确定
艺
金属型铸造
熔模铸造
压力铸造
特种铸造
低压铸造 陶瓷型铸造
内是由表及里的逐层凝固。在凝固过程中,如得不到合金液的 补充,在铸件最后凝固的地方就会产生缩孔.
2. 铸件的生产—缩松的形成 缩松的形成原因:
铸件最后凝固的收缩未能得到补充,或者结晶温度范围宽的 合金呈糊状凝固,凝固区域较宽,液、固两相共存,树枝晶发 达,枝晶骨架将合金液分割开的小液体区难以得到补缩所致。
合金的收缩的过程:
合金从液态冷却至室温的过程中,其体积或尺寸缩减的 现象。合金的收缩给液态成形工艺带来许多困难,会造成许 多铸造缺陷。(如:缩孔、缩松、裂纹、变形等)。
- 1、下载文档前请自行甄别文档内容的完整性,平台不提供额外的编辑、内容补充、找答案等附加服务。
- 2、"仅部分预览"的文档,不可在线预览部分如存在完整性等问题,可反馈申请退款(可完整预览的文档不适用该条件!)。
- 3、如文档侵犯您的权益,请联系客服反馈,我们会尽快为您处理(人工客服工作时间:9:00-18:30)。
(3) 适用于各种批量的生产;
3. 铸造生产成本较低 由于铸造过程中使用的造型材料、模样(或模板)、
砂箱等各种装备都可以反复使用,所以大批量生产时, 铸件的成本较低。
4. 铸件的力学性能较低 由于液态成形件
晶粒粗大,内部组织 的均匀性及致Байду номын сангаас度都 较低,所以铸件的综 合力学性能(特别是 塑性)较差。
1
热应力
结果:铸件缓冷处(厚壁或心部)受拉伸;
快冷处(薄壁或表层)受压缩。
应力防治: 设计时,应尽量使铸件的壁厚均匀;
铸造时,应采用同时凝固的原则制定工艺。
大牙圈铸造工艺特点:
(1)采用底注式浇注系 统,铁水从20个内浇口 均匀地切入型腔,充型 平稳。 (2)滚齿部分放置外冷 铁圈,保证铸件同时凝 固。 (3)上表面均匀地放置 8个冒口,起补缩和出气 的作用。
(2)理论联系实际
金工实习 金工实验 机械创新设计及制造大赛
(3)以自学为主 ,通过课堂教学、讨论与答疑、课后 练习与实验等方式辅助学习。
以教材为主,根据需要参看有关书籍。 主要参考资料: 1. «材料成形工艺基础» 沈其文 主编 华中科技大学出版社 2. «机械制造技术基础» 熊良山 主编 华中科技大学出版社
2. 合金的收缩性 从浇铸到室温铸件的体积或尺寸缩减的现象。 合金收缩的三个阶段:
(1)液态收缩 液 (2)凝固收缩 凝
用体收缩率表示。
(3)固态收缩 固 用线收缩率表示。
总= 液+凝+固
讨论: 在常用铸造合金中,为
什么钢的收缩率大(约为12%) ,铁的收缩率小(约7.8%)?
铸件中的缩孔和缩松
凡能熔化成液态的材料(包括金 属、塑料和陶瓷等)几乎均可用于铸 造。而应用广泛的铸铁件只能通过 铸造方法成形。
(2) 铸件的大小几乎不受限制;
出土于曾侯乙墓的编钟,是我国战国早期的打击乐器,共有64件,总重 量2567公斤,全部为青铜铸件。其中最小的一件重2.4公斤,高20.2厘米;最 大的一件重203.6公斤,高153.4厘米。
§1-1 合金的铸造性能 1. 合金的充型能力
液态合金充满型腔、获得形 状完整、轮廓清晰铸件的能力。
(1)合金的流动性 液态金属自身的流动能力。其
大小主要受合金化学成分的影响。 结论:
共晶合金的流动性好,结晶间隔大的合金流动性差。
(2) 浇注条件
a) 浇注温度 b) 充型压力
(3) 铸型条件
a)铸型导热能力 b)铸型温度 c)铸型中的气体
(1) 180转/分 (2) 720转/分 (1)金属型 (2)硅橡胶型
讨论:
(1)Sn-10%Pb (2)Sn-37%Pb
(1) 在离心铸造实习中,为什么不使用纯锡而选用锡铅合金? (2) 当加热温度过高时,金属液会产生什么现象? 这种状况对 铸件质量有何影响? (3) 当模具转速过高时,铸件易产生什么缺陷? 怎样防治? (4) 试比较金属型、砂型、橡胶型的导热性,根据铸件的尺寸 变化如何选用铸型?
提问: 该梁壁厚均匀,为什么还会产生变形?
怎样改进槽型梁的结构?
采用“反变形”工艺;
车床床身挠曲变形示意图
(3) 铸件的裂纹与防止
裂纹产生的条件: 内 > b 1) 热裂纹
铸件凝固末期、在接近固相线的高温下形成的。
2) 冷裂纹 在较低温度下,铸件的
内应力超过了合金的强度极 限而产生的。
3) 防止裂纹的措施 a、增加型砂和芯砂的退让性。 b、设计铸造园角或防裂筋。
3. 合金的吸气性 析出气孔 在冷却及凝固过程中,因气体溶解度下降,
析出气体,来不及从液面排出而形成气孔。
Al-Si合金中的典型析出性气孔
作业1: 图示槽形梁,铸造后立即进行了机械加工,使用
一段时间后在梁的长度方向发生了弯曲变形,试分析: ① 该梁壁厚均匀,为什么还会变形?判断梁的变形方向; ② 有何铸造工艺措施能减少变形? ③ 为防止铸件变形,请改进槽型梁的结构。
实验报告占10
成绩评定办法:
作业及表现占20
考试成绩占70 考试方式: 开卷。
第1章 铸造工艺
铸造是将液态金属浇入铸型型腔,使其冷却凝固 而获得毛坯或零件的成形工艺。
铸造成形的特点: 1. 可以生产形状复杂(特别是内腔复杂)的毛坯或零件。
2. 铸造生产的适应范围广。 (1) 使用的材料广泛;
2)机械应力 是铸件的固态收缩受到铸型或型芯等机械阻碍
而形成的内应力。
防治: 提高铸型和型芯的退让性; 通过退火处理消除内应力。
(2) 铸件的变形与防止 1)变形条件:内 > S ,铸件将自发地通过变形来缓 解其内应力,以趋稳定。
2)变形方向: 受拉部位尺寸减小 , 受压部位尺寸伸长。
3) 减少变形的措施 设计铸件时,使其截面形状对称;
三. 学习安排 本课程共计40学时。
第1章 铸造工艺 ( 6 学时)
第2章 锻压工艺 ( 6 学时)
第3章 焊接工艺 ( 6 学时) 第4章 材料切削加工基础 ( 4 学时)
第5章 形面加工方法 ( 6 学时) 第6章 材料成形新工艺与特种加工 ( 2 学时)
第7章 机械加工工艺规程 ( 6 学时) 实验 4 学时
(1)形成原因 (2)缩孔和缩松对铸件 质量的影响
(3)防止措施 选用收缩性小的合金铸造; 设计铸件时,应尽量地使其壁厚均匀;
采用顺序凝固的原则制定铸造工艺。
顺序凝固
例一
铸造内应力、变形和裂纹 (1)内应力的形成
原因:固受阻。 结果:导致铸件变形、开裂。 1) 热应力 铸件各部分冷却速度不同,以致在同一 时间内,各部分收缩不一致、相互约束而引起。