中频电炉冶炼过程中脱磷、脱硫操作要点
脱硫岗位操作规程
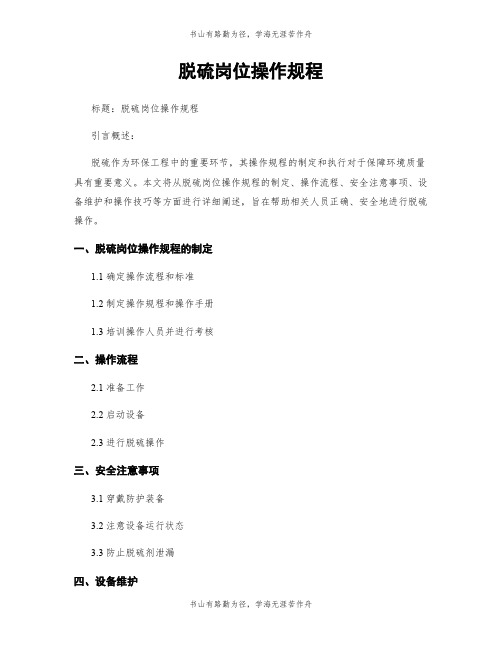
脱硫岗位操作规程
标题:脱硫岗位操作规程
引言概述:
脱硫作为环保工程中的重要环节,其操作规程的制定和执行对于保障环境质量具有重要意义。
本文将从脱硫岗位操作规程的制定、操作流程、安全注意事项、设备维护和操作技巧等方面进行详细阐述,旨在帮助相关人员正确、安全地进行脱硫操作。
一、脱硫岗位操作规程的制定
1.1 确定操作流程和标准
1.2 制定操作规程和操作手册
1.3 培训操作人员并进行考核
二、操作流程
2.1 准备工作
2.2 启动设备
2.3 进行脱硫操作
三、安全注意事项
3.1 穿戴防护装备
3.2 注意设备运行状态
3.3 防止脱硫剂泄漏
四、设备维护
4.1 定期检查设备
4.2 清洁设备表面
4.3 及时更换耗材
五、操作技巧
5.1 控制脱硫剂用量
5.2 调节操作参数
5.3 注意操作细节
结语:
脱硫岗位操作规程的制定和执行是确保脱硫工作顺利进行、环境质量得到有效保障的关键。
只有严格按照规程操作,做好安全防护和设备维护工作,才能有效地完成脱硫任务,为环境保护事业做出贡献。
希望本文所述内容能对相关人员在脱硫岗位操作中起到一定的指导作用。
钢液脱磷、脱硫 炼钢过程

钢液脱磷、脱硫
《转炉炼钢生产》
一、钢液的脱磷
脱磷反应是炼钢过程的基本反应之一,也是一个必要的冶金反应。 磷是一个有害元素,其含量越低越好。在脱氧合金化和炉外精炼过 程中,会发生一定量的回磷现象。而减少其含量是降低危害的唯一 措施。
[S]+(O2-)=(S2-)+[O]
在酸性渣中几乎没有自由的O2-,因此酸性渣脱硫作用很小,
而碱性渣则不同,具有较强的脱硫能力。上式反应的平衡常数可写为:KSa (S2
)
.a[O
]
a[
S
]
.a (O
2
)
(%S) [%S ]
f(S 2 ) a[O] f[S ] a(O2 )
二、钢液的脱硫
影响钢渣间脱硫反应的因素 •炼钢温度的影响。钢渣间的脱硫反应属于吸热反应,吸热在 108.2-128kJ/mol之间,因此,高温有利于脱硫反应进行。 温度的重要影响主要体现在高温能促进石灰溶解和提高炉渣 流动性,改善脱硫反应的动力学条件(如扩散、活化能等) 。 •炉渣碱度的影响。炉渣碱度高,游离CaO多,或(O2-)增大, 有利于脱硫。但过高的碱度,常出现炉渣粘度增加,反而降 低脱硫效果。
一炉钢 冶炼过 程金属 成分和 炉渣成 分的变 化规律
二、钢液的脱硫
脱硫反应动力学 •在炼钢过程中,脱硫反应和脱磷反应相同,都是渣、钢界面 反应,脱硫反应的速率方程可表示为:
d[%S] A Ls[%S] (%S)
电弧炉冶炼脱硫工艺操作讲解

电弧炉冶炼脱硫工艺操作讲解首先,脱硫工艺设计。
根据原料的硫含量和冶炼工艺要求,确定脱硫工艺方案。
一般有湿法脱硫和干法脱硫两种方法可供选择。
在湿法脱硫中,常用的脱硫剂有氧化钙,氧化钠,氢氧化钙等。
在冶炼过程中,将脱硫剂直接投放到电弧炉中,通过化学反应去除炉内金属中的硫。
这种方法操作简单,但会增加脱硫剂的使用费用以及产生大量含水脱硫渣。
在干法脱硫中,常用的脱硫剂是含氧化剂的矿石粉末或其他氧化剂。
在冶炼过程中,将脱硫剂与金属一同投放到电弧炉中,通过高温氧化反应去除炉内的硫。
这种方法所产生的脱硫渣含硫量较低,但会增加金属的氧化量和能耗。
其次,脱硫工艺操作。
在电弧炉冶炼过程中,将脱硫剂按一定比例加入到电弧炉中。
脱硫剂的加入可以分为一次加入和多次加入两种方式。
一次加入是将所有脱硫剂一次性加入到电弧炉中,适用于脱硫剂含量较低、脱硫时间较长的情况。
在一次加入过程中,需要将脱硫剂均匀铺散在炉底,避免出现脱硫剂堆积,影响脱硫效果。
多次加入是将脱硫剂分多次投放到电弧炉中,适用于脱硫剂含量较高、脱硫时间较短的情况。
多次加入的好处是可以使脱硫剂更好地与金属接触,提高脱硫效果。
在多次加入过程中,需要根据脱硫时间和脱硫剂的加入量确定每次加入的脱硫剂量,保证脱硫效果的稳定性。
最后,脱硫工艺的检验和调整。
在冶炼过程中,应及时对脱硫效果进行检验。
可以通过取样分析的方式,对炉前和炉后的金属样品进行硫含量检测,以评估脱硫效果。
如果脱硫效果不理想,可以适时对脱硫工艺进行调整。
比如增加脱硫剂的加入量、调整脱硫剂的投放方式等。
总之,电弧炉冶炼脱硫工艺操作主要包括脱硫工艺设计、脱硫剂的加入和脱硫效果的检验和调整。
根据具体情况选择合适的脱硫方法和脱硫剂,并注意控制脱硫剂的加入量,以提高脱硫效果。
金属冶炼中的脱硫与脱磷技术
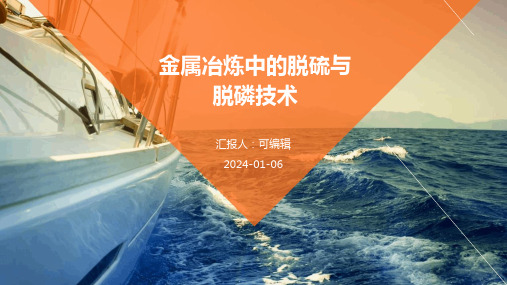
常用方法
生物浸出法和生物吸附法。
优点
环保友好,操作简便,成本低廉。
02
01
缺点
微生物培养条件较为苛刻,且对某些金属冶 炼过程的应用尚在研究阶段。
04
03
04 脱硫与脱磷技术的比较与选择
技术比较
脱硫技术
主要采用物理或化学方法,将金 属矿石中的硫化物去除,常用的
技术包括浮选法、焙烧法等。
脱磷技术
通常采用化学方法,通过添加适 当的还原剂或酸,将矿石中的磷 氧化物还原或溶解,再将其去除 ,常用的技术包括还原焙烧法、
重力脱硫
利用矿物密度不同,通过重选将 硫化物与其它矿物分离,如摇床 、溜槽等。
化学脱硫技术
焙烧脱硫
通过高温氧化作用将硫化物转化为硫 酸盐或硫氧化物,再用水或酸进行浸 出,从而达到脱硫的目的。
化学沉淀法
向含硫溶液中加入适当的沉淀剂,使 硫化物沉淀下来,从而实现脱硫。
生物脱硫技术
生物浸出法
利用微生物的氧化作用将硫化物转化为可溶性的硫酸盐,再通过洗涤、过滤等 手段去除。
生物堆浸法
将矿石堆积在特定的场地,通过自然界的微生物氧化作用将硫化物转化为硫酸 盐,再用水冲洗去除。
03 金属冶炼中的脱磷技术
氧化脱磷技术
原理
通过向熔融金属中加入 氧化剂,将磷氧化成磷 氧化物,从而降低金属 中的磷含量。
常用方法
熔融氧化法和炉渣处理 法。
优点
操作简单,适用于大多 数金属冶炼过程。
02
对金属材料性能的影响
硫和磷的存在会影响金属材料的机械性能,如硬度、韧 性和耐腐蚀性等。的存在会导致金属表面出现斑点、锈蚀等现象, 影响金属制品的外观质量。
硫与磷的来源
中频感应电炉熔炼操作规程
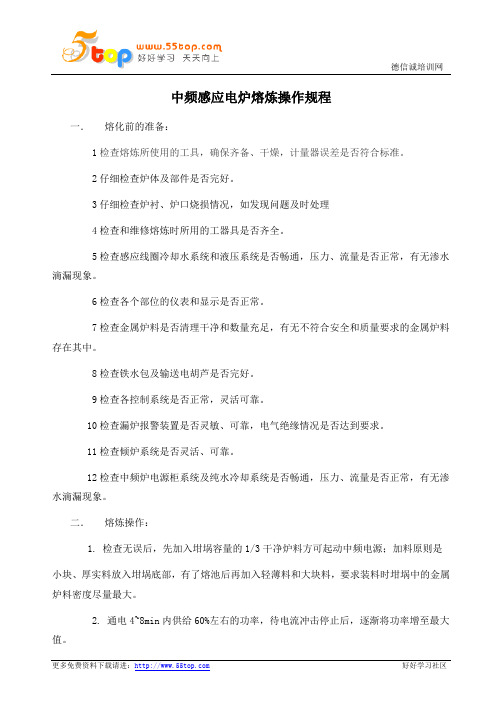
中频感应电炉熔炼操作规程一.熔化前的准备:1检查熔炼所使用的工具,确保齐备、干燥,计量器误差是否符合标准。
2仔细检查炉体及部件是否完好。
3仔细检查炉衬、炉口烧损情况,如发现问题及时处理4检查和维修熔炼时所用的工器具是否齐全。
5检查感应线圈冷却水系统和液压系统是否畅通,压力、流量是否正常,有无渗水滴漏现象。
6检查各个部位的仪表和显示是否正常。
7检查金属炉料是否清理干净和数量充足,有无不符合安全和质量要求的金属炉料存在其中。
8检查铁水包及输送电胡芦是否完好。
9检查各控制系统是否正常,灵活可靠。
10检查漏炉报警装置是否灵敏、可靠,电气绝缘情况是否达到要求。
11检查倾炉系统是否灵活、可靠。
12检查中频炉电源柜系统及纯水冷却系统是否畅通,压力、流量是否正常,有无渗水滴漏现象。
二.熔炼操作:1.检查无误后,先加入坩埚容量的1/3干净炉料方可起动中频电源;加料原则是小块、厚实料放入坩埚底部,有了熔池后再加入轻薄料和大块料,要求装料时坩埚中的金属炉料密度尽量最大。
2. 通电4~8min内供给60%左右的功率,待电流冲击停止后,逐渐将功率增至最大值。
3. 熔炼过程中要经常检查炉衬的烧损情况、中频电源柜上各种仪表、冷却水循环状况;炉膛里不准有炉料架空棚料现象,如有此现象,随时注意捣料,防止“搭桥”。
4. 95%的炉料熔毕时,取钢样进行成分分析,并将其余5%的炉料加入炉内继续熔化。
5.全部炉料溶毕后,降低功率至40%~60%,倾炉扒渣;为防止铁水溢出,铁水液面与炉沿保持50mm的距离。
6. 往铁水液面上加脱氧剂(质量比为:石灰粉:铝粉=2:1)进行扩散脱氧;脱氧过程中可用石灰粉和氟石粉调整炉渣的粘度,使炉渣具有良好的流动性。
7.根据化学分析结果,调整钢液化学成分,其中含硅量应在出钢前10min以内进行调整。
8. 测温,做圆杯试样:测量钢液温度,并作圆杯试样,检查钢液脱氧情况。
9. 钢液温度达到1630~1650°C(高锰钢1520~1560℃),圆杯试样收缩良好时,扒除一半炉渣后,加硅锰各0.15%,镇静一分钟,每吨钢液插铝0.15-0.25%终脱氧,插铝后2~3min以内停电倾炉出钢。
2024年中频感应电炉岗位操作规程
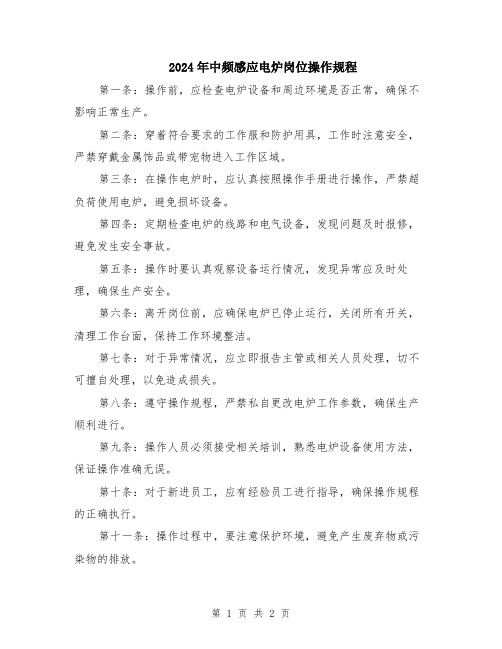
2024年中频感应电炉岗位操作规程
第一条:操作前,应检查电炉设备和周边环境是否正常,确保不影响正常生产。
第二条:穿着符合要求的工作服和防护用具,工作时注意安全,严禁穿戴金属饰品或带宠物进入工作区域。
第三条:在操作电炉时,应认真按照操作手册进行操作,严禁超负荷使用电炉,避免损坏设备。
第四条:定期检查电炉的线路和电气设备,发现问题及时报修,避免发生安全事故。
第五条:操作时要认真观察设备运行情况,发现异常应及时处理,确保生产安全。
第六条:离开岗位前,应确保电炉已停止运行,关闭所有开关,清理工作台面,保持工作环境整洁。
第七条:对于异常情况,应立即报告主管或相关人员处理,切不可擅自处理,以免造成损失。
第八条:遵守操作规程,严禁私自更改电炉工作参数,确保生产顺利进行。
第九条:操作人员必须接受相关培训,熟悉电炉设备使用方法,保证操作准确无误。
第十条:对于新进员工,应有经验员工进行指导,确保操作规程的正确执行。
第十一条:操作过程中,要注意保护环境,避免产生废弃物或污染物的排放。
第十二条:对于电炉设备的日常保养,应按照操作手册要求,做好维护工作,延长设备的使用寿命。
脱硫岗位工艺技术操作规程
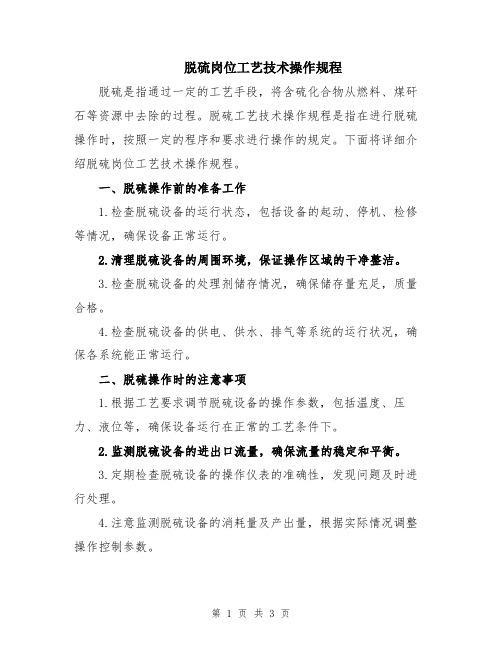
脱硫岗位工艺技术操作规程脱硫是指通过一定的工艺手段,将含硫化合物从燃料、煤矸石等资源中去除的过程。
脱硫工艺技术操作规程是指在进行脱硫操作时,按照一定的程序和要求进行操作的规定。
下面将详细介绍脱硫岗位工艺技术操作规程。
一、脱硫操作前的准备工作1.检查脱硫设备的运行状态,包括设备的起动、停机、检修等情况,确保设备正常运行。
2.清理脱硫设备的周围环境,保证操作区域的干净整洁。
3.检查脱硫设备的处理剂储存情况,确保储存量充足,质量合格。
4.检查脱硫设备的供电、供水、排气等系统的运行状况,确保各系统能正常运行。
二、脱硫操作时的注意事项1.根据工艺要求调节脱硫设备的操作参数,包括温度、压力、液位等,确保设备运行在正常的工艺条件下。
2.监测脱硫设备的进出口流量,确保流量的稳定和平衡。
3.定期检查脱硫设备的操作仪表的准确性,发现问题及时进行处理。
4.注意监测脱硫设备的消耗量及产出量,根据实际情况调整操作控制参数。
门报告,并采取相应的处理措施。
三、脱硫操作后的处理工作1.关闭脱硫设备,包括关闭进出口阀门,断开电源等。
2.对脱硫设备进行清洁、检修和维护,确保设备的正常运行。
3.记录脱硫设备的操作过程和参数,包括设备运行时间、消耗量、产出量等,并进行整理和归档。
4.对脱硫设备进行日常保养工作,包括设备的润滑、加油、清洗等,延长设备使用寿命。
5.做好脱硫设备的安全防护工作,包括设备周围的围栏、警示标志等,确保人员和设备的安全。
四、脱硫操作的安全注意事项1.在脱硫操作过程中,必须穿戴符合规定的劳动保护用品,如防护眼镜、手套、防护服等。
2.不得私自操作脱硫设备,必须经过专业培训并持有相应的操作证书方可操作。
3.严禁在脱硫设备周围吸烟和使用明火,以防发生火灾事故。
4.操作过程中要注意设备的停运和停机要求,不得随意操作。
部门报告,并采取相应的措施。
综上所述,脱硫岗位工艺技术操作规程是保证脱硫工艺正常运行的重要文件。
操作人员在进行脱硫操作时,必须严格按照规程进行操作,做到安全可靠,确保脱硫过程的高效性和环保性。
吹炼过程中的脱磷和脱硫
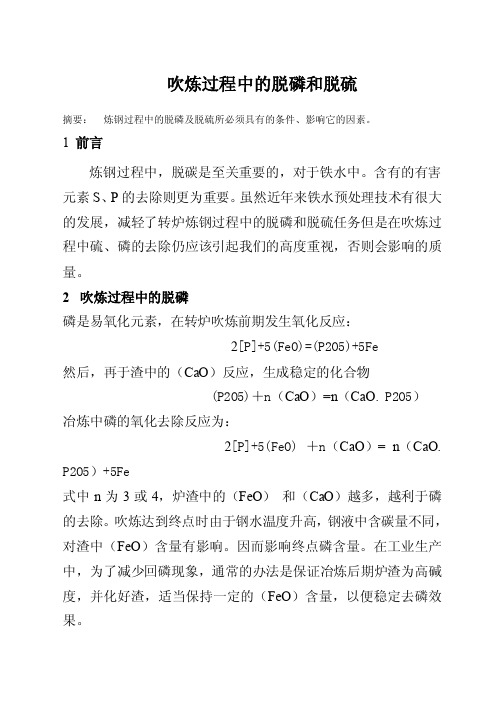
吹炼过程中的脱磷和脱硫摘要:炼钢过程中的脱磷及脱硫所必须具有的条件、影响它的因素。
1前言炼钢过程中,脱碳是至关重要的,对于铁水中。
含有的有害元素S、P的去除则更为重要。
虽然近年来铁水预处理技术有很大的发展,减轻了转炉炼钢过程中的脱磷和脱硫任务但是在吹炼过程中硫、磷的去除仍应该引起我们的高度重视,否则会影响的质量。
2吹炼过程中的脱磷磷是易氧化元素,在转炉吹炼前期发生氧化反应:2[P]+5(FeO)=(P2O5)+5Fe然后,再于渣中的(CaO)反应,生成稳定的化合物(P2O5)+n(CaO)=n(CaO. P2O5)冶炼中磷的氧化去除反应为:2[P]+5(FeO) +n(CaO)= n(CaO. P2O5)+5Fe式中n为3或4,炉渣中的(FeO)和(CaO)越多,越利于磷的去除。
吹炼达到终点时由于钢水温度升高,钢液中含碳量不同,对渣中(FeO)含量有影响。
因而影响终点磷含量。
在工业生产中,为了减少回磷现象,通常的办法是保证冶炼后期炉渣为高碱度,并化好渣,适当保持一定的(FeO)含量,以便稳定去磷效果。
为了去磷,吹炼过程中,应根据去磷的热力学条件,首先要搞好前期渣,尽快形成高氧化性的炉渣,以利于前期低温去磷。
而在吹炼后期要控制好炉渣碱度和渣中的(FeO),以利于后期高温、高碱度、高(FeO)脱磷。
当脱磷反应达到平衡时,用浓度来表示的平衡常数为:Kp= (P2O5)/[p]2(FeO)5(CaO)4常用磷在炉渣和金属中的分配比来表示脱磷能力,其表示方法很多。
常用L p=(P2O5)或Lp= (P2O5)/ [p].Lp越大,炼钢过程中脱磷能力也越大。
平衡常数和温度的关系:Lg=51875/T-33.16从脱磷反应的反应式、平衡常数及温度关系,可知影响脱磷的因素有:2.1炉渣碱度的影响。
由分配比公式可知:渣中的CaO越高,分配比越高,脱磷能力就越强。
CaO的脱磷作用在于:它能使P2O5生成稳定的磷酸钙。
脱硫操作规程

脱硫操作规程脱硫是工业生产过程中常见的一项重要操作,其目的是降低燃烧产生的二氧化硫排放量,减少对环境的污染。
下面是一份脱硫操作规程,以确保操作安全和有效性。
一、操作目的脱硫操作的目的是降低燃烧排放的二氧化硫含量,达到环保要求。
二、操作对象脱硫操作的对象为含有二氧化硫的废气或烟气。
三、操作流程1. 检查设备:在操作开始前,检查脱硫设备及相关附件是否完好,有无漏水、渗漏等情况。
2. 准备脱硫剂:根据工艺要求准备适量的脱硫剂,并确保其质量符合要求。
3. 调节设备参数:根据工艺要求,调节脱硫设备的操作参数,包括温度、压力、流量等。
4. 启动设备:按照操作流程启动脱硫设备,确保设备运行正常。
5. 进料操作:将含有二氧化硫的废气或烟气输入脱硫设备,精确控制进气量和压力。
6. 加入脱硫剂:根据工艺要求,逐步加入预先准备好的脱硫剂,确保脱硫剂的加入均匀。
7. 混合搅拌:通过搅拌设备对废气和脱硫剂进行充分混合搅拌,以增加反应效果。
8. 反应时间控制:根据工艺要求,控制脱硫反应的时间,确保二氧化硫能够被有效吸收。
9. 过滤操作:将反应后的废气或烟气进行过滤,除去反应产物和杂质。
10. 排放处理:对脱硫后的废气或烟气进行处理,以确保排放符合环保要求。
11. 清洗设备:在脱硫操作结束后,对设备进行彻底清洗,清除残留物和污染物。
四、安全注意事项1. 操作人员必须经过相关培训,具备操作脱硫设备的资格和技能。
2. 在操作过程中,严禁吸烟、明火等明显源火操作。
3. 注意脱硫剂的搬运和储存,保持良好的通风条件,避免脱硫剂中毒。
4. 在加入脱硫剂时,应根据工艺要求逐步加入,避免因一次加量过多导致设备堵塞。
5. 定期检查设备和管道的密封性,发现问题及时排查和处理,以确保操作的安全性。
6. 操作结束后,及时清洗设备,确保设备的长期使用效果和减少对环境的污染。
以上是一份脱硫操作规程,根据实际情况和工艺要求可进行相应的调整和完善。
在操作中,一定要严格遵守安全规定,确保操作的安全性和操作效果的有效性。
中频电炉冶炼过程中脱磷、脱硫操作要点

中频电炉冶炼过程中脱磷、脱硫操作要点(总4页)本页仅作为文档封面,使用时可以删除This document is for reference only-rar21year.March一.前言内容导读:中频电炉在铸钢行业中的应用已经极为普遍,特别是在小型砂型铸钢和失蜡熔模精密铸钢中几乎都是采用中频电炉炼钢,由于技术力量的不足,绝大多数企业对中频电炉在熔炼过程中的冶金反应研究较少,以至于形成了一种较为普遍的观点,即中频电炉在钢熔炼过程中只有较弱的冶金反应,难以进行脱磷、脱硫操作,基本上是一种废钢和铁合金的重熔过程。
现实生产当中,很多使用中频电炉冶炼铸钢材质的企业,在遇到原材料出现波动时,造成钢液成份中磷或硫超标,解决问题的方法基本上是倾倒出部分钢液,再加低磷硫的废钢重新配料熔化,常常造成较大的损失,因此,强化中频电炉熔炼过程中的冶金反应,掌握脱磷、脱硫的方法,是一项很有价值的工作。
二.钢水熔炼过程中脱P、脱S的冶金原理(一)脱P的冶金反应原理磷在钢液中以Fe2P的形式存在,在钢液中溶解度很高,容易与自炉渣扩散到钢液中的(FeO)作用并释放热量,反应式:2[P]+5(FeO)→(P2O5)+5[Fe];△H=-260000J磷的氧化物在钢液中溶解度很低,但易溶于炉渣,并与炉渣中的(FeO)反应生成(3FeOP2O5),反应式如下:(P2O5)+3(FeO)→(3FeOP2O5);△H=-127900J(P2O5)和(3FeOP2O5),都是不稳定的氧化物,在冶炼时,温度稍高就会分解,使磷重回钢液,因此,以FeO为主的炉渣脱磷能力很差,为了取得很好的脱P效果,就必须向炉渣中加入强碱性氧化物CaO(石灰),与(P2O5)结合成稳定的磷酸钙,反应式如下:(P2O5)+4(CaO)→[(CaO)4 P2O5];△H=-689700J脱P过程综合反应式如下:2[P]+ 5(FeO)+ 4(CaO)→[(CaO)4 P2O5]+ 5[Fe];△H=-949700J由以上反应式可知,做好脱P工作,注意以下几个方面:(1)钢液氧化性强,炉渣碱度高是脱P的必要条件;(2)控制钢液温度,由于脱磷是放热反应,因此钢液温度低有利于脱P;(3)流动性良好的炉渣能提高渣中的CaO活性,有利于脱P;(4)加强钢液与渣的搅拌,有利于脱P。
金属冶炼中的脱硫与脱磷

产物分离
将脱硫产物与金属分离 ,得到纯净的金属。
金属熔炼
将纯净的金属进行熔炼 ,得到最终产品。
脱硫的实践与案例
钢铁脱硫
钢铁工业中常用的脱硫方法有喷粉法 、夹套式反应罐法和悬浮法等。其中 ,喷粉法是最常用的方法之一,可以 有效降低钢铁中的硫含量。
有色金属脱硫
对于铜、铝等有色金属,常用的脱硫 方法有酸洗、氧化等。这些方法可以 有效去除有色金属中的硫化物杂质, 提高金属的品质和加工性能。
化学法
通过化学反应将硫化物转化为其他形态或将其从 金属中分离出来的方法,如酸洗、氧化等。
生物法
利用微生物的代谢作用将硫化物转化为可溶性物 质或将其从金属中分离出来的方法。
脱硫的工艺流程
原料准备
对原料进行破碎、筛分 、混合等预处理,以便
后续处理。
脱硫处理
根据所选择的脱硫方法 和技术,对原料进行脱
硫处理。
脱磷的工艺流程
熔融金属的制备
将原料加入高温熔炉 中熔化,形成熔融金 属。
脱磷剂的添加
根据需要加入适量的 脱磷剂。
脱磷反应
在一定的温度和压力 下进行脱磷反应,使 磷元素与脱磷剂反应 生成不溶于金属的化 合物。
过滤与分离
将生成的化合物通过 过滤等方法从熔融金 属中分离出来。
金属的浇注
将脱磷处理后的熔融 金属浇注入铸模中, 冷却凝固后得到所需 的金属材料。
03
脱硫与脱磷在金属冶炼中的关系
脱硫与脱磷的相互影响
脱硫和脱磷在金属冶炼过程中 是相互关联的,因为它们都涉 及到去除杂质和有害元素。
脱硫和脱磷的相互影响主要体 现在它们对金属冶炼过程的影 响上。
脱硫和脱磷的相互影响还表现 在它们对金属产品质量的影响 上。
脱硫安全操作规程

脱硫安全操作规程脱硫是炼油厂和化工厂等许多工厂的常见生产过程,它可以使燃料、燃气和其他化学物质中的硫化物化合物被去除。
然而,这个过程也带来了一些有害的风险,包括可能引起爆炸、易燃、毒气和化学反应等。
因此,制定一份脱硫安全操作规程对于维护工作场所的安全至关重要。
1. 安全设备和工具对于脱硫工作,必须配备必要的安全设备和工具。
例如,化学处理过程中使用的面罩、手套和防护服等。
同时,也要准备必要的灭火器材、急救箱、安全带以及通风密闭设备等。
这些都是保护工作人员安全的重要物品。
2. 工作区域和工作指导所有的脱硫操作都必须在经过充分检查和批准的工作区域进行,这个区域必须满足运行环境和作业安全的标准。
所有工作人员必须在脱硫操作的安全规程方面得到充分的指导和培训,以确保他们可以安全完成工作。
如果有任何疑问,都必须接受现场管理者的指导。
3. 确认所有的疑问在脱硫操作之前,必须认真检查设备和材料,以排除任何风险。
如果不存在任何问题,就可以开始操作。
但如果存在任何疑问或不清楚的地方,必须马上暂停工作,等待确认后再继续工作。
4. 注意工作环境在脱硫过程中,必须注意工作环境的状态。
任何环境的异常变化都可能对工作产生影响,例如温度、湿度、气压、风速等。
如果出现异常,必须暂停工作,重新确认环境是否符合操作标准,并采取必要的行动以消除风险和危险。
5. 清理现场在完成脱硫工作之后,必须彻底清理现场,包括清除所有废弃物和材料、打扫工作区域和设备、关闭所有排放设备等。
这可以帮助防止任何压力和返工,确保操作的顺利和安全。
总之,脱硫作业是重要的工艺操作,仅仅满足操作标准还不够,必须考虑安全和环保方面的考虑,制定好并执行规范的脱硫安全操作规程,确保工作人员的安全和减少风险。
中频炉-LF-VD炉工艺
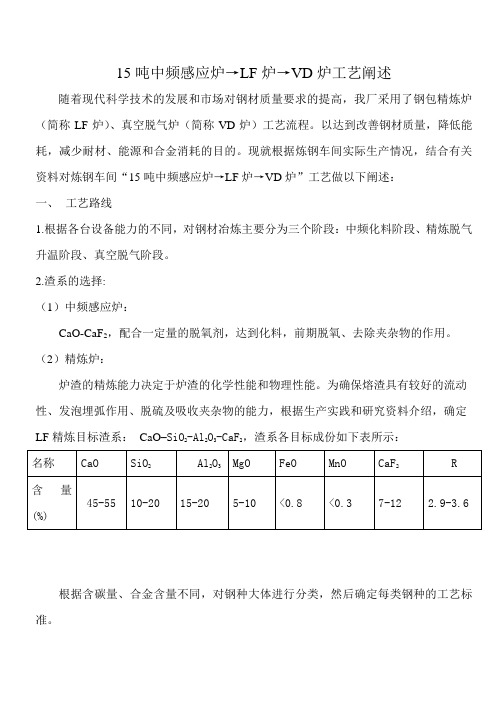
15吨中频感应炉→LF炉→VD炉工艺阐述随着现代科学技术的发展和市场对钢材质量要求的提高,我厂采用了钢包精炼炉(简称LF炉)、真空脱气炉(简称VD炉)工艺流程。
以达到改善钢材质量,降低能耗,减少耐材、能源和合金消耗的目的。
现就根据炼钢车间实际生产情况,结合有关资料对炼钢车间“15吨中频感应炉→LF炉→VD炉”工艺做以下阐述:一、工艺路线1.根据各台设备能力的不同,对钢材冶炼主要分为三个阶段:中频化料阶段、精炼脱气升温阶段、真空脱气阶段。
2.渣系的选择:(1)中频感应炉:CaO-CaF2,配合一定量的脱氧剂,达到化料,前期脱氧、去除夹杂物的作用。
(2)精炼炉:炉渣的精炼能力决定于炉渣的化学性能和物理性能。
为确保熔渣具有较好的流动性、发泡埋弧作用、脱硫及吸收夹杂物的能力,根据生产实践和研究资料介绍,确定LF精炼目标渣系:CaO–SiO2-Al2O3-CaF2,渣系各目标成份如下表所示:根据含碳量、合金含量不同,对钢种大体进行分类,然后确定每类钢种的工艺标准。
1.碳素钢:按其含碳量不同分为低碳钢(钢中碳质量分数0.08%-0.25%)、中碳钢(钢中碳质量分数0.25%-0.55%)、高碳钢(钢中碳质量分数0.60%-2.20%)2.低合金钢:其钢种合金元素(C、Si、Mn、P、S除外)总质量分数小于5%。
同时考虑到含碳量的不同,又在其基础上分为低碳低合金钢、中碳低合金钢、高碳低合金钢(中合金钢、高合金钢也按此进行分类)。
3.中合金钢:其钢种合金元素(C、Si、Mn、P、S除外)总质量分数5%-10%。
其包括低碳中合金钢、中碳中合金钢、高碳高合金钢。
4.高合金钢:其钢种合金元素(C、Si、Mn、P、S除外)总质量分数10%以上。
其包括低碳高合金钢、中碳高合金钢、高碳高合金钢。
根据上述分类,将钢种大体上分为4大类、12小类,制订冶炼工艺,为生产提供参考。
二、脱氧及造渣材料脱氧及造渣材料根据生产使用情况,冶炼时造高碱度还原渣,有利于脱气、除杂、提高合金回收率等。
冶炼厂脱硫工艺流程

冶炼厂脱硫工艺流程英文回答:The desulfurization process in a smelting plant is crucial for reducing the emission of sulfur dioxide (SO2) into the atmosphere. There are several methods used in the industry to remove sulfur from the flue gas, including wet scrubbing, dry scrubbing, and regenerative processes.Wet scrubbing is a commonly used method, which involves the use of a liquid absorbent to capture the sulfur dioxide. The flue gas is passed through a scrubber, where it comes into contact with the absorbent, usually a solution of limestone or lime. The sulfur dioxide reacts with the absorbent to form calcium sulfite or calcium sulfate, which can be further processed into gypsum.Dry scrubbing, on the other hand, involves theinjection of a dry sorbent into the flue gas stream. The sorbent, such as activated carbon or sodium bicarbonate,reacts with the sulfur dioxide to form solid byproducts that can be collected and disposed of. Dry scrubbing is often used in smaller smelting plants or in situations where water availability is limited.Another method is the regenerative process, which utilizes a sorbent material that can be regenerated and reused. This process involves the use of a solid sorbent, such as calcium oxide or activated alumina, which reacts with the sulfur dioxide to form a solid compound. The sorbent is then regenerated by heating it to release the sulfur dioxide, which can be collected and converted into sulfuric acid or other useful products.In addition to these primary methods, there are also secondary methods used to further reduce sulfur emissions. These include catalytic oxidation, which converts sulfur dioxide into sulfur trioxide, and absorption using amine solutions, which can remove additional sulfur compounds from the flue gas.Overall, the desulfurization process in a smeltingplant is a complex and essential part of reducing sulfur emissions and minimizing the environmental impact of the operation.中文回答:冶炼厂的脱硫工艺流程对于减少二氧化硫(SO2)排放至关重要。
炉外脱硫脱硅脱磷技术要求
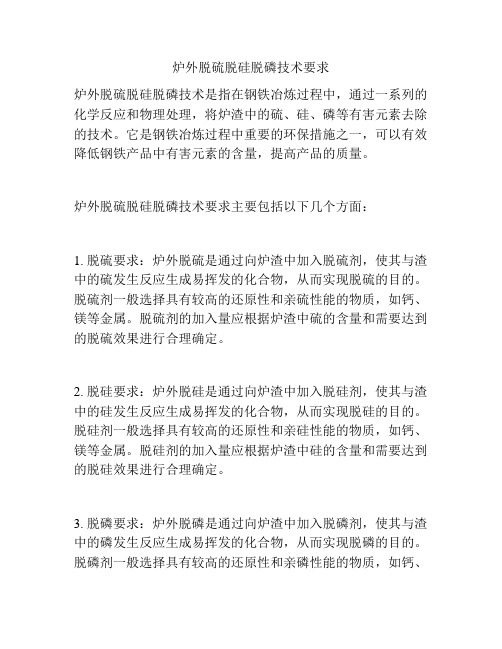
炉外脱硫脱硅脱磷技术要求炉外脱硫脱硅脱磷技术是指在钢铁冶炼过程中,通过一系列的化学反应和物理处理,将炉渣中的硫、硅、磷等有害元素去除的技术。
它是钢铁冶炼过程中重要的环保措施之一,可以有效降低钢铁产品中有害元素的含量,提高产品的质量。
炉外脱硫脱硅脱磷技术要求主要包括以下几个方面:1. 脱硫要求:炉外脱硫是通过向炉渣中加入脱硫剂,使其与渣中的硫发生反应生成易挥发的化合物,从而实现脱硫的目的。
脱硫剂一般选择具有较高的还原性和亲硫性能的物质,如钙、镁等金属。
脱硫剂的加入量应根据炉渣中硫的含量和需要达到的脱硫效果进行合理确定。
2. 脱硅要求:炉外脱硅是通过向炉渣中加入脱硅剂,使其与渣中的硅发生反应生成易挥发的化合物,从而实现脱硅的目的。
脱硅剂一般选择具有较高的还原性和亲硅性能的物质,如钙、镁等金属。
脱硅剂的加入量应根据炉渣中硅的含量和需要达到的脱硅效果进行合理确定。
3. 脱磷要求:炉外脱磷是通过向炉渣中加入脱磷剂,使其与渣中的磷发生反应生成易挥发的化合物,从而实现脱磷的目的。
脱磷剂一般选择具有较高的还原性和亲磷性能的物质,如钙、镁等金属。
脱磷剂的加入量应根据炉渣中磷的含量和需要达到的脱磷效果进行合理确定。
4. 温度要求:炉外脱硫脱硅脱磷技术需要在一定的温度范围内进行。
温度过低会影响反应速率和反应效果,温度过高则会导致能源浪费和设备损耗。
因此,在进行炉外脱硫脱硅脱磷时,需要控制好反应系统的温度,保持在适宜的范围内。
5. 氧气要求:在炉外脱硫脱硅脱磷过程中,氧气起到了重要的作用。
氧气可以提供氧化剂,促进反应物与有害元素之间的氧化反应。
因此,在进行炉外脱硫脱硅脱磷时,需要控制好氧气供给量,保证反应系统中氧气的充足。
6. 反应时间要求:炉外脱硫脱硅脱磷技术需要一定的反应时间才能达到理想的效果。
反应时间过长会导致能源浪费和设备损耗,反应时间过短则可能无法完全去除有害元素。
因此,在进行炉外脱硫脱硅脱磷时,需要根据具体情况确定合理的反应时间。
中科院科技成果——中频炉深脱磷技术

中科院科技成果——中频炉深脱磷技术项目简介
在特殊钢行业,我国半数以上企业均采用电弧炉粗炼钢水加炉外精炼的传统方法生产合金钢和优质碳素钢;在重机行业,几乎所有企业均采用此方法生产大型铸锻件;在普通铸锻行业,全国采用电弧炉炼钢的企业也有数百家,而采用中频炉生产铸钢件的规模企业达数千家。
中频炉采用感应方法加热,可以达到清洁熔炼的效果,有害气体、固废和颗粒物排放量少。
但是,中频炉替代电弧炉存在难以逾越的技术瓶颈,业内人士普遍认为,中频炉不能去除有害元素磷。
研究团队经过中试和生产现场5t、20t中频炉验证及小批量生产,成功开发了中频炉深脱磷技术,金属原材料收率达90%以上,超过电弧炉5%以上。
在熔炼过程中根据碳、硅等元素的变化,进行渣系调控,将磷含量由通常的0.025%降低到0.005%,脱磷率达到了80%。
生产实践表明,中频炉替代电弧炉的优点在于:
(1)排放方面,有害气体排放量降低50%以上,固废排放量降低60%以上,颗粒物产生量降低50%以上;
(2)成本方面,吨钢成本降低200元以上。
因此中频炉冶炼加炉外精炼具有不可比拟的优势,我们认为可以替代电弧炉。
中频炉冶炼品质的提升,废弃物排放大量减少,将成为科技创新驱动和引领经济发展目标的具体实施。
- 1、下载文档前请自行甄别文档内容的完整性,平台不提供额外的编辑、内容补充、找答案等附加服务。
- 2、"仅部分预览"的文档,不可在线预览部分如存在完整性等问题,可反馈申请退款(可完整预览的文档不适用该条件!)。
- 3、如文档侵犯您的权益,请联系客服反馈,我们会尽快为您处理(人工客服工作时间:9:00-18:30)。
一.前言
内容导读:中频电炉在铸钢行业中的应用已经极为普遍,特别是在小型砂型铸钢和
在钢熔炼过程中只有较弱的冶金反应,难以进行脱磷、脱硫操作,基本上是一种废钢和铁合金的重熔过程。
现实生产当中,很多使用中频电炉冶炼铸钢材质的企业,在遇到原材料出现波动时,造成钢液成份中磷或硫超标,解决问题的方法基本上是倾倒出部分钢液,再加低磷硫的废钢重新配料熔化,常常造成较大的损失,因此,强化中频电炉熔炼过程中的冶金反应,掌握脱磷、脱硫的方法,是一项很有价值的工作。
二.钢水熔炼过程中脱P、脱S的冶金原理
(一)脱P的冶金反应原理
磷在钢液中以Fe2P的形式存在,在钢液中溶解度很高,容易与自炉渣扩散到钢液中的(FeO)作用并释放热量,反应式:
2[P]+5(FeO)→(P2O5)+5[Fe];△H=-260000J 磷的氧化物在钢液中溶解度很低,但易溶于炉渣,并与炉渣中的(FeO)反应生成
(3FeOP2O5),反应式如下:
(P2O5)+3(FeO)→(3FeOP2O5);△H=-127900J (P2O5)和(3FeOP2O5),都是不稳定的氧化物,在冶炼时,温度稍高就会分解,使磷重回钢液,因此,以FeO为主的炉渣脱磷能力很差,为了取得很好的脱P效果,就必须向炉渣中加入强碱性氧化物CaO(石灰),与(P2O5)结合成稳定的磷酸钙,反应式如下:
(P2O5)+4(CaO)→[(CaO)4P2O5];△H=-689700J 脱P过程综合反应式如下:
2[P]+ 5(FeO)+ 4(CaO)→[(CaO)4P2O5]+ 5[Fe];△H=-949700J 由以上反应式可知,做好脱P工作,注意以下几个方面:
(1)钢液氧化性强,炉渣碱度高是脱P的必要条件;
(2)控制钢液温度,由于脱磷是放热反应,因此钢液温度低有利于脱P;
(3)流动性良好的炉渣能提高渣中的CaO活性,有利于脱P;
(4)加强钢液与渣的搅拌,有利于脱P。
(二)脱S的冶金反应原理
硫在钢液与炉渣中均以FeS形态存在,钢液中的[FeS]与炉渣中的(FeS)可以通过扩散互相转移,在一定温度下,两者质量分数比是一个常数,脱S过程,就是利用这一原理。
在钢液脱氧还原充分的条件下,促使炉渣中的(FeS)与Ca2+作用形成CaS,减少渣中的(FeS),从而导致钢液中的[FeS]往渣中扩散,来达到钢液脱S的目的,反应式如下:
(FeS)+(CaO)=(CaS)+ (FeO)
因此,做好脱硫工作注意以下方面:
(1)钢液脱氧越充分越好,钢液在还原期必须做好脱氧工作,这是脱硫的必要前提条件。
(2)增加渣的碱度,以使渣有足够的(CaO)参与反应。
一般认为炉渣碱度以~最佳。
(3)适当的较高的钢液温度。
提高钢液的温度可以降低炉渣的黏度,利于FeS的扩散,提高脱硫效率。
(4)加强钢液与渣的搅拌作用。
脱硫过程是缓慢的扩散过程,加强搅拌、增强钢液与炉渣的接触面积是提高脱硫效率的最有效的措施。
基于此,出钢时的“钢渣混出”是一种最佳有效的重要操作方法。
(一)熔化期的脱磷
根据脱磷的冶金反应机理,脱磷的操作应安排在熔化期,并注意注重钢液的氧化、初渣的制备、扒渣和二次造渣四个环节。
(1)钢液的氧化
为了尽快达到脱磷的目的,以使钢液在熔化的整个过程中都有效参与脱磷的反应,在熔化前加炉料时可将氧化铁皮或铁矿石与废钢一起放入炉中熔化,每吨钢液准备氧化铁皮或铁矿石8~10kg,先期加入废钢总量所需的氧化铁皮或铁矿石量的一半。
如果没有氧化铁皮或铁矿石,可以在熔化初期吹氧,以使钢液氧化。
(2)初渣的准备
废钢开始熔化后,即可进行造初渣。
秤取总炉料的~%左右的石灰与萤石(石灰与萤石的比例为10:1),边熔化边随废钢一起加入,至废钢化至要求总量的70%时,准备扒渣,以便造二次渣更好地脱磷。
注意造渣用的石灰必须是干燥的有粒度的。
粉状的石灰由于吸潮,严禁使用,因此石灰必须随烘随用。
氧化铁皮和萤石必须经烘干使用。
(3)扒渣
钢液化至要求的60~70%时停止加料并降低功率,维持熔化状态,搅拌渣液,倾炉出渣。
(4)二次造渣
待渣基本出净后,重新加入废钢,加大功率熔化,并秤取总炉料%的渣料与剩余的氧化铁皮或铁矿石加入炉内。
使废钢全部熔清后,倾炉扒渣,取样化验P是否在允许的范围内。
一般来说,碳素废钢经以上操作,脱磷效果可以达50%。
(二)还原期的脱硫
炉渣直接曝露在空气中,相对于电弧炉在造还原渣时可关闭炉门减少炉内气氛与外界交换的
以下操作:
(1)熔化后期出尽氧化渣后,加入适量的石灰和萤石,以能覆盖整个液面即可,防止钢液吸气氧化。
待稀薄渣形成后,用硅钙粉预脱氧,然后加入各种合金,调整成份,以使除硫以外的钢液化学成份符合企业内控标准,随后撒Si-Ca粉预脱氧为造还原渣脱硫做好准备。
(2)将准备好的占钢液总量%的还原渣(生石灰:三氧化二铝:碳酸钠:萤石=20:5:2:2)分批加入,提升钢液至相对高温,并不断搅拌渣液,维持20~30分钟的时间。
其间为了渣液的稳定,需间隔5分钟左右往渣面撒入Si-Ca粉。
(3)出钢时,终脱氧在包内进行,一般将铝放入钢包内,按t计算。
坚持钢渣同出,如果需要脱去的硫量较多,可以将包内的渣扒除,钢液重新回炉,重复第二步骤的造渣过程。
1. 脱P实例:
由于脱P扒渣后的钢液氧化严重,为了取样对照,加入了少许碳粉和硅钙粉,导致对比样略微增碳增硅。
2.脱硫实例:
四. 总结
中频感应电炉只要掌握好正确的冶炼操作工艺,是完全可以做好钢液的脱磷脱硫
工作,达到净化钢液降低成本的目的。
1.选购合适的炉衬材料,因为熔炼过程中的脱磷脱硫冶金反应对炉衬侵蚀严重,选择合适的炉衬材料非常重要,建议选用中性耐火材料烧结坩埚,中性料耐急冷急热,不易开裂。
酸性炉衬是无法开展脱磷脱硫操作的。
2.脱磷操作过程中钢水氧化严重,与O结合比Fe亲和力更强的合金元素会大量烧损,在扒除脱磷渣时会去除掉,因此同材质的合金钢浇冒口建议在脱磷工作完成以后加入。
效率的关键所在。