瓦楞纸箱工艺解决方案(纸板印刷问题)
常见纸板问题及解决方案
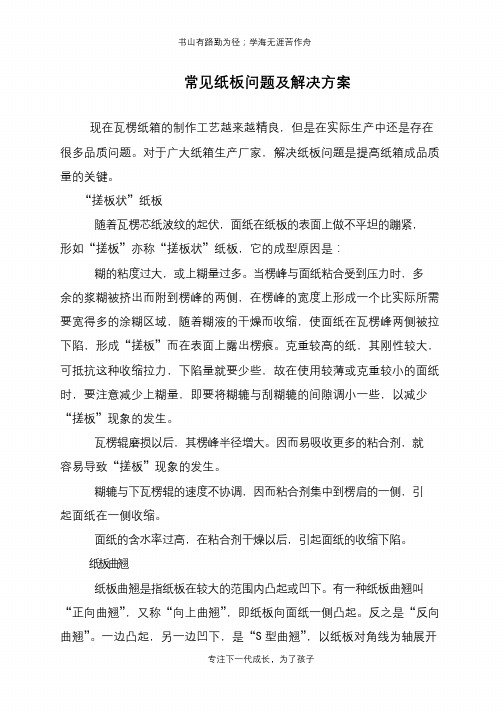
书山有路勤为径;学海无涯苦作舟
常见纸板问题及解决方案
现在瓦楞纸箱的制作工艺越来越精良,但是在实际生产中还是存在很多品质问题。
对于广大纸箱生产厂家,解决纸板问题是提高纸箱成品质量的关键。
“搓板状”纸板
随着瓦楞芯纸波纹的起伏,面纸在纸板的表面上做不平坦的蹦紧,
形如“搓板”亦称“搓板状”纸板,它的成型原因是:
糊的粘度过大,或上糊量过多。
当楞峰与面纸粘合受到压力时,多
余的浆糊被挤出而附到楞峰的两侧,在楞峰的宽度上形成一个比实际所需要宽得多的涂糊区域,随着糊液的干燥而收缩,使面纸在瓦楞峰两侧被拉下陷,形成“搓板”而在表面上露出楞痕。
克重较高的纸,其刚性较大,
可抵抗这种收缩拉力,下陷量就要少些,故在使用较薄或克重较小的面纸时,要注意减少上糊量,即要将糊辘与刮糊辘的间隙调小一些,以减少“搓板”现象的发生。
瓦楞辊磨损以后,其楞峰半径增大。
因而易吸收更多的粘合剂,就
容易导致“搓板”现象的发生。
糊辘与下瓦楞辊的速度不协调,因而粘合剂集中到楞肩的一侧,引
起面纸在一侧收缩。
面纸的含水率过高,在粘合剂干燥以后,引起面纸的收缩下陷。
纸板曲翘
纸板曲翘是指纸板在较大的范围内凸起或凹下。
有一种纸板曲翘叫“正向曲翘”,又称“向上曲翘”,即纸板向面纸一侧凸起。
反之是“反向
曲翘”。
一边凸起,另一边凹下,是“S型曲翘”,以纸板对角线为轴展开
专注下一代成长,为了孩子。
瓦楞纸箱生产中常见问题和解决方法

瓦 纸 发 翘曲 形 解 法 I 送 工 对 箱 量 影 和 决 法 I 瓦 纸 粘 中 现 质 问 和 决 法 楞 板 生 变 和 决方 纸 艺 纸 质 的 响 解 方 楞 箱 合 出 的 量 题 解 方
楞纸箱生产中
见闻题和解决方法
1瓦楞纸板发生翘 曲变形对纸箱的影响 .
瓦楞 纸板发生翘 曲变形 的外 观形状大体分 为3种 : 横 向拱 形 、 向拱形 和任 意拱 形 。 向拱 形 , 指沿 着瓦 楞 纵 横 是 方向产生 的拱形 ; 向拱形 , 纵 是指 纸板沿 着生产 线速度 方
要使 纸板 具 有较 好 的平 整度 , 层纸 的 收缩 率就 必须 基 各 本相 同 , 中最 为主要 的是 面 、 纸 。 纸 收缩率 小于 里 其 里 面 纸 呈正拱 形 , 反之 呈负 拱形 、 面 里纸 收 缩率 局部 不 均则 成正 负拱 形。
文/ 谢毅 李波 邓国臣
瓦楞纸 箱 是使 用瓦 楞纸板 制 成 的全 纸 质包 装容 器 。
开槽 尺寸位移 , 纸箱 上下摇盖 重叠或 不合缝 ; 切送料 同 模
它具有重 量轻 、 结构 性能好 、 度大 、 强 缓冲 性能好 、 易于 回 收再 利用 符 合环保 要求 等优 点 。 能够 有效地 替代木材 和
相同 的纸质 。
③含 水 率大 的纸 经预 热器 的 受热 面使 长 度加 大 , 用
3 0
今 日印刷
20 . 0 61 0
维普资讯
本
期
聚 焦
之
电扇通 风 . 加散 发 水分 时 间 . 增 减慢 生产 线 速度 : 水率 含 小 的纸 经 预 热 器 的 受热 面 长度 减 小 . 自然 通风 . 汽 喷 蒸 雾. 加快生产 线速度 。 ④各层 纸 的上 胶量 保持 一致 . 瓦楞 方 向全 幅 宽度 沿 上胶 量均匀适 中。 ⑤气压 稳定 、 疏水 阀等管道配 件保持 正常功能 。 ⑥对刚从生产线制成 的部 分拱形 较大 的纸板 . 片 以1 0 左右 为一叠 . 反叠 放后 上方加压 板 . 正 让纸 板在 半成 品存 放过 程 中 受到正 反压 平 的外 力作 用 . 一天 后可 以达 到 较 好 的平 整度 。
纸箱纸板各种常见不良的解决方案

纸箱纸板各种常见不良的解决方案纸箱纸板在使用过程中常会出现一些不良,如折痕、开胶、断裂等问题。
下面是纸箱纸板常见不良的解决方案。
一、折痕问题1.质量控制:加强材料的质量管理,确保纸板的强度和刚度满足要求。
2.设计优化:合理设计纸箱的结构,避免出现折痕问题。
比如在纸箱侧面加强支撑板等。
3.减少叠压:降低堆码的高度和层数,减少纸箱在运输和存储过程中的压力,以减少折痕问题的发生。
二、开胶问题1.使用优质胶水:选择质量好的胶水,确保胶水的黏性和耐久性。
2.加强胶线的密度:增加胶线的密度,使胶层更加紧密,提高胶线的附着力。
3.加强胶合工艺:在胶水施加和压合的过程中,合理控制压力和温度,确保胶水完全固化粘结。
三、断裂问题1.加强纸板的强度:控制纸浆浓度和纤维长度,增加纸板的强度。
2.加强纸板的厚度:增加纸板的厚度,提高其负荷能力和抗拉强度。
3.加强纸板的湿强度:通过调整纸板的湿度和环境温度等条件,提高纸板的湿强度,减少断裂问题的发生。
四、印刷问题1.控制印刷压力:合理调整印刷机的压力,确保印刷品的清晰度和准确度。
2.提高油墨附着力:选择合适的油墨和印版,控制油墨的粘度和稠度,以提高油墨的附着力。
3.加强印刷技术培训:加强对印刷工人的技术培训,提高他们的专业素养和操作技巧。
五、包装问题1.加强包装材料的质量:选择优质的包装材料,提高其防潮、防震和防撞能力。
2.加强包装设计:合理设计包装结构,增加包装材料的厚度和缓冲层,提高纸箱的抗震能力。
3.加强包装测试:进行包装材料和纸箱的抗压试验,确保其在运输和储存过程中的安全性。
总之,要解决纸箱纸板的常见不良问题,需要从质量控制、设计优化、工艺改进和包装提升等多个方面入手,确保纸箱纸板的质量和性能满足使用要求。
瓦楞纸板各种常见纸病的解决方案
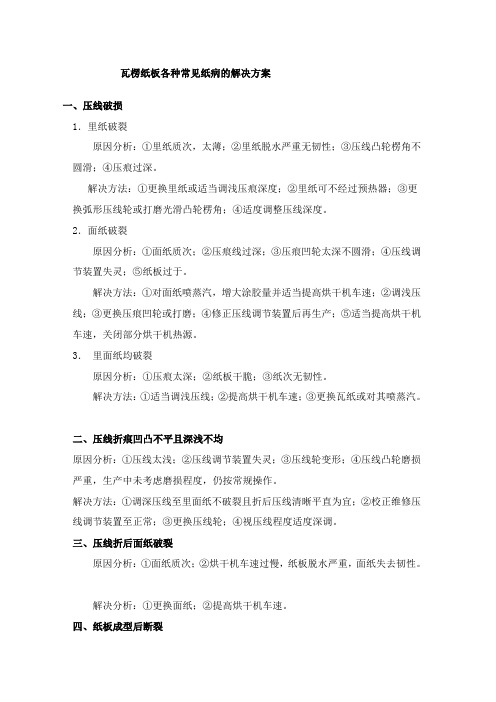
瓦楞纸板各种常见纸病的解决方案一、压线破损1.里纸破裂原因分析:①里纸质次,太薄;②里纸脱水严重无韧性;③压线凸轮楞角不圆滑;④压痕过深。
解决方法:①更换里纸或适当调浅压痕深度;②里纸可不经过预热器;③更换弧形压线轮或打磨光滑凸轮楞角;④适度调整压线深度。
2.面纸破裂原因分析:①面纸质次;②压痕线过深;③压痕凹轮太深不圆滑;④压线调节装置失灵;⑤纸板过于。
解决方法:①对面纸喷蒸汽,增大涂胶量并适当提高烘干机车速;②调浅压线;③更换压痕凹轮或打磨;④修正压线调节装置后再生产;⑤适当提高烘干机车速,关闭部分烘干机热源。
3.里面纸均破裂原因分析:①压痕太深;②纸板干脆;③纸次无韧性。
解决方法:①适当调浅压线;②提高烘干机车速;③更换瓦纸或对其喷蒸汽。
二、压线折痕凹凸不平且深浅不均原因分析:①压线太浅;②压线调节装置失灵;③压线轮变形;④压线凸轮磨损严重,生产中未考虑磨损程度,仍按常规操作。
解决方法:①调深压线至里面纸不破裂且折后压线清晰平直为宜;②校正维修压线调节装置至正常;③更换压线轮;④视压线程度适度深调。
三、压线折后面纸破裂原因分析:①面纸质次;②烘干机车速过慢,纸板脱水严重,面纸失去韧性。
解决分析:①更换面纸;②提高烘干机车速。
四、纸板成型后断裂原因分析:①瓦纸质次;②纸板过分干燥;③成型工序设备调节不当;④压线太浅,瓦楞未压扁或成型后折叠摇盖时高强瓦楞将面纸撑破,瓦楞随之断裂。
解决方法:①更换瓦纸;②保证纸板含水量在10±3左右;③注意成形各工序的设备调节并调至最佳状态;④烘干机加速并加大涂胶量,压线调深。
五、纵切毛边原因分析:①分纸刀已钝或刀刃有缺口;②上下刀咬合过深;③上下刀之间有间隙。
解决方法:①打磨或更换新刀;②调节上下刀重合至最佳状态;③将上下两刀靠紧,用手转动刀轮,灵活不伤刀为宜。
六、横切纸板拖尾原因分析:①横刀已钝;②横切刀上下两片咬合不正,纸板切不断的部位在机械力作用下带起撕裂的面瓦纸;③横切机瞬时加速调节不当,引起阻纸。
纸箱纸板三大常见问题解决方案

纸箱纸板三大常见问题解决方案目录印刷色差问题油墨耐磨性不佳纸板湿软一、印刷色差问题纸箱印刷机的时候,往往在使用一段时间后可能会出现印品变色的情况,对于这一情况往往无从下手,而且要花费大量的时间和金钱来维修。
如何能尽量解决掉这个办法呢?1 检查印刷品在版面上的设计是否合理。
(如把墨量比较大的图案放在拖稍位置,这样的版面设计肯定是不利于我们印刷出高质量的印刷品的,我们应该把他们放在叼口位置,才有利于叼牙对纸张的控制,更容易印刷出不变色的印刷品。
)如果做了这些印刷品仍然变色尽快通知公司进行维修,让问题快速解决。
2 检查墨路系统是否出现问题。
检查墨路系统,使用洗车水(可加水)将墨路彻底清洗干净,停车后应该检查墨路中是否有白色结晶的颗粒物存在,如果发现有这样的物质存在,那么出现的变色情况有可能是结晶物质堆墨尔产生的印刷品局部变色,这种变色往往更体现出来的品刷品局部色彩偏色。
在洗车后如没有发现这些结晶物质,重新启动印刷机,打墨到每一根墨辊,打墨结束合上靠版墨辊和靠版水辊,检查压力是否达到标准,如果没有,建议将所有墨辊压力重新调整,达到较好的状态。
3 试印。
试印时尽量选择比较好的铜版纸进行试印,避免纸张的问题影响。
对于薄纸在压印上的风量要尽量开小,对于厚纸我们要适量开大。
如果已经出现了印刷品变色的情况,不要立马判断是印刷机本身问题这样的结论,应该先在印刷机的外围寻找原因,首先应该使用放大镜观察印刷版上的网点,检查它是否已经出现的网点的变形,如果发现在印刷版上已经出现了网点的变形,那么应该对片子进行检查,排除在出片的时候的问题。
4 检查纸张下纸的情况。
包括下纸风的调节,纸张在前规的平整度,纸张与压纸片之间的配合,输纸皮带的运行情况等等。
5 清洗牙垫牙片。
摘掉弹簧进行清洗,只清洗牙垫,不清洗牙片这样不对的。
检查是否有死牙的情况,使用WD-40这样的高效除锈剂,并且对牙和牙轴进行打油,确保没有死牙。
在水墨路都没有问题的情形下,应该检查橡皮的衬垫是否是标准,新橡皮布在使用一段时候后最好再重新紧一次。
瓦楞纸板及印刷不良问题产生的原因及解决办法(PPT54页)

二
双面机加热板温度不够
部
车速太快
分
脱
原纸含水量太高
胶
胶黏剂质量不好
胶黏剂附着量小
解决办法
检查冷凝水排放装置和 供水气压是否符合要求 检查供气部分是否有故障
适当降低车速 加大预热或换纸
修正胶黏剂质量 加大胶黏剂附着量
产生原因
单面机涂胶量过小
涂胶机涂胶量过大
一
双面机加热温度不够
横
向
面纸预热包角太小 、里纸预热包角太大
原因
滚筒压力不足 墨层太厚
油墨黏度太高
解决办法
适量调高滚筒之间的压力 调薄墨层
适当稀释油墨
四 印面油 墨粉化 ,摩擦 后容易 脱落, 墨色浑 浊
原因
油墨过稀 油墨变质
解决办法
减少稀释溶剂,增加油墨浓度 给油墨增添树脂剂量,增强 油墨黏性和粘接附着性能
换掉变质的油墨
原因
五
印
印版上有旧墨堆积
上
翘
输送桥架纸板过多堆积
输送桥架输出瓦 楞纸板张力过大
解决办法
适当加大张力系 统的控制力度
适当预热 检查、修整传动装 置,保证运转正常
减少堆积量
适当减少纸板输出张力控制
产生原因
传送带运行压力不够
四
纵
输送桥架输出瓦 楞纸板张力不够
向
向
下
面纸含水量不均衡
翘
面纸张力太大
解决办法
适当加大张力系 统的控制力度
调整前色干燥速度、尽 量在后一色印刷前干燥
问题
供墨系统清洁不彻底
七 墨 杠
水墨本身含有未完 全溶解的颜料颗粒
解决办法
更换产品时将供墨系统彻底 清洁干净,注意避免前后两 种产品颜色相差很远且使用 同一印刷色组的大面积印刷
瓦楞纸印刷工艺常见的问题
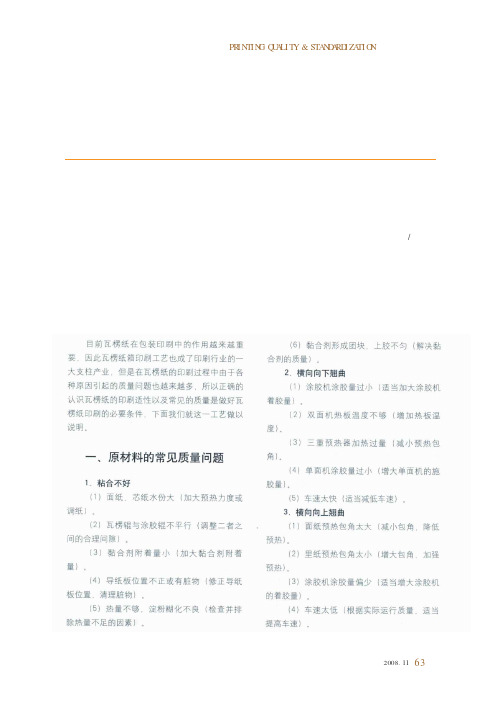
目前瓦楞纸在包装印刷中的作用越来越重要,因此瓦楞纸箱印刷工艺也成了印刷行业的一大支柱产业,但是在瓦楞纸的印刷过程中由于各种原因引起的质量问题也越来越多,所以正确的认识瓦楞纸的印刷适性以及常见的质量是做好瓦楞纸印刷的必要条件,下面我们就这一工艺做以说明。
一、原材料的常见质量问题1.粘合不好(1)面纸、芯纸水份大(加大预热力度或调纸)。
(2)瓦楞辊与涂胶辊不平行(调整二者之间的合理间隙)。
(3)黏合剂附着量小(加大黏合剂附着量)。
(4)导纸板位置不正或有脏物(修正导纸板位置,清理脏物)。
(5)热量不够,淀粉糊化不良(检查并排除热量不足的因素)。
(6)黏合剂形成团块,上胶不匀(解决黏合剂的质量)。
2.横向向下翘曲(1)涂胶机涂胶量过小(适当加大涂胶机着胶量)。
(2)双面机热板温度不够(增加热板温度)。
(3)三重预热器加热过量(减小预热包角)。
(4)单面机涂胶量过小(增大单面机的施胶量)。
(5)车速太快(适当减低车速)。
3.横向向上翘曲(1)面纸预热包角太大(减小包角、降低预热)。
(2)里纸预热包角太小(增大包角、加强预热)。
(3)涂胶机涂胶量偏少(适当增大涂胶机的着胶量)。
(4)车速太低(根据实际运行质量,适当提高车速)。
(5)双面机热板温度高(提高车速或人为降低热板温度)。
常见的问题瓦楞纸印刷工艺文/南静生4.纵向向上翘曲(1)原纸张力不够(适当加大张力系统的控制力度)。
(2)原纸含水不均衡(适当预热或喷水后预热)。
(3)预热器包角调控不平衡(检查并修整传动装置,保证运行平行)。
(4)过纸天桥过多堆积(减少堆积)。
(5)过纸天桥输出瓦楞纸板张力过大(适当减小输出张力控制)。
5.纵向向下翘曲(1)帆布带运行压力不够(检查并修正帆布带的张力)。
(2)过纸天桥输出瓦楞纸板张力不够(适当增大输出张力控制)。
(3)面纸含水不均衡(喷水并适当预热)。
(4)面纸张力太大(减小对面纸的张力控制)。
6.S形翘曲(1)原纸水份分布不均匀(喷淋或预热控制)。
瓦楞纸箱印刷常见几个问题
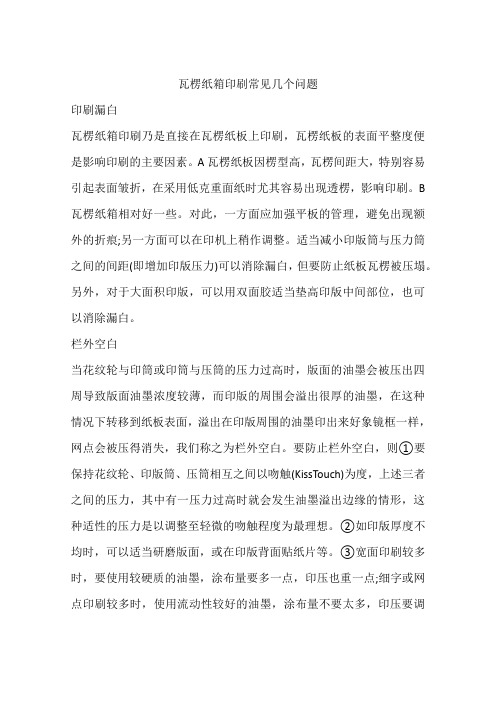
瓦楞纸箱印刷常见几个问题印刷漏白瓦楞纸箱印刷乃是直接在瓦楞纸板上印刷,瓦楞纸板的表面平整度便是影响印刷的主要因素。
A瓦楞纸板因楞型高,瓦楞间距大,特别容易引起表面皱折,在采用低克重面纸时尤其容易出现透楞,影响印刷。
B 瓦楞纸箱相对好一些。
对此,一方面应加强平板的管理,避免出现额外的折痕;另一方面可以在印机上稍作调整。
适当减小印版筒与压力筒之间的间距(即增加印版压力)可以消除漏白,但要防止纸板瓦楞被压塌。
另外,对于大面积印版,可以用双面胶适当垫高印版中间部位,也可以消除漏白。
栏外空白当花纹轮与印筒或印筒与压筒的压力过高时,版面的油墨会被压出四周导致版面油墨浓度较薄,而印版的周围会溢出很厚的油墨,在这种情况下转移到纸板表面,溢出在印版周围的油墨印出来好象镜框一样,网点会被压得消失,我们称之为栏外空白。
要防止栏外空白,则①要保持花纹轮、印版筒、压筒相互之间以吻触(KissTouch)为度,上述三者之间的压力,其中有一压力过高时就会发生油墨溢出边缘的情形,这种适性的压力是以调整至轻微的吻触程度为最理想。
②如印版厚度不均时,可以适当研磨版面,或在印版背面贴纸片等。
③宽面印刷较多时,要使用较硬质的油墨,涂布量要多一点,印压也重一点;细字或网点印刷较多时,使用流动性较好的油墨,涂布量不要太多,印压要调整至最小限度。
叠色漏白当在一种颜色上盖上另一种颜色时(通常为黑色),常会出现第二色印刷不上的情况。
其原因可以归结为二种油墨颜料的表面张力相差较大,上面油墨颜料无法均匀地覆盖在下面墨层上。
目前尚没有找到一种方法可以彻底解决这一毛病。
在纸板印刷实际操作中,以下方法可稍作改善:1.提高第一色干燥速度,可以适当添加酒精或氨水等;2降低第二色的粘度,或提高其附着力,适当增加印刷压力。
粘度增加油墨在使用过程中常常会出现粘度增加,颜色加深的情况,这是由于油墨中氨水的挥发造成的。
粘度与PH值有关,随着油墨不停地循环,氨水挥发,PH值下降,粘度增加;同时水分的挥发,使印刷颜色加深。
怎样解决常见纸板问题
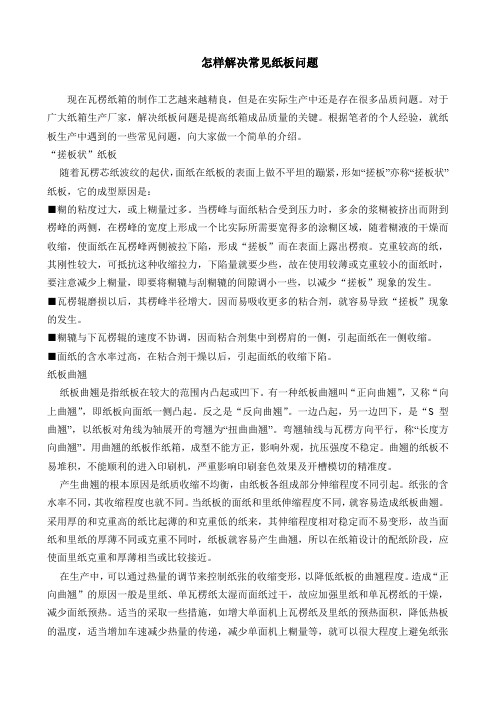
怎样解决常见纸板问题现在瓦楞纸箱的制作工艺越来越精良,但是在实际生产中还是存在很多品质问题。
对于广大纸箱生产厂家,解决纸板问题是提高纸箱成品质量的关键。
根据笔者的个人经验,就纸板生产中遇到的一些常见问题,向大家做一个简单的介绍。
“搓板状”纸板随着瓦楞芯纸波纹的起伏,面纸在纸板的表面上做不平坦的蹦紧,形如“搓板”亦称“搓板状”纸板,它的成型原因是:■糊的粘度过大,或上糊量过多。
当楞峰与面纸粘合受到压力时,多余的浆糊被挤出而附到楞峰的两侧,在楞峰的宽度上形成一个比实际所需要宽得多的涂糊区域,随着糊液的干燥而收缩,使面纸在瓦楞峰两侧被拉下陷,形成“搓板”而在表面上露出楞痕。
克重较高的纸,其刚性较大,可抵抗这种收缩拉力,下陷量就要少些,故在使用较薄或克重较小的面纸时,要注意减少上糊量,即要将糊辘与刮糊辘的间隙调小一些,以减少“搓板”现象的发生。
■瓦楞辊磨损以后,其楞峰半径增大。
因而易吸收更多的粘合剂,就容易导致“搓板”现象的发生。
■糊辘与下瓦楞辊的速度不协调,因而粘合剂集中到楞肩的一侧,引起面纸在一侧收缩。
■面纸的含水率过高,在粘合剂干燥以后,引起面纸的收缩下陷。
纸板曲翘纸板曲翘是指纸板在较大的范围内凸起或凹下。
有一种纸板曲翘叫“正向曲翘”,又称“向上曲翘”,即纸板向面纸一侧凸起。
反之是“反向曲翘”。
一边凸起,另一边凹下,是“S型曲翘”,以纸板对角线为轴展开的弯翘为“扭曲曲翘”。
弯翘轴线与瓦楞方向平行,称“长度方向曲翘”。
用曲翘的纸板作纸箱,成型不能方正,影响外观,抗压强度不稳定。
曲翘的纸板不易堆积,不能顺利的进入印刷机,严重影响印刷套色效果及开槽模切的精准度。
产生曲翘的根本原因是纸质收缩不均衡,由纸板各组成部分伸缩程度不同引起。
纸张的含水率不同,其收缩程度也就不同。
当纸板的面纸和里纸伸缩程度不同,就容易造成纸板曲翘。
采用厚的和克重高的纸比起薄的和克重低的纸来,其伸缩程度相对稳定而不易变形,故当面纸和里纸的厚薄不同或克重不同时,纸板就容易产生曲翘,所以在纸箱设计的配纸阶段,应使面里纸克重和厚薄相当或比较接近。
瓦楞纸箱工艺缺陷弥补方案-纸板印刷问题
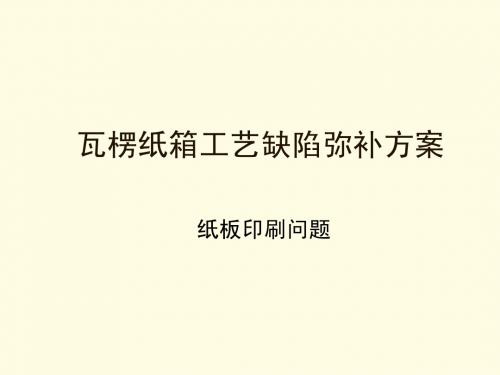
印刷滚筒的定位不准确 进纸辊和引出辊磨损严重 印版的各套色图案不符合标准要求, 以至于不能达到良好的套准效果
原因
印版排列不准确 印刷机机械状况不良(如齿轮、键槽 或轴承磨损) 纸板控制不当 纸板严重翘曲 没使用或没有正确使用带纸条 纸板宽度相对于印刷机太窄
措施
重新组合印版以恰当套准。使用校准器确保套 印准确 进行适当的维修,在印刷机上使用齿轮控制器, 按客户的套准要求进行印刷 调整夹点(包括平行状况),增加引纸带 如果可能,将纸板处理后压平 如果可能,调换纸板,重启瓦线 使用高度合适的带纸条,并使之位置正确 使用小型号的印刷机印刷
印版——排版不准确
是指各个印版位置或整体组合不准确
原因
印版排列或印版位置不准确而整体不协调
措施
在印刷开槽机、柔性折叠糊箱机或柔性 圆压圆模切机上使用印刷小样前,先检 查印刷原件和所有印版的尺寸 检查装置并调整所有位置不当的印版
印刷机上印刷小样位置不准确(或部分印 刷小样位置不准确
印版——印刷质量很差
措施
调整刮墨辊 调换刮墨辊 调换刮墨刀 调换刮墨刀 清除网纹辊上的污垢 调换网纹辊 减少印刷滚筒和印刷滚筒之间的距离 调换网纹辊 向造纸厂或油墨供应商技术代表寻求帮忙 减少印刷滚筒和压印滚筒之间的距离或调换瓦楞纸板 增加新油墨或使用另一墨盒中的油墨 清除印版上的污垢或调换印版 咨询印版供应商,使用标准的硬度计 增加印版在承印物上的压力
印迹上缺失油墨的空白
印刷后纸板上的印迹有缺失油墨的空白处
原因
印版有缺损(通常失被损坏) 瓦楞纸板上有凹处 承印物表面吸收油墨不均
措施
调换印版或印刷小样的部分 调换瓦楞纸板 瓦线传送带表面的斑点或下瓦楞辊传送带 上堆积的异物通常是主要原因。如果这种 情况并不太严重,减少印刷滚筒到压印滚 筒之间的距离是一种解决办法。然而为了 弥补纸板的凹陷而增加印版的压力可能会 严重地将瓦楞压碎 咨询原纸生产商或油墨生产商的技术人员
纸箱、纸板存在的质量问题及解决方法分析

纸箱、纸板存在的质量问题及解决方法分析摘要:纸箱、纸板的材料经济实惠、使用方便且环保,因此深受用户的欢迎.但是纸箱、纸板也存在着一些问题,因此需要针对这些问题进行解决.本文通过对纸箱、纸板中存在的一些问题进行分析,提出了改进纸箱纸板质量的一些措施,希望能够对提高纸箱纸板的质量有些帮助。
关键词:纸箱纸板、质量问题、解决方法、分析引言:产品的质量是企业各项管理工作的综合反映,也是企业的生命,因此必须要加强管理和领导,提高产品的质量。
纸箱质量的好坏与瓦楞纸板以及纸箱成型的工艺有关。
随着社会的进步,客户对纸箱的质量要求越来越严格.因此生产纸箱的厂家只有提高产品的质量并且防止出现各种质量问题,才能够满足市场的需求,进而使企业取得良好的经济效益以及社会效益。
一、纸箱纸板存在质量问题的原因1、尺寸不准确纸箱的尺寸可以分为内外径尺寸以及加工尺寸.内径的尺寸要求在装入物品后还得再留有3-5毫米的空隙,而外径的尺寸也需要满足集装箱、火车以及卡车的装运要求。
在进行加工时,要充分考虑这些尺寸的需求,否则就会造成失误而出现经济损失。
2、印刷质量差在纸箱表面通常需要印一些文字、数字,而进行印刷时经常会出现印刷的字母或者数字排列不齐或者大小不一等不规范、不标准的现象出现.出现这些问题没有得到及时的纠正,因而出现了质量问题而导致纸箱报废。
版面如果印刷模糊或者颜色深浅不一致以及跑版都会使纸箱的美观和质量受到影响。
如果印刷时没有控制好水墨的粘度、传送的状态,或者送纸不稳定、纸版不平整都有可能会导致跑版、颜色深浅不一致等问题的出现。
而印刷压力过大或者版面上粘有多余的印刷痕迹,就会造成版面模糊。
在印刷时需要进行重点控制,如果纸板的印刷质量好,就会使纸箱的外观美观,同时也会受到用户的好评。
3、纸箱外观较差如果在制纸箱时使用的原材料的强度差就会使制造出来的纸板发软,同时原纸的质量也对纸箱的抗压强度产生直接的影响。
如果纸板倒瓦就会使纸箱的质量变得发软,同时如果原材料中含水率或者施胶量过大,胶液中的水份就有可能渗入到瓦楞中,进而使瓦楞变软而导致质量下降。
纸板问题解决工艺流程全控制
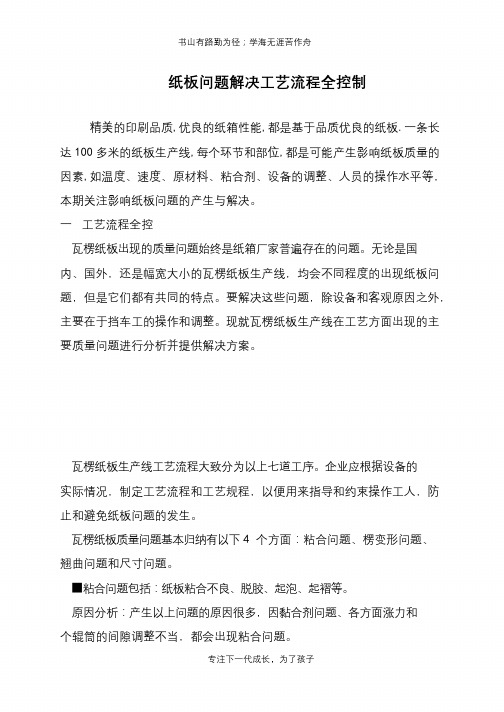
书山有路勤为径;学海无涯苦作舟
纸板问题解决工艺流程全控制
精美的印刷品质,优良的纸箱性能,都是基于品质优良的纸板.一条长
达100多米的纸板生产线,每个环节和部位,都是可能产生影响纸板质量的
因素,如温度、速度、原材料、粘合剂、设备的调整、人员的操作水平等,本期关注影响纸板问题的产生与解决。
一工艺流程全控
瓦楞纸板出现的质量问题始终是纸箱厂家普遍存在的问题。
无论是国
内、国外,还是幅宽大小的瓦楞纸板生产线,均会不同程度的出现纸板问题,但是它们都有共同的特点。
要解决这些问题,除设备和客观原因之外,主要在于挡车工的操作和调整。
现就瓦楞纸板生产线在工艺方面出现的主要质量问题进行分析并提供解决方案。
瓦楞纸板生产线工艺流程大致分为以上七道工序。
企业应根据设备的
实际情况,制定工艺流程和工艺规程,以便用来指导和约束操作工人,防止和避免纸板问题的发生。
瓦楞纸板质量问题基本归纳有以下4个方面:粘合问题、楞变形问题、
翘曲问题和尺寸问题。
■粘合问题包括:纸板粘合不良、脱胶、起泡、起褶等。
原因分析:产生以上问题的原因很多,因黏合剂问题、各方面涨力和
个辊筒的间隙调整不当,都会出现粘合问题。
专注下一代成长,为了孩子。
印刷纸板不良解决办法
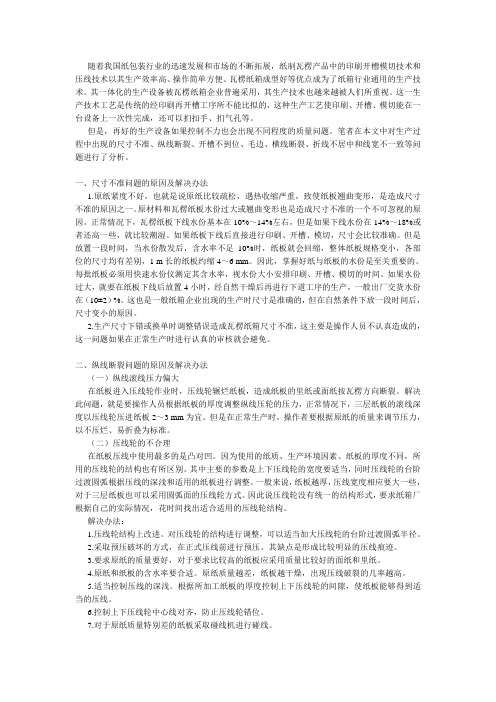
随着我国纸包装行业的迅速发展和市场的不断拓展,纸制瓦楞产品中的印刷开槽模切技术和压线技术以其生产效率高、操作简单方便、瓦楞纸箱成型好等优点成为了纸箱行业通用的生产技术。
其一体化的生产设备被瓦楞纸箱企业普遍采用,其生产技术也越来越被人们所重视。
这一生产技术工艺是传统的经印刷再开槽工序所不能比拟的,这种生产工艺使印刷、开槽、模切能在一台设备上一次性完成,还可以扪扣手、扪气孔等。
但是,再好的生产设备如果控制不力也会出现不同程度的质量问题。
笔者在本文中对生产过程中出现的尺寸不准、纵线断裂、开槽不到位、毛边、横线断裂、折线不居中和线宽不一致等问题进行了分析。
一、尺寸不准问题的原因及解决办法1.原纸紧度不好,也就是说原纸比较疏松,遇热收缩严重,致使纸板翘曲变形,是造成尺寸不准的原因之一。
原材料和瓦楞纸板水份过大或翘曲变形也是造成尺寸不准的一个不可忽视的原因。
正常情况下,瓦楞纸板下线水份基本在10%~14%左右,但是如果下线水份在14%~18%或者还高一些,就比较潮湿。
如果纸板下线后直接进行印刷、开槽、模切,尺寸会比较准确。
但是放置一段时间,当水份散发后,含水率不足10%时,纸板就会回缩,整体纸板规格变小,各部位的尺寸均有差别,1 m长的纸板约缩4~6 mm。
因此,掌握好纸与纸板的水份是至关重要的。
每批纸板必须用快速水份仪测定其含水率,视水份大小安排印刷、开槽、模切的时间。
如果水份过大,就要在纸板下线后放置4小时,经自然干燥后再进行下道工序的生产,一般出厂交货水份在(10±2)%。
这也是一般纸箱企业出现的生产时尺寸是准确的,但在自然条件下放一段时间后,尺寸变小的原因。
2.生产尺寸下错或换单时调整错误造成瓦楞纸箱尺寸不准,这主要是操作人员不认真造成的,这一问题如果在正常生产时进行认真的审核就会避免。
二、纵线断裂问题的原因及解决办法(一)纵线滚线压力偏大在纸板进入压线轮作业时,压线轮辗烂纸板,造成纸板的里纸或面纸按瓦楞方向断裂。
印刷质量三大问题快速解决方法

印刷质量三大问题快速解决方法一、印刷露白的处理印刷露白是瓦楞纸箱生产中最常见也是最难以杜绝的质量问题,其产生的原因有:纸质吸墨性能差;印版脏;纸板上有约屑、灰尘等。
对这些问题传统的处理方法是人工改箱,或是增加人工擦版的频率。
这些方法在客观上会起到一定的作用,但改箱后改善效果不大,且易造成效率下降;擦版还会造成水、电、人工的浪费。
印猫网小编经过长期的观察分析,认为在设备安装、维修、管理的过程中,解决印刷露白的关键在于除尘。
灰尘的主要来源是单刀分纸时产生的,基于这一情况,小编两年前在纸板生产线的电脑横切刀后以及印刷机的送纸部先后安装了静电吸风吸尘装置,在电脑横切刀前使用吹风机,将单片刀分纸时隐藏于坑纹中的约屑吹出来或吹掉,而后在电脑横切刀后的收纸架处利用静电吸风吸尘装置将纸屑吸走。
在印刷机送纸部的送纸胶圈与送纸轮间隙处利用静电吸尘将纸板上的灰尘吸走,保质印刷面干净无尘,在这样的条件下,纸板进入印辊时,上墨无障碍,及墨均匀。
经过这样的改良后,产品印刷效果大大改观,并从根本上克服了灰尘造成的印刷露白现象。
二、套印走位的处理现在商品包装愈来愈注重图案的艺术性、立体感,使消费者从外包装上感受到所购商品的完善。
为达到该目的,包装印刷必须采用多色印刷,即多色套印。
在套印工艺中,往往出现后一色与前一色叠加或定位位置产生错位,致使印刷图案不能体现产品包装的设计效果,甚至大相径庭,完全破坏了产品的形象。
针对这一特殊问题,小编所在公司经过一段时间深入现场的调查研究,对电控反映速度到机械配合公差精度,进行了详细的计算,对现有设备进行了多处改良,同时制定了相关的设备维修措施。
1、提高印刷滚筒相位定位的精度印刷滚筒相位定位采用encoder与counter配合控制,若counter的精度太低,则会造成encoder位置不准确,印刷时走位。
聚鉩ounter反映速度为3k,但在定位时往往±1mm的误差,经与台湾电控公司商讨,生产出5krcounter,使印刷滚筒定位误差缩小到±0.4mm。
瓦楞纸箱印刷中常见的几个问题分析

瓦楞纸箱印刷中常见的几个问题分析瓦楞纸箱作为一种常见的包装材料,其图案的印刷质量对于产品的外观和质量都具有重要的影响。
然而,在瓦楞纸箱印刷过程中,常常会遇到一些问题,影响印刷质量和产量。
本文将对瓦楞纸箱印刷中常见的几个问题进行分析,并提出相应的解决方案。
1. 印刷颜色不真实在瓦楞纸箱印刷中,有时会出现印刷颜色不够真实的情况。
这种问题的主要原因是印刷机的墨路设置不当。
当墨路不均衡或者墨量不适当时,就会导致印刷颜色变淡或者色差过大的情况。
解决方案:(1)调整墨路:对于印刷颜色不真实的情况,可以考虑调整墨路。
首先需要使用专业的测试仪器来测试各个墨路的墨量,找出墨量不均衡的原因。
然后可以通过调整辊道压力或者调整墨槽和刮刀的间距来解决问题。
(2)调整墨量:对于印刷颜色过淡或者过浓的情况,可以通过调整墨量来解决。
可以尝试减少或者增加墨量,或者调整墨盘的转速来改变墨量。
2. 印刷墨层不均匀瓦楞纸箱的印刷墨层不均匀是另一个常见的问题。
这种问题的主要原因是印刷机的墨路设置不当、印刷机的辊子表面磨损或者印版的质量不好。
解决方案:(1)检查印刷机的墨路:如果墨路有问题,需要检查印刷机的墨路是否畅通无阻,然后做出相应的调整。
(2)检查印刷机的辊子表面:如果辊子表面磨损,可以考虑更换新的辊子表面或者使用适当的润滑剂来解决。
(3)检查印版的质量:如果印版的质量不好,可以更换新的印版。
3. 印刷机速度过慢在实际的印刷过程中,有时会出现印刷速度过慢的情况。
这种情况主要是因为印刷机的机械部分出现了问题。
解决方案:(1)检查印刷机的机械部分:在印刷机运行过程中,需要定期检查印刷机的机械部分是否出现了问题。
如果出现了问题,需要及时修理。
(2)使用质量更好的配件:使用质量更好的配件可以增强印刷机的稳定性和耐久性,从而避免发生故障。
总之,对于瓦楞纸箱印刷过程中出现的问题,我们需要及时检查,确定问题原因并采取相应的措施,从而确保印刷质量和生产效率。
- 1、下载文档前请自行甄别文档内容的完整性,平台不提供额外的编辑、内容补充、找答案等附加服务。
- 2、"仅部分预览"的文档,不可在线预览部分如存在完整性等问题,可反馈申请退款(可完整预览的文档不适用该条件!)。
- 3、如文档侵犯您的权益,请联系客服反馈,我们会尽快为您处理(人工客服工作时间:9:00-18:30)。
印刷滚筒的定位不准确 进纸辊和引出辊磨损严重 印版的各套色图案不符合标准要求, 以至于不能达到良好的套准效果
原因
印版排列不准确 印刷机机械状况不良(如齿轮、键槽 或轴承磨损) 纸板控制不当 纸板严重翘曲 没使用或没有正确使用带纸条 纸板宽度相对于印刷机太窄
措施
重新组合印版以恰当套准。使用校准器确保套 印准确 进行适当的维修,在印刷机上使用齿轮控制器, 按客户的套准要求进行印刷 调整夹点(包括平行状况),增加引纸带 如果可能,将纸板处理后压平 如果可能,调换纸板,重启瓦线 使用高度合适的带纸条,并使之位置正确 使用小型号的印刷机印刷
套印/叠印质量差
是指纸板印刷时一种颜色与另一种颜色重叠处颜色太浓。
原因
印刷时油墨颜色顺序排列不准确,例如, 试图用较浅的一种颜色去覆盖较深的颜 色(只适用于柔版印刷) 上墨量太多 油墨颜色和油墨粘度不准确(只用胶版 印刷)
措施
如果可能,调换墨色印刷顺序
减少油墨流量,用最少的油墨量达到最 好的油墨覆盖效果 浅色油墨必须先涂而且粘度要比第二种 颜色的油墨高
措施
通过以下方式加快油墨变干速度: 降低油墨粘度 应用较好的刮墨装置降低油墨层厚度 改变油墨配方使油墨变干速度加快 降低印刷机运转速度 减少网纹辊中油墨流量 提高干燥器温度
印迹模糊 原因
因承印物的表面质量问题导致油墨不干
措施
调换承印物,降低油墨层厚度,或加强干 燥系统功能 咨询纸板生产商或油墨生产商的技术人员 向油墨生产商的技术人员寻求帮助 咨询油墨生产商的技术人员 调整油墨计量辊,印刷滚筒,网纹辊(只 适用于柔版印刷)和压印滚筒之间的平行 状况 检查印版的水平情况 清除印版上的污垢 重新调整带纸轮使之与印刷部位对齐,或 使之置于瓦楞纸板的外缘 调换或调整折带 调整或将之去除以使其影响降低到最小 将输送带从印刷区域移走或抬高其位置 调整纸板挡板位置或纸板传送带的速度, 如果涂墨量太多,有必要提高传送带的速 度
措施
更换有缺陷的印版 为防止有污点产生,使印刷辊筒和压印辊 筒之间保持足够的间距 减少油墨使用量 清除印版上的污垢 增加成型辊和印版之间的距离
歪曲的印刷字迹或图像
是指印刷字迹或图像歪曲,而不符合印刷要求。
原因
印刷压力太大 印版生产时没有考虑到平面变弧形时的伸 展变形因素,尤其是在印刷精确的圆圈时 需特别注意
印迹上缺失油墨的空白
印刷后纸板上的印迹有缺失油墨的空白处
原因
印版有缺损(通常失被损坏) 瓦楞纸板上有凹处 承印物表面吸收油墨不均
措施
调换印版或印刷小样的部分 调换瓦楞纸板 瓦线传送带表面的斑点或下瓦楞辊传送带 上堆积的异物通常是主要原因。如果这种 情况并不太严重,减少印刷滚筒到压印滚 筒之间的距离是一种解决办法。然而为了 弥补纸板的凹陷而增加印版的压力可能会 严重地将瓦楞压碎 咨询原纸生产商或油墨生产商的技术人员
措施
降低油墨粘度 咨询机械供应商有关材料和实际操作的建 议 减少油墨流量 清洗印版 减少印版到承印物表面的压力 使印版保持水平,填充凹处,清洗或调换 印版或调整印版组合 通过以下方式降低油墨层的厚度 降低油墨粘度 加强刮墨装置功能 减少网纹辊中的油墨流量
印迹空隙间填充油墨
(接上文)
原因
网线数相对于油墨层厚度或刮刀太小
印迹不干净
(接上文)
原因
油墨层太厚
措施
通过以下方式降低墨层的厚度 降低油墨粘度 提高刮墨装置的准确度 减少网纹辊中的油墨量 通过添加溶剂降低油墨变干速度 排除印版上或新印刷表面的气流或 热流提高机器运转速度 调整刮墨装置,承印纸板,网纹辊 压力,辊的平行状况,调换印版 使用硬度大些的印版 调整印版网线数使其配合印刷要求
措施
减少压力 使用制造工艺准确的印版,调换原来 的印版
套印不准
套印是指一种颜色平滑的与另一种颜色交搭以保证相邻颜色的高质量边缘。而在印刷 中常常出现套印不准的情况。
原因
多色印刷机上的版辊位置不准确
措施
因为纸板被拉出印刷机时厚度有细微的变化, 所以每种颜色的版辊都应比其前一个更紧固些 ,这样才能使所有颜色上施加的压力都相等 检查并确定是哪种颜色套印时有问题。一次调 整一种颜色 检查并更换 检查所有的印版。标准的印版在恰当组合后可 以使不同颜色套准时的重叠部分大小
印版——排版不准确
是指各个印版位置或整体组合不准确
原因
印版排列或印版位置不准确而整体不协调
措施
在印刷开槽机、柔性折叠糊箱机或柔性 圆压圆模切机上使用印刷小样前,先检 查印刷原件和所有印版的尺寸 检查装置并调整所有位置不当的印版
印刷机上印刷小样位置不准确(或部分印 刷小样位置不准确
印版——印刷质量很差
措施
调整刮墨辊 调换刮墨辊 调换刮墨刀 调换刮墨刀 清除网纹辊上的污垢 调换网纹辊 减少印刷滚筒和印刷滚筒之间的距离 调换网纹辊 向造纸厂或油墨供应商技术代表寻求帮忙 减少印刷滚筒和压印滚筒之间的距离或调换瓦楞纸板 增加新油墨或使用另一墨盒中的油墨 清除印版上的污垢或调换印版 咨询印版供应商,使用标准的硬度计 增加印版在承印物上的压力
措施
清除纸板上的灰尘 定期停机清除印版上的污垢 印刷机上增加真空吸尘功能用来清理灰尘和 纤维碎屑 调整或打磨模切刀 降低印版到承印物表面的压力 检查并调整油墨的PH值至标准 调整并降低网纹辊压力,检查印版的水平 状况
模切刀边缘粗糙 印版压力过大 油墨PH值太低(只适用于柔版印刷) 网纹辊至印版的压力过大(只适用 于 柔版印刷)
是指印刷图案表面有刮伤痕迹、露底或字迹模糊等情况。
原因
印版磨损或硬化 印版磨损程度不均
措施
调换印版 重新组合印版或调换印版的个别部分。使 用印版校样机来确保印版组合恰当并且厚 度一致 重新装版
印版垫材
印刷字迹轮廓模糊
是指印刷出的字迹或图像轮廓不清晰。
原因
印版厚度不均 印刷压力太大 油墨使用量太多 印版上有污垢 成型辊和印版(胶版印刷中)之间压力太大 印刷字迹有晕圈(柔版印刷中)
油墨——不标准的颜色密度和亮度
是指与标准印刷效果相比,所印刷出来的字迹颜色密度将上墨系统彻底 清洗干净 颜色使用不当 油墨浓度不当,没有充分混合,或 配方不当 油墨中混入水,阀门被粘在自动冲 洗位置上
措施
用标准颜色样本,比重计和分光光度计检查每 一批油墨,用颜色标准的油墨调换原来的油墨 将上墨系统中的墨垢清除,清洗系统,并使用 新鲜油墨 使用颜色标准的油墨 检查油墨浓度,坚持每半小时检查一次,调整 油墨浓度。印刷前将油墨在搅拌器中充分搅拌 3-5分钟。咨询油墨供应商油墨配方的问题 检查关水阀,(活塞可能会被粘住)。增加空 气供应量来校正
油墨变干太快
因为机器问题或印版位置不水平 导致油墨层厚度不均 印版太软 印版的网线数和网纹辊网穴数目 比率不匹配
印迹空隙间填充油墨
印刷字迹或图像间隙中填充油墨
原因
油墨粘度太高(只适用于柔版印刷) 网纹辊上油墨层德刮墨装置功能不足 油墨流量过大 印版上有污垢 印版不水平、磨损、凹陷、不净、或 组合不当 油墨层相对于印版和印迹太厚
套印/叠印质量差 原因
因为油墨质量问题或油墨层的厚度问题, 先印刷上的油墨不干
措施
通过以下方式,提高油墨变干速度 降低先涂上的油墨的粘度 用较好的刮墨装置降低油墨层的厚度 改变油墨配方以加快变干速度 降低印刷机的运转速度 减少网纹辊的油墨流量 提高干燥器的温度 增加第二种油墨的粘度并使之比第一种 油墨的粘度高 通过以下措施降低变干速度 加入降低变干速度的溶剂(慢干剂) 停止印版上的气流或热流 提高印刷机运转速度 调整油墨的PH值,使之符合油墨供应 商推荐的规格或调换油墨 调整承印物,降低油墨层厚度,或加强 油墨干燥系统功能 咨询油墨供应商关于改变油墨、添加 剂或有关产品的建议
油墨——覆盖不均
(只适用于柔版印刷) 是指油墨在整张纸上的浓度和分布不均。
原因
刮墨辊调整不当 刮墨辊严重磨损 刮墨刀调整不当 刮墨刀严重磨损 网纹辊上有污垢 网纹辊严重磨损或网穴堵塞 网纹辊压力太小 网纹辊损坏 承印物不着墨,或着墨不均 纸板面纸露楞 油墨浓度太低 印版表面不净 印版硬度不准确 印版压印压力太小
减少油墨流量 胶版印刷中的油墨渗透可能是由于堆纸架上的 纸板互相叠压引起。可以通过减少堆纸架上数 量降低油墨渗透 从油墨生产商的技术代表那寻求帮助 调换纸板面纸或油墨,或咨询面纸或油墨生产 商的技术代表
油墨干燥系统功能不良 承印物表面不附着油墨
印迹模糊
是指油墨溢出字迹轮廓之外。
原因
由于油墨太厚而油墨不干(涂墨量太多)
印刷时将瓦楞压溃
因为印版向纸板施压太大,大量瓦楞被压溃。
原因
印刷滚筒压力太大 印版衬垫不平或不合适 印版磨损程度不均 带纸条压力太大 带纸条尺寸太大
措施
增加印刷滚筒和压印滚筒之间的距离 调换印版衬垫,使用校准器以确保所有印版 厚度一致 重新组合印版(必要时调换部分印刷原件), 使用校准器以确保所有印版厚度一致 如果印刷质量不能达到要求,增加印刷滚筒 和压印滚筒之间的距离 装置厚度合适的牵引纸带
印刷机上一个或多个辊或滚筒尺寸不当引 起滚筒和瓦楞纸板间的线速度比率不准确 纸板进入印刷机前印版上油墨较多 承 双色中或多色印刷中先涂上的油墨粘度太 大
原因
印刷滚筒高速运转时油墨喷溅
措施
干速度应比后涂上的颜色变干速度快 减少油墨流量
印迹不干净
是指有纸屑或其它灰尘粘在印刷图案上,产生露面。
原因:
纸板干燥且上有灰尘
油墨本身干燥功能不足 油墨配方问题 承印物上油墨层不均(印迹旁有晕圈,或 整体印刷颜色不均
印版上有污垢 带纸轮与印版原件不对齐 折带磨损或滑落 输纸导板或杆碰到印刷图案 堆纸机传送带碰到印刷图案 印刷机附件使印迹模糊
印迹模糊 原因
模切或折叠操作中,平台垫粗糙或磨损 模切压力太大