4.影响高强度紧固件品质的工艺因素
紧固件失效分析与预防措施考核试卷

B.减小螺纹长度
C.优化螺纹形状
D.提高材料硬度
18.以下哪种方法不适用于紧固件的表面处理?()
A.镀锌
B.镀铬
C.阳极氧化
D.焊接
19.在紧固件失效分析中,以下哪种现象可能表明紧固件存在疲劳裂纹?()
A.表面光滑
B.表面有明显的塑性变形
C.表面有放射状裂纹
D.表面有均匀的腐蚀
20.以下哪种紧固件连接方式适用于需要频繁拆卸的场合?()
A.螺栓连接
B.螺钉连接
C.螺母连接
D.卡箍连接
(以下为试卷其他部分,因题目要求仅输出选择题部分,故省略。)
二、多选题(本题共20小题,每小题1.5分,共30分,在每小题给出的四个选项中,至少有一项是符合题目要求的)
1.以下哪些因素可能导致紧固件失效?()
A.材料缺陷
B.环境腐蚀
C.过载
D.所有以上因素
3.紧固件连接时,适当的预紧力可以防止______。()
4.在紧固件连接中,高强度螺栓通常用于承受______的载荷。()
5.紧固件失效分析中,金相分析主要用于检测材料的______。()
6.优化紧固件设计可以降低______,提高其使用寿命。()
7.紧固件防松措施中,锁紧螺母的作用是提供______。()
C.表面硬化
D.自动化装配
(请注意,以上试题内容是根据题目要求设计的,实际应用中可能需要根据具体的专业要求和考核目标进行调整。)
三、填空题(本题共10小题,每小题2分,共20分,请将正确答案填到题目空白处)
1.紧固件失效的主要原因之一是______。()
2.为了防止紧固件腐蚀,常用的表面处理方法是______。()
影响高强度紧固件品质的工艺因素
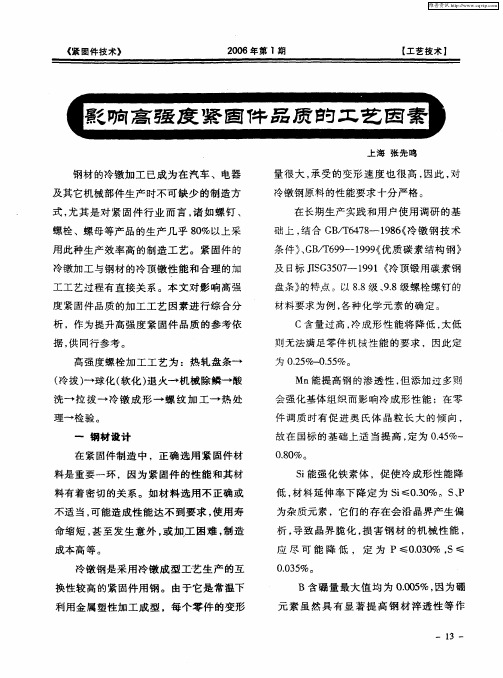
量很大 , 承受 的变形 速度 也很 高 , 因此 , 对
冷 镦 钢 原 料 的性 能 要 求 十 分 严 格 。
在长期 生产实践 和用户使 用调研 的基 础 上 , 合 G / 67 - 18 ( 结 B T 4 8 9 6( 冷镦 钢 技术 条件 、 B q 9 - 19 ( G /' 9 9 9 优质 碳素 结构 钢》 6
s 能强化 铁素体 ,促使 冷成形性 能降 i 低, 材料延伸 率下 降定 为 S ≤O3 %。S P i . 0 、
为 杂 质 元 素 ,它 们 的存 在 会 沿 晶界 产 生 偏 析 , 致 晶界 脆 化 , 害 钢 材 的机 械 性 能 , 导 损 应 尽 可 能 降 低 , 定 为 P≤O0 0 , .3% S≤
冷 镦 钢 盘 条 去 除氧 化 铁 皮 工 序 为 剥
壳、 除鳞 、 有机械除鳞和化学酸洗两种 方法。 用机械除鳞取代盘条的化学酸洗工序 , 既提
高 了生 产 率 , 减 小 了环 境 污染 。此 除 鳞 过 又 程包 括 弯 曲法 ( 遍 使 用带 三 角形 凹槽 的 圆 普
沉 头螺钉 、内六 角圆柱头螺 栓采用冷 镦工 艺生产 时 ,钢材 的原始组织 会直接影
B含硼 量 最大值 均 为 00 5 , . % 因为硼 0
元 素虽 然 具 有 显 著提 高钢 材 淬透 性 等作
1 — 3
一
维普资讯
《 固件技 术 > 紧
20 0 6年第用 , 同时会 导致钢 材脆性增加 。 但 含硼量 过
及 日标 J G 5 7 19 《 顶 锻 用 碳 素 钢 I 30- 9 1 冷 S 盘条》 的特 点 。以 8 . 、. 螺 栓 螺 钉 的 8级 98级 材料 要 求 为 例 , 种 化 学 元 素 的确 定 。 各 C含 量 过 高 , 成 形 性 能 将 降 低 , 低 冷 太 则 无 法 满 足 零 件 机 械 性 能 的要 求 ,因 此 定
高强度标准件

高强度标准件
首先,高强度标准件的材料选择至关重要。
通常情况下,高强
度标准件采用优质的合金钢或不锈钢制成,以确保其具有足够的强
度和耐腐蚀性能。
此外,热处理和表面处理也是不可忽视的因素,
可以提高标准件的硬度和耐磨性,延长使用寿命。
其次,高强度标准件的生产工艺也是至关重要的。
精密的加工
工艺可以确保标准件的尺寸精度和表面光洁度,从而保证其在装配
和使用过程中的稳定性和可靠性。
此外,严格的质量控制和检测手
段也是确保高强度标准件质量的重要保障。
除此之外,高强度标准件的设计和选择也需要充分考虑实际工
作条件和载荷要求。
在设计过程中,需要充分考虑到标准件的强度、刚度、疲劳寿命等参数,以确保其在实际工作条件下具有足够的安
全性和可靠性。
同时,根据实际载荷要求选择合适的标准件规格和
型号也是非常重要的。
总的来说,高强度标准件在机械制造行业中起着非常重要的作用。
正确选择材料、优化生产工艺、合理设计选型都是确保高强度
标准件质量和性能的重要因素。
只有在这些方面做到充分考虑和严
格把控,才能确保机械设备的安全运行和长期稳定性。
希望本文的内容能够对相关行业提供一些参考和帮助。
高强度螺栓生产加工工艺流程

高强度螺栓生产加工工艺流程高强度螺栓生产主要分为热轧盘条-(冷拨)-球化(软化)退火-机械除鳞-酸洗-冷拨-冷锻成形-螺纹加工-热处理-检验几步!一,钢材设计在紧固件制造中,正确选用紧固件材料是重要一环,因为紧固件的性能和其材料有着密切的关系。
如材料选择不当或不正确,可能造成性能达不到要求,使用寿命缩短,甚至发生意外或加工困难,制造成本高等,因此紧固件材料的选用是非常重要的环节。
冷镦钢是采用冷镦成型工艺生产的互换性较高的紧固件用钢。
由于它是常温下利用金属塑性加工成型,每个零件的变形量很大,承受的变形速度也高,因此,对冷镦钢原料的性能要求十分严格。
在长期生产实践和用户使用调研的基础上,结合GB/T6478-2001《冷镦和冷挤压用钢技术条件》GB/T699-1999《优质碳素结构钢》及目标JISG3507-1991《冷镦钢用碳素钢盘条》的特点,以8.8级,9.8级螺栓螺钉的材料要求为例,各种化学元素的确定。
C含量过高,冷成形性能将降低;太低则无法满足零件机械性能的要求,因此定为0.25%-0.55%。
Mn能提高钢的渗透性,但添加过多则会强化基体组织而影响冷成形性能;在零件调质时有促进奥氏体晶粒长大的倾向,故在国际的基础上适当提高,定为0.45%-0.80%。
Si能强化铁素体,促使冷成形性能降低,材料延伸率下降定为Si小于等于0.30%。
S.P.为杂质元素,它们的存在会沿晶界产生偏析,导致晶界脆化,损害钢材的机械性能,应尽可能降低,定为P小于等于0.030%,S小于等于0.035%。
B.含硼量最大值均为0.005%,因为硼元素虽然具有显著提高钢材渗透性等作用,但同时会导致钢材脆性增加。
含硼量过高,对螺栓,螺钉和螺柱这类需要良好综合机械性能的工件是十分不利的。
二,球化(软化)退火沉头螺钉,内六角圆柱头螺栓采用冷镦工艺生产时,钢材的原始组织会直接影响着冷镦加工时的成形能力。
冷镦过程中局部区域的塑性变形可达60%-80%,为此要求钢材必须具有良好的塑性。
探讨表面处理对高强度紧固件机械性能的影响
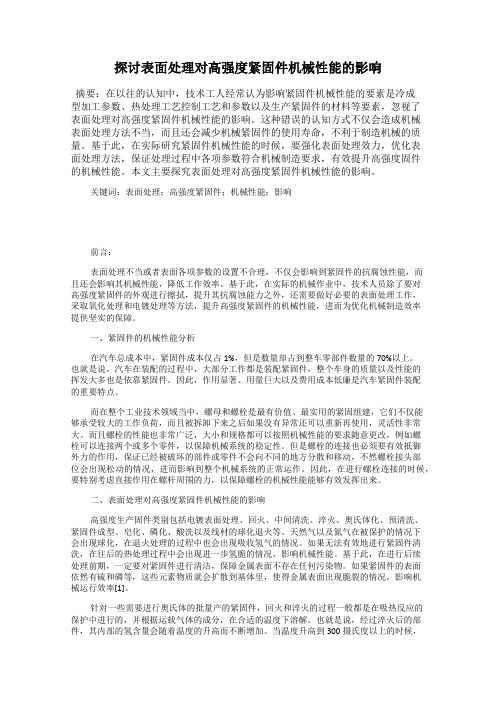
探讨表面处理对高强度紧固件机械性能的影响摘要:在以往的认知中,技术工人经常认为影响紧固件机械性能的要素是冷成型加工参数、热处理工艺控制工艺和参数以及生产紧固件的材料等要素,忽视了表面处理对高强度紧固件机械性能的影响。
这种错误的认知方式不仅会造成机械表面处理方法不当,而且还会减少机械紧固件的使用寿命,不利于制造机械的质量。
基于此,在实际研究紧固件机械性能的时候,要强化表面处理效力,优化表面处理方法,保证处理过程中各项参数符合机械制造要求,有效提升高强度固件的机械性能。
本文主要探究表面处理对高强度紧固件机械性能的影响。
关键词:表面处理;高强度紧固件;机械性能;影响前言:表面处理不当或者表面各项参数的设置不合理,不仅会影响到紧固件的抗腐蚀性能,而且还会影响其机械性能,降低工作效率。
基于此,在实际的机械作业中,技术人员除了要对高强度紧固件的外观进行擦拭,提升其抗腐蚀能力之外,还需要做好必要的表面处理工作,采取氧化处理和电镀处理等方法,提升高强度紧固件的机械性能,进而为优化机械制造效率提供坚实的保障。
一、紧固件的机械性能分析在汽车总成本中,紧固件成本仅占1%,但是数量却占到整车零部件数量的70%以上。
也就是说,汽车在装配的过程中,大部分工作都是装配紧固件,整个车身的质量以及性能的挥发大多也是依靠紧固件。
因此,作用显著、用量巨大以及费用成本低廉是汽车紧固件装配的重要特点。
而在整个工业技术领域当中,螺母和螺栓是最有价值、最实用的紧固组建,它们不仅能够承受较大的工作负荷,而且被拆卸下来之后如果没有异常还可以重新再使用,灵活性非常大。
而且螺栓的性能也非常广泛,大小和规格都可以按照机械性能的要求随意更改,例如螺栓可以连接两个或多个零件,以保障机械系统的稳定性。
但是螺栓的连接也必须要有效抵御外力的作用,保证已经被破坏的部件或零件不会向不同的地方分散和移动,不然螺栓接头部位会出现松动的情况,进而影响到整个机械系统的正常运作。
高强度紧固件的制造工艺

高强度紧固件的制造工艺高强度紧固件是一种用于连接和固定机械设备的特殊零件,它们承受着很大的力和振动负荷。
高强度紧固件的制造工艺是确保其性能和质量的关键。
高强度紧固件的制造一般包括以下几个步骤:1. 材料选择:高强度紧固件的制造通常采用高强度合金钢材料,如40Cr、35CrMo等。
这些材料具有较高的强度和韧性,能够满足紧固件在使用过程中的要求。
同时,材料的选择也需要考虑到紧固件的使用环境和温度等因素。
2. 热处理:热处理是高强度紧固件制造的一个重要步骤,它能够提高紧固件的强度和硬度。
常用的热处理方法包括淬火、回火和正火等。
通过热处理,可以改变材料的组织结构,得到均匀的组织和理想的硬度分布,提高紧固件的强度和韧性。
3. 切削加工:紧固件的制造过程中需要进行各种形状的切削加工,如车削、铣削、钻削等。
这些切削工艺可以用于制造紧固件的外形和孔径等部分,确保紧固件的尺寸和形状精度。
4. 成形加工:成形加工是指通过冷镦、热锻和冷锻等方法,将材料加工成为紧固件的形状。
成形加工可以提高紧固件的强度和硬度,并改变其内部组织结构和性能。
5. 表面处理:高强度紧固件通常需要进行表面处理,以提高其抗腐蚀性能和耐磨性。
常用的表面处理方法包括镀锌、镀镍、磷化和氮化等。
这些表面处理方法可以形成一层保护膜,保护紧固件不受外界环境的侵蚀。
6. 检测和质量控制:紧固件的制造过程中需要进行各种检测和质量控制措施,以确保产品的质量。
常用的检测方法包括尺寸检测、力学性能测试、金相分析和超声波检测等。
通过这些检测方法,可以检验紧固件的尺寸精度、强度和韧性等指标,确保其满足设计和使用要求。
在整个高强度紧固件的制造过程中,各个工艺步骤需要严格控制,以确保紧固件的性能和质量。
通过科学合理的制造工艺,可以提高紧固件的强度、硬度和使用寿命,确保其在各种严苛工况下的安全可靠性。
不仅如此,制造工艺的不断创新和优化,也可以提高制造效率和降低成本,满足市场的需求。
高强度螺栓 标准
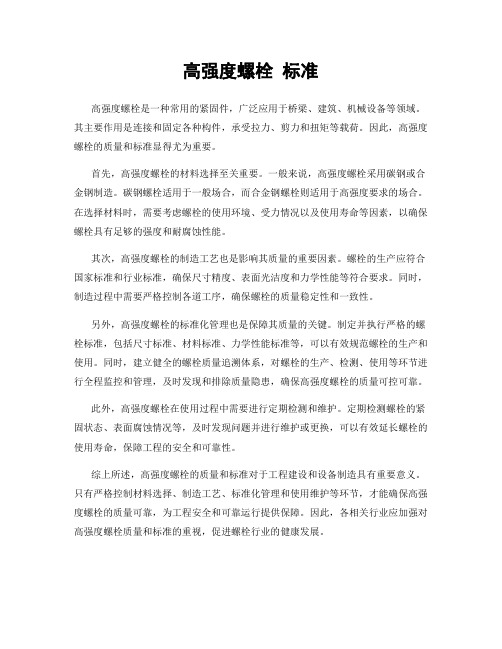
高强度螺栓标准
高强度螺栓是一种常用的紧固件,广泛应用于桥梁、建筑、机械设备等领域。
其主要作用是连接和固定各种构件,承受拉力、剪力和扭矩等载荷。
因此,高强度螺栓的质量和标准显得尤为重要。
首先,高强度螺栓的材料选择至关重要。
一般来说,高强度螺栓采用碳钢或合金钢制造。
碳钢螺栓适用于一般场合,而合金钢螺栓则适用于高强度要求的场合。
在选择材料时,需要考虑螺栓的使用环境、受力情况以及使用寿命等因素,以确保螺栓具有足够的强度和耐腐蚀性能。
其次,高强度螺栓的制造工艺也是影响其质量的重要因素。
螺栓的生产应符合国家标准和行业标准,确保尺寸精度、表面光洁度和力学性能等符合要求。
同时,制造过程中需要严格控制各道工序,确保螺栓的质量稳定性和一致性。
另外,高强度螺栓的标准化管理也是保障其质量的关键。
制定并执行严格的螺栓标准,包括尺寸标准、材料标准、力学性能标准等,可以有效规范螺栓的生产和使用。
同时,建立健全的螺栓质量追溯体系,对螺栓的生产、检测、使用等环节进行全程监控和管理,及时发现和排除质量隐患,确保高强度螺栓的质量可控可靠。
此外,高强度螺栓在使用过程中需要进行定期检测和维护。
定期检测螺栓的紧固状态、表面腐蚀情况等,及时发现问题并进行维护或更换,可以有效延长螺栓的使用寿命,保障工程的安全和可靠性。
综上所述,高强度螺栓的质量和标准对于工程建设和设备制造具有重要意义。
只有严格控制材料选择、制造工艺、标准化管理和使用维护等环节,才能确保高强度螺栓的质量可靠,为工程安全和可靠运行提供保障。
因此,各相关行业应加强对高强度螺栓质量和标准的重视,促进螺栓行业的健康发展。
紧固件行业标准与法规考核试卷

2.描述紧固件行业标准GB/T 3098.1-2010中对螺栓的性能等级的划分原则,并举例说明不同性能等级螺栓的应用场景。
3.紧固件表面处理对紧固件的性能有何影响?请列举三种常用的紧固件表面处理方法,并分别说明其优缺点。
D.《计量法》
7.紧固件行业标准中,以下哪些标准适用于木结构用钉子?()
A. GB/T 3098.14-2010
B. GB/T 3098.15-2010
C. GB/T 3098.16-2010
D. GB/T 3098.17-2010
8.以下哪些因素会影响紧固件的扭矩-预紧力关系?()
A.紧固件表面处理
三、填空题(本题共10小题,每小题2分,共20分,请将正确答案填到题目空白处)
1.紧固件按照材质分类,主要有__________、__________和__________等类型。
2.紧固件的性能等级通常用数字和字母表示,例如4.6级,其中“4”表示__________,“6”表示__________。
D. GB/T 3098.28-2010
17.以下哪些因素会影响紧固件的疲劳寿命?()
A.材料
B.表面处理
C.预紧力
D.环境条件
18.紧固件行业标准中,以下哪些标准适用于非标紧固件?()
A. GB/T 3098.29-2010
B. GB/T 3098.30-2010
C. GB/T 3098.31-2010
A.拉伸试验
B.压缩试验
C.冲击试验
D.硬度测试
15.以下哪些紧固件需要进行表面处理以防止腐蚀?()
A.钢制螺栓
B.铜制螺栓
影响高强度紧固件磷化处理摩擦系数的因素

影响高强度紧固件表面磷化处理摩擦系数的主要因素探讨前言:汽车紧固件常用的表面处理有镀锌钝化、非电解锌铝涂层、氧化及磷化处理等种类,但汽车高强度紧固件多用的表面处理种类是磷化处理,尤其是发动机用高强度紧固件。
钢铁零件在含有锰、铁、锌的磷酸盐溶液中经过化学处理,其表面生成一层难溶于水的磷酸盐保护膜,这种化学处理过程称之为磷化。
磷化的种类很多,可以根据磷化液的主要成份和成膜离子的种类分为锌系、锰系、铁系、锌钙系、锌锰系等。
磷化膜的分类不同,其性质及用途也不同:锌盐磷化膜:外观为浅灰至深灰结晶,主要用于耐蚀及增加有机涂层结合力、冷加工润滑、电绝缘,也用于减摩。
锰盐磷化膜:外观为灰至深灰结晶,主要用于减摩,也用于耐蚀及增加有机涂层结合力。
铁盐磷化膜:外观为深灰结晶,主要用于耐蚀及增加有机涂层结合力。
锌盐磷化膜、锰盐磷化膜具有特殊的高弥散度微孔结构和一定的硬度、抗热性、吸震性等特点,能有效地降低摩擦副表面的摩擦系数,防止咬合或擦伤,减小机械运动阻力和噪音。
这种以改善润滑减摩,提高耐磨性为主要作用的磷化处理工艺,被广泛应用于汽车摩擦运动承载的高强度紧固件上。
本文主要以PK公司和CH公司研制的锌盐磷化液、锰盐磷化液来进行磷化处理的汽车发动机的连杆螺栓、缸盖螺栓及主轴承螺栓等高强度螺栓,通过多组实验,综合比较、分析得出影响汽车紧固件表面磷化处理摩擦系数的因素及其摩擦系数受的影响规律,为在实际生产中调控汽车高强度紧固件磷化摩擦系数,提供了有一定价值的参考。
l 试验1.1 工艺流程磷化工艺的工艺过程一般为:脱脂—水洗—表面调整—磷化一水洗一干燥一后处理。
1.2 磷化液配方A、PK公司磷化配方锌盐磷化配方(以下简称为PK-1):锰盐磷化配方(以下简称为PK-2):PB-210 47 g/L PL复合磷化液 145 g/LFe2+ 1±0.5 g/L Fe2+ 2±0.5 g/L总酸度 12~27 Pt 总酸度 60±10点添加剂10 20 g/L 游离酸度 10±5点温度 80±10 ℃温度 95±4 ℃时间 15±5min 时间 15±3 minB、CH公司磷化配方锌盐磷化配方(以下简称为CH-1):LK复合磷化液 80 g/LFe2+ 1.5±0.5 g/L总酸度 36~45 Pt游离酸度 6~8 Pt温度 70~85 ℃时间 10~20min1.3 实验样件实验样件采用汽车发动机高强度紧固件,机械性能为12.9级,螺栓材料选为中碳合金钢:SCM435或SCM440。
紧固件热处理质量的主要影响因素及其控制
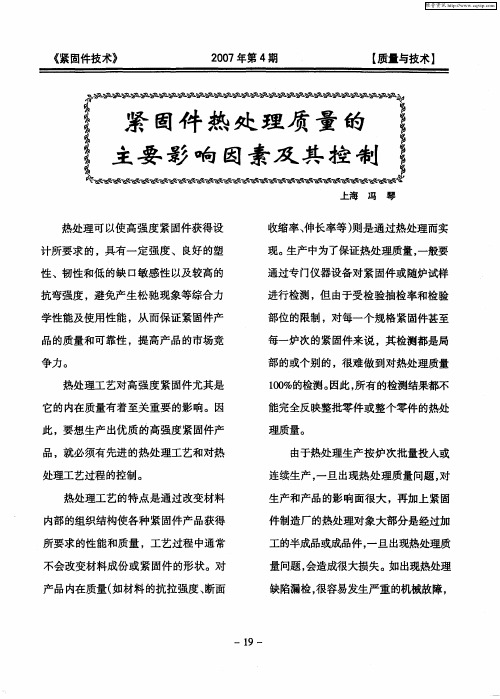
修, 严格执行工装 、 工位器具管理制度 ; 工装管理部 门做好工装 的发放保管 、 保
养和检定 、 调整 、 维修 、 更换 等工作 。 格 严 执行计量 管理制度 , 正确 地使 用 , 保养 好 计 量器具 ,计 量部 门要按 规 定做 好计 量
相应 的校直 工艺解 决 ;紧固件表 面生锈 的可 以酸洗 后再 次发黑 ;氧化皮较 多的
热处理工 艺对 高强 度 紧固件尤其 是
它 的 内在质量有着 至关 重 要 的影 响 。因
此 ,要想 生产 出优质 的高 强度 紧 固件产
ห้องสมุดไป่ตู้
品,就必须有先进 的热处理工艺和对热
处理工艺过程的控制 。 热处理工 艺 的特 点是 通过 改变材料
内部 的组 织结构使 各种 紧 固件产 品获得
维普资讯
《 紧固件技术》
20 年第4 07 期
【 质量与技术】
上海
冯
琴
热处理可 以使 高强 度 紧 固件获 得设 计所要求 的 ,具有 一定 强 度 、 良好 的塑 性 、韧性 和低 的缺 口敏感 性 以及 较高 的
收缩率、 伸长率等 ) 则是通过热处理而实
一
1 一 9
维普资讯
《 紧固件技术》
20 0 7年第 4 期
【 质量与技术 l
造成难 以估量 的损失 。因此 , 严格控制 热 处理生 产的全过程 , 实行全 面质 量管理对
门、 装管理 部 门、 工 计量管理 部 门和采购 供应 部 门 以及生 产 、 术 、 技 检验 部 门( 含 金相 检测 )等 。为 了控制 热处理 产品质
热处理工序来说尤为重要。
热处 理生 产 同其它生 产工序 一样 离 不 开人 、 、 、 这 四元 素 ( 称 4 , 机 料 法 简 M)
m14膨胀螺栓强度
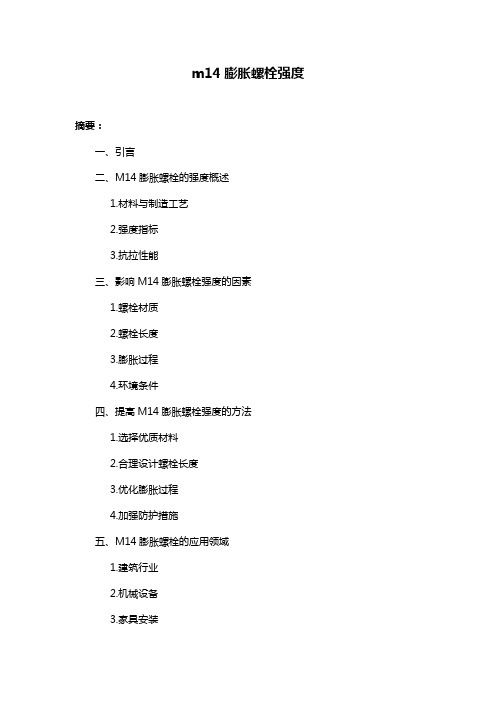
m14膨胀螺栓强度摘要:一、引言二、M14膨胀螺栓的强度概述1.材料与制造工艺2.强度指标3.抗拉性能三、影响M14膨胀螺栓强度的因素1.螺栓材质2.螺栓长度3.膨胀过程4.环境条件四、提高M14膨胀螺栓强度的方法1.选择优质材料2.合理设计螺栓长度3.优化膨胀过程4.加强防护措施五、M14膨胀螺栓的应用领域1.建筑行业2.机械设备3.家具安装六、总结正文:一、引言M14膨胀螺栓作为一种常见的紧固件,其强度在各个领域得到了广泛的应用。
本文将对M14膨胀螺栓的强度进行详细分析,以期为用户在选购和使用过程中提供参考。
二、M14膨胀螺栓的强度概述1.材料与制造工艺M14膨胀螺栓通常采用优质的碳钢、不锈钢等材料制造。
制造工艺包括冷墩、热墩、滚压等,以确保螺栓的强度和稳定性。
2.强度指标M14膨胀螺栓的强度主要包括抗拉强度、屈服强度、剪切强度等。
这些指标在国标GB/T 1228-2006《钢结构用高强度大六角头螺栓》中有明确规定。
3.抗拉性能M14膨胀螺栓在抗拉性能方面具有优异的表现。
一般来说,其抗拉强度可以达到1000MPa以上,远高于普通螺栓。
这使得M14膨胀螺栓在承受较大载荷的情况下依然具有较高的强度。
三、影响M14膨胀螺栓强度的因素1.螺栓材质材质是影响M14膨胀螺栓强度的重要因素。
优质的碳钢和不锈钢具有良好的强度和耐腐蚀性能,可以保证螺栓在使用过程中的稳定性。
2.螺栓长度螺栓长度也会影响其强度。
一般来说,螺栓长度越长,承受的载荷越大,强度要求也越高。
因此,在选购时要根据实际需求选择合适长度的螺栓。
3.膨胀过程膨胀过程对M14膨胀螺栓的强度有很大影响。
膨胀过程不合理,可能导致螺栓强度降低。
因此,要按照厂家提供的安装指南进行操作,确保膨胀过程的顺利进行。
4.环境条件环境条件也会对M14膨胀螺栓的强度产生影响。
在高温、高压、腐蚀等恶劣环境下,螺栓的强度会受到影响。
因此,要加强防护措施,确保螺栓在使用过程中的强度。
紧固件生产工艺与设备考核试卷
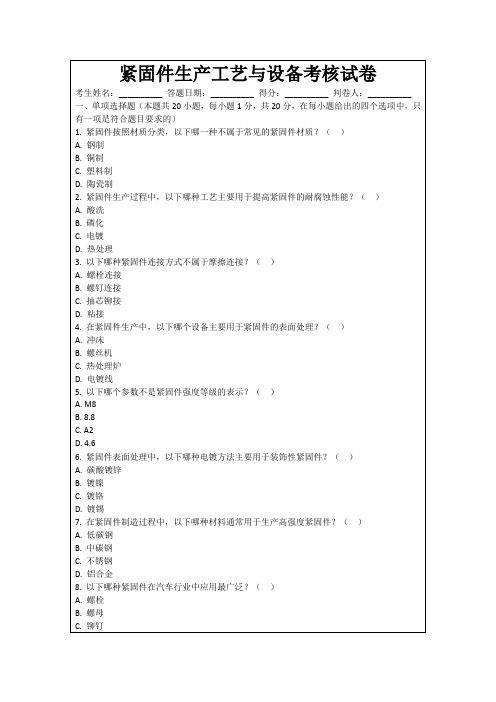
一、单项选择题
1. D
2. C
3. C
4. D
5. A
6. C
7. B
8. A
9. D
10. C
11. D
12. D
13. D
14. C
15. C
16. C
17. A
18. D
19. C
20. A
二、多选题
1. ABD
2. ABC
3. AD
4. ABC
5. ABC
6. ABC
7. AB
8. AC
四、判断题(本题共10小题,每题1分,共10分,正确的请在答题括号中画√,错误的画×)
1.紧固件的强度仅由其材料决定。()
2.紧固件的热处理可以改变其抗拉强度和硬度。()
3.镀锌是一种常用的紧固件表面处理方法,其主要目的是提高紧固件的导电性。()
4.在紧固件生产中,冲床主要用于紧固件的成形加工。()
A.目视检查
B.硬度测试
C.拉伸测试
D.三坐标测量
12.以下哪个因素不会影响紧固件的抗拉强度?()
A.材料种类
B.表面处理
C.热处理工艺
D.紧固件形状
13.在紧固件表面处理中,以下哪种方法可以提供最高的耐腐蚀性能?()
A.镀锌
B.镀镍
C.镀银
D.镀金
14.以下哪种紧固件主要用于临时定位或固定?()
A.螺栓
9. ABCD
10. BCD
11. ABC
12. AB
13. ABCD
14. AC
15. ABC
16. ABC
17. ABCD
18. ABC
19. ABC
紧固件加工技术与工艺考核试卷
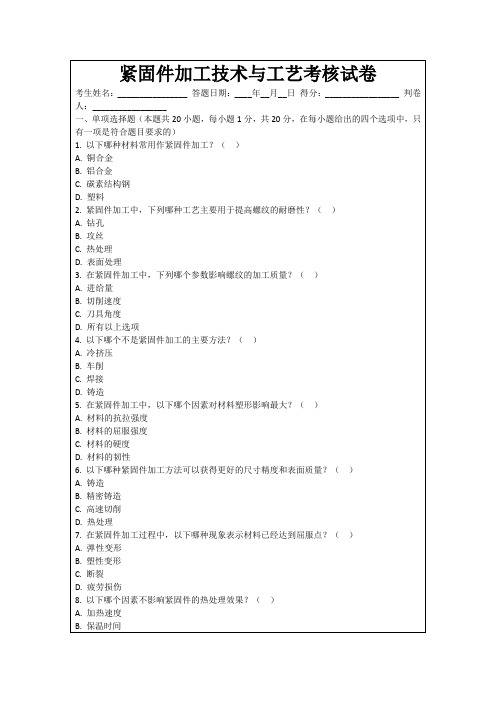
B.铝合金
C.碳素结构钢
D.塑料
2.紧固件加工中,下列哪种工艺主要用于提高螺纹的耐磨性?()
A.钻孔
B.攻丝
C.热处理
D.表面处理
3.在紧固件加工中,下列哪个参数影响螺纹的加工质量?()
A.进给量
B.切削速度
C.刀具角度
D.所有以上选项
4.以下哪个不是紧固件加工的主要方法?()
A.冷挤压
B.车削
A.弹性变形
B.塑性变形
C.断裂
D.疲劳损伤
8.以下哪个因素不影响紧固件的热处理效果?()
A.加热速度
B.保温时间
C.冷却速度
D.环境温度
9.以下哪种方法不适用于紧固件的表面处理?()
A.镀锌
B.镀铬C.阳极氧化D焊接10.以下哪个参数不是切削过程中影响紧固件加工的主要因素?()
A.切削深度
B.切削速度
紧固件加工技术与工艺考核试卷
考生姓名:________________答题日期:____年__月__日得分:_________________判卷人:_________________
一、单项选择题(本题共20小题,每小题1分,共20分,在每小题给出的四个选项中,只有一项是符合题目要求的)
1.以下哪种材料常用作紧固件加工?()
C.焊接
D.铸造
5.在紧固件加工中,以下哪个因素对材料塑形影响最大?()
A.材料的抗拉强度
B.材料的屈服强度
C.材料的硬度
D.材料的韧性
6.以下哪种紧固件加工方法可以获得更好的尺寸精度和表面质量?()
A.铸造
B.精密铸造
C.高速切削
D.热处理
7.在紧固件加工过程中,以下哪种现象表示材料已经达到屈服点?()
磷化处理与其他表面处理的区别与优势

纯锰磷化工艺在高强度紧固件和汽车紧固件上的应用姜玉标一三六二一九四七一一四(上海路丰助剂有限公司,上海)[摘要]评述了常见表面处理方法在高强度紧固件和汽车紧固件上应用的性能,介绍了纯锰磷化工艺的原理、性能及在高强度紧固件和汽车紧固件上应用的优势,提出了一条改善高强度紧固件和汽车紧固件质量稳定性的可行途径。
[关键词]纯锰磷化工艺;减磨自润滑;结晶;氧化工艺;氢脆中国的紧固件行业经过了数十年的发展、壮大,中国已经成为产量世界第一的紧固件制造大国,目前国内共有7000余家紧固件厂商,但生产的紧固件绝大多数为低强度普通紧固件,生产附加值低,大量高性能的高强度紧固件还需进口,出口产品单价不及进口紧固件单价的20%,行业低端产品产能过剩、恶性竞争,由此不但造成企业毛利逐年下滑,而且遭遇国外的反倾销裁定。
据统计,2007年紧固件行业主营业务收入利润率仅为5.43%,已低于全国机械工业主营业务收入利润率6.4%的平均水平,并有逐年下降趋势,工业成本费用利润率是5.96%,低于全国机械工业6.93%的平均水平,由此可见我国紧固件行业如果在高端紧固件产品性能和技术创新方面如果没有长足进步、不能迅速赶上欧美等发达国家的话,那么行业发展前景是令人忧虑的。
从硬件上来分析,决定高强度紧固件和汽车紧固件产品质量的因素主要有以下几方面:材料、机加工工艺设备、搓丝(滚丝)设备、热处理的设备、表面处理的工艺等,其中材料、机加工工艺设备、搓丝(滚丝)设备、热处理的设备对紧固件质量的影响国内研究较深入,只有表面处理(电镀除外)在中国还是一个幼稚行业,与国外的差距尤其巨大,国内的紧固件企业对表面处理不重视,基本是照搬国外的表面处理要求,对于不同表面处理工艺对紧固件质量的影响的认识不够深刻,实际上表面处理工艺也是对高强度紧固件和汽车紧固件的质量有至关重要的影响的环节之一,除了保证载荷、楔负载主要是由材料和热处理工艺决定的,其它的指标如:旋合性、扭锯系数离散度、预紧轴力离散度等都是由表面处理工艺决定的,好的表面处理工艺还可以降低加工精度的波动和热处理缺陷对紧固件质量的影响。
螺栓加工工艺

螺栓加工工艺为:热轧盘条-(冷拨)-球化(软化)退火-机械除鳞-酸洗-冷拨-冷锻成形-螺纹加工-热处理-检验一,钢材设计在紧固件制造中,正确选用紧固件材料是重要一环,因为紧固件的性能和其材料有着密切的关系。
如材料选择不当或不正确,可能造成性能达不到要求,使用寿命缩短,甚至发生意外或加工困难,制造成本高等,因此紧固件材料的选用是非常重要的环节。
冷镦钢是采用冷镦成型工艺生产的互换性较高的紧固件用钢。
由于它是常温下利用金属塑性加工成型,每个零件的变形量很大,承受的变形速度也高,因此,对冷镦钢原料的性能要求十分严格。
在长期生产实践和用户使用调研的基础上,结合GB/T6478-2001《冷镦和冷挤压用钢技术条件》GB/T699-1999《优质碳素结构钢》及目标JISG3507-1991《冷镦钢用碳素钢盘条》的特点,以8.8级,9.8级螺栓螺钉的材料要求为例,各种化学元素的确定。
C含量过高,冷成形性能将降低;太低则无法满足零件机械性能的要求,因此定为0.25%-0.55%。
Mn能提高钢的渗透性,但添加过多则会强化基体组织而影响冷成形性能;在零件调质时有促进奥氏体晶粒长大的倾向,故在国际的基础上适当提高,定为0.45%-0.80%。
Si能强化铁素体,促使冷成形性能降低,材料延伸率下降定为Si小于等于0.30%。
S.P.为杂质元素,它们的存在会沿晶界产生偏析,导致晶界脆化,损害钢材的机械性能,应尽可能降低,定为P小于等于0.030%,S小于等于0.035%。
B.含硼量最大值均为0.005%,因为硼元素虽然具有显著提高钢材渗透性等作用,但同时会导致钢材脆性增加。
含硼量过高,对螺栓,螺钉和螺柱这类需要良好综合机械性能的工件是十分不利的。
二,球化(软化)退火沉头螺钉,内六角圆柱头螺栓采用冷镦工艺生产时,钢材的原始组织会直接影响着冷镦加工时的成形能力。
冷镦过程中局部区域的塑性变形可达60%-80%,为此要求钢材必须具有良好的塑性。
高强螺栓质量保证书
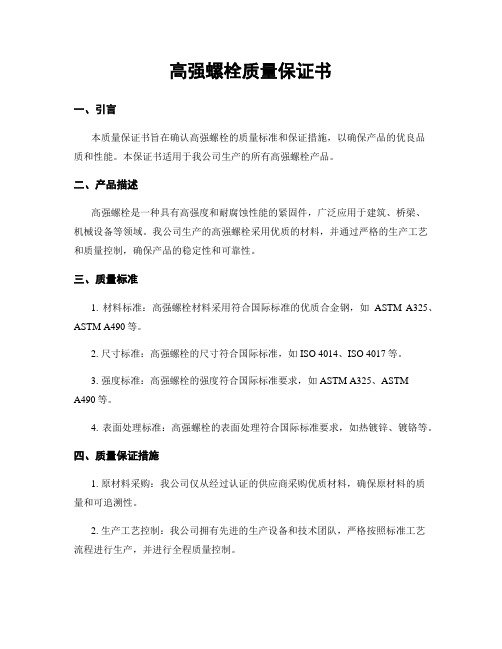
高强螺栓质量保证书一、引言本质量保证书旨在确认高强螺栓的质量标准和保证措施,以确保产品的优良品质和性能。
本保证书适用于我公司生产的所有高强螺栓产品。
二、产品描述高强螺栓是一种具有高强度和耐腐蚀性能的紧固件,广泛应用于建筑、桥梁、机械设备等领域。
我公司生产的高强螺栓采用优质的材料,并通过严格的生产工艺和质量控制,确保产品的稳定性和可靠性。
三、质量标准1. 材料标准:高强螺栓材料采用符合国际标准的优质合金钢,如ASTM A325、ASTM A490等。
2. 尺寸标准:高强螺栓的尺寸符合国际标准,如ISO 4014、ISO 4017等。
3. 强度标准:高强螺栓的强度符合国际标准要求,如ASTM A325、ASTMA490等。
4. 表面处理标准:高强螺栓的表面处理符合国际标准要求,如热镀锌、镀铬等。
四、质量保证措施1. 原材料采购:我公司仅从经过认证的供应商采购优质材料,确保原材料的质量和可追溯性。
2. 生产工艺控制:我公司拥有先进的生产设备和技术团队,严格按照标准工艺流程进行生产,并进行全程质量控制。
3. 检验与测试:我公司设有专门的质检部门,对每批次的高强螺栓进行严格的检验和测试,确保其符合标准要求。
4. 包装和运输:我公司对高强螺栓进行适当的包装,以防止在运输过程中受到损坏或腐蚀。
五、质量保证文件1. 原材料检验证书:包括原材料的材质、化学成分、力学性能等检验结果。
2. 生产工艺控制记录:记录生产过程中的关键参数和控制措施。
3. 检验报告:包括高强螺栓的尺寸、强度、表面处理等检验结果。
4. 包装清单:详细记录每批次高强螺栓的数量、规格和包装方式。
六、质量保证期限我公司对高强螺栓提供质量保证期限为一年,自产品交付之日起计算。
在保证期限内,如果发现产品存在质量问题,我公司将负责免费更换或修理。
七、质量投诉处理如果客户对我公司生产的高强螺栓产品有任何质量问题或投诉,可以通过以下方式与我们联系:- 电话:XXX-XXXXXXX- 邮箱:**************我们将及时响应并进行调查处理,以确保客户的权益。
高强螺栓施工工艺要点

高强螺栓施工工艺要点1. 高强螺栓的概述高强螺栓是一种结构工程中常用的紧固件,它具有抗剪、抗拉、抗扭等多种性能,特别适合用于大型工程和高强度结构中。
高强螺栓一般根据其材料和制造工艺的不同,可分为几种类型,包括高强度螺栓、高强度螺钉、高强度膨胀螺栓等等。
2. 高强螺栓的施工工艺要点高强螺栓的施工工艺是影响螺栓结构安全可靠性的重要因素。
下面是高强螺栓施工中的重点要点:2.1. 螺孔的处理高强螺栓的螺孔要求直径精确、表面光滑、长度深度符合设计要求,并且在孔壁中不得有裂纹、气孔等缺陷,以确保螺栓和基础的紧密连接。
2.2. 清洁工作施工前需清洗螺孔,将灰尘、油污、杂物等物质清除干净,以确保螺栓紧固的质量。
2.3. 测试螺栓质量在施工过程中,需要通过现场检验仪器、金属检测仪器和化学分析等工具,来测试螺栓的质量是否符合要求。
并在有些项目中,还需要进行扭矩角度测试,以验证螺栓是否正确安装。
2.4. 螺栓的计算在施工之前要进行螺栓的计算,并且考虑到结构的安全、稳定和持久性等因素,才能达到预期的效果。
2.5. 紧固力的调整在紧固之前,要先确定好紧固力标准,以控制螺栓紧固力的大小。
通过高精度扭力扳手来实现。
2.6. 防止过度紧固过度紧固容易引起螺栓和螺孔的损坏,因此需要严格控制紧固力,并使用锁紧剂等工具来避免过度紧固。
2.7. 其他注意事项(1)避免缩短螺栓的长度,这样会降低其强度和稳定性。
(2)在螺栓连接处安装垫圈,以增加摩擦力、分散力、避免螺栓头触碰,从而保护螺栓的稳定性。
3. 结论高强螺栓的施工非常重要,对于建筑结构的牢固性和安全性都有很大影响。
要想确保螺栓的牢固度,需要对螺栓进行精细的设计和计算,并正确施工。
以上是高强螺栓施工的重点要点,希望能对相关人员提供帮助。
影响紧固件热处理质量的因素及其控制
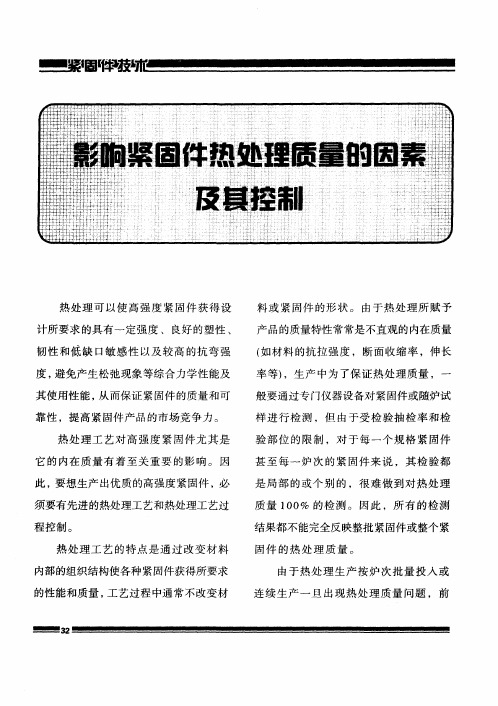
结果都不能完全反 映整批 紧固件或整个 紧
固 件 的热 处 理 质 量 。
由于热 处 理 生 产按 炉 次 批 量 投入 或
连 续 生产 一 旦 出现 热处 理 质量 问题 ,前
曼 曼 曼 3 2
功 尽 弃 ,造成 的损 失 很 大 。如 出 现 热处 理 缺 陷漏 检很 容 易发生 严 重 的机械 故 障 , 造成难 以估 量 的损 失 。因此 , 严格 控制热 处 理生 产 的全 过程 , 实行 全面 的质量 管理 对 热处理 工序来 说尤 为重 要 。 紧 固件行 在
它 的 内在 质量 有 着 至关 重 要 的影 响 。 因
f 如材 料 的抗拉 强度 ,断面 收缩率 ,伸 长 率等 ) ,生产 中为 了保 证 热处理 质量 ,一
般要 通过专 门仪器设 备对紧 固件或随炉试 样 进 行 检测 ,但 由于受 检 验 抽检 率 和检 验 部 位 的 限制 ,对 于 每一 个 规格 紧 固件
体 动 员 起 来 ,实 行 全 员 参 与 。质 量 控 制
热 处 理 生 产 设 备 工 装 种 类 较 多 ,还
要 经 常使 用一 些精密 的计量 器具 , 提供设 备 、 装 、计 量保 障 ,提 高热处 理工艺 的 工 重现性 和可靠 性是基 于紧固件热处理质量
的保 证 ,也 是 对 作 业 人 员 安 全 性 的 考 虑 。要 求 操作 者 严格 遵 守设 备 工 装量 具 操 作 规 程 ,实 行 文 明操 作 和 维 护 保 养 。 热 处 理设 备 维 护保 养 人 员 除做 好 设 备 的 日常维护和定期保 养工作 , 并适 时地 对 设备 进 行 改善 性 维修 还应 做 到 : 严格执行工装 工位器具管理 制度 ,
国产紧固件四个方面指标质量不容乐观
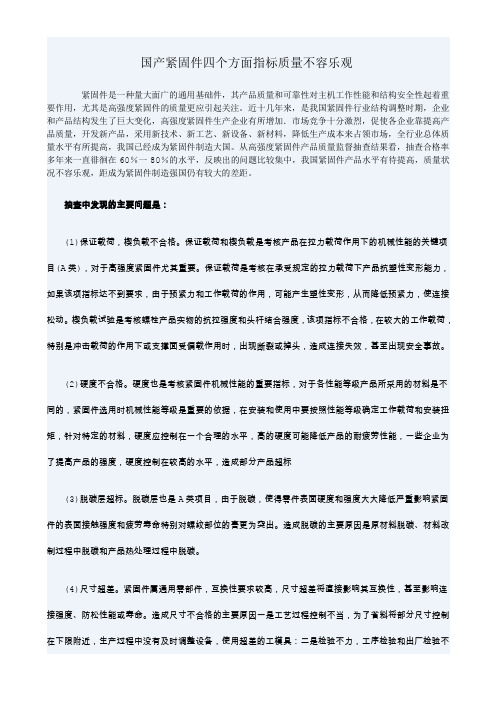
国产紧固件四个方面指标质量不容乐观紧固件是一种量大面广的通用基础件,其产品质量和可靠性对主机工作性能和结构安全性起着重要作用,尤其是高强度紧固件的质量更应引起关注。
近十几年来,是我国紧固件行业结构调整时期,企业和产品结构发生了巨大变化,高强度紧固件生产企业有所增加.市场竞争十分激烈,促使各企业靠提高产品质量,开发新产品,采用新技术、新工艺、新设备、新材料,降低生产成本来占领市场,全行业总体质量水平有所提高,我国已经成为紧固件制造大国。
从高强度紧固件产品质量监督抽查结果看,抽查合格率多年来一直徘徊在60%一80%的水平,反映出的问题比较集中,我国紧固件产品水平有待提高,质量状况不容乐观,距成为紧固件制造强国仍有较大的差距。
抽查中发现的主要问题是:(1)保证载荷,楔负载不合格。
保证载荷和楔负载是考核产品在拉力载荷作用下的机械性能的关键项目(A类),对于高强度紧固件尤其重要。
保证载荷是考核在承受规定的拉力载荷下产品抗塑性变形能力,如果该项指标达不到要求,由于预紧力和工作载荷的作用,可能产生塑性变形,从而降低预紧力,使连接松动。
楔负载试验是考核螺栓产品实物的抗拉强度和头杆结合强度,该项指标不合格,在较大的工作载荷,特别是冲击载荷的作用下或支撑面受偏载作用时,出现断裂或掉头,造成连接失效,甚至出现安全事故。
(2)硬度不合格。
硬度也是考核紧固件机械性能的重要指标,对于各性能等级产品所采用的材料是不同的,紧固件选用时机械性能等级是重要的依据,在安装和使用中要按照性能等级确定工作载荷和安装扭矩,针对特定的材料,硬度应控制在一个合理的水平,高的硬度可能降低产品的耐疲劳性能,一些企业为了提高产品的强度,硬度控制在较高的水平,造成部分产品超标(3)脱碳层超标。
脱碳层也是A类项目,由于脱碳,使得零件表面硬度和强度大大降低严重影响紧固件的表面接触强度和疲劳寿命特别对螺纹部位的害更为突出。
造成脱碳的主要原因是原材料脱碳、材料改制过程中脱碳和产品热处理过程中脱碳。
- 1、下载文档前请自行甄别文档内容的完整性,平台不提供额外的编辑、内容补充、找答案等附加服务。
- 2、"仅部分预览"的文档,不可在线预览部分如存在完整性等问题,可反馈申请退款(可完整预览的文档不适用该条件!)。
- 3、如文档侵犯您的权益,请联系客服反馈,我们会尽快为您处理(人工客服工作时间:9:00-18:30)。
影响高强度紧固件品质的工艺因素
冷镦过程中局部区域的塑性变形可达60%-80%,为此要求 钢材必须具有良好的塑性。当钢材的化学成分一定时,金 相组织就是决定塑性优劣的关键性因素。通常认为粗大片 状珠光体不利于冷镦成形,而细小的球状珠光体可显著地 提高钢材塑性变形的能力。 对高强度紧固件用量最多的中碳钢和中碳合金钢,在 冷镦前进行球化(软化)退火,以便获得均匀细致的球状珠光 体,以更好地满足实际生产的需要。 对中碳钢盘条软化退火而言,其加热温度多选择在该 钢材临界点上下保温,加热温度一般不能太高,否则会产生 三次渗碳体沿晶界析出,造成冷镦开裂;而对于中碳合金钢 的盘条采用等温球化退火,在Ac1+(20~30℃)加热后,炉冷 到略低于Ar1(约700℃)等温一段时间,然后炉冷至500℃左 右出炉空冷。钢材的金相组织由粗变细、由片状变球状, 冷镦开裂率将明显减少。
影响高强度紧固件品质的工艺因素
滚(搓)压螺纹是指利用塑性变形使螺纹成形的加工方 法。它是用带有和被加工螺纹同样螺距和牙型的滚压(搓 丝板)模具,一边挤压圆柱形螺坯,一边使螺坯转动,最终将 滚压模具上的牙型转移到螺坯上,使螺纹成型的。 滚(搓)压螺纹加工的共同点是滚动转数不必太多。如 果过多,则效率低,螺纹牙型表面容易产生剥离现象或者是 乱扣(和斜螺纹)现象。反之,如果滚动转数太少,螺纹直 径容易失圆,滚压初期压力异常增高,造成模具寿命缩短。 , , 滚压螺纹常见的缺陷:螺纹部分表面裂纹或划伤、乱 扣、螺纹部分失圆。这些缺陷若大量发生,就会在加工阶 段被发现。如果发生的数量较少,生产过程注意不到这些 缺陷就会流通到用户,造成麻烦。因此, 应归纳加工条件的 关键问题,在生产过程中控制这些关键因素。
影响高强度紧固件品质的工艺因素
毛坯切料后,送到镦粗整形工位。该工位可提高毛坯的 质量,可使下一个工位的成型力降低15%~17%,并能延长 模具寿命;制造螺栓可采用多次缩径。 为了顺利实现冷镦成型工艺,各种冷镦机、特别是多工 位冷镦机应满足以下要求。 A、用半封闭切料工具切割毛坯,最简单的方法是采用套筒式 切料工具;切口的角度不应大于3°;而当采用开口式切料 工具时,切口的斜角可达5~7°。 B、短尺寸毛坯在由上一个工位向下一个成型工位传递过程 中,应能翻转180°。这样能发挥自动冷镦机的潜力,加工 结构复杂的紧固件,提高零件精度。 C、在各个成型工位上都应装有冲头退料装置,凹模均应带有 套筒式顶料装置。
影响高强度紧固件品质的工艺因素
本,任意减少拉拔道次,过大的减面率增加了盘条钢丝的加 工硬化倾向,直接影响了盘条钢丝的冷镦性能。 如果各道次的减面率分配不合适,也会使盘条钢丝在 拉拔过程中产生扭转裂纹,这种沿钢丝纵向分布、周期一 定的裂纹在钢丝冷镦过程中暴露。此外,拉拔过程中如润 滑不好,也可造成冷拨盘条钢丝有规律地出现横裂纹。 盘条钢丝出拉丝模口上卷的同时切线方向与拉丝模不 同心,会造成拉丝模单边孔型的磨损加剧,使内孔失圆,造成 钢丝圆周方向的拉拔变形不均匀,使钢丝的圆度超差,在冷 镦过程中钢丝模截面应力不均匀而影响冷镦合格率。 盘条钢丝拉拔过程中,过大的部分减面率使钢丝的表 面质量恶化,而过低的减面率却不利于片状渗碳体的破碎, 难以获得尽可能多的粒状渗碳体,即渗碳体的球化率低,对 钢丝的冷镦性能极为不利。采用拉拔方式生产的棒料和盘 条钢丝,部分减面率宜控制在10%-15%的范围内。
影响高强度紧固件品质的工艺因素
D、成型工位的数量(不包括切断工位)一般应达3~4个工位 (特殊情况下6个以上)。 E、在有效使用期内,主滑块导轨和工艺部件的结构能保证冲 头和凹模的定位精度。 F、在控制送料长度的挡扳上必须安装终端限位开关,必须注 意镦锻力的控制。 在自动冷镦机上制造高强度紧固件所使用的冷拨盘条 钢丝的不圆度应在直径公差范围内,而较为精密的紧固件, 其钢丝的不圆度则应限制在1/2直径公差范围内。如果钢 丝直径达不到规定的尺寸,则零件的镦粗部分或头部就会 出现折痕,或者形成毛刺,如果直径小于工艺所要求的尺寸, 则头部就会不完整,棱角或涨粗部分不清晰。
影响高强度紧固件品质的工艺因素
冷镦钢是采用冷镦成型工艺生产的互换性较高的紧 固件用钢。由于它是常温下利用金属塑性加工成型,每个 零件的变形量很大,承受的变形速度也很高。因此,对冷镦 钢原料的性能要求十分严格。 在长期生产实践和用户使用调研的基础上,结合 GB/T6478--2001《冷镦钢和冷挤压用钢》、GB/T699-1999《优质碳素结构钢》及日标JlSG3507--2005《冷顶 锻用碳素钢盘条》的特点,以8.8级、9.8级螺栓的材料要 求为例,各种化学元素的确定。 C含量过高,冷成形性能将降低,太低则无法满足零件 机械性能的要求,因此定为0.20%-0.50%。
影响高强度紧固件品质的工艺因素
螺纹的脱碳会导致紧固件在未达到机械性能要求的拉 力时先发生脱扣,使螺纹紧固件失效,缩短使用寿命。由于 原材料的脱碳,如果退火不当,更会使原材料脱碳层加深。 调质热处理过程中,一般会从炉外带进一些氧化气体。棒 料钢丝的铁锈或冷拔后盘条钢丝表面上的残留物,入炉加 热后也会分解,反应生成一些氧化气体。例如钢丝的表面 铁锈,它的成分是碳酸铁及氢氧化物,在加热后将分解成 CO2及H2O,从而加重了脱碳。研究表明,中碳合金钢的脱 碳程度较碳钢严重,而最快的脱碳温度在700~800℃之间。 由于钢丝表面的附着物在一定条件下分解化合成CO2及 H2O的速度很快,如果连续式网带炉炉气控制不当,也会造 成螺纹脱碳超差。 高强度紧固件当采用冷镦成形时,原材料和退火的脱 碳层不但仍然存在,而且被挤压到螺纹的顶部,对于需要淬 火的紧固件表面,得不到所要求的硬度,其机械性能(特别是 强度和耐磨性)降低。另外,钢丝表面脱碳,表层与内部组织 不同,而且有不同的膨胀系数,淬火时有可能产生表面裂纹。
影响高强度紧固件品质的工艺因素
七、热处理 高强度紧固件根据技术要求都要进行调质处理。调质 处理是为了提高紧固件的综合机械性能,以满足产品规定 的抗拉强度值和屈强比。 热处理工艺对高强度紧固件尤其是它的内在质量有着 至关重要的影响,因此,生产优质的高强度紧固件,必须要有 先进的热处理技术和装备。 由于高强度螺栓生产量大,价格低廉,螺纹部分又是比 较细微相对精密的结构,因此,要求热处理设备必须具备生 产能力大、自动化程度高、热处理质量好的能力,进入20 世纪90年代以来,带有保护气氛的连续式热处理生产线 己占主导地位,震底式、铸链炉、连续式网带炉尤其适用 于中小规格紧固件的热处理调质。调质线除了炉子密封性 能好以外,还具有先进的气氛、温度和工艺参数计算机控 制,设备故障报警和显示等功能。高强度紧固件从上料→ 清洗→加热→淬火→清洗→回火→着色到下线,全部自动 控制运行,有效保证了热处理质量。
冷镦材料与热处理方法
4.影响高强度紧固件品质的工艺因 素
ቤተ መጻሕፍቲ ባይዱ
影响高强度紧固件品质的工艺因素
钢材的冷镦加工己成为在汽车、电器及其它机械部件 生产时不可缺少的制造方式,尤其是对紧固件行业而言,诸 如螺钉、螺栓、螺母等产品的生产几乎80%以上采用此种 生产效率高的制造工艺。紧固件的冷镦加工必须依赖钢材 卓越的冷顶锻性能和合理的加工工艺过程。本文对影响高 强度紧固件品质的加工工艺因素进行综合分析,作为提升 高强度紧固件品质的参考依据,供同行参考。 高强度螺栓加工工艺为:热轧盘条→(冷拔)→球化(软 化)退火→机械除鳞→酸洗→拉拔→冷镦成形→螺纹加工 →热处理→检验。 一、钢材设计 在紧固件制造中,正确选用紧固件材料是重要一环,因 为紧固件的性能和其材料有着密切的关系。如材料选用不 正确或不适当,可能造成性能达不到要求,使用寿命缩短,甚 至发生意外,或加工困难,制造成本高等。
影响高强度紧固件品质的工艺因素
35、45、ML35、SWRCH35K钢软化退火温度一般区 域为725~735℃;而SCM35、40Cr、SCR435钢球化退火 加热温度的一般区域为745~770℃,等温温度680~700℃。 三、剥壳除鳞 冷镦钢盘条去除氧化铁皮工序为剥壳、除鳞(有机械 除鳞和化学酸洗工序)。机械除鳞替代化学酸洗既提高了 生产率,又减小了环境污染。此除鳞过程包括弯曲法(普遍 使用带三角形凹槽的圆轮反复弯曲盘条)、喷丸法等,除鳞 ) , 效果较好,但不能使残余铁鳞去净(氧化铁皮清除率为98% 以上),尤其是氧化铁皮粘附很强时。因此,机械除鳞受铁皮 厚度、结构和应力状态的影响,仅用于低强度紧固件(≤6.8 级)用的低碳钢盘条。高强度紧固件(≥8.8级)用盘条在机械 除鳞后,为除净所有的氧化铁皮,再经化学酸洗工序即复合 除鳞。
影响高强度紧固件品质的工艺因素
Mn能提高钢的淬透性,但添加过多则会强化基体组织 而影响冷成形性能;在零件调质时有促进奥氏体晶粒长大 的倾向,故在国标的基础上适当提高,定为0.45%-0.80%。 Si能强化铁素体,促使冷成形性能降低,材料延伸率下 降。定为Si≤0.30%。S、P为杂质元素,它们的存在会沿晶 界产生偏折,导致晶界脆化,损害钢材的机械性能,应尽可能 降低,定为P≤0.030%,S≤0.035%。 B B含硼量最大值均为0.005%,因为硼元素虽然具有显 0.005%, 著提高钢材淬透性等作用,但同时会导致钢材脆性增加。 含硼量过高,对螺栓、螺钉和螺柱这类需要良好综合机械 性能的工件是非常不利的。 二、球化(软化)退火 沉头螺钉、内六角圆柱头螺栓采用冷镦工艺生产时, 钢材的原始组织会直接影响着冷镦加工时的成形能力。
影响高强度紧固件品质的工艺因素
冷镦成型所能达到的精度还同成型方法的选择和所采 用的工序有关。此外,它还取决于所用设备的结构特点、 工艺特点及使用状态,工模具精度、寿命和磨损程度。 冷镦成型和挤压使用的高合金钢、硬质合金模具的工 作表面粗糙度不应大于Ra=0.2 µm,这类模具工作表面的 粗糙度达到Ra=0.025~0.050µm时,具有最高寿命。 六、螺纹加工 螺栓螺纹一般采用冷加工,使一定直径范围内的螺纹 坯料通过搓(滚)丝板(模),由丝板(滚模)压力使螺纹成形。 可获得螺纹部分的塑性流线不被切断,强度增加、精度高、 质量均一的产品,因而被广泛采用。 为了制出最终产品的螺纹外径,所需要的螺纹坯径是 不同的,因为它受螺纹精度、材料有无镀层因素限制。