冶金过程分析监测系统
冶金企业自动化系统的分级

冶金企业自动化系统的分级一、背景介绍冶金企业作为重要的工业部门之一,其生产过程需要依靠自动化系统来实现高效、安全、稳定的生产。
冶金企业自动化系统的分级是为了满足不同层次的管理需求,确保生产过程的顺利进行。
本文将详细介绍冶金企业自动化系统的分级标准及其应用。
二、分级标准1. 一级系统:生产控制系统一级系统是冶金企业自动化系统的核心,主要负责控制整个生产过程。
其功能包括生产计划制定、生产过程控制、设备状态监测等。
一级系统需要具备以下特点:- 实时性:能够实时监测生产过程中的各项指标,并对异常情况进行及时处理。
- 稳定性:能够保证系统的稳定运行,不受外界干扰影响。
- 可靠性:能够确保系统的可靠性,避免因系统故障导致生产中断。
- 扩展性:能够根据生产需求进行系统的扩展,满足不同规模的生产要求。
2. 二级系统:过程监控系统二级系统是对一级系统的补充和支持,主要负责对生产过程中的关键参数进行监测和控制。
其功能包括设备状态监测、异常报警、数据分析等。
二级系统需要具备以下特点:- 精确性:能够准确监测和控制生产过程中的关键参数,确保生产的稳定性和质量。
- 可视化:能够通过图表、曲线等形式直观地展示生产过程中的数据和变化趋势。
- 分析能力:能够对生产过程中的数据进行分析,提供决策支持和优化建议。
- 与一级系统的集成:能够与一级系统实现数据的共享和交互,实现信息的无缝传递。
3. 三级系统:管理信息系统三级系统是冶金企业自动化系统的管理层,主要负责对生产过程进行监控和管理。
其功能包括生产计划制定、资源调度、成本控制等。
三级系统需要具备以下特点:- 综合性:能够对整个冶金企业的生产过程进行综合管理,实现资源的合理利用。
- 决策支持:能够提供决策支持和优化建议,帮助管理层做出科学决策。
- 数据分析:能够对生产过程中的数据进行分析,发现问题和改进的空间。
- 与一、二级系统的集成:能够与一、二级系统实现数据的共享和交互,实现信息的无缝传递。
冶金企业自动化系统的分级

冶金企业自动化系统的分级一、引言冶金企业自动化系统的分级是指根据自动化程度和功能需求,将冶金企业的自动化系统划分为不同的级别。
通过分级可以更好地管理和控制冶金生产过程,提高生产效率和质量,降低能耗和人力成本。
本文将详细介绍冶金企业自动化系统的分级标准和各级别的功能要求。
二、冶金企业自动化系统的分级标准根据冶金企业的规模、工艺流程和自动化需求,将自动化系统分为以下几个级别:1. 一级自动化系统:一级自动化系统是冶金企业最基础的自动化系统,主要用于数据采集和监控。
该级别的系统主要包括传感器、数据采集设备、数据传输设备和监控终端。
通过采集和传输设备,将生产过程中的各种数据传输到监控终端,实时监测生产状态,提供数据支持给管理层做出决策。
2. 二级自动化系统:二级自动化系统是在一级自动化系统基础上增加了控制功能。
该级别的系统主要包括控制设备、执行机构和控制终端。
通过控制设备和执行机构,实现对冶金生产过程的控制,如温度控制、压力控制、流量控制等。
控制终端用于设置控制参数和监测控制效果。
3. 三级自动化系统:三级自动化系统是在二级自动化系统基础上增加了优化功能。
该级别的系统主要包括优化算法、模型预测和自动调节。
通过优化算法和模型预测,对冶金生产过程进行优化调度,提高生产效率和质量。
自动调节功能可以根据实时数据进行自动调整,保持生产过程的稳定性。
4. 四级自动化系统:四级自动化系统是在三级自动化系统基础上增加了智能化功能。
该级别的系统主要包括人工智能、机器学习和大数据分析。
通过人工智能和机器学习技术,对冶金生产过程进行智能化管理和优化。
大数据分析可以对海量数据进行分析和挖掘,发现潜在的规律和问题,提供决策支持。
三、各级别自动化系统的功能要求1. 一级自动化系统功能要求:- 实时数据采集和传输:采集和传输冶金生产过程中的各种数据,如温度、压力、流量等。
- 数据监控和报警:实时监测生产状态,及时发现异常情况并报警。
过程分析系统简介
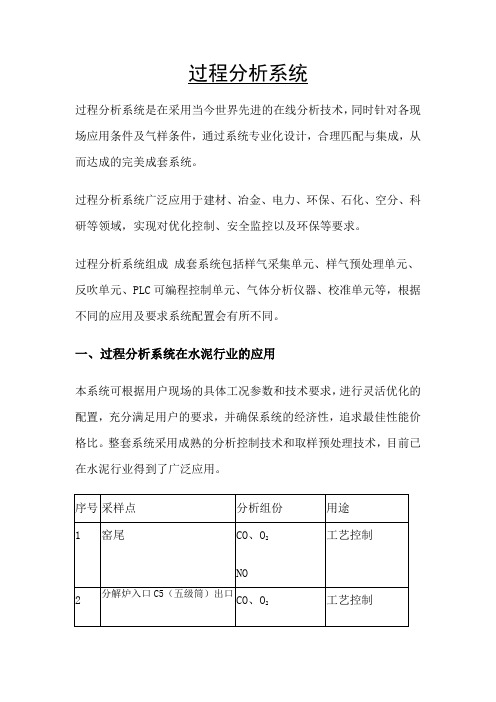
过程分析系统
过程分析系统是在采用当今世界先进的在线分析技术,同时针对各现场应用条件及气样条件,通过系统专业化设计,合理匹配与集成,从而达成的完美成套系统。
过程分析系统广泛应用于建材、冶金、电力、环保、石化、空分、科研等领域,实现对优化控制、安全监控以及环保等要求。
过程分析系统组成成套系统包括样气采集单元、样气预处理单元、反吹单元、PLC可编程控制单元、气体分析仪器、校准单元等,根据不同的应用及要求系统配置会有所不同。
一、过程分析系统在水泥行业的应用
本系统可根据用户现场的具体工况参数和技术要求,进行灵活优化的配置,充分满足用户的要求,并确保系统的经济性,追求最佳性能价格比。
整套系统采用成熟的分析控制技术和取样预处理技术,目前已在水泥行业得到了广泛应用。
二、过程分析系统在冶金行业的应用
三、过程分析系统在电力行业的应用
四、其他
根据工艺要求或安全需要用于气体在线分析。
主要技术参数:
1、测量范围:
SO2 0-100ppm至0-20% CH4 0-200ppm至0-20% NO 0-200ppm至0-20% CO 0-100ppm至0-100% CO2 0-100ppm至0-100% O2 0-500ppm至0-25%
2、响应时间: 1.5秒
3、模拟输出 4—20mA DC
4、气体流量1.2—1.6L/min
5、电源AC220V±10% 50±0.5Hz 150VA。
SCR炉铸区CO检测分析系统故障分析及控制改进

SCR炉铸区CO检测分析系统故障分析及控制改进张伟旗【摘要】针对SCR炉铸区CO检测分析系统故障进行分析及控制改进,系统检测分析响应速度快,准确度、精度及稳定性高,故障率低,有利于及时调整与监控铜液的氧含量,铸锭质量好,铜杆线氧含量波动小,完全能满足国内外客户对高端铜细线及超微线的特殊需求.【期刊名称】《有色设备》【年(卷),期】2016(000)006【总页数】6页(P34-39)【关键词】CO检测分析系统;故障率;控制改进【作者】张伟旗【作者单位】江西铜业集团铜材有限公司,江西贵溪335424【正文语种】中文【中图分类】TG23;TG291烟气分析在冶金、石油化工、火力发电、水泥及化肥等行业占有重要地位。
行业不同,其烟气成分也不尽相同,主要包括CO、CO2、SO2、O2及氮氧化物等气体。
江铜引进美国南线铜业公司SCR3000/4500二条铜杆连铸连轧生产线,分别于2003、2006年建成投产,而作为该生产线自动化控制的重要组成部分,其SCR炉铸区CO监测分析系统能实时、精确、高效地采集燃烧样气中CO的相关数据,分析工艺流程中的介质组成,能为铜杆连铸连轧生产提供相关的控制依据,实现该自动化生产线的连铸过程控制,将直接影响到铜液铸造、锭坯结晶的质量好坏及铜杆后序加工质量,甚至最终产品质量[1]。
然而,尽管罗斯蒙特Rosemount CO监测分析技术在世界上领先,但其设计过程监控和数据采集存在一些缺陷,应用技术尚有不足之处,在使用过程中存在问题也不少,且随着该公司产能的不断攀升及生产组织模式的变化,SCR炉铸区烟气含尘和含水增加,导致CO监测分析系统故障率过高,铜液温度难以控制,氧含量变化大,铸锭夹杂缺陷率高,导致铜杆线产品氧含量超标,客户意见大、投诉率高,严重影响企业的形象及社会经济效益,使企业发展陷入窘境。
因而对SCR炉铸区CO检测分析系统故障进行分析、研究,且作针对性的控制改进,对改善和提高SCR铜杆连铸连轧生产线的工艺装备技术水平,至关重要。
有色冶金全流程高效转化智能协同控制关键技术及应用_概述及解释说明

有色冶金全流程高效转化智能协同控制关键技术及应用概述及解释说明1. 引言1.1 概述有色冶金行业是指对非铁金属矿石(如铜、镍、铅、锌等)进行冶炼、提纯及加工的产业,其在国民经济发展中具有重要地位。
随着科技的不断进步和市场需求的增长,有色冶金企业面临着提高生产效率和质量,降低能耗排放的压力。
因此,针对有色冶金全流程的智能化协同控制技术应运而生。
本文主要介绍了有色冶金全流程高效转化智能协同控制关键技术及应用。
通过采用智能传感与数据采集技术、数据处理与分析技术以及高效转化控制算法与模型预测技术,实现了对有色冶金过程的精确监测和控制。
同时,结合实际应用案例分析,在某XX冶炼厂成功应用了智能协同转炉控制系统以及数据驱动的能源优化方法,并总结了2020年A市某有色冶金企业全流程智能协同控制项目的实施经验。
1.2 文章结构本文主要分为以下几个部分:2. 有色冶金全流程高效转化智能协同控制关键技术及应用在这一部分,我们将详细介绍有色冶金全流程高效转化智能协同控制的概述,并重点介绍其中的关键技术。
这些技术包括智能传感与数据采集技术、数据处理与分析技术以及高效转化控制算法与模型预测技术。
2.1 全流程高效转化智能协同控制概述我们将阐述有色冶金全流程高效转化智能协同控制的基本原理和目标。
通过实现全过程的信息收集和处理以及精确的控制策略,使得有色冶金行业能够提高生产效率、降低成本以及优化资源利用。
2.2 关键技术介绍在这一小节中,我们将详细介绍几个关键技术,包括智能传感与数据采集技术、数据处理与分析技术以及高效转化控制算法与模型预测技术。
通过使用这些关键技术,可以有效地实现对有色冶金过程中关键参数的监测和优化控制。
2.3 应用案例分析我们将介绍几个实际应用案例,包括XX冶炼厂智能协同转炉控制系统的应用实践、XX冶炼厂数据驱动的能源优化在行业中的推广以及2020年A市某有色冶金企业全流程智能协同控制项目的实施经验总结。
通过这些案例,我们可以更清楚地了解有色冶金全流程智能协同控制技术的实际效果和应用前景。
冶金行业中的质量控制方法与技术

冶金行业中的质量控制方法与技术在现代工业生产中,质量控制是确保产品质量的关键环节。
冶金行业作为重要的基础产业,对于质量控制更是尤为重视。
本文将介绍冶金行业中常用的质量控制方法与技术,并讨论其应用与效果。
一、质量控制方法1. 严格进货检验:冶金行业的原材料对产品质量有着重要影响。
因此,严格的进货检验是确保产品质量的第一步。
通过对原材料的化学成分、物理性能等进行检测,可以以保证产品的质量稳定性。
2. 过程控制:冶金生产过程中,合理的过程控制是保证产品质量的重要手段。
通过监测关键工艺参数,如温度、压力、流量等,实时调整操作参数,以确保产品在生产过程中达到预定的质量标准。
3. 检测分析:冶金行业在产品质量控制中广泛应用各种检测分析技术。
例如,化学成分分析、金相检测、力学性能测试等。
这些检测分析手段能够及时发现产品中的缺陷和问题,并及时调整生产工艺,保障产品的质量稳定性。
二、质量控制技术1. 先进的制造技术:随着科技的进步,冶金行业也不断引入先进的制造技术。
例如,数控机床、激光切割设备等。
这些技术的应用,可以提高产品的加工精度和一致性,从而提高产品的质量水平。
2. 自动化控制系统:针对冶金行业生产过程中复杂多变的特点,引入自动化控制系统是实现高质量生产的有效手段。
自动化控制系统能够实现对关键参数的实时监测和调整,提高生产效率和产品质量的稳定性。
3. 数据分析与智能决策:通过大数据分析技术,冶金企业能够收集和存储大量的生产数据,并利用智能决策技术进行数据分析和运营优化。
通过分析数据,企业可以找到生产中的不合理因素,并及时做出调整,提高产品质量和生产效益。
三、质量控制效果评估1. 控制图分析:控制图是质量控制中的常用工具,能够直观反映产品的质量稳定性。
通过对生产过程中的关键参数进行统计和分析,可以判断产品变异是否在可接受范围内,并及时采取措施进行调整。
2. 系统审核与认证:为了评估企业的质量管理水平和产品质量稳定性,冶金企业常常进行ISO质量管理体系认证。
在线分析技术如何改善过程控制
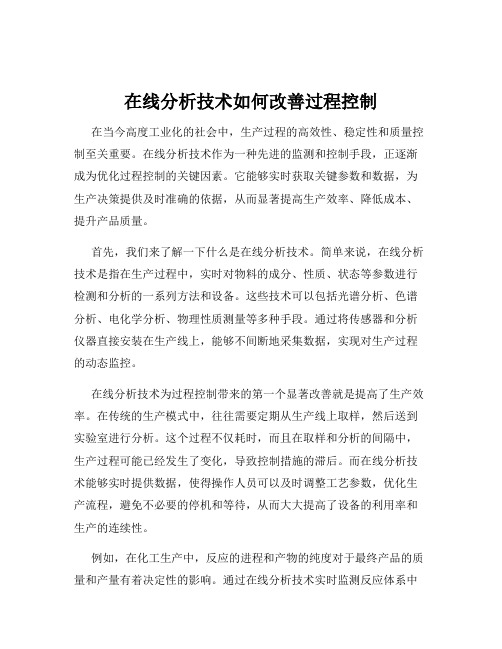
在线分析技术如何改善过程控制在当今高度工业化的社会中,生产过程的高效性、稳定性和质量控制至关重要。
在线分析技术作为一种先进的监测和控制手段,正逐渐成为优化过程控制的关键因素。
它能够实时获取关键参数和数据,为生产决策提供及时准确的依据,从而显著提高生产效率、降低成本、提升产品质量。
首先,我们来了解一下什么是在线分析技术。
简单来说,在线分析技术是指在生产过程中,实时对物料的成分、性质、状态等参数进行检测和分析的一系列方法和设备。
这些技术可以包括光谱分析、色谱分析、电化学分析、物理性质测量等多种手段。
通过将传感器和分析仪器直接安装在生产线上,能够不间断地采集数据,实现对生产过程的动态监控。
在线分析技术为过程控制带来的第一个显著改善就是提高了生产效率。
在传统的生产模式中,往往需要定期从生产线上取样,然后送到实验室进行分析。
这个过程不仅耗时,而且在取样和分析的间隔中,生产过程可能已经发生了变化,导致控制措施的滞后。
而在线分析技术能够实时提供数据,使得操作人员可以及时调整工艺参数,优化生产流程,避免不必要的停机和等待,从而大大提高了设备的利用率和生产的连续性。
例如,在化工生产中,反应的进程和产物的纯度对于最终产品的质量和产量有着决定性的影响。
通过在线分析技术实时监测反应体系中各物质的浓度变化,操作人员可以精确控制反应条件,如温度、压力、反应物的添加速度等,确保反应按照预期的方向进行,最大程度地提高反应转化率和选择性,从而提高生产效率和经济效益。
其次,在线分析技术有助于提升产品质量的稳定性。
产品质量的一致性是企业在市场竞争中立足的关键之一。
在线分析技术能够实时检测产品中的关键质量指标,如成分含量、杂质水平、物理性能等,一旦发现偏差,立即采取纠正措施,从而将质量波动控制在最小范围内。
以制药行业为例,药品的质量直接关系到患者的健康和生命安全,因此对生产过程的控制要求极为严格。
通过在线分析技术,如高效液相色谱(HPLC)和近红外光谱(NIR),可以实时监测药品生产过程中活性成分的含量、杂质的种类和含量等关键指标。
人工智能在冶金自动化中的应用

人工智能在冶金自动化中的应用一、引言随着科技的不断发展,人工智能(Artificial Intelligence,AI)已经成为当今世界的热门话题。
人工智能技术在各个领域都有广泛的应用,其中之一便是冶金自动化。
本文将探讨人工智能在冶金自动化中的应用,并详细介绍其在冶金过程中的具体应用场景和优势。
二、人工智能在冶金自动化中的应用场景1. 生产过程优化人工智能技术可以通过分析大量的数据,帮助冶金企业优化生产过程。
通过对冶金生产过程中的各种参数进行实时监测和分析,人工智能系统可以自动调整生产参数,提高生产效率和产品质量。
例如,通过人工智能系统对冶炼过程中温度、压力、流量等参数的实时监测和分析,可以实现精确控制,提高冶金产品的质量和产量。
2. 故障预测与维护人工智能技术可以通过对设备传感器数据的实时监测和分析,预测设备故障,并提前采取维护措施。
通过建立故障预测模型,人工智能系统可以根据设备的运行状态和历史数据,预测设备故障的可能性,并提醒相关人员采取相应的维护措施。
这样可以减少设备故障对生产过程的影响,提高生产的稳定性和可靠性。
3. 质量控制人工智能技术可以通过对产品质量数据的实时监测和分析,实现质量控制的自动化。
通过建立质量预测模型,人工智能系统可以根据生产过程中的各种参数,预测产品的质量,并自动调整生产参数,以实现产品质量的稳定控制。
这样可以减少人为因素对产品质量的影响,提高产品的一致性和稳定性。
4. 能源消耗优化人工智能技术可以通过对能源消耗数据的实时监测和分析,优化能源的使用效率。
通过建立能源消耗预测模型,人工智能系统可以根据生产过程中的各种参数,预测能源消耗的趋势,并自动调整生产参数,以实现能源消耗的最优化。
这样可以减少能源的浪费,降低生产成本,提高企业的竞争力。
三、人工智能在冶金自动化中的优势1. 数据分析能力强人工智能技术可以通过对大量的数据进行分析,提取出有用的信息,为冶金企业提供决策支持。
钢铁行业LIMS系统的开发与应用
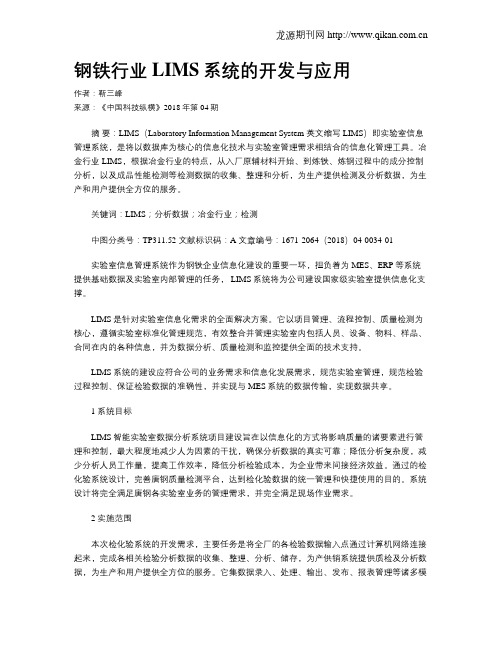
钢铁行业LIMS系统的开发与应用作者:靳三峰来源:《中国科技纵横》2018年第04期摘要:LIMS(Laboratory Information Management System 英文缩写LIMS)即实验室信息管理系统,是将以数据库为核心的信息化技术与实验室管理需求相结合的信息化管理工具。
冶金行业LIMS,根据冶金行业的特点,从入厂原辅材料开始、到炼铁、炼钢过程中的成分控制分析,以及成品性能检测等检测数据的收集、整理和分析,为生产提供检测及分析数据,为生产和用户提供全方位的服务。
关键词:LIMS;分析数据;冶金行业;检测中图分类号:TP311.52 文献标识码:A 文章编号:1671-2064(2018)04-0034-01实验室信息管理系统作为钢铁企业信息化建设的重要一环,担负着为MES、ERP等系统提供基础数据及实验室内部管理的任务, LIMS系统将为公司建设国家级实验室提供信息化支撑。
LIMS是针对实验室信息化需求的全面解决方案。
它以项目管理、流程控制、质量检测为核心,遵循实验室标准化管理规范,有效整合并管理实验室内包括人员、设备、物料、样品、合同在内的各种信息,并为数据分析、质量检测和监控提供全面的技术支持。
LIMS系统的建设应符合公司的业务需求和信息化发展需求,规范实验室管理,规范检验过程控制、保证检验数据的准确性,并实现与MES系统的数据传输,实现数据共享。
1 系统目标LIMS智能实验室数据分析系统项目建设旨在以信息化的方式将影响质量的诸要素进行管理和控制,最大程度地减少人为因素的干扰,确保分析数据的真实可靠;降低分析复杂度,减少分析人员工作量,提高工作效率,降低分析检验成本,为企业带来间接经济效益。
通过的检化验系统设计,完善唐钢质量检测平台,达到检化验数据的统一管理和快捷使用的目的。
系统设计将完全满足唐钢各实验室业务的管理需求,并完全满足现场作业需求。
2 实施范围本次检化验系统的开发需求,主要任务是将全厂的各检验数据输入点通过计算机网络连接起来,完成各相关检验分析数据的收集、整理、分析、储存,为产供销系统提供质检及分析数据,为生产和用户提供全方位的服务。
铜冶炼生产全流程自动化关键技术及应用

铜冶炼生产全流程自动化关键技术及应用铜冶炼是一项重要的冶金工艺,其生产全流程自动化是提高生产效率、优化工艺参数和保证产品质量的关键。
本文将介绍铜冶炼生产全流程自动化的关键技术及其应用。
铜冶炼生产全流程自动化的关键技术主要包括:数据采集、过程控制、设备控制和机器视觉等。
在这些关键技术的应用下,铜冶炼的生产过程可以实现连续、稳定和智能化。
首先,数据采集技术是实现铜冶炼生产全流程自动化的基础。
通过传感器、仪表等设备,可以实时、准确地采集到铜矿石的物理性质、化学成分和工艺参数等信息。
这些数据对于优化冶炼工艺和保障产品质量至关重要。
其次,过程控制技术是铜冶炼生产全流程自动化中的核心技术。
通过对数据采集的处理和分析,可以实现对冶炼过程的监控、调节和优化。
例如,在冶炼炉的温度、氧气流量和矿石添加量等方面,可以根据实时的数据来调节工艺参数,以达到最佳的冶炼效果。
设备控制技术是实现铜冶炼生产全流程自动化的关键之一。
通过对冶炼设备的自动化控制,可以实现生产过程的连续性和稳定性。
例如,在炼铜炉的控制中,可以通过对电极电流、电压和氧化剂流量等参数的控制,使得冶炼过程更加稳定和高效。
最后,机器视觉技术在铜冶炼生产全流程自动化中的应用也越来越广泛。
通过图像识别和处理技术,可以对冶炼过程中的关键设备和产品进行检测和分析。
例如,在铜炉的内部和外部,可以通过红外摄像机和激光测温仪等设备实时监测温度分布和熔炼情况,从而保证冶炼过程的稳定性和产品质量的一致性。
总之,铜冶炼生产全流程自动化的关键技术及其应用对于提高生产效率和产品质量具有重要意义。
通过数据采集、过程控制、设备控制和机器视觉等关键技术的应用,可以实现铜冶炼过程的连续、稳定和智能化,为冶炼工艺的优化和产品质量的保证提供有力支持。
此外,铜冶炼生产全流程自动化中的关键技术还包括智能控制系统和数据分析技术。
智能控制系统是铜冶炼生产全流程自动化的重要组成部分,它基于先进的控制算法和模型,实现对冶炼过程的智能监控和控制。
冶金生产过程危险识别及评价技术

冶金生产过程危险识别及评价技术冶金生产过程中存在着许多潜在的危险风险,包括爆炸、火灾、化学品泄漏、射线辐射等。
为了确保生产过程的安全和员工的健康,需要进行危险识别及评价。
下面将介绍一些常用的冶金生产过程危险识别及评价技术。
一、危险识别技术:1. 历史数据分析:通过分析历史事故数据和事故发生的原因,可以识别出潜在的危险因素,为制定相应的预防措施提供依据。
2. 现场巡视:定期进行现场巡视,在生产过程中及时发现潜在的危险源和不安全行为,例如未正确佩戴安全帽、操作不规范等,及时采取措施进行改进。
3. 系统分析方法:利用系统思维,综合考虑不同因素之间的相互作用,识别出可能的危险因素。
例如,通过综合分析导致爆炸的可能因素包括可燃性材料、氧气、点火源等。
4. 专家咨询:邀请专家对生产过程进行评估,识别潜在的危险因素,提供改进建议。
二、危险评价技术:1. 危险源辨识和评价技术:通过对各个工艺环节进行详细的调研和分析,识别出潜在的危险源,并对其进行评价、分类、排序。
2. 安全风险评估技术:对危险源的可能性、严重性和风险程度进行评估,在确定危险源的优先级和采取相应预防措施时提供科学依据。
3. 事件树分析:采用树状图的形式,从事故发生后的不同发展路径进行分析,可提前预测事故的发生概率,以及事故后果的严重程度。
4. 风险矩阵分析:将危险源的可能性和严重性分别划分为几个等级,通过将两者交叉得到的矩阵来评估风险水平。
以上只是部分常用的技术,实际的危险识别及评价工作中还可以结合具体的生产工艺和设备特点,选择合适的技术方法。
同时,还需要密切关注冶金行业的最新技术和规范要求,及时进行技术更新和改进。
危险识别及评价工作不仅要进行一次性的评估,还需要定期进行复查和改进,以确保生产过程的持续安全性。
同时,也要加强员工的安全培训和意识,提高员工对危险因素的识别和应对能力。
人工智能在冶金行业的应用前景

人工智能在冶金行业的应用前景人工智能(AI)作为一种新兴技术,正在迅速应用于各个行业,并且在冶金行业也有着广阔的应用前景。
AI技术的发展为冶金行业提供了新的机遇和挑战,在提高生产效率、降低成本、提升产品质量等方面发挥着重要的作用。
首先,人工智能在冶金行业的应用可以最大限度地提高生产效率。
通过对冶金过程的自动化控制和优化,AI技术可以使生产线实现智能化和自动化。
例如,智能控制系统可以根据实时数据和模型预测,自动调整生产参数,最大程度地提高冶金设备的效能。
此外,AI还可以结合大数据分析技术,对冶金过程中的数据进行实时监测和分析,从而及时发现并纠正潜在的问题,减少生产中的故障和停机时间,提高生产效率。
其次,人工智能还可以帮助冶金企业降低生产成本。
通过利用AI技术进行能源消耗的优化和控制,冶金企业可以减少能源消耗,降低生产成本。
AI还可以根据历史数据和预测分析,对原材料的采购和库存进行精确控制,避免过量采购和物料短缺的情况发生。
此外,AI还可以通过优化生产流程和资源调度,提高能源利用效率,从而减少生产过程中的能源浪费。
此外,人工智能还可以提升冶金产品的质量。
通过AI技术对生产过程的实时监测和分析,可以发现并纠正生产中的偏差和问题,提高产品的一致性和质量稳定性。
例如,AI可以在生产线上对产品进行实时检测和测试,及时发现并剔除不符合要求的产品,从而保证产品的质量。
AI还可以通过数据分析和模型预测,优化冶金配方和工艺参数,提高产品的性能和功能,满足不同客户的需求和要求。
另外,人工智能在冶金行业的应用还可以提升企业的安全性和可靠性。
通过对工艺过程的实时监测和预警,AI可以帮助企业及时发现和解决潜在的安全隐患,并避免事故的发生。
例如,AI可以通过对设备运行状态的监测和分析,预测设备故障的可能性,并提前进行维护和保养,减少设备故障和事故的发生。
此外,AI还可以通过对数据的实时分析和模型的建立,帮助企业进行风险评估和决策优化,提升企业的可靠性和竞争力。
IBA公司过程数据采集及分析系统在冶金企业中的应用

第 2 卷 2 1 年第 3 总第 13 9 01 期( 5 期)
IA公 司过程数据采集及分 析系统在 冶金企业 中的应用 B
裴 云 李雁 志 柳 妞
( 钢股 份设 备 管理部 武
摘 要
武汉
408 ) 303
介绍 了 IA公 司的过程数据 采集和分析 系统 的硬 件配置 , B 应用软件和通讯 构成 以及在 冶金企 业的
称 P A 即Por s a qitn 被广泛使用 , D , r e tA u io ) g sD a si 过 程数 据 分 析系 统 ( aA aye)采集 的数 据 有 : i — nlzr, b 主 传动直流系统 、 新的工艺控制系统T C 顺控系统 D、 P S 以及交 流 V V 传 动等的参 数 , C7 VF 采集的数据 有数字 量 , 有模 拟量 , 同时进行 大量数据 的采 可 集、 分析 和存档 , 对采集 的数据进行实时显示 , 并 且可 以长 期保 存 。极 大地 方便 了调 试数 据 分 析 和 故 障诊 断 , 日常运 行 维 护 中 , 于 故 障 的诊 断 和 在 用 生产 参 数 的查 询 。IA公 司 的过 程 数 据 采 集 和 分 B 析 系统 具 有一 定 优 势 , 到技 术 人 员 的喜 爱 。现 受 就 IA公 司 的 过程 数 据 采 集 和分 析 系统 的硬件 配 B 置 、 件及应 用 进行 初 步分 析和介 绍 。 软
一Hl —l h l fb 丝 T… Pl D P T A D A [ 0 u 2
一
析程序 , 用于采集数据的进一步处理。 过程 数 据采 集 和分 析 系统 概况 如 图 1 示 , 所 其 中 P A 1 P A 2进 行 数 据 的 在 线 采 集 检 测 , D 0 和 D 0 P A 0 采集 的数 据进 行存 档 和离 线分 析 。 D O对
DCS在冶金行业中的应用案例解析
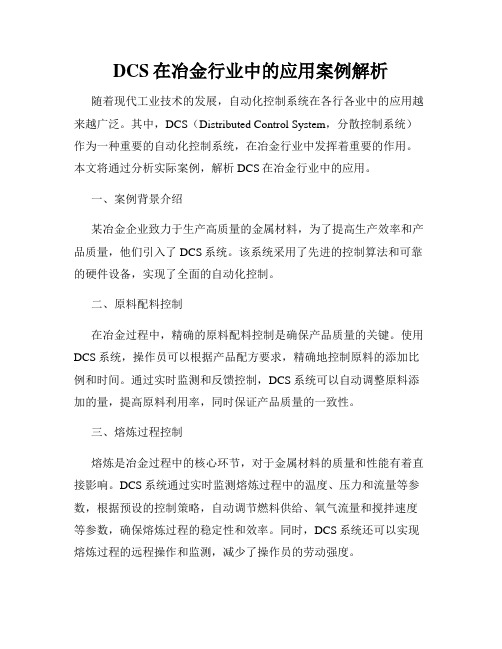
DCS在冶金行业中的应用案例解析随着现代工业技术的发展,自动化控制系统在各行各业中的应用越来越广泛。
其中,DCS(Distributed Control System,分散控制系统)作为一种重要的自动化控制系统,在冶金行业中发挥着重要的作用。
本文将通过分析实际案例,解析DCS在冶金行业中的应用。
一、案例背景介绍某冶金企业致力于生产高质量的金属材料,为了提高生产效率和产品质量,他们引入了DCS系统。
该系统采用了先进的控制算法和可靠的硬件设备,实现了全面的自动化控制。
二、原料配料控制在冶金过程中,精确的原料配料控制是确保产品质量的关键。
使用DCS系统,操作员可以根据产品配方要求,精确地控制原料的添加比例和时间。
通过实时监测和反馈控制,DCS系统可以自动调整原料添加的量,提高原料利用率,同时保证产品质量的一致性。
三、熔炼过程控制熔炼是冶金过程中的核心环节,对于金属材料的质量和性能有着直接影响。
DCS系统通过实时监测熔炼过程中的温度、压力和流量等参数,根据预设的控制策略,自动调节燃料供给、氧气流量和搅拌速度等参数,确保熔炼过程的稳定性和效率。
同时,DCS系统还可以实现熔炼过程的远程操作和监测,减少了操作员的劳动强度。
四、冷却过程控制在冶金行业中,冷却过程对于金属材料的晶体结构和性能具有重要影响。
DCS系统可以实现对冷却过程的精确控制,通过调节冷却剂的供给和温度,控制冷却速率,从而实现对金属材料的结晶过程的控制。
这种精确的控制可以提高产品的均匀性和稳定性,避免产生缺陷和变形。
五、质量监测与故障诊断冶金行业对产品的质量要求非常高,任何质量问题都可能导致严重的经济损失。
DCS系统可以实时采集和分析冶金过程中的各种参数数据,并将其与预设的质量标准进行比较。
一旦发现异常情况,系统会及时报警并提供故障诊断信息,帮助操作员快速定位和解决问题,最大限度地避免质量问题的发生。
六、安全管理与环境监测在冶金行业中,安全管理和环境保护是非常重要的议题。
安全仪表系统(SIS)的研发和应用方案(一)

安全仪表系统(SIS)的研发和应用方案一、实施背景随着工业生产的日益复杂化,安全问题变得越来越突出。
安全仪表系统(SIS)作为保障工业生产安全的关键技术,其研发与应用具有重要意义。
当前,国内SIS技术尚处于发展阶段,亟待进一步的技术创新和产业升级。
为了提高工业生产安全水平,满足日益严格的法规要求,SIS系统的研发与应用成为了紧迫的任务。
二、工作原理安全仪表系统(SIS)是一种基于计算机技术的安全控制系统,它通过实时监测、分析生产过程中的各种数据,及时发现安全隐患,并采取相应的控制措施,确保生产过程的安全。
SIS系统的工作原理主要包括数据采集、数据处理、风险评估和安全控制四个环节。
数据采集是SIS系统的第一步,通过各种传感器和监测设备获取生产过程中的温度、压力、液位等关键参数。
数据处理是对采集到的数据进行处理和分析,提取出与安全相关的信息。
风险评估是根据数据处理的结果,对生产过程的安全性进行评估,判断是否存在安全隐患。
安全控制是根据风险评估的结果,采取相应的控制措施,如切断、报警等,以消除或减轻安全隐患。
三、实施计划步骤1.需求分析:明确SIS系统的功能需求和性能指标,包括监测范围、测量精度、响应时间等。
2.系统设计:根据需求分析结果,进行系统架构设计和功能模块划分,确定系统的硬件和软件组成。
3.硬件选型与配置:选择合适的硬件设备,如传感器、PLC、HMI等,并进行配置和连接。
4.软件编程:编写SIS系统的控制程序和算法,包括数据采集、数据处理、风险评估和安全控制等功能模块。
5.系统集成与测试:将硬件和软件集成在一起,进行系统测试和调试,确保系统正常运行和满足性能要求。
6.现场安装与调试:将SIS系统安装到工业现场,进行实地调试和优化,确保系统与实际生产过程的匹配度。
7.用户培训:为用户提供SIS系统的操作和维护培训,确保用户能够正确使用和维护系统。
8.售后服务:提供系统的售后服务和技术支持,解决用户在使用过程中遇到的问题。
DCS系统的基本原理和架构
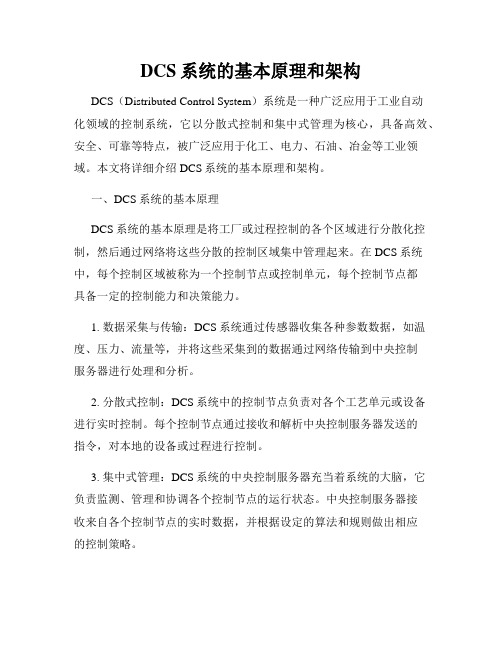
DCS系统的基本原理和架构DCS(Distributed Control System)系统是一种广泛应用于工业自动化领域的控制系统,它以分散式控制和集中式管理为核心,具备高效、安全、可靠等特点,被广泛应用于化工、电力、石油、冶金等工业领域。
本文将详细介绍DCS系统的基本原理和架构。
一、DCS系统的基本原理DCS系统的基本原理是将工厂或过程控制的各个区域进行分散化控制,然后通过网络将这些分散的控制区域集中管理起来。
在DCS系统中,每个控制区域被称为一个控制节点或控制单元,每个控制节点都具备一定的控制能力和决策能力。
1. 数据采集与传输:DCS系统通过传感器收集各种参数数据,如温度、压力、流量等,并将这些采集到的数据通过网络传输到中央控制服务器进行处理和分析。
2. 分散式控制:DCS系统中的控制节点负责对各个工艺单元或设备进行实时控制。
每个控制节点通过接收和解析中央控制服务器发送的指令,对本地的设备或过程进行控制。
3. 集中式管理:DCS系统的中央控制服务器充当着系统的大脑,它负责监测、管理和协调各个控制节点的运行状态。
中央控制服务器接收来自各个控制节点的实时数据,并根据设定的算法和规则做出相应的控制策略。
4. 实时通信:DCS系统中的各个控制节点之间通过网络进行实时的通信。
这种实时通信可以确保系统的响应时间和控制效果,同时也可以实现控制节点之间的数据共享和相互协作。
5. 可靠性与安全性:DCS系统设计了多重冗余和安全机制,以确保系统在故障或攻击时能够正常运行。
例如,系统采用了双重备份和实时数据同步技术,确保数据的可靠性和系统的高可用性。
二、DCS系统的架构DCS系统的架构包括硬件和软件两个方面,下面将对其进行详细介绍。
1. 硬件架构DCS系统的硬件架构由以下几个关键组件构成:- 控制节点:每个控制节点都由一台工控机或PLC(Programmable Logic Controller)组成,负责实时控制和数据采集。
Matlab在冶金工程中的应用方法

Matlab在冶金工程中的应用方法在当今工程科技的快速发展中,计算机软件的应用已成为各个领域的重要组成部分。
其中,Matlab作为一种功能强大的数学软件,被广泛应用于各个行业。
本文将探讨Matlab在冶金工程中的应用方法,介绍其在分析、设计和优化等方面的作用。
一、Matlab的基本功能Matlab作为一种计算机编程语言和开发环境,主要用于数值计算、数据分析和可视化等方面。
它具有丰富的内置函数库和工具箱,能够快速进行算法的实现和模拟,为用户提供高效的数据处理和图形展示功能。
二、冶金工程中的数据处理与分析冶金工程涉及大量的数据处理和分析工作,包括原材料分析、生产工艺参数监控、产品质量控制等。
Matlab提供了丰富的数学函数和统计工具,能够高效地处理和分析复杂的冶金数据。
例如,在冶金原料分析中,我们通常需要对样品进行化学成分分析。
传统的方法是通过化学方法进行分析,然后使用手工计算得出结果。
而利用Matlab,我们可以通过编写相应的程序,实现对样品成分的自动分析和计算。
同时,Matlab还提供了多种数据处理和可视化的工具,能够更好地展示分析结果和趋势变化。
除了样品分析,冶金生产过程中的参数监控也是很重要的一项任务。
通过对生产过程中的各项参数进行实时监测和统计,可以及时发现问题并采取相应的措施。
Matlab提供了强大的数据处理和模拟功能,可以对大量实时数据进行分析和处理。
我们可以编写程序实现对关键参数的监控和预测,从而提高生产的稳定性和效率。
三、冶金工程中的模拟和优化冶金工程中的一项重要任务是对冶金过程进行模拟和优化。
通过模拟和分析,我们可以深入了解冶金过程中的各种现象和机理,从而优化生产工艺和提高产品质量。
Matlab作为一种功能强大的数值计算软件,可以实现对冶金过程的模拟和仿真。
通过编写相应的数学模型和算法,我们可以对冶金过程进行精确的数值计算和模拟。
例如,在冶炼过程中,我们可以利用Matlab对炉内温度、浓度和流速等参数进行模拟,从而进行优化设计和工艺改进。
ICP-AES在冶金分析中的应用

ICP-AES在冶金分析中的应用摘要:电感耦合等离子体原子发射光谱技术(ICP—AES) 一直是材料领域中最为常用的元素测定和分析的手段。
ICP~AES分析法具有检出限低、灵敏度高、稳定性好、可多元素同时分析、基体效应干扰小等优点,因此被广泛应用于冶金分析、地质分析、环境科学、半导体的研发和生命科学等领域,特别是在冶金分析领域,ICP—AES做出了重要贡献。
我国每年从国外进口了数百台包括直读光谱、ICP光谱在内的原子发射光谱仪器,在冶金分析方面取得了不小的突破,制造了大量高性能的合金材料。
关键词:ICP-AES;冶金分析;应用;前言:ICP-AES 技术在冶金分析领域中应用十分广泛,具有多元素同时分析、检出限低、灵敏度高、稳定性好等优势。
我国每年都要从国外进口数百台原子发射光谱仪器( 只读光谱、ICP 光谱等),促进了冶金分析领域的发展进程,生产出了诸多高性能合金材料。
由此可见,加强ICP-AES 分析技术研究的重要性。
一、ICP-AES相关阐述ICP-AES( 电感耦合等离子原子发射光谱法),是一种以电感耦合等离子矩为激发光源的光谱分析方法,具有线性范围宽、检出限低、精度高、效率高、同时测定等优势。
如今国内外已经广泛将ICP-AES 应用到环境样品、矿物、岩石、金属等数十种元素测定。
在ICP-AES 分析当中,不同金属元素含量不同其发射特征光强弱也存在差异,定量关系为:I=aCb公式中,I 表示发射特征谱线强度;C表示被测元素浓度;a 为试样相关系数;b 自吸系数(b ≤ 1)。
:近年来商品仪器推出轴向(端视),有较高的灵敏度和较好的检出限。
炬管通常是垂直放置,从侧面观察,称为径向(侧视)。
端视(炬管水平放置)的检出限通常要比侧视(炬管垂直放置)提高几倍至一个数量级。
这是由于侧视只观测到正常分析区的一部分,信号量较小且背景较高。
端视可以观测整个正常分析区的光发射信号。
增加了可测的信号量,同时光谱背景较低,信背比高。
《DCS集散控制系统》课件
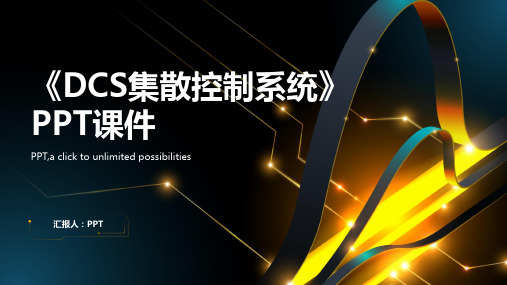
其他领域的应用
电力系统:发电、输电、变电、配电等 环节
石油化工:炼油、化工、天然气等环节
冶金行业:钢铁、有色金属等环节
交通领域:铁路、公路、航空、港口等 环节
环保领域:污水处理、大气污染控制等 环节
建筑领域:楼宇自动化、智能建筑等环 节
Part Six
DCS集散控制系统 的设计与实施
系统设计原则与方法
特点:人机界面友 好,操作简便
应用:广泛应用于 工业自动化、电力 、石化等领域
系统网络
网络拓扑结构:星型、环型、总线型等 网络协议:TCP/IP、Modbus等 网络设备:交换机、路由器、防火墙等 网络管理:监控、配置、故障诊断等
硬件设备选型与配置
控制器:选择合适的控制器类型和型号,如PLC、DCS等 输入输出设备:选择合适的输入输出设备,如传感器、执行器等 通信设备:选择合适的通信设备,如网络交换机、路由器等 电源设备:选择合适的电源设备,如UPS、电源模块等 安全设备:选择合适的安全设备,如防火墙、安全网关等 辅助设备:选择合适的辅助设备,如显示器、键盘等
Part Four
DCS集散控制系统 的软件功能
控制算法与策略
控制算法:PID控制、模糊控制、神经网络控制等 控制策略:集中控制、分散控制、混合控制等 控制目标:提高系统稳定性、准确性、实时性等 控制效果:降低能耗、提高生产效率、减少故障率等
数据采集与处理
数据采集:从现场设备中 获取实时数据,如温度、 压力、流量等
报警功能:当系统 出现异常时,自动 报警并提示操作人 员
操作功能:提供手 动、自动等多种操 作方式,方便操作 人员控制设备
数据记录与分析: 记录系统运行数据 ,便于分析设备运 行情况,优化控制 策略。
- 1、下载文档前请自行甄别文档内容的完整性,平台不提供额外的编辑、内容补充、找答案等附加服务。
- 2、"仅部分预览"的文档,不可在线预览部分如存在完整性等问题,可反馈申请退款(可完整预览的文档不适用该条件!)。
- 3、如文档侵犯您的权益,请联系客服反馈,我们会尽快为您处理(人工客服工作时间:9:00-18:30)。
ZYF-602冶金过程分析检测系统
武汉正元自动化仪表有限公司
一、研究背景
ZY-602系列冶金过程分析系统是专业为冶金行业的转炉煤气回收过程、高炉喷煤过程、高炉炉顶、重力除尘、以及各种工业煤气气柜等设备所配套的成套在线过程分析系统,是以在线气体自动分析仪器为核心,运用现代传感器技术、自动测量技术、自动控制技术、计算应用技术以及相关的专业分析田间和通讯网络所组成的新一代工业在线分析气体分析系统。
ZY-602系列冶金过程分析监测系统适用于钢铁、化工、煤气化、生物气化等领域,测量焦炉煤气、高炉煤气、转炉煤气、混合煤气、发生炉煤气、生物燃气等可燃气体的热值和不同成分的体积浓度。
转炉煤气分析系统(CO、O2)
高炉煤气分析系统(CO、CO2、H2)
焦炉煤气分析流程(O2)
煤粉制备、高炉喷煤分析系统(CO、O2)
干熄焦分析系统(H2、O2、CO、CO2)
二、技术指标
样气处理系统技术指标
●全不锈钢取样探头运行时问≥5年,且免维护
●经处理后洁净样气含尘粒度≤03Μμm
●系统滞后时问≤4min(管线长度≤50水)
●系统单线连续采样在线运行时问≤24小时
●过滤装置不更换时间≥3年
●所有取样过滤装置均为全不锈钢焊接,完全免维护
分析系统技术指标
分析系统检测量程
CO:0-75%(红外检测)
CO2:0-25%(红外检测)
H2:0-75%(热导检测)
CH4:0-40%(可选)(红外检测)
N2:0-100%(归一法)
零漂≤±1.0%,周SF★线性度≤±1.0%周SF
重复性≤±l.0%,周SF★灵敏度≤±0.5%
环境温度:+5–45℃:
输出信号:标准电流4-20mA信号
数据通迅:PROFIBUS、ETHERNET
报警状态信号:光源干接点
技术指标
三、主要特点
●采用国际先进、具有自主知识产权的NDIR非分光红外和TCD热导气体分析
技术
●一台仪器同时测量燃气中CO、CO2、CH4、H2、O2、CnHm六种气体的体积浓
度
●能够自动计算、显示煤气的热值,热值单位Kcal/m3和MJ/m3可以自由切
换
●测量CnHm浓度,保证焦炉煤气、混合煤气、发生炉煤气、秸秆燃气等气体
热值的准确性
●CnHm气体对CH4测量结果无干扰,能够精确测量CH4的浓度
●CO、CO2、CH4以及对H2测量结果无干扰
●气体采样流量变化对H2热导传感器测量结果无影响
●中、英文软件操作界面,并且可以自由切换
●具备RS-232数字输出和4-20mA模拟输出接口
●内置进口调零气象,可以实现空气自动调零
●可选配预处理装置,可以实现7d*24h模式连续不间断测试
四、主要应用
高炉工艺点及系统选型表
高炉喷煤工艺点及系统选型表
转炉工艺点及系统选型表.
焦炉、兰炭炉工艺点及系统选型表
干熄焦工艺点及系统选型表
燃气厂、动力厂、冷轧、热轧、连铸厂工艺点及系统选型表
五、注意事项
使用本产品注意以下事项:
请在所规定的环境条件下使用,避免阳光直射和有水滴滴到仪器上; 请在不含腐蚀性气体的环境下使用;
请避免放置在大功率用电装置的附近;
请避免撞击及强烈振动;
请不要用湿手操作设备;
请将仪器外壳可靠接地。