车间深入管理提效
车间管理的五大基本方法

车间管理的五大基本方法在现代工业生产中,车间管理是至关重要的一环。
有效的车间管理既能提高生产效率,又能确保产品质量和员工安全。
下面将介绍五大基本方法,帮助车间管理者更好地组织和管理生产过程。
1. 生产过程优化生产过程是车间管理的核心。
通过优化生产流程、精简生产步骤和合理分配资源,可以提高生产效率,缩短生产周期。
车间管理者应定期对生产过程进行分析和评估,找出存在的问题并及时改进,确保生产运作顺畅。
2. 人员培训与激励员工是车间生产的重要组成部分,他们的素质和工作态度直接影响生产质量和效率。
车间管理者应通过培训课程提升员工技能,增强他们的工作动力,激发潜在潜力。
同时,建立有效的激励机制,奖励表现优秀的员工,推动整个车间团队不断进步。
3. 设备保养与维护设备是生产的重要保障,良好的设备状况直接关系到生产效率和产品质量。
车间管理者应制定科学的设备保养计划,定期对设备进行检查和维护,及时处理设备故障,确保设备正常运转,防止因设备问题导致的生产中断。
4. 原材料采购与管理原材料是产品生产的基础,原材料采购及管理的合理性直接决定产品质量和成本。
车间管理者应建立完善的原材料供应链,选择有资质和信誉的供应商,确保原材料供应的及时性和稳定性。
同时,严格管理原材料库存,避免因原材料短缺或浪费影响生产进度。
5. 质量控制与检验产品质量是企业竞争力的重要体现,质量控制是车间管理中至关重要的一环。
车间管理者应建立完善的质量管理体系,明确质量标准和检验流程,制定严格的质量管控措施,确保产品符合标准。
综上所述,车间管理的五大基本方法包括生产过程优化、人员培训与激励、设备保养与维护、原材料采购与管理、质量控制与检验。
只有将这五大方法有机结合,车间管理才能更加科学合理,实现高效生产、优质产品的目标。
车间管理提升实施方案
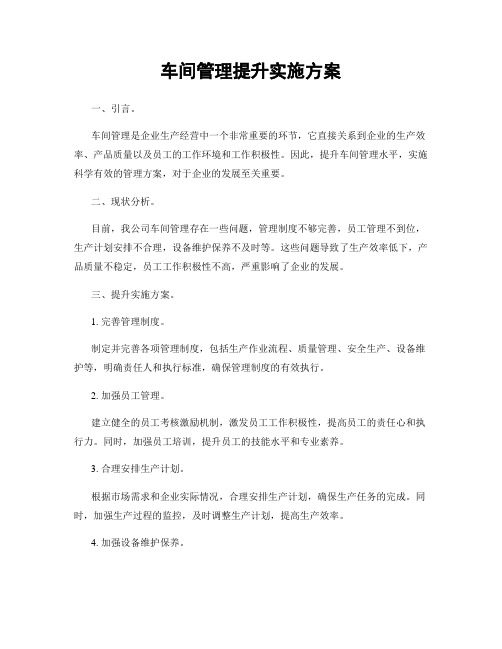
车间管理提升实施方案一、引言。
车间管理是企业生产经营中一个非常重要的环节,它直接关系到企业的生产效率、产品质量以及员工的工作环境和工作积极性。
因此,提升车间管理水平,实施科学有效的管理方案,对于企业的发展至关重要。
二、现状分析。
目前,我公司车间管理存在一些问题,管理制度不够完善,员工管理不到位,生产计划安排不合理,设备维护保养不及时等。
这些问题导致了生产效率低下,产品质量不稳定,员工工作积极性不高,严重影响了企业的发展。
三、提升实施方案。
1. 完善管理制度。
制定并完善各项管理制度,包括生产作业流程、质量管理、安全生产、设备维护等,明确责任人和执行标准,确保管理制度的有效执行。
2. 加强员工管理。
建立健全的员工考核激励机制,激发员工工作积极性,提高员工的责任心和执行力。
同时,加强员工培训,提升员工的技能水平和专业素养。
3. 合理安排生产计划。
根据市场需求和企业实际情况,合理安排生产计划,确保生产任务的完成。
同时,加强生产过程的监控,及时调整生产计划,提高生产效率。
4. 加强设备维护保养。
建立设备维护保养台账,制定设备维护保养计划,定期对设备进行检修和保养,确保设备的正常运转,提高设备利用率和生产效率。
四、实施效果评估。
实施以上提升方案后,需要对实施效果进行评估,主要包括生产效率、产品质量、员工满意度等方面的评估。
通过评估结果,及时发现问题,进一步完善管理方案,确保提升车间管理的效果持续稳定。
五、结语。
提升车间管理水平,需要全员参与,需要科学合理的管理方案,更需要坚定的执行力和持续改进的精神。
希望通过我们的努力,能够实现车间管理水平的提升,为企业的发展做出更大的贡献。
汽修车间精细化管理制度

汽修车间精细化管理制度第一章总则第一条为了更好地规范汽修车间的经营管理,提高服务质量,确保安全生产,特制定本制度。
第二条本制度适用于汽修车间的生产经营活动,包括员工管理、设备维护、车辆维修等方面。
第三条全体员工必须严格遵守本制度,任何违反本制度的行为将受到相应的处罚。
第二章管理人员职责第四条汽修车间的管理人员应当具有相关的专业知识和管理经验,能够独立承担车间的运营管理工作。
第五条管理人员应当对车间的生产经营活动负责,确保生产安全,提高效率,降低成本。
第六条管理人员应当建立健全的车间管理制度和规章制度,确保车间的正常运转。
第七条管理人员应当对车间的日常运营进行监督和管理,及时发现并解决问题。
第八条管理人员应当督促员工切实履行各项工作职责,提高服务质量,确保生产安全。
第三章员工管理第九条汽修车间应当建立健全的员工管理制度,包括招聘、考核、培训、奖惩等方面。
第十条汽修车间的员工应当具有相应的技术水平和职业道德,能够胜任所分配的工作。
第十一条汽修车间的员工应当严格遵守工作纪律,服从管理人员的指挥,不得擅自改变工作内容。
第十二条汽修车间应当定期对员工进行培训,提高其技术水平和服务意识。
第十三条汽修车间应当根据员工的表现进行考核,并及时给予奖励或者处罚。
第四章设备维护第十四条汽修车间应当建立健全的设备维护制度,包括设备的保养、保修、更新等方面。
第十五条汽修车间的设备应当进行定期的检查和维护,确保其正常运转。
第十六条汽修车间应当配备专业的设备维护人员,负责设备的维护和维修工作。
第十七条汽修车间应当对设备进行定期的检测和更新,保证其技术水平和安全性。
第五章车辆维修第十八条汽修车间应当建立健全的车辆维修制度,包括维修流程、质量标准、服务保障等方面。
第十九条汽修车间的维修人员应当具有相关的资格和经验,能够胜任各类车辆的维修工作。
第二十条汽修车间应当对车辆维修流程进行标准化管理,确保维修质量。
第二十一条汽修车间应当配备专业的维修设备和工具,保证维修工作的顺利进行。
车间加强操作管理制度
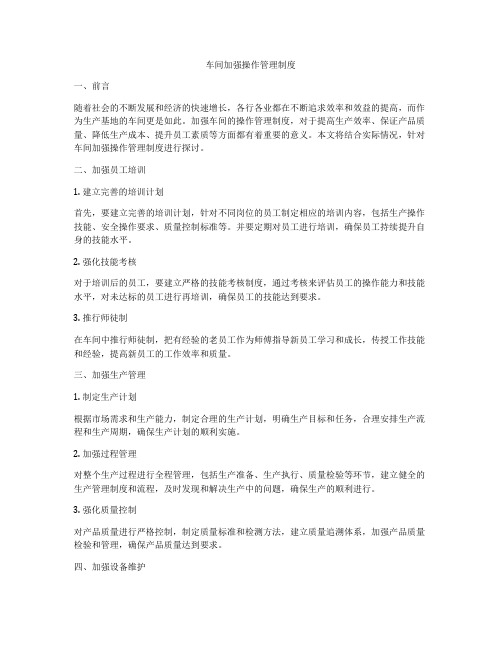
车间加强操作管理制度一、前言随着社会的不断发展和经济的快速增长,各行各业都在不断追求效率和效益的提高,而作为生产基地的车间更是如此。
加强车间的操作管理制度,对于提高生产效率、保证产品质量、降低生产成本、提升员工素质等方面都有着重要的意义。
本文将结合实际情况,针对车间加强操作管理制度进行探讨。
二、加强员工培训1. 建立完善的培训计划首先,要建立完善的培训计划,针对不同岗位的员工制定相应的培训内容,包括生产操作技能、安全操作要求、质量控制标准等。
并要定期对员工进行培训,确保员工持续提升自身的技能水平。
2. 强化技能考核对于培训后的员工,要建立严格的技能考核制度,通过考核来评估员工的操作能力和技能水平,对未达标的员工进行再培训,确保员工的技能达到要求。
3. 推行师徒制在车间中推行师徒制,把有经验的老员工作为师傅指导新员工学习和成长,传授工作技能和经验,提高新员工的工作效率和质量。
三、加强生产管理1. 制定生产计划根据市场需求和生产能力,制定合理的生产计划,明确生产目标和任务,合理安排生产流程和生产周期,确保生产计划的顺利实施。
2. 加强过程管理对整个生产过程进行全程管理,包括生产准备、生产执行、质量检验等环节,建立健全的生产管理制度和流程,及时发现和解决生产中的问题,确保生产的顺利进行。
3. 强化质量控制对产品质量进行严格控制,制定质量标准和检测方法,建立质量追溯体系,加强产品质量检验和管理,确保产品质量达到要求。
四、加强设备维护1. 建立设备台账对车间内的设备进行统一管理,建立设备台账,记录设备的基本信息、维护记录、维修历史等,定期对设备进行检查和保养,确保设备的正常运转。
2. 制定维护计划根据设备的使用情况和维护要求,制定设备的维护计划,定期对设备进行保养和维修,及时发现和排除设备故障,确保设备的正常运转。
3. 强化设备管理加强设备的管理和维护,建立设备维护团队,定期进行设备巡检和维护,提高设备的利用率和性能,延长设备的使用寿命。
生产车间改善提效方案范文
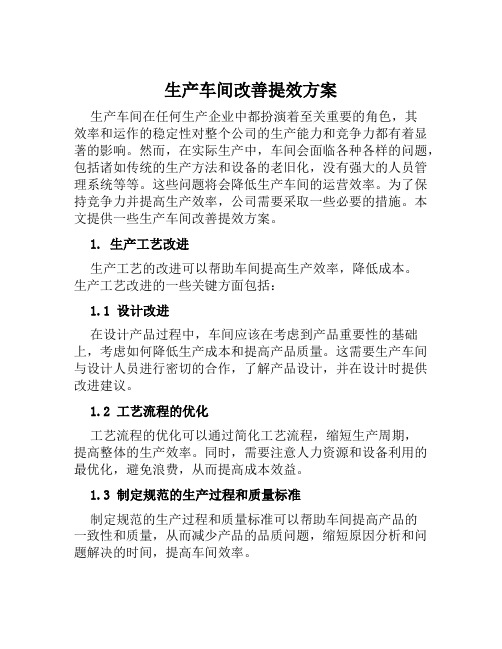
生产车间改善提效方案生产车间在任何生产企业中都扮演着至关重要的角色,其效率和运作的稳定性对整个公司的生产能力和竞争力都有着显著的影响。
然而,在实际生产中,车间会面临各种各样的问题,包括诸如传统的生产方法和设备的老旧化,没有强大的人员管理系统等等。
这些问题将会降低生产车间的运营效率。
为了保持竞争力并提高生产效率,公司需要采取一些必要的措施。
本文提供一些生产车间改善提效方案。
1. 生产工艺改进生产工艺的改进可以帮助车间提高生产效率,降低成本。
生产工艺改进的一些关键方面包括:1.1 设计改进在设计产品过程中,车间应该在考虑到产品重要性的基础上,考虑如何降低生产成本和提高产品质量。
这需要生产车间与设计人员进行密切的合作,了解产品设计,并在设计时提供改进建议。
1.2 工艺流程的优化工艺流程的优化可以通过简化工艺流程,缩短生产周期,提高整体的生产效率。
同时,需要注意人力资源和设备利用的最优化,避免浪费,从而提高成本效益。
1.3 制定规范的生产过程和质量标准制定规范的生产过程和质量标准可以帮助车间提高产品的一致性和质量,从而减少产品的品质问题,缩短原因分析和问题解决的时间,提高车间效率。
2. 运作管理改进在车间运作管理方面,可以采取一些措施,如:2.1 人员管理人员管理对生产车间的生产效率至关重要。
需要在一个强有力的人员管理系统下,确保车间人员熟悉企业的文化和价值观,增强团队合作意识,并且能够有效地利用员工的技能和能力。
2.2 设备管理设备是生产车间推动生产的关键要素。
车间管理人员应该从设备使用、检修和维护方面入手,提高设备利用率和寿命,避免设备故障和停机。
2.3 物料管理物料管理也是生产车间的一项重要工作。
车间需要一个科学的物料管理系统,以确保原材料,半成品和成品的准确性和可靠性,同时保证自身生产管理的有效性。
3. 待解决的问题在改善生产车间的过程中,管理人员应该深入挖掘一些为所知的或未知的问题。
以下是一些可能会影响车间效率的问题:•环境污染如果车间环境不良,将会给员工的身心健康以及生产效率带来很大的影响。
提能提效、降本增效、对标挖潜、扭亏减亏工作情况

提能提效、降本增效、对标挖潜、扭亏减亏工作情况近年来,随着市场竞争日益激烈,企业面临着提高生产效率、降低成本的重大挑战。
为此,我们不断积极探索各种方法和策略,以提高企业的竞争力,实现久远可持续的发展。
下面将分别就提能提效、降本增效、对标挖潜、扭亏减亏工作情况进行介绍和总结。
在提能提效方面,我们注重优化工作流程,提高员工能力和效率。
通过不断引进先进的技术设备和管理模式,我们努力提升产能,减少资源浪费。
同时,我们还注重培养员工的专业技能和团队协作能力,激发员工的潜力,使之更好地适应市场需求。
经过一段时间的努力,我们取得了显著成果,不断提高了生产效率和产品质量。
而在降本增效方面,我们持续推行成本管理和节约措施,严控固定成本和变动成本。
通过合理配置资源、降低能耗和减少废品率,我们成功地实现了成本的降低和效益的提高。
同时,我们还加强与供应商的合作,争取更优惠的采购价格和供应链的优化。
这些举措对于降低企业运营成本和提高利润起到了积极的推动作用。
在对标挖潜方面,我们积极学习借鉴行业优秀企业的经验和成功案例。
通过竞争对手的对比分析,我们不断改进自身的管理和运营模式,实现优胜劣汰的目标。
我们深入研究市场需求和消费者行为,加强市场调研和产品创新,做出更符合客户需求的产品。
这种对标挖潜的努力有助于我们更好地了解市场动态,提高竞争力和市场份额。
最后,在扭亏减亏方面,我们针对存在的亏损问题,采取有力措施进行纠正。
我们深入分析亏损原因,找出问题所在,并制定具体的解决方案。
通过削减不必要的费用支出、提高销售额和开发新的盈利业务,我们逐步扭亏为盈,实现了企业的可持续发展。
综上所述,提能提效、降本增效、对标挖潜、扭亏减亏是我们企业持续发展的关键工作。
我们将始终把提高效率、降低成本作为企业管理的重要目标,注重创新和学习,不断追求卓越。
我们相信,在全体员工的共同努力下,我们一定能够实现更加辉煌的业绩和壮大的规模。
车间深入管理如何提效、保质、降成本
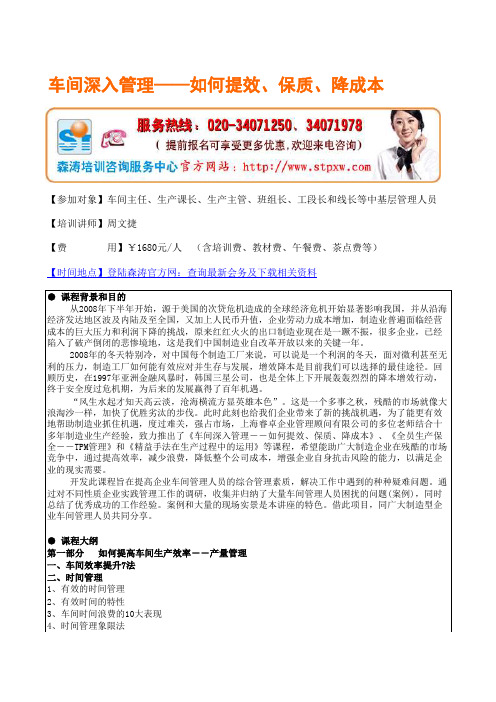
车间深入管理——如何提效、保质、降成本【参加对象】车间主任、生产课长、生产主管、班组长、工段长和线长等中基层管理人员【培训讲师】周文捷【费 用】¥1680元/人 (含培训费、教材费、午餐费、茶点费等)【时间地点】登陆森涛官方网:查询最新会务及下载相关资料● 课程背景和目的从2008年下半年开始,源于美国的次贷危机造成的全球经济危机开始显著影响我国,并从沿海经济发达地区波及内陆及至全国,又加上人民币升值,企业劳动力成本增加,制造业普遍面临经营成本的巨大压力和利润下降的挑战,原来红红火火的出口制造业现在是一蹶不振,很多企业,已经陷入了破产倒闭的悲惨境地,这是我们中国制造业自改革开放以来的关键一年。
2008年的冬天特别冷,对中国每个制造工厂来说,可以说是一个利润的冬天,面对微利甚至无利的压力,制造工厂如何能有效应对并生存与发展,增效降本是目前我们可以选择的最佳途径。
回顾历史,在1997年亚洲金融风暴时,韩国三星公司,也是全体上下开展轰轰烈烈的降本增效行动,终于安全度过危机期,为后来的发展赢得了百年机遇。
“风生水起才知天高云淡,沧海横流方显英雄本色”。
这是一个多事之秋,残酷的市场就像大浪淘沙一样,加快了优胜劣汰的步伐。
此时此刻也给我们企业带来了新的挑战机遇,为了能更有效地帮助制造业抓住机遇,度过难关,强占市场,上海睿卓企业管理顾问有限公司的多位老师结合十多年制造业生产经验,致力推出了《车间深入管理――如何提效、保质、降成本》、《全员生产保全――TPM管理》和《精益手法在生产过程中的运用》等课程,希望能助广大制造企业在残酷的市场竞争中,通过提高效率,减少浪费,降低整个公司成本,增强企业自身抗击风险的能力,以满足企业的现实需要。
开发此课程旨在提高企业车间管理人员的综合管理素质,解决工作中遇到的种种疑难问题。
通过对不同性质企业实践管理工作的调研,收集并归纳了大量车间管理人员困扰的问题(案例),同时总结了优秀成功的工作经验。
提升车间管理效率的方法
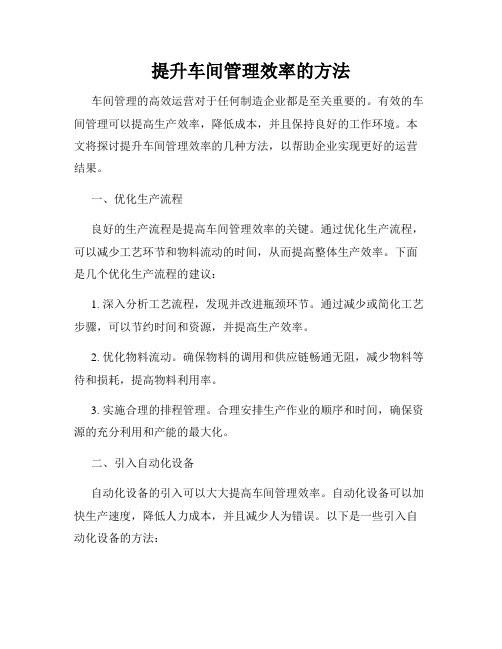
提升车间管理效率的方法车间管理的高效运营对于任何制造企业都是至关重要的。
有效的车间管理可以提高生产效率,降低成本,并且保持良好的工作环境。
本文将探讨提升车间管理效率的几种方法,以帮助企业实现更好的运营结果。
一、优化生产流程良好的生产流程是提高车间管理效率的关键。
通过优化生产流程,可以减少工艺环节和物料流动的时间,从而提高整体生产效率。
下面是几个优化生产流程的建议:1. 深入分析工艺流程,发现并改进瓶颈环节。
通过减少或简化工艺步骤,可以节约时间和资源,并提高生产效率。
2. 优化物料流动。
确保物料的调用和供应链畅通无阻,减少物料等待和损耗,提高物料利用率。
3. 实施合理的排程管理。
合理安排生产作业的顺序和时间,确保资源的充分利用和产能的最大化。
二、引入自动化设备自动化设备的引入可以大大提高车间管理效率。
自动化设备可以加快生产速度,降低人力成本,并且减少人为错误。
以下是一些引入自动化设备的方法:1. 投资先进的生产设备。
选择能够实现自动化操作和高效产能的设备,以提高生产效率。
2. 引入机器人技术。
机器人可以执行重复性高、精度要求高的任务,大幅提高生产效率。
3. 使用自动化控制系统。
通过自动控制系统,可以实现对生产过程的监控和调节,提高生产质量和效率。
三、推行员工培训与激励车间管理效率不仅仅依赖于设备和流程,员工的素质和动力也是至关重要的。
以下是一些培训与激励员工的方法:1. 提供全面的岗位培训。
确保员工掌握所需的技能和知识,提高其操作能力和工作效率。
2. 鼓励员工学习和创新。
为员工提供学习和成长的机会,激发他们的创新潜力,带来更好的生产效益。
3. 设立奖励和激励机制。
通过设立奖励和激励措施,激励员工积极性和工作动力,提高他们的工作效率。
四、建立有效的沟通机制有效的沟通是提高车间管理效率的关键。
良好的沟通可以减少误解和冲突,提高工作效率和协作效果。
以下是一些建立有效沟通机制的方法:1. 建立定期的团队会议。
生产车间管理方案
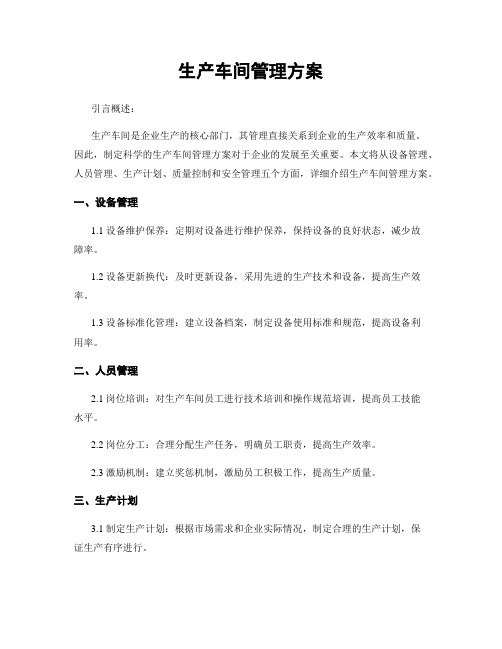
生产车间管理方案引言概述:生产车间是企业生产的核心部门,其管理直接关系到企业的生产效率和质量。
因此,制定科学的生产车间管理方案对于企业的发展至关重要。
本文将从设备管理、人员管理、生产计划、质量控制和安全管理五个方面,详细介绍生产车间管理方案。
一、设备管理1.1 设备维护保养:定期对设备进行维护保养,保持设备的良好状态,减少故障率。
1.2 设备更新换代:及时更新设备,采用先进的生产技术和设备,提高生产效率。
1.3 设备标准化管理:建立设备档案,制定设备使用标准和规范,提高设备利用率。
二、人员管理2.1 岗位培训:对生产车间员工进行技术培训和操作规范培训,提高员工技能水平。
2.2 岗位分工:合理分配生产任务,明确员工职责,提高生产效率。
2.3 激励机制:建立奖惩机制,激励员工积极工作,提高生产质量。
三、生产计划3.1 制定生产计划:根据市场需求和企业实际情况,制定合理的生产计划,保证生产有序进行。
3.2 生产进度监控:及时监控生产进度,发现问题及时调整,确保生产计划的顺利实施。
3.3 资源调配:合理分配生产资源,确保生产过程中各项资源的充分利用。
四、质量控制4.1 品质检验:建立完善的质量检验体系,对产品进行全面检测,确保产品质量。
4.2 质量管理:建立质量管理制度,强调全员参与,持续改进,提高产品质量。
4.3 不良品处理:建立不良品处理机制,及时处理不良品,防止不良品流入市场。
五、安全管理5.1 安全意识培训:对生产车间员工进行安全意识培训,提高员工安全意识。
5.2 安全设施完善:确保生产车间安全设施完善,消防设备齐全,安全通道畅通。
5.3 安全检查:定期进行安全检查,发现安全隐患及时处理,确保生产车间安全生产。
结语:生产车间管理方案是企业生产的重要保障,只有做好生产车间管理,才能提高生产效率、保证产品质量、确保生产安全。
企业应根据自身情况,制定科学的生产车间管理方案,并不断完善和优化,以适应市场需求和企业发展。
车间现场量化管理制度

车间现场量化管理制度一、制度目的为了提高车间现场管理效率,确保生产生产过程的稳定性和质量,制定车间现场量化管理制度。
二、管理范围本制度适用于公司所有生产车间。
三、管理要求1. 车间生产计划定量化:每个生产车间负责人应根据公司生产计划,制定每日、每周、每月的生产计划,并明确任务分工和责任人员。
2. 车间设备设施定量化:每个生产车间负责人应及时对车间设备设施进行检查和保养,确保设备设施的正常运转,定期清点和管理车间工具。
3. 车间人员管理定量化:每个生产车间负责人应对车间人员进行编制管理,明确每个人员的职责和任务,并进行考核和激励。
4. 车间作业规范化:每个生产车间负责人应制定作业规范,规范作业程序和作业流程,确保作业质量和效率。
5. 车间质量管理定量化:每个生产车间负责人应建立质量管理制度,制定质量检测标准和质量控制措施,确保产品质量达标。
6. 车间安全管理定量化:每个生产车间负责人应建立安全管理制度,做好安全教育和安全培训,制定安全检查制度和应急预案,确保车间安全生产。
7. 车间环境管理定量化:每个生产车间负责人应对车间环境进行管理,保持车间整洁、无尘、通风良好,确保员工的健康和安全。
四、管理流程1. 车间生产计划定量化流程:(1)确定生产计划需求。
(2)分解生产计划任务。
(3)制定生产计划。
(4)下发生产任务。
(5)跟踪执行情况。
(6)总结评估计划实施。
2. 车间设备设施定量化流程:(1)设备设施清点。
(2)设备设施保养。
(3)设备设施维修。
(4)设备设施更新。
3. 车间人员管理定量化流程:(1)编制车间组织结构。
(2)制定人员职责和任务。
(3)进行人员考核和激励。
4. 车间作业规范化流程:(1)规范作业程序和流程。
(2)培训作业人员。
(3)执行作业规范。
5. 车间质量管理定量化流程:(1)建立质量管理制度。
(2)制定质量检测标准。
(3)执行质量控制措施。
6. 车间安全管理定量化流程:(1)建立安全管理制度。
车间解决方案

车间解决方案
《车间解决方案》
在现代工业生产中,车间是生产流程中至关重要的一环。
为了提高生产效率和质量,许多企业都在不断探索和实施各种车间解决方案。
这些解决方案涉及技术、管理、人力资源等多个领域,旨在提高车间生产效率、降低成本、改善产品质量。
首先,技术方面的解决方案是车间改进的重要一环。
自动化设备、智能制造技术、数字化生产系统等技术的应用可以大大提高生产效率,减少人为操作错误,降低生产成本。
例如,通过引入机器人自动组装生产线,可以提高装配速度和精度,降低废品率,减少人力成本。
其次,管理方面的解决方案也是关键。
有效的生产计划、物料管理、设备维护和保养,都可以帮助车间提高运转效率。
并且,通过引入现代化的生产管理系统,可以实现生产过程的实时监控和数据分析,帮助企业及时发现问题并采取措施解决。
此外,人力资源方面的解决方案同样不可忽略。
对车间员工进行培训,提高他们的生产技能和质量意识,对于提高生产效率至关重要。
同时,合理的工资政策和激励机制也能够激发员工的积极性,促进车间的稳定发展。
总之,车间解决方案是一个综合性的课题,需要技术、管理和人力资源等多方面的努力。
只有综合运用各种解决方案,才能实现车间生产水平的全面提升。
希望更多的企业能够关注这一
领域,努力寻求更多更好的解决方案,促进工业生产的持续发展。
工作要提效
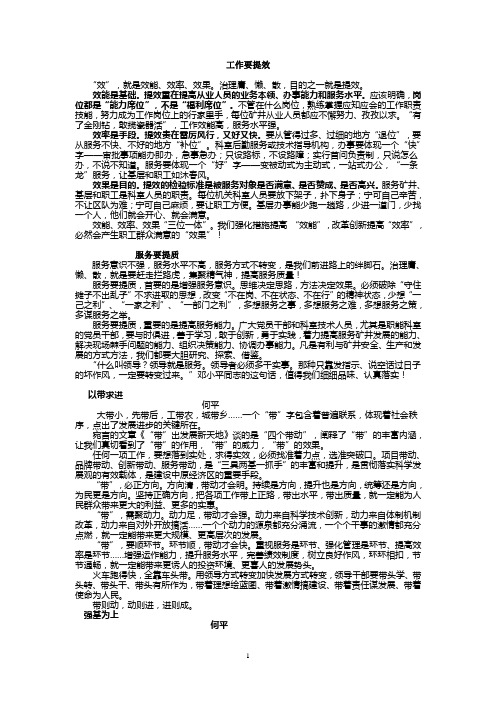
工作要提效“效”,就是效能、效率、效果。
治理庸、懒、散,目的之一就是提效。
效能是基础。
提效重在提高从业人员的业务本领、办事能力和服务水平。
应该明确,岗位都是“能力席位”,不是“福利席位”。
不管在什么岗位,熟练掌握应知应会的工作职责技能,努力成为工作岗位上的行家里手,每位矿井从业人员都应不懈努力、孜孜以求。
“有了金刚钻,敢揽瓷器活”,工作效能高,服务水平强。
效率是手段。
提效贵在雷厉风行,又好又快。
要从管得过多、过细的地方“退位”,要从服务不快、不好的地方“补位”。
科室后勤服务或技术指导机构,办事要体现一个“快”字——审批事项能办即办,急事急办;只设路标,不设路障;实行首问负责制,只说怎么办,不说不知道。
服务要体现一个“好”字——变被动式为主动式,一站式办公,“一条龙”服务,让基层和职工如沐春风。
效果是目的。
提效的检验标准是被服务对象是否满意、是否赞成、是否高兴。
服务矿井、基层和职工是科室人员的职责。
每位机关科室人员要放下架子,扑下身子;宁可自己辛苦,不让区队为难;宁可自己麻烦,要让职工方便。
基层办事能少跑一趟路,少进一道门,少找一个人,他们就会开心、就会满意。
效能、效率、效果“三位一体”。
我们强化措施提高“效能”,改革创新提高“效率”,必然会产生职工群众满意的“效果”!服务要提质服务意识不强,服务水平不高,服务方式不转变,是我们前进路上的绊脚石。
治理庸、懒、散,就是要赶走拦路虎,集聚精气神,提高服务质量!服务要提质,首要的是增强服务意识。
思维决定思路,方法决定效果。
必须破除“守住摊子不出乱子”不求进取的思想,改变“不在岗、不在状态、不在行”的精神状态,少想“一己之利”、“一家之利”、“一部门之利”,多想服务之事,多想服务之难,多想服务之策,多谋服务之举。
服务要提质,重要的是提高服务能力。
广大党员干部和科室技术人员,尤其是职能科室的党员干部,要与时俱进,善于学习,敢于创新,勇于实践,着力提高服务矿井发展的能力、解决现场棘手问题的能力、组织决策能力、协调办事能力。
车间管理提升方案
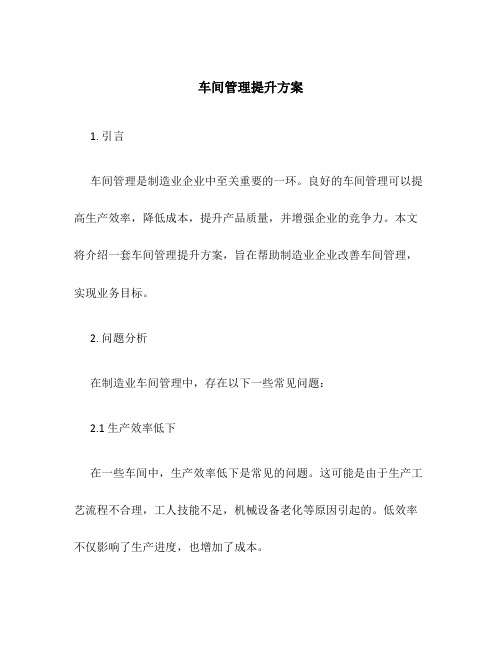
车间管理提升方案1. 引言车间管理是制造业企业中至关重要的一环。
良好的车间管理可以提高生产效率,降低成本,提升产品质量,并增强企业的竞争力。
本文将介绍一套车间管理提升方案,旨在帮助制造业企业改善车间管理,实现业务目标。
2. 问题分析在制造业车间管理中,存在以下一些常见问题:2.1 生产效率低下在一些车间中,生产效率低下是常见的问题。
这可能是由于生产工艺流程不合理,工人技能不足,机械设备老化等原因引起的。
低效率不仅影响了生产进度,也增加了成本。
2.2 缺乏质量控制一些车间在质量控制方面存在缺陷。
由于缺乏有效的质量管理系统和监测手段,很难发现产品质量问题,导致产品质量不稳定。
2.3 信息沟通不畅信息沟通不畅是车间管理中常见的问题之一。
信息传递不及时,导致生产计划、工艺改进、问题反馈等方面存在滞后现象。
这给生产运营带来了困扰,阻碍了问题的及时解决。
3. 车间管理提升方案3.1 生产效率提升为了提高生产效率,可以采取以下措施:•优化生产工艺流程:分析工艺流程中的瓶颈,通过优化和简化流程,减少不必要的步骤,提高生产效率。
•培训提升员工技能:通过培训和学习计划,提高员工的专业知识和技能水平,使其能够更好地适应生产工艺。
•更新升级机械设备:使用新的机械设备能够提高生产效率,减少故障停机时间,保证生产顺利进行。
3.2 质量控制改进为了改进质量控制,可以采取以下措施:•建立质量管理体系:制定一套完善的质量管理流程和标准,确保每个生产环节都能按照要求进行。
•强化质量检测:引进更先进的质量检测设备,提高检测效率和准确性。
并且建立严格的产品质量抽检制度,及时发现和处理质量问题。
•注重员工质量意识:加强员工质量培训,提高员工的质量意识和责任心,使其在生产过程中能够主动发现并解决质量问题。
3.3 加强信息沟通为了加强车间内部的信息沟通,可以采取以下措施:•建立信息发布平台:建立一个集中的信息发布平台,包括生产计划、工艺改进、问题反馈等信息,实现信息的及时发布和集中管理。
强化内部管理 降低生产成本 提升经济效益

强化内部管理降低生产成本提升经济效益保持企业安全稳定良好发展态势(2021年7月19日)为应对严峻的经济形势,切实强化成本费用管理。
厂领导班子于2021年7月19日下午在三楼会议室召开了中心组学习会议。
会议学习贯彻了《关于应对经济危机加强成本管理的通知》[2021]8号文件精神,讨论了目前影响我厂生产成本控制的关键因素,明确了下半年经营管理工作思路。
现将会议主要内容通报如下:一、加强组织领导,建立成本费用管理工作机制为保证厂成本费用管理工作顺利实施,会议研究决定,成立以党政主要领导为组长,厂副职为副组长的成本费用管理工作领导小组。
成员有下列人员和单位组成:厂副总师、综合科、调度室、机电科、经营科、计划科、物管中心、生产技术科、财务科、人力资源科、审计科、纪检监察科、宣教科等科室负责人。
领导小组下设办公室,办公室设在财务科,aaa同志兼任办公室主任。
领导小组负责厂成本费用管理工作的协调、部署,对成本费用管理成效直接负责。
领导小组办公室负责制定厂成本费用管理办法,明1确各单位管理职责,研究提出成本管理措施并具体实施;组织成本管理的专项工作及降本增效活动,指导、督促、检查厂所属单位成本管理工作,协调处理成本管理工作中存在的问题;对厂成本管理工作进行评价考核。
二、坚定不移抓安全,全力以赴保稳定当前是十八大召开前的敏感时期,也是应对严峻经济形势的关键时期,广大干部职工要深刻认清形势发展对安全稳定工作提出的新要求。
在安全工作上,要锁定“三零”目标,牢记“三不四可”,深入落实“三基三抓一追究”。
按照集团《关于加强煤矿安全生产管理的特别规定》中平[2021]34号文件中有关要求,扎实做好安全工作,保持安全高压态势,确保安全工作可控、能控、在控。
稳定是企业压倒一切的政治任务。
越是经济形势困难的时候,越要发挥好基层党支部的战斗堡垒作用和共产党员的先锋模范作用,政工部门、基层党支部要积极主动做好职工群众的思想政治工作,全力以赴保证企业和谐稳定。
车间管理方法

车间管理方法车间管理是企业生产运营中非常重要的一环,它直接关系到生产效率、产品质量、成本控制等方面。
因此,良好的车间管理方法对企业的发展至关重要。
下面将就车间管理方法进行详细介绍。
首先,合理规划车间布局是车间管理的重要一环。
合理的车间布局可以提高生产效率,减少生产过程中的浪费,降低生产成本。
在规划车间布局时,需要考虑设备摆放位置、原材料存放位置、半成品和成品存放位置等方面,以确保生产流程顺畅,提高生产效率。
其次,建立科学的生产计划是车间管理的关键。
科学的生产计划可以帮助企业合理安排生产任务,提高生产效率,减少生产周期,及时交付产品。
生产计划需要充分考虑原材料供应、生产设备状况、人力资源等因素,确保生产计划的可行性和有效性。
另外,严格执行标准化操作是车间管理的重要手段。
通过制定标准化操作流程和作业指导书,可以规范生产操作,提高产品质量,减少因操作失误导致的质量问题。
同时,标准化操作也有利于培训新员工,提高员工操作技能,确保生产过程稳定、可控。
此外,加强车间安全管理也是不可或缺的一环。
车间作为生产现场,安全问题关乎员工的生命安全和企业的稳定生产。
因此,建立健全的安全管理制度,加强安全教育培训,定期进行安全检查和隐患排查,及时消除安全隐患,确保车间生产安全。
最后,建立高效的沟通协调机制是车间管理的关键。
车间内部各部门之间、员工之间以及车间与其他部门之间的沟通协调,直接关系到生产运营的顺畅与否。
因此,建立高效的沟通协调机制,促进信息畅通,协调各方利益关系,提高工作效率,是车间管理的重要内容。
总之,良好的车间管理方法对企业的生产运营至关重要。
通过合理规划车间布局、科学制定生产计划、严格执行标准化操作、加强安全管理以及建立高效的沟通协调机制,可以提高生产效率,降低生产成本,保证产品质量,推动企业持续健康发展。
希望以上车间管理方法对您有所帮助。
车间生产工作总结汇报:质量管理与生产效率提升
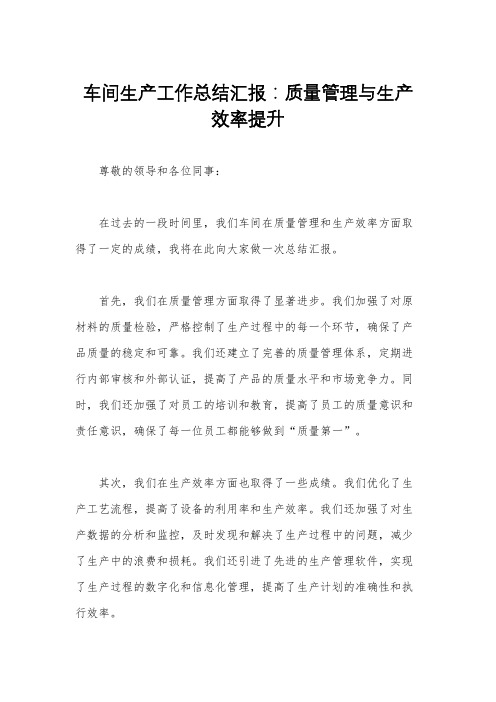
车间生产工作总结汇报:质量管理与生产
效率提升
尊敬的领导和各位同事:
在过去的一段时间里,我们车间在质量管理和生产效率方面取得了一定的成绩,我将在此向大家做一次总结汇报。
首先,我们在质量管理方面取得了显著进步。
我们加强了对原材料的质量检验,严格控制了生产过程中的每一个环节,确保了产品质量的稳定和可靠。
我们还建立了完善的质量管理体系,定期进行内部审核和外部认证,提高了产品的质量水平和市场竞争力。
同时,我们还加强了对员工的培训和教育,提高了员工的质量意识和责任意识,确保了每一位员工都能够做到“质量第一”。
其次,我们在生产效率方面也取得了一些成绩。
我们优化了生产工艺流程,提高了设备的利用率和生产效率。
我们还加强了对生产数据的分析和监控,及时发现和解决了生产过程中的问题,减少了生产中的浪费和损耗。
我们还引进了先进的生产管理软件,实现了生产过程的数字化和信息化管理,提高了生产计划的准确性和执行效率。
总的来说,我们在质量管理和生产效率方面取得了一些成绩,但也存在一些问题和不足。
我们将继续努力,进一步加强质量管理和生产效率的工作,确保产品质量的稳定和生产效率的持续提升。
希望在各位的支持和帮助下,我们能够取得更好的成绩,为企业的发展做出更大的贡献。
谢谢大家!。
车间深入管理提效 ppt课件

制造/生管
制造/工程
原因多元的管理 盲点:
1.非主要材料断 料才是问题
2. 前制程排配 与质量造成 待料
3. 人力安排
生管/品管/工程
✓ 断料与待料是 制造需要严格 督促生管与质 量单位
✓ 工程单位消耗 制造资源的管 理
✓ 快速换线是持 续改善的机会
C D E ACD
E A
setup
1
Click to add工T时itle说明
项目
总时间 负荷时间 作业时间 标准产出工时
说明
设备可提供的总时间 可用于排产的时间
公式
周:7D*24H; 月:日历天数*24H
总时间-未排配
用于生产的时间
总时间-停机时间-未排配
生产产品所耗用的时间 产品数量*T.T/3600
3 准Cl确ick数to a据dd收Tit集le 及机制运作
1.详细生产记录 2.异常处理流程 3.一套表单 4.各司其职 5.资讯化系统
4 Click to aIEdd七Tit大le 手法
①流程法 ②人机法 ③动改法 ④双手法 ⑤防呆法 ⑥五五法 ⑦抽查法
4 ClicIkEto手ad法d T一itle﹕流程法
Uti li n z1atTio ot.oaR pl eurna.ttiimoen Run Set uEpng
Utilizn2atTioo.toaplera .titm ioen Run
Utilizan3tioUpDown
2 Cl满ick载to稼ad动d T率itle/设备可动率
满产稼动率是指设备可提供的最大产能状况下的稼动率
标准良品产出工时 生产良品所耗用的工时 良品数量*T.T/3600
车间管理活动方案
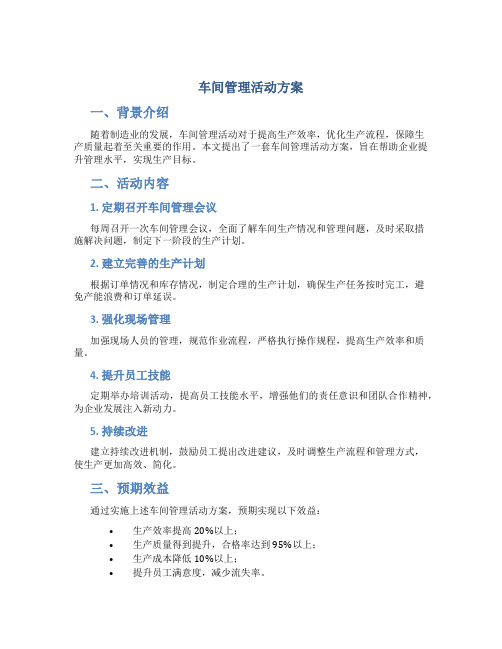
车间管理活动方案
一、背景介绍
随着制造业的发展,车间管理活动对于提高生产效率,优化生产流程,保障生
产质量起着至关重要的作用。
本文提出了一套车间管理活动方案,旨在帮助企业提升管理水平,实现生产目标。
二、活动内容
1. 定期召开车间管理会议
每周召开一次车间管理会议,全面了解车间生产情况和管理问题,及时采取措
施解决问题,制定下一阶段的生产计划。
2. 建立完善的生产计划
根据订单情况和库存情况,制定合理的生产计划,确保生产任务按时完工,避
免产能浪费和订单延误。
3. 强化现场管理
加强现场人员的管理,规范作业流程,严格执行操作规程,提高生产效率和质量。
4. 提升员工技能
定期举办培训活动,提高员工技能水平,增强他们的责任意识和团队合作精神,为企业发展注入新动力。
5. 持续改进
建立持续改进机制,鼓励员工提出改进建议,及时调整生产流程和管理方式,
使生产更加高效、简化。
三、预期效益
通过实施上述车间管理活动方案,预期实现以下效益:
•生产效率提高20%以上;
•生产质量得到提升,合格率达到95%以上;
•生产成本降低10%以上;
•提升员工满意度,减少流失率。
四、总结
车间管理是企业生产的关键环节,通过规范管理、优化流程、提升员工素质,可以有效提高生产效率、提高产品质量,实现企业的良性发展。
希望本文提出的车间管理活动方案能够对贵企业的生产管理工作有所启发,切实提高企业的竞争力和盈利能力。
以上是本文的内容,希望对贵企业有所帮助。
提效增效实施方案
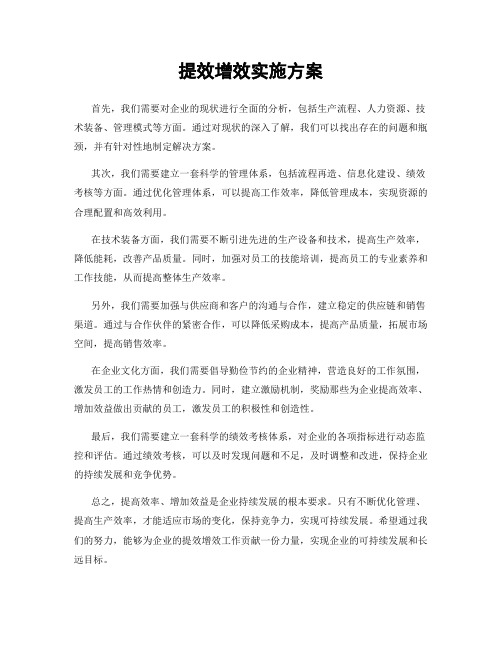
提效增效实施方案
首先,我们需要对企业的现状进行全面的分析,包括生产流程、人力资源、技术装备、管理模式等方面。
通过对现状的深入了解,我们可以找出存在的问题和瓶颈,并有针对性地制定解决方案。
其次,我们需要建立一套科学的管理体系,包括流程再造、信息化建设、绩效考核等方面。
通过优化管理体系,可以提高工作效率,降低管理成本,实现资源的合理配置和高效利用。
在技术装备方面,我们需要不断引进先进的生产设备和技术,提高生产效率,降低能耗,改善产品质量。
同时,加强对员工的技能培训,提高员工的专业素养和工作技能,从而提高整体生产效率。
另外,我们需要加强与供应商和客户的沟通与合作,建立稳定的供应链和销售渠道。
通过与合作伙伴的紧密合作,可以降低采购成本,提高产品质量,拓展市场空间,提高销售效率。
在企业文化方面,我们需要倡导勤俭节约的企业精神,营造良好的工作氛围,激发员工的工作热情和创造力。
同时,建立激励机制,奖励那些为企业提高效率、增加效益做出贡献的员工,激发员工的积极性和创造性。
最后,我们需要建立一套科学的绩效考核体系,对企业的各项指标进行动态监控和评估。
通过绩效考核,可以及时发现问题和不足,及时调整和改进,保持企业的持续发展和竞争优势。
总之,提高效率、增加效益是企业持续发展的根本要求。
只有不断优化管理、提高生产效率,才能适应市场的变化,保持竞争力,实现可持续发展。
希望通过我们的努力,能够为企业的提效增效工作贡献一份力量,实现企业的可持续发展和长远目标。
加强基础工作深化属地管理

加强基础工作深化属地管理把“强达争”活动不断引向深入今年以来,我们紧紧围绕“强、达、争”主题实践活动的开展,加强基础工作,深化属地管理,不断提升管理水平,引领全体员工以实现“四零”目标为己任,努力为钻井生产提速提效提供优质技术服务,保证了各项工作的平稳运行。
下面,结合“强、达、争”活动的开展谈一下机属地管理的经验。
一、加大各项管理制度的落实为保证分公司及项目部各项管理文件在项目部属地内的实施,机械加工车间坚持把不同时期安全环保工作重点和需要掌握的内容,及时下发给车间管理人员、班组员工,采用集中学习、岗位自学和督查考试等方法,使各项安全环保工作落实到各个岗位。
还结合工作实际,进一步修订完善了车间班组所涉及到的共其中一些岗位HSE职责,达到无论从事何种作业或操作何种设备,都有岗位HSE作为约束机制保障,并督促各级员工无论做任何工作,都必须履行各级的岗位HSE职责和属地责任,实现了各尽其职,各负其责,从而进一步健全了以“管理制度”为核心内容的体系推进基础工作。
二、加重处罚力度三、加强属地管理卡的应用为全面推广“我的属地我管理、我的区域我负责”的管理理念,根据员工所在岗位,全面推行属地管理卡,明确各岗位在HSE管理体系推进中的职责,做好内部职责分工,并通过各种岗位培训,使车间管理人员、操作人员掌握本岗位的相关知识及要求。
车间员工根据属地管理卡内容,更加熟知自身属地区域内的设备设施和区域环境,自觉开展岗位巡检、自觉识别属地风险,并重点进行防范和控制,从而更加规范了作业规程,也从中提高自身的安全意识,使属地责任由人的强制管理向制度化管理迈进了一大步。
深化属地管理的工作实践使我们体会到,深入开展好“强、达、争”主题实践活动,是提高基础组织建设、基础管理水平和员工队伍素质的坚强保证,是企业安全、高效、和谐发展的动力。
通过活动的开展,使全员在遵章守纪、安全生产、服务质量等方面都有了新的提升。
诚然,和兄弟单位相比,我们还存在许多不足。
- 1、下载文档前请自行甄别文档内容的完整性,平台不提供额外的编辑、内容补充、找答案等附加服务。
- 2、"仅部分预览"的文档,不可在线预览部分如存在完整性等问题,可反馈申请退款(可完整预览的文档不适用该条件!)。
- 3、如文档侵犯您的权益,请联系客服反馈,我们会尽快为您处理(人工客服工作时间:9:00-18:30)。
制程
烤漆 (?%)
Unscheduled Time
Down Time
Setup Time
类别
单次 周次 总时 时间 数 间
类别
单次 周次 总时 时间 数 间
类别
单次 周次 总时 时间 数 间
人员吃饭
设备保养
首件
周末休息
设备异常
换线
平时休息
工单切换
成型 (?%)
2
Click to add T练itle习
4.分析搬运、物流状况,调整布局,以减少搬 运,提高物流效率
5.整理加工工序流程,使其合理、平衡、经济
4 流Cl程ick法to a工dd具Tit:le 流程程序图
4 Click程to a序dd分Tit析le 的符号
序号 记号
意
义
1
〇
加工:改变对象的物理、化学状态的过 程,或进行装配与分解的过程
UP
DOWN
Run
setup ENG
Idle
down
repair
maintain
Not scheduled
3
制造的设备单位管理重点: 检讨故障发生的
频次与时长:
✓ 设备的可动率提升
1.设备问题
(Downtime的减少) 2.维修能力
✓ 定期保养的成效(保养过 3.保养问题
度与保养不足)
4.合理的目标
Total operation time
UP
DOWN
Run 6
setup ENG 5
Idle
down
repair
maintain
Not scheduled
制造与支持单位
4
的管理重点:
缩短换线(初件) 时间: 1.换线流程合理 与标准化(快速 换线) 2.初件一次成功 率与换线能力 3.生产排配优化
量试与工程借机 管理 1.合理的预估 2.量试效率 3.使用者付费 4.落实资源使用 监督
E A
1 COlicEkEto趋ad势d T及itle工时结构图
2 Click to设ad备d T稼itle动率定义
Total operating time
Run
setup ENG
Idle
down
repair
maintain
Not scheduled
UP
DOWN
Total operating time:可供工时﹐其中每台机日可 供工时為24hr,周可供工时为7*24hr Up time:处于开机状态的时间 Down time:处于未开机状态的时间 Not scheduled:机台未排配时间 Run:正常生产工时﹐直接产出产品和创造价值 Set up:机台开机﹐调机﹐以及换模工时 ENG:工程验证﹐包括试模与量试工时等 Idle:因断料﹑品质﹑人力等原因造成损失工时 Down:机故﹑模故造成损失工时 Repair:机台维修工时 Maintain:机台保养工时
1
Click to aOddETEit时le 间结构
总时间(A)
负荷时间(B)
计划停机损失
作业时间(C)
非计划停机损失
标准产出工时(D)
速度损失
标准良品产出工时(E) 不良品损失
down repair
Not scheduled
maintain
ENG
Run
Idle
OEE =时间稼动率 * 性能稼动率 * 良率
0 Click成to a本dd结Tit构le 与利润
售价 成本ห้องสมุดไป่ตู้
固定成本
管销研成本 加工成本 材料成本
利润 研发费用 销售费用 管理费用 耗能以及生产杂项费用 固定资产折旧 间接员工 直接员工 间接材料 直接材料
产品成本
变动成本
0 企Cl业ick增to a加dd利Tit润le 的三个途径
项目
营收 产品成本
✓ 故障结果分析,找到保养 的重点
✓ 提升维修效果与效率(设
备维修能力的提升)
*制造/设备
2
1
检讨定期保养 的频次与时长:
1.流程 2.项目 3.耗用的材料 及零配件(CD) 4.合理的目标
影响稼动 率高低的 主因:由 制造以外 的单位来 努力
*制造/设备
业务
3 C改lic善k to设a备dd异Tit常le 的管理循环
Max.Utilization TotalOprationTime - EssentialUnscheduledTime - EssentialDownTime - EssentialSetupTime TotalOprationTime
➢Total OperationTime:每周7x24小时 ➢Essential UnscheduledTime:规范无法排产时间。
产能规划
D
责任单位
纪录与收 集实际值
生产日报/ MES/SFC
P
责任单位 修订目标 或预估值
Increase
Capacity 提供低成本与
稳定的产能
C
责任单位
分析与檢 討差异
A
责任单位 进行改善
3 C设lic备k to稼a动dd率Tit改le 善方向(1/2)
Total operation time
责任部门
N/A 市场/销售
设备 产发 设备 设备 生产 生产 生产 生产 生产/设备
1 Click toOaPddET时itle间结构
记薪人力工时(A)
投入人力工时(B)
产出人力工时(C)
效率损失
标准良品产出工时(E) 不良品损失
停线损失
OPE =人力工时效率 * 作业效率 * 良率
BCE ABC
把加工工艺流程划分为加工、检查 、搬运、等待和贮存等五种状态加
以记录和分析。
4 Click to a流dd程Tit法le 目的
1.加工工序中是否存在不合理﹑停滞等作業现 象,取消它们
2.合并一些过于细分或重复的工作,提高产线 平衡率
3.检查是否有导致相同作业动作无价值重复的 作业程序,改变它们避免重複作业
标准良品产出工时 生产良品所耗用的工时 良品数量*T.T/3600
1
Click to 时add间T损itle失说明
损失类别
停机损失
性能损失 不良品损失
损失名称
计划停机
非计划停机 性能损失 不良品损失
内容说明
节假日未排配计划 定单缺失未排配计划 机台保养未排配计划 新产品导入未排配 设备/模具等故障异常工时 设备/模具等维修异常工时 因人员/缺料等异常工时 换线/调机等工时损失 换料造成的损失 机台未停机的暂停 制造不良品/重工等工时
制造/生管
制造/工程
原因多元的管理 盲点:
1.非主要材料断 料才是问题
2. 前制程排配 与质量造成 待料
3. 人力安排
生管/品管/工程
✓ 断料与待料是 制造需要严格 督促生管与质 量单位
✓ 工程单位消耗 制造资源的管 理
✓ 快速换线是持 续改善的机会
3 准Cl确ick数to a据dd收Tit集le 及机制运作
2 Cl满ick载to稼ad动d T率itle的目的/作用
➢满产稼动代表管理基准而非一个绝 对值
➢工厂定单充足状况下,实际稼动率 的优劣评价
➢不同制程横向比较 ➢设定目标管理的基准 ➢计算标准成本和客户报价的依据
2
Click to a讨dd论Tit及le 案例
➢各标准/目标如何定义?谁来定义? ➢自己所在生产制程满产稼动率是多少? ➢烤漆?冲压?CNC?成型?组装?......
某成型機CT 10.9S,12小时生产过程如下图,产出良品 2700片,不良品50片,进行OEE分析
8:00
1
10:00
12:00
14:00
16:00
18:00
20:00
8:008:30 交接班 (A)
11:0011:30 换线
(B)
12:0013:00 午餐
(C)
15:3016:00 断料
(D)
17:0018:00 晚餐
(设备总合效率,缩写成OEE)
– OEE是实践TPM过程中,衡量设备关连损失, 并加以改善,以达成设备效率化的一种方法。
– OEE的组成是由三个指标所组成
• 监控设备的妥善程度:时间稼动率(Availability Rate) • 了解设备运作绩效:性能稼动率(Performance Rate) • 设备产出产品质量状况:良率(Quality Rate)
CDE ACD
E A
setup
1
Click to add工T时itle说明
项目
总时间 负荷时间 作业时间 标准产出工时
说明
设备可提供的总时间 可用于排产的时间
公式
周:7D*24H; 月:日历天数*24H
总时间-未排配
用于生产的时间
总时间-停机时间-未排配
生产产品所耗用的时间 产品数量*T.T/3600
1.详细生产记录 2.异常处理流程 3.一套表单 4.各司其职 5.资讯化系统
4 Click to aIEdd七Tit大le 手法
①流程法 ②人机法 ③动改法 ④双手法 ⑤防呆法 ⑥五五法 ⑦抽查法
4 ClicIkEto手ad法d T一itle﹕流程法
流程法全称流程分析法,它是以产 品或零件的加工制造全过程为对象,
Run Utilization1 Total.operation.time
Utilization2
Run Setup Eng Total.operation.time
Utilization3
Up