我国钢铁企业的炼铁技术
炼铁技术
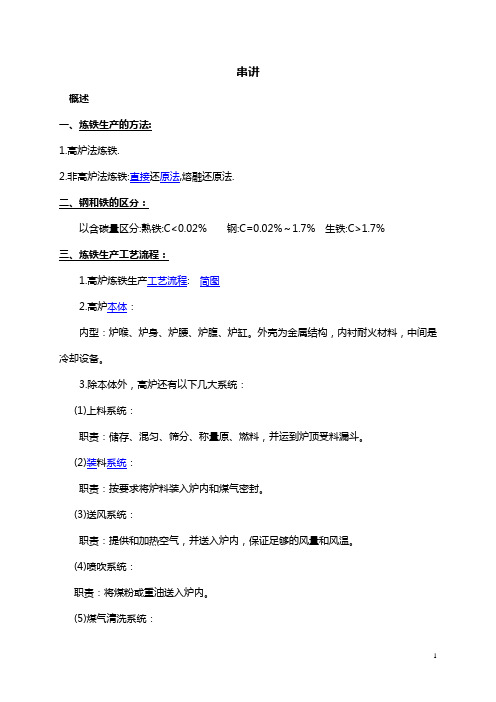
串讲概述一、炼铁生产的方法:1.高炉法炼铁.2.非高炉法炼铁:直接还原法,熔融还原法.二、钢和铁的区分:以含碳量区分:熟铁:C<0.02% 钢:C=0.02%~1.7% 生铁:C>1.7%三、炼铁生产工艺流程:1.高炉炼铁生产工艺流程: 简图2.高炉本体:内型:炉喉、炉身、炉腰、炉腹、炉缸。
外壳为金属结构,内衬耐火材料,中间是冷却设备。
3.除本体外,高炉还有以下几大系统:(1)上料系统:职责:储存、混匀、筛分、称量原、燃料,并运到炉顶受料漏斗。
(2)装料系统:职责:按要求将炉料装入炉内和煤气密封。
(3)送风系统:职责:提供和加热空气,并送入炉内,保证足够的风量和风温。
(4)喷吹系统:职责:将煤粉或重油送入炉内。
(5)煤气清洗系统:职责:收集和清洗煤气。
(6)渣铁处理系统:职责:定期排放炉内渣铁并运走,保证高炉连续生产。
(7)动力系统:职责:为高炉的正常生产提供"风、水、电、气"等能源.是高炉正常生产的保障.四、高炉炼铁主要经济技术指标:1.高炉利用系数:指每昼夜每立方米高炉有效容积生产的合格炼钢生铁量。
2.冶炼强度:指每昼夜、每立方米高炉有效容积消耗的干焦量。
干焦耗用量冶炼强度=—————————————(t/(m3.d))有效容积×实际工作日3.综合冶炼强度:除干焦外,还考虑有喷吹的其他类型的辅助燃料。
综合干焦耗用量综合冶炼强度=————————————(t/(m3.d))有效容积×实际工作日4.焦比:冶炼一吨铁消耗的干焦量。
干焦耗用量(kg)入炉焦比=————————合格生铁产量(t)5.综合焦比:生产每吨生铁所消耗的干焦数量以及各种辅助燃料折算为干焦之总和。
干焦数量+Σ喷吹燃料×折算系数综合焦比= —————————————————(kg/t)合格生铁产量综合干焦耗用量= ——————————(kg/t)合格生铁产量6.休风率:高炉休风停产时间占规定日历作业时间的百分数。
高炉炼铁技术创新实践及未来展望

千里之行,始于足下。
高炉炼铁技术创新实践及未来展望高炉炼铁技术是钢铁工业中非常重要的一个环节,对于钢铁产量和质量有着直接影响。
随着科技的不断发展和进步,高炉炼铁技术也在不断创新和实践。
本文将介绍高炉炼铁技术的创新实践及未来展望。
高炉炼铁技术主要包括焦炭冶炼、铁矿石还原和炉渣处理三个方面。
近年来,针对这几个环节进行了一系列的技术创新,以提高钢铁产量和质量,减少能源消耗和环境污染。
首先,在焦炭冶炼方面,高炉炼铁技术实践了煤炭气化技术,将煤炭转化为合成气或制备气,用来代替部分焦炭。
这样可以减少焦炭的消耗量,提高炉温和炉效,提高炼铁效果和节约能源。
其次,在铁矿石还原方面,高炉炼铁技术实践了混合还原技术,将不同种类的铁矿石混合使用,以提高还原效率和减少还原剂的消耗。
同时,还运用了制粒和球团矿技术,提高了炉料的密实度和还原性能,使得炼铁效果更好。
再次,在炉渣处理方面,高炉炼铁技术实践了炉渣处理技术,包括高炉渣套料、炉渣粉磨和炉渣稳定化等。
这些技术可以减少炉渣的生成和排放,降低对环境的污染,同时还能回收利用一部分有价值的元素。
未来,高炉炼铁技术仍将继续创新和发展。
一方面,可以进一步拓宽原料的来源,包括使用青海盐湖等资源,以降低对传统铁矿石的依赖程度。
另一方面,可以进一步提高炉渣的利用率,实现钢铁工业的循环经济。
此外,还可以用高效节能的加热方式替代传统的冶炼方法,以进一步降低能源消耗和环境污染。
第1页/共2页锲而不舍,金石可镂。
综上所述,高炉炼铁技术的创新实践为钢铁工业的发展提供了重要支撑。
未来,随着技术的不断进步和创新,高炉炼铁技术将更加高效、环保和可持续,为钢铁产量和质量的提高做出更大贡献。
同时,需要在技术创新的同时,加强对环境保护的重视,实现钢铁工业的可持续发展。
高炉冶炼炼铁技术探讨
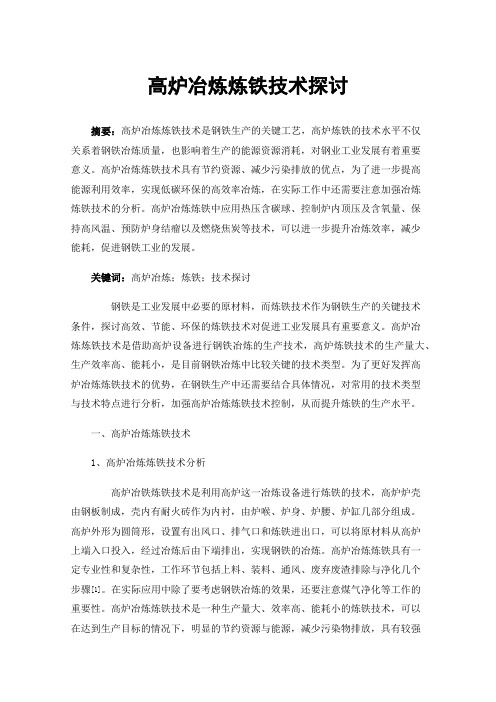
高炉冶炼炼铁技术探讨摘要:高炉冶炼炼铁技术是钢铁生产的关键工艺,高炉炼铁的技术水平不仅关系着钢铁冶炼质量,也影响着生产的能源资源消耗,对钢业工业发展有着重要意义。
高炉冶炼炼铁技术具有节约资源、减少污染排放的优点,为了进一步提高能源利用效率,实现低碳环保的高效率冶炼,在实际工作中还需要注意加强冶炼炼铁技术的分析。
高炉冶炼炼铁中应用热压含碳球、控制炉内顶压及含氧量、保持高风温、预防炉身结瘤以及燃烧焦炭等技术,可以进一步提升冶炼效率,减少能耗,促进钢铁工业的发展。
关键词:高炉冶炼;炼铁;技术探讨钢铁是工业发展中必要的原材料,而炼铁技术作为钢铁生产的关键技术条件,探讨高效、节能、环保的炼铁技术对促进工业发展具有重要意义。
高炉冶炼炼铁技术是借助高炉设备进行钢铁冶炼的生产技术,高炉炼铁技术的生产量大、生产效率高、能耗小,是目前钢铁冶炼中比较关键的技术类型。
为了更好发挥高炉冶炼炼铁技术的优势,在钢铁生产中还需要结合具体情况,对常用的技术类型与技术特点进行分析,加强高炉冶炼炼铁技术控制,从而提升炼铁的生产水平。
一、高炉冶炼炼铁技术1、高炉冶炼炼铁技术分析高炉冶铁炼铁技术是利用高炉这一冶炼设备进行炼铁的技术,高炉炉壳由钢板制成,壳内有耐火砖作为内衬,由炉喉、炉身、炉腰、炉缸几部分组成。
高炉外形为圆筒形,设置有出风口、排气口和炼铁进出口,可以将原材料从高炉上端入口投入,经过冶炼后由下端排出,实现钢铁的冶炼。
高炉冶炼炼铁具有一定专业性和复杂性,工作环节包括上料、装料、通风、废弃废渣排除与净化几个步骤[1]。
在实际应用中除了要考虑钢铁冶炼的效果,还要注意煤气净化等工作的重要性。
高炉冶炼炼铁技术是一种生产量大、效率高、能耗小的炼铁技术,可以在达到生产目标的情况下,明显的节约资源与能源,减少污染物排放,具有较强的环保效果,满足低碳生产的需求。
随着高炉冶炼炼铁技术的不断发展,高炉炼铁的工作质量也在不断提升,为钢铁生产提供了良好的技术条件。
钢铁行业的绿色技术环保和可持续发展的解决方案

钢铁行业的绿色技术环保和可持续发展的解决方案钢铁行业一直被认为是环境污染较重的行业之一,其高能耗、高排放的特点给环境造成了严重负担。
然而,在不断发展的过程中,钢铁行业也在积极探索和应用绿色技术,以实现环保和可持续发展。
本文将介绍钢铁行业的绿色技术环保和可持续发展的解决方案。
一、节能减排技术1.1 高效炼钢技术高效炼钢技术是钢铁行业实现节能减排的重要手段之一。
采用高效炼钢技术可以降低炼钢过程中的能耗和二氧化碳排放。
例如,采用先进的烧结技术可以减少炼钢过程中的热能损失,降低能耗;采用脱硫脱氮技术可以减少炼钢过程中的气体污染物排放。
1.2 废气处理技术钢铁生产过程中产生大量的废气,其中含有二氧化硫、氮氧化物等有害物质。
采用废气处理技术可以有效降低废气中有害物质的排放。
例如,采用除尘技术可以净化废气中的颗粒物;采用脱硫脱硝技术可以减少废气中的二氧化硫、氮氧化物排放。
1.3 循环冷却技术循环冷却技术是钢铁行业减少耗水量的重要手段之一。
通过循环水系统,可以将炼钢过程中的冷却水进行循环利用,减少对水资源的需求。
同时,循环冷却技术还可以减少废水的排放,达到环保的目的。
二、优化矿石利用技术2.1 废渣综合利用技术钢铁行业产生大量的废渣,传统上往往会将废渣直接堆放或填埋,对环境造成严重的污染。
采用废渣综合利用技术可以将废渣转化为资源,降低对原材料的需求。
例如,通过废渣回收技术可以将废渣中的铁精粉、矿物质等有价值成分提取出来,再利用于生产过程中。
2.2 先进的炼铁技术炼铁过程中会产生大量的烟尘、废水和废渣,给环境带来严重的污染。
采用先进的炼铁技术可以减少废物的产生,提高矿石的利用率。
例如,采用高炉煤气发电技术可以将炼铁过程中产生的高炉煤气进行能量回收,实现资源的循环利用。
三、绿色设计与环境管理3.1 环境评估与规划在钢铁项目建设前,进行全面、系统的环境评估,制定科学合理的环境规划,将环境保护纳入设计、审批和管理的全过程。
熔融还原炼铁技术综述

目录1.概述 (1)2.国际熔融还原技术发展 (3)2.1.工业化的COREX工艺 (5)2.2.进入示范性工厂试验的Hismelt技术 (7)2.3.FINEX技术 (8)2.4.第三代炼铁法--ITmk3 (9)3.国内熔融还原(非高炉炼铁)技术发展现状 (11)3.1.概述 (11)3.2.2T/h的半工业联动热态试验装置-COSRI (11)3.3.宝钢Corex 3000 (14)3.4.20万吨纯氧非高炉炼铁工业试验装置 (14)3.5.8m3一步法熔融还原试验装置 (18)3.6.基于氢冶金的熔融还原炼铁新工艺 (20)3.6.1.万吨级两级循环流化床示范装置-营口中板厂 (21)3.6.2.宝钢万吨级两级冷态循环流化床装置建设 (24)3.7.直接还原在国内的发展 (24)3.8.几种非高炉炼铁的综合分析 (26)4.炼铁技术的发展方向 (28)4.1.欧盟——ULCOS超低CO2排放钢铁技术研究 (28)4.2.日本——COURSE50技术研究 (30)4.3.中国——新一代可循环钢铁流程工艺技术技 (30)5.具有自主知识产权的熔融还原炼铁技术发展建议 (31)5.1.建立长期开发组织机构与募集资金 (31)5.2.加强合作、充分利用现有成果深入研究 (31)5.3.新一代具有自主知识产权的熔融还原流程建议 (32)熔融还原炼铁技术综述全强1.概述改革开放30年来,中国钢铁冶炼技术取得了巨大的进步。
在炼铁领域,技术进步的主要表现是装备的大型化、操作的自动化信息化、生产的高效与清洁化,高风温技术、富氧技术、喷煤技术、煤气干式除尘技术、煤气余压发电、煤气燃气技术、高炉长寿技术、与高炉废弃物的综合利用等方面的应用取得明显的进步。
据2010年的统计,国内炼铁产量已超过5.9亿吨,约占世界产量的40%。
其中大于1000m3以上高炉的产量约为60%,也就是说,按照国家产业政策的要求,有40%的产能需要进行技术改造。
钢铁生产主要工艺流程
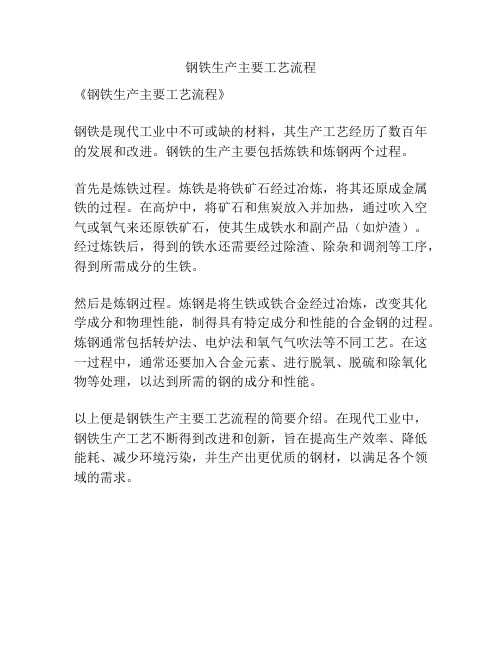
钢铁生产主要工艺流程
《钢铁生产主要工艺流程》
钢铁是现代工业中不可或缺的材料,其生产工艺经历了数百年的发展和改进。
钢铁的生产主要包括炼铁和炼钢两个过程。
首先是炼铁过程。
炼铁是将铁矿石经过冶炼,将其还原成金属铁的过程。
在高炉中,将矿石和焦炭放入并加热,通过吹入空气或氧气来还原铁矿石,使其生成铁水和副产品(如炉渣)。
经过炼铁后,得到的铁水还需要经过除渣、除杂和调剂等工序,得到所需成分的生铁。
然后是炼钢过程。
炼钢是将生铁或铁合金经过冶炼,改变其化学成分和物理性能,制得具有特定成分和性能的合金钢的过程。
炼钢通常包括转炉法、电炉法和氧气气吹法等不同工艺。
在这一过程中,通常还要加入合金元素、进行脱氧、脱硫和除氧化物等处理,以达到所需的钢的成分和性能。
以上便是钢铁生产主要工艺流程的简要介绍。
在现代工业中,钢铁生产工艺不断得到改进和创新,旨在提高生产效率、降低能耗、减少环境污染,并生产出更优质的钢材,以满足各个领域的需求。
钢铁氢基竖炉技术

钢铁氢基竖炉技术
钢铁氢基竖炉技术是一种创新的炼铁工艺,它使用氢气作为还原剂,替代传统的碳还原。
这项技术被认为是钢铁行业实现低碳、绿色发展的关键途径之一。
氢基竖炉技术的核心在于使用氢气还原铁矿石中的氧化铁,从而得到纯铁。
与传统的高炉炼铁相比,氢基竖炉技术具有以下几个显著优势:
1.低碳环保:使用氢气作为还原剂,避免了碳排放,从而降低了钢铁生产过程中
的温室气体排放。
2.高效节能:氢气的还原效率远高于碳,因此氢基竖炉技术可以提高炼铁过程的
能源利用效率。
3.提高产品质量:由于氢气还原过程中不会产生杂质,因此可以生产出更高纯度
的铁,从而提高钢铁产品的质量。
然而,氢基竖炉技术也面临一些挑战和限制:
1.氢气生产成本高:目前氢气的生产成本仍然较高,这限制了氢基竖炉技术的广
泛应用。
2.技术成熟度有待提高:虽然氢基竖炉技术已经取得了一定的进展,但其技术成
熟度仍然有待提高,需要进一步的研究和试验验证。
3.基础设施需求:为了实现氢基竖炉技术的规模化应用,需要建设相应的氢气生
产、储存和运输基础设施。
总的来说,钢铁氢基竖炉技术是一种具有广阔前景的创新炼铁工艺,有望为钢铁行业的低碳、绿色发展提供有力支持。
然而,要实现这一技术的广泛应用,还需要克服一系列技术、经济和政策方面的挑战。
炼铁简述描述

铁矿石分类及特性
一、矿石和脉石
随着选矿和冶炼技术的开展,矿石的来源和 范围不断扩大。如含铁较低的贫矿,经过富 选也可用来炼铁;过去认为不能冶炼的攀枝 花钒钛磁铁矿,已成为重要的炼铁原料。
矿石中除了用来提取金属的有用矿物外,还 含有一些工业上没有提炼价值的矿物或岩石, 统称为脉石。对冶炼不利的脉石矿物,应在 选矿和其它处理过程中尽量去除。
其它用途
1.2 高炉本体及消费附属系统
高炉消费以高炉 本体为主体,包 括八大系统:
⒈高炉本体:高 炉本体是冶炼生 铁的主体设备, 由炉基、炉壳、 炉衬及冷却设备、 支柱或框架组成。
任务:高炉冶 炼在其内部连续 进展。
⒉供上料系统:包括贮矿场、贮 矿槽、焦炭滚筛、称量漏斗、称 量车、料坑、斜桥、卷扬机、料 车上料机、大型高炉采用皮带上 料机。
⒍渣铁处理系统:包括出铁场、 开口机、泥炮、炉前吊车、铁水 罐、堵渣机、水渣池及炉前水力 冲渣设施等。
任务:定期将炉内的渣、铁
出净并及时运走,以保证高炉连 续消费。
⒎喷吹系统:包括原煤的储存、 运输、煤粉的制备、搜集及煤 粉喷吹等系统。
任务:均匀稳定地向高炉喷
吹大量煤粉,以煤代焦,降低 焦炭消耗。
铁矿石分类及特性
氟 在冶炼过程中以CaF2形态进入渣中。CaF2
能降低炉渣的熔点,增加炉渣流动性,当 铁矿石中含氟高时,炉渣在高炉内过早形 成,不利于矿石复原。矿石中含氟不超过 1%时对冶炼无影响,当含量到达4%~5% 时需要注意控制炉渣的流动性。采外,高 温下氟挥发对耐火材料和金属构件有一定 的腐蚀作用。
铁矿石分类及特性
3.有害杂质和有益元素的含量 有害杂质通常指S、P、Pb、Zn、As等,
它们的含量愈低愈好。Cu有时为害,有时 为益,视详细情况而定。表2-2 为入炉铁矿 石有害杂质的界限含量。
钢铁行业的新技术及产业升级

钢铁行业的新技术及产业升级随着时代的不断进步和科技的不断发展,传统的产业也在不断的升级和转型。
在现代工业中,钢铁产业一直是一个十分重要的部门,其重要性不仅仅体现在民生方面,还体现在国家经济运行和发展上。
因此,随着人们对生活和生产的需求不断增加,钢铁行业的技术和制造工艺也在不断更新和升级。
本文将分析钢铁行业的新技术及产业升级。
一、钢铁行业的传统技术及问题首先,需要了解钢铁行业传统的技术和制造工艺。
传统的钢铁制造过程分为三个步骤:炼铁、炼钢和轧制。
在该过程中,炼铁是将铁矿石变成铁的过程,炼钢和轧制是将铁制成钢和制造钢材的过程。
然而,这个过程存在很多问题和缺点,如:1. 能耗高炼制钢铁过程需要很高的温度,非常耗能。
传统的高炉炼铁技术需要耗费大量的煤炭、煤气和电力等资源,导致能源浪费和环境污染,同时也会带来昂贵的生产成本。
2. 产量低传统的炼钢和轧制生产线需要投入大量工作人员和设备,生产效率低下,无法满足大规模生产的需求。
3. 生产过程复杂传统的炼钢和轧制生产线需要多个环节,需要多个环节对钢材进行加工,难以实现自动化生产。
二、钢铁行业的新技术为了解决上述问题,钢铁行业开始探索新的技术,通过数字化智能化改造,提升生产效率,节约能源,降低生产成本。
目前,钢铁行业已经采用了一系列新技术,使得传统的生产方式变得更加现代和高效。
这些技术包括:1. 自动化生产线新型智能化控制技术和机器人技术,实现钢铁生产过程自动化。
这不仅可以减少人工参与,提高生产效率,而且还能够减少生产过程中的重大事故,增强企业安全性。
2. 3D打印技术3D打印技术被广泛应用于钢铁制造领域中,它可以制造出形状复杂、重量轻的零部件,同时降低物料浪费,满足环保标准。
3. 光纤控制技术光纤控制技术是基于传感器网络和人工智能技术的应用。
它可以监测钢铁生产过程中的安全性和质量,并及时调整生产流程,实现对生产过程全方位的监测,提高生产安全和品质。
三、钢铁行业的产业升级随着新技术的引入和应用,钢铁行业正在朝着数字化、智能化、精益化的方向不断发展。
国内外高炉炼铁技术的发展现状和趋势

国内外高炉炼铁技术的发展现状和趋势
国内外高炉炼铁技术的发展现状和趋势
一、发展现状
1、国内
(1)钢铁厂炼铁技术的改造力度加大,已实现超低碳、超低强度、超低消耗的可持续发展。
(2)新型储能灶的兴起,使煤的消耗大大减少,同时也提高了炼铁设备的智能度。
(3)智能化技术的广泛应用,大大提升了传统炼铁技术的能源利用率。
2、国外
(1)德国、日本、西班牙等国在炼铁方面都有着非常成熟的技术,通过智能化技术的大量应用,以及不断提升设备抗磨损能力,使炼铁设备的性能得到持续提升。
(2)美国的炼铁技术也在不断发展,尤其是节能技术的提升,使温室气体排放量大幅减少,符合可持续发展的要求。
二、发展趋势
1、储能灶的广泛应用:储能灶的智能化技术可以大大减少给炉内喷射的煤,从而提高炼铁效率。
2、球化技术的提升:通过提高炉内样品的球化度,大大提升炼铁炉设备的耐板材性和智能度。
3、炼铁技术创新:不断创新和应用抗磨损、节能、轻量化、小型化等技术,提高设备的使用效率和产量。
4、炉前技术的完善:通过构建智能、优化的炉前技术,可以有效将煤、矿石等进料质量提高。
5、可持续发展:国内外高炉炼铁技术都趋向于节能、低碳、环境友好的可持续发展方向。
钢铁冶炼技术介绍

中国钢铁企业正逐步实现智能化转型,通过信息技术和自动化技术提高生产效率和降低能耗。
智能化转型
中国钢铁企业正积极拓展国际市场,通过出口高性能钢材和提供技术服务,提高国际竞争力。
拓展国际市场
国际钢铁企业之间正进行广泛的技术交流,分享最新的技术和经验,促进共同发展。
技术交流
合作研发
资源共享
人才培养
国际钢铁企业正开展合作研发,共同攻克技术难题和开发新产品。
自动化技术
钢铁冶炼企业将推广自动化技术,实现生产过程的自动化控制和智能化管理。例如,利用自动化设备进行钢水测温、成分分析等,提高生产效率和产品质量。
钢铁冶炼企业将加大低碳排放技术的研发和应用力度,降低生产过程中的碳排放量。例如,利用低碳炼铁技术、碳捕获和储存技术等,降低碳排放量。
低碳排放技术
钢铁冶炼企业将推广环保处理技术,实现生产过程中的废弃物减量化、资源化和无害化处理。例如,利用废弃物制取还原剂、利用余热发电等,实现废弃物的资源化利用。
转炉炼钢技术是一种以氧气为主要还原剂的炼钢方法,具有流程短、成本低等优点。
总结词
转炉炼钢技术利用氧气和铁水的化学反应,将铁水中多余的碳和其他杂质去除,从而得到钢水。该技术具有流程短、成本低等优点,适用于生产不同品种和规格的钢材。在转炉炼钢过程中,温度和成分控制是关键因素,需要精确控制以获得高质量的钢材。
电炉炼钢技术的优点在于其能源利用率高、环保性能好和产品质量稳定,但同时也存在一些缺点,如成本高、生产规模小等。
电炉炼钢技术的优点
详细描述
总结词
详细描述
钢铁冶炼的环境影响与可持续发展
03
钢铁工业应采取有效措施降低能耗和减少排放,如采用先进的工艺和技术,提高能源利用效率。
炼铁工艺流程
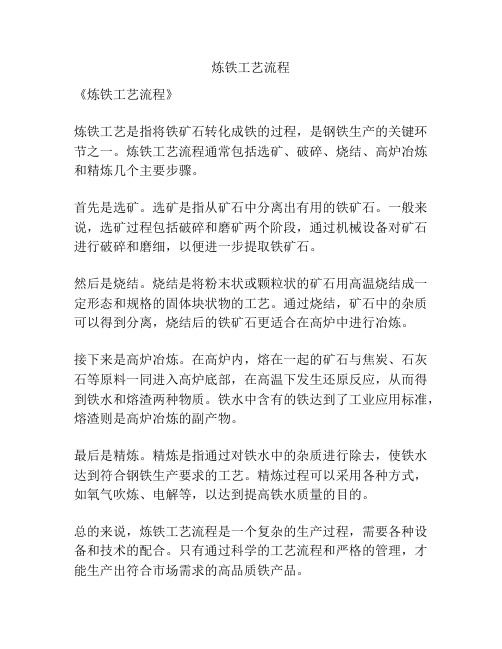
炼铁工艺流程
《炼铁工艺流程》
炼铁工艺是指将铁矿石转化成铁的过程,是钢铁生产的关键环节之一。
炼铁工艺流程通常包括选矿、破碎、烧结、高炉冶炼和精炼几个主要步骤。
首先是选矿。
选矿是指从矿石中分离出有用的铁矿石。
一般来说,选矿过程包括破碎和磨矿两个阶段,通过机械设备对矿石进行破碎和磨细,以便进一步提取铁矿石。
然后是烧结。
烧结是将粉末状或颗粒状的矿石用高温烧结成一定形态和规格的固体块状物的工艺。
通过烧结,矿石中的杂质可以得到分离,烧结后的铁矿石更适合在高炉中进行冶炼。
接下来是高炉冶炼。
在高炉内,熔在一起的矿石与焦炭、石灰石等原料一同进入高炉底部,在高温下发生还原反应,从而得到铁水和熔渣两种物质。
铁水中含有的铁达到了工业应用标准,熔渣则是高炉冶炼的副产物。
最后是精炼。
精炼是指通过对铁水中的杂质进行除去,使铁水达到符合钢铁生产要求的工艺。
精炼过程可以采用各种方式,如氧气吹炼、电解等,以达到提高铁水质量的目的。
总的来说,炼铁工艺流程是一个复杂的生产过程,需要各种设备和技术的配合。
只有通过科学的工艺流程和严格的管理,才能生产出符合市场需求的高品质铁产品。
钢铁行业智能炼铁技术

钢铁行业智能炼铁技术智能炼铁技术在钢铁行业发挥着越来越重要的作用。
这些技术的引入和应用,不仅可以提高钢铁生产的效率和质量,还可以降低环境污染和能源消耗。
本文将介绍钢铁行业智能炼铁技术的发展现状和未来趋势。
一、智能炼铁技术的发展现状智能炼铁技术是指利用先进的信息技术和自动化技术,对炼铁过程进行监控、控制和优化,从而提高生产效率和产品质量。
目前,智能炼铁技术已经在钢铁行业的不同环节得到了广泛应用。
1. 自动化控制系统的应用自动化控制系统是实现智能炼铁技术的基础。
它通过传感器、数据采集和处理设备,实时监测和控制炼铁过程中的温度、压力、流量等参数,以及各种设备的运行状态。
自动化控制系统可以精确调节工艺参数,提高产品质量和生产效率。
2. 数据分析和预测模型通过大数据分析和建立预测模型,可以更好地理解和优化炼铁过程。
大数据分析可以从大量的历史数据中提取有用的信息,帮助决策者做出科学决策。
预测模型可以根据历史数据和当前数据,预测未来的生产状况,并进行相应的调整。
3. 人工智能技术的应用人工智能技术在智能炼铁中扮演着重要角色。
通过机器学习和深度学习等方法,可以自动学习和识别炼铁过程中的特征和规律。
这样,智能系统可以根据数据和模型的输入,自主地做出决策和控制。
二、智能炼铁技术的未来趋势随着科技的不断进步和钢铁行业的发展需求,智能炼铁技术有望在未来取得更大的突破和应用。
1. 联网化和云计算未来的智能炼铁技术将更加联网化,实现设备之间和部门之间的信息共享和协同。
云计算技术可以实现海量数据的存储和处理,使得炼铁过程的优化和控制更加智能和高效。
2. 物联网和传感器技术物联网和传感器技术的发展,将使得炼铁过程中的信息获取更加准确和及时。
通过在设备和产品上安装传感器,可以实现对温度、压力、流量等参数的实时监测和反馈。
这样,炼铁过程的控制和调整将更加精确。
3. 智能化的生产设备未来的钢铁生产设备将更加智能化。
例如,具有自主学习能力的机器人可以在炼铁过程中代替人工进行操作和监控。
高炉炼铁新技术(1)

1) 解放初至1958年大办钢铁期间高炉操作方针:大风(全风量操 作)高温4字方针。 2) 经过大办钢铁后,1959年总结出:“以原料为基础,以风为纲, 提高冶炼强度与降低焦比并举”的操作方针。 3) 经过60、70年代的实践至80年代,提出了“高产、低耗、优质 的六字方针”。 4) 1980年又总结提出了“高产、低耗、优质、长寿”的八字方针, 这方针一直延续到21世纪,在此过程中逐步建立了一套科学且附合实 际的评价方法。 5) 2008年在落实科学发展观,实现钢铁工业可持续发展的大背景 下,总结提出了 “高效、低耗、优质、长寿、环保”十字方针。实践 中为了突出低耗和环保,次序又调为“低耗、环保、优质、长寿、高 效”,把追求高产(高利用系数)转变为降低燃料比,从而达到高效的 目的。其中追求“高效”包括高效利用资源、高效利用能源和降低消 耗,把降低燃料比放到追求“高效”之首。
v
高炉容积 (V m )
3
高炉容积为铁口中心线平面以上至料线平面以下的容积(m3) 高 平 日 量 炉 均 产 (p t / d ) 高炉炉缸断面积利用系数(t/m2· d) 炉 断 积 缸 面 (A m ) (t/m2· d) 以上两种方法都有一定道理,炉缸断面积表达法更为合理。
燃料比 Kg/t 520 510 500 490 480 利用系数 t/m3.d 2.20 2.26 2.31 2.36 2.41 冶炼强度 t/m3.d 1.112 1.140 1.169 1.194 1.220 入炉风量 Nm3/min. 7242.6 7242.0 7241.3 7240.7 7240.1
1.176
1.203 1.229 1.253 1.274
7379.7
7222.4 7067.7 6915.7 6766.3
高炉炼铁技术工艺及应用分析
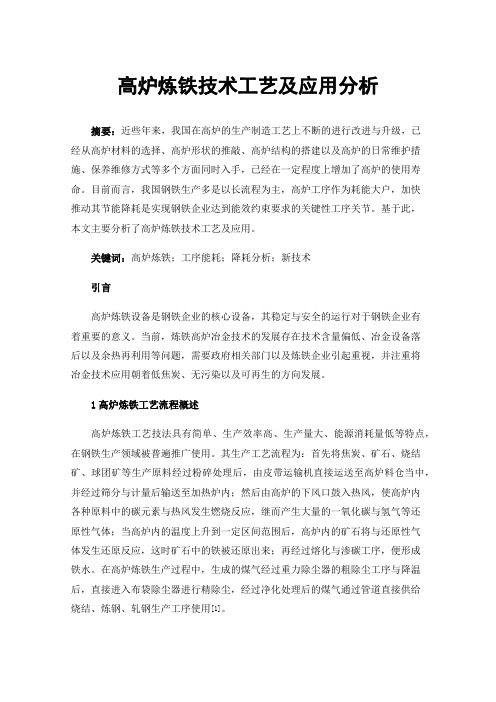
高炉炼铁技术工艺及应用分析摘要:近些年来,我国在高炉的生产制造工艺上不断的进行改进与升级,已经从高炉材料的选择、高炉形状的推敲、高炉结构的搭建以及高炉的日常维护措施、保养维修方式等多个方面同时入手,已经在一定程度上增加了高炉的使用寿命。
目前而言,我国钢铁生产多是以长流程为主,高炉工序作为耗能大户,加快推动其节能降耗是实现钢铁企业达到能效约束要求的关键性工序关节。
基于此,本文主要分析了高炉炼铁技术工艺及应用。
关键词:高炉炼铁;工序能耗;降耗分析;新技术引言高炉炼铁设备是钢铁企业的核心设备,其稳定与安全的运行对于钢铁企业有着重要的意义。
当前,炼铁高炉冶金技术的发展存在技术含量偏低、冶金设备落后以及余热再利用等问题,需要政府相关部门以及炼铁企业引起重视,并注重将冶金技术应用朝着低焦炭、无污染以及可再生的方向发展。
1高炉炼铁工艺流程概述高炉炼铁工艺技法具有简单、生产效率高、生产量大、能源消耗量低等特点,在钢铁生产领域被普遍推广使用。
其生产工艺流程为:首先将焦炭、矿石、烧结矿、球团矿等生产原料经过粉碎处理后,由皮带运输机直接运送至高炉料仓当中,并经过筛分与计量后输送至加热炉内;然后由高炉的下风口鼓入热风,使高炉内各种原料中的碳元素与热风发生燃烧反应,继而产生大量的一氧化碳与氢气等还原性气体;当高炉内的温度上升到一定区间范围后,高炉内的矿石将与还原性气体发生还原反应,这时矿石中的铁被还原出来;再经过熔化与渗碳工序,便形成铁水。
在高炉炼铁生产过程中,生成的煤气经过重力除尘器的粗除尘工序与降温后,直接进入布袋除尘器进行精除尘,经过净化处理后的煤气通过管道直接供给烧结、炼钢、轧钢生产工序使用[1]。
2目前高炉生产的现状从世界范围来讲,我国目前拥有当之无愧的高炉炼铁生产技术大国称号,而这与我国在冶铁行业大量采用高炉炼铁技术是密不可分的。
高炉炼铁技术由于其生产的钢铁质量较为稳定,并且可以在冶炼时极大的提高钢铁生产的效率并且操作简单,钢铁的生产数量因而大幅度的提升,因此也成为了目前使用最多的钢铁生产技术之一,正是由于我国的钢铁产量不断攀升,因此需要更高效、高质量的生产方法,因而也促进了高炉炼铁技术的不断发展与进步,二者相辅相成。
钢铁行业工作原理

钢铁行业工作原理钢铁行业是现代工业中关键的基础支撑产业之一。
钢铁材料广泛应用于建筑、制造业、交通运输和能源等领域。
在钢铁行业中,各种工艺和机械设备相互配合,以完成原料处理、冶炼、轧制和加工等工序,从而生产出各种规格型号的钢材产品。
本文将针对钢铁行业的工作原理进行详细介绍。
一、原料处理钢铁行业的原料主要包括铁矿石、废钢和其他辅助原料。
首先,铁矿石通过矿石选矿和破碎等工序被处理成符合冶炼要求的矿石粉末。
其次,废钢经过分类、破碎和清洁处理等工序,被熔化回收利用。
辅助原料包括焦炭、石灰石和脱硫剂等,用于调节矿石中的化学成分和物理性质。
二、冶炼过程1. 高炉炼铁高炉是一种重要的冶炼设备,用于将铁矿石和废钢等原料进行还原反应,提取出铁。
高炉内部温度高达1500摄氏度左右,铁矿石和废钢在高炉内与煤气进行反应,产生熔化的铁和炉渣。
铁水通过铁口流出,炉渣则通过炉渣口排出。
2. 转炉冶炼转炉是另一种常见的冶炼设备,采用吹氧气炼钢法。
高炉产生的生铁和废钢等原料被转移到转炉中,通过吹氧气的方式进行冶炼。
吹氧气可以去除铁中的杂质,并调节钢的成分和温度。
转炉冶炼是生产高品质钢的重要工艺。
三、轧制与加工1. 钢坯轧制钢坯是从冶炼过程中得到的连续铸造坯或钢锭,通常需要通过轧制设备进行加工、调整形状和规格。
钢坯进入轧机后,经过多道次的轧制、拉拔和整形等工序,最终变成特定的钢材产品。
2. 钢材加工钢材经过轧制后,根据不同的需求可以进一步进行加工。
例如,钢材可以通过剪切、焊接、冲压和热处理等工艺,制成满足特定用途的零部件或成品。
四、质量控制与检测在钢铁行业中,质量控制和检测是至关重要的环节。
通过定期取样和实验室检测,可以对原料、冶炼过程和成品钢材进行全面检验。
这包括化学成分分析、物理性能测试以及金相显微镜检测等,以确保钢铁产品的质量符合标准。
总结:钢铁行业的工作原理包括原料处理、冶炼过程、轧制与加工以及质量控制与检测。
各个环节相互协作,以确保钢铁产品能够满足各行各业的需求。
051粤裕丰钢铁公司炼铁技术进步
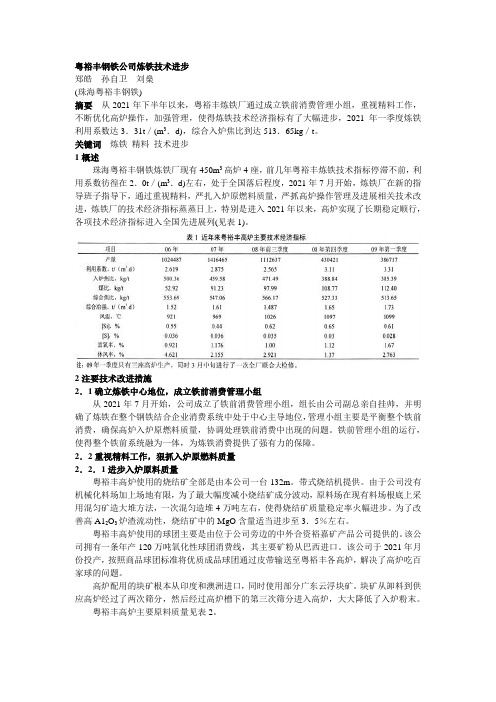
粤裕丰钢铁公司炼铁技术进步郑皓孙自卫刘燊(珠海粤裕丰钢铁)摘要从2021年下半年以来,粤裕丰炼铁厂通过成立铁前消费管理小组,重视精料工作,不断优化高炉操作,加强管理,使得炼铁技术经济指标有了大幅进步,2021年一季度炼铁利用系数达3.31t/(m3.d),综合入炉焦比到达513.65kg/t。
关键词炼铁精料技术进步1概述珠海粤裕丰钢铁炼铁厂现有450m3高炉4座,前几年粤裕丰炼铁技术指标停滞不前,利用系数彷徨在2.0t/(m3.d)左右,处于全国落后程度,2021年7月开始,炼铁厂在新的指导班子指导下,通过重视精料,严扎入炉原燃料质量,严抓高炉操作管理及进展相关技术改进,炼铁厂的技术经济指标蒸蒸日上,特别是进入2021年以来,高炉实现了长期稳定顺行,各项技术经济指标进入全国先进展列(见表1)。
2注要技术改进措施2.1确立炼铁中心地位,成立铁前消费管理小组从2021年7月开始,公司成立了铁前消费管理小组,组长由公司副总亲自挂帅,并明确了炼铁在整个钢铁结合企业消费系统中处于中心主导地位,管理小组主要是平衡整个铁前消费,确保高炉入炉原燃料质量,协调处理铁前消费中出现的问题。
铁前管理小组的运行,使得整个铁前系统融为一体,为炼铁消费提供了强有力的保障。
2.2重视精料工作,狠抓入炉原燃料质量2.2.1进步入炉原料质量粤裕丰高炉使用的烧结矿全部是由本公司一台132m。
带式烧结机提供。
由于公司没有机械化料场加上场地有限,为了最大幅度减小烧结矿成分波动,原料场在现有料场根底上采用混匀矿造大堆方法,一次混匀造堆4万吨左右,使得烧结矿质量稳定率火幅进步。
为了改善高A12O3炉渣流动性,烧结矿中的MgO含量适当进步至3.5%左右。
粤裕丰高炉使用的球团主要是由位于公司旁边的中外合资裕嘉矿产品公司提供的。
该公司拥有一条年产120万吨氧化性球团消费线,其主要矿粉从巴西进口。
该公司于2021年月份投产,按照商品球团标准将优质成品球团通过皮带输送至粤裕丰各高炉,解决了高炉吃百家球的问题。
浅谈炼铁高炉的组成及炼铁技术
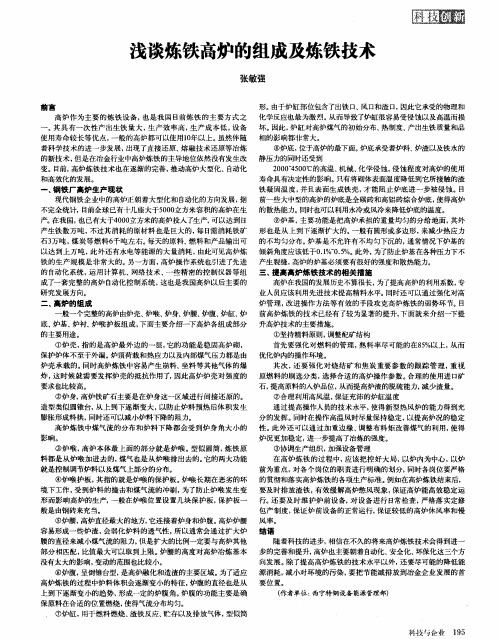
张敏 强
形。由于 炉 缸 部 位包含 了出铁 口、 风 口和 渣 口, 因此 它承 受的 物理 和 前言 高 炉 作 为 主要 的 炼 铁 设 备 , 也 是 我 国 目前炼 铁 的 主要 方 式 之 化学 反应 也 最为 激 烈 。 从而 导 致了炉缸 很 容 易受侵 蚀 以 及 高温 而损
一
炉管理, 改进操作方法等有效的手段攻克高炉炼铁的弱势环节。目 般一 个 完整 的高 炉 由炉 壳 、 炉喉、 炉身、 炉腰 、 炉 腹、 炉 缸、 炉 前高炉炼铁的技术已经有了较 为显著的提升, 下面就来介绍—下提 底、 炉基 、 炉 衬、 炉 喉 护板 组 成 , 下面 主要 介 绍 1 高炉各 组 成 部 分 升高 炉技 术 的主 要 措施 。 的 主要 用途 。 ①坚持 精 料 原则 , 调 整配 矿结 构 ①炉壳, 指的是高炉最外边的一层, 它的功能是稳 固高炉砌 , 首先 要 强化 对燃 料 的管 理 , 熟 料 率 尽 可能 的在 8 5 %以 上 , 从 而 保护 炉 体 不至 于外 漏 。 炉顶 荷 载 和热 应 力 以及 内部 煤气 压 力都是 由 优化 炉 内的操 作 环境 。 炉壳承 载的。 同时高炉炼铁中容易产生崩料、 坐料等其他气体的爆 其次 , 还要 强化 对烧 结矿和焦炭 重要参数 的跟 踪管理 , 重视 炸, 这时 候就 需要发挥炉壳的抵抗作用了, 因此高炉炉壳 对强度的 原燃 料 的 刷 选 分类 , 选 择合 适 的 高炉 操 作 参数 。 合 理 的 使用 进 口矿 要求 也 比较 高。 石, 提 高 原料 的入 炉品 位 , 从而 提高 炉 渣的 脱硫 能 力, 减 少渣 量 。 ②炉 身, 高 炉铁 矿 石主 要 是 在炉 身 这一 区域 进 行 间接 还 原 的。 ②合 理利 用 高凤 温 , 保证 充 沛的 炉缸 温 度 造型类似圆锥台, 从上到下逐渐变大 , 以防止炉料预热后体积发生 通过提高操作人员的技术水平, 使得新型热风炉的能力得到充 膨胀 形成 料 拱 , 同时还 可 以减 小 炉料 下降 的 阻力 。 分 的发 挥 。 同时 在 操 作高 温 风 时 尽量保 持 稳 定 , 以 提 高炉 况 的稳 定 高炉炼铁中煤气流的分布和炉料下降都会受到炉身角大小的 性 。 此 外 还 可 以 通 过加 重 边缘 、 调 整 布料 矩 改善 煤 气的 利 用 , 使得 影 响。 炉况更加稳定, 进一步提高了冶炼的强度。 ③炉喉, 高炉本体最上面的部分就 是炉 喉。 型似圆简, 炼铁原 料都是从炉喉加进去的, 煤 气也 是 从 炉喉 排 出去 的 。 它的 两 大功 能 ③协调生产组织 , 加强设备管理 在高炉炼 铁的过程中, 应该把 控好大局, 以炉 内为中心, 以炉 就 是 控 制 调节 炉料 以 及煤 气上 部分 的分 布。 前为 重 点 , 对 各 个 岗位 的职 责 进 行 明确 的 划 分 , 同 时各 岗位 要 严格 ④炉喉护板, 其指的就是炉喉的保护板 。 炉喉长期在恶劣的环 的 贯彻 和落 实 高 炉炼 铁 的各 项 生产 标 准 。 例 如在 高炉 炼 铁 结束 后 ,
钢铁行业的生产工艺与质量控制
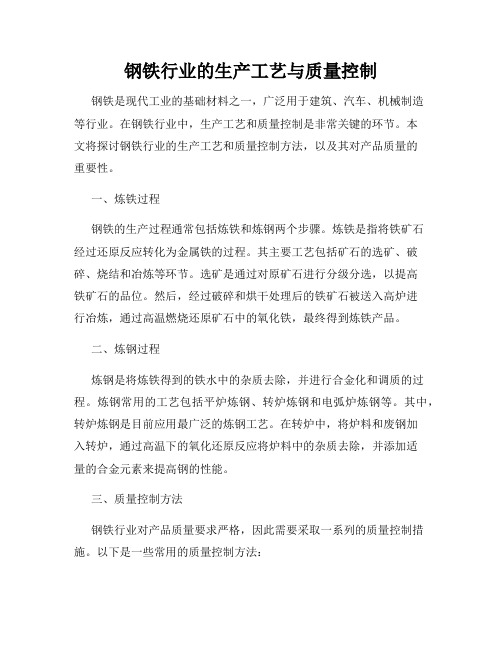
钢铁行业的生产工艺与质量控制钢铁是现代工业的基础材料之一,广泛用于建筑、汽车、机械制造等行业。
在钢铁行业中,生产工艺和质量控制是非常关键的环节。
本文将探讨钢铁行业的生产工艺和质量控制方法,以及其对产品质量的重要性。
一、炼铁过程钢铁的生产过程通常包括炼铁和炼钢两个步骤。
炼铁是指将铁矿石经过还原反应转化为金属铁的过程。
其主要工艺包括矿石的选矿、破碎、烧结和冶炼等环节。
选矿是通过对原矿石进行分级分选,以提高铁矿石的品位。
然后,经过破碎和烘干处理后的铁矿石被送入高炉进行冶炼,通过高温燃烧还原矿石中的氧化铁,最终得到炼铁产品。
二、炼钢过程炼钢是将炼铁得到的铁水中的杂质去除,并进行合金化和调质的过程。
炼钢常用的工艺包括平炉炼钢、转炉炼钢和电弧炉炼钢等。
其中,转炉炼钢是目前应用最广泛的炼钢工艺。
在转炉中,将炉料和废钢加入转炉,通过高温下的氧化还原反应将炉料中的杂质去除,并添加适量的合金元素来提高钢的性能。
三、质量控制方法钢铁行业对产品质量要求严格,因此需要采取一系列的质量控制措施。
以下是一些常用的质量控制方法:1. 原材料检测:在生产过程中,对采购的原材料进行化学成分、物理性能等方面的检测,以确保原材料的质量符合要求。
2. 工艺参数监控:钢铁生产过程中,通过监控工艺参数如温度、压力、流速等,调整生产参数以保证产品的质量稳定。
3. 技术人员培训:提供必要的培训和技术指导,以确保生产操作规范和技术水平符合要求。
4. 检验检测:通过对成品钢材进行物理性能、化学成分以及表面缺陷等方面的检测,以确保产品质量符合标准要求。
5. 完善的质量管理体系:建立完善的质量管理体系,包括合理的质量控制计划、质量审核、质量反馈等,以不断提高钢铁产品的质量。
四、质量控制对产品质量的重要性优良的生产工艺和严格的质量控制措施对钢铁产品的质量影响重大。
合理的生产工艺可以优化产品的物理性能和化学成分,提高产品的强度、塑性等机械性能。
同时,质量控制措施可以有效地避免产品中存在的缺陷和质量问题,确保产品的使用安全性和可靠性。
钢铁行业智能炼铁技术

钢铁行业智能炼铁技术近年来,随着科技的不断发展和创新,智能化技术逐渐渗透到各个行业,钢铁行业也不例外。
智能炼铁技术作为钢铁行业数字化转型的重要组成部分,对提高生产效率和质量起着关键作用。
本文将就钢铁行业智能炼铁技术的意义、应用和展望进行探讨。
1. 智能炼铁技术的意义在传统的炼铁过程中,人工操作频繁,精度受到限制,而智能炼铁技术的引入可以有效地提升炼铁过程的自动化程度和智能化水平。
通过搭建数据采集和分析平台,实时监控炉况、燃烧状态和材料性质变化等信息,可以精准控制炼铁过程中的温度、压力和化学成分等关键参数,提高产能,减少资源浪费,提高产品质量。
2. 智能炼铁技术的应用(1)物联网技术的应用:物联网技术的发展使得各种设备和传感器能够实时获取和传输数据。
在智能炼铁技术中,物联网技术可以连接各个环节的设备和传感器,将各种数据进行集中管理和分析,实现整个炼铁过程的数字化和自动化控制。
(2)大数据分析的应用:通过大数据分析,可以从庞大的数据中挖掘出有价值的信息和规律,为智能炼铁提供决策支持。
例如,利用大数据分析可以实现对原材料特性的精准预测,优化炼铁配料和工艺参数;通过对过往数据进行模型训练,可以预测故障和异常情况,提前采取措施,避免生产事故的发生。
(3)人工智能的应用:人工智能技术的发展为智能炼铁带来新的机遇。
通过机器学习和深度学习算法,智能系统可以从大量的数据中学习和模仿人工操作的经验,不断优化炼铁过程和决策,实现自动化和智能化。
3. 智能炼铁技术的展望目前,智能炼铁技术的应用虽然已经取得了一定的成果,但仍然存在一些挑战和待解决的问题。
例如,数据安全性和隐私保护问题,智能设备的可靠性和稳定性问题,以及智能化技术的推广和普及问题等。
未来,随着技术的不断进步和经验的积累,这些问题将逐步得到解决,智能炼铁技术的应用将更加广泛,效果将更加显著。
结论:智能炼铁技术作为钢铁行业数字化转型的重要手段,对提高生产效率和质量具有重要作用。
- 1、下载文档前请自行甄别文档内容的完整性,平台不提供额外的编辑、内容补充、找答案等附加服务。
- 2、"仅部分预览"的文档,不可在线预览部分如存在完整性等问题,可反馈申请退款(可完整预览的文档不适用该条件!)。
- 3、如文档侵犯您的权益,请联系客服反馈,我们会尽快为您处理(人工客服工作时间:9:00-18:30)。
重点企业高炉焦比升高
• 从2006年国际钢铁协会公布的数据来看,
– 世界高炉平均燃料比为543kg/t – 欧盟15国平均为494kg/t – 德国为486kg/t – 日本为498kg/t – 韩国为503kg/t – 中国为555kg/t
• 要从技术和管理两个方面进行提高,以促进企业技术进步, 提高企业的竞争能力。要加大淘汰落后技术装备的工作力 度,加强对环境的治理,实现企业的可持续发展。
高炉燃料比
• 2011年上半年我国重点钢铁企业燃料比为 520kg/t,比上年升高2kg/t。与2010年相比, 有42家企业燃料比升高,有30家企业燃料 比下降。
我国钢铁工业炼铁技术
我国炼铁生产
• 2011年上半年 • 生铁产量为32457.8万t,增长8.4%;
• 重点钢铁企业其他企业 • 生铁产量:27852.6万t4605.17万t, • 同期增长:6.3%;23.1% 。 • 其他企业生铁产量增幅大于重点钢铁企业,说明
地方企业发展较快。
炼铁技术经济指标下滑
• 这一数据可能出现计算问题,因为2011年上半年燃料比、 焦比在升高,铁矿石品位下降,这些均应该促使炼铁工序 能耗升高。
• 2011年上半年炼铁工序能耗较低的企业有:涟钢、太钢、 宣钢、邯钢、天铁、新余、国丰、承钢、湘钢、建龙、张 店、冷水江、重钢、衡管。高炉炼铁用能有78%来自碳素 (焦炭和煤粉)燃烧,燃料比对工序能耗的影响起决定性作 用。
重点企业喷煤比下降
• 高炉喷煤是炼铁系统结构优化的中心环节,是降低炼铁生 产成本的重要手段,也是减少炼焦过程中环境污染的有效 措施。
• 我国重点企业高炉喷煤比已达国际水平,但仍有较大的提 升空间。
• 衡量提高喷煤比效果的标准是:
– 喷煤比升高后燃料比不升高, – 煤粉与焦炭的置换比高, – 除尘灰中含碳量没有升高。
– 燃料比较低的企业:宝钢、冶钢、首钢、邯钢、 兴澄、太钢、马钢、昆钢、沙钢、青钢、韶钢、 柳钢、鞍钢、唐钢、衡管、武钢。
– 燃料比降低较多的企业:重钢、邯钢、锡钢、 南昌、新抚钢、达钢、承钢、徐州、衡管、石 横、涟钢、敬业、水钢等。
重点钢铁企业炼铁用原燃料质量情况
• 高炉炼铁是以精料为基础。精料水平对高炉指标的影响率 在70%。所以要重视改善原燃料质量的作用。
高炉燃料比
• 2010年我国重点钢铁企业高炉精料水平得到提高,特别是 焦炭质量得到改善,起到了重要作用。
• 2010年与2009年相比,重点企业焦炭M40升高0.56%, M10下降0.15%,灰分升高0.16%,硫分升高0.01%。
• 高炉生产实践表明,焦炭M平的提高,也会促进指标的改善。
• 由于高炉炼铁所需能量有78%是由碳素(焦炭和煤 粉)燃烧获得的,19%是由热风提供的。燃料比对 工序能耗的影响占80%以上。风温提高有利干提 高喷煤比、降低焦比。但2011年上半年我国重点 钢铁企业炼铁工序能耗实际数据是相反的结果。 这说明,原燃料质量恶化。
炼铁工序能耗情况
• 2011年上半年我国重点钢铁企业炼铁工序能耗为 404.99kgce/t,比上年有所下降。
• 我国燃料比高于世界平均水平,是我国高炉入炉 矿含铁品位低、热风温度偏低、焦炭品质差(灰分 高3%、硫高、转鼓指数和热性能较差)等原因、 造成的。
重点企业喷煤比下降
• 2011年上半年我国重点钢铁企业煤比为 147kg/t,比上年下降2kg/t;
• 与上年相比,有36家企业喷煤比下降,有 34家企业喷煤比得到提高。
• 2010年重点企业高炉燃料比(缺少小块焦比)为 518kg/t,比2009年下降1kg/t。
• 燃料比较低的企业有:
– 湖北新冶钢473kg/t,首钢478kg/t, – 宝钢469kg/t,莱钢486kg/t, – 马钢490kg/t,太钢496kg/t, – 首钢京唐472kg/t,兴澄特钢477kg/t, – 青钢486kg/t,马钢490kg/t, – 沙钢491kg/t,本钢493kg/t, – 通钢496kg/t,涟钢、鞍钢和邯钢为498kg/t。
高炉燃料比
• 多种因素可以实现燃料比降低:
– 矿品位升高1%,燃料比下降1.5%; – 风温升高100℃,燃料比下降10-15kg/t; – 焦炭M40升高1%,燃料比下降5kg/t; – M10下降0.2%,燃料比下降7kg/t; – 烧结矿转鼓指数提高1%,燃料比下降0.5%。
重点企业高炉焦比升高
重点企业高炉焦比升高
• 2011年上半年我国重点钢铁企业焦比为373kg/t,比上年 升高4kg/t;
• 升高的主要原因是原燃料质量和热风温度有不同程度的下 降。
• 焦比较低的企业有:太钢、兴澄、宝钢、首钢、青岛、营 口中板、涟钢、柳钢、武钢、合钢、长治、唐钢、邯钢、 鞍钢、湘钢、沙钢。
• 焦比下降幅度较大的企业有;营口中板、天钢、石横、张 店、重钢、太钢、南昌、徐州、敬业、新抚钢、首钢、达 钢、衡管、杭钢、兴澄。
炼铁技术经济指标下滑
• 2010年我国一些重点企业高炉技术经济指 标创出历史最高水平:
– 入炉焦比为369kg/t, – 喷煤比为149kg/t, – 热风温度为1160℃。
• 这些指标的提升,表明我国高炉炼铁技术 水平已经达到国际水平。
炼铁技术经济指标下滑
• 2011年上半年我国重点钢铁企业燃料比、焦比升 高,煤比、入炉矿品位、高炉利用系数下降,这 些因素会使炼铁工序能耗上升。风温提高17℃, 对工序能耗影响比例较小。但统计数据出现炼铁 工序能耗下降,值得质疑。
• 企业的炼铁工序能耗数据应与燃料比有对应关系。但上述 炼铁工序能耗较低的企业,有些燃料比相对还是较高的, 而且风温偏低,这让人产生疑问。
炼铁技术经济指标下滑
• 我国钢铁企业之间技术发展不平衡,先进 值与落后值差距甚大。
• 造成差距的原因是多方面的:
– 技术装备水平、原燃料质量 – 企业管理水平和地理环境