钢铁冶金学(炼铁部分)
钢铁冶金学(炼铁部分)
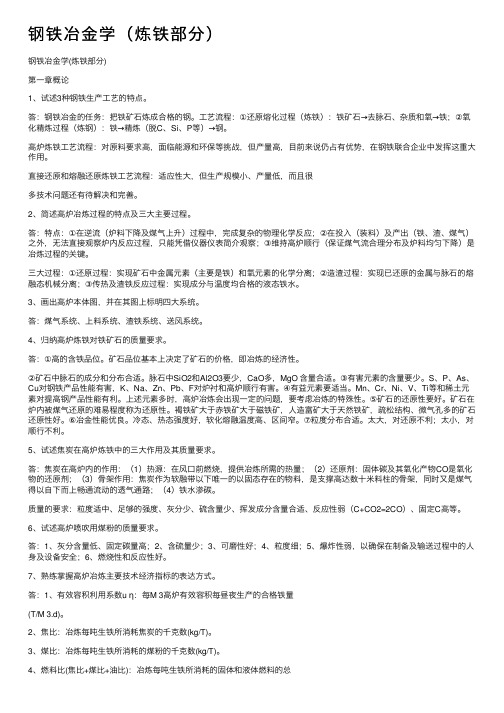
钢铁冶⾦学(炼铁部分)钢铁冶⾦学(炼铁部分)第⼀章概论1、试述3种钢铁⽣产⼯艺的特点。
答:钢铁冶⾦的任务:把铁矿⽯炼成合格的钢。
⼯艺流程:①还原熔化过程(炼铁):铁矿⽯→去脉⽯、杂质和氧→铁;②氧化精炼过程(炼钢):铁→精炼(脱C、Si、P等)→钢。
⾼炉炼铁⼯艺流程:对原料要求⾼,⾯临能源和环保等挑战,但产量⾼,⽬前来说仍占有优势,在钢铁联合企业中发挥这重⼤作⽤。
直接还原和熔融还原炼铁⼯艺流程:适应性⼤,但⽣产规模⼩、产量低,⽽且很多技术问题还有待解决和完善。
2、简述⾼炉冶炼过程的特点及三⼤主要过程。
答:特点:①在逆流(炉料下降及煤⽓上升)过程中,完成复杂的物理化学反应;②在投⼊(装料)及产出(铁、渣、煤⽓)之外,⽆法直接观察炉内反应过程,只能凭借仪器仪表简介观察;③维持⾼炉顺⾏(保证煤⽓流合理分布及炉料均匀下降)是冶炼过程的关键。
三⼤过程:①还原过程:实现矿⽯中⾦属元素(主要是铁)和氧元素的化学分离;②造渣过程:实现已还原的⾦属与脉⽯的熔融态机械分离;③传热及渣铁反应过程:实现成分与温度均合格的液态铁⽔。
3、画出⾼炉本体图,并在其图上标明四⼤系统。
答:煤⽓系统、上料系统、渣铁系统、送风系统。
4、归纳⾼炉炼铁对铁矿⽯的质量要求。
答:①⾼的含铁品位。
矿⽯品位基本上决定了矿⽯的价格,即冶炼的经济性。
②矿⽯中脉⽯的成分和分布合适。
脉⽯中SiO2和Al2O3要少,CaO多,MgO 含量合适。
③有害元素的含量要少。
S、P、As、Cu对钢铁产品性能有害,K、Na、Zn、Pb、F对炉衬和⾼炉顺⾏有害。
④有益元素要适当。
Mn、Cr、Ni、V、Ti等和稀⼟元素对提⾼钢产品性能有利。
上述元素多时,⾼炉冶炼会出现⼀定的问题,要考虑冶炼的特殊性。
⑤矿⽯的还原性要好。
矿⽯在炉内被煤⽓还原的难易程度称为还原性。
褐铁矿⼤于⾚铁矿⼤于磁铁矿,⼈造富矿⼤于天然铁矿,疏松结构、微⽓孔多的矿⽯还原性好。
⑥冶⾦性能优良。
冷态、热态强度好,软化熔融温度⾼、区间窄。
钢铁冶金学(炼钢学)
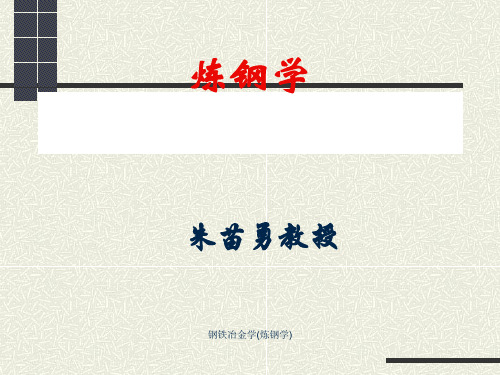
炼 钢 方 法(6)
• 瑞典人罗伯特·杜勒首先进行了氧气顶吹 转炉炼钢的试验,并获得了成功。1952 年奥地利的林茨城(Linz)和多纳维兹城 (Donawitz)先后建成了30吨的氧气顶吹 转炉车间并投入生产,所以此法也称为 LD法。美国称为BOF法(Basic Oxygen Furnace)或BOP法。
钢铁冶金学(炼钢学)
钢 O铁B冶M金学/ Q(炼-钢B学O) P
炼 钢 方 法(8)
• 在顶吹氧气转炉炼钢发展的同时,19781979年成功开发了转炉顶底复合吹炼工 艺,即从转炉上方供给氧气(顶吹氧), 从转炉底部供给惰性气体或氧气,它不仅 提高钢的质量,降低了消耗和吨钢成本, 更适合供给连铸优质钢水。
钢铁冶金学(炼钢学)
钢铁冶金学(炼钢学)
钢铁冶金学(炼钢学)
LD/ BOF/ BOP
炼 钢 方 法(7)
• 1965年加拿大液化气公司研制成双层管氧 气喷嘴,1967年西德马克西米利安钢铁公 司引进此技术并成功开发了底吹氧转炉炼钢 法,即OBM法(Oxygen Bottom Maxhuette) 。1971年美国钢铁公司引进 OBM法,1972年建设了3座200吨底吹转 炉,命名为Q-BO钢铁P冶金(学Q(炼钢u学i)et BOP)。
钢L铁D冶金- 学Q(炼- 钢B学O) P
炼 钢 方 法(9)
•我国首先在 1972-1973 年 在沈阳第一炼钢 厂成功开发了全 氧侧吹转炉炼钢 工艺。并在唐钢 等企业推广应用。
钢铁冶金学(炼钢学)
总之,炼钢技术经过200多 年的发展,技术水平、自动化程 度得到了很大的提高,21世纪炼 钢技术会面临更大的挑战,相信 会有不断的新技术涌现。
1.1 炼钢的发展历程
钢铁冶金学炼钢部分总结(知识点)
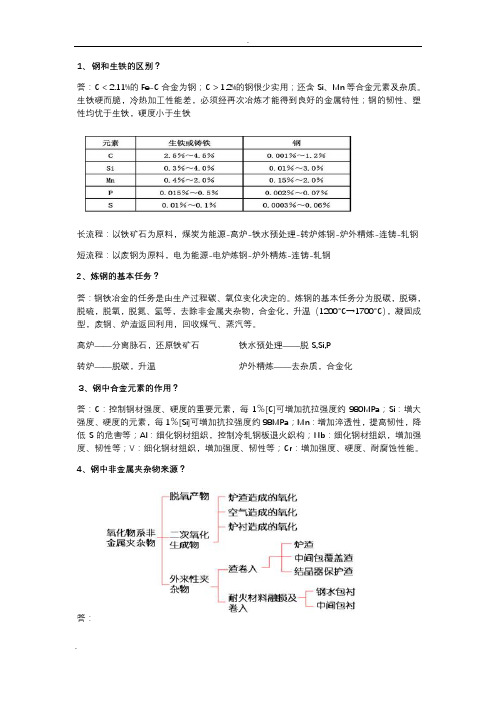
1、钢和生铁的区别?答:C<2.11%的Fe-C合金为钢;C>1.2%的钢很少实用;还含Si、Mn等合金元素及杂质。
生铁硬而脆,冷热加工性能差,必须经再次冶炼才能得到良好的金属特性;钢的韧性、塑性均优于生铁,硬度小于生铁长流程:以铁矿石为原料,煤炭为能源-高炉-铁水预处理-转炉炼钢-炉外精炼-连铸-轧钢短流程:以废钢为原料,电为能源-电炉炼钢-炉外精炼-连铸-轧钢2、炼钢的基本任务?答:钢铁冶金的任务是由生产过程碳、氧位变化决定的。
炼钢的基本任务分为脱碳,脱磷,脱硫,脱氧,脱氮、氢等,去除非金属夹杂物,合金化,升温(1200°C→1700°C),凝固成型,废钢、炉渣返回利用,回收煤气、蒸汽等。
高炉——分离脉石,还原铁矿石铁水预处理——脱S,Si,P转炉——脱碳,升温炉外精炼——去杂质,合金化3、钢中合金元素的作用?答:C:控制钢材强度、硬度的重要元素,每1%[C]可增加抗拉强度约980MPa;Si:增大强度、硬度的元素,每1%[Si]可增加抗拉强度约98MPa;Mn:增加淬透性,提高韧性,降低S的危害等;Al:细化钢材组织,控制冷轧钢板退火织构;Nb:细化钢材组织,增加强度、韧性等;V:细化钢材组织,增加强度、韧性等;Cr:增加强度、硬度、耐腐蚀性能。
4、钢中非金属夹杂物来源?答:5、主要炼钢工艺流程?答:炒钢→坩埚熔炼等→平炉炼钢→电弧炉炼钢→氧气顶吹转炉炼钢→氧气底吹转炉和顶底复吹炼钢。
主要生产工艺为转炉炼钢工艺和电炉炼钢工艺。
与电炉相比,氧气顶吹转炉炼钢生产率高,对铁水成分适应性强,废钢使用量高,可生产低S、低P、低N的杂质钢,可生产几乎所有主要钢品种。
顶底复吹工艺过氧化程度低,熔池搅拌好,金属-渣反应快,控制灵活,成渣快。
现代炼钢流程:炼铁,炼钢(铁水预处理、炼钢、炉外精炼),连铸,轧钢,主要产品。
6、铁的氧化和熔池的基本传氧方式?答:火点区:氧流穿入熔池某一深度并构成火焰状作用区(火点区)。
钢铁冶金学(炼钢部分)
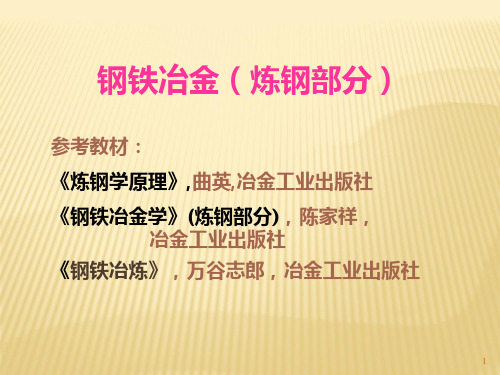
耐火材料融损及 卷入
炼钢任务:
9)凝固成型
12
炼钢的基本任务:
1、脱碳; 2、脱磷; 3、脱硫; 4、脱氧; 5、脱氮、氢等; 6、去除非金属夹杂物; 7、合金化; 8、升温; 9、凝固成型 。
13
主要炼钢工艺: 铁水预处理; 转炉或电弧炉炼钢; 炉外精炼(二次精炼); 连铸。
14
3
伴随脱碳反应, 钢的熔点提高。
炼钢任务: 4)升温
1200℃ 1700℃
4
伴随脱碳反应,钢液[O]含量增加。
C(石墨)+1/2O2=CO C(石墨)=[C] 1/2O2=[O]
[C]+[O]=CO
G=-116204-83.617040-2.88T[2]
G=-20482-38.94T
[1]Reed Thomas, Free Energy of Formation of Binary Compounds, MIT Press, 1971 [2]J.F. Elliott, Thermochemistry for Steelmaking, Vol.2, Addison-Wesley 1963
30
熔池在氧流作用下形成的强烈运动和高度弥散的气 体-熔渣-金属乳化相,是吹氧炼钢的特点。
1-氧枪 2-乳化相 3-CO气泡 4-金属熔池 5-火点 6-金属液滴 7-作用区释放出的 CO气泡 8-溅出的金属液滴 9-烟尘
31
2、铁的氧化和还原
向熔池吹氧时
第一步,气体氧分子分解并吸附在铁的表面:
5
0.6
炼钢任务:
¬ wt% [O]£
1650¡ æ 0.5 0.4 0.3 0.2 0.1 0 0 0.2 0.4 0.6 0.8 1
钢铁冶金学炼铁部分第三版
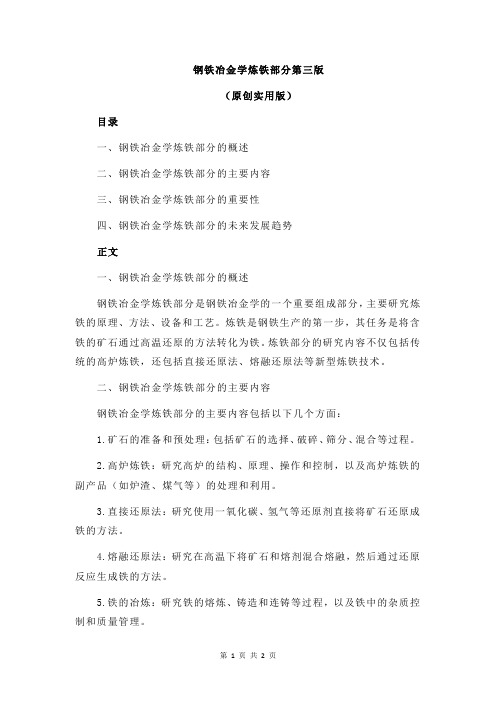
钢铁冶金学炼铁部分第三版(原创实用版)目录一、钢铁冶金学炼铁部分的概述二、钢铁冶金学炼铁部分的主要内容三、钢铁冶金学炼铁部分的重要性四、钢铁冶金学炼铁部分的未来发展趋势正文一、钢铁冶金学炼铁部分的概述钢铁冶金学炼铁部分是钢铁冶金学的一个重要组成部分,主要研究炼铁的原理、方法、设备和工艺。
炼铁是钢铁生产的第一步,其任务是将含铁的矿石通过高温还原的方法转化为铁。
炼铁部分的研究内容不仅包括传统的高炉炼铁,还包括直接还原法、熔融还原法等新型炼铁技术。
二、钢铁冶金学炼铁部分的主要内容钢铁冶金学炼铁部分的主要内容包括以下几个方面:1.矿石的准备和预处理:包括矿石的选择、破碎、筛分、混合等过程。
2.高炉炼铁:研究高炉的结构、原理、操作和控制,以及高炉炼铁的副产品(如炉渣、煤气等)的处理和利用。
3.直接还原法:研究使用一氧化碳、氢气等还原剂直接将矿石还原成铁的方法。
4.熔融还原法:研究在高温下将矿石和熔剂混合熔融,然后通过还原反应生成铁的方法。
5.铁的冶炼:研究铁的熔炼、铸造和连铸等过程,以及铁中的杂质控制和质量管理。
三、钢铁冶金学炼铁部分的重要性钢铁冶金学炼铁部分对于我国钢铁工业的发展具有重要意义,主要表现在以下几个方面:1.提高钢铁产量:炼铁是钢铁生产的第一步,其产量和质量直接影响到钢铁的总产量和质量。
2.降低生产成本:研究炼铁过程中的节能、减排和资源综合利用等技术,有助于降低钢铁生产的成本。
3.提高钢铁质量:研究炼铁过程中的杂质控制和质量管理技术,有助于提高钢铁的质量和性能。
4.保护环境:研究炼铁过程中的环保技术和副产品利用,有助于减少污染,实现绿色生产。
四、钢铁冶金学炼铁部分的未来发展趋势随着科技的进步和社会的发展,钢铁冶金学炼铁部分将面临以下发展趋势:1.绿色发展:加大对环保技术和副产品利用的研究,实现炼铁过程的绿色化和可持续发展。
2.智能化:借助大数据和人工智能技术,实现炼铁过程的智能化控制和优化,提高生产效率和质量。
钢铁冶金学炼铁部分第三版
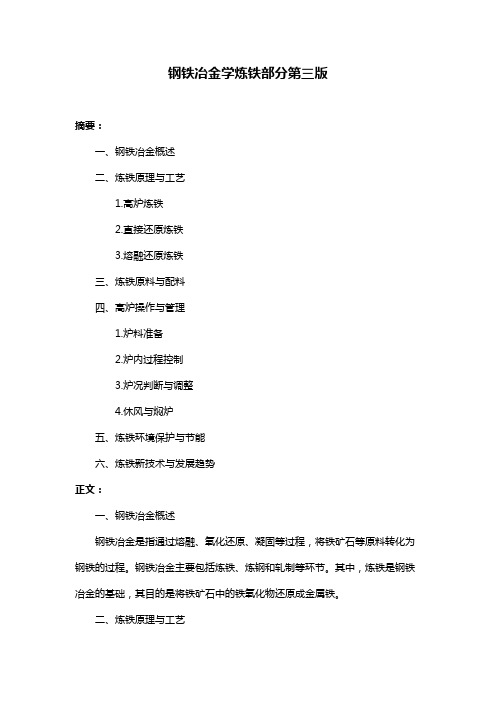
钢铁冶金学炼铁部分第三版摘要:一、钢铁冶金概述二、炼铁原理与工艺1.高炉炼铁2.直接还原炼铁3.熔融还原炼铁三、炼铁原料与配料四、高炉操作与管理1.炉料准备2.炉内过程控制3.炉况判断与调整4.休风与焖炉五、炼铁环境保护与节能六、炼铁新技术与发展趋势正文:一、钢铁冶金概述钢铁冶金是指通过熔融、氧化还原、凝固等过程,将铁矿石等原料转化为钢铁的过程。
钢铁冶金主要包括炼铁、炼钢和轧制等环节。
其中,炼铁是钢铁冶金的基础,其目的是将铁矿石中的铁氧化物还原成金属铁。
二、炼铁原理与工艺1.高炉炼铁高炉炼铁是将铁矿石、焦炭、熔剂等原料经过高温加热,使铁矿石中的铁氧化物被焦炭还原成金属铁的过程。
高炉炼铁具有生产能力大、成本低、金属回收率高等优点。
2.直接还原炼铁直接还原炼铁是将铁矿石等原料在高温下直接还原成金属铁的过程。
与高炉炼铁相比,直接还原炼铁具有能耗低、投资省、占地面积小等优点。
3.熔融还原炼铁熔融还原炼铁是将铁矿石等原料在高温下熔融,然后通过还原剂将铁氧化物还原成金属铁的过程。
熔融还原炼铁具有生产效率高、产品质量好等优点。
三、炼铁原料与配料炼铁原料主要包括铁矿石、焦炭、熔剂等。
铁矿石是炼铁的主要原料,其质量直接影响到炼铁过程和产品质量。
焦炭作为还原剂,在炼铁过程中起到关键作用。
熔剂主要用于调节炉内气氛和矿石的熔化。
四、高炉操作与管理1.炉料准备炉料准备包括铁矿石、焦炭、熔剂等原料的采购、储存、破碎、筛分等环节。
合理的炉料准备有利于保证高炉炼铁的稳定运行。
2.炉内过程控制炉内过程控制是高炉炼铁的关键,主要包括煤气流量、温度、压力等参数的调节。
通过炉内过程控制,可以使高炉达到最佳状态,提高金属回收率。
3.炉况判断与调整炉况判断与调整是根据高炉运行参数,判断高炉内发生的问题,并采取相应措施进行调整。
合理的炉况判断与调整有助于提高高炉炼铁的生产效率。
4.休风与焖炉休风是指高炉在短时间内停止煤气供应,以清理炉内积料和调整炉内气氛。
钢铁冶金学炼铁部分第三版
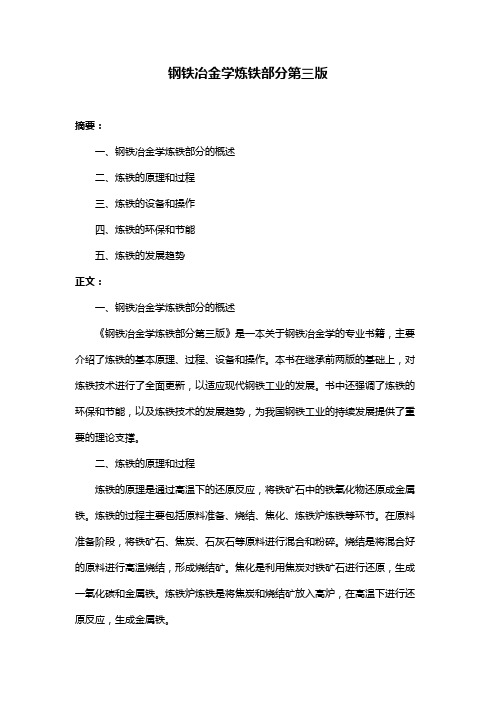
钢铁冶金学炼铁部分第三版摘要:一、钢铁冶金学炼铁部分的概述二、炼铁的原理和过程三、炼铁的设备和操作四、炼铁的环保和节能五、炼铁的发展趋势正文:一、钢铁冶金学炼铁部分的概述《钢铁冶金学炼铁部分第三版》是一本关于钢铁冶金学的专业书籍,主要介绍了炼铁的基本原理、过程、设备和操作。
本书在继承前两版的基础上,对炼铁技术进行了全面更新,以适应现代钢铁工业的发展。
书中还强调了炼铁的环保和节能,以及炼铁技术的发展趋势,为我国钢铁工业的持续发展提供了重要的理论支撑。
二、炼铁的原理和过程炼铁的原理是通过高温下的还原反应,将铁矿石中的铁氧化物还原成金属铁。
炼铁的过程主要包括原料准备、烧结、焦化、炼铁炉炼铁等环节。
在原料准备阶段,将铁矿石、焦炭、石灰石等原料进行混合和粉碎。
烧结是将混合好的原料进行高温烧结,形成烧结矿。
焦化是利用焦炭对铁矿石进行还原,生成一氧化碳和金属铁。
炼铁炉炼铁是将焦炭和烧结矿放入高炉,在高温下进行还原反应,生成金属铁。
三、炼铁的设备和操作炼铁的主要设备包括烧结炉、焦炉、高炉等。
烧结炉用于将原料进行烧结,形成烧结矿。
焦炉用于焦化,生成焦炭。
高炉用于炼铁,将铁矿石通过还原反应生成金属铁。
炼铁的操作主要包括原料配比、烧结矿破碎、烧结、焦化、高炉炼铁等环节。
四、炼铁的环保和节能炼铁过程中会产生大量的烟尘、二氧化硫等污染物,需要采取相应的环保措施进行治理。
目前,我国炼铁企业普遍采用除尘、脱硫等技术,有效降低了污染物排放。
此外,炼铁企业还通过提高资源利用率、降低能耗等措施,实现了炼铁过程的节能减排。
五、炼铁的发展趋势随着我国钢铁工业的转型升级,炼铁技术也在不断发展。
未来,炼铁技术将朝着绿色、高效、智能化的方向发展。
具体表现在:提高炼铁矿利用率,降低能耗;推广绿色炼铁技术,降低污染物排放;应用智能化技术,提高炼铁生产效率。
钢铁冶金学(炼铁)课件第2章

第二章铁矿粉造块(Agglomeration of Fine Iron Ores)2.1 铁矿粉造块的意义和作用铁矿石造块的必要性现代高炉(Blast furnace)生产对原料(Raw materials)提出更加严格的要求(精料方针);天然富矿(Natural rich ore)少,富矿粉(Ore fines)和贫矿(Lean ore)选矿(Ore-dressing或Beneficiation)后的精矿粉(Concentrates)粒度(Size)细,不适合在填充床(Packed bed)中的冶炼;通过造块工艺,可改善铁矿石(Iron ores)的冶金性能(Metallurgical properties);通过造块过程,可脱除某些杂质,如:S、P、K、Na等;造块过程可综合利用冶金企业产生的大量粉尘(Fines or Dusts)和烟尘(Flue dust)。
我国烧结矿(Sinter)生产的发展铁矿石烧结的发展简史2.2 造块的基础理论散料造块的基础理论2.3 烧结过程(Sintering Process)2.3.1 烧结工艺流程现代烧结生产是一种抽风烧结(Wind-drawing sintering)过程;料层厚度(Sinter mix/blend bed height)为350~700mm;点火温度(Ignition temperature)为950~1200℃;抽风负压(Wind-drawing negative pressure)为1000~1600mmH2O柱;烧结温度(Sintering temperature)为1260~1500℃。
烧结过程沿料层高度的变化状况1. 烧结矿层(Sinter ore layer)——上冷下热,约40~50 mm为脆性层(T低、急冷);2. 燃烧层(Combustion layer)——即烧结层(Sintering layer),厚度约为15~50 mm,温度为1100~1400℃,主要反应为燃烧反应;3. 预热层(Preheating layer)——厚度为20~40 mm,特点是热交换剧烈,温度快速下降,主要反应为水分蒸发、结晶水及石灰石分解、矿石氧化还原及固相反应;4. 冷料层(Mix/Blend layer)——即过湿层(Wetting layer),上层带入的水分由于温度低而凝结,¯过多的重力水使混合料小球被破坏¯影响料层透气性(Permeability);5. 垫底料层(Hearth layer)——为保护烧结机炉篦子不因燃烧带下移而烧坏。
钢铁冶金学工艺原理—炼铁部分

1982年4000万吨钢 1996年1.01亿吨 2003年2.22亿吨 2005年3.49亿吨 2006年4.23亿吨 2008年5.00亿吨
2009年5.65亿吨
1.5 钢铁联合企业中的炼铁生产
钢铁联合企业系统作业图
1.5 钢铁联合企业中的炼铁生产
钢铁联合企业:将铁矿石在高炉内冶炼成生铁,用铁水炼成 钢,再将钢水铸成钢锭或连铸坯,经轧制等塑性变形方法加 工成各种用途的钢材
1.6.1 高炉炼铁的本质及生产工艺流程
高炉炼铁的本质
还原:将铁的氧化物还原为金属铁 造渣:实现渣铁分离 加热与控制:获得温度与化学成分合格的铁水
生 产 工 艺 流 程
1.6.2 高炉结构及附属设备
高炉内型
概念:高炉是一个竖立圆筒形炉子,其内部工作空间的形 状称为高炉内型,即通过高炉中心线的剖面轮廓。现代高 炉内型一般由炉缸、炉腹、炉腰、炉身、炉喉五段组成
特点:两头小,中间粗略带锥度的圆柱形空间 高炉有效容积:由高炉出铁口中心线所在水平面到大料钟
下降位置下沿水平面之间的容积。目前我国最大的高炉是 上海宝山钢铁总厂的l号高炉,容积为4063m3。在国外已 有5000m3以上的巨型高炉
高炉内型尺寸
H-全高,H=Hu十H6 Hu-有效高度,
Hu=hl十h2十h3十h4十h5 h0—死铁层高度 h1-炉缸高度 h2—炉腹高度 h3—炉腰高度 h4—炉身高度 H5 —炉喉高度 H6 —炉头高度 D —炉腹直径 al—炉喉直径 a0—大钟直径
1.6.4 高炉炼铁原料及其他辅助材料
分类 赤铁矿
矿物成分: Fe2O3,TFe70%,红色或褐色,又称红 矿。一般无磁性
晶形:α-Fe2O3,γ-Fe2O3(有磁性) 硬度:5.3~6 常形成巨大矿床,占铁矿总储量48.3% 脉石成分:石英、硅酸盐 有害元素:硫、磷、砷较少
钢铁冶金学(炼铁部分)
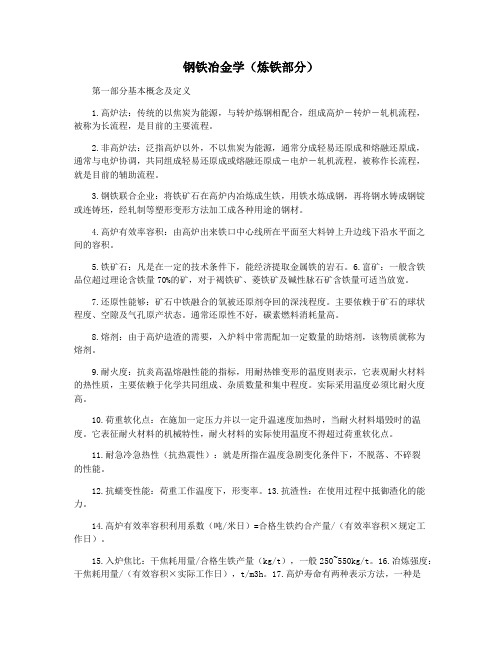
钢铁冶金学(炼铁部分)第一部分基本概念及定义1.高炉法:传统的以焦炭为能源,与转炉炼钢相配合,组成高炉―转炉―轧机流程,被称为长流程,是目前的主要流程。
2.非高炉法:泛指高炉以外,不以焦炭为能源,通常分成轻易还原成和熔融还原成,通常与电炉协调,共同组成轻易还原成或熔融还原成―电炉―轧机流程,被称作长流程,就是目前的辅助流程。
3.钢铁联合企业:将铁矿石在高炉内冶炼成生铁,用铁水炼成钢,再将钢水铸成钢锭或连铸坯,经轧制等塑形变形方法加工成各种用途的钢材。
4.高炉有效率容积:由高炉出来铁口中心线所在平面至大料钟上升边线下沿水平面之间的容积。
5.铁矿石:凡是在一定的技术条件下,能经济提取金属铁的岩石。
6.富矿:一般含铁品位超过理论含铁量70%的矿,对于褐铁矿、菱铁矿及碱性脉石矿含铁量可适当放宽。
7.还原性能够:矿石中铁融合的氧被还原剂夺回的深浅程度。
主要依赖于矿石的球状程度、空隙及气孔原产状态。
通常还原性不好,碳素燃料消耗量高。
8.熔剂:由于高炉造渣的需要,入炉料中常需配加一定数量的助熔剂,该物质就称为熔剂。
9.耐火度:抗炎高温熔融性能的指标,用耐热锥变形的温度则表示,它表观耐火材料的热性质,主要依赖于化学共同组成、杂质数量和集中程度。
实际采用温度必须比耐火度高。
10.荷重软化点:在施加一定压力并以一定升温速度加热时,当耐火材料塌毁时的温度。
它表征耐火材料的机械特性,耐火材料的实际使用温度不得超过荷重软化点。
11.耐急冷急热性(抗热震性):就是所指在温度急剧变化条件下,不脱落、不碎裂的性能。
12.抗蠕变性能:荷重工作温度下,形变率。
13.抗渣性:在使用过程中抵御渣化的能力。
14.高炉有效率容积利用系数(吨/米日)=合格生铁约合产量/(有效率容积×规定工作日)。
15.入炉焦比:干焦耗用量/合格生铁产量(kg/t),一般250~550kg/t。
16.冶炼强度:干焦耗用量/(有效容积×实际工作日),t/m3h。
钢铁冶金学炼铁学
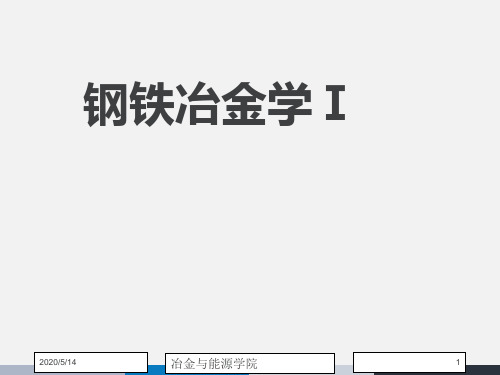
一、钢铁工业在国民经济中的地位 1、发展钢铁工业的条件 2、钢铁材料的优越性能
二、钢铁企业的炼铁生产
从矿石到钢材的生产可分为两个流程。 1、高炉—转炉—轧机 “长流程”主要流程 2、直接还原或熔融还原—电炉—轧机 “短流程”
2019/2/23
冶金与能源学院
4
三、高炉
炉喉 炉身
炉腰 炉腹 炉缸 死铁层
2019/2/23冶金与能源学院源自122 高炉用原 燃料
2019/2/23
冶金与能源学院
13
2 高炉用原燃料
2.1 铁矿石(烧结矿、球团矿、天然块矿 ) 基本定义: 矿物:自然界存在的自然元素和化合物。 矿石:可以提取有用物质并获取利润的矿物。 脉石:不可以提取有用物质或不能获取利润的矿物。 铁矿石种类:赤铁矿(Fe2O3),红色; 磁铁矿(Fe3O4),黑色,有磁性; 褐铁矿(Fe2O3· nH2O),含有结晶水; 菱铁矿(FeCO3)碳酸盐。
2019/2/23
冶金与能源学院
8
六、高炉辅助设备
1、供料系统 2、送风系统 3、除尘系统 4、渣铁处理系统 5、燃料喷吹系统
七、高炉冶炼的概况
分为五带: 1、块状带:间接还原 分解反应 CaCO3=CaO+CO2 部分直接还原 FeO+C=Fe+CO
2019/2/23
冶金与能源学院
9
2、软熔带:造渣 CaO+SiO2+Al2O3=硅酸盐 渗碳反应:3Fe+2CO=Fe3C+CO2 3、滴落带:直接还原(FeO)+C= (MnO)+C= ( SiO2 )+C= ( P2O5 )+C= 4、风口燃烧带:2C+O2=2CO 5、炉缸部分:脱硫反应 FeS+CaO+C =CaS+ Fe+CO
钢铁冶金学炼铁部分第三版
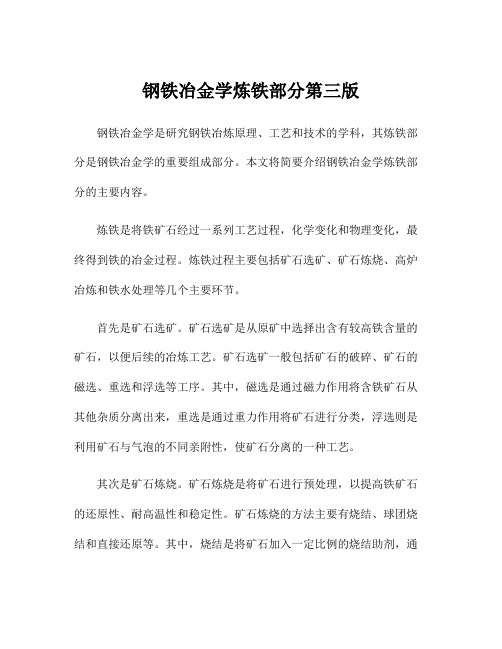
钢铁冶金学炼铁部分第三版钢铁冶金学是研究钢铁冶炼原理、工艺和技术的学科,其炼铁部分是钢铁冶金学的重要组成部分。
本文将简要介绍钢铁冶金学炼铁部分的主要内容。
炼铁是将铁矿石经过一系列工艺过程,化学变化和物理变化,最终得到铁的冶金过程。
炼铁过程主要包括矿石选矿、矿石炼烧、高炉冶炼和铁水处理等几个主要环节。
首先是矿石选矿。
矿石选矿是从原矿中选择出含有较高铁含量的矿石,以便后续的冶炼工艺。
矿石选矿一般包括矿石的破碎、矿石的磁选、重选和浮选等工序。
其中,磁选是通过磁力作用将含铁矿石从其他杂质分离出来,重选是通过重力作用将矿石进行分类,浮选则是利用矿石与气泡的不同亲附性,使矿石分离的一种工艺。
其次是矿石炼烧。
矿石炼烧是将矿石进行预处理,以提高铁矿石的还原性、耐高温性和稳定性。
矿石炼烧的方法主要有烧结、球团烧结和直接还原等。
其中,烧结是将矿石加入一定比例的烧结助剂,通过高温烧结得到具有一定强度的矿石块,球团烧结则是在矿石表面涂覆一层球团剂,通过高温烧结得到球团状的矿石块。
接下来是高炉冶炼。
高炉冶炼是将矿石块和冶炼燃料(焦炭)反应生成铁的过程。
高炉是炼铁的主要设备,一般由炉体、上、下风、煤气管道等组成。
高炉冶炼主要包括炉料装入、炉况操作、还原炉内矿石等几个主要环节。
其中,炉料装入是将经过选矿和炼烧处理的矿石和冶炼燃料按一定的比例装入高炉中,炉况操作是根据高炉内的温度、压力、气体组成等参数来调整高炉操作。
最后是铁水处理。
铁水处理是指通过一系列的工艺过程,将高炉产生的铁水精炼成合格钢铁产品。
铁水处理主要包括脱硫、脱脂、炼石和炼钢等几个环节。
脱硫是通过加入适量的脱硫剂,将铁水中的硫元素还原为低硫铁合金。
脱脂是利用渣浆的剪切作用将铁水中的夹杂物除去。
炼石是指将铁水中的脱硫剂和夹杂物等固体杂质分离出来。
炼钢是通过加入一定比例的合金元素和调整温度、压力等参数,使铁水中的碳含量和合金元素达到所需标准。
综上所述,钢铁冶金学炼铁部分主要包括矿石选矿、矿石炼烧、高炉冶炼和铁水处理等几个重要环节。
- 1、下载文档前请自行甄别文档内容的完整性,平台不提供额外的编辑、内容补充、找答案等附加服务。
- 2、"仅部分预览"的文档,不可在线预览部分如存在完整性等问题,可反馈申请退款(可完整预览的文档不适用该条件!)。
- 3、如文档侵犯您的权益,请联系客服反馈,我们会尽快为您处理(人工客服工作时间:9:00-18:30)。
第一章概论1、试述3种钢铁生产工艺的特点。
答:钢铁冶金的任务:把铁矿石炼成合格的钢。
工艺流程:①还原熔化过程(炼铁):铁矿石→去脉石、杂质和氧→铁;②氧化精炼过程(炼钢):铁→精炼(脱C、Si、P等)→钢。
高炉炼铁工艺流程:对原料要求高,面临能源和环保等挑战,但产量高,目前来说仍占有优势,在钢铁联合企业中发挥这重大作用。
直接还原和熔融还原炼铁工艺流程:适应性大,但生产规模小、产量低,而且很多技术问题还有待解决和完善。
2、简述高炉冶炼过程的特点及三大主要过程。
答:特点:①在逆流(炉料下降及煤气上升)过程中,完成复杂的物理化学反应;②在投入(装料)及产出(铁、渣、煤气)之外,无法直接观察炉反应过程,只能凭借仪器仪表简介观察;③维持高炉顺行(保证煤气流合理分布及炉料均匀下降)是冶炼过程的关键。
三大过程:①还原过程:实现矿石中金属元素(主要是铁)和氧元素的化学分离;②造渣过程:实现已还原的金属与脉石的熔融态机械分离;③传热及渣铁反应过程:实现成分与温度均合格的液态铁水。
3、画出高炉本体图,并在其图上标明四大系统。
答:煤气系统、上料系统、渣铁系统、送风系统。
4、归纳高炉炼铁对铁矿石的质量要求。
答:①高的含铁品位。
矿石品位基本上决定了矿石的价格,即冶炼的经济性。
②矿石中脉石的成分和分布合适。
脉石中SiO2和Al2O3要少,CaO多,MgO含量合适。
③有害元素的含量要少。
S、P、As、Cu对钢铁产品性能有害,K、Na、Zn、Pb、F对炉衬和高炉顺行有害。
④有益元素要适当。
Mn、Cr、Ni、V、Ti 等和稀土元素对提高钢产品性能有利。
上述元素多时,高炉冶炼会出现一定的问题,要考虑冶炼的特殊性。
⑤矿石的还原性要好。
矿石在炉被煤气还原的难易程度称为还原性。
褐铁矿大于赤铁矿大于磁铁矿,人造富矿大于天然铁矿,疏松结构、微气孔多的矿石还原性好。
⑥冶金性能优良。
冷态、热态强度好,软化熔融温度高、区间窄。
⑦粒度分布合适。
太大,对还原不利;太小,对顺行不利。
5、试述焦炭在高炉炼铁中的三大作用及其质量要求。
答:焦炭在高炉的作用:(1)热源:在风口前燃烧,提供冶炼所需的热量;(2)还原剂:固体碳及其氧化产物CO是氧化物的还原剂;(3)骨架作用:焦炭作为软融带以下唯一的以固态存在的物料,是支撑高达数十米料柱的骨架,同时又是煤气得以自下而上畅通流动的透气通路;(4)铁水渗碳。
质量的要求:粒度适中、足够的强度、灰分少、硫含量少、挥发成分含量合适、反应性弱(C+CO2=2CO)、固定C高等。
6、试述高炉喷吹用煤粉的质量要求。
答:1、灰分含量低、固定碳量高;2、含硫量少;3、可磨性好;4、粒度细;5、爆炸性弱,以确保在制备及输送过程中的人身及设备安全;6、燃烧性和反应性好。
7、熟练掌握高炉冶炼主要技术经济指标的表达方式。
η:每M3高炉有效容积每昼夜生产的合格铁量答:1、有效容积利用系数u(T/M 3.d)。
2、焦比:冶炼每吨生铁所消耗焦炭的千克数(kg/T)。
3、煤比:冶炼每吨生铁所消耗的煤粉的千克数(kg/T)。
4、燃料比(焦比+煤比+油比):冶炼每吨生铁所消耗的固体和液体燃料的总和(kg/T)。
5、综合焦比(焦比+煤比×煤焦置换比))()()()(t kg 产量折算合格生铁干焦耗用量入炉焦比折算= )()()()(t kg 产量折算合格生铁综合干焦耗用量综合焦比折算=6、煤焦置换比:喷吹1kg 煤粉所能替代的焦炭的kg 数。
一般为0.8~1.0(不包括褐煤)。
7、焦炭冶炼强度:每M 3高炉有效容积每昼夜燃烧的焦炭吨数(t/ M 3.d)。
通常为0.8~1.0t/M 3.d 。
8、综合冶炼强度:每M 3高炉有效容积每昼夜燃烧的综合焦炭的吨数(t/M 3.d)。
一般为0.9~1.15t/M 3.d 。
9、利用系数、焦比及冶炼强度三者关系:纯焦冶炼时,利用系数=焦炭冶炼强度/焦比;喷吹燃料时:利用系数=综合冶炼强度/综合焦比。
10、燃烧强度:每M 3炉缸截面积每昼夜燃烧的焦炭的吨数(t/ M 3.d)11、工序能耗Ci =(燃料消耗+动力消耗-回收二次能源)/产品产量(吨标准煤/T),1kg 标准煤的发热量为29310 kJ(7000千卡)。
注:1、把铁矿石炼成合格的钢:①还原熔化过程(炼铁):铁矿石→去脉石、杂质和氧→铁;②氧化精炼过程(炼钢):铁→精炼(脱C 、Si 、P 等)→钢。
2、高炉原料:①铁矿石(凡是在当前的技术条件下,可经济地提取出金属铁的岩石,称为铁矿石。
地壳中Fe 元素居第四位,占4.2 %;在鉄矿石中不存在纯金属的铁,而是以氧化物、硫化物的形式存在;除含Fe 氧化物外,含有其他化合物,统称为脉石,常见的SiO 2、Al 2O3、CaO 、MgO 。
):天然富矿、人造富矿(烧结矿、球团矿);②熔剂:碱性熔剂(石灰、石灰石、白云石)、酸性熔剂(硅石)、特殊熔剂(萤石);③其他含铁代用品(要求含铁梁高、杂质少、有一定的块度):高炉和转炉炉尘、残铁、轧钢铁皮、硫酸渣。
3、铁矿石的分类:赤铁矿(Fe 2O 3),理论含Fe70%,红条痕,较软,易还原;铁矿(Fe 3O 4),理论含Fe72.4%,黑条痕,较硬,难还原;褐铁矿(xFe 2O 3.yH 2O),黄褐条痕,疏松多孔,易还原;菱铁矿(FeCO 3),理论含Fe48.2%,灰黄条痕,焙烧后易还原。
由于地表的氧化作用,自然界中纯磁铁矿少见。
磁铁矿变成:半假象赤铁矿(Fe/FeO 在3.5-7)或假象赤铁矿(Fe/FeO>7)。
所谓假象:化学成分:Fe 3O 432e O F →,结晶构造不变,保持磁铁矿特征。
4、高炉燃料:气体燃料(焦炉煤气、高炉煤气)用于热风炉;固体燃料(焦炭、煤粉)用于高炉本体。
第二章铁矿粉造块1、试述高炉冶炼对含铁原料的要求,如何达到这些要求?答:贫矿经选矿后的精矿粉经造块(烧结或球团过程),可改善矿石的冶金性能,脱去某些杂质(S、P、K、Na等),并综合利用大量粉尘和烟尘。
2、简述固相反应的特点及对烧结反应的影响。
答:在一定温度下,某些离子克服晶格结合力,进行位置交换,并扩散到与之相邻的其它晶格的过程,称为固相反应。
特点:反应温度远低于固相反应物的熔点或它们的低共熔点;温度高有利于固相反应的进行;固相反应受化学组成的影响,虽不能形成有效的固相连接,但为液相的生成提供了前提条件(低熔点的固相反应产物)。
3、简述烧结矿的固结机理,何种液相利于烧结矿质量的提高?答:固结机理:烧结物料中主要矿物是高熔点的,当被加热到一定温度时,各组分间有了固相反应,生成新的能与原组分形成具有低共熔点的化合物,使得它们在较低的温度下生成液相,开始熔融。
熔融的液态物质冷却时成为那些尚未溶入液相的颗粒的坚固的连接桥,从而实现固结。
粘结相由铁酸钙组成。
可使烧结矿的强度和还原性同时得到提高。
这是因为:①铁酸钙(CF)自身的强度和还原性都很好;②铁酸钙是固相反应的最初产物,熔点低,生成速度快,超过正硅酸钙的生成速度,能使烧结矿中的游离CaO和正硅酸钙减少,提高烧结矿的强度;③由于铁酸钙能在较低温度下通过固相反应生成,减少Fe2O3和Fe3O4的分解和还原,从而抑制铁橄榄石的形成;改善烧结矿的还原性。
4、改善烧结料层透气性的对策如何?5、试述烧结生产中“自动蓄热现象”扬长避短的技术对策。
答:扬长:厚料层烧结技术正是基于自动蓄热技术的,为降低固体燃料提供了可能,也为低温烧结技术创造了有利条件。
同时对改善烧结矿质量亦有好处。
避短:自动蓄热现象导致烧结料层上下热量不均匀,上部热量不足,下部过剩。
所以应该控制燃料在料层高度上的分布,以降低燃料消耗,节约能量。
6、试述低温烧结理论的要点。
答:高碱度下生成的钙的铁酸盐——铁酸钙,不仅还原性好,而且强度也高。
铁酸钙主要是由Fe2O3和CaO组成。
烧结温度超过1300℃后,Fe2O3易发生热分解,形成Fe3O4和FeO,而Fe3O4是不能与CaO结合的。
相反,FeO的出现会导致2FeO•SiO2,CaO•FeO•SiO2的生成,从而恶化还原性。
不同形态的铁酸钙组成的烧结矿,其质量是不同的;而烧结温度对铁酸钙的形态影响显著。
为了生成铁酸钙矿物,需要实现低温烧结工艺。
7、归纳影响烧结矿强度的因素。
8、简述影响烧结矿还原性的因素以及提高还原性的主攻方向。
9、简述铁精矿粉的成球机理,并讨论其影响因素。
答:铁精粉粒度小,表面能大,存在着以降低表面力来降低表面能的倾向,易发生吸附现象。
含铁粉料多为氧化矿物,易吸附水。
其中部分水在微细空隙中产生凹液面,具有将细粒了挤向水滴而凝聚的作用。
即毛细水对成球过程的主导作用。
加水润湿的同时,机械滚动作用使靠水润湿产生的母球被挤压,毛细结构变化,挤出毛细水,过湿表面又吸附分矿使母球长大。
形成母球。
母球是造球的核心,靠加水润湿产生母球长大(机械力+润湿作用)。
滚动中压紧→毛细结构变化→挤出毛细水→过湿表面又粘附粉矿→母球长大生球压实(机械力作用)。
使矿粉颗粒以最紧密方式排列,最大限度发挥水的分子引力、毛细管力以及物料的摩擦阻力,使生球强度大大提高。
10、简述氧化球团矿的焙烧固结机理。
答:1)Fe2O3的微晶键连接:磁铁矿生球在氧化气氛中焙烧时,当加热到200~300℃就开始氧化形成Fe2O3微晶。
由于新生的Fe2O3微晶中原子迁移能力较强,在各个颗粒的接触面上长大成“连接桥”(又称Fe2O3微晶键),使颗粒互相连接起来。
在900℃以下焙烧时,这种连接形式使球团矿具有一定的强度。
但由于温度低,Fe2O3微晶长大有限,因此仅靠这种形式连接起来的球团矿强度是不够。
2)Fe2O3的再结晶:当磁铁矿生球在氧化性气氛下继续加热到1000~1300℃时,磁铁矿可全部转变成赤铁矿,而由磁铁矿氧化形成的Fe2O3微晶开始再结晶,使一个个相互隔开的微晶长大成连成一片的赤铁矿晶体,使球团矿具有很高的氧化度和强度。
3)在缺乏氧气的地方温度达到一定水平时,磁铁矿颗粒也能够通过扩散产生Fe3O4晶键连接,然后再更高温度下,发生Fe3O4的再结晶和晶粒长大,使磁铁矿颗粒结合成一个整体。
4)液相粘结:两颗矿粒被液相粘结起来,如果生产酸性球团矿,在氧化气氛中,可能产生的液相为低熔点的脉石矿物或添加剂藻土等。
在中性或弱还原性气氛中焙烧,则磁铁矿与脉石中的二氧化硅反应,产生2FeO.SiO2液相。
注:1、烧结矿—加入CaO,还原性;球团矿—加入MgO,软熔性能。
2、散粒物料聚结现象是颗粒间相互联结力与相互排斥力作用的结果,结合力=联结力-排斥力(重力)。
3、烧结过程矿层分布:烧结矿层—上冷下热,约40~50 mm为脆性层(T低、急冷),冷烧结矿层和热烧结矿层;燃烧层—即烧结层,厚度约为15~50mm,温度为1100~1400℃,主要反应为燃烧反应;预热层—厚度为20~40 mm,特点是热交换剧烈,温度快速下降,主要反应为水分蒸发、结晶水及石灰石分解、矿石氧化还原及固相反应;冷料层—即过湿层,上层带入的水分由于温度低而凝结,过多的重力水使混合料小球被破坏 影响料层透气性;垫底料层—为保护烧结机炉篦子不因燃烧带下移而烧坏。