球墨铸铁
球墨铸铁性能和生产工艺
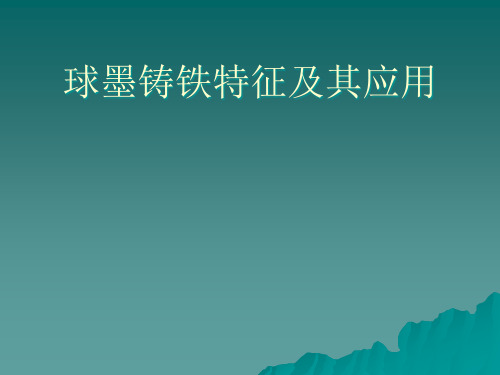
球墨铸铁旳化学成份
选择合适旳化学成份是确保球墨铸铁 取得良好旳金相组织和高性能旳基本条件, 化学成份旳选择既要利于石墨旳球化和取 得满意旳基体,以期取得满意旳性能,又 要使球墨铸铁具有良好旳铸造性能。
一、五大元素
1、碳和硅
因为石墨球对基体旳减弱作用很小,所以碳含量在 3.2-3.8%时,对力学性能无明显影响。拟定球墨铸铁旳 碳硅含量时,主要从确保铸造性能考虑,将碳当量选择在 共晶成份左右。
2、缩孔和缩松
特征:缩孔发生于第一次收缩阶段。 表面凹陷及局部热节凹陷,含气孔旳暗 缩孔,内壁粗糙。缩松发生于第二次收 缩阶段。被树枝晶分割旳溶池处成为真 空,凝固后旳孔壁粗糙、排满树枝晶旳 疏松孔为缩松。
原因:碳当量低,磷含量高,增长缩 孔缩松倾向。
措施:提升铸型刚度,如使用树脂砂, 提升铁液碳当量。
形核物质 1、石墨:未溶石墨、添加晶体石墨、非平 衡石墨 2、岩状构造碳化物基底 3、氧化物 4、硫化物/氧化物 5、铋及铋旳化合物
球墨铸铁旳孕育
球墨铸铁孕育旳主要性 灰铸铁、球墨铸铁孕育旳异同点 孕育衰退现象 提升孕育效果旳措施
a.选择强效孕育剂 b.必要旳S旳含量 c.改善处理措施 d.提升铸件冷却速度
这些条件旳实质在于变化石 墨结晶旳冷却情况。
球墨铸铁旳金相组织与力学性能旳关系
球墨铸铁旳力学性能是和它旳金相 组织亲密有关旳。确保铸铁中石墨球化 良好,是熔制球墨铸铁旳第一要求。
只有石墨球化,才干充分发挥金属 基体旳作用,使铸铁旳力学性能大幅度 提升。也只有石墨球化后,进一步变化 基体旳性能才更有意义。
球墨铸铁旳形成
球状石墨旳形成经历了形核与生长两个阶段。 其中旳形核是石墨旳首要过程,铁液在熔炼及随 即旳球化、孕育处理中产生大量旳非金属夹杂物, 初生旳夹杂物非常小,在随即浇铸、充型、凝固 过程相互碰撞、聚合变大,上浮或下沉,成为石 墨析出旳关键。
球 墨 铸 铁
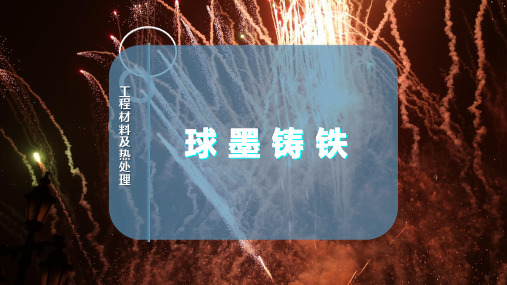
1.2 球墨铸铁的热处理
球墨铸铁的热处理工艺:
主要有退火、正火、调质、等温淬火
1.2 球墨铸铁的热处理
退火的目的在于获得铁素体基体。球化剂增大 铸件的白口化倾向,当铸件薄壁处出现渗碳体时,为 了获得塑性好的铁素体基体,并改善切削性能,消除 铸造应力,根据铸铁的铸造组织,可采用两种退火工 艺。
正火的目的在于温度,又分高温正火(完全奥氏 体化正火)和低温正火(不完全奥氏体化正火)两种。
1.1 球墨铸铁的成分、组织、
性能和用途
应用:
由于球铁具有优异的力学性能,因此可用 于负荷较大、受力较复杂的零件,甚至能代替碳 钢制造某些零件。
如珠光体基体的球铁,常用于制造柴油机曲 轴、连杆、齿轮、机床主轴、蜗轮、蜗杆,轧 钢机的轧辊,水压机的工作缸、缸套、活塞等。 而铁素体的球铁,可用于制造受压阀门、机 器底座、汽车后桥壳等。
工 程 材 料 及 热 处 理
球墨铸铁
石墨成球状的铸铁称为球墨铸铁,是 在灰口铸铁的铁液中加入球化剂(稀土镁合 金等)和变质剂(硅铁)进行球化变质处理 后得到的。
铸造性能好 成本低廉 生产方便
1.1 球墨铸铁的成分、组织、 性能和用途
与灰铸铁相比,它的硫含量较低,而 碳含量较高,一般为过共晶成分,以利于石 墨球化。
但是调质处理一般只适用于小尺寸的铸件,当 尺寸过大时,铸件内部淬不透,处理效果不好。
1.2 球墨铸铁的热处理
淬火等温淬火时,将零件加热到奥氏体区,保温一定时 间后,在300℃左右的等温盐浴中冷却并保温,使基体 在此温度下转变为下贝氏体。球墨铸铁经等温淬火后不 仅可以获得较高的强度,同时还具有良好的塑性和韧性。
1.2 球墨铸铁的热处理
完全奥氏体正火工艺曲线图
球墨铸铁性能及生产工艺
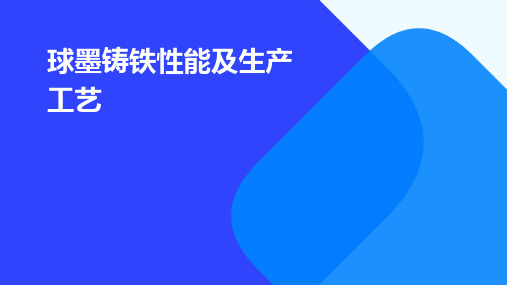
铸造缺陷预防
总结词
铸造缺陷会影响球墨铸铁的质量和性能,因此需要采取一系列措施预防铸造缺陷的产生。
详细描述
在生产过程中,要严格控制浇注温度、模具温度、冷却速度等工艺参数,以防止产生气 孔、缩孔、夹渣等铸造缺陷。同时,要定期检查模具的磨损情况,及时修复和更换损坏
的模具,以防止出现不均匀冷却等缺陷。
质量检测与评估
用于生产建筑构件、水 管、阀门等。
用于制造各种承受复杂 应力的机械零件和工具。
在电力、化工、船舶等 领域也有广泛应用。
02
球墨铸铁性能
力学性能
强度
球墨铸铁具有较高的强度,其抗拉强度和屈 服点均高于灰铸铁。
耐磨性
球墨铸铁的耐磨性优于其他铸铁,适用于需 要承受摩擦和磨损的场合。
韧性
球墨铸铁的韧性较好,不易脆化,能够承受 较大的冲击和振动。
提高生产效率与降低成本
自动化和智能化铸造生产线
采用先进的机器人技术、传感器技术和大数据分析技术, 实现铸造生产线的自动化和智能化,提高生产效率,降低 人工成本。
高效熔炼与连铸技术
研究新型的熔炼和连铸技术,提高铁水的纯净度和连铸坯 的质量,减少生产过程中的损耗和废品率,降低生产成本。
循环经济与资源再利用
的机械性能。
废钢
适量加入废钢,调节铁水成分,降 低成本。
球化剂和孕育剂
选用合适的球化剂和孕育剂,提高 球墨铸铁的球化率和石墨形态。
熔炼与浇注
熔炼
采用电炉或冲天炉熔炼铁水,控制熔炼温度和时间,确保铁 水质量。
浇注
根据铸件的大小和复杂程度,选择合适的浇注系统和浇注温 度,确保铁水充型良好。
球化与孕育处理
通过废旧铸件回收、再生利用和资源循环利用,降低原材 料成本,同时减少对环境的污染。
球 墨 铸 铁

图1-11 球墨铸铁高温正火工艺曲线
2)低温正火
球墨铸铁
一般将铸件加热到820 ℃~860 ℃,保温1~4 h, 然后出炉空冷,获得珠光体 和分散铁素体的球墨铸铁。 低温正火后的铸件的塑性和 韧性提高了,但强度比高温 正火略低,其工艺曲线如图 1-12所示。
图1-12 球墨铸铁低温正火工艺曲线
球墨铸铁
球墨铸铁
图1-9 球墨铸铁低温石墨化退火工艺曲线
球墨铸铁
3)高温石墨化退火
由于球墨铸铁白口倾向较大,因而铸态组织中往往 出现自由渗碳体,为了获得铁素体球墨铸铁,需要进行 高温石墨化退火。
高温石墨化退火工艺是将铸件加热到900 ℃~950 ℃,保温2~4 h,使自由渗碳体石墨化,然后炉冷至 600 ℃,再出炉空冷,其工艺曲线如图1-10所示。
球墨铸铁
2)低温石墨化退火
当铸态基体组织为珠光体+铁素体而无自由渗 碳体存在时,为了获得塑性、韧性较高的铁素体球 墨铸铁,可进行低温石墨化退火。
低温石墨化退火工艺是将铸件加热到共析温度 范围附近,即720 ℃~760 ℃,保温2~8 h,使铸 件发生第三阶段石墨化,然后炉冷至600 ℃,再出 炉空冷,其工艺曲线如图1-9所示。
球墨铸铁的化学成分为ωC=3.6%~3.9%,ωSi=2.0% ~2.8%,ωMn=0.6%~0.8%,ωS<0.04%,ωP<0.1%, ωMg=0.03%~0.05%。与灰铸铁相比,球墨铸铁的碳、硅 含量较高,有利于石墨球化。
球墨铸铁
2. 球墨铸铁的显微组织
球墨铸铁按其基体组 织不同,可分为铁素体球 墨铸铁、铁素体+珠光体 球墨铸铁和珠光体球墨铸 铁三种,它们的显微组织 如图1-8所示。
球墨铸铁除了能采用上述热处理工艺外,还可以采用表面强化处 理,如表面淬火和渗氮等。
球墨铸铁材质牌号

球墨铸铁是一种铸铁材料,其内部原子结构呈现球状,具有高强度、高韧性、良好的加工性能、耐腐蚀性和低成本等优点。
下面将详细介绍几种常见的球墨铸铁材质牌号:
1.QT400-18:这是一种常见的球墨铸铁牌号,其化学成分含碳量约为3.6%,铁的含量占比约为93%。
它的机械性能较高,强度和硬度较好,同时也有一定的韧性和延展性。
QT400-18常用于制造零配件、泵体、阀门等机械零件。
2.QT450-10:另一种常见的球墨铸铁牌号是QT450-10。
它的化学成分含碳量为
3.4%左右,铁的含量占比约为91%。
与QT400-18相比,其强度、硬度和抗腐蚀性都有所提高。
QT450-10主要用于制造重型机械、汽车制品、建筑工程等领域。
3.QT600-3:这种牌号的球墨铸铁具有较高的强度和硬度,同时也具备良好的韧性和延展性。
它主要用于制造要求较高、耐磨性好的零件和部件,如汽车发动机缸体、缸盖等。
4.QT700-2A:这种牌号的球墨铸铁具有更高的强度和硬度,同时也具有较好的韧性和延展性。
它主要用于制造要求更高、耐磨性更好的零件和部件,如航空航天发动机零部件等。
5.QT800-2A:这种牌号的球墨铸铁具有极高的强度和硬度,同时也具有较好的韧性和延展性。
它主要用于制造要求极高、耐磨性最好的零件和部件,如高速列车车轮等。
除了以上介绍的几种牌号外,还有许多其他的球墨铸铁材质牌号,它们都具有不同的化学成分、物理性质和应用领域。
在选择使用时,需要根据具体的应用场景和要求选择合适的材质牌号。
球墨铸铁的化学成分

锰可以部分替代硅的作用,并改善球墨铸铁的铸造 性能和耐腐蚀性。
03
锰含量的增加还可以提高球墨铸铁的淬透性和回火 稳定性。
磷(P)和硫(S)的影响
磷和硫是有害元素,会导致球 墨铸铁脆化,降低其韧性和耐 腐蚀性。
控制磷和硫的含量是生产高质 量球墨铸铁的关键之一。
通过合理的熔炼技术和合金化 处理,可以降低磷和硫的含量, 提高球墨铸铁的性能。
VS
智能制造领域
智能制造的发展对球墨铸铁提出了更高的 要求,需要不断优化材料性能和生产工艺 ,以满足智能制造领域的需求。
感谢您的观看
THANKS
生产与应用
生产
通过高温熔炼、球化和孕育处理、浇 注和冷却等工艺过程制备而成。
应用
广泛应用于汽车、机械、化工、电力 、建筑等工业领域,用于制造各种承 受重载和复杂应力的零部件可以追溯到20世纪初,经过多年的研究和发展,其生产工艺和 应用领域不断拓展。
发展
随着科技的进步和应用需求的不断提高,球墨铸铁在成分优化、工艺改进、性 能提升等方面仍有很大的发展空间。
02
球墨铸铁的化学成分
碳(C)
01
碳是球墨铸铁的主要元素,通常 含量在3.0-3.8%之间。碳有助于 提高铸铁的强度和耐磨性,同时 对韧性也有一定影响。
02
碳含量的增加可以提高铸铁的硬 度和强度,但也会降低韧性。因 此,在选择碳含量时,需要根据 具体的应用需求进行平衡。
硅(Si)
硅是球墨铸铁中常见的元素,通常含 量在1.8-3.0%之间。硅有助于提高 铸铁的强度和耐磨性,同时也有助于 提高铸铁的热稳定性和抗氧化性。
硫含量的增加会降低铸铁的韧性和耐腐蚀性。因此,在选 择硫含量时,应尽量控制其含量在较低水平。
球墨铸铁

三、G球形成的条件及立体外貌
1、 G球形成的条件 一是铁液在凝固时必须有较大的过冷度ΔT; 二是必须使铁液和石墨之间具有较大的界面张力,也就 是使铁液中的杂质(表面活性元素如S、O等)含量足够低; 三是铁液中还必须有一定的球化元素残留量; 四是要有良好的石墨成核条件,即良好的石墨化孕育。 只要满足上上几个条件,就能生产出球墨铸铁。 2、球化处理(孕育)的机理: 在铁液中加入球化剂,使铁液中的表面活性物质硫和氧 降低,铁液中石墨的界面张力增大,同时使铁液过冷度加大, 以促使球状石墨的形成。球化处理后再进行炉前孕育处理, 使石墨的成核条件得以改善,从而获得量大、形小、外形圆 整、成分均匀的球状石墨铸铁。
球状石墨外貌接近球形,内部呈放射状,有明显的 偏光效应。石墨是由很多角锥体枝晶组成的多晶体,各 枝晶的基面垂直于球径C轴呈辐射状指向球心。
片状石墨
球状石墨
四、球状石墨的生长
1、球状石墨的生长条件
a、极低的硫、氧含量 b、限制反球化元素 c、保证必要的冷却速度 d、添加的球化元素
2、石墨球的生长方式
螺旋生长
3、石墨球生长的工艺措施 • 从生产实践中得知,使石墨按球状生长的工艺措施为改变 化学成分和控制冷却速度。 化学成分中,对石墨生长有 重要影响的是一些能显著改变铁液过冷倾向的元素;而引 起铸铁冷却速度产生变化的因素则是铸件壁厚、铸型以及 浇铸。这些条件的实质在于改变石墨结晶的冷却状况。
§3.3.4 球墨铸铁的化学成分及熔制工艺
球墨铸铁的金相组织、性能特点、 牌号及技术要求
球墨铸铁的金相组织: • G+F体、G+P体、G+ F体+ P体等,而且直 接决定着球墨铸铁的力学性能。
球墨铸铁化学成分国家标准

球墨铸铁化学成分国家标准球墨铸铁是一种优质的铸铁材料,具有较高的强度和韧性,广泛应用于机械制造、汽车制造、建筑工程等领域。
为了保证球墨铸铁产品的质量,国家对其化学成分制定了相应的标准,以便生产和使用过程中能够达到统一的质量要求。
根据国家标准,球墨铸铁的化学成分主要包括碳、硅、锰、磷和硫等元素。
其中,碳是影响球墨铸铁组织和性能的主要元素之一。
适当的碳含量可以提高球墨铸铁的强度和韧性,但过高或过低的碳含量都会对其性能造成不利影响。
因此,国家标准对球墨铸铁中碳的含量进行了严格的限制,以确保产品的质量稳定。
除了碳以外,硅是另一个重要的元素。
适当的硅含量可以提高球墨铸铁的流动性和润滑性,有利于铸造过程的顺利进行。
同时,硅还可以稳定铁水中的碳,减少球墨铸铁的组织缺陷,提高产品的性能。
因此,国家标准对球墨铸铁中硅的含量也进行了严格的控制。
此外,锰、磷和硫等元素虽然含量较少,但对球墨铸铁的性能同样有着重要的影响。
锰的适量添加可以提高球墨铸铁的强度和耐磨性,但过高的锰含量会导致铁水的浑浊和晶粒变粗,降低产品的韧性。
而磷和硫是有害元素,其含量过高会导致球墨铸铁的脆性和疲劳性能下降,因此国家标准对其含量也有相应的限制。
总的来说,国家标准对球墨铸铁的化学成分进行了严格的规定,旨在保证产品的质量稳定和性能可靠。
在生产和使用过程中,必须严格按照国家标准的要求进行生产和检测,确保产品符合标准,以满足不同领域的使用需求。
综上所述,球墨铸铁化学成分国家标准的制定对于保障产品质量、推动行业发展具有重要意义。
只有严格遵守标准要求,才能生产出优质的球墨铸铁产品,满足市场需求,推动行业的健康发展。
希望相关企业和生产单位能够重视国家标准,不断提升产品质量,为行业发展做出积极贡献。
球墨铸铁特性及其应用
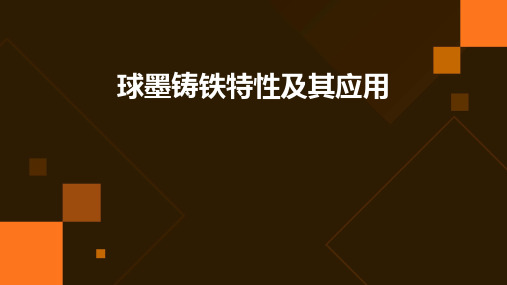
目录
• 球墨铸铁的特性 • 球墨铸铁的生产工艺 • 球墨铸铁的应用领域 • 球墨铸铁的未来发展 • 球墨铸铁的局限性及解决方案
01
球墨铸铁的特性
力学性能
01
02
03
强度和韧性
球墨铸铁具有较高的强度 和韧性,能够承受较大的 压力和冲击力,不易发生 脆性断裂。
抗疲劳性能
由于其良好的韧性和抗疲 劳性能,球墨铸铁在反复 承受压力的情况下仍能保 持其完整性。
铸造工艺改进
采用先进的铸造工艺和设备,提高铸件质量和生产效率。
热处理工艺优化
通过优化热处理工艺,改善球墨铸铁的机械性能和加工性能。
应用领域的拓展
汽车工业
随着新能源汽车和智能驾驶技术的快速发展,球墨铸铁在汽车工业 中的应用将进一步扩大,如发动机部件、悬挂系统等。
轨道交通
随着城市轨道交通的快速发展,球墨铸铁在轨道交通车辆的制造中 具有广泛应用,如转向架、制动系统等。
石油化工
在石油化工领域,球墨铸铁可以用于制造各种压力容器、管道和阀门 等关键部件。
05
球墨铸铁的局限性及解决 方案
成本问题
总结词
球墨铸铁的生产成本较高,这限制了其在某些领域的应用。
详细描述
球墨铸铁的生产需要较高的温度和特殊的处理过程,导致其 成本相对较高。为了解决这一问题,可以采用优化生产工艺 、提高设备效率以及寻找替代材料等方法来降低成本。
耐腐蚀、耐磨损材料
针对特殊环境下的应用,如海洋工程、化工设备 等,研发具有优异耐腐蚀和耐磨损性能的球墨铸 铁材料。
多功能复合材料
通过材料复合技术,将球墨铸铁与其他材料(如 金属、陶瓷等)进行复合,以获得具有多种优异 性能的复合材料。
球墨铸铁的名词解释

球墨铸铁的名词解释球墨铸铁(Ductile Iron),也称球墨铸造铁、球墨球铸铁、球墨铸铁等,是一种铸铁中的一种特殊种类。
它以其优异的机械性能和高强度而被广泛应用于各个领域,从汽车工业到建筑工程,都有着重要的作用。
球墨铸铁是在铸铁基体中添加一定量的镁合金元素(通常为硫酸镁或硫酸镁盐溶解沉淀)后铸造而成。
这种特殊的合金化处理赋予了球墨铸铁既具有铸铁的良好流动性和铸造性能,又具有钢铁的高强度和高韧性。
首先,球墨铸铁的名字来自其外观,它铸造后的铁皮表面呈现出许多球状的石墨颗粒。
这些石墨球形态的存在是由于镁在铁水中与硫形成的镁硫化合物与石墨晶体反应,造成晶体失稳并生成球状石墨颗粒。
这些球状石墨颗粒在弯曲和扭曲应力下具有更好的断裂性能,从而提高了球墨铸铁的韧性和延展性。
其次,球墨铸铁具有出色的机械性能。
相对于灰口铸铁和普通铸铁,球墨铸铁的抗拉强度和抗压强度更高。
这是由于镁在铁水中的作用,能够阻碍石墨晶体的成长,增加铁素体晶格的不规则度,从而提高合金的强度,降低矩阵组织间的应力集中程度。
此外,球墨铸铁还具有良好的耐磨性、耐热性和耐冲击性能,能够适应复杂的工作环境和高强度的使用要求。
此外,球墨铸铁还具有优良的切削加工性能和耐蚀性。
球墨铸铁较硬度低,易于切削和加工,大大降低了模具制造和加工的困难度。
同时,球墨铸铁的耐腐蚀性也较好,对酸、碱和盐等介质有良好的抗腐蚀能力,使其在化工、食品加工等行业中得到广泛应用。
然而,球墨铸铁也存在一些不足之处。
例如,其冷却收缩系数相对较大,易引起内部晶间缩孔和表面缺陷。
此外,球墨铸铁在高温下容易发生奥氏体再生,导致性能下降。
因此,在生产过程中需要严格控制降温速度和冷却条件,以保证球墨铸铁的质量。
综上所述,球墨铸铁是一种通过镁合金化处理铸铁而成,具有石墨球颗粒分布、优良的机械性能、良好的切削加工性能和耐腐蚀性能的特殊合金材料。
它在汽车、机械、建筑、化工等各个领域具有广泛的应用前景。
球墨铸铁简介介绍
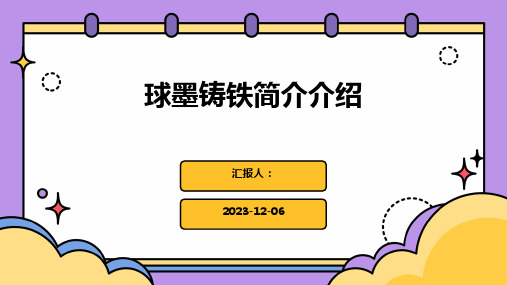
研究高效熔炼和浇注技术,缩短生产周期,降低能源消耗 和成本。例如,采用电炉熔炼、感应炉加热等先进技术, 提高熔炼效率和质量。
循环利用与废品再利用
加强废品回收和再利用,提高资源利用效率,降低生产成 本。例如,将废品进行破碎、熔炼后重新用于生产。
环保与可持续发展
减少污染排放
采取有效措施减少生产过程中的 废气、废水和固体废弃物的排放 ,降低对环境的影响。例如,采 用环保涂料和除尘设备等减少废
性质
具有高强度、高韧性、耐磨性等 优良性能,同时具有良好的可加 工性和耐腐蚀性。
球墨铸铁的历史与发展
历史
球墨铸铁最早由美国人发明,于19 世纪80年代问世。
发展
随着铸造技术的进步和新型材料的出 现,球墨铸铁的应用领域不断扩大。
球墨铸铁的生产过程
处理
对原材料进行质量 检验、合金化处理 、熔炼等步骤。
耐磨性
良好的耐磨性
球墨铸铁具有较好的耐磨性,能够在摩擦磨损条件下长期使 用。
磨损率低
球墨铸铁的磨损率较低,能够减少零件的磨损和更换频率。
耐腐蚀性
良好的耐腐蚀性
球墨铸铁具有较好的耐腐蚀性,能够抵抗常见的化学腐蚀。
在腐蚀环境下长期使用
球墨铸铁可以在腐蚀环境下长期使用,适用于各种恶劣环境。
03
球墨铸铁的应用领域
后处理工艺与设备
后处理工艺
包括热处理、切割、打磨等工序,以进一步提高产品 的力学性能和外观质量。
后处理设备
包括热处理炉、切割机、磨床等设备,其中热处理炉 需具备温度控制精度高、炉内温度均匀等特点。
05
球墨铸铁的未来发展趋势 与挑战
新材料与新工艺的研究与应用
01
球墨铸铁
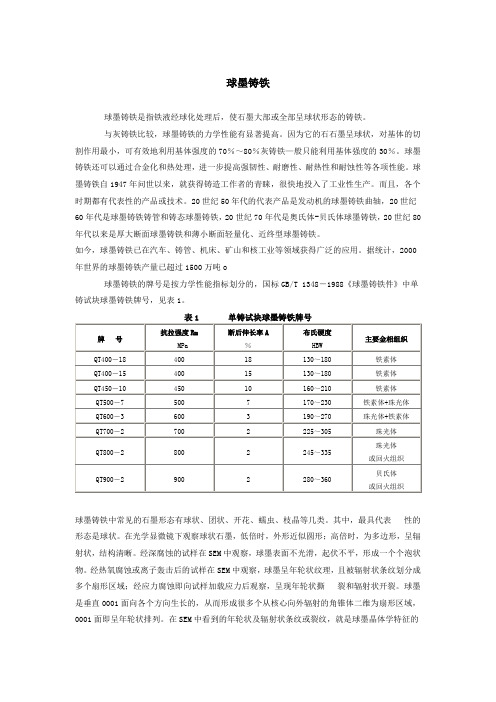
球墨铸铁球墨铸铁是指铁液经球化处理后,使石墨大部或全部呈球状形态的铸铁。
与灰铸铁比较,球墨铸铁的力学性能有显著提高。
因为它的石石墨呈球状,对基体的切割作用最小,可有效地利用基体强度的70%~80%灰铸铁—般只能利用基体强度的30%。
球墨铸铁还可以通过合金化和热处理,进一步提高强韧性、耐磨性、耐热性和耐蚀性等各项性能。
球墨铸铁自1947年问世以来,就获得铸造工作者的青睐,很快地投入了工业性生产。
而且,各个时期都有代表性的产品或技术。
20世纪50年代的代表产品是发动机的球墨铸铁曲轴,20世纪60年代是球墨铸铁铸管和铸态球墨铸铁,20世纪70年代是奥氏体-贝氏体球墨铸铁,20世纪80年代以来是厚大断面球墨铸铁和薄小断面轻量化、近终型球墨铸铁。
如今,球墨铸铁已在汽车、铸管、机床、矿山和核工业等领域获得广泛的应用。
据统计,2000年世界的球墨铸铁产量已超过1500万吨o球墨铸铁的牌号是按力学性能指标划分的,国标GB/T 1348-1988《球墨铸铁件》中单铸试块球墨铸铁牌号,见表1。
球墨铸铁中常见的石墨形态有球状、团状、开花、蠕虫、枝晶等几类。
其中,最具代表性的形态是球状。
在光学显微镜下观察球状石墨,低倍时,外形近似圆形;高倍时,为多边形,呈辐射状,结构清晰。
经深腐蚀的试样在SEM中观察,球墨表面不光滑,起伏不平,形成一个个泡状物。
经热氧腐蚀或离子轰击后的试样在SEM中观察,球墨呈年轮状纹理,且被辐射状条纹划分成多个扇形区域;经应力腐蚀即向试样加载应力后观察,呈现年轮状撕裂和辐射状开裂。
球墨是垂直0001面向各个方向生长的,从而形成很多个从核心向外辐射的角锥体二维为扇形区域,0001面即呈年轮状排列。
在SEM中看到的年轮状及辐射状条纹或裂纹,就是球墨晶体学特征的反映。
球墨铸铁一般为过共晶成分,因此球状石墨的长大,应包括两个阶段:①先共晶结晶阶段,球墨核心形成后,在铁液及贫碳富铁的奥氏体晕圈中长大。
②共晶结晶阶段,球墨周围形成奥氏体外壳,即球墨-奥氏体共晶团。
球墨铸铁技术介绍
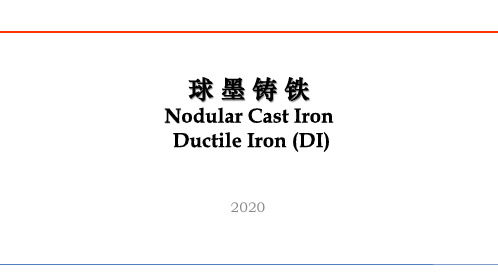
弹性模量:159,000~172,000MPa
➢ 球墨铸铁的弹性模量随球化率的降低而降低。
球墨铸铁的验收
➢ 以抗拉强度和延伸率两个指标作为验收依据。 ➢ 生产工艺稳定的条件下,可根据硬度值进行验收。
硬度与强度的对应关系必须建立在球化合格,化学成 分、孕育稳定的基础上。
的基体类型。
焊补性
➢ 球墨铸铁不能焊接,只能焊补。
➢ 球墨铸铁中稀土镁合金含量较高时,在焊缝和近焊 缝区易产生白口或马氏体组织,形成内应力和裂 纹。
➢ 国家标准GB/T10044-1988规定了适用于球墨铸 铁焊补用的焊条,按照要求,可获得高强度珠光体 基体球墨铸铁的焊缝。
9
铁素体球墨铸铁(F体高韧性)
➢ 铸造工艺合理稳定,为保证性能,规定按硬度验收 时,必须检验金相组织,其球化率不得低于4级。
➢ 即使硬度和球化合格,由于基体其中存在渗碳体、 磷共晶、高硅固溶强化等,强度和韧性也可能达不 到要求。
➢ 生产工艺不稳定时,不能根据硬度值验收。
13
冲击韧度
➢ 铁素体球墨铸铁由于含硅量变化,贝氏体球墨铸铁 由于上、下贝氏体及奥氏体数量变化,冲击韧度的 变化范围较大。
强度和塑性
➢ 球墨铸铁的强度和塑性主要取决于基体组织
• 下贝氏体B下或回火马氏体M回强度最高; • 其次是上贝氏体B上、索氏体S体、珠光体P体、F体; • 铁素体增多,强度下降,延伸率增加; • 奥氏体或铁素体强度较低,塑性较好。
➢ 球墨铸铁的屈服点σ0.2高,超过正火45钢 ➢ 比强度σ0.2/σb也高于钢
布氏硬度HBS
四种退火球墨铸铁的高温硬度
180
球墨铸铁

球墨铸铁铸铁是含碳量大于2.11%的铁碳合金,由工业生铁、废钢等钢铁及其合金材料经过高温熔融和铸造成型而得到,除Fe外,还含及其它铸铁中的碳以石墨形态析出,若析出的石墨呈条片状时的铸铁叫灰口铸铁或灰铸铁、呈蠕虫状时的铸铁叫蠕墨铸铁、呈团絮状时的铸铁叫白口铸铁或码铁、而呈球状时的铸铁就叫球墨铸铁。
球墨铸铁是一种具有优良机械性能的灰口铸铁。
一般在浇注之前,在铁液中加入少量球化剂(通常为镁、稀土镁合金或含铈的稀土合金)和孕育剂(通常为硅铁),使铁水凝固后形成球状石墨。
此种铸铁的强度和韧性比其他铸铁高,有时可代替铸钢和可锻铸铁(malleablecastiron),在机械制造工业中得到了广泛应用。
球墨铸铁在国外是1947年用于工业生产的。
主要性能球铁铸件差不多已在所有主要工业部门中得到应用,这些部门要求高的强度、塑性、韧性、耐磨性、耐热和机械冲击、耐高温或低温、耐腐蚀以及尺寸稳定性等。
为了满足使用条件的这些变化、球墨铸铁有许多牌号,提供了机械性能和物理性能的一个很宽的范围。
如国际标准化组织ISO1083所规定的大多数球墨铸铁铸件,主要是以非合金态生产的。
显然,这个范围包括抗拉强度大于800牛顿/平方毫米,延伸率为2%的高强度牌号。
另一个极端是高塑性牌号,其延伸率大于17%,而相应的强度较低(最低为370牛顿/平方毫米)。
强度和延伸率并不是设计者选择材料的唯一根据,而其它决定性的重要性能还包括屈服强度、弹性模数、耐磨性和疲劳强度、硬度和冲击性能等。
另外,耐蚀性和抗氧化以及电磁性能对于设计者也许是关键的。
为了满足这些特殊使用,研制了一组奥氏体球铁,通常叫Ni一Resis球铁。
这些奥氏体球铁,主要用镍、铬和锰合金化,并且列入国际标准。
为珠光体型球墨铸铁,具有中高等强度、中等韧性和塑性,综合性能较高,耐磨性和减振性良好,铸造工艺性能良好等特点。
能通过各种热处理改变其性能。
球墨铸铁常用于生产受力复杂,强度、韧性、耐磨性等要求较高的零件,主要用于各种动力机械曲轴、凸轮轴、连接轴、连杆、齿轮、离合器片、液压缸体等零部件。
球墨铸铁概述介绍课件
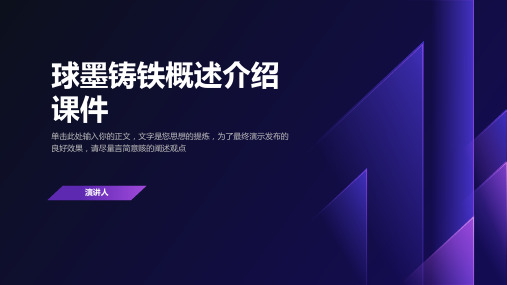
04
浇注控制:控 制浇注速度, 保证球墨铸铁 的成型质量
球墨铸铁的质量控 制
化学成分的控制
碳含量:控制碳含量在2 硅含量:控制硅含量在0 锰含量:控制锰含量在0 磷含量:控制磷含量在0 硫含量:控制硫含量在0 稀土含量:控制稀土含量在0
球化处理工艺的控制
01
球化剂的选择: 选择合适的球化 剂,保证球化效
果
02
球化处理温度: 控制球化处理温 度,保证球化效
果
03
球化处理时间: 控制球化处理时 间,保证球化效
果
04
球化处理搅拌: 控制球化处理搅 拌,保证球化效
果
05
球化处理后处理: 控制球化处理后 处理,保证球化
效果
06
球化处理质量检 测:控制球化处 理质量检测,保
证球化效果
铸件质量的检测与控制
原材料质量控制: 选择优质原材料, 确保化学成分和物 理性能符合要求
冲天炉:适用于中小型球墨铸铁生产,具有 生产效率高、能耗低、环保性能好等优点。
熔炼炉:适用于大型球墨铸铁生产,具有生 产效率高、能耗低、环保性能好等优点。
熔炼工艺的控制
温度控制:严 格控制熔炼温 度,确保球墨 铸铁的质量
01
脱氧控制:采用 合适的脱氧方法, 防止氧化物对球 墨铸铁的影响
03
02
成分控制:精 确控制合金成 分,保证球墨 铸铁的性能
球墨铸铁的生产工艺和技术不断创新,提高了产品质量 和生产效率,降低了生产成本,增强了市场竞争力。
谢谢
冲击性能。
耐磨损:球墨铸铁
3
的耐磨性优于灰口
铸铁,适用于耐磨
损的部件。
耐腐蚀:球墨铸铁
4
塑钢和球墨铸铁

塑钢和球墨铸铁是两种完全不同的材料,它们在性能、用途和生产工艺等方面都有很大的差异。
塑钢是一种塑料制品,其主要成分是聚氯乙烯(PVC)或高密度聚乙烯(HDPE)。
塑钢具有轻便、耐腐蚀、不易变形、不易碎等特点,因此被广泛应用于门窗、隔断、管道等领域。
塑钢的强度较低,承受能力较弱,一般需要添加增强材料来提高其承载能力。
球墨铸铁则是一种金属材料,通过将铁水加入铁水包中,加入球化剂和孕育剂,在离心机的作用下浇注成铸铁件。
球墨铸铁具有较高的强度、韧性和耐磨性,因此被广泛应用于制造高强度、高承载能力的机械零件和构件。
球墨铸铁的生产工艺较复杂,成本较高,需要进行高温退火处理,以消除内应力、稳定组织和提高性能。
总的来说,塑钢和球墨铸铁是两种不同的材料,它们的性能、用途和生产工艺都有很大的差异。
在实际应用中,需要根据具体的使用要求和条件来选择合适的材料。
球墨铸铁熔炼与铸造工艺

球墨铸铁是一种高强度、高韧性的铸铁材料,其熔炼与铸造工艺主要包括以下几个步骤。
原料准备:主要原料是铸铁和球化剂。
铸铁通常是废铁、废钢等回收材料,而球化剂则是一种能够使铸铁中的碳以球形形式存在的添加剂。
熔炼铸造:将原料放入高温熔炉中进行熔炼,熔炼温度通常在1400℃以上。
在熔炼过程中,加入球化剂,使铸铁中的碳以球形形式存在。
浇注铸造:将熔融的球墨铸铁液体倒入铸型中,待其冷却凝固后,取出铸件。
热处理:对铸件进行热处理,以提高其强度和韧性。
通常采用淬火和回火的方法进行热处理。
加工和表面处理:对铸件进行加工和表面处理,以达到所需的形状和表面质量。
在整个铸造过程中,还需要特别注意以下几点:
球墨铸铁铸造工艺比普通灰铁铸件造型更为严格,其缩量要大于普通灰铁铸件,因此在造型时要加大冒口尺寸,确保冒口内铁液能够完全补充需要的缩量。
造型用型砂不能使用水泥砂造型,而要选用树脂砂或水玻璃砂进行造型,且耐火涂料要选择高温耐火材料。
在熔炼过程中,要严格控制球墨铸铁的含量要求,如要求球墨铸件材质为QT450材质,就需要控制五大元素含量在特定范围内。
浇铸时要采用高温出炉低温浇铸的原则,开始浇铸后要保证每个冒口铁液都能浇满,并持续为冒口补充铁液直至冒口内铁液不再下沉减少为止。
球铁
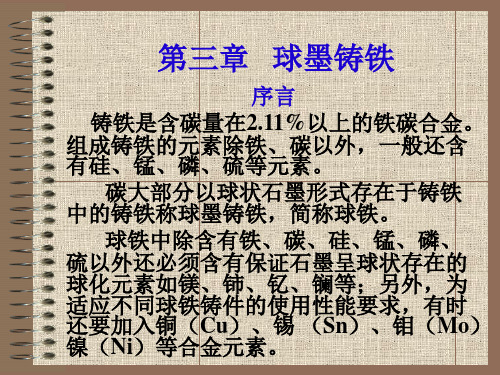
• 在球铁生产中遇到一些微量元素和合金元素是 起干扰球化作用的。归纳起来这些元素及其在 球铁中的临界含量见表3.2。 • 消耗型:硫(S)氧(O)硒(Se)碲(Te)是
在球化处理时优先与球化元素起反应,消耗一部分球 化剂,剩余部分球化剂才能去起到球化作用,促成蠕 虫状、片状石墨; 晶界偏析型:钛(Ti)砷(As)铝(Al)锑(Sb)锡 (Sn)等元素是富集在共晶团边界,形成畸变石墨; 混合型:铅(Pb)铋(Bi)镉(Cd)锌(Zn)是即消 耗球化剂,又可产生共晶团晶界偏析。 值得关注的是,上述干扰元素(除钛以外)对采用 高度净化的铁水浇注打断面球铁铸件时,在有适量稀 土的情况下,适量加入反而起到圆整石墨防止畸变石 墨、增加球墨数量的好作用。加入量限于: 锑0.002~0.01%、铋≤0.01%、铅≤0.01%。千万不能过 量。 另外,国外已开发应用了含氧硫总量0.1%的氧硫孕育 剂,用于厚大球铁铸件生产获得良好效果。
球铁与其他材料机械性能对比表
材料 类别
铸态铁素体 球铁 铸态珠光体 球铁 正火珠光体 球铁
抗拉强度 σb MPa
400~600 600~800 600~900
屈服强度 延伸率 硬度 冲击韧性 σsMPa (%) (HB)(J/cm2)
280~420 320~420 420~600 8~22 2~4 2~8 130~ 190 180~ 230 230~ 302 5~15 1.5~3.5 2~4
第一节 球墨铸铁的组织和性能
一、球墨铸铁的石墨组织及球化剂 1. 石墨形成机理
• 石墨是碳(C)的一种同素异 构体,属六方晶系。石墨的晶 体结构如图3.1。石墨的密度为 2.25g/cm3,比重比铁轻得多, 铁的密度是7.68g/cm3,所以铸 铁凝固时析出石墨会使铸件体 积膨胀。石墨晶体中的碳原子 是层状排列的,在同层原子之 间是以共价键结合,其结合力 较强;而层与层之间是以极性 键结合,其结合力较弱。因此, 石墨极易分层剥落,强度极低。 由于石墨具有这样的结构特点, 因此在铁液中长大时应该是沿 基面择优生长,最后形成片状。
球墨铸铁管的特点
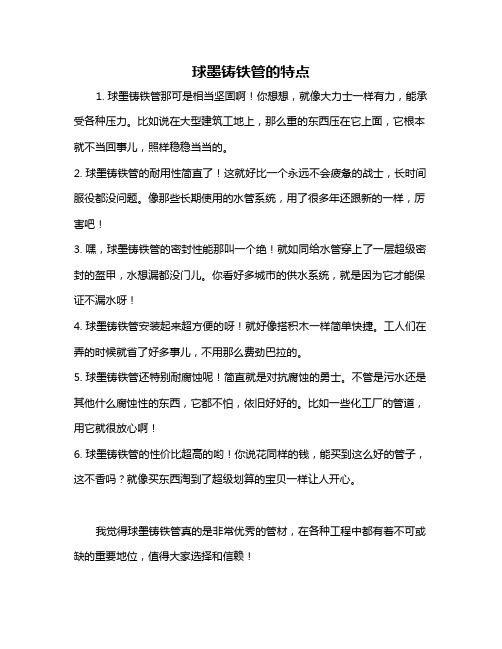
球墨铸铁管的特点
1. 球墨铸铁管那可是相当坚固啊!你想想,就像大力士一样有力,能承受各种压力。
比如说在大型建筑工地上,那么重的东西压在它上面,它根本就不当回事儿,照样稳稳当当的。
2. 球墨铸铁管的耐用性简直了!这就好比一个永远不会疲惫的战士,长时间服役都没问题。
像那些长期使用的水管系统,用了很多年还跟新的一样,厉害吧!
3. 嘿,球墨铸铁管的密封性能那叫一个绝!就如同给水管穿上了一层超级密封的盔甲,水想漏都没门儿。
你看好多城市的供水系统,就是因为它才能保证不漏水呀!
4. 球墨铸铁管安装起来超方便的呀!就好像搭积木一样简单快捷。
工人们在弄的时候就省了好多事儿,不用那么费劲巴拉的。
5. 球墨铸铁管还特别耐腐蚀呢!简直就是对抗腐蚀的勇士。
不管是污水还是其他什么腐蚀性的东西,它都不怕,依旧好好的。
比如一些化工厂的管道,用它就很放心啊!
6. 球墨铸铁管的性价比超高的哟!你说花同样的钱,能买到这么好的管子,这不香吗?就像买东西淘到了超级划算的宝贝一样让人开心。
我觉得球墨铸铁管真的是非常优秀的管材,在各种工程中都有着不可或缺的重要地位,值得大家选择和信赖!。
- 1、下载文档前请自行甄别文档内容的完整性,平台不提供额外的编辑、内容补充、找答案等附加服务。
- 2、"仅部分预览"的文档,不可在线预览部分如存在完整性等问题,可反馈申请退款(可完整预览的文档不适用该条件!)。
- 3、如文档侵犯您的权益,请联系客服反馈,我们会尽快为您处理(人工客服工作时间:9:00-18:30)。
球墨铸铁
球墨铸铁是指铁液经球化处理后,使石墨大部或全部呈球状形态的铸铁。
与灰铸铁比较,球墨铸铁的力学性能有显著提高。
因为它的石石墨呈球状,对基体的切割作用最小,可有效地利用基体强度的70%~80%灰铸铁—般只能利用基体强度的30%。
球墨铸铁还可以通过合金化和热处理,进一步提高强韧性、耐磨性、耐热性和耐蚀性等各项性能。
球墨铸铁自1947年问世以来,就获得铸造工作者的青睐,很快地投入了工业性生产。
而且,各个时期都有代表性的产品或技术。
20世纪50年代的代表产品是发动机的球墨铸铁曲轴,20世纪60年代是球墨铸铁铸管和铸态球墨铸铁,20世纪70年代是奥氏体-贝氏体球墨铸铁,20世纪80年代以来是厚大断面球墨铸铁和薄小断面轻量化、近终型球墨铸铁。
如今,球墨铸铁已在汽车、铸管、机床、矿山和核工业等领域获得广泛的应用。
据统计,2000年世界的球墨铸铁产量已超过1500万吨o
球墨铸铁的牌号是按力学性能指标划分的,国标GB/T 1348-1988《球墨铸铁件》中单铸试块球墨铸铁牌号,见表1。
表1xx试块球墨铸铁牌号
牌号
QT400-18
QT400-15
QT450-10
QT500-7
QT600-3
QT700-2
QT800-2抗拉强度Rm
MPa
400
400
450
500
600
700
800断后伸长率A%18
15
107322布氏硬度
HBW
130~180
130~180
160~210
170~230
190~270
225~305
245~335主要金相组织
铁素体铁素体+珠光体+铁素体珠光体或回火组织贝氏体或回火组织QT900-~360
球墨铸铁中常见的石墨形态有球状、团状、开花、蠕虫、枝晶等几类。
其中,最具代表性的形态是球状。
在光学显微镜下观察球状石墨,低倍时,外形近似圆形;高倍时,为多边形,呈辐射状,结构清晰。
经深腐蚀的试样在SEM 中观察,球墨表面不光滑,起伏不平,形成一个个泡状物。
经热氧腐蚀或离子轰击后的试样在SEM中观察,球墨呈年轮状纹理,且被辐射状条纹划分成多个扇形区域;经应力腐蚀即向试样加载应力后观察,呈现年轮状撕裂和辐射状开裂。
球墨是垂直0001面向各个方向生长的,从而形成很多个从核心向外辐射的角锥体二维为扇形区域,0001面即呈年轮状排列。
在SEM中看到的年轮状及辐射状条纹或裂纹,就是球墨晶体学特征的反映。
球墨铸铁一般为过共晶成分,因此球状石墨的长大,应包括两个阶段:
①先共晶结晶阶段,球墨核心形成后,在铁液及贫碳富铁的奥氏体晕圈中长大。
②共晶结晶阶段,球墨周围形成奥氏体外壳,即球墨-奥氏体共晶团。
此时,球墨是在奥氏体壳包围下长大的。
虽然球墨在共晶阶段的长大速度比在液态阶段迟缓,但球墨的大部分是在共晶阶段长大的。
球墨铸铁的共晶团比灰铸铁的共晶团细小,其数量约为灰铸铁的50~200倍。
还应说明,球墨铸铁的共晶结晶是一种变态共晶,即球墨和奥氏体均可在单独、互不依存的情况下长大。
为了评价石墨球化的好坏,国标GB/T 9441-1988《球墨铸铁金相检验》将球化等级分为6级,见表2。
这是根据观察视场内各种石墨的相对数量及球化率的高低划分的。
表2球化分级
球化级别123456球化率%
≥95
90~< 95
80~< 90
7O~< 80
60~< 70
不规定说明
石墨呈球状,少量团状,允许极少量团絮状石墨大部分呈球状,余为团状和极少量团絮状石墨大部分呈团状和球状,余为团絮状,允许有极少量蠕虫状
石墨大部分呈团絮状和团状,余为球状和少量蠕虫状
石墨呈分散分布的蠕虫状和球状、团状、团絮状石暴呈聚集分布的蠕虫状和片状及球状、团状、团絮状石墨球的数量是衡量球墨铸铁质量的一项重要指标。
某些工厂在检验中,只注意球化率,忽视石墨球数,是不全面的。
理由是:
①石墨球数增加,球径减小,球墨圆整度提高,分布也趋于均匀。
②用石墨球数来评价球墨铸铁的孕育效果,是一种有效、直观的方法。
③球墨铸铁中的球数基本上反应了共晶团数。
④在薄壁铸件中,铸态是否出现渗碳体,主要取决于石墨球数。
美国铸造师协会AFS把石墨球数分成7级,见表1-3-3。
由表可见,石墨球径和石墨球数之间的对应关系较好,而石墨大小和石墨球数之间的对应关系则较差。
表3球墨铸铁石墨球数与大小
项目
石墨球数个/mm
石墨大小级
石墨球径mm100×2标准
AFS图谱
GB/T9441-1988
AFS图谱2558~125063~6对应数值或级别
100
6~7
2~415072~3200
7~8
1.5~32507~81~2300
8<1.5球化处理是球墨铸铁的关键工序。
大致来说,球化处理的历史经历了两个阶段:
①20世纪50年代,以纯镁和压入法为主:
②20世纪60年代中期开始,以稀土镁合金球化剂和冲入法为主,还相继采用了盖包法、型内法和密流法,20世纪80年代又采用了喂丝法工艺。
将纯镁与稀土镁球化剂比较:
纯镁的球化能力强,球墨圆整,白口化倾向小,缺点是反应激烈,铁液沸腾,安全性差,还难以避免缩松、夹渣和皮下气孔等铸造缺陷;合金球化剂的稀土,有脱硫去气的作用,能减少缩松、夹渣等铸造缺陷,生产也较安全,但石墨的圆整度往往稍逊于纯镁处理的球墨铸铁,且白口化倾向较大。
孕育处理是球化处理后不可或缺的工序。
它能促进石墨化,增加石墨球数,提高石墨圆整度。
但加强孕育并不是一味提高孕育量和增加孕育次数。
孕育过量,反而会造成孕育缺陷,如缩松、缩孔和石墨漂浮等:
孕育剂颗粒大,未曾熔化,残留于铸件内,会成为“硬点”。
孕育处理是受多种因素制约的,睹如孕育剂种类,孕育剂粒度、孕育剂数量、孕育方式、铁液温度和孕育位置等等,总之应使处于饱和孕育状态的铁液尽可能接近铁液凝固的瞬间,这样才能以最小的孕育重达到最大的孕育效果。
表3中8个牌号的球墨铸铁,QT900-2一般用热处理制取例如等温淬火,其余7个牌号分别为珠光体、珠光体+铁素体和铁素体球墨铸铁。
在球墨铸铁生产初期,这些牌号都是用正火或退火获得基体组织的,如今都可以由铸态制取了。
生产铸态铁素体球墨铸铁必须注意:
①采用低锰wMn<0.03%、低磷wP<0.07%、低硫wS<0.025%生铁。
还应考虑促进碳化物形成元素的影响:
碳化物系数
CS=Mn+15Cr+20V+30B+10S+7Mo+5Sn+1.5P,其值应取CS<0.8。
②控制终硅量,在铁素体达到要求的前提F,尽量降低终硅量。
例如,美国某些工厂的终硅量为wSi2.2%~2.4%。
③降低终硅量又要不出现白口,就应该加强孕育,采用浇口杯孕育、型内孕育等后期孕育工艺,增加石墨球数,这对薄壁铸件尤为重要。
④控制残留稀土的wRE,薄壁铸件为0.015%~0.03%,厚壁铸件为
0.02%~0.04%。
生产铸态珠光体球墨铸铁必须注意:
①采用低磷低硫生铁,严格控制有害微量元素的含量。
②”Mn以0.25%~0.50%为宜。
⑧为了增加珠光体含量,常用的合金化元素有铜、锡、锑等;若以铜对珠光体的作用为1,则锡、锑的作用分别为10倍和100倍。
厚壁铸件宜加入适量的铜。
锡易形成晶间碳化物,加入量要控制。
④加强孕育,防止出现碳化物。
各种牌号铸态球墨铸铁中珠光体与铁素体的相对数量,与球墨铸铁生产的初期比较,珠光体球墨铸铁中的铁素体量己上升。
例如,QT700-2允许铁素体为35%体积分数,这已趋向于混合基体了。
球墨铸铁的铸造缺陷如缩孔、缩松、夹渣、反白口等,是其他铸铁都有的,有些缺陷如球化不良、球化衰退等,则是球墨铸铁特有的。