有色金属加工企业生产物流合理化研究
有色金属企业可行性研究报告
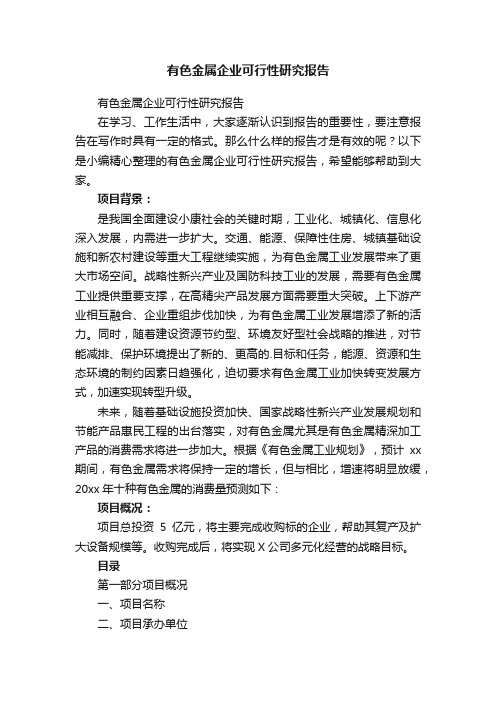
有色金属企业可行性研究报告有色金属企业可行性研究报告在学习、工作生活中,大家逐渐认识到报告的重要性,要注意报告在写作时具有一定的格式。
那么什么样的报告才是有效的呢?以下是小编精心整理的有色金属企业可行性研究报告,希望能够帮助到大家。
项目背景:是我国全面建设小康社会的关键时期,工业化、城镇化、信息化深入发展,内需进一步扩大。
交通、能源、保障性住房、城镇基础设施和新农村建设等重大工程继续实施,为有色金属工业发展带来了更大市场空间。
战略性新兴产业及国防科技工业的发展,需要有色金属工业提供重要支撑,在高精尖产品发展方面需要重大突破。
上下游产业相互融合、企业重组步伐加快,为有色金属工业发展增添了新的活力。
同时,随着建设资源节约型、环境友好型社会战略的推进,对节能减排、保护环境提出了新的、更高的.目标和任务,能源、资源和生态环境的制约因素日趋强化,迫切要求有色金属工业加快转变发展方式,加速实现转型升级。
未来,随着基础设施投资加快、国家战略性新兴产业发展规划和节能产品惠民工程的出台落实,对有色金属尤其是有色金属精深加工产品的消费需求将进一步加大。
根据《有色金属工业规划》,预计xx 期间,有色金属需求将保持一定的增长,但与相比,增速将明显放缓,20xx年十种有色金属的消费量预测如下:项目概况:项目总投资5亿元,将主要完成收购标的企业,帮助其复产及扩大设备规模等。
收购完成后,将实现X公司多元化经营的战略目标。
目录第一部分项目概况一、项目名称二、项目承办单位三、并购动因四、投资主体(一)投资方(二)被投资方五、并购计划六、项目主要经济技术指标七、可行性研究编制依据第二部分项目背景和必要性与可行性分析一、项目背景二、投资的必要性与可行性分析第三部分投资方案一、预计投资总额二、并购定价原则三、并购方式四、其他有关约定及承诺五、资金来源六、并购流程第四部分有色金属行业现状及市场形势分析一、有色金属行业政策环境分析二、中国有色金属行业发展概况三、中国有色金属行业发展潜力分析第五部分目标公司的主要情况一、目标公司概况(一)企业基本情况(二)现有股权结构及股东情况(三)企业组织架构二、目标公司的经营及财务情况(一)生产能力及经营情况(二)主要客户(三)主要财务情况第六部分并购后的经营发展规划一、并购后的经营与管理二、未来发展规划第七部分投资估算及资金筹措一、投资估算依据和说明二、资金使用计划三、资金筹措方案第八部分财务评价一、基本财务数据假设二、销售收入预测与成本费用估算三、盈利能力分析四、盈亏平衡分析五、财务评价结论第九部分项目并购影响效果分析第十部分项目风险分析及对策一、法律风险及对策二、信息风险及对策三、市场风险及对策四、管理风险及对策第十一部分结论。
有色金属供应链管理关键问题和最佳策略

有色金属供应链管理关键问题和最佳策略供应链管理是现代企业成功的重要因素之一。
在有色金属行业,供应链管理尤为关键,因为这个行业涉及到多个环节和参与方,包括原料供应商、生产商、分销商以及最终客户。
本文将探讨有色金属供应链管理中的关键问题,并提出最佳策略来解决这些问题。
一、供应链可视化在有色金属供应链管理中,最重要的是实现供应链的可视化。
这意味着通过技术手段和信息共享,将整个供应链上的各个环节和参与方的信息整合起来,以便实时了解和控制每个环节的相关数据。
供应链可视化可以帮助企业管理者更好地预测和应对可能出现的问题,提高供应链的运作效率。
二、供应链协同在有色金属供应链中,不同环节之间的协同合作至关重要。
供应商、生产商和分销商之间需要建立紧密的合作关系,共同制定计划和目标,并进行有效的信息共享。
只有通过协同,才能够避免过多的库存、减少订单延误,并提高整体供应链的响应能力。
三、供应链风险管理有色金属行业面临的风险包括原材料价格波动、交通运输不确定性、政策和法规变化等。
供应链管理者需要对这些风险进行评估,并采取相应的风险管理策略。
例如,可以建立备货储备,以减少供应不足的风险;同时,也可以与供应商建立长期合作关系,以确保稳定的供应。
四、供应链技术创新随着信息技术的不断发展,有色金属供应链管理也需要不断创新和引入新的技术。
例如,物联网技术可以帮助企业实时监控仓库和运输车辆的情况,提高库存管理的精确度;人工智能技术可以帮助企业进行预测和决策分析,提高供应链管理的智能化水平。
五、供应链可持续发展有色金属供应链管理不能只考虑短期利益,还需要关注可持续发展和环境保护。
企业应该积极采取措施,减少对环境的负面影响,提高资源利用效率,并与符合环保标准的供应商开展合作。
只有实现可持续发展,企业才能够在激烈的市场竞争中立于不败之地。
六、供应链绩效评估和持续改进有色金属供应链管理需要进行定期的绩效评估和持续改进。
通过评估供应链的核心指标,如交货准时率、库存周转率等,可以发现供应链中的不足之处,并采取相应的改进措施。
有色金属压延加工中的物流与仓储管理考核试卷
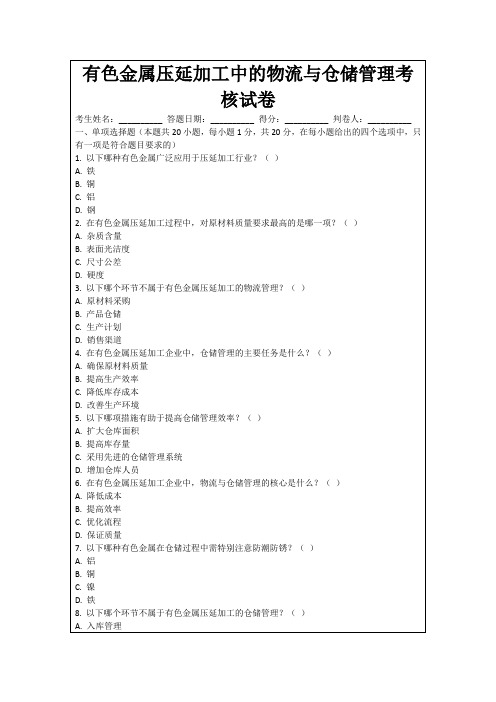
6.仓库的存储密度越高,其仓储效率就越低。()
答题括号:__________
7.有色金属在运输过程中不需要考虑环境因素对材料的影响。()
答题括号:__________
8.企业的物流与仓储管理可以完全独立于生产计划进行。()
答题括号:__________
9.仓储管理中,合理的库存水平可以减少库存积压和缺货的风险。()
答题括号:__________
2.仓储成本控制主要依赖于减少仓库的数量。()
答题括号:__________
3.在物流管理中,运输距离越短,运输成本就越低。()
答题括号:__________
4.采用自动化仓库系统可以完全替代人工进行仓储作业。()
答题括号:__________
5.物流与仓储管理的目标是降低成本,提高客户满意度。()
四、案例分析题(本题共2小题,每小题15分,共30分)
二、多选题(本题共20小题,每小题1.5分,共30分,在每小题给出的四个选项中,至少有一项是符合题目要求的)
1.有色金属压延加工的物流管理主要包括以下哪些环节?()
A.原材料采购
B.产品运输
C.仓储管理
D.销售渠道
2.以下哪些因素会影响有色金属压延加工的仓储效率?()
D.人员管理
17.在有色金属物流管理中,以下哪些技术可以提高运输效率?()
A.车辆追踪系统
B.路径优化算法
C.电子标签系统
D.自动驾驶技术
18.以下哪些因素可能导致有色金属压延加工企业仓储成本增加?()
A.仓库租金上涨
B.能源消耗增加
C.仓储设备维护费用
D.库存积压
19.以下哪些做法有助于提高有色金属压延加工企业物流与仓储管理的协调性?()
有色金属生产过程中的原材料采购与供应链管理
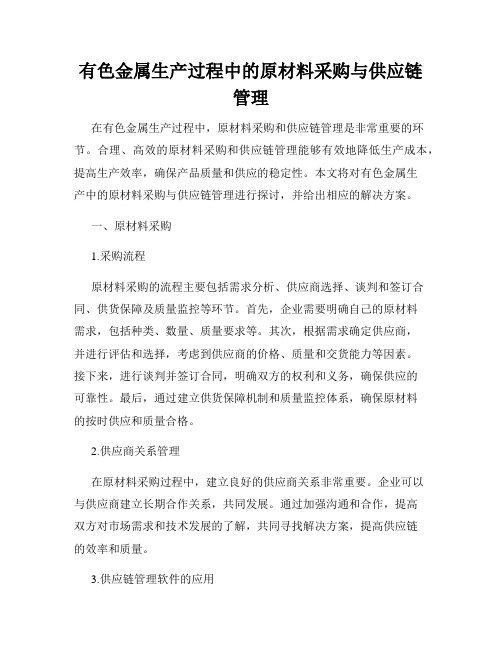
有色金属生产过程中的原材料采购与供应链管理在有色金属生产过程中,原材料采购和供应链管理是非常重要的环节。
合理、高效的原材料采购和供应链管理能够有效地降低生产成本,提高生产效率,确保产品质量和供应的稳定性。
本文将对有色金属生产中的原材料采购与供应链管理进行探讨,并给出相应的解决方案。
一、原材料采购1.采购流程原材料采购的流程主要包括需求分析、供应商选择、谈判和签订合同、供货保障及质量监控等环节。
首先,企业需要明确自己的原材料需求,包括种类、数量、质量要求等。
其次,根据需求确定供应商,并进行评估和选择,考虑到供应商的价格、质量和交货能力等因素。
接下来,进行谈判并签订合同,明确双方的权利和义务,确保供应的可靠性。
最后,通过建立供货保障机制和质量监控体系,确保原材料的按时供应和质量合格。
2.供应商关系管理在原材料采购过程中,建立良好的供应商关系非常重要。
企业可以与供应商建立长期合作关系,共同发展。
通过加强沟通和合作,提高双方对市场需求和技术发展的了解,共同寻找解决方案,提高供应链的效率和质量。
3.供应链管理软件的应用为了提高原材料采购的效率和透明度,企业可以引入供应链管理软件。
这类软件可以实现供应链各环节间的信息共享和协调,包括需求计划、订单管理、供应商管理等。
通过采用供应链管理软件,企业可以实时了解原材料库存情况、供应商交货情况等,及时调整采购计划,提高效率。
二、供应链管理1.供应链协同管理在有色金属生产过程中,供应链的各个环节之间存在着密切的联系和依赖关系。
供应链协同管理的核心是实现供需双方的信息共享和协调。
通过建立供应链管理平台,各个环节间的信息可以实时传递和分析,从而实现生产计划的优化和协调,减少库存和运输成本,并能够更好地应对市场需求的变化。
2.风险管理在有色金属生产中,供应链管理需要关注各种潜在的风险,如价格波动、原材料供应不稳定等。
为了降低这些风险的影响,企业可以进行风险评估和管理,并建立相应的应对措施。
钢铁企业物流优化

钢铁企业物流优化
随着我国钢铁行业的不断发展,企业物流优化已成为钢铁行业企业的
必要任务。
优化的目的是提高企业的物流效率,降低物流成本,提升客户
满意度。
一、构建钢铁物流精细化管理体系
企业要完善钢铁物流精细化管理体系,推行精细化管理,实现物流活
动可追溯,用最快捷、最安全的方式将货物从厂家运输到客户。
建立完善
的物流信息系统,对加工、装运、仓储、报关等物流环节进行全过程管理,使物流系统更加细化,提高物流效率,降低物流成本,满足客户需求。
二、实施产品质量管理体系
要实施产品质量管理体系,建立完善的质量管理流程,每批货物都应
有严格的质量检验、签收程序,并及时对有异常现象的货物进行报告,控
制质量数据,减少物流质量问题。
三、推行完善物流服务
钢铁企业要推行完善的物流服务,包括车辆调度、仓储管理、订单管理、报关报检、货运结算等。
提供实时的货物定位、查询、跟踪等服务,
实现物流信息共享,不断改善服务管理,为客户提供优质高效的物流服务,提高客户满意度。
四、强化供应链管理
加强供应链管理,全面实施供应链管理体系。
铅锌矿的供应链管理与物流优化
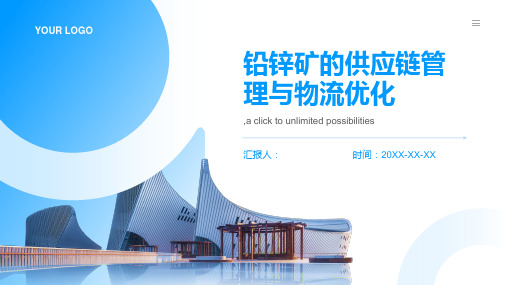
库存优化:通过数据分析和 模型计算,确定最佳库存水
平和订货策略
库存跟踪:实时监控库存状 态,及时调整库存策略,确
保供应链稳定运行
运输管理
运输方式:公路、铁路、水路、航空等 运输成本:运输距离、运输时间、运输方式等因素影响 运输效率:优化运输路线、提高装载率、减少运输环节等 运输安全:遵守交通规则、确保货物安全、防止污染环境等
风险监控:实时监控供应链运行情况, 及时发现风险
风险改进:根据监控结果,对供应链 进行改进和优化,降低风险发生概率
PART 6
铅锌矿供应链数字化转型
数字化转型的必要性
数字化转型的关键技术
大数据技术:收集、处理和分析大量数据,以支持供应链决策 人工智能技术:利用机器学习、深度学习等算法,提高供应链管理效率 物联网技术:通过传感器、RFID等设备,实时监控供应链各环节 区块链技术:提高供应链透明度和信任度,降低风险和成本 云计算技术:提供强大的计算和存储能力,支持供应链管理平台的运行 5G技术:提高数据传输速度和实时性,支持供应链的实时监控和响应
YOUR LOGO
铅锌矿的供应链管 理与物流优化
,a click to unlimited possibilities
汇报人:
时间:20XX-XX-XX
目录
01
02
03
04
05
06
添加标题
铅锌矿供 应链概述
铅锌矿供 应链管理 实践
铅锌矿物 流优化方 法
铅锌矿供 应链风险 管理
铅锌矿供 应链数字 化转型
铅锌产品回收:包括废旧铅锌产品回收、 再生利用等环节
供应链中的主要参与者
有色金属产业发展调研报告

有色金属产业发展调研报告有色金属产业发展调研报告一、产业概述有色金属产业是指矿山开采、冶炼、加工各种有色金属的产业。
有色金属是指除铁和钢之外的金属,包括铜、铝、铅、锌、镍、锡、钨、钼等。
这些金属具有优良的导电、导热、抗腐蚀等特性,是现代产业的重要原材料。
二、行业分析1.市场份额根据商务部数据,2019年我国有色金属产业销售收入约为9.94万亿元,占工业总产值的比重为16.2%。
其中铜、铝、铅、锌等占据市场份额比较大的有色金属的销售收入分别为3.77万亿元、2.7万亿元、1906亿元、1216亿元。
2.主要问题有色金属产业在发展过程中存在以下问题:(1)采矿技术落后,有色金属储量有限。
目前我国有色金属矿产储量总量较大,但金属品位较低,部分储量难以开发。
解决方法:引进国外先进的开采技术,提高开采效率。
(2)高能耗、高污染,对环境造成影响。
矿山开采和冶炼属于重污染行业,会对周围的环境产生影响。
解决方法:加强环保措施,提高资源利用率。
(3)产品价格波动较大,市场不稳定。
有色金属产业收到市场需求、供给、政策等多方面的影响,市场价格难以预测,波动较大。
解决方法:建立先进的市场监管机制,加强市场预警与调控。
3.发展前景有色金属产业是与国计民生密切相关的战略性产业。
随着技术的进步和环保意识的加强,有色金属产业的发展前景非常广阔。
预计未来几年,我国有色金属产业将持续稳定发展,市场需求也将稳步增长。
三、案例分析以铜产业为例,对有色金属产业的发展做出分析。
1.行业背景中国是全球最大的铜消费国和最大的铜精炼生产国。
我国铜生产量逐年增加,自然形成了产业链,以及从上游的原矿加工、生产、中游的铜精炼加工、下游的电线电缆、车用线束、水管、发动机等成品生产。
2.现状分析铜产业过去几年一直面临着环保、火灾等风险,整体发展情况不够稳定。
受疫情影响导致产量下降,但随着环保趋严,环保投入加大,对落后产能进行淘汰、整合,打击不法企业,使得铜产业整体上趋向健康。
有色金属运输储存管理制度
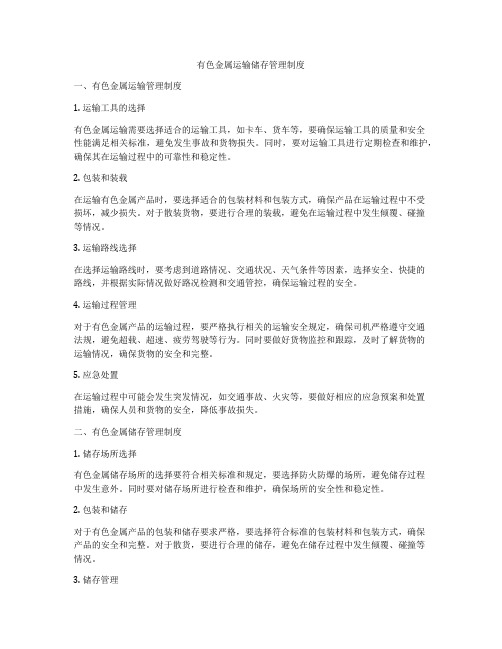
有色金属运输储存管理制度一、有色金属运输管理制度1. 运输工具的选择有色金属运输需要选择适合的运输工具,如卡车、货车等,要确保运输工具的质量和安全性能满足相关标准,避免发生事故和货物损失。
同时,要对运输工具进行定期检查和维护,确保其在运输过程中的可靠性和稳定性。
2. 包装和装载在运输有色金属产品时,要选择适合的包装材料和包装方式,确保产品在运输过程中不受损坏,减少损失。
对于散装货物,要进行合理的装载,避免在运输过程中发生倾覆、碰撞等情况。
3. 运输路线选择在选择运输路线时,要考虑到道路情况、交通状况、天气条件等因素,选择安全、快捷的路线,并根据实际情况做好路况检测和交通管控,确保运输过程的安全。
4. 运输过程管理对于有色金属产品的运输过程,要严格执行相关的运输安全规定,确保司机严格遵守交通法规,避免超载、超速、疲劳驾驶等行为。
同时要做好货物监控和跟踪,及时了解货物的运输情况,确保货物的安全和完整。
5. 应急处置在运输过程中可能会发生突发情况,如交通事故、火灾等,要做好相应的应急预案和处置措施,确保人员和货物的安全,降低事故损失。
二、有色金属储存管理制度1. 储存场所选择有色金属储存场所的选择要符合相关标准和规定,要选择防火防爆的场所,避免储存过程中发生意外。
同时要对储存场所进行检查和维护,确保场所的安全性和稳定性。
2. 包装和储存对于有色金属产品的包装和储存要求严格,要选择符合标准的包装材料和包装方式,确保产品的安全和完整。
对于散货,要进行合理的储存,避免在储存过程中发生倾覆、碰撞等情况。
3. 储存管理有色金属产品的储存管理要求严格,要对产品进行分类、编号、登记和盘点,确保产品的清晰可查。
并对产品的储存环境进行监控,确保环境的稳定和干燥,避免产品的腐蚀和氧化。
4. 安全防范对于有色金属储存场所要做好安全防范工作,包括防火、防盗、防爆等工作。
要配置相应的安全设施和器材,确保储存过程中的安全。
5. 应急处置在储存过程中可能会发生突发情况,如火灾、泄露等,要做好相应的应急预案和处置措施,确保人员和货物的安全,降低事故损失。
总结有色金属加工过程中的优化经验
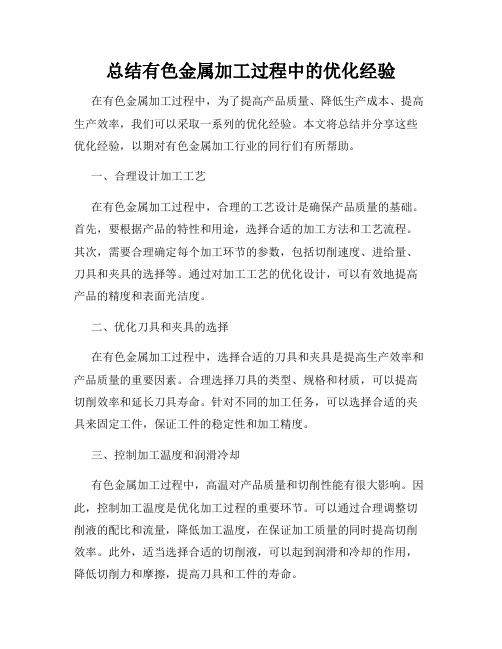
总结有色金属加工过程中的优化经验在有色金属加工过程中,为了提高产品质量、降低生产成本、提高生产效率,我们可以采取一系列的优化经验。
本文将总结并分享这些优化经验,以期对有色金属加工行业的同行们有所帮助。
一、合理设计加工工艺在有色金属加工过程中,合理的工艺设计是确保产品质量的基础。
首先,要根据产品的特性和用途,选择合适的加工方法和工艺流程。
其次,需要合理确定每个加工环节的参数,包括切削速度、进给量、刀具和夹具的选择等。
通过对加工工艺的优化设计,可以有效地提高产品的精度和表面光洁度。
二、优化刀具和夹具的选择在有色金属加工过程中,选择合适的刀具和夹具是提高生产效率和产品质量的重要因素。
合理选择刀具的类型、规格和材质,可以提高切削效率和延长刀具寿命。
针对不同的加工任务,可以选择合适的夹具来固定工件,保证工件的稳定性和加工精度。
三、控制加工温度和润滑冷却有色金属加工过程中,高温对产品质量和切削性能有很大影响。
因此,控制加工温度是优化加工过程的重要环节。
可以通过合理调整切削液的配比和流量,降低加工温度,在保证加工质量的同时提高切削效率。
此外,适当选择合适的切削液,可以起到润滑和冷却的作用,降低切削力和摩擦,提高刀具和工件的寿命。
四、加强设备维护与保养设备的维护与保养对于优化有色金属加工过程至关重要。
定期检查设备的运行状况,及时更换磨损严重的零部件,清洗和润滑设备,可以保证设备的正常运转和加工的稳定性。
另外,培养设备操作员的技术水平和维护意识,建立完善的设备管理制度,对于提高设备的利用率和延长设备的寿命也具有重要作用。
五、强化质量管理和技术创新在有色金属加工过程中,质量管理和技术创新是实现产业升级和提高竞争力的关键。
引进先进的质量管理体系,建立完善的质量控制流程,从源头上控制产品质量,避免不合格品的产生。
同时,加强研发和创新,探索新的加工方法和工艺,提高生产效率和产品质量。
总之,有色金属加工过程中的优化经验主要涉及合理设计加工工艺、优化刀具和夹具的选择、控制加工温度和润滑冷却、加强设备维护与保养、强化质量管理和技术创新等方面。
有色金属的供应链管理介绍有色金属供应链管理的关键要素和最佳实践
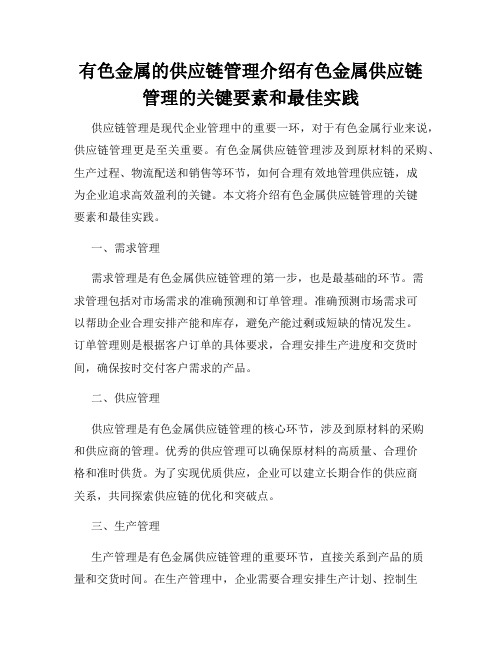
有色金属的供应链管理介绍有色金属供应链管理的关键要素和最佳实践供应链管理是现代企业管理中的重要一环,对于有色金属行业来说,供应链管理更是至关重要。
有色金属供应链管理涉及到原材料的采购、生产过程、物流配送和销售等环节,如何合理有效地管理供应链,成为企业追求高效盈利的关键。
本文将介绍有色金属供应链管理的关键要素和最佳实践。
一、需求管理需求管理是有色金属供应链管理的第一步,也是最基础的环节。
需求管理包括对市场需求的准确预测和订单管理。
准确预测市场需求可以帮助企业合理安排产能和库存,避免产能过剩或短缺的情况发生。
订单管理则是根据客户订单的具体要求,合理安排生产进度和交货时间,确保按时交付客户需求的产品。
二、供应管理供应管理是有色金属供应链管理的核心环节,涉及到原材料的采购和供应商的管理。
优秀的供应管理可以确保原材料的高质量、合理价格和准时供货。
为了实现优质供应,企业可以建立长期合作的供应商关系,共同探索供应链的优化和突破点。
三、生产管理生产管理是有色金属供应链管理的重要环节,直接关系到产品的质量和交货时间。
在生产管理中,企业需要合理安排生产计划、控制生产进度和质量,并及时反馈生产情况。
同时,生产过程中的物料管理和设备维护也是关键,确保生产能够顺利进行。
四、物流管理物流管理是有色金属供应链管理中的重要一环,包括仓储管理和运输管理。
仓储管理涉及到原材料和成品的存储和配送,需要合理规划仓库容量和布局,确保物料的安全储存和及时供应。
运输管理则包括物流配送的路线规划、运输工具选择和成本控制等,以降低物流成本并提高运输效率。
五、销售管理销售管理是有色金属供应链管理的最后一环,涉及到订单接收、销售预测和客户关系管理。
一个良好的销售管理可以及时响应客户需求,准确预测销售情况,并建立稳固的客户关系,保持长期合作和稳定销售。
最佳实践:1.建立合作伙伴关系:与供应商和客户建立长期的合作伙伴关系,共同优化供应链。
2.信息共享:建立信息化系统,实现供应链各环节的实时数据共享,提高协同效率。
云南有色金属行业发展方向与发展政策研究
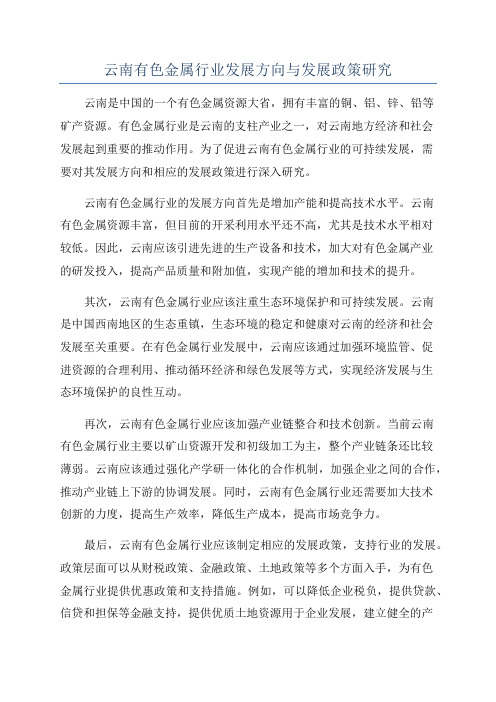
云南有色金属行业发展方向与发展政策研究云南是中国的一个有色金属资源大省,拥有丰富的铜、铝、锌、铅等矿产资源。
有色金属行业是云南的支柱产业之一,对云南地方经济和社会发展起到重要的推动作用。
为了促进云南有色金属行业的可持续发展,需要对其发展方向和相应的发展政策进行深入研究。
云南有色金属行业的发展方向首先是增加产能和提高技术水平。
云南有色金属资源丰富,但目前的开采利用水平还不高,尤其是技术水平相对较低。
因此,云南应该引进先进的生产设备和技术,加大对有色金属产业的研发投入,提高产品质量和附加值,实现产能的增加和技术的提升。
其次,云南有色金属行业应该注重生态环境保护和可持续发展。
云南是中国西南地区的生态重镇,生态环境的稳定和健康对云南的经济和社会发展至关重要。
在有色金属行业发展中,云南应该通过加强环境监管、促进资源的合理利用、推动循环经济和绿色发展等方式,实现经济发展与生态环境保护的良性互动。
再次,云南有色金属行业应该加强产业链整合和技术创新。
当前云南有色金属行业主要以矿山资源开发和初级加工为主,整个产业链条还比较薄弱。
云南应该通过强化产学研一体化的合作机制,加强企业之间的合作,推动产业链上下游的协调发展。
同时,云南有色金属行业还需要加大技术创新的力度,提高生产效率,降低生产成本,提高市场竞争力。
最后,云南有色金属行业应该制定相应的发展政策,支持行业的发展。
政策层面可以从财税政策、金融政策、土地政策等多个方面入手,为有色金属行业提供优惠政策和支持措施。
例如,可以降低企业税负,提供贷款、信贷和担保等金融支持,提供优质土地资源用于企业发展,建立健全的产权保护和市场准入机制等。
这些政策旨在吸引更多的投资、促进行业的发展壮大。
总之,云南有色金属行业的发展方向应该是增加产能、提高技术水平、注重生态环境保护、加强产业链整合和技术创新。
同时,云南应该制定相应的发展政策,为有色金属行业的可持续发展提供支持和保障。
这样,云南有色金属行业将能够承担更多的社会责任,为区域经济的发展做出更大的贡献。
有色金属加工企业生产物流合理化研究
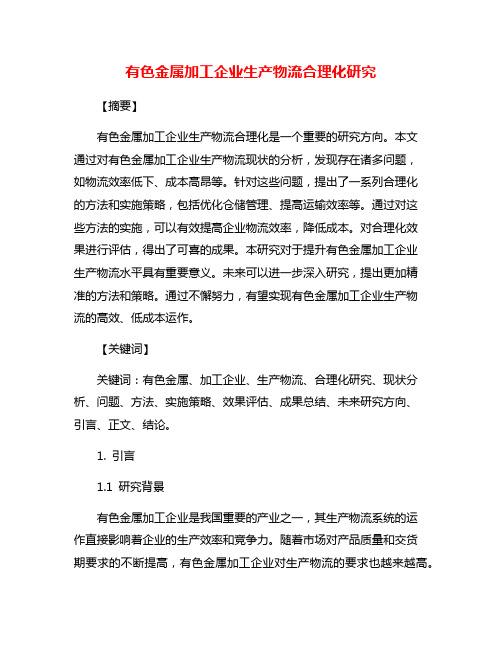
有色金属加工企业生产物流合理化研究【摘要】有色金属加工企业生产物流合理化是一个重要的研究方向。
本文通过对有色金属加工企业生产物流现状的分析,发现存在诸多问题,如物流效率低下、成本高昂等。
针对这些问题,提出了一系列合理化的方法和实施策略,包括优化仓储管理、提高运输效率等。
通过对这些方法的实施,可以有效提高企业物流效率,降低成本。
对合理化效果进行评估,得出了可喜的成果。
本研究对于提升有色金属加工企业生产物流水平具有重要意义。
未来可以进一步深入研究,提出更加精准的方法和策略。
通过不懈努力,有望实现有色金属加工企业生产物流的高效、低成本运作。
【关键词】关键词:有色金属、加工企业、生产物流、合理化研究、现状分析、问题、方法、实施策略、效果评估、成果总结、未来研究方向、引言、正文、结论。
1. 引言1.1 研究背景有色金属加工企业是我国重要的产业之一,其生产物流系统的运作直接影响着企业的生产效率和竞争力。
随着市场对产品质量和交货期要求的不断提高,有色金属加工企业对生产物流的要求也越来越高。
在当前的情况下,许多企业的生产物流存在着许多不合理之处,如生产过程中存在着浪费、物流成本过高、交货周期长等问题。
为了解决这些问题,有色金属加工企业急需对生产物流进行合理化研究。
通过对生产物流系统的现状分析和存在的问题进行深入剖析,可以找到改进的方法和实施策略,提高生产物流的效率和质量,降低成本,从而增强企业的竞争力。
本研究旨在探讨有色金属加工企业生产物流的合理化问题,寻找解决之道,为企业经营管理提供参考依据。
通过对生产物流合理化效果的评估,为企业未来的发展提供指导,促进行业的良性发展和持续发展。
1.2 研究目的研究目的是通过对有色金属加工企业生产物流的现状进行分析,找出存在的问题,探讨合理化的方法和实施策略,从而提高生产效率、降低成本、优化资源配置,促进企业的可持续发展。
通过本研究,可以为有色金属加工企业提供有针对性的改进建议,指导其物流管理工作,推动企业的产业升级和转型发展。
物流毕业论文题目大全

物流毕业论文题目物流毕业论文题目大全时光飞逝,已经接近年末,也是到了毕业论文选题的时候了。
下面是小编带来的物流毕业论文题目大全,希望可以帮到有需要的朋友,欢迎阅读分享。
物流毕业论文题目1一:供应链管理方向1. 企业供应链管理策略研究2. 网络时代供应链管理模式的研究3. 供应链风险形成机理分析4. 构建我国企业间供应链的对策初探5. 供应链管理下企业采购管理的发展趋势6. 基于供应链管理的库存管理模式比较7. 企业内部供应链流程中的时间分析8. 某商品供应链各环节的时间分析9. 供应链的风险防范对策研究10. 供应链运作对企业的影响研究11. 供应链管理中的信息共享问题研究12. 供应链管理的发展及运行机制探讨13. 供应链企业间的委托代理问题研究14. 供应链管理环境下的运输问题研究15. 供应链管理环境下的物流成本研究16. 条码技术在物流中的应用研究17. 物流信息技术应用研究18. 配送中心仓储管理信息系统设计19. 采购管理信息系统设计20. 国内ERP应用状况分析21. 物流企业物流信息化建设案例分析22. RFID应用案例研究23. EPC应用案例研究24. 某企业ERP实施方案分析25. 电子产品代码(EPC)在物流中的应用26. 物流技术的经济性研究27. 货物运输方案优化研究28. 物流配送中货物装载问题研究29. 货物运输系统优化分析30. 车船配载理论与方法研究31. 城市建材配送中心选址研究32. 城市日用品配送中心选址研究33. 配送中心作业计划优化方法研究34. 物流设施选址问题研究35. 随机需求的最优库存策略研究36. 逆向物流网络中的选址问题研究37. 试论某地区回收物流网络的形成与发展38. 试论废弃物物流体系的建立39. 某企业物流规划案例分析40. 某地区物流发展规划研究41. 信息时代物流企业网络化发展模式探讨42. 物流网络化运营模式的探讨43. 物流网络化中的风险分析44. 虚拟库存案例分析45. 仓储企业向现代物流转型研究46. 企业生产物料的合理采购及存储47. 制造企业原料库存量的控制研究48. 企业仓库管理流程中的时间分析49. 物流成本核算研究50. 运用物流成本进行企业物流决策51. 商业企业物流成本分析52. 企业物流作业环节费用的比较分析53. 物流行业客户满意度研究54. 物流客户服务策略的制定55. 某企业物流业务流程分析56. 企业物流作业流程的再造与控制57. 医药品储备应急物流研究58. 医药储备问题研究59. 农业供应物流研究60. 农产品物流发展现状和对策61. 我国农产品物流与发达国家的差距分析62. 农业销售物流研究63. 建设项目物流管理模式的比较64.图书物流合理化研究65.印刷行业物流发展战略66.汽车企业供应物流研究67.出版物物流标准化研究68.企业销售物流研究69.企业供应物流研究70.敏捷制造与精益制造中的物流管理比较71.市场营销渠道组合与物流模式分析72.企业物流资产经营模式分析73.我国物流企业上市公司现状分析74.物流外包决策分析75.物流企业综合竞争力评价的探讨76.第四方物流对中国物流产业发展战略的影响研究77.我国物流企业策略创新研究78. 某地区物流发展史研究79.物流产业发展初探80.第三物流的发展现状及趋势研究81.城市物流需求分析82.城市居民消费结构与物流需求研究83.物流服务的价格问题分析84.物流设施投资风险管理研究85. 区域经济与物流产业发展研究86.循环经济条件下逆向物流体系的建立87.废弃集装箱的收集、加工与再生88.绿色包装在物流企业中的应用89.政府行为在物流业发展中的地位与作用90.运输路径优化问题研究91.试论企业降低物流成本的途径92.物流企业提高物流服务质量的探讨93.试论提高物流设施(设备)利用率的途径94.市场经济条件下合理运输的探讨95.生产企业内部物流合理化探讨96.试论流通加工对物流合理化的影响97.试论电子商务环境下的物流对策98.我国发展第三方物流面临的挑战与对策研究二:对外物流方向1. 国内外主要港口物流发展模式及对深圳的启示2. 第三方物流的风险识别及防范3. 中国邮政物流的现状与发展建议4. 区域物流与区域经济的关系探讨——以深圳为例5. 我国社会XXXX资源回收物流的经济意义及物流体系建立6. 我国XXXX废弃物物流策略研究7. 企业物流模式的选择8. 浅析我国第三方物流业发展战略9. 物流客户关系管理10. 我国物流现状及发展趋势分析11. 业务外包的风险管理和控制12. 基于循环经济的汽车逆向物流研究13. 深圳海港快速发展的成因分析14. 我国国际货运代理业的改革和发展15. 物流企业绩效评价体系研究16. 基于循环经济的逆向物流研究17. 国外零售企业供应链管理经验及对我国本土企业的借鉴18. CEPA基础上深港物流合作19. 供应链管理下通讯和电子行业价值探讨20. 中小物流企业共同配送问题研究21. 浅析中国物流企业的服务营销22. 国际快递巨头压力下中国快递业的现状及发展对策23. 连锁零售企业物流配送模式及其发展探究24. 戴尔直销模式下的供应链管理25. 汽车企业的采购模式26. 供应链中的牛鞭效应与库存控制27. 深港集装箱港口竞合经济学分析28. 基于循环经济的逆向物流研究29. 浅析物流外包的风险与防范30. 关于中远物流核心竞争力的探讨31. 基于循环经济的逆向物流研究32. 基于循环经济的逆向物流研究33. 现代物流发展对深圳产业结构的影响研究34. 现代物流业与深圳经济的发展35. 标准化、信息化物流对深圳经济的促进作用36. 我国快递业法制化建设研究与分析37. 通过逆向物流实现餐饮业“绿色化”的策略研究38. 我国第三方物流企业运行模式探讨39. 电子供应链管理环境下的企业采购管理40. 物流园区选址浅析41. 基于电子商务的物流公共信息平台的探索42. 深圳湾口岸公共交通情况调查及其线路设计43. 我国医药逆向物流发展的策略研究44. 我国IT供应链中渠道管理问题研究45. 浅析我国国际货运代理业的发展与未来46. 国内连锁超市与沃尔玛的配送系统比较分析47. 零售连锁企业物流成本的控制48. 基于循环经济的逆向物流研究49. 制造企业的物流成本核算与控制对策分析50. 基于VMI的供应链库存控制分析51. CtoC电子商务物流与配送52. 广州会展物流行业的发展模式与策略研究53. 大珠三角地区港口群整体发展战略探讨54. 基于循环经济的逆向物流研究55. 淘宝网物流配送模式分析56. 国外多式联运发展经验及其对我国的启示57. 关于深圳物流产业发展几个问题的探讨58. RFID在道路集装箱运输管理中的应用59. 浅析我国废旧电池回收处理存在的问题及对策60. 国际物流企业在中国的本土化研究61. 我国国际货代业向现代物流发展的分析与对策62. 对供应链中的物流发展的思考63. 我国制造业企业供应链伙伴关系研究——上海家化的物流外包研究64. 国际多式联运单证的无纸化研究65. 基于供应链的虚拟企业构建战略研究66. 论政府在循环经济与逆向物流中的作用67. 生产主导型供应链信息共享机制研究68. 中小物流企业共同配送系统规划69. 现代物流园区选址探讨—以平湖物流园区为例70. 基于供应链的虚拟企业构建战略研究71. RFID在路口车辆监控的应用72. 供应链采购中的供应商质量管理73. 中小型物流企业电子商务应用模式研究74. 货运网络营销研究75. 关于中国现代物流发展的几点思考76. 传统物流企业向现代物流企业转型研究77. 珠三角区域经济下的港口格局及发展分析78. 货运营销管理相关问题探讨79. 浅析再制造工程中的逆向物流80. 粤港澳物流业的发展现状及合作研究81. 自营、外购--企业物流模式选择82. 第三方物流企业关系营销策略的探讨83. 企业逆向物流的SWOT分析与发展策略84. 深圳与香港港口的`集装箱运输状况研究85. 物流外包的利弊及其与市场诚信的关系研究86. 物流外包的发展及其风险管理87. 提升港口企业核心竞争力的途径和策略88. IT行业物流的发展现状与对策研究89. 湛江发展物流业的对策90. 现代企业物流模式选择研究91. 深圳和香港交通状况与合作研究92. 国际航运市场态势与深圳航运企业的应对策略93. 物流外包的决策分析及风险防范94. 关于深圳发展绿色物流业的对策研究95. 港口物流发展策略研究96. 物流信息网络平台研究97. 对我国逆向物流发展的探讨98. 西部开发与环境保护—交通基础设施的建设对环保的影响99. 我国汽车行业物流实行JIT运作的风险与对策100.中国现代物流发展战略和措施101.运输现代化与我国现代物流建设102.深圳货代市场存在的问题与对策研究103.传统货代企业向现代物流企业转型的策略研究104.珠江三角洲主要港口之间的合作策略研究105.企业发展绿色物流的动因及策略分析106.物流外包的动因及风险管理策略研究107.传统物流企业向现代物流企业转型的探讨--以宝供物流为例108.国际集装箱枢纽港发展分析109.企业物流外包的风险及其与市场诚信的关系研究110.中国邮政快递(EMS)的发展现状与对策研究111.集装箱运输需求弹性分析与营销对策112.物流企业核心竞争力分析与评价113.我国本土零售物流的发展现状及对策分析114.珠三角港口群竞争与合作115.物流外包的风险类别及其防范措施116.提升第三方物流企业核心竞争力117.加快我国铁路运输业现代物流化的对策探讨118.珠江三角洲港口群发展趋势的分析研究119.港口对其经济腹地的贡献度分析--以深圳港为例120.现代物流与中心城市经济发展的互动效应研究121.我国零售物流的发展现状与对策研究122.我国制造企业物流实行JIT运作的风险与对策123.集装箱港口竞争力评价指标研究124.提升港口群整体竞争力的策略研究--腹地地缘的战略优势125.供应链管理思想在现代港口中的应用126.我国家电行业物流发展现状与运作模式研究127.电子商务环境下的逆向物流的模式选择128.以区域经济理论浅析深圳与香港两地的港口合作129.物流金融的内涵辨析130.提升港口群整体竞争力的策略研究--以长三角港口群建设实践作案例分析131.珠三角区域经济下的港口格局演变132. 绿色物流——物流中的新亮点133. 物流品牌的原点回归——品牌定位134. 整合物流管理,提升企业竞争力(现状、机会、威胁) 135. 在校大学生的消费心理特点及企业营销策略136. 顺应时代潮流,树立绿色物流观137.第三方物流信息技术应用研究138. 知识经济对企业物流的影响139. 企业如何建立有效的分销渠道140. 如何进行企业的品牌建设141.论包装在运输过程中的作用142. 如何塑造企业形象143. 论企业文化与企业核心竞争力144. 企业物流的战术策略145. 企业要重视文化塑造146. 企业物流与企业文化147. 买方市场条件下企业的市场物流148. 试论我国企业物流配送能力的培养与增强149. 现代企业物流发展趋势及其对策150. 第三方物流的发展现状与趋势151. 传统企业如何发展电子商务152. 试论电子商务与中国物流的发展153. 我国电子商务发展中的问题及其对策154. 电子商务发展中的税收问题及其对策155. 电子商务与现代物流的关系分析156. 网络商品直销与网络商品中介交易的对比分析157. 浅谈知识型员工的管理158. 谈企业文化的建设159. 浅谈我国民营企业的发展160. 全球经济一体化条件下市场物流的新思考161. 我国加入WTO如何规避企业的不正当竞争162. 企业网络营销物流中存在的主要障碍及其对策163. 企业战略结构的调整及分析164. 市场调查分析及经济活动分析165. 企业物流中的法律问题探讨研究166. 国有企业的经营发展战略167. 食品企业的生产加工及经营发展探讨168. 广告设计与策划169. 创业设计及商务活动策划170. 连锁经营与特许经营171. 商品结构分析及商品创新172. 消费者权益保护研究173. 浅谈我国“绿色物流“存在的问题与对策174.企业库存控制方案设计175.企业运输方案设计176.企业配送体系的构建177.制造企业生产物流合理化的研究178.仓储业物流战略探讨179.物流企业资源整合与规模化研究180.第三方物流企业资源整合研究181.现代粮食企业物流经济模式分析182.绿色物流的政策环境分析与对策研究183.中小物流企业竞争力研究184.浅谈国家对物流产业的政策支持185.现代采购管理对提升企业竞争力的探讨186.基于VMI的供应连管理模式187.绿色物流管理的研究188.企业物流外包的战略决策和关系管理189.条码技术分析及其在物流中的应用190.供应商的选择与评价191.配送中心的选址及规划192.仓储业物流战略讨论193.危险品仓库质量管理体系构建研究194.中国汽车物流发展现状及对策研究195.连锁经营企业开展物流服务问题研究196.物流企业信息化管理研究197.我国第四方物流的发展模式及其策略研究198.连锁企业配送中心信息系统规划199.基于CRM(客户关系管理)的供应链管理研究200.供应链协同化管理面临的困难与应对策略201.企业物流模式决策分析202.逆向物流的经济价值及管理策略研究203.六西格玛与物流服务质量管理204.制约我国第三方物流发展因素的研究205.我国第三方物流发展趋势研究206.商业连锁企业配送中心运作研究207.第三方物流企业的网络化经营问题研究208.绿色物流管理的研究209.企业采购外包管理研究210.浅析供应商开发与控制211.基于WTO形式下,中国企业如何应对国际采购212.浅议准时化采购管理213.对采购管理中供应商数量选择的研究214.郑州市物流业发展现状调查;215.某企业物流管理设计;216.某企业在2006~2010年间的物流发展规划; 217.电子商务环境下发展物流的策略;218.高职高专物流人才培养模式的探讨219.第三方物流企业发展定位模型的研究220.公路运输业对发展物流服务的研究221.传统储运如何向现代物流转化222.供应链企业间战略合作模式研究223.企业物流成本管理的对策研究物流毕业论文题目21、“互联网+”时代物流业的创新发展2、“一带一路”区域物流协同发展分析3、5R管理在钢铁物流中的实践4、B2C电子商务企业物流配送质量研究5、B2C电子商务物流企业顾客体验评价研究6、DH公司应急物流系统的优化研究7、SC公司物流服务模式创新的研究8、北京市废旧汽车逆向物流系统优化分析9、北京市物流需求预测研究10、菜鸟物流模式对现代物流发展启示11、超高频射识别在物流中的应用研究12、大连港第三方物流的发展13、当当网物流服务质量评价研究14、德邦物流企业物流服务质量评价研究15、第三方物流的仓储管理16、第三方物流的利与弊17、第三方物流供应商选择问题研究18、第三方物流企业仓单质押风险评价研究19、第三方物流企业仓单质押服务现状问题的探讨20、第三方物流企业发展的现状与前景21、第三方物流企业客户关系管理22、第三方物流企业市场营销研究述评23、第三方物流企业盈利模式与成本管理分析24、第三方物流实施VMI配送优化的研究25、第三方物流信息系统设计探讨26、第三方物流与供应链的融合研究27、第三方物流运输云计算应用28、对比分析农产品的冷链物流模式29、对我国物流成本的再认识30、多车场物流协同运输调度的方法研究31、改革中小制造业物流成本控制的策略32、高职物流英语的特点及翻译探讨33、公路低碳物流发展影响因素分析34、公路煤炭物流网络优化研究35、关联物流运输调度问题研究36、关于铁路物流能力提升路径的探讨37、广西农村电子商务物流网点布局方案研究38、广西物流产业空间集聚水平分析39、杭州地区第三方物流发展对策40、合肥农产品物流管理模式创新研究41、河北烟草物流增值服务研究42、基于RFID技术的生产物流管理系统改进研究43、基于第四方物流平台的快递末端网点优化整合44、基于电子商务的现代物流业新型发展模式分析45、基于供应链系统下的企业物流管理研究46、基于供应链下上海通用汽车整车分销物流的方案实施47、基于物联网技术的甩挂物流信息平台建设探讨48、基于物联网技术的铁路物流运作模式研究49、集宁现代物流园区发展战略研究50、计算机之大数据对智慧物流的影响51、荆州港口物流发展对策研究52、精益思想应用于企业物流管理探讨--供应链环境下53、军地物流深度融合发展研究54、考虑供应不足的应急物流车辆路径优化模型及算法55、跨境电子商务物流发展问题的研究56、兰州铁路局物流基地布局规划方案的探讨57、零售商主导下物流外包的三级供应链决策58、绿色物流园区评价方法初探59、宁波电商与物流产业协同发展对策探讨60、企业物流管理绩效评价体系的构建61、企业物流中心的选址问题研究62、企业物流周转与存货管理的关系研究63、浅析军民融合应急物流体系建设实践64、如何加强钢铁行业物流企业综合事务管理65、试论物流机械设备使用管理66、数据挖掘技术在物流企业信息共享中的应用67、铁路物流中心仓库平面设计研究68、网络购物背景下的物流服务质量测评69、网络视角下的物流集群研究进展70、我国第三方物流企业服务创新研究71、我国电力企业物流管理及其信息化建设探究72、我国零担物流时效性问题探究73、我国生鲜农产品第三方冷链物流系统模型研究74、我国物流金融业务运作及盈利模式构建75、我国物流运输现状及其发展路径76、我国现代农业与物流业耦合关联的实证研究77、我国医药第三方物流发展探讨78、我国制造业企业物流模式研究79、物联网环境下金属物流电子商务的优化供应链设计80、物流包装箱改进及信息技术研究物流毕业论文题目31、第三方物流信息技术应用研究2、B2B电子商务对交易成本的影响的分析3、电子商务的发展对第三产业结构的影响4、电子商务时代的企业价值创新5、电子商务时代网络营销的变迁6、电子商务的发展创新与环境构筑7、电子商务环境下的敏捷制造研究8、电子商务环境下物流企业经营战略分析9、电子商务时代和信息时代的供应链管理与物流配送10、电子商务环境下物流业发展对策探讨11、电子商务时代的物流配送思考12、电子商务对企业的影响与对策13、试论企业电子商务的风险控制14、试论电子商务与高新技术产业发展战略15、网络经济时代下的传统企业电子商务化16、电子商务发展的现状、难题及对策分析17、论包装在运输过程中的作用18、浅谈运输成本控制19、论智能运输系统在我国的发展20、中国公路货物运输发展研究21、公路危险品运输管理探讨22、浅谈超载运输的危害及其对策23、浅谈超限运输的危害及其对策24、道路危险货物运输中的若干问题研究25、浅谈运输工具的选择对成本的影响26、道路运输责任划分的研究与分析27、浅谈运输线路的选择和优化28、道路货运装卸搬运合理化的研究与探讨29、浅谈运输合理化30、关于XX市快速公交系统的调查与分析31、关于XX市XX集装箱运输公司的调查与研究32、关于公路集装箱运输经济学初步理论研究33、基于集装箱的离散型、分布式运输生产与运作初步研究34、关于公路集装箱运输企业IT战略研究35、浅议公路集装箱运输系统及关键系统需求36、公路与铁路集装箱运输相关法规调查与分析37、公路集装箱运输管理信息系统初步研究38、供应链管理环境下第三方物流企业发展策略研究39、第三方物流企业经营战略研究40、XX物流信息系统规划设计41、物流企业核心竟争力研究42、XX物流通道系统规划设计43、物流中心规划与设计方法研究44、物流配送路线优化的研究45、试论区域经济中的现代物流发展战略46、试析供应链管理对中国企业发展的影响与作用47、关于现代物流园区建设的思考与建议48、关于建立区域物流规划的的战略思考49、区域现代物流产业发展规划50、XX企业物流系统整体规划51、基于供应链设计和规划的方法应用52、基于中部崛起的河南物流业发展对策分析53、“牛鞭效应”产生的机理与对策研究54、关于我国内陆地区现代物流系统规划的几点思考55、论货物运输合同的法律适用56、如何构建我国的物流法律法规体系57、论海上货物运输合同的违约责任58、仓单制度研究59、仓储法律制度研究60、校园规划设计招投标若干问题的研究61、试述招投标工作应遵循的原则62、保留所有权买卖合同期待权的若干问题研究物流毕业论文题目41、RFID技术研究及其在仓储管理中的应用2、基于RFID的仓储管理信息系统研究与设计3、基于RFID技术的仓储管理系统研究与应用4、ZX公司电子产品仓储管理的研究5、医药冷链物流仓储管理系统关键问题研究6、远征药业仓储管理研究7、X仓库仓储管理问题与对策研究8、RFID在物流仓储管理系统中的应用研究及设计9、S联通公司物资仓储管理策略研究10、基于供应链管理的物流仓储管理系统研究与开发11、RFID技术在仓储管理中的应用研究12、基于RFID的供应链仓储管理研究及系统设计13、仓储管理自动化系统的研究和开发14、现代物流仓储管理系统的研究与设计15、A公司仓储管理研究16、基于RFID的百货超市仓储管理系统的设计与实现17、RFID技术在物流仓储管理系统中的研究及应用18、基于RFID的现代邮政物流仓储管理信息系统研究19、面向自动化化立体仓库的仓储管理系统的研究与应用20、面向自动化立体仓库的仓储管理系统的研究21、VMI模式下A公司仓储管理研究22、某备件库仓储管理系统效率优化研究23、基于RFID技术的仓储管理系统开发24、射频识别技术在仓储管理中应用的研究25、仓储管理系统的设计与实现26、基于RFID的立体仓库仓储管理系统的研究27、仿真技术在仓储管理中的应用研究28、海港发电厂仓储管理优化研究29、J公司仓储管理优化研究及系统开发30、JDZ电厂仓储管理优化设计与研究31、基于RFID的零售业仓储管理信息系统应用设计32、基于第三方物流的仓储管理信息系统研究33、配送中心仓储管理信息系统的研究与设计。
关于有色金属产业发展情况调研报告
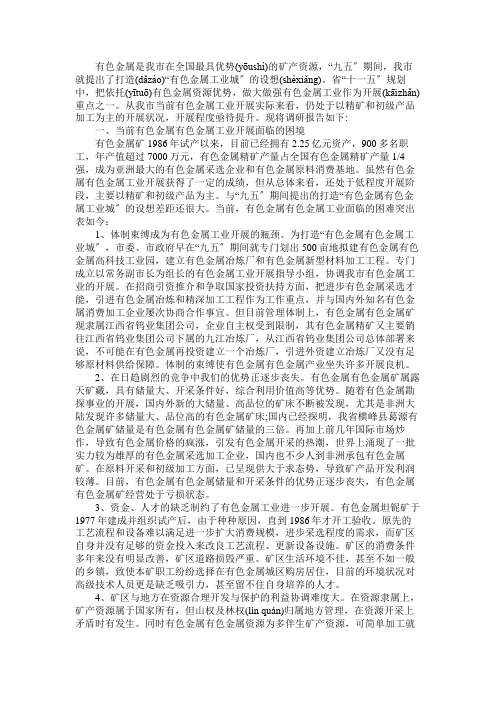
有色金属是我市在全国最具优势(yōushì)的矿产资源,“九五〞期间,我市就提出了打造(dǎzào)“有色金属工业城〞的设想(shèxiǎng)。
省“十一五〞规划中,把依托(yītuō)有色金属资源优势,做大做强有色金属工业作为开展(kāizhǎn)重点之一。
从我市当前有色金属工业开展实际来看,仍处于以精矿和初级产品加工为主的开展状况,开展程度亟待提升。
现将调研报告如下:一、当前有色金属有色金属工业开展面临的困境有色金属矿1986年试产以来,目前已经拥有2.25亿元资产,900多名职工,年产值超过7000万元,有色金属精矿产量占全国有色金属精矿产量1/4强,成为亚洲最大的有色金属采选企业和有色金属原料消费基地。
虽然有色金属有色金属工业开展获得了一定的成绩,但从总体来看,还处于低程度开展阶段,主要以精矿和初级产品为主。
与“九五〞期间提出的打造“有色金属有色金属工业城〞的设想差距还很大。
当前,有色金属有色金属工业面临的困难突出表如今:1、体制束缚成为有色金属工业开展的瓶颈。
为打造“有色金属有色金属工业城〞,市委、市政府早在“九五〞期间就专门划出500亩地拟建有色金属有色金属高科技工业园,建立有色金属冶炼厂和有色金属新型材料加工工程。
专门成立以常务副市长为组长的有色金属工业开展指导小组,协调我市有色金属工业的开展。
在招商引资推介和争取国家投资扶持方面,把进步有色金属采选才能,引进有色金属冶炼和精深加工工程作为工作重点,并与国内外知名有色金属消费加工企业屡次协商合作事宜。
但目前管理体制上,有色金属有色金属矿现隶属江西省钨业集团公司,企业自主权受到限制,其有色金属精矿又主要销往江西省钨业集团公司下属的九江冶炼厂,从江西省钨业集团公司总体部署来说,不可能在有色金属再投资建立一个冶炼厂,引进外资建立冶炼厂又没有足够原材料供给保障。
体制的束缚使有色金属有色金属产业坐失许多开展良机。
有色金属行业研究报告

有色金属行业研究报告1历史上的大宗商品超级周期大宗商品的超级周期通常是由某种结构性需求刺激引发的,这种刺激大到足以在全球范围内提振对大宗商品的需求,而其供应却对此反应迟缓。
在自然资源方面,往往存在供给滞后,因为建设一个大矿山可能需要10年甚至更长时间。
虽然业内对于超级周期没有明确定义,但它通常用于描述商品价格在10至30年内高于其长期趋势的时期。
自19世纪以来,经济学家已经确定了四个商品价格持续高于趋势的时期。
第一次,恰逢美国在1880年代崛起成为全球经济强国;另一个伴随着1930年代的全球重整军备运动,并持续到二战后的重建时期;第三次,是在1970年代的油价冲击期间,通过增加生产成本间接推高了其他商品的价格;最近的一次价格上涨发生在2000年代初期开始的中国快速工业化期间,增加了对铁、铜和石油的需求,在此期间,农产品价格也急剧上涨,引发了2007-2008年的粮食危机。
本次是一种非常不同的大宗商品周期,2013年后随着中国这一世界制造业引擎逐步迈向高质量发展阶段,对大宗商品的需求开始历史性下滑,同时气候变化成为首要考虑因素,投资者更加重视环境、社会和治理等ESG问题,加剧了本已日益严重的投资不足问题,阻碍了大宗商品产能的增长。
随着全球经济从新冠疫情的封锁中复苏,这些紧张的供应和被压抑的需求助长了全球通胀持续高企,即使中国可能无法发挥上一个大宗商品超级周期的助推作用,但全球各国减少石化燃料排放的努力和对清洁能源基础设施支出的增加将意味着对特定金属需求增加,全球绿色资本支出的故事将变得越来越大,这些代价高昂、长达数十年的计划将改变许多商品的供需状况,在这样的背景下大宗商品出现短缺,并推动价格上涨。
2本轮有色金属周期的特征从能源到金属,对原材料的抢购已经反映在期货市场上,在金属方面的这一问题尤其严重,伦敦金属交易所的几份金属合约的现货价格高于后期交割的价格,大量商品已经转为现货溢价,这是一种表明稀缺性的定价结构,这种市场结构表明贸易商和投资者准备为商品的即时供应支付高额溢价。
调研有色金属企业情况报告

调研有色金属企业情况报告
一、调研背景
1. 调研目的与意义:解析有色金属企业的发展现状及面临的挑战,为制定相应政策提供依据。
2. 调研方法与过程:通过实地访谈、问卷调查和数据分析等手段收集有色金属企业的相关信息。
3. 调研范围与样本选择:选择代表性有色金属企业,涵盖不同规模、不同地区,以获取全面的调研结果。
二、有色金属企业的生产与销售情况
1. 生产概况:分析有色金属企业的生产规模、生产工艺和主要产品等关键指标。
2. 销售概况:调查有色金属企业的销售渠道、销售额及销售市场等相关信息。
3. 企业竞争力:评估有色金属企业的市场份额、技术水平以及品牌影响力等方面的竞争力。
三、有色金属企业的环境与社会责任
1. 环境保护措施:调查有色金属企业在生产过程中的环境保护措施与环保标准的执行情况。
2. 资源利用效率:分析有色金属企业在资源利用方面的效率,关注能耗和废物处理等问题。
3. 社会责任履行:研究有色金属企业在员工福利、慈善捐赠和社区参与等方面的社会责任履行情况。
四、有色金属企业的发展前景与建议
1. 市场趋势分析:研判有色金属企业未来发展的市场趋势,并对行业竞争格局作出预测。
2. 发展机遇与挑战:探讨有色金属企业面临的机遇和挑战,为企业制定合理战略提供参考。
3. 发展建议:基于调研结果和前瞻性分析,提出相应的发展建议,以促进有色金属企业的可持续发展。
每个小章节大致100字左右,希望这些内容能对你的文章撰写提供帮助。
如果还有其他问题或需要进一步修改,请随时告诉我。
2024年有色金属压延加工市场环境分析
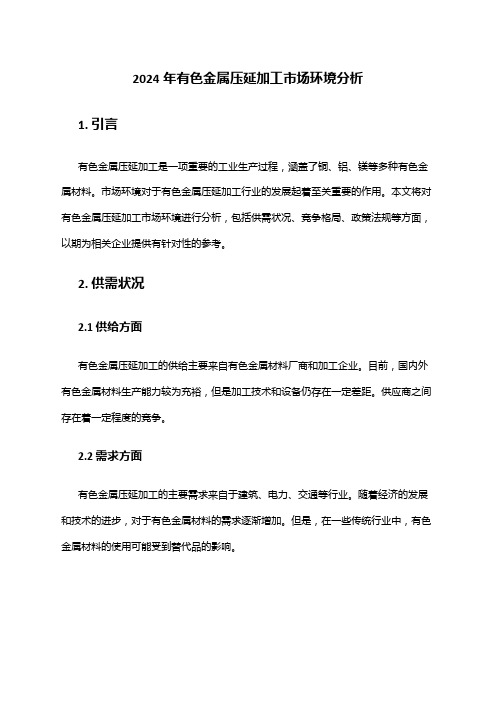
2024年有色金属压延加工市场环境分析1. 引言有色金属压延加工是一项重要的工业生产过程,涵盖了铜、铝、镁等多种有色金属材料。
市场环境对于有色金属压延加工行业的发展起着至关重要的作用。
本文将对有色金属压延加工市场环境进行分析,包括供需状况、竞争格局、政策法规等方面,以期为相关企业提供有针对性的参考。
2. 供需状况2.1 供给方面有色金属压延加工的供给主要来自有色金属材料厂商和加工企业。
目前,国内外有色金属材料生产能力较为充裕,但是加工技术和设备仍存在一定差距。
供应商之间存在着一定程度的竞争。
2.2 需求方面有色金属压延加工的主要需求来自于建筑、电力、交通等行业。
随着经济的发展和技术的进步,对于有色金属材料的需求逐渐增加。
但是,在一些传统行业中,有色金属材料的使用可能受到替代品的影响。
3. 竞争格局有色金属压延加工行业存在较为激烈的竞争。
竞争主要集中在产品品质、价格和服务等方面。
3.1 产品品质优质的产品品质是吸引客户的关键因素。
一些企业利用先进的生产技术和设备,提高产品品质,获取竞争优势。
3.2 价格价格是影响购买决策的一个重要因素。
因此,企业需要通过合理的价格策略来争夺市场份额。
此外,企业还需关注原材料价格的波动,以控制成本。
3.3 服务良好的售后服务能够提高客户忠诚度和市场竞争力。
企业需要加强对客户的沟通与关心,及时解决客户的问题,树立良好的企业形象。
4. 政策法规政策法规对于有色金属压延加工行业的发展具有重要影响。
4.1 国家政策国家政策对于有色金属行业的发展有一定引导作用。
政府可以通过财政支持、税收优惠等方式,促进有色金属压延加工行业的健康发展。
4.2 环保法规环保法规对于有色金属压延加工行业来说尤为重要。
企业需要遵守相关环保法规,减少环境污染,并加大环保设备的投入。
5. 总结有色金属压延加工市场环境的分析对于企业的战略决策具有重要意义。
根据市场供需状况、竞争格局和政策法规等因素,企业可以制定适应性的发展策略,提高市场竞争力。
有色金属加工项目可行性研究报告

有色金属加工项目可行性研究报告一、项目背景随着工业化进程的加快,有色金属加工领域的需求不断增长。
有色金属材料具有优良的导电、导热、耐腐蚀等性能,在航空、汽车、电子等领域有广泛应用。
因此,开展有色金属加工项目有着广阔的市场前景。
二、项目市场分析1.市场需求:有色金属在航空、汽车、电子等行业的需求稳定增长,市场需求前景广阔。
2.竞争情况:目前有色金属加工行业存在一定的竞争压力,但市场容量大,仍有发展空间。
3.市场规模:根据调研数据显示,有色金属加工市场规模约为1000亿人民币,预计将持续增长。
三、项目可行性分析1.技术可行性:有色金属加工涉及多种加工工艺和技术,目前技术水平较为成熟,可以满足市场需求。
2.经济可行性:有色金属加工项目具备一定的经济可行性。
首先,市场需求旺盛,有足够的市场空间。
其次,有色金属的价格相对较高,有利于项目盈利。
再次,项目的投资成本相对较低,回收周期较短,对资金的要求较少。
3.社会可行性:有色金属加工项目对于推动地方经济发展具有积极意义,可以提供大量就业机会,促进经济增长。
四、项目实施方案1.选址:根据市场需求和能源条件,选用地处交通便利、电力资源丰富的地方进行项目建设。
2.设备采购:根据加工需求和工艺要求,购买先进的有色金属加工设备。
3.员工组建:根据项目规模和需求,招聘具备相关技术和管理经验的员工。
4.市场推广:加强市场调研,深化对顾客需求的了解,同时积极开展产品宣传和推广。
5.质量管理:严格按照相关质量标准进行生产,确保产品质量稳定。
五、风险分析1.市场风险:有色金属加工市场存在一定的竞争压力,需密切关注市场变化,灵活调整营销策略。
2.技术风险:有色金属加工项目对技术要求较高,需要保持技术更新,不断提高加工工艺。
3.资金风险:项目运营需要一定的资金支持,需要合理的财务规划和资金筹措手段。
六、项目预期效益1.经济效益:有色金属加工项目盈利前景广阔,能够实现经济效益的稳定增长。
企业物流过程中的金属平衡实证研究

适用于生产经营、 质量监控 、 环境监测 、 能源计量和
职业健康安全管理等方面 测量数据的管理与控制。 3 职责 . 以 金属冶炼企业为例, 其金属平衡过程设计应该考 测量设备使用单位应确保在用的测量设备始终处于 虑4 个过程 : 一是原料供应过程的金属平衡 , 主要应该考 核合理途耗 、 供应商与冶炼厂之间的检斤、 检验合理误差 确认合格状态。计量检验部门负责贸易结算测量数据的
金属的直收率 、 回收率、 弃渣含有价金属 、 产品含有价金 属等指标 。三是产品销售过程的金属平衡 , 主要应该考
核冶炼厂产品与用户之间的检斤 、 检验合理误差等指 标。四是从原料供应到生产过程 , 再到产品销售整个大
主要应该考核有价金属含量减去上述 系到企业的 经营效益。 对于金属冶炼企业来说, 原料供 过程 的金属平衡 , 3 个过程的合理损耗是否等于产品中有价金属的合理含 应物流中的金属是否平衡 , 冶炼过程中的金属是否平衡 、 量等指标 。通过大过程的金属平衡管理与考核 , 可以有 有价金属是否得以有效回收, 产品销售物流中的金属是 效规避各过程衔接中的金属流失。 否平衡 , 是冶炼企业各项工作好与坏的集 中体现。对于
冶金 经 济与 管理
文章 编号 :0 2 17 (0 00 -0 0 10 — 79 2 1 )4 0 1- 2 1
企业物流过程中的金属平衡实证研究
口 董 效林
摘 要 : 金 属 平 衡 工 作 在 金 属 开 采 企 业 、 属 冶 炼 企 业 、 属 加 工 企 业 和 机 械 制 造 企 业 中的 重 要 性 对 金 金
部门负责生产过程中物流平衡的检斤 、 检验与检测; 出厂
产品由销售部门负责检斤计量 , 产品生产单位负责检斤 计量比对 ; 出厂产品由计量检验部门负责检验、 , 检测 产 品生产单位负责检验 、 检测比对。
采矿业中的矿石运输与物流优化

采矿业中的矿石运输与物流优化在采矿业中,矿石的运输与物流优化是至关重要的环节。
有效的矿石运输和物流优化方案可以提高生产效率,降低成本,减少环境影响。
本文将探讨采矿业中的矿石运输与物流优化的挑战和解决方案。
一、矿石运输的挑战采矿业中的矿石运输面临着许多挑战。
首先是矿石的体积和重量问题。
矿石通常具有较大的体积和重量,对运输工具和设备提出了较高的要求。
其次是运输距离的问题。
许多矿山位于偏远地区,需要长距离的运输。
这增加了物流成本和时间。
另外,矿石中可能含有有害物质,需要专门的运输和处理措施。
最后,采矿业中的运输需要考虑环境影响,减少对生态环境的破坏。
二、矿石运输的解决方案1.选用合适的运输工具和设备针对不同类型的矿石,选择合适的运输工具和设备是至关重要的。
对于体积较大的矿石,可以使用卡车或火车进行运输;对于体积较小的矿石,可以使用输送带或管道进行运输。
此外,科技的进步也为矿石运输带来了新的选择,例如使用自动化的无人机或无人驾驶车辆进行运输。
2.优化运输路线和运输方式在采矿业中,通常需要从矿山将矿石运输至加工厂或港口。
为了降低运输成本和时间,需要优化运输路线和运输方式。
通过使用地理信息系统(GIS)和运输规划软件,可以确定最短、最经济的运输路线,并选择合适的运输方式,如公路运输、铁路运输或水路运输。
3.建立高效的物流系统优化矿石运输不仅仅涉及到运输本身,还需要建立高效的物流系统。
物流系统应该包括供应链管理、库存管理和仓储管理等方面。
通过合理的物流规划和管理,可以降低库存成本,提高物流效率。
此外,物流系统还应考虑到环境保护和安全问题,采取相应的措施减少对环境的影响。
4.加强信息技术支持信息技术在矿石运输与物流优化中发挥着重要作用。
通过使用物联网、云计算和大数据分析等技术,可以实时监测矿石运输过程中的各项指标,进行数据分析和预测,提高运输效率和准确性。
此外,信息技术还可以用于运输路线的规划和调度,提供实时的交通信息和天气预报等信息。
- 1、下载文档前请自行甄别文档内容的完整性,平台不提供额外的编辑、内容补充、找答案等附加服务。
- 2、"仅部分预览"的文档,不可在线预览部分如存在完整性等问题,可反馈申请退款(可完整预览的文档不适用该条件!)。
- 3、如文档侵犯您的权益,请联系客服反馈,我们会尽快为您处理(人工客服工作时间:9:00-18:30)。
1 生产物流的含义
生产物流,就是指原料从进厂开始,按照一定的工艺流程,以在制品的形式经过各个车间或者各道工序进行加工,通过某些运输机械或者设备进行装卸、运输,最终实现成品出厂的过程。
2 有色金属加工企业的物流特点
有色金属加工企业的生产一般都有一些共同特点,通常体现在:
2.1 生产工艺流程复杂多变
有色金属加工往往伴随着热加工和压力加工同时进行。
在制品在生产过程中有着复杂的金属性能变化,是复杂的物理和化学变化,所以像铜、铝铸锭在生产中对温度的控制要求就很高,这就要求在制品在物流流转的过程中效率要高,尽可能减少热损失。
2.2 生产过程的连续化和自动化
随着工艺技术、机械加工能力的提高,我国有色金属加工生产的连续化和自动化也在不断提高。
企业拥有的大型设备和自动控制设备越来越多,这就要求在制品在生产的过程中运送到下一个车间、下一道工序的时间要掌握得比较准确,以实现生产的连续化、效率化。
2.3 生产过程的信息量大
有色金属加工需要原材料、中间合金、生产辅助材料同时在生产的过程中进行物料的流转和在制品形态的变化,以保证产品的按时、按量产出。
3 有色金属加工企业生产物流中存在的问题
通过对有色金属加工企业生产物流的现状进行调查与研究,发现总体上我国有色金属加工企业生产物流正逐步向现代化物流方向前进,但仍然存在诸多问题。
具体情况如下:
3.1 工艺流程
在生产中工艺流程应该是顺畅、连续的,但是在实际中,有许多车间、工序中存在很多不科学、不合理的情况。
如:工艺流程在流转中物料折返严重、物料运输的线路过于迂回、安排不合理导致运输线路过长。
这些都体现了在工艺设计中对物流没有经过充分的考虑。
3.2 工厂布置
工厂的总平面布置就是在满足各种要求的前提下,确定企业各功能分区和功能区之间互相合理位置的工作,但工厂的实际生产中存在的问题,都反映了在进行总图设计时缺乏物流的考虑。
随着企业发展,在不断改建、扩建中无法完全遵循物流合理化的原则,导致平面布置上形成一定的缺陷,物流流量大、运输方式复杂、运输不合理现象较为严重。
另外,物流基础设施落后、库存管理水平不高、生产物流管理分散化等。
这些问题都会影响到有色金属加工企业的效益和物流的效率。
4 发展有色金属加工企业合理化物流的措施
4.1 工艺流程的合理布局
有色金属加工企业应按照其自身的工艺要求,合理安排原料从进厂到成品出厂的工艺流程。
各个车间或者工序的装卸点、作业点和存贮点之间的线路物流短捷、合理,避免折返、迂回,减少不必要的运输环节,以提高整体的生产运输效率。
4.2 总平面布置中的物流
4.2.1 厂址选择。
厂址的选择应根据资源分布和消费地点,靠近主要原理、燃料基地或者产品主要销售地。
同时也要把压缩运距、力求外部运输总费用最少作为重要考虑因素。
和厂外公路、铁路、港口的连接应最短捷,具有经济合理、便捷通顺的交通运输条件。
4.2.2 总平面布置。
总平面布置的内容是根据企业的生产性质、规模和生产工艺等要求,合理布置生产车间、辅助生产设施和生活辅助设施等。
设计时要结合建厂地区的具体条件,按照原料进厂到成品出厂的整个生产工艺过程,经济合理地布置厂区内的建、构筑物,组织好厂内外的交通运输。
4.2.3 合理总平面布置对企业物流的影响。
第一,生产使用要求。
在进行有色金属加工企业总平面布置时,首先要了解企业的生产工艺流程,了解组成企业的各个建、构筑物的形式、体量和功能,合理布置建、构筑物的相对位置,尽量做到运输线路短捷通顺。
(1)在厂区中心位置布置主要生产区,同时将与生产有关的辅助设施布置在生产区周围,这样不仅使辅助设施靠近主要负荷,可以减少能耗损失,减少运输环节;(2)生产性质类似或者生产联系紧密的车间要靠近或集中布置,这样使生产工艺流程更加顺畅,同时减少相应的物料运输量,以提高生产效率;(3)运输量大的车间、仓库要结合生产工艺要求,布置在主要的干道或者货运出入口,这样就可以使物料尽快投入到流转过程中,提高运输效率;(4)人流量较大的车间及生活辅助设施区应接近主要的人流出入口布置,同时应尽量避免人、货流交叉。
第二,建、构筑物的合理布局。
工艺流程虽然是影响总平面布置的重要因素,但在合理布置厂区建、构筑物时,更要注意用地紧凑,合理划分厂区,妥善布置生活设施,这些都是影响企业总平面布置的重要因素。
第三,合理缩小建、构筑物之间间距。
厂区用地中,建、筑间距、道路等用地往往占用很大比重。
所以在满足卫生、防火、安全等要求下,应合理紧缩建、构筑物的间距。
通过这
样的布置,可以有效地减少各个车间运输车辆的行驶距离,缩短员工往返于各个车间的时间,提高全厂的生产劳动效率。
第四,厂房集中布置或加以合并。
由于生产、运输、防火、卫生及敷设管线等的要求,压缩建筑间距是有限度的。
实践证明,厂房集中布置或车间加以合并则可以更大限度地减少在制品在物料流转中的时间及费用。
车间的合并必须充分了解其性质和要求,一般同类型的车间可以考虑合并;成品库尽可能和最后一个生产工序相合并、为主车间服务的辅助生产设施用房尽可能与主车间合并。
如在有色金属加工企业的布置中,小型的有色金属加工企业就往往可以把熔铸车间和板带车间、熔铸车间和挤压车间、板带车间和箔材车间,联系紧密、生产工艺相同或相似的下游深加工车间,在设计中布置成联合大厂房。
这样的设计不仅可以使在制品在生产过程中流转的时间减少,甚至如果是熔铸工段到下一工段,如挤压工段、轧制工段,还可以有效减少热损失,节约能耗,大大提高生产效率和能源利用率。
第五,合理划分厂区,满足使用要求,留有发展余地。
平面布置中要根据生产特点及管理要求合理地划分厂区用地界线,使近期建设尽可能集中。
有些企业盲目占地,在前期规划设计时厂房过多、产品过全。
后期实施中,只有部分生产车间进行生产,生产车间又因为前期规划时布置较为分散,导致生产运行过程中,工艺流程折返,在制品在各生产车间之间的运输线路混乱。
同时也给该企业后期的扩大生产带来了不利影响,企业的未来发展是一个目标明确,但思路和过程动态变化的进程,而且由于市场的不断变化,有可能企业的产品和定位也在不断发生变化,前期规划过早、过全、过于分散,使得企业前期规划的预留场地无法使用或者制约因素较多影响使用。
第六,因地制宜、结合地形。
总平面布置既要考虑厂区所在地的地形地貌,又要满足生产运输的要求,安全可靠,经济合理。
某些地区地形高差大,给前期的建设带来一定难度,但如果在平面布置中认真思考,布置合理得当,就可能将不利因素适当地转化为有利条件,反而还会给生产带来很大便利。
如在重庆地区的某有色金属加工企业,建于坡度几乎为18%的坡地上,但该厂在设计时结合工艺特点,充分利用地形条件,使整个企业的工艺流程从高处往低处,随着部分在制品按物体自重下送和生产用量大的循环水重力自流,有效替代了部分运输设备。
同时利用高差,还可以设置高位水箱、运量大的车间按地形设置装卸货平台等。
4.2.4 厂内外合理运输方式的选择。
有色金属加工企业的物流是否合理,很大程度上就反映在企业运输线路的组织是否合理。
企业的运输设计应充分考虑工艺流程和厂区所在地的具体情况,正确选择企业运输方式和运输线路,尽可能做到运输线路短捷,没有往返和交叉现象的出现。
第一,运输方式的选择。
无论选用哪种运输方式,都要结合厂区所在地的地形条件、厂区的用地、厂内建、构筑物之间的布置关系和间距,企业的货物运输量及货物特点来考虑。
同时在进行技术经济比较和分析之后,来确定经济合理、便捷顺畅的运输方式。
运输方式一般分为道路运输、铁路运输、水路运输和其他运输方式。
道路运输是企业中采用最多的方式。
在场地平坦的地区,道路只要考虑横坡平顺连接,保证厂内运输路线的顺畅、运输道路的便捷。
但在场地起伏较大、地形复杂地区,还要考虑道路的纵坡要求,某些地区甚至还要利用当地高差使用适当的机械运输设备。
铁路运输一般用于运输量大的大型有色金属加工企业,厂内铁路应尽可能连接到厂区的边缘地带,便于原料进厂和产品出厂。
水路运输量大、费用低,但局限性也很大,一般仅限于厂外运输。
第二,合理组织货流与人流的交叉。
在进行厂内货物运输设计时,也要充分考虑人行线路。
在保证货物可以按时按点地进行正常运输时,也要充分考虑员工生产生活的安全性及便利性。
厂内运输以道路或者铁路为主,在进行总平面布置时,货流与人流的方向最好可以相反并且平行布置,同时尽可能将货运出入口与人流出入口分开,以减少相互的交叉。
对于小型企业,一般厂内道路的交叉口为平面交叉。
但是对于某些大型有色金属加工企业,如果交叉口的流量较少还可以平面交叉,如果流量过大还应该考虑立体交叉。
5 结语
本篇着重讨论了有色金属加工企业的生产物流的内容。
由于篇幅所限,一些细节问题未能在此一一讨论。
总之,生产物流系统是生产过程的重要组成部分,是联系生产制造各环节的纽带。
我国的有色金属加工企业应该更多着手于对自己企业物流现状的分析、反思,对物流管理观念的更新、借鉴和逐步引进现代的生产物流模式,积极稳妥地向物流现代化方向前进。