化纤生产过程中毛丝的形成与处理方法
毛丝的
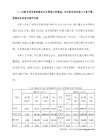
化纤生产工艺流程

化纤生产工艺流程化纤生产工艺流程是指将原材料加工制作成化纤产品的整个生产过程。
以下是一般化纤生产工艺流程的简要描述,包括聚合、纺丝、拉丝、加工等主要环节。
首先,化纤生产的第一步是聚合。
聚合是将化学原料加入反应容器中,通过化学反应产生聚合物。
聚合物的类型决定了最终产品的性质,常见的聚合物有聚酯、聚酰胺等。
在聚合过程中,控制反应条件如温度、压力和反应时间非常重要,以确保聚合物的分子量和分子量分布符合要求。
接下来是纺丝环节。
纺丝是将聚合物溶液经过加热、融化后,通过旋转的喷孔将溶液喷出,形成连续的纤维。
喷孔的形状和大小决定了纤维的直径和形态。
在纺丝过程中,要控制溶液的温度、粘度和喷丝速度等参数,以获得均匀细长的纤维。
拉丝是将纺丝得到的初纤维经过一系列的拉伸和拉丝操作,使纤维更细长、更强度更高。
首先,初纤维经过热氧化处理,增加纤维的表面活性,然后在拉伸机上进行拉伸操作,使纤维逐渐变细。
拉丝后,经过冷却和喷丝油处理,最终得到的拉丝丝线可以用来制作纺织品。
在化纤生产过程中,还有一些附加的环节,如浸渍、涂覆、染色等。
浸渍是将拉丝得到的纤维经过浸渍液处理,使其具有防静电、防水等特性。
涂覆是将薄膜状的聚合物涂覆在纤维表面,改变纤维的手感和外观。
染色则是将纤维浸泡在染料中,使其具有丰富的颜色。
最后,化纤产品还需要进行一系列的加工。
加工包括纺织、织布、印花、染整等。
纺织将纤维交错编织成纺织品,织布是将纺织品的纱线通过织机纵、横交错编织成织物。
印花是将彩色图案印刷在织物上,染整是对织物进行整理和处理,使其具有特定的品质和外观效果。
综上所述,化纤生产工艺流程包括聚合、纺丝、拉丝、加工等环节。
每个环节都有其特定的工艺和技术要求,需要精确控制参数,以获得符合要求的化纤产品。
化纤产业的发展离不开对生产工艺的不断改进和创新,并且在生产过程中要重视环境保护和安全生产。
化纤纺织品生产的生产流程

化纤纺织品生产的生产流程化纤纺织品是现代纺织品产业中重要的一部分,其生产流程经过多个环节,包括原料的准备、纺丝、织造、印染和后整理等。
下面将详细介绍化纤纺织品的生产流程。
第一步:原料的准备化纤纺织品的主要原料是合成纤维,如涤纶、尼龙、腈纶等。
这些原料通常是以原粒的形式出售,并由专门的化纤纺织品生产厂家按照一定的比例混合,以获得所需的产品性能。
此外,还需准备一定数量的染料、助剂和其他辅助材料。
第二步:纺丝纺丝是将化纤原料经过一系列加工步骤,使其变成细长的纤维的过程。
在这个过程中,原料首先被加热到高温,然后经过加压、拉伸和旋转等力的作用,使纤维逐渐变细。
最后,纤维被冷却并卷成纱线。
第三步:织造纱线经过纺织机织造成织物。
织造是将纱线穿过织机上的织眼,交错着形成布面结构的过程。
织机上的织眼数量和排列方式决定了织物的细密程度和花纹。
不同的织机还能进行附加工艺,如提花、绣花等,以形成不同的纺织品款式和质感。
第四步:印染织物可经过印染工艺进行染色或印花。
印染过程中,织物首先经过预处理,包括漂白、脱浆和酸洗等步骤,以去除杂质和增强染色效果。
然后,将织物浸泡在染料中,使颜色渗透到纤维内部,并通过热处理或化学反应固定颜色。
最后,织物通过漂洗、干燥和烫平等后处理步骤,使染色或印花的织物具有光滑、柔软和牢固的特性。
第五步:后整理在印染后,织物可能需要进行后整理以改善其外观和性能。
后整理包括整经、熨烫、压光、防缩等步骤。
整经是将织物拉直并锁定其尺寸,以防止织物在使用过程中变形。
熨烫和压光是通过加热和压力处理织物,使其表面光滑、平整。
防缩是一种特殊的整理工艺,在高温下对织物进行处理,使其具有抗缩性能,以减少使用后的变形。
以上是化纤纺织品的主要生产流程,每个环节都需要严格控制质量,以确保最终产品的平整、柔软和耐用等性能。
随着科技的进步和纺织技术的发展,化纤纺织品的生产流程也在不断创新和改进,以提高生产效率和产品质量,满足消费者不断变化的需求。
毛丝产生要因分析及解决方案PPT课件
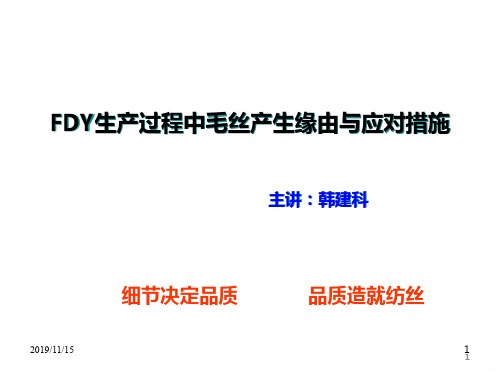
主讲:韩建科
细节决定品质
2019/11/15
品质造就纺丝
1
1
课题大纲
一、整条线大批量产生毛丝,这种情况主 要可能的原因:
二、个别位及个别锭位某个丝卷出现的毛 丝,这种情况主要可能的原因:
2019/11/15
2
一、整条线大批量产生毛丝,这种情况主 要可能的原因:
2019/11/15
9
二、个别位及个别锭位某个丝卷出现的 毛丝,这种情况主要有如下几个可能原
因
2019/11/15
10
1、组件
个别锭位上某锭组件上机质量不好(喷丝 板不清洁、组装问题,出现弱丝,细丝带 入丝束,弱丝或细丝在挂伸时断裂产生毛 丝,或过滤网被击穿。如果由于组件因素 造成的毛丝是粗长的双面毛丝。
5
3、上油方式
长丝的上油方式可选择油嘴上油和油轮上油两种方式。 采用油嘴上油可有效降低纺丝张力,但上油均匀性不好, 导致丝条在拉伸过程中张力波动大,产品染斑多;采用 油轮上油,虽然上油均匀,染色均匀性好,但纺丝张力 大,对各项细节工作要求严格,稍有不到位的地方易出 现毛丝。
我们的情况:油轮上油。
我们的现状是:通过观察发现有这样的毛丝。(要因)
2019/11/15
7
5、拉伸工艺
长丝中的加工速度一旦确定下来 ,其总加工倍数就是一个常数,若热辊拉伸 倍数过低,不但产品剩余伸长率高,而且由于拉伸张力低,丝条在热辊表面 稳定性差,容易造成产品出现染斑或绕辊断头。提高热辊的拉伸倍数 ,可克 服以上缺点,同时由于单丝表面积大,在低温下拉伸可以减少在拉伸过程中 所产生的毛丝。热辊的拉伸倍数也不宜过高,当拉伸倍数过高时,将会导致 拉伸张力过高而造成出现毛丝和断头。另外,第一组热辊的温度对染色性能 的影响比较大,采用较低的热辊温度虽然有利于染色均匀的提高,但也有可 能因为拉伸张力的提高而导致产品出现毛丝和断头。
细纱机纱线毛羽的成因及控制措施
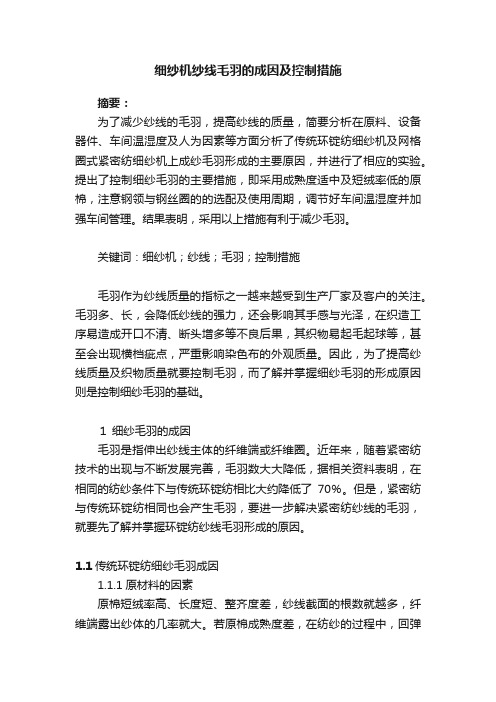
细纱机纱线毛羽的成因及控制措施摘要:为了减少纱线的毛羽,提高纱线的质量,简要分析在原料、设备器件、车间温湿度及人为因素等方面分析了传统环锭纺细纱机及网格圈式紧密纺细纱机上成纱毛羽形成的主要原因,并进行了相应的实验。
提出了控制细纱毛羽的主要措施,即采用成熟度适中及短绒率低的原棉,注意钢领与钢丝圈的的选配及使用周期,调节好车间温湿度并加强车间管理。
结果表明,采用以上措施有利于减少毛羽。
关键词:细纱机;纱线;毛羽;控制措施毛羽作为纱线质量的指标之一越来越受到生产厂家及客户的关注。
毛羽多、长,会降低纱线的强力,还会影响其手感与光泽,在织造工序易造成开口不清、断头增多等不良后果,其织物易起毛起球等,甚至会出现横档疵点,严重影响染色布的外观质量。
因此,为了提高纱线质量及织物质量就要控制毛羽,而了解并掌握细纱毛羽的形成原因则是控制细纱毛羽的基础。
1细纱毛羽的成因毛羽是指伸出纱线主体的纤维端或纤维圈。
近年来,随着紧密纺技术的出现与不断发展完善,毛羽数大大降低,据相关资料表明,在相同的纺纱条件下与传统环锭纺相比大约降低了70%。
但是,紧密纺与传统环锭纺相同也会产生毛羽,要进一步解决紧密纺纱线的毛羽,就要先了解并掌握环锭纺纱线毛羽形成的原因。
1.1传统环锭纺细纱毛羽成因1.1.1原材料的因素原棉短绒率高、长度短、整齐度差,纱线截面的根数就越多,纤维端露出纱体的几率就大。
若原棉成熟度差,在纺纱的过程中,回弹力小易扭结,也易使纤维两端伸出纱体形成毛羽。
1.1.2歪锭子或钢领直径不准确锭子与钢领、导纱钩不同心,就会形成歪气圈,纱体就会碰撞隔纱板,造成钩挂摩擦,使纤维伸出纱体形成毛羽。
由于钢领直径愈大,钢丝圈的线速度越大且运转不稳定,纱线摩擦力也越大,纱线与隔纱板间的摩擦撞击就愈厉害,从而使毛羽增加。
1.1.3钢丝圈与钢领不匹配或钢丝圈、钢领进入衰退期钢丝圈与钢领不匹配,在纺纱过程中会出现“小纱碰隔纱板,大纱擦筒管头”的现象,致使毛羽增加;在钢领稳定的状态下,钢丝圈进入衰退期后,钢丝圈由于磨损变得不光滑会对纱体钩刮,飞圈多,纱线气圈膨大,使进入纱体的纤维露出形成毛羽;在钢丝圈稳定的状态下,钢领进入衰退期后,由于钢丝圈长时间的摩擦,钢领表面形成不同程度的钢丝圈“跑道”,使钢丝圈运转不稳,造成纱体与“跑道”不断摩擦与碰撞,使毛羽增加。
DTY生产过程中网丝、毛丝产生原因及解决办法
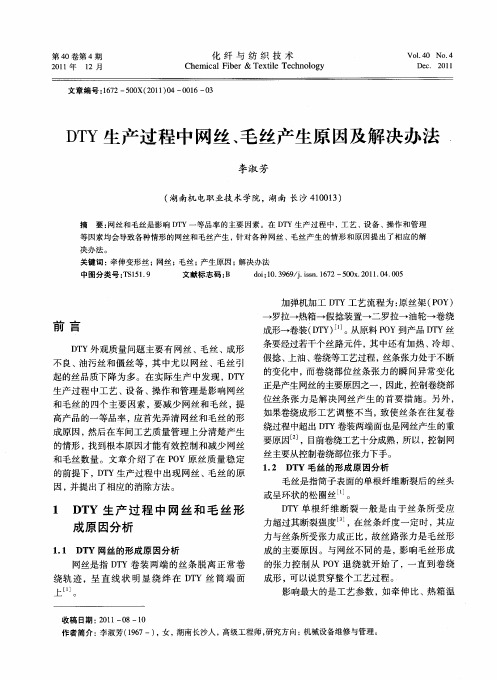
李淑芳 : T D Y生产 过程 中网丝 、毛丝产 生原因及解决办法
1 7
度、 假捻器的配置 、 喂率等 , 超 故工艺参数调整 是质量的首要保障 , 丝路张力的控制是减少毛丝 的有效 途径 。
因后即更换筒管, 并将信息反馈给筒管厂家 ; 另 外, 检修 时对筒管夹及其轴承应定期检查 , 如发
成原 因分析
1 1 DT 网丝 的形成 原 因分路张力是毛丝形
成 的主要原 因 。与 网丝 不 同 的是 , 响毛 丝形 成 影
网丝是指 D Y卷装两端 的丝条脱离正常卷 T 绕轨 迹 , 直线 状 明显 绕 绊在 D Y丝 筒端 面 呈 T
的张力控制从 P Y退绕就开始了, O 一直到卷绕
可 能 没有 放 到位 ,没 被筒 管夹 牢 牢 卡住 , 筒 管 使 与 卷 绕 黑 辊 不 平 行 ,卷 装 在 卷 绕 过 程 中跳 动 严
决办法。
关键词 : 牵伸变形丝 ;网丝 ; 毛丝 ; 生原 因 ; 产 解决办法
中图 分 类 号 :S 5 . T 1 19 文 献标 志 码 : B d i1 .99 ji n 17 o:0 3 6 /.s .62—50 .0 10 .0 s 0 x2 1.4 0 5
加弹机加 工 D Y工 艺 流程 为 : 丝 架 ( O T 原 P Y)
1 2 DT 毛丝 的形成 原 因分析 . Y
毛 丝是 指筒子 表 面的单根 纤维 断裂后 的丝 头 或 呈环 状 的松圈丝 。
1 DT 生 产 过 程 中 网 丝 和 毛 丝 形 Y
D Y单 根 纤 维 断 裂 一 般 是 由于 丝 条 所 受 应 T 力 超过 其断 裂强度 j ,在丝 条 纤 度一 定 时 , 应 其
我的化纤生产工艺

我的化纤生产工艺
化纤是一种合成纤维,通常由聚合物原料制成。
常用的化纤有聚酯纤维、尼龙纤维和聚丙烯纤维等。
化纤生产的工艺一般分为以下几个步骤:
1. 原材料准备:将合成纤维的原料聚酯、聚酰胺或聚丙烯等制成颗粒或液体状态,以备后续加工使用。
2. 聚合物合成:将原材料加入到聚合反应器中,加入催化剂和反应助剂,在高温高压下进行聚合反应,使聚合物形成。
3. 纤维拉伸成型:将聚合物通过挤出机或纺丝机挤出成纤维状,进一步拉伸、延伸和冷却,使纤维变得更加细长、均匀。
4. 纤维加工:将拉伸成型后的纤维进行涂覆、交织、组织等加工工艺,以改善纤维的性能和功能。
5. 纤维后处理:对纤维进行稳定处理,如热定型、光亮处理等,以改善纤维的外观和性能。
6. 检验和质量控制:对成品纤维进行严格的检验和质量控制,确保产品符合规
定的标准和要求。
7. 包装和存储:将成品纤维进行包装和储存,以备后续销售和使用。
需要注意的是,具体的化纤生产工艺会根据不同的纤维种类和生产厂家的要求有所差异,上述步骤仅为一般化纤生产工艺的简单介绍。
毛丝产生要因分析及解决方案讲解
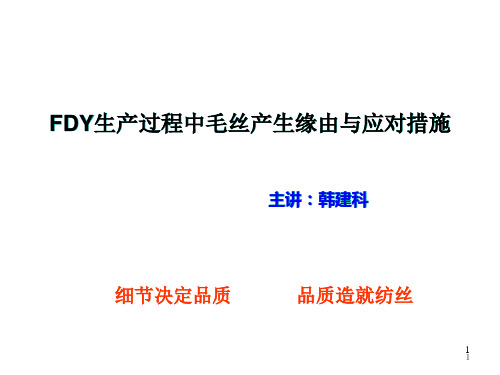
7
5、拉伸工艺
长丝中的加工速度一旦确定下来 ,其总加工倍数就是一个常数,若热辊拉伸 倍数过低,不但产品剩余伸长率高,而且由于拉伸张力低,丝条在热辊表面 稳定性差,容易造成产品出现染斑或绕辊断头。提高热辊的拉伸倍数 ,可克 服以上缺点,同时由于单丝表面积大,在低温下拉伸可以减少在拉伸过程中 所产生的毛丝。热辊的拉伸倍数也不宜过高,当拉伸倍数过高时,将会导致 拉伸张力过高而造成出现毛丝和断头。另外,第一组热辊的温度对染色性能 的影响比较大,采用较低的热辊温度虽然有利于染色均匀的提高,但也有可 能因为拉伸张力的提高而导致产品出现毛丝和断头。
9
二、个别位及个别锭位某个丝卷出现的 毛丝,这种情况主要有如下几个可能原
因
10
1、组件
个别锭位上某锭组件上机质量不好(喷丝 板不清洁、组装问题,出现弱丝,细丝带 入丝束,弱丝或细丝在挂伸时断裂产生毛 丝,或过滤网被击穿。如果由于组件因素 造成的毛丝是粗长的双面毛丝。
11
2、上油的均匀性
某锭位上由于有油垢影响上油效果丝束上 油少且不均。在拉伸过程中出现单丝断裂, 造成毛丝,这种情况通过观察丝卷就能确 定是否该原因造成的毛丝。一般表现为细 小的圈毛,同时观察两热相间有毛羽。 (要因)
我们情况是:通过调整牵伸工艺毛丝没有改变。(非要因)
8
6、标准化操作
周期管理的一些部件未能按照周期清理或者周期清理不干净,这种 情况下一般是毛丝逐渐增多,最后大批量出现。应该对周期清理的 部件(如油轮、热辊、主予网络器、瓷件、卷绕机等)进行清洗、 保养)。 日常的操作不规范,造成热辊和分丝辊表面受损使单丝断裂,出现 毛丝和断头并存的现象。 我们的现状是:大家都在做,但清洗的方法需要改进。如清洗油轮、 热辊、主予网络器、瓷件,最好用除盐水清洁效果更好,同时要清 洁主予网络器的内部喷洗。(要因)
对位芳纶生产中毛丝的产生原因及控制方法
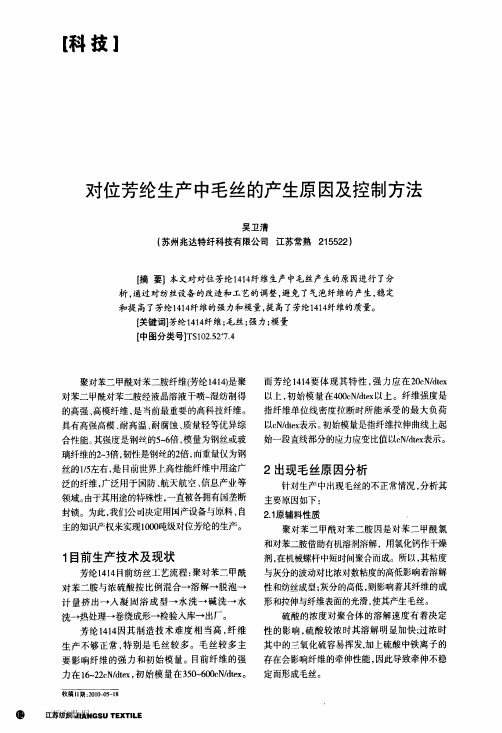
万方数据万方数据对位芳纶生产中毛丝的产生原因及控制方法作者:吴卫清作者单位:苏州兆达特纤科技有限公司,江苏常熟,215522刊名:江苏纺织A版英文刊名:JIANGSU TEXTILE年,卷(期):2010(10)本文读者也读过(10条)1.我国建成芳纶1313工业生产线[期刊论文]-高科技纤维与应用2002,27(1)2.韩霜.周雪松.郑炽嵩.胡健.于天对位芳纶纤维的槽式打浆研究[期刊论文]-纸和造纸2008,27(3)3.杨拯.吴清基.胡盼盼.刘兆峰.YANG Zheng.WU Qing-ji.HU Pan-pan.LIU Zhao-feng芳纶1414纺丝过程中聚合体的相对分子质量变化及其控制[期刊论文]-合成纤维2010,39(4)4.芳纶1414长丝及浆粕中试技术的研究与开发项目通过鉴定[期刊论文]-产业用纺织品2009,27(2)5.肖改丽.韩卿.XIAO Gai-li.HAN Qing用LiCl/极性溶剂制备芳纶浆粕纤维溶液[期刊论文]-中华纸业2008,29(24)6.王泽好.王泽君.宋威芳纶纤维的性能及在轮胎中的应用[会议论文]-20037.李金宝.张美云.吴养育.修慧娟.LI Jin-bao.ZHANG Mei-yun.WU Yang-yu.XIU Hui-juan间位与对位芳纶纤维造纸性能比较[期刊论文]-纸和造纸2005(5)8.何敏珠.毕景中.王学.王中平.宋翠艳.HE Min-zhu.BI Jing-zhong.WANG Xue.WANG Zhong-ping.SONG Cui-yan 间位芳纶低线密度纺纱技术的工艺优化研究[期刊论文]-高科技纤维与应用2010,35(4)9.唐京荣.吴艳菊芳纶织物的开发与实践[期刊论文]-江苏纺织2003(4)10.李同起.王成扬芳纶的制备及其微观结构与测试方法[期刊论文]-合成纤维工业2002,25(4)引用本文格式:吴卫清对位芳纶生产中毛丝的产生原因及控制方法[期刊论文]-江苏纺织A版 2010(10)。
化纤知识(涤纶短纤)
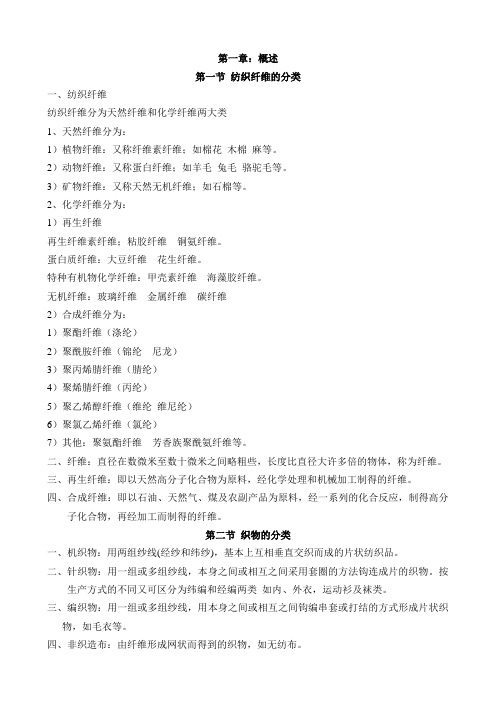
第一章:概述第一节纺织纤维的分类一、纺织纤维纺织纤维分为天然纤维和化学纤维两大类1、天然纤维分为:1)植物纤维:又称纤维素纤维;如棉花木棉麻等。
2)动物纤维:又称蛋白纤维;如羊毛兔毛骆驼毛等。
3)矿物纤维:又称天然无机纤维;如石棉等。
2、化学纤维分为:1)再生纤维再生纤维素纤维;粘胶纤维铜氨纤维。
蛋白质纤维:大豆纤维花生纤维。
特种有机物化学纤维:甲壳素纤维海藻胶纤维。
无机纤维:玻璃纤维金属纤维碳纤维2)合成纤维分为:1)聚酯纤维(涤纶)2)聚酰胺纤维(锦纶尼龙)3)聚丙烯腈纤维(腈纶)4)聚烯腈纤维(丙纶)5)聚乙烯醇纤维(维纶维尼纶)6)聚氯乙烯纤维(氯纶)7)其他:聚氨酯纤维芳香族聚酰氨纤维等。
二、纤维:直径在数微米至数十微米之间略粗些,长度比直径大许多倍的物体,称为纤维。
三、再生纤维:即以天然高分子化合物为原料,经化学处理和机械加工制得的纤维。
四、合成纤维:即以石油、天然气、煤及农副产品为原料,经一系列的化合反应,制得高分子化合物,再经加工而制得的纤维。
第二节织物的分类一、机织物:用两组纱线(经纱和纬纱),基本上互相垂直交织而成的片状纺织品。
二、针织物:用一组或多组纱线,本身之间或相互之间采用套圈的方法钩连成片的织物。
按生产方式的不同又可区分为纬编和经编两类如内、外衣,运动衫及袜类。
三、编织物:用一组或多组纱线,用本身之间或相互之间钩编串套或打结的方式形成片状织物,如毛衣等。
四、非织造布:由纤维形成网状而得到的织物,如无纺布。
五、其他特种织物:如由两组(或多组)经纱,一组纬纱用梭织方法生产三向织物,三维织物。
第三节纤维分类一、长丝:包括单丝、复丝和帘子丝。
1、单丝:指用单孔喷丝板纺制而成的一根连续单纤维。
但在实际应用中,往往也包括3---6孔喷丝板纺制的3---6根单纤维组成的少孔丝。
较粗的合成纤维单丝(直径0.02—2mm)称为鬃毛,用作绳索毛刷日用网兜鱼网等,细的用作透明丝袜等其他用品。
有光三角PA6 FDY生产中毛丝产生原因及对策
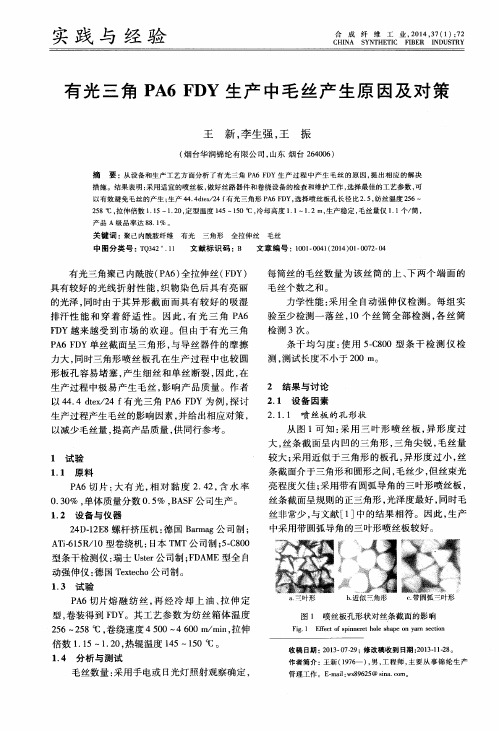
F D Y越 来越 受 到市 场 的欢 迎 。但 由 于 有 光 三 角 P A 6 F D Y单丝截 面 呈三 角 形 , 与导 丝 器 件 的摩 擦
有光 三角 聚 己内酰胺 ( P A 6 ) 全拉 伸 丝 ( F D Y)
具有 较好 的光 线 折射 性 能 , 织 物 染 色 后具 有 亮 丽
每 筒丝 的毛 丝数 量 为 该 丝 筒 的上 、 下 两 个 端 面 的 毛丝个 数之 和 。
的光 泽 , 同时 由 于其 异形 截 面而 具 有 较好 的 吸湿
王 新, 李生强 , 王 振
( 烟台华润锦纶有限公司 , 山东 烟台 2 6 4 0 0 6 )
摘 要: 从设备和生产工艺方 面分析 了有光三角 P A 6 F D Y生产过 程 中产生 毛丝 的原 因 , 提 出相应 的解决
措施。结果 表明: 采用适宜的喷丝板 , 做好丝路 器件和卷绕设备 的检查和维护工作 , 选择最佳 的工艺参数 , 可 以有效避免毛丝的产生 ; 生产 4 4 . 4 d t e x / 2 4 f 有光三角形 P A 6 F D Y, 选择喷丝板孔长径 比2 . 5 , 纺丝温度 2 5 6~ 2 5 8℃ , 拉伸倍 数 1 . 1 5~1 . 2 0, 定型温度 1 4 5~1 5 0℃ , 冷却高度 1 . 1~1 . 2 m, 生产稳定 , 毛丝量仅 1 . 1 个/ 筒,
毛 丝数 量 : 采 用手 电或 日光灯 照 射观察 确定 ,
1 试 验
关于纺丝时产生毛丝、僵丝的成因
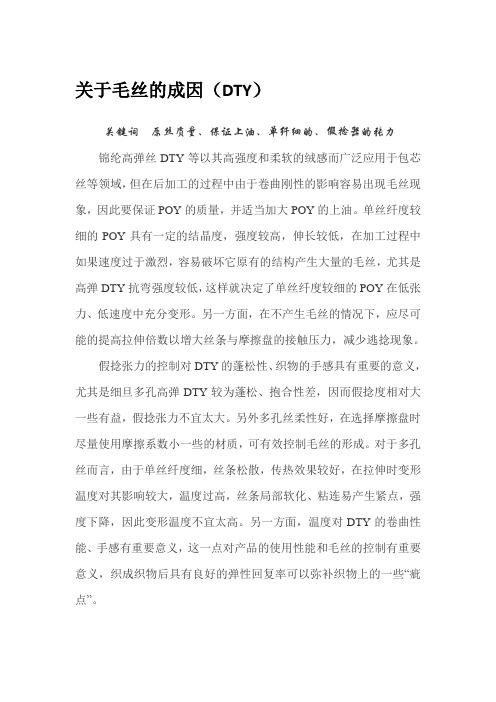
关于毛丝的成因(DTY)关键词原丝质量、保证上油、单纤细的、假捻器的张力锦纶高弹丝DTY等以其高强度和柔软的绒感而广泛应用于包芯丝等领域,但在后加工的过程中由于卷曲刚性的影响容易出现毛丝现象,因此要保证POY的质量,并适当加大POY的上油。
单丝纤度较细的POY具有一定的结晶度,强度较高,伸长较低,在加工过程中如果速度过于激烈,容易破坏它原有的结构产生大量的毛丝,尤其是高弹DTY抗弯强度较低,这样就决定了单丝纤度较细的POY在低张力、低速度中充分变形。
另一方面,在不产生毛丝的情况下,应尽可能的提高拉伸倍数以增大丝条与摩擦盘的接触压力,减少逃捻现象。
假捻张力的控制对DTY 的蓬松性、织物的手感具有重要的意义,尤其是细旦多孔高弹DTY较为蓬松、抱合性差,因而假捻度相对大一些有益,假捻张力不宜太大。
另外多孔丝柔性好,在选择摩擦盘时尽量使用摩擦系数小一些的材质,可有效控制毛丝的形成。
对于多孔丝而言,由于单丝纤度细,丝条松散,传热效果较好,在拉伸时变形温度对其影响较大,温度过高,丝条局部软化、粘连易产生紧点,强度下降,因此变形温度不宜太高。
另一方面,温度对DTY的卷曲性能、手感有重要意义,这一点对产品的使用性能和毛丝的控制有重要意义,织成织物后具有良好的弹性回复率可以弥补织物上的一些“疵点”。
关于僵丝的成因(DTY)DTY 的“僵丝”会使织物明显地产生“疵点(细节)和色斑”。
僵丝的类别及形成原因如下:(1)长片段变形不良丝即“长段僵丝”。
外部形态缺乏卷曲弹性和蓬松性,丝僵直发亮,状似原丝。
织物表面产生明显条纹,染色后为深色条斑。
形成的原因有违反操作规程,设备状况欠佳,原丝纤度不匀率高。
(2)叠捻丝。
外部形态处于松弛状态时.形成重叠捻度.以枝岔状突起,手感发硬。
织物表面发挺.染色后为僵硬的色点、色条。
形成原因如下:D/Y比太大.POY纤度不匀,或解捻张力’。
降低.使叠捻。
(3)紧捻丝即“熔融紧点。
单丝间熔融粘结形成节点,用一定外力或至拉断不易拉开,手感发硬。
高强涤纶工业丝生产中毛丝的产生原因及控制措施

实践与经验合成纤维工业,2023,46(4):83CHINA㊀SYNTHETIC㊀FIBER㊀INDUSTRY㊀㊀收稿日期:2023-01-05;修改稿收到日期:2023-06-04㊂作者简介:唐兵兵(1987 ),男,工程师,现从事涤纶工业丝的研发及生产管理工作㊂E-mail:tangbingbing@㊂高强涤纶工业丝生产中毛丝的产生原因及控制措施唐兵兵,杨㊀勇,施玉琦,刘树生(江苏恒力化纤股份有限公司,江苏苏州215226)摘㊀要:以特性黏数1.100~1.150dL /g 的高黏聚酯切片为原料,通过螺杆挤压熔融㊁热辊拉伸生产3300dtex /384f 高强涤纶工业丝,从高黏聚酯切片的特性黏数及含水率㊁组件结构㊁冷却条件㊁油剂上油方式㊁热辊温度等方面分析了生产中毛丝产生的原因,并提出了控制措施㊂结果表明:控制高黏聚酯切片的特性黏数在1.120~1.130dL /g,切片含水率低于25μg /g,有利于减少毛丝的产生;在纺丝组件分配板下方增设导流板,在缓冷区与无风区之间增设多孔板,均可减少毛丝的产生;与使用乳液油㊁油轮上油相比,使用原油㊁油嘴上油,可有效减少毛丝的产生;随着第二热辊温度的升高,毛丝降等率呈现先降低后增加的趋势,第二热辊温度为91ħ时毛丝降等率最低,为2.22%㊂关键词:聚对苯二甲酸乙二酯纤维㊀工业丝㊀毛丝㊀控制措施中图分类号:TQ342+.21㊀㊀文献标识码:B㊀㊀文章编号:1001-0041(2023)04-0083-04㊀㊀高强涤纶工业丝具有强度高㊁模量大㊁伸长小㊁耐热性能好㊁耐冲击及耐疲劳性能好等优点,广泛应用于安全带㊁海洋缆绳㊁消防水带等特殊设备中[1]㊂随着我国经济的高速发展,涤纶工业丝的需求量逐年增加,但高性能涤纶工业丝的生产对技术软件和设备硬件都有着极高的要求[2]㊂因熔体质量㊁纺丝温度㊁拉伸工艺㊁上油方式等工艺条件的影响,涤纶工业丝生产中容易产生毛丝[3]㊂毛丝是指丝条受伤呈毛绒现象或因单丝断裂丝头凸出于复丝表面,通常是检验丝筒的表面,以每个丝筒累计毛丝根数进行表征㊂圈丝(单丝未断裂)也是毛丝的一种类型,是指露于丝筒表面成弧状的单根丝㊁且长度大于2mm 的丝条,检验时也计入毛丝根数[4]㊂产品出现毛丝直接影响其后道加工工序,断头增加,形成疵点,严重影响用户使用㊂因此,解决毛丝问题是提高涤纶工业丝产品质量的关键㊂目前,国内对涤纶民用丝生产中毛丝的形成原因研究较多,这为涤纶工业丝生产中毛丝产生的原因分析和控制措施提供了借鉴㊂黄凯等[5]在涤纶工业丝生产中使用拉伸点定位器使拉伸过程更为顺利,降低了由于快速拉伸对纤维造成的毛丝㊁断头等损伤㊂李惊涛[6]提出从上油方式㊁拉伸辊排布㊁网络器压力等方面进行控制,可以减少涤纶工业丝生产中毛丝的形成㊂曹剑[7]分析了涤纶工业丝生产中毛丝的形成原因,提出及时更换组件及导丝器等可以有效减少毛丝的产生㊂李晓东[8]研究了纺丝温度㊁螺杆温度㊁组件过滤精度和冷却风等对毛丝产生的影响,适当提高纺丝温度,控制纺丝速度在3200m /min 以内,并适当提高纺丝组件的过滤精度,可以有效减少毛丝的产生㊂涤纶工业丝由于应用在特殊领域,毛丝过多不仅影响其断裂强度,还对后道加工产生影响,通常要求产品断裂强度大于8.40cN /dtex,毛丝降等率小于等于2.0%㊂作者以特性黏数1.100~1.150dL /g 的高黏聚酯切片为原料,生产3300dtex /384f 高强涤纶工业丝,从工艺和设备两方面分析了生产中毛丝产生的原因,并提出了控制措施㊂1㊀试验1.1㊀原料高黏聚酯切片:特性黏数1.100~1.150dL /g,熔点(261.0ʃ2.0)ħ,端羧基含量(13.0ʃ3.0)mol /t,二甘醇质量分数(0.92ʃ0.10)%,江苏恒力化纤股份有限公司生产;涤纶工业丝油剂:日本竹本公司生产㊂1.2㊀主要设备及仪器纺丝及卷绕设备:包括纺丝箱体㊁冷却风箱㊁ATi-412HR/4型卷绕机,日本TMT公司制;HL-IND-001型全自动外检系统:东华大学制;SF-1型微量水分测定仪:常州八方力士纺织仪器有限公司制㊂1.3㊀高强涤纶工业丝的生产以特性黏数1.100~1.150dL/g的高黏聚酯切片为原料,通过螺杆挤压熔融㊁五辊热拉伸生产3300dtex/384f高强涤纶工业丝,生产工艺流程见图1,纺丝工艺参数见表1㊂聚酯切片预结晶ң预加热ң固相增黏ңң氮气输送螺杆挤出ң纺丝箱体ң计量泵ңң纺丝组件无风区ң冷却ң上油ңң预网络拉伸定型ң主网络ң卷绕成型ңң检验包装图1㊀高强涤纶工业丝生产工艺流程Fig.1㊀Flow chart of high-strength polyester industrial yarn表1㊀纺丝工艺参数Tab.1㊀Spinning process parameters项目参数螺杆温度/ħ285~310纺丝温度/ħ290~305缓冷区温度/ħ290~310冷却风速度/(m㊃s-1)0.45~0.60纺丝速度/(m㊃min-1)3000~3100主网络压力/MPa0.20~0.30含油率/%0.5~0.6拉伸倍数 5.5~6.21.4㊀分析与测试特性黏数:按照GB/T14190 2017‘纤维级聚酯切片(PET)试验方法“,采用乌氏黏度计测定㊂含水率:按照GB/T14190 2017‘纤维级聚酯切片(PET)试验方法“,采用SF-1型微量水分测定仪测定㊂毛丝降等率:按照GB/T16604 2017‘涤纶工业丝“外观要求进行判定,统计一段时间内的毛丝降等丝饼数量和满卷丝饼数量,毛丝降等丝饼数量占满卷丝饼数量的百分数为毛丝降等率㊂2㊀结果与讨论2.1㊀原料对毛丝的影响2.1.1㊀聚酯切片特性黏数对毛丝的影响聚酯切片特性黏数较低,熔体黏度低,拉伸时容易出现单丝拉断,产生毛丝甚至断头;聚酯切片特性黏数过大,熔体黏度高,流动性变差,熔体在出喷丝板时膨化率较大,容易产生注头丝,断头率增加㊂由表2可知:在其他工艺条件一定时,当聚酯切片特性黏数为1.100dL/g时,毛丝降等率为12.26%;聚酯切片特性黏数提高到1.123dL/g时,毛丝降等率降低至8.92%,毛丝现象有所改善;继续提高聚酯切片黏数至1.138~1.150dL/g 时,毛丝降等率反而升高至12.0%㊂因此,涤纶工业丝生产中聚酯切片特性黏数控制在1.120~ 1.130dL/g较为合适㊂聚酯切片特性黏数提高后,相应地需要提高螺杆纺丝温度,使熔体流动性变好,提高可纺性㊂实际生产中,需要保证聚酯切片质量的稳定性,选择合适的纺丝温度㊂表2㊀聚酯切片特性黏数对毛丝降等率的影响Tab.2㊀Effect of intrinsic viscosity of polyester chipon broken filament rate特性黏数/(dL㊃g-1)端羧基含量/(mol㊃t-1)毛丝降等率/%1.10014.612.261.11213.511.181.12313.28.921.13813.310.021.15012.312.002.1.2㊀聚酯切片含水率对毛丝的影响聚酯分子链中含有大量的酯键和端羧基,高温环境下受到水分子和端羧基的影响,聚酯分子很容易发生逆反应,导致分子链断裂,纤维经热辊拉伸时单丝易拉断,产生毛丝㊂从图2可以看出:在其他工艺条件一定时,聚酯切片含水率小于25μg/g时,毛丝降等率在2.00%~2.20%;当含水率超过25μg/g时,毛丝降等率迅速上升,含水率为30μg/g时毛丝降等率达到3.29%,且断头增多,可纺性变差㊂因此,在生产过程中应控制聚酯切片含水率小于25μg/g㊂图2㊀聚酯切片含水率与毛丝降等率的关系Fig.2㊀Relationship between moisture contentof polyester chip and broken filament rate48㊀合㊀成㊀纤㊀维㊀工㊀业㊀㊀㊀㊀㊀㊀㊀㊀㊀㊀㊀㊀㊀㊀2023年第46卷2.2㊀组件结构对毛丝的影响该生产装置配套纺丝组件由原设备供应商提供,其结构主要包括壳体㊁紧固环㊁上盖㊁压盖㊁分配板㊁喷丝板等㊂在压盖与分配板之间有上下两层滤网,起到过滤作用;分配板与喷丝板之间放置单层网片;熔体进入纺丝组件,通过上盖㊁压盖进入分配板,从孔深65mm㊁直径2.5mm的分配板孔道流出后经过单层网片迅速分配到直径为190~200mm的喷丝板上㊂分配板孔道长径比大,熔体在孔道中存储的能量不能及时释放,熔体无法均匀分配到喷丝板板面上,从而导致喷丝板出丝不匀,毛丝㊁断头增加[9]㊂为了改善熔体的流动性,在分配板下方增设导流板,导流板上下设有一定的角度,使经过分配板孔道的熔体存储的能量能够充分释放,同时也对熔体起到再混合重新分配的作用㊂从表3可知,在其他工艺条件一定时,通过使用增设导流板后的组件,在考察生产周期28d内,生产的涤纶工业丝毛丝降等率下降明显,未加导流板时毛丝降等率为4.63%,增设导流板后毛丝降等率为3.21%,毛丝降等率明显降低㊂表3㊀组件结构对毛丝降等率的影响Tab.3㊀Effect of spin pack structure on broken filament rate 组件结构生产时间/d毛丝降等率/%未加导流板28 4.63增设导流板28 3.212.3㊀无风区多孔板对毛丝的影响涤纶工业丝单丝线密度较大,丝条内部热量不容易传导至表面,纤维出喷丝板冷却时容易产生 皮芯 结构,不利于纤维的进一步拉伸和热定型,因此,在生产涤纶工业丝时使用缓冷区㊁无风区㊁侧吹风冷却区等多级冷却结构,从而减少丝条 皮芯 结构的产生,使单根丝束冷却更加均匀,最大限度降低初生纤维的取向和结晶,以利于拉伸倍数的提高,从而获得高强力㊁高质量的纤维[10]㊂为了进一步改善冷却效果,在缓冷区与无风区之间增设多孔板,增设多孔板主要有以下作用:(1)避免纺丝成型过程中紊流的产生,降低黏丝㊁并丝发生的可能性,以减少毛丝;(2)降低初生纤维之间取向㊁结晶不同引起的内应力差异,进而降低由此引起的拉伸不均匀程度;(3)可有效减少黏附在喷丝板表面的单体和低聚物,提高熔体剥离喷丝板能力,减少熔体黏附在喷丝板表面形成断丝的可能性㊂从表4可知,在其他工艺条件一定时,与未增加多孔板相比,使用多孔板后毛丝降等率明显降低,在考察生产周期5d内,毛丝降等率从5.33%降至3.96%㊂因此,在涤纶工业丝的生产中,为了减少毛丝的产生,可在缓冷区与无风区之间增设多孔板㊂表4㊀多孔板对毛丝降等率的影响Tab.4㊀Effect of perforated plate on broken filament rate多孔板生产时间/d毛丝降等率/%无5 5.33有5 3.962.4㊀油剂及上油方式对毛丝的影响涤纶工业丝油剂应具备以下条件[11-13]: (1)良好的匀附性,易于在纤维表面吸附并迅速铺展开;(2)优良的平滑性,使纤维易于拉伸,减少毛丝㊁断头;(3)优良的抱合性,使丝束集束性好㊂原油具有较高的表面张力,在丝条表面形成的油膜不易破损,从而降低丝条与金属表面㊁丝条与丝条的动摩擦系数,单丝不易被拉断㊂乳液油中含有大量的水分,丝束经过高温热辊时,水分蒸发导致油剂中不同组分发生共蒸发现象,油膜容易破裂,同时由于水分的蒸发,丝束抖动加剧,丝与丝之间碰撞增加,更容易产生毛丝㊂从表5可知,使用乳液油㊁油轮上油方式时毛丝降等率为9.31%,而使用原油㊁油嘴上油方式时毛丝降等率为1.98%,毛丝降等率大幅度降低㊂因此,在涤纶工业丝的生产中,选择使用原油㊁油嘴上油方式可有效减少毛丝的产生㊂表5㊀油剂及上油方式对毛丝降等率的影响Tab.5㊀Effect of spinning finish and oiling methodon broken filament rate油剂㊀㊀上油方式毛丝降等率/%乳液油油轮9.31原油油嘴 1.982.5㊀第二热辊温度对毛丝的影响涤纶工业丝生产中采用五辊热拉伸定型工艺,其中第二热辊的作用是将丝束加热到玻璃化转变温度以上,以便于在第三热辊开始拉伸㊂第二热辊温度太低,丝束在离开第二热辊时未能充分预热,拉伸时会出现 冷拉伸 ,导致单丝拉伸不匀,出现弱丝,后续拉伸时会被拉断出现毛丝;第二热辊温度过高,丝束在第二热辊上过热,会导致拉伸点前移,丝束在第二热辊上出现部分拉伸,离开第二热辊后受到第三热辊的高倍拉伸时就会导致拉伸不匀的发生㊂因此,选择合适的第二热58第4期㊀㊀㊀㊀㊀㊀㊀㊀㊀㊀㊀唐兵兵等.高强涤纶工业丝生产中毛丝的产生原因及控制措施辊温度对丝束的拉伸很重要㊂从表6可知:随着第二热辊温度的升高,毛丝降等率呈现先降低后增加的趋势;第二热辊温度为85ħ时,毛丝降等率为3.51%;当第二热辊温度升高至91ħ时,毛丝降等率最低,为2.22%;继续升高第二热辊温度,毛丝反而增加,第二热辊温度为97ħ时,毛丝降等率为3.10%㊂因此,在涤纶工业丝的生产中,应合理选择第二热辊温度,控制第二热辊温度在91ħ左右,毛丝较少㊂表6㊀第二热辊温度对毛丝降等率的影响Tab.6㊀Effect of second hot roller temperature onbroken filament rate第二热辊温度/ħ毛丝降等率/%85 3.5188 3.0291 2.2294 2.7397 3.103㊀结论a.在高强涤纶工业丝生产中,控制高黏聚酯切片特性黏数在1.120~1.130dL/g,含水率小于25μg/g,有利于降低毛丝降等率㊂b.高强涤纶工业丝生产中,在纺丝组件分配板下方增加导流板,在缓冷区与无风区之间增设多孔板,均可减少毛丝的产生,降低毛丝降等率㊂c.高强涤纶工业丝生产中,采用原油㊁油嘴上油,控制第二热辊温度为91ħ左右,毛丝较少,毛丝降等率大幅度降低㊂参㊀考㊀文㊀献[1]㊀王玉萍.涤纶工业丝行业发展现状及应用研究[J].合成纤维,2011,40(9):1-6.[2]㊀崔再治,牛家祥,姜晓江.涤纶工业丝的生产[J].聚酯工业,2002,15(3):21-22,35.[3]㊀张荣根,冯培,刘大双,等.涤纶工业长丝毛丝在线检测系统的研究[J].纺织学报,2022,43(4):153-159. [4]㊀中国国家标准化管理委员会.涤纶工业长丝:GB/T166042017[S].北京:中国标准出版社,2017:1-28. [5]㊀黄凯,程嘉祺,张金德.高性能聚酯工业丝的生产工艺研究[J].合成纤维,2005,34(1):25-28.[6]㊀李惊涛.国产涤纶工业丝拉伸卷绕设备及工艺浅析[J].纺织机械,2013(3):18-24.[7]㊀曹剑.涤纶工业长丝生产中毛丝的形成原因及解决措施[J].化纤与纺织技术,2021,50(12):43-45. [8]㊀李晓东.浅析涤纶工业长丝生产过程中毛丝形成的原因及解决措施[J].黑龙江纺织,2007(2):12-13,15. [9]㊀张烨,王鹏,唐兵兵,等.一种高强涤纶工业丝纺丝组件:114921859B[P].2022-11-22.[10]王丽丽,李文刚,汤方明,等.一种高强高模低缩涤纶工业丝的制造方法:102797054B[P].2014-10-01. [11]杨玉敏,张瑞波.乳化液型涤纶工业丝油剂的性能及应用[J].合成纤维工业,2011,34(2):54-56. [12]陶义清,丁雷,戴泽青,等.涤纶工业丝油剂的研制和性能评测[J].精细石油化工进展,2021,22(5):10-13. [13]张瑞波,杨玉每,贺哓江,等.涤纶工业丝用油剂单体的耐热性能研究[J].合成纤维工业,2010,33(3):39-41.Reasons and control of broken filaments in high-strengthpolyester industrial yarnTANG Bingbing,YANG Yong,SHI Yuqi,LIU Shusheng(Jiangsu Hengli Chemical Fiber Co.,Ltd.,Suzhou215226)Abstract:Using a high-viscosity polyester chip with an intrinsic viscosity of1.100-1.150dL/g as raw material,3300dtex/ 384f high-strength polyester industrial yarn was produced through screw extrusion melting and hot roller drawing.The reasons for the formation of broken filaments during production were analyzed from the aspects of the intrinsic viscosity and moisture content of high-viscosity polyester chips,spin pack structure,quenching conditions,oiling method and hot roller temperature,and the control measures were proposed.The results showed that it was conducive to reducing the formation of broken filaments when the intrinsic viscosity of the high-viscosity polyester chip was controlled at1.120-1.130dL/g and the moisture content lower than25μg/g;and the formation of broken filaments can be also depressed by adding a guide plate under the distribution plate of the spin pack and a perforated plate between the annealing zone and the windless zone;compared with emulsion and tanker oiling method, crude oil and nozzle oiling method can effectively reduce the production of broken filaments;and the broken filament rate showed a downward and then upward trend as the second hot roller temperature increased and was minimized as2.22%when the second hot roller temperature was91ħ.Key words:polyethylene terephthalate fiber;industrial yarn;broken filament;control measures68㊀合㊀成㊀纤㊀维㊀工㊀业㊀㊀㊀㊀㊀㊀㊀㊀㊀㊀㊀㊀㊀㊀2023年第46卷。
化纤生产工艺流程

化纤生产工艺流程
《化纤生产工艺流程》
化纤是指以天然或合成高分子化合物为原料,通过化学加工生产而成的纤维。
化纤生产工艺流程是一个复杂的过程,涉及到许多步骤和工艺。
以下是化纤生产的一般工艺流程:
1. 原料准备:化纤的原料可以是天然纤维或者合成高分子化合物,如聚脂纤维、聚酯纤维、聚酰胺纤维等。
在生产过程中,要先将原料进行准备和储存。
2. 聚合反应:对于合成纤维,首先要进行聚合反应,即将单体分子通过聚合反应组装成高分子链。
这个过程需要一定的催化剂和稳定剂来控制反应的速度和过程。
3. 纺丝:聚合后的高分子物质需要通过纺丝机进行拉伸,使其变得柔软并成为纤维。
这是将高分子物质转化成纤维的重要步骤。
4. 固化处理:纺丝后的纤维要进行固化处理,即使其具备一定的机械强度和耐热性,以便后续的加工和使用。
5. 牵伸加工:对于特殊要求的纤维,还需要进行牵伸加工,使其具备更好的物理性能。
6. 染色加工:完成纤维的基本加工后,还需要进行染色、整理等加工过程,以满足市场的需求。
7. 成品生产:最后,将处理好的纤维经过纺纱、织造等工艺,制成成品纺织品,供人们使用。
化纤生产的工艺流程是一个复杂且多步骤的过程,需要在每一个环节都保持高度的注意和严格的操作,以确保纤维的质量和性能。
同时,对于不同种类的化纤,其生产工艺也会有所不同,需要根据具体的原料和要求进行调整。
化纤作为纺织品中非常重要的一种原料,其生产工艺流程的优化和改进将对行业的发展起到重要的作用。
光扁平FDY生产中毛丝形成的原因及对策

轮上油。 采用油嘴上油可有效降低纺丝张力, 但上 油的均匀性不好, 导致丝条在拉伸过程中张力波动 大, 产品染斑多; 采用油轮上油, 虽然上油均匀、 染色均匀性好, 但纺丝张力大, 从而使毛丝和断头 率增加, 使消耗增加, 满卷率下降。 权衡利弊, 本
实验采用油轮上油, 并且通过调整油轮转速和丝条 与油轮包角的大小来有效地降低纺丝张力, 减少毛 丝和断头的出 现。 2 . 拉伸工艺 .5 2
LU n-n LU g I Y gu, Fn o j I a d mc E gH nn i e ni en, t 4 11 (etf msy C e i l . ua I t toEg er gXag n 10) D poC e ira h a n , - h t n n t f n i i a 1 su n A sat Ra n o f z m tn i bgt PT Y outn r d cs d h ees btc e os u f ao drg h ft F p dco w e us . e c o r : s f o i un r l E D r i e i e T f t f z r i a s f si e t i ad cs pr e r h d i cni n si i t pru , on cni n p nr dsn p e a m t sc a rn odi , n g e t e olg di , n e eg n r s a e u s g t o y o p n e a rc i o t n m o d wn t pru ad wn rio poutn csw raa zdI apie ot t s t l r i e e t e d i ao r co p e e nl e. s t ut t ua e a g a r n r g n d i r s e y m a t o t o d h h ib w n a e p c sl ao, e si i t pru , et lg pru ad t a d wn ri ad r r tl tn h hr n g e tecrccon t e te o i l i ao e ai i i y g g p n e ar o n m r o i e a r n pm r g n m a t t pru s u b s io efr ce f m tn e e te l e n r e u f z ao. m a r h d e r o o t d d u o i z r Ky d: fr fter , , n ap cs ew r ft , dg ef zt hi l e o sl i el - e u e c r s a b a z c o
化纤的工艺与生产工艺

化纤的工艺与生产工艺
化纤的工艺包括聚合、纺领、织造、印染等环节。
下面是化纤的工艺流程:
1.聚合:将单体(如聚酯、尼龙、丙烯等)在催化剂及其他条件下,经过化学反应形成聚合物。
2.纺领:将聚合物经过拉伸、加热、冷却等步骤形成长而细的丝状物,即预加工。
3.织造:将预加工后的丝状物进行纵、横的交叉编织,形成布匹。
4.印染:将布匹经过印刷和染色等加工,形成各种色彩和花型。
化纤的生产工艺包括原材料选用、工艺控制、质量检验等方面。
具体包括以下环节:
1.原材料选用:选用质量好、稳定的单体及其他辅助材料(如催化剂、溶剂等)。
2.工艺控制:通过控制加工温度、时间、压力、转速等工艺条件,确保化纤的物理和化学性能达到设计要求。
3.质量检验:对化纤生产过程中的原材料、半成品和成品进行各种指标的检测,保证化纤的质量符合国家标准及行业规范。
化纤生产过程中毛丝的形成与处理方法综述
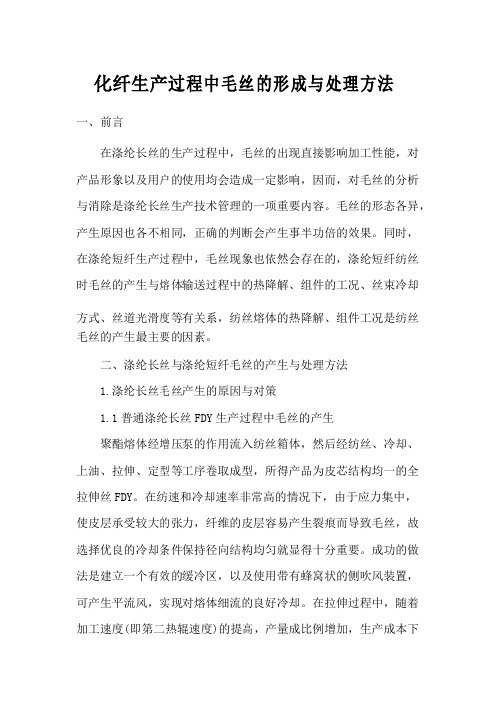
化纤生产过程中毛丝的形成与处理方法一、前言在涤纶长丝的生产过程中,毛丝的出现直接影响加工性能,对产品形象以及用户的使用均会造成一定影响,因而,对毛丝的分析与消除是涤纶长丝生产技术管理的一项重要内容。
毛丝的形态各异,产生原因也各不相同,正确的判断会产生事半功倍的效果。
同时,在涤纶短纤生产过程中,毛丝现象也依然会存在的,涤纶短纤纺丝时毛丝的产生与熔体输送过程中的热降解、组件的工况、丝束冷却方式、丝道光滑度等有关系,纺丝熔体的热降解、组件工况是纺丝毛丝的产生最主要的因素。
二、涤纶长丝与涤纶短纤毛丝的产生与处理方法1.涤纶长丝毛丝产生的原因与对策1.1普通涤纶长丝FDY生产过程中毛丝的产生聚酯熔体经增压泵的作用流入纺丝箱体,然后经纺丝、冷却、上油、拉伸、定型等工序卷取成型,所得产品为皮芯结构均一的全拉伸丝FDY。
在纺速和冷却速率非常高的情况下,由于应力集中,使皮层承受较大的张力,纤维的皮层容易产生裂痕而导致毛丝,故选择优良的冷却条件保持径向结构均匀就显得十分重要。
成功的做法是建立一个有效的缓冷区,以及使用带有蜂窝状的侧吹风装置,可产生平流风,实现对熔体细流的良好冷却。
在拉伸过程中,随着加工速度(即第二热辊速度)的提高,产量成比例增加,生产成本下降,并且染色均匀性有所提高。
但是加工速度过高时,产品断头和毛丝随之增加,因此必须权衡确定合适的加工速度。
如果拉伸不足而使张力低下,使丝条的摇动幅度增大,也会造成毛丝和断头,但张力过高会对丝饼成型及退绕产生负作用。
从油剂的附着性与纤维起毛的关系来讲,维持较高的油剂乳液的浓度及丝质含油率,可使得纤维的毛丝减少,但也要防止油剂浓度过高而导致油剂渗透性下降而使得丝质降低。
FDY上油方式可选择油嘴上油和油轮上油。
采用油嘴上油可有效降低纺丝张力,但上油的均匀性不好,导致丝条在拉伸过程中张力波动大,产品染斑多。
采用油轮上油,虽然上油均匀、染色均匀性好,但纺丝张力大,从而使毛丝和断头率增加,使消耗增加,满卷率下降。
化纤生产工艺流程
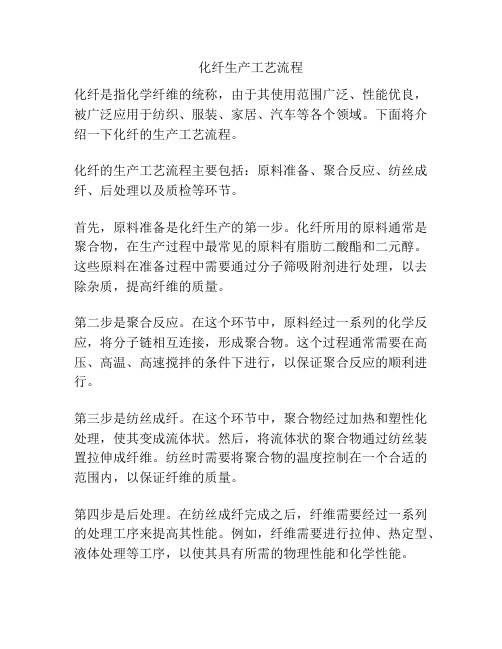
化纤生产工艺流程化纤是指化学纤维的统称,由于其使用范围广泛、性能优良,被广泛应用于纺织、服装、家居、汽车等各个领域。
下面将介绍一下化纤的生产工艺流程。
化纤的生产工艺流程主要包括:原料准备、聚合反应、纺丝成纤、后处理以及质检等环节。
首先,原料准备是化纤生产的第一步。
化纤所用的原料通常是聚合物,在生产过程中最常见的原料有脂肪二酸酯和二元醇。
这些原料在准备过程中需要通过分子筛吸附剂进行处理,以去除杂质,提高纤维的质量。
第二步是聚合反应。
在这个环节中,原料经过一系列的化学反应,将分子链相互连接,形成聚合物。
这个过程通常需要在高压、高温、高速搅拌的条件下进行,以保证聚合反应的顺利进行。
第三步是纺丝成纤。
在这个环节中,聚合物经过加热和塑性化处理,使其变成流体状。
然后,将流体状的聚合物通过纺丝装置拉伸成纤维。
纺丝时需要将聚合物的温度控制在一个合适的范围内,以保证纤维的质量。
第四步是后处理。
在纺丝成纤完成之后,纤维需要经过一系列的处理工序来提高其性能。
例如,纤维需要进行拉伸、热定型、液体处理等工序,以使其具有所需的物理性能和化学性能。
最后一步是质检。
在化纤生产的最后阶段,对纤维进行品质检验和质量控制,确保其达到规定的标准。
质检通常包括纤维的外观检查、物理性能测试、化学性能测试等。
总结而言,化纤生产的工艺流程包括原料准备、聚合反应、纺丝成纤、后处理以及质检。
这些步骤相互关联,每一个环节都非常关键,决定了最终产品的质量和性能。
随着科技的不断发展,化纤的生产工艺也在不断进步,使得化纤的质量和性能得到了更大的提升。
蚕吐丝缫丝纺纱化纤制造流程
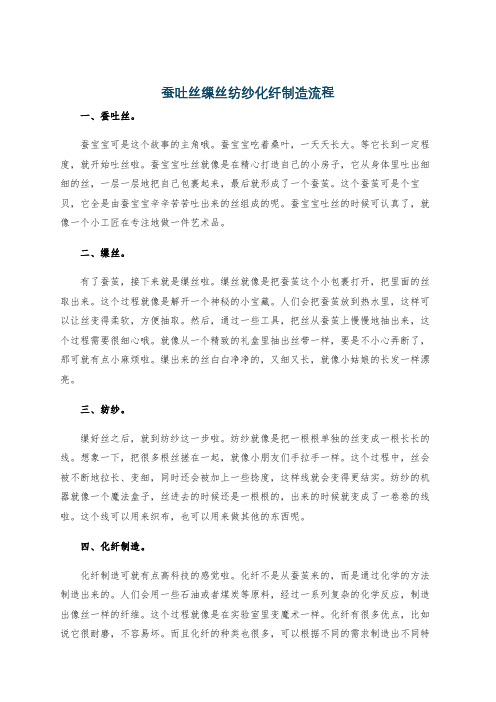
蚕吐丝缫丝纺纱化纤制造流程一、蚕吐丝。
蚕宝宝可是这个故事的主角哦。
蚕宝宝吃着桑叶,一天天长大。
等它长到一定程度,就开始吐丝啦。
蚕宝宝吐丝就像是在精心打造自己的小房子,它从身体里吐出细细的丝,一层一层地把自己包裹起来,最后就形成了一个蚕茧。
这个蚕茧可是个宝贝,它全是由蚕宝宝辛辛苦苦吐出来的丝组成的呢。
蚕宝宝吐丝的时候可认真了,就像一个小工匠在专注地做一件艺术品。
二、缫丝。
有了蚕茧,接下来就是缫丝啦。
缫丝就像是把蚕茧这个小包裹打开,把里面的丝取出来。
这个过程就像是解开一个神秘的小宝藏。
人们会把蚕茧放到热水里,这样可以让丝变得柔软,方便抽取。
然后,通过一些工具,把丝从蚕茧上慢慢地抽出来,这个过程需要很细心哦。
就像从一个精致的礼盒里抽出丝带一样,要是不小心弄断了,那可就有点小麻烦啦。
缫出来的丝白白净净的,又细又长,就像小姑娘的长发一样漂亮。
三、纺纱。
缫好丝之后,就到纺纱这一步啦。
纺纱就像是把一根根单独的丝变成一根长长的线。
想象一下,把很多根丝搓在一起,就像小朋友们手拉手一样。
这个过程中,丝会被不断地拉长、变细,同时还会被加上一些捻度,这样线就会变得更结实。
纺纱的机器就像一个魔法盒子,丝进去的时候还是一根根的,出来的时候就变成了一卷卷的线啦。
这个线可以用来织布,也可以用来做其他的东西呢。
四、化纤制造。
化纤制造可就有点高科技的感觉啦。
化纤不是从蚕茧来的,而是通过化学的方法制造出来的。
人们会用一些石油或者煤炭等原料,经过一系列复杂的化学反应,制造出像丝一样的纤维。
这个过程就像是在实验室里变魔术一样。
化纤有很多优点,比如说它很耐磨,不容易坏。
而且化纤的种类也很多,可以根据不同的需求制造出不同特性的纤维。
比如说有的化纤很柔软,适合做衣服;有的化纤很结实,就可以用来做工业用品。
从蚕宝宝吐丝到最后的化纤制造,这整个流程就像是一个充满惊喜的旅程。
每一个环节都很重要,都离不开人们的智慧和努力。
就像我们生活中的很多事情一样,都是一环扣一环的,缺了哪一个都不行呢。
- 1、下载文档前请自行甄别文档内容的完整性,平台不提供额外的编辑、内容补充、找答案等附加服务。
- 2、"仅部分预览"的文档,不可在线预览部分如存在完整性等问题,可反馈申请退款(可完整预览的文档不适用该条件!)。
- 3、如文档侵犯您的权益,请联系客服反馈,我们会尽快为您处理(人工客服工作时间:9:00-18:30)。
化纤生产过程中毛丝的形成与处理方法一、前言在涤纶长丝的生产过程中,毛丝的出现直接影响加工性能,对产品形象以及用户的使用均会造成一定影响,因而,对毛丝的分析与消除是涤纶长丝生产技术管理的一项重要容。
毛丝的形态各异,产生原因也各不相同,正确的判断会产生事半功倍的效果。
同时,在涤纶短纤生产过程中,毛丝现象也依然会存在的,涤纶短纤纺丝时毛丝的产生与熔体输送过程中的热降解、组件的工况、丝束冷却方式、丝道光滑度等有关系,纺丝熔体的热降解、组件工况是纺丝毛丝的产生最主要的因素。
二、涤纶长丝与涤纶短纤毛丝的产生与处理方法1.涤纶长丝毛丝产生的原因与对策1.1普通涤纶长丝FDY生产过程中毛丝的产生聚酯熔体经增压泵的作用流入纺丝箱体,然后经纺丝、冷却、上油、拉伸、定型等工序卷取成型,所得产品为皮芯结构均一的全拉伸丝FDY。
在纺速和冷却速率非常高的情况下,由于应力集中,使皮层承受较大的力,纤维的皮层容易产生裂痕而导致毛丝,故选择优良的冷却条件保持径向结构均匀就显得十分重要。
成功的做法是建立一个有效的缓冷区,以及使用带有蜂窝状的侧吹风装置,可产生平流风,实现对熔体细流的良好冷却。
在拉伸过程中,随着加工速度(即第二热辊速度)的提高,产量成比例增加,生产成本下降,并且染色均匀性有所提高。
但是加工速度过高时,产品断头和毛丝随之增加,因此必须权衡确定合适的加工速度。
如果拉伸不足而使力低下,使丝条的摇动幅度增大,也会造成毛丝和断头,但力过高会对丝饼成型及退绕产生负作用。
从油剂的附着性与纤维起毛的关系来讲,维持较高的油剂乳液的浓度及丝质含油率,可使得纤维的毛丝减少,但也要防止油剂浓度过高而导致油剂渗透性下降而使得丝质降低。
FDY上油方式可选择油嘴上油和油轮上油。
采用油嘴上油可有效降低纺丝力,但上油的均匀性不好,导致丝条在拉伸过程中力波动大,产品染斑多。
采用油轮上油,虽然上油均匀、染色均匀性好,但纺丝力大,从而使毛丝和断头率增加,使消耗增加,满卷率下降。
为此,可采用油轮上油,并且通过调整油轮转速和丝条与油轮包角的大小来有效地降低纺丝力,减少毛丝和断头的出现。
1.2异形涤纶长丝FDY生产过程中毛丝的产生实践中经常发现异形涤纶长丝生产过程中毛丝和断头现象比较普遍,其中喷丝板的设计是制造异形纤维的关键部件。
采用哑铃形孔形的喷丝板可有效减小熔体挤出胀大的不均匀性,并且可有效提高异形度。
异型丝的生产对切片的干燥均匀性和含水率的要求均比常规纤维要高,因此理论上应该强化干燥条件。
预结晶应采用较缓和的条件,适当降低预结晶温度,延长切片在预结晶中的停留时间,使切片达到一定的结晶度以确保切片在干燥过程中不发生粘连。
如果干切片含水率过高,或干、湿切片的粘度降过大,都会引起纺丝过程中毛丝和断头现象的增加。
纺丝温度对于异形丝加工性能影响较大,选择合适的纺丝温度比如293℃较为理想,因为既可兼顾异形度,同时毛丝和断头的产生相对较少。
冷却成形的条件是影响异形度和后拉伸产品质量的关键参数,冷却越快,异形度越高。
但是由于高异形度和急剧冷却可能产生的皮芯结构,使纤维在拉伸过程中容易出现毛丝和断头,同时使染色性能变差,因此,为减少毛丝和断头,在兼顾异形度的前提下应尽量采用缓和的冷却条件。
1.3涤纶低弹丝DTY生产过程中毛丝的产生在涤纶低弹丝的加工过程中,假捻器是牵伸假捻机的心脏,其材质对假捻效果和丝条的质量影响较大。
通常摩擦片的材质有硬质和软质两大类,硬质盘常用全瓷盘、等离子喷涂瓷盘等,软质盘有聚氨酯盘(简称PU盘),硬质盘虽然使用寿命长,但打滑系数大,假捻效果不如软质盘。
在生产中,由于瓷盘对丝的损伤较大,使产品的毛丝较多。
通过PU盘与瓷盘的有机组合,可有效地解决毛丝问题,产品质量得以提高。
原料采用涤纶预取向丝(POY),在拉伸变形过程中,丝条在假捻器前后的最佳加捻力和解捻力是确保生产正常进行的重要因素。
加捻力应尽量控制得低些,但解捻力与加捻力的比值必须适当,比值过低,则假捻效果差,加捻不匀;比值过大,摩擦阻力增大,易产生毛丝和解捻不完全,并形成紧点僵丝。
PU盘的加入主要影响DTY 的卷曲性能和毛丝、僵丝的控制,其他性能指标和全瓷盘基本一致,这是由假捻盘材质引起的。
PU盘属软质盘,在加工过程中,其打滑系数比瓷盘小。
假捻效果好。
其加工的DTY卷曲收缩率较高,对加工的丝条损伤较小,因此,其加工的DTY外观毛丝较少,但如果PU 盘与瓷盘的组合不当,会出现大量的紧点僵丝。
通过瓷盘与PU盘的有机结合,能大幅度地减少DTY的毛丝,提高产品质量,降低成本,对提高企业的经济效益具有重要意义。
2.涤纶短纤毛丝产生与处理方法2.1聚酯熔体的热降聚酯PET的热稳定性很好,但对杂质很敏感。
纯PET在250-300℃开始降解,但在350℃以上才明显释放出挥发性产物。
降解的引发过程中包括酯部位的异裂,生成羧酸和乙烯基酯端基,后者可与聚酯PET中的羟乙基酯端基发生酯交换反应放出乙醛,它是最主要的挥发性产物。
气相热媒总管把热媒蒸气自脱过热器分配到熔体输送管线夹套,由各段的最低点进入。
根据纺丝生产的品种不同,熔体输送管线的热媒蒸气温度为280℃-290℃纺丝箱体及其中的纺丝组件是由气相热媒加热的。
加热情况与熔体输送管道相似,纺丝箱体通常的操作温度围是275-285℃。
熔体从聚酯终聚釜至生成原丝之前。
都是由热媒保温的。
如果热媒保温温度过高。
熔体输送停留时间较长,熔体大分子降解相对就严重。
在经过计量泵增压挤出、经牵引机牵引形成原丝时,原丝就有缺陷。
易拉断,产生毛丝。
2.2丝束冷却过程环吹装置均匀地分配进入各个纺位的冷却风以保证得到高品质的冷却均匀的丝束。
如果丝束冷却吹风洁净度不够、风压及风量设置失当。
就会出现并丝、断头,产生毛丝。
而针对冷却存在问题,要求环吹置钢网必须是无尘的,如果发生污染或该纺位的丝束因吹风发生涡旋,则要更换环吹筒;为从制度上保证正常吹风品质,规定环吹筒吹风网必须定期更换,以保证清洁的丝束冷却吹风,避免因吹风原因产生的毛丝。
2.3丝束经过丝道过程熔体从组件挤出丝束后,要经过上油辊、导丝棒、上下清洁导丝器、纺丝甬道、大小导辊、转向辊、并向辊、牵引机等,如果它们与丝束接触的表面不光滑、有缺损,必对丝束造成伤害,产生毛丝。
而针对丝道缺陷,必须加大各辊巡检力度,发现问题,及时处理和更换,经常校正销片间隙,减少对丝束的摩擦,保证丝道处于正常运行状态,减少毛丝的产生。
2.3.1丝道各辊如果丝道各辊安装不中正。
辊表面有缺陷或毛刺,丝束与它们接触时,摩擦加剧,产生毛丝。
2.3.2上下清洁导丝器上下清洁导丝器是由2个平行的、中间有一小的缝隙的销片组成的,丝束便由这2个销片中间通过。
销片间隙可以在O.5-1.2mm围调节。
2.4纺丝组件工况差纺丝组件是短纤维装置的关键设备,在短纤维生产中起着过滤清除熔体杂质、混合匀化聚酯熔体、将熔体均匀分配到喷丝板上的每一个微孑L、并从喷丝板挤出形成丝束的作用。
2.4.1组件压力非正常上升如果组件压力升降剧烈,则原丝纤度、断裂强度和伸长率就会发生较大变化甚至会出现竹节丝,产生断头,出现毛丝。
2.4.2组件漏浆组件漏浆的原因:密封垫圈制作精度及材质缺陷严重影响纺丝组件密封性能。
严重时无法进行正常生产。
2.4.3修板精度差涤纶短纤维装置采取定期修板作业,修板间隔为48h。
如果修板精度差,在48h之就出现毛丝,甚至不定期断头。
2.4.4解决对策优化组件装砂方案,金属过滤砂品质及配比影响着组件过滤性能,为了在保证组件过滤性能前提下减缓组件升压速度,改用耐压强度高,在25MPa高压下受压不变形的过滤砂,并对装砂方案多次优化,逐步降低组件升压速度;其次,控制组件漏浆,只有提高密封垫圈精度,把密封垫圈厚室偏差控制在O.02mm,最大不超过O.04mm,并选用较好材质的密封垫圈才能解决组件漏浆问题。
3.粘胶长丝生产过程中毛丝的产生与处理方法粘胶长丝丝筒的毛丝主要分为三种,即绒毛丝、长毛丝和环形毛丝。
所谓绒毛丝即指在丝筒的端面和侧面出现类似起绒现象的毛丝,长毛丝是单丝断裂出现的单根长丝,长度为lmm以上,环形毛丝是单丝呈环状隆起但丝条并未断裂的表现形态。
绒毛丝的产生一般有两种原因,一为机械损伤,二为工艺的匹配因素。
机械损伤一般是由于丝条在成形或运行过程中,与接触物体摩擦而造成丝条的分叉和断裂。
一般通过巡回检查或周期性更换机配件来减少机械损伤的发生。
工艺的匹配因素多是由于在粘胶与酸浴反应、凝固再生过程的速度与拉伸程度不匹配而引起。
分析粘胶和酸浴的工艺参数匹配状况,可通过丝条剩余酯化度测试、纤维截面照相分析等方法进行发析判断。
一般情况下,采用较为强烈的粘胶凝固成形条件有利于减少绒毛丝的产生。
产生长毛丝的原因主要有喷头孔部分堵塞、拉伸不稳、粘胶中含有较大杂质或存在气泡、酸浴较脏、丝条的运行路线存在较大毛刺等。
长毛丝的产生一般是因单丝完全断裂而成,其量一般不是很大,一般在生产过程中稍加注意即可找到根源并加以消除,因而长毛丝一般不会造成较大损失。
生产过程中可根据毛丝在丝筒上的分布等具体情况细致分析。
环形毛丝严格讲并不是毛丝,但由于其单丝纤细,较为脆弱,在加工过程中极易断裂形成毛丝,因而归为毛丝之类。
环形毛丝的产生的主要原因是单丝线密度不均,可以通过适当调节成筒过程力使环形毛丝得以控制。
在粘胶长丝生产过程中,通常有一些丝筒不能达到高质量水平,如变形、油污和污渍等明显的结构缺陷,或者如毛丝、跳丝(或称为绊丝)等难以发现的微细结构方面的缺陷等。
兰精仪器公司根据最新的激光技术、照明技术和数码摄像技术,研究开发了LIS200丝筒自动检测系统。
它具备非常良好的检测质量、分辨能力和再现性。
当丝筒由机械手操纵沿其轴线转动时,数字摄像头、激光以及专门的照明系统就同时检测丝筒的表面。
除了可靠地检测断裂毛丝外,在丝筒的几何缺陷、宏观缺陷以及微观缺陷方面的检测速度均好于人工视觉检测效果。
在断裂毛丝的检测过程中,尽管丝筒表面在受到激光照射时呈现出的是一条实线,但丝筒表面冒出的单丝却表现为闪光。
只要计算丝筒转动一圈时闪光的次数,就可以非常准确和可靠地检测到断裂毛丝、环形毛丝和绒毛丝。
通常情况下,LIS200这样的自动化系统主要经济效益在于减少人工、降低检测成本以及次品和废品的数量,缺陷检测的直接效果在于减少了在质量成本和客户索赔。
三、结束语化纤长丝生产过程中,毛丝的出现会直接影响后道工序的加工,带来断头率的增加,甚至形成织疵等质量问题。
因此,快速准确找出生产中毛丝产生的原因,在最短时间排除故障,对企业降低生产成本、提高经济效益具有重要意义。
要想把毛丝消除在萌芽中,就应该建立科学、完善的工艺、设备管理制度,工艺参数要保持合理和稳定,设备管理要规,其中组件的更换周期、喷丝板板面的清洁、摩擦辊的擦拭、各导丝钩的检查、油轮的检查、卷绕头的保养及检修等,均应严格按规程进行,要不断提高检修人员的各项素质,提高检修质量和水平。