石油钻杆的生产现状与发展趋势
2023年钻杆行业市场规模分析

2023年钻杆行业市场规模分析钻杆行业市场规模分析近年来,国内外石油天然气勘探开发活动不断加强,推动着采油钻探设备行业进一步发展壮大。
然而,与此同时,市场竞争加剧,行业整合不断推进,较高的生产成本也制约了行业的发展。
钻杆是采油钻探设备行业的重要组成部分,其市场规模也随之扩大。
本文将详细分析钻杆行业市场规模。
一、国内钻杆市场据统计,中国石油行业在2019年实现原油产量创新高,其中普通石油钻探井总米数达到6321.7万米,同比增长1.5%。
这一增长带动了钻探设备行业的发展,也推动了钻杆市场的扩大。
截至目前,我国的钻杆生产企业主要分布在东部沿海地区和中西部,其中河南、山东、江苏、河北、陕西等省份钻杆生产量较大。
此外,国内的采油钻探设备出口也在不断扩大。
当前,我国钻杆的主要出口国家包括俄罗斯、哈萨克斯坦、伊朗等,出口数量也在逐年增加。
其中,钻杆进入俄罗斯市场成本较低,因此占据了比较大的市场份额。
二、国际钻杆市场全球石油天然气市场面临多重挑战,因此相应的钻探设备市场也受到了影响。
国际钻杆市场主要分布在北美、欧洲等地区。
近年来,随着页岩油开采的增加,北美地区的钻探活动呈上升趋势,也推动了钻探设备行业的发展,钻杆的需求也在逐步扩大。
相较于国内市场,国际钻杆市场更加竞争激烈。
主要钻杆生产企业包括希尔公司、格兰特普雷斯顿公司等,它们的产品品质和技术水平都比较高,因此市场份额较大。
三、市场规模分析根据国内外市场的发展情况和需求量的增加,预计未来钻杆市场规模还将继续扩大。
据最新研究报告,全球钻杆市场规模在2020年超过50亿美元。
在中国市场方面,2019年中国石油行业增长1.5%,预计未来市场规模将达到3000万元。
此外,国内钻杆生产企业数量众多,市场竞争也比较激烈。
这对提高产品品质和技术水平都起到重要推动作用,进一步促进了市场的发展。
总之,随着需求的不断增加,钻杆市场规模将进一步扩大。
同时,行业整合和市场竞争将是面临的主要挑战。
石油钻杆的生产现状与发展趋势

石油钻杆的生产现状与发展趋势引言石油钻杆是石油开采中必不可少的工具,它承载着整个钻井过程的重要任务。
本文将深入探讨石油钻杆的生产现状与发展趋势,对钻杆的材料、制造工艺、市场需求以及未来发展进行全面剖析。
二级标题1:石油钻杆的材料选择石油钻杆的材料选择对于其耐腐蚀性、强度和重量等方面具有至关重要的影响。
目前,常用的石油钻杆材料主要包括碳素钢、合金钢和钛合金。
三级标题1:碳素钢碳素钢是石油钻杆最常用的材料之一,因其具有良好的强度和耐腐蚀性而备受青睐。
然而,碳素钢的密度较高,导致石油钻杆的重量加大,对于深水和超深水开采等特殊环境下的钻井作业造成了一定的困难。
三级标题2:合金钢合金钢是在碳素钢的基础上添加了一定量的合金元素,以提高其强度和耐腐蚀性。
合金钢的使用可以在一定程度上减轻石油钻杆的重量,提高钻井的效率,但成本相对较高。
三级标题3:钛合金钛合金由于其低密度、高强度和优异的耐腐蚀性,成为石油钻杆材料的新选择。
钛合金制造的钻杆不仅具有较轻的重量,还具备很高的耐腐蚀性能,适用于复杂的海洋环境和极端条件下的钻井作业。
然而,钛合金的制造技术和成本仍然是制约其广泛应用的主要问题。
二级标题2:石油钻杆的制造工艺石油钻杆的制造工艺直接影响着其质量和性能。
传统的制造工艺包括锻造、热处理、钻杆成型等。
三级标题1:锻造锻造是制造石油钻杆的主要工艺之一,通过加热和变形,使钢坯达到所需形状和尺寸。
锻造可以提高钻杆的强度和耐腐蚀性,但对材料的塑性要求较高。
三级标题2:热处理热处理是针对石油钻杆的材料进行加热和冷却处理,以改变其组织和性能。
热处理可以提高钻杆的硬度和耐磨性,增强其抗腐蚀能力,提高使用寿命。
三级标题3:钻杆成型钻杆的成型是指对钻杆进行加工和整形的工艺。
现代钻杆通常采用先进的机械加工和数控技术,确保钻杆的精度和质量。
二级标题3:石油钻杆市场需求全球石油产业的快速发展带来了对石油钻杆的持续需求增长。
石油钻杆市场需求主要受以下因素影响:三级标题1:石油产量石油产量是影响石油钻杆市场需求的关键因素。
钻杆行业分析报告

钻杆行业分析报告钻杆行业分析报告一、定义钻杆是用于石油、天然气、水井等不同领域的钻井活动中,承担起下钻及管道运输的功能性工具。
它用于将钻头和其他钻井工具运送到井底,并将地下物资运送上来。
二、分类特点根据不同的用途及各自的材质和形状,钻杆可以分为三类:钢体钻杆、合金钻杆和柔性钻杆。
钢体钻杆是钢制成品,主要用于石油、天然气、地下水井等行业,其优点为质量稳定、强度高、操作简单。
合金钻杆是将钢体钻杆表层涂上一层合金,其优点为不易腐蚀,经久耐用,适合于海洋环境或恶劣天气下的使用。
柔性钻杆则是过去几年来的新型产品,一般由许多张薄片和钢丝张成的架子加上橡胶或聚酯树脂材料制成,具有更小的尺寸以及更高的适应性,它们可以自由弯曲,动态控制井道轨迹。
三、产业链钻杆产业链是指在钻杆生产和使用过程中的各种产业环节,包括各种资源、技术和经济要素的投入,以及钻杆运输和销售等各个环节。
它从资源的开采、加工、制造、销售和使用等环节逐步构成了一个完整的产业链。
四、发展历程钻杆生产行业的发展始于20世纪60年代的美国,当时美国成为了石油行业的核心,为了满足采油需求,美国开始积极投入并发展钻杆生产。
随着时间的推移,钻杆行业得到了飞速发展,在全球范围内各国都有着不同程度的发展,其中美国、加拿大、俄罗斯、中国等国家成为了钻杆生产业的主要制造商和消费市场。
五、行业政策文件及其主要内容《石油天然气资源管理条例》:该条例主要管理石油和天然气领域的资源。
《石油天然气采矿许可证的发放与管理规定》:该规定主要管辖石油和天然气采掘的每一步。
《中华人民共和国出口管制条例》:该条例规范对石油和天然气出口的管理。
《石油天然气行业标准化规范》:该规范对钻杆的制造、测试、实验室质量管理、采购管理、现场品控等进行了规范。
六、经济环境随着世界经济的发展,大型石油和天然气公司的拓展不断扩大,进而也推动了钻杆行业的发展。
全球能源需求的强劲增长,尤其是对石油和天然气较大的需求,为钻杆产业带来了较大的市场需求。
2023年螺杆钻具行业市场发展现状

2023年螺杆钻具行业市场发展现状螺杆钻具行业是石油工业中的一个重要领域,由于随着全球对能源需求的不断增加,石油钻探行业发展前景广阔,螺杆钻具行业也得以迅速发展。
下面将从市场规模、市场竞争、市场特点等方面对螺杆钻具行业的市场发展现状进行分析。
一、市场规模螺杆钻具行业是石油工业的关键领域,其市场规模与全球石油市场的发展密切相关。
目前,全球原油需求量急剧增加,原油储量的开采也越来越困难,加之环保政策日渐严格,石油钻探难度逐渐加大,因此,螺杆钻具行业将迎来更多的发展机遇。
据市场研究机构统计,2019年全球螺杆钻具市场规模超过100亿美元,预计到2026年将达到200亿美元以上。
在全球螺杆钻具市场中,北美地区占据了最大的市场份额,其他地区如亚太地区、欧洲和中东等也在逐渐增长。
二、市场竞争螺杆钻具行业是一种技术密集型、集成度较高的产业,市场竞争十分激烈。
当前,全球螺杆钻具市场主要由美国、加拿大、挪威、英国、俄罗斯等少数国家的厂商垄断。
这些国家的企业具有强大的研发能力和生产能力,已经形成了较为成熟的销售和服务网络。
国内螺杆钻具厂商与国际品牌相比还存在一定差距,但是随着技术不断进步,国内螺杆钻具企业已经开始增加自主研发力度,打造中高端产品,提升品牌竞争力。
三、市场特点1. 技术升级和创新驱动螺杆钻具行业的技术升级和创新进程十分迅速,为市场带来新的商业机会。
大多数企业都将资源投资于研发,加强技术创新,提高产品性能和质量,增强产品的市场竞争力。
2. 行业市场前景广阔随着全球经济趋势的变化和能源需求的持续增加,螺杆钻具行业将迎来更多的发展机遇。
尤其是在发展中国家,石油工业的快速发展和不断引进的国际石油合作项目,将给螺杆钻具行业带来更多的机遇。
3. 服务和技术支持也是市场竞争的关键点随着市场需求的变化和企业竞争的加剧,除了产品性能外,服务和解决方案的提供也逐渐成为市场竞争的一个重要方面。
与此同时,提供良好的售后服务、技术支持及培训也是提高客户消费者忠诚度的有效途径。
石油钻机制造行业的现状及发展

石油钻机制造行业的现状及发展首先,石油钻机制造行业的现状是充满挑战的。
随着全球石油资源日益减少,越来越多的石油企业开始深海钻探和陆上探矿。
这使得石油钻机需求量大增,市场竞争激烈。
此外,石油钻机的制造技术和设备要求高,对企业的技术实力和生产能力提出了更高要求。
其次,石油钻机制造行业的发展前景广阔。
随着全球经济的发展,石油需求量将继续增长。
特别是在新兴市场国家和地区,石油需求增长迅速。
这将为石油钻机制造企业提供更大的市场机会。
另外,随着石油资源逐渐减少,企业追求高效、环保的石油采掘方式,对石油钻机设备提出了更高的技术要求。
为了应对市场竞争和技术挑战,石油钻机制造企业应注重技术创新和质量提升。
石油钻机制造行业是一个高科技产业,只有不断改进和创新技术才能在市场上占据优势地位。
同时,企业还应加强与石油勘探和生产企业的合作,了解市场需求,提供定制化的产品和服务。
此外,企业还应关注环保和可持续发展。
石油钻机制造行业是一个资源密集型行业,对环境污染和能源消耗都有一定影响。
企业应加强环境管理,推动能源节约和绿色制造,提高产品的能效和环境友好性。
同时,企业还应关注人才培养和技术交流,加强与高校和科研机构的合作,提升企业的创新能力和核心竞争力。
总之,石油钻机制造行业既面临挑战,也有广阔的发展前景。
为了在竞争激烈的市场中立于不败之地,企业需要加强技术创新和质量提升,关注环保和可持续发展,与石油勘探企业合作,提供定制化的产品和服务。
同时,企业还应加强人才培养和技术交流,提升企业的创新能力和核心竞争力。
只有这样,石油钻机制造企业才能在激烈的市场竞争中取得成功。
2024年钻杆市场规模分析

2024年钻杆市场规模分析引言钻杆是石油行业中常用的钻井工具之一,用于在地下通过旋转和推进的方式进行钻井作业。
钻杆市场是石油行业的重要组成部分,其规模和发展状况对整个行业具有重要意义。
本文将对钻杆市场的规模进行详细分析,并对市场发展趋势进行展望。
钻杆市场规模钻杆市场的规模可以通过以下几个方面进行评估。
1. 地理分布钻杆市场的规模在不同地区有所差异。
目前,全球主要的钻杆市场集中在北美、中东和亚洲地区。
这些地区的石油资源富集度高,钻井活动频繁,因此钻杆市场规模相对较大。
而欧洲和非洲等地区的钻杆市场规模相对较小。
2. 市场需求钻杆市场的规模也受市场需求的影响。
随着全球石油需求的增长,石油公司对钻井活动的需求也在增加。
特别是在新兴市场的快速发展,石油行业对钻井工具的需求呈现出稳定增长的趋势。
这些市场的需求推动了钻杆市场的扩大。
3. 技术进步随着技术的进步,钻杆市场也得到了推动。
新材料的应用、钻井设备的改进等技术突破,提高了钻杆的效率和使用寿命。
这些技术创新推动了钻杆市场的增长,并促进了行业的发展。
钻杆市场发展趋势1. 区域转移随着石油资源的逐渐枯竭和环保要求的提高,钻井活动正逐渐从传统的石油资源丰富地区向新的勘探领域转移。
这意味着钻杆市场规模可能会出现地区转移的趋势。
尤其是一些新兴市场的崛起,将成为钻杆市场增长的新动力。
2. 技术升级钻杆市场将随着技术的不断进步而发展。
新材料的应用、智能化设备的使用等将提高钻杆的性能,并降低运营成本。
这种技术升级将推动钻杆市场的发展,并进一步提高行业的竞争力。
3. 环境保护在全球环保意识不断提高的背景下,石油行业也在加强环保措施。
这将对钻杆市场的发展产生一定的影响。
未来,环保型的钻杆将受到更多的关注和需求,相应的市场规模也将有所增长。
结论钻杆市场作为石油行业的重要组成部分,在全球范围内具有巨大的市场潜力。
其规模和发展趋势受到地理分布、市场需求和技术进步等因素的影响。
随着石油资源的转移和环保要求的提高,钻杆市场的发展将呈现出区域转移、技术升级和环境保护的趋势。
2024年螺杆钻具市场环境分析

2024年螺杆钻具市场环境分析1. 市场概况螺杆钻具是一种重要的石油钻采设备,主要用于石油勘探和生产过程中的钻井作业。
随着全球石油需求的不断增长,螺杆钻具市场也在不断扩大。
本文将对螺杆钻具市场的环境进行分析。
2. 市场需求全球能源需求的增长驱动了螺杆钻具市场的发展。
石油是目前全球最重要的能源资源之一,而螺杆钻具在石油勘探和生产过程中起到了至关重要的作用。
随着全球石油储量的逐渐减少,对于更高效的钻采设备的需求也越来越大。
3. 市场竞争螺杆钻具市场竞争激烈。
主要竞争者包括国内外的石油设备制造商和供应商。
这些竞争者不断推出新的技术和产品,以提升其在市场中的竞争力。
同时,一些新兴市场也在不断涌现,给传统的螺杆钻具市场带来了一定的冲击。
4. 市场发展趋势螺杆钻具市场发展趋势表现为以下几个方面:4.1 技术创新随着科技的不断进步,螺杆钻具行业也在不断进行技术创新。
新的钻井技术和设备的出现,提高了钻井效率和钻井质量,满足了不同地质条件下的钻井需求。
4.2 环保要求全球对环境保护的要求越来越高,石油行业也不例外。
螺杆钻具制造商和供应商需要不断提升产品的环保性能,降低对环境的影响。
4.3 地区发展差异不同地区的能源需求和钻采条件存在差异,导致螺杆钻具市场发展存在差异。
发达国家市场饱和,而新兴市场在能源开发方面的需求仍然强劲,给市场带来了发展的机会和挑战。
4.4 产业链合作螺杆钻具市场涉及地质勘探、钻井、生产等多个环节,各环节的合作与协同将成为市场发展的重要推动力。
钻具制造商、石油公司和服务商之间的紧密合作,将推动市场持续健康发展。
5. 我国螺杆钻具市场状况我国是全球最大的石油消费国之一,对螺杆钻具的需求日益增长。
我国的螺杆钻具市场竞争激烈,国内外企业均有一定市场份额。
随着我国对能源需求的增长,螺杆钻具市场仍有较大的发展空间。
6. 总结螺杆钻具市场在全球范围内具有较大的发展潜力,随着能源需求的增长和钻采技术的不断提升,市场将持续扩大。
2024年螺旋钻具市场发展现状

2024年螺旋钻具市场发展现状引言螺旋钻具作为一种重要的工具,在石油、天然气、地热等采矿行业中发挥着关键的作用。
本文将对螺旋钻具市场的发展现状进行分析和探讨。
市场规模与增长趋势近年来,全球能源需求的不断增长推动了螺旋钻具市场的发展。
特别是中国、美国和俄罗斯等地的大规模能源开发项目,为螺旋钻具市场提供了巨大的需求。
据市场研究机构的数据显示,螺旋钻具市场在过去几年内实现了稳定的增长。
预计未来几年内,该市场的规模将继续扩大,并且增长速度有望加快。
这主要归因于以下几个因素的影响。
首先,不断增长的能源需求驱动了螺旋钻具市场的扩张。
随着新能源的开发和传统能源的开采,对钻井工具的需求不断增长。
螺旋钻具作为一种高效稳定的工具,受到了能源行业的广泛关注和采用。
其次,不断进步的钻井技术促进了螺旋钻具市场的发展。
随着科技的不断进步,钻井技术得到了极大的改进和创新。
现代螺旋钻具具备更好的适应性和高效性,满足了复杂地质环境下的钻井需求。
最后,国家政策的支持也推动了螺旋钻具市场的发展。
许多国家为了加强能源独立性和能源安全,出台了一系列支持能源开发的政策。
这些政策为螺旋钻具市场的发展提供了有力支持。
主要市场参与者螺旋钻具市场的竞争激烈,拥有众多的参与者。
以下是一些主要的市场参与者:1.Schlumberger:作为全球领先的石油服务公司之一,Schlumberger在螺旋钻具领域拥有丰富的经验和技术优势。
2.Halliburton:Halliburton是另一家全球知名的石油服务公司,其在螺旋钻具市场上也具有一定的竞争优势。
3.Baker Hughes:Baker Hughes是一家全球性的石油服务公司,其在螺旋钻具行业有着广泛的产品线和服务网络。
4.National Oilwell Varco:作为螺旋钻具制造商,National Oilwell Varco在市场上拥有独特的竞争优势。
5.Weatherford International:Weatherford International是螺旋钻具市场上的一家重要参与者,其产品被广泛应用于全球各地的能源开发项目中。
石油钻杆的生产现状与发展趋势

石油钻杆的生产现状与发展趋势石油钻杆作为石油钻探行业的重要工具,其生产现状和发展趋势一直备受行业关注。
本文将从以下几个方面介绍石油钻杆的生产现状和发展趋势:生产状况、技术改进和趋势预测。
一、生产状况石油钻杆的生产商主要集中在国外,如美国、加拿大、墨西哥等。
这些国家的石油钻杆生产商拥有雄厚的技术实力和资金实力,能够为世界各地的石油钻探企业提供高品质的产品和服务。
国内石油钻杆生产企业数量相对较少,主要用于满足国内石油钻探企业的需求。
其中,长城钻探、天津石化等企业是国内石油钻杆生产的领头企业。
二、技术改进随着石油勘探和开发的深入,对石油钻杆质量和性能的要求也越来越高。
为了满足市场需求,石油钻杆生产商不断进行技术改进。
近年来,石油钻杆主要的技术改进集中在以下几个方面:1. 材料技术:石油钻杆需要经受极端的工作环境和高负荷的工作条件。
为了提高石油钻杆的耐用性和韧性,石油钻杆生产商采用高强度合金钢、高强度不锈钢等特殊材料。
2. 生产工艺:石油钻杆的生产工艺直接关系到产品的质量和性能。
近年来,石油钻杆生产商利用新的加工设备和工艺,提高了生产效率和产品的一致性。
3. 先进设备:石油钻杆的生产需要大型先进设备的支持,如自动化装配线、数字化检测设备等。
三、趋势预测随着全球能源需求的增长,石油钻探行业将保持快速增长。
未来几年,石油钻杆的生产趋势主要分为以下几个方面:1. 多样化需求:随着勘探的深入和油田建设的扩大,石油钻杆的用途也将日趋多样化。
未来的石油钻杆产品将不仅仅是单纯的鑽杆,还需要具有力强、高效、耐磨等多种特性。
2. 智能制造:随着大数据、人工智能等技术的广泛应用,石油钻杆的生产将越来越智能化。
未来的石油钻杆将具有更高的自适应性和智能化,从而提高生产效率和降低成本。
3. 环保生产:石油钻杆生产是一项高耗能、高污染的行业,未来将越来越注重环保生产。
石油钻杆生产商将通过优化生产工艺和设备、采用新型材料等方式来实现环保生产。
探讨钻井工程技术现状及发展趋势
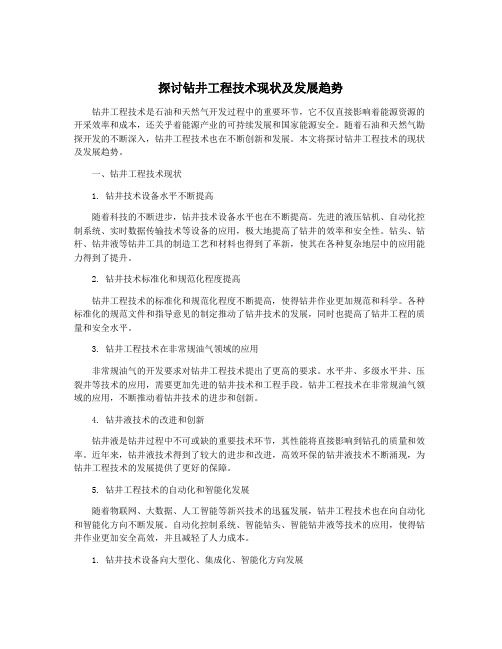
探讨钻井工程技术现状及发展趋势钻井工程技术是石油和天然气开发过程中的重要环节,它不仅直接影响着能源资源的开采效率和成本,还关乎着能源产业的可持续发展和国家能源安全。
随着石油和天然气勘探开发的不断深入,钻井工程技术也在不断创新和发展。
本文将探讨钻井工程技术的现状及发展趋势。
一、钻井工程技术现状1. 钻井技术设备水平不断提高随着科技的不断进步,钻井技术设备水平也在不断提高。
先进的液压钻机、自动化控制系统、实时数据传输技术等设备的应用,极大地提高了钻井的效率和安全性。
钻头、钻杆、钻井液等钻井工具的制造工艺和材料也得到了革新,使其在各种复杂地层中的应用能力得到了提升。
2. 钻井技术标准化和规范化程度提高钻井工程技术的标准化和规范化程度不断提高,使得钻井作业更加规范和科学。
各种标准化的规范文件和指导意见的制定推动了钻井技术的发展,同时也提高了钻井工程的质量和安全水平。
3. 钻井工程技术在非常规油气领域的应用非常规油气的开发要求对钻井工程技术提出了更高的要求。
水平井、多级水平井、压裂井等技术的应用,需要更加先进的钻井技术和工程手段。
钻井工程技术在非常规油气领域的应用,不断推动着钻井技术的进步和创新。
4. 钻井液技术的改进和创新钻井液是钻井过程中不可或缺的重要技术环节,其性能将直接影响到钻孔的质量和效率。
近年来,钻井液技术得到了较大的进步和改进,高效环保的钻井液技术不断涌现,为钻井工程技术的发展提供了更好的保障。
5. 钻井工程技术的自动化和智能化发展随着物联网、大数据、人工智能等新兴技术的迅猛发展,钻井工程技术也在向自动化和智能化方向不断发展。
自动化控制系统、智能钻头、智能钻井液等技术的应用,使得钻井作业更加安全高效,并且减轻了人力成本。
1. 钻井技术设备向大型化、集成化、智能化方向发展未来,钻井技术设备将更加向大型化、集成化和智能化方向发展。
大型钻机、多功能集成钻机、智能钻井设备等将成为发展的趋势。
这不仅可以降低钻井成本,提高钻井效率,还可以减少工人的作业强度和提高工作安全性。
2024年钻杆市场前景分析

2024年钻杆市场前景分析引言钻杆是石油勘探和开发领域中广泛使用的工具,用于在地下钻探井口,获取地下资源的信息。
钻杆市场作为石油工业的核心部分,对于石油勘探和开发的进展起着关键的作用。
本文将对钻杆市场的前景进行分析,并探讨未来趋势和机会。
市场概况钻杆市场是一个庞大而复杂的市场,涉及到多个领域和产业。
根据钻杆的类型,市场可以分为钻杆钻头、钻杆管、钻杆连接器等子市场。
根据应用领域,市场可以分为石油勘探、地质科研、水井钻探等不同市场。
同时,全球范围内也存在着多个钻杆制造商和供应商。
市场驱动因素1.石油需求增长:全球对于石油和天然气的需求持续增长,尤其是新兴经济体的能源需求增加,对钻杆市场带来了巨大的增长机遇。
2.技术创新:随着石油勘探和开发技术的不断发展,对于更高效、更耐用的钻杆需求不断增加,促使市场不断创新和升级。
3.环境监管:全球对于环境保护的关注度提高,石油勘探和开发领域也受到越来越多的环境监管限制,进一步推动了钻杆市场的发展。
市场前景分析1. 市场规模扩大随着全球石油需求的增长,钻杆市场规模也在逐步扩大。
预计未来几年市场规模将稳步增长。
特别是在亚太地区和中东地区,由于石油勘探和开发的加速推进,钻杆市场将迎来新的机遇。
2. 技术升级与创新钻杆市场在技术方面的需求也在不断增加。
新材料技术、钻探工艺和智能化技术的应用将成为市场的发展方向。
同时,市场也将出现更多的创新产品和解决方案。
3. 竞争格局调整目前钻杆市场存在着一些大型制造商和供应商垄断的情况。
然而,随着市场需求的增加和竞争的加剧,市场竞争格局将发生调整。
新进入市场的厂商将有机会在市场上获得份额。
挑战与机遇钻杆市场面临着一些挑战,但也蕴藏着巨大的机遇。
1. 环保压力石油勘探和开发活动受到环保压力的影响,对于环保技术和环保产品的需求增加。
钻杆制造商有机会通过研发环保型钻杆,满足市场需求并获得竞争优势。
2. 新兴市场增长新兴市场对于石油勘探和开发的需求增加,为钻杆市场提供了新的增长机会。
2024年石油钻井井下工具市场前景分析

2024年石油钻井井下工具市场前景分析概述石油钻井井下工具是指在石油钻井作业过程中使用的各种工具和设备,用于提高钻井效率和降低风险。
随着全球能源需求的增长,石油钻井井下工具市场一直保持着稳定的增长态势。
本文将分析石油钻井井下工具市场的当前情况和未来发展趋势,以及相关的市场机会和挑战。
当前市场情况1.需求增长:随着全球经济的发展和人口的增加,对能源的需求也在不断增长。
石油仍然是主要的能源来源之一,因此石油钻井活动也在全球范围内增加。
2.新技术的应用:随着技术的不断进步,石油钻井井下工具市场也在不断创新。
新技术的引入使得钻井作业更加高效和安全,为市场的发展提供了新的机遇。
3.区域市场差异:石油钻井井下工具市场在不同的地区存在一定的差异。
发达国家的市场相对成熟,市场份额相对较大,而新兴市场的增长潜力更大。
市场机会1.深水钻井市场:随着陆地油田资源逐渐减少,深水油田的开发成为了石油钻井井下工具市场的一个重要方向。
深水钻井工作环境恶劣,对工具的可靠性和性能提出了更高的要求。
2.智能井下工具:随着人工智能和物联网技术的快速发展,智能井下工具正逐渐应用于钻井作业中。
智能井下工具能够实时监测和分析钻井过程中的各种参数,提高作业效率和安全性。
3.可再生能源钻井市场:随着全球对可再生能源的需求增加,可再生能源钻井市场也在不断发展。
相关的钻井井下工具的需求也将随之增长。
市场挑战1.油价波动:石油价格的波动性对石油钻井井下工具市场产生了一定的影响。
油价下跌可能导致石油公司减少投资,从而影响市场需求。
2.环保压力:全球对环境保护的需求增加,石油钻井活动受到了更严格的监管和限制。
这使得钻井井下工具市场需要更加环保和节能的解决方案。
3.技术壁垒:石油钻井井下工具领域已经形成了一定的技术壁垒,新进入者需要具备较强的技术实力和资金支持才能在市场中立足。
发展趋势1.数字化和自动化:随着数字化和自动化技术的应用,石油钻井井下工具市场正朝着更智能化的方向发展。
2024年石油钻采机械市场发展现状
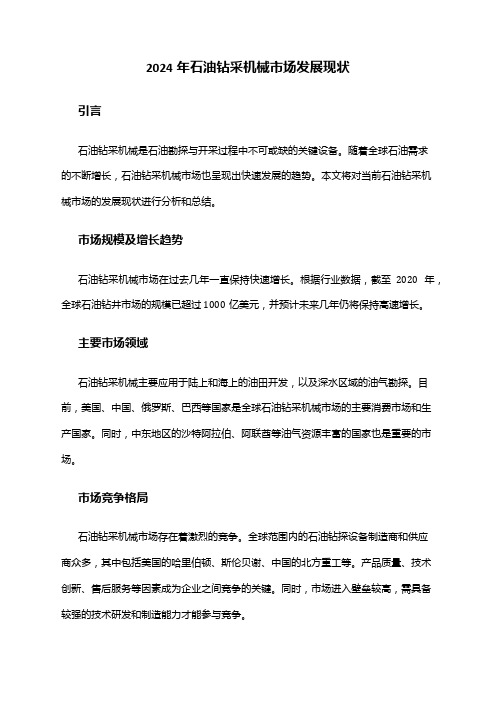
2024年石油钻采机械市场发展现状引言石油钻采机械是石油勘探与开采过程中不可或缺的关键设备。
随着全球石油需求的不断增长,石油钻采机械市场也呈现出快速发展的趋势。
本文将对当前石油钻采机械市场的发展现状进行分析和总结。
市场规模及增长趋势石油钻采机械市场在过去几年一直保持快速增长。
根据行业数据,截至2020年,全球石油钻井市场的规模已超过1000亿美元,并预计未来几年仍将保持高速增长。
主要市场领域石油钻采机械主要应用于陆上和海上的油田开发,以及深水区域的油气勘探。
目前,美国、中国、俄罗斯、巴西等国家是全球石油钻采机械市场的主要消费市场和生产国家。
同时,中东地区的沙特阿拉伯、阿联酋等油气资源丰富的国家也是重要的市场。
市场竞争格局石油钻采机械市场存在着激烈的竞争。
全球范围内的石油钻探设备制造商和供应商众多,其中包括美国的哈里伯顿、斯伦贝谢、中国的北方重工等。
产品质量、技术创新、售后服务等因素成为企业之间竞争的关键。
同时,市场进入壁垒较高,需具备较强的技术研发和制造能力才能参与竞争。
发展动力与挑战石油钻采机械市场的快速发展得益于全球范围内的石油需求增长和油田开发的不断扩大。
然而,市场也面临一些挑战。
首先,石油价格波动以及环保压力对市场供需产生影响。
其次,技术创新的速度也是市场发展的关键因素。
随着技术的进步,新一代的高效、低能耗、环保的石油钻采机械将逐渐取代传统设备。
发展趋势与展望未来,石油钻采机械市场将继续保持快速增长。
新兴市场的开发和旧有油田的再开发将推动市场需求的增长。
同时,技术进步将改变市场格局,提升设备的效率和可靠性。
另外,可再生能源的发展也将对石油钻采机械市场产生一定影响。
结论石油钻采机械市场在全球石油勘探与开采行业中扮演着重要的角色。
随着全球石油需求的增长,市场规模持续扩大。
竞争激烈的市场环境下,企业需要不断创新、提高产品质量和服务水平才能在市场中获得竞争优势。
技术进步、环保压力和新兴市场开发将是市场发展的重要驱动因素。
石油钻杆的生产现状与发展趋势

杆 以及 双 台肩钻杆 等 多元化 发展 。 关键 词 :石 油钻杆 ;生产现 状 ;发 展趋 势
中图分 类号 :T 一 E9
文献 标志码 :B
文 章编 号 :10— 9 82 1)10 3— 4 0 133 (0 1- 05 0 1
( . oa K rl ieC . t ,fC P oa q im n nfcuigC .Ld, 1 B h i KD i p o, d o N CB h i u e t N lP L . E p Ma u tr , t. a no QnXa 6 6 8 H b iC i ;.ot hn erl m Sel ieC .Ld o N CB h i ig i 0 2 5 , e e,hn 2 r C i P t e t p , t.fC P o a; n a N h a ou eP o u m n nfcui o Ld, i X a 6 6 8Hee,hn ) i e tMauatr gC . t.Qn in0 2 5 , biC ia p n , g
The Pr d to S a us a d De e o o uc i n t t n v l pm e e fDr l Pi e ntTr nd o il p
L inqa g, U L- n 2N U C e g i ,I h—a Y E P n C N Y -o g I a —i Y i o g, I h n  ̄e L i o, U e g, HE usn J n s Z h
d me t n e a r a a ay e o r b e xse n d i i e p o e sa d p o u t n s c sf s e v l o si a d t b o d,n lz d s me p o l ms e i d i r lp p rc s n r d c i ,u h a a h rmo a , c h t l o l
2024年螺杆钻具市场分析现状
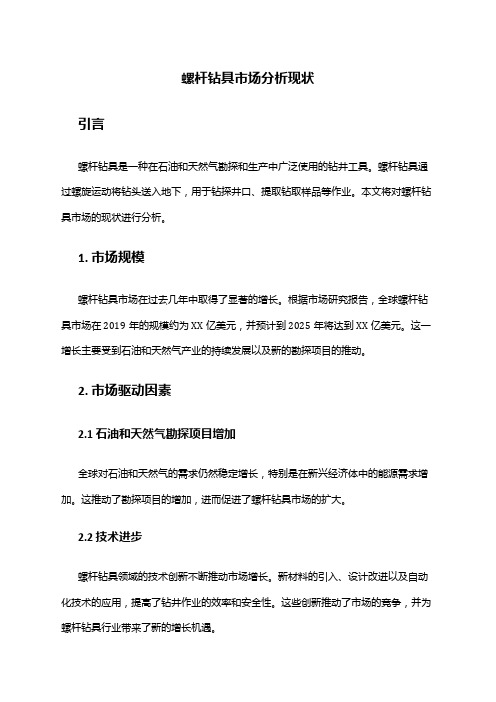
螺杆钻具市场分析现状引言螺杆钻具是一种在石油和天然气勘探和生产中广泛使用的钻井工具。
螺杆钻具通过螺旋运动将钻头送入地下,用于钻探井口、提取钻取样品等作业。
本文将对螺杆钻具市场的现状进行分析。
1. 市场规模螺杆钻具市场在过去几年中取得了显著的增长。
根据市场研究报告,全球螺杆钻具市场在2019年的规模约为XX亿美元,并预计到2025年将达到XX亿美元。
这一增长主要受到石油和天然气产业的持续发展以及新的勘探项目的推动。
2. 市场驱动因素2.1 石油和天然气勘探项目增加全球对石油和天然气的需求仍然稳定增长,特别是在新兴经济体中的能源需求增加。
这推动了勘探项目的增加,进而促进了螺杆钻具市场的扩大。
2.2 技术进步螺杆钻具领域的技术创新不断推动市场增长。
新材料的引入、设计改进以及自动化技术的应用,提高了钻井作业的效率和安全性。
这些创新推动了市场的竞争,并为螺杆钻具行业带来了新的增长机遇。
2.3 环境意识的提高全球对环境保护和可持续发展的呼声越来越高,这对传统的石油和天然气行业产生了一定影响。
螺杆钻具作为一种相对环保、高效的钻井工具,在这一背景下受到了更广泛的应用。
政府部门和能源公司的环保要求推动了市场对螺杆钻具的需求增长。
3. 市场挑战3.1 市场竞争加剧螺杆钻具市场竞争激烈,主要供应商之间存在激烈的价格战和产品差异化竞争。
随着新的厂商进入市场,市场份额分布变得更加分散,这对现有供应商构成了一定的挑战。
3.2 石油价格波动螺杆钻具市场的发展与石油价格密切相关。
全球石油价格的波动和不确定性对市场预测和投资决策带来了风险。
石油价格的下跌可能导致勘探项目的减少,从而影响螺杆钻具市场的需求。
3.3 环境监管加强随着环保监管的加强,能源公司需要更高的环境责任和合规性。
这对于螺杆钻具供应商来说,意味着更严格的质量标准和环保要求。
这增加了供应商的成本,并可能对市场竞争力产生一定的影响。
4. 市场前景螺杆钻具市场在未来几年有望保持稳定的增长势头。
2024年石油钻采专用设备市场分析现状
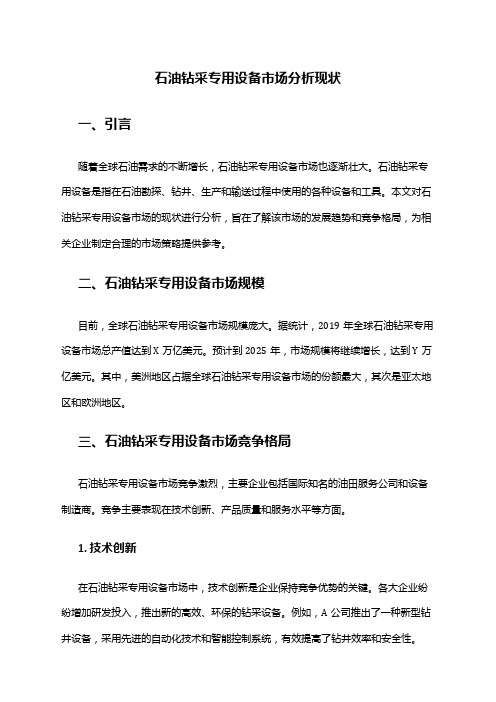
石油钻采专用设备市场分析现状一、引言随着全球石油需求的不断增长,石油钻采专用设备市场也逐渐壮大。
石油钻采专用设备是指在石油勘探、钻井、生产和输送过程中使用的各种设备和工具。
本文对石油钻采专用设备市场的现状进行分析,旨在了解该市场的发展趋势和竞争格局,为相关企业制定合理的市场策略提供参考。
二、石油钻采专用设备市场规模目前,全球石油钻采专用设备市场规模庞大。
据统计,2019年全球石油钻采专用设备市场总产值达到X万亿美元。
预计到2025年,市场规模将继续增长,达到Y万亿美元。
其中,美洲地区占据全球石油钻采专用设备市场的份额最大,其次是亚太地区和欧洲地区。
三、石油钻采专用设备市场竞争格局石油钻采专用设备市场竞争激烈,主要企业包括国际知名的油田服务公司和设备制造商。
竞争主要表现在技术创新、产品质量和服务水平等方面。
1. 技术创新在石油钻采专用设备市场中,技术创新是企业保持竞争优势的关键。
各大企业纷纷增加研发投入,推出新的高效、环保的钻采设备。
例如,A公司推出了一种新型钻井设备,采用先进的自动化技术和智能控制系统,有效提高了钻井效率和安全性。
2. 产品质量石油钻采专用设备在恶劣的工作条件下使用,对于产品质量要求较高。
市场上较有竞争力的企业注重产品的研发和生产质量控制,确保产品的可靠性和稳定性。
B公司通过ISO9001质量管理体系认证,提升了产品质量和市场竞争力。
3. 服务水平由于石油钻采专用设备的复杂性,售后服务至关重要。
优秀的售后服务可以提高客户满意度,增加企业的口碑和市场份额。
C公司建立了全球服务网络,提供及时的技术支持和维修保养服务,赢得了客户的信赖。
四、石油钻采专用设备市场发展趋势1. 自动化技术应用的普及随着科技的不断发展,自动化技术在石油钻采专用设备中的应用逐渐普及。
自动化设备不仅提高了钻井效率和安全性,还减少了人力成本。
预计未来几年,石油钻采专用设备市场将继续增加自动化设备的需求。
2. 环保意识提升随着环保意识的提升,石油钻采专用设备市场对环保型设备的需求也逐渐增加。
2024年石油钻井井下工具市场发展现状
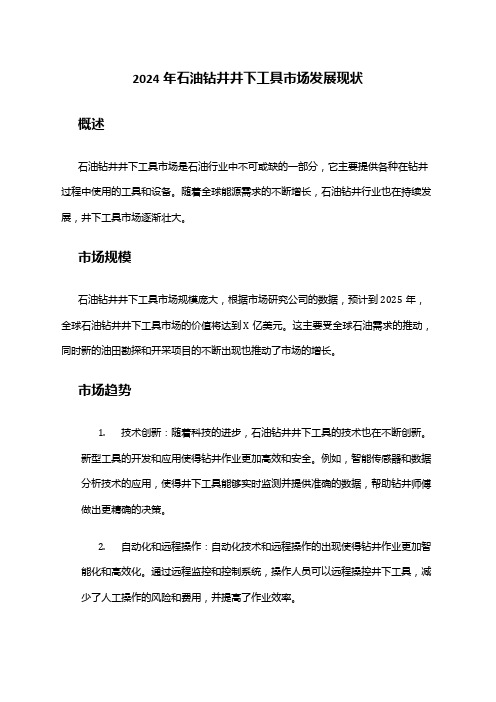
2024年石油钻井井下工具市场发展现状概述石油钻井井下工具市场是石油行业中不可或缺的一部分,它主要提供各种在钻井过程中使用的工具和设备。
随着全球能源需求的不断增长,石油钻井行业也在持续发展,井下工具市场逐渐壮大。
市场规模石油钻井井下工具市场规模庞大,根据市场研究公司的数据,预计到2025年,全球石油钻井井下工具市场的价值将达到X亿美元。
这主要受全球石油需求的推动,同时新的油田勘探和开采项目的不断出现也推动了市场的增长。
市场趋势1.技术创新:随着科技的进步,石油钻井井下工具的技术也在不断创新。
新型工具的开发和应用使得钻井作业更加高效和安全。
例如,智能传感器和数据分析技术的应用,使得井下工具能够实时监测并提供准确的数据,帮助钻井师傅做出更精确的决策。
2.自动化和远程操作:自动化技术和远程操作的出现使得钻井作业更加智能化和高效化。
通过远程监控和控制系统,操作人员可以远程操控井下工具,减少了人工操作的风险和费用,并提高了作业效率。
3.环保和可持续性:环保和可持续性也成为石油钻井井下工具市场的重要考量因素。
随着社会对环境保护的重视,市场对环保型井下工具的需求不断增加。
例如,减少废弃物和污染物的产生,提高能源利用效率等。
4.区域分布:石油钻井井下工具市场在全球范围内存在着一定的区域分布特点。
例如,北美地区由于页岩气和页岩油的开采,市场需求较为旺盛;中东地区由于石油资源的丰富,市场规模也相当大。
市场竞争格局石油钻井井下工具市场竞争激烈,市场上存在着多家知名企业。
这些企业通过不断的技术创新和产品优化来提高自身竞争力。
市场上的主要参与者包括:1.贝克休斯2.哈里伯顿3.斯伯丁股份公司4.沙伯基础工业公司5.霍尔布鲁克有限公司市场前景石油钻井井下工具市场的前景仍然向好。
随着全球能源需求的继续增长和新的油田开采项目的不断涌现,市场需求将继续增加。
同时,技术创新和环保意识的提高也将推动市场的发展。
在未来几年,石油钻井井下工具市场有望保持稳定增长。
- 1、下载文档前请自行甄别文档内容的完整性,平台不提供额外的编辑、内容补充、找答案等附加服务。
- 2、"仅部分预览"的文档,不可在线预览部分如存在完整性等问题,可反馈申请退款(可完整预览的文档不适用该条件!)。
- 3、如文档侵犯您的权益,请联系客服反馈,我们会尽快为您处理(人工客服工作时间:9:00-18:30)。
石油钻杆的生产现状与发展趋势1、石油钻杆的发展人类利用工具钻探而获取资源的历史可以追溯到11世纪,那时人们利用竹木做工具,以人畜为动力,冲击钻凿盐井,并利用伴随开采出来的天然气煮盐水获得食盐。
这些最早用来钻井的竹木可以称作第一代钻杆。
20世纪初,利用钢铁工具和设备,以蒸汽机作动力,开始了顿钻打井,当时的钻探工具可以称得上是第二代钻杆。
真正意义的钻杆产生于20世纪40年代,那时利用钻头钻取岩屑,利用钻杆传递扭矩和泥浆液,钻井速度和深度也大大提高。
到了70年代,随着计算机技术的高速发展,钻井进入自动化阶段,同时对钻杆性能提出了更高的要求,这个时期到现在使用的钻杆称为第三代钻杆。
由于水平井、深井和超深井、大位移井等钻井技术的应用,钻井成本和钻井风险也在不断提高,传统意义的钻杆已不能满足使用要求,第四代钻杆正向着高强度、高韧性、智能化、数字化、防腐蚀、安全环保等方面发展。
2、钻杆的生产现状世界上著名的钻杆生产厂有美国格兰特钻具公司(现已被美国国民油井公司收购)和法德合资的瓦姆公司,两家的生产能力约占全世界的一半。
国内具有代表性的钻杆生产企业有上海宝钢、江苏曙光格兰特钻杆有限公司、渤海能克钻杆有限公司等。
近几年随着石油价格的上涨,钻杆用量和价格也随之上涨,山西风雷钻具有限公司、无锡西姆莱斯石油专用管制造有限公司、上海华实海隆石油装备有限公司、江阴德马斯特集团等也加入了钻杆的生产行列,普通钻杆已经完全替代了进口,并形成了一定的出口能力。
20世纪70年代,加压气焊及闪光对焊技术用于钻杆的修复和生产,这两种焊接方法的工艺参数不易控制,容易在焊接过程中使粒状或块状氧化物和硅酸盐类非金属夹杂物残留在焊缝中,形成致命的浅平微坑状焊接灰斑缺陷。
存在灰斑缺陷的钻杆在使用中极易导致早期脆性断裂,远不能满足钻井要求,因此,这两种焊接方法很快被淘汰。
摩擦焊作为一种新型焊接方法,具有加热时间短、热影响区小、焊接质量稳定、高效环保等特点,很快在钻杆生产中得到应用。
3、钻杆的生产工艺我国的钻杆生产开始于20世纪90年代,钻杆的生产大致包括三个部分:管端加厚、工具接头加工、摩擦对焊及后续处理。
3.1管端加厚石油钻杆的管体材料是低碳合金钢,连铸连轧的圆钢坯经过大型回转炉加热后进入延伸机、芯棒自动穿孔机成型,再次加热后进行内外径精整,矫直进入墩锻工序。
由于石油钻杆的焊缝部位是使用过程中最薄弱的环节,无缝管在焊接前要对管体的两端进行管端加厚,以增加厚度来提高薄弱部位的强度,使焊缝部位的整体强度大于管体的整体强度。
根据管径不同一般分为内外加厚、内加厚、外加厚3种型式,其中以内外加厚型式为主。
管端加厚的过程首先是对无缝管的管端进行加热、均热;其次是用液压或者气动的方式对管端进行墩打,外表面靠模具成型,内表面靠温度梯度自然成型;最后对整个管体进行热处理、矫直、无损探伤检查。
管端加厚管的关键技术在于内表面过渡带的成型,因为这个部位在使用中最薄弱,受力最复杂,大约有70%的事故都发生在这个部位,所以对钻杆的质量举足轻重。
3.2工具接头加工工具接头的材料一般采用中碳合金钢,毛坯经过加热后分三次冲压成型,经过正火后进行机械加工。
首先对毛坯进行内孔、外圆、端面的车削加工,其次是对接头进行调质热处理以获取综合的力学性能,最后对接头进行螺纹加工,螺纹部分要进行镀铜或磷化处理,防止在使用过程中发生粘扣现象。
接头质量的好坏在于热处理和螺纹加工这两个关键工序。
热处理组织直接影响接头的各项力学性能,所以先进的钻杆厂采用全自动连续可控气氛保护加热,油质或水基淬火剂淬火,接头加热过程中采用还原性气氛保护,保证了工件不氧化、脱碳和渗碳。
接头淬火和回火后,逐个进行表面硬度检测和磁粉探伤。
热处理之后进行螺纹加工,钻杆螺纹是粗牙锥形螺纹,在钻杆的连接过程中,螺纹起着关键的作用。
因此,螺纹加工大都采用高精度数控机床进行,对加工出的接头逐个进行螺纹紧密距、螺距、锥度、牙高等参数的测量,以保证螺纹扣型和精度要求,从而有力保证了钻杆接头的连接性能。
3.3摩擦对焊及后续处理钻杆的摩擦对焊是整个钻杆生产的重要一环,为了保证焊接质量,几乎所有的钻杆厂都采用全自动摩檫焊机,并配备焊接参数监控装置,对焊接过程中的摩擦时间、摩擦压力、顶锻压力、顶锻时间和缩短量等参数进行自动监控和记录,从而保证焊缝质量。
焊后需把焊接毛刺去除,对焊接热影响区进行调质处理,对焊缝进行无损探伤检查。
其中焊缝的调质热处理至关重要,几乎全部厂家都采用中频加热方式进行,并对加热温度、加热时间、保温时间、淬火时间等参数自动记录。
这种焊缝热处理的优点是:加热热影响区窄,加热时间短;焊区组织均匀稳定,性能可靠;焊区表面的残余应力小。
4、钻杆生产中存在的问题4.1焊接飞边的去除钻杆在摩擦焊接过程中会形成内外飞边,其中高钢级钻杆由于公接头内径小于管体焊接部内径,给去除内飞边造成很大困难。
传统机床车削由于接头内径的限制,车床刀杆直径小易造成加工时刀杆振颤,严重影响了加工质量与效率。
目前,多数厂家采用冲切方式去除内飞边,加工效率较高。
由于冲头型式、冲切时机、冲切力大小等因素影响,有时会造成冲切时毛刺划伤管体内壁或在内壁粘连等现象,影响了钻杆的正常使用。
4.2抗硫钻杆的应用硫化氢腐蚀造成钻杆失效的事故已经很多了,国内的钻杆厂家也已经研制出抗硫钻杆,但现在还没有得到推广用。
归纳有两点:①抗硫钻杆的价格贵,大约是普通钻杆的2倍。
因为抗硫钻杆材料特殊,生产工艺复杂,造成价格居高不下。
②强度有待提高,在含硫环境中钻井,钻杆钢强度越高,受腐蚀破裂危险性越大。
4.3强度与韧性在钻杆的生产和制造过程中常常遇到强度与韧性的矛盾。
现在打井过程中,多数井眼不是竖直的,斜井、水平井的应用越来越多,在“狗腿”部位钻杆受到交变应力的作用,韧性差,很容易发生断裂或刺穿事故。
面对这样的矛盾,生产厂开始尝试开发新的钢种,通过改变钢的成分和组织来增加强度和韧性,如添加金属钼。
5、钻杆生产的前景及发展方向5.1智能钻杆智能钻杆是由美国格兰特公司首先开始研制的,他们在军方的资助下,在钻杆接头部植入芯片,通过钻杆将打井过程中的地下信息传递到地面,由地面上的仪器在线分析以提高打井的效率。
准确地说智能钻杆是一种可通过钻井过程中钻杆的连接,以实时方式利用井下控制工具将高精度数据提供给司钻的一种新系统,这项技术的研制将是石油技术史上又一次技术革命。
格兰特公司利用该技术在美国本土4口油井上进行了试验,取得了一定经验。
众所周知,钻井时井下状况异常复杂,传输系统要经受高温、高压、地磁等干扰考验,所以此项技术还处于试验阶段,大面积的推广应用还需要时间。
5.2铝合金钻杆虽然铝合金钻杆已经制定了GB/T20659—2006《铝合金钻杆》,并于2007年5月1日颁布实施,但国内还没有一家钻杆生产企业可以制造铝合金钻杆。
铝合金钻杆用于石油工业已有数十年的历史,绝大多数经验来自俄罗斯和周边国家。
它的优点是:在强度相同的情况下,重量仅为钢钻杆的一半,因而在设备、动力、运输和劳力方面都可大大节约,由于壁厚的增加,使耐磨性增强,寿命延长,铝合金钻杆的寿命几乎是普通薄壁钢钻杆的两倍多;铝合金钻杆有较大的回弹力,因而其抗冲击能力增加,从而改善了钻头在井底的工作条件,使寿命延长;抗腐蚀性强,除不易氧化外,还不易受酸性物质的侵蚀,在酸性井(含H2S和CO2等)使用可节省大量费用。
其不足之处是屈服强度相对较低,特别是在高温情况下,屈服强度将急剧下降;壁厚要比钢钻杆厚,造成水马力下降。
我国的塔里木油田由于勘探开发的需要,近期向俄罗斯订购了两套铝合金钻杆,除价格贵外,采购也非常困难,需承诺不用于军事行业。
从目前塔里木油田的使用情况看并不理想,其主要缺陷是强度低。
5.3抗腐蚀钻杆随着钻井深度增加,复杂地层不断出现,特别是含S地层和含CO2地层的增多,给钻井安全带来了考验,特殊的油气田迫切需要抗腐蚀的钻杆。
CO2的腐蚀主要是CO2气体溶于钻井液后形成酸性介质,对钻杆产生电化学腐蚀。
CO2含量高的油气田主要分布在加拿大北部,我国的江苏地区也有CO2含量高的油气田。
日本的JFE钢铁株式会社针对这样的油气田率先研制出JFE-13Cr马氏体不锈钢钻杆,产品不但具有更高的强度和卓越的抗腐蚀特性,而且还具有良好的低温韧性。
H2S气体的危害要远远大于CO2,H2S气体在溶于钻井液后形成弱酸并释放出H+,H+浓度增大后会渗透到钻杆内部形成“氢脆”使钻杆的冲击韧性大大降低,在很短的时间内突然断裂,危害性非常大。
H2S气体还是一种有毒有害气体,人在少量闻到时会产生恶心、头晕、眼痛等症状,大量的H2S可以致人死亡。
我国的H2S气田主要分布在四川省,在四川的开县和河北的赵县都曾发生过因井控不当,造成H2S气体泄露危害周围村民致死的事故。
所以说研制和应用抗S钻杆成为减小钻井风险、保障生产安全的必然趋势。
以前我国使用的抗S钻杆主要是从美国格兰特公司和德国曼内斯曼公司进口,近几年我国的钻杆生产企业也在开发研制抗S钻杆,代表的厂家有渤海能克钻杆有限公司和上海宝钢。
抗S钻杆的研制主要从两个方面入手,一是从原材料自身的特性出发,开发新钢种,如添加能有力对抗S的Cr和Al等元素,减少对抗S不利的Mn和Ni等元素,进一步提高钢的纯净度。
另一方面是从热处理工艺入手,相同化学成分的钢材,通过不同的热处理条件可以获得不同的金相组织以达到抗S的目的。
随着我国高酸性气田的逐步开发和钻井技术的进步,空气钻井和欠平衡钻井等技术被大量应用,抗腐蚀钻杆的需求越来越多,国内各油田迫切需要“经济型”的抗腐蚀钻杆。
5.4高强度钻杆目前API系列钻杆强度最高的是S135级,但随着钻井深度的不断增加,对钻杆强度的要求也在不断提高。
宝鸡石油机械有限责任公司已研制成功9000m钻机,需要相应强度的钻杆与之配套,2007年在塔里木完钻的塔深1井井深高达8400m。
在这样的情况下,油田需要V150级甚至V170级的钻杆来提供更大的动力,从而满足石油勘探超深井的钻井需要。
5.5复合材料钻杆由于钻杆在使用中对腐蚀性、冲击韧性、钻杆质量等提出了各种各样的要求,人们开始关注非钢钻杆的开发。
复合钻杆通过在卷筒上缠绕碳纤维然后应用一种环氧基复合材料覆盖并密封而成。
目前生产复合钻杆的成本大约是常规钢钻杆的3倍,但其优势在于质量轻,具有高强度质量比,超高的抗腐蚀能力和抗疲劳能力。
阻碍复合材料钻杆推广的原因在于:复合钻杆的壁厚可能要达到常规钢钻杆壁厚的2倍,这将明显降低钻杆的内径从而导致压力损失。
5.6内平外加厚钻杆由于塔里木油田的钻井需要,塔里木工程技术部牵头,委托宝山钢铁公司、渤海能克钻杆公司、西南石油学院共同合作开发出新型内平外加厚钻杆。
顾名思义,它是改变原有过渡带的形式,降低内过渡,增大外过渡。