高速棒材轧制技术
棒材切分轧制工艺

郭宝峰
学习目标
1、让大家对切分轧制工艺有个初 步的认识。
2、理解切分轧制的概念、意义。 3、了解实际生产过程中的注意事
项。
切分轧制的概念
• 所谓切分轧制,就是在轧制过程中把一根 轧件利用孔型和导卫的作用,轧成具有两 根或两根以上相同形状的并联轧件,再利 用切分设备或轧辊的辊环将并联的轧件沿 纵向切分成两个或两个以上的单根轧件, 这些切分后的轧件有的可直接作为成品, 有的则作为中间坯继续在线同时进行轧制。 根据切分后形成轧件的数目多少,又可分 为二切分、三切分、四切分、五切分等。
四切分工艺概况
切分轧制对温度的要求
• 承钢各线均配备侧进侧出双蓄热步进 式加热炉,坯料165*165*118000,切分 开轧温度控制在1030-1150之间,或高 或低均会引起切分轮故障,即温度低 切分负荷重,切分轴承容易坏,温度 高切分刀容易粘铁,切分终轧温度不 低于850℃。
温度高低对轧制的影响
• 轧机全部使用短应力机型,一般配套120米冷床, 3#剪和冷床距离为120米,即与冷床长度1:1设计。 我们由于地形限制,冷床96米,上冷床距离63米, 这将成为制约提速的关键问题。
切分轧制工艺的意义
1、不同规格产品的生产能力基本均衡。因为 炼钢连铸能力相对稳定,而轧钢能力因为 生产规格不同波动大,特别是小规格棒材 产量低。采用切分工艺可以使多种规格棒 材的轧制能力基本相等,同时,对于轧钢 工序来说,可使加热炉、轧机、冷床及其 它辅助设备的生产能力充分发挥。
• 棒材切分轧机区的设计一般采用18架布置,即 6+6+6,粗中精各6架。粗中轧平立交替无扭轧制, 精轧16、18架平立可转换,轧单线时全部平立交 替无扭轧制。切分时,16、18架为平轧,13架平 辊,14架立轧,15架预切,16架切分,17架成前 扭转后经活套进入18架成品。也有19架的,预切 分为两架。
棒材直接轧制打捆工艺及装备

棒材直接轧制打捆工艺及装备赵辉1,2① 许鑫1,2(1:北京首钢国际工程技术有限公司 北京100043;2:北京市冶金三维仿真设计工程技术研究中心 北京100043)摘 要 棒材直接轧制打捆工艺可以减少设备和土建投资,降低生产成本,提高成材率和作业效率。
分析了达涅利公司棒材直接轧制打捆技术的特点及优势。
同时,介绍了棒材直接轧制打捆技术的典型工艺布置和关键设备。
最后针对该技术在国内的推广应用给出了合理化建议。
关键词 直接轧制打捆;棒材;工艺与装备中图法分类号 TG335.6 文献标识码 ADoi:10 3969/j issn 1001-1269 2024 01 010DirectRollingandBundlingProcessandEquipmentofBarZhaoHui1,2 XuXin1,2(1:BeijingShougangInternationalEngineeringTechnologyCo.,Ltd.,Beijing100043;2:MetallurgicalEngineering3 DSimulationDesignEngineeringTechnologyResearchCenterofBeijing,Beijing100043)ABSTRACT Thedirectrollingandbundlingprocessofbarscanreduceequipmentandcivilengineeringinvestment,reduceproductioncosts,andimproveyieldandoperationalefficiency.ThetechnicalcharacteristicsandadvantagesofbardirectrollingandbundlingtechnologyofDanieliCompanyareanalyzed.Meanwhile,thetypicallayoutandkeyequipmentsofbardirectrollingandbundlingtechnologyareintroduced.Finally,reasonablesuggestionsaregivenforthepromotionandapplicationofthistechnologyinChina.KEYWORDS Drietrollingdundling;Bar;Technologyandequipment1 前言直接轧制打捆工艺(Directrollingandbundlingprocess(DRB))是一种具有革命意义的创新技术,该技术使传统的倍尺棒材冷却用长冷床和相应的冷定尺剪切设备不再需要,使普通钢种直条棒材生产技术发生划时代的巨大变化。
棒材20螺2线切分轧制技术的开发与应用
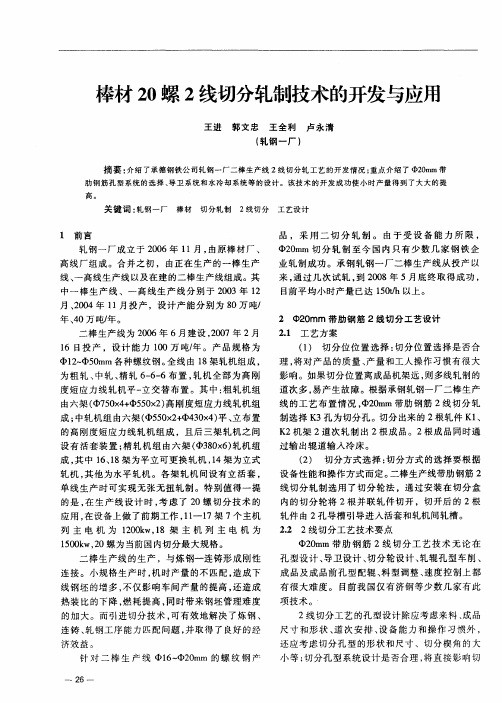
关键 词 : 轧钢一厂 棒材 切分轧制 2 线切分 工艺设计
பைடு நூலகம்1 前 言
品 ,采 用 二 切 分 轧 制 。 由 于 受 设 备 能 力 所 限 ,  ̄2 mm 切 分 轧 制 至 今 国 内 只有 少 数几 家 钢 铁 企 0 业 轧 制 成 功 。承 钢 轧 钢一 厂 二 棒 生产 线 从 投产 以
的高 刚 度短 应力 线 轧 机组 成 ,且后 三 架 轧机 之 间
设 有 活 套装 置 ; 轧机 组 由六 架 ( 8 x ) 机 组 精  ̄3 0 6 轧
道次多 , 易产 生故 障。根 据 承钢 轧钢 一厂 二棒 生产
线 的工 艺 布 置 情 况 , 0 m 带肋 钢 筋 2线 切 分 轧  ̄2 m 制 选 择 K3孔 为切 分 孔 。切 分 出来 的 2根 轧件 Kl 、 K 2机架 2道 次轧 制 出 2根 成 品 。2根成 品 同时通 过 输 出辊 道输 入 冷床 。 ( ) 切分 方 式选 择 : 分 方式 的选 择 要 根据 2 切 设 备 性 能 和操作 方 式而 定 。 二棒 生产线 带肋 钢筋 2 线 切分 轧制 选 用 了 切分 轮 法 ,通 过 安装 在 切 分 盒 内的切 分 轮 将 2根 并 联 轧 件切 开 ,切开 后 的 2根 轧件 由 2孔 导槽 引导进 入 活套 和轧 机 间轧槽 。 22 2线切 分 工艺 技 术要 点 .  ̄2 m 带 肋 钢 筋 2线 切 分 工 艺 技 术 无 论 在 0m
21 工艺 方 案 .
( ) 切 分 位 位 置选 择 : 分位 置选 择是 否 合 1 切 理 , 对 产 品的 质量 、 量 和工 人操 作 习惯 有 很 大 将 产
影 响 。如 果切 分 位 置离 成 品机架 远 , 多线 轧 制 的 则
微张力轧制的控制与研究
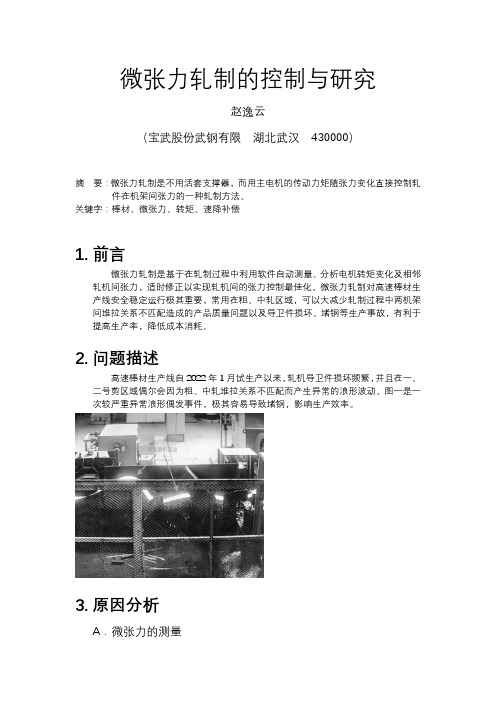
微张力轧制的控制与研究赵逸云(宝武股份武钢有限湖北武汉430000)摘要:微张力轧制是不用活套支撑器,而用主电机的传动力矩随张力变化直接控制轧件在机架间张力的一种轧制方法。
关键字:棒材、微张力、转矩、速降补偿1.前言微张力轧制是基于在轧制过程中利用软件自动测量、分析电机转矩变化及相邻轧机间张力,适时修正以实现轧机间的张力控制最佳化。
微张力轧制对高速棒材生产线安全稳定运行极其重要,常用在粗、中轧区域,可以大减少轧制过程中两机架间堆拉关系不匹配造成的产品质量问题以及导卫件损坏、堵钢等生产事故,有利于提高生产率,降低成本消耗。
2.问题描述高速棒材生产线自2022年1月试生产以来,轧机导卫件损坏频繁,并且在一、二号剪区域偶尔会因为粗、中轧堆拉关系不匹配而产生异常的浪形波动。
图一是一次较严重异常浪形偶发事件,极其容易导致堵钢,影响生产效率。
3.原因分析A.微张力的测量图二是微张力的测量示意图,当轧件通过N架轧机时,N架轧机咬钢时,计算机对N架轧机的电机转矩进行检测和储存,作为无张力转矩值;当N+1架轧机咬钢后,再检测和储存N架轧机的电机转矩。
B.微张力轧制的实现高速棒材生产线粗、中轧的各组机架间一般都由微张力控制来完成轧件的轧制,其大多是通过主传动电机转矩比较法来实现的。
具体实现原理如下:在轧件进入相邻下一个轧机之前和之后,在轧机主传动电机达到稳定运行状态的前提下,分别对本架电机的转矩值进行测量并储存,并通过比较的差值来反映堆钢、拉钢以及堆拉钢的程度,然后再由对本机架速度的调整来使转矩的差值达到允许范围以内,这个调节过程只能在轧件于各机架间的穿料过程中才能进行。
调节过程中还要对原速度设定值进行修正,然后将修正后的值储存起来,作为下一根轧件的初始设定。
C.微张力的影响因素微张力的计算容易受到电机转矩波动影响,导致其计算不准确。
轧机在轧件咬入瞬间会受到冲击使得电机的转速有一个动态降低过程,此过程会导致轧件头部产生不规则形变,轧件头部粗细不均又会导致电机转矩不合理波动。
棒材工艺轧制原理

• 热轧生产线:热轧生产线主要包括加热炉、轧机、冷却设备等 • 冷轧生产线:冷轧生产线主要包括矫直机、剪切机、冷床等 • 在线轧制生产线:在线轧制生产线主要包括连轧机、飞剪、卷取机等
棒06材工艺轧制技术的发展与展 望
棒材工艺轧制技术的 最新进展
• 棒材工艺轧制技术的最新进展 • 高性能轧制技术:通过优化轧制工艺,提高金属的力学性能和 表面质量 • 智能化轧制技术:利用计算机技术和传感器技术,实现轧制过 程的自动化和智能化 • 环保节能轧制技术:通过优化生产工艺和设备,降低能源消耗 和环境污染
棒材工艺轧制技术的未来挑战
• 技术难题:解决棒材工艺轧制过程中的技术难题,提高 产品质量和生产效率 • 市场竞争:应对市场竞争,提高棒材工艺轧制技术的竞 争力和市场份额
THANK YOU FOR WATCHING
谢谢观看
棒材工艺轧制的基本原理及其影响因素
棒材工艺轧制的基本原理
• 金属在塑性变形过程中的晶格位错和滑移 • 通过改变金属的晶粒形状和晶粒大小来实现塑性变形
棒材工艺轧制的影响因素
• 轧制温度:影响金属的塑性和流动性 • 轧制速度:影响金属的变形速度和冷却速度 • 轧制压力:影响金属的变形程度和密度 • 轧制间隙:影响金属的变形均匀性和表面质量
轧制间隙的调整
• 自动调整:通过自动控制系统实时调整轧制间隙 • 手动调整:根据轧制过程中的实际情况手动调整轧制间 隙
棒03材工艺轧制过程中的组织性 能变化
轧制过程中的微观组织演变
金属在轧制过程中的微观组织变化
• 晶粒形状和大小的变化:轧制过程中晶粒逐渐拉长,晶 粒大小减小 • 晶格位错和滑移的产生:轧制过程中晶格位错和轧制技术的发展趋势 • 高生产效率:提高轧制速度,提高生产效率,降低生产成本 • 高质量:提高金属的力学性能和表面质量,满足市场需求 • 环保节能:降低能源消耗和环境污染,实现可持续发展
棒线材MI.DA.无头轧制技术介绍

棒线材MI.DA.无头轧制技术介绍赵辉1,2①(1:北京首钢国际工程技术有限公司 北京100043;2:北京市冶金三维仿真设计工程技术研究中心 北京100043)摘 要 本文主要介绍MI.DA.无头轧制技术以及国内应用现状。
以山西建邦MI.DA.生产线为例,详细介绍了MI.DA.无头轧制的生产工艺和装备,总结了MI.DA.无头轧制技术的优缺点,为今后国内新建类似项目给出建议。
关键词 无头轧制 棒材 线材 MI.DA.中图法分类号 TG333 TG335.1 文献标识码 BDoi:10 3969/j issn 1001-1269 2023 06 025IntroductiontoMI.DA.HeadlessRollingTechnologyofBarandWireZhaoHui1,2(1:BeijingShougangInternationalEngineeringTechnologyCo.,Ltd.,Beijing100043;2:MetallurgicalEngineering3-DSimulationDesignEngineeringTechnologyResearchCenterofBeijing,Beijing100043)ABSTRACT MI.DA.headlessrollingtechnologyanditsdomesticapplicationstatusareintroduced.TakingShanxiJianbangMI.DAproductionlineasanexample,theproductionprocessandequipmentofMI.DAheadlessrollingareintroducedindetail,theadvantagesanddisdvantagesofMI.DAheadlessrollingtechnologyaresummarized,andsuggestionsaregivenfornewsimilarprojectsinChinainthefuture.KEYWORDS Headlessrolling Rod Wire MI.DA.1 前言节能降本一直是我国钢铁企业追求的目标,如何在保证产量的同时,降低生产成本,无头轧制工艺是一个很好的选择。
棒材厂无槽轧制技术研发应用
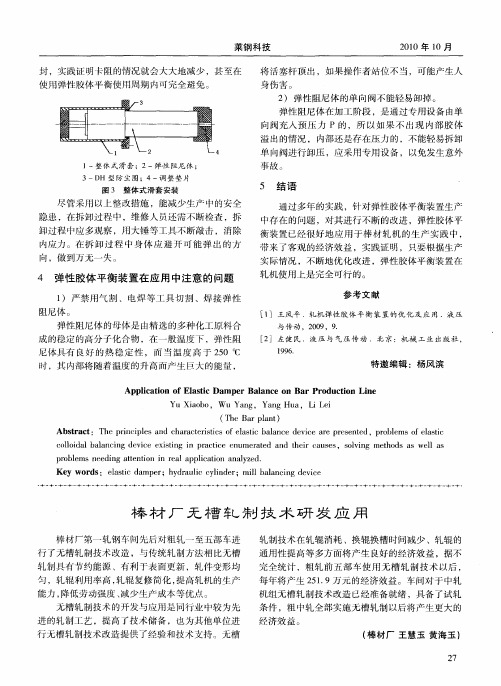
无 槽轧 制技 术 的开 发与 应用 是 同行业 中较为 先
每年 将产 生 2 19万 元 的经 济效 益 。车 间对 于 中轧 5.
机 组 无槽 轧制 技术 改造 已经准 备就 绪 ,具备 了试轧 条件 ,粗 中轧 全 部实施 无 槽轧 制 以后将 产 生更 大 的 经 济效 益 。 ( 材 厂 王 慧玉 黄海 玉 ) 棒
行 了无 槽轧 制技 术 改造 ,与将产 生 良好 的经 济效 益 ,据不
完 全 统计 ,粗 轧 前 五 部 车使 用无 槽 轧 制 技 术 以后 ,
轧制具有节约能源 、有利于表面更新 ,轧件变形均 匀 ,轧 辊利 用率 高 , 轧辊 复修 简 化 , 提高 轧机 的生 产
・+ ・
・+ ・
・+ ・
“+
・+ ・
・+ ・
・+ ・
. . +
・+ ・
・+ ・
”+
・— ・+ ・- ■ ・
“+
・+ ・
・+ -
・+ ・
“
”+
“+
”
一+
・+ ・
棒 材 厂 无 槽 轧 制 技 术 研 发 应 用
棒 材 厂第一 轧 钢 车问 先后 对粗 轧一 至 五部 车进 轧制 技术 在 轧辊 消耗 、换 辊 换槽 时 问减少 、轧辊 的
参考 文 献
[ ] 王凤 平 .轧机弹性胶体 平衡 装置的优 化及 应 用 .液压 1
与传 动 ,2 0 0 9,9 .
尽管 采用 以上 整 改措施 ,能减 少生 产 中 的安全
隐患 ,在 拆卸 过程 中 ,维 修人 员还 需不 断检 查 ,拆 卸过 程 中应 多 观察 ,用 大锤 等 工具 不断 敲击 ,消除
棒材轧制(生产)工艺

目录热轧带肋钢筋的生产工艺及车间设计摘要:从工艺配置,设备选型,工艺控制,平面布置,设备等多方面介绍了热轧带肋钢筋的生产工艺及车间平面布置的情况,并提供了热轧线上主要机组的工艺技术参数。
关键词:热轧带肋钢筋,工艺,平面布置,设备。
Abstract: Focused on the process configuration, equipment selection, process control, layout, equipment, etc., and introduces the rolled ribbed bars production craft and workshop layout, and provides the hot line of main technical parameters.Key words:Rolled ribbed bars, craft, layout, equipment。
第一张热轧带肋钢筋国内外发展概况及建厂的必要性与可行性分析1.1螺纹钢筋市场分析与前景展望螺纹钢筋广泛应用于普通混凝土结构和预应力混凝土结构,是房屋、桥梁、隧道、水坝、桩基等建筑设施的重要材料,在国民经济中占有极其重要的地位,是我国重点发展和研究的钢材品种之一。
目前,我国有四十多个厂家生产螺纹钢筋,产量逐年上升,1982年全国总产量近166万吨,除了满足国内需要外,近年来出口钢筋数量迅速增加,1981年为18万吨,1982年约30万吨;1983年预计可达35万吨。
国内生产的螺纹钢筋,规格有小6一小40毫米,其中小40毫米规格主要供出口。
钢筋的强度级别主要为GB1499一79标准规定的1级和l级钢筋。
W级钢筋产量较低。
目前,各厂家生产螺纹钢筋的工艺,基本上为热轧、随后在冷床上空冷的传统流程。
控制轧制尚未应用于生产。
仅有少数厂家开展了轧后控制冷却工艺的试验生产。
螺纹钢筋的纹型,国内l、l 级钢筋大部分按首钢、唐钢和冶金部建筑研究总院共同制定的《热轧月牙纹钢筋技术条件》生产纵横筋不相交的月牙纹钢筋,少数仍采用国际规定的人字纹型;F级钢筋则采用不带纵筋的连续螺旋型。
高速线材与棒材轧制工艺参数优化与质量控制研究

高速线材与棒材轧制工艺参数优化与质量控制研究新疆乌鲁木齐市830000摘要:本研究致力于高速线材与棒材的轧制工艺参数优化与质量控制。
通过深入分析材料的物理特性和轧制过程的影响因素,结合先进的数值模拟方法,对高速线材与棒材的轧制工艺进行了系统研究与分析。
在此基础上,通过设计合理的工艺参数,并引入先进的质量控制手段,实现了产品质量的提升和稳定生产。
研究结果表明,优化的工艺参数能够显著改善材料的力学性能和表面质量,为相关行业的生产提供了有力支撑。
关键词:高速线材、棒材、轧制工艺、参数优化、质量控制引言:在金属加工领域,高速线材与棒材的制造工艺一直备受关注。
然而,如何在保障质量的前提下优化工艺参数,以实现更好的力学性能和表面质量,仍是一个挑战。
本文聚焦于高速线材与棒材的轧制工艺,结合先进的数值模拟和质量控制方法,旨在找到创新性的解决方案。
通过深入研究材料特性与工艺影响,我们迈向了产品质量提升与稳定生产的目标,为相关领域的技术发展和实际应用注入新的活力。
一材料特性与工艺关联分析在金属加工领域,高速线材与棒材的制造工艺一直是追求高质量和高效率的关键挑战。
为了实现优化的工艺参数和最终的产品质量,深入了解材料特性与工艺之间的关联显得尤为重要。
材料特性,包括金属的组织结构、硬度、塑性等,直接影响产品的力学性能和表面质量。
而工艺参数,如轧制温度、轧制速度、压下量等,则对材料的组织和性能产生深远影响。
研究发现,材料特性与工艺参数之间存在着紧密的相互作用。
首先,材料的组织结构与力学性能对工艺参数的选择具有明显影响。
例如,不同的轧制温度可以导致晶粒尺寸和取向的变化,从而影响材料的强度和延展性。
其次,工艺参数的优化可以通过调整材料的应力分布来改善其性能。
例如,在轧制过程中适当的压下量可以促使材料发生塑性变形,从而减小内部应力,提高抗疲劳性能。
此外,工艺参数还会影响材料的表面质量,如轧制速度的增加可能会导致表面粗糙度的提高。
线棒材无头轧制技术

线棒材无头轧制技术摘要:在目前的钢铁行业生产中,线棒材构成了其中很关键的生产对象。
具体在制造以及生产线棒材时,企业通常都需要借助无头轧制的措施予以完成。
因此在现阶段的钢材生产中,针对无头轧制有关的线棒材加工措施仍需着眼于全方位的运用,因地制宜探求可行的技术改进举措。
关键词:线棒材;无头轧制;具体技术早在上世纪末,无头轧制技术就已经诞生。
从当前现状来看,无头轧制工艺已经能够灵活运用于现阶段的冷轧工艺、酸洗工艺、连续退火工艺与其他工序生产。
近些年以来,无头轧制工艺正在被更多用来制造线棒材,其中涉及到连续性的钢坯焊接方式以及其他生产工艺。
相比而言,无头轧制技术本身具备更优的设备利用效率以及更高的线棒材产能特征,与此同时还能显著减少轧制线棒材耗费的资金与其他资源。
针对不同种类的线棒材而言,与之相适应的无头轧制工艺也应当体现为差异性。
因此在实践中,企业有必要结合当前的线棒材生产状况来灵活选择合适的轧制工艺方式,从而保证达到最优的节能生产实效性。
一、无头轧制工艺的基本技术特征无头轧制工艺,指的是运用一次咬入的方式来加工坯料或者轧件,其中涉及到连续性的轧制操作。
对于轧件在连续轧制的前提下,确保其呈现磨损的轧辊状态,而不能够继续予以轧制操作。
因此可见,无头轧制工艺相比而言更加能够显著缩短轧制操作有关的操作间隔,对于特定时间段内的轧制操作实效性也能够得以显著优化。
与此同时,运用无头轧制的方式也有助于避免轧机频繁受到轧件给其带来的冲击,从而在根源上减少了备件与设备的损耗。
近些年以来,无头轧制工艺正在逐步受到更多企业的青睐与认同。
究其根源,就在于此类工艺本身具备优良的稳定性,因此尤其能够适用于轧制板材、线棒材以及其他种类的钢材。
在此前提下,运用无头轧制的措施还能消除较大的轧制尺寸偏差,从而保障了轧制钢件符合最优的稳定性与张力特征。
通常来讲,对于某些适合用于无头轧制的钢材或者其他材料都要全面保证其符合连续性的轧制操作特征,从而妥善连接各个轧制操作工序。
棒材直接轧制

棒材直接轧制1. 引言棒材直接轧制是一种常见的金属加工方法,用于将金属坯料通过轧制工艺加工成具有特定形状和尺寸的棒材产品。
这种加工方法广泛应用于钢铁、铝合金、铜合金等金属材料的生产中,具有高效、经济、灵活等优点。
本文将对棒材直接轧制的工艺流程、设备和应用领域进行详细介绍。
2. 工艺流程棒材直接轧制的工艺流程通常包括原料准备、预轧制、精轧制、冷却和整形等步骤。
2.1 原料准备原料准备是棒材直接轧制的第一步,主要包括选择合适的金属材料、切割成适当的坯料尺寸和加热处理等操作。
金属材料的选择应根据产品的要求和生产成本进行综合考虑,常见的金属材料有碳钢、不锈钢、铝合金等。
切割成适当尺寸的坯料可以提高轧制效率和产品质量。
加热处理可以改善金属的塑性和可加工性。
2.2 预轧制预轧制是棒材直接轧制的第二步,主要目的是通过辊道的压力和摩擦力将坯料逐渐塑性变形成较小的截面尺寸。
预轧制可以提高轧制效率、减少轧制力和改善产品表面质量。
预轧制通常采用多道次的轧制,每道次的辊道间隙逐渐减小,使坯料逐渐变形。
2.3 精轧制精轧制是棒材直接轧制的第三步,主要目的是进一步减小截面尺寸、提高产品的表面质量和机械性能。
精轧制通常采用单道次的轧制,辊道间隙较小,轧制力较大。
精轧制过程中需要控制轧制温度、轧制速度和轧制力等参数,以保证产品的质量和尺寸精度。
2.4 冷却和整形冷却和整形是棒材直接轧制的最后一步,主要目的是通过冷却和整形工艺使产品获得所需的形状和尺寸。
冷却可以改善产品的力学性能和表面质量,通常采用水冷或空冷方式。
整形包括切割、修直、打标等操作,以满足产品的需求。
3. 设备棒材直接轧制需要使用一系列专用设备,包括轧机、辊道、传动系统、冷却系统和控制系统等。
3.1 轧机轧机是棒材直接轧制的核心设备,用于通过辊道的压力和摩擦力将金属坯料塑性变形成棒材产品。
轧机通常由上辊和下辊组成,辊道间隙可以调节,以适应不同的轧制需求。
轧机的类型和规格根据产品的要求和生产能力确定。
Φ14棒材生产中三切分轧制技术研究

Φ14棒材生产中三切分轧制技术研究摘要:本文叙述了棒材生产中φ14螺纹钢三切分的工艺选择、调试时出现的问题、改进方案及效果。
关键词:螺纹钢三切分工艺方案1、前言切分轧制是在轧机上利用特殊的轧辊孔型和导卫或者其他切分装置,将原来的一根坯料纵向切成两根以上的轧件,进而轧制多根成品或中间坯的轧制工艺。
采用切分轧制技术可缩短轧制节奏,提高机时产量,显著提高生产效率,降低能耗和成本。
目前切分轧制技术已发展到五切分轧制,且两线切分轧制技术和三线切分轧制技术作为成熟技术已经普遍应用在小规格螺纹钢的生产中。
本文所述棒材厂从2005年开始逐步应用切分轧制技术,现已成功开发了φ14、φ16、φ18螺纹钢二切分、φ12螺纹钢三切分轧制技术。
2010年,为了实现147万吨的年产量目标,棒材厂决定充分发挥切分技术的产能优势,在ф12螺纹钢三切分的基础上实施ф14螺纹钢的三切分轧制。
2、设备配置情况车间的工艺布置为粗轧7架平轧闭口轧机、中轧为平立交替的6架两辊闭口轧机、精轧为平立交替6架预应力轧机。
、3、工艺方案的选择3.1 工艺布局的确定在φ12螺纹三切工艺和φ14螺纹两切分工艺的经验基础上,对一道预切与两道预切的方案进行了比较:如采用一道预切,则预切分孔(k4)的压下和延伸比较大,轧制负荷大、轧制不稳定,且其切分楔处的压下系数远大于槽底的压下系数,造成切分楔处磨损严重;来料进预切分孔时的对中性差,进而导致预切料型进切分孔时不均匀,这样3支成品之间的尺寸不均匀,负差也不易控制。
采用两道预切,可减小k4孔(第二道预切)的变形量,降低k4孔的轧制负荷,减轻其变形不均匀性,提高轧制稳定性;同时带有凹陷部位的来料进k4孔时,容易对中,对轧辊切分楔的冲击较小,成品尺寸较均匀;由于k4变形系数小,故改变k4的压下量对轧件的断面面积影响较小,降低了成品尺寸随k4料型变化而变化的敏感性,提高了轧制的稳定性及料型调整的方便性和精确性。
3.2 孔型设计切分工艺的孔型设计中预切分和切分孔的设计尤为重要,其次是立箱孔型,这几道次的孔型设计,关系到切分轧制是否能成功。
高速钢轧辊的特征及使用技术要求

高速钢轧辊的特征及使用技术要求目前人们所称的高速钢轧辊均为高碳高速钢复合轧辊,即轧辊的工作层材料采用高碳高速钢,轧辊的芯部材料采用球墨铸铁、石墨钢或锻钢等,两种不同的材料通过离心铸造或者是采用CPC工艺复合而成,与传统的M2、M4等标准类型钨钼高速钢有着本质上的区别。
在正常的轧制条件下,高速钢轧辊的使用寿命是合金铸铁轧辊3倍以上。
一、高速钢轧辊的特点1、高速钢轧辊含碳量较高,而且含有较高的钒、铬、钨、钼、铌等合金元素,因此,轧辊组织中碳化物的类型以MC型和M2C型为主,碳化物硬度高、耐磨性好。
2、高速钢轧辊具有较好的热稳定性,在轧制温度下,辊面具有较高的硬度和良好的耐磨性。
3、高速钢轧辊具有良好的淬透性,从辊身表面到工作层内部的硬度几乎不降,从而确保轧辊从外到内具有同等良好的耐磨性。
4、轧辊使用过程中,在良好的冷却条件下,辊身表面形成薄而致密的氧化膜,这种均匀、薄而致密的氧化膜长时间存在而不脱落,使得高速钢轧辊耐磨性得到显著提高。
5、高速钢轧辊在轧制时辊面氧化膜的形成,降低了轧材与辊面间的磨擦,因此在轧制过程中易引起打滑现象,使轧机调整难度增加。
6、高速钢材料膨胀系数大,导热性能好,在轧制时易引起辊形变化,影响轧材精度。
因此,高速钢轧辊在板带材轧机上使用时,不仅要改变冷却系统的设计,而且还要重新改变辊形的设计。
7、由于高速钢轧辊芯部采用合金球墨铸铁、石墨钢或者是锻钢等材料制成,因此轧辊辊颈强度高。
8、由于高速钢材料耐磨性好、抗事故能力差,因此高速钢轧辊使用效果的好坏不仅取决于高速钢轧辊本身的质量,而且更重要取决于轧辊的使用条件和轧辊的维护保养。
二、高速钢轧辊的加工轧辊的硬度提高后,轧辊的加工难度相应就增加,对用于线、棒材轧机高速钢轧辊的孔型加工,特别是轧制螺纹钢轧辊在重复使用时的切削加工,由于是断续切削,其加工难度更大,因此选用合理的加工刀具和切削用量是决定高速钢轧辊能否在线棒材轧机上正常使用的先决条件。
轧制概述与工艺

本课程讲授的主要内容: ●轧制概述 ●轧制过程中的力学概述
●轧制过程中的金属变形
●轧制后续的处理技术及设备概述
2
轧制概述
1.轧制概述 2.我国轧钢技术发展 3.无头轧制技术 4.今后我国轧钢领域的发展方向
3
绪论
轧制过程是由轧件与轧辊之间的摩擦力将轧件拉 进不同旋转方向的轧辊之间使之产生塑性变形的过程。
轧制新技术新工艺概述
新一代TMCP技术 无头轧制技术
边部温度控制技术 连铸坯热送热装 无酸洗除鳞技术 板厚、板形自动控制系统 轧制-激光焊接技术
宽厚板轧制
● ● ● ● -
热连轧
● ● ● ● ● -
38
冷轧 棒线材轧制
-
●
-
●
-
-
-
●
●
-
●
-
●
-
39
4.今后我国轧钢领域的发展方向 轧钢领域要向提高热装温度和热装率,开
——咬入角,轧件被咬入轧辊时轧件和轧辊最先
接触点(实际上为一条线)和轧辊中心的连线与 两轧辊中心连线所构成的角度;
l——接触弧长的水平投影,也叫变形区长度;
F ——接触面水平投影面积,简称接触面积;
l/hm ——变形区形状参数,hm=(H+h)/2(变形
区平均高度)。
简单轧制(理想轧制)
为了便于进行研究分析,对一些轧制条件作出假设和
4
金属材料尤其是钢铁材料的塑性加工,90%以上是通过 轧制完成的。由此可见,轧制工程技术在冶金工业及国民 经济生产中占有十分重要的地位。
5
轧制工艺按照产品类型可以分为板带轧制、管材轧 制、型材轧制以及棒、线材轧制四种基本类型;按生 产工艺可以分为热轧和冷轧工艺;按厚度可分为薄板 ( 厚 度 <4mm) 、 中 板 ( 厚 度 4~20mm) 、 厚 板 ( 厚 度 20~60mm)、特厚板(厚度>60mm,最厚达700mm)。 在实际工作中,中板和厚板通称为“中厚板”。
轧钢棒线材生产技术创新研究

轧钢棒线材生产技术创新研究【摘要】钢铁工业的飞速发展,为用户提供了充足的钢铁产品,使得国内钢材市场逐渐由卖方市场向买方市场过渡。
为了提高市场竞争能力,必须在提高产品质量的同时,降低生产成本,加大企业技术进步,大胆应用近年来出现的新技术、新设备、新工艺,这无疑是增强其竞争能力的有效手段。
棒线材生产已有 200 多年的历史。
尽管板带钢产品比重迅速增加,其生产技术日趋完善,生产成本显著下降,但是棒线材产品仍然占据其独有而不可取代的地位。
正是由于这个原因,其生产技术发展水平正日新月异地飞速发展。
本文主要针对轧钢棒线材生产技术问题进行分析和讨论,望与同行之间交流探讨。
关键词:钢材生产;轧钢技術;棒线材;新技术1轧钢棒线材市场现状目前我国棒线管材行业企业的技术装备水平得到较大提高,特别是二十世纪九十年代以来,我国钢铁工业获得了长足进步:新建的一大批具有世界先进水平的大型高炉、大型转炉和电炉、炉外精炼、连铸、热连轧、冷连轧、涂镀层生产线、冷轧硅钢生产线、高速线材轧机、连续小型棒材轧机的建成投产等,使我国棒线材管行业的装备水平有了显著提高。
特别是我们正在进行的为配合我国家电、轿车、石油、建筑、造船等行业走向世界,钢铁行业“十五”技术改造完成后,再经过“十一五”的努力,我国整个棒线材管工业的工艺和装备水平将会发生新的质的飞跃。
2轧钢棒线材生产工艺概述我国钢铁行业“量喜质忧”现状,表明了相对炼铁和炼钢技术而言,现有的轧钢技术发展相对落后。
因此,加强轧钢技术研究和轧钢专用设备研发,对提升我国钢材整体质量乃至推动钢铁工业进步具有十分重要的意义。
轧钢技术环节,轧钢技术水平和特点主要体现在提高产品质量及附加值、提高生产效率、扩大产品品种、降低成本、节能降耗和环保等方面,以满足下游领域对钢材质量的严格要求。
因此,轧钢技术水平和装备等级是钢铁企业提高产品质量和降低能耗的一个重要环节。
第一,有利于提高钢材质量。
通过精确设计和提高轧机导卫装置装备水平能最大限度解决现有钢材产品在外形、尺寸(直径)等方面存在的问题;通过测径、测温、智能控制轧制系统的研发和装备投入能够大幅降低现有钢材产品在尺寸、面瑕疵方面存在的问题。
轧钢厂棒材工艺流程
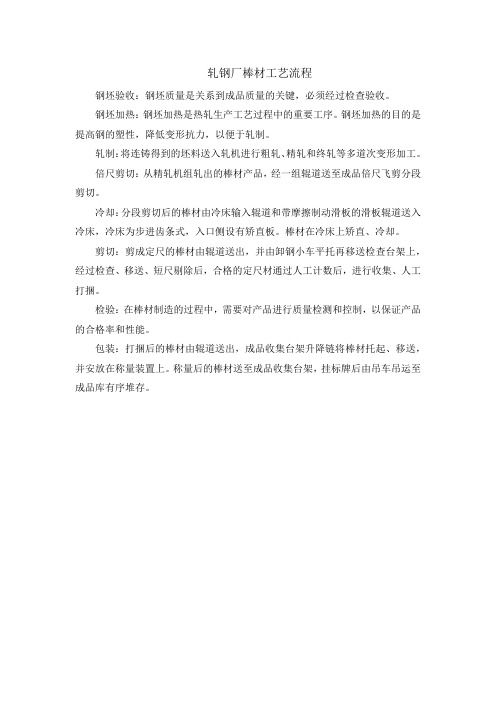
轧钢厂棒材工艺流程
钢坯验收:钢坯质量是关系到成品质量的关键,必须经过检查验收。
钢坯加热:钢坯加热是热轧生产工艺过程中的重要工序。
钢坯加热的目的是提高钢的塑性,降低变形抗力,以便于轧制。
轧制:将连铸得到的坯料送入轧机进行粗轧、精轧和终轧等多道次变形加工。
倍尺剪切:从精轧机组轧出的棒材产品,经一组辊道送至成品倍尺飞剪分段剪切。
冷却:分段剪切后的棒材由冷床输入辊道和带摩擦制动滑板的滑板辊道送入冷床,冷床为步进齿条式,入口侧设有矫直板。
棒材在冷床上矫直、冷却。
剪切:剪成定尺的棒材由辊道送出,并由卸钢小车平托再移送检查台架上,经过检查、移送、短尺剔除后,合格的定尺材通过人工计数后,进行收集、人工打捆。
检验:在棒材制造的过程中,需要对产品进行质量检测和控制,以保证产品的合格率和性能。
包装:打捆后的棒材由辊道送出,成品收集台架升降链将棒材托起、移送,并安放在称量装置上。
称量后的棒材送至成品收集台架,挂标牌后由吊车吊运至成品库有序堆存。
棒材无孔型轧制技术

棒材无孔型轧制技术摘要:本文结合多年的工作经验棒材无孔型轧制技术与降低生产成本相结合来进行了钢铁企业的成本控制规划,并从负公差轧制带肋钢筋时,从控制加热供热温度,优化成孔设计方面进行了简要介绍。
实现钢铁企业向着国际化低成本、高效益的方向发展。
关键词:钢铁企业;棒材无孔型轧制技术;效益;成本控制;竞争一、棒材无孔型轧制技术上文提到棒材无孔型轧制技术能够降低生产成本,提高企业的经济效益,现将棒材无孔型轧制技术与孔型轧制技术进行对比,来说明棒材无孔型轧制技术能够降低生产成本的原因。
相对与孔型轧制技术,无孔型轧制具有轧件变形均匀、能耗低、轧槽及轧辊寿命高、轧辊车削简化、有利于成品质量等优点,是优化棒线材生产的轧制技术,目前国内一些棒材生产线已成功应用了此项技术。
通过上文对棒材无孔型轧制技术优势的介绍,我们知道此项技术是符合現代对节能的要求,是一种节能低耗的轧制技术。
运用棒材无孔型轧制技术可以将轧槽的使用寿命延长百分之四十,在很大程度上实现了对节能的要求。
为了从最大程度上提高钢铁企业的经济效益,我们可以利用同一机组多架轧机的特点,可将后面架次报废轧辊返修为平辊,用于前面架次轧机。
钢铁企业要想在行业中立于不败之地,首先应该严把质量关,当质量能够达到人们对钢材的要求时,钢材企业只是拿到了市场准入的资格,要想提高在行业间的竞争力,就必须提高企业的经济效益。
这就要从降低长本来入手。
在实现高质量的同时,以低价位来赢得市场占有率,提高本企业在钢材市场的占有率。
二、结合无孔型棒材技术等技术措施来降低钢材企业成本(一)上文已经提到棒材无孔型轧制技术具有很大的优势,可以使轧材具有更好的表面质量并且可以使不同胚料和工艺的适应性更强。
由于这种优势就解决了棒材在生产过程中有多种规格,施工工艺复杂的问题,大大提高了钢材企业的经济效益,降低了生产成本。
所以钢铁企业在实际生产过程中应该充分利用此项技术来降低生产成本,提高经济效益。
(二)钢铁企业可以建立高速连铸机,采用全连续流程作用,以此来降低生产周期,降低成本、提高经济效益。
棒材工艺教程轧制原理

棒材工艺教程:轧制原理1. 简介轧制是一种常用的金属加工工艺,用于将金属材料加工成条形、面板或棒材的形状。
棒材是一种常见的金属产品,广泛应用于建筑、制造和其他行业。
本教程将介绍棒材的轧制原理及相关工艺。
2. 轧制方法棒材的轧制主要有两种方法,分别是冷轧和热轧。
2.1 冷轧冷轧是指在常温下对金属进行轧制。
其主要工艺流程包括下述几个步骤:1.材料准备:选择适当的金属材料,并根据需要将其切割成合适的尺寸。
2.加热退火:将材料加热至一定温度,然后进行退火处理,以改善材料的塑性和可加工性。
3.直道轧制:将加热退火后的材料送入轧辊间,通过轧制机构的作用,将材料逐渐压制成所需的形状。
轧辊间的间隙可以根据需要进行调整,以控制棒材尺寸的精度。
4.冷却处理:轧制后的棒材需要进行冷却处理,以提高材料的强度和硬度。
5.切割定尺:将冷却后的棒材按照需要的长度进行切割。
2.2 热轧热轧是指在高温下对金属进行轧制。
其工艺流程与冷轧有所差异:1.加热:将金属材料加热至合适的温度,通常高于其再结晶温度。
高温能够提高金属的塑性,使得轧制更加容易进行。
2.轧制:将加热后的金属材料送入预热轧机中,通过轧辊的作用将材料压制成所需的形状。
3.冷却处理:热轧后的棒材需要进行冷却处理,以提高材料的强度和硬度。
4.切割定尺:将冷却后的棒材按照需要的长度进行切割。
3. 轧制原理3.1 原理介绍轧制原理可以简单地描述为:通过轧辊施加的力使金属材料发生塑性变形,从而改变其断面形状和尺寸。
轧制过程中,材料在轧辊间经历了挤压、剪切、弯曲等力的作用,最终实现了棒材的塑性变形。
3.2 轧辊和轧制力轧辊是轧机中最重要的部件之一,它们负责施加压力,并将材料引导到适当位置。
轧制力由辊缝、轧制速度、材料性质等因素决定。
对于冷轧,辊缝较小,轧制力会比热轧大;而对于热轧,辊缝较大,轧制力较小。
3.3 形变和再结晶轧制过程中,金属材料会发生塑性变形。
随着变形的进行,材料的应力和形变逐渐增加,超过一定程度后,材料内部会发生再结晶现象。
- 1、下载文档前请自行甄别文档内容的完整性,平台不提供额外的编辑、内容补充、找答案等附加服务。
- 2、"仅部分预览"的文档,不可在线预览部分如存在完整性等问题,可反馈申请退款(可完整预览的文档不适用该条件!)。
- 3、如文档侵犯您的权益,请联系客服反馈,我们会尽快为您处理(人工客服工作时间:9:00-18:30)。
高速棒材轧制技术
1.炼轧棒材轧制的新技术有哪些?
(1)全短应力无扭告诉轧制。
目前国际上先进的生产线,像意大利ABSIWNA厂,就采用全短应力线平立交替无扭轧制。
(2)大批料低能耗。
全热装式热送直接轧制技术,以日本NKK高森厂为代表的大批料直接轧制,边角补热的方式是降低成本,提高产品竞争力的有效途径,我国有数家工厂也做过尝试。
目前广泛应用的是连铸热装·蓄热式加热炉等。
(3)控轧·控冷超级钢技术。
采用低成本材料生产高强度(400Mpa)螺纹钢筋时我国“973“科研项目。
在淮阳·南钢·三明等棒材厂进行了尝试,并取得了一些成绩,预测很快便有产品进入市场。
2002年新上项目基本上都考虑了生产超级钢的可能性。
(4)多线切分技术。
国内两线切分技术已经得到广泛应用,三线切分技术目前在几家轧钢厂得到成功应用,并取得预期效益。
四线切分仅广钢从巴登引进,目前尚不稳定。
随着材料研究的深入,高强度钢在市场上所占的比重会越来越大,用小规格产品来替代原来的中大规格已经成为必然的趋势。
熟练掌握并应用好多线切分技术对炼轧棒材生产线是十分必要的,
(5)成卷交货技术的应用。
国外的轧机,尤其是棒线才复合生产线,生产Ф8~16mm螺纹钢,并以成卷状态交货,大大方便了客户不同的要求,尤其是高速公路·机场·大型桥梁等用户。
近年来又有设备制造公司专门为棒线材生产线设计制造的卷取机。
像意大利POMINI公司,最大规格可以卷曲Ф25以上的棒材。
这些产品除直接供各户使用外,大部分进行深加工,直接送到工地。
(6)螺纹刚的深加工。
国外的建筑市场已基本实现机械化,而且由于劳动力成本等问题,使得客户愈来愈多的面向加工配送中心订购螺纹钢深加工制品,而不是直接向钢厂订货。
这样客户可以根据自己的建设进度,要求螺纹钢加工线每天运来螺纹钢制品,(7)硬质合金辊环在连轧棒材生产线上的应用。
由于生产小规格产品和降低制造成本的要求,许多生产厂开始采用硬质合金辊环。
目前应用最多的是德国SAAK的组合辊环。
国内有5家公司也开始生产并投入应用这种辊环,从其使用效果看,与国外进口的差距不大,但加工难度很大。
(8)自动计数技术。
最新的自动计数是采用光学摄像机配合CCD(电荷藕合器件,是一种半导体装置,能够把光学影像转化为数字信号)处理系统,可以精确读取每捆的根数,但不能在线自动分捆解决自动计数也可以从钢坯优化·倍尺优化上做工作,冷剪前计齿条动作,让每批钢的根数保持一致,也可保证每捆的根数严格一致。
2.现代棒材生产线主要有哪些设备,其主要作用是什么?现代棒材生产线主要有以下设
备:加热炉·轧机·剪机·冷床·冷剪·打捆机等。
加热炉:用于对炉内钢坯的预热,加热,升温,是钢坯有一定的塑性,以满足轧机的轧制要求。
轧机:轧件在转动的轧辊间产生塑性变形,轧出所需要的断面形状和尺寸的钢材
1号剪·2号剪:用于对轧件进行切头·切尾或在事故状态下进行碎断。
3号剪:主要对成品钢材在热态下进行倍尺剪切和优化剪切。
冷床:对所有轧件进行冷却矫直·齐头·保证轧件成品的平直度。
冷剪:进行定尺剪切,便于下到工序的加工和运输。
打捆机:对剪切后的成品钢材按要求进行打捆的设备。
3.什么是无头轧制?
无头轧制及在轧制过程中,将前后钢坯的头尾焊接起来,达到连续供坯,不断轧制,
在一个换辊周期内,轧件长度可无限延长的轧制方法。
4.什么事无头焊接轧制技术?
所谓无头焊接轧制就是无头轧制的详细称呼。
它将传统轧钢生产中的定尺钢坯(长度根据加热炉规格型式而定),在进入粗轧以前,通过钢坯焊接机将前后两根钢坯的头尾焊接在一起(此时,钢坯的头部已经进入粗轧机),并去除焊瘤,作为一根钢坯进入粗轧机,从而实现无头轧制。
5.无头焊接轧制工艺过程有哪些?
焊接过程从加热炉出口开始,钢坯在加热炉出口经高压水除鳞后,其前端与已进入粗轧机的前一根钢坯的尾部闪光对焊在一起。
具体程序如下:
(1)脉冲发生器落下,测量已进入粗轧机的钢坯尾部的运行速度,光电管测出钢坯头尾出现的时间,焊机启动,加速至钢坯的运行速度,即与第一架轧机的咬入速度一至;(2)两套夹钳分别将两根钢坯两端部夹紧。
(3)脉冲发生器抬起,焊接开始:钢坯定位调整——预热打火——闪光焊接——金属熔化——沿钢坯轴向施以很大的挤压力。
(4)分别沿水平·垂直方向去除焊瘤。
(5)夹钳打开,焊机减速。
(6)焊机返回到起始位置,光电管探测钢坯尾部,准备下一次焊接周期。
此时,对接在一起的两根钢坯作为一根钢坯进入粗轧机完成轧制过程。
6.无头焊接的优点有哪些?
无头焊接轧制具有提高产量,提高成材率和轧机作业率·降低成本·便于生产管理·适应性强等特点。
(1)提高产量。
省去了钢坯间隔时间,增加了有效生产时间,提高了产量:废品通常出现在棒料头部,因而大大减少了废品率以及产生废品所消耗的时间:消除了钢坯切
头·切尾损失。
(2)提高了成材率和轧机作业率。
1)在无头焊接轧制中可以实现一个生产班对第一根钢坯切头,对最后一根钢坯切尾;2)无需在冷床上位实现棒材长度最优化而进行的
剪切作业,剪床只剪切倍尺而没有短尺产生:3)。