Minimum Variation Surfaces
机械制造专业英语课后短语翻译

英语课后重点短语LESSON 1(P15)1)the fundamental concept 基本概念2)cross section 横截面3)the internal stresses produced in the bar 棒内应力4)continuous distribution of bydrostatic pressure 净水压力的连续分布5)the tensile load 拉伸载荷6) a uniform distribution over the cross section 横截面上的均匀分布7)arbitrary cross-sectional shape 任意横截面形状8)tensile stress 拉应力9)compressive stresses 压应力10)a normal stress 正应力11)through the centroid of the cross sectional area 通过质心的横截面积12)the uniform stress condition 均应力状态13)the stress distribution at the end of the bar14)high localized stresses 局部高应力15)an axially loaded bar 轴向加载杆16)a tensile strain 拉伸应变17)an elongation or stretching of the material 延长或拉伸的材料18)a compressive strain 压应变19)the ratio of two lengths20)purely statical and geometrical considerations 从纯静态和几何关系考虑LESSON 2(P25)1)the main manifestations of capacity 功能的主要表现形式2)the maximum unit load(stress) 最大单位载荷3)stress-strain diagram 应力-应变图4)the simple tensile test 简单拉伸试验5)the percentage elongation at rupture 断裂延伸率6)the end of tensile specimens 拉伸试样的末端7)permanent deformation 永久变形8)the resulting load-displacement curve 所产生的载荷-位移曲线9) a substsntial yielding of the material 大量高产的物质10)yield point 屈服点11)the trainsition from elastic to plastic behavior12)material property table 材料性能表13)plastic defomation 塑性变形14)a specified standard length of the specimen 指定的标准试样的长度15)at the moment of rupture 在破裂时16)short cylindrical specimens 短圆柱试样17)ductile materials 任性材料18)high stress concentration 高应力集中19)ultimate tensile strength 极限抗拉强度20)strain hardening zone 应变硬化区LESSON 3(P37)1)circular cross section 圆截面2)the position of mountings 安装位置3)nominal size 标准尺寸4)length of shaft subjected to twist 轴的受扭长度5)minimize stress concentration 尽量减小应力集中6)from the standpoint of stress 从应力角度7)equations for a shaft in pure torsion 轴纯扭转的方程式8)diameter of solid shaft 实心轴的直径9)outside diameter of hollow shaft 空心轴的外径10)the amount of twist in a shaft 轴的扭转量11)torsional deflection 扭转变形12)shear modulus of elasticity 剪切弹性模量13)be closer to the vertical load 接近于垂直载荷14)the endurance limit 疲劳极限15)the allowable shearing stress 许用剪切应力16)equation for equivalent moments 方程的等效力矩17)the design stress values for flexure 设计弯曲应力值18)the angle of twist 扭转角19)antifricton bearings 滚动轴承20)the amount of twist in a shaft 轴的扭转量LESSOM 4(P51)1)herringbone gears 人字齿轮2)spiral gears 螺旋齿轮3)worn gears 蜗轮4)bevel gears 圆锥齿轮5)hypoid gears 准双曲面齿轮6)sizes of spur-gear teeth 齿轮轮齿的尺寸7)the automotive rear axle drives 汽车后桥驱动8)rack-and-pinion drives 齿条和小齿轮驱动器9)diametral pitch 径节10)pitch circle 节圆11)the tangency point 切点12)pressure angles 压力角13)an involute curve 渐开线14)the radial distant 径向距离15)at right angles 成直角16)the average number of teeth in contact17)the reciprocal of the diametral pitch 对等径节18)to change inches to millimeters 把英寸换算成毫米19)a line perpendicular to the centerlines 垂直中心线的直线20)center distance between two meshed gears 两个齿轮的中心距LESSION 5(P62)1)plate cams 盘形凸轮2)cylindrical cams 圆柱凸轮3)the cam assembles in automatic record players 汽车发动机上的凸轮组件4)cam profiles 凸轮轮廓5)make a full-scale template 制造一个实体样板6)in the course of several revolutions of the cam 在凸轮中转几圈7) a tangential plate cam 切向盘形凸轮8) a translation cam 移动凸轮9)the groove in the periphery of the cam 凸轮表面的槽10)a guided vertical reciprocated follower 做垂直运动的往复件11)a constant-diameter cam 等径凸轮12)automatic washing machines13)a face cam 面凸轮14)the edge of a pivoted follow 摆动从动件的边缘15)a reciprocating knife-edged follower 作往复运动的刀口式从动件16)miniature snap-action electrical switchies 小的速动开关17)a pivoted flat-faced follower 安装在摆臂上的滚子从动件18)air pilot values19)the abrupt change in cam profile 在凸轮轮廓上的突变20)a Scotch yoke mechanism 苏格兰的克机构LESSION 6(P73)1)developing and demanding industry 一个处在发展中社会需要的产业2)propeller shaft 传动轴3)suspension components4) a sliding splined type of joint 滑动花键连接5)two rear axle shafts 两个后半轴6)to mesh with a larger bevel gear 与更大的锥齿轮啮合7)the universal joint 万向节8) a steering wheel 转向轮9)unevenness of road surfaces 路面的不平度10)the transverse line of the axle shafts 后横半轴11)to cause excessive tyre wear 造成轮胎的过度磨损12)the exactly similar diameter 直径非常接近13)quarter-elliptic leaf springs 四分之一随圆形钢板板式弹簧14)the transmission of shock 冲击15)road surface variation 路面变化16)the final-drive gears 最终传动齿轮副17)the precise alignment of shaft 精确同轴18)a rotating drum 转动筒鼓19)a hand lever 手刹杆20)be locked in the one position 被固定某一位置LESSION 8(P99)1)bulk deformation of metals 金属的变形2)forging,rolling or extruding 锻造滚压挤压3)plastic deformation 塑性变形4)impact blows 冲击5)the recrystallization point of the mental6)hot working and cold working 热加工和冷加工7)better surface finish8)hammer forging 锤锻9)striking the hot metal 锻打热金属10)a slow squeezing action 缓慢加压11)open dies and closed dies 开模和闭模12)bevel gears with traight or helical teeth 用直齿或螺旋加工锥齿轮13)impression dies 型腔模14)each of several die cavities 每一个模膛15)mass production16)a homogeneous circumferential grain fiow 均匀的周向纤维流17)the three-dimensional description 三维描述18)computer simulation 计算机仿真19)hydraulic presses 液压压力20)be rough- and finished-machined 粗加工和精加工LESSION 9(P110)1)carrying high-amperage current 携带高安培电流2)the electrode and the work-piece 电机和工件3)the weld pool 焊接熔池4) a column of ionized gas called plasma 一个列的电离气体称为等离子体5)the oxides and nitrides 氧化物和氮化物6)the positive ions 阳离子7)deleterious substances 有害物质8)the newly solidified mental 刚凝固的金属9)in overhead welding 仰焊10)current density 电流密度11)deposition rate 沉积速率12)an unbalanced magnetic field 不平横磁场13)arc blow 电弧偏吹14)the electrode coating 电极涂层15)in overhead position 在仰焊的位置16)the cooling rate of the deposited metal 沉积金属的冷却速度17)a more homogeneous microstructure 更均匀的微观结构18)a smooth flow of molten metal 顺畅熔融19)cellulosic-coated electrodes 纤维质涂层的焊条20)perpendicular to the current path 与电路垂直LESSION 10(P123)1)plain carbon steel 碳素钢2)carbon content 碳含量3)low carbon steel 低碳钢4)medium carbon steel 中碳钢5)high carbon steel 高碳钢6)be cold worked 冷加工7)be heat treated 热处理8)contain 20 point of carbon 含20%的碳9)in the hot-rolled condition 在热轧条件下10)heat-treat-hardened plain carbon steel 热处理硬化普通碳钢11)free-machining steels 易切削钢12)hot short 热脆性13)cold shortness 冷脆性14)the isothermal transformation curves 等温移动曲线15)grain refinement 细化晶粒16)stainless steel 不锈钢17)AISI steels 美国钢铁协会钢18)Iron-carbon equilibrium diagram 铁碳平衡表19)Tool and die steel 工具钢和模具钢20)High corrosion chemical resistance 高耐腐蚀和耐化学性能LESSION 11(P134)1)allotropic materials 同素异晶材料2)plain low carbon steel 普通低碳钢3)hypoeutectiod steel 亚共析钢4)normalized steel 正火钢5)hypereutectoid steel 过共析钢6)eutectoid composistion 共析钢7)grain houndaries 晶界8)ferrite matrix 铁氧体矩阵9)about 60℃about the Ac1 temperature 大约Ac1温度以上60摄氏度10)the nose of the I-T curve I-T曲线鼻共处11)cooling rate 冷却速率12)quenching shock 淬火介质13)thermal stress 热应力14)thermal shock 热冲击15)a tempered steel 回火钢16)temper brittlement 回火脆性17)in the tempering or drawing proceduce 在回火阶段18)hardened steel 硬化钢19)full annealing 充分退火20)to dissolve all the cementite 溶解渗碳体LESSION 15(P177)1)turning,facing and boring 车削,车端面和镗孔2)split nut 对开螺母3) a single setup of the workplace 工件在一次性定位安装4)headstock assembly 主轴箱组件5)tailstock assembly 尾座组件6)carriage assembly 溜板箱组件7)lead screw and feed rod 丝杠和光杆8)two sets of parallel,longitudinal ways 两组平行的导轨9)to assure accuracy of alignment 为了保证装配的精确度10)a set of transmission gears 一套传动齿轮11)the maximum size of bar stock 棒料的最大尺寸12)gear box 齿轮箱13)a V-belt or silent-chain drive V型带和无声传动装置14)carbide and ceramic tools 硬质合金和金属陶瓷刀15)the inner ways of the end 床身的内侧导轨16)tailstock quill 尾座套筒17)a graduated scale 通常情况18)in the direction normal to the axis of rotation of the work 在垂直工件旋转轴线方向19)manual movement of the carriage 托盘的手工移动20)per revolution of the spindle 主轴旋转一周LESSION 16 (P188)1) a multiple-tooth cutter 多齿铣刀2)progressive formation 逐渐成形3)in a direction perpendicular to the axis of the cutter 在垂直刀具轴线的方向4)the metal removal rate 金属切除率5)produce good surface finish 产生好的表面光洁度6)in job-shop and tool and die work7)teeth located un the periphery of the cutter body8)slab milling 板铣9)face milling 端面铣削10)up milling 逆铣11)down milling 顺铣12)the direction of feed of the workpiece 工件的进给方向13)the clamping device 夹具14)the smoothness of the generated surface 铣削表面的平整度15)the sharpness of the cutter edges 切削刃的锋利程度16)at the end of the tooth engagement17) p rofile cutters 仿形铣刀18) c arbide- and ceramic- tipped cutters 硬质合金及陶瓷-硬质合金刀具19)negative-rake-angle cutters 负倾角刀20)arbor cutters and shank cutters 乔木刀和柄刀。
机械图纸中常见的符号及意义

机械图纸中常见的符号及意义《机械识图》根据最新的中等职业学校机械制图教学大纲,针对中等职业学校学生在识图知识与技能方面的就业需求编写而成,注重对中等职业学校学生的识图能力培养。
《图文对半,直观形象,方便教学。
全书共分9个项目:抄画平面图形,三视图的形成与投影作图,基本几何体的视图,绘制与识读组合体视图,识读视图、剖视图和断面图,识读轴套类零件图,识读盘盖轮类零件图,识读叉架类和箱壳类零件图,识读装配图。
通过这9个项目将知识点与任务有机地结合,由浅入深,循序渐进,使学生完成技能的训练,达到学以致用的目的。
自劳动开创人类文明史以来,图形与语言、文字一样,是人们认识自然、表达和交流思想的基本工具,在图学发展的历史长河中,经过不断地完善和发展得到了广泛的应用。
在现代工业生产中,机械、化工或建筑都是根据图样进行制造和施工的。
设计者通过图样表达设计意图;制造者通过图样了解设计要求、组织制造和指导生产;使用者通过图样了解机器设备的结构和性能,进行操作、维修和保养。
因此机械图样是交流传递技术信息、思想的媒介和工具,是工程界通用的技术语言。
作为职业技术教育培养目标的生产第一线的现代新型技能型人才,必须学会并掌握这种语言,具备识读和绘制机械图样的基本能力。
从以下几方面可以体现其重要性:从事机械制造行业就须掌握机械制图 ,学习机械制图感到抽象、困难,其原因之一是习惯于在平面上思考问题,缺乏空间思维能力。
在学习过程中教师要有针对性地借助各种媒体,直观、形象地引导学生建立起空间概念,由平面思维转换到空间思维。
把物体的投影与实际零件结构紧密联系,不断地“由物画图”和“由图画物”,既要想象物体的形状,又要思考图形间的投影规律,步提高空间想象和思维能力。
有了这种能力,在实际工作时,才会通过二维的平面图——零件图(或装配图)想象出来三维的空间物体——实际零件(装配体),只有掌握这种技能,才能顺利完成零件加工或机器装配的工作。
所以,空间想象能力是学习机械制图的核心内容。
LOW-E 玻璃钢化(英文)
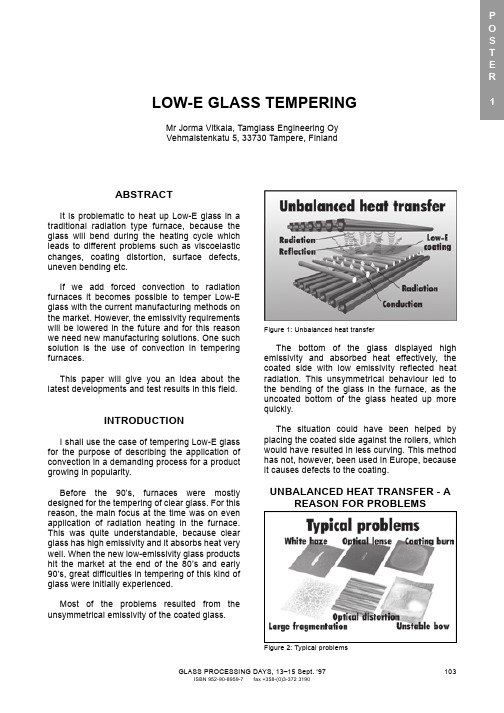
INTRODUCTION
I shall use the case of tempering Low-E glass for the purpose of describing the application of convection in a demanding process for a product growing in popularity.
Most of the problems resulted from the unsymmetrical emissivity of the coated glass.
Figure 1: Unbalanced heat transfer
The bottom of the glass displayed high emissivity and absorbed heat effectively, the coated side with low emissivity reflected heat radiation. This unsymmetrical behaviour led to the bending of the glass in the furnace, as the uncoated bottom of the glass heated up more quickly.
where T is the temperature of the glass, t and x stand for time and space and a is the thermal diffusivity.
陶瓷瓦工程规范说明书
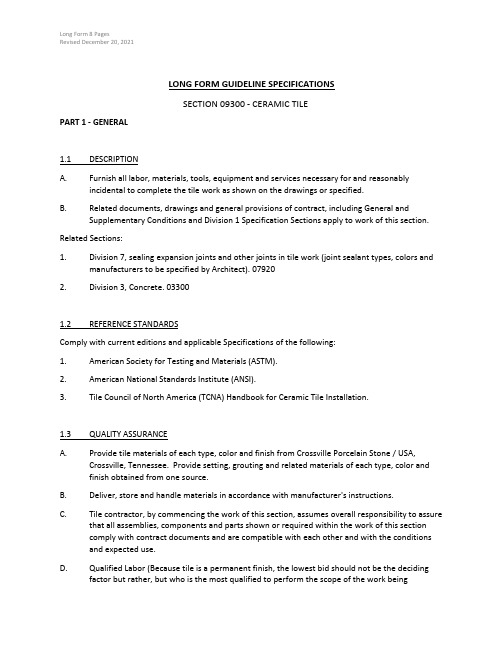
LONG FORM GUIDELINE SPECIFICATIONSSECTION 09300 - CERAMIC TILEPART 1 - GENERAL1.1 DESCRIPTIONA. Furnish all labor, materials, tools, equipment and services necessary for and reasonablyincidental to complete the tile work as shown on the drawings or specified.B. Related documents, drawings and general provisions of contract, including General andSupplementary Conditions and Division 1 Specification Sections apply to work of this section. Related Sections:1. Division 7, sealing expansion joints and other joints in tile work (joint sealant types, colors andmanufacturers to be specified by Architect). 079202. Division 3, Concrete. 033001.2 REFERENCE STANDARDSComply with current editions and applicable Specifications of the following:1. American Society for Testing and Materials (ASTM).2. American National Standards Institute (ANSI).3. Tile Council of North America (TCNA) Handbook for Ceramic Tile Installation.1.3 QUALITY ASSURANCEA. Provide tile materials of each type, color and finish from Crossville Porcelain Stone / USA,Crossville, Tennessee. Provide setting, grouting and related materials of each type, color andfinish obtained from one source.B. Deliver, store and handle materials in accordance with manufacturer's instructions.C. Tile contractor, by commencing the work of this section, assumes overall responsibility to assurethat all assemblies, components and parts shown or required within the work of this sectioncomply with contract documents and are compatible with each other and with the conditionsand expected use.D. Qualified Labor (Because tile is a permanent finish, the lowest bid should not be the decidingfactor but rather, but who is the most qualified to perform the scope of the work beingspecified. See TCNA Handbook for a list of recognized programs). Engage an installer with aminimum of five (5) commercial tile installations similar in material, design and scope to thatindicated.E. Pre-Installation Meeting: Prior to tile installation, conduct a pre-installation project meeting.Contractor, Subcontractor, Material Suppliers, Architect and Owner representative shall benotified of the meeting.F. Field Mock-Up: Recommended scaled to appropriate size of the scope of the work ______ sq ft(Insert) and will be reviewed for joint quality, color range, pattern and workmanship.G. Extra Stock: Furnish extra stock of quantity equal to ________% of amount installed, in full-sizeunits, for each type, color, size and finish of tile.1.4 SUBMITTALSA. Verification Samples: Submit the following for each type, color, size, and finish included in thework.1. Full size tile and trim shapes, (indicate number of pieces required).2. Grout color samples.3. Sealant color samples or Prefabricated Joint/Transition Strip SamplesB. Product and Installation Data:1. Porcelain tile manufacturer's product and technical data indicating compliance with applicablestandards.2. Master Grade Certificates for each type of tile issued by tile manufacturer and signed by theinstaller, only available after the material has shipped from the manufacturer.3. Mortar and grout manufacturer's technical data sheets indicating suitability for the installationspecified and compliance with applicable standards.4. Sealant or prefabricated joint manufacturer's product and technical data.1.5 ENVIRONMENTALA. Comply with requirements of referenced standards and recommendations of materialmanufacturers for environmental conditions before, during and after installation.B. Maintain environmental conditions and protect work during and after installation to complywith referenced standards and manufacturer's printed recommendations.C. Maintain minimum and maximum temperature limits as recommended by manufacturers.D. Protect adjacent surfaces during progress of the work in this section.E. Illuminate the work area during installation providing the same level and angle of illumination aswill be available for final inspection. The use grazing or cove type lighting where lights arelocated either at the wall/ceiling interface, or mounted directly to the wall prompts the light to strike the tile finish at a straight down angle, creating unwanted shadows from grout lines giving the tile layout an un-flat irregular appearance. Installing overhead lighting at a wide downward angle 18”-24” away from the tiled wall will provide a flatter more uniform appearance to thetiled surface.PART 2 - PRODUCTS2.1 GENERAL REQUIREMENTSA. Furnish tile complying with "Standard/First Grade" requirements per ANSI A137.1 - 2021, fortypes of tile indicated.B. Comply with ANSI Standard for Tile Installation Material and current Tile Council of NorthAmerica (TCNA) Handbook for products and materials indicated for setting and grouting.2.2 TILEA. Unglazed and glazed porcelain tile shall be standard/first grade quality as manufactured byCrossville Inc., Crossville, Tennessee, and shall conform to the requirements of ANSI A137.1 -2021.1. Size: Porcelain and ceramic tile shall be manufactured to specific size after firing and shall beNominal -_________________ (Insert). All measurements are in inches unless otherwisespecified.2. Type: Porcelain tile shall be_________________(Insert)3. Thickness: Porcelain tile shall be manufactured to specific thickness after firing and shall benominal _________________ ([8.0 mm or greater] for large unit tile or [6.0mm or greater] forMosaics).4. Color: _____________________ (Insert Crossville color name and number).5. Product Test Data:a. Water Absorption (ASTM C373):______________%.b. Breaking Strength (ASTM C648):_________________lbf.c. Bond Strength (ASTM C482):________________psi.d. DCOF Dynamic Coefficient of Friction (ANSI A326.3-2021)______ wet.6. According to availability, provide matching trim shapes such as bullnose, corners, borders andcove base when specified.7. Environmental Propertiesa. ANSI 138.1 Green Squared Certified2.3 SETTING AND GROUTING MATERIALS:A. Use appropriate installation mortars according to ANSI A118-2021.B. Grouting Materials: Select grouting materials according to the following types: Tile setting andgrouting epoxy: A118.6 Standard Cement Grout, A118.7, High Performance Cement Grout orA118.8, Modified Epoxy Emulsion Grout. Provide grout in colors selected by the Architect from standard colors available from the approved manufacturers.C. Use waterproofing/Anti Fracture Membrane as required according to ANSI A118.12.2.4 EXPANSION JOINTS, CONTROL, CONTRACTION, AND ISOLATION JOINTS:A. Refer to most current TCNA Handbook, Method EJ171 for recommendations on locating,treating and detailing various types of construction joints. NOTE: Architect must specify type of expansion joints and show location and details on drawings.B. Use sealant complying with ASTM C920 according to Type, Grade, Class and Uses required. D. Prefabricated expansion joints can also be used when suitable for installation.PART 3 – EXECUTION3.1 EXAMINATIONA. Examine substrates where tile will be installed for compliance with requirements for installationtolerances and other conditions effecting performance of installed tile. Before tiling concretesurfaces saturated dry (SSD), free of standing water verify that substrates for setting tile are well cured, structurally sound dry, clean, and free from oil or waxy films, curing compounds or other coatings and surface treatments. Nonstructural shrinkage cracks should be pretreated with acrack suppression membrane (to prevent telegraphing of cracks through the finished tileinstallation) ANSI A118.12.B. Do not proceed with installation until unsatisfactory conditions have been corrected.Commencement of work signifies acceptance of substrate and installation conditions.3.2 PREPARATIONA. Substrate Preparation: Prepare and clean substrate in accordance with installation standardsand manufacturer's instructions, and as follows:1. Remove protrusions, bumps and ridges by grinding or chipping.2. Repair, fill, and level cracks, holes, depressions and rough or chipped areas in substrate usingpatching material recommended by setting materials manufacturer.3. Slab to have light broom finish when tile is installed by thin-set method.4. Before tiling, verify that all surfaces to be tiled are structurally sound true to plane, and fallwithin maximum variations shown below: Ensure that the substrate is within the followingtolerances:a. Horizontal surfaces (floors) - Maximum variation in substrate shall not exceed 1/4 " inten feet* from required plane, depending on substrate.b. Vertical surfaces (walls) - Maximum variation in substrate shall not exceed1/4 " in tenfeet* from the required plane, depending on substrate.* When using large format tile, normally considered as tiles with at least one edge 15” in length or greater; a more stringent tolerance 1/8” in 10’ or 1/16” in 24” when measure from the high points on the surface is required.Report all unacceptable surfaces to the architect in writing, and do not tile such surfaces untilthey are leveled enough to meet above requirements.B. Jobsite Blending: Blend tiles before installing in accordance with reference standards to producean even range and distribution of color and finish.3.3 INSTALLATIONA. Manufacturers' Instructions: Perform work in compliance with standard accepted installationguidelines, Crossville Porcelain Stone/USA instructions and setting materials manufacturers'instructions.B. Comply with appropriate ANSI A108-2021 specification and current Tile Council of NorthAmerica Handbook (TCNA) for appropriate method of installation for each specification. Forthin set adhesive mortar application use following technique:•With the flat side of trowel, key mortar into substrate.•Using the appropriate size trowel, comb mortar in one direction with notched side of the trowel.•Set tile with a sliding motion, perpendicular to the mortar ridges.•Obtain as near 100% coverage as possible of mortar to tile.•Mortar coverage shall be no less than 85% and shall be sufficiently distributed to give full support under all corners and edges of the tile.•Note: 95-100% coverage is mandatory for wet and exterior areas. Periodically, remove sheets or individual tiles to assure proper bond coverage consistent with industry specifications.C. Installing Tile:1. Install tile in pattern indicated. Align joints when adjoining tiles on floor, base, walls, and trimare same size. Adjust to minimize tile cutting and to avoid tile less than half size.2. When possible, smooth cut edges of tile and/or use appropriate cutter or wet saw to producesmooth cuts. Provide straight cuts which align with adjacent materials.3. Extend tile into recesses and under equipment and fixtures to form a complete covering withoutinterruption.4. Terminate tile neatly at obstructions, edges, and corners, without disruption of pattern or jointalignment.5. Provide tile joints uniform in width, subject to variance in tolerance allowed in tile size. Makejoints smooth and even, without voids, cracks, or excess mortar or grout.6. Mix mortar in strict accordance with manufacturer's recommendations.7. Apply setting material in accordance with manufacturer's directions and install tile beforemortar has started initial cure. For thin set mortar application, use a notch trowel that willachieve the recommended coverage of mortar after tiles have been installed. Referencestandard coverage information and follow manufacturer's recommendations for trowel sizewhen using mortar.8. Do not spread more material than can be covered within 10 to 15 minutes. If "skinning" occurs,remove mortar and spread fresh material. Spread mortar with notches running in one direction that shall be perpendicular to the pressing, pushing and pulling of tile during placement.9. Place tile in fresh mortar, press, push and pull the tile slightly to achieve as near 100% coverageand contact of tile with setting material and substrate as possible. The coverage shall be no less than 85% and be sufficiently distributed to give full support of the tile. Make sure that allcorners and edges are well supported with mortar. Leave no hollow corners or edges. NOTE:95-100% coverage is mandatory for wet or exterior areas. A skim coat (“back-butter”) of mortar can be placed onto the entire back of the tile using a trowel in order to assist in optimumadhesion and coverage of the mortar being used.10. Ensure there is a minimum 1/8" of mortar between tile and substrate after proper bedding.Installer must periodically remove sheets or individual tiles to assure proper bond coverageconsistent with industry specifications. If coverage is found to be insufficient, use a larger sizenotch trowel.11. Use a beating block and hammer or rubber mallet so that faces and edges of individual tiles areflush and level with faces and edges of adjacent tiles, and to reduce lippage.12. For running bond/brick joint patterns utilizing tiles (square or rectangular) where the side beingoffset is greater than 18” (nominal dimension), the running bond offset will be a maximum of33% unless otherwise specified by the tile manufacturer. If an offset greater than 33% isspecified, specifier and owner must approve mock-up and lippage.D. Grouting:1. Install grout in accordance with ANSI A108.10, A108.6, A108.8, A108.9 correlating to grout typechosen and manufacturer’s recommendations.2. Mix grout material in strict accordance with manufacturer's directions.3. Apply grout to produce full, smooth grout joints of uniform width, and free of voids and gaps.4. Before grouting entire area do a test area to assure there will be no permanent staining ordiscoloration of the tile and to verify that the grout is easily removed from the surface. Ifnecessary, pre-coat exposed surfaces of tile with a grout release as recommended by themanufacturer, as this will facilitate removal of the grout.5. Cure all setting and grouting materials in accordance with manufacturer's recommendations.E. Cleaning and Protection:1. If one has been used, remove grout release and clean tile surfaces so they are free of groutresidue and foreign matter, in accordance with manufacturer's instructions. If a grout haze orresidue remains, use a suitable grout haze remover or cleaner and contact grout manufacturer for recommendations. Flush surface with clean water before and after cleaning. Do not useharsh hydrochloric, muriatic or sulfuric acid or acid-based cleaners to clean glazed tiles or tilesgrouted with latex modified grout.2. When a heavy residue of Portland cement grout is present, acceptable tile cleaning acids may beused. However, the grout should be allowed to cure a minimum of 10 days before thisaggressive cleaning method is employed. Tile and grout shall be soaked with water beforecleaning. In the absence of a recommendation from the grout manufacturer, acid cleaning may be done with a saturated solution of phosphoric or sulfamic acid, mixed in accordance withmanufacturer's recommendations.3. Protect all floor tile installations with clean construction paper or other heavy covering duringconstruction period to prevent staining or damage. After cleaning, provide protective covering and maintain conditions to protect tile work from damage or deterioration. Where tiledsurfaces will be subject to equipment or wheel traffic or heavy construction traffic, and during move-in of furniture and equipment, cover protective covering with 1/4" hardboard, plywood or similar material. No foot or wheel traffic permitted on floor for at least 3 days after grouting.Owner/specifier is responsible for protecting tile from damage including allowing sufficient time for installed materials to cure properly typically 30-45 days is required for full cure of thin setbonding mortars.4. Leave finished installation clean and free of cracked, chipped, broken, un-bonded, andotherwise defective tile work.5. Consult most current Crossville Brochure "Care & Maintenance" for information on postinstallation cleanup and routine maintenanceThis form document is intended as a general guideline only. It is the responsibility of the design professional to revise this form to suit specific requirements of the project. Crossville Porcelain Stone / USA makes no representation or warranties that the general information contained within this document is suitable for the specific requirements of the project. Consult your Crossville Porcelain Stone / USA representative and the installation and maintenance material manufacturers specified for technical assistance. The design professional should refer to the current edition of the TCNA handbook and other reference standards for additional information. The design professional should coordinate this section with the drawings and with general provisions of the contract, including general andsupplementary conditions and Division I general requirements.Inquiries- Crossville Incorporated – Technical Services(931) 484 – 2110(931) 484-8418 Fax******************************。
GMP规范中英文对照

GMP规范中英文对照Chapter 1: General Provisions第一章总则Article 1: This Regulation is enacted in accordance with the "Drug Administration Law of The People's Republic of China".第一条根据《中华人民共和国药品管理法》规定,制定本规范。
Article 2: This Regulation is promulgated as the basic guideline for manufacturing and quality control of pharmaceutical products. This Regulation shall be applicable to all the manufacturing processes of drug preparations and to the key manufacturing processes of raw materials which may cause variation in the quality of finished products.第二条本规范是药品生产和质量管理的基本准则。
适用于药品制剂生产的全过程、原料药生产中影响成品质量的关键工序。
Chapter 2: Organization and PersonnelArticle 3: A pharmaceutical enterprise shall establish production and quality control departments. The responsibilities of departments at all levels and personnel shall be clarified, and each department shall be staffed by an appropriate number of management and technical personnel with expert knowledge, manufacturing experience and organization ability. 第三条药品生产企业应建立生产和质量管理机构。
几何量具测量器具术语及英文对照
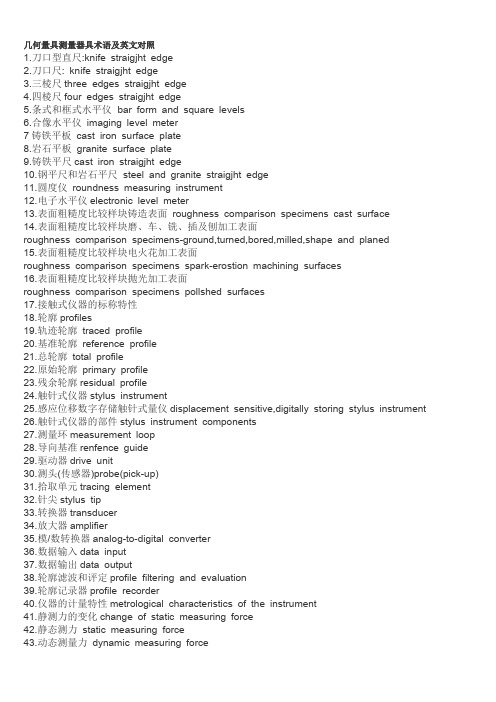
几何量具测量器具术语及英文对照1.刀口型直尺:knife straigjht edge2.刀口尺: knife straigjht edge3.三棱尺three edges straigjht edge4.四棱尺four edges straigjht edge5.条式和框式水平仪 bar form and square levels6.合像水平仪imaging level meter7铸铁平板cast iron surface plate8.岩石平板granite surface plate9.铸铁平尺cast iron straigjht edge10.钢平尺和岩石平尺 steel and granite straigjht edge11.圆度仪roundness measuring instrument12.电子水平仪electronic level meter13.表面粗糙度比较样块铸造表面roughness comparison specimens cast surface14.表面粗糙度比较样块磨、车、铣、插及刨加工表面roughness comparison specimens-ground,turned,bored,milled,shape and planed15.表面粗糙度比较样块电火花加工表面roughness comparison specimens spark-erostion machining surfaces16.表面粗糙度比较样块抛光加工表面roughness comparison specimens pollshed surfaces17.接触式仪器的标称特性18.轮廓profiles19.轨迹轮廓traced profile20.基准轮廓reference profile21.总轮廓total profile22.原始轮廓primary profile23.残余轮廓residual profile24.触针式仪器stylus instrument25.感应位移数字存储触针式量仪displacement sensitive,digitally storing stylus instrument26.触针式仪器的部件stylus instrument components27.测量环measurement loop28.导向基准renfence guide29.驱动器drive unit30.测头(传感器)probe(pick-up)31.拾取单元tracing element32.针尖stylus tip33.转换器transducer34.放大器amplifier35.模/数转换器analog-to-digital converter36.数据输入data input37.数据输出data output38.轮廓滤波和评定profile filtering and evaluation39.轮廓记录器profile recorder40.仪器的计量特性metrological characteristics of the instrument41.静测力的变化change of static measuring force42.静态测力static measuring force43.动态测量力dynamic measuring force44.滞后hysteresis45.测头的测量范围transmission function for the sine waves46.仪器的测量范围measuring range of the instrument47.模数转换器的量化步距quantization step of the ADC48.仪器分辨力instrument resolution49.量程分辨力比range-to-resolution ratio50.测头线性偏差probe linearity deviation51.短波传输界限short-wave transmission limitation52.轮廓垂直成分传输vertical profile component transmission153表面粗糙度比较样块抛丸、喷砂加工表面roughness comparison specimens shot blasted and blasted surfaces54产品结构几何量计术规范(GPS)geometrical product specifications(GPS)55表面结构surface texture56接触式仪器的标称特性nominal characteristics of contact instruments57公法线千分尺micrometer for mearsuring root tangent lenghths of gear teeth58最大允许误差maximum permissible error59圆柱直齿渐开线花键量规gauges for straight cylindrical involute splines60齿厚游标卡尺Gear tooth vernier calipers61齿轮渐开线样板the involute master of gear62齿轮螺旋线样板the helix master of gear63矩形花键量规gauges for straight –sided splines64测量蜗杆master worm65万能测齿仪universal gear measuring instrument66万能渐开线检查仪universal involute measuring instrument67齿轮齿距测量仪gear circular pictch measuring instrument68万能齿轮测量机Universal gear measuring machine69齿轮螺旋线测量仪gear helix measuring instrument70便携式齿轮齿距测量仪manual gear circular pitch measuring instrument71便携式齿轮基节测量仪manual gear base pitch measuring instrument72立式滚刀测量仪vertical hob measuring instrument73齿轮双面啮合综合测量仪Gear dual-flank measuring instrument74齿轮单面啮合整体误差测量仪Gear single-flank meshing integrated error measuring instrument 75梯形螺纹量规gauges for metric trapezoidal screw threads76工作螺纹量规work gauges for metric trapezoidal screw threads77校对螺纹量规check gauges for metric trapezoidal screw threads78.梯形螺纹量规型式与尺寸Types and dimensions of metric trapezoidal screw threads79.普通螺纹量规型式与尺寸Types and dimensions of gauges purpose screw threads80.非螺纹密封的管螺纹量规Gauges for pipe threads prcessure-tight joints are not made on the threads81.螺纹千分尺Screw thread micrometer82.最大允许误差maximum permissible error83.间隙螺纹量规Clearance screw gauge84.量针Bar gauge85.螺纹样板Screw thread template86.用螺纹密封的管螺纹量规Gauges for pipe threads where pressure-tight joints are made on the threads87.刀具预调测量仪精度Accuracy of the presetting instrument88.薄膜式气动量仪Membrane type pneumatic measuring instrument89.光栅线位移测量系统Grating linear displacement measuring system90.光栅角位移测量系统Grating angular displacement measuring system91.磁栅线位移测量系统Magnet-grid linear displacement measuring system92.量块附件Accessories for gauge blocks93.V形架Vee blocks94.比较仪座Comparator stand95.磁性表座Magnetic stand96.万能表座Universal stand for dial indicator一般术语:1. 几何量geometrical product2. 量值value(of a quantity)3. 真值true value(of a quantity)4. 约定真值conventional true value(of a quantity)5. 单位unit(of measurement)6. 测量measurement7. 测试measurement and test8. 检验inspecte9. 静态测量static measurement10. 动态测量dynamic measurement11. 测量原理principle of measurement12. 测量方法method of measurement13. 测量程序measurement procedure14. 被测量measurand15. 影响量influence quantity16. 变换值transformed value(of a measurand)17. 测量信号measurement signal18. 直接测量法direct method of measurement19. 间接测量法indirect method of measurement20. 定义测量法definitive method of measurement21. 直接比较测量法direct-comparison method of measurement22. 替代测量法substitution method of measurement23. 微差测量法differential method of measurement24. 零位测量法nulll method of measurement25. 测量结果result of a measurement26. 测得值measured value27. 实际值actual value28. 未修正结果uncorrected result (of a measurement)29. 已修正结果corrected result(of a measurement)30. 测量的准确度accuracy of measurement31. 测量的重复性repeatability of measurement32. 测量复现性reproducibility of measurements33. 实验标准偏差experimental standard deviation34. 测量不确定度uncertainty of measurement35. 测量绝对误差absolute error of measurement36. 相对误差relative error37. 随机误差random error38. 系统误差systematic error39. 修正值correction40. 修正系数correction factor41. 人员误差personal error42. 环境误差environmental error43. 方法误差error of method44. 调整误差adjustment error45. 读数误差reading error46. 视差parallax error47. 估读误差interpolation error48. 粗大误差parasitic error49. 检定verification50. 校准calibration51. 调准gauging52. 调整adjustment几何量测量器具术语1. 几何量具测量器具dimensional measuring instruments2. 长度测量器具length measuring instruments3. 角度测量器具angle measuring instruments4. 坐标测量机coordinate measuring machine5. 形状和位置误差测量器具form and position error measuring instruments6. 表面质量测量器具surface quality measuring instruments7. 齿轮测量器具gear measuring instruments8. 实物量具(简称“量具”)material measure9. 测量仪器(简称“量仪”)measuring instruments10. 测量链measuring chain11. 测量装置measuring system12. 指示式测量仪器indicating(measuring )instrument13. 记录式测量仪器recording(measuring)instrument14. 累计式测量仪器totalizing(measuring)instrument15. 积分式测量仪器integrating(measuring)instrument16. 模拟式测量仪器analogue(measuring)instrument17. 数字式测量仪器digital(measuring)instrument18. 测量变换器measuring transducer19. 传感器sensor20. 指示装置indicating device21. 记录装置recording device22. 记录载体recording medium23. 标尺标记scale mark24. 指示器index25. 标尺scale26. 度盘dail测量器具术语1. 标称值nominal value2. 示值indication(of a measuring instrument)3. 标尺范围scale range4. 标称范围nominal range5. 标尺长度scale length6. 标尺分度scale division7. 分度值value of a scale division8. 标尺间距scale spacing9. 线性标尺linear scale10. 非线性标尺non-linear scale11. 标尺标数scale numbering12. 测量仪器的零位zero of a measuring instrument13. 量程span14. 测量范围measuring range15. 额定工作条件vated operating conditions16. 极限条件reference condition17. 标准条件reference condition18. 仪器常数instrument constant19. 响应特性response characteristic20. 灵敏度senstivity21. 鉴别力discrimination22. 分辨力resolution(of an indicating device)23. 死区dead band24. 准确度accuracy of a measuring instruments25. 准确度等级accuracy class26. 重复性repeatability of a measuring instrument27. 示值变动性varation of indication28. 稳定度stability29. 可靠性reliability30. 回程hysteresis31. 漂移drift32. 响应时间response time33. 测量力(简称“测力”)measuring force测量器具术语1. 实物量具示值误差error of indication of a material measure2. 测量仪器示值误差error of indication of a measuring instrument3. 重复性误差repeatability error of a measuring instrument4. 回程误差hysteresis error5. 测量力变化variation of measuring force6. 测量力落差hysteresis of measuring force7. 偏移误差bias error (of a measuring instrument)8. 允许误差maximum permissible errors(of measuring instruments)9. 跟踪误差tracking error (of a measuring instrument)10. 响应率误差response-law error (of a measuring instrument)11. 量化误差quantization error (of a measuring instrument)12. 基值误差datum error (of a measuring instrument)13. 零值误差zero error (of a measuring instrument)14. 影响误差influence error15. 引用误差fiducial error16. 位置误差position error17. 线性误差linear error18. 响应特性曲线response characteristic curve19. 误差曲线error curve20. 校准曲线calibration curve21. 修正曲线correction curve。
几何测度论——精选推荐

几何测度论高维空间中低维点集的测度及低维点集上的积分理论。
20世纪初测度论的建立,使得人们对Rn中的子集关于n维勒贝格测度μn的行为有了很好的了解。
大部分函数论由于勒贝格积分论而产生了巨大变化。
但是在处理与Rn中低维点集有关的数学问题时遇到了困难。
例如著名的普拉托问题,在二维曲面时尚可以结合共形变换和狄利克雷原理巧妙地应用勒贝格方法而解决。
而在曲面的维数超出2时,这些经典的方法就失败了。
几何测度论正是在这种背景下产生。
它始于1914年C.卡拉西奥多里关于测度论的基础性工作,经过几十年的发展,熔合了来自分析、几何、代数拓扑中的许多技巧,产生了许多新的概念,成为数学研究的一个有力工具。
豪斯多夫测度与可求积集合在卡拉西奥多里的工作出现以后的开始20~30年内,大部分的兴趣在于了解Rn中的子集关于m 维豪斯多夫测度, 积分几何测度等各类测度的行为。
对于A嶅Rn,0≤k<∞,δ>0,定义A的k维豪斯多夫测度(简称hk测度)为,式中。
hk测度是Rn中的一个博雷尔正则测度。
又定义inf{k:hk(A)=0}为A的豪斯多夫维数,简称h 维数。
当k=n时,hn(A)=μn(A),n=0时h0(A)为A的元素个数。
0和n中间每个数均可出现为Rn中某个子集的h 维数。
例如康托尔集的h 维数为ln2/ln3。
设A的hk测度有限, 在k>0时,若存在Rk中某个有界子集到A的李普希茨映射(即二点距离的增长比受到某个正常数控制的映射),那就称A为k可求积集(k=0时为有限集,也称可求积集)。
如果A除了一个hk测度为0的子集外,为可列个k可求积集合覆盖,就称A为(hk,k)可求积集。
集合的可求积性质是一阶光滑流形的某种推广。
事实上,A 为(hk,k)可求积集合的充要条件是:除了一个hk测度为0的子集外,它可由Rn中可列个C1类k维子流形所覆盖。
可求积集合的这种描述使得对于它的构造的研究,特别是它的射影性质的研究成为几何测度论的重要内容。
机械图纸中常见的符号及意义(中英文)

直度-一个条件,一个面元素或轴是一条直线。
Straightness - a condition where an element of a surface or an axis is a straight line. 平整度-是条件,表面有所有的元素在一个平面。
Flatness - is the condition of a surface having all elements in one plane.圆度-描述条件对革命的表面(圆柱,圆锥,球)在所有点的表面相交的任何飞机。
Roundne ss - describes the condition on a surface of revolution (cylinder, cone, sphere) where all points of the surface intersected by any plane.圆柱度-描述了一个条件的旋转面,使所有的点面距离相等,一个共同的旋转轴。
Cylindricity - describes a condition of a surface of revolution in which all points of a surface are equidistant from a common axis.线轮廓度-是条件允许量相同的剖面变化,醚单边或双边,沿着一条线元素的特征。
Profile of a Line - is the condition permitting a uniform amount of profilevariation, ether unilaterally or bilaterally, along a line element of a feature.面轮廓度-是条件允许量相同的剖面变化,醚单边或双边,上表面。
Profile of a Surface - is the condition permitting a uniform amount of profilevariation, ether unilaterally or bilaterally, on a surface.周围标志-表明公差适用于所有周围的部分表面。
大底模具技术术语中英文对照

LN3--PU/Phylon/Rubber ProcessContents for these three sections of English Version PFC:∙Phylon Work Sheet PH数据表∙Components Specification Sheet(Phylon) 部件明细单(Phylon)∙Component Specification Sheet Set Up(Phylon) (此部分无中文)∙Phylon Midsole Specifications PH全插规格∙Phylon Preform Specifications PH粗胚规格∙Preform Drawing 粗胚图∙Component Specification Sheet Set Up(PU) (此部分无中文)∙PU Midsole Specifications PU全插规格∙PU Midsole Specifications II PU数据表∙Components Specification Sheet(PU) 部件明细单(PU)∙PU Midsole Pouring Specification PU灌注明细∙Outsole Color Schedule 本底颜色明细∙Outsole Preform Specifications 本底粗胚规格∙Outsole Pressing Process 本底压制流程∙Outsole Degreasing Process 本底水洗流程********************************************************************* ΦPU Section ΦPU部分********************************************************************* air bag schedule 空气袋分段specific instructions 特别说明air bag diagram 空气袋图示hardness(skin on) 硬度(带皮)density 密度elongation 延伸率tear 撕力tensile 拉力split tear 撕裂painting 喷漆MCS number 材料编号mold release agent 脱模剂polyurethane 聚安脂polyester 聚脂Density must be within NIKE spec and follow weight chart 密度必须符合NIKE要求及重量表No dirty midsole sidewalls yellowing or poor cosmetics due to mold condition.无因模具造成的边墙黄变及外观不良。
Zemax操作数(中英文对照)

一阶光学性能1EFFL 透镜单元的有效焦距Effective focal length in lens units2AXCL 透镜单元的轴向色差Axial color, measured in lens units for focal systems and diopters for afocal systems 3LACL 透镜单元的垂轴色差Lateral color4PIMH 规定波长的近轴像高Paraxial image height at the paraxial image surface at the wavelength defined by Wave 5PMAG 近轴放大率Paraxial magnification6AMAG 角放大率Angular magnification7ENPP 透镜单元入瞳位置Entrance pupil position in lens units, with respect to the first surface8EXPP 透镜单元出瞳位置Exit pupil position in lens units, with respect to the image surface9PETZ 透镜单元的PETZVAL 半径Petzval radius of curvature in lens units at the wavelength defined by Wave10PETC 反向透镜单元的PETZVAL 半径Petzval curvature in inverse lens units at the wavelength defined by Wave11LINV 透镜单元的拉格朗日不变量Lagrange (or optical) invariant of system in lens units at the wavelength defined by Wave12WFNO 像空间F/#Working F/#13POWR 指定表面的权重The surface power (in inverse lens units) of the surface defined by Surf at the wavelength defined14EPDI 透镜单元的入瞳直径Entrance pupil diameter in lens units15ISFN 像空间F/# (近轴)Image space F/#16OBSN 物空间数值孔径Object space numerical aperture17EFLX “X”向有效焦距Effective focal length in the local x plane of the range of surfaces defined by Surf1and Surf2 at the18EFLY “Y”向有效焦距Effective focal length in the local y plane of the range of surfaces defined by Surf1and Surf2 at the19SFNO 弧矢有效F/#Sagittal working F/#, computed at the field point defined by Field and the wavelength defined byWave像差1SPHA 在规定面出的波球差分布(0则计算全局)Spherical aberration in waves contributed by the surface defined by Surf at the wavelength defined2COMA 透过面慧差(3阶近轴)Coma in waves contributed by the surface defined by Surf at the wavelength defined by Wave3ASTI 透过面像散(3阶近轴)Astigmatism in waves contributed by the surface defined by Surf at the wavelength defined byWave 4FCUR透过面场曲(3阶近轴)Field curvature in waves contributed by the surface defined by Surf at the wavelength defined byWave 5DIST 透过面波畸变(3阶近轴)ortion” on page 1786DIMX 畸变最大值Distortion maximum 7AXCL 轴像色差(近轴)Axial color, measured in lens units for focal systems and diopters for afocal systems 8LACL垂轴色差Lateral color 9TRAR径像像对于主光线的横向像差Transverse aberration radial direction measured in image space at the wavelength defined by Wave 10TRAX“X”向横向色差Transverse aberration x direction measured in image space at the wavelength defined by Wave 11TRAY“Y”向横向色差Transverse aberration y direction measured in image space at the wavelength defined by Wave 12TRAI规定面上的径像横向像差Transverse aberration radius measured at the surface defined by Surf at the wavelength defined 13TRAC径像像对于质心的横向像差Transverse aberration radial direction measured in image space with respect to the centroid for the 14OPDC主光线光程差Optical path difference with respect to chief ray in waves at the wavelength defined by Wave 15OPDX衍射面心光程差Optical path difference with respect to the mean OPD over the pupil with tilt removed at the 16PETZ 透镜单元的PETZVAL 半径Petzval radius of curvature in lens units at the wavelength defined by Wave 17PETC 反向透镜单元的PETZVAL 半径Petzval curvature in inverse lens units at the wavelength defined by Wave 18RSCH 主光线的RMS 光斑尺寸RMS spot radius with respect to the chief ray in lens units 19RSCE 类RSCH RMS spot radius with respect to the centroid in lens units 20RWCH 主光线的RMS 波前偏差RMS wavefront error with respect to the chief ray in waves 21RWCE 衍射面心的RMS 波前偏差RMS wavefront error with respect to the centroid in waves22ANAR 像差测试Angular aberration radius measured in image space at the wavelength defined by Wave with 23ZERN Zernike 系数Zernike Fringe coefficient 24RSRE 几何像点的RMS 点尺寸(质心参考)RMS spot radius with respect to the centroid in lens units 25RSRH 类同 RSRE (主光线参考)RMS spot radius with respect to the chief ray in lens units 26RWRE 类同 RSRE (波前偏差)RMS wavefront error with respect to the centroid in waves 27TRAD “X”像TRAR 比较The x component of the TRAR only 28TRAE“Y”像TRAR 比较The y component of the TRAR only 29TRCX像面子午像差”X”向(质心基准)Transverse aberration x direction measured in image space with respect to the centroid 30TRCY像面子午像差”Y”向(质心基准)Transverse aberration y direction measured in image space with respect to the centroid 31DISG广义畸变百分数Generalized distortion, either in percent or as an absolute distance 32FCGS弧矢场曲Generalized field curvature, sagittal 33DISC子午场曲Distortion, calibrated 34OPDM限制光程差,类同TRAC Optical path difference with respect to the mean OPD over the pupil at the wavelength defined byWave 35BSER对准偏差Boresight error 36BIOC集中对准Biocular Convergence 37BIOD垂直对准偏差Biocular Dipvergence MTF 数据1MTFT切向调制函数Modulation transfer function, tangential 2MTFS径向调制函数Modulation transfer function, sagittal 3MTFA平均调制函数Diffraction modulation transfer function, average of sagittal and tangential 4MSWT切向方波调制函数Modulation square-wave transfer function, tangential 5MSWS径向方波调制函数Modulation square-wave transfer function, sagittal 6MSWA平均方波调制函数Modulation square-wave transfer function, average of sagittal and tangential 7GMTA几何MTF 切向径向响应Geometric MTF average of sagittal and tangential response 8GMTS 几何MTF 径向响应Geometric MTF sagittal response9GMTT几何MTF切向响应Geometric MTF tangential response衍射能级1DENC衍射包围圆能量Diffraction Encircled Energy (distance) 2DENF衍射能量Diffraction Encircled Energy (fraction) 3GENC几何包围圆能量Geometric Encircled Energy (distance)4XENC Extended source encircled energy (distance)透镜数据约束1TOTR透镜单元的总长Total track (length) of lens in lens units 2CVVA规定面的曲率=目标值Curvature value3CVGT规定面的曲率>目标值Curvature greater than4CVLT规定面的曲率<目标值Curvature less than5CTVA规定面的中心厚度=目标值Center thickness value6CTGT规定面的中心厚度>目标值Center thickness greater than7CTLT规定面的中心厚度<目标值Center thickness less than8ETVA规定面的边缘厚度=目标值Edge thickness value9ETGT规定面的边缘厚度>目标值Edge thickness greater than10ETLT规定面的边缘厚度<目标值Edge thickness less than11COVA圆锥系数=目标值Conic value12COGT圆锥系数>目标值Boundary operand that constrains the conic of the surface defined by Surf to be greater than the13COLT圆锥系数<目标值Boundary operand that constrains the conic of the surface defined by Surf to be less than the14DMVA约束面直径=目标值Diameter value15DMGT约束面直径>目标值Diameter greater than16DMLT约束面直径<目标值Diameter less than17TTHI面厚度统计Sum of thicknesses of surfaces from Surf1 to Surf2 18VOLU元素容量Volume of element(s) in cubic cm19MNCT最小中心厚度Minimum center thickness20MXCT最大中心厚度Maximum center thickness21MNET最小边缘厚度Minimum edge thickness22MXET最大边缘厚度Maximum edge thickness23MNCG最小中心玻璃厚度Minimum center thickness glass 24MXEG最大边缘玻璃厚度Maximum edge thickness glass 25MXCG最大中心玻璃厚度Maximum center thickness glass 26MNCA最小中心空气厚度Minimum center thickness air 27MXCA最大中心空气厚度Maximum center thickness air 28MNEA最小边缘空气厚度Minimum edge thickness air29MXEA最大边缘空气厚度Maximum edge thickness air30ZTHI控制复合结构厚度This operand controls the variation in the total thickness of the range surfaces defined by Surf1 andSurf2 over multiple configurations31SAGX透镜在”XZ”面上的面弧矢The sag in lens units of the surface defined by Surf at X = the semi-diameter, and Y = 032SAGY透镜在”YZ”面上的面弧矢The sag in lens units of the surface defined by Surf at Y = the semi-diameter, and X = 033MNSD最小直径Minimum semi-diameter34MXSD最大直径Maximum semi-diameter35XXET最大边缘厚度Maximum edge thickness for the range of surfaces defined by Surf1 and Surf236XXEA最大空气边缘厚度Maximum edge thickness for the range of air surfaces defined by Surf1 and Surf2 37XXEG最大玻璃边缘厚度Maximum edge thickness for the range of glass surfaces defined by Surf1 and Surf2 38XNET最小边缘厚度Minimum edge thickness for the range of surfaces defined by Surf1 and Surf239XNEA最小边缘空气厚度Minimum edge thickness for the range of air surfaces defined by Surf1 and Surf2 40XNEG最小玻璃边缘厚度Minimum edge thickness for the range of glass surfaces defined by Surf1 and Surf2 41TTGT总结构厚度>目标值Total thickness greater than42TTLT总结构厚度<目标值Total thickness less than43TTVA总结构厚度=目标值Total thickness value44TMAS结构总质量Total mass45MNCV最小曲率Minimum curvature46MXCV最大曲率Maximum curvature47MNDT最小口径与厚度的比率Minimum diameter to thickness ratio48MXDT最大口径与厚度的比率Maximum diameter to thickness ratio参数数据约束1PnVA约束面的第n个控制参数=目标值This operand is obsolete, use PMVA instead 2PnGT约束面的第n个控制参数>目标值This operand is obsolete, use PMGT instead 3PnLT约束面的第n个控制参数<目标值This operand is obsolete, use PMLT instead 附加数据约束1XDVA附加数据值=目标值(1~99)Extra data value2XDGT附加数据值>目标值(1~99)Extra data value greater than3XDLT附加数据值<目标值(1~99)Extra data value less than玻璃数据约束1MNIN最小折射率Minimum index at d-light2MXIN组大折射率Maximum index at d-light3MNAB最小阿贝数Minimum Abbe number4MXAB最大阿贝数Maximum Abbe number5MNPD最小ΔPg-f Minimum6MXPD最大ΔPg-f Maximum7RGLA合理的玻璃Reasonable glass近轴光线数据1PARX指定面近轴X向坐标Paraxial ray x-coordinate in lens units at the surface defined by Surf at the wavelength defined byWave2PARY指定面近轴Y向坐标Paraxial ray y-coordinate in lens units at the surface defined by Surf at the wavelength defined byWave3REAZ指定面近轴Z向坐标Real ray z-coordinate in lens units at the surface defined by Surf at the wavelength defined byWave4REAR指定面实际光线径向坐标Real ray radial coordinate in lens units at the surface defined by Surf at the wavelength defined byWave5REAA指定面实际光线X向余弦Real ray x-direction cosine of the ray after refraction from the surface defined by Surf at the6REAB 指定面实际光线Y 向余弦Real ray y-direction cosine of the ray after refraction from the surface defined bySurf at the7REAC 指定面实际光线Z 向余弦Real ray z-direction cosine of the ray after refraction from the surface defined by Surf at the8RENA 指定面截距处,实际光线同面X 向正交Real ray x-direction surface normal at the ray-surface intercept at the surfaced defined by Surf at9RENB 指定面截距处,实际光线同面Y 向正交Real ray y-direction surface normal at the ray-surface intercept at the surface defined by Surf at10RENC 指定面截距处,实际光线同面Z 向正交Real ray z-direction surface normal at the ray-surface intercept at the surface defined by Surf at11RANG 同Z 轴向相联系的光线弧度角Ray angle in radians with respect to z axis12OPTH 规定光线到面的距离Optical path length13DXDX “X”向光瞳”X”向像差倒数Derivative of transverse x-aberration with respect to x-pupil coordinate14DXDY “Y”向光瞳”X”向像差倒数Derivative of transverse x-aberration with respect to y-pupil coordinate15DYDX “X”向光瞳”Y”向像差倒数Derivative of transverse y-aberration with respect to x-pupil coordinate16DYDY “Y”向光瞳”Y”向像差倒数Derivative of transverse y-aberration with respect to y-pupil coordinate17RETX 实际光线”X”向正交Real ray x-direction ray tangent (slope) at the surface defined by Surf at the wavelength defined byWave18RETY 实际光线”Y”向正交Real ray y-direction ray tangent (slope) at the surface defined by Surf at the wavelength defined byWave19RAGX 全局光线”X”坐标Global ray x-coordinate20RAGY 全局光线”Y”坐标Global ray y-coordinate21RAGZ 全局光线”Z”坐标Global ray z-coordinate22RAGA 全局光线”X”余弦Global ray x-direction cosine23RAGB 全局光线”Y”余弦Global ray y-direction cosine24RAGC 全局光线”Z”余弦Global ray z-direction cosine25RAIN 入射实际光线角Real ray angle of incidence变更系统数据1CONF 结构参数Configuration2PRIM主波长ary wavelength3SVIG设置渐晕系数Sets the vignetting factors for the current configuration一般操作数for all layers1SUMM两个操作数求和0 2OSUM合计两个操作数之间的所有数Sums the values of all operands between the two operands defined by Op#1 and Op#2 3DIFF两个操作数之间的差raction encircled, ensquared, x only, or y only (enslitted) energy defined by Frac 4PROD两个操作数值之间的积Product of two operands (Op#1 X Op#2)5DIVI两个操作数相除Division of first by second operand (Op#1 / Op#2)6SQRT操作数的平方根Square root of the operand defined by Op#7OPGT操作数大于Operand greater than8OPLT操作数小于Operand less than9CONS常数值truction systems used to define an optically fabricated hologram10QSUM所有统计值的平方根Quadratic sum11EQUA等于操作数Equal operand12MINN返回操作数的最小变化范围013MAXX返回操作数的最大变化范围Returns the largest value within the indicated range of operands defined by Op#1 and Op#214ACOS操作数反余弦Arccosine of the value of the operand defined by Op#15ASIN操作数反正弦Arcsine of the value of the operand defined by Op#16ATAN操作数反正切Arctangent of the value of the operand defined by Op# 17COSI操作数余弦Cosine of the value of the operand defined by Op#18SINE操作数正弦Sine of the value of the operand defined by Op#19TANG操作数正切ential EFL use Data = 12ZPL宏指令优化1ZPLM Used for optimizing numerical results computed in ZPL macros 像面控制操作数1RELI像面相对亮度Relative illumination。
汽车工程英语缩略语大全

"A"A Assembly总成A.R.B Anti Roll Bar横向稳定杆A/C Air Conditioning空调A/F Air Fuel Ratio空气燃料混合比A/RST Armrest扶手A/RTL Anti Rattle防震A/T Automatic Transmission自动变速器AA Architecture Approval结构批准AAM Alliance of Automobile Manufactures汽车制造商联盟ABAG Airbag气囊ABC Active Body Control车身主动控制系统ABIW Architectural Body In White白车身结构ABIWM Architecture Body in White Mule Mule车白车身结构A-BOM Analytical Bill of Material A-BOMABPR ABS Pump Request防抱制动系统泵作用ABS Anti-lock Brake System or Anti-Block Steering防抱死制动系统ABSL Absolute绝对的ABSL ABS Lamp防抱制动系统警告灯ABSR ABS Relay防抱制动系统继电器ABSS ABS Stop防抱制动系统停止ABUT Abutment对接、邻接AC Architecture Confirmation结构确认AC Architecture Criteria结构标准ACC Air Condition Clutch空调离合器ACC Activated Carbon Canister活性碳罐ACC Accept允收ACC Access通道,住处存取(软件名)ACC Architecture Configuration Complete结构配置完成ACCEL Accelerator加速ACCL A/C Clutch 空调机离合器ACCUM Accumulator储能器,储压器ACD Actual Completion Date实际完成数据ACE Advanced Concept Engineering先期概念工程ACEV A/C Evaporate Temperature空调机蒸发温度ACI Automatic car identification system汽车自动识别系统ACL Air Cleaner空气滤清器ACMD Accommodate调节ACSRY Accessory附件ACST A/C Status 空调机状态ACSTC Acoustic阻尼ACSW A/C Press Switch 空调机压力开关ACT Air Charge Temperature进气温度ACTR Actuator执行器AD Alternatives Development选择性开发ADEL Air Delivery Mode 空气传送模式ADH Adhesive粘合剂ADJ Adjust调节ADJMT Adjustment调节ADM Absolute Dimension Measure全尺寸测量ADPR Adaptor转接器ADT Architecture Development Team结构开发小组ADV Analysis / Development / Validation分析/开发/验证ADVMS/PQMS Analysis Development Validation Management System /Performance & Quality Management System 分析开发验证管理系统/性能&质量管理系统AE Application Engineer应用工程师AFC Air Flow Control空气流量控制AFLO Air Flow空气流量计AFMA Actual Force Motor Amplifier实际强力马达放大器AFS Air Flow Sensor空气流量传感器AFUE Average Fuel Switch平均油耗开关AFV Alternative Fuel Vehicle代用燃料汽车AGR Actual Gear实际档位AGV Automatic Guided Vehicle自动导向车辆AHTY Ashtray烟灰缸AI Air Injection二次空气喷射AIAG Automotive Industry Action Group汽车工业行为组织AIGN ABS Ignition Volts防锁刹车系统点火电压AIRC Air Control 空气控制AIRD Air Delivery Mode空气传送模AIS Air Induction System二次喷气装置AIV Air Injection Valve空气喷射阀ALBS Automated Line Balance System-Sequence of assembly estab自动化流水线平衡系统—工业工程建立的装配次序ALCL Assembly Line Communication Link总装线测试插座ALDL Assembly Line Diagnostic Link组装线通信线路ALIAS Styling Software Brand Name ALIAS(软件)ALM Alarm警报ALR Automatic Lock Return自动馈回缩器ALT Alternator交流发电机ALT Altitude Switch 海拔高度开关ALY Alloy铝合金AM Ante Meridian上午AM Architecture Mule Mule车结构AMB Ambient环境AMBR Architecture Mule Build Readiness Review Mule车结构试制评估准备就绪AMP Amperes电流强度AMPF Amplifier放大器AMT Armature电枢AMT Automated Manual Transmission 自动手动传动ANC Anchor固定点ANC/L Ancillary辅助ANRM Architecture Non-Running Mule Mule车结构(无法开动)ANSI American National Standards Institute美国国家标准协会ANT Antenna天线AOQ Average Output Quality平均出厂品质AP Accelerator Pedal加速踏板AP Advanced Purchasing先期采购APC Aperture card穿孔卡片APD Approved Product Description批准的产品描述APE Annual Program Execution年度项目执行APEAL Auto Performance Execution and Layout汽车性能执行和规划APEC Asia Pacific Economic Cooperation亚太经济联盟APET Advanced Program Execution Team先期项目执行小组APLQ Applique饰件APM Assistant Program Manager助理项目经理APO Asian and Pacific Operations亚太地区业务APP Approve核准,认可,承认APPROX Approximately大约,近似APQP Advanced Product Quality Planning先期产品质量策划APRL Air Pump Relay 空气泵继电器APRTG Aspirating除尘APRTL Area Peer Review Topic List同等区域主题评估表APS Absolute Pressure Sensor绝对压力传感器APTR Aperture孔径APV All Purpose Vehicle多用途车辆AQL Acceptable Quality Level运作类允收品质水准AR Appropriation Request经费要求AR Averary Range全距平均值ARA Appropriations Request Approved批准的拨款申请ARB Anti Roll Bar横向稳定杆ARC Arch罩Arch.Architecture结构AREQ A/C Request 空调机作用ARL Aerial天线ARM Architecture Running Mule Mule车结构(可开动)ARP Appropriations Request Process拨款申请流程ARYM Aerodynamic空气动力学的ASB Automotive Strategy Board汽车战略委员会ASC Architecture Selection Complete结构选择完成ASE Automotive Safety Engineering汽车安全工程ASE Aftersales Engineering售后工程ASI Architecture Studies Initiation结构研究开始ASQ&R Advanced Supplier Quality & Readiness先期供应商质量&准备就绪ASR Acceleration Slip Regulation汽车驱动防滑控制系统ASR Automatic Stability Regulation自动稳定调节ASRC Automatic Stability Regulation Controller自动稳定调节控制器ASRS ASR Switch自动稳定调节控制器开关ASSI Architecture Statement of Strategic Intent战略意图的结构状态ASST Assistant辅助(设备)ASSY Assembly总成ATCU Auto Condition Control Unit自动空调控制单元ATDC After Top Dead Center到上止点后ATF Automatic Transmission Fluid自动变速箱油液ATS Architecture Technical Specification结构技术规范ATS Air Temperature Sensor空气温度传感器ATT Attachment附件ATV Advance Technology Vehicle高科技车辆ATV Active活动AUD Audio声频的AUDL Auto Door Locks 自动门锁AUX Auxiliary辅助装置AVD Advanced Vehicle Development先期车辆开发AVDC Advance Vehicle Development Center先期车辆开发中心AVDP Advanced Vehicle Development Process (Time between先期车辆开发流程(在DSI与VPI之间)DSI and VPI)AVPM Advanced Vehicle Planning Manager先期车辆计划经理AWD All wheel Drive全轮驱动AWL ABS Warning Light防锁刹车系统警示灯AXL Axle桥,轴"B"B+Battery Positive Voltage蓄电池正极B Build试制B/HD Bulkhead防水壁B/SD Bodyside车身侧部B+U Build + Utilities土建动能BAD Build Authorization Document试制授权文档BAD Badge标牌BAL Balance平衡BALAST Balast整流器BAR Barrel桶形BARO Barometric Pressure大气压力BAROS Barometric Pressure Sensor大气压力传感器BARV Barometric Pressure Voltage 大气压力电压BAT Battery电瓶BATT Battery Volts 电瓶电压BBS Bulletin Board System报告模板系统BBW Brake By Wire汽车电制动系统BCR BOM Change Request零件清单更改申请BCU Body Control Unit车身控制单元BD Body车身BDC Bottom Dead Center下止点BE Body and Exterior Department车身外饰部BEB Body Section车身科BEC Closure Section门盖科BEE Exterior Section外饰科BEI Body-In-White, Exteriors & Interiors白车身,内部和外部BELT Seat Belt Telltale 安全带显示器BER Bearing支座BFL Baffle导流板BGAM Burglar Alarm防盗警报BGT Bright光亮的BHP Brake Horse Power制动热效率BIF Batch Implementation Freeze批量执行冻结BIR Prototype Build Issue Report试制问题报告BIR Build Issues Resolution试制问题BIR Build Incident Report装车问题报告BIS Best In Segment最佳分割BIW Body-In-White白车身BK Back后板BKLG Backlight后灯BKUT Backout拆除BL Ball球BLA Blade片BLCK Block盖板BLD Bleed排气,排放BLN Blend混合BLNK Blanking盖板BLO Blower送风BLT Belt带BMEP Brake Mean Effective Pressure空燃比BNC Bench长条座椅BND Band带BNT Bonnet发动机罩BOA Bill of Architecture结构表BOD Bill Of Design设计清单BOE Bill of Equipment设备清单BOF Body On Frame车身框架BOI Base Oil Interchanger基础油互换BOL Bill Of Lading提单BOLS Bolster枕座BOM Bill of Material物料清单Bom View Bill of Materials View 产品明细表视图Bom View Revision Bill of Materials View Revision产品明细表视图版本BOP Bill Of Process工艺清单BP Basis Point基点BP Business plan业务计划BPR Bumper保险杠BR Brace拉杆,撑臂BRD Braid编织物BRK Brake制动BRKT Bracket支架BROCH Brochure册子BRT Ball Rust Tes球腐蚀试验BS Base基本的BSCT Basecoat底漆BSD Build Site Direction试制现场指导书BSFC Brake Specific Fuel Consumption制动油耗率BT Boot后备箱,护罩BTDC Before Top Dead Center上止点前BTHR Breather通风BTM Bottom底部BTN Button按钮BTU British Thermal Units英热单位BTW Between之间BUG Burglar防窃BUH Bush衬套BYP Bypass旁通BZL Bezel玻璃嵌框"C"C&M Care and maintenance 维修及保养C.CARB Conventional carburetor常规化油器C.P.Car park(停)车场C/FBR Carbon Fibre碳纤维C/MBR Crossmember横梁C/O Carry over携带C/S Concept Sheet概念表CAB Change Approval Board 更改审批会CAB Curtain Airbag 侧面气帘CAC Corporate Advisory Council联合顾问委员会CAC Charge Air Cooler增压中冷器CAD Computer Aided Design计算机辅助设计CADAM Computer Augmented Design and Manufacturing计算机辅助设计及制造CAE Computer Aided Engineering计算机辅助工程CAF Cubing Assurance Fixture(Interiors Only)空间保证装置(只限内部)CAFE Corporate Average Fuel Economy公司平均燃油经济性CALN Calibration校准CAM Computer-Aided Manufacturing计算机辅助制造CAMI Canadian Automotive Manufacturing,Inc.加拿大汽车制造有限公司CAR Corrective action request改正行动要求CARB Carburetor化油器CARE Corporate average regulated emission公司规定的平均有害物排放量CARE Customer Acceptance Review and Evaluation用户接受度和审查评估CARP Cooperate automotive research program 汽车合作研究程序CARR Carrier运载工具,载体CARR Carriage车溜板CART Carton 卡片纸CASG Casing蒙皮CAT Catalytic Converter触酶转换器CAT Carburetor air temperature化油器空气温度CAV Cavity模穴CBC Costbook control成本控制CBL Cable电缆CBR Costbook release发布第一版costbookCC Carbon Copy副本复印相关人员CC Change Control更改控制CCB Cross Car Beam仪表板横梁CCC Converter Clutch Control转换离合器控制CCD Combustion Chamber Deposit燃烧室沉积CCP Collaborative Criteria Process合作的标准流程CCS Cold Cranking Simulator冷启动模拟器CCS Cruise Control System汽车巡航控制系统CDB Corporate Data Base公司数据库CDI Central Multiport fuel Injection 中央多点燃油喷射CDLS Common Datum Locating Strategy The purpose is toprovide vehicle technical direction for integratingproduct(BOM) and process(BOP) at system interfaces toachieve designs/processes that are insensitive to variation.The assembly sequence, component break up, andproduct/process design enablers(slip planes, matingsurfaces, clearances, interfaces, joint design) provide“how” the vehicle, major sub-systems, assemblies, sub-assemblies and/or parts will be designed at interfaces forcontrol of variation. In essence, “how to” design the tools公共信息配置策略CE Cost Estimator成本评估者CE Chief Engineer总工程师CEIT Central Engineering Improvement Team主要的工程改进小组CES Clutch Engage Switch离合器接合开关CFC Chlorofluorocarbon氯氟碳化合物CFI Central Fuel Injection中央燃油喷射CFIT Cross Functional Implementation Team跨功能执行小组CFPP Cold Filter Plugging Point冷滤点CFRC Carbon fiber friction material碳纤维摩擦材料CFRP Carbon fiber reinforced plastic碳纤维强化塑料CGLG Ciger Lighter点烟器CGS Computer Graphics System计算机图形系统CH Chassis Department底盘部CHA Advanced Engineering Section前期工程科CHAN Channel通道CHARCAN Charcoal Chanister碳罐CHC Chassis Systems Section底盘系统科CHD/RETAT Child Restraint儿童保护装置CHG Charge充电CHGR Charger充电器CHGVR Changeover转换器CHK Check确认CHKM Check Arm限位器CHM Chamber室CHMSL High Mounted Stop Lamp高位制动灯CHNG Change转换CHNGR Changer转换装置CHP Chassis Performance Section底盘性能科CHR Chrome铬CHS Chassis Structure Section底盘结构科CHU Chute框架CI Check-in 数据签入CIA Component Integration Analyst零件综合分析CID Cubic Inch Displacement立方英寸排放量CID Cylinder Identification Sensor气缸传感器CIL Coil线圈CIM Computer Integrated Manufacturing计算机集成制造CIRT Consolidated Issues Resolution and Tracking System统一发布决议和跟踪系统CIT Compartment Integration Team隔间融合为组CKC Critical Key Commodity关键部件CKD Completely Knocked Down散装零件装配CKP/CP Crank Shaft Position曲轴位置CKP/CPS Crank Shaft Position Sensor曲轴位置传感器CKPT Cockpit座舱CL Closed Loop闭环控制CL Car load车辆载负CLA Clamp夹具CLCT Clearcoat清漆CLG Cooling/Cool冷却CLMPG Clamping箝位CLNG Cleaning清洁CLNR Cleaner滤清器CLP Clip卡扣CLPR Caliper卡钳CLR Colour颜色CLSG Closing封闭CLSR Closure闭合CLU Clutch离合器CLV Clevis U形夹CM Change Management 更改管理CM Configuration Management配置管理CM Contribution Margin贡献毛利率CM/SHF Camshaft凸轮轴CMA Change Management Administrator更改管理管理员CMA Camera摄像CME Change Management Engineer更改管理工程师CMM Coordinate Measuring Machine坐标测量仪CMP Cost Management Process成本管理流程CMP Camshaft Position凸轮轴位置CMPG Compages组合CMPLN Complaiance适用性CMPNT Components成分CMPR Compressor压缩机CMPU Computer计算机CMVSS Canadian Moter Vehicle Safety Standard加拿大机动车安全法规C-NCAP China New CAR Assessment Process中国标准新车评估体系CNG Compressed Natural Gas压缩天然气CNTAL Cantrail侧梁CNTC Contact联系/接触CNTNR Container容器CO Carbon Monoxide一氧化碳CO Check-out 数据签出CO2Carbon dioxide二氧化碳COC Centre of Competence能力中心COC Certificate of Conformity加盖单位公章COL Column管柱COLR Cooler冷却器COMPL Complete完全的COMPT Compartment室,厢CONDR Condenser冷凝器CONN Connector连接器CONS Console控制台CONT Connection(s)/Connecting连接COOLT Coolant冷却液COVE Customer Oriented Vehicle Evaluation客户取向车辆评估CP Centipoise厘泊CP Capability index能力指数CP/HLD Cupholder托杯CPA Component Planning Analyst零件计划分析CPC Clutch Pressure Control离合器压力控制CPC Critical Product Characteristics临界产品特性CPIP Current Product Improvement Process现有产品改进流程CPIT Current Product Improvement Team现有产品改进小组CPK Capability index of process模具制程能力参数CPP Clutch Pedal Position离合器踏板位置CPS Camshaft Position Sensor凸轮轴位置传感器CPT Carpet地毯CPU Central processing Unit中央处理器CPU Cost per unit提供单车实际成本CR Common Rail (Diesel Injection)同轨(柴油喷射)CR Critical极严重的CR Change Request更改请求CR/CASE Crankcase曲轴箱CR/DN Change Request/Decision Notice更改请求/决议通知CR/SHF Crankshaft曲轴CRS Child Restraint System儿童约束系统CRSB Crossbar十字CRSH Crush挤压CRSN Corrosion腐蚀CRT Cathode Ray Tube阴极射线管CRTV Commercial Road Transport Vehicle公路商用运输车辆CRV Comfortable Runabout Vehicle舒适轻便车辆CS Contract Signing合同签署CSI Customer Satisfaction Index用户满意度指标CSO Contract Sign-Off 合同签署CSO HC Contract Sign-Off Health Check合同签署健康度检查CSS Component Status Summary零件状态汇总CST Centistokes厘沱CSTG Casting铸件CT Cycle Time制程周期CT Critical Test临界试验CTD Concept Technical Descriptors概念技术描述CTH Catch卡子CTL Central中间的CTN Carton卡通箱CTP Closed Throttle Position节气门关闭位置CTR Center/Centre中央CTRL Control控制CTS Engine Coolant Temperature Sensor发动机水温传感器CTS Component Technical Specifications零件技术规格CTSY Courtesy礼貌CUCV Commercial utility cargo vehicle商用,轻型,多用途载货汽车CUPR Coupler连接器CUS Cruise巡航CUSN Cushion坐垫CV Concept Vehicle概念样车CVER Concept Vehicle Engineering Release概念车工程发布CVI Concept Vehicle Integration (formerly known as AVI)概念车辆综合CVR Cover盖、壳CVS Completed Vehicle Specification Drawing-Released UGdrawing that show the final DTS requirements for end of 最终车身特征绘制,UG绘制发布的用于曲线检查的DTS要求。
ProE Mechanica有限元分析入门教程

Pro/E Mechanica有限元分析入门教程一、进行Mechanica分析的步骤:1)建立几何模型:在Pro/ENGINEER中创建几何模型。
2)识别模型类型:将几何模型由Pro/ENGINEER导入Pro/MECHANICA中,此步需要用户确定模型的类型,默认的模型类型是实体模型。
我们为了减小模型规模、提高计算速度,一般用面的形式建模。
3)定义模型的材料属性。
包括材料、密度、弹性模量、泊松比等。
4)定义模型的约束。
5)定义模型的载荷。
6)有限元网格的划分:由Pro/MECHANICA中的Auto GEM(自动网格划分器)工具完成有限元网格的自动划分。
7)定义分析任务,运行分析。
8)根据设计变量计算需要的项目。
9)图形显示计算结果。
二、下面将上述每一步进行详解:1、在Pro/ENGINEER模块中完成结构几何模型后,单击“应用程序”→“Mechanica”,弹出下图所示窗口,点击Continue继续。
弹出下图,启用Mechanica Structure。
一定要记住不要勾选有限元模式前面的复选框,最后确定。
2、添加材料属性单击“材料”,进入下图对话框,选取“More”进入材料库,选取材料Name---------为材料的名称;References-----参照Part(Components)-----零件/组件/元件V olumes-------------------体积/容积/容量;Properties-------属性Material-----材料;点选后面的More就可以选择材料的类型Material Orientation------材料方向,金属材料或许不具有方向性,但是某些复合材料是纤维就具有方向性,可以根据需要进行设置方向及其转角。
点选OK,材料分配结束。
3、定义约束1):位移约束点击,出现下图所示对话框,Name 约束名称Number of Set 约束集名称,点击New可以新建约束集的名称。
ISO 翻译作业

21_______________________ Differences between ISO Standards and other Standards21.1ASME Y14.5M – 1994,ANSI B89.3.1In the following the terminology of ASME Y14.5 is used (see Table 21.3).21.1.1SymbolsThe National Standard of the United States of America ASME Y14.5M–1994 specifies in addition to or deviating from ISO 1101 the symbols and drawing indications shown in Tables 21.1 and 21.2.Table 21.1Symbols according to ASME Y14.5M*Not specified in ASME Y14.5M but usual in US practice.327328Geometrical Dimensioning and Tolerancing for Design, ManufacturingThe symbol “CZ” is not standardized according to ASME Y14.5. When it is used in drawings referenced to ASME Y14.5 the reference to ISO 1101 should also be intro-duced into the drawing title block, together with the remark: In cases of contradiction ASME Y14.5 applies.21.1.2RulesASME Y14.5M deviates in some rules from the specifications given in the ISO Standards. ASME Y14.5M specifies the following rules:Rule #1:Where only a tolerance of size is specified, the limits of size of an individual feature prescribe the extent to which variations in its geometrical form, as well as size, are allowed.In other words, for individual features of size the envelope requirement applies with-out drawing indication. Exceptions are as follows:●stock materials (such as bars, sheets, tubing, structural shapes) for which straight-ness, flatness or other geometrical tolerances are standardized and which remain in the “as-furnished” condition on the finished part;Table 21.2Drawing indications according to ASME Y14.5MDifferences between ISO standards and other standards 329●(non-rigid) parts subject to free state variation in the unrestrained condition (see 12);●features with a straightness tolerance to the axis or a flatness tolerance to the median face.Features with straightness tolerances to the generator lines are not exceptions. The envelope requirement applies as well as the straightness tolerance. Both requirements have to be respected.Rule #1 applies only to individual features of size. The rule does not apply to devia-tions of orientation or location or run-out of one feature related to another feature.Rule #1 is similar to the drawing title box indication ISO 2768 … E and to the German Standard DIN 7167. The difference is that ASME14.5M rule #1 excludes also those features with a straightness tolerance of the axis indicated that is smaller than the size tolerance (the other standards do not exclude those features).Rule for radii:A radius symbol R (preceding the dimension) creates a zone defined by two arcs (the minimum and maximum radii) that are tangent to the adjacent sur-faces. The part surface must lie within this zone (Fig. 21.1).“A controlled radius symbol CR (preceding the dimension) creates a tolerance zone defined by two arcs (the minimum and maximum radii) that are tangent to the adjacent surfaces. When specifying a controlled radius, the part contour within the crescent-shaped tolerance zone must be a fair curve without reversals. Additionally, radii taken at all points on the part contour shall neither be smaller than the specified minimum limit nor larger than the maximum limit (see Fig. 21.2).”There is not yet a precise definition of the radius tolerance in the ISO standards.*Fig.21.1Radius tolerance:(a) drawing indication, (b) interpretationFig.21.2Controlled radius tolerance CR:(a) drawing indication, (b) interpretation *A Technical report ISO TR 16570 is in preparation.Rule for angular surfaces:“Where an angular surface is defined by a combination of a linear dimension and an angle, the surface must lie within a tolerance zone repre-sented by two non-parallel planes [see Fig. 21.3]. The tolerance zone will become wider as the distance from the apex of the angle increases. Where a tolerance zone with parallel330Geometrical Dimensioning and Tolerancing for Design, Manufacturing boundaries is desired, a basic angle may be specified as in Fig. 21.4. Additionally, an angularity tolerance may be specified within these boundaries (Fig. 21.5).”In Figs 21.3 and 21.4 it is indicated by the symbol that the dimension between the two features shall originate from the lower feature. The high points of the surface indi-cated as the origin define a plane of measurement.Only tolerancing according to Fig. 21.5 complies with international practice, and is therefore recommended. Tolerancing according to Fig. 21.4 is not in accordance with ISO 1101. Drawing indications according to Fig. 21.3 have a different meaning accord-ing to ISO 8015 (see Fig. 3.45).Fig.21.3Tolerancing of an angular surface using a combination of linear and angular dimensions, according to ASME Y14.5Fig.21.4Tolerancing of an angular surface with a basic angleFig.21.5Tolerancing of an angular surface with an angularity tolerance Former rule #2 ANSI Y14.5M – 1982 (positional tolerance rule):With tolerances of position “regardless of feature size”S, the maximum material requirement M or the least material requirement L must be specified on the drawing with respect to the indi-vidual tolerance, datum reference, or both, as applicable.Differences between ISO standards and other standards331 According to a former rule (USASI Y14.5 – 1966 and ANSI Y14.5 – 1973), with positional tolerances, the maximum material requirement M was always applied to the toleranced feature as well as to the datum feature, without any indication of M. This was not in line with the international practice, according to which S always applies without the indication S, if not otherwise specified (with M or L), ISO 8015 and ISO 2692.Former rule #3 ANSI Y14.5M – 1982 (regardless of feature size rule for all other geometrical tolerances than positional tolerances):For all geometrical tolerances, other than positional tolerances, “regardless of feature size” S applies, with respect to the individual tolerance, datum reference, or both, where no modifying symbol is specified.Without the exception this coincides with the International Standards ISO 8015, ISO 2692 and ISO 1101. This rule was later covered by the new rule #2 ASME Y14.5M – 1994. New rule #2 ASME Y14.5M – 1994:Regardless of feature size applies, with respect to the individual tolerance, datum reference, or both, where no modifying symbol is specified.M or L must be specified on the drawing where it is required.This rule #2 coincides with ISO practices (ISO 1101, ISO 2692 and ISO 8015). New rule #2a ASME Y14.5M – 1994 (alternative praxis):For a tolerance of posi-tion S may be specified on the drawing with respect to the individual tolerance, datum reference, or both as applicable.This new rule #2a is not in line with international practice. The symbol S does not exist in the ISO standards. Regardless of feature size, applies everywhere, if not other-wise specified (with M or L).Pitch diameter rule (rule #4):Each tolerance of orientation or position (location) and datum reference specified for a screw thread applies to the axis of the thread derived from the pitch cylinder. Where an exception to this practice is necessary, the specific feature of the screw thread (such as MINOR DIA or MAJOR DIA) shall be stated beneath the feature control frame, or beneath or adjacent to the datum feature symbol, as applicable.Each tolerance of orientation or location and datum reference specified for gears and splines must designate the specific feature of the gear or spline to which each applies (such as MAJOR DIA, PITCH DIA or MINOR DIA). This information is stated beneath the feature control frame or beneath the datum feature symbol, as applicable. The new edition of ISO 1101-2004 gives a similar rule but different indications (MD for major, LD for minor (least) and PD for pitch diameter).Datum virtual condition rule:Where a datum feature of size is applied on an MMC basis, machine and gauging elements in the processing equipment, which remain con-stant in size, may be used to simulate a true geometrical counterpart of the feature and to establish the datum. In each case, the size of the true geometric counterpart (simu-lated datum) is determined by the specified MMC limit of size of the datum feature or its MMC virtual condition, where applicable.Where a primary or single datum feature of size is controlled by a roundness or cylindricity tolerance, the size of the true geometric counterpart used to establish the simulated datum is the MMC limit of size. Where a straightness tolerance is applied on an MMC basis, the size of the true geometric counterpart used to establish the simulated332Geometrical Dimensioning and Tolerancing for Design, Manufacturingdatum is the MMC virtual condition of the datum feature. Where a straightness toler-ance is applied on an RFS basis, the size of the true geometric counterpart used to establish the simulated datum is the applicable inner or outer boundary (see 21.1.10). Where secondary or tertiary datum features of size in the same datum reference frame are controlled by a specified tolerance of location or orientation with respect to each other, the size of the true geometric counterpart used to establish simulated datum is the virtual condition of the datum feature.Analysis of tolerance controls applied to a datum feature is necessary in determining the size for simulating its true geometrical counterpart. Consideration must be given to the effects of the difference in size between the applicable virtual condition of a datum feature and its MMC limit of size. Where a virtual condition equal to MMC is the design requirements a zero geometrical tolerance at MMC is to be specified (0M).In other words, for a datum feature of size used as a datum and for a feature of size with a geometrical tolerance applied to its axis or median face, a virtual condition (maximum material virtual condition) applies. The size of the virtual condition depends on the maximum material size and on the value of the geometrical tolerance applied to the axis or median face of the datum. When the datum is used as a secondary or terti-ary datum, the orientation and location of the virtual condition depend on the primary and secondary datums.For datum features of size (features with an axis or median plane) with the indica-tion M behind the datum letter in the tolerance frame, the following applies:(a)When for the datum feature with an axis a form tolerance to the feature (not to itsaxis) is indicated (e.g. roundness tolerance, straightness tolerance of the generator line), the maximum material virtual size is equal to the maximum material size (Fig. 21.6).When for a datum feature with an axis, a form tolerance to the axis is indicated(e.g. straightness tolerance of the axis), the maximum material virtual size is equalto the maximum material size plus (shafts) or minus (holes) the form tolerance of the axis (Figs 21.7 and 21.8).(b)When secondary or tertiary datum features of size (with an axis or median plane)occur in the same tolerance frame and are interrelated by a different tolerance ofFig.21.6Datum feature (B) with an axis and with a form tolerance that does not apply to the axis (MMVS for B M is ø10)Differences between ISO standards and other standards 333orientation or location between each other, the maximum material virtual condi-tion in the geometrical exact orientation and location relative to each other applies (Fig. 21.9). The maximum material virtual size of the datum is equal to the maxi-mum material size plus or minus the corresponding tolerance of orientation or location (Fig. 21.10).The datum virtual condition rule is not yet internationally standardized. However, part of it is self-evident (see 9.2). What is internationally disputed is that part of the rule deal-ing with geometrical tolerances to axes without the symbol M (Fig. 21.7, see 9.2).Figure 21.6 shows a case of rule (a). For the datum B the maximum material require-ment M applies. In addition, a form tolerance applies to the feature (generator line), not to the feature axis. For the gauge (to inspect the position of the four holes) at the datumB the virtual condition is equal to the maximum material condition (size ø10). This coincides with international practice.Fig.21.7Datum feature (B) with an axis and with a straightness tolerance to the axis (MMVS for B M is ø10.02)Fig.21.8Datum feature (B) with an axis and with a straightness tolerance to the axis and with the maximum material requirement to this straightness tolerance (MMVS for B M is ø10.02)334Geometrical Dimensioning and Tolerancing for Design, ManufacturingFigure 21.7 shows another case of rule (a). For the datum B the maximum material requirement M applies. In addition, a straightness tolerance of the axis (without M )applies. For the gauge (to inspect the position of the four holes) at the datum B the max-imum material virtual condition of ø10.02 applies. This is internationally disputed. ISO will probably specify that the maximum material size (ø10) applies.Fig.21.9Datums withM , in the same tolerance frame and toleranced in rela-tion to each other Fig.21.10Gauge according to Fig.21.9Differences between ISO standards and other standards 335The same maximum material virtual condition of ø10.02 applies when the straight-ness tolerance of the axis is ø0.02M (Fig. 21.8). This coincides with international practice.Figure 21.9 shows a case of rule (b). The datums A, B and C occur in the same tol-erance frame (tolerancing the position of the four holes). The maximum material requirement applies to B and C. B is toleranced in relation to A (with M ). C is toler-anced in relation to A and B (with M ). For the gauge (to inspect the position of the four holes) at the datums B and C the maximum material virtual conditions (ø12 and 8)apply (Fig. 21.10). This coincides with international practice.Figure 21.11 shows a part similar to Fig. 21.9. However, there is an additional posi-tional tolerance indicated at the datum feature C in relation to the datum D. Datum D does not occur in the tolerance frame of the positional tolerance of the four holes.Therefore the tolerance related to D is not to be taken into account for the calculation of the maximum material virtual condition of the datum C of the gauge (to inspect the position of the four holes). The gauge is the same as according to Figs 21.9 and 21.10.This coincides with international practice.21.1.3Positional tolerances according to ASME Y14.5In the past, according to USASI Y14.5 – 1966 and according to ANSI Y14.5 – 1973,with positional tolerances, the maximum material requirement was applied to the tol-eranced features as well as to the datum features without any drawing indication of the maximum material requirement. This was applied if not otherwise indicated in the drawing (e.g. by S or L ).ANSI Y14.5M – 1982 required, with positional tolerancing, the indication M , S , or L at the toleranced features (behind the positional tolerance) as well as at the datum features (behind the datum letter in the tolerance frame).Fig.21.11Datums with M , but in different tolerance frames336Geometrical Dimensioning and Tolerancing for Design, ManufacturingASME Y14.5M – 1994 specifies with the new rule #2 that it also applies with posi-tional tolerances regardless of feature size, if not otherwise specified with M or L. According to ISO 1101, if not otherwise specified (i.e. without any specific indica-tion), S applies. This coincides with the new rule #2.In the past, according to USASI Y14.5 – 1966 and according to ANSI Y14.5 – 1973, the following was applied to a positional toleranced pattern (group) of features (e.g. pattern of holes) with adjacent dimensional tolerances (Fig. 6.7).The dimensional tolerances of the adjacent dimensions were applied to the centres of the positional tolerance zones of the pattern (group) of features. Therefore individ-ual positional tolerance zones could be half outside the dimensional tolerance when the feature was at MMC, provided that the positional tolerance zone centres were within the dimensional tolerances. Therefore the actual axes of the holes were allowed to exceed the dimensional tolerances by half of the positional tolerance when the feature was at MMC (Fig. 6.7).According to ISO 8015, this is not permitted. Dimensional tolerances as well as posi-tional tolerances apply to the actual axes of the features.According to ANSI Y14.5M – 1982 dimensional tolerances for positioning a pattern (group) of features that is positional toleranced between each other should be avoided and replaced by positional tolerances related to a datum system (Fig. 6.8). ASME Y14.5M – 1994 gives similar advice.21.1.4Composite tolerancing and single tolerancingASME Y14.5M – 1994 distinguishes between composite tolerancing and single toler-ancing where there are two tolerances of the same type (position or profile) specified for the same features. Composite tolerancing is to be identified by one single toleranceFig.21.12Composite positional tolerancing (a) and (b);single positional tol-erancing (c)symbol for two tolerances, whereas single tolerancing is to be identified by separate tolerance symbols for each tolerance (Fig. 21.12).In the case of composite tolerancing the upper (always larger) tolerance applies to the location of the pattern of features relative to the datums specified, and defines the Pattern-Locating Tolerance Zone Framework (PLTZF)*. The lower (always smaller) tol-erance applies to the features relating to each other (interrelation of the features within the pattern) and, if applicable, to the orientation of the features as a group relative to the datums specified in the lower tolerance frame, and defines the Feature-Relating Tolerance Zone Framework FRTZF*. The theoretical exact dimensions from the datums (used to relate the PLTZF to the datums, TED 3 in Fig. 21.12) do not apply to the smaller tolerance (in the lower tolerance frame) that defines the FRTZF. The actual features (e.g. the actual axes) must lie within both tolerance zones (frameworks) (Fig. 21.12 (a) and (b)).In the case of single tolerancing each tolerance applies as if no other tolerance were indicated, i.e. the theoretical exact dimensions from the datums specified in the lower tolerance frame apply also to the Feature-Relating Tolerance Zone Framework FRTZF. The actual features (e.g. the actual axes) must lie within both tolerance zones (frame-works) (Fig. 21.12 (c)).ISO 1101 and ISO 5458 do not provide this differentiation. Also, when only one symbol is indicated for two tolerances, the indications of the theoretical exact dimen-sions relative to the datum(s) apply (as explained above for single tolerancing). See also Fig. 20.13.21.1.5Symmetry and concentricity tolerancesANSI Y14.5M – 1982 did not specify the symbol for symmetry tolerances (it was only contained as former practice). Where it was required that a feature be located symmetrically with respect to the median plane of a datum feature, positional toler-ancing (symbol ) was to be used. According to ISO 1101 in these cases the symbolis used.ASME Y14.5M – 1994 distinguishes between positional tolerances (with or without modifier M or L) and concentricity tolerances or symmetry tolerances (without mod-ifier M or L).Positional tolerances (symbol ) are applied to the axis or median plane of theactual mating envelope (e.g. maximum inscribed cylinder for holes or minimum cir-cumscribed cylinder for shafts orientated relative to the datum(s)) (Fig. 21.13). Concentricity tolerances (symbol ) and symmetry tolerances (symbol ) areapplied to the centres of the actual local sizes.Figure 21.13 shows an actual workpiece that is within the positional tolerance but exceeds the concentricity tolerance.ISO 1101 does not provide this distinction. According to ISO 1101 the tolerances of position, concentricity (coaxiality), symmetry, all without modifier, apply (all in the same way) to the actual axis or actual median face of the actual feature (see 3.5).*The acronyms are pronounced “Fritz” and “Plahtz”.21.1.6Orientation tolerances for axes or median planesOrientation tolerances according to ASME Y14.5 apply to the (perfect) axes or median planes of the mating envelope (true geometric counterpart). Orientation tolerances accord-ing to ISO 1101 apply to the (imperfect) actual axes or median faces (Fig. 21.14).21.1.7Tangent plane requirementASME Y14.5M – 1994 introduced the tangent plane requirement to be specified by the symbol T after the orientation or location tolerance value. Then the tolerance zone applies to the high points of the controlled feature only (not to the entire surface irregu-larities) as shown in Fig. 21.5.Fig.21.13Positional tolerance, concentricity tolerance, according to ASME Y14.5, top:extreme permissible workpiece below:workpiece within the posi-tional tolerance but exceeding the concentricity toleranceFor inspection a contacting plate with sufficiently parallel planes may be used (Fig.21.15). At present there is no rule for how to proceed in cases when the plate rocks about the highest points (e.g. when the controlled feature is convex).21.1.8Roundness measurementsANSI B89.3.1 gives the possibility of specifying on drawings for roundness tolerances the measuring conditions, i.e.●reference method, to be selected from:–MRS minimum radial separation –LSC least squares circle –MIC maximum inscribed circle –MCC minimum circumscribed circle ●filter, to be selected from:–0,1.67,5,15,50,150,1500cycles per revolution ●stylus tip radius, to be selected from:–0.001,0.003,0.010,0.030,0.100inFig.21.14Orientation (parallelism) tolerance according to ASME Y14.5applied to the axis of the mating envelope and according to ISO 1101 applied to the actual axisFig.21.15Tangent plane requirement TSee Fig. 21.16.The filters are defined as electrical low-pass filters equivalent to two unloaded RC networks in series. Their nominal value (cut-off) corresponds to the sinusoidal fre-quency (cycles per revolution, cpr) whose amplitude is 70.7% transmitted by the filter.The former standard ISO 4291 specified a slightly different filter characteristic. The nominal value (cut-off) corresponds to the sine wavelength with 75% amplitude trans-mission. However, this difference is practically negligible. The new standard ISO 12181 will change the nominal value (cut-off) corresponding to the sine wavelength with 50% amplitude transmission by the Gauss filter.ANSI B89.3.1 states further that, if not otherwise specified (default case), for round-ness measurements (roundness tolerances) the following measuring conditions apply:●reference method MRS ●filter 50cpr ●tip radius 0.010 in (0.25mm)The ISO Standards have not yet standardized measuring conditions for the default case. If necessary, they must be agreed upon between the parties (e.g. by reference to ANSI B89.3.1). See also 18.10.21.1.9Multiple patterns of featuresAccording to ASME Y14.5M – 1994 positional toleranced multiple patterns of features (two or more patterns of features) located by theoretical exact dimensions relative to the same datum system (datums in the same order of precedence and modification) are regarded as a single pattern (simultaneous requirement), if not otherwise specified, e.g.with the notation “SEP REQT”. This does not apply to the lower segment of compos-ite tolerances (see 21.1.4) unless specific notation is added, e.g. “SIM REQT”. ISO Standards do not specifically express this, see 20.6.5.21.1.10TerminologySome terms given in ASME Y14.5 differ from those given by ISO (see Table 21.3).ASME Y14.5M specifies: FIM Full Indicator Movement: the total movement of an indicator when appropriately applied to a surface to measure its variations. The former terms FIR Full Indicator Reading and TIR Total Indicator Reading have the same meaning as FIM.Fig.21.16Roundness tolerance with measuring conditions according to ANSI B89.3.1ASME Y14.5M defines the terms “resultant condition”, “inner boundary” and “outer boundary” (which are not yet used in ISO Standards) as follows.Resultant condition: The variable boundary generated by the collective effects of a size feature specified MMC or LMC material condition, the geometric tolerance for that material condition, the size tolerance, and the additional geometric tolerance derived from the feature departure from its specified material condition, see Figs 21.17 to 21.20.Inner boundary: A worst case boundary (that is, locus) generated by the smallest fea-ture (MMC for an internal feature and LMC for an external feature) minus the stated geometric tolerance and any additional geometric tolerance (if applicable) from the fea-ture’s departure from its specified material condition, see Figs 21.17 to 21.20.Outer boundary: A worst case boundary (that is, locus) generated by the largest fea-ture (LMC for an internal feature and MMC for an external feature) plus the stated geometric tolerance and any additional geometric tolerance (if applicable) from the fea-ture’s departure from its specified material condition, see Figs 21.17 to 21.20.Table 21.3Comparison of ASME Y14.5 and ISO terminologiesASME Y14.5MISO Basic dimensionTheoretical exact dimension (TED)Feature control frameTolerance frame VariationDeviation True position (TP)Theoretical exact position Reference dimension Auxiliary dimensionFig.21.17Virtual and resultant condition boundaries, internal feature, MMC (a) drawing indication, (b) virtual condition, (c) resultant conditionThese terms may serve to assess the extent of a feature of size relative to its true (theoretical exact) position or to other features.21.1.11Survey of differences between ASME and ISOTable 21.4 together with Tables 21.1 to 21.3 give a survey of the differences between ASME and ISO Standards.Fig.21.18Virtual and resultant condition boundaries, internal feature, LMC (a)drawing indication, (b) virtual condition, (c) resultant conditionFig.21.19Virtual and resultant condition boundaries, external feature, MMC (a) drawing indication, (b) virtual condition, (c) resultant condition21.1.12Drawings for both systems21.1.12.1GeneralDrawings for both systems, ISO and ASME, may be identified by the indication in the drawing title block:ISO 1101, ISO 8015, ASME Y14.5 without rule #1This gives the information where the meanings of the symbols are found. When the same symbol has different meanings in both systems, both meanings must be allowed by the function of the workpiece (and be accepted from the manufacturer) or the stan-dard of the applicable meaning must be allocated to the drawing indication.The following gives recommendations as to how to proceed in the relevant cases.21.1.12.2Envelope requirementThe use of the more economic principle of independency according to ISO 8015 is rec-ommended. When the envelope requirement is necessary the symbol E (ISO 8015) or straightness zero M (ASME Y14.5) is to be indicated, see e.g. Fig. 20.50 (d) and (e).21.1.12.3Angular tolerancesAngular dimensional tolerances (Figs 21.3, 21.4 and 3.45) should be avoided or only be applied to less important cases, when the location of the angle and the form devia-tions need not to be toleranced.Tolerancing of angularity, profile or position according to ISO 1101 is recommended (Figs 3.46, 20.14(b) and 20.19).Fig.21.20Virtual and resultant condition boundaries, external feature, LMC (a) drawing indication, (b) virtual condition, (c) resultant condition。
codev变形非球面表达式_理论说明

codev变形非球面表达式理论说明1. 引言1.1 概述本章节旨在引入本篇文章的主题:CodeV变形非球面表达式。
我们将介绍CodeV软件以及变形非球面表达式的概念、基本原理和数学模型,并提供示例和应用实例。
此外,我们也会总结文章的主要结论并讨论存在的问题和改进方向。
1.2 文章结构本文共分为五个部分,各部分内容如下:- 第一部分是引言,对文章的主题进行了简要介绍。
- 第二部分是CodeV变形非球面表达式,其中包括CodeV软件简介、变形非球面表达式概述和表达式的基本原理。
- 第三部分是理论说明,涵盖了变形非球面的数学模型、表达式的推导过程与参数说明以及示例及应用实例。
- 第四部分是结论与展望,总结了文章的主要结论,并探讨存在问题和改进方向。
- 最后一部分是参考文献,列出了本文所引用的相关文献。
1.3 目的本文旨在阐明CodeV中变形非球面表达式的相关理论知识,并通过概述、数学模型推导、参数说明及应用示例等方式深入解释其工作原理和应用场景。
通过本文的阅读,读者将能够全面了解CodeV变形非球面表达式,并具备一定的理论指导和实际应用能力。
2. CodeV变形非球面表达式2.1 CodeV软件简介CodeV是一款用于光学设计和分析的专业软件。
它提供了多种功能,包括光学系统设计、非球面表面设计、光学材料模型以及成像质量评估等。
CodeV在光学行业中被广泛应用,能够帮助工程师们快速高效地进行光学系统设计和优化。
2.2 变形非球面表达式概述变形非球面是指那些不符合传统几何形状的光学表面。
传统的几何形状通常可以用简单的数学公式表示,而变形非球面则需要更复杂的数学模型来描述其曲率分布。
在CodeV中,变形非球面由一系列参数化的表达式来描述。
这些表达式可以根据具体需求进行修改和调整,从而实现特定的光学效果。
通过调整这些参数,工程师们可以方便地控制和优化光学系统的性能。
2.3 表达式的基本原理Variation(Var)语言是CodeV用于描述变形非球面表达式的编程语言。
Mechanical Drawing机械制图-8 geometric tolerances形位公差

4MD_08_0910Mechanical Drawing Dependence between dimension and form •Evaluating the fit conditions with the reference element just through the dimensions takes you to ignore the form deviation effects: A clearance (sliding) fit h/H shaft-hole becomes an interference fit if cylindricity and straightness conditions are poorParallel axes Coaxial axesIncident axes Skew axesTolerance zone+57%15MD_08_0910Mechanical Drawing L, M are dimensions to position the feature Datum •Datum is a theoretical point, line, plane, or other dimensions are measured when so specified orDatum planes Measurement directions Datum axis Datum axis Datum axis Datum Reference Frame origin Each part to be machined or measured has 6 degrees of freedom •The reference system three datum planes mutually perpendicular, referred to as: Three-plane datum system Datum Reference Frame22MD_08_0910Mechanical Drawing•The box is connected to a solid or blank triangle27MD_08_0910Mechanical Drawing Primary Datum :•Orients the part •At least 3 points of contact to eliminate • 1 translation • 2 rotations Secondary Datum :•Positions the part •Perpendicular to primary datum •At least 2 points of contact to eliminate • 1 translation • 1 rotation Tertiary Datum :•Blocks the part •Perpendicular to the other planes •At least 1 point of contact to eliminate • 1 translationMD_08_0910Mechanical Drawing centerMechanical Drawing35MD_08_091036Mechanical Drawing •The tolerance zone can be bilateral or unilateral 37Mechanical Drawing Profile of a surface •The tolerance zone is limited by two envelope diameter equal to the tolerance value where the centers are on the true surface •The tolerance zone can be bilateral or unilateralMD_08_0910Mechanical Drawing。
土木工程英文翻译1

* Corresponding author. Tel.: +852-2766-7820; fax: +852-23654703.
E-mail address: mmlhyam@.hk (L.H. Yam).
0263-8223/$ - see front matter Ó 2003 Elsevier Ltd. All rights reserved. doi:10.1016/pstruct.2003.09.038
378
Z. Wei et al. / Composite Structures 64 (2004) 377–387
齿轮参数中英文对照表
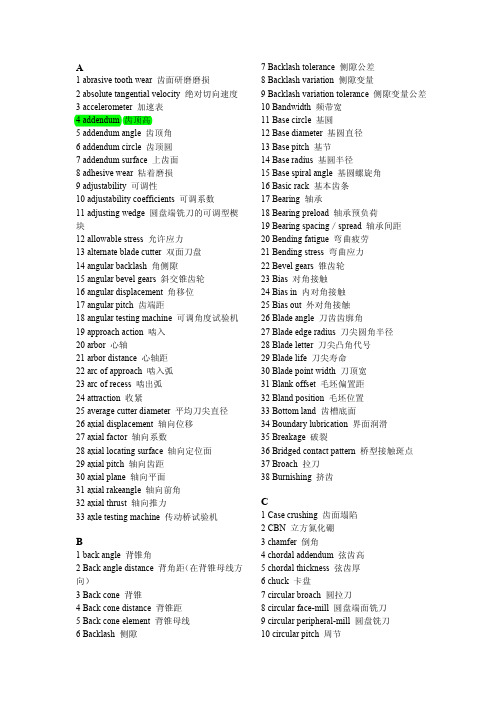
A1 abrasive tooth wear 齿面研磨磨损2 absolute tangential velocity 绝对切向速度3 accelerometer 加速表4 addendum 齿顶高5 addendum angle 齿顶角6 addendum circle 齿顶圆7 addendum surface 上齿面8 adhesive wear 粘着磨损9 adjustability 可调性10 adjustability coefficients 可调系数11 adjusting wedge 圆盘端铣刀的可调型楔块12 allowable stress 允许应力13 alternate blade cutter 双面刀盘14 angular backlash 角侧隙15 angular bevel gears 斜交锥齿轮16 angular displacement 角移位17 angular pitch 齿端距18 angular testing machine 可调角度试验机19 approach action 啮入20 arbor 心轴21 arbor distance 心轴距22 arc of approach 啮入弧23 arc of recess 啮出弧24 attraction 收紧25 average cutter diameter 平均刀尖直径26 axial displacement 轴向位移27 axial factor 轴向系数28 axial locating surface 轴向定位面29 axial pitch 轴向齿距30 axial plane 轴向平面31 axial rakeangle 轴向前角32 axial thrust 轴向推力33 axle testing machine 传动桥试验机B1 back angle 背锥角2 Back angle distance 背角距(在背锥母线方向)3 Back cone 背锥4 Back cone distance 背锥距5 Back cone element 背锥母线6 Backlash 侧隙7 Backlash tolerance 侧隙公差8 Backlash variation 侧隙变量9 Backlash variation tolerance 侧隙变量公差10 Bandwidth 频带宽11 Base circle 基圆12 Base diameter 基圆直径13 Base pitch 基节14 Base radius 基圆半径15 Base spiral angle 基圆螺旋角16 Basic rack 基本齿条17 Bearing 轴承18 Bearing preload 轴承预负荷19 Bearing spacing/spread 轴承间距20 Bending fatigue 弯曲疲劳21 Bending stress 弯曲应力22 Bevel gears 锥齿轮23 Bias 对角接触24 Bias in 内对角接触25 Bias out 外对角接触26 Blade angle 刀齿齿廓角27 Blade edge radius 刀尖圆角半径28 Blade letter 刀尖凸角代号29 Blade life 刀尖寿命30 Blade point width 刀顶宽31 Blank offset 毛坯偏置距32 Bland position 毛坯位置33 Bottom land 齿槽底面34 Boundary lubrication 界面润滑35 Breakage 破裂36 Bridged contact pattern 桥型接触斑点37 Broach 拉刀38 Burnishing 挤齿C1 Case crushing 齿面塌陷2 CBN 立方氮化硼3 chamfer 倒角4 chordal addendum 弦齿高5 chordal thickness 弦齿厚6 chuck 卡盘7 circular broach 圆拉刀8 circular face-mill 圆盘端面铣刀9 circular peripheral-mill 圆盘铣刀10 circular pitch 周节11 circular thickness 弧齿厚12 circular thickness factor 弧齿厚系数13 clearance 顶隙14 clearance angle 后角15 coarse pitch 大节距16 coast side 不工作齿侧17 combination 组合18 combined preload 综合预负荷19 complementary crown gears 互补冠状齿轮20 completing cycle 全工序循环21 composite action 双面啮合综合检验误差22 compressive stress 压应力23 concave side 凹面24 concentricity 同心度25 concentricity tester 同心度检查仪26 cone distance 锥距27 cone element 锥面母线28 conformal surfaces 共型表面29 coniskoid 斜锥齿轮30 conjugate gears 共轭齿轮31 conjugate racks 共轭齿条32 contact fatigue 接触疲劳33 contact norma 接触点法线34 contact pattern (tooth contact pattern) 轮齿接触斑点35 contact ratio 重合度36 contact stress 接触应力37 continuous index 连续分度38 control gear 标准齿轮,检验用齿轮39 convex side 凸面40 coolant 冷却液41 corrosive wear 腐蚀性磨损42 corrugated tool 阶梯刨刀43 counter forma surfaces 反法向表面44 cradle 摇台45 cradle test roll 摇台角46 cross 大小端接触47 crossing point 交错点48 crown 齿冠49 crown circle 锥齿轮冠圆50 crowned teeth 鼓形齿51 crown gear 冠轮52 crown to back (轮冠距)轮冠至安装定位面距离53 crown to crossing point 轮冠至相错点距离54 cutter 刀盘55 cutter axial 刀盘的轴向位置56 cutter axial plane 刀盘轴向平面57 cutter axis 刀盘轴线58 cutter diameter 刀盘直径59 cutter edge radius 刀刃圆角半径60 cutter head 刀盘体61 cutter number 刀号62 cutter parallel 刀盘平垫片63 cutter point diameter 刀尖直径64 cutter point radius 刀尖半径65 cutter point width 刀顶距66 cutter spindle 刀盘主轴67 cutter spindle rotation angle 刀盘主轴转角68 cutting distance 切齿安装距69 CV testing mashing 常速试验机70 cyclex 格里森粗铣精拉法圆盘端铣刀71 cylindrical gears 圆柱齿轮D1 Datum tooth 基准齿2 Debur 去毛刺3 Decibel (CB) (噪音)分贝4 Decimal ratio 挂轮比值5 Dedendum 齿根高6 Dendendum angle 齿根角7 Dedendum surface 下齿面8 Deflection 挠曲9 Deflection test 挠曲试验10 Deflection testing machine 挠曲试验机11 Depthwise taper 齿高收缩12 Design data sheet 设计数据表13 Destructive pitting 破坏性点蚀14 Destructive wear 破坏性磨损15 Developed setting 试切调整16 Dial indicator 度盘式指示表17 Diametral pitch 径节18 Diamond 菱形接触19 Dinging ball check 钢球敲击检查20 Disc-mill cuter 盘铣刀21 Dish angle 凹角22 Displacement 位移23 Displacement error 位移误差24 Double index 双分度25 Double roll 双向滚动26 Down roll 向下滚动27 Drive side 工作齿侧28 Duplete 双刃刀29 Duplex 双重双面法30 Duplex helical 双重螺旋法(加工方法之一)31 Duplex spread blade 双重双面刀齿(加工/磨齿方法)32 Duplex taper 双重收缩齿33 Durability factor 耐久系数34 Dynamic factor 动载荷系数E1 Ease-off 修正、失配2 Eccentric 偏心3 Eccentric angle 偏心角4 Eccentricity 偏心度5 Edge radius 刀尖圆角半径6 Effective bearing spacing 轴承有效间距7 Effective face width 有效宽度(有效齿宽)8 Elastic coefficient 弹性系数9 Elastic deformation 弹性变形10 Elastic limit 弹性极限11 Elastohydrodynamic lubrication 弹性液压润滑12 Element 母线、要素13 End movement 轴向移动14 Endrem 修内端凸轮、导程凸轮15 Endurance life 耐久寿命16 Endurance limit 耐久极限17 Engine torque 发动机扭矩18 Enveloping 包络19 EP lubricant, EP 极压润滑剂20 EPG check, “EPG” 检查21 Equal addendum teeth 等齿顶高齿22 Equicurv 等高齿大轮成形法23 Equidep 等高齿24 Equiside 等边25 Equivalent fear ratio 当量传动比26 Equivalent number of teeth 当量齿数27 Equivalent pitch radius 当量节圆半径28 Equivalent rack 当量齿条29 Expander 涨胎30 Expanding arbor 可张心轴31 Extreme pressure lubricant 极压润滑剂F1 Face acvance 斜齿轮扭曲量2 Face angle 顶锥角(面锥角)3 Face angle distance 顶锥角距4 Face apex 顶锥顶5 Face apex beyond crossing point 顶锥顶至相错点距离6 Face cone 顶锥7 Face cone element 齿顶圆锥母线,面锥母线8 Face contact ratio 齿长重合度,轴向重合度(圆柱齿轮)9 Face line 齿面与轴面交线10 Face width 齿宽11 Factor of safety 安全系数12 Fatigue breakage 疲劳破裂13 Fatigue failure 疲劳失效14 Fatigue test 疲劳测试15 Feed cam 进给凸轮16 Feed gears 进给齿轮17 Fillet 齿根圆角18 Fillet curve 齿根过渡曲线19 Fillet radius 齿根圆角半径20 Film strength 液膜强度21 Filter (electronic) (电子的)滤波器22 Filter (mechanical) (机械的)滤波器23 Fine pitch (小模数)细径节24 Finisher 精切机床25 Fishtail 鱼尾形26 Fixed setting 固定安装法27 Flank 下齿面28 Flanking 下齿面加工29 Formarc 加工齿轮用的曲线齿廓刀具30 Formate 成形法31 Former 齿廓样板,靠模32 Forming 成型,在磨具内挤压成型33 Form tool 成形刀34 Fourier analysis 傅里叶分析35 Frequency 频率36 Friction load 摩擦负荷37 Front angle 前角38 Front cone 前锥39 Front crown 前锥齿冠40 Front crown to crossing point 前锥齿冠至交错点41 Full-depth teeth 全齿高齿42 Fundametal 基频G1 Gable 山形齿沟底面2 Gear 齿轮3 Gear axial displacement 齿轮轴向位移4 Gear axial plane 齿轮轴向平面5 Gear axis 齿轮轴线6 Gear center 齿轮中心7 Gear combination 齿轮组合8 Gear cone 大轮锥距9 Geared index 齿轮系分度10 Gear finisher 成形法齿轮精切机床11 Gear manufacturing summary 齿轮加工调整卡12 Gear marking compound 检查齿轮啮合涂色剂13 Gear member 大轮14 Gear planer 成型刨齿机15 Gear ratio 齿数比16 Gear rougher 齿轮粗切机床17 Gears 齿轮组18 Gear tipping 齿轮倾斜19 Generated gear 展成法齿轮20 Generating cam 展成凸轮21 Generating gear 展成齿轮22 Generating pressure angle 产形轮压力角23 Generating train 展成传动键24 Generation 展成25 Generator 展成齿轮加工机床26 Geneva index 星形轮分度,槽轮分度27 Geometry factor-durability 齿面接触强度几何系数28 Geometry factor0-strength 强度几何系数29 G-flow 格里森制金属件的商标,采用冷挤压成形法30 G-form 采用热锻成形法制造31 GLE-sine 砂轮内外压力角正弦波进行修整用机构32 G-plete 全工序法33 Gradeability 托曳力34 Grinding cracks 磨削裂纹35 G-spin 精密主轴的机床36 G-trac 圆柱齿轮的无端链式机床的商标H1 Hand of cutter 刀盘方向2 Hand of spiral 螺旋方向3 Hand-rolling tester 手动滚动试验机4 Hardac 镶篇淬硬刀体精切刀盘5 Hard finishing 硬齿面精加工6 Hardness ratio factor 硬度比系数7 Harmonic 谐振8 Harmonic search 谐振追踪9 Harmonic sweep 谐振扫描10 Heel 轮齿大端11 Heel pattern 大端接触12 Helical duplex 双重螺旋法13 Helical motion 螺旋运动14 Helixact 螺旋运动法15 Helixform 螺旋成形法16 Hertz (Hz) 赫兹17 Hook angle 断面前角18 Horizontal displacement 水平位移19 Horizontal offset 水平偏置20 HRH 高减速比准双曲面齿轮(大于10:1的减速比)21 Hunting tooth combination 大小齿轮齿数无公因数的齿轮副22 Hudrodynamic lubrication 液压润滑23 Hupermesh 超配合24 Hypoid gears 准双曲面齿轮25 Hypoid offset 准双曲面齿轮偏置距I1 Imaginary generating gear 假想成形法2 Incremental index 逐齿分度3 Index gears 分度齿轮4 Index interval 分度跳跃齿齿数5 Index plate 分度盘6 Index tolerance 分度公差7 Index variation 分度变化量8 Indicator anchorage 指示表支撑座9 Inertia factor 惯量系数10 Initial pitting 初期点蚀11 Inner addendum 小端齿顶高12 Inner cone distance 小端锥距13 Inner dedendum 小端齿根高14 Inner slot width 小端槽宽15 Inner spiral angle 小端螺旋角16 Inserted blade cutter 镶片刀盘17 Inside blade 内切刀齿18 Inside point diameter 内切刀尖直径19 Instantaneous contact pattern 瞬时接触斑点20 Interference 干涉21 Interference point 干涉点22 Interlocking disc-mill cutters 交错齿盘形铣刀23 Intermittent index 间断分度24 Internal bevel gear 内锥齿轮25 Inverse gear ratio 反齿数比26 Involute 渐开线27 Involute gear 渐开线齿轮28 Involute interference point 渐开线干涉点29 Involute spiral angle 渐开线螺旋角30 Involute teeth 渐开线齿J1 Jet lubrication 喷射润滑L1 Lame 顶根接触2 Lapping 研磨3 Lead cam 导程凸轮4 Length of action 啮合长度5 Lengthwise bridge 纵向桥型接触6 Lengthwise mismatch 纵向失配7 Lengthwise sliding velocity 纵向滑动速度8 Life factor 寿命系数9 Lift 垂直位移10 Limit point width 极限刀顶距11 Limit pressure angle 极限压力角12 Linear displacement transducer 线性位移传感器13 Line of action 啮合线14 Line of centers 中心线15 Line of contact 接触线16 Load sharing ratio 负荷分配比17 Localized tooth contact 齿局部接触18 Locating surface 定位表面19 Long-and-short-addendum teeth 高变位齿轮20 Long-toe-short-heel 小端长,大端短接触21 Lubricant 润滑剂22 Lubrication 润滑23 Lubricity 润滑性M1 Machine center 基床中心点2 Machine center to back 机床中心至工件安装基准面3 Machine plane 机床切削平面4 Machine root angle 毛坯安装角5 Marking compound 检查齿轮啮合型情况使用的涂色剂6 Master blade 标准刀齿7 Master gear 标准齿轮8 Mean addendum 中点齿顶高9 Mean cone distance 中点锥距10 Mean dedendum 中点齿根高11 Mean diametral pitch 中点径节12 Mean measuring addendum 中点测量齿顶高13 Mean measuring depth 中点测量齿高14 Mean measuring thickness 中点测量厚度15 Mean normal base pitch 中点法向基节16 Mean normal diameter pitch 中点法向径节17 Mean normal module 中点法向模数18 Mean point 中点,平均点19 Mean radius 中点半径20 Mean section 中点截面21 Mean slot width 中点齿槽宽22 Mean spiral angle 中点螺旋角23 Measuring addendum 测量齿顶高24 Measuring tooth thickness 测量齿厚25 Member 齿轮,元件26 Mesh point 啮合点27 Minimum slot width 最小槽宽28 Mismatch 失配29 Miter gears 等齿数整角锥齿轮副30 Mixed lubrication 混合润滑31 Modified contact ratio 修正总重合度32 Modified roll 滚修正比33 Module 模数34 Motion curves 运动曲线35 Motor torque 电机扭矩36 Mounting distance 安装距37 Mounting surface 安装面N1 Narrow-tow-wide-heel 小端窄大端宽接触2 No load 空载3 Nominal 名义4 Non-generated gear 非展成大轮5 Normal 法向,法线,法面6 Normal backlash 法向侧隙7 Normal backlash tolerance 法向侧隙公差8 Normal base pitch 法向基节9 Normal chordal addendum 法向弦齿高10 Normal chordal thickness 法向弦齿厚11 Normal circular pitch 法向周节12 Normal circular thickness 法向弧齿厚13 Normal contact ratio 法向重合度14 Normal diametral pitch 法向径节15 Normal direction 法线方向16 Normal (perpendicular) load 法向(垂直)负载17 Normal module 法向模数18 Normal plane 法向平面19 Normal pressure angle 法向压力角20 Normal section 法向截面21 Normal space-width taper 正常齿槽宽收缩22 Normal thickness taper 正常齿厚收缩23 Normal tilt 法向刀倾24 Normal wear 正常磨损25 No-roll roughing 无滚动粗切26 Number of teeth 齿数O1 Octoid teeth 锥齿轮的“8”字啮合2 Offset 偏置距3 Operating load 工作负荷4 Operating pressure angle 工作压力角5 Operating torque 工作扭矩6 Outer addendum 大端齿顶高7 Outer cone distance 外锥距8 Outer dedendum 大端齿根高9 Outer slot width 大端槽宽10 Outer spiral angle 大端螺旋角11 Outside blade 外切刃点12 Outside diameter 外径,大端直径13 Outside point diameter 外切刀尖直径14 Outside radius 齿顶圆半径15 Outside surface 外表面16 Overhung mounting 双支承安装17 Overload breakage 超负荷破裂18 Overload factor 超负荷系数P1 Path of action 啮合点轨迹2 Path of contact 接触迹3 Peak load 峰值负荷4 Peak torque 峰值扭矩5 Pedestal bearings 安装差速器壳的架座轴承6 Performance torque 性能扭矩7 Perim-mate 研磨锥齿轮和准双面齿轮用的全齿面研磨法8 Pinion 小轮9 Pinion axial displacement 小轮轴向位移10 Pinion cone 小轮锥距11 Pinion front bearing 小轮前端轴承12 Pinion head bearing 小轮后端前轴承13 Pinion rear bearing 小轮后端后轴承14 Pinion rougher 小轮粗切机15 Pinion offset 小轮偏置距16 Pitch 节距,齿距17 Pitch angle 节锥角18 Pitch apex 节锥顶19 Pitch apex beyond crossing point 节锥顶超出至相错点20 Pitch apex to back 节锥顶至安装端面21 Pitch apex to crown 节锥顶至轮冠22 Pitch circle 节圆23 Pitch cone 节锥24 Pitch curve 节面曲线25 Pitch diameter 节径26 Pitch element 节面母线27 Pitch line 节线28 Pitch-line chuck 节圆夹具29 Pitch-line runout 节线跳动30 Pitch plane 节面31 Pitch point 节点32 Pitch radius 节圆半径33 Pitch surfaces 节曲面34 Pitch tolerance 齿距公差35 Pitch trace 节线36 Pitch variation 齿距变化量37 Pitting 点蚀38 Plane of action 啮合平面39 Plane of rotation 旋转平面40 Planning generator 展成法刨齿机41 Plastic deformation 塑性变形42 Plastic flow 塑性流动43 Plate index 分度盘44 Point diameter 刀尖直径45 Point of contact 接触点46 Point radius 刀尖半径47 Point width 刀顶距48 Point width taper 刀顶距收缩49 Pressure lubrication 压力润滑50 Prime mover torque 原动机扭矩51 Profile angle 齿廓角52 Profile bridge 齿廓桥形接触53 Profile contact ratio 齿廓重合度54 Profile mismatch 齿廓啮合失配55 Profile radius of curvature 齿廓曲率半径56 Proof surface 检测基准面Q1 Quality measurement system 质量检测系统2 Quenching cracks 淬火裂纹3 Quenching die 淬火压模4 Quenching press 淬火压床R1 Rack 齿条2 Radial 径向刀位3 Radial load 径向负荷4 Radial locating surface 径向定位表面5 Radial rake angle 径向前角6 Ratio control roughing 变滚比粗切7 Ratio gears 滚比挂轮8 Ratio of roll 滚比9 Ratio of roll gears 滚比挂轮10 Recess action 啮出11 Relative displacement 相对位移12 Relative movement 相对运动13 Relative radius of curvature 相对曲率半径14 Residual stress 残余应力15 Revacycle 直齿锥齿轮圆拉法用机床及刀具16 Revex 直齿锥齿轮粗拉法17 Ridg-AC 镶片圆盘端面粗铣刀18 Ridging 沟条变形19 Ring gear 大轮,环形齿轮20 Rippling 振纹21 Roll centering 滚动定心22 Roll queching 滚动式淬火压床23 Roll gears 摆角挂轮24 Rolling 滚轧25 Rolling velocity 滚动速度26 Root angle 根锥角27 Root angle tilt 齿根角倾斜28 Root apex 根锥顶29 Root apex beyond crossing point 根锥顶至相错点的距离30 Root apex to back 根锥顶至安装基准面距离31 Root circle 齿根圆32 Root cone 根锥33 Root diameter 根圆直径34 Root line 齿根线35 Root radius 根圆半径36 Root surface 齿根曲面37 Roughac 弧齿锥齿轮粗切刀38 Rougher 粗切机39 RSR 弧齿锥齿轮条形刀齿铣刀盘40 Runout 径向跳动41 Runout tolerance 径向跳动公差S1 Scoring 胶合2 Scoring index 胶合指数3 Scuffing 胶合4 Sector 扇形齿/齿弧5 Segment 扇形齿/体6 Segmental-blade cutter 大轮精切刀7 Separation 分离间隙8 Separating factor 分离系数9 Separating force 分离力10 Set-in 补充切入,进刀11 Set-over 补充转角,调整转换12 Shaft angle 轴转角13 Shot peening 喷丸强化14 Sidebank 边频15 Side movement 侧向位移16 Side rake angle 侧前角17 Single cycle 单循环法18 Single roll 单滚动19 Single setting 单面调整法20 Single side 单面精切法21 Single-side taper 齿槽收缩22 Size factor 尺寸系数23 Skew bevel gears 斜直齿锥齿轮24 Skip index 跳齿分度25 Slide-roll ratio 单位滑滚比,比滑26 Sliding base 床鞍,滑座27 Sliding base setting 床鞍调整,滑座调整28 Sliding velocity 滑动速度29 Slip-chip 直齿锥齿轮一次成形刀30 Slip torque 滑移扭矩31 Slotting tool 切槽刀32 Slot width 槽宽33 Slot-width taper 槽宽收缩34 Small cutter development 小刀盘试切,能产生接近渐开线的刀具35 Solid cutter 整体刀盘36 Sound test 噪声试验37 Space-width taper 齿距收缩38 Spacing tolerance 齿距公差39 Spacing variation 齿距变动量40 Spalling 剥落41 Specific sliding 单位滑动比42 Speed gears 速度挂轮43 Spherical involute teeth 球面渐开线齿44 Spherica limacon teeth 球面钳线齿45 Spindle rotation angle 主轴旋转角46 Spiral angle 螺旋角47 Spiral bevel gears 弧齿锥齿轮48 Splash lubrication 飞溅润滑49 Split profile 齿型中断50 Spread blade 双面刀51 Spread blade 双面刀渐缩52 Standard depthwise taper 标准深锥度53 Standard taper 正常收缩54 Standard thickness 正常齿厚收缩55 Stock allowance 毛坯加工流量56 Straddle cutter 双列刀齿刀盘57 Straddle mounting 跨装58 Straight bevel gears 直齿锥齿轮59 Strength factor 强度系数60 Stress concentration factor 应力集中系数61 Stub teeth 短齿62 Subsurface initiated fatigue breakage 金属表面斜层初始疲劳破裂63 Summary of machine settings 机床调整卡64 Sump lubrication 油槽润滑65 Sum velocity 总速度66 Surface asperities 表面粗糙度67 Surface condition factor 表面条件系数68 Surface deformation 表面变形69 Surface durability 表面耐久度70 Surface fatigue 表面疲劳71 Surface initiated fatigue breakage 表面初始疲劳破裂72 Surface of action 啮合面73 Surface of revolution 回转面74 Surface treatment 表面处理75 Swinging base 回转底座76 Swing pinion cone 摆动小轮节锥法77 Swivel 刀转78 Swivel angle 刀转角79 Symmetrical rack 对称齿条80 Symmetrical rack proportions 对称齿条比例T1 Tangential load 切向负荷2 Tangent plane 切平面3 Tanline 小轮夹具4 Tanruf 双联粗切刀,85模数一下5 Tan-tru 用在加工1016-2540mm的锥齿刀具6 Taper roughing 具有刀顶距收缩的大小轮粗切过程7 Temperature factor 温度系数8 Testing machine 试验机9 Thickness taper 齿厚收缩10 Tilt 刀倾11 Tilt angle 刀倾角12 Tilted rootline taper 倾斜齿根收缩13 Tip radius 齿顶圆角半径14 Toe 轮齿小端15 Toe pattern 小端接触16 Tool 刀具17 Tool advance 刀具进刀18 Tool edge radius 刀刃圆角半径19 Tool point width 刀顶距20 Tooth angle 齿角21 Tooth bearing 齿支撑面,轮齿接触面22 Tooth contact analysis 轮齿接触分析23 Tooth contact pattern 轮齿接触斑点24 Tooth horizontal 齿水平面25 Tooth layout 轮齿剖面图26 Tooth-mesh frequency 齿啮合频率27 Tooth number 齿数28 Tooth profile 齿形,齿廓29 Tooth spacing testing 齿距检查仪30 Tooth spiral 齿螺旋线31 Tooth surface 轮齿表面32 Tooth taper 轮齿收缩33 Tooth-to-tooth composite tolerance 一齿度量中心距公差34 Tooth-to- Tooth composite variation 一齿度量中心距变量35 Tooth trace 齿线36 Tooth vertical 齿垂直面37 Top 齿顶38 Topland 齿顶面39 Topland width 齿顶面宽度40 Topping 修顶41 Top relief angle 顶刃后角42 Toprem 修根刀片43 Toprem angle 刀齿突角角度44 Top slope angle 刀齿顶刃倾角45 Total composite tolerance 总综合公差46 Total composite variation 总度量中心距变动量47 Total contact ratio 总重合度48 Total index tolerance 总分度公差49 Total index variation 总分度变动量50 Tractive effort torque 牵引力扭矩51 Transverse circular pitch 端面周节52 Transverse circular thickness 端面弧齿厚53 Transverse contact ratio 端面重合度54 Transverse diametral pitch 端面径节55 Transverse module 端面模数56 Transverse plane 端平面57 Transverse pressure angle 端面压力角58 Transverse space-width taper 端面槽宽收缩59 Transverse thickness taper 端面齿厚收缩60 Tredgold’s approximation 背锥近似法61 Tribology 润滑与磨损学62 Triplex 三面刃圆盘端铣刀63 Two-tool generator 双刀展成加工机床U1 Undercut 根切2 Undeveloped settings 试切前调整3 Uniform roll 匀速滚动4 Uniform velocity tester 匀速试验机5 Uni-spand 大轮心轴6 Unit load 单位负荷7 Unitool 曲面镶片刀8 Up-roll 向上滚动V1 V and H check 锥齿轮啮合的VH检查2 Variable roll 变滚动3 Velocity factor 速度系数4 Versacut 弧齿锥齿轮加工多用刀盘5 Vers-grip 卡紧小齿轮用的卡盘(商标名称)6 Vertical direction 垂直方向7 Vertical displacement 垂直位移8 Vertical factor 垂直系数9 Vertical force 垂直力10 Vertical offset 垂直偏置距11 Vertical plane 垂直面12 Virtual number of teeth 当量齿数13 Virtual pitch radius 当量节圆半径14 Viscosity 粘度15 V-tool V型刀具W1 Waveform 波形2 Wear 磨损3 Webless-type gear 无幅板式齿轮4 Web-type gear 幅板式齿轮5 Wheel slip torque 车轮打滑扭矩6 Whole depth 齿全高7 Workhead 工件头座8 Workhead offset 垂直轮位9 Workholding equipment 工件夹具10 Working depth 工作齿高11 Working stress 工作允许应力12 Work tests roll 检验工件主轴转角X1X-pandisk 大轮蝶形,涨胎心轴Z1 Zero depthwise taper 等齿高2 Zerol 零度锥齿轮。
VW 137 05-2003-粗糙度(英文)

Vertragspartner erhalten die Norm nur über die zuständige Beschaffungsabteilung.Confidential. All rights reserved. No part of this document may be transmitted or reproduced without the prior written permission of a Standards Department of the Volkswagen Group.Parties to a contract can only obtain this standard via the responsible procurement department.VOLKSWAGEN AGN o r m v o r A n w e n d u n g a u f A k t u a l i t ät p r üf e n / C h e c k s t a n d a r d f o r c u r r e n t i s s u e p r i o r t o u s a g e .T h e E n g l i s h t r a n s l a t i o n i s b e l i e v e d t o b e a c c u r a t e . I n c a s e o f d i s c r e p a n c i e s t h e G e r m a n v e r s i o n s h a l l g o v e r n .Q U E L L E : N O L I SPage 2VW 137 05: 2003-01of entry (15)9 Examplesflanks (15)9.1 Toothform elements (15)9.2 Repeated9.3 Symmetrical parts (16)specifications on one surface (16)9.4 Differentsurfaces (16)9.5 Contactchamfers (17)9.6 Radii,9.7 Radii and chamfers without specific surface requirements (18)9.8 Multiplerequirements (18)process, surface character (19)9.9 Production9.10 Length of the evaluation length (19)9.10.1 Length of the evaluation length in the event of dominant waviness (20)of the surface lay (20)9.11 Specificationthe machining allowance (22)of9.12 Specificationspecification (22)9.13 Simplified9.14 Examples of entries for porous and stratified heavy-duty contact surfaces (23)10 Surface parameter for special functions (23)transmission characteristic (23)10.1 Specificationof10.2 Meaning and specification of the evaluation length and the sampling length for special cases (23)Annex A Synoptive tables (informative) (26)Annex B Examples (informative) (28)Annex C Comparison of Ra and Rz (informative) (31)Annex D Former practice (informative) (33)Books to refer to: (33)ChangesThe following changes have been made as compared to VW 137 05: 1992-09:─Terms coordinated with the national and international standards─Symbols introduced for the textual indication of surface─Code letter introduced for the minimum dimension─Specification of the sampling lengths changed─Surface requirements specifications for dominant waviness introduced─Surface parameters for specific functions introduced─Position of Ra amendedPrevious issues1967-08; 1971-02; 1974-10; 1975-07; 1983-10; 1983-11; 1992-09Page 3VW 137 05: 2003-01PrefaceEssential points relating to the indication of surface texture were changed in the standard DIN EN ISO 1302:2002 with respect to the preceding issue DIN ISO 1302:1993.The new issue contains surface parameters, some of which are not common in the automotive industry, while other, previously common, parameters are no longer standardized. In addition, new rules, which were previously not the norm, were introduced to describe exactly the nature of the surface along with new filters. This standard was developed in order to maintain the continuity of the previous specifications and to keep the possible number of specifications for the general case under control.The following metrological basis applies:The standardized filter is the Gaussian filter according to DIN EN ISO 11562.The normal evaluation length for the R profile comprises 5 sampling lengths.The original meaning for the maximum roughness, Rmax, and the designation are retained and defined in VW 101 24 (VDA 2006).The use of the short wave filter λs is not permitted unless specifically requested in the technical product documentation.The long wave filter λc is used.The 16% rule is not applied. The actual values may not exceed or fail to reach the specified roughness values, as appropriate.The motif parameters according to DIN EN ISO 12085 and the description of the height of surfaces from two vertical random components using the material probability curve according to DIN EN ISO 13565-3 are not used because there has been no experience with them.Comparison of DIN EN ISO 1302 / VW 137 05 (VDA 2005)DIN EN ISO 1302 VW 137 05 (VDA 2005)Motif parameters Not permissibleRzmax 2.5 Rz 2.5No longer standardized RmaxRz1max 2.5 Not permissibleRz3max 2.5 0.8x3/Rz 2.5Rtmax 2.5 Not permissible16% rule Not permissible0.08-2.5/Rz 6.3 Not permissible1 ScopeThis standard describes the rules applicable within the automotive industry for specifying surface texture, the primary concern of surface finish analysis, in technical product documentation (e.g. drawings, specifications, contracts, reports) by means of graphical symbols and textual indications. Its aim is to simplify the use of the new edition of DIN EN ISO 1302 and it describes the normal case.The surface specifications listed are recommendations. Particular requirements may necessitate the use of other surface specifications.The images in this standard are examples to illustrate the relevant rule. They are complete only insofar as they represent the described situation.This standard does not describe the specification of requirements for surface imperfections, such as pores and scratches.The rules and procedures for assessing surface texture are defined in VW 101 24 (VDA 2006).Page 4VW 137 05: 2003-01references2 NormativeThe following normative documents contain specifications that, through reference in this text, constitute provisions of this standard. For dated references, subsequent amendments or revisions to this publication do not apply. Users of this standard are nevertheless requested to check whether it is possible to use the latest versions of the following normative documents. For undated references, the latest edition of the normative document referred to applies. Members of ISO and IEC maintain registers of valid international standards. DIN 6790-1:1980, Specification by terms in technical drawings; termsDIN EN ISO 1302:2002, Geometrical Product Specifications (GPS) – Indication of Surface Texture in Technical Product DocumentationDIN EN ISO 3098-1:1999, Technical Product Documentation – Lettering – Part 1: Latin Alphabet, Numerals and MarksDIN EN ISO 4287:1998, Geometrical Product Specifications (GPS) – Surface Texture: Profile Method – Terms, Definitions and Surface Texture ParametersDIN EN ISO 4288:1998, Geometrical Product Specifications (GPS) – Surface Texture: Profile Method – Rules and Procedures for the Assessment of Surface TextureDIN EN ISO 11562:1998, Geometrical Product Specifications (GPS) – Surface Texture: Profile Method – Metrological Characteristics of Phase Correct FiltersDIN EN ISO 12085:1998, Geometrical Product Specifications (GPS) – Surface Texture: Profile Method – Motif ParametersDIN EN ISO 13565-1:1998, Geometrical Product Specifications (GPS) – Surface Texture: Profile Method – Surfaces Having Stratified Functional Properties – Part 1: Filtering and General Measurement ConditionsDIN EN ISO 13565-2:1998, Geometrical Product Specifications (GPS) - Surface Texture: Profile Method – Surfaces Having Stratified Functional Properties – Part 2: Height Characterization using the Linear Material Ratio CurveDIN EN ISO 13565-3:2000, Geometrical Product Specifications (GPS) – Surface Texture: Profile Method – Surfaces Having Stratified Functional Properties – Part 3: Height Characterization using the Material Probability CurveVW 101 24: 2002 (VDA 2006: 2002), Geometrical Product Specifications (GPS), Surface Texture: Rules and Procedures for Evaluating the Surface Finish.VW 101 25: 2003 (VDA 2007: 2002), Geometrical Product Specifications (GPS), Surface Texture: Definitions and Characteristic Values of the Dominant Waviness.Page 5VW 137 05: 2003-013 Definitionssymbol3.1 BasicGraphical symbol indicating that surface texture requirements exist, figure 1.symbol3.2 ExpandedExpanded basic symbol indicating that material is to be either removed or not removed in order to obtain a required surface texture, figures 2 and 3.3.3 CompletesymbolBasic or expanded symbol expanded in order to facilitate the indication of additional surface texture requirements, figure 4.3.4 Surface (texture) parameterParameter expressing micro-geometrical properties of a surface.3.5 (Surface) parameter symbolSymbol indicating the type of surface texture parameter.NOTE Parameter symbols comprise letters and numerical values, e.g.: Ra, Rz, Rmax, Rpk, etc.4 Specification of surface textureSurface specifications should only be made if they are required for the function of the surface.In general, the following shall apply:- as coarse as possible and no finer than necessary for the drawing entry,- as detailed as necessary for production (even more so if this does notcause additional expenditure)Surface specifications can be omitted if the normal production processes ensure that the end condition of the surface is appropriate.The parameter designation and the associated numerical values contain five pieces of information that are essential for the interpretation of the requirement:─Which of the three surface profiles (R, W or P) is indicated (see section 4.1).─Which characteristic of the profile is indicated.─How many sampling lengths make up the evaluation length (if this is significant, see sections 4.2, 6.1.2,9.10, 9.10.1 and 10.2).─How the indicated specification limits are set out (see section 4.3).─What cut off is used for measurement (see DIN EN ISO 4288).The indication of a surface texture requirement must therefore contain both the designation of the parameters and the numerical value of the specified limit.parameters4.1 ProfileProfile parameters are standardized for the three surface profiles (R, W and P profiles).Profile parameters are defined using the Gaussian filter according to DIN EN ISO 11562.Page 6VW 137 05: 2003-014.1.1 Parameters based on the material ratio curve (ISO 13565-2)Table 1 lists designations of parameters that relate to the linear material ratio curve. The parameters are only defined for the R profile. The definition of parameters is based on a filter process according to DIN EN ISO 13565-1.Table 1 – Designation of parameters based on the material ratio curve according to ISO 13565-2Parameters Roughness profile parameters acc. to DIN EN ISO 13565-2Filtering acc. to DIN EN ISO 13565-1Rk Rpk Rvk Mr1 Mr24.2 Evaluation length lnThe surface texture requirements apply to the evaluation length.If no indications are given for the evaluation length in the technical product documentation, e.g. in the drawing, then the normal evaluation length applies to the R profile. This is made up of 5 sampling lengths. The length of a sampling length corresponds to the wave length limit λc.For small surfaces, it must be noted that the scan length comprises the normal evaluation length, the run-in length and the run-out length. As the lengths of the run in and run out measure λc/2 and λc respectively (depending on the measuring device), the surfaces to be tested must be at least 6 x λc and 7 x λc respectively.If the surface to be measured is smaller than this, the number of evaluation lengths must be indicated (see also sections 6.1.2 and 9.10). The length of the sampling length is stipulated in DIN EN ISO 4288:1998 in tables 1 through 3.For the P profile, the normal evaluation length according to DIN EN ISO 4288 is the same length as the geometrical element to be measured. In the event that this cannot be realized e.g. due to equipment-related reasons, the evaluation length must be indicated appropriately.4.3 Tolerance limits for numerical values of surface parametersIn the automotive industry, the following applies: If a value is specified for surface roughness, it represents the highest permissible value for the parameter, see also VW 101 24 (VDA 2006). If a lower limit is specified, then this must be achieved.NOTE The 16% rule is not applied.5 Graphical symbols for the indication of surface textureAll the symbols indicated in DIN EN ISO 1302 are permitted. The symbol “for all surfaces around a workpiece outline” shall be avoided.5.1 Basic symbol for surface textureThe basic symbol shall consist of two straight lines of unequal lengths inclined at approximately 60° to the line representing the surface in question, as shown in figure 1. If the basic symbol according to figure 1 is used alone (without additional information), this is not deemed to be a requirement.Figure 1 – Basic symbol for surface textureIf the basic symbol is used with additional information (see section 6), then no decision has yet been made as to whether removal of material is necessary in obtaining the specified surface (see section 5.2) or whether removal of material is prohibited (see section 5.3).Page 7VW 137 05: 2003-015.2 Symbol for material removalIf removal of material, e.g. by machining, is required to obtain the prescribed surface, a cross bar, as shown in figure 2, shall be added to the basic symbol. The expanded basic symbol according to figure 2 alone (without additional information) is still not a requirement.Figure 2 – Expanded symbol for material removal5.3Symbol, if material removal is prohibitedIf removal of material is not permitted to obtain the specified surface, a circle shall be added to the basic symbol, as shown in figure 3.Figure 3 – Expanded symbol, if removal of material is prohibited5.4 Complete symbolWhen additional requirements with respect to the nature of the surface have to be indicated (see section 6), a line as shown in figure 4 shall be added to the longer of the two lines in the graphical symbols illustrated in figures 1 through 3.a) Any production process allowed b) Material removal is required c) Material removal is prohibitedFigure 4 – Complete symbolFor textual indications, e.g. in reports or contracts, the following abbreviations shall be used, whereby said abbreviations have the following meanings: Figure 4, symbol a APA (any process allowed) Figure 4, symbol b MRR (material removal required) Figure 4, symbol cNMR (non material removal)ab cPage 8VW 137 05: 2003-016 Specification of requirementsThe following surface parameters are used in the automotive industry to describe surface texture:For homogenous surfaces─(average) roughness Rz─(arithmetic) average roughness Ra (see note)─maximum roughness Rmax─overall height of waviness profile Wt─overall height of the profiles of the dominant waviness WDt─average height of the profiles of the dominant waviness WDc─overall height of the primary profile PtNOTE The arithmetic average roughness Ra is the arithmetic average of the absolute amounts from the individual roughness values within the evaluation length after the waviness has been filtered out. One disadvantage here is that individual freak values are not taken into consideration and the level of information provided is thus very low. Nonetheless, the arithmetic average roughness has its legitimacy e.g. for providing surface specifications for semifinished products.For porous and stratified heavy-duty contact surfaces─reduced peak height Rpk─core peak-to-valley roughness Rk─reduced score depth RvkFor special applications, it may be necessary to specify other requirements in addition to a surface parameter and its numerical value, such as e.g. Mr1 and Mr2, sampling length, production process, surface lay and orientation, machining allowance or other roughness parameters. See Annexes A and B for further details. NOTE The motif parameters according to DIN EN ISO 12085 and the description of the height of the surface from two vertical random components using the material probability curve according to DIN EN ISO 13565-3 are not used because there has been no experience with them.6.1 Position of the surface texture specifications on the complete symbolThe positions of the different surface texture requirements on the symbol are shown in figure 5.a = Surface parameter and numerical value (numerical value in µm)c = Production processb = Second surface texture requirement(surface parameter, numerical value in µm)d = Indication of the surface laye = Machining allowance (numerical value in mm)e d bFigure 5 – Positions (a to e) indicating additional requirements(designation areas on the complete symbol).If a third or further requirements are to be indicated under position b, the symbol must be enlarged accordingly in the vertical direction to create space for more lines. Positions a and b move upwards when the symbol is enlarged.Page 9VW 137 05: 2003-016.1.1 Surface texture symbols (surface parameters, positions a and b)If a value is indicated for the surface roughness and this is not marked with an L, it always represents the highest permissible roughness value for the surface and may not be exceeded.If there is only one surface texture requirement, then the surface parameter (e.g. Rz) and the numerical value (e.g. 10) shall be arranged at position “a” in the complete symbol, see figure 6.aFigure 6If a minimum dimension is required, the surface parameter, numerical value and the letter L (lower) shall be arranged at the position “a” in the complete symbol, see figure 7. The minimum dimension must be achieved.L aFigure 7If two surface texture requirements are required, i.e. if an upper and lower limit are to be specified, the maximum dimension shall be arranged at position “a” and the minimum dimension at position “b” in the complete symbol, see figure 8.NOTE U (for upper) and L (for lower) shall only be positioned before the surface parameter if there is a risk of confusion.abFigure 8A blank space shall be left between the indicated parameter and the limit value.6.1.2 Number of sampling lengthsIf it is necessary to indicate the number of sampling lengths (in the R profile) or the length of an evaluation length (in the P and W profiles), this shall be entered in position f as shown in figure 9, separated by an oblique stroke (see also section 9.10). In the R profile, the λc filter shall always be indicated with the number of sampling lengths.f / a λc x f / aP or W profile R profilef = length of the evaluation length (P or W profile)Number of sampling lengths (R profile)Figure 9NOTE The wave length limit for the long wave filter λc is also designated as a sampling lengthPage 10VW 137 05: 2003-017 Drawing 7.1Type and size of symbolsThe size and line width of symbols is dependent on the lettering size used in the drawing to note dimensions, see figures 10 and 11. It is not possible to change the symbols, e.g. mirror-image presentation.Figure 10Figure 11The lettering in field c, figure 11, can contain upper and/or lower case letters; the height of the field can be larger than h, in order to accommodate a range of additional specifications.The dimensions of the symbols and additional specifications shall comply with table 2.Table 2Dimensions in millimetersh Size of figures and letters, see DIN EN ISO 3098-2 2.5 3.5 5 7 10 14 20 d 1 1)Line width for symbols and letters 0.25 0.35 0.5 0.7 1 1.4 2 H 1 3.5 5 7 10 14 20 28 H 28 11 15 21 30 42 601) In CAD systems the line widths closest to these values shall applydepending on the length of the specificationsurfaceson7.2 SymbolsSymbols and lettering (same size as dimension figures) are to be arranged in a manner so they can be read from the bottom or from the right hand side of the drawing, with the drawing placed in the normal reading position. The symbol points from the outside either directly to the part edge, to an extension line used as a lengthening of the part edge or if needed, to a datum line, the arrow of which is to point from the outside to the edge of the part or extension line, see figure 12.The symbols of figures 1 to 3 can be arranged as desired; however, the lettering is to be entered according to the above-mentioned rule.Figure 12In general, surface requirements shall be entered individually on all surfaces where they are required. This also applies to opposing surfaces with the same surface texture.In accordance with the basic principles of dimensioning, the symbol is to be entered only once for a given surface, preferably in the view that also includes the dimensions of the surface. For rotating parts the surface specifications are to be entered only once for each plane of a symmetrical representation, see figure 13.Figure 137.3 Collective specifications in the field provided in the drawing frameBy way of example, letters are assigned to the symbol for the individual surface textures in figures 14 to 16.If the same specification applies to all the surfaces of a part, then only a collective specification shall be entered in the field “Surface finish” (if present) or near the title block, see figure 14.Figure 14If the same specification applies to most of the surfaces of a part, the collective specification shall likewise be entered in the “Surface finish” field (if present) or near the title block, together with an additional parenthesized basic symbol as shown in figure 1, without further information.NOTE When using collective specifications, it can arise that small surfaces are overlooked and cannot be measured as a result of the necessary evaluation length (for the R profile). In this case, Pt can be measured or the surface texture can be compared visually, e.g. with surface comparison samples.Symbols with surface specifications that indicate exceptions to the majority of the surface texture shall be specified at the respective surfaces in the drawing, see figure 15.If the deviating surface specifications on the drawing are uncomplicated and of limited scope, the complete surface texture may be parenthesized (see figure 16) instead of the basic symbol according to figure 15. NOTE The letters and numbers are provided by way of example.Figure 15Figure 167.4Depth of waviness Wt requirementsIf the Wt value is specified below the roughness parameter Rz, both measuring values are validindependently, see figure 17.NOTE The waviness shall only be specified when the function demands it.Meaning: Rz ≤ 25 µm Wt ≤ 10 µmFigure 17Rz 25 Wt 107.5Dominant waviness surface requirementsThere are 3 criteria for specifying the dominant waviness─dominant projections are not permitted ─ dominant projections are permitted to an upper limit value ─ dominant projections are not permitted or are conditionally permitted within a maximum/minimum orbilaterally limited period length rangeThe specification in the drawing is entered as follows:orif a dominant waviness is not permittedif the upper limit value for the average height of the profile elements and the total height of the profile cannot exceed 1.6 µm and 2.5 µm respectively.The indications in the drawing for a limited period wave range and indications as to the evaluation length are described in section 9.10.1.8 Preferred valuesIt is economically sensible to stipulate preferred values for surface parameters, whereby no more than one place after the decimal point should be allowed.For Rz, values from the following series shall be selected:0.4 0.6 1 1.6 2.5 4 6.3 10 16 25 40 63 100 160WDc 0WDt 0WDc 1.6 WDt 2.59Examples of entryThe following figures and the corresponding requirements are examples of surface texture specifications in technical product documentation (TPD), e.g. drawings. 9.1 Tooth flanksIn order to indicate the surface texture of tooth flanks that are not shown in the drawing, the surface specification shall be located on the reference circle, either in the section or in the view, see figure 18.Figure 189.2Repeated form elementsThe surface texture of repeated form elements shall only be specified once, together with the dimension entry, as long as confusion with similar form elements is not possible, see figure 19.Figure 19or9.3 SymmetricalpartsThe surface texture of clear and obviously symmetrical parts with a symmetry axis shall only be entered once, see figures 20 and 21.Figure 20 Figure 219.4 Different specifications on one surfaceIn the event of different surface textures on one surface, the area of the deviating requirement is designated and dimensioned with a wide dash-dot line, see figure 22.Figure 22surfaces9.5 ContactIn the case of contact surfaces of parts drawn in the assembled condition with identical surface textures, the requirements are entered according to figure 23.Figure 239.6 Radii,chamfersThe surface texture for concave radii (fillets), convex radii and chamfers shall be indicated on the dimension line of the radius or on a special line which points to every form element, see figure 24.Figure 24If the surface texture of all radii is the same, a general note with the corresponding symbol is entered in the “Surface finish” field (if present) or near the title block, see figure 25. As a result, the individual specification on the drawing is omitted.NOTE When specifying the surface texture for radii and chamfers, it is important to note that it is often impossible to perform an actual measurement because the available evaluation lengths are too short. In this case, a visual inspection, e.g. using surface comparison samples, may be performed, see also section 9.7.Figure 259.7Radii and chamfers without specific surface requirementsIf both the surfaces adjacent to the radii or chamfers can be measured using the relevant measuring equipment, the following rule shall apply:Concave radii (fillets) for which no surface textures are expressly specified shall have the texture of the smoother adjacent surface requirement, see table 3.Table 3Convex radii and chamfers for which no surface textures are expressly specified shall have the finish of the rougher adjacent surface requirement, see table 4.Table 4If only the longer of the adjacent surfaces can be measured using the relevant measuring equipment, the same surface specification shall apply to the adjacent radius or chamfer. Figure 26Figure 27Rz 16 Rz 25Rz 25 Rz 25Rz 25Rz 2.5Rz 6.3Rz 6.39.9Production process, surface characterIf a specific production process or surface character is required for individual surfaces, this shall be noted in unabbreviated format on the extension line of the symbol. The terms refer to the final surface condition. Caution! The final surface condition is called, e.g. according to DIN 6790-1, “lapped” not “lap”, see figures 28 to 34.If a surface with a specific surface texture must be post-treated, the area shall be identified with a wide dash-dot line on which the process shall be entered, see figure 35.Figure 28Figure 29Figure 30Figure 31Figure 32 Figure 33 Figure 34 Figure 359.10Length of the evaluation lengthFor the P profile, the normal evaluation length according to DIN EN ISO 4288 is the same length as the geometrical element to be measured. In the event that this cannot be realized, e.g. due to equipment-related reasons, the evaluation length must be specified. In figure 36, the evaluation length is specified as 4 mm. For the R profile, the normal evaluation length comprises 5 sampling lengths (5 x λc), see also section 4.2. If the surface to be tested is too small, the number of sampling lengths can be reduced and specified, see figure 37.Figure 36Figure 37honedfree from。
公差符号中英文对照

Straightness直线度- a condition where an element of a surface or an axis is a straight line.Flatness平面度- is the condition of a surface having all elements in one plane.Roundness圆度- describes the condition on a surface of revolution (cylinder, cone, sphere) where all points of the surface intersected by any plane.Cylindricity圆柱度- describes a condition of a surface of revolution in which all points of a surface are equidistant from a common axis.Profile of a Line线轮廓度- is the condition permitting a uniform amount of profile variation, etherunilaterally or bilaterally, along a line element of a feature.Profile of a Surface面轮廓度- is the condition permitting a uniform amount of profile variation, etherunilaterally or bilaterally, on a surface.All Around Symbol全周符号- indicating that a tolerance applies to surfaces all around the part. Angularity倾斜度- is the condition of a surface, axis, or centerplane, which is at a specified angle from adatum plane or axis.Perpendicularity垂直度- is the condition of a surface, axis, or line, which is 90 deg. From a datum plane or a datum axis.Parallelism平行度- is the condition of a surface, line, or axis, which is equidistant at all points from adatum plane or axis.Position Tolerance位置度- defines a zone within which the axis or center plane of a feature is permittedto vary from true (theoretically exact) position.Concentricity同轴度- describes a condition in which two or more features , in any combination, have acommon axis.Symmetry对称度- is a condition in which a feature (or features) is symmetrically disposed about thecenter plane of a datum feature.Runout圆跳动- is the composite deviation from the desired form of a part surface of revolution throughon full rotation (360 deg) of the part on a datum axis.Total Runout全跳动- is the simultaneous composite control of all elements of a surface at all circular andprofile measuring positions as the part is rotated through 360.Maximum Material Condition (MMC) 最大实体要求- is that condition of a part feature wherein itcontains the maximum amount ofmaterial within the stated limits of size. That is: minimum hole size and maximum shaft size.Least Material Condition (LMC)最小实体要求- implies that condition of a part feature of size wherein itcontains the least (minimum) amount of material, examples, largest hole size and smallest shaft size. It is opposite to maximum material condition.Regardless Of Feature Size (RFS) - the condition where the tolerance of form, runout or location must be met irrespective of where the feature lies within its size tolerance.Projected Tolerance Zone延伸公差带- applies to a hole in which a pin, stud, screw, etc., is to be inserted. It controls the perpendicularity of the hole to the extent of the projection from the hole and as itrelates to the mating part clearance. The projected tolerance zone extends above the surface of the part to the functional length of the pin, stud, and screw relative to its assembly with the mating part.Tangent Plane相切面- indicating a tangent plane is shown. The symbol is placed in the feature controlframe following the stated tolerance.Free State Variations自由状态变形- is a term used to describe distortion of a part after removal of forcesapplied during manufacture.Diameter直径- indicates a circular feature when used on the field of a drawing or indicates that thetolerance is diametrical when used in a feature control frame.Basic Dimension基本尺寸- used to describe the exact size, profile, orientation or location of a feature. Abasic dimension is always associated with a feature control frame or datum target. (Theoretically exact dimension in ISO)Reference Dimension参考尺寸- a dimension usually without tolerance, used for information purposesonly. It does not govern production or inspection operations. (Auxiliary dimension in ISO)Datum Feature参考特征- is the actual component feature used to establish a datum.Dimension Origin尺寸源- Signifies that the dimension originates from the plane established by theshorter surface and dimensional limits apply to the other surface.Feature Control Frame公差控制框- is a rectangular box containingthe geometric characteristics symbol, andthe form, runout or location tolerance. If necessary, datum referencesand modifiers applicable to the feature or the datums are alsocontained in the box.Conical Taper - is used to indicate taper for conical tapers. This symbol is always shown with the vertical leg to the left.Slope坡度- is used to indicate slope for flat tapers. This symbol is always shown with the vertical leg tothe left.Counterbore/Spotface沉孔- is used to indicate a counterbore or a spotface. The symbol precedes thedimension of the counterbore or spotface, with no spaceCountersink埋头孔- is used to indicate a countersink. The symbol precedes the dimensions of thecountersink with no space.Depth/Deep深度- is used to indicate that a dimension applies to the depth of a feature. This symbolprecedes the depth value with no space in between.Square - is used to indicate that a single dimension applies to a square shape. The symbol precedes thedimension with no space between.Number of Places位置数量- the X is used along with a value to indicate the number of times a dimension or feature is repeated on the drawing.Arc Length弧长- indicating that a dimension is an arc length measured on a curved outline. The symbolis placed above the dimension.Radius半径- creates a zone defined by two arcs (the minimum and maximum radii). The part surfacemust lie within this zone.Spherical Radius球半径- precedes the value of a dimension or tolerance.Spherical Diameter球直径- shall precede the tolerance value where the specified tolerance value represents spherical zone. Also, a positional tolerance may be used to control the location of a sphericalfeature relative to other features of a part. The symbol for spherical diameter precedes the size dimension of the feature and the positional tolerance value, to indicate a spherical tolerance zone.Controlled Radius可控半径- creates a tolerance zone defined by two arcs (the minimum and maximum radii) that are tangent to the adjacent surfaces. Where a controlled radius is specified, the part contourwithin the crescent-shaped tolerance zone must be a fair curve without flats or reversals. Additionally, radii taken at all points on the part contour shall neither be smaller than the specified minimum limit nor larger than the maximum limit.Between - to indicate that a profile tolerance applies to several contiguous features, letters may designatewhere the profile tolerance begins and ends. These letters are referenced using the between symbol (since 1994) or the word between on drawings made to earlier versions of the Standard.Statistical Tolerance统计公差- i s the assigning of tolerances to related components of an assembly on the basis of sound statistics (such as the assembly tolerance is equal to the square root of the sum of the squares of the individual tolerances). By applying statistical tolerancing, tolerances of individualcomponents may be increased or clearances between mating parts may be reduced. The increased tolerance or improved fit may reduce manufacturing cost or improve the product's performance, but shall only be employed where the appropriate statistical process control will be used. Therefore, consideration should be given to specifying the required Cp and /or Cpk or other process performance indices.Datum Target目标参考特征- is a specified point, line, or area on a part that isused to establish the Datum Reference Plane for manufacturing and inspectionoperations.Target Point - indicates where the datum target point is dimensionally located on the direct view of the surface.。
- 1、下载文档前请自行甄别文档内容的完整性,平台不提供额外的编辑、内容补充、找答案等附加服务。
- 2、"仅部分预览"的文档,不可在线预览部分如存在完整性等问题,可反馈申请退款(可完整预览的文档不适用该条件!)。
- 3、如文档侵犯您的权益,请联系客服反馈,我们会尽快为您处理(人工客服工作时间:9:00-18:30)。
Genus 5
Oh
The most pleasing smooth surfaces… Constrained only by topology, symmetry, size.
Comparison: MES MVS
(genus 4 surfaces)
Comparison MES MVS
For Closed Manifold Surfaces
Use thin-plate (Bernoulli) “Elastica”
Minimize bending energy:
k2 ds
Splines;
k12 + k22 dA
Minimum Energy Surfaces.
Closely related to minimal area functional:
Some are defined almost entirely by their functions
Ships hulls Airplane wings
Others have a mix of function and aesthetic concerns
Car bodies e cases, aesthetic concerns dominate
Abstract mathematical sculpture
Geometrical models
TODAY’S FOCUS
“Beauty” ? Fairness” ?
What is a “ beautiful” or “fair” geometrical surface or line ?
Other Optimization Functionals
Penalize Minimize
change in curvature !
Curvature Variation: (no natural model ?) Minimum Variation Curves (MVC): (dk /ds)2 ds Circles.
Start with a crude polyhedral object
Subdivide triangles Optimize vertices
Repeat the process
Limitations of “Minimal Surfaces”
“Minimal
Surface” - functional works well for large-area, open-edge surfaces.
Minimum Variation Surfaces (MVS): (dk1/de1)2 + (dk2/de2)2 dA Cyclides: Spheres, Cones, Various Tori …
Minimum-Variation Surfaces (MVS)
Genus 3
D4h
Inspiration from Nature
Soap films in wire frames:
Minimal
area
Balanced
k 1 = – k 2; mean curvature = 0
curvature:
Natural beauty functional:
Minimum
Length / Area: rubber bands, soap films polygons, minimal surfaces ds = min dA = min
(k1+ k2)2 = k12 + k22 + 2k1k2
4H2 = Bending Energy + 2G
Integral over Gauss curvature is constant: 2k1k2 dA = 4p * (1-genus)
Minimizing “Area” minimizes “Bending Energy”
“Volution” Surfaces (Séquin, 2003)
“Volution 0”
---
“Volution 5”
Minimal surfaces of different genus.
Brakke’s Surface Evolver
For creating constrained optimized shapes
Things get worse for MES as we go to higher genus:
Smoothness
geometric continuity, at least G2, better yet G3. unnecessary undulations. in constraints are maintained. … Examples ?
No
Symmetry
Inspiration,
Minimum Energy Surfaces (MES)
Lawson
surfaces of absolute minimal energy:
12 little legs
Genus 3
Genus 5
Genus 11
Shapes get worse for MES as we go to higher genus …
CS 284
Minimum Variation Surfaces
Carlo H. Séquin
EECS Computer Science Division
University of California, Berkeley
Smooth Surfaces and CAD
Smooth surfaces play an important role in engineering.
But
what should we do for closed manifolds ?
Spheres,
tori, higher genus manifolds … cannot be modeled by minimal surfaces.
We need another functional !