冲压模具常用公式及数据表
冲压件模具设计常用公式

冲压件模具设计常用公式1. 材料和工艺参数计算公式1.1 冲击力的计算公式冲击力是冲压件模具设计中重要的参考指标之一,它可以用于确定模具的强度和稳定性。
冲击力的计算公式如下:F = K × A × T × σ其中,F表示冲击力,K表示冲击系数,A表示冲压件的有效面积,T表示冲压时间,σ表示材料的抗拉强度。
1.2 冲床力的计算公式冲床力是指冲床在冲压过程中对工件所产生的压力。
冲床力的计算公式如下:P = F / A其中,P表示冲床力,F表示冲击力,A表示冲压件的有效面积。
1.3 冲压时间的计算公式冲压时间是指冲床一次冲压周期所需的时间。
冲压时间的计算公式如下:T = (L / V) + t其中,T表示冲压时间,L表示冲压件的长度,V表示冲床的下行速度,t表示冲程停留时间。
1.4 最大冲床力的计算公式最大冲床力是指冲床所能承受的最大压力。
最大冲床力的计算公式如下:P_max = K × A × σ其中,P_max表示最大冲床力,K表示冲击系数,A表示冲压件的有效面积,σ表示材料的抗拉强度。
2. 模具结构设计公式2.1 模具剪切强度的计算公式模具剪切强度是指模具在剪切过程中所能承受的最大剪切力。
模具剪切强度的计算公式如下:P_shear = F / A_shear其中,P_shear表示模具剪切强度,F表示冲击力,A_shear表示模具剪切面积。
2.2 模具挤压强度的计算公式模具挤压强度是指模具在挤压过程中所能承受的最大挤压力。
模具挤压强度的计算公式如下:P_extrusion = F / A_extrusion其中,P_extrusion表示模具挤压强度,F表示冲击力,A_extrusion表示模具挤压面积。
2.3 模具弯曲强度的计算公式模具弯曲强度是指模具在弯曲过程中所能承受的最大弯曲力。
模具弯曲强度的计算公式如下:P_bending = F / A_bending其中,P_bending表示模具弯曲强度,F表示冲击力,A_bending表示模具弯曲面积。
冲压件模具设计常用公式

冲压件模具设计常用公式1. 冲裁力计算公式冲裁力是模具在冲裁过程中对工件施加的力的大小,可以使用以下公式进行计算:$$ P = K \\cdot T \\cdot L \\cdot S $$其中: - P 是冲裁力〔单位:N〕 - K 是系数〔根据材料和冲裁方式进行选择〕 - T 是材料的厚度〔单位:mm〕 - L 是冲裁长度〔单位:mm〕 - S 是材料强度的保险系数2. 冲孔力计算公式冲孔是冲压件模具中常见的一个工序,为了计算冲孔力,可以使用以下公式:$$ F = K \\cdot T \\cdot L \\cdot S $$其中: - F 是冲孔力〔单位:N〕 - K 是系数〔根据材料和冲孔方式进行选择〕 - T 是材料的厚度〔单位:mm〕 - L 是冲孔孔径〔单位:mm〕 - S 是材料强度的保险系数3. 模具开孔面积计算公式在冲压件模具设计中,开孔面积对模具的设计和选择起着重要的作用。
开孔面积可以通过以下公式计算:$$ A = L \\cdot W $$其中: - A 是开孔面积〔单位:mm²〕 - L 是模具的长度〔单位:mm〕 - W 是模具的宽度〔单位:mm〕4. 模具强度计算公式模具强度的计算是冲压件模具设计中的关键步骤之一。
可以使用以下公式计算模具的强度:$$ P_t = P \\cdot S_f $$其中: - P_t 是模具的强度〔单位:N〕 - P 是冲裁力或冲孔力〔单位:N〕 - S_f 是平安系数5. 模具寿命计算公式模具寿命的计算是冲压件模具设计过程中需要关注的一个重要指标。
可以使用以下公式计算模具寿命:$$ N_m = \\frac{S_m}{f \\cdot V_c} $$其中: - N_m 是模具的使用寿命〔单位:次〕 - S_m 是模具材料的疲劳强度〔单位:MPa〕 - f 是载荷系数 - V_c 是模具的速度〔单位:m/s〕6. 模具热应力计算公式模具在使用过程中会受到热应力的影响,为了进行热应力的计算,可以使用以下公式:$$ \\sigma = \\frac{Q}{A} $$其中: - σ 是热应力〔单位:MPa〕 - Q 是热量〔单位:J〕 - A 是模具横截面积〔单位:mm²〕7. 模具变形计算公式模具在使用过程中会发生一定的变形,为了进行变形的计算,可以使用以下公式:$$ \\delta = \\frac{{F \\cdot L}}{{E \\cdot A}} $$其中: - δ 是变形量〔单位:mm〕- F 是施加在模具上的力〔单位:N〕 - L 是模具的长度〔单位:mm〕 - E 是弹性模量〔单位:MPa〕 - A 是模具的截面积〔单位:mm²〕总结在冲压件模具设计过程中,常用的公式可以帮助工程师快速准确地进行相关计算,从而确保模具的性能和可靠性。
模具尺寸估算公式(免费)

550~650 600~700 650~750 700~800
300~500
带斜楔的模具
在依照上表估算的模具尺寸基础上,再在需要斜楔的方向+(100~300)
坯料长度<100
坯料长度+500
坯料长度+(300~450) 坯料长度+(200~350) 坯料长度+(150~250)
坯料长度+150
坯料长度+(200~350)
坯料宽度+400
坯料宽度+350 坯料宽度+(200~300) 坯料长度+(150~200)
坯料长度+100
坯料宽度+(200~300)
模具高度
1250
产ቤተ መጻሕፍቲ ባይዱ高度
<50
650
50~100
700
100~150
750
150~200
800
450~650
350~550
300~400
250~350
按所需压床的闭合高度确定
300~400
250~350
产品高度 <50
50~100 100~150 150~200
200~300 1250
400~650 300~450 250~350 150~250
坯料宽度+200
200
坯料宽度+250
产品宽度方向
有翻边
坯料宽度+250
无翻边
坯料宽度+200
有翻边
坯料宽度+200
无翻边
坯料宽度+150
坯料长度+150
坯料宽度+(550~650)
冲压件模具设计的常用公式

冲压件模具设计的常用公式
一、材料力学公式
1.应力公式:σ=F/A,其中σ为应力,F为受力,A为受力面积。
2.应力应变关系公式:σ=E×ε,其中E为杨氏模量,ε为应变。
3.屈服强度公式:σs=F/A0,其中σs为屈服强度,F为屈服点所受力,A0为初始横截面积。
二、材料成形公式
1. 塑性变形公式:ε = ln (h0 / hn) ,其中ε为塑性变形,h0为初始厚度,hn为最终厚度。
2.变形力公式:F=S×σs,其中F为变形力,S为变形面积,σs为屈服强度。
3.针对特定形状的材料成形公式,如直冲材料成形公式、弯曲材料成形公式等。
三、模具设计公式
1.强度计算公式:F=σ×A,其中F为受力,σ为应力,A为受力面积。
2. 弯曲应力公式:σ = M / (W × yc),其中σ为弯曲应力,M为弯矩,W为截面模量,yc为弯曲轴心距离。
四、装配公式
1.装配公差公式:A=A1+A2+A3,其中A为总公差,A1为尺寸公差,
A2为形位公差,A3为相对公差。
五、切削力公式
1. 切削功率公式:P = F × V × kc,其中P为切削功率,F为切
削力,V为切削速度,kc为切削功率系数。
以上是冲压件模具设计中的常用公式,通过这些公式的运用,可以对
冲压件进行力学、成形、模具设计、装配以及切削力等方面的优化和设计。
当然,具体的设计中还需要根据实际情况和不同材料的特性来选择合适的
公式。
冲压模具常用公式及数据表

冲压模具常⽤公式及数据表常⽤公式及数据表冲压件模具设计常⽤公式⼀.冲裁间隙分类见表4-1表4-1 冲裁间隙分类(JB/Z 271-86)⼆.冲裁间隙选择(提供参考) 见表4-2(⾒下⾴)表4-2 冲裁间隙⽐值(單邊间隙) (單位:%t)(注: 1. 本表適⽤于厚度為10mm以下的⾦屬材料, 厚料间隙⽐值應取⼤些;2. 凸,凹模的制造偏差和磨損均使间隙變⼤, 故新模具應取最⼩间隙;3. 硬質合⾦冲模间隙⽐鋼模⼤20% 左右.)注: 冲裁间隙选择應綜合考慮下列因素:1.冲床﹑模具的精度及剛性.2.產品的斷⾯品質﹑尺⼨精度及平整度.3.模具壽命.4.跳屑.5.被加⼯材料的材質﹑硬度﹑供應狀態及厚度.6.廢料形狀.7.冲⼦﹑模仁材質﹑硬度及表⾯加⼯質量.三.冲裁⼒﹑卸(剝)料⼒﹑推件⼒﹑頂件⼒F冲= 1.3 * L * t *τ(N) (公式4-1)F卸= K卸* F冲(N) (公式4-2)F推= N * K推* K冲(N) (公式4-3)F頂= K頂* F冲(N) (公式4-4)其中:L ――冲切線⾧度(mm)t ――材料厚度(mm)τ――材料抗剪強度(N/mm2 )1.3 ――安全系數K卸――卸(剝)料⼒系數K推――推料⼒系數K頂――頂料⼒系數K卸K推K頂數值见表4-3表4-3 卸料⼒﹑推件⼒和頂件⼒系數注:卸料⼒系數K卸在冲多孔﹑⼤搭邊和輪廓復雜時取上限值.四.中性層彎曲半徑R = r + x * t (mm) (公式4-5) 其中:R――中性層彎曲半徑(mm)r ――零件內側半徑(mm)x ――中性層系數中性層系數见表4-4(提供参考)表4-4 中性層系數x值注: 彎曲件展開尺⼨與下列因素有關:1.彎曲成形⽅式.2.彎曲间隙.3.有無压料.4.材料硬度﹑延伸率﹑厚度.5.根据實際狀況精確修正.五.材料最⼩彎曲半徑,见表4-5表4-5 最⼩彎曲半徑。
计算公式

06-B151理论计算公式1、模具重量:G=LWHρKL:模具长度(mm) W:模具宽度(mm) H:模具高度(mm)ρ:密度g/mm3 K:减轻系数G=2900*1850*950*7.8*0.4=15.9T2、顶盖前后两侧翻边力计算公式如下:查资料《冲压手册》王孝培主编翻边力公式:F=1.25LTKσb材料:ST16(上海宝钢)σb=350Mpa T=0.7mmF:翻边力(N) L:翻边口线周长(mm) T:材料厚度(mm)σb:材料抗拉强度(Mpa) K:系数0.2~0.3测得总弧长:L=3000mm T=0.7mm σb=350MpaF=1.25LTKσb=1.25*3000*0.7*0.25*350=23T压料力F=0.25-0.3F 取0.28压F压=0.28X23=6.44T查《汽模标准》,选择QM7112中型50X150的弹簧。
单位压缩力为:144.3N/mm; 预计选用16根弹簧预压34mm,则产生的压缩力F2则,F2=144.3*34*16=7.9T>F卸=6.44T工作行程16mm,则总压缩量为50mm,产生压缩力F3。
则,F3=144.3*50*16=11.5T>F卸=6.44T由此可知,所选弹簧符合此工序翻边卸料力要求。
3、顶盖前后两侧侧修冲裁力计算公式如下:查资料《冲压手册》王孝培主编冲裁力公式:F=1.3VLT材料:ST16(上海宝钢) V=350Mpa T=0.7mmF:冲裁力(N) L:侧修口线周长(mm) T:材料厚度(mm) V:材料抗剪强度(Mpa)测得侧修口线弧长:L=300mm T=0.7mm σb=350MpaF=1.3VLT=1.3*300*0.7*350=9.6T压料力F=0.04F压F压=0.04X9.6=0.384T查《汽模标准》,选择QM7112中型50X150的弹簧。
单位压缩力为:144.3N/mm; 预计选用1根弹簧工作行程50mm,则总压缩量为50mm,产生压缩力F4。
五金冲压模具冲裁间隙与公差
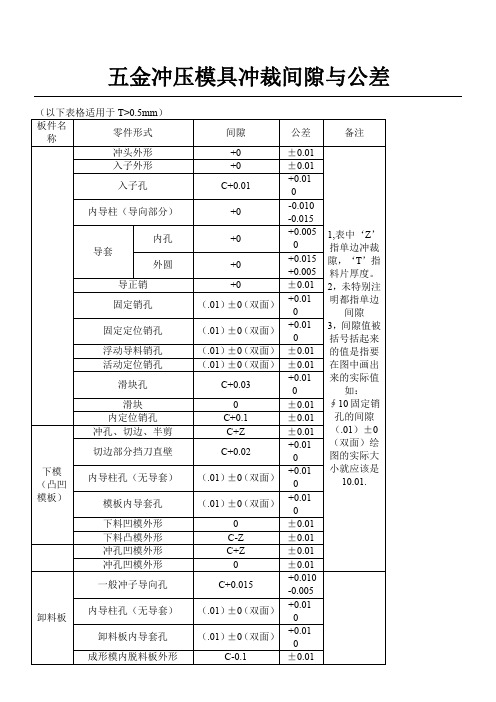
+0
±0.01
入子孔
C+0.01
+0.01
0
内导柱(导向部分)
+0
-0.010
-0.015
导套
内孔
+0
+0.005
0
外圆
+0
+0.015
+0.005
导正销
+0
±0.01
固定销孔
(.01)±0(双面)
+0.01
0
固定定位销孔
(.01)±0(双面)
+0.01
0
浮动导料销孔
(.01)±0(双面)
±0.01
固定板
冲子固定孔
C+0.02
±0.01
导正销固定孔
C+0.01
+0.01
0
内导柱固定孔(无)
(.01)±0(双面)
+0Leabharlann 010脱料板、脱料垫板
冲子及导柱销孔
+1
+0.1
0
内脱料板外形
+1
+0.1
0
下垫板
落料孔
+1
+0.1
0
下模座
落料孔
+1.5
±0.01
上表中Z值取值依下表所列:
G1,EG,SGCC, SECC、 CRS、SPCC材质
活动定位销孔
(.01)±0(双面)
±0.01
滑块孔
C+0.03
+0.01
0
滑块
0
±0.01
内定位销孔
C+0.1
冲压模具闭合高度计算公式

冲压模具闭合高度计算公式
冲压模具闭合高度是指模具在闭合时的压紧高度,是决定冲压产品质量和模具寿命的重要参数。
下面介绍冲压模具闭合高度的计算公式:
1. 常见的冲压模具闭合高度计算公式为:H=(T×S)÷(2×π×D)
其中,H为闭合高度,T为材料的屈服强度,S为材料的厚度,D 为模具的直径,π为圆周率。
2. 对于复杂形状的冲压模具,可以采用以下公式计算闭合高度: H=(T×S×L)÷(2×π×D×F)
其中,L为模具轮廓长度,F为模具轮廓周长。
需要说明的是,以上公式只是参考值,实际计算还需考虑具体的冲压材料、模具形状、模具结构等因素,以确保模具能够正常工作并保证冲压产品的质量。
- 1 -。
模具冲压机吨位计算公式
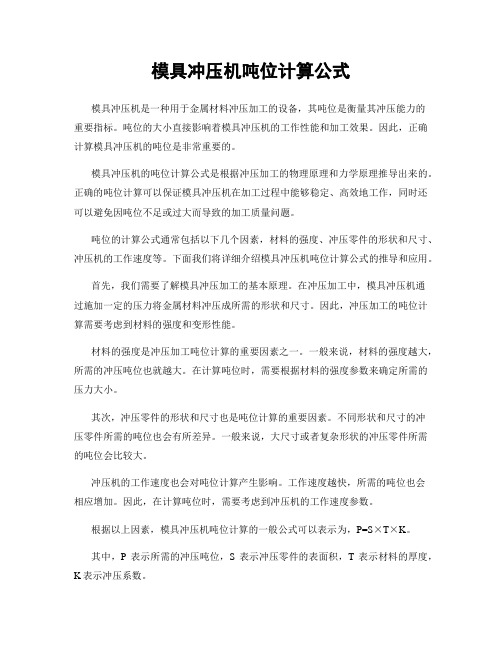
模具冲压机吨位计算公式模具冲压机是一种用于金属材料冲压加工的设备,其吨位是衡量其冲压能力的重要指标。
吨位的大小直接影响着模具冲压机的工作性能和加工效果。
因此,正确计算模具冲压机的吨位是非常重要的。
模具冲压机的吨位计算公式是根据冲压加工的物理原理和力学原理推导出来的。
正确的吨位计算可以保证模具冲压机在加工过程中能够稳定、高效地工作,同时还可以避免因吨位不足或过大而导致的加工质量问题。
吨位的计算公式通常包括以下几个因素,材料的强度、冲压零件的形状和尺寸、冲压机的工作速度等。
下面我们将详细介绍模具冲压机吨位计算公式的推导和应用。
首先,我们需要了解模具冲压加工的基本原理。
在冲压加工中,模具冲压机通过施加一定的压力将金属材料冲压成所需的形状和尺寸。
因此,冲压加工的吨位计算需要考虑到材料的强度和变形性能。
材料的强度是冲压加工吨位计算的重要因素之一。
一般来说,材料的强度越大,所需的冲压吨位也就越大。
在计算吨位时,需要根据材料的强度参数来确定所需的压力大小。
其次,冲压零件的形状和尺寸也是吨位计算的重要因素。
不同形状和尺寸的冲压零件所需的吨位也会有所差异。
一般来说,大尺寸或者复杂形状的冲压零件所需的吨位会比较大。
冲压机的工作速度也会对吨位计算产生影响。
工作速度越快,所需的吨位也会相应增加。
因此,在计算吨位时,需要考虑到冲压机的工作速度参数。
根据以上因素,模具冲压机吨位计算的一般公式可以表示为,P=S×T×K。
其中,P表示所需的冲压吨位,S表示冲压零件的表面积,T表示材料的厚度,K表示冲压系数。
冲压系数K是根据具体的冲压加工情况来确定的,一般需要根据实际情况来进行调整。
在实际应用中,可以通过试验和经验来确定冲压系数的数值。
在实际的吨位计算中,需要根据具体的冲压加工要求和材料参数来确定吨位的大小。
通过正确的吨位计算,可以保证模具冲压机在加工过程中能够稳定、高效地工作,同时还可以避免因吨位不足或过大而导致的加工质量问题。
2。2-冲压模具
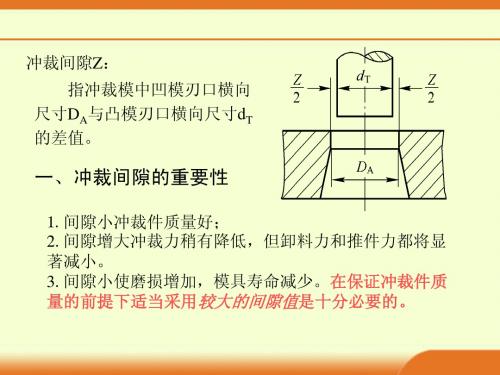
3、典型的冲裁模结构及特点:
1)、单工序冲裁模:指在压力机的一次工作行程中只 完成一个基本冲裁工序的模具。 ①固定导板式落料模: 是将凸模与导板用H7/h6的间隙配合,导板与导 料板、凹模、下模座联接在一起,既对凸模导向,又 起固定卸料作用。回程时凸模不能离开导板。
第二章 冲裁工艺与冲裁模设计
1-上模座 2-凸模 3-卸料板 4-导料板 5-凹模 6-下模座 7-定位板
第二章 冲裁工艺与冲裁模设计
第二章 冲裁工艺与冲裁模设计
落料凸、凹模尺寸 a) 落料凹模尺寸 b) 落料凸模尺寸
2.4.3冲裁力和压力中心的计算
一、冲裁力的计算
冲裁力:冲裁过程中凸模对板料施加的压力。
用普通平刃口模具冲裁时,冲裁力F一般按下式计算:
F=1.3L·t·τ(N)
注: F——冲裁力; L——冲裁件周长; t——材料厚度; τ——材料抗剪强度; b
无导向单工序落料模
1-模柄 2-上模座 3-导套 4-导柱 5下模座图2-57 滑动导向模架
第二章 冲裁工艺与冲裁模设计
1-模柄 2-止动销 3-上模座 4、8-内六角螺钉 5-凸模 6-垫板 7-凸模固定板 9-导板 10-导料板 11-承料板 12-螺钉 13-凹模 14-圆柱销 15-下模座 16-固定挡料销 17-止动销 18-限位销 19-弹簧 20-始用挡料销
DA Dmax x0
A (36 0.5 0.62)0 0.025 mm 35.690 0.025 mm
DT D A Z min t (35.69 0.04 ) 0 0.016 mm 35.65 0 0.016 mm
0
校核:0.016 + 0.025 = 0.04 > 0.02(不能满足间隙公差条件) 因此,只有缩小,提高制造精度,才能保证间隙在合理范围内, 由此可取: T ≤ 0.4Z max Z min =0.4×0.02=0.008mm A ≤ 0.6Z Z =0.6×0.02=0.012mm max min
冲压模具设计用公式表
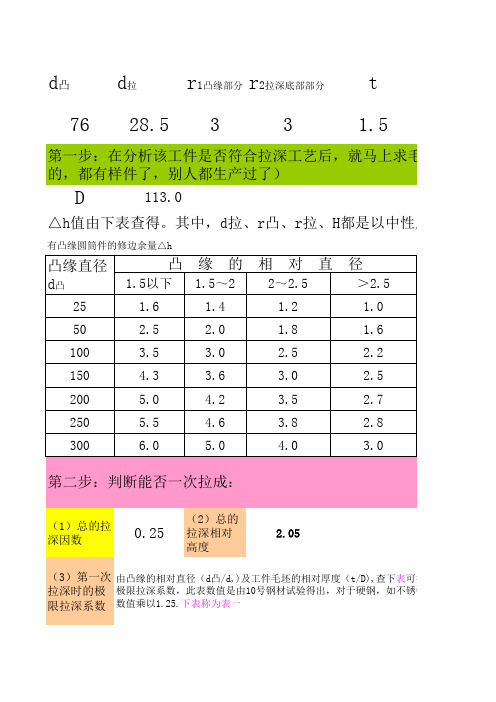
d凸d拉r1凸缘部分r2拉深底部部分t 7628.533 1.5第一步:在分析该工件是否符合拉深工艺后,就马上求毛坯的,都有样件了,别人都生产过了)D113.0△h值由下表查得。
其中,d拉、r凸、r拉、H都是以中性层计有凸缘圆筒件的修边余量△h<1.0~0.6<0.6~0.31.1以下0.510.530.550.571.30.490.510.530.541.50.470.490.500.511.80.450.460.470.482.00.420.430.440.452.20.400.410.420.422.50.370.380.380.382.80.340.350.350.353.00.320.330.330.33凸/d说明:1、表中数值适用于10号钢,对于比10号钢塑性更大的金属取接近于大的数值、对金属,取接近于小的数值;2、表中较大的数值适用于圆角半径较大的工件,较小值适用于圆角半径较小的工件毛坯相对厚度(t/D)*10012、第一次拉深时的凹模圆角半径初次决定r 凹7.1这个7.1是初次计算值,还要作如下处理:r1=7.1+t/2=7.85,圆整取8,填入右边栏82.0~1.0<1.0~0.3<03~0.1无凸缘(4-6)*t(6-8)*t(8-12)*t有凸缘(8-12)*t (12-15)*t (15-20)*t3、第一次拉深时的凸模圆角半径初次决定r 凸7.1这个7.1是初次计算值,还要作如下处理:r2=7.1+t/2=7.85,圆整取8,填入右边栏8最后确定r凸11.1第三步:试确定首次拉深因数右边的11.1可以灵活处理为:9.5-12之间的数,但不能比等,并把所确定的值填入右栏以上所确定的“再次确定r凸”是由经验公式计算得出的最小值,实际工作中,应该对前面由表均值那这样子说来,坯料直径就应该比当初所确定的113要大,大多少呢?见下面的D'初选第一次拉深完成后,凸缘相对直径(d凸/d1)=1.1,则由前面表一可知d1=m1*D=0.53*113=59.89(圆整到61,把此圆整数值填入右边一栏)为了首次拉深后的各次拉深过程中,不至于使前面加工出来的凸缘产生变形,必须在首拉入材料量的5%。
冲压件报价公式

冲压件报价公式摘要:一、冲压件报价概述1.报价前提条件2.报价涉及因素二、冲压件报价方法与计算公式1.材料费计算2.冲压模具费计算3.冲压费计算4.其他费用计算三、影响报价的因素1.时间2.地区3.材料4.产量四、报价案例分析与应用1.客供模具报价2.包工包料报价3.按需按量按时生产报价正文:一、冲压件报价概述冲压件报价涉及多个方面,主要包括材料费、冲压模具费、冲压费以及其他费用。
在进行报价时,需要考虑客户需求、生产条件、市场行情等多种因素。
以下为冲压件报价的基本流程和注意事项。
1.报价前提条件在进行冲压件报价前,首先要明确报价的前提条件,如客户是否提供模具、是否包工包料,以及生产方式等。
不同的前提条件会影响到报价的具体内容。
2.报价涉及因素冲压件报价涉及的因素较多,主要包括:材料费、副料及人工费、设备折旧费、工厂综合开支(如运费、包装、厂租等)、利润、资金结算期利息等。
二、冲压件报价方法与计算公式1.材料费计算材料费是冲压件报价的基础,需要根据零件展开尺寸和所选材料的单价来计算。
计算公式为:材料费= 材料单价× 材料用量。
2.冲压模具费计算冲压模具费根据零件形状和复杂程度来计算。
一般来说,模具费用与零件复杂度成正比。
计算公式为:冲压模具费= 模具单价× 模具数量。
3.冲压费计算冲压费根据零件的吨位和冲压次数来计算。
计算公式为:冲压费= 吨位费率× 冲压次数。
4.其他费用计算其他费用包括副料费、人工费、设备折旧费、工厂综合开支等。
这些费用需要根据实际情况和生产成本来估算。
三、影响报价的因素1.时间不同的时间节点,市场行情和成本会发生变化,从而影响报价。
在报价时,要考虑当前市场状况和趋势。
2.地区不同地区的生产成本、消费水平和市场需求不同,因此报价也会有所差异。
在报价时,要考虑地区因素对成本和价格的影响。
3.材料材料种类、规格和质量对报价有很大影响。
不同材料的采购成本和加工难度不同,直接关系到冲压件的价格。
五金冲压成型冲压力计算公式

五金冲压成型冲压力计算公式
五金冲压成型是指通过压力将金属材料冲压成所需形状的加工
方法。
在冲压过程中,需要计算冲压力来保证成型质量和加工效率。
以下是五金冲压成型冲压力计算公式:
1. 单位冲压力公式:P=K×T×L
其中,P表示单位冲压力,K表示材料的力学性能系数,T表示材料的厚度,L表示冲孔边缘距离。
2. 冲压力公式:F=P×A
其中,F表示冲压力,A表示冲孔面积。
以上公式是五金冲压成型中常用的计算冲压力的公式。
在实际应用中,还需要根据具体材料、模具和工艺进行调整和优化,以达到最佳加工效果。
- 1 -。
冲压模具 常用公式总结

一.冲裁间隙分类见表4-1表4-1 冲裁间隙分类(JB/Z 271-86)二.冲裁间隙选取(仅供参考) 见表4-2(见下页)表4-2 冲裁间隙比值(单边间隙) (单位:%t)(注: 1. 本表适用于厚度为10mm以下的金属材料, 厚料间隙比值应取大些;2. 凸,凹模的制造偏差和磨损均使间隙变大, 故新模具应取最小间隙;3. 硬质合金冲模间隙比钢模大20% 左右.)注: 冲裁间隙选取应综合考虑下列因素:1.冲床﹑模具的精度及刚性.2.产品的断面质量﹑尺寸精度及平整度.3.模具寿命.4.跳屑.5.被加工材料的材质﹑硬度﹑供应状态及厚度.6.废料形状.7.冲子﹑模仁材质﹑硬度及表面加工质量.三.冲裁力﹑卸(剥)料力﹑推件力﹑顶件力F冲= 1.3 * L * t *τ(N) (公式4-1)F卸= K卸* F冲(N) (公式4-2)F推= N * K推* K冲(N) (公式4-3)F顶= K顶* F冲(N) (公式4-4)其中:L ――冲切线长度(mm)t ――材料厚度(mm)τ――材料抗剪强度(N/mm2 )1.3 ――安全系数K卸――卸(剥)料力系数K推――推料力系数K顶――顶料力系数K卸K推K顶数值见表4-3表4-3 卸料力﹑推件力和顶件力系数注:卸料力系数K卸在冲多孔﹑大搭边和轮廓复杂时取上限值.四.中性层弯曲半径R = r + x * t (mm) (公式4-5) 其中:R――中性层弯曲半径(mm)r ――零件内侧半径(mm)x ――中性层系数中性层系数见表4-4(仅供参考)表4-4 中性层系数x值注: 弯曲件展开尺寸与下列因素有关:1.弯曲成形方式.2.弯曲间隙.3.有无压料.4.材料硬度﹑延伸率﹑厚度.5.根据实际状况精确修正.五.材料最小弯曲半径,见表4-5表4-5 最小弯曲半径注:表列数据用于弯曲中心角≧90∘﹑断面质量良好的情况. 六﹑弯曲回弹半径及回弹角r 凸 = r 0 / ( 1 + K r 0 / t ) (公式4-6)回弹角的数值为Δα = (180°-α0 )( r 0 / r 凸 - 1) (公式4-7)式中 r 凸 ―― 凸模的圆角半径, [r 凸 ]为mm; r 0 ―― 工件的圆角半径, [r 0 ]为mm; α0 ――工件的弯曲角度, [α0]为(°); t ―― 工件材料厚度, [t]为mm; K ―― 简化系数, 见表4-6表4-6 简化系数k 值七﹑ 弯曲力计算针对“v ”型弯曲:F 弯 = 0.6kbt σb / (R + t ) (N) (公式4-8)其中:b ――― 弯曲线长度 (mm) t ――― 材料厚度 (mm) r ――― 内侧半径 (mm) σb ―― 材料极限强度 (N/mm 2)k―――安全糸数,一般k=1.3八﹑拉深(抽引)系数m = d/D (公式4-9)其中:d ――拉深(抽引)后工件直径(mm)D――毛坯直径(mm)1. 无凸缘或有凸缘筒形件用压边圈拉深系数见表4-7表4-7 无凸缘或有凸缘筒形件用压边圈拉深的拉深系数(适用08,10号钢)注: 1) 随材料塑性高低,表中数值应酌情增减.2) ――在线方为直筒件(d凸=d1 ).3) 随d凸/D 数值增大, r/t 值可相应减小, 满足2r1≦h1, 保証筒部有直壁.4) 查用时, 可用插入法, 也可用偏大值.5)多次拉深首次形成凸缘时,为考虑多拉入材料,m1增大0.02.2. 带凸缘筒形件第一次拉深系见表4-8表4-8 带凸缘筒形件第一次拉深时的拉深系数m 1注:适用于08﹑10号钢 3.无凸缘筒形件用压边圈拉深系数见表4-9表4-9 无凸缘筒形件用压边圈时的拉深系数注: 1. 凹模圆角半径大时 (r 凹 = 8 ~ 15t ), 拉深系数取小值, 凹模圆角半径小时 (r 凹 = 4 ~ 8t ),拉深系数取大值.2. 表中拉深系数适用于08﹑10S ﹑15S 钢与软黄铜H62 ﹑ H68. 当拉深塑性更大的金属时(05﹑08Z 及10Z 钢﹑铝等), 应比表中数值减小1.5-2%. 而当拉深塑性较小的金属时(20﹑25﹑A2﹑A3﹑酸洗钢﹑硬铝﹑硬黄铜等), 应比表中数值增大1.5-2%(符号S 为深拉深钢, Z 为最深拉深钢).4. 无凸缘筒形件不用压边圈拉深系数见表4-10表4-10 无凸缘筒形件不用压边圈时的拉深系数注:适用于08﹑10以及15Mn等材料5. 有工艺切口的第一次拉深系数见表4-11表4-11有工艺切口的第一次拉深系数m1 (材料:08﹑10)6. 有工艺切口的以后各次拉深系数见表4-12表4-12有工艺切口的以后各次拉深系数m n(材料:08﹑10))7. 有工艺切口的各次拉深系数见表4-13表4-13有工艺切口的各次拉深系数九﹑拉深(抽引)力F抽=3(σb + σs )( D – d - r凹)t (N) (公式4-10)其中:σb――材料极限强度(N/mm2)σs――材料屈服强度(N/mm2)D―――毛坯直径(mm)d―――拉深凹模直径(mm)r凹――拉深凹模圆角(mm)t―――材料厚度(mm)十﹑孔的翻边1. 翻边系数K = d/D (公式4-11)d ――预冲孔直径(mm)D ――翻边后平均直径(mm)各种材料极限翻边系数见表4-14,表4-15表4-14 低碳钢的极限翻边系数K表4-15 其它一些材料的翻边系数2. 预冲孔直径d = D-2( h - 0.43r - 0.72t ) (公式4-12)h ――翻边高度(mm)r ――翻边圆角(mm)t ――材料厚度(mm)3. 翻边高度h = D/[( 1-k )/2] + 0.4r + 0.72t (公式4-13)4. 翻边口部材料厚度t1 = t√k (mm) (公式4-14)5.翻边力F = 1.1tπtσs( D-d )σs ――材料屈服强度(Mpa)十一设计连接器五金零件应注意的要点1.尺寸标注:1)尺寸标注在最显要位置,直观,不封闭;2)重要﹑关键尺寸直接标注,不能有累积公差;3)尺寸公差大小应综合考虑功能及制造成本,并非越小越好,体现“该精就精,该粗就粗”一般经济公差为:下料±0.03,成形±0.05,角度±0.5°4)重要及关键尺寸应综合考虑制程稳定性、装配、使用功能并非多益善.5)设计基准,制造基准,测量基准相统一;2.形位公差:1)基准(面或线)不应有变形2)标注应清楚明确,方便量测;3)设计基准,制造基准,测量基准相统一;4)应综合考虑制程稳定性及使用要求,并非多多益善,精度一般可达到0.10;5)很稳定的尺寸, 如下料尺寸等可以不标.3.结构设计及强度要求1)材料选用满足使用要求,又方便采购的原料;2)零件外形园角,防止滚镀表面刮伤;3)零件应有足够的强度及刚性,防止在贮存,电镀、搬运过程中的变形及尺寸变异;4)特殊零件,可采用多种工序组合方式,如多轴成形加工.五金模具+治具等不同方式来完成;5)连续料带要求:A)Carrier应有足够的强度及刚性B)尽量采用双侧CarrierC)注意包装时Carrier及零件是否变形D)连续电镀的孔径、孔距特殊要求4.五金零件加工工艺:1)冲裁A)断面质量、光亮面比例大小B)毛刺大小(一般不超过0.05)及方向,对外观、功能的影响C)倒刺结构,不允许有园角D)尽量避免长悬臂或长槽E)零件平整度要求,一般为0.102) 弯曲A)最小弯曲半径B)外侧龟裂的影响C)弯起高度应大于2t,如图4-4D)孔边距离应大于t,如图4-5,也可采用如图4-6所示工艺 F)材料方向性对使用性能的影响 3) 抽引A) 形状尽量简单对称B) R 角不应太小,一般可达R0.30, 如图4-7 C) 内外尺寸不可同时标注 D) 表面模痕不应有苛刻要求E) 平面度一般可达0.10第八章工程图面作业标准第二节五金模具一.五金模具开发流程,见表8-1二.五金模具装配图(图8-1)三.模具图面常见符号含义M,MC ――铣SP ――――基准点H ―――热处理TYP ――――典型尺寸ELE ――镀铬RP ――――圆弧点DYE ――染黑CEN,CL ――中心线G ―――磨TAN ――――切点PG ―――光学曲线磨THR ――――穿孔JG ―――坐标磨BOTT ―――底面W/C,W ――线割TOP ――――顶面E,EDM――放电SYM ――――对称L ――――车T ―――――厚度INT ―――交点CB ――――沉孔C ――――倒角CLEAR ―――间隙四.典型零件排样1.HOOK类,见图8-22.抽引类,见图8-33.外壳类,见图8-4。
冲压件模具设计的常用公式
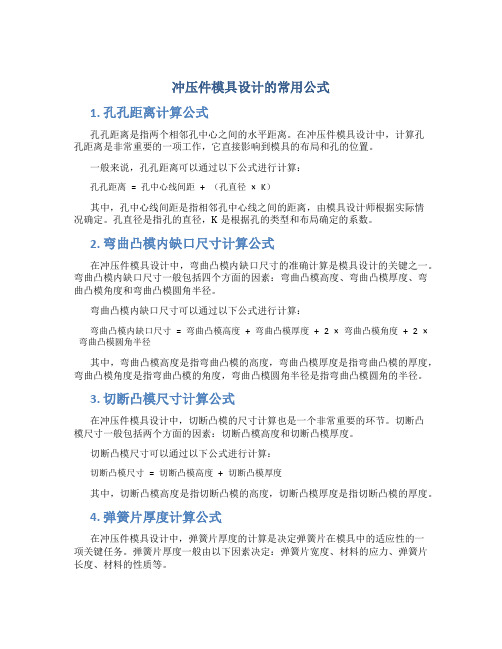
冲压件模具设计的常用公式1. 孔孔距离计算公式孔孔距离是指两个相邻孔中心之间的水平距离。
在冲压件模具设计中,计算孔孔距离是非常重要的一项工作,它直接影响到模具的布局和孔的位置。
一般来说,孔孔距离可以通过以下公式进行计算:孔孔距离 = 孔中心线间距 + (孔直径 × K)其中,孔中心线间距是指相邻孔中心线之间的距离,由模具设计师根据实际情况确定。
孔直径是指孔的直径,K是根据孔的类型和布局确定的系数。
2. 弯曲凸模内缺口尺寸计算公式在冲压件模具设计中,弯曲凸模内缺口尺寸的准确计算是模具设计的关键之一。
弯曲凸模内缺口尺寸一般包括四个方面的因素:弯曲凸模高度、弯曲凸模厚度、弯曲凸模角度和弯曲凸模圆角半径。
弯曲凸模内缺口尺寸可以通过以下公式进行计算:弯曲凸模内缺口尺寸 = 弯曲凸模高度 + 弯曲凸模厚度 + 2 × 弯曲凸模角度 + 2 ×弯曲凸模圆角半径其中,弯曲凸模高度是指弯曲凸模的高度,弯曲凸模厚度是指弯曲凸模的厚度,弯曲凸模角度是指弯曲凸模的角度,弯曲凸模圆角半径是指弯曲凸模圆角的半径。
3. 切断凸模尺寸计算公式在冲压件模具设计中,切断凸模的尺寸计算也是一个非常重要的环节。
切断凸模尺寸一般包括两个方面的因素:切断凸模高度和切断凸模厚度。
切断凸模尺寸可以通过以下公式进行计算:切断凸模尺寸 = 切断凸模高度 + 切断凸模厚度其中,切断凸模高度是指切断凸模的高度,切断凸模厚度是指切断凸模的厚度。
4. 弹簧片厚度计算公式在冲压件模具设计中,弹簧片厚度的计算是决定弹簧片在模具中的适应性的一项关键任务。
弹簧片厚度一般由以下因素决定:弹簧片宽度、材料的应力、弹簧片长度、材料的性质等。
弹簧片厚度可以通过以下公式进行计算:弹簧片厚度 = (弹簧片宽度 × 弹簧片宽度 × 弹簧片长度 × 弹簧片长度)/ (16 × 弹簧片宽度 × 材料的应力)其中,弹簧片宽度是指弹簧片的宽度,弹簧片长度是指弹簧片的长度,材料的应力是指材料的屈服应力。
冷冲压模具常用零件标准

冷冲压模具常用零件标准一、弹簧与橡胶的选用1.橡胶橡胶允许承受的载荷较大,占据的空间较小,安装调整比较灵活方便,而且成本低,是中小型冷冲模弹性卸料、顶件及压边的常用弹性元件。
选用橡胶时,应主要确定其自由高度、预压缩量及截面积。
其计算公式及步骤可由表1确定。
表1 卸料橡胶计算公式2.弹簧弹簧常用圆柱螺旋压缩弹簧和碟形弹簧可按表2至表4选用。
表2 圆柱螺旋压缩弹簧注:1. 材料:65Mn 、60Si2Mn ,热处理硬度40~48HRC ,表面磷化处理。
2. 带“*”的系细长比大于3.7,应考虑设置心轴或套筒。
3. 标准:GB/T2089-1994。
表3 碟形弹簧系列B3.0;/206000;75.0;280==≈≈mm N E th tD注:1. 材料:60Si2MnA 或50CrV A ,硬度42~52HRC 。
2. 摘自GB/T1972-1992。
表4 碟形弹簧的主要计算公式注:表中—一个弹簧在压缩量等于0.75h 0时的最大允许负荷; 0h —弹簧的极限行程(mm );n —装置中一组弹簧的总数;z —组合弹簧中每叠的弹簧数(图b 中3=z ); h —一个弹簧的高度(mm );δ—弹簧板厚度(mm ),dD h --=)(2t a n δϕ。
二、模具常用螺钉与销钉冷冲模零件的连接与紧固常用圆柱头内六角螺钉和沉头螺钉(表5和表6),零件的定位常用圆柱销(表7)。
表5 圆柱头内六角螺钉注:1. 标准:GB/T70.1-20002. 材料:35钢。
表6开槽沉头螺钉注:1. 标准:GB/T5279; 2. 材料:Q235。
2. 材料:Q235,35,45。
三、模具上有关螺钉孔得尺寸1. 螺钉通过孔的尺寸见表8。
2. 螺钉旋进的最小深度、窝座最小深度以及圆柱销配合长度见下图所示。
螺纹攻螺纹前钻孔直径:1)当螺距mm t 1<时 t d d -=M 0 2)当螺距mmt 1>时t d d )06.1~04.1(M 0-=式中 0d —钻孔直径(mm ); M d —螺纹标称直径(mm )。
铜冲压模具步距计算公式

铜冲压模具步距计算公式在金属加工行业中,冲压模具是一种常见的工具,用于将金属材料加工成所需形状的零件。
铜材料作为一种常见的金属材料,在冲压加工中也有着广泛的应用。
在铜冲压模具的设计和制造中,步距是一个非常重要的参数,它直接影响着模具的加工效率和加工质量。
因此,合理计算铜冲压模具的步距是非常重要的。
步距的定义。
步距是指在冲压加工过程中,连续两次冲压动作之间的距离。
在铜冲压模具中,步距的大小直接影响着模具的加工效率和加工质量。
如果步距过小,可能会导致模具在连续冲压过程中出现卡死或者卡料的情况,从而影响加工效率;如果步距过大,可能会导致冲压零件的尺寸精度不高,影响加工质量。
铜冲压模具步距计算公式。
在铜冲压模具的设计中,通常会根据材料的性质、模具的结构和加工要求等因素来计算步距。
一般来说,铜冲压模具的步距计算公式可以表示为:步距 = (材料的厚度 + 冲裁间隙)×冲裁次数。
其中,材料的厚度是指待加工的铜材料的厚度,冲裁间隙是指冲模和模具之间的间隙,冲裁次数是指在完成一个零件的冲压加工之后,模具需要移动的次数。
举例说明。
假设待加工的铜材料的厚度为2mm,冲裁间隙为0.1mm,冲裁次数为10次,那么根据上述的步距计算公式,可以得到步距为:步距 = (2mm + 0.1mm)× 10 = 21mm。
因此,在这个例子中,铜冲压模具的步距应该设置为21mm。
需要注意的是,上述的步距计算公式是一个基本的计算公式,实际在设计和制造铜冲压模具时,还需要考虑到具体的加工要求、模具结构、材料的性质等因素,可能需要对步距进行调整和优化。
总结。
铜冲压模具的步距是一个非常重要的参数,它直接影响着模具的加工效率和加工质量。
合理计算铜冲压模具的步距,可以提高模具的加工效率,保证加工零件的尺寸精度,从而提高生产效率和产品质量。
因此,在设计和制造铜冲压模具时,需要根据具体的加工要求和材料的性质等因素,合理计算步距,并进行优化调整。
- 1、下载文档前请自行甄别文档内容的完整性,平台不提供额外的编辑、内容补充、找答案等附加服务。
- 2、"仅部分预览"的文档,不可在线预览部分如存在完整性等问题,可反馈申请退款(可完整预览的文档不适用该条件!)。
- 3、如文档侵犯您的权益,请联系客服反馈,我们会尽快为您处理(人工客服工作时间:9:00-18:30)。
常用公式及数据表
冲压件模具设计常用公式
一.冲裁间隙分类见表4-1
表4-1 冲裁间隙分类(JB/Z 271-86)
二.冲裁间隙选择(提供参考) 见表4-2
(見下頁)
表4-2 冲裁间隙比值(單邊间隙) (單位:%t)
(注: 1. 本表適用于厚度為10mm以下的金屬材料, 厚料间隙比值應取大些;
2. 凸,凹模的制造偏差和磨損均使间隙變大, 故新模具應取最小间隙;
3. 硬質合金冲模间隙比鋼模大20% 左右.)
注: 冲裁间隙选择應綜合考慮下列因素:
1.冲床﹑模具的精度及剛性.
2.產品的斷面品質﹑尺寸精度及平整度.
3.模具壽命.
4.跳屑.
5.被加工材料的材質﹑硬度﹑供應狀態及厚度.
6.廢料形狀.
7.冲子﹑模仁材質﹑硬度及表面加工質量.
三.冲裁力﹑卸(剝)料力﹑推件力﹑頂件力
F冲= 1.3 * L * t *τ(N) (公式4-1)
F卸= K卸* F冲(N) (公式4-2)
F推= N * K推* K冲(N) (公式4-3)
F頂= K頂* F冲(N) (公式4-4)
其中:
L ――冲切線長度(mm)
t ――材料厚度(mm)
τ――材料抗剪強度(N/mm2 )
1.3 ――安全系數
K卸――卸(剝)料力系數
K推――推料力系數
K頂――頂料力系數
K卸K推K頂數值见表4-3
表4-3 卸料力﹑推件力和頂件力系數
注:卸料力系數K卸在冲多孔﹑大搭邊和輪廓復雜時取上限值.
四.中性層彎曲半徑
R = r + x * t (mm) (公式4-5) 其中:
R――中性層彎曲半徑(mm)
r ――零件內側半徑(mm)
x ――中性層系數
中性層系數见表4-4(提供参考)
表4-4 中性層系數x值
注: 彎曲件展開尺寸與下列因素有關:
1.彎曲成形方式.
2.彎曲间隙.
3.有無压料.
4.材料硬度﹑延伸率﹑厚度.
5.根据實際狀況精確修正.
五.材料最小彎曲半徑,见表4-5
表4-5 最小彎曲半徑。