车刀的主要角度
车刀种类和角度选择原则详解
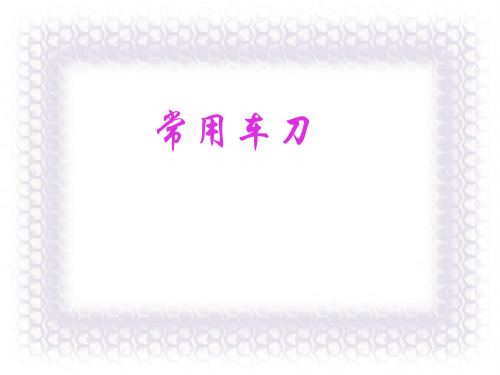
车刀不对准工件中心对角度的影响
五、车刀刃磨
无论硬质合金车刀(焊接)或高速钢 车刀,在使用之前都要根据切削条 件所选择的合理切削角度进行刃磨 ,一把用钝了的车刀,为恢复原有 的几何形状和角度,也必须重新刃 磨。
重 要 性
三分手艺、七分刀 徒弟的手、师傅的刀
1.磨刀步骤(图a~d)
⑴磨前刀面 把前角和刃倾角磨正确。 ⑵磨主后刀面 把主偏角和主后角磨正确。 ⑶磨副后刀面 把副偏角和副后角磨正确。 ⑷磨刀尖圆弧 圆弧半径约0.5~2mm左右。 ⑸研磨刀刃 车刀在砂轮上磨好以后,再用油石加些机油研磨车 刀的前面及后面,使刀刃锐利和光洁。这样可延长车刀的使用寿命。 车刀用钝程度不大时,也可用油石在刀架上修磨。硬质合金车刀可 用碳化硅油石修磨。
前角γo
——在主切削刃选定点的正交平面po内, 前刀面与基面之间的夹角
。
后角αo
——在正交平面po内,主后刀面与切削 平面之间的夹角。
主偏角κr
——主切削刃在基面上的投影与进给方 向的夹角。
刃倾角λs ——在切削平面ps内,主切削刃与 基面pr的夹角。
其他角度:
副前角γoˊ、 副后角αoˊ、 副偏角κrˊ、 刃倾角λsˊ
3.主偏角、副偏角的选择 (1)主偏角的选择 A、主偏角κr的增大或减小对切削加工有利的一 面 在背吃刀量ap与进给量f 不变时,主偏角κr减小 将使切削厚度hD减小,切削宽度bD增加,参加 切削的切削刃长度也相应增加,切削刃单位长度 上的受力减小,散热条件也得到改善。 主偏角κr减小时,刀尖角增大,刀尖强度提高, 刀尖散热体积增大。 所以,主偏角κr减小,能提高刀具耐用度。
(4)良好的工艺性和经济性
车刀的安装
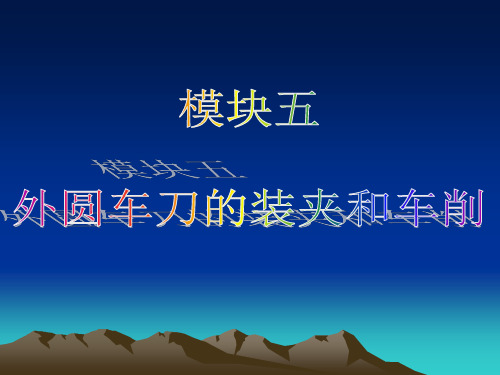
1)使用活顶尖对中心。 2)利用机床导轨到主轴中心的高度,使用直尺对中心。 3)工件端面划线对中心。
4、粗精车的概念
车削工件,一般分为粗车和精车。 1)粗车 在车床动力条件允许的情况下,通常采用进刀深、进给量大、低 转速的做法,以合理的时间尽快的把工件的余量去掉,因为粗车对切 削表面没有严格的要求,只需留出一定的精车余量即可。由于粗车切 削力较大,工件必须装夹牢靠。粗车的另一作用是:可以及时的发现 毛坯材料内部的缺陷、如夹渣、砂眼、裂纹等。也能消除毛坯工件内 部残存的应力和防止热变形。 2 )精车 精车是车削的末道工序,为了使工件获得准确的尺寸和规定的表 面粗糙度、操作者在精车时、通常把车刀修磨的锋利些,车床的转速 高一些,进给量选的小一些。
3、看生产实习图和确定加工步骤:
加工步骤: 1.用卡盘夹住工件φ78外圆长20左右,找正夹紧。 2.粗精车平面、外圆,尺寸达到要求,倒角1×45 °。 3.检查卸车
4、容易产生的问题和注意事项:
1、初学者使用机动进给注意力要集中,以防滑板等与卡盘碰撞。 2、粗车切削力较大,工件易发生移位,在精车接刀前应进行一次复查。 3、车削较大直径的工件时,平面易产生凹凸,应随时用钢直尺检验。 4、为了保证工件质量,掉头装夹时要垫铜皮。
二、用手动进给车削外圆、平面和倒角
1 、车平面的方法
开动车床使工件旋转,移动小滑板或床鞍控制进刀深度,然后锁 紧床鞍,摇动中滑板丝杠进给、由工件外向中心或由工件中心向外进 给车削。见下图。
2、车外圆的方法
• 1)移动床鞍至工件的右端、用中滑板控制进刀深度、摇动小滑 板丝杠或床鞍纵向移动车削外圆,一次进给完毕,横向退刀,再纵向 移动刀架或床鞍至工件右端,进行第二、第三次进给车削,直至符合 图样要求为止。 • 2)再在车削外圆时,通常要进行试切削和时测量。其具体方法 是:根据工件直径余量的二分之一作横向进刀,当车刀在纵向外圆上 进给2毫米左右时,纵向快速退刀,然后停车测量,(注意横向不要 退刀)。然后停车测量,如果已经符合尺寸要求,就可以直接纵向进 给进行车削,否则可按上述方法继续进行试切削和试测量,直至达到 要求为止。 • 3 )为了确保外圆的车削长度,通常先采用刻线痕法,后采用测 量法进行,即在车削前根据需要的长度,用钢直尺、样板或卡尺及车 刀刀尖在工件的表面刻一条线痕。然后根据线痕进行车削,当车削完 毕,再用钢直尺或其他工具复测。
刀主要角度
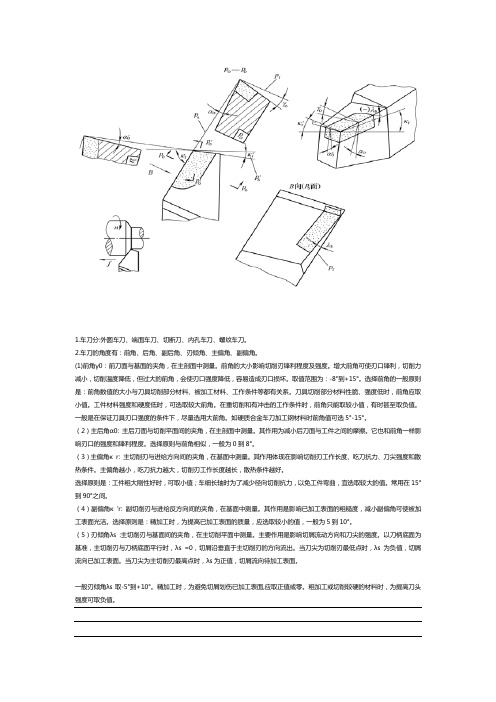
1.车刀分:外圆车刀、端面车刀、切断刀、内孔车刀、螺纹车刀。
2.车刀的角度有:前角、后角、副后角、刃倾角、主偏角、副偏角。
(1)前角γ0:前刀面与基面的夹角,在主剖面中测量。
前角的大小影响切削刃锋利程度及强度。
增大前角可使刃口锋利,切削力减小,切削温度降低,但过大的前角,会使刃口强度降低,容易造成刃口损坏。
取值范围为:-8°到+15°。
选择前角的一般原则是:前角数值的大小与刀具切削部分材料、被加工材料、工作条件等都有关系。
刀具切削部分材料性脆、强度低时,前角应取小值。
工件材料强度和硬度低时,可选取较大前角。
在重切削和有冲击的工作条件时,前角只能取较小值,有时甚至取负值。
一般是在保证刀具刃口强度的条件下,尽量选用大前角。
如硬质合金车刀加工钢材料时前角值可选5°-15°。
(2)主后角α0: 主后刀面与切削平面间的夹角,在主剖面中测量。
其作用为减小后刀面与工件之间的摩擦。
它也和前角一样影响刃口的强度和锋利程度。
选择原则与前角相似,一般为0到8°。
(3)主偏角κr: 主切削刃与进给方向间的夹角,在基面中测量。
其作用体现在影响切削刃工作长度、吃刀抗力、刀尖强度和散热条件。
主偏角越小,吃刀抗力越大,切削刃工作长度越长,散热条件越好。
选择原则是:工件粗大刚性好时,可取小值;车细长轴时为了减少径向切削抗力,以免工件弯曲,宜选取较大的值。
常用在15°到90°之间。
(4)副偏角κ'r: 副切削刃与进给反方向间的夹角,在基面中测量。
其作用是影响已加工表面的粗糙度,减小副偏角可使被加工表面光洁。
选择原则是:精加工时,为提高已加工表面的质量,应选取较小的值,一般为5到10°。
(5)刃倾角λs :主切削刃与基面间的夹角,在主切削平面中测量。
主要作用是影响切屑流动方向和刀尖的强度。
以刀柄底面为基准,主切削刃与刀柄底面平行时,λs =0,切屑沿垂直于主切削刃的方向流出。
解释车刀的主要几何角度,并说明对车削加工的影响

在车削加工中,车刀的主要几何角度对加工效果和加工质量有着重要的影响。
在本文中,我将从深度和广度上对车刀的几何角度进行全面评估,并探讨它们对车削加工的影响。
1. 切削角:切削角是指车刀切削刃上的主切削刃与前方切削方向的夹角。
切削角的大小直接影响着切屑的形成和流动。
当切削角较大时,切削力减小,但切削刃容易磨损;当切削角较小时,切削力增大,但切削刃磨损减小。
选择适当的切削角对于保证加工质量和提高加工效率至关重要。
2. 后角:后角是指车刀主切削刃与切削方向之间的夹角。
后角的大小影响着车刀的进给力和阻力。
当后角增大时,进给力增大,加工效率提高;但阻力也会增大,对车刀和工件的刚性要求也会增加。
合理选择后角是为了在保证加工效率的尽可能减小刀具和工件的损耗。
3. 主偏角:主偏角是指车刀主切削刃与工件表面的夹角。
主偏角的大小直接影响着工件的表面质量和加工精度。
一般来说,主偏角越小,加工表面的质量越好,但车刀的刚度和稳定性要求也越高。
在实际应用中需要根据工件的要求和加工条件选择合适的主偏角。
4. 副偏角:副偏角是指车刀副切削刃与工件表面的夹角。
副偏角的大小影响着切削刃与工件的接触面积和切削力的大小。
合理选择副偏角可以有效减小切削力,提高车削加工的效率和质量。
车刀的几何角度对车削加工有着重要的影响,其合理选择可以有效提高加工效率和加工质量。
在实际应用中,需要根据具体的加工要求和工件材料来选择合适的几何角度,以达到最佳的加工效果。
个人观点和理解:车刀的几何角度是车削加工中的关键参数,合理选择和调整这些角度对于提高加工质量和效率至关重要。
在实际应用中,需要综合考虑工件材料、加工条件和车刀性能等因素,进行合理的选择和调整,以达到最佳的加工效果。
以上是对“解释车刀的主要几何角度,并说明对车削加工的影响”的文章撰写,希望能帮助你更深入地理解这一主题。
在车削加工中,车刀的几何角度对加工效果和加工质量有着重要的影响。
除了切削角、后角、主偏角和副偏角外,还有其他几何角度也对车削加工起着重要作用,比如前角、刀尖半径等。
车刀的角度如何确定

车刀属于单锋刀具,因车削工作物形状不同而有很多型式,但它各部位的名称及作用却是相同的。
一支良好的车刀必须具有刚性良好的刀柄及锋利的刀锋两大部份。
车刀的刀刃角度,直接影响车削效果,不同的车刀材质及工件材料、刀刃的角度亦不相同。
车床用车刀具有四个重要角度,即前间隙角、边间隙角、后斜角及边斜角。
1)前间隙角自刀鼻往下向刀内倾斜的角度为前间隙角,因有前间隙角,工作面和刀尖下形成一空间,使切削作用集中于刀鼻。
若此角度太小,刀具将在表面上摩擦,而产生粗糙面,角度太大,刀具容易发生震颤,使刀鼻碎裂无法光制。
装上具有倾斜中刀把的车刀磨前间隙角时,需考虑刀把倾斜角度。
高速钢车刀此角度约8~10度之间,碳化物车刀则在6~8度之间。
2)边间隙角刀侧面自切削边向刀内倾斜的角度为边间隙角。
边间隙角使工作物面和刀侧面形成一空间使切削作用集中于切削边提高切削效率。
高速钢车刀此角度约10~12度之间。
3)后斜角从刀顶面自刀鼻向刀柄倾斜的角度为后斜角。
此角度主要是在引导排屑及减少排屑阻力。
切削一般金属,高速钢车刀一般为8~16度,而碳化物车刀为负倾角或零度。
4)边斜角从刀顶面自切削边向另一边倾斜,此倾斜面和水平面所成角度为边斜角。
此角度是使切屑脱离工作物的角度,使排屑容易并获得有效之车削。
切削一般金属,高速钢车刀此角度大约为10~14度,而碳化物车刀可为正倾角也可为负倾角。
5)刀端角刀刃前端与刀柄垂直之角度。
此角度的作用为保持刀刃前端与工件有一间隙避免刀刃与工件磨擦或擦伤已加工之表面。
6)切边角刀刃前端与刀柄垂直之角度,其作用为改变切层的厚度。
同时切边角亦可改变车刀受力方向,减少进刀阻力,增加刀具寿命,因此一般粗车时,宜采用切边角较大之车刀,以减少进刀阻力,增加切削速度。
7)刀鼻半径刀刃最高点之刀口圆弧半径。
刀鼻半径大强度大,用于大的切削深度,但容易产生高频振动。
一、车刀各种角度常识

六、数控刀具标准点击上面相关内容观看一、车刀的各种角度常识车刀的主要角度前角γo在主剖面P0内测量的前刀面与基面之间的夹角。
前角表示前刀面的倾斜程度,有正、负和零值之分,其符号规定如图所示。
后角αo 在主剖面P0内测量的主后刀面与切削平面之间的夹角。
后角表示主后刀面的倾斜程度,一般为正值。
主偏角κr在基面内测量的主切削刃在基面上的投影与进给运动方向的夹角。
主偏角一般为正值。
副偏角κr'在基面内测量的副切削刃在基面上的投影与进给运动反方向的夹角。
副偏角一般为正值。
刃倾角λs在切削平面内测量的主切削刃与基面之间的夹角。
当主切削刃呈水平时,λs=0;刀尖为主切削刃最低点时,λs<0;刀尖为主切削刃上最高点是,λs>0,如图示。
点击回到页首二、新型陶瓷刀具简介新型陶瓷刀具的出现,是人类首次通过运用陶瓷材料改革机械切削加工的一场技术革命的成果。
早在20世纪初,德国与英国已经开始寻求采用陶瓷刀具取代传统的碳素工具钢刀具。
陶瓷材料因其高硬度与耐高温特性成为新一代的刀具材料,但陶瓷也由于其人所共知的脆性受到局限,于是如何克服陶瓷刀具材料的脆性,提高它的韧性,成为近百年来陶瓷刀具研究的主要课题。
陶瓷的应用范围亦日益扩大。
工程技术界努力研制与推广陶瓷刀具的主要原因,(一)是可以大大提高生产效率;(二)是由于构成高速钢与硬质合金的主要成分钨资源在全球范围内的枯竭所决定。
20世纪80年代初估计,全世界已探明的钨资源仅够使用50年时间。
钨是世界上最稀缺的资源,但其在切削刀具材料中的消耗却很大,从而导致钨矿价格不断攀升,几十年中上涨好多倍,这在一定程度上也促进了陶瓷刀具研制与推广,陶瓷刀具材料的研制开发取得了令人瞩目的成果。
到目前为止,用作陶瓷刀具的材料已形成氧化铝陶瓷,氧化铝—金属系陶瓷、氧化铝—碳化物陶瓷、氧化铝—碳化物金属陶瓷、氧化铝—氮化物金属陶瓷及最新研究成功的氮化硼陶瓷刀具。
就世界范围讲,德国陶瓷刀具已不仅用于普通机床,且已将其作为一种高效、稳定可靠的刀具用于数控机床加工及自动化生产线。
刀具的标注角度

刀具的标注角度1.前角:当前面与切削平面夹角小于90度时,前角为正值,大于90度时为负值.2.后角; 当后面与基面夹角小于90度时,后角为正值,大于90度时,后角为负值。
车切基本知识一、车刀材料在切削过程中,刀具的切削部分要承受很大的压力、摩擦、冲击和很高的温度。
因此,刀具材料必须具备高硬度、高耐磨性、足够的强度和韧性,还需具有高的耐热性(红硬性),即在高温下仍能保持足够硬度的性能。
常用车刀材料主要有高速钢和硬质合金。
1.高速钢高速钢又称锋钢、是以钨、铬、钒、钼为主要合金元素的高合金工具钢。
高速钢淬火后的硬度为HRC63~67,其红硬温度550℃~600℃,允许的切削速度为25~30m/min。
高速钢有较高的抗弯强度和冲击韧性,可以进行铸造、锻造、焊接、热处理和切削加工,有良好的磨削性能,刃磨质量较高,故多用来制造形状复杂的刀具,如钻头、铰刀、铣刀等,亦常用作低速精加工车刀和成形车刀。
常用的高速钢牌号为W18Cr4V和W6Mo5Cr4V2两种。
2.硬质合金硬质合金是用高耐磨性和高耐热性的WC(碳化钨)、TiC(碳化钛)和Co(钴)的粉末经高压成形后再进行高温烧结而制成的,其中Co起粘结作用,硬质合金的硬度为HRA89~94(约相当于HRC74~82),有很高的红硬温度。
在800~1000℃的高温下仍能保持切削所需的硬度,硬质合金刀具切削一般钢件的切削速度可达100~300m/min,可用这种刀具进行高速切削,其缺点是韧性较差,较脆,不耐冲击,硬质合金一般制成各种形状的刀片,焊接或夹固在刀体上使用。
常用的硬质合金有钨钴和钨钛钴两大类:(1)钨钴类(YG)由碳化钨和钴组成,适用于加工铸铁、青铜等脆性材料。
常用牌号有YG3、YG6、YG8等,后面的数字表示含钴量的百分比,含钴量愈高,其承受冲击的性能就愈好。
因此,YG8常用于粗加工,YG6和YG3常用于半精加工和精加工。
(2)钨钛钴类(YT)由碳化钨、碳化钛和钴组成,加入碳化钛可以增加合金的耐磨性,可以提高合金与塑性材料的粘结温度,减少刀具磨损,也可以提高硬度;但韧性差,更脆、承受冲击的性能也较差,一般用来加工塑性材料,如各种钢材。
车刀角度分析
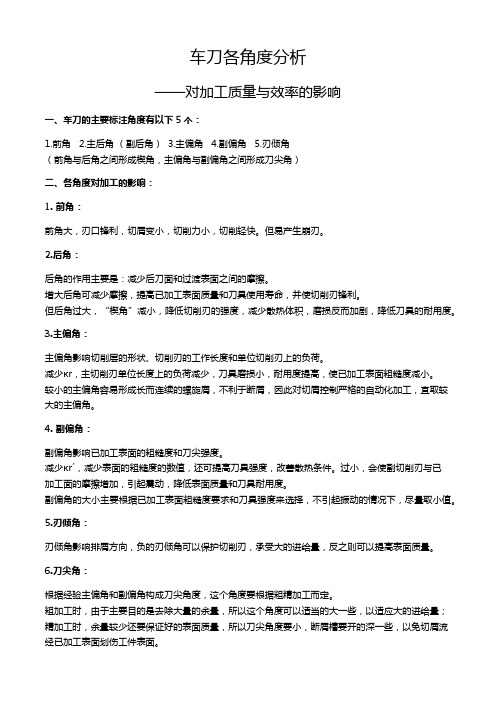
车刀各角度分析——对加工质量与效率的影响一、车刀的主要标注角度有以下5个:1.前角2.主后角(副后角)3.主偏角4.副偏角5.刃倾角(前角与后角之间形成楔角,主偏角与副偏角之间形成刀尖角)二、各角度对加工的影响:1. 前角:前角大,刃口锋利,切屑变小,切削力小,切削轻快。
但易产生崩刃。
2.后角:后角的作用主要是:减少后刀面和过渡表面之间的摩擦。
增大后角可减少摩擦,提高已加工表面质量和刀具使用寿命,并使切削刃锋利。
但后角过大,“楔角”减小,降低切削刃的强度,减少散热体积,磨损反而加剧,降低刀具的耐用度。
3.主偏角:主偏角影响切削层的形状、切削刃的工作长度和单位切削刃上的负荷。
减少κr,主切削刃单位长度上的负荷减少,刀具磨损小,耐用度提高,使已加工表面粗糙度减小。
较小的主偏角容易形成长而连续的螺旋屑,不利于断屑,因此对切屑控制严格的自动化加工,宜取较大的主偏角。
4. 副偏角:副偏角影响已加工表面的粗糙度和刀尖强度。
减少κr´,减少表面的粗糙度的数值,还可提高刀具强度,改善散热条件。
过小,会使副切削刃与已加工面的摩擦增加,引起震动,降低表面质量和刀具耐用度。
副偏角的大小主要根据已加工表面粗糙度要求和刀具强度来选择,不引起振动的情况下,尽量取小值。
5.刃倾角:刃倾角影响排屑方向,负的刃倾角可以保护切削刃,承受大的进给量,反之则可以提高表面质量。
6.刀尖角:根据经验主偏角和副偏角构成刀尖角度,这个角度要根据粗精加工而定。
粗加工时,由于主要目的是去除大量的余量,所以这个角度可以适当的大一些,以适应大的进给量;精加工时,余量较少还要保证好的表面质量,所以刀尖角度要小,断屑槽要开的深一些,以免切屑流经已加工表面划伤工件表面。
第二讲:车刀的角度及刃磨 ppt课件
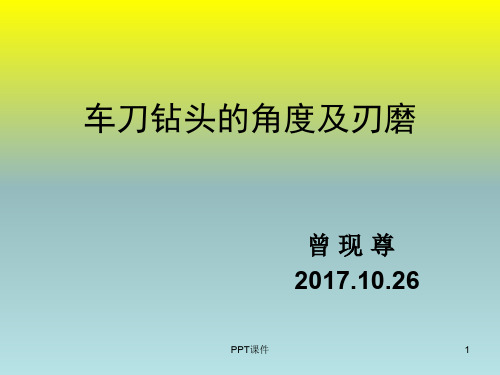
(b)副偏角κr´:副刀刃在基面上 投影与进给反方向的夹角。
主要作用是减少副刀刃和已加工表 面之PPT课件
10
3)在切削平面内测量的角度
刃倾角λs:主刀刃与基面间的夹 角。
(4)当加工精度要求高的细长轴时,为了减小振动,须选用较大的主偏 角;为避免划伤已加工表面,须选用正的刃倾角,并相应减小前角。
PPT课件
12
四、砂轮知识
PPT课件
碳化硅砂 轮 适用 于硬质合 金车刀的 刃磨。
氧化铝砂 轮 适用于 高速钢和 碳素工具 钢刀具的 刃磨。
13
五、车刀刃磨的步骤
磨主后刀面,同时磨出主 偏角及主后角,如图所示;
18
车刀刃磨操作技巧与注意事项
刃磨开机先检查,设备安全最重要;
砂轮转速稳定后,双手握刀立轮侧;
两肘夹紧腰部处,刃磨平稳防抖动;
车刀高低须控制,砂轮水平中心处;
刀压砂轮力适中,反力太大易打滑;
手持车刀均匀移,温高烫手则暂离;
刀离砂轮应小心,保护刀尖先抬起;
高速钢刀可水冷,防止退火保硬度;
硬质合金勿水淬,骤冷易使刀具裂;
切削速度 进给量 背吃刀量
在单位时间内,工件和刀具沿主 运动方向相对移动的距离。
在主运动的一个循环(或单位时 间)内,工件与刀具间沿进刀方 向相对运动的距离。
待加工表面和已加工表面的 垂直距离。
PPT课件
4
1、刀具结构
二、刀具
车刀的组成和形式
(a)焊接式 (b)整体式 (c)机夹式
PPT课件
5
PPT课件
PPT课件
17
车刀的几何角度及切削参数

4.刀尖形状的选择 刀尖概念:主切削刃与副切削刃连接的地方 刀尖是刀具强度和散热条件都很差的地方。切 削过程中,刀尖切削温度较高,非常容易磨损, 因此增强刀尖,可以提高刀具耐用度。刀尖对 已加工表面粗糙度有很大影响。
Hale Waihona Puke (a)倒角刃(b)圆弧刃
(c)修光刃
1、工件材料强度或硬度较高时,为加强切 削刃,一般采用较小后角。 2、对于塑性较大材料,已加工表面易产生 加工硬化时,后刀面摩擦对刀具磨损和加 工表面质量影响较大时,一般取较大后角。
在一定切削条件下的基本选择方法
1.前角和前刀面形状的选择 2.后角及形状的选择 3.主偏角、副偏角的选择
:
4.刀尖形状的选择 5.刃倾角的选择
1.前角和前刀面形状的选择
(1)
前角的选择: 在选择刀具前角时首先应保证刀刃锋 利,同时也要兼顾刀刃的强度与耐用 度。 刀具前角的合理选择,主要由刀具材 料和工件材料的种类与性质决定。
B、主偏角κr的增大或减小对切削加工不利的一面 主偏角的减小也会产生不良影响。因为根据切削 力分析可以得知,主偏角κr减小,将使背向力Fp 增大,从而使切削时产生的挠度增大,降低加工 精度。同时背向力的增大将引起振动。 因此主偏角的减小对刀具耐用度和加工精度产生 不利影响。
②、工艺系统刚性较差时 (工件长径比lw/dw = 612) ,或带有冲击性的切削,主偏角κr可以取大 值,一般κr=60o~75o,甚至主偏角κr可以大于 90o,以避免加工时振动。 硬质合金刀具车刀的主偏角多为60o~75o 。 ③、根据工件加工要求选择。 当车阶梯轴时, κr =90o;同一把刀具加工外圆、 端面和倒角时, κr =45o。
车刀几何角度及其作用

A正值
B负值
一、车刀的几何角度
基本角度 基 面Pr:
ΚΚ’
r r
εr
β
o
主截面Po :γo 切削面Ps:
αo
λs
车刀的几何角度及其作用
一、车刀的几何角度
基本角度 基 面Pr:
ΚΚ’
r r
εr
β
o
主截面Po :γo 切削面Ps:
αo
λs
二、车刀几何角度的作用
1.主偏角 主偏角
Κr
改变主切削刃和刀头的受力和 散热情况
减小 ,轴向力FX 增加 。 ◇主偏角增大,径向力FY
◇加工细长轴,主偏角应选择(
C )车刀。
A45° B75° C90°
二、车刀几何角度的作用
2.副偏角 Κr ’ 副偏角 减少副切削刃与工件已加工表 面的摩擦,影响表面质量。
◇精加工时,应选择(
B
)的副偏角
A.较大
B.较小
二、车刀几何角度的作用
3.前角 γo 前角 影响刃口的锋利程度和强度, 影响切削变形和切削力。
减小 ,切削力 减小 。 ◇前角增大,变形
◇粗加工或加工不连续表面,要选择 B 的前角
A较大
B较小
C无所谓
二、车刀几何角度的作用
4.后角αo 后角
减少车刀后刀面与工件的摩擦, 影响切削刃和刀头的强度。
◇精加工时,要选择Fra bibliotekA的后角 C无所谓
A较大
B较小
二、车刀几何角度的作用
5.刃倾角 λs 刃倾角 主要作用是控制排屑方向
◇刀尖位于切削刃的最高点时, λs 为正值,切屑 流向待加工表面 ◇刀尖位于切削刃的最低点时,λs为负值,切屑 流向已加工表面 ◇精加工时,要选择 A 的后角
车刀的主要角度

二、车刀的角度
1、前角:前刀面与基面之间的夹角 2、后角:后刀面与切削平面之间的夹角 3、楔角:前刀面与后刀面之间的夹角 三个角之和为90度
二、车刀的角度
4、主偏角:主切削刃在基面内的投影与进给方向之间 的夹角
5、副偏角:主切削刃在基面内的投影与进给方 向之间的夹角 6、刀尖角:主切削与副切削刃在基面内的投影 之间的夹角
二、车刀几何角度的选择
(3)前角的选择:
选择原则:在刀具强度允许的条件下,尽量选较大的前角, 具体选择时根据工件的材料、刀具材料、加工性质等因素 选择。 ①加工脆性材料或硬度较高的材料时应选较小的前角, 反之,选较大的前角 ②高速钢车刀的前角一般应大于硬质合金车刀的前角。 ③精加工时选择较大的前角,反之选较小的前角。
三个角之和为180度
7、刃倾角:主切削刃与基面之间的夹角
二、车刀几何角度的选择
1、前角的选择: (1)前角的作用:
①影响车刀的锋利程序、切削力的大小与切削变形的大小。 ②影响车刀强度、受力情况和散热条件。
③影响加工表面质量。前角增大,刃口锋利,摩擦力小, 提高表面质量。 (2)前角正负的规定:我们要磨成正前角,刀尖高一点
2、后角的选择:
(1)后角的作用: ①减小后刀面与过渡表面之间的摩擦。 ②增大后角可使车刀刃口锋利。 (2)后角的正负的规定: 我们要磨成正后角,刀尖朝外面倾斜 (3)后角的选择: ①粗车时:选择较小的前角。
②精车时:选择较大的前角。
2、后角的选择:
③断续切削时或切削力较大时选取较大的前角。
3、主偏角与副偏角的选择:
(1)主偏角的作用:影响车刀的散热条件、断效果。
(2)主偏角的选择 ①刚性较差时选较大的主偏角。硬度高的工件选较小的 主偏角 ②刚性较差时选较大的主偏角。
车刀种类和刀刃角度选取原则

正交平面参考系
1.正交平面参考系时各参考面 :(右图)
——过切削刃选定点平行或垂直刀具安装面(或轴线)的平面。
——过切削刃选定点与 切削刃相切并垂直于基面的平面。
切削平面ps
正交平面po
基面pr
2. 刀具的标注角度
前角γo ——在主切削刃选定点的正交平面po内,前刀面与基面之间的夹角。 后角αo ——在正交平面po内,主后刀面与切削平面之间的夹角。
3.在一定切削条件下的基本选择方法 :
1)前角和前刀面形状的选择
5)刃倾角的选择
3)主偏角、副偏角的选择
2)后角及形状的选择
4)刀尖形状的选择
1.前角和前刀面形状的选择 (1) 前角的选择: 在选择刀具前角时首先应保证刀刃锋利,同时也要兼顾刀刃的强度与耐用度。 刀具前角的合理选择,主要由刀具材料和工件材料的种类与性质决定。
三分手艺、七分刀
徒弟的手、师傅的刀
重要性
1.磨刀步骤(图a~d)
(a) (b) (c) (d) 图a~d 刃磨外圆车刀的一般步骤 a)磨前刀面 b)磨主后刀面 c)磨副后刀面 d)磨刀尖圆弧
C、负前角平面型 (右图) 特点:切削刃强度较好, 但刀刃较钝,切削变形大。 主要用于硬脆刀具材料。加工高强度高硬度材料,如淬火钢。 图示类型负前角后部加有正前角,有利于切屑流出。
螺纹车刀角度参数

螺纹车刀角度参数
以下是螺纹车刀的主要角度参数:
1. 刀尖角:此角度等于牙型角。
车削普通螺纹时,牙型角为60度。
英制螺纹时,牙型角为55度。
2. 前角:一般为0度至15度。
精车或精度要求高的螺纹,径向前角取得小些,约为0度至5度。
3. 后角:一般为5度至15度。
因受螺纹升角的影响,进刀方向一面的后角应磨得稍大些。
但大直径、小螺距的三角形螺纹,这种影响可忽略不计。
此外,在车削较大螺距以及硬度较高的螺纹时,应在车刀的两个切削刃上磨出宽度为4mm的倒棱,以防止崩刃并减少切削力。
以上信息仅供参考,如需了解更多信息,建议查阅专业书籍或咨询专业人士。
车刀的主要几何角度及选择

车刀的重要几何角度及选择1)前角(γ0 )选择的原则前角的大小重要解决刀头的坚固性与锋利性的冲突。
因此首先要依据加工材料的硬度来选择前角。
加工材料的硬度高,前角取小值,反之取大值。
其次要依据加工性质来考虑前角的大小,粗加工时前角要取小值,精加工时前角应取大值。
前角一般在—5°~25°选取。
通常,制作车刀时并没有预先制出前角(γ0),而是靠在车刀上刃磨出排屑槽来获得前角的。
排屑槽也叫断屑槽,它的作用是折断切屑,不产生缠绕;掌控切屑的流出方向,保持已加工表面的精度;降低切削抗力,延长刀具寿命。
2)后角(α0 )选择的原则首先考虑加工性质。
精加工时,后角取大值,粗加工时,后角取小值。
其次考虑加工材料的硬度,加工材料硬度高,主后角取小值,以加强刀头的坚固性;反之,后角应取小值。
后角不能为零度或负值,一般在6°~12°选取。
3)主偏角(Kr )的选用原则首先考虑车床、夹具和刀具构成的车削工艺系统的刚性,如系统刚性好,主偏角应取小值,这样有利于提高车刀使用寿命、改善散热条件及表面粗造度。
其次要考虑加工工件的几何形状,当加工台阶时,主偏角应取90°,加工中心切入的工件,主偏角一般取60 °。
主偏角一般在30°~90°,*常用的是45°、75 °、90 °。
4)副偏角(Kr)的选择原则首先考虑车刀、工件和夹具有充足的刚性,才能减小副偏角;反之,应取大值;其次,考虑加工性质,精加工时,副偏角可取10°~15°,粗加工时,副偏角可取5°左右。
5)刃倾角(λS)的选择原则重要看加工性质,粗加工时,工件对车刀冲击大,取λS≤ 0°,精加工时,工件对车刀冲击力小,取λS≥ 0°;通常取λS=0°。
刃倾角一般在—10°~5°选取。
车刀的六个基本角度作用
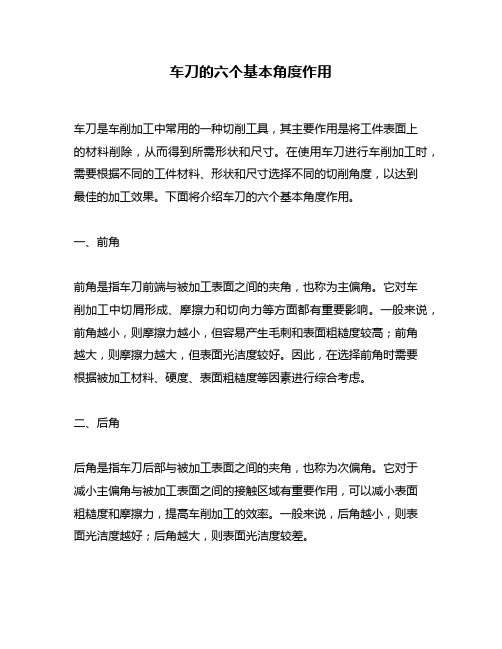
车刀的六个基本角度作用车刀是车削加工中常用的一种切削工具,其主要作用是将工件表面上的材料削除,从而得到所需形状和尺寸。
在使用车刀进行车削加工时,需要根据不同的工件材料、形状和尺寸选择不同的切削角度,以达到最佳的加工效果。
下面将介绍车刀的六个基本角度作用。
一、前角前角是指车刀前端与被加工表面之间的夹角,也称为主偏角。
它对车削加工中切屑形成、摩擦力和切向力等方面都有重要影响。
一般来说,前角越小,则摩擦力越小,但容易产生毛刺和表面粗糙度较高;前角越大,则摩擦力越大,但表面光洁度较好。
因此,在选择前角时需要根据被加工材料、硬度、表面粗糙度等因素进行综合考虑。
二、后角后角是指车刀后部与被加工表面之间的夹角,也称为次偏角。
它对于减小主偏角与被加工表面之间的接触区域有重要作用,可以减小表面粗糙度和摩擦力,提高车削加工的效率。
一般来说,后角越小,则表面光洁度越好;后角越大,则表面光洁度较差。
三、切削角切削角是指车刀主刃与被加工表面之间的夹角,也称为刃偏角。
它对于车削加工中的主要切削过程有重要影响。
一般来说,切削角越大,则切屑形成越容易,但对车床主轴负荷和机床精度要求也会更高;反之,则会降低负荷和精度要求,但容易产生毛刺和表面粗糙度较高。
因此,在选择切削角时需要根据被加工材料、硬度、表面粗糙度等因素进行综合考虑。
四、侧后角侧后角是指车刀侧面与被加工表面之间的夹角。
它对于车削加工中的侧向力和摩擦力有重要影响。
一般来说,侧后角越小,则侧向力和摩擦力越小,但容易产生毛刺和表面粗糙度较高;反之,则侧向力和摩擦力会增大,但表面光洁度较好。
因此,在选择侧后角时需要根据被加工材料、硬度、表面粗糙度等因素进行综合考虑。
五、刃倾角刃倾角是指车刀主刃与车床主轴中心线之间的夹角,也称为主偏角。
它对于车削加工中的切屑形成和排出有重要影响。
一般来说,刃倾角越小,则容易产生长而细的切屑,但对车床主轴负荷和机床精度要求也会更高;反之,则会降低负荷和精度要求,但容易产生短而厚的切屑。
外圆车刀的五个基本角度
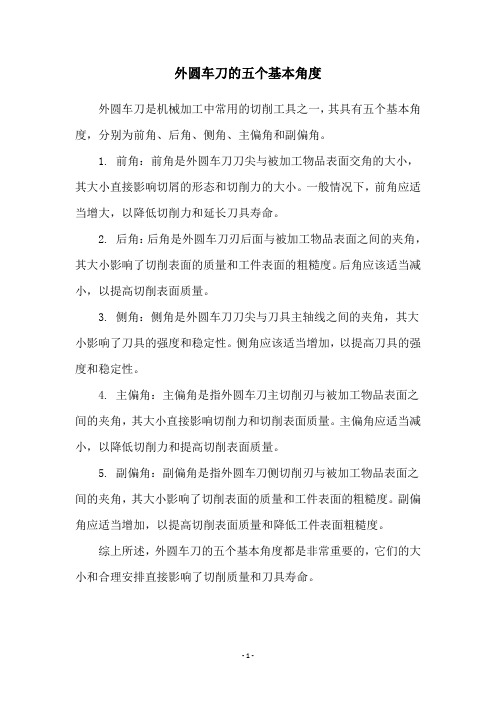
外圆车刀的五个基本角度
外圆车刀是机械加工中常用的切削工具之一,其具有五个基本角度,分别为前角、后角、侧角、主偏角和副偏角。
1. 前角:前角是外圆车刀刀尖与被加工物品表面交角的大小,其大小直接影响切屑的形态和切削力的大小。
一般情况下,前角应适当增大,以降低切削力和延长刀具寿命。
2. 后角:后角是外圆车刀刃后面与被加工物品表面之间的夹角,其大小影响了切削表面的质量和工件表面的粗糙度。
后角应该适当减小,以提高切削表面质量。
3. 侧角:侧角是外圆车刀刀尖与刀具主轴线之间的夹角,其大小影响了刀具的强度和稳定性。
侧角应该适当增加,以提高刀具的强度和稳定性。
4. 主偏角:主偏角是指外圆车刀主切削刃与被加工物品表面之间的夹角,其大小直接影响切削力和切削表面质量。
主偏角应适当减小,以降低切削力和提高切削表面质量。
5. 副偏角:副偏角是指外圆车刀侧切削刃与被加工物品表面之间的夹角,其大小影响了切削表面的质量和工件表面的粗糙度。
副偏角应适当增加,以提高切削表面质量和降低工件表面粗糙度。
综上所述,外圆车刀的五个基本角度都是非常重要的,它们的大小和合理安排直接影响了切削质量和刀具寿命。
- 1 -。
车刀切削部分的四个基本角度
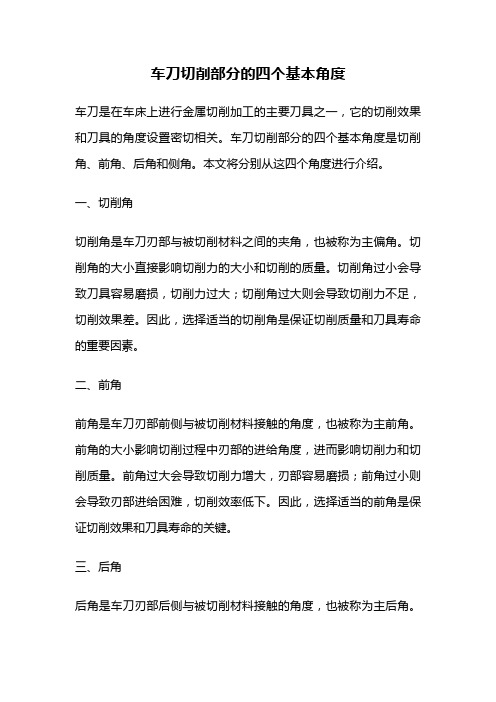
车刀切削部分的四个基本角度车刀是在车床上进行金属切削加工的主要刀具之一,它的切削效果和刀具的角度设置密切相关。
车刀切削部分的四个基本角度是切削角、前角、后角和侧角。
本文将分别从这四个角度进行介绍。
一、切削角切削角是车刀刃部与被切削材料之间的夹角,也被称为主偏角。
切削角的大小直接影响切削力的大小和切削的质量。
切削角过小会导致刀具容易磨损,切削力过大;切削角过大则会导致切削力不足,切削效果差。
因此,选择适当的切削角是保证切削质量和刀具寿命的重要因素。
二、前角前角是车刀刃部前侧与被切削材料接触的角度,也被称为主前角。
前角的大小影响切削过程中刃部的进给角度,进而影响切削力和切削质量。
前角过大会导致切削力增大,刃部容易磨损;前角过小则会导致刃部进给困难,切削效率低下。
因此,选择适当的前角是保证切削效果和刀具寿命的关键。
三、后角后角是车刀刃部后侧与被切削材料接触的角度,也被称为主后角。
后角的大小影响切削过程中刃部的切削深度,进而影响切削力和切削质量。
后角过大会导致切削力增大,刃部容易磨损;后角过小则会导致刃部切削深度不足,切削效果差。
因此,选择适当的后角是保证切削效果和刀具寿命的关键。
四、侧角侧角是车刀刃部侧面与被切削材料接触的角度,也被称为主侧角。
侧角的大小影响切削过程中的切削力和切削质量。
侧角过大会导致切削力增大,刀具容易破碎;侧角过小则会导致切削力不足,切削效率低下。
因此,选择适当的侧角是保证切削质量和刀具寿命的关键。
总结车刀切削部分的四个基本角度,即切削角、前角、后角和侧角,是影响车刀切削效果和刀具寿命的重要因素。
选择适当的角度可以保证切削质量和刀具寿命,同时减少切削力和提高切削效率。
因此,在进行车刀切削加工时,需要根据被切削材料的性质和切削要求来合理设置这四个角度,以获得最佳的切削效果。
- 1、下载文档前请自行甄别文档内容的完整性,平台不提供额外的编辑、内容补充、找答案等附加服务。
- 2、"仅部分预览"的文档,不可在线预览部分如存在完整性等问题,可反馈申请退款(可完整预览的文档不适用该条件!)。
- 3、如文档侵犯您的权益,请联系客服反馈,我们会尽快为您处理(人工客服工作时间:9:00-18:30)。
的几何角度,创造生动的情境,增强直观的推理能力。
价值情感:
培养学生的分析能力、解决问题的能力及口头表达的能力。
重点难点
1、教学重点:车刀切削部分的几何要素和七个主要角度 的定义与标注。
2、教学难点:确定车刀角度的三个基准坐标平面和刃倾角。
复习导入
1、对刀具切削部分材料的基本要求? 硬度高、耐磨性好、耐热性好、有足够的强度与韧性、
车刀的主要角度
教学 目标
重点 难点
复习 导入
讲解 新课
巩固 练习
回顾 反思
布置 作业
知识与能力:
教学目标
ห้องสมุดไป่ตู้
1、了解车刀的组成,熟悉车刀切削部分“三面、二刃、一刀尖” 2、理解测量车刀角度的三个辅助平面的定义; 3、理解并掌握车刀的七个主要角度,初步了解它们在切削中的
作用。
过程与方法: 通过“行为引导型教学法” 运用多媒体并结合演示教具分析车
主后刀面:与正在切削的表面相对的面;
副后刀面:与已加工表面相对的面。
②二刃: 主切削刃:前刀面与主后刀面相交的部位; 副切削刃:前刀面与副后刀面相交的部位。
③一刀尖: 刀尖:主切削刃与副切削刃相交的部位。
3、测量车刀角度的三个辅助平面:
演示
①基面( Pr ):通过车刀主切削刃上一选定点并与该点切削 速度 方向垂直的平面;
布置作业
习题册:
1、P11,11~12; 2、P17,3; 3、P18,7。
课件说明
本课件采用:全国中等职业技术学校机械类专用教材 《车工工艺学与技能训练》第一单元课题五车刀组成部 分;中国劳动社会保障出版社。
制作人:
地址:河北省卢龙县职业技术教育中心
2、 在主截面内测量的角度:
演示
①主偏角kr:主切削刃在基面内的投影与进给方向之间的夹角;
②副偏角k’r:副切削刃在基面内的投影与进给反方向之间的夹角;
③刀尖角 εr:主、副切削刃在基面内的投影之间的夹角。 注:三者关系为kr+ k’r+ εr=1800
3、 在切削平面内测量的角度: 刃倾角λs:主切削刃与基面之间的夹角 。
有良好的工艺性 。
2、常用的刀具材料有哪两大类? 高速刚和硬质合金。高速钢工艺性好、韧性好能承受
较大的冲击,但耐热性差;硬质合金高硬度,耐磨耐热性 好,但韧性差 。
车刀切削部分的定义
1 、车刀的组成: 刀体和刀杆
①刀体:承担切削
②刀杆:装夹
演示
2、刀头部分的组成
前刀面:切屑流出经过的表面 ; ①三面:
②切削平面( Ps ):过车刀主切削刃上一选定点并与加工 表面相切的平面;
③截面( Po ):垂直与过改点的切削平面与基面的平面。
注:三者关系是互相垂直。
车刀的主要角度
1、 在主截面内测量的角度: ①前角γ0:前刀面与基面之间的夹角; ②后角α0 :后刀面与切削平面之间的夹角; ③契角β0:前后刀面之间的夹角。 注:三者关系为γ0+α0 + β0=900
巩固练习
1、请你说出下面弯头车刀的组成 3、主切削刃与基面之间的夹
角叫(
)。
4、基面、切削平面和截面 三者之间的关系是什么?
2、前刀面与基面之间的夹角
叫(
)。
5、前角、主后角和楔角之 间的关系。
6、主、副偏角和刀尖角 之的关系。
刀头 前面
副切削刃 副后面
刀杆
主切削 刃 刀尖
主后面
主剖面Po: ⊥ Ps ⊥ Pr
切削平面 Ps: 与 S相切 且 ⊥Pr
主切削 刃上选 定点
假定主运动方向Vc
基面Pr: Pr⊥Vc ∥刀具安装面(车刀)
主剖面参考系(Pr-Ps-Po)
回顾反思
1、以750外圆车刀为例,其切削部分由哪些内容组成? 2、量取车刀角度需哪三个基准坐标平面;它们之间有 什么关系? 3、车刀主要角度有哪些?且各在哪个基准内测量的?