促进砂状氧化铝生产的工艺措施
砂状氧化铝简介

砂状氧化铝简介砂状氧化铝简介⼀、我国氧化铝⼯业⽬前的状况⼆、我⼚研究开发⽣产砂状氧化铝的迫切性和重要意义三、砂状氧化铝的⾏业标准(什么才是真正意义上的砂状氧化铝)四、我⼚⽬前搞砂状氧化铝所⾯临的困难及所能采取的措施五、氧化铝⼆⼚的两段法砂状氧化铝⼯艺六、附聚作⽤在砂状⼯艺中的作⽤(在砂状⼯艺中为什么要设置⼀个⼀段分解过程)七、如何更好地发挥分级机在砂状氧化铝⽣产中的作⽤⼀、我国氧化铝⼯业⽬前的状况1、我国的铝⼟矿资源状况铝在地壳中的平均含量为8.7%折成氧化铝为16.4%,仅次于氧和硅,⽽居第三位,在⾦属元素中居第⼀。
铝⼟矿是⽬前⽣产氧化铝的最主要的矿⽯资源(但并不是唯⼀的),世界99.0%以上的氧化铝是⽤铝⼟矿为原料⽣产的,铝⼟矿中氧化铝的含量变化很⼤,低的在40%,⾼的可达到70%,我国的铝⼟矿中氧化铝的含量⼤约在50~~60%之间,与其它有⾊⾦属矿⽯相⽐,铝⼟矿可算是很富的矿。
就全球范围来讲铝⼟矿资源丰富,资源保证程度很⾼,按世界铝⼟矿产量1.5亿吨/年计算,静态的保证年限在200年以上,2002年世界上探明的铝⼟矿储量约为250亿吨,储量基础为340亿吨。
主要分布在南美洲(33%)⾮洲(27%)亚洲(17%)⼤洋州(13%)和其它地区(10%)。
其中⼏内亚、澳⼤利亚两国的储量约占世界储量的⼀半,南美的巴西、⽛买加、圭(gui)亚那、苏⾥南约占世界储量的1/4,据近年的报道,越南和印度也有丰富的铝⼟矿资源,越南的储量在40~~50亿吨,印度储量为24亿吨。
世界主要的铝⼟矿产出国为:澳⼤利亚、⼏内亚、巴西、⽛买加等,产量约占全球产量的70%。
我国的铝⼟矿资源并不⼗分丰富,我国的铝⼟矿资源只占世界储量的 1.5%,世界铝⼟矿的⼈均储量为4000kg,⽽我国只有283kg,有资料显⽰我国45种主要矿产对2010年需求的保证程度,有10种矿产是不能保证的,其中包括铝⼟矿,按照⽬前氧化铝产量的增长速度和铝⼟矿开采中的浪费,即使考虑到远景储量,我国铝⼟矿的保证年限也很难达到50年,所以应积极进⾏我国铝⼟矿资源的勘探并合理的开采和利⽤现有的铝⼟矿资源,以此来保证我国氧化铝⼯业的可持续发展。
对我国砂状氧化铝生产技术的初步探讨
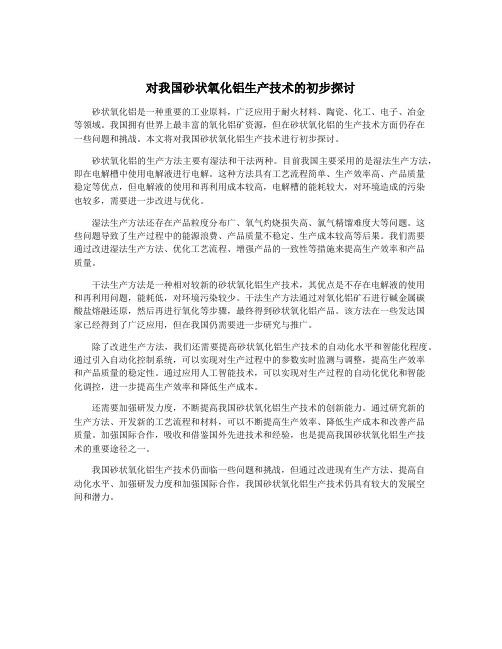
对我国砂状氧化铝生产技术的初步探讨砂状氧化铝是一种重要的工业原料,广泛应用于耐火材料、陶瓷、化工、电子、冶金等领域。
我国拥有世界上最丰富的氧化铝矿资源,但在砂状氧化铝的生产技术方面仍存在一些问题和挑战。
本文将对我国砂状氧化铝生产技术进行初步探讨。
砂状氧化铝的生产方法主要有湿法和干法两种。
目前我国主要采用的是湿法生产方法,即在电解槽中使用电解液进行电解。
这种方法具有工艺流程简单、生产效率高、产品质量稳定等优点,但电解液的使用和再利用成本较高,电解槽的能耗较大,对环境造成的污染也较多,需要进一步改进与优化。
湿法生产方法还存在产品粒度分布广、氧气灼烧损失高、氯气精馏难度大等问题。
这些问题导致了生产过程中的能源浪费、产品质量不稳定、生产成本较高等后果。
我们需要通过改进湿法生产方法、优化工艺流程、增强产品的一致性等措施来提高生产效率和产品质量。
干法生产方法是一种相对较新的砂状氧化铝生产技术,其优点是不存在电解液的使用和再利用问题,能耗低,对环境污染较少。
干法生产方法通过对氧化铝矿石进行碱金属碳酸盐熔融还原,然后再进行氧化等步骤,最终得到砂状氧化铝产品。
该方法在一些发达国家已经得到了广泛应用,但在我国仍需要进一步研究与推广。
除了改进生产方法,我们还需要提高砂状氧化铝生产技术的自动化水平和智能化程度。
通过引入自动化控制系统,可以实现对生产过程中的参数实时监测与调整,提高生产效率和产品质量的稳定性。
通过应用人工智能技术,可以实现对生产过程的自动化优化和智能化调控,进一步提高生产效率和降低生产成本。
还需要加强研发力度,不断提高我国砂状氧化铝生产技术的创新能力。
通过研究新的生产方法、开发新的工艺流程和材料,可以不断提高生产效率、降低生产成本和改善产品质量。
加强国际合作,吸收和借鉴国外先进技术和经验,也是提高我国砂状氧化铝生产技术的重要途径之一。
我国砂状氧化铝生产技术仍面临一些问题和挑战,但通过改进现有生产方法、提高自动化水平、加强研发力度和加强国际合作,我国砂状氧化铝生产技术仍具有较大的发展空间和潜力。
氧化铝工艺流程
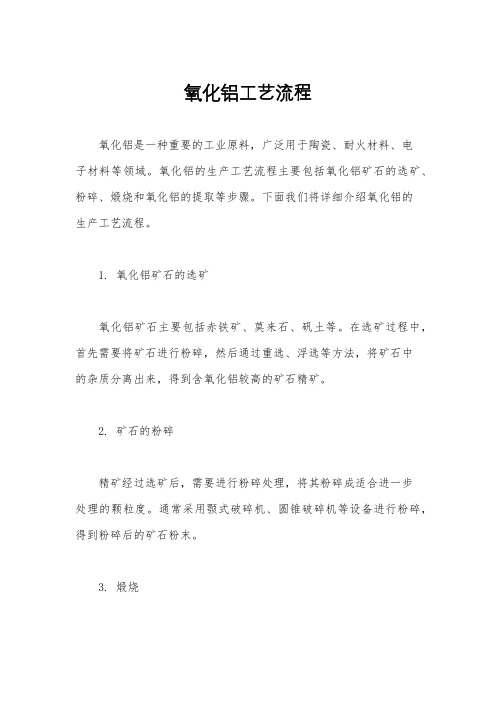
氧化铝工艺流程氧化铝是一种重要的工业原料,广泛用于陶瓷、耐火材料、电子材料等领域。
氧化铝的生产工艺流程主要包括氧化铝矿石的选矿、粉碎、煅烧和氧化铝的提取等步骤。
下面我们将详细介绍氧化铝的生产工艺流程。
1. 氧化铝矿石的选矿氧化铝矿石主要包括赤铁矿、莫来石、矾土等。
在选矿过程中,首先需要将矿石进行粉碎,然后通过重选、浮选等方法,将矿石中的杂质分离出来,得到含氧化铝较高的矿石精矿。
2. 矿石的粉碎精矿经过选矿后,需要进行粉碎处理,将其粉碎成适合进一步处理的颗粒度。
通常采用颚式破碎机、圆锥破碎机等设备进行粉碎,得到粉碎后的矿石粉末。
3. 煅烧粉碎后的矿石粉末需要进行煅烧处理,将其转化为氧化铝。
煅烧是将矿石在高温下进行热处理,使其发生化学变化,生成氧化铝。
煅烧的温度通常在1000℃以上,需要根据矿石的性质和工艺要求进行调控。
4. 溶解经过煅烧处理后的氧化铝粉末需要进行溶解处理,将其溶解于氢氧化钠溶液中,生成氢氧化铝溶液。
溶解的过程需要在一定的温度和压力条件下进行,通常采用高温高压釜进行溶解处理。
5. 晶化溶解后的氢氧化铝溶液需要进行晶化处理,将其中的杂质去除,得到纯净的氢氧化铝晶体。
晶化的过程通常通过降温结晶的方式进行,控制晶化条件可以得到不同形态和大小的氢氧化铝晶体。
6. 煅烧晶化后的氢氧化铝晶体需要进行再次煅烧处理,将其转化为氧化铝。
煅烧的温度和时间需要根据晶体的性质和工艺要求进行控制,通常在1200℃以上进行煅烧处理。
7. 氧化铝的提取经过煅烧处理后的氧化铝晶体可以通过化学方法进行提取,得到纯净的氧化铝产品。
提取的过程通常采用酸碱法或氧化法进行,将氢氧化铝溶解或氧化成氧化铝,然后经过过滤、干燥等步骤得到成品氧化铝。
以上就是氧化铝的生产工艺流程,通过选矿、粉碎、煅烧和提取等步骤,可以将氧化铝矿石转化为纯净的氧化铝产品。
在生产过程中需要严格控制各个环节的工艺参数,确保产品质量达到标准要求。
希望以上内容能够对氧化铝生产工艺有所帮助。
新型两段分解生产砂状氧化铝的集成工艺配置

108新型两段分解生产砂状氧化铝的集成工艺配置鄢 艳,岳 玲,于水波(东北大学设计研究院(有限公司),辽宁 沈阳 110013)摘 要:随着原材料的价格上涨和人工费用增加,降低生产成本建造节能型氧化铝厂的理念已然成为业内共识。
结合工艺流程走向,充分利用位差缩短以及简化流程进行车间的工艺配置,能达到节省电耗、降低生产成本的目的。
本文基于以上需求阐述了拜耳法氧化铝生产中的一种两段分解新型的工艺集成配置。
关键词:两段分解;利用位差;集成;工艺配置中图分类号:TF821 文献标识码:A 文章编号:11-5004(2019)09-0108-2收稿日期:2019-09作者简介:鄢艳(1981-),女,辽宁沈阳人,本科,高级工程师,研究方向:有色冶金。
氧化铝生产中,针对三水铝石大多采用高温、低碱浓度的二段分解工艺。
二段分解强调氢氧化铝晶粒的附聚和长大过程,附聚就是晶种中的细颗粒相互聚集并黏结在一起形成牢固附聚体的过程,是晶体粒度增大的一个重要手段,它是在范德华力、自黏力、附着力以及毛细管力和物质之间的紧密接触而形成的表面张力等力的共同作用下,微粒物质自发和定向地连接在一起的现象。
其有利条件为:较低的初始MR、中等种子添加量、高种子表面积、高过饱和度。
氢氧化铝晶体的长大,是在晶种表面结晶并沿平面展开,使晶粒直径长大,这是氧化铝从液相到固相传递的唯一机理,是影响分解槽的分解率和产品粒度的关键。
在一定条件下,铝酸钠溶液加种子分解析出氢氧化铝可表现为种子晶体的直径变大。
其有利条件为:适中的种子添加量,高起始过饱和度。
二段分解工艺分为附聚段和长大段,在附聚段添加细种子,在长大段添加粗种子,通过控制各个阶段的温度和固含以及成品、粗细种子分级系统,可以生产出砂状氧化铝。
而砂状氧化铝作为电解铝的原料具有流动性好、飞扬损失低、粉尘量低、比表面积高的优点,市场竞争力强。
1 本系统工艺流程简介本系统的工艺流程如下:通过向细种子过滤机抽吸和反吹进行过滤,通入部分冷精液冲稀卸下的滤饼,两者混合后,连同一部分短路热精液,进入附聚段首槽,附聚完成后通过分解溜槽进入长大段首槽;通过向粗种子过滤机抽吸和反吹进行过滤,通入部分冷精液冲稀卸下的滤饼,两者混合后,同时进入长大段首槽;混合料浆经过各级长大槽配合中间降温系统进行分解,分解完成后经长大段倒数第二槽出料经泵部分出料进入成品旋流器组,旋流器组的底流进入成品过滤车间,溢流和剩余分解出料由长大段倒数第一槽进入种子分级旋流器组;种子旋流器组的溢流通过细晶种沉降槽去细种子过滤机,底流去粗种子过滤机。
对我国砂状氧化铝生产技术的初步探讨
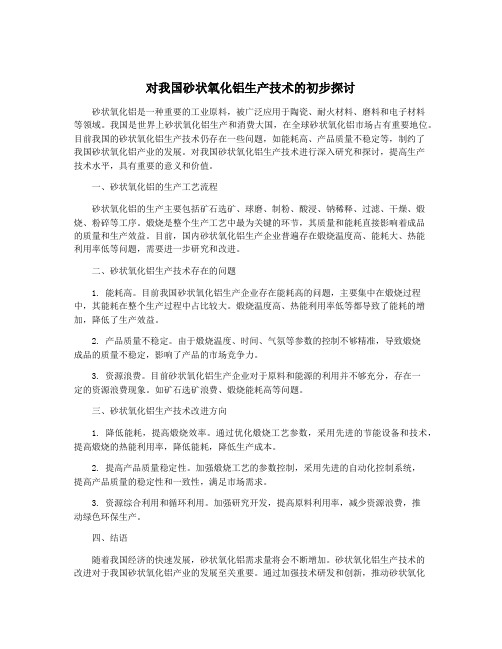
对我国砂状氧化铝生产技术的初步探讨砂状氧化铝是一种重要的工业原料,被广泛应用于陶瓷、耐火材料、磨料和电子材料等领域。
我国是世界上砂状氧化铝生产和消费大国,在全球砂状氧化铝市场占有重要地位。
目前我国的砂状氧化铝生产技术仍存在一些问题,如能耗高、产品质量不稳定等,制约了我国砂状氧化铝产业的发展。
对我国砂状氧化铝生产技术进行深入研究和探讨,提高生产技术水平,具有重要的意义和价值。
一、砂状氧化铝的生产工艺流程砂状氧化铝的生产主要包括矿石选矿、球磨、制粉、酸浸、钠稀释、过滤、干燥、煅烧、粉碎等工序。
煅烧是整个生产工艺中最为关键的环节,其质量和能耗直接影响着成品的质量和生产效益。
目前,国内砂状氧化铝生产企业普遍存在煅烧温度高、能耗大、热能利用率低等问题,需要进一步研究和改进。
二、砂状氧化铝生产技术存在的问题1. 能耗高。
目前我国砂状氧化铝生产企业存在能耗高的问题,主要集中在煅烧过程中,其能耗在整个生产过程中占比较大。
煅烧温度高、热能利用率低等都导致了能耗的增加,降低了生产效益。
2. 产品质量不稳定。
由于煅烧温度、时间、气氛等参数的控制不够精准,导致煅烧成品的质量不稳定,影响了产品的市场竞争力。
3. 资源浪费。
目前砂状氧化铝生产企业对于原料和能源的利用并不够充分,存在一定的资源浪费现象。
如矿石选矿浪费、煅烧能耗高等问题。
三、砂状氧化铝生产技术改进方向1. 降低能耗,提高煅烧效率。
通过优化煅烧工艺参数,采用先进的节能设备和技术,提高煅烧的热能利用率,降低能耗,降低生产成本。
2. 提高产品质量稳定性。
加强煅烧工艺的参数控制,采用先进的自动化控制系统,提高产品质量的稳定性和一致性,满足市场需求。
3. 资源综合利用和循环利用。
加强研究开发,提高原料利用率,减少资源浪费,推动绿色环保生产。
四、结语随着我国经济的快速发展,砂状氧化铝需求量将会不断增加。
砂状氧化铝生产技术的改进对于我国砂状氧化铝产业的发展至关重要。
通过加强技术研发和创新,推动砂状氧化铝生产技术的持续改进和提高,将为我国砂状氧化铝产业的发展注入新的动力,提升企业竞争力,实现可持续发展。
氧化铝生产工艺教学(拜耳法)

煅烧目的:是在一定温度下把氢氧化铝的附着水和结合水脱除,
并发生分解反应,形成氧化铝,再进行晶型转变,得到具有一定物理 和化学性能的氧化铝产品。
煅烧产品的质量指标:化学纯度、灼减、а-Al2O3含量、粒度、
安息角等。
煅烧过程的技术经济指标:煅烧温度、燃料消耗量、产量等。
第五章 铝土矿中氧化铝的溶出
铝土矿溶出动力学 一水硬铝石型铝土矿
V K C N K C N K (C N C A / K E )
K+—正反应的速率常数 K-—逆反应的速率常数 KE—铝土矿溶出反应的平衡常数 CA—AlO2-浓度 CN—OH-浓度
流体反应物在固体表面的吸附 在固体表面上发生的化学反应 流体产物由固体表面上的解吸,并通过固体产物层向流体的扩散 反应的控制步骤:由最慢的步 骤决定着整个反应过程的速度
流体反应物在主流体中通过固体颗粒表面的扩散层的传质
铝土矿的溶出过程:铝土矿与碱液的反应属于复杂的液-固多相反应
含氧化铝矿物的表面被含大量游离NaOH的循环母液所浸润 含氧化铝矿物与OH-相互作用生成铝酸钠 铝酸根离子通过在矿物表面上生成的扩散层扩散到整个溶液中 去,而OH-通过扩散层扩散到矿物的表面上来,使反应继续下去
氢氧化铝的分离与洗涤
分离目的:经种子分解或碳酸化分解得到的氢氧化铝浆液,用过
滤设备将氢氧化铝和母液分离,分离得到的氢氧化铝一部分直接返回 生产流程,作种子分解的晶种,其余部分经进一步洗涤生产氢氧化铝 成品。
洗涤目的:氢氧化铝浆液经分离所得的氢氧化铝滤饼仍含有一定
量的分解母液,必须加以洗涤,以回收Na2O和Al2O3,并保证氢氧化 铝产品中Na2O含量符合质量标准要求。
铝土矿类型 三水铝石 一水软铝石 一水硬铝石 温度(℃) 145 230 250 Na2O(g/L) 110 110 120 Al2O3(g/L) 130 120 120 分子比MR 1.40 1.50 1.65
氧化铝工艺控制方案

氧化铝工艺控制方案一.工艺简介氧化铝的生产工艺,是用碱来处理铝矿石,使矿石中的氧化铝转变成铝酸钠溶液。
矿石中的铁、钛等杂质和绝大部分的硅则成为不溶解的化合物,将不溶解的残渣与溶液分离,经洗涤后弃去或综合利用,以回收其中的有用组分。
纯净的铝酸钠溶液分解析出氢氧化铝,经与母液分离、洗涤后进行焙烧,得到氧化铝产品。
分解母液可循环使用,处理另外一批矿石。
整个生产工艺分为8个工段:原料磨、溶出、赤泥沉降、控制过滤、分解分级、蒸发、成品过滤、焙烧。
下面从这八个工段分别介绍。
二.原料磨在原料磨工段,铝土矿、石灰及循环母液按比例加入棒磨和球磨机中磨制原矿浆,原矿浆由水力旋流器进行分级,分级机溢流为合格的原矿浆,送入原矿浆槽,再用矿浆泵送往溶出车间的常压脱硅工段。
三.溶出从原料车间送来的原矿浆进入常压脱硅工段的加热槽中,采用蒸汽加热,将矿浆温度控制在100℃~110℃,然后送入脱硅槽中进行连续脱硅。
在脱硅槽的末槽用母液调整经脱硅后的原矿浆RP和温度。
合格原矿浆送至高压泵房的隔膜泵,脱硅机理底部设有返砂管、返砂泵,每班定期将粗砂返回原料磨工段。
用隔膜泵将原矿浆送往溶出工段的套管预热器,由六级套管加热器将原矿浆温度预热至174~180℃,而后采用高压新蒸汽间接加热,原矿浆加热至260℃,保温停留60分钟。
溶出后料浆经十级闪蒸,温度从260℃降至125℃,然后送入稀释槽。
从赤泥洗涤送来的赤泥洗液同时加入稀释槽中,稀释料浆用泵送往溶出后槽,停留守4小时以上,以脱除溶液中的硅、铁、锌等杂质。
四.赤泥沉降从溶出后槽送来的稀释料浆与从絮凝剂制备工段来的絮凝剂一同进入分离沉降槽中,分离沉降槽底流含固量约38%~42%,用泵送往洗涤沉降槽,采用四次反向洗涤,洗水从末槽加入,末次洗涤底流固体含量约46%~54%,拟用高压隔膜泵送往赤泥堆场堆存。
五.控制过滤分离沉降槽溢流送控制过滤工段的粗液槽,控制过滤采用立式叶滤机,同时将少量石灰乳加进粗液槽中作为助滤剂,叶滤得到的精液送分解车间的精液板式热交换工段,叶滤渣进滤渣槽中,用泵送回一洗沉降槽。
氧化铝生产工艺

氧化铝生产工艺氧化铝是一种广泛应用的重要非金属材料,具有高熔点、高硬度、耐酸碱腐蚀等特点,在工业生产中有着重要的作用。
氧化铝的生产工艺包括矿石选矿、矿石破碎、矿石浸出、过滤、溶液纯化、氧化、沉淀、过滤、洗涤、干燥等多个环节。
首先,在氧化铝的生产过程中,要选取合适的矿石作为原料。
常用的氧化铝矿石有硬铝石、泡沫铝石等。
选矿过程中,需要进行矿石的破碎和磨矿操作,将矿石分解成适合生产的颗粒大小。
接下来,经过破碎后的矿石进行浸出处理。
将矿石放入酸性浸出液中,通过化学反应将氧化铝从矿石中溶解出来。
浸出过程中,需要控制浸出液的温度、浸出时间和浸出液的酸碱度等参数,以保证氧化铝的溶解率和纯度。
在浸出过程中,得到的氧化铝溶液需要进行过滤,将固体杂质分离出来。
过滤后的溶液进一步进行纯化处理,去除其中的杂质和铝矾土。
随后,对纯化后的氧化铝溶液进行氧化处理。
将溶液导入反应器,在一定的温度和压力下,氧气与铝离子发生氧化反应,生成氧化铝颗粒。
氧化反应过程中,要控制反应温度和氧气的流量等,以使氧化铝颗粒具有所需的形貌和粒径。
氧化反应完成后,需要将生成的氧化铝颗粒进行沉淀。
将反应体系中的氧化铝颗粒沉淀到底部,与溶液分离。
然后,通过过滤等工艺步骤,将沉淀物进行分离和干燥,得到粗氧化铝。
最后,对粗氧化铝进行洗涤和干燥处理,将其中的杂质和水分去除。
洗涤过程中,可以使用水或其他洗涤剂进行清洗,以提高氧化铝的纯度。
干燥过程中,通过加热等方式将氧化铝颗粒中的水分和挥发物去除,以得到最终的氧化铝产品。
综上所述,氧化铝的生产工艺涉及矿石选矿、矿石破碎、矿石浸出、过滤、溶液纯化、氧化、沉淀、过滤、洗涤和干燥等多个环节。
每个环节都需要严格控制操作条件和参数,以保证氧化铝产品的质量和产量。
随着科学技术的不断进步,氧化铝生产工艺也在不断改进和优化,以提高生产效率和降低生产成本。
对我国砂状氧化铝生产技术的初步探讨

对我国砂状氧化铝生产技术的初步探讨砂状氧化铝是一种广泛应用于建筑、陶瓷、电子等领域的重要材料。
我国砂状氧化铝生产技术在经过多年的发展和积累后已初具规模和成熟度。
本文将对我国砂状氧化铝生产技术进行初步探讨。
一、生产工艺砂状氧化铝的生产工艺主要分为两类:碱法和酸法。
碱法生产工艺流程为碱浸、脱硅、脱铝、沉淀、过滤、干燥、粉碎、筛分。
酸法生产工艺流程为硫酸浸、分离、增白、沉淀、过滤、干燥、粉碎、筛分。
二、生产设备砂状氧化铝的生产设备包括碱浸设备、脱硅设备、脱铝设备、沉淀设备、过滤设备、干燥设备、粉碎设备和筛分设备。
不同工艺需要的设备略有区别,但一般都包括以上设备。
三、技术发展趋势随着市场对砂状氧化铝的需求不断增加,我国的砂状氧化铝生产技术也在不断发展。
未来的技术发展趋势主要有以下几个方面:1.提高产品品质砂状氧化铝的品质对于不同领域的应用有不同的要求。
如建筑领域要求产品粘度低,电子领域要求产品粒度均匀等。
因此,提高产品品质是技术发展的必然趋势之一。
2.降低生产成本生产成本的降低对于企业的发展至关重要。
未来的技术发展应当围绕着如何降低原材料和能源的消耗、提高工艺效率等方面展开。
3.发展绿色化生产砂状氧化铝生产过程中会产生致污物质,对环境造成影响。
由此,未来的技术发展应当致力于减少产生的污染物质,降低环境污染。
4.加强信息化管理现代科技的应用,极大地提高了企业管理的效率。
加强信息化管理可以优化生产流程、提高产品品质、降低成本,从而推动企业健康发展。
综上所述,我国砂状氧化铝生产技术已经初具规模和成熟度。
未来的技术发展应当围绕着如何提高产品品质、降低生产成本、发展绿色化生产和加强信息化管理等方面展开。
促进砂状氧化铝生产的工艺措施
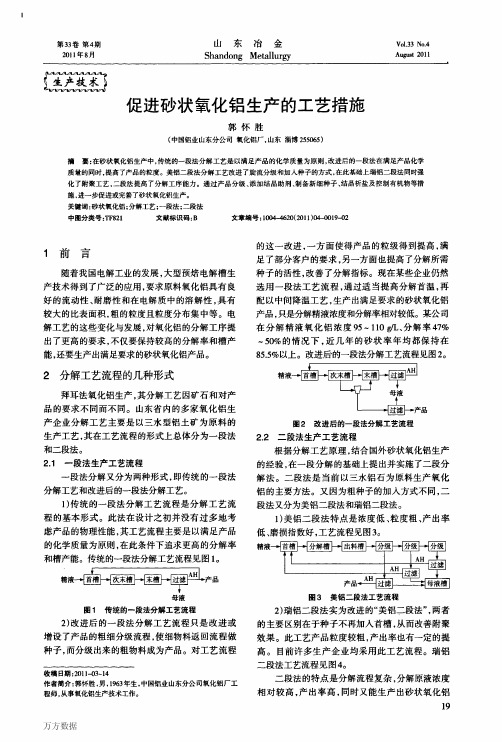
mea8嘲,the
sandy alumina production
promoted
and improved
further.
process;one-step decomposidom two--step decomposition
万方数据
沉降槽蒸发溢流过滤滤饼混合槽烧结法碱液烧结法配料液固分离循环母液制备赤泥分离洗涤系统石灰乳蒸发结晶析盐工艺流程35控制有机物的影响有机物草酸盐等杂质含量对砂状氧化铝的形成及分解率等都有影响
第33卷第4期 2011年8月
山
东
冶
金
V01.33 No.4 August 2011
Shandong
Metallurgy
几个厂家已经开展了不同程度的添加结晶助剂的
试验,并取得了一定的效果。通过进一步摸索和完
善,可以促进分解工艺的改进,对提高产能、满足砂
状氧化铝产品的需求。 3.3制备细种子
时,带动了有机物的排除,取得了较明显的效果。
新沉淀出来的氢氧化铝的活性比经过长期循
环的氢氧化铝的活性大很多;粒度细、比表面积大
4结语
收稿日期:201l-03一14 作者简介:郭怀胜,男。1963年生,中国铝业山东分公司氧化铝厂工 程师。从事氧化铝生产技术工作。
相对较高,产出率高,同时又能生产出砂状氧化铝
19
万方数据
2011年8月
山东冶金
第33卷
精液
Na2C03+Ca(OH)2+aq=2NaOH+CaC03+aq。
由于随原材料的带入和生产过程中对二氧化 碳的吸收,使流程中的碳酸钠不断增加,对分解工
the
decomposition
process.moush
对我国砂状氧化铝生产技术的初步探讨
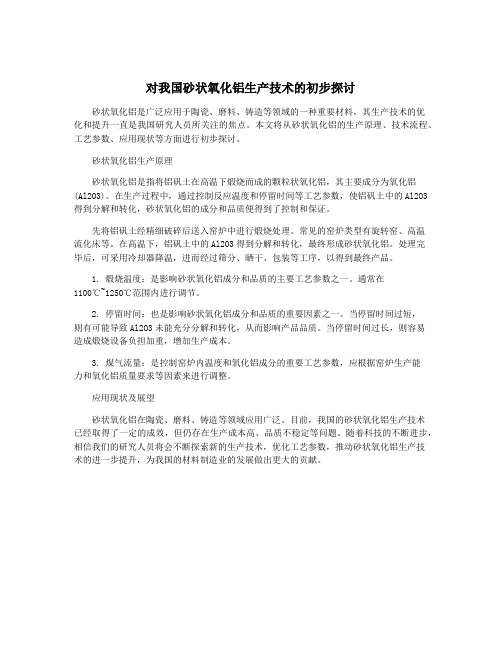
对我国砂状氧化铝生产技术的初步探讨砂状氧化铝是广泛应用于陶瓷、磨料、铸造等领域的一种重要材料,其生产技术的优化和提升一直是我国研究人员所关注的焦点。
本文将从砂状氧化铝的生产原理、技术流程、工艺参数、应用现状等方面进行初步探讨。
砂状氧化铝生产原理砂状氧化铝是指将铝矾土在高温下煅烧而成的颗粒状氧化铝,其主要成分为氧化铝(Al2O3)。
在生产过程中,通过控制反应温度和停留时间等工艺参数,使铝矾土中的Al2O3得到分解和转化,砂状氧化铝的成分和品质便得到了控制和保证。
先将铝矾土经精细破碎后送入窑炉中进行煅烧处理。
常见的窑炉类型有旋转窑、高温流化床等。
在高温下,铝矾土中的Al2O3得到分解和转化,最终形成砂状氧化铝。
处理完毕后,可采用冷却器降温,进而经过筛分、晒干、包装等工序,以得到最终产品。
1. 煅烧温度:是影响砂状氧化铝成分和品质的主要工艺参数之一。
通常在1100℃~1250℃范围内进行调节。
2. 停留时间:也是影响砂状氧化铝成分和品质的重要因素之一。
当停留时间过短,则有可能导致Al2O3未能充分分解和转化,从而影响产品品质。
当停留时间过长,则容易造成煅烧设备负担加重,增加生产成本。
3. 煤气流量:是控制窑炉内温度和氧化铝成分的重要工艺参数,应根据窑炉生产能力和氧化铝质量要求等因素来进行调整。
应用现状及展望砂状氧化铝在陶瓷、磨料、铸造等领域应用广泛。
目前,我国的砂状氧化铝生产技术已经取得了一定的成效,但仍存在生产成本高、品质不稳定等问题。
随着科技的不断进步,相信我们的研究人员将会不断探索新的生产技术,优化工艺参数,推动砂状氧化铝生产技术的进一步提升,为我国的材料制造业的发展做出更大的贡献。
从工艺角度分析如何提高氧化铝产量

目前提高产量和稳定生产的措施工艺技术质量部根据公司近期的生产情况,要提高产量并稳定生产,我部从工艺方面提出目前存在主要问题和解决的措施。
一、问题和措施(1).保证使用矿石的质量。
公司采购部门应加大采购力度,多进一些高品位的矿石;质检部门要加强取样力度,确保取样的代表性和准确性,从而确保使用矿石的氧化铝含量达65%、A/S达7以上。
(2).保证碎矿均化、配料准确和解决堵料问题。
应按要求对碎铝矿进行均化,发挥均化库的作用;准确控制矿石、碱、石灰的配入量,做到配料准确、稳定;定期对原料磨磨头仓进行清理,预防堵矿;严禁矿石、石灰仓内混合使用,避免配料不准确。
这样才能做到配料准确,给溶出创造有利条件。
(3).提高石灰乳氧化钙浓度。
现石灰乳氧化钙浓度为80克/升左右,离设计要求180克/升相差甚远,应控制好消化热水的量,提高石灰乳氧化钙浓度,满足生产要求,减小精液浓度被冲淡的程度。
(4).确保溶出高流量、稳定、连续运行。
溶出应定期对套管结疤进行清理,提高套管的传热效率;充分利用矿浆自蒸发器产生的乏汽,提高预热温度;煤气质量要稳定,煤气产量要充足,确保熔盐炉稳定运行。
(5).保证精液质量,降低赤泥附液损失。
长期以来,精液浮游物指标合格率都较低,产品质量不是很好。
现精液浮游物严重超标,产品中硅、铁含量上升较快,产品质量难以保证,各相关部门应查明原因,采取措施,控制好精液质量以保证产品质量。
赤泥附液损失投产以来一直偏高,近期尤为突出,应控制好沉降槽底流液固比和洗涤热水加入量,降低赤泥附液损失,以减少氧化铝和氧化钠的损失。
(6).蒸发机组蒸发效率低,蒸发母液浓度偏低。
现蒸发原液浓度和温度都偏低,应逐步提高原液浓度,并想办法提高原液温度;蒸发器布膜器结疤严重,影响布膜效果,应加以清理;蒸发器加热管结疤严重,应进行酸洗;新蒸汽压力不稳定,应协调好各用汽车间的用汽情况,确保新蒸汽压力的稳定;要加强对蒸发机组的控制操作,力保操作做到“五稳定”,确保蒸发机组的稳定运行。
氧化铝工艺流程
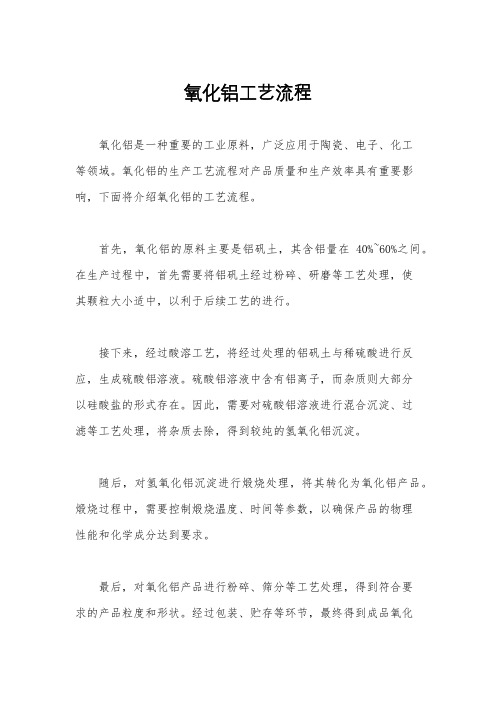
氧化铝工艺流程
氧化铝是一种重要的工业原料,广泛应用于陶瓷、电子、化工
等领域。
氧化铝的生产工艺流程对产品质量和生产效率具有重要影响,下面将介绍氧化铝的工艺流程。
首先,氧化铝的原料主要是铝矾土,其含铝量在40%~60%之间。
在生产过程中,首先需要将铝矾土经过粉碎、研磨等工艺处理,使
其颗粒大小适中,以利于后续工艺的进行。
接下来,经过酸溶工艺,将经过处理的铝矾土与稀硫酸进行反应,生成硫酸铝溶液。
硫酸铝溶液中含有铝离子,而杂质则大部分
以硅酸盐的形式存在。
因此,需要对硫酸铝溶液进行混合沉淀、过
滤等工艺处理,将杂质去除,得到较纯的氢氧化铝沉淀。
随后,对氢氧化铝沉淀进行煅烧处理,将其转化为氧化铝产品。
煅烧过程中,需要控制煅烧温度、时间等参数,以确保产品的物理
性能和化学成分达到要求。
最后,对氧化铝产品进行粉碎、筛分等工艺处理,得到符合要
求的产品粒度和形状。
经过包装、贮存等环节,最终得到成品氧化
铝产品。
总的来说,氧化铝的工艺流程包括原料处理、酸溶、沉淀、煅烧和精制等环节。
在每个环节中,都需要严格控制工艺参数,确保产品质量和生产效率。
同时,不断优化工艺流程,采用先进的设备和技术,也是提高氧化铝生产效率和产品质量的关键。
以上就是氧化铝的工艺流程的介绍,希望对相关行业的从业人员有所帮助,也希望我国的氧化铝工艺能够不断创新,提高产品质量,推动相关产业的发展。
对我国砂状氧化铝生产技术的初步探讨

对我国砂状氧化铝生产技术的初步探讨砂状氧化铝是一种重要的工业原料,广泛用于铝冶炼、耐火材料、制陶、化工等领域。
我国作为世界上最大的砂状氧化铝生产国,其生产技术一直处于全球领先地位。
在近年来,随着我国经济的飞速发展和技术的不断提升,砂状氧化铝生产技术也得到了长足的进步。
本文将对我国砂状氧化铝生产技术进行初步探讨,以期为相关研究和生产提供参考。
砂状氧化铝的主要生产工艺包括赖氏法、碱法和氧化铝硅溶胶-凝胶法等。
赖氏法是目前砂状氧化铝生产中应用最为广泛的工艺,其主要原理是将氢氧化铝通过回流沉淀的方式制得。
这种生产工艺具有生产成本低、生产设备简单、能耗低等优点,但也存在着对原料要求高、废水处理困难等问题。
碱法生产工艺通过使用氢氧化钠来溶解铝石英矿石,然后经过酸化、沉淀等步骤得到氧化铝产品。
这种生产工艺具有成本低、原料适应性强的优点,但也存在着生产过程中废弃物排放多、操作条件苛刻等问题。
氧化铝硅溶胶-凝胶法是一种新兴的砂状氧化铝生产工艺,其主要原理是通过硅铝溶胶的酸性或碱性水解作用形成凝胶,然后通过烘干、焙烧等步骤得到氧化铝产品。
这种生产工艺具有生产过程简单、产品质量高等优点,但也存在着生产设备复杂、能耗高等问题。
砂状氧化铝的生产过程中存在着一些问题需要解决。
首先是原料质量波动大。
砂状氧化铝的主要原料是氢氧化铝,而氢氧化铝的质量波动会直接影响到砂状氧化铝产品的质量。
其次是废水处理难题。
砂状氧化铝的生产过程中会产生大量的废水,其中含有大量的氢氧化钠、铝碱渣等有毒有害物质,如不得当处理会对环境造成严重污染。
展望未来,我国砂状氧化铝生产技术还有很大的提升空间。
在原料部分,可以通过技术创新和工艺改进,实现氢氧化铝的生产和利用效率的提高,降低生产成本,推进绿色生产。
在废水处理部分,可以加强废水处理设施建设,引进国外先进废水处理技术,实现废水零排放,保护环境。
在生产工艺部分,可以通过研发新型生产工艺,提高生产效率,优化产品结构,满足不同领域对砂状氧化铝产品的需求。
氧化铝生产工艺

氧化铝生产工艺氧化铝是一种重要的工业原材料,在许多行业中都有广泛的应用。
它通常通过氧化铝生产工艺来制备,以下是氧化铝的生产工艺的简要介绍。
氧化铝生产工艺主要包括矿石提取、粉煤灰制备、氧化铝制备和精细处理四个主要步骤。
首先,矿石提取是氧化铝生产的第一步。
氧化铝的主要矿石有脱水铝土矿和熔融铝土矿。
脱水铝土矿经过开采、破碎和磨粉等处理,得到的矿石经过采矿车运输到选矿场,在选矿场经过一系列的工艺,如洗选、磁选、重选等,将矿石中的杂质除去,得到纯度较高的氧化铝矿石。
其次,粉煤灰制备是氧化铝生产的重要步骤之一。
煤矸石是煤炭生产过程中产生的废弃物,经过粉碎、分级等工艺处理,得到粉煤灰。
粉煤灰中含有丰富的氧化铝资源,可以作为氧化铝生产的原料。
接下来,氧化铝制备是氧化铝生产的关键步骤。
氧化铝制备主要分为两个过程,即氧化和还原。
首先,将矿石和粉煤灰按一定比例混合,并加入一定量的石灰石作为催化剂。
然后,将混合物放入氧化反应釜中,在高温下进行氧化反应。
氧化反应使矿石中的氧化铝与其他金属氧化物分离,并生成氧化铝产物。
接着,将产物经过洗涤、沉淀和干燥等工艺处理,得到纯度较高的氧化铝。
最后,精细处理是氧化铝生产的最后一个步骤。
精细处理主要是对氧化铝的粒度、物理性质和化学性质进行调整,以满足不同行业的需求。
精细处理的方法包括研磨、筛分、分类、电磁分选等工艺。
总的来说,氧化铝的生产工艺包括矿石提取、粉煤灰制备、氧化铝制备和精细处理四个主要步骤。
通过这些工艺的处理,可以得到纯度较高的氧化铝产品,广泛应用于建筑材料、电子产业、化工等行业中。
随着科技的不断发展,氧化铝生产工艺也在不断改进,以提高产能、降低成本和减少环境污染。
对我国砂状氧化铝生产技术的初步探讨

对我国砂状氧化铝生产技术的初步探讨砂状氧化铝是一种重要的工业原料,广泛应用于陶瓷、建筑材料、热力电站等领域。
由于其在高温、高压等恶劣环境下表现出良好的性能,因此在我国国内生产砂状氧化铝的技术也越来越受关注。
目前,我国砂状氧化铝的生产主要依赖于湿法法生产与干法法生产两种技术路线。
湿法法生产砂状氧化铝是利用水溶性铝矿石,通过浸取、沉淀、分离等工艺步骤来获取氧化铝。
其中较为典型的湿法法生产技术是贝耳法。
该技术主要分为氧化铝工段、还原工段和结晶工段。
在氧化铝工段,将矾石与碱液反应生成氢氧化铝,再通过加热、过滤、洗涤等步骤得到纯度较高的氧化铝尘。
然后将氧化铝尘在还原工段进行还原,得到氧化铝裸晶。
通过结晶工段降温结晶和离心等步骤,得到砂状氧化铝。
贝耳法生产砂状氧化铝技术成熟,工艺稳定,但存在污染环境、能耗高等问题。
干法法生产砂状氧化铝则是利用非水溶性铝矿石,通过矿浆烘干、击碎、筛分等工艺步骤获取氧化铝。
干法法生产技术相对成熟,主要分为闫泰莫夫法和矿浆烘干法两种。
闫泰莫夫法主要经过碳酸氢铵沉淀、高温煅烧等过程来得到粗砂状氧化铝,然后通过破碎、筛分等步骤细化加工,得到砂状氧化铝。
矿浆烘干法则通过将铝矿石研磨成矿浆,利用煤热煅烧脱水,从而实现矿浆中的水分蒸发,进而得到砂状氧化铝。
干法法生产砂状氧化铝的技术相对成熟,但仍存在能耗相对高、对原材料的要求较高等问题。
与国外先进技术相比,我国砂状氧化铝生产技术还存在一些不足之处。
在技术创新方面,国内砂状氧化铝生产企业还需要加大对新材料、新工艺的研究力度,提高产品质量和技术水平。
在环保方面,砂状氧化铝生产过程中产生大量废气、废水和固体废弃物,企业需要加强对废弃物处理和资源化利用的研究,减少对环境的影响。
在能耗方面,目前国内砂状氧化铝生产过程中的能耗较高,需要通过技术改造和工艺优化等方式来降低能耗。
我国砂状氧化铝生产技术有着较为成熟的湿法法和干法法两种技术路线。
随着我国工业发展的不断壮大和技术进步,我国砂状氧化铝生产技术的研究将变得更加重要,在节能减排、提高产品质量和技术水平等方面进行进一步的探索,以满足国内需求并提高国际竞争力。
生产砂状氧化铝的工艺条件.
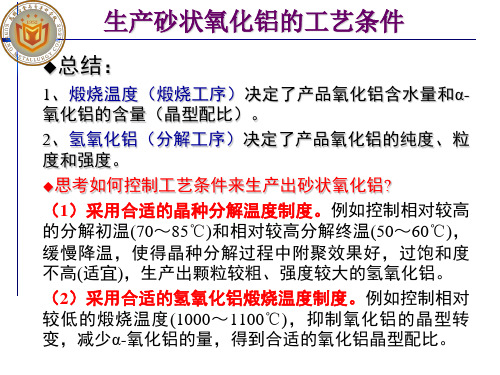
氧化铝生产工艺

1 我国氧化铝工业现状我国铝土矿资源居世界第六位,储量仅占世界总量的2.4%,但具有经济意义可开采利用的储量只占查明资源储量的21.5%,资源保障程度有限,是铝土矿资源相对缺乏的国家。
铝土矿资源主要分布在山西、广西、贵州和河南四省区,占全国资源储量的90%以上。
大部分地区矿床类型以沉积型为主,适于露天开采的矿量占总量的38%,坑采储量约占总储量的60%以上,年开采量占世界开采总量的8%。
国外铝土矿多为铝硅比高的三水铝石和一水软铝石,而我国铝土矿资源可经济应用的大部分是高铝、高硅、低铁、难溶(铝硅比较低)的中低品位的一水硬铝石。
沉积型一水硬铝石占全国铝土矿资源总量的98%以上,与国外应用的铝土矿相比,其提取氧化铝的难度大,磨矿及溶出条件苛刻,工艺能耗及生产成本较高。
三水型铝土矿占全国总量的不足1%,且由于品位低、规模小、生产工艺不成熟,尚不具备工业意义。
1.1 氧化铝生产工艺世界上氧化铝的生产主要是碱法,包括三种不同方法,即拜耳法、烧结法和联合法,工艺技术方法应用主要依据铝矿石的质量。
拜耳法是利用较高品位的铝矿石,与碱液、石灰乳及母液按比例混合后磨制成料浆,经预脱硅后在相应温度、压力条件下直接溶出铝酸钠,再经赤泥分离、种子分解和氢氧化铝焙烧等工序制得成品氧化铝。
对于铝硅比大于7的高品位矿石,以拜耳法生产工艺为首选,其能耗低、投资省、产品质量好且污染物产生量少,属于氧化铝工业清洁生产工艺。
烧结法是将铝土矿破碎后与石灰、纯碱、无烟煤及返回母液按比例混合,磨成生料浆,喷入烧成窑制成熟料,再经熟料溶出、赤泥分离、铝酸钠分解和氢氧化铝焙烧等工序,制得成品氧化铝。
该工艺流程长、能耗高、污染物产生量大,但其最大优点是可利用低品位铝土矿,符合我国铝土矿资源的特点。
联合法是将拜耳法和烧结法联合起来,处理铝硅比3~7的矿石,充分发挥各自的长处,联合法有并联、串联以及混联三种基本流程。
混联法是将高品位矿石采用拜耳法处理,拜耳法赤泥与低品位的矿石一起进入烧结法生产系统。
氧化铝生产工艺简介

氧化铝性质、 氧化铝性质、用途
一、通性
名称 :氧化铝 刚玉 白玉 红宝石 蓝宝石 刚玉粉。 氧化铝;刚玉 白玉;红宝石 蓝宝石;刚玉粉 刚玉;白玉 红宝石;蓝宝石 刚玉粉。 分子量102,白色无定形粉状物,属原子晶体,成键为共价 ,白色无定形粉状物,属原子晶体 成键为共价 分子量 熔点为2050℃,沸点为 键,熔点为 熔点为 ℃ 沸点为3000℃,真密度 3.97 g/cm3 松 ℃ 装密度:0.85g/mL(325目~0)0.9g/mL(120目~325目)。 装密度: ( 目 ) ( 目 目 流动性好,不溶于水,能溶解在熔融的冰晶石中。 流动性好,不溶于水,能溶解在熔融的冰晶石中。 有四种同素异构体β-; - 有四种同素异构体 -; δ- ; v-; a-氧化铝 ,有α -; - 型和γ型两种变体 型两种变体。 型和 型两种变体。
出料泵
Q=200m3/h
54m3/h
354.76m3/h
186m3/h
356.19m3/h
167.21m3/h
3×80m3/h ×
153.85m3/h 217.3m3/h 63.88m3/h 217.3m3/h
φ10×10m
φ10×20m
360~490m3/h ~
120~165m3/h ~
356.19m3/h
Q=610m3/h
Q=400m3/h
自原料制备
240m3/h
去高压隔膜泵 蒸汽 蒸汽
高位槽 停留12h后出料 后出料 停留
蒸汽
240m3/h
增压泵
预脱硅槽 105℃
240m3/h
φ10.5×32m ×
Q=300m3/h
105℃
240m3/h
105℃
- 1、下载文档前请自行甄别文档内容的完整性,平台不提供额外的编辑、内容补充、找答案等附加服务。
- 2、"仅部分预览"的文档,不可在线预览部分如存在完整性等问题,可反馈申请退款(可完整预览的文档不适用该条件!)。
- 3、如文档侵犯您的权益,请联系客服反馈,我们会尽快为您处理(人工客服工作时间:9:00-18:30)。
2 1年 8 0 1 月
山 东 冶 金
S a d n M eal r y hnog tl g u
V0 _ 3 No4 l3 . Au u t 2 1 g s 01
促进 砂状Байду номын сангаас化铝 生产 的工艺措 施
郭 怀 胜
( 中国铝业 山东分公 司 氧化铝 厂, 山东 淄博 25 6 ) 5 05 摘 要: 在砂状氧化铝 生产中 , 传统 的一 段法分解工艺是 以满足产 品的化 学质量为原则 , 改进后的一段法在满 足产品化学
艺 产生 重要 影 响 , 因此 加强 流 程 中碳 酸碱 的苛 化有 重 要 意 义 。某企 业 对 流 程碳 酸碱 的苛 化 主要 采取
产 企 业 分解 工 艺 主 要 是 以三 水 型 铝 土矿 为 原 料 的
廿H
图 2 改进 后 的 一 段 法 分解 工 艺 流 程
生产 工 艺 , 其在 工 艺流程 的形式 上 总体分 为 一段 法
和二 段法 。 21 一段 法生产 工艺流 程 .
一
22 二段 法生产 工艺流程 -
质量 的同时 , 提高 了产品 的粒度 。美铝 二段法分解工艺改进 了旋 流分级 和加入种子的方式 , 在此基 础上瑞 铝二段法同时强 化 了附聚工艺 , 二段法 提高 了分解 工序能力 。通过产 品分级 、 添加 结晶助 剂 、 制备新 细种子 、 结晶析盐及 控制有机物 等措 施, 进一步促进或完善 了砂状氧化 铝生产 。 关键词 : 砂状 氧化铝 ; 分解工 艺 ; 一段法 ; 二段法
中图分类 号: F 2 T81 文献标识码 : B 文章编 号:0 4 4 2 ( 0 10 —0 9 0 10 — 6 02 1 )4 0 1 — 2
1 前
言
的这 一 改 进 , 方 面 使 得 产 品 的粒 级得 到 提 高 , 一 满 足 了部 分客 户 的要求 , 一方 面也 提 高 了分解 所需 另
根据 分解 工 艺原 理 , 结合 国外 砂状 氧 化铝 生产 的经 验 , 在一 段 分解 的基 础上 提 出并 实施 了二 段分 解 法 。二 段 法 是 当前 以三 水 铝石 为 原 料 生产 氧 化 铝 的主要 方法 。又 因为粗 种子 的加 入方 式 不 同 , 二 段 法又 分为美 铝二段 法和瑞 铝二段 法 。 1美 铝 二 段法 特 点 是 浓 度低 、 度 粗 、 出率 ) 粒 产 低、 磨损指 数好 , 工艺 流程见 图 3 。
精液
段 法分 解 又分 为两 种形 式 , 即传 统 的一 段 法
分 解工 艺和 改进后 的一段法 分解工 艺 。
1传 统 的一 段 法 分解 工 艺 流程 是 分 解 工 艺 流 ) 程 的基 本 形 式 。 此法 在 设 计 之初 并 没 有 过 多 地考 虑 产 品 的物理 性 能 , 工 艺流 程主 要是 以满 足 产 品 其 的化 学质 量 为原则 , 此条 件 下追 求更 高 的分解 率 在 和槽产 能 。传统 的一段 法分解 工艺 流程见 图 1 。
随着 我 国 电解 工业 的发展 , 大型 预焙 电解 槽 生
种子 的活性 , 改善了分解指标 。现在某些企业仍然
选 用 一 段 法 工艺 流程 , 过 适 当提 高分 解 首 温 , 通 再 配 以 中间降温 工艺 , 生产 出满 足要 求 的砂状 氧 化铝 产 品 , 分解精液浓度和分解率相对较低 。某公 司 只是 在 分 解 精 液 氧 化 铝 浓 度 9 ~10g 、 解 率 4 % 5 1 / 分 L 7
增 设 了产 品 的粗 细分 级 流程 , 细物 料返 回流程做 使 种 子 , 分级 出来 的粗物 料成 为 产 品 。对 工 艺流程 而
收稿 日期 :0 1 0 — 4 2 1- 3 1
效果 。此工艺产品粒度较粗 , 产出率也有一定的提 高 。 目前 许 多 生 产企 业 均 采 用 此工 艺 流 程 。瑞 铝
精液
母液
产 品
图 3 美 铝 二 段 法 工 艺 流 程
图 1 传统的一段 法分解工 艺流 程
2瑞 铝 二段 法实 为 改进 的 “ 铝 二段 法 ”两 者 ) 美 , 的 主要 区别 在 于种子 不再 加 入 首槽 , 而 改善 附 聚 从
2 改进后 的一段法分解工艺流程只是改进或 )
~
产技 术得 到 了广 泛 的应用 , 求原 料 氧化 铝具 有 良 要 好 的流 动性 、 磨 性 和 在 电解 质 中 的溶 解 性 , 耐 具有
较大 的 比表 面积 , 的粒 度且 粒度 分 布集 中等 。电 粗 解 工 艺 的这些 变 化与 发展 , 氧化 铝 的分解 工 序提 对
出 了更高 的要 求 , 不仅 要 保持 较高 的分 解率 和 槽产 能, 还要 生产 出满足要 求 的砂 状氧化 铝产 品 。
山 精液
东
冶
金
第3 3卷
N 2O+ a O 2a= N O + a 0+a 。 aC 3C ( H) q 2 a H C c 3 q +
由于 随 原材 料 的带 人 和 生 产 过 程 中对 二 氧化
碳 的吸 收 , 流 程 中的碳 酸 钠 不 断 增 加 , 分 解 工 使 对
图 4 瑞铝二段法工艺流程
二段法工 艺 流程见 图 4 。
作者简 介 : 郭怀胜 , ,9 3 男 16 年生 , 国铝业 山东分公司氧化铝厂 工 中 程师 , 从事氧化铝生产技术工作 。
二 段法 的特点 是分 解 流程 复杂 , 解原 液浓 度 分
相对较高 , 出率高 , 产 同时又能生产 出砂状氧化铝
1 9
5%的情 况 下 , 几 年 的 砂 状 率 年 均 都 保 持 在 0 近
8. 55 %以上 。改进后 的一段 法分解 工艺 流程见 图 2 。
精液
2 分解工 艺流程 的几种形 式
拜耳 法 氧化 铝 生产 , 分解 工 艺 因矿石 和 对产 其 品 的要 求 不 同而 不 同 。山东 省 内 的多 家 氧化 铝 生