汽提精馏脱氨技术方案
汽提精馏法高浓度氨氮废水处理装备使用计划方案
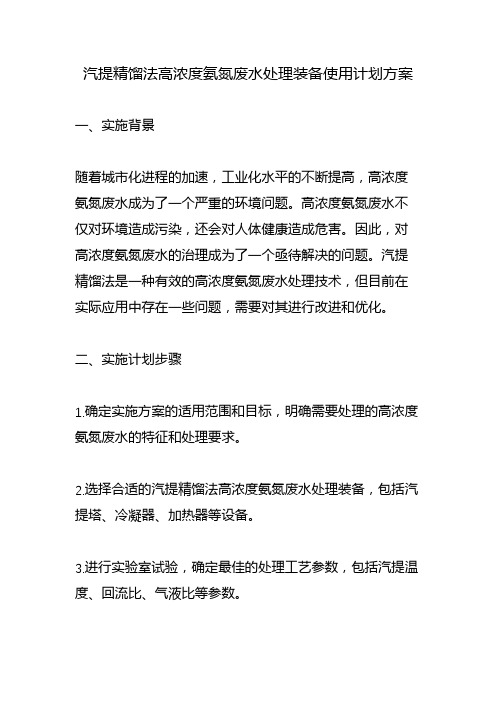
汽提精馏法高浓度氨氮废水处理装备使用计划方案一、实施背景随着城市化进程的加速,工业化水平的不断提高,高浓度氨氮废水成为了一个严重的环境问题。
高浓度氨氮废水不仅对环境造成污染,还会对人体健康造成危害。
因此,对高浓度氨氮废水的治理成为了一个亟待解决的问题。
汽提精馏法是一种有效的高浓度氨氮废水处理技术,但目前在实际应用中存在一些问题,需要对其进行改进和优化。
二、实施计划步骤1.确定实施方案的适用范围和目标,明确需要处理的高浓度氨氮废水的特征和处理要求。
2.选择合适的汽提精馏法高浓度氨氮废水处理装备,包括汽提塔、冷凝器、加热器等设备。
3.进行实验室试验,确定最佳的处理工艺参数,包括汽提温度、回流比、气液比等参数。
4.进行小试、中试和工程试验,验证处理效果和经济效益。
5.根据实验结果和经济效益,确定最终的处理工艺参数和设备配置方案。
6.进行装备采购、安装和调试,确保设备正常运行。
7.对处理效果进行监测和评估,对不足之处进行改进和优化。
三、适用范围汽提精馏法高浓度氨氮废水处理装备适用于高浓度氨氮废水的处理,可以有效地将氨氮浓度降低到国家排放标准以下。
四、创新要点1.采用先进的汽提精馏法技术,能够有效地处理高浓度氨氮废水。
2.通过实验室试验和工程试验,确定最佳的处理工艺参数和设备配置方案,提高处理效果和经济效益。
3.对处理效果进行监测和评估,及时发现不足之处并进行改进和优化。
五、预期效果通过采用汽提精馏法高浓度氨氮废水处理装备,预期能够达到以下效果:1.将高浓度氨氮废水处理成符合国家排放标准的废水。
2.降低氨氮浓度,减少对环境的污染和对人体健康的危害。
3.提高处理效率和经济效益,降低处理成本。
六、达到收益采用汽提精馏法高浓度氨氮废水处理装备,可以达到以下收益:1.减少对环境的污染,保护生态环境。
2.降低氨氮浓度,保障人体健康。
3.提高企业形象和社会责任感。
4.降低处理成本,提高经济效益。
七、优缺点优点:1.采用先进的汽提精馏法技术,能够有效地处理高浓度氨氮废水。
高效节能的高浓度氨氮废水处理成套技术

摘要:本文介绍了多套高浓度氨氮废水处理技术:汽提精馏脱氨成套技术、双效节能汽提脱氨成套技术、蒸汽循环汽提脱氨成套技术、超重力汽提脱氨成套技术。
所开发的高浓度氨氮废水处理技术已经应用于实际的工业废水处理中,为高浓度氨氮废水的处理提供了新型高效的处理技术。
关键词:高浓度氨氮废水;汽提精馏;双效节能;蒸汽循环;超重力技术1、引言当前我国工业企业所排出的废水种类众多,废水总量很大,其中仅氨氮废水一项其氨氮年排放量超过30万吨。
大量的氨氮排放不仅严重污染环境,而且造成巨大资源浪费。
一般情况下,对于低浓度氨氮废水一般可以采用生化处理,其处理费用较低。
但是,对于多数工业企业来说,其氨氮废水中氨氮浓度很高(最高可达几万毫克/升),无法进行生化处理,需要首先对氨氮废水进行脱氨处理。
当前,大部分氨氮废水处理技术是将废水中的氨氮定义为污染物,一般对其采用反应转化方式,即采用去除的方法达到降低废水中氨氮的目的,没有实现氨氮的资源化回收利用。
例如:硝化反硝化法、折点加氯法、反应沉淀法等。
我们在研究开发高浓度氨氮处理技术过程中没有简单地将废水中氨氮定义为污染物,而是将其定义为可回收利用的资源。
实现氨氮废水中氨氮的资源化回收利用,不仅可以实现污染物的减排,同时可以利用所回收的资源补偿一部分废水处理的费用,降低氨氮废水处理综合成本。
鉴于此指导思想,我们在多年废水脱氨技术研究成果及项目实施实践经验的基础上,结合最新研究开发的节能降耗技术及装备研究成果,以效率高、技术成熟度好的蒸汽汽提脱氨技术为基础,针对传统蒸汽汽提废水脱氨技术中存在的蒸汽耗量大(一般为250~300kg/吨废水),废水处理单耗高的难题,采用创新性工艺流程设计、高效脱氨技术及设备、节能降耗技术及设备等,通过研究攻关,开发了适合于多种工况的氨氮废水处理技术,并付诸工业化应用。
现已完成的氨氮废水处理工业化装置已经有十几家,包括外资企业、中石化、国内大型农药企业等。
我们开发的高效节能的高浓度氨氮废水处理成套技术特点如下:(1)脱氨效率高。
某炼厂富氢气体脱氨技术实施及效果
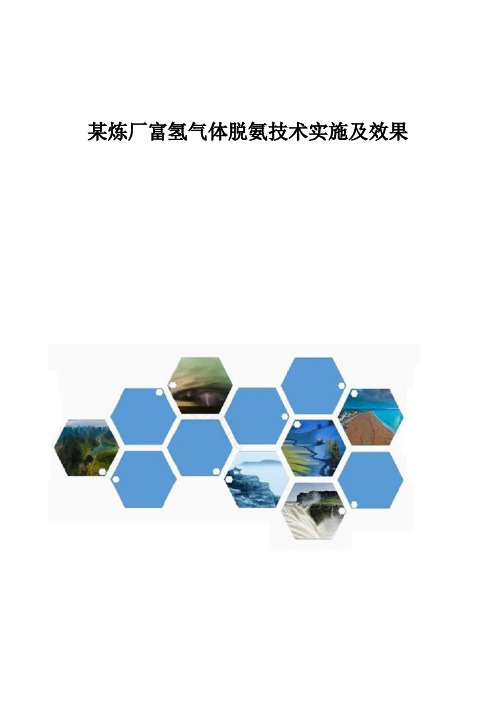
某炼厂富氢气体脱氨技术实施及效果摘要:本文重点介绍了三种常用炼厂富氢气体脱氨技术,对三种脱氨技术进行了比选。
选择炼厂富氢气体脱氨技术时应充分考虑炼厂富氢气体特点与炼化企业自身装置相结合。
重点介绍了水洗氨技术在低浓度含氨炼厂富氢气体脱氨方面具有广泛的优势。
关键词:炼厂富氢气体;脱氨工艺;水洗氨工艺随着社会的发展进步,国家对环保要求越来越高,严格的环保标准实施倒逼炼化企业需要对同时含有氨和硫化氢的燃料气进行脱硫处理,以免影响燃料气燃烧造成烟气二氧化硫化硫排放超标。
另外随着企业对厂内装置挖潜增效的进一步落实,我国炼化企业由粗放式管理改为精细化管理,对过去同时含有氨和硫化氢的高价值气体仅作为燃料烧掉已采取重要措施,对高价值的气体进一步回收。
不管对燃料气进行预处理还是对高价值气体进行回收,都需要将气体中的硫化氢进行脱除,为避免气体中的氨对脱硫工艺的影响,需先将气体中氨进行脱除。
本文以中石化某炼化公司富氢气体预处理项目为例,对炼厂富氢气体脱氨技术进行探讨。
1.气体特点中石化某炼化分公司富氢气体的组成见表1-l。
表1-1 含氨气体组成介质含氨气体流量Nm3/h5150温度℃40压力MPa(G)0.70组份mol%H275.67N20.70CO0.20CO20.00CH413.80C2 4.77C3 1.97C4 1.71C5 1.12C60.00NH30.04H2S0.02合计100.00从表1-1可知,氢气含量较高,摩尔分率高达70%以上,为高价值气体。
如果仅作为燃料烧掉,浪费严重,需要对气体中的氢气通过变压吸附装置进行回收。
另外从表中可知该气体中同时含有氨气和硫化氢,其中氨气高达400ppm。
氨气和硫化氢的存在会影响后续氢气回收工艺,危害氢气吸附剂、压缩机的正常运转。
为免除氨与硫化氢结晶对压缩机造成损害需要预先脱除气体中氨气。
2.炼厂富氢气体脱氨技术目前常用的气体脱氨技术主要为硫铵工艺、无水氨工艺和水洗氨工艺[1]。
汽提脱氨 技术
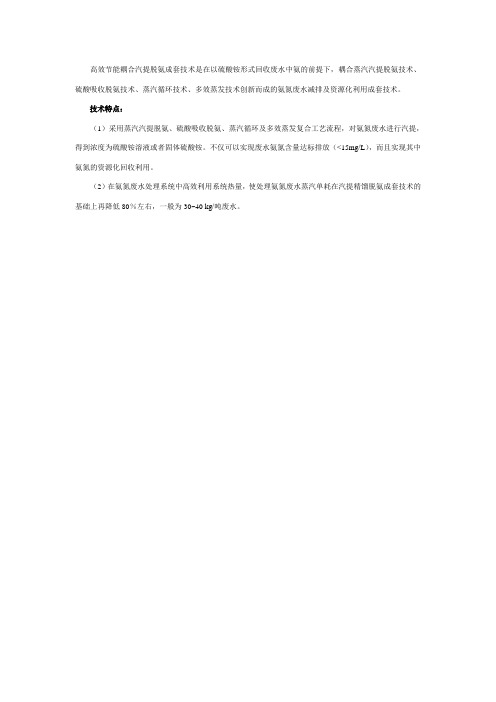
高效节能耦合汽提脱氨成套技术是在以硫酸铵形式回收废水中氨的前提下,耦合蒸汽汽提脱氨技术、硫酸吸收脱氨技术、蒸汽循环技术、多效蒸发技术创新而成的氨氮废水减排及资源化利用成套技术。
技术特点:
(1)采用蒸汽汽提脱氨、硫酸吸收脱氨、蒸汽循环及多效蒸发复合工艺流程,对氨氮废水进行汽提,得到浓度为硫酸铵溶液或者固体硫酸铵。
不仅可以实现废水氨氮含量达标排放(<15mg/L),而且实现其中氨氮的资源化回收利用。
(2)在氨氮废水处理系统中高效利用系统热量,使处理氨氮废水蒸汽单耗在汽提精馏脱氨成套技术的基础上再降低80%左右,一般为30~40 kg/吨废水。
变换气提含氨污水处置方案(上报
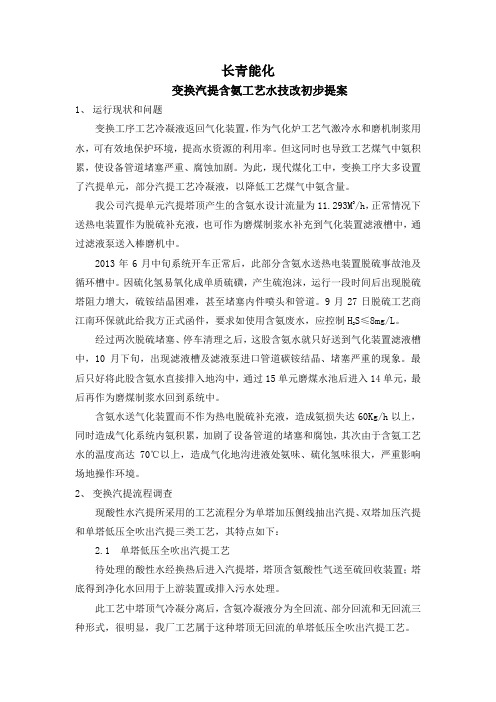
859.87
mol%
24.86%
16.29%
55.48%
0.07%
0.03%
1.86%
0.06%
0.07%
1.30%
100%
Kg/h
250.59
11.731
878.86
0.687
0.157
22.77
1.232
0.946
7.954
42.87
1174.9
1217.8
2111
含氨水
w%
0.00%
我公司汽提单元汽提塔顶产生的含氨水设计流量为11.293M3/h,正常情况下送热电装置作为脱硫补充液,也可作为磨煤制浆水补充到气化装置滤液槽中,通过滤液泵送入棒磨机中。
2013年6月中旬系统开车正常后,此部分含氨水送热电装置脱硫事故池及循环槽中。因硫化氢易氧化成单质硫磺,产生硫泡沫,运行一段时间后出现脱硫塔阻力增大,硫铵结晶困难,甚至堵塞内件喷头和管道。9月27日脱硫工艺商江南环保就此给我方正式函件,要求如使用含氨废水,应控制H2S≤8mg/L。
3、变换汽提运行数据
3.1 设计数据
我公司变换汽提设计数据如下:
物料
平衡点
项目
CO
H2
CO2
N2
CH4
H2S
COS
AR
NH3
H2O
干基
湿基
g/mol
28
2
44
28
16
34
60
40
17
18
2110
汽提尾气
Nm3/h
200.47
131.39
447.42
0.55
0.22
汽提精馏脱氨技术在锂电池材料生产废水中的现代应用
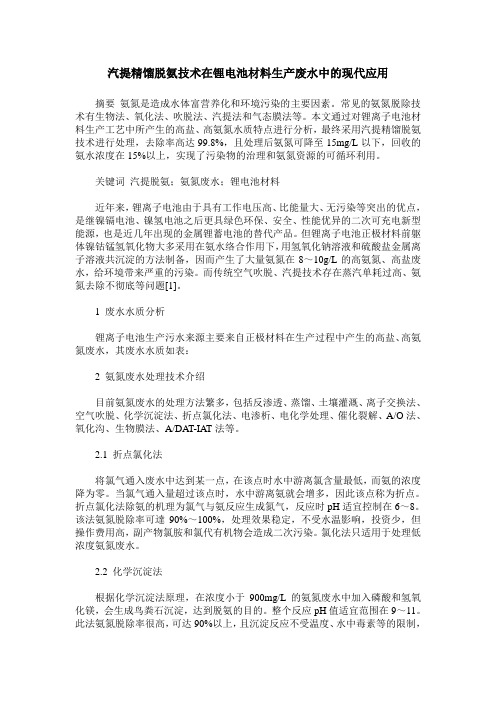
汽提精馏脱氨技术在锂电池材料生产废水中的现代应用摘要氨氮是造成水体富营养化和环境污染的主要因素。
常见的氨氮脱除技术有生物法、氧化法、吹脱法、汽提法和气态膜法等。
本文通过对锂离子电池材料生产工艺中所产生的高盐、高氨氮水质特点进行分析,最终采用汽提精馏脱氨技术进行处理,去除率高达99.8%,且处理后氨氮可降至15mg/L以下,回收的氨水浓度在15%以上,实现了污染物的治理和氨氮资源的可循环利用。
关键词汽提脱氨;氨氮废水;锂电池材料近年来,锂离子电池由于具有工作电压高、比能量大、无污染等突出的优点,是继镍镉电池、镍氢电池之后更具绿色环保、安全、性能优异的二次可充电新型能源,也是近几年出现的金属锂蓄电池的替代产品。
但锂离子电池正极材料前躯体镍钴锰氢氧化物大多采用在氨水络合作用下,用氢氧化钠溶液和硫酸盐金属离子溶液共沉淀的方法制备,因而产生了大量氨氮在8~10g/L的高氨氮、高盐废水,给环境带来严重的污染。
而传统空气吹脱、汽提技术存在蒸汽单耗过高、氨氮去除不彻底等问题[1]。
1 废水水质分析锂离子电池生产污水来源主要来自正极材料在生产过程中产生的高盐、高氨氮废水,其废水水质如表:2 氨氮废水处理技术介绍目前氨氮废水的处理方法繁多,包括反渗透、蒸馏、土壤灌溉、离子交换法、空气吹脱、化学沉淀法、折点氯化法、电渗析、电化学处理、催化裂解、A/O法、氧化沟、生物膜法、A/DAT-IAT法等。
2.1 折点氯化法将氯气通入废水中达到某一点,在该点时水中游离氯含量最低,而氨的浓度降为零。
当氯气通入量超过该点时,水中游离氨就会增多,因此该点称为折点。
折点氯化法除氨的机理为氯气与氨反应生成氮气,反应时pH适宜控制在6~8。
该法氨氮脱除率可達90%~100%,处理效果稳定,不受水温影响,投资少,但操作费用高,副产物氯胺和氯代有机物会造成二次污染。
氯化法只适用于处理低浓度氨氮废水。
2.2 化学沉淀法根据化学沉淀法原理,在浓度小于900mg/L的氨氮废水中加入磷酸和氢氧化镁,会生成鸟粪石沉淀,达到脱氨的目的。
基于ASPEN计算的高氨氮渗沥液汽提精馏耦合脱氨中试工艺设计
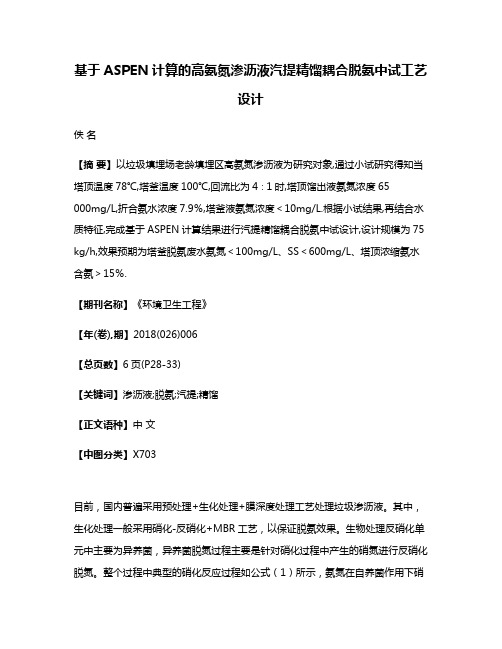
基于ASPEN计算的高氨氮渗沥液汽提精馏耦合脱氨中试工艺设计佚名【摘要】以垃圾填埋场老龄填埋区高氨氮渗沥液为研究对象,通过小试研究得知当塔顶温度78℃,塔釜温度100℃,回流比为4∶1时,塔顶馏出液氨氮浓度65000mg/L,折合氨水浓度7.9%,塔釜液氨氮浓度<10mg/L.根据小试结果,再结合水质特征,完成基于ASPEN计算结果进行汽提精馏耦合脱氨中试设计,设计规模为75 kg/h,效果预期为塔釜脱氨废水氨氮<100mg/L、SS<600mg/L、塔顶浓缩氨水含氨>15%.【期刊名称】《环境卫生工程》【年(卷),期】2018(026)006【总页数】6页(P28-33)【关键词】渗沥液;脱氨;汽提;精馏【正文语种】中文【中图分类】X703目前,国内普遍采用预处理+生化处理+膜深度处理工艺处理垃圾渗沥液。
其中,生化处理一般采用硝化-反硝化+MBR工艺,以保证脱氨效果。
生物处理反硝化单元中主要为异养菌,异养菌脱氮过程主要是针对硝化过程中产生的硝氮进行反硝化脱氮。
整个过程中典型的硝化反应过程如公式(1)所示,氨氮在自养菌作用下硝化形成硝氮,硝氮在异养菌作用下反硝化形成氮气,如公式(2)所示,从而完成脱氮。
反硝化过程需要消耗有机物[1],因此,需要保证废水中有足够的有机碳源。
而垃圾填埋区整体封闭为厌氧环境,随着填埋时间的延长,渗沥液中部分有机物厌氧发酵转化为甲烷,导致碳氮比失调[2],如东部某老龄垃圾填埋场处理项目渗沥液COD浓度为5 000 mg/L,氨氮浓度高达2 500 mg/L,碳氮比仅为2∶1,致使反硝化脱氮过程中需要补充大量碳源,额外增加了处理成本。
此外,垃圾组分对于渗沥液处理也有较大影响,如南方某老龄垃圾填埋场因填埋垃圾中有机物和蛋白类物质较多,其渗沥液COD浓度约为10 000 mg/L,氨氮浓度约为5 000mg/L,生化处理所需的最低碳氮比经验值为3∶1,故该项目中需要投加碳源将原水COD调节至15 000 mg/L方可满足脱氨需求,但额外投加碳源后,整个生化系统的处理负荷总量上涨幅度超过30%,按照生化系统设置20%余量的设计惯例,投加碳源后将导致整体处理负荷上涨幅度超过生化系统设计限值,且如此高氨氮的废水对于微生物具有毒害作用,自养菌的活性也会受到抑制,致使出水水质难以持续稳定达标,该情况下的已有渗沥液处理系统通常不得不降水量运行来确保水质稳定达标。
煤气化污水单塔加压处理脱酸脱氨工艺
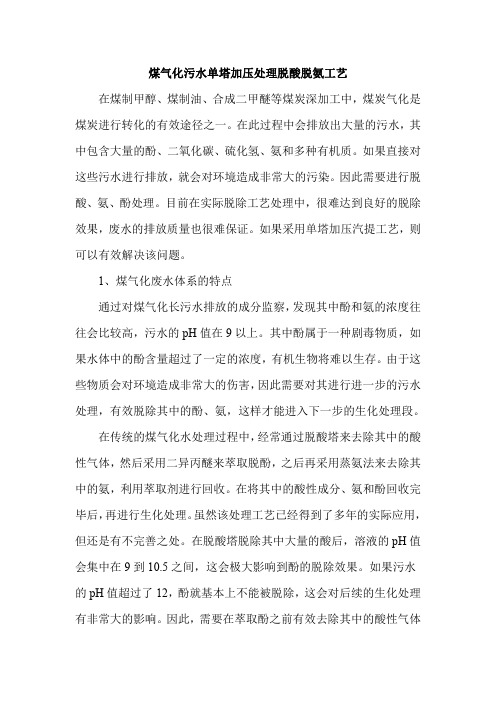
煤气化污水单塔加压处理脱酸脱氨工艺在煤制甲醇、煤制油、合成二甲醚等煤炭深加工中,煤炭气化是煤炭进行转化的有效途径之一。
在此过程中会排放出大量的污水,其中包含大量的酚、二氧化碳、硫化氢、氨和多种有机质。
如果直接对这些污水进行排放,就会对环境造成非常大的污染。
因此需要进行脱酸、氨、酚处理。
目前在实际脱除工艺处理中,很难达到良好的脱除效果,废水的排放质量也很难保证。
如果采用单塔加压汽提工艺,则可以有效解决该问题。
1、煤气化废水体系的特点通过对煤气化长污水排放的成分监察,发现其中酚和氨的浓度往往会比较高,污水的pH值在9以上。
其中酚属于一种剧毒物质,如果水体中的酚含量超过了一定的浓度,有机生物将难以生存。
由于这些物质会对环境造成非常大的伤害,因此需要对其进行进一步的污水处理,有效脱除其中的酚、氨,这样才能进入下一步的生化处理段。
在传统的煤气化水处理过程中,经常通过脱酸塔来去除其中的酸性气体,然后采用二异丙醚来萃取脱酚,之后再采用蒸氨法来去除其中的氨,利用萃取剂进行回收。
在将其中的酸性成分、氨和酚回收完毕后,再进行生化处理。
虽然该处理工艺已经得到了多年的实际应用,但还是有不完善之处。
在脱酸塔脱除其中大量的酸后,溶液的pH值会集中在9到10.5之间,这会极大影响到酚的脱除效果。
如果污水的pH值超过了12,酚就基本上不能被脱除,这会对后续的生化处理有非常大的影响。
因此,需要在萃取酚之前有效去除其中的酸性气体和氨,这样才能让污水的pH值保持在一个比较合适的范围,满足生化处理对酚的要求。
为了有效解决这个问题,设计了一种单塔测抽氨的设备,可以同时去除污水中的氨和酸性成分,是一种比较理想的处理工艺。
该工艺在石油炼化生产中已经得到了成功的应用,单煤气化水体系和石化行业中废水成分并不相同:1)煤气化污水的成分更为复杂。
煤气化水中的成分主要以CO2为主,其中硫化氢的量往往较低,CO2在常温下水中的溶解度更低,因此如果采用汽提的方法更容易脱除其中的酸性气体。
氨汽提工艺运行中存在的问题及技改措施
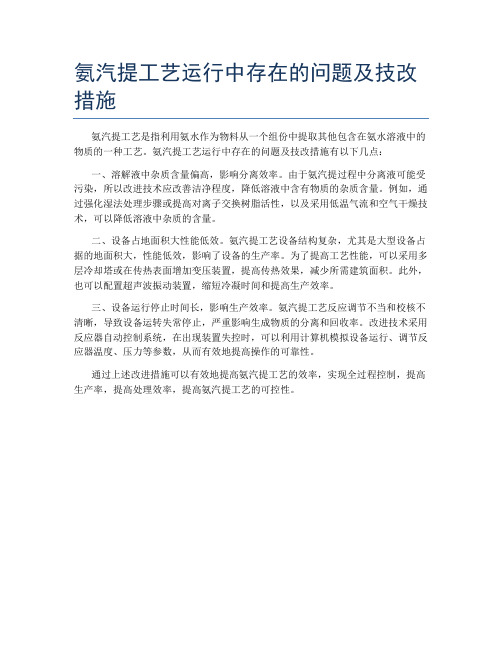
氨汽提工艺运行中存在的问题及技改措施
氨汽提工艺是指利用氨水作为物料从一个组份中提取其他包含在氨水溶液中的物质的一种工艺。
氨汽提工艺运行中存在的问题及技改措施有以下几点:
一、溶解液中杂质含量偏高,影响分离效率。
由于氨汽提过程中分离液可能受污染,所以改进技术应改善洁净程度,降低溶液中含有物质的杂质含量。
例如,通过强化湿法处理步骤或提高对离子交换树脂活性,以及采用低温气流和空气干燥技术,可以降低溶液中杂质的含量。
二、设备占地面积大性能低效。
氨汽提工艺设备结构复杂,尤其是大型设备占据的地面积大,性能低效,影响了设备的生产率。
为了提高工艺性能,可以采用多层冷却塔或在传热表面增加变压装置,提高传热效果,减少所需建筑面积。
此外,也可以配置超声波振动装置,缩短冷凝时间和提高生产效率。
三、设备运行停止时间长,影响生产效率。
氨汽提工艺反应调节不当和校核不清晰,导致设备运转失常停止,严重影响生成物质的分离和回收率。
改进技术采用反应器自动控制系统,在出现装置失控时,可以利用计算机模拟设备运行、调节反应器温度、压力等参数,从而有效地提高操作的可靠性。
通过上述改进措施可以有效地提高氨汽提工艺的效率,实现全过程控制,提高生产率,提高处理效率,提高氨汽提工艺的可控性。
一种结构简单的高效脱NH_3汽提塔
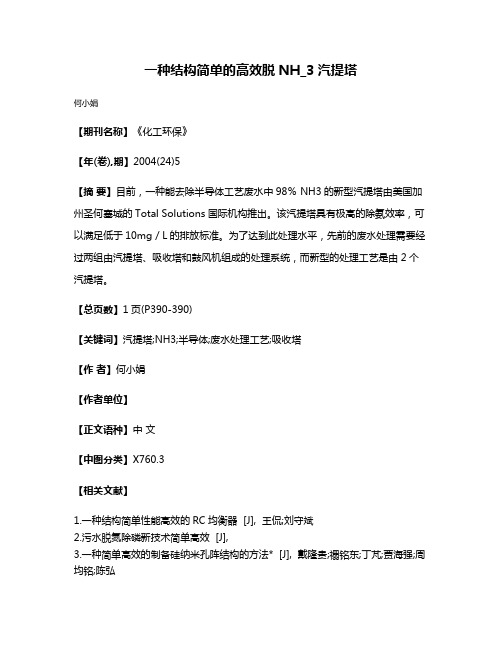
一种结构简单的高效脱NH_3汽提塔
何小娟
【期刊名称】《化工环保》
【年(卷),期】2004(24)5
【摘要】目前,一种能去除半导体工艺废水中98% NH3的新型汽提塔由美国加州圣何塞城的Total Solutions国际机构推出。
该汽提塔具有极高的除氨效率,可以满足低于10mg/L的排放标准。
为了达到此处理水平,先前的废水处理需要经过两组由汽提塔、吸收塔和鼓风机组成的处理系统,而新型的处理工艺是由2个汽提塔。
【总页数】1页(P390-390)
【关键词】汽提塔;NH3;半导体;废水处理工艺;吸收塔
【作者】何小娟
【作者单位】
【正文语种】中文
【中图分类】X760.3
【相关文献】
1.一种结构简单性能高效的RC均衡器 [J], 王侃;刘守斌
2.污水脱氮除磷新技术简单高效 [J],
3.一种简单高效的制备硅纳米孔阵结构的方法* [J], 戴隆贵;禤铭东;丁芃;贾海强;周均铭;陈弘
4.一种简单而快捷的半薄切片脱树脂新方法 [J], 武昕;周骊楠
5.用可生物降解的聚合物处理饮用水——一种简单的脱氮和去除有机污染物的方法Muller, W. R. 等( Germany ) .Stuttgarter Berichte Zur Siedlungswasserwirtschaft 2001, 166 ( Stickstoffom Wasser/Abwasser)[J],
因版权原因,仅展示原文概要,查看原文内容请购买。
酸性水汽提产液氨技术

106-P-301AB 106-D-307 106-D-305
106-E-302
106-E-306AB
106-A-301AB
106-E-307
106-E-3
三、酸性水处理工艺(产液氨)
3、粗氨气的三级分凝
三级冷凝原理。工艺基本出发点是“逐渐降温降 压,高温分水,低温固硫”。 自汽体塔来的富氨气经一级冷凝至120℃左右, 在此温度下使70%左右的水被冷凝,又可使一级 冷凝液保持较低氨浓度,即高温分水,若将分一 温度提高,虽然可以将一凝液中氨浓度进一步降 低,但分水率要下降,大量的水将移至后两级, 使循环液中氨浓度增加,严重时使分凝器操作失 常。经一分后,氨水浓度提高达一倍。A/( S十C) 分子比提高达到10以上,为后两级“固硫”创造 了条利。 第二级分凝属过渡,温度控制70℃,进一步分水 固硫,提高A/(S十C)分子比,进入三级的气液两 相氨浓度都很高,A/(S+C)分子比很大,这有利 于少量的H2S与NH3向生成盐类方向进行。在低 压小40℃温度条件下, 亦利于向生成NH4HS盐类 方向进行,实现低温固硫。三级分凝后氨浓度达 到97%。
三、酸性水处理工艺(产液氨)
6、氨水精馏
氨水精馏法制取液氨工
艺原理就是将氨气用精馏 塔底的稀氨水(20%)吸收, 经冷却制成浓氨水,浓氨 水经精馏氨水塔进料泵抽 出后,作为精馏塔的进料。 精馏塔塔底采用热源加热, 将吸收氨气后得到的浓氨 水进行汽提蒸发,形成压 力较高(1.44MPa)、纯度 较高的氨气,经冷凝制得 液氨,塔底得到的稀氨水 循环去吸收氨气,精馏塔 的操作压力由冷凝器中氨 的冷凝温度所决定。
DW02
酸性水自预处理装置来
3
862
酸性水自催化裂解装置来
气提脱氨处理工艺在高氨氮污水处理中的应用
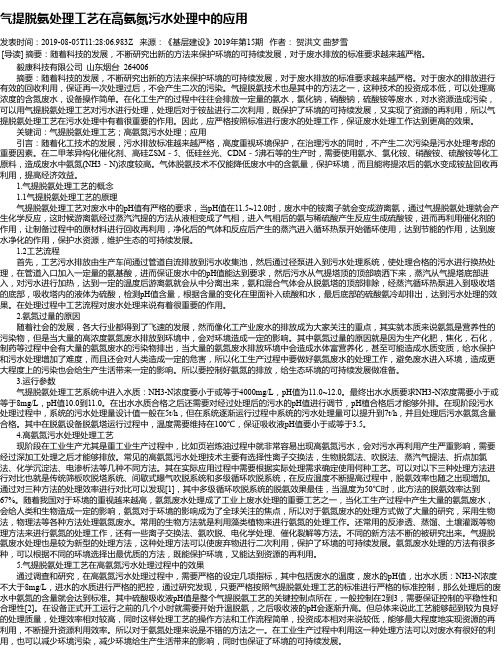
气提脱氨处理工艺在高氨氮污水处理中的应用发表时间:2019-08-05T11:28:06.983Z 来源:《基层建设》2019年第15期作者:贺洪文曲梦雪[导读] 摘要:随着科技的发展,不断研究出新的方法来保护环境的可持续发展,对于废水排放的标准要求越来越严格。
毅康科技有限公司山东烟台 264006摘要:随着科技的发展,不断研究出新的方法来保护环境的可持续发展,对于废水排放的标准要求越来越严格。
对于废水的排放进行有效的回收利用,保证再一次处理过后,不会产生二次的污染。
气提脱氨技术也是其中的方法之一,这种技术的投资成本低,可以处理高浓度的含氮废水,设备操作简单。
在化工生产的过程中往往会排放一定量的氨水,氯化钠,硝酸钠,硫酸铵等废水,对水资源造成污染,可以用气提脱氨处理工艺对污水进行处理,处理后对于铵盐进行二次利用,既保护了环境的可持续发展,又实现了资源的再利用,所以气提脱氨处理工艺在污水处理中有着很重要的作用。
因此,应严格按照标准进行废水的处理工作,保证废水处理工作达到更高的效果。
关键词:气提脱氨处理工艺;高氨氮污水处理;应用引言:随着化工技术的发展,污水排放标准越来越严格,高度重视环境保护,在治理污水的同时,不产生二次污染是污水处理考虑的重要因素。
在二甲苯异构化催化剂、高硅ZSM-5、低硅丝光、CDM-5沸石等的生产时,需要使用氨水、氯化铵、硝酸铵、硫酸铵等化工原料,造成废水中氨氮(NH3-N)浓度较高。
气体脱氨技术不仅能降低废水中的含氨量,保护环境,而且能将提浓后的氨水变成铵盐回收再利用,提高经济效益。
1.气提脱氨处理工艺的概念1.1气提脱氨处理工艺的原理气提脱氨处理工艺对废水中的pH值有严格的要求,当pH值在11.5~12.0时,废水中的铵离子就会变成游离氨,通过气提脱氨处理就会产生化学反应,这时候游离氨经过蒸汽汽提的方法从液相变成了气相,进入气相后的氨与稀硫酸产生反应生成硫酸铵,进而再利用催化剂的作用,让制备过程中的原材料进行回收再利用,净化后的气体和反应后产生的蒸汽进入循环热泵开始循环使用,达到节能的作用,达到废水净化的作用,保护水资源,维护生态的可持续发展。
- 1、下载文档前请自行甄别文档内容的完整性,平台不提供额外的编辑、内容补充、找答案等附加服务。
- 2、"仅部分预览"的文档,不可在线预览部分如存在完整性等问题,可反馈申请退款(可完整预览的文档不适用该条件!)。
- 3、如文档侵犯您的权益,请联系客服反馈,我们会尽快为您处理(人工客服工作时间:9:00-18:30)。
氨氮废水处理及资源化利用
技术方案
项目名称:氨氮废水处理及资源化利用
项目地点:中国··
委托方:
设计方:
第一部分工艺设计概述
一.设计原则及依据:
将含氨废水中的氨予以脱除,并以浓氨水的形式回收利用。
1.氨氮废水:
处理量:300 t/d;
氨氮含量: 20000mg/L;
氯离子含量: mg/L;
废水pH值:约8;
废水温度:常温。
2、处理要求:
回收浓氨水浓度(wt):15~20%;
脱氨水氨氮含量:≤ 15mg/L。
二.工艺选择:
通过分析研究有关含氨废水工艺条件,在其废水脱氨技术研究及项目实施实际过程经验的基础上,针对氨氮废水处理及氨的资源化回收利用问题,提出采用汽提+精馏工艺技术方案处理含氨废水。
本工艺技术方案设计力求降低系统蒸汽消耗,在解决企业氨氮废水排放问题的同时,回收废水中的氨,以降低运行成本,提高经济效益。
三.工艺流程考虑主要因素
1.工艺过程可靠,满足生产任务的要求。
2.操作简便,安全可靠,操作弹性大。
3.设备投资费用尽可能少。
4.单位产品的能耗尽可能低。
四.工艺流程图(见附页)
系统工艺流程图见附页:图号BUCT-AR1215。
五、工艺流程说明:
如工艺流程示意图(图号BUCT-AR1215)所示:含氨废水经过换热后送入汽提精馏塔。
汽提精馏塔的操作压力为常压,塔釜操作温度为110℃,塔顶操作温度为50℃。
在汽提精馏塔汽提段,含氨废水自上而下运动,与来自塔底的直接蒸汽逆流接触,其中的氨被脱除。
在塔底得到氨含量低于100mg/L的脱氨废水排出系统。
在汽提精馏塔的精馏段氨气及水蒸汽与来自塔顶回流的浓氨水逆流接触,氨浓度进一步提高,水分进一步减少,从塔顶进入塔顶氨冷凝器。
塔顶冷凝器的操作温度为50℃。
在塔顶氨冷凝器中氨和水蒸汽被循环水冷凝为浓氨水,并全部作为塔顶回流。
自塔顶氨冷凝器采出浓度为90%左右的氨气进入氨气吸收塔。
在氨气吸收塔,来自汽提精馏塔的氨气用工艺水吸收为约20%左右的浓氨水。
由于来自汽提精馏塔的浓氨水中含有少量蒸汽,另外氨气溶于水将放出溶解热,因此浓氨水的温度会升高。
因此,流程中设有浓氨水冷却器,采用循环水冷却,以控制氨气吸收塔的反应温度在45℃以下。
经过氨气吸收塔吸收后剩余的不凝气体自塔顶排放。
第二部分主要设备及参数1、汽提精馏塔:
设备形式:立式填料塔;
填料类型:RPP鲍尔环;
设备尺寸:Φ1000mm/Φ1500mm;
设备高度约:约45m;
操作压力:0.05Mpa;
设计压力:0.1Mpa;
精馏段操作温度:50℃;
汽提段操作温度:110℃;
设计温度:120℃;
设备主体材质:Q345R/2205
塔件材质:2205;
数量:1台。
2、氨气吸收塔:
设备形式:立式填料塔;
填料类型:RPP鲍尔环;
设备直径:Φ300mm/Φ600mm/Φ1200mm;
设备高度:约20m;
操作压力:0.05Mpa;
设计压力:0.1Mpa;
操作温度:50℃;
设计温度:100℃;
材质:304;
数量:1台。
3、塔顶回流罐:
设备形式:卧式储罐;
设备容积:1.5m3;
操作压力:0.05Mpa;
设计压力:0.1Mpa;
操作温度:50℃;
设计温度:100℃;
材质:Q345R。
数量:1台。
4、塔顶冷凝器:
设备形式:立式管壳式换热器;
换热面积:240m2;
壳程操作压力:0.05Mpa;
壳程设计压力:0.1Mpa;
壳程操作温度:50℃;
壳程设计温度:100℃;
管程操作压力:0.4Mpa;
管程设计压力:0.6Mpa;
管程操作温度:35℃(循环水温度);
管程设计温度:50℃;
材质:Q345R/20。
数量:1台。
5、再沸器:
设备形式:立式管壳式换热器;
换热面积:240m2;
壳程操作压力:0.2Mpa;
壳程设计压力:0.4Mpa;
壳程操作温度:130℃;
壳程设计温度:150℃;
管程操作压力:0.3Mpa;
管程设计压力:0.4Mpa;
管程操作温度:110℃;
管程设计温度:140℃;
材质:Q345R/2205。
数量:1台。
6、原料预热器:
设备形式:螺旋板换热器;
换热面积:200m2;
设计压力:0.6 Mpa;
设计温度:100℃
材质:Q345R;
数量:1台。
7、浓氨水冷却器:
设备形式:板式换热器;
换热面积:30m2;
设计压力:0.6 Mpa;
设计温度:100℃
材质:304;
数量:1台。
6、脱氨水泵:
设备型式:离心泵;
流量:15m3/h;
扬程:40m;
操作温度:110℃;
材质:碳钢衬氟;
数量:两台(用一备一)。
6、脱氨水循环泵:
设备型式:离心泵;
流量:150m3/h;
扬程:10m;
操作温度:110℃;
材质:碳钢衬氟;
数量:两台(用一备一)。
7、塔顶回流泵:
设备型式:漩涡泵;
流量:2m3/h;
扬程:75m;
操作温度:50℃;
材质:304;
数量:两台(用一备一)。
8、浓氨水循环泵:
设备型式:离心泵;
流量:15m3/h;
扬程:30m;
操作温度:50℃;
材质:304;
数量:两台(用一备一)。
9、含氨废水泵:
设备型式:离心泵;
流量:15m3/h;
扬程:60m;
操作温度:常温;
材质:碳钢衬氟;
数量:两台(用一备一)。
第三部分工艺系统投资估算
对氨回收系统有关设备、仪表、土建等的投资估算如下:
1、设备投资:260万元。
2、管道、管件、阀门及安装:30万元。
3、仪表、电气及自动化控制系统:40万元。
4、土建、钢结构及安装:20万元。
5、技术费、工程设计费等:50万元。
以上投资总计:400万元。
投资估算补充说明:
1、本投资估算不包括氨氮废水由生产装置到本装置的界区外管道。
2、本投资估算不包括公用工程(变电、循环水、冷冻、压缩风、仪表风等)、公用工程界区外管道(水、汽、风等)、界区外电缆外线及桥架、界区外管及管廊等。
3、本投资估算不包括前期场地准备费用(假如场地需要大量回填或平整等)。
4、本投资估算中电气开关使用中档产品,比如人民电器、士林等,若采用施耐德或ABB等高端产品,则价格另协商。
5、本投资估算中仪表及控制系统采用PLC系统。
第四部分工艺系统主要经济技术指标
氨回收系统主要经济技术指标如下
1、蒸汽(0.6pa)消耗:
蒸汽消耗:约180kg/吨废水。
蒸汽价格以200元/吨计算,则蒸汽产生的成本约为36元/吨废水。
2、电耗:
电力消耗约为2度/吨浓氨水,电价以0.7元/度计算,则电力消耗产生的成本约为1.4元/吨废水。
3、30%氢氧化钠消耗:
30%氢氧化钠消耗为30kg/吨浓氨水,30%氢氧化钠以800元/吨计算,则30%氢氧化钠消耗产生的成本约为24元/吨废水。
4、以20%浓氨水形式回收废水中的氨:
回收氨量:20kg/吨废水,以20%浓氨水计则为100kg/吨废水。
20%浓氨水的价格以350元/吨,则处理每吨废水产生35元/吨废水的效益。
5、人工成本、管理费:
人工成本、管理费及设备折旧约为1元/吨废水。
综上所述,该氨氮废水处理成本约为27.4元/吨废水。
略
1、中化新网(),2011年6月21日,专项技术报告:《高效节能的高浓度氨氮废水处理成套技术》。
获多家。
2、《中国化工报》,2011年7月12日,科技创新版头条:《高效低耗资源化利用——高效氨氮废水处理技术全面推广》。
3、《中国农药》,2010年8月,第8期(总第41期):《高浓度氨氮废水处理成套技术工程应用实例介绍》。