河科大铸造机械化课后习题答案
2014河南科技大学《铸造机械化》考试重点

问答总结第一章造型和制芯设备工艺5、预震加压实与震压有哪些区别?预震加压实是在加压前先进行微震,震压是压实的同时微震,相比之下同样的比压压实,预震加压实可以获得更好的紧实度。
3何为静压造型?静压造型的工艺过程及特点是什么?气流渗透实砂后,利用气流在短时间内渗透型砂而使型砂紧实的方法。
工艺过程:型砂--砂箱或辅助框--压紧在造型机的射孔下--开启阀--气体至砂型顶部--短时间过型砂--模板上气孔排出特点:高硬度且均匀分布,高紧实度,生产率高,动能消耗少,透气性好。
9:漏斗堵塞:气冲紧实过程中,模样上方先紧实形成一个锥型区,然后再紧实过程中,砂子将会沿着锥型斜向下运动,当遇到模样四周仍处于自上而下初步紧实的砂子时,形成一个高度紧实区,将会堵在那里,阻止了下面砂子紧实,称为漏斗堵塞。
消除:1.使用紧实度低的型砂:可以提高气冲紧实度分布的均匀性。
2.液态气冲法:辅助框带夹缝——(快速)3.差动气冲法:设一导气框——(减速)4.二次气冲:第一次小气压,第二次大气压(迅速)第二章粘土砂造型设备及生产线1、如果Z145B震压造型机发生双震现象,什么原因?如何消除?:原因:管路气压低、工作负荷过大或者是进气孔过小消除:增大管路气压、卸载负荷、适当增大气孔6:为什么自动造型生产线上力求自动化模块更换装置?这对于提高开动率和工作灵活性有什么好处?原因:模块十分笨重,人工更换费力,且更换时要停机操作,会影响造型生产线的生产率。
好处:a、可以在不停机的情况下自动更换,不占用机动时间,提高机械生产率b、在对复杂铸钢件造型时,造型前需放置冷铁,活块及覆盖防粘砂材料,采用自动更换可将这些工序移至造型机外进行,有利于增加机械的机动时间c、在对于小批量,多品种生产中也能使用自动化高压造型线d、调节生产,均衡生产线对型砂,型芯及金属溶液的需要11静压多触头高压造型线与气冲造型线相比有什么优缺点?优点:a、结构紧凑简单,不需要底坑b、砂型紧实度高而均匀,且流动性好,提高充填性c、模板利用率高,可以生产薄壁、复杂的铸件,且铸件的表面质量好d、对加沙量控制准确,节省用砂,采用压实起模框,起摸精度高e、噪音小、振动小缺点:a、不适合多品种、小批量生产b、设备投资高12:封闭式与开放式各有何特点?各适用于什么场合?开放式:采用间歇式铸型输送机组成直线布置的流水生产线,铸型输送线的条数由冷却时间确定,并在其两端有转运小车相连,适合生产复杂、多芯、重量大、需长时间冷却的铸件封闭式:采用连续式或脉动式铸型输送机组成的不间断环形流水生产线,其优点是铸型转运少,辅机类型少,对控制系统较为有利,因此适合于大量生产、连续浇注不需要铸型储备的铸件生产13:什么叫串联式和并联式布线?各有何特点?串联式:造好的上型从造型机到合箱机之间的运行方向,与造型段或下芯段铸型输送机小车的运行方向平行或重叠,适合于占地狭长的场合,布线较为紧凑除动态合箱机外所用的辅机结构比较简单,但铸型通过的辅机多砂粒易落入型腔中并联式:造好的上型从主机到合箱机的运行方向与铸型输送机在造型段或下芯段的运行方向垂直或呈一定角度,适合于车间跨度较大,允许占地短而宽的场合。
《铸造工艺学》课后习题答案

《铸造工艺学》课后习题答案《铸造工艺学》课后习题答案湖南大学1、什么是铸造工艺设计?铸造工艺设计就是根据铸造零件的结构特点、技术要求、生产批量、生产条件等,确定铸造方案和工艺参数,绘制铸造工艺图,编制工艺卡等技术文件的过程。
2、为什么在进行铸造工艺设计之前要弄清楚设计的依据,设计依据包括哪些内容?在进行铸造工艺设计前设计者应该掌握生产任务和要求,熟悉工厂和车间的生产条件这些是铸造工艺设计的基本依据,还需要求设计者有一定的生产经验,设计经验并应对铸造先进技术有所了解具有经济观点发展观点,才能很好的完成设计任务设计依据的内容一、生产任务1)铸件零件图样提供的图样必须清晰无误有完整的尺寸,各种标记2)零件的技术要求金属材质牌号金相组织力学性能要求铸件尺寸及重量公差及其它特殊性能要求3)产品数量及生产期限产品数量是指批量大小。
生产期限是指交货日期的长短。
二、生产条件1)设备能力包括起重运输机的吨位,最大起重高度、熔炉的形式、吨位生产率、造型和制芯机种类、机械化程度、烘干炉和热处理炉的能力、地坑尺寸、厂房高度大门尺寸等。
2)车间原料的应用情况和供应情况3)工人技术水平和生产经验4)模具等工艺装备制造车间的加工能力和生产经验三、考虑经济性对各种原料、炉料等的价格、每吨金属液的成本、各级工种工时费用、设备每小时费用等、都应有所了解,以便考核该工艺的经济性。
3.铸造工艺设计的内容是什么?铸造工艺图,铸件(毛坯)图,铸型装配图(合箱图),工艺卡及操作工艺规程。
4.选择造型方法时应考虑哪些原则?1、优先采用湿型。
当湿型不能满足要求时再考虑使用表干砂型、干砂型或其它砂型。
选用湿型应注意的几种情况1)铸件过高的技术静压力超过湿型的抗压强度时应考虑使用干砂型,自硬砂型等。
2)浇注位置上铸件有较大水平壁时,用湿型易引起夹砂缺陷,应考虑使用其它砂型3)造型过程长或需长时间等待浇注的砂型不宜选用湿型4)型内放置冷铁较多时,应避免使用湿型2、造型造芯方法应和生产批量相适应3、造型方法应适用工厂条件4、要兼顾铸件的精度要求和生产成本5-浇注位置的选择或确定为何受到铸造工艺人员的重视?应遵循哪些原则?确定浇注位置是铸造工艺设计中重要的一环,关系到铸件的内在质量、铸件的尺寸精度铸造工艺过程中的难易,因此往往须制定出几种方案加以分析,对此择优选用。
铸造部分习题参考答案讲解

方案I: 分型面为 曲面,不利于分 型。 方案II:分型面在 最大截面处,且 为平面,方案可 行。
金属工艺学
2. 确定两种比上造型方案,比较 各方案的优劣,画铸造工艺图(见 教材72页)
SUST
金属工艺学
SUST
下
Ⅰ
上 上
Ⅱ
下
金属工艺学
SUST
金属工艺学
铸造工艺图范例(仿照范例,完成前述问 题铸造工艺图的绘制。
φ85 φ50
b) 修改方案
20
15
39 0 46 0 50 0
55 15
120
SUST
金属工艺学
在零件设计中所确定的非加工表面斜度为结构斜度。而在绘 制铸造工艺图中加在垂直分型面的侧面所具有的斜度称为拔 模斜度,以使工艺简化和保证铸件质量。图中铸件之孔和外 圆面应具有斜度才合理。如果外表面加工则在加上加工余量 后再加上部分金属使其具有斜度。
课后习题:P49-2、4、5、6、8;P73-3、4;书上各种图的分析
SUST
金属工艺学
何谓合金的充型能力?影响充型能力的主要因素有哪些? 合金的充型能力不好时,易产生哪些缺陷?设计铸件时应如何考虑充型能 力? 为什么对薄壁铸件和流动性较差的合金,要采用高温快速浇注? 合金的收缩经历了哪几个阶段,会产生什么样的影响? 合金的凝固有哪几种类型,会产生什么样的影响? 缩孔和缩松产生原因是什么?如何防止? 什么是定向凝固原则和同时凝固原则?如果保证铸件按规定凝固方式进行 凝固? 哪类合金易产生缩孔?哪类合金易产生缩松?如何促进缩松向缩孔转化? 各种特点铸造方法的工艺特点和工艺过程是什么?
SUST
金属工艺学
1.有一测试铸造应力用的应力框铸件,如图1-1所示,凝 固冷却后,用钢锯沿A-A线锯断,此时断口间隙的大小会 发生什么变化?为什么?
河南科技大学 机械设计答案
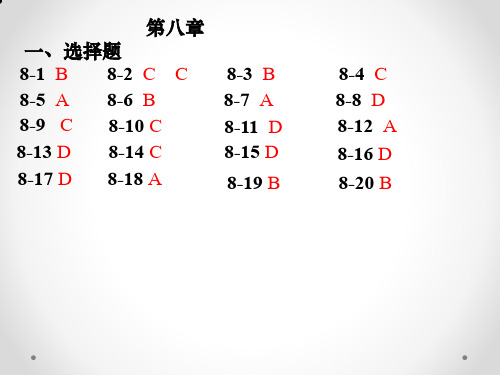
第八章 8-3 B 8-7 A 8-11 D 8-15 D 8-19 B 8-4 C 8-8 D 8-12 A 8-16 D 8-20 B
二、填空题 8-21 在平带或V带传动中,影响最大有效圆周力Fec的因素是 初拉力F0 、 摩擦系数μ(当量摩擦系数μV ) 和 小轮包角α1 。 8-22 V带传动在工作过程中,带内应力有:紧边、松边拉应力(σ1、σ2)、 离 心拉应力σc 、 弯曲应力(σb1、σb2 ) ,最大应力σmax= σ1+σc+σb1 ,发生在 紧边刚绕上小带轮处 。 8-23 带传动的主要失效形式为 疲劳破坏 和 打滑 ,其设计准则为 在不打滑的
1、将dd2减小到280mm;
电动机
dd2 V带传动
2、将dd1增大到200mm;
dd1
减速器
3、将鼓轮直径D增大到355mm。
解
输出功率P出=F· v 1、 dd2 , n2 , v,F不变,则 P出
v D
F 输送带
n1d d 1 不变 而 v带 60 1000 Fe带(42%)可能引起打滑或疲劳失效。
∵原运输带速度: v
n y D 60000
n y D 60000
,
F 输送带 D
现运输带速度:
v
,
∵原运输带鼓轮转速: n y 现运输带鼓轮转速: n y
n电 i12 i减
n电 2.857 i减
n电 n电 i12 i减 2 i减
∴方案1、2运输带速度提高: 1 1 v v n y n y 2 2.857 2.857 ( 1) 42.9% 1 v ny 2 2.857 同理方案3运输带速度提高: v v D D 355 250 42% v D 250
河科大铸造机械化考试要点
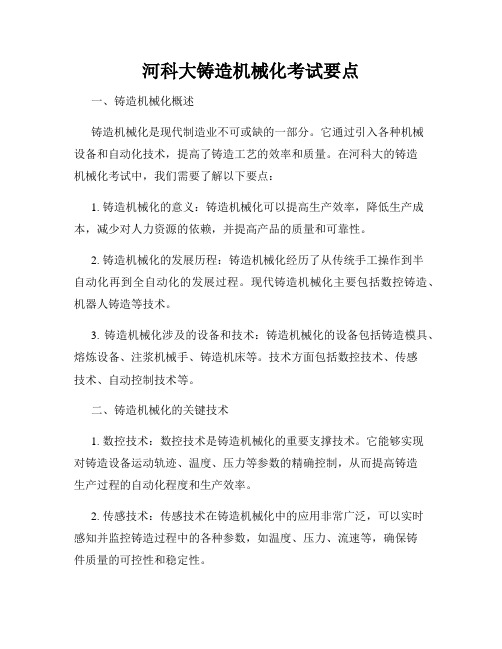
河科大铸造机械化考试要点一、铸造机械化概述铸造机械化是现代制造业不可或缺的一部分。
它通过引入各种机械设备和自动化技术,提高了铸造工艺的效率和质量。
在河科大的铸造机械化考试中,我们需要了解以下要点:1. 铸造机械化的意义:铸造机械化可以提高生产效率,降低生产成本,减少对人力资源的依赖,并提高产品的质量和可靠性。
2. 铸造机械化的发展历程:铸造机械化经历了从传统手工操作到半自动化再到全自动化的发展过程。
现代铸造机械化主要包括数控铸造、机器人铸造等技术。
3. 铸造机械化涉及的设备和技术:铸造机械化的设备包括铸造模具、熔炼设备、注浆机械手、铸造机床等。
技术方面包括数控技术、传感技术、自动控制技术等。
二、铸造机械化的关键技术1. 数控技术:数控技术是铸造机械化的重要支撑技术。
它能够实现对铸造设备运动轨迹、温度、压力等参数的精确控制,从而提高铸造生产过程的自动化程度和生产效率。
2. 传感技术:传感技术在铸造机械化中的应用非常广泛,可以实时感知并监控铸造过程中的各种参数,如温度、压力、流速等,确保铸件质量的可控性和稳定性。
3. 自动控制技术:自动控制技术是铸造机械化的核心技术之一。
通过对铸造生产过程中各个环节的控制,包括温度控制、压力控制、速度控制等,实现铸造过程的自动化和优化。
三、铸造机械化的应用领域铸造机械化技术广泛应用于各个领域,例如汽车制造、航空航天、机械制造、能源等行业。
在河科大铸造机械化考试中,我们需要了解以下应用领域:1. 汽车制造:铸造机械化可以提高汽车零部件的生产效率和质量,降低制造成本,满足汽车行业对大批量、高精度铸件的需求。
2. 航空航天:航空航天领域对铸件质量和可靠性要求极高。
铸造机械化可以确保铸件精度和一致性,提高航空航天产品的安全性和可用性。
3. 机械制造:铸造机械化可以提高机械零部件的生产效率和一致性,满足不同行业对复杂、精密零部件的需求,推动机械制造业的发展。
4. 能源领域:铸造机械化在能源领域的应用包括核能、火电等。
kxx第2章铸造成形习题及参考答案

kxx第2章铸造成形习题及参考答案习题第2章铸造成形填空题:1、铸造⽅法从总体上可分为普通铸造和特种铸造两⼤类,普通铸造是指砂型铸造⽅法,不同于砂型铸造的其他铸造⽅法统称为特种铸造,常⽤的特种铸造⽅法有:()、()、()、()、()等。
2、凝固过程中所造成的体积缩减如得不到液态⾦属的补充,将产⽣()或()。
3、对砂型铸件进⾏结构设计时,必须考虑合⾦的()和铸造()对铸件结构提出的要求。
4、()是铸造合⾦本⾝的物理性质,是铸件许多缺陷()产⽣的基本原因。
5、浇注位置是指造型时()在铸型中所处的位置,它影响铸件的质量。
6、铸造应⼒按产⽣的原因不同,主要可分为()和()两种。
7、铸件上各部分壁厚相差较⼤,冷却到室温,厚壁部分的残余应⼒为()应⼒,⽽薄壁部分的残余应⼒为()应⼒。
8、任何⼀种液态⾦属注⼊铸型以后,从浇注温度冷却⾄室温都要经过三个联系的收缩阶段,即()、()和()。
9、在低压铸造、压⼒铸造和离⼼铸造时,因⼈为加⼤了充型压⼒,故()较强。
提⾼浇铸温度是改善合⾦()的重要措施。
10、铸件浇铸位置的选择必须正确,如重要加⼯⾯、⼤平⾯和薄壁部分在浇铸时应尽量(),⽽厚⼤部位应尽量(),以便安放冒⼝进⾏()。
单项选择题:1、下列合⾦流动性最好的是:()①普通灰铸铁;②球墨铸铁;③可锻铸铁;④蠕墨铸铁。
2、摩托车活塞应具有良好的耐热性、热膨胀系数⼩,导热性好、耐磨、耐蚀、重量轻等性能。
在下列材料中,⼀般选⽤:()①铸造黄铜;②合⾦结构钢;③铸造铝硅合⾦;④铸造碳钢。
3、在下列铸造合⾦中,⾃由收缩率最⼩的是:()①铸钢;②灰铸铁;③铸造铝合⾦;④⽩⼝铸铁4、图⽰圆锥齿轮铸件,齿⾯质量要求较⾼。
材料HT350,⼩批⽣产。
最佳浇5①采⽤在热节处加明、暗冒⼝或冷铁以实现顺序凝固②尽量使铸件壁厚均匀以实现同时凝固③提⾼浇注温度④采⽤颗粒⼤⽽均匀的原砂以改善填充条件多项选择题:1、液态合⾦浇注温度冷却到室温所经历的收缩阶段有:()①⾼温收缩;②液态收缩;③凝固收缩④低温收缩;⑤固态收缩2、挖沙或假箱造型时候,分型⾯:()①⼀定是曲⾯;②⼀定是圆锥⾯;③可以是平;④⼀定是平⾯;⑤可以是曲⾯3、影响液态合⾦充型能⼒的主要因素是:()①合⾦的结晶特性;②浇注温度;③合⾦的收缩率;④铸造⼯艺凝固原则;⑤铸件壁厚和铸型条件4、影响液态合⾦充型能⼒的主要因素是:()①合⾦的结晶特性;②浇注温度;③合⾦的收缩率;④铸造⼯艺凝固原则;⑤铸件壁厚和铸型条件5、产⽣缩孔、缩松的基本原因:()①液态收缩;②固态收缩;③凝固收缩;④线收缩;⑤等温收缩结构改错题:1、如下图所⽰,浇铸位置是否合理?若不合理请改为合理。
大学本科-机械设计及其自动化专业-《机械制造基础》课后练习题(有答案和解析)

大学本科-机械设计及其自动化专业-《机械制造基础》课后练习题(有答案和解析)1.(单选题)下面的叙述正确的是( )。
A顺序凝固有利于防止铸造应力的产生B同时凝固有利于防止缩孔的产生C铸造时浇注温度越高越好D铸件的结构斜度应设置在非加工表面正确答案:D题目解析:铸件的结构斜度应设置在非加工表面,这是为了便于从模具中取出铸件,同时避免在加工表面上留下不必要的痕迹。
选项A错误,因为顺序凝固并不能完全防止铸造应力的产生;选项B错误,因为同时凝固容易导致缩孔的产生;选项C错误,因为浇注温度过高会导致铸件产生缺陷。
2.(单选题)钢套镶铜轴承是一个双金属结构件,能够方便的铸造出该件的铸造方法是( )。
A金属型重力铸造B熔模铸造C离心铸造D低压铸造正确答案:C题目解析:离心铸造是一种利用离心力将液态金属浇入旋转的铸型中,使金属液在离心力的作用下贴紧铸型壁,从而获得各种形状的中空回转体铸件的铸造方法。
钢套镶铜轴承是一个双金属结构件,内层为钢套,外层为铜套,可以采用离心铸造的方法将两种金属材料结合在一起。
因此,答案为C。
3.(单选题)下面属于压焊的是( )。
A电渣焊B缝焊C氩弧焊D埋弧焊正确答案:B题目解析:缝焊是一种压焊方法,它使用旋转的滚轮电极对搭接的工件施加压力并进行焊接。
在焊接过程中,滚轮电极与工件接触部位产生电阻热,加上滚轮电极的挤压作用,形成连续的焊缝。
因此,正确的选项是B。
4.(单选题)在低碳钢焊接接头的热影响区中,力学性能最好的区域是( )。
A熔合区B正火区C部分相变区D过热区正确答案:B题目解析:在低碳钢焊接接头的热影响区中,正火区的力学性能最好。
正火区是焊接时焊缝两侧的金属正处于相变重结晶温度范围内,冷却后得到均匀细小的铁素体和珠光体组织,其力学性能优于母材。
相比之下,熔合区的化学成分和组织性能极不均匀,力学性能较差;部分相变区的组织不均匀,力学性能也不好;过热区的晶粒粗大,力学性能也较差。
因此,答案为B。
铸造工艺习题及答案

一、名词解释1、(铸造用原砂中的)泥份:是指原砂中直径小于20μm的颗粒2、钙膨润土活化处理:;根据阳离子的交换特性对钙土进行处理使之转化为钠基膨润土,蒙脱石的晶层间阳离子交换{PNa(+1)→PCa(+2)}3、铸件工艺出品率:铸件出品率=铸件质量除以铸件质量+冒口总质量+浇注系统质量乘以100%4、通用冒口:在铸型内储存供补缩铸件用熔融金属的空腔5、浇注系统:铸型中液态金属流入型腔的通道6、铸造收缩率:由于合金的收缩,为保证铸件应有的尺寸,在模型上必须比铸件放大一个该合金的收缩量。
它取决于合金种类、铸件结构、尺寸等因素7、起模斜度:为便于起模样或开芯盒,在铸件垂直分型面的各个侧面上设计的斜度8、封闭式浇注系统:在正常浇注条件下,所有组元都能为金属液充满的浇注系统9、开放式浇注系统:金属液不能充满所有组元的的浇注系统。
10、粘土型砂:以粘土为粘结剂的型砂11、紧实率:型砂紧实前后的体积变化12、侵入气孔:-也叫外因气孔由于型砂中的气体侵入金属造成的在湿型铸件中常见的一种缺陷13、破碎指数:生产中常采用落球法测出的破碎指数来间接表示型砂的韧性。
测量时,将一个钢球在一定高度落下,砸在一个放在筛网上的标准试样上,用留在筛网上的砂块重量与标准试样重量之比值表示破碎指数14、铸件的分型面:两半铸型相互接触的表面15、铸件的浇注位置:指浇注时铸件在铸型中所处的位置16、化学粘砂:在高温条件下金属氧化物与铸型间发生化学作用而使金属表面与铸型发生粘结的现象。
17、机械粘砂:金属熔液渗入砂粒间隙,凝固后将砂粒机械的粘连在铸件的表面上18、型砂的透气性:型砂允许气体通过并逸出的能力19、覆模砂:指树脂以一层薄膜包覆在砂粒表面,这样可以完全发挥树脂的粘结作用,改善树脂砂的性能,节省树脂用量20、型砂的残留强度:是将∮30mm*50mm或者∮50mm环形钠水玻璃砂试样加热到一定温度并在该温度下保温30-40分钟在随炉冷却至室温测定的抗压强度21、铸造工艺设计:对于某一个铸件,编制出其铸造生产工艺过程的技术文件就是铸造工艺设计22、铸造工艺方案:造型,造芯方法和铸型种类的选择,浇注位置及分析面的确定23、剩余压力角:24、冷芯盒法:在室温下,通过吹气使砂芯在芯盒内快速硬化的制芯方法叫冷芯盒法。
铸造复习题答案解析版1

铸造工程学复习提纲1.什么是充型和凝固?影响铸件凝固方式的主要因素是什么?充填铸型(充型):亦称浇注,是指液态合金填充铸型的过程,是一种运动速度变化的机械过程。
冷却凝固:液态金属通过冷却凝固而形成铸件的过程,是结晶和组织变化的热量传递过程。
合金的结晶温度范围铸件的温度梯度2.合金的收缩分为几个阶段?各易产生何种缺陷?三个阶段:液态收缩、凝固收缩、固态收缩液态收缩和凝固收缩是产生缩孔和缩松的基本原因,铸件的固态收缩不仅对铸件的尺寸精度有着直接的影响,而且是铸造应力、变形、裂纹的变形。
3.砂型分为几类?粘土砂型、水玻璃砂型各分为几类?湿型砂的基本组成是什么?其粘结机理?粘土砂型、无机化学粘结剂砂型、有机粘结剂砂型。
粘土砂型包括湿型、表面干型、干型。
水玻璃砂型包括CO2硬化水玻璃砂(包括VRH法)、自硬水玻璃砂(有机酯硬化)、物理硬化水玻璃砂(烘干法/微波法)。
湿型砂的分类面砂、干砂、单一砂。
湿型砂的基本组成是原砂、粘土、附加物和水粘结机理:粘土表面带有电荷和可交换性阳离子。
4.什么是夹砂结疤和鼠尾?①夹砂结疤均是指在铸件比较开阔的表面上出现一片或多片粗糙而不规则的金属凸出物,其内部金属层中还常夹有砂层,称为夹砂结疤。
②鼠尾:铸件表面上细长而不规则的线状凹槽,形状好象裂纹或隙缝,凹槽深度不超过5mm,有一定方向性,无金属瘤状物,这种缺陷通常沿下型内浇口正前方产生,在下型表面上可看到与这些凹槽相对应的线状棱纹,称为鼠尾。
5.浇注系统的组成是什么?各有什么作用?浇口杯、直浇道、直浇道窝、横浇道、内浇道、末端延长段。
浇口杯作用:①承接来自浇包的金属液,防止飞溅和溢出,方便浇注;②减少金属液对铸型的直接冲击;③可能撇去部分熔渣、杂质、阻止其进入直浇道内;提高金属液静压力。
直浇道作用:从浇口杯中将浇口杯中的金属液引入横浇道、内浇道或直接进入型腔。
直浇道窝作用:①缓冲作用,减轻金属液对直浇道底部型砂冲刷②缩短直横道拐弯处的高度紊流区;③改善内浇道的流量分布,有利于内浇道流量分布的均匀化;④减少直-横浇道拐弯处的局部阻力系数和水头损失,有利于金属液中气泡的浮出。
河南科技大学机械基础学习知识原理课后复习规范标准答案
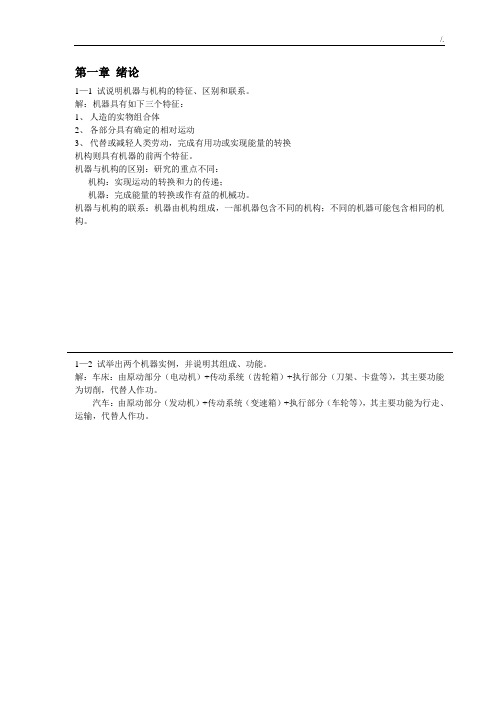
第一章绪论1—1 试说明机器与机构的特征、区别和联系。
解:机器具有如下三个特征:1、人造的实物组合体2、各部分具有确定的相对运动3、代替或减轻人类劳动,完成有用功或实现能量的转换机构则具有机器的前两个特征。
机器与机构的区别:研究的重点不同:机构:实现运动的转换和力的传递;机器:完成能量的转换或作有益的机械功。
机器与机构的联系:机器由机构组成,一部机器包含不同的机构;不同的机器可能包含相同的机构。
1—2 试举出两个机器实例,并说明其组成、功能。
解:车床:由原动部分(电动机)+传动系统(齿轮箱)+执行部分(刀架、卡盘等),其主要功能为切削,代替人作功。
汽车:由原动部分(发动机)+传动系统(变速箱)+执行部分(车轮等),其主要功能为行走、运输,代替人作功。
第二章平面机构的结构分析2—1 试画出唧筒机构的运动简图,并计算其自由度。
2—2 试画出缝纫机下针机构的运动简图,并计算其自由度。
142332343=⨯-⨯=--====hlhlppnFppn,,解:解:142332343=⨯-⨯=--====hlhlppnFp pn,,2— 3 试画出图示机构的运动简图,并计算其自由度。
2—4 试画出简易冲床的运动简图,并计算其自由度。
解:或1423323043=××=====hlh l p p n F p p n ,,解:1725323075=××=====hl h l p p n F p p n ,,2—5 图示为一简易冲床的初拟设计方案。
设计者的思路是:动力由齿轮1输入,使轴A连续回转,而装在轴A上的凸轮2与杠杆3组成的凸轮机构使冲头4上下运动,以达到冲压的目的,试绘出其机构运动简图,分析是否能实现设计意图,并提出修改方案。
解:机构简图如下:机构不能运动。
可修改为:1725323143=-⨯-⨯=--====hlhlppnFppn,,或11524323154=-⨯-⨯=--====hlhlppnFppn,,2—6 计算图示自动送料剪床机构的自由度,并指出其中是否有复合铰链、局部自由度或虚约束。
河科大机械设计作业第12.13章作业解答[1]
![河科大机械设计作业第12.13章作业解答[1]](https://img.taocdn.com/s3/m/b711f5d0ce2f0066f5332219.png)
第十二章滑动轴承一、分析与思考题12-20 在滑动轴承上开设油孔和油槽时应注意哪些问题?答: 1、应开设在非承载区;2、油槽沿轴向不能开通。
12-21 一般轴承的宽径比在什么范围内?为什么宽径比不宜过大或过小?答:一般B/d为0.3—1.5;B/d过小,承载面积小,油易流失,导至承载能力下降。
但温升低;B/d过大,承载面积大,油易不流失,承载能力高。
但温升高。
12-22 滑动轴承常见的失效形式有哪些?答:磨粒磨损,刮伤,咬粘(胶合),疲劳剥落和腐蚀。
12-23 对滑动轴承材料的性能有哪几方面的要求?答: 1、良好的减摩性,耐磨性和抗咬粘性。
2、良好的摩擦顺应性,嵌入性和磨合性。
3、足够的强度和抗腐蚀能力。
4、良好的导热性、工艺性、经济性。
12-24 在设计滑动轴承时,相对间隙ψ的选取与速度和载荷的大小有何关系?答:速度愈高,ψ值应愈大;载荷愈大,ψ值应愈小。
12-25 验算滑动轴承的压力p、速度v和压力与速度的乘积pv,是不完全液体润滑滑轴承设计的内容,对液体动力润滑滑动轴承是否需要进行此项验算?为什么?答:也应进行此项验算。
因在起动和停车阶段,滑动轴承仍处在不完全液体润滑状态。
另外,液体动力润滑滑动轴承材料的选取也是根据[p]、[pv]、[v]值选取。
12-26 试说明液体动压油膜形成的必要条件。
答: 相对滑动的两表面间必须形成收敛的楔形间隙;有相对速度,其运动方向必须使油由大端流进,小端流出; 润滑油必须有一定的粘度,且充分供油; 12-27 对已设计好的液体动力润滑径向滑动轴承,试分析在仅改变下列参数之一时,将如何影响该轴承的承载能力。
⑴ 转速n=500r/min 改为n=700r/min ; ⑵ 宽径比B/d 由1.0改为0.8;⑶ 润滑油由采用46号全损耗系统用油改为68号全损耗系统用油 ⑷ 轴承孔表面粗糙度由R z =6.3μm 改为R z =3.2μm 。
答:(1)承载能力↑ (2)承载能力↓ (3)η↑,承载能力↑(4)R Z ↓,允许h min ↓,偏心率↑,承载能力↑。
机械设计作业答案(河科大版)
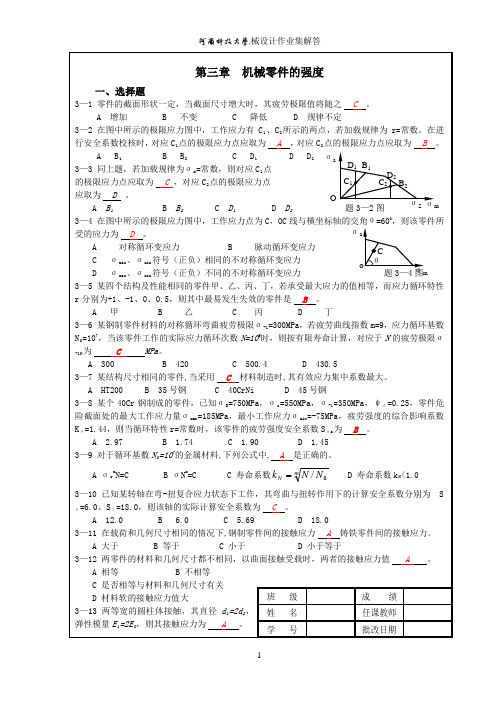
SσSτ
2 2 Sσ + Sσ
≥ [ S ] 检验。
班 姓 学
-3-
级 名 号
成
绩
任课教师 批改日期
机械设计作业集解答
四、设计计算题
3—27 某材料的对称循环弯曲疲劳极限应力σ -1 =350Mpa,疲劳极限σ S =550Mpa,强度极限 6 4 5 7 σ B =750Mpa,循环基数 N 0 =5×10 ,m=9,试求对称循环次数 N 分别为 5×10 、5×10 、5×10 次时 的极限应力。 解: ∴ ∵ ,
m
B σN =C
m
C 寿命系数 k N =
m
N / N0
D 寿命系数 k N <1.0
3—10 已知某转轴在弯-扭复合应力状态下工作,其弯曲与扭转作用下的计算安全系数分别为 S C 。 σ =6.0、S τ =18.0,则该轴的实际计算安全系数为 A 12.0 B 6.0 C 5.69 D 18.0 3—11 在载荷和几何尺寸相同的情况下,钢制零件间的接触应力 A 铸铁零件间的接触应力。 A 大于 B 等于 C 小于 D 小于等于 3—12 两零件的材料和几何尺寸都不相同,以曲面接触受载时,两者的接触应力值 A 。 A 相等 B 不相等 C 是否相等与材料和几何尺寸有关 班 级 成 绩 D 材料软的接触应力值大 3—13 两等宽的圆柱体接触,其直径 d 1 =2d 2 , 姓 名 任课教师 弹性模量 E 1 =2E 2 ,则其接触应力为 A 。
d1
A
D
题 3—14 图 3—15 在上题 A 图中,d 2 =2d 1 ,小圆柱的弹性模量为 E 1 ,大圆柱的弹性模量为 E 2 ,E 为一定值, 大小圆柱的尺寸及外载荷 F 一定,则在以下四种情况中, D 的接触应力最大, A 的接触应 力最小。 A E 1 =E 2 =E/2 B E 1 =E、E 2 =E/2 C E 1 =E/2、E 2 =E D E 1 =E 2 =E
机械制造基础第十章铸造习题解答
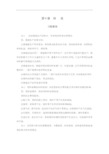
第十章铸造习题解答10-1 试述铸造生产的特点,并举例说明其应用情况。
答:铸造生产的特点有:①铸造能生产形状复杂,特别是内腔复杂的毛坯。
例如机床床身、内燃机缸体和缸盖、涡轮叫叶片、阀体等。
②铸造的适应性广。
铸造既可用于单件生产,也可用于成批或大量生产;铸件的轮廓尺寸可从几毫米至几十米,重量可从几克到几百吨;工业中常用的金属材料都可用铸造方法成形。
③铸造成本低。
铸造所用的原材料来源广泛,价格低廉,还可利用废旧的金属材料,一般不需要价格昂贵的设备。
④铸件的力学性能不及锻件,一般不宜用作承受较大交变、冲击载荷的零件。
⑤铸件的质量不稳定,易出现废品。
⑥铸造生产的环境条件差等。
10-2 型砂由哪些材料组成?试述型砂的主要性能及其对铸件质量的影响。
答:型砂由原砂、粘结剂和附加物组成。
型砂的主要性能有:①耐火度。
型砂的耐火度好,铸件不易产生粘砂缺陷。
②强度。
若强度不足,铸件易产生形状和砂眼等缺陷。
③透气性。
透气性差,浇注时产生的气体不易排出,会使铸件产生气孔缺陷。
④可塑性。
可塑性好,造型时能准确地复制出模样的轮廓,铸件质量好。
⑤退让性。
退让性不好,易使铸件收缩时受阻而产生内应力,引起铸件变形和开裂。
10-3 试列表分析比较整模造型、分模造型、挖砂造型、活块造型和刮板造型的特点和应用情况。
答:列表进行比较:10-4 试结合一个实际零件用示意图说明其手工造型方法和过程。
答:以双联齿轮毛坯手工造型为例,手工造型过程如下:①造下砂型——②造上砂型——③开外浇口、扎通气孔——④起出模样——⑤合型——⑥浇注铁水——⑦带浇口铸件。
10-5 典型浇注系统由哪几个部分组成?各部分有何作用?答:典型浇注系统由浇口杯、直浇道、横浇道和内浇道组成。
浇口杯的作用是将来自浇包的金属引入直浇道,缓和冲击分离熔渣。
直浇道为一圆锥形垂直通道,其高度使金属液产生一定的静压力,以控制金属液流入铸型的速度和提高充型能力。
横浇道分配金属液进入内浇道,并起挡渣的作用,它的断面一般为梯形,并设在内浇道之上,使得上浮的熔渣不致流入型腔。
铸造复习题-全套题目+正确答案
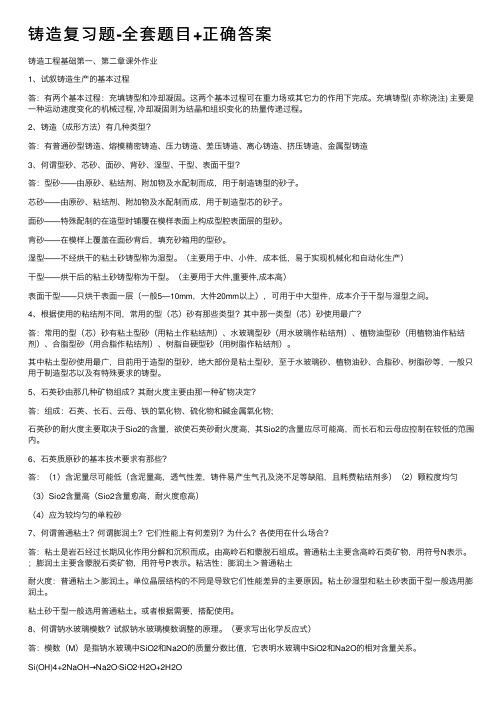
铸造复习题-全套题⽬+正确答案铸造⼯程基础第⼀、第⼆章课外作业1、试叙铸造⽣产的基本过程答:有两个基本过程:充填铸型和冷却凝固。
这两个基本过程可在重⼒场或其它⼒的作⽤下完成。
充填铸型( 亦称浇注) 主要是⼀种运动速度变化的机械过程, 冷却凝固则为结晶和组织变化的热量传递过程。
2、铸造(成形⽅法)有⼏种类型?答:有普通砂型铸造、熔模精密铸造、压⼒铸造、差压铸造、离⼼铸造、挤压铸造、⾦属型铸造3、何谓型砂、芯砂、⾯砂、背砂、湿型、⼲型、表⾯⼲型?答:型砂——由原砂、粘结剂、附加物及⽔配制⽽成,⽤于制造铸型的砂⼦。
芯砂——由原砂、粘结剂、附加物及⽔配制⽽成,⽤于制造型芯的砂⼦。
⾯砂——特殊配制的在造型时铺覆在模样表⾯上构成型腔表⾯层的型砂。
背砂——在模样上覆盖在⾯砂背后,填充砂箱⽤的型砂。
湿型——不经烘⼲的粘⼟砂铸型称为湿型。
(主要⽤于中、⼩件,成本低,易于实现机械化和⾃动化⽣产)⼲型——烘⼲后的粘⼟砂铸型称为⼲型。
(主要⽤于⼤件,重要件,成本⾼)表⾯⼲型——只烘⼲表⾯⼀层(⼀般5—10mm,⼤件20mm以上),可⽤于中⼤型件,成本介于⼲型与湿型之间。
4、根据使⽤的粘结剂不同,常⽤的型(芯)砂有那些类型?其中那⼀类型(芯)砂使⽤最⼴?答:常⽤的型(芯)砂有粘⼟型砂(⽤粘⼟作粘结剂)、⽔玻璃型砂(⽤⽔玻璃作粘结剂)、植物油型砂(⽤植物油作粘结剂)、合脂型砂(⽤合脂作粘结剂)、树脂⾃硬型砂(⽤树脂作粘结剂)。
其中粘⼟型砂使⽤最⼴,⽬前⽤于造型的型砂,绝⼤部份是粘⼟型砂,⾄于⽔玻璃砂、植物油砂、合脂砂、树脂砂等,⼀般只⽤于制造型芯以及有特殊要求的铸型。
5、⽯英砂由那⼏种矿物组成?其耐⽕度主要由那⼀种矿物决定?答:组成:⽯英、长⽯、云母、铁的氧化物、硫化物和碱⾦属氧化物;⽯英砂的耐⽕度主要取决于Sio2的含量,欲使⽯英砂耐⽕度⾼,其Sio2的含量应尽可能⾼,⽽长⽯和云母应控制在较低的范围内。
6、⽯英质原砂的基本技术要求有那些?答:(1)含泥量尽可能低(含泥量⾼,透⽓性差,铸件易产⽣⽓孔及浇不⾜等缺陷,且耗费粘结剂多)(2)颗粒度均匀(3)Sio2含量⾼(Sio2含量愈⾼,耐⽕度愈⾼)(4)应为较均匀的单粒砂7、何谓普通粘⼟?何谓膨润⼟?它们性能上有何差别?为什么?各使⽤在什么场合?答:粘⼟是岩⽯经过长期风化作⽤分解和沉积⽽成。
铸造习题参考答案

铸造习题参考答案铸造习题参考答案铸造是一种传统的金属加工工艺,它通过将熔化金属倒入铸型中,使其冷却凝固成为所需形状的工件。
在学习和实践铸造过程中,习题是不可或缺的一部分,它们能够帮助我们巩固知识,理解铸造的原理和技术。
下面是一些常见铸造习题的参考答案,希望能对大家的学习有所帮助。
习题一:什么是铸造?请简要描述铸造的工艺流程。
答案:铸造是一种将熔化金属倒入铸型中,使其冷却凝固成为所需形状的工件的金属加工工艺。
铸造的工艺流程包括模具制备、熔炼金属、浇注、冷却凝固、脱模和后处理等步骤。
首先,根据工件的形状和尺寸,制备出相应的铸型。
然后,将金属加热至熔化温度,得到熔融金属。
接着,将熔融金属倒入铸型中,使其充满整个铸型腔体。
在金属冷却凝固过程中,形成所需的工件形状。
待金属完全凝固后,进行脱模,取出铸件。
最后,对铸件进行必要的后处理工艺,如去除毛刺、修整尺寸等。
习题二:铸造中常用的铸型材料有哪些?它们的特点是什么?答案:铸造中常用的铸型材料主要包括砂型、金属型和陶瓷型等。
砂型是最常见的铸型材料,其主要成分是砂粒和黏结剂。
砂型具有成本低、制备简单、适用范围广的特点,但耐火性和表面粗糙度较差。
金属型由金属材料制成,具有良好的耐火性和导热性能,适用于高温铸造。
陶瓷型是一种高温材料,具有较好的耐火性和表面光滑度,适用于高精度铸造。
不同的铸型材料适用于不同的铸造工艺和要求。
习题三:请简要介绍常见的铸造缺陷及其原因。
答案:常见的铸造缺陷包括气孔、夹杂、缩孔、砂眼、砂洞等。
气孔是由于金属中存在气体,在凝固过程中形成的孔洞。
夹杂是指金属中杂质的存在,如氧化物、硫化物等。
缩孔是由于金属凝固收缩不均匀而形成的孔洞。
砂眼是指铸件表面出现的小孔洞,通常是由于砂型中的气体无法排出所致。
砂洞是指铸件表面出现的凹陷,通常是由于砂型中的砂粒脱落或砂芯移位所致。
这些缺陷的形成原因多种多样,包括金属液质量不佳、铸造工艺参数不合理、铸型材料质量差等。
黄河科技学院年之年机械制造工艺学考试习题集及参考答案要点
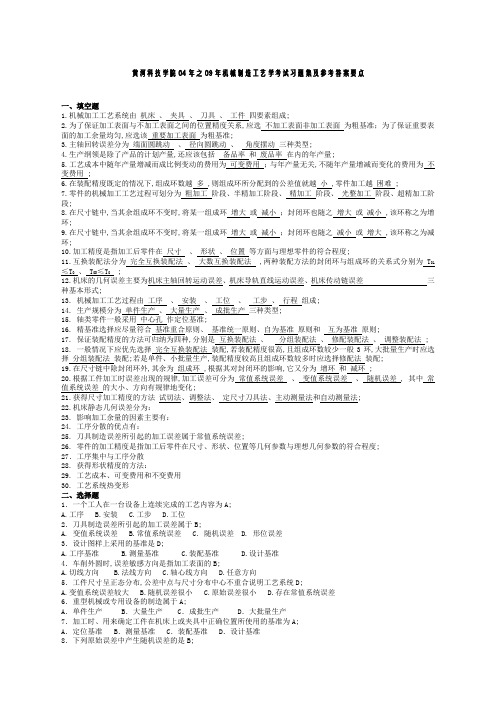
黄河科技学院04年之09年机械制造工艺学考试习题集及参考答案要点一、填空题1.机械加工工艺系统由机床、夹具、刀具、工件四要素组成;2.为了保证加工表面与不加工表面之间的位置精度关系,应选不加工表面非加工表面为粗基准;为了保证重要表面的加工余量均匀,应选该重要加工表面为粗基准;3.主轴回转误差分为端面圆跳动、径向圆跳动、角度摆动三种类型;4.生产纲领是除了产品的计划产量,还应该包括备品率和废品率在内的年产量;5.工艺成本中随年产量增减而成比例变动的费用为可变费用;与年产量无关,不随年产量增减而变化的费用为不变费用 ;6.在装配精度既定的情况下,组成环数越多 ,则组成环所分配到的公差值就越小 ,零件加工越困难 ;7.零件的机械加工工艺过程可划分为粗加工阶段、半精加工阶段、精加工阶段、光整加工阶段、超精加工阶段;8.在尺寸链中,当其余组成环不变时,将某一组成环增大或减小;封闭环也随之增大或减小 ,该环称之为增环;9.在尺寸链中,当其余组成环不变时,将某一组成环增大或减小;封闭环也随之减小或增大 ,该环称之为减环;10.加工精度是指加工后零件在尺寸、形状、位置等方面与理想零件的符合程度;11.互换装配法分为完全互换装配法、大数互换装配法 ,两种装配方法的封闭环与组成环的关系式分别为 T OL ≤T O、 T OS≤T O ;12.机床的几何误差主要为机床主轴回转运动误差、机床导轨直线运动误差、机床传动链误差三种基本形式;13. 机械加工工艺过程由工序、安装、工位、工步、行程组成;14. 生产规模分为单件生产、大量生产、成批生产三种类型;15. 轴类零件一般采用中心孔作定位基准;16. 精基准选择应尽量符合基准重合原则、基准统一原则、自为基准原则和互为基准原则;17. 保证装配精度的方法可归纳为四种,分别是互换装配法、分组装配法、修配装配法、调整装配法 ;18. 一般情况下应优先选择完全互换装配法装配,若装配精度很高,且组成环数较少一般3环,大批量生产时应选择分组装配法装配;若是单件、小批量生产,装配精度较高且组成环数较多时应选择修配法装配;19.在尺寸链中除封闭环外,其余为组成环 ,根据其对封闭环的影响,它又分为增环和减环 ;20.根据工件加工时误差出现的规律,加工误差可分为常值系统误差、变值系统误差、随机误差 , 其中常值系统误差的大小、方向有规律地变化;21.获得尺寸加工精度的方法试切法、调整法、定尺寸刀具法、主动测量法和自动测量法;22.机床静态几何误差分为:23. 影响加工余量的因素主要有:24. 工序分散的优点有:25. 刀具制造误差所引起的加工误差属于常值系统误差;26. 零件的加工精度是指加工后零件在尺寸、形状、位置等几何参数与理想几何参数的符合程度;27.工序集中与工序分散28. 获得形状精度的方法:29. 工艺成本、可变费用和不变费用30. 工艺系统热变形二、选择题1.一个工人在一台设备上连续完成的工艺内容为A;A.工序B.安装C.工步D.工位2.刀具制造误差所引起的加工误差属于B;A. 变值系统误差B.常值系统误差C. 随机误差D. 形位误差3.设计图样上采用的基准是D;A.工序基准B.测量基准C.装配基准D.设计基准4.车削外圆时,误差敏感方向是指加工表面的B;A.切线方向B.法线方向C.轴心线方向D.任意方向5.工件尺寸呈正态分布,公差中点与尺寸分布中心不重合说明工艺系统D;A.变值系统误差较大B.随机误差很小C.原始误差很小D.存在常值系统误差6.重型机械或专用设备的制造属于A;A.单件生产 B.大量生产C.成批生产 D.大批量生产7.加工时、用来确定工件在机床上或夹具中正确位置所使用的基准为A;A.定位基准 B.测量基准 C.装配基准 D.设计基准8.下列原始误差中产生随机误差的是B;A .原理误差B .定位误差C .刀具磨损D .工件热变形9.加工轴类零件时,能保证各外圆表面的同轴度以及各外圆表面与端面的垂直度要求的定位基准是B;A .外圆B .中心孔C .端面D .中心面10.D 是指:利用电能、化学能、声能或热能等来去除工件余量的一些加工方法,国外又称其为非传统加工工艺;A .磨削加工B .机械加工C .传统加工D .特种加工11.制订加工工艺规程的最基本的原始资料是B;A .装配图B .零件图C .工序图D .毛坯图三、判断题1、加工误差是原始误差的如实反映; ×2、切削加工时,若工件公差T ≥ 6σ就不会产生废品; ×3、加工零件时应尽量选择工艺能力系数大的加工方法; ×4、采用滑动轴承时,车床主轴轴颈的形状精度对主轴的回转精度影响较大,而轴承孔的形状精度对主轴的回转精度影响较小; ∨5、由于粗基准对精度要求不高,所以粗基准可多次使用; ×6、选择加工方法时,工艺能力越强越好; ×7、某工序的工艺能力系数Cp >1,尺寸分布中心与工件公差中点重合,则该工序不会产生废品; ×8、拟定工艺路线时,目前的趋势是采用工序集中原则; ∨9、采用修配装配法可以获得很高的装配精度,所以应该优先选择这种装配方法; ×10、安排加工顺序时应先加工定位基准面,后加工其他表面; ∨11. 若一孔与轴的配合精度很高,需采用分组互换法装配,孔的公差值应大于轴的公差值;12. 车床导轨在水平面内的直线度误差对工件的加工精度影响较大,而在垂直面内的直线度误差对工件的加工精度影响较小;13. 加工零件时应尽量选择工艺能力系数大的加工方法; ×14. 在传动链中低速传动件的精度应高于高速传动件; ×15. 一批工件的尺寸在公差范围内呈正态分布,说明这批工件的变值系统误差很小; ×16. 刀具磨损引起的加工误差属于变值系统误差; ∨17. 为了减少工件的装卡次数,工件一次装卡后应完成从粗加工到精加工的全部工序内容; ×18. 安排加工顺序时应先加工定位基准面,后加工其他表面; ∨19. 工艺基准是在制造工艺过程中采用的基准; ∨20. 拟定工艺路线时,目前的趋势是采用工序集中原则; ∨21. 工艺系统达到热平衡后会产生变值系统误差;22.相同的原始误差在误差敏感方向上产生的加工误差比误差非敏感方向上要小;23. 工件上各点的受力变形相同,则只产生尺寸误差而不产生形状误差;24. 工序的最小余量包括上道工序尺寸的公差值;四、名词解释与简答1.生产纲领:企业在计划期内应当生产的产品产量和进度计划,通常以年,所以又称年产量;其计算方式是:N=Qn1+a1+b;N ——零件的年产量件/年;Q ——产品的年产量台/年;n ——每台产品中,该零件的数量件/台;a ——备品的百分率;b ——废品的百分率;2.工艺规程:规定产品和零部件制造工艺过程和操作方法等的工艺文件称为工艺规程;3.工序:一个工人一组人,在一台设备工作地点上,连续完成的工艺内容;4.工艺过程: 改变生产对象的形状、尺寸、相对位置和性质等,使其成为成品或半成品的过程;5.设计基准: 设计图样时所采用的基准;6.加工余量: 加工过程中所切除的金属层厚度,包括工序余量与总余量;7.精基准的选择原则:基准重复的原则、基准统一的原则、自为基准的原则、互为基准的原则;8.最短尺寸链原则:因为当封闭环公差一定时,若尺寸链环数多,则每个组成环分得的公差值较少,制造时比较困难,而当各组成环公差值一定时,若尺寸链环数多,则封闭环的公差就较大,所以应采用最短尺寸链原则;9. 误差传递系数:10. 机床导轨副误差的三种形式及其对加工产生的影响五、计算1、一批工件其部分工艺过程为:车外圆至mm 006.05.40-φ;渗碳淬火;磨外圆至mm 003.040-φ;磨外圆后须保证渗碳层深度~1mm;试计算渗碳工序的渗碳深度t 及其偏差,并画出尺寸链图;假设各尺寸均为正态分布; 答:因须保证加工后的渗碳层的深度为—1.0 mm 表示为03.00.1- ;依题意可做出该加工过程中的尺寸链图如图,则加工后的渗碳层尺寸为该尺寸链中的封闭环,尺寸:0015.020-为减环,t 与0030.025.20-为增环;基本尺寸:=t+t= mm偏差计算:0=0+ES t ==+EI t +0EI t =015.0270.025.1+-=t mm 2、磨削一批d = 30±0.02 mm 的小轴,抽取若干件加工的工件测量直径,求得算术平均值为Φ30.008 mm,已知该工序的标准偏差σ=0.003 mm, 已知这批工件的尺寸分布为正态分布;1、计算这批工件的最大尺寸及最小尺寸;2、问该批工件的常值系统误差、变值系统误差、随机误差为多少答:1、依题意,可知:008.30=X mm ,003.0=σ mm ;则该批工件的最大尺寸为:dmax =X + 3 σ = + 3 × = mm 该批工件的最小尺寸为:dmin =X- 3 σ = - 3 × = mm 2、首先计算工艺能力系数C PT = = C P = >1工艺能力系数C P=>1,说明工艺能力过高,允许出现异常波动,不一定经济; 工件最大尺寸为:30.017 mm ,工件的最小尺寸为29.999 mm ;按6σ得工件的最大尺寸为σ3+X =<按6σ得工件的最小尺寸为σ3-X => 不可能产生不可修复的废品; 依题意,该批工件的尺寸为正态分布,因此,其总体平均值 μ= 0 总体标准偏差 σ =1故:其常值性系统误差为 :其变值系统误差为:0随机误差为:03、在加工如图所示的零件时,图样要求保证尺寸8±0.1mm,因这一尺寸不便于测量,只能通过度量尺寸L 来间接保证,试用极值法求工序尺寸L 及其偏差;要求:画出尺寸链图;判定封闭环、增环、减环;计算工序尺寸及其偏差;入体原则标注;验算封闭环尺寸公差;答:1如图20.18±为封闭环,005.040-和L 为增环,0.0528±为减环;3按基本尺寸公式求尺寸L8=40+L-28L=20按上偏差公式求ES A+ =0+ES L -ES L = +同理:EI L = +则:15.010.020+-=A mm4按入体原则:020.015.20-=A mm 或 35.0080.19+=A mm 5按极值法验算:如果尺寸L 加工到最小,即为19.80mm 时,尺寸40mm 也为最小 尺寸28则为最大时,有- - = mm如果尺寸L 加工到最大,即为20.15mm 时,尺寸40mm 为最大,尺寸28mm 为最小时,– – = mm满足设计要求4、已知工艺系统的误差复映系数为,工件毛坯的椭圆度误差为0.6mm,若本工序加工后要求工件形状精度公差为0.01mm,问至少加工几次方能使形状精度合格试计算工件加工后的形状误差是多少解:已知 ε= , Δm =0.6 mm , Δw =0.01 mm ;设该工序的进给量λ均为 1,则有Δw = λn ×εn ×Δm=1× ×n = ≈ 3 次加工后的工件形状误差 Δw =λn ×εn ×Δm = 13× × = mm5、如图1为齿轮内孔及键槽尺寸,键槽深度尺寸为442.00+mm;加工顺序为: 1精镗内孔至φ39.606.00+mm ;2插键槽深至尺寸A 1;3热处理;4磨内孔至φ4004.00+mm;试用尺寸链极值解法;求:1画出尺寸链图;2判定封闭环、增环、减环;3 计算尺寸A 1及其偏差;4按入体原则标注;5 验算封闭环尺寸公差;答:1如图23.0046+为封闭环,A 和025.0020+为增环,05.008.19+为减环;3按基本尺寸公式求尺寸A46=20+A —19.8A=按上偏差公式求ES A+=++ES A —0ES A =同理:EI A =则:275.005.080.45++=A4按入体原则:225.0085.45+=A5 6、某零件的材料为1Cr13Mo,其内孔的加工工序如下:1车内孔至尺寸14.008.31+φmm;2液态碳氮共渗,共渗层厚度为t;3磨内孔至035.0010.032++φmm,并保证液体碳氮共渗层厚度为—0.3mm;试求工序尺寸t 及其偏差;答:所要保证的共渗层的厚度—表示为1.02.0±,为封闭环,0175.0005.016++为减环,t 与07.009.15+为增环, 基本尺寸:=t+t=偏差计算:=+ES t ==0+EI t =035.00825.03.0+-=t mm7、在磨床上加工销轴,要求外径016.0043.012--=d,抽样后测得974.11=X ,005.0=σ,其尺寸分布符合正态分布,试分析该工序的加工质量;1 2 3 4 0.3413 0.4772 0.49865 0.499968首先计算工艺能力系数C P C P = <1工艺能力系数CP=<1,说明工艺能力不足,因此会出现不合格的产品,工件最大尺寸为:,工件的最小尺寸为;按6σ得工件的最大尺寸为σ3+X =>可产生可修复废品;σ3-X =>不可能产生不可修复的废品;废品率Q=πσ2 ,Z= =2,)(z φ=,故Q=)(z φ=%六、综合分析1、 横向磨内孔,磨后加工表面呈何形状;答:横向磨内孔时,在切削力、重力等作用下,工艺系统将产生相应的变形,导致工件加工表面产生带有锥度的圆柱度误差;如图所示2、 从热变形分析,磨削加工机床导轨上表面,冷却后导轨上表面呈何形状;试分析哪个位置高哪个位置低;答:由于机床床身导轨上表面温度比床身底面温度高,形成了温差,因此,对于床身将产生弯曲变形,呈现出沿导轨长度方向的中间高,两端低的形状;如图所示3、车削细长轴时,工件左端用三爪卡盘夹持,工件右端由尾座顶尖顶紧,试从受力变形分析工件加工后呈何形状答:在车削细长轴时,由于切削力、惯性力,夹紧力以及重力的作用,工件将产生弯曲变形,加工后呈现出腰鼓形的圆柱度误差;如图所示; σX X -。
华中科技大学机械制造工艺基础部分课后答案
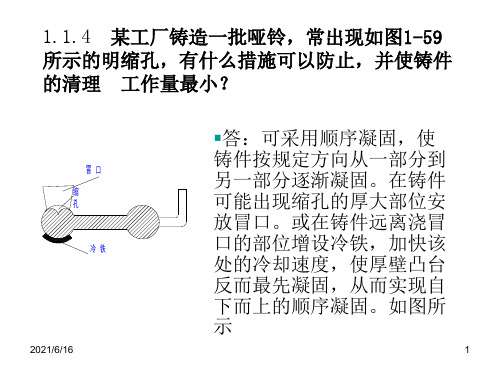
2.4.4 用Φ50冲孔模具来生产Φ50落料件能否保证冲压件的精度?为什么?
答:不能。冲孔模的设计以凸模为基准,考虑到磨损,凸模取合乎公差要求的 最大值,因而,使用冲孔模,来生产落料件,尺寸偏大。
2.4.5 用Φ250×1.5板料能否一次拉深成直径为Φ50的拉深件?应采取哪些措 施才能保证正常生产?如果为多次拉深,请设计每次拉深系数。
2021/6/16
13
图 2-57 不同的零件
2.2.9 图2-58所示零件采用模锻方法制坯,设计上有哪些不合理的地方?为什 么?
2021/6/16
14
不合理的地方如图:
1.应设计为圆角,减小金属流动时的摩 擦阻力和使金属液更厚,不然金属容易冷却, 不易充满模膛;
2021/6/16
17
3.2.11 产生焊接应力与变形的原因是什么?焊接过程中和焊后,焊缝区 纵向受力是否一样?清除和防止焊接应力有哪些措施?
答:焊接过程的加热和冷却受到周围冷金属的约束,不能自由膨胀和收 缩。当约束很大时,则会产生残余应力,无残余变形。当约束很小时, 既产生残余应力,又产生残余变形。 采取以下措施可以防止或消除焊接应力: (1)焊接不要有密集交叉,截面和长度也要尽可能小,以减少焊接局 部加热,从而减少焊接应力。 (2)采取合理的焊接顺序,使焊缝能够自由收缩,以减少应力。 (3)采用小线能量,多层焊,也可减少焊接应力。 (4)焊前预热可以减少工件温差,也能减少残余应力。 (5)当焊缝还处于较高温度时,锤击焊缝使金属伸长,也能减少焊接 残余应力。
焊缝 2~6,8~10,
T形接头,不 开坡口
焊缝7
2021/6/16
- 1、下载文档前请自行甄别文档内容的完整性,平台不提供额外的编辑、内容补充、找答案等附加服务。
- 2、"仅部分预览"的文档,不可在线预览部分如存在完整性等问题,可反馈申请退款(可完整预览的文档不适用该条件!)。
- 3、如文档侵犯您的权益,请联系客服反馈,我们会尽快为您处理(人工客服工作时间:9:00-18:30)。
第一章 1.用平板压实时,砂型内的应力大体如何分布?在没有模样情况下,平板压实后,砂型内哪些点的紧实度较低,哪些点的紧实度较高? 平板慢速压实时,在砂型中心的高度上,紧实度的差别不大,在大约相当于砂型宽度2/3的深度上,出现极大值。
在砂型的边角处,紧实度上高下低,特别是下边模板的边角处,紧实度很低。
平板高速压实时,紧实度分布呈C 形,顶部及底部应力高,中部应力较低。
型砂下面模板的边角处和砂型中心最高处紧实度较低,砂型宽度2/3深度紧实度较高。
2.为什么减小压缩比的差别能使压实紧实度均匀化?有哪些减小压缩比的方法? 1)210δδδ分别为压实前的紧实度以及压实后模样四周及模样顶上型砂平均紧实度,其中1δ=0δ+0δh/H 2δ=2δ+0δh/(H-m)。
h/H 和h/(H-m) 为砂柱的压缩比。
由上式可以看出减小压缩比能使1δ约等于2δ,也即是砂型紧实度均匀化。
2)方法:用油脂作粘结剂或流态砂等湿强度很低的型砂;提高模样顶上砂柱的高度比B=hs/bmin 使B 大于等于1—1.25;适当的提高压实比 3.有哪一些因素能影响射砂时型砂从射砂孔顺利射出? 影响射砂的因素:(1)射砂气压及气压梯度:提高射砂气压,能提高气压梯度,加强气流渗透,使砂能顺利射出。
(2)型砂性能与射砂筒中型砂的紧实:型砂性能 粘结力小,流动性好(油砂,树脂砂);湿强度高,粘结力大的型砂,流动性差,不易出砂,易搭棚。
射筒中型砂的紧实,型砂越紧实,气流渗透阻力越大。
(3)进气方式:采用均匀进气时,有利于射砂。
这时气压梯度密集在锥型射砂孔处,增强气流渗透有利于射砂。
射头边上的等压线比中心密不易搭棚。
但均匀进气的射砂机构设计制造较复杂。
(4)锥型射头与射孔大小:锥形射头使射砂筒的气流向射头集中,增大渗透速度。
有利于射砂。
射孔不易过小,小射孔孔壁对砂粒的射出阻力相对增大,使渗透气流速度减小,不利于射砂,射孔足够大,利于射砂。
4.为什么气冲第一阶段紧实过程可以视为为初实层形成、扩展及冲击过程? 在低紧实度范围内,紧实力提高不大,可使型砂的紧实度提高很多,所以在气压差的作用下,ab 区间的型砂迅速形成一层紧实度较高,对空气渗透阻力较大,对上面下来的气流渗透有一定隔离作用的砂层,这一隔绝层使气体对砂层的推动力变大,使以后的气冲过程成为这一砂层推动下面砂层向下运动及扩大的过程。
这一在气冲紧实的最初所形成的砂层可称为初实层。
初实层以下的紧实主要由于这一初实层的推动及扩展。
砂层的紧实和向下运动像一个快速运动的紧实波向下扩展,直至底板,最后与底板发生冲击。
所以气冲冲击过程可以视为初实层的形成、扩展及冲击过程。
5.以前的砂型都用翻转法起摸,而现在高压造型生产线上却主要用托箱法起摸这是什么原因?翻箱法用于砂型强度较低的砂型起摸而高压造型的砂型强度较高,在起摸过程中不易掉砂,翻转法翻转砂箱耗费机动时间相应的生产效率较低,而且要求机器的结构比较复杂,只有在工艺上必要时才采用,所以高压造型机上虽然砂型较大仍主要用拖箱法。
第二章1.若震击的排气孔因积灰而部分堵塞,这将使造型机的排气上升行程增大还是减小?同时将对整个震击循环有什么影响?排气上升行程增大,因排气孔部分堵塞排气不畅气缸内还有一定的气体压力使惯性行程增大。
影响:如果排气孔部分堵塞排气孔不够大,惯性行程后,缸内气体不能及时排出,则活塞下落时,缸内仍有相当大的气压,会影响震击的力量。
2.若拟对一台震压造型机的震击机构进行测试,对其摩擦阻力R 大小如何测得?利用起动开关或管道阀门,使进气气缸中的空气节流,来调节带负荷的工作台只作上下移动而无撞击。
在这种情 况下,测出示功图,设其面积为f i0,又因e=0,e ’=0,代入FRS FW e e 2,-=-SF F W R 2=便得一次循环中单位面积上的平均摩擦阻力。
3、弹簧式微震压实造型机的工作台下沿与压实活塞上沿间,要留有一定的间隙,为什么?间隙的大小,应怎么考虑?原因:为防止工作台与压实活塞在预震是发生撞击,工作台下沿和压实活塞上沿间,留有一定的间隙Δ,Δ一般为15---20mm 。
4、如果在现场发现弹簧式气动微震压实造型机不能进行压震,你将从哪几个方面去查清原因?原因:运动部件(活塞、震铁和震击缸)的加工精度地,配合过紧或进气通道阻力过大等,而弹簧恢复力(或弹簧刚度)过大往往是不能实现压震的主要原因, 在设计压震机构时,必须对微震弹簧的刚度进行认真的核算。
5.如图2-21的压实机构,设中心导柱的直径为d1,活塞2的外径为d2,而压实缸3的内径为d3,试问用同样的流量,从A 孔进油与从B 、C 孔同时进油,所得的活塞1上升速度相差几倍?又设从C 孔进油的油压为p0,则在中心液压缸内得到多大的油压?224dQ V A ∏=)(42123d d QV BC -∏=222123/)(d d d V V BCA -= 2221230222223/)(44)(d d d P d d d P -=∏-∏=6.设浮动式多触头压头的触头活塞截面积为A ,油压为p ,密封圈等对触头运动的阻力为f ,而压缩弹簧对于伸出的触头的回弹力为Cx(x 为触头伸出的距离),试比较伸出及压进触头对型砂压实力的不同。
对于压进的触头,对型砂压实力=Ap+f ;对于伸出的触头,对型砂压实力=Ap-f-Cx ;因此,两种状态的压实力差= Ap+f-Ap+f+Cx=2f+Cx 7.设在如图2-40那样的四工位热芯核射芯机中,射芯所需时间为10s ,硬化加热时间共需100s ,顶芯及取走砂芯时间为12s ,工位转移所需时间为8s ,试计算机器的循环工作时间和理论生产率。
射完后3次工位转移所需时间3*8=24s ,硬化所需时间100s ,射芯时间10s ,射芯加热硬化所需时间110s ,110s 分配在三个工位转移和三个加热硬化工位,3工位转移用24s ,故3个硬化加热工位需时间110-24=86s ,在每个加热硬化工位需停留时间为86/3=29s ,故机器循环工作时间(29+8)*3=111s ,理论生产率(3600/111)*3=97件。
8.为了改善气冲阀的特性曲线,可以用一些什么方法?除书中介绍的几种方法外,还可能有一些什么方法?使用撞击式气冲阀和中途开阀法别的方法我也不晓得,望分享0.09.垂直分型无箱射压造型机的射砂机构采用二次射砂的目的是什么?这一方法能否用于一般射芯的射砂机构?目的:降低砂型下部的紧实度,提高射砂后期的射砂筒内气压,使型块上部紧实度提高,使最终得到的型块紧实度上下均匀。
可以用于一般射芯的射砂机构10、垂直分型无箱射压造型机的生产率很高,而且造型基本能自动化,但是为什么许多小型铸件的造型仍然希望采用水平分型的脱箱造型机?水平分型下芯和下冷铁比较方便、水平分型,铁液压力主要取决于上半型的高度,比较容易保证铸件质量,有的旧铸造改造,小件往往原来就用手工造型,水平分型可以保持原来的工艺特点,有的模板稍微改装甚至稍加改装就可以用于水平分型的脱箱造型机,比较方便。
第三章1.为完成造型工艺有哪些辅机?为完成砂箱运输的辅机有哪些辅机?生产线主要辅机:为完成铸造工艺过程而设置的辅机有:刮砂装置,扎气孔器,翻箱机,合型机,落箱机,压铁机,浇注机,捅箱机,落砂机,分箱机,清扫机等;为完成砂箱运送而设置的辅机有:升箱机,降箱机,转箱机,推箱机构,挡箱机构等。
2.为什么有的生产线上箱造型机处也设置翻箱机?其动作有何特点?原因:为检查砂型有无缺损、修型及翻落浮砂,之后再翻回原状。
其动作特点:在翻转时砂箱要有可靠的定位夹紧(或限位)装置,在翻转过程中启动和到位时平稳而无冲击。
3.惯性冲击式落砂机与惯性振动落砂机有什么不同?单轴惯性振动落砂机工作原理:落砂栅床被弹簧支承于机坐上,落砂栅床上带有偏重的主轴,当主轴旋转时,由偏重产生的离心力使落砂栅床振动,并与砂箱发生撞击而进行落砂。
单轴惯性振动落砂机特点:整个落砂栅床支承弹簧上,落砂时撞击力一部分被弹簧吸收,主轴及其轴承所受的冲击力小,机器使用寿命长,对机器基础的要求可以降低。
振幅的大小将随载荷的大小而变化。
适用于成批生产。
惯性撞击振动落砂机工作原理:铸型放在固定支架上,下面安置惯性振动落砂机,靠落砂栅床的撞击而进行落砂。
惯性撞击振动落砂机特点:第一,撞击振动落砂机可以保证足够大的振幅。
第二,撞击振动落砂机允许的载荷变化范围远比一般惯性式的大。
第三,在相同载荷情况下撞击落砂机比一般惯性式落砂机消耗功率较小。
4.封闭式与开放式造型生产线各何特点?各适用什么地方?封闭式造型生产线:是采用连续式或脉动式铸型输送机组成不间断地环形流水线开放式造型生产线:是采用间歇式铸型输送机组成直线布置的流水线①开放式的布置对铸型来说能形成一个合适的储存段和较为灵活的冷却段,而封闭的布置较难做到②开放式布线较为灵活,受车间限制小,而封闭布线受车间限制较大③封闭式布置铸型转运少,辅机类型少,对控制系统较为有利,开放式则正相反对于大量生产,连续浇注的铸件来说,不需要铸型的储存,所以选择辅机少的封闭式环形布线较为合适。
而对于品种多而批量较少,周期性浇注的铸件生产,希望有适当的铸型储存不同的型内冷却时间,用开放直线布置较为有利5.什么叫串联分布线及并联分布线?各有什么特点?按照造型机与铸型输送机的位置不同,有两种不同的布置形式,即串联布置和并联布置。
串联式布线特点:是造好的上型从造型机到合型机之间的运行方向。
与造型段或下芯段铸型输送机小车运行方向平行或重迭。
并联式布线特点:是造好的上型从主机到合型机的运行方向与铸型输送机在造型段或下芯段的运行方向垂直或成一定角度。
6.铸型为什么采用二次冷却?有什么特点?二次冷却的优点是在能保证铸件有足够的型内冷却条件下,缩短铸型输送机的展开长度,并减少了砂箱的周转量。
第四章1、砂铁比的大小和变化对回用砂有什么影响,在设计和使用砂处理系统时,应如何考虑因砂铁比变化而带来的一些问题?影响:随着砂铁比得增大,砂温升高逐渐减弱,当砂铁比为10以上时,砂温升趋于平缓和稳定。
在设计和使用砂处理系统时,应按造型线上砂铁比小的铸件考虑系统中的冷却装置和混砂时的新材料补加量,决定对回用砂处理的质量要求:以砂铁比最大、产量最多的铸件和造型线生产能力,确定砂处理系统的生产率。
在安排铸件生产计划时,应将砂铁比不同的铸件合理搭配,力求减少回用砂变化的波动,以稳定型砂制备质量。
2.热砂将带来哪些问题?冷却热砂有几类方法?问题:1)砂温大于60℃,特别是超过70℃时,加入的水分会立即蒸发,很难在混砂时控制水分,制备的型砂性能也不稳定。
2)当型砂温度高于49℃时,其紧实率、透气性、湿压强度和砂型风干强度都会降低;3)型砂中的水蒸气会凝结在较低的砂斗壁和模样上,造成砂斗和模样粘砂;4)用高温型砂紧实的砂型,其表面水分极易散失,使型腔边角处的强度降低,导致铸件缺陷。