冲压工艺学 第四章
冲压工艺学知识要点

板材冲压工艺知识要点绪 论 1.冲压-是通过模具对板材施加压力或拉力,使板材塑性成形,有时对板料施加剪切力而使板 材分离,从而获得一定尺寸、形状和性能的一种零件加工方法。
由于冲压加工经常在材料冷状 态下进行,因此也称冷冲压。
冲压加工的原材料一般为板材或带材,故也称板材冲压。
2.冲压工艺可以分成分离工序和成形工序两大类 。
第一章 冲压成形原理与成形极限1.冲压工艺与厚度变化及破坏形式的关系2.冲压成形工艺的应力状态类别可以用变形区内的静水应力smσ来判别,即 ,压缩类,剪切类=拉伸类00,0<>sm sm sm σσσ3. n 值、r 值与成形性能的关系第二章 冲裁工艺与模具设计1冲裁变形分离过程大致可分为3个阶段。
弹性变形阶段, 塑性变形阶段,断裂分离阶段2冲裁断面可明显地分成4个特征区,即圆角带、光亮带、断裂带和毛刺3降低冲裁力的方法:阶梯凸模冲裁, 斜刃口冲裁4.凸模侧面的磨损最大,是因为从凸模上卸料,长距离摩擦加剧了侧面的磨损.5.确定合理间隙的理论计算法依据主要是:在合理间隙情况下冲裁时,材料在凸、凹模刃口产生的裂纹成直线会合.6. 冲裁模刃口尺寸确定(1)落料模先确定凹模刃口尺寸,其标称尺寸应取接近或等于制件的最小极限尺寸,以保证凹模磨损到一定尺寸范围内,也能冲出合格制件,凸模刃口的标称尺寸比凹模小一个最小合理间隙。
(2)冲孔模先确定凸模刃口尺寸,其标称尺寸应取接近或等于制件的最大极限尺寸,以保证凸模磨损到一定尺寸范围内,也能冲出合格的孔。
凹模刃口的标称尺寸应比凸模大一个最小合理间隙。
7.工件尺寸公差应按“入体”原则标注为单向公差,所谓“入体”原则是指标注工件尺寸公差时应向材料实体方向单向标注,即:落料件正公差为零,只标注负公差;冲孔件负公差为零,只标注正公差。
8.模具工作部分尺寸及公差的计算方法可分为两类。
⑴.凸模与凹模分开加工,是指凸模和凹模分别按图样加工至尺寸。
此种方法适用于圆形或形状简单的工件⑵.凸模和凹模配合加工对于冲制形状复杂或薄板制件的模具,其凸、凹模往往采用配合加工的方法。
ZY-冲压工艺学.doc

绪论内容简介:本章讲述冲压及模具的概念;冲压的特点、发展及应用,冲压工序的分类及基本冲压工序。
学习目的与要求:1、掌握冲压及模具的概念;2、了解冲压冲压的特点、发展及应用;3、掌握冲压工序的分类,认识基本冲压工序。
重点:冲压及模具的概念、冲压的特点、发展及应用,冲压工序的分类。
难点:冲压基本工序。
1.1 冲压的概念1.1.1 冲压冲压:在室温下,利用安装在压力机上的模具对被冲材料施加一定的压力,使之产生分离和塑性变形,从而获得所需要形状和尺寸的零件(也称制件)的一种加工方法。
因为通常使用的材料为板料,故也常称为板料冲压。
冲压成形产品示例一——日常用品:易拉罐、餐盘、垫圈等。
冲压成形产品示例二——兵器产品:子弹壳等。
冲压成形产品示例三——高科技产品:汽车覆盖件、飞机蒙皮等。
1.1.2 冲模冲压模具:将材料加工成所需冲压件的一种工艺装备,称为冲压模具(俗称冲模)1.1.2 冲压生产的三要素:冲压生产的三要素:合理的冲压工艺、先进的模具、高效的冲压设备1.2 冲压加工特点与应用1.2.1 冲压加工的特点(1)生产率高、操作简单。
高速冲床每分钟可生产数百件、上千件。
(2)一般无需进行切削加工,节约原料、节省能源。
(3)冲压件的尺寸公差由冲模来保证,产品尺寸稳定、互换性好。
“一模一样”(4)冲压产品壁薄、量轻、刚度好,可以加工形状复杂的小到钟表、大到汽车纵梁、覆盖件等。
局限性:由于冲模制造是单件小批量生产,精度高,是技术密集型产品,制造成本高。
因此,冲压生产只适应大批量生产。
1.2.2 冷冲压的应用由于冷冲压在技术上和经济上的特别之处,因而在现代工业生产中占有重要的地位。
在汽车、拖拉机、电器、电子、仪表、国防、航空航天以及日用品中随处可见到冷冲压产品。
如不锈钢饭盒,搪瓷盆,高压锅,汽车覆盖件,冰箱门板,电子电器上的金属零件,枪炮弹壳等等。
据不完全统计,冲压件在汽车、拖拉机行业中约占60%,在电子工业中约占85%,而在日用五金产品中占到约90%。
冲压工艺培训资料

Байду номын сангаас
5.国冷轧碳素薄钢板适用牌号:st12、st13、st14、st15、st14-T符号:ST-钢(Steel)、12-普 通级冷轧薄钢板、13-冲压级冷轧薄钢板、14-深冲级冷轧薄钢板、15-特深冲级冷轧薄钢板、 14-T-超级冷轧薄钢板。表面质量:FC-高级的精整表面,FB-较高级的精整表面。表面结构: b-特别光滑、g-平滑、m-无光泽、r-粗糙。标记:产品名称(钢板或钢带)、本产品标准号、 表面质量代号、拉延级别(仅对St14、St14-T、St15)、表面结构、边缘状态(切边EC,不切 边EM)、产品规格及尺寸、外形精度(厚度和/或宽度、长度、不平度)。标记示例:钢板、 标准号Q/BQB403,牌号St14,表面结构为特别平滑(b),表面质量为FC,切边(EC), 厚度0.8mm,A级精度、宽度1200mm,A级精度,长度2000mm,A级精度,不平度为PF.B 精度,标记为:Q/BQB403St14-FC-ZF-b钢板EC:0.8A×1200A×2000A-PF.B产地:
(2)、屈强比σs/σb屈强比小,即σs值小而σb值大,容易产生塑性变形而不易产生拉裂。
(3)、伸长率δ一般地说,伸长率或均匀伸长率是影响翻孔或扩孔成形性能的主要
(4)、硬化指数n单向拉伸硬化曲线可写成σ=Kε,其中指数n即为硬化指数,表示在塑性 变形中材料的硬化程度n偏大时,说明在变形中材料加工硬化严重。
《冲压工艺学》本科教学大纲

《冲压工艺学》教学大纲课程编号:E0331144学时数:48学分数:3适用专业:材料成型及控制工程(本科、模具方向)先修课程:《机械制造基础》、《机械设计基础》、《金属塑性成形原理》、《认识实习》考核方式:平时成绩(实验、作业、课堂提问、考勤)占30%,期末考试占70%。
一、本课程的性质和任务性质:本课程是材料成型及控制工程专业的一门专业课。
通过本课程学习和课程设计,能掌握分析、制定工艺方案和设计冲压模具的方法。
任务:1、初步掌握冲压成形的原理、板料成形规律及其与冲压工艺和模具设计的关系;2、掌握冲压工艺过程的设计方法,具有设计中等复杂程度冲压工艺过程的能力;3、掌握冲压模具的设计方法,具有设计中等复杂程度的冲模及必要的辅助机构的能力;4、具有应用冲压成形基本原理,冲压工艺及冲模设计方法的知识,分析和解决冲压生产中常见的产品质量和模具方面技术问题的能力;5、了解冲压新工艺、新型模具及冲压技术的发展方向。
二、课程内容和要求(一)、理论教学:48学时第一章绪论(2学时)教学内容1、本课程的性质和任务2、冲压加工的地位、种类和发展教学要求1、明确本课程的研究对象和内容,以及学习本课程的目的。
2、了解本课程在培养材料成型专业工程技术人才的地位、任务和作用。
3、了解冲压技术的发展趋势。
第二章冲裁(8学时)教学内容1、冲裁变形机理2、模具间隙3、凸. 凹模刃口尺寸的计算4、冲裁力的计算及降低冲裁力的方法5、排样6、精密冲裁7、其它冲裁法教学要求1、掌握冲裁变形机理和工艺分析方法。
2、掌握冲裁模具设计要点和方法。
3、了解其他冲裁技术。
第三章弯曲(6学时)教学内容1、板料的弯曲现象及其原因2、窄板弯曲和宽板弯曲时的应力应变状态分析3、宽板弯曲时的应力(σθ. σρ. σb)4、弯曲力计算和设备选择5、弯曲件毛坯长度计算6、最小相对弯曲半径rmin/t7、弯曲回弹8、弯曲模工作部分的尺寸计算教学要求1、了解板料的弯曲现象及其原因,能分析板料弯曲时的应力应变状态。
冲压工艺基础知识培训讲义

圈与上模之间必须加导柱
导向。
•
当料厚t > 1.2mm时,可不
加导柱导向。
镶块拉延模
当料厚比较厚大于1.2,拉延 的材料为高强度板,或者客 户有特殊要求时,会考虑用 镶块拉延模。
修边冲孔模结构介绍:下模
下模仁镶块 下模仁 顶料器
工序件废料部分 废料刀 废料盒 定位具 吊耳
导柱组 停止块 绶冲器
修边冲孔模的组成部分:上模
V型中心线:对应的是模具中心。
销孔
数控加工用三销孔进行拉直分中,将机床中心,模具中心, 加工坐标三者合一。
切角拉延
定义:板料拉延成型时,因局部材料流动困 难、易破裂,需要去除局余料,为了节约一 套落料模,而把此项冲裁工序结合到拉延工 序上称切角拉延。
废料斜溜,角度≥15°
•
当料厚t ≤ 1.2mm时,压边
1、上模扣合模块
3、下模(含预弯机构+胎膜+顶 料+传送机构)
2、上模压料芯
1、上模扣合模块 2、上模压料芯 3、下模
包边形式的分类及简单介绍
压合模的简单介绍
包边机构及简单的原理介绍
1、插刀
NO1:预弯
预弯刀块 2、斜楔
NO2:压合
4、压死刀块 5、胎膜
1、插刀 2、斜楔 1、2组合使用
包边形式的分类及简单介绍
拉延模的起吊翻转及安全区
a.起吊、翻转装置:
b.安全区的设计:
一般在模座的前后方向(相 一般情况下,安全圈和上模座上,但有些时
起重棒,规格根据压边圈的重 量确定;如有特殊要求,起重
候,下安全区设计在下模座上, 分布在压边圈的四角,尺寸按 模具大小有
棒也可设计在模座的左右2端。100x100mm,120x120mm,150
冲压工艺与模具设计课程教案

冲压工艺与模具设计课程教案授课教案《冲压工艺与模具设计》20~20学年第一学期学院(部)材料工程学院系(室)材料工程系课程代码总学时64课程类别必修();核心();公选();选修(√)授课专业材料成型及操纵工程授课班级任课教师赵中华职称副教授教案(章节备课)章节第一章绪论教学目的了解冲压工艺的差不多概念,熟悉本专业的历史、现状和进展方向。
了解本课程学习的任务、要紧内容以及要紧的参考文献资料。
重点难点重点:冲压工艺的特点、冲压工艺的差不多工序。
教学内容教学方法教学手段学时分配教学内容:1.介绍冲压工艺的定义、用途及加工范畴。
2.介绍冲压工艺的特点。
3.讲解冲压工艺的两大差不多工序。
4.讲解冲压工艺的材料种类及选用材料的差不多依据。
教学方法:在绪论这一章,讲授时要紧采纳师生互动的教学方法,通过国民经济的进展现状、进展趋势及平常的日常生活中的典型事例,介绍本课程的一些差不多概念。
教学手段:课堂讲授学时分配:2学时章摸索题1.冲压工艺有什么的优缺点?2.冲压常用材料有哪几种?3.选用冲压材料的差不多依据是什么?要紧参考资料1.肖景容主编. 冲压工艺学[M]. 北京:机械工业出版社,19932. 王孝培主编.冲压手册[M]. 北京:机械工业出版社, 19913. S.A.Elenev.PRESSWORKING[M].MOSCOW: MIR PUBLISHERS,1983备注教案(章节备课)学时:18章节第二章冲裁工艺教案(章节备课)学时:16章节第三章冲裁模结构及零件设计教学目的使学生了解冲裁模具的分类方法,通过对各类典型冲裁模的结构分析,对冲裁模的结构及特点有了较深的了解,比较各类模具的特点,把握冲裁模零件的设计要点和设计方法;把握冲裁模封闭高度、压力机封闭高度之间的关系。
重点难点重点:典型冲裁简单模具的结构;各类模具的特点。
难点:冲裁模零件的设计要点和设计方法;冲裁模封闭高度、压力机封闭高度之间的关系。
《冲压工艺学》教学大纲讲课教案

《冲压工艺学》教学大纲《冲压工艺及模具设计》教学大纲开课单位:材料工程系学分:3 总学时:48H(理论教学48学时)课程类别:选修考核方式:考试课程编号:00000000基本面向:材料成型与控制工程专业一、本课程的目的、性质及任务本课程是“材料成型及控制工程”专业三个方向的主干专业课之一,它是一门理论与实践联系很紧密的课程。
冲压工艺理论是模具设计的基础,而模具设计则是实现冲压工艺的核心,学生在学习中两者不可偏废。
本课程的主要任务是使学生掌握各种冲压成形的变形规律,掌握工艺计算方法,判断板料成形难易程度以及掌握各种模具结构与设计要点。
通过学习,能够对中等难度冲压零件进行工艺分析、设计,基本能确定各种冲压零件生产的最佳工艺方案并能够设计冲压模具。
二、本课程的基本要求1、了解国内外冲压工艺及模具技术的发展现状和趋势。
2、掌握冲压工艺的基本成形理论、分析各类冲压件成形工艺特点,具有初步分析各种常见冲压缺陷和提出生产中解决措施的基本能力。
3、能够运用冲压参考书籍和资料,对中等程度的冲压零件进行工艺分析,拟定工艺路线和确定工艺参数,并能设计出技术上可靠、经济上合理的冲压模具。
4、熟悉冲压模具与各种压力机的连接要求。
5、通过冲压理论课程学习和冲压实验课动手能力培养,使学生具有一定的设计能力和科研能力。
三、本课程与其它课程的关系先修课程:《机械制图C》、《机械设计A》、《金属材料及热处理》、《互换性与测量技术基础a》、《机械制造技术基础C》、《材料成形原理》、《材料成形设备》、《模具CAD/CAM》。
在学本课程同时应学《模具制造技术》、《材料成形CAE》《汽车覆盖件模具设计与制造》、《锻造工艺及模具设计》、《塑料成型工艺及模具设计》、《模具寿命及失效分析》、《特种塑性成形技术》、《材料成形技术的新发展(讲座)》。
四、本课程的教学内容第一章绪论(一)冲压生产在国民经济中的地位和作用,冲压生产的特点及优越性,国内外冲压技术的现状及发展趋势;(二)冲压工艺的分类及特点;(三)本课程的基本内容及学习方法。
冲压工艺学 第四章 拉深工艺及模具设计.

拉深工艺及模具设计
(a) 图4-9 拉深件的工艺性
(b)
拉深工艺及模具设计
(5)拉深件的精度要求不宜过高 拉深件的精度包括
拉深件内形或外形的直径尺寸公差、高度尺寸公差等,一般
合适的精度在GB6(IT11)级以下,其精度等级如表4-1所示。 (6)拉深件的尺寸标注应合适 拉深件直径尺寸应明
显注明必须保证外部尺寸或是必须保证内部尺寸,不能同时
2 D d12 6.28rd1 8r 2 d32 d2 )
拉深工艺及模具设计
表4-2 拉深件展开尺寸计算公式(四)
D d12 4d 2 h 6.28rd1 8r 2 或D d12 4d 2 H 1.72rd 2 0.56r 2
2 D d12 2 r2 d1 8r22 4d 2 h 2 r1d 2 4.56r12 d 4 d32
拉深工艺及模具设计
4.1.2 以后各次拉深 通常,当筒形件高度较大时,由于受板料成形极限的限 制,不可能一次拉成,而需要二次或二次以上拉深。以后各 次拉深,就是指由浅筒形件拉成更深筒形件的拉深。 以后各次拉深大致有两种方法:一种是正拉深,如图47(a)所示,另一种是反拉深,如图4-7(b)所示。反拉深就是 将经过拉深的半成品倒放在凹模上再进行拉深。这时,材料 的内、外表面将互相转换。
12
若r1 r2 r3时,则 D d12 4d 2 h 2 r (d1 d 2 ) 4 r 2
拉深工艺及模具设计
表4-2 拉深件展开尺寸计算公式(五)
13
D d12 4d2 h 2 r d1 8r 2 2L(d 2 d3 )
14
D d12 2 r (d1 d2 ) 4 r 2
冲压工艺与模具设计课件(2016)

1.应力状态 2.应变状态 3.屈服准则(塑性条件) 4.塑性变形时应力应变关系
3种主应变状态
9种主应力状态
精品课件
2.3 塑性成形基本规律
1.加工硬化规律 2.卸载弹性恢复规律 3.最小阻力定律 4.塑性变形体积不变
定律
拉深 精品课件 翻孔
胀形
思考题
1.试说明冲压加工的含义 2.简述冲压加工的特点 3.试说明冲压加工的种类 4.简述冲压技术的发展趋势 5.冲压对板料的基本要求有哪些? 6.板料的力学性能对冲压成形性能有哪些影响? 7.常用的冲压原材料有哪几种规格? 8.试列举冲压加工设备的主要类型 9.冲床的主要技术参数与模具有怎样的关系?
3--压力机的级别 63--公称压力 A--改进设计号
C--锤
T--其它 63T开式双柱可倾式第二种改进型压力机
精品课件
指滑块在下死点前 某一位置滑块所具 有的压力。
(2)技术参数 1)公称压力 F
2)公称压力行程 S F 3) 滑块行程S
上死点→下死点
4)滑块行程次数n
上死点→下死点 →上死点
5)压力机的闭合高度
4)根据需方要求,经供需双方协商,可以供应其他尺寸的钢 板
和钢带。
精品课件
2.冲压材料的下料方法
(1)剪板机下料
精品课件
(2)圆盘剪床下料
精品课件
(3)其他下料方法
➢激光切割机 ➢等离子切割机 ➢高压水切割机 ➢电火花线切割机 ➢电冲剪等
精品课件
1.4 冲压设备
冲压设备的选用原则:
➢ 冲压工序的性质:分离或成型工序 ➢ 冲压力的大小:开式、闭式 ➢ 模具结构形式 ➢ 模具闭合高度、轮廓尺寸 ➢ 生产批量 ➢ 生产成本 ➢ 产品质量 ➢ 结合单位现有设备条件
冲压工艺学4弯曲课件

第四章 弯曲
第三节 最小弯曲半径
最小弯曲半径的近似计算:
断面收缩率可表示为:
弯曲最外侧的拉伸应变
=
1+
t
2
1 2 r 1
t
r=( 1 1)t
2
r =( 1 1)
t 2
实际应用: 最小弯曲半径rmin =t Kmin
其中,最小弯曲系数Kmin
1
2max
1,
不必计算,查表4-1可得。
第四章 弯曲
第四节 弯曲卸载后的回弹
二、回弹值的确定(续)
1.大半径自由弯曲( 弯曲系数K r / t 10 )时的回弹值
K>10时,弯曲半径较大,弯曲变形程 度较小,弹性变形的影响较大,回弹 明显。
凸模工作部分的圆角半径可按下式
进行计算:
卸载前弯曲半径,
rp
即凸模圆角半径
卸载后弯曲半径
rp
1
r
第四章 弯曲
第三节 最小弯曲半径
2.提高弯曲极限变形程度的方法 (1)经冷变形硬化的材料,可热处理后再弯曲。 (2)清除冲裁毛刺,或将有毛刺的一面处于弯曲受压的内缘。 (3)对于低塑性的材料或厚料,可采用加热弯曲。 (4)采取两次弯曲的工艺方法,中间加一次退火。 (5)对较厚材料的弯曲,如结构允许,可采取开槽后弯曲。
三、影响回弹值的因素
1.材料的力学性能 S / E 越大,回弹越大。
材料的力学性能对回弹值的影响 1、3-退火软钢 2-软锰黄铜 4-经冷变形硬化的软钢
第四章 弯曲
第四节 弯曲卸载后的回弹
三、影响回弹值的因素(续)
2.弯曲系数 K r / t
K越大,弹性变形在总变形 的比例越大,回弹就越大。
《锻造冲压工艺学》幻灯片

• III 热模锻车间
•
产品:模锻件
•
原材料:棒材
•
生产方式:大批量
•
设备:蒸汽-空气模锻锤
•
热模锻压力机
•
平锻机
•
螺旋压力机
•
模锻水压机
• IIV 冷锻车间
•
产品:通用件或标准件
•
原材料:冷拉棒材、卷材
•
生产方式:大批量,多品种
•
设备:冷挤压机、冷墩机等
• V 冲压车间
•
2、 钢加热过程中应注意的四点现象:氧化、脱碳、过热、过烧 (1)氧化 氧化性气体〔O2,CO2,H2O和SO2〕与钢发生反响。 例如 Fe+(1/2)O2→←FeO (2)脱碳 化学反响造成钢外表层碳含量的减少叫脱碳。 例如 Fe3C+O2→←3Fe+CO2 (3) 过热 温度过高造成晶粒粗大。 (4)过烧 加热到接近熔化温度并在此温度下长期保存,不仅晶 粒粗大,而且晶界熔化。
冲压件数量是锻压件的几倍。 D 锻压与其它成形方法〔轧制、挤压、拉伸等〕比照锻压指向品
种多而复杂的坯料或零件。轧制、挤压、拉伸等指向板、带、
3.3 开展方向 A 设备向巨型化开展。
一组数据说明:70万KN模锻水压力机〔液体压力传动〕 12万KN热模锻压力机〔机械传动〕 145万KJ 对击锤 11万KN螺旋压力机
2、锻压加工的主要方法如图1和图2所示。
热锻
冷锻
自由锻 在上下工具
之间成形
模锻 模腔中成形
冷挤
ቤተ መጻሕፍቲ ባይዱ
图1 锻造方法
冷锻
冲裁
弯曲
深拉延
图2 冲压方法
胀形
冲压工艺学(第一章绪论)

冷冲压基本工序分类图
•冷冲压工序
•分分离工序 变形工序 复合工序 装配工 序
• 冲裁 弯曲 拉延 成形 体积冲压
剪落 冲切切弯 扭拉起成压冲 裁料 孔口边曲 曲延伏形印眼
1、分离工序(shearing)
是指板料受力后,应力超过材料的强度 极限σb ,而使板料产生剪裂或局部剪裂。
其目的是在冲压过程中,使冲压件与板 料沿一定的轮廓线相互分离,同时,冲压 件分离断面的质量也要满足一定的要求。
* 拉深 —— 把平板毛坯冲制成各种空心的零 件,也有称之为拉延、压延、引伸
* 变薄拉深 —— 把拉深加工后的空心半成品 进一步加工成底部厚度大于侧壁厚度的零件
* 成形 —— 把弯曲和拉深以外的许多变形类 工序统称为成形。包括:翻边、局部成形、 胀形、扩口、缩口、旋压、强力旋压、校平 与整形等。
—— 成形(forming)
* 翻边 —— 把板料的边缘按曲线翻成竖立的 边缘,可分为内孔翻边和外缘翻边 内孔翻边 —— 圆孔翻边、异形孔翻边 外缘翻边 —— 凸曲线翻边、凹曲线翻边
冲压工艺学-4-成形工序_弯曲
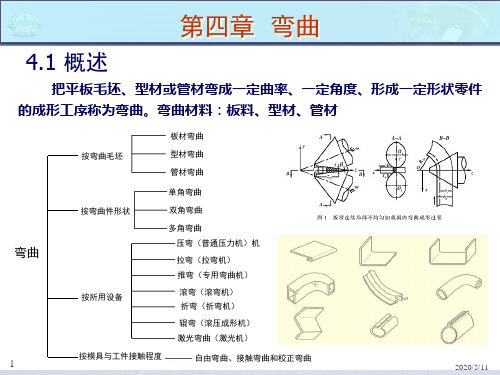
7
2019/8/28
第四章 弯曲
内区
外区
窄板为平面应力状态,
宽板为立体应力状态,
立体应变状态
平面应变状态
8
2019/8/28
3.弯曲件质量问题
第四章 弯曲
拉裂、回弹和弯曲畸变。 弯曲变形区横截面形状和尺寸发生变化(由矩形 变为梯形)的现象称为弯曲畸变。一种是横截面的尺寸发生了变化:外层宽度 变窄,而内层变宽;二种是弯曲件断面会发生翘曲,即断面宽度方向内凹。
2019/8/28
第四章 弯曲
3)提高制件结构刚性 K 1 1 M
' EI
增加条形筋
局部增加三角筋
33
在环箍上压筋
2019/8/28
第四章 弯曲
4.5 最小弯曲半径
弯曲时,毛坯变形区外表面的金属在切向拉应力作用下,产生切向伸
长变形 。
2
1 r 1
t
在保证毛坯外层纤维不发生破坏的条件下,所能弯成零件内表面的最
40
M
2b 2
0
s
d
bt 2 4
s
s s
17
2019/8/28
第四章 弯曲
4.3 弯曲时的弹复(回弹)
1. 弹复
弯曲弹复
弯曲卸载以后,总变形中的塑性变形保留,弹 性变形部分立刻恢复消失,引起工件形状和尺 寸都发生与加载时变形方向相反的变化
分类:曲率和角度弹复 弯曲弹复显著的原因:内外层应力-应变性质相反;不变形区惯性作用
M
(3 2
3F 2E
2 2 s2
E2t 2
2 2F s2
钣金冲压工艺
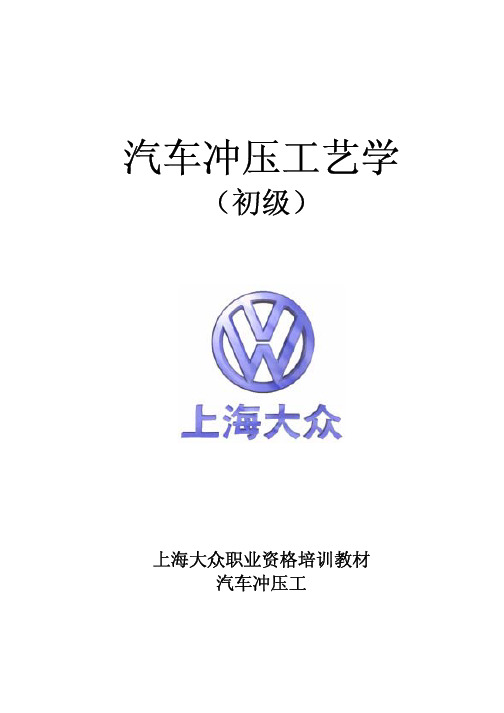
二、 材料种类及牌号 SVW 使用的材料主要有三个大类:冷轧钢板,热镀锌钢板和电镀锌钢板: 1、 冷轧钢板: 主要有 ST12O3,ST13O3,ST13O5,ST14O3,ST14O5,ST14O5-T 等。 其中 ST12,ST13,ST14 等代表了钢板的机械性能,机械性能 主要有三个指标,屈服 强度,抗拉强度,和延伸率。ST14 的延伸率最大,深冲效果最好,ST13 次之,ST12 最差。他 们的屈服和抗拉强度都比较适中,三种钢的屈服和抗拉的允许的最小值是相同的,最大值 ST12 最高,ST13 次之,ST14 最低,因此 ST14 的钢其技术标准最高,但价格也贵,因此只有在比
-5-
SVW-TS
冲压工艺培训教材
较难冲,冲压形变很大的零件才采用。变形较小的零件用 ST12 就够了。 在 ST12 等代表技术性能的编号后往往还会跟上 O5 或 O3 的编号,这其实是指钢板的表
面质量,O5 代表较高的表面质量,O3 则是普通的表面质量。O5 板一般使用在外覆盖件等表面 质量要求较高的零件上。需要注意的是牌号中有 O5 的钢板只是保证其中一面是较高的表面质 量,另一面并不做要求,所以 O5 板是有正反面之分的,使用时一定要注意。
(2)不对称的覆盖件。诸如车门的内、外板,翼子板,侧围板等。这类覆盖件又可分 为深度浅度比较平坦的、深度均匀形状较复杂的和深度深的几种。
(3)可以成双冲压的覆盖件。所谓成双冲压既指左右件组成一个便于成型的封闭件, 也指切开后变成两件的半封闭型的覆盖件。
(4)具有凸缘平面的覆盖件。如车门内板,其凸缘面可直接选作压料面。 (5)压弯成型的覆盖件。
-3-
SVW-TS
冲压工艺培训教材
主模型一致,图面上无法标注的尺寸要依赖主模型量取,从这个意义上看,主模型是覆盖件 图必要的补充。
冲压工艺学(全)

(2)
冲压应力图的DOE,冲压应变图的GOL
33 与该种情况相对的变形有缩口变形等。
2019/12/21
第二章 冲压变形基础
3)变形区受异号应力作用,且拉应力绝对值大于压应力绝对值
(1)
,且
冲压应变图的MON;
,处于冲压应力图的GOF,
(2)
,且
冲压应变图的COD;
,处于冲压应力图的AOB,
与该种情况相对的变形有扩口等。
可以把冲压变形方式按毛坯变形区的受力情况(应力状态)和变 形特点从变形力学理论的角度归纳为以下几种情况,并分别研究它们 的变形特点。
31
2019/12/21
第二章 冲压变形基础
1.变形分类
1)冲压毛坯变形区受两向拉应力作用 分为两种情况:
(1)
再确定 , 的变化范围是
,
当
时,为两向等拉,
当
时,为单拉,
第一类硬化曲线: ~
第二类硬化曲线: ~ 第三类硬化曲线: ~
27
2019/12/21
第二章 冲压变形基础
2.硬化曲线及表达式
直线式-以硬化曲线上缩颈点处的切线表示:
式中: -截距
F -硬化模数,为硬化直线斜率
1)当应变 用延伸率 表示时,
2)当应变 用断面缩减率 表示时,
4)变形区受异号应力作用,且压应力绝对值大于拉应力绝对值
(1)
,且
冲压应变图的MOL;
,处于冲压应力图的EOF,
(2)
,且
冲压应变图的DOE;
,处于冲压应力图的BOC,
与该种情况相对的变形有拉深等。
34
2019/12/21
第二章 冲压变形基础
冲压工艺基础专题培训课件

模具标准件
各种不同的冲头以及衬套
氮气缸:与弹簧起相同作用,能提供比弹簧更大 的压料力
第四章 冲压工艺简介
冲压基本工序分类 冷冲压概括起来分两大类:分离工序和成形工序 1.分离工序是使板料按一定的轮廓线分离而获得一定形状、尺寸和切断面
质量的冲压件。 2.成形工序是坯料在不破裂的条件下产生塑性变形而获得一定形状和尺寸
压料面
B
A
A
修边线
B
修边线
数据工艺编制例子说明
废料刀
拉延筋 修边线
修边线
翻边线
侧冲孔
整形线
翻边线
翻边线
数据工艺编制例子说明
修边线
侧修边线 修边线
翻边线
侧 冲 孔
侧修边线
侧翻边线
侧修边线
数据工艺编制例子说明
侧修边线 修边线
侧
侧修边线
翻
边
侧冲孔
翻边线
侧围的冲压工艺
OP05 落料
冲头折断;冲套堵死 操作时有拖、拉等现象
机
曲 柄 压 力 机
利用曲柄连杆机构进行工作,电机通过皮带轮及齿轮带动
曲轴传动,经连杆使滑块作直线往复运动。曲柄压力机分
为偏心压力机和曲轴压力机,二者区别主要在主轴,前者 主轴是偏心轴,后者主轴是曲轴。偏心压力机一般是开式
生产率高,适用于各类冲压加工
压力机,而曲轴压力机有开式和闭式之分。
高速 冲床
工作原理与曲柄压力机相同,但其刚度、精度、行程次数 都比较高,一般带有自动送料装置、安全检测装置等辅助 装置。
压料面有两种: 1.由工件本身的法兰面组成; 2.由工艺补充部分组成;
制定压料面基本原则: 1.为了降低拉深深度,压料面可以设计成一定的弯曲形状,使毛坯拉深前先弯成一定 的形状。但压料面的形状应尽量简单、平滑,防止毛坯在压料过程中就产生摺皱现 象,并利于毛坯在拉深时材料向凹模内流动 2.压料面与凸模的形状之间,应保持一定的几何关系——保证在拉深过程中毛坯处于 张紧状态,并能平稳地、渐次地紧贴凸模,以防止产生皱纹。为此,必须满足如下 关系:压料面长度﹤凸模表面展开长度
冲压工艺学(3篇)
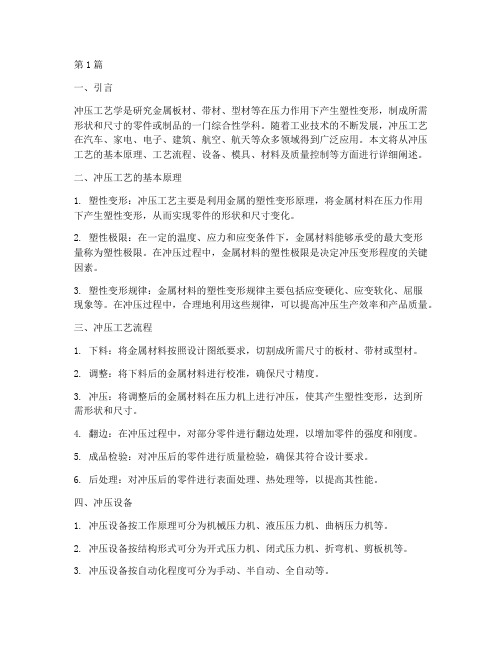
第1篇一、引言冲压工艺学是研究金属板材、带材、型材等在压力作用下产生塑性变形,制成所需形状和尺寸的零件或制品的一门综合性学科。
随着工业技术的不断发展,冲压工艺在汽车、家电、电子、建筑、航空、航天等众多领域得到广泛应用。
本文将从冲压工艺的基本原理、工艺流程、设备、模具、材料及质量控制等方面进行详细阐述。
二、冲压工艺的基本原理1. 塑性变形:冲压工艺主要是利用金属的塑性变形原理,将金属材料在压力作用下产生塑性变形,从而实现零件的形状和尺寸变化。
2. 塑性极限:在一定的温度、应力和应变条件下,金属材料能够承受的最大变形量称为塑性极限。
在冲压过程中,金属材料的塑性极限是决定冲压变形程度的关键因素。
3. 塑性变形规律:金属材料的塑性变形规律主要包括应变硬化、应变软化、屈服现象等。
在冲压过程中,合理地利用这些规律,可以提高冲压生产效率和产品质量。
三、冲压工艺流程1. 下料:将金属材料按照设计图纸要求,切割成所需尺寸的板材、带材或型材。
2. 调整:将下料后的金属材料进行校准,确保尺寸精度。
3. 冲压:将调整后的金属材料在压力机上进行冲压,使其产生塑性变形,达到所需形状和尺寸。
4. 翻边:在冲压过程中,对部分零件进行翻边处理,以增加零件的强度和刚度。
5. 成品检验:对冲压后的零件进行质量检验,确保其符合设计要求。
6. 后处理:对冲压后的零件进行表面处理、热处理等,以提高其性能。
四、冲压设备1. 冲压设备按工作原理可分为机械压力机、液压压力机、曲柄压力机等。
2. 冲压设备按结构形式可分为开式压力机、闭式压力机、折弯机、剪板机等。
3. 冲压设备按自动化程度可分为手动、半自动、全自动等。
五、冲压模具1. 冲压模具是冲压工艺中的关键工具,主要包括冲模、凹模、导向装置等。
2. 冲压模具的设计应遵循以下原则:结构合理、制造方便、使用可靠、寿命长、成本低。
3. 冲压模具的材料主要有碳素钢、合金钢、高速钢等。
六、冲压材料1. 冲压材料主要有低碳钢、低合金钢、不锈钢、铝及铝合金、铜及铜合金等。
冲压工艺学

因此,在近代机器制造业中,冲压工艺被得到广泛
应用。很多机器中,冲压件占有相当大的比重,例如 在汽车工业中比重占50~75%,在电机制造业中比 重占60~80%,在电子工业中比重占70~80%,在 金属制品工业中占95%。
板料冲压主要的缺点如下: 1、模具制造周期长,费用高。因此,在小批量生产 中受到一定的限制。 2、冲压适于批量生产,且大部分是手工操作,这样 如果不重视安全生产和缺乏必要的防护装置,就易发 生事故。因此,提高冲压操作的机械化和自动化,减 轻工人劳动强度,确保安全生产,是一个很重要的问 题。
接触处形成很小的圆角。
②塑性变形阶段:当凸模继续下压,板料应力超过了
屈服极限,部分金属被挤入凹模洞口,产生塑性剪切
变形,形成光亮的剪切断面。
③剪裂阶段:凸模继续下压,凸凹模刃口处出现微小
裂纹不断向材料内部扩展,若凸模间隙合理时,上,
下裂纹重合,板料被拉断分离。
零件
零件
零件
凹模
板料 凹模
板料 凹模
板料
冲压工艺学
2017年 农机自动
冲压工 理论培训
第一章:冲压工艺基础
前言:冲压:是利用冲模在压力机上对板 料施加压力使其变形或分离,从而获得 具有一定形状、尺寸的零件的一种压力 加工方法。
冲压主要用于加工板料制件,所以有 时也叫板料冲压。常温下进行的板料冲 压叫泠冲压,我公司的农机零件,大多 数为冷冲压,在本次培训中的内容,仅 限于冷冲压。
二、冲裁间隙:凹模与凸模之间的尺寸差。
间隙的影响:冲裁间隙的大小对冲裁件断面质量和尺寸精度、 冲裁力、卸料力以及模具寿命均有较大的影响。所以对冲裁 工序来说,冲裁间隙是一个极为重要的工艺参数。
间隙合理:上、下面出现的裂纹相互重合,所得断面光洁、 略带斜度,见图a。间隙过小:上、下两裂纹相互不重合,隔 着一定的距离,互相平行,最后形成毛刺和层片,并产生两 个光亮带,见图b。间隙过大:,会使薄料拉入间隙中,形成 拉长的毛刺,对于厚料,则形成很大的塌角,见图c。
- 1、下载文档前请自行甄别文档内容的完整性,平台不提供额外的编辑、内容补充、找答案等附加服务。
- 2、"仅部分预览"的文档,不可在线预览部分如存在完整性等问题,可反馈申请退款(可完整预览的文档不适用该条件!)。
- 3、如文档侵犯您的权益,请联系客服反馈,我们会尽快为您处理(人工客服工作时间:9:00-18:30)。
c ( 1 ~ 1.1 )tmax
间隙方向的选取: a.中间过渡拉深工序,间隙方向不作规定,通常取在凸模上; b.最后一道工序, 当工件要求外形尺寸时,凹模为基准;间隙取在凸模上。 当工件要求内形尺寸时, 以凸模为基准,间隙取在凹模上。
4.凸、凹模尺寸及制造公差
中间过渡工序,以凹模为基准: d δ Dp d 0
各次拉深件的直径d确定后,初始拉深直径d1>50t时如下图 所示。 t=0.8mm,α=30°。 t=0.8~1.6mm,α=40°。 T>1.6mm,α=45°。
d n 1 d n rn d d A ,An 2 n 2 n 1 n 1 2 4 2 2 d n 3 d n 2 An 2 An 3 2 2 rn1 0.6 An 1 , rn 2 0.6 An 2 , rn 3 0.6 An 3 An 1
dh 9.3 1.2 35.042mm2
4 d d
2 2 1
4 14.5
2
11.32 64.842mm2
由于材料各向异性及间隙不均等原因,出现凸耳现象,一都要修边。因此在 产品边缘加上修边余量。 表4-4为圆筒件修边余量△h。当拉深次数多或板料方向性较大时,取表中较 大值,当零件的h/d很小时,可不进行修边。
可知该零件要拉深四次才行
影响拉深系数的因素
①材料的机械性能: σs、 σb 延伸率δ 屈强比σs/σb ↓ → m↓。延伸率δ↑→ m↓,当 σ s/ σ b ≤0.65 时,δ≥28% , 拉深性好。 ②材料的相对厚度t/D t/D↑→凸缘材料不易起皱→金属流动阻力小→拉深顺利。 t/D↑↑→可不用压边装置→相应拉深力小。危险断面的拉应力就小→m↓。 ③润滑条件 润滑条件好→易于流动→阻力小→ m↓ 润滑条件太好→易起皱。 ④模具情况 rd↑→ m↓; rd↑↑,筒形件口部易起小皱。 rp↑→弯曲不厉害→m↓, rp太小,转角处易拉裂。 模具表面光滑,间隙值合理,m↓。 ⑤拉深次数越多,板料硬化越严重,塑性下降。 根据需要增加工序退火。
3.凸耳的产生 凸耳:因毛坯的各向异性。
残余应力:由弯曲—反向弯曲产生。从而产生口部切向拉应力。如黄 铜零件或不锈钢零件拉深后口部没有后续工序直接存放,放一段时间就会 产生开裂现象。
二、筒形拉深工艺计算及模具设计
1.拉深零件的毛坯尺寸
原则:拉深前后的毛坯面积与工件的表面积相等。
F毛坯=F工件
计算毛坯尺寸是,先将零件划分为若干个便于计算的简单几何体,分别求出 其面积后相加,得零件总面积ΣA ,则毛坯直径:
解:(1)拉深系数
m d / D 88 / 283 0.31
t / D 100 0.7
查P89表4-5可知:
m1 0.55、m2 0.78、 m3 0.80、m4 0.82 m1m2 0.429 m1m2 m3 0.343 m1m2 m3m4 0.281 、 、
3)采用拉深筋或拉深槛。 2.筒壁的拉裂
筒壁起到传递拉深力的作用,受单向拉应力,当筒壁拉应力超过筒壁材 料的抗拉强度时,拉深件就会在底部圆角与筒壁交界处——“危险断面” 产生破裂。
防止拉裂措施:
1)采用适当的拉深比和压边力。 2)增加凸模表面的粗糙度。
3)通过改善材料的力学性能,提高筒壁抗拉强度; 4)降低筒壁所受拉应力,控制材料的变形程度,
3.凸、凹模工作部分尺寸
(1)凹模圆角半径 在不产生 起皱的前提下,rd越大越好。凹 模圆角半径与毛坯厚度、零件的 形状尺寸和拉深方法等有关。按 卡切马列克经验公式:
首次拉深:
rd 0.8 ( D d d )t
式中:rd—凹模圆角半径,mm。D—毛坯直径,mm。dd—凹模内径,mm。 t—板料厚度,mm。 上式适用于D-dd≤30。当D-dd>30时,应取较大的rd值。 当工件直径d >200mm时,rd可按下式确定:
D D
( Dd Z )
0 p
最后一道工序,零件给定外形尺寸和公差时
Dd ( D 0.75△) 0δ d Dp (D 0.75△-Z)0δ p
零件给定内形尺寸和公差时:
Dp (d 0.4△)
D——工件外径 。 d——工件内径。
0 p δ
Dd (d 0.4△Z)0δБайду номын сангаасp
2.直壁非轴对称零件
3.曲面轴
4.曲面非轴对称零件 主要讲圆筒形零件的拉深,并以此作为基 础讲其他形状零件的拉深。 拉深分为变薄拉深和不变薄拉深。主要讲 不变薄拉深。
不变薄拉深:在拉 深过程中不产生较 大的变薄,筒壁与 筒底厚度较一致的 拉深工艺。
变薄拉深:指以空心开 口零件为毛坯,通过减 小壁厚成形零件的拉深 工艺。
2.拉深系数和次数的确定
1).圆筒件拉深系数: 指用于表示拉深变形程度的工艺指数。其值为拉深后制件直径与拉深 前毛坯直径之比值。
式中:D-平面毛坯直径。d-拉深 后的圆筒直径。
m<1
拉深比:
圆筒件的第n次拉深系数为:
注意:拉深系数系愈小,表示拉深变形程度愈大。
一般在制定拉深工艺时,减少拉深次数,采用小的拉深系数(大的拉深比)。
解决破裂问题主要是控制变形程度。
圆筒形需要的拉深系数为:m=d/D,若m≥m1,则可以一次拉深成形,若m< m1,则需要n次拉深,则拉深系数n为:
m1m2m3…mn≤m。
实际采用的拉深系数为: 应使: 则得到的各次拉深后的圆筒直径为:
、
、…
,
例题:已知所要拉深筒形件的直径为88mm,所需要的毛坯 直径尺寸为283mm,则该拉深件需要几次拉深才能成形?
△——工件公差。 Z——凸、凹模双面间隙。 δp——凸模制造公差 。
δd——凹模制造公差。
圆形件 :见表4-23取δp 、δd 或采用IT6—IT8 非圆形件: 工件公差在IT13以上者,δp 、δd采用IT6—IT8 工件公差IT14以上者,δp 、δd采用IT10
异形件采用配作,只在基准件上标注公差,另一件配作。
极限拉深系数:指当拉深系数减小至使拉深件起皱、断裂或严 重变薄超差时的临界拉深系数。
根据之前的力学分析,拉深系数过小,将会在危险断面产生破裂。 要保证拉深的顺利进行每次拉深系数应大于极限拉深系数。
mn产品 mn极限
极限拉深系数m与板料成形性能、毛坯相对厚度t/D、凸凹模间隙及其圆角半 径等有关。
第四章 拉深
4.1 拉深工艺概述
拉深:将板料在具有一定圆角半径的凸、凹模作用下变成
开口空心零件的冲压方法。
拉深工艺性质及其分类:
拉伸件 形状
旋转体件拉深 盒形件拉深 复杂形状件拉深
无凸缘圆筒形件、 带凸缘圆筒形件、 球形、锥形、抛物 线形、阶梯件等
拉 深
变形
变薄拉深
方式
不变薄拉深
拉深件分类: 1.直壁轴对称零件
m m1
需多次拉深
(2) 计算拉深次数
d1 m1 D 0.55 283m m 155.65m m d 2 m2 d1 0.78155.65m m 121.4m m d 3 m3 d 2 0.80121.4m m 97.1m m d 4 m4 d 3 0.82 97.1m m 79.6m m
如图所示的圆筒件,可分为三个 部分,每个部分面积分别为:
将上述格式代入毛坯直径公式得:
实例分析:
带凸缘制件
无凸缘制件
将制件分割为
1)1/4凹球环
2)圆柱
3)1/4凸球环
4)圆板
1)1/4凹球环
4 2 rd 8r
2
4 2 111.3 8 1 49.48mm
防止措施 1)采用压边圈。
压边圈的装置有刚性和弹性两种。 刚性压扁装置在双动压力机上利用外滑块压边, 刚性压边圈压边力大小,靠调整压边圈和凹模之间的间隙c来调节。 弹性压边装置用于单动压床。压边力系由气垫、弹簧或橡皮产生。 使径向拉应力↑和减少切向压应力。防止起皱的有效措施。
2)采用反拉深。
一般用于多道工序的拉深。有前道拉深得 到直径为d1为半成品,套在筒状凹模1上 进行反拉深时,毛坯内表面变成外表面。 板料沿凹模流动的摩擦阻力和变形抗力显 著增大。使径向拉应力增大,切向压应力 相应减小,有效防止起皱。故反拉深的拉 深系数可比正拉深降低10%~15%,拉深 力则增大10~20%。
(3)凸、凹模间隙
间隙大小影响产品质量(形状、起皱、划伤等),模具寿命。
①采用压边圈拉深时:
c t max kt
式中:tmax——材料最大厚度。K——间隙系数,查手册或表。 ②不用压边圈 ③拉深件精度要求达到较高(IT11—13) 黑色金属 c=t 有色金属 c=0.95t ④拉深H/d<0.15 回弹大 采用负间隙 C=(0.9-0.95t)
凸、凹模制造公差可查下表。
5、凸、凹模结构形式 出气孔作用:卸件作用;使产品贴模。
1)无压边圈的拉深模: 2)有压边圈的拉深模: A 多用于直径小于100的拉深件 B 多用于直径大于100的拉深件,减轻毛坯的反复弯曲,改善拉深条 件。
3)带限制圈的结构: 改善切向受拉力的状况,从而改善口部开裂的现象, h=(0.4-0.6)d d1比上次拉深直径小0.1-0.2。
由于平面凸缘部分受切向压应力作用而失去稳定的结果。
与拉深力大小、压边条件、材料厚度、变形程 度等因素相关。
1.起皱及其防止措施防止措施
起皱主要是由于法兰的切向压应力超过了板料的临界压应力所引起。 法兰起皱与压杆失稳有些类似。它不仅与压应力有关,且与法兰的相对厚 度t/(DW-dp)有关。 当DW↓或t↑时,从而提高了毛坯抗失稳的能力。 当拉伸时压应力σθ↑→失稳起皱↑。压边力过大,导致拉深力过大而使危险 断面拉裂;压边力过小,则不能防止起皱。