改善煤泥分选效果提高精煤产率
山西焦煤汾西矿业高阳选煤厂:尽心尽力出精煤

山西焦煤汾西矿业高阳选煤厂:尽心尽力出精煤来源:山西焦煤集团网站作者:张燕2014年,山西焦煤汾西矿业精煤超计划40万吨,其中36万吨出自高阳选煤厂。
该选煤厂是如何在困境中做到增产增收、降本提效的呢?该厂以“五全管理”为核心,大力推行优化生产工艺,引入新技术、新设备,鼓励小改小革等多项举措。
其中,全面预算管理的效果最为显著。
“我们的目标是用最少的消耗、最短的入洗时间来洗最多的煤,从而提高生产效率。
”该厂厂长汪小琪介绍。
自全面预算实施以来,该厂进行全方位经营管控,利用成本倒逼机制,将材料费、电耗、修理费、职工薪酬等费用指标下发到各管控部门,各管控部门制订指标要求及考核范围,各队组根据考核范围将各经营指标分解到班组,实现了预算指标的层层落实。
将现场岗位责任制与全面预算工资管理相结合,实行岗位责任工序工资明码标价,做到日清日结就是最为推崇的亮点之一。
以明确岗位责任、落实岗位职责为突破口,划分32个岗位,根据每个岗位的职责范围、设备台数、需要多少人,先后多次组织各部室队组对各岗位责任制和包机制度进行重新编订——这一举措解决了职工们所在岗位需要干什么,怎么干,干到什么程度的问题。
在此基础上,通过与绩效挂钩的管理办法,让每位职工每天都清楚地知道自己的收入、支出及各考核项目。
“我们把生产一吨精煤每个岗位挣多少钱都进行细化、量化,这样上一天班,不同岗位的职工都能自己算出日工资,并上墙公布,公开透明。
但是还要考核,有奖有罚。
如果因为设备故障等问题影响生产,那么就根据时间长短来扣罚。
这样一来也就促使职工养成有问题及时处理的好习惯,提高了职工检查设备的积极性、自觉性。
”汪小琪说。
工资管控透明化使生产故障率显著降低,全员效率提高到43.92吨/工,影响时间较2013年减少了59小时/月。
职工的工作效率、岗位操作水平和检修质量均明显提高。
以前一天洗1000吨和2000吨精煤,挣的都是一样的钱,甚至一天不生产也挣钱,职工的积极性自然不高。
选煤厂煤质管理措施
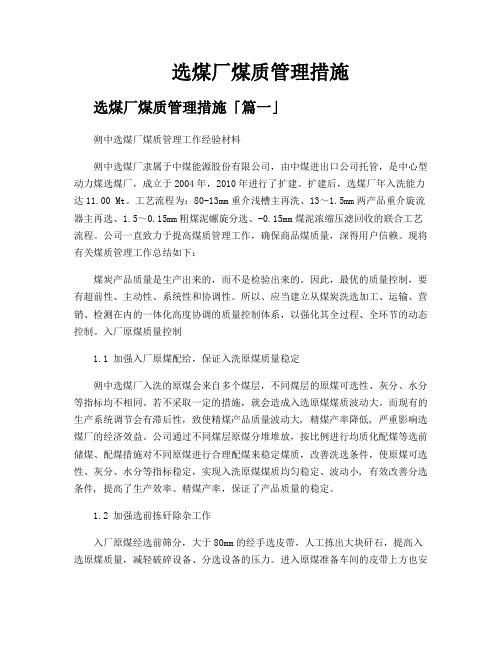
选煤厂煤质管理措施选煤厂煤质管理措施「篇一」朔中选煤厂煤质管理工作经验材料朔中选煤厂隶属于中煤能源股份有限公司,由中煤进出口公司托管,是中心型动力煤选煤厂,成立于2004年,2010年进行了扩建。
扩建后,选煤厂年入洗能力达11.00 Mt。
工艺流程为:80-13mm重介浅槽主再洗、13~1.5mm两产品重介旋流器主再选、1.5~0.15mm粗煤泥螺旋分选、-0.15mm煤泥浓缩压滤回收的联合工艺流程。
公司一直致力于提高煤质管理工作,确保商品煤质量,深得用户信赖。
现将有关煤质管理工作总结如下:煤炭产品质量是生产出来的,而不是检验出来的。
因此,最优的质量控制,要有超前性、主动性、系统性和协调性。
所以、应当建立从煤炭洗选加工、运输、营销、检测在内的一体化高度协调的质量控制体系,以强化其全过程、全环节的动态控制。
入厂原煤质量控制1.1 加强入厂原煤配给,保证入洗原煤质量稳定朔中选煤厂入洗的原煤会来自多个煤层,不同煤层的原煤可选性、灰分、水分等指标均不相同。
若不采取一定的措施,就会造成入选原煤煤质波动大。
而现有的生产系统调节会有滞后性,致使精煤产品质量波动大, 精煤产率降低, 严重影响选煤厂的经济效益。
公司通过不同煤层原煤分堆堆放,按比例进行均质化配煤等选前储煤、配煤措施对不同原煤进行合理配煤来稳定煤质,改善洗选条件,使原煤可选性、灰分、水分等指标稳定,实现入洗原煤煤质均匀稳定、波动小, 有效改善分选条件, 提高了生产效率、精煤产率,保证了产品质量的稳定。
1.2 加强选前拣矸除杂工作入厂原煤经选前筛分,大于80mm的经手选皮带,人工拣出大块矸石,提高入选原煤质量,减轻破碎设备、分选设备的压力。
进入原煤准备车间的皮带上方也安装了除铁器,把进入原煤中的铁器及时清除出去。
煤流中有超限物料要及时处理,经常对原煤场受煤坑篦子进行检查,发现断条等问题时,及时汇报处理。
1.3 提高筛分效率,降低煤泥进入系统为了降低煤泥水浓度,保证分选密度的稳定性,朔中选煤厂对原煤筛分系统进行了改造,增加两台弛张筛,实现3mm粒度的有效分级,减少进入洗煤系统的末煤量,不仅降低了选煤系统的介耗,减轻了煤泥水系统的负担,节约了煤泥水处理的成本,提高企业经济效益。
提高浮选精煤回收率的研究

271近年来,随着煤炭开采量的增大,炼焦煤种越来越稀缺,原煤中的煤泥含量逐渐增加,尤其是污染浮选精矿最为严重的高灰细泥含量的增加,给浮选环节造成很大压力。
这部分难以脱除的高灰细泥不仅会污染精煤灰分,使精煤灰分升高,还会制约浮选精煤产率,同时增加浮选药剂消耗量。
随着选煤技术的发展,本着“吃干榨净”的原则,对浮选系统和粗煤泥回收系统进一步完善,进一步提高精煤回收率,以创造更多的经济效益和社会效益。
1 矿井原煤现状1.1 原煤粒度变化随着煤田地质条件的恶化,采煤工作面距离地面越来越远,导致毛煤运输过程中转载点增多,工作面回采率提高;综合采煤、井下破碎、转载这一系列的过程,使进入选煤厂原煤中的次生煤泥含量不断增加。
另外,随着煤炭价格的升高,以及优质焦煤的数量急剧减少,使得各选煤厂需要最大限度的提高精煤的回收率,实现优质资源合理利用,以创造更大的经济效益。
原煤中细粒级含量的不断增加,煤质的不断变化使得重介选煤成为主流的选煤方法,而介质系统循环又会造成次生煤泥量的增加。
重介旋流器分选粒度下限通常为0.5 mm,浮选是回收-0.5 mm精煤最有效、最广泛的选煤方法,浮选入料量占原煤入洗量20%~30%,因此煤泥浮选效果好坏成为制约最终精煤产品数质量的关键。
2 影响浮选效率的因素2.1 入浮煤泥的物性入浮煤泥物性是影响浮选效果的根本因素,包括粒度、灰分、入料浓度和可浮性等。
(1)浮选入料的粒度特性和灰分特性是决定浮选工艺、设备选型、粗煤泥回收系统的重要因素。
它是提高浮选精煤产率最重要一环,也是现阶段各选煤厂改造浮选系统、煤泥水处理系统的重要依据。
通过统计浮选入料(精煤磁尾)小浮沉试验数据可知,粒度<0.125 mm的累计产率在28.78%,产率累计灰分38.75%,其中<0.045 mm粒度级的灰分高达56.99%,产率8.56%。
说明该厂浮选入料中高灰细泥含量较高。
+0.5 mm粒度级的占比在7.92%,说明跑粗现象严重,这部分粗颗粒如果直接进入浮选系统,就会导致尾矿跑粗,尾矿灰分偏低,浮选精煤产率下降;+0.25 mm平均灰分为8.51%,该厂重介旋流器分选下限为0.25 mm。
田庄选煤厂末煤分选系统优化实践
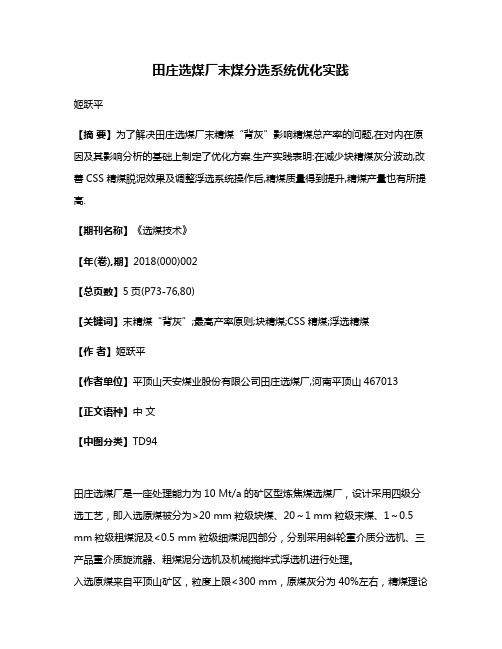
田庄选煤厂末煤分选系统优化实践姬跃平【摘要】为了解决田庄选煤厂末精煤“背灰”影响精煤总产率的问题,在对内在原因及其影响分析的基础上制定了优化方案.生产实践表明:在减少块精煤灰分波动,改善CSS精煤脱泥效果及调整浮选系统操作后,精煤质量得到提升,精煤产量也有所提高.【期刊名称】《选煤技术》【年(卷),期】2018(000)002【总页数】5页(P73-76,80)【关键词】末精煤“背灰”;最高产率原则;块精煤;CSS精煤;浮选精煤【作者】姬跃平【作者单位】平顶山天安煤业股份有限公司田庄选煤厂,河南平顶山467013【正文语种】中文【中图分类】TD94田庄选煤厂是一座处理能力为10 Mt/a的矿区型炼焦煤选煤厂,设计采用四级分选工艺,即入选原煤被分为>20 mm粒级块煤、20~1 mm粒级末煤、1~0.5 mm粒级粗煤泥及<0.5 mm粒级细煤泥四部分,分别采用斜轮重介质分选机、三产品重介质旋流器、粗煤泥分选机及机械搅拌式浮选机进行处理。
入选原煤来自平顶山矿区,粒度上限<300 mm,原煤灰分为40%左右,精煤理论产率约为50%,矸石含量在30%以上,挥发分介于22%~33%之间,硫分<0.5%,主导产品为焦精煤和1/3焦精煤。
田庄选煤厂的末原煤产率在50%左右,末煤系统是影响最终精煤数质量的关键环节。
与以重介质旋流器为核心设备的重介分选系统相比,其他三种分选系统的精煤质量控制较为困难,因此末精煤经常存在不同程度的“背灰”,造成总精煤产率下降,对企业经济效益有着严重的负面影响。
1 存在问题以四矿原煤作为煤样,按照精煤最高产率原则对四种精煤产品的指标进行设计,并与实际完成指标进行对比分析。
四种精煤产品的设计指标见表1。
由表1可知:按照十级精煤的指标要求,第3项最佳,不但精煤灰分合格,而且精煤产率最高,块精煤灰分为11.30%,末精煤灰分为9.70%,CSS精煤灰分为8.70%,浮选精煤灰分为10.90%,最终精煤灰分为9.98%,对应的理论产率为52.25%;而在实际生产中,块精煤灰分为12.00%,末精煤灰分为9.18%,CSS 精煤灰分为11.00%,浮选精煤灰分为11.00%。
2024年选煤厂月工作总结(二篇)

2024年选煤厂月工作总结(一)本期工作成果概述1. 安全生产方面,本厂全面实现了安全零事故目标,有效杜绝了人身伤害及二级以上非伤亡事故,同时避免了严重“三违”现象的发生,确保了安全生产的稳定局面。
2. 精煤生产方面,按照计划,本厂应生产精煤____万吨,实际完成____万吨,完成计划的____%。
____%,实际达到____%;综合产率计划为____%,实际完成____%。
这一成果的取得,主要得益于年底原煤增加____万吨,使得实际生产均超过或达到计划。
3. 入洗能力方面,本厂小时入洗量达到____吨,超出设计小时入洗量____吨。
4. 效率方面,数量效率实现____%,较计划提高____%。
5. 物耗方面,介耗计划为____kg/t原煤,实际消耗为____kg/t 原煤,比计划降低了0.23kg/t原煤。
6. 劳动生产率方面,计划全员效率为____吨/工,实际达到____吨/工,比计划提高____吨/工。
7. 药耗方面,浮选药剂实际消耗为____kg/吨干煤泥,比计划降低____kg/吨干煤泥。
8. 矸石污染控制方面,计划污染率为____%,实际为____%,较计划降低了____%。
(二)本期具体工作亮点1. 通过系统优化,生产能力显著提升,在____月份实现了生产能力的全面提升。
(1) 工艺系统环节的改造:年初对设备工艺进行了强化改造,包括优化原煤浓缩旋流器溢流水去向,提升三产品旋流器的分选效果,改善产品质量;优化浮选环节,提高尾矿灰分;利用加压过滤机提高中煤产率,确保综合产品产率的完成;采取有效措施控制磁铁矿粉技术介耗;更换粗煤泥系统中的弧形筛,减少细粒高灰煤泥对粗煤泥的污染。
通过这些改造,系统问题得到有效解决,为完成全年计划目标奠定了基础。
(2) 对重点薄弱环节进行强化管理:对排矸车间和机械队实施重点监控和管理,加强车辆定检、定修、维护保养,增加铲车、装载机等设备,保证生产正常进行;对煤泥堆放场地进行硬化和扩大,改善雨季车辆损坏和工农关系等问题。
五沟选煤厂中煤带精优化研究

五沟选煤厂中煤带精优化研究摘要:由于矿井开采深度的增加,1035工作面原煤粒度变细,再加上洗选任务重,小时带量大,以及长期形成的操作习惯和设备老化,致使中煤带精偏高,通过采取加大原煤入料的润湿效果,更换弧形筛的筛缝大小,提高中煤细颗粒的透筛率,减少了中煤带精,提高精煤产率,使企业效益最大化。
关键词:中煤带精;优化;悬浮液;措施1概述五沟选煤厂是一座设计入洗能力150万吨/年的矿井型炼焦煤选煤厂。
选煤厂采用不脱泥分级重介选煤工艺,50mm以上采用动筛跳汰、0.5-50mm原煤采用无压给料三产品重介旋流器、0.25-0.5mm采用TBS分选、-0.25mm直接浮选的工艺流程。
中煤含精一直在20%左右,严重影响了选煤厂的经济效益。
为了减少中煤中精煤的损失,提高精煤产率,降低生产成本, 五沟选煤厂在现有工艺流程和设备的基础上,通过现场调查找出带精高的原因,在不增加选煤厂工艺环节的基础上,经过现场改造和加强管理等措施,探索出降低中煤含精的途径,并取得了良好的效果。
2存在问题降低中煤中的精煤损失不仅能实现精煤回收率最大化,减少精煤资源浪费,还能提高选煤厂经济效益。
因此降低中煤带精尤为重要。
表1 五沟重介中煤浮沉试验0.5-1mm1-3mm3-50mm0.5-50mm密度级(g/cm3)全产率(%)本产率(%)灰分(%)全产率(%)本产率(%)灰分(%)全产率(%)本产率(%)灰分(%)全产率(%)灰分(%)-1.404.6652.356.218.3339.816.31.690.997.3813.686.331.4-1.452.4026.9810.674.6422.1911.74.791.1312.257.8311.461.45 -1.5.647.2016.731.517.2418.09.701.0020.082.8518.271.5-1.6.525.8124.582.2110.5527.1338.0154.1627.9640.7427.871.6-1.8.687.6645.174.2320.2143.4629.9942.7332.7634.9034.30小计8.90100.0012.2220.92100.0018.0770.18100.0029.55100.0025.61说明:采样条件:旋流器压力:240-250KPa,小时流量280吨/小时,显示密度1.635g/cm3由表1可以看出,中煤随着粒度减小灰分递减。
选煤厂粗煤泥分选系统的优化设计

选煤厂粗煤泥分选系统的优化设计包小燕【摘要】介绍了朝川选煤厂生产现状和粗煤泥分选系统存在的问题;结合该厂的炼焦煤煤质特征,确定了粗煤泥回收的优化设计方案;为满足产品指标要求,设计选择用TBS三产品分选机分选脱泥筛下粗煤泥;TBS精矿和精煤磁选尾矿分级浓缩后,通过高频叠筛以及煤泥离心机回收,最大程度减少了高灰细泥对粗精煤的影响,从而达到提质降耗的目的.【期刊名称】《煤炭加工与综合利用》【年(卷),期】2019(000)001【总页数】3页(P36-38)【关键词】选煤厂;粗煤泥分选;工艺改造;优化设计;效果【作者】包小燕【作者单位】中煤科工集团北京华宇工程有限公司,河南平顶山 467002【正文语种】中文【中图分类】TD9481 项目概况朝川选煤厂现有分选工艺为:原煤(-50 mm)先经过0.5 mm脱泥后进入无压三产品重介质旋流器分选,煤泥采用浮选+加压过滤机回收,浮选尾煤采用浓缩+压滤联合回收。
脱泥筛下的煤泥水经过浓缩分级以及弧形筛、高频筛脱水回收后和脱泥筛上的物料一起进入三产品旋流器进行分选,选后产品经脱介、脱水出精煤、中煤、矸石三种产品。
分级旋流器溢流、弧形筛筛下水、高频筛筛下水进入浮选系统。
浮选精煤通过加压过滤机(2台)和隔膜压滤机(1台)回收,浮选尾煤通过浓缩机沉淀后采用快开压滤机回收。
2 朝川选煤厂存在的问题(1)原生煤泥量大,影响介质系统的稳定性。
目前,朝川选煤厂脱泥筛的筛孔为0.5 mm,由于入选原煤具有粒度细、煤泥含量大的特点(原生煤泥含量占比达40%~50%),造成脱泥筛筛分效率低,过多的煤泥进入重介质分选系统,影响介质系统的稳定性。
(2)重介质精煤“背灰”严重。
根据现场实际情况,精煤磁选尾矿通过分级浓缩、弧形筛以及高频筛回收后,其灰分比重介质精煤高出至少4~5个百分点,掺入精煤产品后,导致重介质精煤“背灰”严重。
(3)浮选系统煤泥量大,生产成本高。
脱泥系统产生的大量煤泥水与精煤粗煤泥回收系统的煤泥水一起进入浮选系统,造成进入浮选系统的煤泥量大,生产成本高。
tbs论文

精煤产率低的原因分析及应对措施
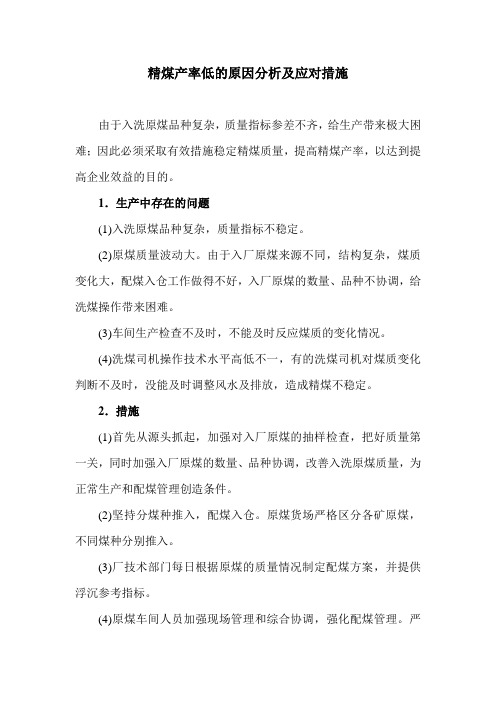
精煤产率低的原因分析及应对措施由于入洗原煤品种复杂,质量指标参差不齐,给生产带来极大困难;因此必须采取有效措施稳定精煤质量,提高精煤产率,以达到提高企业效益的目的。
1.生产中存在的问题(1)入洗原煤品种复杂,质量指标不稳定。
(2)原煤质量波动大。
由于入厂原煤来源不同,结构复杂,煤质变化大,配煤入仓工作做得不好,入厂原煤的数量、品种不协调,给洗煤操作带来困难。
(3)车间生产检查不及时,不能及时反应煤质的变化情况。
(4)洗煤司机操作技术水平高低不一,有的洗煤司机对煤质变化判断不及时,没能及时调整风水及排放,造成精煤不稳定。
2.措施(1)首先从源头抓起,加强对入厂原煤的抽样检查,把好质量第一关,同时加强入厂原煤的数量、品种协调,改善入洗原煤质量,为正常生产和配煤管理创造条件。
(2)坚持分煤种推入,配煤入仓。
原煤货场严格区分各矿原煤,不同煤种分别推入。
(3)厂技术部门每日根据原煤的质量情况制定配煤方案,并提供浮沉参考指标。
(4)原煤车间人员加强现场管理和综合协调,强化配煤管理。
严格按技术部门提供配煤比例配比入仓。
(5)技术检查部门增加入洗原煤的采样点,提前掌握原煤仓原煤的质量情况,为洗煤操作提供了及时、准确的依据。
(6)洗煤车间技术人员建立了质量管理台账,将每天入厂原煤、外销精煤和加工煤的灰分、水分、挥发分、G值等信息反馈给洗煤操作司机,使他们心中有数。
(7)为减少大块矸石进入跳汰机,影响跳汰机一段的分选效果,制定了《手选矸管理考核办法》对手选矸带煤量、限下率、原煤仓的含矸率等指标进行考核,为稳定精煤和加工煤质量创造了条件,并取得了较好的效果。
(8)加大车间小指标考核力度,制定车间精煤块灰的合格范围为9.70%~10.50%,减少低灰出现的频率;且坚持动态质量管理。
根据外销精煤的质量情况,可随时对各项操作指标进行调整,发生质量事故作为重大事故进行分析、追查,严格追究操作者的责任,有效保证了精煤的合格率和稳定率。
煤泥水系统改造提高精煤产率

两部煤泥筛及 浮选 的原矿 、 尾矿进行 了取样分 析, 分析结果如下 : 击打式弧形筛 的泄水情况较好 ,泄水量达 到入料量的 8%以上 , 0 振动筛筛上物的z- K ̄ U A ' 1%, 8 筛上物进 入重介 系统后对重介系统基本没 有影响 , 达到工艺要求 。 从截粗效果上分析: 改造 原矿 中+5 m的 0m 线振动筛 , 激振器改成 自同步式激振。弧形筛选 后浮选原矿小筛分试验表明 , 用 B S 126 O B 8 0 0型棒 条式 不 锈钢 筛 面 ,包 角 含量仅 占5 2 见表 3 , 4 %( )比改造前的 3%, 3 减少 5 ̄筛孔  ̄ .mm。 0, 0 5 了 2 5 %。 7 8 从浮选效果来看 : 浮选尾矿灰分 由 改 捞坑溢流水 捞 流 坑溢 水 前的 4 9%( Q 9 见表 4提高到改后 的 6. %, ) 17 浮选 4 精煤灰分按 18 2 %汁算 , 的浮选精煤抽 出率 改前 为 6. %, 9 2 改后浮选精煤抽 出率为 7 . % 浮选 4 77 。 6 精煤抽 出率提高了 8 5 . %。 2 表 3改造后浮选入料 小筛分试验表
供
其 中有 2台已经损 坏拆除 , 现使用 6台, 在 分布 主洗楼 7 2 . 米和 lA 米 的南北两侧。 6 3 I 该煤泥筛 设备陈 旧, 筛分效率很低 , 而且事故多发 , 约着 制
生产 的正常组 织。筛 面为 自制的木框结构加金 属编织 网 筛面,使用中木框损坏变形严重 , 状 更 换频繁 , 木框与木框之间的缝 隙漏煤 比 严重 , 较
0 2 一 0.5 -O 1 l .5 25 2.l 23
~
—
大大减 少因振动筛数量的减 少而带 来的工作压 力, 解决可能造成 的筛面跑水问题 。 3 . 2现场条件分析 从现场安装位置上分析 , 振动筛筛 面在标 高 86 , . 米 弧形筛安装在振动筛 人料点的上方 , 7 可用空间约 8 , 筛加上人料箱和振动筛人 米 弧形 料箱的总高度为 4 米 , 中弧形筛高度 1 米 , . 其 2 . 8 弧形筛下缘距离振动筛 筛面 0 米 , . 两个箱体 高 2
CSS主洗与TBS再选工艺在霄云煤矿洗煤厂技改中的应用

CSS主洗与TBS再选工艺在霄云煤矿洗煤厂技改中的应用吴德金;吕明【摘要】提出了TBS粗煤泥主再洗概念,阐述了霄云煤矿洗煤厂工艺流程,详尽的分析了介耗多、煤质差等问题原因,提出了改进方案,并介绍了实施和调试过程以及改造后的效果。
%In this thesis putting forward the method of refine coal using TBS,and illustrate the process flows of Xiaoyun coal washery,mean-while,analyzing the problem of medium consuming and poor quality of coal as specific as possible.Then putting forward the improve scheme and illustrate the practice and debug process and the result after reformation.【期刊名称】《煤矿现代化》【年(卷),期】2016(000)003【总页数】3页(P87-89)【关键词】选煤工艺;原煤脱泥;CSS;TBS;主再洗【作者】吴德金;吕明【作者单位】济宁矿业集团有限公司霄云煤矿,山东金乡 272213;济宁矿业集团有限公司霄云煤矿,山东金乡 272213【正文语种】中文【中图分类】TD922由于近年来我国环境状况日益恶化,各地“雾霾”频发,国家加大环境保护力度,其中包括对煤炭质量提出了更高的要求。
如果原煤得不到有效洗选,不仅无法满足国家环保政策,煤炭销售也受到了制约;其次由于洗煤厂原工艺设计中存在一些不合理环节,导致洗煤厂分选精度较差、介耗高等问题,严重影响到企业经济效益提升。
因此企业发展从数量攀升型向质量效益型转变已成必然,通过技术改造提高洗煤厂的生产能力,提升生产效率、降低能耗、保证产品质量、最终提高效益是必然的选择。
提高精煤产率 稳定产品质量的技术分析

提高精煤产率稳定产品质量的技术分析摘要:依据白洞选煤厂原煤性质确定了各粒级产品的最大产率;从脱介喷水管理、入洗量控制、精煤快灰检查、产品水分控制4个方面分析了稳定产品质量的途径。
关键词:选煤厂产率质量技术分析0 引言大同煤矿集团精煤分公司白洞选煤厂是一座入选能力为120万t的现代化矿井型选煤厂,2004年7月投产。
主要对大同煤矿集团白洞煤业公司石炭二叠系原煤进行洗选加工。
采用原煤选前破碎、脱泥分级、重介旋流器加螺旋分选机联合洗选。
50-1.5mm粒级原煤采用重介旋流器分选,1.5-0.1mm粒级原煤采用螺旋分选机分选,-0.1mm粒级原煤,采用板框压滤机回收并混入精煤。
产品为50-0mm洗混煤。
1 问题的提出白洞煤业公司上大采高综采后,原煤性质发生了很大变化,灰分、内水增高。
为了最大限度地在稳定产品质量前提下提高精煤产率,必须对原煤性质作一个准确的测定和分析,以供调节工艺参数时参考;同时加强现场工艺环节管理,以稳定产品质量。
2 依据原煤性质确定各粒级最大产率以下是根据2008年7月白洞选煤厂原煤综合煤样取得的一些数据。
从原煤浮沉资料、筛分组成、各粒级可选性曲线和产品结构表可以看出:2.1 1.5-0.1 mm粒级原煤的产率为7.6%左右,用螺旋分选机分选后回收率很高,螺旋精煤灰分为21.66%时,占本级产率为79.65%,占原煤产率为6.10%。
但是,在此基础上灰分提高6.58%时,产率仅提高0.83%。
所以说,若继续提高1.5-0.1 mm粒级回收率,螺旋精煤灰分将大幅度提高。
2.2 在1.70kg/l分选密度下,总精煤产率为64.29%,灰分为20.86%,矸石的实际产率和灰分为35.71%和65.13%。
若将50-1.5mm粒级原煤的分选密度提高到1.80kg/l,则总精煤产率为67.91%,灰分为22.32%,矸石的实际产率和灰分为32.09%和67.04%。
精煤灰分提高1.46%的情况下,精煤产率可提高3.62%。
山西焦煤集团浮选技术现状研究与分析
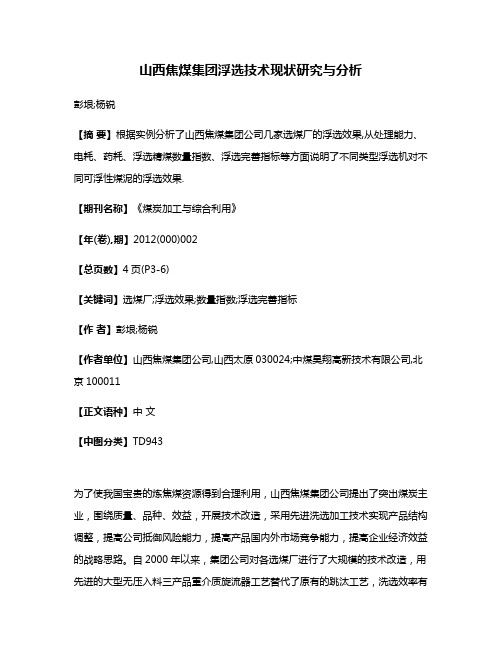
山西焦煤集团浮选技术现状研究与分析彭垠;杨锐【摘要】根据实例分析了山西焦煤集团公司几家选煤厂的浮选效果,从处理能力、电耗、药耗、浮选精煤数量指数、浮选完善指标等方面说明了不同类型浮选机对不同可浮性煤泥的浮选效果.【期刊名称】《煤炭加工与综合利用》【年(卷),期】2012(000)002【总页数】4页(P3-6)【关键词】选煤厂;浮选效果;数量指数;浮选完善指标【作者】彭垠;杨锐【作者单位】山西焦煤集团公司,山西太原030024;中煤昊翔高新技术有限公司,北京100011【正文语种】中文【中图分类】TD943为了使我国宝贵的炼焦煤资源得到合理利用,山西焦煤集团公司提出了突出煤炭主业,围绕质量、品种、效益,开展技术改造,采用先进洗选加工技术实现产品结构调整,提高公司抵御风险能力,提高产品国内外市场竞争能力,提高企业经济效益的战略思路。
自2000年以来,集团公司对各选煤厂进行了大规模的技术改造,用先进的大型无压入料三产品重介质旋流器工艺替代了原有的跳汰工艺,洗选效率有了大幅度提高,数量效率达到95%以上。
随后各厂对浮选系统也进行了改造,采用了各种先进的浮选设备。
1 开展浮选现状研究的意义浮游选煤是精选细粒煤泥的常用方法,也是选煤厂煤泥水系统的核心,对于煤泥水处理起着重要作用。
随着采煤机械化程度的提高和开采深度的增加,原煤质量逐渐变差,原生和次生的细粒粉煤在原煤中所占比例逐年增加,平均达到了20%~30%,甚至更高。
按照选煤能力统计,浮选法占到入选原煤总量的20%以上,而且随着选煤厂入选原煤中细颗粒比例的逐步提高,采用浮选工艺处理的原煤数量呈上升趋势。
根据煤炭的原始粒度组成不同、煤炭泥化性质差异和重选工艺的区别,浮选入料约占原煤入洗量的20%~30%。
在精煤产品中约有1/3是浮选精煤。
同时,用户和社会各方面要求进一步提高精煤质量,重介质改造仅解决了粗颗粒的分选,细粒浮选精煤的灰分比重介质选精煤灰分高很多,造成重选背灰严重,从而影响了选煤厂的经济效益。
阳城煤矿选煤厂生产中存在的问题及解决方案
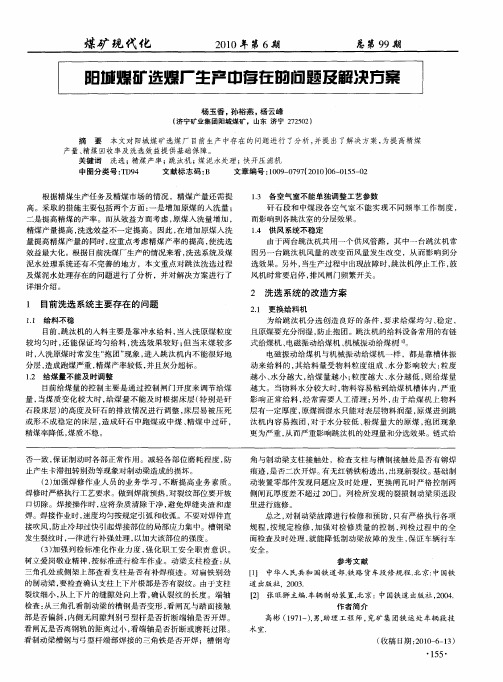
由于两台跳汰机共用一个供 风管 路 ,其 中一 台跳 汰机 常
因 另 一 台 跳 汰 机 风 量 的 改 变 而 风 量 发 生 改 变 ,从 而 影 响到 分
选效 果。另外 , 当生产过程 中出现故 障时, 跳汰机停止工作 , 鼓 风机 时常要启停 , 排风 闸门频繁开关 。
中 图 分 类 号 :D 4 T 9 文献 标 志 码 : B 文 章 编 号 :0 9 09 (0 0)6 0 5 — 2 10 — 7 7 2 1 0 — 15 0 1 各 空气 室 不 能 单 独调 整工 艺 参 数 . 3
根据精煤生产任务及精煤 市场的情况 ,精煤 产量还需提
高 。采取 的措施 主要包括两个方 面 : 一是增 加原煤 的入洗量 ; 二是提高精煤的产率 。而从效益方 面考 虑 , 原煤 入洗量增加 ,
焊 。焊 接 作业 时 , 度 均 匀 按规 定 引弧 和 收 弧 。不 要对 焊件 直 速
角与制动梁支柱接触处 ,检查支柱 与槽 钢接触处是否有铆焊 痕迹 , 是否二次开焊。 有无红锈铁粉透 出, 出现新裂纹 。 基础制
动装 置零 部件 发 现 问题 应 及 时 处 理 ,更 换 闸 瓦 时 严 格 控 制 两
2 洗 选 系统 的改造 方案
21 更换 给 料 机 . 为 给 跳 汰 机 分 选 创 造 良好 的 条 件 , 求 给 煤 均 匀 、 定 , 要 稳
1 目前洗 选 系统主 要存在 的 问题
11 给料 不 稳 .
目前 , 汰 机 的 入 料 主 要 是 靠 冲水 给 料 , 跳 当入 洗 原 煤 粒 度
更 为 严 重 , 而严 重 影 响跳 汰 机 的处 理 量 和分 选 效 果 。链 式 给 从
粗煤泥分级优化分选工艺的应用研究

粗煤泥分级优化分选工艺的应用研究摘要:提出了采用螺旋分级机对煤泥进行分级,对分级溢流和沉砂分别使用不同筛孔的振动筛进行筛分的粗煤泥洗选方法,并对王庄煤矿进行实践。
该工艺能有效提高对粗煤泥的分选效果,精煤产率和灰分均能够满足用户需求。
关键词:优化分级工艺分选粗煤泥煤泥的高效率分选是洗煤行业的技术难题之一。
目前对原煤中1~0mm粒度级别分选来说,+0.5mm采用重力分选方法,-0.15mm粒级采用浮选方法能够得到有效处理;但0.5~0.15mm粒度级的分选效率则较低。
对于1~0mm的煤泥中回收精煤,目前很多分选设备,如螺旋分选机、煤泥重介质旋流器、浮选柱、干扰床分选机(TBS)和水介质旋流器等进行分选,但效果并不理想。
本文采用分级回收煤泥中精煤的新工艺方法,在王庄煤矿煤泥分选的实验研究,取得了良好的效果。
1 概况王庄煤矿是井工煤矿,煤质以烟煤为主,局部地段为天然焦。
洗煤厂主要生产主焦煤精煤、中煤、电煤、工程煤等。
原煤灰分含量一般在10%~30%之间,个别煤样中的灰分含量大于40%,灰分含量较高。
王庄煤矿现有工艺及特点如下:井下开采的原煤经矿车提升,用翻车机倒入原煤给煤机,给入原煤皮带经原煤振动筛筛分后,筛上产品进入原煤手选皮带经人工拣选,选出的块煤破碎后与原煤振动筛筛下产品混合,再经皮带运输机运至原煤矿仓。
进入选煤生产车间,原煤由原煤矿仓下的给煤机给入皮带转运至跳汰机洗选,选出的中煤和矸石混合后进入皮带转运至中煤矿仓;精煤则进入2.4mm的A筛进行筛分,筛下产品进入浓缩罐浓缩,浓缩溢流作为循环水,底流用泵打入带式真空过滤机,过滤产品与A筛筛上产品进入精煤皮带混合后作为精煤产品。
最终产品主要有主焦煤精煤、中煤、电煤、工程煤等,用户对主焦煤精煤灰分要求小于10%。
在2009年1至10月份之间,该选煤厂生产的精煤灰分平均为10.32%,严重的影响企业的经济效益,因此,改进工艺,探索降低精煤灰分、提高分选效率、适应生产的新方法尤为迫切。
新洗选工艺的探索及TBS3000干扰床分选机在田庄选煤厂的应用

新洗选工艺的探索及TBS3000干扰床分选机在田庄选煤厂的应用摘要:针对田庄选煤厂选煤工艺存在的问题,提出采用新的洗选工艺,通过对粗煤泥分选工艺的探索及TBS/3000干扰床分选机的应用,优化了洗选工艺,提高了精煤产率,降低了介质消耗,提高了经济效益。
关键词:洗选工艺粗煤泥干扰床分选机田庄选煤厂隶属于中国平煤神马集团,是由我国自行设计、施工的第一座大型矿区型选煤厂,采用块煤斜轮重介质分选机、末煤两产品重介质旋流器及煤泥浮选的洗选工艺,于1970年投产,实际生产能力已达600万吨/年。
虽进行了几次技术改造,但由于受技术条件的限制,其基本的工艺流程未改变,与近年来建设的现代化选煤厂相比,技术水平相对落后,分选效率低,影响了选煤厂的经济效益。
大直径重介质旋流器的分选下限及浮选机的分选上限均为0.5 mm,实际生产中证明,大直径重介质旋流器对细粒级的分选效率低,浮选机对粗粒级分选效率低。
由于大直径重介质旋流器的有效分选下限及浮选机的入料粒度上限的限制,导致介于大直径重介质旋流器的有效分选下限和浮选有效分选上限之间的这部分粗煤泥(1.6~0.3 mm)得不到有效分选,且造成重介产品脱介效果差,吨煤介耗高,给生产管理造成困难。
1 选煤厂生产系统存在的问题(1)田庄选煤厂入洗原煤中1~0.5 mm及0.5~0.25 mm粒级含量大,这两部分原煤进入生产系统分选效果均不理想。
(2)18~0.5 mm粒级采用Φ800 mm两产品重介质旋流器分选。
实际生产中,1~0.5 mm分选效率低,影响精煤质量,造成了一定的精煤损失,且精煤、中煤产品脱介效果差,带介量大,吨煤介耗高。
(3)煤泥浮选环节采用机械搅拌式浮选机及自主研发的微泡浮选机进行分选。
微泡浮选机采用入料泵给料及压气方式进行矿化过程,其对0.5~0.3 mm分选效果差,致使精煤抽出率低,尾煤灰分低。
针对选煤厂生产工艺存在的上述问题,经过选煤厂和设计部门技术人员讨论及对新工艺新设备的调研,提出采用国产TBS干扰床分选机。
TSS分选效果分析及改善方案
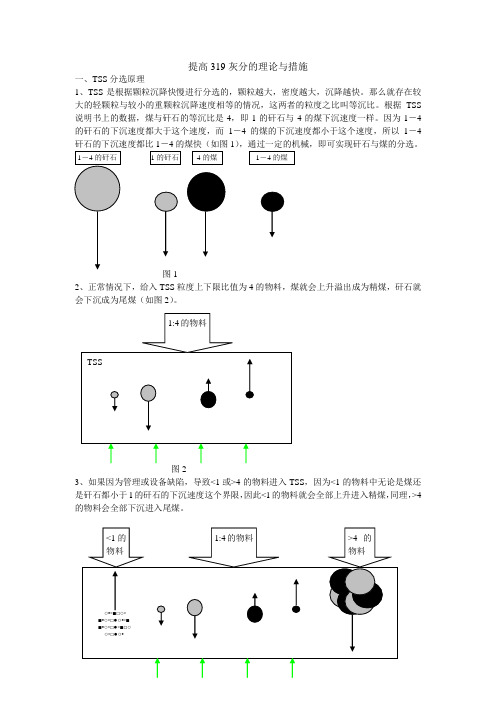
1、2013年8月6日筛分结果
表1
图4图5
2、从筛分数据可以看出:
①>1mm的煤97.9%直接去了319,且灰分只有22.86,与入料灰分20.05接近,是煤料损失的直接原因,这部分煤占319的2/3;>1mm的煤中有2.1%去了318,灰分为3.78这样的超低灰,可以看出,>1的煤只有极少一部分灰分特别低的煤能够回收进入精煤,可以认为>1的煤是以原煤的形式直接去了319
③上表可看出,如果排除TSS中>1mm的煤,319的量将只有现在的1/3,且灰分达到了59,
四、319损失煤计算
1、319与原煤的灰分及发热量对比
2、319中煤料损失量
319产率=煤泥产率-板压产率=(108033.01-8267×6.3)/955572.66=5.8%
319>1mm的产率=319产率×>1的含量=5.8%×65.3%=3.79%
既然TSS有效分选上下限之比是1:4,基本的方法有两个,第一个方法是排除入料中超出上下限的物料,让它们分别去主洗和浮选,第二个是增加一台TSS,两台并连分选,这样的话甚至可以让主洗入料中部分1-2mm的煤进入TSS,在系统末煤量大时增加系统的适应性。
由于第二个方法涉及的改造量大,现在我们先考虑第一个方法,而且只考虑将>1mm的物料尽可能多的进入主洗,也就是在302脱泥的时候,尽量不让>1mm的物料进入筛下。
319中>1mm理论可回收精煤产率=3.79%×55%=2.08%
五、提高319灰分措施
1、改善TSS的方法
通过上面的分析,现在已经清楚TSS只对入料上下限为4的物料有好的分选效果,大于上限的煤绝大部分会进入煤泥中损失掉,小于下限的煤绝大部分会进入精煤中导致精煤灰分过高,我们要做的就是通过提高分级效率,尽可能让这些不适合TSS分选的物料进入它本来应该去的地方
初稿选煤厂2011年集控员试题(题库)
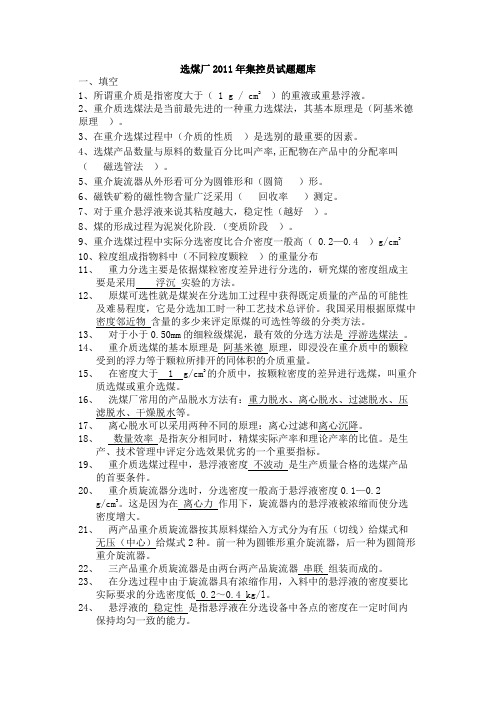
选煤厂2011年集控员试题题库一、填空1、所谓重介质是指密度大于( 1 g / cm2)的重液或重悬浮液。
2、重介质选煤法是当前最先进的一种重力选煤法,其基本原理是(阿基米德原理)。
3、在重介选煤过程中(介质的性质)是选别的最重要的因素。
4、选煤产品数量与原料的数量百分比叫产率,正配物在产品中的分配率叫(磁选管法)。
5、重介旋流器从外形看可分为圆锥形和(圆筒)形。
6、磁铁矿粉的磁性物含量广泛采用(回收率)测定。
7、对于重介悬浮液来说其粘度越大,稳定性(越好)。
8、煤的形成过程为泥炭化阶段.(变质阶段)。
9、重介选煤过程中实际分选密度比合介密度一般高( 0.2—0.4 )g/cm310、粒度组成指物料中(不同粒度颗粒)的重量分布11、重力分选主要是依据煤粒密度差异进行分选的,研究煤的密度组成主要是采用浮沉实验的方法。
12、原煤可选性就是煤炭在分选加工过程中获得既定质量的产品的可能性及难易程度,它是分选加工时一种工艺技术总评价。
我国采用根据原煤中密度邻近物含量的多少来评定原煤的可选性等级的分类方法。
13、对于小于0.50mm的细粒级煤泥,最有效的分选方法是浮游选煤法。
14、重介质选煤的基本原理是阿基米德原理,即浸没在重介质中的颗粒受到的浮力等于颗粒所排开的同体积的介质重量。
15、在密度大于 1 g/cm3的介质中,按颗粒密度的差异进行选煤,叫重介质选煤或重介选煤。
16、洗煤厂常用的产品脱水方法有:重力脱水、离心脱水、过滤脱水、压滤脱水、干燥脱水等。
17、离心脱水可以采用两种不同的原理:离心过滤和离心沉降。
18、数量效率是指灰分相同时,精煤实际产率和理论产率的比值。
是生产、技术管理中评定分选效果优劣的一个重要指标。
19、重介质选煤过程中,悬浮液密度不波动是生产质量合格的选煤产品的首要条件。
20、重介质旋流器分选时,分选密度一般高于悬浮液密度0.1—0.2g/cm3。
这是因为在离心力作用下,旋流器内的悬浮液被浓缩而使分选密度增大。
浅谈新庄孜厂入洗外来煤技术改造

浅谈新庄孜厂入洗外来煤技术改造【摘要】新庄孜选煤厂新增外来煤系统,原设计安装一台皮带输送机及给煤漏斗,通过铲车供煤。
从实际运行情况来看,易出现下料不畅、生产不连续,致使系统稳定性差、分选效果变差等问题;该厂针对以上问题,提出增设刮板输送机的方案,该方案投入运行后,解决了以上问题,保证了生产连续运行,提高了系统稳定性,分选效果得以改善。
【关键词】皮带机;刮板机;闸板;系统稳定性;分选效果;小时处理量1 概述淮南矿业集团选煤分公司新庄孜选煤厂是一座大型现代化炼焦煤选煤厂,入洗新庄孜矿原煤。
2011年进行技术改造,技改后采用三产品重介+煤泥重介+浮选+尾煤压滤联合工艺流程,年处理能力为450万吨。
因相邻矿井产量不足,结合目前煤炭市场经济形势,根据集团公司精神,为加大炼焦精煤产量,新庄孜选煤厂新增外来煤系统。
在厂区原西门新增外来煤场,煤场原煤通过铲车供入新增给煤漏斗及皮带输送机,经256#、257#新原煤系统进行入洗。
2 存在问题新庄孜选煤厂外来煤系统生产中存在以下问题:(1)入料不畅,易堵大块造成断煤。
新增皮带机型号为DTII1200,外置式电动滚筒驱动,功率22KW;皮带机机尾安装3组给料漏斗,利用两台重型铲车交替向漏斗内输送物料。
实际生产过程中,该漏斗易发生蓬眼,阴雨天气更甚;因原煤中大块,易造成堵眼断煤,并且处理困难。
针对入料不畅问题,该厂采取溜槽内敷设搪瓷板、改造溜槽角度、扩大下料口径等;从使用效果来看,蓬眼问题有所改善,但大块堵眼未得到解决。
(2)入料不均,瞬时量控制困难。
原煤通过铲车给入,供煤连续性差,煤量忽大忽小;因给煤漏斗设计问题,瞬时量控制困难,铲车供煤量无法调节,物料过大时甚至导致皮带电机过载。
(3)生产连续性差,原煤合介桶液位忽高忽低,实际测量密度频繁波动。
测量密度波动高达15—30Kg/L,严重影响质量控制。
(4)重介精煤、粗精煤灰分异常波动,精煤产率亏损、中煤产率偏高。
自外来煤入洗,2月份重介精煤灰分最低为8.14%,最高高达11.26%。