用于微流控芯片的PDMS微混合器工艺和数值分析_陈实
微流控芯片加工中的PDMS软刻蚀技术和聚合物成型介绍

微流控芯⽚加⼯中的PDMS软刻蚀技术和聚合物成型介绍微流控芯⽚⼤致可以分为三种类型:PDMS芯⽚、聚合物芯⽚(COC、PMMA、PC等)和玻璃芯⽚。
三种不同类型的芯⽚各有不同的加⼯⽅法。
本⽂主要介绍PDMS芯⽚加⼯的软光刻/软刻蚀技术(soft lithography technique)和聚合物成型技术。
什么是PDMS软刻蚀技术?软刻蚀技术可以被看做光刻技术的⼀种扩展延伸。
最初,标准的光刻技术在微电⼦企业中主要被⽤来处理半导体材料。
光刻技术从本质上讲⾮常适合⽤来处理光刻胶。
因此,⼤部分微流控器件仍旧使⽤光刻技术来加⼯SU-8模板,集成微结构的PDMS层的加⼯过程如图1所⽰。
图1 集成微结构的PDMS层的加⼯过程[1]。
图中(a)-(d)对应通过光刻技术加⼯硬质模板的过程。
图中(e)-(f)可以被认为是软刻蚀过程的⼀部分。
软刻蚀技术扩展了传统光刻技术的可能性。
不同于光刻技术,软刻蚀技术可⽤于加⼯处理⼴泛的弹性材料例如机械软材料。
由于涉及的材料具有⼀定的“柔软性”,这就是为什么这种刻蚀技术使⽤“soft”这个单词。
软刻蚀技术⾮常适合⽤于聚合物、凝胶以及有机单层材料。
PDMS材料具有许多⾮常优异的特性如廉价、⽣物兼容性、低毒性、化学惰性、多种多样的表⾯化学绝缘性以及机械灵活性和耐久性等,因此,其在软刻蚀应⽤中被⼴泛的⼤量使⽤。
此外,PDMS很容易被操控和加⼯,所以,仅需要很少的仪器设备[2]便可加⼯PDMS器件。
应该注意的是属于软刻蚀技术并不是指⼀个独特的加⼯技术。
软刻蚀技术实际上包含了许多的加⼯⽅法,这种加⼯⽅法全部是基于使⽤类似于图1f的PDMS模板层。
为了⽅便提供⼀个简要的概述,如下部分将会介绍和软刻蚀技术相关的核⼼技术。
微流控芯⽚中的PDMS软刻蚀技术软刻蚀技术的第⼀个基本特性是获得密封的微流控器件。
典型的情形是,压印在PDMS层上微通道紧密的与玻璃⽚结合在⼀起,请见如下图2。
另外⼀种情况是另外⼀⽚没有通道的PDMS⽚与带有微通道的PDMS层紧密的结合在⼀起。
pdms基微流控芯片的制作

pdms基微流控芯片的制作英文回答:PDMS-based Microfluidic Chip Fabrication.PDMS (polydimethylsiloxane) is a widely used material for microfluidic chip fabrication due to its biocompatibility, optical transparency, and ease of fabrication. Here are the general steps involved in PDMS-based microfluidic chip fabrication:1. Design and Layout:The first step is to design and layout the microfluidic chip using computer-aided design (CAD) software. This involves defining the channels, chambers, and other features of the chip.2. Master Mold Fabrication:Once the design is complete, a master mold isfabricated using photolithography. A photoresist is applied to a silicon wafer and patterned using ultraviolet (UV) light through a mask. The exposed photoresist is then developed, leaving a pattern of the microfluidic channels on the wafer.3. PDMS Preparation:PDMS is a two-part silicone elastomer. To prepare the PDMS, the two parts are mixed thoroughly and degassed to remove air bubbles.4. PDMS Casting:The degassed PDMS is poured onto the master mold and placed in a vacuum chamber to remove any remaining air bubbles. The PDMS is then cured in an oven at a temperature of typically 65-85°C for 30 minutes to 2 hours.5. Bonding:Once the PDMS is cured, it is peeled off the mastermold and bonded to a glass or PDMS substrate. Bonding canbe achieved using oxygen plasma treatment, which creates a hydrophilic surface on both the PDMS and the substrate, allowing them to bond together.6. Inlet and Outlet Formation:Holes are punched into the PDMS chip to create inlets and outlets for fluidic connections.7. Functionalization:The microfluidic chip may be further functionalizedwith various coatings or treatments to improve its performance or to enable specific applications. For example, the chip can be coated with a protein-resistant coating to prevent non-specific protein binding.Applications of PDMS-based Microfluidic Chips.PDMS-based microfluidic chips have a wide range ofapplications in various fields, including:Biomedical research: Cell culture, drug screening, microfluidics for diagnostics.Chemical analysis: Microreactors, microchip electrophoresis.Environmental monitoring: Water quality monitoring, air pollution detection.Lab-on-a-chip devices: Miniaturized and portable devices for point-of-care diagnostics and analysis.Advantages of PDMS as a Microfluidic Chip Material.Biocompatible and non-cytotoxic.Transparent, allowing for optical imaging.Easy to fabricate and mold into complex shapes.Gas-permeable, allowing for oxygen exchange in cell culture applications.Chemically inert and resistant to most solvents.中文回答:PDMS基微流控芯片的制作。
PDMS微流控芯片关键工艺技术研究
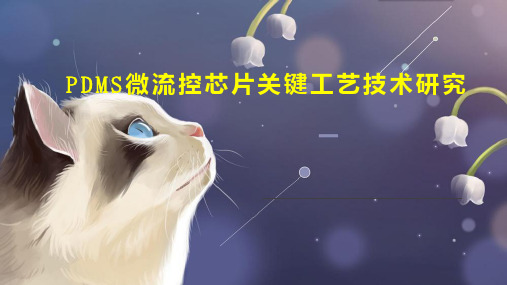
总之,PDMS微流控芯片中的微通道加工技术是一种具有重要应用价值和发展前 景的技术。通过深入研究和不断创新,我们有理由相信,未来PDMS微流控芯片 将在更多领域发挥重要作用,为人类的生产和生活带来更多便利和效益。
引言
随着科技的不断进步,微流控芯片技术在医疗、生物、化学等领域的应用越来 越广泛。微流控芯片具有高效、快速、集成度高、能耗低等优点,而微结构制 品注塑成型工艺技术则是实现微流控芯片大规模生产的关键技术之一。本次演 示旨在探讨基于微流控芯片的微结构制品注塑成型工艺技术,以期为微流控芯 片技术的发展提供新的思路和方法。
2、高集成度:微流控芯片内部通常包含多种不同功能的微通道,可以将多个 实验步骤集成在一起,提高实验效率。
3、自动化:通过微流控芯片,可以实现实验过程的自动化,减少人工操作, 提高实验的准确性和可重复性。
4、实时检测:微流控芯片可以集成传感器,实现实验数据的实时检测和记录, 为科学研究提供更多的信息和便利。
2、成本低:使用该技术,可以大幅降低微流控芯片的生产成本,有利于技术 的推广和应用。
3、结构稳定:通过微结构制品注塑成型工艺技术制备的微流控芯片,具有较 高的结构稳定性和可靠性,可以满足长期使用的要求。
实验方法与结果
本次演示采用微结构制品注塑成型工艺技术,制备了一系列微流控芯片,并对 其性能进行了检测。首先,选取合适的聚合物材料,制备出模具。然后,将聚 合物材料注入模具,并在适当的温度和压力下进行成型。最后,对成型的微流 控芯片进行切割、打磨和检测。
微通道加工的方法主要包括光刻和微磨削等。光刻是一种通过光敏材料和光照 来制造微通道的技术。首先,在光敏材料上涂覆一层光刻胶,然后通过紫外线 或其他光源照射光刻胶,使其发生化学反应。最后,通过显影剂将反应后的光 刻胶溶解,从而得到所需的微通道图案。
PDMS柔性微流控芯片制造工艺调整策略讨论

PDMS柔性微流控芯片制造工艺调整策略讨论概述:PDMS(聚二甲基硅氧烷)柔性微流控芯片具有广泛的应用前景,因其优异的柔软性、生物相容性和可加工性而备受关注。
然而,在制造过程中,工艺参数的调整至关重要,以确保最佳的性能和可靠性。
本文将讨论PDMS柔性微流控芯片制造工艺调整的策略以及可能的影响因素。
工艺调整策略:1. PDMS比例的选择:PDMS通常以基胶和交联剂的混合物形式存在,不同的比例将直接影响PDMS的硬度和柔软性。
为了实现所需的柔性微流控芯片,可以通过调整PDMS的比例来改变其硬度。
通常,较高的交联剂比例会导致更硬的芯片,而较低的交联剂比例会导致更柔软的芯片。
因此,在制备芯片之前,需要根据实际需求选择适当的PDMS比例。
2. 模具设计和制备:模具的设计和制备是PDMS微流控芯片制造过程中关键的一步。
确保模具的精确性和可靠性对实现高质量的芯片至关重要。
模具的设计应考虑到所需通道的形状、尺寸和布局,以及连接物和流体进出口的位置。
此外,选择适当的制模材料和制备方法也对芯片的质量和可靠性有重要影响。
3. PDMS的准备和处理:在得到适当比例的PDMS混合物后,需要进行准备和处理以确保最佳的性能。
首先,应将混合物放入真空箱中除气,以避免在PDMS固化过程中产生气泡。
其次,在PDMS固化之前,可在混合物表面使用等离子处理等方法,提高与其他材料的粘合性。
最后,热处理PDMS 样品可以提高其机械性能和抗老化能力。
影响因素:1. 材料的选择:除了PDMS外,一些其他材料也广泛应用于微流控芯片的制造中。
例如,硅基或玻璃基材可用于制作刚性微流控芯片,而聚合物基材(如PET和PVC)可用于制作柔性微流控芯片。
选择适当的材料取决于应用需求和工艺技术。
2. 设计参数的优化:微流控芯片的性能主要由设计参数决定。
例如,通道的形状、尺寸和排列方式直接影响流体在芯片中的流动性能。
通过优化这些设计参数,可以实现更好的流动控制、混合效果和生物反应效率。
一种PDMS微流控芯片加工中套刻工艺的对准操作流程[发明专利]
![一种PDMS微流控芯片加工中套刻工艺的对准操作流程[发明专利]](https://img.taocdn.com/s3/m/b0080a22f08583d049649b6648d7c1c708a10b22.png)
(19)中华人民共和国国家知识产权局(12)发明专利申请(10)申请公布号 (43)申请公布日 (21)申请号 202011243536.8(22)申请日 2020.11.10(71)申请人 南通大学地址 226000 江苏省南通市啬园路9号(72)发明人 赵幸福 孙逸凡 印唐臣 朱海燕 张迎洁 (74)专利代理机构 南京瑞弘专利商标事务所(普通合伙) 32249代理人 许洁(51)Int.Cl.G03F 9/00(2006.01)(54)发明名称一种PDMS微流控芯片加工中套刻工艺的对准操作流程(57)摘要本发明公开了一种PDMS微流控芯片加工中套刻工艺的对准操作流程,本发明在光刻之前充分、系统地做好准备工作,光刻时便得心应手,可以快速而顺利完成套刻对准。
准备工作完成后,光刻机操作时间可以控制在半小时以内,提高了工作效率,也减少了机器的消耗。
使用本发明的技术方案,初学者也能较好地完成高难度的套刻对准。
使用本技术方案在普通国产曝光机JKG ‑2A进行套刻也可以实现与进口光刻机ABM.Inc.Mask Aligner相同的套刻结果,使用本技术进行微流控加工的套刻对准,对准偏差小于5微米,然而对准精度要求为只要能连通高低通道即可,完全满足微流控芯片加工使用。
权利要求书1页 说明书5页 附图2页CN 112346308 A 2021.02.09C N 112346308A1.一种PDMS微流控芯片加工中套刻工艺的对准操作流程,其特征在于:包括如下步骤:步骤一、首先在掩膜上找到四个参考点,延长掩膜X、Y轴在它们与边缘交点位置做标记;步骤二、一次曝光时硅片放在硅片呈物台中央,并在呈物台上做好硅片位置记号,安装掩膜尽量将掩膜中心置于掩膜台中心,后用记号笔在掩膜台上留下掩膜边缘四个点的位置信息,为防止后续操作中掩膜位置发生偏移可以用胶带黏附掩膜初步固定;步骤三、二次曝光即套刻时,在硅片上标记点可以用彩色水笔涂布色彩,参照事先记号笔做好的硅片位置记号与掩膜位置记号放好硅片、掩膜,掩膜再用胶带固定,完成此“位置重叠”掩膜硅片安装;步骤四、然后,显微镜下操作进行粗对准:先透过掩膜找到硅片上的彩色,在彩色周围找到对准标记,这里对准标记一定要成对查找,找对位的两个标记,前后移动光刻机平台查找对位位置对准标记并进行位置调整、对准,单独一个对准标记的对准无效,必须要对位的两个标记都对准,选择对位两标记点进行对准很有必要,操作简便,也能够有效克服掩膜硅片角度偏差造成的偏离;步骤五、前后移动光刻机平台,分析偏差,缓慢旋转硅片纠正偏差,这一角度偏差是套刻都要面临的问题,对准时先进行角度偏差的纠正,再进一步进行精对准,当两个对准标记都对准后便实现套刻对准,曝光可以进行;步骤六、套刻结束,掩膜台上记号应及时除去,以免干扰下一次套刻操作。
pdms微流体生物芯片加工

pdms微流体生物芯片加工
1PDMS微流体生物芯片加工
PDMS微流体生物芯片加工是一种高精度的加工技术,它利用PDMS (共聚二甲基硅氧烷)材料,开发出与微型流体和生物元素相似的芯片。
这种技术在微型生物芯片研究领域已被广泛采纳。
PDMS微流体生物芯片加工技术的主要优点是芯片体积小、加工精度高。
通常,它可以在体积小于微米级的尺寸上一次性完成设计和生产。
目前,已掌握的最小的制程尺寸约为50微米,而它可以实现1微米的制程精度。
PDMS微流体生物芯片加工技术具有很多优点。
首先,它具有良好的精度和可重复性,可以实现高质量、高制程质量的微型生物芯片。
另外,PDMS微流体生物芯片加工技术可以节省大量的制造时间,减少了大量的制程步骤,从而在成本上取得节省。
此外,PDMS微流体生物芯片加工技术也简化了生物及其环境之间的交互。
它可以模拟各种复杂的液体路径,这有助于研究水平的精细调控,一定程度上可以提高实验室工作效率和准确度。
综上所述,PDMS微流体生物芯片加工技术为微型生物芯片研究者提供了一种精确、可靠、可重复的制造技术,为微型生物芯片研究者提供了一种新的解决方案。
因此,PDMS微流体生物芯片加工技术越来
越受到微型生物芯片研究者的关注和认可,届时将在该领域发挥更大的作用。
用于微流控芯片的PDMS微混合器工艺和数值分析

。本 文提出的微混 合器是
依靠改变微通道的外形来增大流体间微接触面积, 以达到提高混合效率的目的, 是一种被动式微混合 器。
# " 微混合器的加工工艺研究
到目前为止, 微混合器的加工材料选择经历了 若干个发展阶段, 从最初的硅材 料发展到玻璃、 石
9 9 收稿日期: "##!:#;:"<; 修订日期: "##!:#!:"= 9 9 作者简介: 陈实 ($<=$ > ) , 男, 湖南人, 硕士, 主要研究
向为 %/%? 微流体。
第 ! 期"
陈实等: 用于微 流控芯片的 #$%& 微混合器工艺和数值分析
8:
一层厚度为 ’(( !) 的 &*+, -(( 型负胶, 甩胶在德 国 ./01 &233 公司生产的自动甩胶机上进行, 然后前 烘以使光刻胶固化。研究发现, ’(( !) &*+, 胶前 烘条件为: !’ 4 烘 5( )67, 升温 8( )67 到 ,’ 4 烘 5 9, 升温到 :’ 4 烘 -’( )67。前烘后进行切胶, 以 使胶表面平整, 同时达到所需厚度。曝光是在德国 ./01 &233 公司 %;! 光刻机上进行, 紫外曝光波长为 5!’ 7) , 曝 光 功 率密 度 为 -< )= > ?) < , 本文得出 ’(( !)厚的胶的最佳曝光时间为 5’( 3 。显影是在 &*+, 胶专用的粗细两种显影液中进行, 之后用异丙 醇溶液融掉硅片表面残留的显影液。 !" !# 复制压模制作 #$%& 微通道 把 #$%& 树脂和凝固剂 ( 罗迪亚公司, @+5(8(; 和 @+5(8(A ) 按照体积比 -(B - 的比例均匀混合, 然 后置于真空箱内脱气泡 5( )67 C ’( )67, 将胶体浇 铸到含模具的硅片表面, 接着固化, 烘箱内 !’ 4 烘 约 8 9, 完成后, 将其从模具上揭下, 得到含有与模具 相同图形的 #$%& 基底 ( 如图 - 所示) 。
微流控芯片的制作

PDMS-玻璃杂合芯片快速制作方法详解(初稿)前言本文以实战制作高度15~80µm的通道为例,详细介绍的PDMS-玻璃杂合芯片的快速制作方法。
注意:进入芯片加工间需穿实验服,进行芯片制作时需带上无粉乳胶手套。
目录一、快速制作SU-8阳模步骤:1. 硅片清洗2.基片加热除湿3.倒胶匀胶4.SU-8基片前烘5.SU-8基片曝光6.SU-8基片后烘7.显影8.坚模二、制作PDMS玻璃杂合芯片步骤1.制备PDMS预聚体2.除去PDMS预聚体中的气泡3.倒胶及PDMS预聚体固化4.揭模,切边,打孔5.键合6.粘蓄液池(可选)三、PDMS-玻璃杂合芯片制作中其他相关细节详解一、快速制作SU-8阳模步骤:一、硅片清洗1.丙酮清洗目的:去除或软化硅片表面有机物操作:带上一次性PE手套。
硅片用玻璃棒隔开,将丙酮倒入烧杯,液面高于硅片顶端所在平面2cm 左右,然后放入超声机,超声40分钟左右(对于旧硅片,可以升温超声,时间也可适当延长);丙酮清洗后,将丙酮小心倒入装丙酮的空瓶,标明“回收”。
2、浓硫酸清洗目的:去除硅片表面的无机物和有机物操作:带上乳胶手套,再带上一次性EP手套,穿实验服。
丙酮清洗过的硅片,先用自来水多涮洗几次,较彻底地去除残余丙酮,避免硫酸和丙酮反应;然后将双氧水倒入烧杯至目标体积的1/4。
然后将烧杯移至合成间的通风厨,小心缓慢将浓硫酸倒入烧杯至目标体积,之后在烧杯上盖上一个玻璃培养皿以减少酸雾的挥发。
3个小时后,浓硫酸与双氧水反应基本结束,将烧杯移至超声机(注意作上浓硫酸的标记以避免别人误伤)超声30min左右,即可将浓硫酸回收。
硫酸回收,一定要倒入装硫酸的瓶子,若没有,可用装过乙醇或丙酮的瓶子,但一定要多用自来水多清洗几次,以避免硫酸与之反应,发生安全事故。
将硫酸倒出时,注意倾倒角度,避免烧杯内的硅片和玻璃棒滑落。
(此步相对较危险,一定要注意安全。
)3.去离子水清洗(18.2)目的:清除浓硫酸和硅片表面一些残余小颗粒操作:带上一次性PE手套。
一种用于微流控芯片制造的PDMS浇注系统及浇注方法[发明专利]
![一种用于微流控芯片制造的PDMS浇注系统及浇注方法[发明专利]](https://img.taocdn.com/s3/m/81a22305a22d7375a417866fb84ae45c3b35c2e6.png)
(19)中华人民共和国国家知识产权局(12)发明专利申请(10)申请公布号 (43)申请公布日 (21)申请号 202010578102.7(22)申请日 2020.06.23(71)申请人 江苏敦超电子科技有限公司地址 213000 江苏省常州市新北区常澄路888号申请人 南京汉星工业设计有限公司(72)发明人 唐文来 樊宁 夏培 乔羽 庄勇进 (74)专利代理机构 南京禾易知识产权代理有限公司 32320代理人 张松云(51)Int.Cl.B29C 39/10(2006.01)B29C 39/24(2006.01)B29C 39/44(2006.01)B81C 1/00(2006.01)(54)发明名称一种用于微流控芯片制造的PDMS浇注系统及浇注方法(57)摘要本发明涉及一种用于微流控芯片制造的PDMS浇注系统及浇注方法,包括PDMS浇注控制单元,所述PDMS浇注控制单元包括计算机、压力控制器、与压力控制器相连的空气压缩机和真空泵;PDMS浇注配料单元,所述PDMS浇注制造单元包括储料罐和混料桶,其中压力控制器的输出端分别连接储料罐的进气孔和混料桶的进气孔,储料罐的出料口与混料桶相连且在储料罐与混料桶之间设有储料罐流量计;PDMS浇注成型单元,所述PDMS浇注成型单元包括挤出装置、芯片模具和与计算机通信连接的三维运动平台。
本发明自动实现PDMS预聚体和PDMS固化剂的进料配比,精准度高;同时通过计算机程序实现PDMS浇注的一体化设计,自动控制整个PDMS浇注过程,无需人工操作,减少人工成本。
权利要求书2页 说明书5页 附图2页CN 111823459 A 2020.10.27C N 111823459A1.一种用于微流控芯片制造的PDMS浇注系统,其特征在于:包括PDMS浇注控制单元,所述PDMS浇注控制单元包括计算机、压力控制器、与压力控制器正压输入端相连的空气压缩机、与压力控制器负压输入端相连的真空泵,计算机与压力控制器相连,用于调整压力控制器的输出状态;PDMS浇注配料单元,所述PDMS浇注配料单元包括储料罐和混料桶,其中压力控制器的输出端分别连接储料罐的进气孔,储料罐的出料口与混料桶相连且在储料罐与混料桶之间设有储料罐流量计,所述储料罐流量计与计算机相连,用于设置和监测储料罐的出料量;PDMS浇注成型单元,所述PDMS浇注成型单元包括挤出装置、芯片模具和与计算机通信连接的三维运动平台,所述挤出装置的挤出喷头固定在维运动平台上,所述芯片模具位于挤出喷头的正下方。
- 1、下载文档前请自行甄别文档内容的完整性,平台不提供额外的编辑、内容补充、找答案等附加服务。
- 2、"仅部分预览"的文档,不可在线预览部分如存在完整性等问题,可反馈申请退款(可完整预览的文档不适用该条件!)。
- 3、如文档侵犯您的权益,请联系客服反馈,我们会尽快为您处理(人工客服工作时间:9:00-18:30)。
的键合。阐述了微混合的机理, 用数值分析方法对三种形状微混合器进行了液体混合效率的分
析, 结果表明, 弯形管道特别是 Z 形管道, 由于惯性力在横截面上产生的二次流动能有效增大液体
间的微混合面积, 因而大大提高了液体混合的效率。
关 键 词: 软光刻; 聚二甲基硅氧烷; 复制- 压模 法; 混合效率
中图分类号: T N 305
为了分 析微混合 器形状 对液体 混合效 果的影 响, 利用 Fluent 软件对如下三种形状的微混合器进 行了流场计算和混合效率分析: T 形管、半圆形管和 Z 字形管( 图 3) 。首先用 Gambit 软件生成几何体并 划分网格、设置边界条件, 然后导入到 Fluent 中完成 计算。本文考察两种液体 a 和 b 的混合程度, 用混 合系数 G 表示: G( s) = Cm in/ Cmax, Cm in 和 C max分别 是液体 b 在通道某个横截面内最小和最大的质量分 数, s 是流程, 采用自然坐标系。考虑对称性, 假设两 种液体均具有同样的物理性质( 和纯水相同) , 只是 使用 a 和 b 加以区别。模 拟条件: 入口管道截面尺 寸 为 200 Lm @ 200 Lm, 混 合 管 道 截 面 尺 寸 为 400 Lm @ 200 Lm, 线性长度为 4 200 Lm, 入口平均 速度 v = 0107 m / s, 分子扩散系数 K= 10- 10 m2/ s。
掩模版由 Illustrator 软件绘制, 最小线宽和间距 不少于 20 Lm, 精度要求不是很高, 因此可用微机控 制打 印机( CD- 102- 4- cp2000, Heidelberg ) 在 胶片上 直接输出图形, 就可得到光刻用掩模版。
模具的制作采用软光刻工艺。首先在硅片上甩
收稿日期: 2006- 05- 29; 修订日期: 2006- 06- 28 作者简介: 陈实( 1981- ) , 男, 湖南人, 硕士, 主要研究方向为 M EM S 微流体。
第6期 2006 年 12 月
微细加工技术 M ICRO FABR ICA T ION T ECHNO LOG Y
文章编号: 1003- 8213( 2006) 06-0048- 04
l16 Dec1 , 2006
用于微流控芯片的 PDM S 微混合器工艺和数值分析
陈 实, 张卫平, 陈文元, 牛志强
文献标识 码: A
1 引言
自从 90 年 代初 瑞士 的 Manz 和 Widm er 提出 / 微 型 全分 析 系 统0 ( L- T AS, M icro T ot al Analysis Syst em) 以来[ 1- 2] , 微流控芯片已经成为了人们的研 究热点。微流控芯片以 M EM S 技术为基础, 将样本 驱动控制单元、处理单元、生化反应单元、检测单元 等集成在一块芯片上, 从而达到快速、准确、小剂量 反应与检测的目的。微混合器是微流控芯片的重要 组成部分之一, 流体混合速度的快慢和混合效率的 高低直接影响着生化反应结果的好坏。国内外已有 不少关于微混合器研究进展的报导, 叙述了不同形 状微 混 合 器 加工 工 艺 和 混 合效 果 的 数 值 模拟 方 法[ 3- 4] , 大体来说, 微混合器按混合方式可以分为主 动式和被动式两大类[ 5] 。本文提出的微混合器是依 靠改变微通道的外形来增大流体间微接触面积, 以 达到提高混合效率的目的, 是一种被动式微混合器。
3 微混合机制和仿真分析
微混合器中主要的混合机制是层流混合[ 11] , 根
图可知, 产生微混合的主要方式有两种: 对 流和分子扩散。对流是指不同流体相对位置的重新 分布, 从而使得流体之间达到混杂的状态, 是一个机 械过程, 由流体的运动特性决定; 分子扩散是由于分 子的热运动使流体从浓度高的区域向浓度低的区域 扩散, 是一个热力学过程, 由液体的热学特性决定。 被动式混合器通过设置特殊的几何形状来改变混合 腔中流场的分布, 使不同流体之间的接触面发生扭 曲变形, 在减小微扩散距离的同时增大了微扩散的 接触面积, 从而有效地提高了微尺度流动混合的效 率[ 12] 。
[ 2] Effenhauser CS, M anz A, W idmer HM1 M anioulation of samole fractions on a capillar y electrophoresis chip [ J]1 Anal Chem, 1995, 67: 2284- 22871
2 微混合器的加工工艺研究
到目前为止, 微混合器的加工材料选择经历了 若干 个发展阶段, 从最初的硅 材料发展到玻 璃、石
英、金属和有机高分子聚合物。早期硅和玻璃使用 较多, 如用于 PCR 扩增的腔体和毛细 管电泳[ 6- 8] 。 硅材料由于工艺成熟、化学惰性和热稳定性良好, 首 先被 用于微流体管 道的加工, 但存在脆性大、成本 高、透光性差、表面化学行为复杂等缺陷; 玻璃虽然 透明, 但是其不定形性使得垂直方向上刻蚀难度较 大, 且封装工艺中要求高温或高电压, 不适合快速、 大批量的生产。
对于 T 形管道中液体的混合而言, 影响混合效 率的最大因素是液体分子的热扩散, 液体分子来不 及充分扩散已经通过管道, 因此, 液体之间形成了明
50
微细加工技术
2006 年
图 5 直管道截面速度分布
( 如图 6 所示) , 在截面上壁面附近液体从微管道内 侧壁流向外侧壁, 在截面底部附近出现了从管道外 侧向内侧的流动, 流场呈顺时针方向分布, 二次流动 使液体以螺旋的形式向前流动, 两种液体之间的接 触面拉伸变形, 增大了微接触的面积, 大大提高了液 体混合的效率( 如图 7 和图 8 所示) 。
图 8 Z 形管道液体 b 质量分布图
图 9 三种微混合器混 合系数与流程 s 的 关系图
积增大, 混合效率大大提高, G 约为 50% ~ 60% 。因 此, 在本文所设定的模拟条件下, Z 形管更有利于液 体的快速混合。模拟结果对用于微流控芯片的微混 合器形状设计具有指导意义。
4 结论
本文介绍了使用软光刻法和紫外光键合技术制 作高分子聚合物 P DMS 被动微混合器的工艺。为得 到较为优化的微混合器结构, 利用数值方法对三种 类型的微管道以及两种流体混合的情形进行了仿真 计算, 分析了混合效率系数随流程变化的情况, 得出 了 Z 字形混合器具有较高混合效率的结论。在不同 流速和雷诺数下液体的混合效率还有待进一步的分析。
本研究采用高分子聚合物 P DMS 来制作微流体 管道。PDMS 中文名为聚二甲基硅氧烷, 具有价格 便宜、透光性好、生物兼容性好、易于封装等特性, 通 过紫外光照射改性, 可以使材料的憎水性得到较好 的改善[ 9] 。模 具采用 SU- 8 100 型负胶( 美国Micro Chem 公司) , SU- 8 胶是一种负性、环氧树脂型、近紫 外线光刻胶, 曝光后能得到侧壁陡直、高深宽比的图 形, 而且具有良好的力学性能、抗化学腐蚀性和热稳 定性。 211 SU- 8 微模具的制作
第6期
陈实等: 用于微流控芯片的 PDM S 微混合器工艺和数值分析
51
个微 流 体 系 统的 设 计、制 造、实 验 和 应 用 有待 于 MEMS 技术及其相关技术的进一步发展。今后微混 合器技术的研究重点将主要集中在微混合理论的发 展、新型材料的应用和加工、与微流体器件的集成和 封装、混合器外形设计优化和产品产业化等方面。
[ 3] W ong Seck Hoe, M ichael C, Ward L , et al1 M icro T- mix er as a rapid mix ing micromix er[ J] 1 Sensors and A ctuators B, 2004, 100: 359- 3791
[ 4] V irginie M eng eaud, Jacques Josserand, Hubert H Girault1 M ix ing processes in a zig zagmicrochannel finite element simulations[ J]1A nal Chem, 2002, 74: 4279- 42861
微混合器的研究工作到目前为止已经取得了很 大的进展, 但是微流体运动和混合的基础理论还很 不成熟, 诸如边界形条件、尺度效应、表面效应和多 相流等问题还未得到很好的解决, 微混合器乃至整
参考文献:
[ 1] M anz A, Harriso n JD, Verooorte E, et al1HM : Capillar y electrophor esis on a chip [ J] 1 J Chromatogr , 1992, 593: 253- 2581
把 PDMS 树脂和凝固剂( 罗迪亚公司, V- 3040A 和 V- 3040B) 按照体积比 10B1 的比例均匀混合, 然 后置于真空箱内脱气泡 30 m in~ 50 min, 将胶体浇 铸到含模具的硅片表面, 接着固化, 烘箱内 65 e 烘 约 4 h, 完成后, 将其从模具上揭下, 得到含有与模具 相同图形的 PDMS 基底( 如图 1 所示) 。
将 PDMS 基底用无水乙醇、去离子水清洗干净 后, 放置在 ZF- Ò 型紫 外分析 仪( 三 个波长 分别为 254 nm, 320 nm 和 365 nm) 下照射约 3 h, 然后与清 洗过的玻璃片贴合在一起, 并施加一定的压力, 再将 其置于对流烘箱内 70 e 下烘 12 h, 即可完成 P DMS 和玻璃片的完全键合。整个工艺过程如图 2 所示。
图 7 半圆形管道液体 b 质量分布图
模拟结果得到了三种形状微混合器的混合系数 G 和流程 s 的关系, 如图 9 所示。由图可见, 在相同 流程 s 的情况下, Z 形管混合效率最高, 半圆形管次 之, T 形管最低。在出口端, T 形管 的混合 效率最 低 , G只有10% 左右; 半圆管和Z形管由于微接触面