等离子增强磁控溅射技术介绍
磁控溅射原理详细介绍课件

氮气(N2)
常与氩气混合使用,用于增加 薄膜的硬度和抗氧化性。
氧气(O2)
用于形成氧化物薄膜,如TiO2 和Al2O3。
选择原则
根据被溅射材料和所需薄膜性 质选择合适的工作气体。
溅射功率与控制
01
02
03
溅射功率
指用于产生溅射的功率, 通常以辉光放电的形式提 供。
控制方法
通过调节辉光放电的电流 或电压来控制溅射功率。
03
放电的物理过程
放电过程中,气体分子在电场中被电离,产生带电粒子,这些带电粒子
在电场中加速运动,与气体分子发生碰撞,使气体分子激发和电离,形
成电子和离子的雪崩效应。
粒子运动与碰撞
带电粒子的运动
在电场中,带电粒子受到电场力 的作用,沿着电场线方向加速运
动。
粒子的碰撞
带电粒子在运动过程中与气体分 子发生碰撞,将动能传递给气体 分子,使气体分子获得足够的能 量以克服束缚力,从原子或分子
磁控溅射原理详细介绍课件
目录
• 磁控溅射原理概述 • 磁控溅射装置与工作原理 • 磁控溅射的物理基础 • 磁控溅射技术参数与控制 • 磁控溅射沉积薄膜性能优化 • 磁控溅射研究前沿与展望
01
磁控溅射原理概述
定义与特性
定义
磁控溅射是一种物理气相沉积技术,通过在真空环境下利用磁场控制电子运动 ,实现高速离子轰击靶材表面,将靶材原子溅射出来并沉积在基材表面形成薄 膜。
工作气体
选择适当的工作气体,如氩气、氮气等,以 获得所需的薄膜性能。
薄膜结构与性能表征
成分分析
通过光谱分析技术确定薄膜的元素组 成。
晶体结构
采用X射线衍射技术分析薄膜的晶体 结构。
微波ECR等离子体增强磁控溅射制备SiNx薄膜及其性能分析

微波ECR 等离子体增强磁控溅射制备SiN x 薄膜及其性能分析3丁万昱 徐 军 李艳琴 朴 勇 高 鹏 邓新绿 董 闯(大连理工大学三束材料表面改性国家重点实验室,大连 116024)(2005年5月24日收到;2005年9月12日收到修改稿) 利用微波ECR 磁控反应溅射法在室温下制备无氢S iN x 薄膜.通过傅里叶红外光谱、X 射线电子谱、膜厚仪、纳米硬度仪、原子力显微镜等分析手段,分析了N 2流量、S i 靶溅射功率等实验参数对S iN x 薄膜结构、化学配比以及机械性质的影响.结果表明,S iN x 薄膜中S i 2N 结构、化学配比及机械性质与等离子体中的S i 元素含量关系密切,随着N 2流量的增加或者S i 靶溅射功率的降低,等离子体中的S i 元素含量降低,S iN x 薄膜结构、化学配比及硬度发生变化,红外光谱发生偏移,硬度下降,沉积速率降低.关键词:SiN x ,磁控溅射,傅里叶变换红外吸收光谱,X 射线电子谱PACC :6855,6860,7830L3国家自然科学基金重大项目(批准号:50390060)资助的课题. E -mail :xujun @11引言SiN x ,由于它具有硬度高、抗腐蚀、耐高温、导热性与绝缘性好、光电性能优良等优点,因而在微电子领域、微机械系统、材料表面改性等诸多领域都得到广泛的应用[1—5].最近,Y en 等人发现SiN x 薄膜的膜厚极限非常低,达到115nm 厚度时仍能形成连续的薄膜,非常适用于计算机高密度磁盘保护膜[6],因此,对SiN x 薄膜的研究再一次在国内外引起重视.由于薄膜中成分配比将直接影响到SiN x 薄膜的性能,所以研究影响SiN x 薄膜成分配比的工艺参数也就具有重要意义.SiN x 薄膜的制备方法有多种,其中最常用的有物理气相沉积(PVD )法、离子束增强沉积(I BE D )法[7]和化学气相沉积(C VD )法[8—10]等.本实验利用微波ECR 等离子体增强磁控反应溅射法制备SiN x 薄膜[11].微波ECR 磁控反应溅射法是PVD 方法中的一种,它兼备了磁控溅射和反应溅射的优点,与C VD 方法相比较,可以在低温环境下(室温)制备SiN x 薄膜,解决了反应温度过高限制SiN x 薄膜应用问题,如SiN x 薄膜作为计算机磁盘保护膜[12,13];并且大大降低薄膜中的H 含量,提高薄膜机械性质,如硬度[12,13].此外,本方法在制备SiN x 薄膜过程中易于控制薄膜结构和成分,薄膜的许多性能可以与用C VD 方法、I BE D 方法制得的薄膜相媲美.21实 验本实验制备SiN x 薄膜设备采用自行研制的微波ECR 磁控溅射系统,关于该系统的详细描述请参阅相关文献[11,14,15].基片材料采用经过抛光处理的(100)取向单晶硅片,依次经过丙酮、酒精、去离子水超声清洗,然后吹干,最后固定在加射频偏压(RF )的载物台上.沉积前先对基片进行溅射清洗(Ar =20sccm ,-400V RF ,10min ),以去除单晶硅基片表面的氧化层,溅射靶材选取纯度为99199%的单晶硅靶,溅射硅靶同样加射频偏压.工作气体为高纯N 2(991999%)和高纯Ar (991999%);在实验过程中,真空室的本底真空抽至510×10-3Pa ;反应气压为012Pa 左右;微波功率为850W.本实验通过改变参数制备出不同的SiN x 薄膜.利用美国尼高利(Nicolet )仪器公司生产的智能型AVAT AR360傅里叶变换红外光谱仪(FT 2IR )(该仪器扫描范围在400—4000cm-1之间,扫描步长为第55卷第3期2006年3月100023290Π2006Π55(03)Π1363206物 理 学 报ACT A PHY SIC A SI NIC AV ol.55,N o.3,March ,2006ν2006Chin.Phys.S oc.2cm -1)、美国Acton 公司的SP 2305型单色仪、英国VG 公司MKII 型X 射线光电子能谱仪等设备分析薄膜的结构及成分,通过MTS XP 纳米硬度仪、Surfcorder ET 4000M 型膜厚仪、NanoScope Ⅲ原子力显微镜(AFM )等仪器分析薄膜的机械性质和表面形貌.实验参数如下表1所示,通过改变N 2流量或者Si 靶溅射功率,制备出不同成分、结构及化学配比的SiN x 薄膜.在改变N 2流量或者Si 靶溅射功率时,薄膜的沉积时间皆为120min ,载物台加的沉积偏压皆为-100V (RF ).表1 实验参数表样品N 2流量ΠsccmAr 流量ΠsccmS i 靶溅射功率ΠW111220350222035034203504820350515203506301035074203008420250942020010420150114205031结果与讨论3111红外光谱图1为在不同N 2流量下沉积的SiN x 薄膜的傅里叶变换红外光谱,图中各条谱线旁边的数字为样品编号.1号谱线为N 2流量为112sccm 时沉积的SiN x 薄膜的傅里叶红外变换光谱(FT 2IR ),从光谱中可以看到,谱线在611135cm -1,896178cm -1,110311cm -1处出现吸收峰,它们分别对应的是,Si 基底、Si 2N 伸缩振动峰、Si 2O 伸缩振动峰[16—18].其中Si 2O 伸缩振动峰主要是由于背底真空中或者样品在空气中吸附的O 2或者H 2O.从谱线中可以发现,与其他方法制备SiN x 薄膜的红外光谱相比较[16—18],本实验的光谱在2200cm -1和3400cm -1处并不存在明显的Si 2H 和N 2H 的伸缩振动峰[16,17],这表明利用本系统制备的SiN x 薄膜中H 杂质含量很低,同时也显示本方法对比PEC VD 方法的优势.从图1还可以发现,随着N 2流量的增加,在870cm -1处的Si -N 伸缩振动峰强度逐渐减弱,但是在1080cm -1处的Si 2O 伸缩振动峰强度逐渐增强,主图1 不同N 2流量下制备的S iN x 薄膜傅里叶变换红外光谱峰逐渐由870cm -1处转移至1080cm -1处,这说明随着N 2气流量的增加,薄膜中的O 含量逐渐增加,当N 2气流量超过15sccm 时,Si 2O 伸缩振动峰变为主峰,即此时薄膜以Si 2O 结构为主[11].这种现象可以解释为如下原因:首先,由于背底真空中有少量的O 2分子,并且O 元素活泼性要远高于N 元素,因此,被溅射出来的Si 原子在沉积过程中首先与O 元素结合,形成SiO 2结构;其次,等离子体中引入N 元素会在Si 靶表面形成氮硅化合物,导致靶中毒现象.随着N 2流量的增加,靶中毒现象加剧,导致Si 靶溅射率降低.综合这两个原因,随着N 2流量增加,到达基片的Si 原子数量在减小,并且到达基片的Si 原子,首先与背底真空中残余的O 2反应形成SiO 2,这样就间接导致薄膜中的Si 2O 键含量增加而Si 2N 键含量减少,从而导致薄膜红外光谱主峰位置由870cm -1向1080cm -1处转移.同时,这种现象也说明利用本系统可以在N 2流量很小的情况下制备出优异的SiN x 薄膜,大大的提高了N 2的利用率,仅2sccm N 2流量就可以在红外光谱上产生强烈的Si 2N 伸缩振动峰.图2为在不同溅射功率下制备的SiN x 薄膜红外光谱,图中各条谱线旁边的数字为样品编号.从光谱中依然可以得出相同规律,即随着Si 靶溅射功率的降低,在SiN x 薄膜的红外光谱中,870cm -1处的Si 2N 伸缩振动峰强度逐渐减弱,但1080cm -1处的Si 2O伸缩振动峰强度逐渐增强.这种现象验证了由上文所提到的那两个原因,随Si 靶溅射功率的降低,Si 靶的溅射速率降低,即到达薄膜生长表面的溅射Si 原子密度减少,其效果等同于靶中毒.上述结果说明4631物 理 学 报55卷等离子体中Si 元素的密度是影响SiN x 薄膜成分和结构的重要条件.图2 不同溅射偏压下制备的S iN x 薄膜傅里叶变换红外光谱为了进一步验证等离子体中Si 元素密度的变化对薄膜成分和结构的影响,利用美国Acton 公司的SP 2305型单色仪发射光谱法(OES )对等离子体中Si 元素密度进行定性测量,结果如图3所示.图3中63312nm ,63417nm 处谱峰分别对应Si ,Si +的发射光谱谱峰[19],从图3中可以看出,随着Si 靶溅射功率的降低,等离子体中Si 元素的发射光谱谱峰强度单调降低,说明随着Si 靶溅射功率的降低,等离子体中Si 元素的密度单调降低,这与FT 2IR 结果中关于等离子体中Si 元素密度的推测很好地符合.同样,在图3中可以看出,随着N 2流量的增加,等离子体中Si 元素发射光谱谱峰强度单调降低,即等离子体中Si 元素的密度也相应降低,这也与FT 2IR 结果中关于等离子体中Si元素密度的推测很好地符合.通过这两个发射光谱检测结果,可以很好地验证FT 2IR 的结论,也与随后的XPS 结论相符合,从而直接验证了等离子体中Si 元素的密度是影响SiN x 薄膜成分和结构的重要条件.3121X 射线电子能谱为了进一步了解SiN x 薄膜的结构与成分,我们对薄膜进行了X 射线电子能谱(XPS )检测.通过对Si 2p 的高分辨XPS 谱进行解谱,可以发现三个高斯峰,结合能分别为9915eV ,10119eV 和10314eV ,这三个高斯峰分别对应Si 2Si 键结构、Si 2N 键结构、Si 2O 键结构[20—23],如图4所示.通过对不同N 2流量下制备的SiN x 薄膜的Si 2p 高分辨XPS 谱解谱比较(图4),可以发现,在N 2流图3 等离子体中S i 元素发射光谱谱峰强度随S i 靶溅射功率、N 2流量的变化图4 不同N 2流量下制备的S iN x 薄膜中S i 2p 的高分辨XPS 谱及其解谱量较小时(112sccm ),SiN x 薄膜中Si 2Si 键结构含量较高,并且Si 2N 键结构中N ΠSi 比值偏小,见表2,薄膜呈现富Si 态.随着N 2流量的增加,SiN x 薄膜中的Si 2Si 键结构在减少,间接导致薄膜中的Si 2N 键结构相对含量增加,在N 2流量为4sccm 时,薄膜中的Si 2N 键结构相对含量达到最大值,此时通过对Si 2p 和N 1s 的高分辨XPS 谱面积计算并用灵敏度因子校56313期丁万昱等:微波ECR 等离子体增强磁控溅射制备S iN x 薄膜及其性能分析正,计算得出此时薄膜的Si 2N 键中N ΠSi 值为1133,与Si 3N 4的化学配比相符合,如表2所示,此时的薄膜也显示出了最好的红外光谱图像以及最好的机械性质.继续增加N 2流量,薄膜中Si 2O 结构相对增加.当N 2流量超过15sccm 时,薄膜由以SiN x 结构为主转变为以SiO 2结构为主,薄膜的红外光谱及机械性质也相应地逐渐向SiO 2结构转变.XPS 结果与FT 2IR 结果很好地符合,进一步证明了在SiN x 薄膜的沉积过程中,等离子体中Si 元素的密度直接影响薄膜的化学配比和机械性质.表2 在不同N 2流量下制备的S iN x 薄膜中S i 2p 的不同结构含量及S i 2N 结构中的N ΠS i 比值S i 2S iS i 2N S i 2O N ΠS i N 11220951692317900187N 44771675015431133N 858818651242111383131生长速率利用Surfcorder ET 4000M 型膜厚仪采用台阶法测得薄膜厚度,经计算可得到薄膜的生长速率.图5为SiN x 薄膜生长速率随N 2流量、溅射功率变化曲线.由图中可以得出,随着N 2流量的增加,SiN x 薄膜的生长速率单调降低;并且,随着Si 靶溅射偏压的降低,SiN x 薄膜的生长速率也单调降低.这种现象同样可以解释为随着N 2流量的增加,或者随着Si 靶溅射功率的降低,都会直接导致Si 靶表面溅射率降低,从而导致等离子体中Si 元素的含量降低,最终导致SiN x 薄膜沉积速率降低.综合薄膜的红外光谱和生长速率这两个结果,我们可以得出,Si 靶单位面积的溅射率,也就是等离子体中Si 元素的密度,在SiN x 薄膜沉积过程起着重要作用.314 薄膜硬度图6为SiN x 薄膜硬度随N 2流量、Si靶溅射功率变化曲线.从图中可以看出,随着Si 靶溅射功率的降低,SiN x 薄膜的硬度单调降低.这种现象同SiN x 薄膜的红外光谱相结合,可以解释为,当Si 靶溅射功率降低时,间接导致到达基片的Si 原子数量降低,薄膜SiN x 结构含量减少,薄膜的主要成分变为SiO 2结构.因此,薄膜硬度会降低,由SiN x 结构硬度转变为SiO 2结构硬度.随着N 2流量的增加,SiN x 薄膜硬度先增加后减小,在N 2流量为4sccm 时,图5 S iN x 薄膜生长速率随N 2流量、S i 靶溅射功率变化曲线图6 S iN x 薄膜硬度随N 2流量、S i 靶溅射功率变化曲线SiN x 薄膜得到最大硬度,为2219G Pa ,这一值与其他研究小组所得结果一致[6,12,13].结合SiN x 薄膜的XPS 及FT 2IR 结果,这种现象可以解释为,在N 2流量很小时,SiN x 薄膜呈现富Si 态,此时薄膜硬度是SiN x ,SiO 2,非晶硅三者的混合硬度,因此硬度值介于较软的SiO 2、非晶硅和较硬的SiN x 之间.随着N 2流量的增加,薄膜中的SiN x 含量逐渐增加,当N 流量为4sccm 时,薄膜中的N ΠSi 比例达到最佳的1133,因此薄膜硬度达到最大值,2219G Pa.继续增加N 2流量,由于靶中毒现象增加导致薄膜中SiN x 含量降低,薄膜由以SiN x 结构为主逐渐向以SiO 2结构为主转变,因此薄膜硬度随之向SiO 2硬度转变.当N 2流量增加至35sccm 时,薄膜中SiO 2含量较高,同时Si 2N 键结构中的N ΠSi 比值偏离标准值1133,薄膜的硬度也降低至11G Pa 左右,接近于SiO 2的硬度[24].6631物 理 学 报55卷图7 不同N 2流量下制备的S iN x 薄膜表面形貌3151薄膜表面形貌由AFM 观测得到SiN x 薄膜的表面形貌及表面粗糙度.图7为在不同N 2流量下制备的SiN x 薄膜表面形貌,从图中可以看出薄膜表面光滑,没有明显的岛状生长模式.但是随着N 2流量的增加,薄膜的表面粗糙度程度增大.图8为由以上各图片得到的SiN x 薄膜表面粗糙度随N 2流量变化曲线.从图中可以看出,随着N 2流量的增加,薄膜的表面粗糙度略有增加,但总体保持在012nm 以下,这说明利用本技术制备的SiN x 薄膜可以达到在原子尺度上平滑.由本系统沉积的SiN x 薄膜的表面粗糙度低于由电弧离子镀、LPC VD 或者PEC VD 等其他方法制备的SiN x 薄膜的表面粗糙度1—2个数量级[21].这种现象是由于利用本系统沉积的SiN x 薄膜具有较低的生长速率(与电弧离子镀或者C VD 相比较),因此薄膜具有较低的表面粗糙度.图8 S iN x 薄膜表面粗糙度随N 2流量变化曲线41结 论由微波ECR 磁控溅射系统在室温下制备出具有较好结构及性能的无氢SiN x 薄膜.利用FT 2IR ,76313期丁万昱等:微波ECR 等离子体增强磁控溅射制备S iN x 薄膜及其性能分析XPS,纳米硬度仪,AFM,轮廓仪等设备对薄膜进行了结构和性能分析,结果表明,SiNx薄膜的结构和性能强烈依赖于等离子体中Si元素的含量.增加N2流量或者降低Si靶溅射功率,都会导致等离子体中Si元素含量减少,并最终改变SiN x薄膜的结构及化学配比,降低薄膜的机械性质.在N2流量为4sccm,溅射功率为350W时,等离子体中Si元素含量达到最大值,此时,SiNx薄膜的化学配比达到最佳,x值为1133,薄膜硬度亦达到最高值2219G Pa,同时薄膜显示出了最好的红外吸收光谱以及较低的表面粗糙度.[1]Skordas S,S irinakis G,Y u W et al2000Mater.Res.Soc.Symp.Proc109606[2]M orosanu C E1980Thin.Solid.Films17165[3]French P J,Sarro P M,M alle′e R et al1997Sens.Actuator s A14958[4]Bustillo J M,H owe R T1998Muller.R.S.Proc.IEEE861552[5]Eaton W P,Sm ith J H1997Smart.Mater.Struct6530[6]Y en B K,White R L,W altman R J et al2003J.App.Phys.938704[7]Xu D,Zhu H,T ang L J et al1995Acta.Meta.Sin.431(inChinese)[徐 东、朱 宏、汤丽娟等1995金属学报431] [8]Chen J F,Wu X Q,W ang D Q et al1999Acta.Phys.Sin.481310(in Chinese)[陈俊芳、吴先球、王德秋等1999物理学报481310][9]Zhang G W,Long F2001Semi.Opt.22201(in Chinese)[张顾万、龙 飞2001半导体光电22201][10]Y u W,Liu L H,H ou H H et al2003Acta.Phys.Sin.52687(inChinese)[于 威、刘丽辉、侯海虹等2003物理学报52687][11]Ding W Y,Xu J,Piao Y et al2005Chin.Phys.Lett.222332[12]Vila M,Ca′ceres D,Prieto C et al2003J.App.Phys.947868[13]Savall C,Bruyera J C,S toquert J P et al1995Thin.Solid.Films260174[14]Li X,T ang Z A,M a GJ et al2003Chin.Phys.Lett.20692[15]Xu J,M a T C,Lu W Q et al2000Chin.Phys.Lett.17586[16]Y ota J,Hander J,Saleh A A2000J.Vac.Sci.T echnol A18(2)372[17]Vargheese J K D,Rao G M2001J.Vac.Sci.Technol.A191336[18]Lu Z,Santos2Filho P,S tevens G et al2001J.Vac.Sci.Technol.A191336[19]NIST Atom ic S pectrum Database,ver.310,http:ΠΠphysics.nist.g ov[20]M oulder J F,S tickle W F,S obol P E et al1995Handbook o f X2rayPhotoelectron Spectroscopy,Physical Electronics Inc,page57and253[21]Y ang G R,Zhao Y P,Hu Y Z et al1998Thin.Solid.Films333219[22]Bustarret E,Bens ouda M,Habrard M C et al1988Phys.Revi.B388171[23]Xu S H,X in Y,Ning Z Y et al2003Acta.Phys.Sin.521287[24]Scanlon M R,Cammarata R C1994J.Appl.Phys.763387Characterization of silicon nitride films prepared byMW2ECR magnetron sputtering3Ding W an2Y u Xu Jun Li Y an2Qin Piao Y ong G ao Peng Deng X in2Lü D ong Chuang (State K ey Laboratory o f Material Modification by Laser,Ion and Electron Beams,Dalian Univer sity o f Technology Dalian 116024,China)(Received24M ay2005;revised manuscript received12September2005)AbstractHydrogen2free silicon nitride films were deposited at room tem perature by m icrowave electron cyclotron resonance(ECR) plasma source enhanced unbalanced magnetron sputtering system.F ourier2trans form in frared spectroscopy and X2ray photoelectron spectroscopy were used to study the bond type,the change of bond structures,and the stoichiometry of the silicon nitride films.Atom ic2force m icroscopy and nano2indentation were used to study the m orphological features and mechanical characteristics of the films.The results indicate that the structure and characteristics of the films deposited by this technique depend strongly on the density of sputtered S i in plasma and the films deposited at4sccm N2flow show excellent stoichiometry and properties.K eyw ords:silicon nitride,W M2ECR plasma sputtering,FT2IR,XPSPACC:6855,6860,7830L3Project supported by the National Natural Science F oundation of China(G rant N o.50390060).E-mail:xujun@8631物 理 学 报55卷。
磁控溅射(1讲义理论)

磁控溅射(1讲义理论)磁控溅射【实验目的】1、了解磁控溅射基本原理。
2、了解射频磁控溅射仪器构造及使用方法。
3、了解利用射频磁控溅射制备薄膜。
【实验仪器】DHRM-3射频磁控溅射镀膜装置【实验原理】1、磁控溅射原理:用高能粒子(大多数是由电场加速的正离子)撞击固体表面,在与固体表面的原子或分子进行能量交换后,从固体表面飞出原子或分子的现象称为溅射。
按照溅射理论的级联碰撞模型如图1所示,当入射离子与靶原子发生碰撞时把能量传给靶原子,在准弹性碰撞中,通过动量转移导致晶格的原子撞出,形成级联碰撞。
当级联碰撞延伸到靶表面,使表面粒子的能量足以克服结合能时,表面粒子逸出成为溅射粒子。
溅射粒子沉积到基底或工件表面形成薄膜的方法称为溅射镀膜法。
对于直流溅射,靶材是需要溅射的材料,它作为阴极,相对于基底有数千伏的电压。
对系统预抽真空以后,充入适当压力的惰性气体。
例如Ar2作为气体放电的载体,压力一般为1~10Pa的范围内。
在正负极高压的作用下,极间的气体原子将被大量电离。
电离过程使Ar原子电离成为Ar+离子和可以独立运动的电子e。
其中电子飞向阳极,而带正电荷的Ar+离子则在高压电场的加速作用下高速飞向作为阴极的靶材,并与靶材原子发生级联碰撞而使靶表面粒子逸出,沉积在基底上而形成薄膜。
直流溅射只能沉积金属膜,而不能沉积绝缘介质膜。
其原因是由于,当溅射绝缘介质靶材时,轰击绝缘介质靶材表面的正离子和电荷无法中和,于是导致靶面电位升高,外加电压几乎都加在靶(绝缘介质)上,极间的粒子加速与电离就会变小,以至于溅射不能维持。
如果在靶和基底之间加一射频电压,那么溅射将可以维持。
这是因为在溅射靶电极处于高频电压的负半周时,正离子对靶材进行轰击引起溅射。
与此同时,在介质靶面积累了大量的正电荷。
当溅射靶电极处于高频电压的正半周时,由于电子对靶材进行轰击中和了积累在介质靶面的正电荷,就为下一周期的溅射创造了条件。
这样,在一个周期内正离子和电子可以交替地轰击靶子,从而实现溅射材料实质的目的。
等离子增强磁控溅射Ti_Si_C_N基纳米复合膜层耐冲蚀性能研究
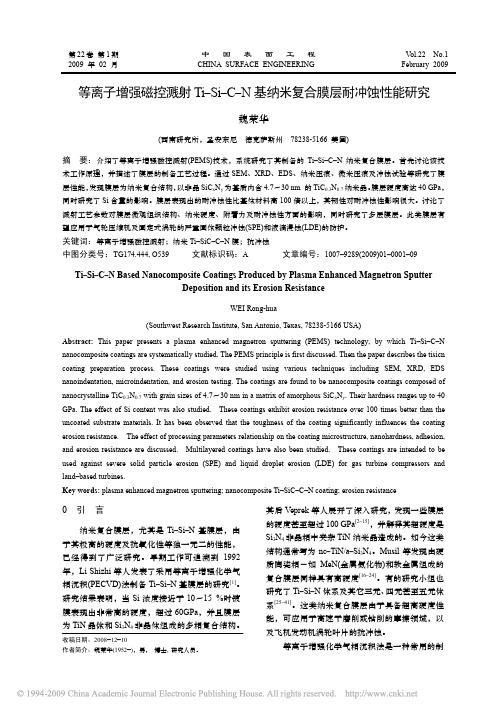
等离子增强磁控溅射Ti–Si–C–N基纳米复合膜层耐冲蚀性能研究魏荣华(西南研究所,圣安东尼德克萨斯州 78238-5166 美国)摘要:介绍了等离子增强磁控溅射(PEMS)技术,系统研究了其制备的Ti–Si–C–N纳米复合膜层。
首先讨论该技术工作原理,并描述了膜层的制备工艺过程。
通过SEM、XRD、EDS、纳米压痕、微米压痕及冲蚀试验等研究了膜层性能,发现膜层为纳米复合结构,以非晶SiC x N y为基质内含4.7~30 nm 的TiC0.3N0.7纳米晶。
膜层硬度高达40 GPa,同时研究了Si含量的影响。
膜层表现出的耐冲蚀性比基体材料高100倍以上,其韧性对耐冲蚀性影响很大。
讨论了溅射工艺参数对膜层微观组织结构、纳米硬度、附着力及耐冲蚀性方面的影响,同时研究了多层膜层。
此类膜层有望应用于气轮压缩机及固定式涡轮的严重固体颗粒冲蚀(SPE)和液滴浸蚀(LDE)的防护。
关键词:等离子增强磁控溅射;纳米Ti–SiC–C–N膜;抗冲蚀中图分类号:TG174.444, O539 文献标识码:A 文章编号:1007–9289(2009)01–0001–09Ti–Si–C–N Based Nanocomposite Coatings Produced by Plasma Enhanced Magnetron SputterDeposition and its Erosion ResistanceWEI Rong-hua(Southwest Research Institute, San Antonio, Texas, 78238-5166 USA)Abstract: This paper presents a plasma enhanced magnetron sputtering (PEMS) technology, by which Ti–Si–C–N nanocomposite coatings are systematically studied. The PEMS principle is first discussed. Then the paper describes the tisicn coating preparation process. These coatings were studied using various techniques including SEM, XRD, EDS nanoindentation, microindentation, and erosion testing. The coatings are found to be nanocomposite coatings composed of nanocrystalline TiC0.3N0.7 with grain sizes of 4.7~30 nm in a matrix of amorphous SiC x N y. Their hardness ranges up to 40 GPa. The effect of Si content was also studied. These coatings exhibit erosion resistance over 100 times better than the uncoated substrate materials. It has been observed that the toughness of the coating significantly influences the coating erosion resistance. The effect of processing parameters relationship on the coating microstructure, nanohardness, adhesion, and erosion resistance are discussed. Multilayered coatings have also been studied. These coatings are intended to be used against severe solid particle erosion (SPE) and liquid droplet erosion (LDE) for gas turbine compressors and land–based turbines.Key words: plasma enhanced magnetron sputtering; nanocomposite Ti–SiC–C–N coating; erosion resistance0 引言纳米复合膜层,尤其是Ti–Si–N基膜层,由于其极高的硬度及抗氧化性等独一无二的性能,已经得到了广泛研究。
等离子增强磁控溅射技术
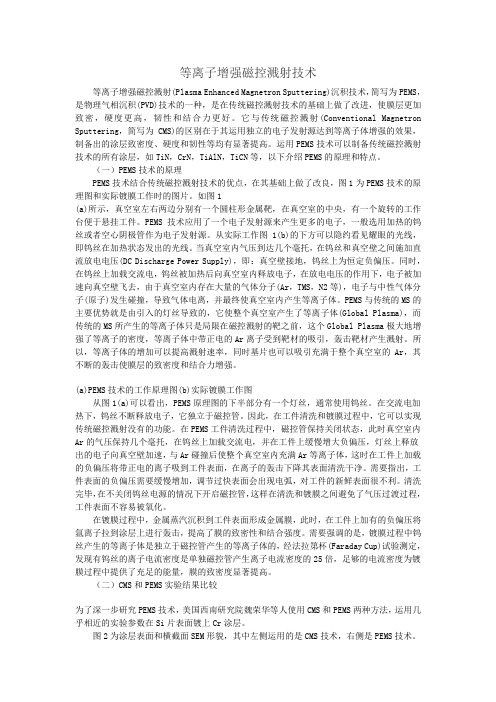
等离子增强磁控溅射技术等离子增强磁控溅射(Plasma Enhanced Magnetron Sputtering)沉积技术,简写为PEMS,是物理气相沉积(PVD)技术的一种,是在传统磁控溅射技术的基础上做了改进,使膜层更加致密,硬度更高,韧性和结合力更好。
它与传统磁控溅射(Conventional Magnetron Sputtering,简写为CMS)的区别在于其运用独立的电子发射源达到等离子体增强的效果,制备出的涂层致密度、硬度和韧性等均有显著提高。
运用PEMS技术可以制备传统磁控溅射技术的所有涂层,如TiN,CrN,TiAlN,TiCN等,以下介绍PEMS的原理和特点。
(一)PEMS技术的原理PEMS技术结合传统磁控溅射技术的优点,在其基础上做了改良,图1为PEMS技术的原理图和实际镀膜工作时的图片。
如图1(a)所示,真空室左右两边分别有一个圆柱形金属靶,在真空室的中央,有一个旋转的工作台便于悬挂工件。
PEMS技术应用了一个电子发射源来产生更多的电子,一般选用加热的钨丝或者空心阴极管作为电子发射源。
从实际工作图1(b)的下方可以隐约看见耀眼的光线,即钨丝在加热状态发出的光线。
当真空室内气压到达几个毫托,在钨丝和真空壁之间施加直流放电电压(DC Discharge Power Supply),即:真空壁接地,钨丝上为恒定负偏压。
同时,在钨丝上加载交流电,钨丝被加热后向真空室内释放电子,在放电电压的作用下,电子被加速向真空壁飞去,由于真空室内存在大量的气体分子(Ar,TMS,N2等),电子与中性气体分子(原子)发生碰撞,导致气体电离,并最终使真空室内产生等离子体。
PEMS与传统的MS的主要优势就是由引入的灯丝导致的,它使整个真空室产生了等离子体(Global Plasma),而传统的MS所产生的等离子体只是局限在磁控溅射的靶之前,这个Global Plasma极大地增强了等离子的密度,等离子体中带正电的Ar离子受到靶材的吸引,轰击靶材产生溅射。
等离子体增强的磁控溅射TiSiN薄膜结构与耐蚀性
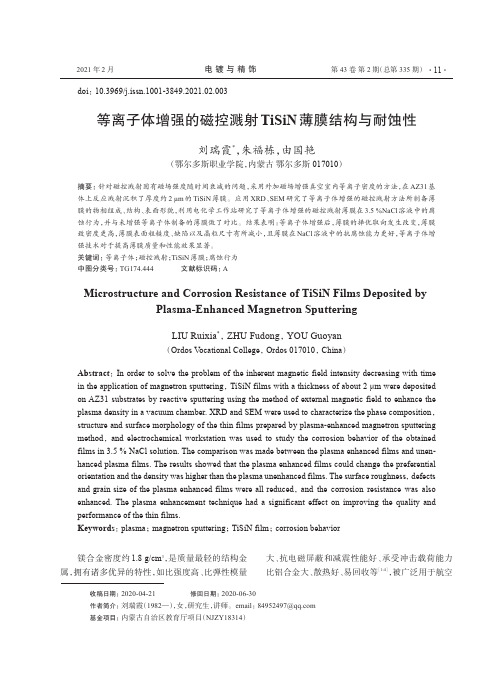
等离子体增强的磁控溅射TiSiN薄膜结构与耐蚀性刘瑞霞*,朱福栋,由国艳(鄂尔多斯职业学院,内蒙古鄂尔多斯017010)摘要:针对磁控溅射固有磁场强度随时间衰减的问题,采用外加磁场增强真空室内等离子密度的方法,在AZ31基体上反应溅射沉积了厚度约2μm的TiSiN薄膜。
应用XRD、SEM研究了等离子体增强的磁控溅射方法所制备薄膜的物相组成、结构、表面形貌,利用电化学工作站研究了等离子体增强的磁控溅射薄膜在3.5%NaCl溶液中的腐蚀行为,并与未增强等离子体制备的薄膜做了对比。
结果表明:等离子体增强后,薄膜的择优取向发生改变,薄膜致密度更高,薄膜表面粗糙度、缺陷以及晶粒尺寸有所减小,且薄膜在NaCl溶液中的抗腐蚀能力更好,等离子体增强技术对于提高薄膜质量和性能效果显著。
关键词:等离子体;磁控溅射;TiSiN薄膜;腐蚀行为中图分类号:TG174.444文献标识码:AMicrostructure and Corrosion Resistance of TiSiN Films Deposited byPlasma-Enhanced Magnetron SputteringLIU Ruixia*,ZHU Fudong,YOU Guoyan(Ordos Vocational College,Ordos017010,China)Abstract:In order to solve the problem of the inherent magnetic field intensity decreasing with time in the application of magnetron sputtering,TiSiN films with a thickness of about2μm were deposited on AZ31substrates by reactive sputtering using the method of external magnetic field to enhance the plasma density in a vacuum chamber.XRD and SEM were used to characterize the phase composition,structure and surface morphology of the thin films prepared by plasma-enhanced magnetron sputtering method,and electrochemical workstation was used to study the corrosion behavior of the obtained films in3.5%NaCl solution.The comparison was made between the plasma enhanced films and unen‐hanced plasma films.The results showed that the plasma enhanced films could change the preferential orientation and the density was higher than the plasma unenhanced films.The surface roughness,defects and grain size of the plasma enhanced films were all reduced,and the corrosion resistance was also enhanced.The plasma enhancement technique had a significant effect on improving the quality and performance of the thin films.Keywords:plasma;magnetron sputtering;TiSiN film;corrosion behavior镁合金密度约1.8g/cm3,是质量最轻的结构金属,拥有诸多优异的特性,如比强度高、比弹性模量大、抗电磁屏蔽和减震性能好、承受冲击载荷能力比铝合金大、散热好、易回收等[1-4],被广泛用于航空doi:10.3969/j.issn.1001-3849.2021.02.003收稿日期:2020-04-21修回日期:2020-06-30作者简介:刘瑞霞(1982—),女,研究生,讲师。
磁控溅射技术
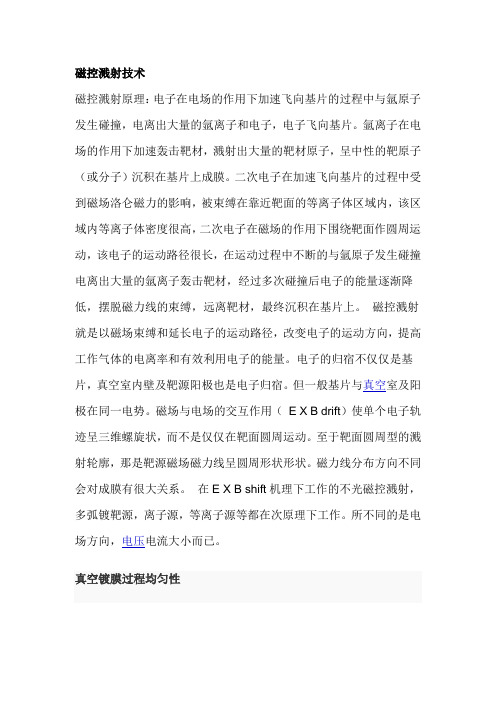
磁控溅射技术磁控溅射原理:电子在电场的作用下加速飞向基片的过程中与氩原子发生碰撞,电离出大量的氩离子和电子,电子飞向基片。
氩离子在电场的作用下加速轰击靶材,溅射出大量的靶材原子,呈中性的靶原子(或分子)沉积在基片上成膜。
二次电子在加速飞向基片的过程中受到磁场洛仑磁力的影响,被束缚在靠近靶面的等离子体区域内,该区域内等离子体密度很高,二次电子在磁场的作用下围绕靶面作圆周运动,该电子的运动路径很长,在运动过程中不断的与氩原子发生碰撞电离出大量的氩离子轰击靶材,经过多次碰撞后电子的能量逐渐降低,摆脱磁力线的束缚,远离靶材,最终沉积在基片上。
磁控溅射就是以磁场束缚和延长电子的运动路径,改变电子的运动方向,提高工作气体的电离率和有效利用电子的能量。
电子的归宿不仅仅是基片,真空室内壁及靶源阳极也是电子归宿。
但一般基片与真空室及阳极在同一电势。
磁场与电场的交互作用( E X B drift)使单个电子轨迹呈三维螺旋状,而不是仅仅在靶面圆周运动。
至于靶面圆周型的溅射轮廓,那是靶源磁场磁力线呈圆周形状形状。
磁力线分布方向不同会对成膜有很大关系。
在E X B shift机理下工作的不光磁控溅射,多弧镀靶源,离子源,等离子源等都在次原理下工作。
所不同的是电场方向,电压电流大小而已。
真空镀膜过程均匀性真空镀膜过程非常复杂,由于镀膜原理的不同分为很多种类,仅仅因为都需要高真空度而拥有统一名称。
所以对于不同原理的真空镀膜,影响均匀性的因素也不尽相同。
并且均匀性这个概念本身也会随着镀膜尺度和薄膜成分而有着不同的意义。
薄膜均匀性的概念:1.厚度上的均匀性,也可以理解为粗糙度,在光学薄膜的尺度上看(也就是1/10波长作为单位,约为100A),真空镀膜的均匀性已经相当好,可以轻松将粗糙度控制在可见光波长的1/10范围内,也就是说对于薄膜的光学特性来说,真空镀膜没有任何障碍。
但是如果是指原子层尺度上的均匀度,也就是说要实现10A甚至1A的表面平整,是现在真空镀膜中主要的技术含量与技术瓶颈所在,具体控制因素下面会根据不同镀膜给出详细解释。
磁控溅射法沉积氮化钛复合涂层工艺研究

磁控溅射法沉积氮化钛复合涂层工艺研究一、磁控溅射法概述磁控溅射法,亦称为磁控溅射沉积技术,是一种先进的物理气相沉积技术,广泛应用于制备各种薄膜材料。
该技术通过在高真空环境中,利用磁场和电场的共同作用,将靶材表面的原子或分子溅射出来,并在基底表面沉积形成薄膜。
磁控溅射法因其高效率、高纯度、良好的薄膜均匀性以及能够制备多种材料薄膜等优点,在材料科学领域中占有重要地位。
1.1 磁控溅射法的工作原理磁控溅射法的工作原理基于等离子体中的离子在电场作用下加速,撞击靶材表面,使靶材原子或分子被溅射出来。
在溅射过程中,靶材表面附近的磁场对等离子体中的电子进行约束,形成高密度的等离子体区域,即所谓的“磁鞘”。
磁鞘的存在显著增加了离子与靶材的碰撞概率,从而提高了溅射效率。
1.2 磁控溅射法的应用领域磁控溅射法在多个领域有着广泛的应用,包括但不限于:- 微电子工业:用于制备半导体器件中的绝缘膜、导电膜等。
- 光学领域:用于制射膜、增透膜等光学薄膜。
- 机械工程:用于提高机械部件的耐磨性、耐腐蚀性等。
- 生物医学:用于制备生物相容性薄膜,如人工关节表面的涂层。
二、氮化钛复合涂层的特性氮化钛(TiN)是一种具有高硬度、高耐磨性、良好耐腐蚀性的陶瓷材料,广泛应用于切削工具、模具、耐磨部件等的表面涂层。
氮化钛复合涂层则是在氮化钛的基础上,通过引入其他元素或化合物,以期获得更优异的综合性能。
2.1 氮化钛复合涂层的组成氮化钛复合涂层通常由氮化钛与金属元素(如铝、铬、钽等)或非金属元素(如碳、硼等)组成。
这些元素的引入可以改变涂层的微观结构,从而优化涂层的硬度、韧性、耐磨性等性能。
2.2 氮化钛复合涂层的性能优势氮化钛复合涂层相较于单一的氮化钛涂层,具有以下性能优势:- 更高的硬度和耐磨性:通过合金化处理,可以提高涂层的硬度,从而增强其耐磨性。
- 改善的韧性:引入某些元素可以增加涂层的韧性,使其在受到冲击时不易破碎。
- 增强的耐腐蚀性:某些元素的加入可以提高涂层的化学稳定性,从而增强其耐腐蚀性。
磁控溅射和电弧离子镀技术和应用介绍

磁控溅射和电弧离子镀技术和应用介绍薄膜/涂层制备技术 (磁控溅射和电弧离子镀)及应用雷浩薄膜/涂层的概念与特点概念:薄膜/涂层是一类用特殊方法获得的,依靠基体支撑并具有与基体不同的结构和性能的二维材料。
薄膜(Films):厚度 < 1m,如光电功能薄膜等;涂层(Coatings):厚度≥ 1m,如硬质涂层、防护涂层等。
薄膜/涂层特征: 1)厚度(纳米,微米,毫米) 2)有基体支撑(不是单独存在的) 3)特殊的结构和性能(与块体材料相区别) 4)特殊的形成方式薄膜/涂层的概念与特点与分类应用:光学薄膜、微电子薄膜、光电子学薄膜、集成电路薄膜、防护功能薄膜。
种类:(1)以材料种类划分:金属、合金、陶瓷、半导体、化合物、高分子薄膜等。
(2)以晶体结构划分:单晶、多晶、纳米晶、非晶(3)以厚度划分:纳米薄膜,微米薄膜和厚膜。
(4)以薄膜组成结构划分:多层薄膜,梯度薄膜,复合薄膜。
薄膜/涂层的种类及应用电子工业:电极、电阻膜、电介质膜、绝缘膜、透明导电膜、超导膜等。
光学工业:荧光膜、反射膜、增透膜、干涉膜等。
机械工业:硬化膜、耐热膜、耐腐蚀膜等。
? 能源工业:聚热膜、防反射膜、透射膜等。
? 传感器:热敏、气敏、压敏、氧气传感器、红外线传感器等。
? 其它:装饰膜等。
薄膜和涂层的制备方法湿式成膜干式成膜电镀化学镀微弧氧化溶胶-凝胶膜涂敷法(喷涂、甩胶、浸涂)热浸渗(化学热处理)、热扩散法电阻热蒸发物理气相沉积(PVD)真空蒸发镀溅射沉积电子束蒸发激光蒸发电弧离子镀化学气相沉积(CVD)等离子体增强CVD(PECVD) 辉光CVD,热丝CVD薄膜和涂层的制备方法热蒸发磁控溅射电弧离子镀物理气相沉积(PVD)定义:薄膜材料通过物理方法输运到基体表面代表技术:蒸发镀膜、溅射沉积、电弧离子镀、离子束辅助沉积、脉冲激光沉积、离子束沉积、团簇沉积等。
技术特点:沉积温度低、工作气压比较低磁控溅射 (Magnetron Sputtering)的介绍概念:利用气体放电产生的正离子在电场作用下轰击作为阴极的靶,使靶材中的原子(或分子)逸出并沉积到基板表面上形成所需要的膜。
磁控溅射技术
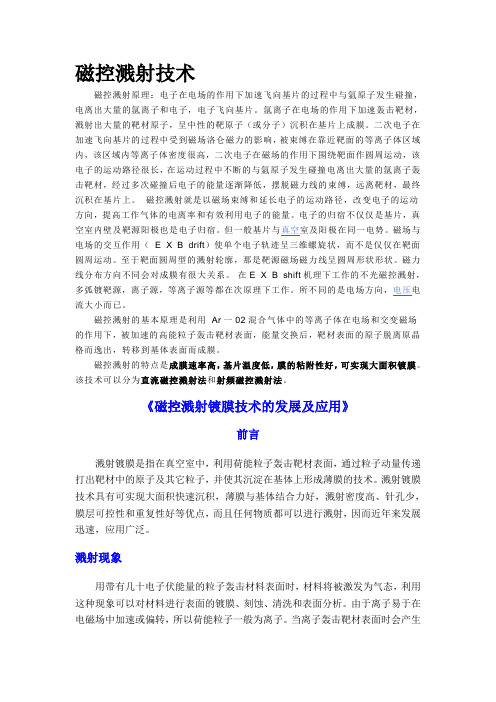
磁控溅射技术磁控溅射原理:电子在电场的作用下加速飞向基片的过程中与氩原子发生碰撞,电离出大量的氩离子和电子,电子飞向基片。
氩离子在电场的作用下加速轰击靶材,溅射出大量的靶材原子,呈中性的靶原子(或分子)沉积在基片上成膜。
二次电子在加速飞向基片的过程中受到磁场洛仑磁力的影响,被束缚在靠近靶面的等离子体区域内,该区域内等离子体密度很高,二次电子在磁场的作用下围绕靶面作圆周运动,该电子的运动路径很长,在运动过程中不断的与氩原子发生碰撞电离出大量的氩离子轰击靶材,经过多次碰撞后电子的能量逐渐降低,摆脱磁力线的束缚,远离靶材,最终沉积在基片上。
磁控溅射就是以磁场束缚和延长电子的运动路径,改变电子的运动方向,提高工作气体的电离率和有效利用电子的能量。
电子的归宿不仅仅是基片,真空室内壁及靶源阳极也是电子归宿。
但一般基片与真空室及阳极在同一电势。
磁场与电场的交互作用( E X B drift)使单个电子轨迹呈三维螺旋状,而不是仅仅在靶面圆周运动。
至于靶面圆周型的溅射轮廓,那是靶源磁场磁力线呈圆周形状形状。
磁力线分布方向不同会对成膜有很大关系。
在E X B shift机理下工作的不光磁控溅射,多弧镀靶源,离子源,等离子源等都在次原理下工作。
所不同的是电场方向,电压电流大小而已。
磁控溅射的基本原理是利用Ar一02混合气体中的等离子体在电场和交变磁场的作用下,被加速的高能粒子轰击靶材表面,能量交换后,靶材表面的原子脱离原晶格而逸出,转移到基体表面而成膜。
磁控溅射的特点是成膜速率高,基片温度低,膜的粘附性好,可实现大面积镀膜。
该技术可以分为直流磁控溅射法和射频磁控溅射法。
《磁控溅射镀膜技术的发展及应用》前言溅射镀膜是指在真空室中,利用荷能粒子轰击靶材表面,通过粒子动量传递打出靶材中的原子及其它粒子,并使其沉淀在基体上形成薄膜的技术。
溅射镀膜技术具有可实现大面积快速沉积,薄膜与基体结合力好,溅射密度高、针孔少,膜层可控性和重复性好等优点,而且任何物质都可以进行溅射,因而近年来发展迅速,应用广泛。
磁控溅射离化率-概述说明以及解释
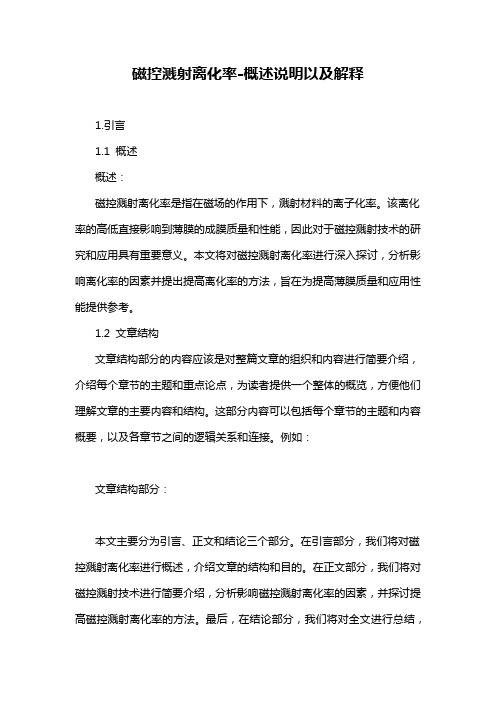
磁控溅射离化率-概述说明以及解释1.引言1.1 概述概述:磁控溅射离化率是指在磁场的作用下,溅射材料的离子化率。
该离化率的高低直接影响到薄膜的成膜质量和性能,因此对于磁控溅射技术的研究和应用具有重要意义。
本文将对磁控溅射离化率进行深入探讨,分析影响离化率的因素并提出提高离化率的方法,旨在为提高薄膜质量和应用性能提供参考。
1.2 文章结构文章结构部分的内容应该是对整篇文章的组织和内容进行简要介绍,介绍每个章节的主题和重点论点,为读者提供一个整体的概览,方便他们理解文章的主要内容和结构。
这部分内容可以包括每个章节的主题和内容概要,以及各章节之间的逻辑关系和连接。
例如:文章结构部分:本文主要分为引言、正文和结论三个部分。
在引言部分,我们将对磁控溅射离化率进行概述,介绍文章的结构和目的。
在正文部分,我们将对磁控溅射技术进行简要介绍,分析影响磁控溅射离化率的因素,并探讨提高磁控溅射离化率的方法。
最后,在结论部分,我们将对全文进行总结,展望未来可能的研究方向,并给出结论。
通过文章的结构安排,读者可以清晰地了解到本文的内容和组织架构,从而更好地把握文章的主要观点和逻辑。
1.3 目的本文旨在探讨磁控溅射离化率的影响因素和提高方法,通过分析磁控溅射技术的原理和离化率的相关理论,为磁控溅射工艺的优化提供理论支持和实践指导。
同时,希望通过本文的研究,为相关领域的科研人员和工程师提供一定的参考和借鉴,推动磁控溅射技术的发展和应用。
1.3 目的部分的内容2.正文2.1 磁控溅射技术简介磁控溅射技术是一种常用的薄膜制备技术,其原理是通过在几乎真空的环境中,利用外加磁场使目标材料形成等离子体,然后将等离子体加速到靶材表面,从而使靶材表面的原子或分子得以离开并沉积在基板上,形成薄膜。
磁控溅射技术通常包括以下主要组成部分:真空室、靶材、基板、磁控溅射源、功率源、离子源和控制系统。
在真空室中,通过抽真空的方式,维持一个非常低的气压,通常在10^-6到10^-4帕之间。
磁控溅射技术及其应用.pptx

第13页/共23页
三、磁控溅射镀膜技术发展
4、中频磁控溅射技术
中频磁控溅射常同时溅射两个靶,并排配置的两个靶的尺寸与外形完全相 同,通常称为孪生靶如图所示,在溅射过程中,两个靶周期性轮流作为阴极和 阳极,既抑制了靶面打火,而且消除普通直流反应溅射是阳极消失现象,使溅 射过程得以稳定进行。
• 打弧:当靶材表面化合物层电位足够高时,进而发生击穿,巨大的电流 流过击穿点,形成弧光放电,导致局部靶面瞬间被加热到很高的温度, 发生喷射出现“打弧”现象。
• 靶中毒和打弧导致了溅射沉积的不稳定,缩短了靶材的使用寿命! • 解决办法:最为有效解决直流反应溅射靶中毒和打弧问题的方式是改变
溅射电源,如采用射频,中频脉冲电源。
第3页/共23页
二、磁控溅射镀膜技术原理
2、磁控溅射技术
• 磁控溅射技术是为了提高成膜速率在直流二级溅射镀膜基础上发 展起来的,在靶材表面建立与电场正交的磁场,氩气电离率从 0.3%~0.5%提高到了5%~6%,解决了溅射镀膜沉积速率低的问题, 是目前工业上精密镀膜的主要方法之一。
• 磁控溅射阴极靶材的原料很广,几乎所有金属、合金以及陶瓷材料 都可以制备成靶材。磁控溅射镀膜在相互垂直的磁场和电场的双 重作用下,沉积速度快,膜层致密且与基片附着性好,非常适合于大 批量且高效率的工业化生产。
第9页/共23页
三、磁控溅射镀膜技术发展
3、反应磁控溅射技术
•随 着 表 面 工 程 技 术 的 发 展 , 越 来 越 多 地 用 到 各 种 化 合 物 薄 膜 材 料 。 可 以 直 接使用化合物材料制作的靶材通过溅射来制备化合物薄膜,也可在溅射金 属或合金靶材时, 通入一定的反应气体,通过发生化学反应制备化合物薄 膜,后者被称为反应磁控溅射。 •一 般 来 说 纯 金 属 作 为 靶 材 和 气 体 反 应 较 容 易 得 到 高 质 量 的 化 合 物 薄 膜 , 因 而大多数化合物薄膜是用纯金属为靶材的反应溅磁控射来制备的。 •在 沉 积 介 电 材 料 或 绝 缘 材 料 化 合 物 薄 膜 的 反 应 磁 控 溅 射 时 , 容 易 出 现 迟 滞 现象。
磁控溅射技术进展及应用
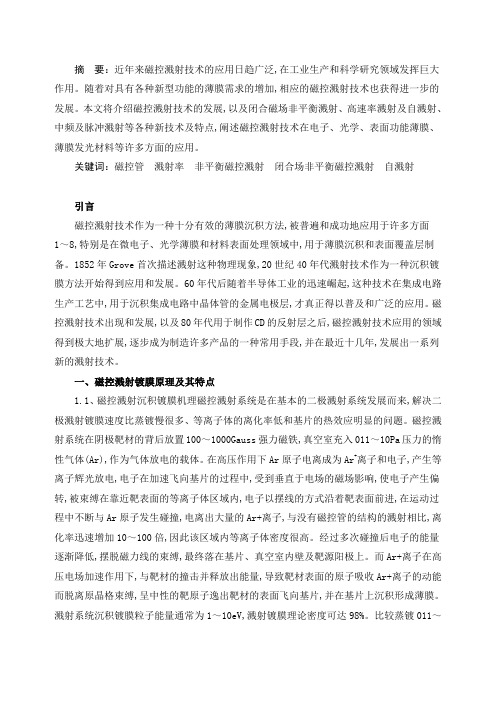
摘要:近年来磁控溅射技术的应用日趋广泛,在工业生产和科学研究领域发挥巨大作用。
随着对具有各种新型功能的薄膜需求的增加,相应的磁控溅射技术也获得进一步的发展。
本文将介绍磁控溅射技术的发展,以及闭合磁场非平衡溅射、高速率溅射及自溅射、中频及脉冲溅射等各种新技术及特点,阐述磁控溅射技术在电子、光学、表面功能薄膜、薄膜发光材料等许多方面的应用。
关键词:磁控管溅射率非平衡磁控溅射闭合场非平衡磁控溅射自溅射引言磁控溅射技术作为一种十分有效的薄膜沉积方法,被普遍和成功地应用于许多方面1~8,特别是在微电子、光学薄膜和材料表面处理领域中,用于薄膜沉积和表面覆盖层制备。
1852年Grove首次描述溅射这种物理现象,20世纪40年代溅射技术作为一种沉积镀膜方法开始得到应用和发展。
60年代后随着半导体工业的迅速崛起,这种技术在集成电路生产工艺中,用于沉积集成电路中晶体管的金属电极层,才真正得以普及和广泛的应用。
磁控溅射技术出现和发展,以及80年代用于制作CD的反射层之后,磁控溅射技术应用的领域得到极大地扩展,逐步成为制造许多产品的一种常用手段,并在最近十几年,发展出一系列新的溅射技术。
一、磁控溅射镀膜原理及其特点1.1、磁控溅射沉积镀膜机理磁控溅射系统是在基本的二极溅射系统发展而来,解决二极溅射镀膜速度比蒸镀慢很多、等离子体的离化率低和基片的热效应明显的问题。
磁控溅射系统在阴极靶材的背后放置100~1000Gauss强力磁铁,真空室充入011~10Pa压力的惰性气体(Ar),作为气体放电的载体。
在高压作用下Ar原子电离成为Ar+离子和电子,产生等离子辉光放电,电子在加速飞向基片的过程中,受到垂直于电场的磁场影响,使电子产生偏转,被束缚在靠近靶表面的等离子体区域内,电子以摆线的方式沿着靶表面前进,在运动过程中不断与Ar原子发生碰撞,电离出大量的Ar+离子,与没有磁控管的结构的溅射相比,离化率迅速增加10~100倍,因此该区域内等离子体密度很高。
- 1、下载文档前请自行甄别文档内容的完整性,平台不提供额外的编辑、内容补充、找答案等附加服务。
- 2、"仅部分预览"的文档,不可在线预览部分如存在完整性等问题,可反馈申请退款(可完整预览的文档不适用该条件!)。
- 3、如文档侵犯您的权益,请联系客服反馈,我们会尽快为您处理(人工客服工作时间:9:00-18:30)。
第二章等离子增强磁控溅射沉积技术等离子增强磁控溅射(Plasma Enhanced Magnetron Sputtering)沉积技术,简写为PEMS,是物理气相沉积(PVD)技术的一种。
它与传统磁控溅射(Conventional Magnetron Sputtering,简写为CMS)的区别在于其运用独立的电子发射源达到等离子体增强的效果,制备出涂层的致密度、硬度和韧性等均有显著提高。
运用PEMS技术可以制备传统磁控溅射技术的所有涂层,如TiN,CrN,TiAlN,TiCN 等[]。
2.1 PEMS技术的原理PEMS技术结合传统磁控溅射技术的优点,在其基础上做了改良,图2.1为PEMS技术的原理图和实际镀膜工作时的图片。
如图2.1(a)所示,PEMS真空室的尺寸为700×700×700mm3,左右两边分别有一个圆柱形金属靶,尺寸为1.5cm ×φ170mm。
在真空室的中央,有一个旋转的工作台便于悬挂工件,工作台旋转的速度为10~20rpm,钨丝的长度为20cm。
图2.1 (a)PEMS技术的工作原理图(b)实际镀膜工作图PEMS技术应用了一个电子发射源来产生更多的电子,一般选用加热的钨丝或者空心阴极管作为电子发射源。
从实际工作图2.1(b)的下方可以隐约看见耀眼的光线,即钨丝在加热状态发出的光线。
当真空室内气压到达几个毫托,在钨丝和真空壁之间施加直流放电电压(DC Discharge Power Supply),即:真空壁接地,钨丝上为恒定负偏压(~-100V)。
同时,在钨丝上加载交流电(电压20~30V,电流40~45A),钨丝被加热后向真空室内释放电子,在放电电压的作用下,电子被加速向真空壁飞去,由于真空室内存在大量的气体分子(Ar,TMS,N2等),电子与中性气体分子(原子)发生碰撞,导致气体电离,并最终使真空室内产生等离子体。
等离子体中带正电的Ar离子受到靶材的吸引,轰击靶材产生溅射。
2.2 PEMS技术与传统磁控溅射技术的比较与传统磁控溅射相比,PEMS在其基础上引入了钨丝产生等离子体。
众所周知,几乎所有的PVD镀膜技术都是为了获得粘附性能好,硬度高,致密的涂层。
因此,在镀膜之前,工件表面的清洗至关重要,它可以使涂层和基体材料之间结合得更好。
在镀膜涂层生长过程中,足够的离子碰撞是获得致密涂层的关键条件。
PEMS技术引入的钨丝为镀膜前的清洗和镀膜过程中提供足够的离子碰撞奠定了基础。
2.2.1 传统磁控溅射技术考虑到工件表面的氧化物和赃物会影响涂层粘附力,将工件放入真空室之前,人们通常使用喷砂,乙醇,丙酮,超声波等手段对表面进行清洗。
但是,由于新鲜表面极易被氧化,一点点氧化皮就可能使涂层性能粘附性能变差,而且可能会导致柱状的生长。
因此,将工件放入真空室后的清洗也非常重要。
传统磁控溅射清洗工件的方法是将靶材的功率调低,在工件上施加一个很高的负偏压,利用靶材产生的Ar等离子体对工件进行清洗。
尽管磁控管的功率很小,由于靶材上使用的是负偏压,Ar+,Ar2+就会对靶表面进行轰击,这样不可避免的产生了少量的溅射,继而沉积于工件表面,这样造成的结果是,在工件表面没有清洗干净的时候就已经开始镀膜了,清洗效果差。
另一种情况是,不开启磁控管,在工件表面使用高的负偏压,利用真空室内较高的气压Ar气产生辉光放电(Glow Discharge),工件清洗完毕后将真空室的气压降到靶材镀膜时的工作气压。
然而,在气体下降的过渡过程中,工件表面的等离子轰击过程会受到影响,因为工件刚形成的新鲜表面会被真空室内残余的水蒸气再次氧化,原因是水蒸气分子在等离子体环境下异常的活跃,容易获得活性的氧原子或氧离子。
2.2.2PEMS技术从图2.1(a)可以看出,PEMS原理图的下半部分有一个灯丝,通常使用钨丝。
在交流电加热下,钨丝不断释放电子,它是独立于磁控管的一部分。
因此,在工件清洗和镀膜过程中,它可以实现传统磁控溅射没有的功能。
在PEMS工件清洗过程中,磁控管保持关闭状态,此时真空室内Ar的气压保持2~6mtorr,在钨丝上加载交流电,并在工件上缓慢增大负偏压,灯丝上释放出的电子向真空壁加速,与Ar碰撞后使整个真空室内充满Ar等离子体,Ar等离子体对工件表面的清洗已经足够。
需要指出,工件表面的负偏压需要缓慢增加,实现发现,调节过快表面会出现电弧,对工件的新鲜表面很不利。
清洗完毕,在不关闭钨丝电源的情况下开启磁控管,这样在清洗和镀膜之间避免了气压过渡过程,工件表面不容易被氧化。
在镀膜过程中,由于钨丝源源不断的向真空室释放电子,与真空室内的的气体分子产生碰撞,以氩气为例,电子轰击氩气分子的最外层或次外层电子,形成Ar+,Ar2+,这些离子轰击靶材最终产生溅射。
需要强调的是,镀膜过程中钨丝产生的等离子体是独立于磁控管产生的等离子体的,经法拉第杯(Faraday Cup)试验测定,发现有钨丝的真空室离子电流密度是单独磁控管产生离子电流密度的25倍。
另外,由于钨丝是由交流电控制,可以从外部调节交流电的电压来控制放电电子的数目,进而控制真空室内等离子体含量。
等离子体的增加直接导致真空室内离子和原子的比值(ion to atom ratio)增加,它是PVD过程当中一个重要的参数。
传统磁控溅射为了提高离子和原子的比值,通常提高靶材的功率,然而靶材中性原子同时也会溅射出来,最终导致净离子和原子的比值几乎没有变化。
2.2.3CMS和PEMS实验结果比较表2.1 Cr涂层沉积于Si片表面的镀膜参数工艺气压(mtorr) 靶功率(W)放电电压(V)放电电流(A)试样偏压(V)偏压电流(A)试样-靶距(cm)沉积时间(hrs)PEMS CMS 2.32.3500500——120——9.0-40-400.010.19101033图2.2 CMS技术(左)和PEMS技术(右)在硅片上沉积Cr涂层的表面形貌(上侧)和横截面(下侧)形貌图为了深一步研究PEMS技术,美国西南研究院魏荣华等人使用CMS和PEMS 两种方法,运用几乎相近的实验参数在Si片表面镀上Cr涂层[],表2.1列出了实验参数。
注:实验数据的引用得到了原文作者的同意。
图2.2为涂层表面和横截面SEM形貌,其中左侧运用的是CMS技术,右侧是PEMS技术。
从表面形貌可以看出,采用传统磁控溅射CMS沉积出来的Cr 涂层表面粗糙,晶粒比较粗大;从横截面上看,CMS沉积的涂层呈现出典型的柱状结构,致密度低。
相近参数下,PEMS技术沉积的Cr涂层表面光滑,无明显的柱状结构,而且非常致密。
这是由于热钨丝释放的电子增加了等离子体密度,剧烈的离子轰击靶材使得涂层的致密度增加,具体可以参考文献[]。
从图中同时可以发现,两种工艺的镀膜时间均为3小时,但PEMS的膜层却更薄(5.5μm),事实上,等离子体浓度的增加会提高镀膜速率。
可见,剧烈的离子轰击可以显著提高致密度。
2.3PEMS镀膜前的离子清洗2.3.1真空室及工件的烘烤除气将工件安装在工作台之后,将真空室的基础气压抽到1×10-5torr以下,加载交流电于钨丝上,这时钨丝处于红热状态,使整个真空室温度上升,水蒸气从工件表面或真空壁逃逸出来,而后被泵体抽出,这个过程大约需要4小时。
2.3.2 离子清洗关闭钨丝电源,等气压稳定在10-6torr后,向真空室充入氩气,通过流速控制或者节流阀控制使真空室内的气压保持在2~6mtorr。
气压稳定后在钨丝上施加交流电(电压20~30V,电流40~45A),并在钨丝和真空壁之间加载放电电压(通常为120V),钨丝发射的电子被加速朝真空壁飞去,产生氩等离子体。
通过调节交流电压的大小可以控制发射电子的数目,从而控制放电电流的大小,试验控制放电电流保持在5A。
之后,工件上加载负偏压-120V,Ar离子受到工件的吸引,不断轰击工件表面的氧化皮和赃物,这时工件离子清洗过程就开始了。
需要注意的是,调节钨丝上的交流电压和工件上的工作偏压需要缓慢调节,调节过快会使工件表面离子轰击过于剧烈,很容易产生电弧,见第三章第二节。
在本试验中,离子清洗时间为2小时。
工件清洗完毕后,在不关闭钨丝电源的状态下,开启磁控管(功率500W),此时靶前的挡板处于遮挡状态,在低功率状态下对靶表面清洗20min以去除表面的赃物和氧化层。
2.4PEMS镀膜靶表面清洗干净后,开启挡板,将靶材的功率调至预设值(2KW~4KW),并把工件表面的负偏压降至-40V,溅射开始。
降低工件表面的负偏压目的是为了降低溅射力度,从而可以减小膜层的内应力。
为了使涂层和基体之间的结合力好,需要在二者之间镀过渡层(Bondlayer),一般为纯金属,即靶材。
而后依据膜层成分的不同向真空室充入N2,TMS,HMDSO,HMDSN等气体,镀膜完成。
需要指出,在工业生产中为了提高沉积速率,可以采用提高靶的数目,增大放电电流,提高靶材功率等方式。
2.5本章小结本章主要介绍了以下几个方面的内容:(1)介绍了等离子增强磁控溅射(PEMS)技术的原理。
指明了传统磁控溅射(CMS)的不足,通过与CMS相比较,PEMS技术引入了一个电子发射源,利用电子轰击气体产生等离子体,在离子清洗和镀膜过程中都起着重要的作用。
(2)运用了CMS技术和PEMS技术在Si片上镀Cr涂层,采用相近的镀膜参数将涂层的形貌进行对比。
结果发现,PEMS技术沉积的涂层致密且无柱状结构,表面粗糙度也较低。
(3)阐述了PEMS技术在离子清洗和镀膜过程中的步骤,以及常用气体和相关经验参数的应用。