(完整版)铝型材氧化、电泳生产车间工艺操作规程[1]
铝型材阳极氧化、电泳涂漆、粉末喷涂、氟碳漆喷涂及木纹处理工艺过程及发展

铝型材阳极氧化、电泳涂漆、粉末喷涂、氟碳漆喷涂及木纹处理工艺过程及发展铝型材阳极氧化、电泳涂漆、粉末喷涂、氟碳漆喷涂及木纹处理工艺过程及发展综述了国内外铝合金建筑型材表面处理技术的现状,重点介绍了铝型材阳极氧化、电泳涂漆、粉末喷涂、氟碳漆喷涂及木纹处理的生产流程和工艺规范,并对各种保护层的特点及其应用作了评述。
同时对建筑铝型材表面处理技术今后的发展趋势进行了展望,提出了未来应大力开发和推广的清洁环保、高效节能技术。
0 引言铝合金建筑型材是当今门窗和幕墙主要的结构材料,在世界范围内广泛应用[1]。
铝合金挤压型材(未经表面处理)外观单一,并且在潮湿大气中容易腐蚀[2],因而很难满足建筑材料高装饰性和强耐侯的要求。
为了提高装饰效果、增强抗腐蚀性及延长使用寿命,铝型材一般都要进行表面处理。
因此,表面处理是铝合金建筑型材生产的一道必不可少且极为重要的工序。
铝型材表面处理技术因原理不同,其工艺也有较大区别。
根据保护层的性质和工艺特点,铝型材表面处理技术可分为阳极氧化处理、阳极氧化-电泳处理、有机涂层处理三大类[3],其中,有机涂层处理包括粉末喷涂、氟碳漆喷涂和木纹处理(见图1)。
1 阳极氧化处理阳极氧化于20世纪50年代应用于铝型材生产,是应用最早也是目前应用最广泛的建筑铝型材表面处理法。
阳极氧化型材的突出特点是外观金属质感强。
1.1 阳极氧化工艺流程阳极氧化工流程见图21.2 机械预处理机械预处理主要有机械喷砂和机械抛光[4]。
机械喷砂是获得砂面型材的一个重要途径,由铝型材喷砂机完成。
机械喷砂可能完全消除表面缺陷和挤压条纹,得到比化学砂面(碱蚀砂面)更加均匀的哑光表面。
另外,机械喷砂在生产成本和环保上也具有较大优势。
机械抛光是铝型材抛光机上进行的。
将铝型材有规则地平放在工作台上,通过高速旋转的抛光轮与表面触压和磨擦,使表面光滑平整,直至达到镜面效果。
生产中常常用抛光来消除挤压条纹,因此,这时又称为“机械扫纹”[5]。
阳极氧化、电泳工艺操作规程
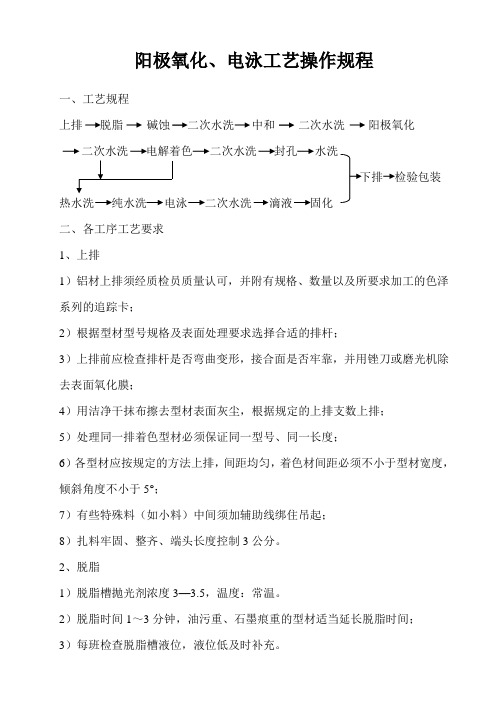
阳极氧化、电泳工艺操作规程一、工艺规程上排脱脂碱蚀二次水洗中和二次水洗阳极氧化二次水洗电解着色二次水洗封孔水洗下排检验包装热水洗纯水洗电泳二次水洗滴液固化二、各工序工艺要求1、上排1)铝材上排须经质检员质量认可,并附有规格、数量以及所要求加工的色泽系列的追踪卡;2)根据型材型号规格及表面处理要求选择合适的排杆;3)上排前应检查排杆是否弯曲变形,接合面是否牢靠,并用锉刀或磨光机除去表面氧化膜;4)用洁净干抹布擦去型材表面灰尘,根据规定的上排支数上排;5)处理同一排着色型材必须保证同一型号、同一长度;6)各型材应按规定的方法上排,间距均匀,着色材间距必须不小于型材宽度,倾斜角度不小于5°;7)有些特殊料(如小料)中间须加辅助线绑住吊起;8)扎料牢固、整齐、端头长度控制3公分。
2、脱脂1)脱脂槽抛光剂浓度3—3.5,温度:常温。
2)脱脂时间1~3分钟,油污重、石墨痕重的型材适当延长脱脂时间;3)每班检查脱脂槽液位,液位低及时补充。
3、酸蚀1)氟化氢铵浓度4.5—5.5,温度35—45℃,PH值2.8—3.4,时间3—8分钟;2)型材酸蚀出槽后,要滴干进入水洗槽清洗;3)每班取槽液分析含量,根据分析结果补充氟化氢铵和酸蚀剂,加水调整液位。
4)视型材表面质量取决酸蚀时间并每排查看砂面质量情况。
4、碱蚀1)N a OH浓度38~55g/l Al3+10~40g/l 温度45~55℃2)碱蚀时间视浓度、温度及质量要求而定,一般平光料60±20秒,喷砂白料2~3min,喷砂着色料5~6min;3)型材碱蚀出槽后要迅速转移到水洗槽清洗,空中停留时间不宜过久;4)水洗时间30秒~2分钟,水洗至少两次;5)每班取槽液分析N a OH和Al3+浓度两次,根据分析结果补充N a OH和碱蚀剂,加水调整液位。
5、中和1)中和槽H2SO4浓度160~180g/l,温度:常温。
2)中和时间1~5分钟;3)水洗时间30秒~5分钟;4)水洗后应检查型材表面质量是否合格,将不合格型材返工或报废,如合格将型材拧紧,待氧化时在空中停留时间不得超过2分钟;5)每天根据分析结果补充工业硫酸,根据需要添加工业硝酸。
铝型材厂工艺操作规程范本

铝型材厂工艺操作规程范本铝型材厂工艺操作规程范本一、安全操作规定:1. 操作人员必须经过专门培训并持有效证件上岗,严禁未经培训和未持证人员进行操作。
2. 操作人员必须配戴相关防护用品,包括安全帽、防护眼镜、防护口罩、耳塞等。
3. 操作人员必须熟悉各类设备的操作规程和安全规定,做到熟悉操作、慎重操作。
4. 禁止擅自解除设备的安全防护装置或篡改操作规程,一旦发现立即上报相关负责人员。
5. 严禁酗酒、吸烟、吸毒等影响工作安全的行为。
二、设备操作规定:1. 操作人员在操作前必须检查设备的运行状态和相关控制装置是否正常,如有异常立即报告维修人员。
2. 在进行设备启动和停止操作前,必须按照规定程序进行,并需确保无人员在设备附近。
3. 操作人员需按照工艺要求设置设备参数并进行调试,确保设备运行稳定。
4. 不得随意改变设备的工作状态和参数,如有需要必须经过相关负责人员批准。
三、操作步骤规定:1. 操作人员在操作前必须熟悉并掌握生产工艺流程和相关质量控制标准。
2. 所有操作必须按照规定的操作步骤和岗位职责进行,不得随意变动和省略操作环节。
3. 操作人员必须认真填写生产记录表格,记录生产过程中的各项数据,确保工序追溯和质量控制。
4. 对于每次生产的样品必须进行质量检验并留样,确保产品质量的稳定性。
四、危险品操作规定:1. 操作人员在操作危险品前必须进行专门的危险品操作培训,并持相关证件。
2. 操作人员必须遵守危险品的存储和使用规定,确保危险品的安全和环境的保护。
3. 操作人员在操作危险品时必须佩戴相关的防护装备,并在操作现场设置相关警示标志。
五、设备维护与保养:1. 设备维护和保养必须按照相关规定进行,包括定期检查、润滑和更换易损件等。
2. 设备维护和保养必须记录并报告相关负责人员,确保设备的正常运行和寿命。
3. 对于出现故障的设备,操作人员需立即停止使用并上报相关负责人员。
六、应急处理规定:1. 操作人员在发生事故或突发状况时必须按照应急处理规定进行处置,确保人员安全和设备保护。
铝厂电泳车间工作流程
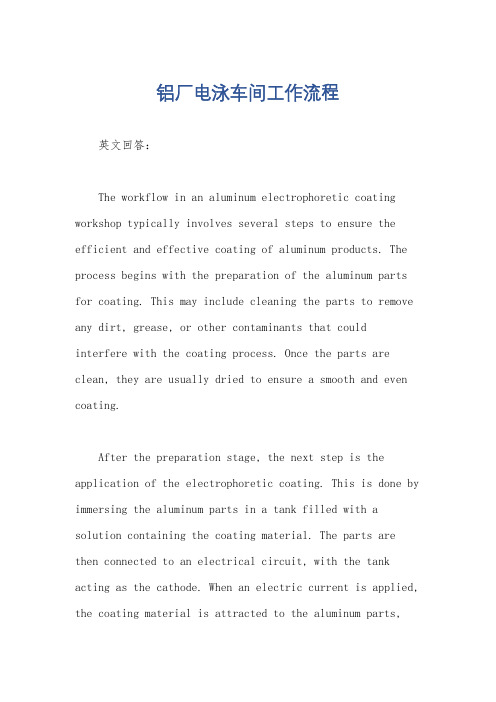
铝厂电泳车间工作流程英文回答:The workflow in an aluminum electrophoretic coating workshop typically involves several steps to ensure the efficient and effective coating of aluminum products. The process begins with the preparation of the aluminum parts for coating. This may include cleaning the parts to remove any dirt, grease, or other contaminants that couldinterfere with the coating process. Once the parts are clean, they are usually dried to ensure a smooth and even coating.After the preparation stage, the next step is the application of the electrophoretic coating. This is done by immersing the aluminum parts in a tank filled with a solution containing the coating material. The parts are then connected to an electrical circuit, with the tank acting as the cathode. When an electric current is applied, the coating material is attracted to the aluminum parts,forming a thin, uniform layer on their surface.Once the parts are coated, they are usually rinsed to remove any excess coating material. This is typically done using water or a rinse solution. The rinsing process helps to remove any residual coating material that may not have adhered to the aluminum parts during the coating process.After rinsing, the coated parts are usually dried to ensure the coating is fully cured. This can be done using various methods, such as air drying or using ovens or drying chambers. The drying process is important to ensure the coating is fully cured and provides the desired properties, such as corrosion resistance and durability.Once the parts are dried, they may undergo additional processes, such as inspection and quality control. This involves checking the coating thickness, adhesion, and appearance to ensure they meet the required specifications. Any defects or issues identified during inspection may require rework or repair before the parts can be considered ready for further processing or shipment.In addition to the main workflow steps, there may be other supporting processes in an aluminum electrophoretic coating workshop. These can include maintenance of the equipment, monitoring and control of process parameters,and waste management. Proper maintenance of the equipment ensures its reliability and longevity, while monitoring and control of process parameters helps to maintain consistent coating quality. Waste management involves proper disposalor recycling of waste materials generated during thecoating process, such as rinse water or excess coating material.中文回答:铝电泳涂装车间的工作流程通常包括多个步骤,以确保对铝制品进行高效和有效的涂装。
铝型材厂工艺操作规程范本
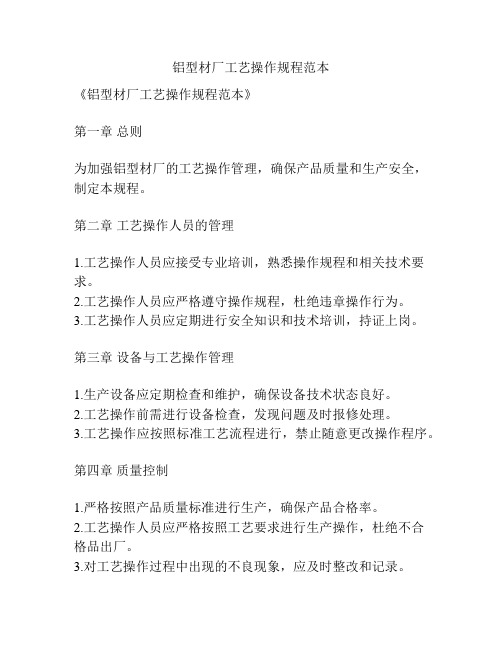
铝型材厂工艺操作规程范本《铝型材厂工艺操作规程范本》第一章总则为加强铝型材厂的工艺操作管理,确保产品质量和生产安全,制定本规程。
第二章工艺操作人员的管理1.工艺操作人员应接受专业培训,熟悉操作规程和相关技术要求。
2.工艺操作人员应严格遵守操作规程,杜绝违章操作行为。
3.工艺操作人员应定期进行安全知识和技术培训,持证上岗。
第三章设备与工艺操作管理1.生产设备应定期检查和维护,确保设备技术状态良好。
2.工艺操作前需进行设备检查,发现问题及时报修处理。
3.工艺操作应按照标准工艺流程进行,禁止随意更改操作程序。
第四章质量控制1.严格按照产品质量标准进行生产,确保产品合格率。
2.工艺操作人员应严格按照工艺要求进行生产操作,杜绝不合格品出厂。
3.对工艺操作过程中出现的不良现象,应及时整改和记录。
第五章废料处理与环保1.废料应按照相关法律法规和企业规定进行严格分类和处理。
2.工艺操作人员应加强环保意识,降低资源浪费和环境污染。
3.严禁在生产过程中随意排放废气和废水,依法进行处理和排放。
第六章安全管理1.严格执行安全操作规程,做好安全防护措施,避免事故发生。
2.发现安全隐患时,应立即报告并做好隐患排查和整改工作。
3.定期进行安全生产培训,提高员工安全意识和应急处置能力。
第七章管理制度和监督检查1.建立完善的工艺操作管理制度,并严格执行。
2.定期进行内部审核和外部审核,发现问题及时整改。
3.对工艺操作违章行为进行严肃处理和监督。
以上是《铝型材厂工艺操作规程范本》的主要内容,员工均应严格遵守并加以执行。
电泳车间安全操作规程
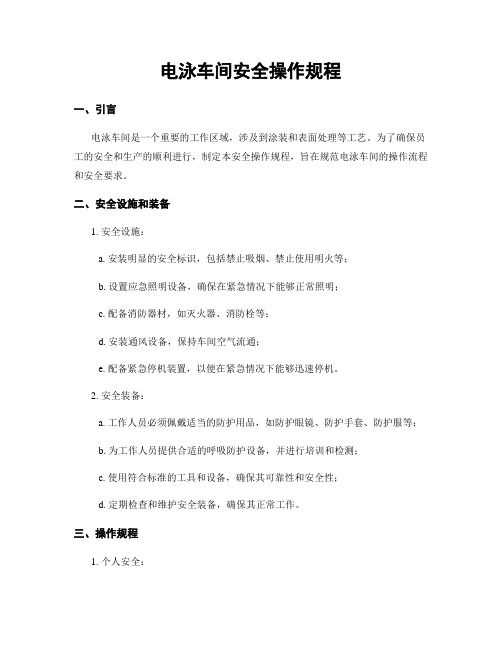
电泳车间安全操作规程一、引言电泳车间是一个重要的工作区域,涉及到涂装和表面处理等工艺。
为了确保员工的安全和生产的顺利进行,制定本安全操作规程,旨在规范电泳车间的操作流程和安全要求。
二、安全设施和装备1. 安全设施:a. 安装明显的安全标识,包括禁止吸烟、禁止使用明火等;b. 设置应急照明设备,确保在紧急情况下能够正常照明;c. 配备消防器材,如灭火器、消防栓等;d. 安装通风设备,保持车间空气流通;e. 配备紧急停机装置,以便在紧急情况下能够迅速停机。
2. 安全装备:a. 工作人员必须佩戴适当的防护用品,如防护眼镜、防护手套、防护服等;b. 为工作人员提供合适的呼吸防护设备,并进行培训和检测;c. 使用符合标准的工具和设备,确保其可靠性和安全性;d. 定期检查和维护安全装备,确保其正常工作。
三、操作规程1. 个人安全:a. 所有工作人员必须经过相关培训,并了解电泳车间的安全操作规程;b. 禁止携带易燃、易爆物品进入车间;c. 禁止在工作区域吃东西或者喝水;d. 禁止穿戴松散的衣物,如围巾、领带等,以防被卷入机械设备中;e. 禁止在工作区域内玩闹或者打闹。
2. 设备操作:a. 在操作电泳设备之前,必须检查设备是否正常运行,如有异常应及时报修;b. 操作人员必须佩戴防护手套和防护眼镜,以防止溅洒物伤害;c. 禁止随意触摸设备的运动部件,如滚筒、链条等;d. 禁止在设备运行时进行维修和清理工作,必须先停机并断电。
3. 化学品使用:a. 使用化学品前必须了解其性质和安全操作要求,并佩戴相应的防护装备;b. 严禁将不同种类的化学品混合使用;c. 使用化学品时应保持通风良好,并避免产生火花;d. 使用后的化学品容器必须正确密封和储存,避免泄漏和污染。
4. 紧急情况处理:a. 在发生火灾、泄漏等紧急情况时,应即将按照应急预案进行处理;b. 火灾发生时,应迅速启动火警报警装置,并使用灭火器进行初期扑救;c. 发生泄漏时,应即将切断泄漏源,并进行必要的清理和处理;d. 在紧急情况下,必须保持镇静,并按照应急预案进行逃生和救援。
铝型材厂工艺操作规程范本

铝型材厂工艺操作规程范本第一章总则第一条为了规范铝型材厂的工艺操作行为,确保生产过程的安全和产品质量,制定本规程。
第二条本规程适用于铝型材厂的生产操作过程中涉及到的工艺操作。
第三条工艺操作人员应严格遵守本规程,保持操作规范和注意安全。
第四条工艺操作人员应接受相关的培训和考核,持有相应的工艺操作证书。
第五条工艺操作人员应了解产品的工艺要求和相关操作规程,确保按规定进行操作。
第二章操作规范第六条工艺操作人员应佩戴防护装备,包括安全帽、防护眼镜、口罩等,确保自身和他人的安全。
第七条工艺操作人员应按照工艺要求,选择合适的设备和工具进行操作。
第八条工艺操作人员在进行设备操作之前,应仔细检查设备的运行状况,确保设备正常。
第九条工艺操作人员应按照工艺要求,准确测量和调整参数,如温度、压力等。
第十条工艺操作人员应按照工艺要求,严格控制操作时间和操作速度,确保产品质量。
第十一条工艺操作人员应按照工艺要求,进行现场清理和维护工作,确保设备和环境的清洁。
第十二条工艺操作人员应及时反馈设备异常和质量问题,并积极参与问题解决过程。
第三章安全措施第十三条工艺操作人员应熟悉厂区的安全规定,并严格遵守。
第十四条工艺操作人员应定期参加安全培训,了解应急处理和事故防范知识。
第十五条工艺操作人员应严格遵守消防安全规定,禁止在生产区域吸烟、使用明火等。
第十六条工艺操作人员应使用防护用品,如手套、耳塞等,减少设备操作对身体的伤害。
第十七条工艺操作人员应注意设备周围的隐患,并及时报告处理,确保设备安全。
第十八条工艺操作人员在操作结束后,应及时关闭设备,切断电源,确保设备的安全。
第四章质量控制第十九条工艺操作人员应按照质量要求,严格控制操作过程中的参数,确保产品质量。
第二十条工艺操作人员应及时记录关键参数和质量数据,做好相关的统计和分析工作。
第二十一条工艺操作人员应及时发现和处理产品质量问题,以及时止损,防止不良品流出。
第二十二条工艺操作人员应及时清理设备和操作环境,减少杂质对产品质量的影响。
铝材氧化电泳设备操作规程
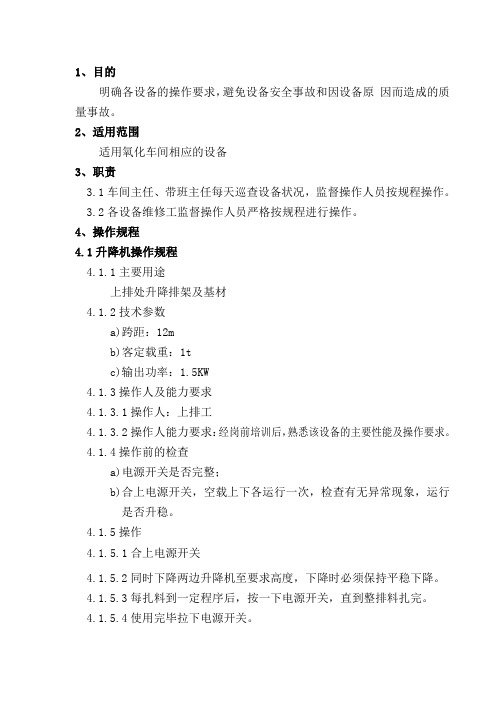
1、目的明确各设备的操作要求,避免设备安全事故和因设备原因而造成的质量事故。
2、适用范围适用氧化车间相应的设备3、职责3.1车间主任、带班主任每天巡查设备状况,监督操作人员按规程操作。
3.2各设备维修工监督操作人员严格按规程进行操作。
4、操作规程4.1升降机操作规程4.1.1主要用途上排处升降排架及基材4.1.2技术参数a)跨距:12mb)客定载重:1tc)输出功率:1.5KW4.1.3操作人及能力要求4.1.3.1操作人:上排工4.1.3.2操作人能力要求:经岗前培训后,熟悉该设备的主要性能及操作要求。
4.1.4操作前的检查a)电源开关是否完整;b)合上电源开关,空载上下各运行一次,检查有无异常现象,运行是否升稳。
4.1.5操作4.1.5.1合上电源开关4.1.5.2同时下降两边升降机至要求高度,下降时必须保持平稳下降。
4.1.5.3每扎料到一定程序后,按一下电源开关,直到整排料扎完。
4.1.5.4使用完毕拉下电源开关。
4.1.6注意事项及维护保养4.1.6.1链条每隔半月检查一次,并加注润滑油,发现链条断裂现象,应立即更换。
4.1.6.2应避免链条染及其他腐蚀性能的物质,如发现已沾染,应立即清洗干净,以防止锈蚀。
4.2 1+1吨行车操作规程4.2.1主要用途a)行走电机功率0.8kwb)提升电机功率3.75kw4.2.3操作人:行车工4.2.4操作人能力要求:上岗前必须参加由公司或劳动部门举办的岗位培训班,经考核合格后方可独站岗,其他人员未经培训一律不准上岗操作。
上岗前必须参加公司或劳动部门举办的行车工岗位培训,经考核合格后,方可上岗操作,其他人员未经操作,一律不准上岗操作。
4.2.5 操作前的检查4.2.5.1 检查行车各紧固点是否松动,如有松动,立即固紧。
4.2.5.2 检查链条的链销是否脱落,如有脱落,应立即固定。
4.2.5.3检查齿轮箱的润滑状态。
4.2.5.4合上控制电闸,将行车空载上下、左右来回运行一次,检查每个动作是否到位,控制按扭和限位开关是否灵敏,听行车是否有异常声音。
氧化、电泳车间工艺操作规程

氧化、电泳车间工艺规程本规程规定了铝型材阳极氧化、电解着色型材生产工艺及电泳涂漆工艺。
在生产过程中如遇特殊情况,需变动工艺按文件资料控制程序进行。
一、工艺流程为关键工序控制点即为特殊工序又是关键工序控制点。
1.酸蚀料、碱蚀料、白料系列:来料检查-绑料-除油-水洗-酸蚀(碱蚀)-水洗-水洗-中和-水洗-紧料-水洗-阳极氧化-水洗-纯水洗-封孔-热水洗-水洗-检验(染点法)-卸料-控水干燥-转入下道工序-成品包装-入库2.香槟料系列:来料检查-绑料-除油-水洗-碱蚀(酸蚀)-温水洗-水洗-中和-水洗-紧料-水洗-阳极氧化-水洗-纯水洗-电解着色-水洗-色板对比-水洗-封孔-热水洗-水洗-检验(染点法)-卸料-控水干燥-转入下道工序-成品包装-入库3.电泳白料,电泳香槟料系列:来料检查-绑料-除油-水洗-碱蚀(酸蚀)-温水洗-水洗-中和-水洗-紧料-水洗-阳极氧化-水洗-纯水洗-(电解着色-水洗一色板对比一水洗)一热纯水洗一纯水洗一电泳一RO]水洗一RO2水洗-控水-烘烤-检验-卸料-(做隔热型材)转入下道工序-成品包装-入库二、生产注意事项1.在岗职工应穿戴好劳动保护用品。
2.生产前按工艺要求检查各槽液情况,应使槽液成份与工艺要求相符。
3.首先检查动力、排风、搅拌、降温、供水、加热、给排水系统以及各类机电设备,氧化脉冲电源、正弦交流着色电源、电泳电源天车、泵、各种管道是否运转正常。
4.维修工定期将导电铜头、铜架用砂纸打磨露出金属光泽。
5.铝挂具的载流量为150A/cm2导电杆反复使用后变细,应以此为依据,计算导电面积不足时,应更换导电杆。
6.检查氧化着色制品、电泳着色制品,批号、规格、型号、重量、根数应与生产工序转序单相符。
7.配制及调整酸碱槽液时必需将酸、碱慢慢倒入水中,严禁将水往浓酸、浓碱中加入,发防过热飞溅伤人。
8.氧化工要熟练掌握专用天车的操作技能。
9.天车工要按工艺流程顺序吊料,以防型材带酸液、碱液滴落在成品上,产生废品和污染槽液。
铝型材阳极氧化工艺操作规程
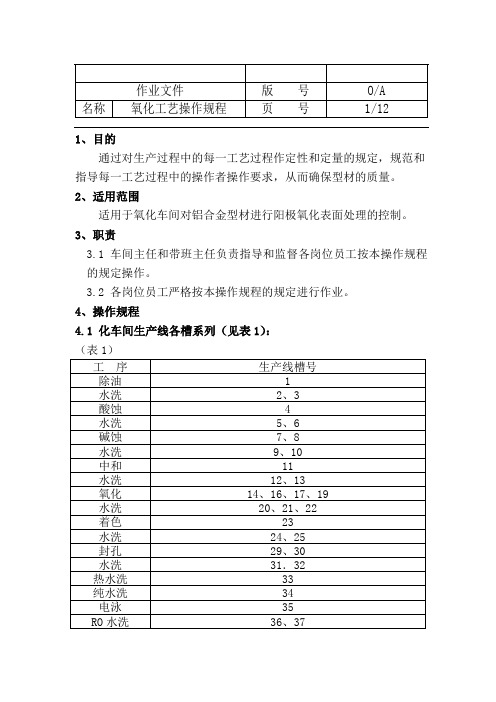
1、目的通过对生产过程中的每一工艺过程作定性和定量的规定,规范和指导每一工艺过程中的操作者操作要求,从而确保型材的质量。
2、适用范围适用于氧化车间对铝合金型材进行阳极氧化表面处理的控制。
3、职责3.1 车间主任和带班主任负责指导和监督各岗位员工按本操作规程的规定操作。
3.2 各岗位员工严格按本操作规程的规定进行作业。
4、操作规程4.1 化车间生产线各槽系列(见表1):(表1)4.2 各工序主要技术性能和参数主要技术性能和参数(见表2):(表2)4.3 氧化车间生产工艺流程4.3.1 氧化工艺流程图4.4 生产前准备4.4.1人员控制:新工人上岗前必须进行有关《氧化车间生产工艺操作规程》、《氧化车间设备操作规程》、《氧化车间岗位操作规程》以及安全生产、劳动纪律等方面的学习教育,经试用合格方能持上岗证到指定岗位上岗。
4.4.2 在岗工人必须按人资行政部制定的培训计划定期接受培训。
4.4.3 按设备操作规程,分别对电流系统、冷却及加热系统、循环系统、通风系统、工艺行车等进行检查,调节无异后时进行空载运行,确定正常后方可生产。
凡出现设备故障必须及时报告车间领导请维修人员修理,带班主任在交接班记录中作好纪录。
日常做好对设备的定期维护保养。
4.4.4 领料:上架班长按生产部下达的《氧化车间生产计划单》从挤压车间领取有合格标识的型材。
领取的顺序应符合生产部下达的《氧化车间生产计划单》要求。
4.4.5 化验室生产前(正常生产期间每天两次),取样化验槽液成分浓度,报告交一份氧化车间,并对采购的化学药品进行批次的抽样化验,合格入库的化学药品才能使用。
氧化车间主任指导工艺员加药。
工艺员负责对各工序的工艺条件进行调整。
只有槽液浓度和工艺条件符合第4.2条“各工序主要技术性能和参数”中的要求才能进行生产。
4.5 上架4.5.1 根据“产品检验随行卡”分清型材的型号及表面处理要求(颜色、膜厚、表面状态要求等)。
表面处理要求不同的型格绝对不能同排上架。
铝型材氧化电泳生产工艺操作

铝型材氧化电泳生产工艺操作1.铝型材氧化工艺操作:操作步骤:(1)准备工作:将需要进行氧化处理的铝型材清洗干净,除去表面的油污和杂质。
(2)确定氧化液:根据需要的氧化效果和材料的特性选择合适的氧化液。
常用的氧化液有硫酸氧化液、硟酸氧化液和硝酸氧化液。
(3)浸泡处理:将铝型材浸泡在氧化液中,温度和时间根据氧化液的选择而定,通常为50-70℃,时间为20-60分钟。
(4)氧化灌注:将铝型材从氧化液中取出,使其表面残留的液体流干净,然后将其放入冷却水中冲洗一段时间,使其迅速冷却。
(5)浸泡封闭处理:将冷却后的铝型材浸泡在封闭液中,以提高氧化膜的密封性和耐蚀性能。
(6)冲洗干燥:将封闭处理后的铝型材取出,用清水冲洗表面的液体,然后进行干燥处理。
2.铝型材电泳工艺操作:铝型材电泳是一种通过电泳将有机胶体颜料沉积在铝合金表面,并在水中固化、形成保护膜的工艺。
操作步骤:(1)准备工作:将需要进行电泳处理的铝型材清洗干净,除去表面的油污和杂质。
(2)标准化电泳槽:根据电泳液的配方,调节电泳槽中的电导率和pH 值,使其符合要求。
(3)水洗处理:将铝型材浸泡在水中进行水洗处理,去除表面的杂质。
(4)电泳处理:将清洗干净的铝型材放入电泳槽中进行电泳处理。
通常采用交流电源,通过正负极的电荷作用,使有机颜料固化在铝型材表面。
(5)水洗去胶:电泳固化后,将铝型材放入清洗槽中进行水洗处理,去除表面的未固化有机胶体颜料。
(6)烘干处理:将洗净的铝型材放入烘干炉中进行烘干处理,使其快速干燥。
以上是铝型材氧化和电泳生产工艺操作的基本步骤。
根据不同的需求和具体情况,操作细节可能会有所不同,但整体流程是相似的。
进行这两种工艺处理可以提高铝型材的耐腐蚀性、防晒性和装饰性能,使其具有更好的应用价值。
铝型材氧化电泳生产车间工艺操作规程
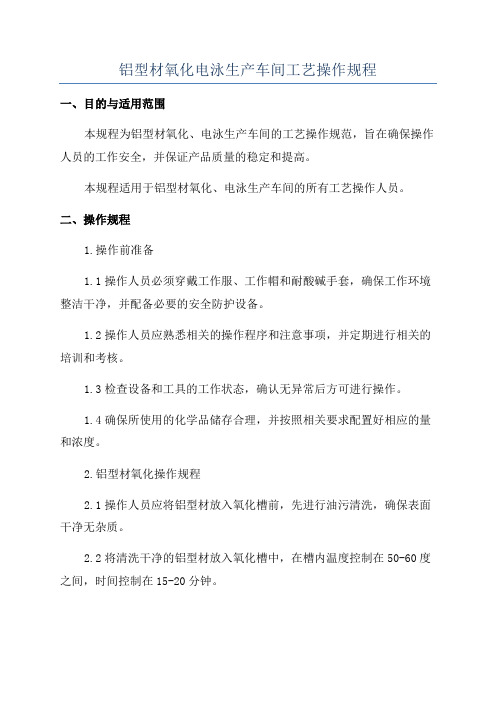
铝型材氧化电泳生产车间工艺操作规程一、目的与适用范围本规程为铝型材氧化、电泳生产车间的工艺操作规范,旨在确保操作人员的工作安全,并保证产品质量的稳定和提高。
本规程适用于铝型材氧化、电泳生产车间的所有工艺操作人员。
二、操作规程1.操作前准备1.1操作人员必须穿戴工作服、工作帽和耐酸碱手套,确保工作环境整洁干净,并配备必要的安全防护设备。
1.2操作人员应熟悉相关的操作程序和注意事项,并定期进行相关的培训和考核。
1.3检查设备和工具的工作状态,确认无异常后方可进行操作。
1.4确保所使用的化学品储存合理,并按照相关要求配置好相应的量和浓度。
2.铝型材氧化操作规程2.1操作人员应将铝型材放入氧化槽前,先进行油污清洗,确保表面干净无杂质。
2.2将清洗干净的铝型材放入氧化槽中,在槽内温度控制在50-60度之间,时间控制在15-20分钟。
2.3及时处理氧化槽中生成的泥浆和废液,确保设备和工作区域的卫生。
3.电泳生产操作规程3.1操作人员应将已氧化好的铝型材放入电泳槽中,温度控制在25-30度之间,时间根据生产要求进行设置。
3.2配置好电泳液,保证质量稳定,每次投入使用前必须进行检测。
3.3正确调整电泳设备参数,确保生产过程中的电流、电压和时间等参数稳定。
3.4注意观察电泳槽中的液面和液位,保证液面恒定,并定期清理槽底的沉淀物。
3.5在电泳过程中,必须保持工作区域的整洁,禁止吸烟和随地乱扔废弃物。
4.工艺控制与质量管理4.1操作人员必须按照工艺要求进行操作,并认真填写相关的操作记录。
4.2定期进行设备和工具的保养和维护,并对其进行定期的检测和校准。
4.3对每一批生产的铝型材进行质量抽检,确保产品符合规定的质量标准。
4.4配合质量检验部门进行工艺参数的优化和改进,提高产品质量和生产效率。
三、安全措施1.操作人员必须按规定佩戴个人防护设备,如口罩、防护眼镜和手套等。
2.禁止在作业过程中吸烟或进食。
3.对工作区域和设备进行定期的检修和维护,确保设备的安全运行。
铝型材电泳过程

铝型材电泳过程一、引言铝型材电泳是一种常见的表面处理工艺,通过电解作用将涂料均匀地附着在铝型材表面,形成一层保护膜。
本文将介绍铝型材电泳的工艺流程、优势以及应用领域。
二、工艺流程铝型材电泳的工艺流程主要包括前处理、电泳涂装、水洗和固化四个步骤。
1. 前处理前处理是铝型材电泳的关键步骤,它包括除油、清洗和酸洗等过程。
首先,将铝型材浸泡在去油剂中,去除表面的油污和杂质。
然后,经过清洗工序,将去油剂残留物洗净,保证表面洁净。
最后,进行酸洗,利用酸性溶液去除铝型材表面的氧化层,增加涂层的附着力。
2. 电泳涂装电泳涂装是铝型材电泳的核心步骤,它利用电解作用将涂料均匀地沉积在铝型材表面。
首先,将铝型材悬挂在电泳槽中,作为阳极。
然后,在电泳槽中加入涂料溶液,涂料颗粒带有正电荷,会被电场吸引向铝型材表面沉积。
在涂料沉积过程中,还可以通过调节电场强度和时间来控制涂层的厚度和均匀度。
3. 水洗电泳涂装后,铝型材表面会残留一些未固化的涂料,因此需要进行水洗。
水洗的目的是清洗掉未固化的涂料,保证涂层的质量。
水洗过程中,通常使用清水或去离子水进行反复冲洗,直到洗净为止。
4. 固化固化是铝型材电泳的最后一步,通过加热使涂料固化,形成坚硬、耐腐蚀的保护层。
固化温度和时间根据涂料的种类和厂家提供的要求进行控制。
固化完成后,铝型材电泳过程就结束了。
三、优势铝型材电泳具有以下优势:1. 均匀涂布:电泳涂装能够实现铝型材表面的均匀涂布,涂层厚度可控。
这样可以提高铝型材的耐腐蚀性和耐候性。
2. 环境友好:电泳涂装过程中无有机溶剂挥发,不会产生有害气体和废水。
相比传统喷涂工艺,更符合环保要求。
3. 良好的附着力:铝型材经过电泳涂装后,涂层与铝型材表面形成了化学键,具有良好的附着力,不易脱落。
4. 处理效率高:电泳涂装是自动化程度较高的表面处理工艺,能够快速高效地完成大批量铝型材的涂装。
四、应用领域铝型材电泳广泛应用于建筑、交通运输、家居装饰等领域。
电泳工艺安全操作规程

电泳工艺安全操作规程
《电泳工艺安全操作规程》
一、前言
电泳工艺是一种广泛应用于工业生产中的涂装技术,但在操作时必须严格遵守安全操作规程,以确保人身安全和设备安全。
本规程旨在规范电泳工艺操作,保障操作人员的安全。
二、操作前准备
1. 在进行电泳工艺操作前,操作人员必须穿戴好相关的劳动防护用具,包括防护眼镜、手套、防护服等。
2. 检查设备和工具是否正常,如有异常及时进行维修或更换。
三、操作过程
1. 操作人员必须全神贯注,不能分心,以避免操作失误造成事故。
2. 禁止使用带有金属的工具进行电泳工艺操作,以避免触电或其他意外发生。
3. 在操作时必须遵守设备操作流程和规程,禁止擅自改变工艺参数。
4. 在操作过程中,如发现异常情况,应立即停止操作,并通知相关人员进行处理。
四、操作后维护
1. 操作结束后,要及时关闭设备电源和清理工作区域,确保设备和场地的整洁和安全。
2. 对操作设备进行定期维护和保养,确保设备的正常运行。
3. 对操作过程中出现的问题或事故进行记录和汇报,以便进行事故分析和改进工艺。
五、紧急处理
在操作过程中如发生事故或意外情况,操作人员应立即采取相应的应急措施,通知相关人员进行处理。
通过遵守以上安全操作规程,能够有效减少电泳工艺操作中的安全风险,保障操作人员和设备的安全,确保工艺的正常运行。
铝型材氧化设备操作规程

立即关闭泄漏 源,防止氧化 液进一步泄漏。
用吸收棉或吸 附材料吸附泄 漏的氧化液, 防止其扩散和
污染环境。
将泄漏的氧化 液进行回收和 处理,防止对 环境造成危害。
对泄漏区域进 行清理和消毒, 确保人员和设
备的安全。
对泄漏原因进 行调查和分析, 采取相应的措 施防止类似事 故再次发生。
立即停止设备运行,防止损坏扩大。 对损坏的工件进行分类处理,可修复的尽快修复,不可修复的进行报废处理。 对损坏原因进行分析,找出原因并采取措施加以改进,防止类似问题再次发生。 对操作人员进行培训,提高操作技能和安全意识,避免人为因素导致的工件损坏。
设备无法制冷:检查制冷系 统是否正常工作,如有异常 及时维修或更换
氧化膜厚度不均匀: 调整氧化时间或氧 化温度,确保氧化 膜厚度均匀
氧化膜颜色不鲜艳: 检查氧化液浓度和 pH值,调整至适宜 范围
氧化膜附着力差: 检查前处理是否彻 底,确保表面无杂 质和油污
氧化膜耐磨性差: 增加氧化时间或调 整氧化温度,提高 氧化膜耐磨性
添加项标题
确认工件状态:检查工件是否已经完全氧化,表面是否有缺陷等。
添加项标题
关闭加热电源:停止加热,确保工件温度适宜。
添加项标题
准备工具:准备好出槽所需的工具,如吊车、叉车等。
添加项标题
操作步骤:将工件吊出氧化槽,放置在指定位置,注意保持工件稳定,避免滑动或碰撞。
添加项标题
清理现场:清理现场,保持工作区域整洁。
氧化膜不均匀:调整工艺参数,改进设备,更换阳极导电棒 氧化膜易脱落:改进阳极氧化溶液温度、浓度、导电性等参数 氧化膜颜色不正:更换阳极氧化溶液,调整工艺参数 工件表面有气泡:改进阳极氧化溶液温度、浓度等参数,更换阳极导电棒
铝型材电泳工艺流程

铝型材电泳工艺流程
《铝型材电泳工艺流程》
铝型材电泳工艺是一种常用的表面处理技术,通过电泳涂装可以使铝型材获得优异的表面性能和外观。
以下是铝型材电泳工艺的流程:
1. 预处理
首先,铝型材需要进行预处理,包括去油、除锈和清洗等工序。
这一步是非常重要的,因为良好的预处理可以确保电泳涂装的附着力和表面质量。
2. 电泳涂料制备
接下来是准备电泳涂料,通常是将固体颗粒的涂料悬浮在水溶液中。
电泳涂料的种类和配方会影响最终的涂层性能和外观。
3. 电泳涂装
当铝型材经过预处理后,就可以进行电泳涂装了。
在电泳涂装过程中,铝型材作为阳极,被浸入电泳槽中。
通过施加电压,涂料颗粒会向铝表面迁移并沉积,形成连续的涂层。
4. 固化
涂装完成后,铝型材需要进行固化处理,通常是在高温下进行烘烤。
固化可以使涂料形成坚硬的保护膜,并提高耐候性和耐腐蚀性。
5. 检测和包装
最后,经过固化处理的铝型材将进行表面质量检测,包括涂层厚度、附着力、耐磨性等指标的检测。
合格的铝型材将会进行包装,准备发往客户。
总的来说,铝型材电泳工艺流程包括预处理、电泳涂装、固化和检测包装等环节,通过这一流程可以为铝型材提供出色的表面处理效果,提高其使用寿命和外观质量。
铝型材电泳工艺流程
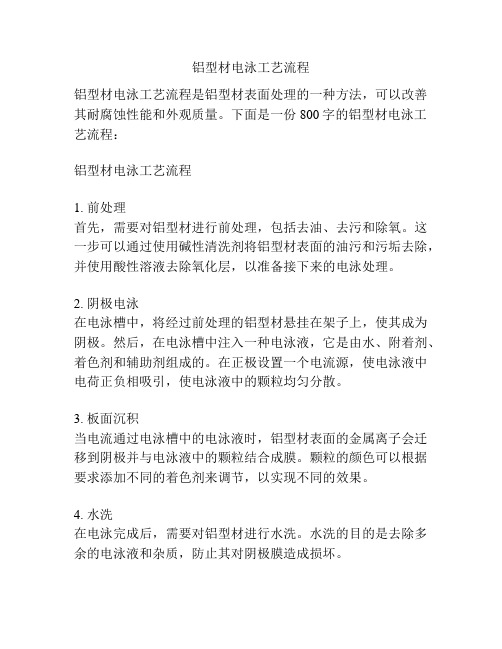
铝型材电泳工艺流程铝型材电泳工艺流程是铝型材表面处理的一种方法,可以改善其耐腐蚀性能和外观质量。
下面是一份800字的铝型材电泳工艺流程:铝型材电泳工艺流程1. 前处理首先,需要对铝型材进行前处理,包括去油、去污和除氧。
这一步可以通过使用碱性清洗剂将铝型材表面的油污和污垢去除,并使用酸性溶液去除氧化层,以准备接下来的电泳处理。
2. 阴极电泳在电泳槽中,将经过前处理的铝型材悬挂在架子上,使其成为阴极。
然后,在电泳槽中注入一种电泳液,它是由水、附着剂、着色剂和辅助剂组成的。
在正极设置一个电流源,使电泳液中电荷正负相吸引,使电泳液中的颗粒均匀分散。
3. 板面沉积当电流通过电泳槽中的电泳液时,铝型材表面的金属离子会迁移到阴极并与电泳液中的颗粒结合成膜。
颗粒的颜色可以根据要求添加不同的着色剂来调节,以实现不同的效果。
4. 水洗在电泳完成后,需要对铝型材进行水洗。
水洗的目的是去除多余的电泳液和杂质,防止其对阴极膜造成损坏。
5. 固化水洗完后,铝型材需要进行固化,即在固化炉中加热一段时间。
固化的目的是使电泳涂层与铝型材表面牢固结合,并增强电泳层的硬度和耐腐蚀性。
6. 后处理最后一步是对固化后的铝型材进行后处理。
后处理可以包括抛光、打磨和上光等工序,以进一步改善铝型材的光泽度和质感。
总结:铝型材电泳工艺流程是一种常用的表面处理方法,通过阴极电泳的方式将颗粒附着在铝型材上,并经过水洗、固化和后处理等环节,使电泳涂层与铝型材表面紧密结合,提高了铝型材的耐腐蚀性和外观质量。
这种工艺具有工艺简单、效果稳定和成本低廉等优点,在家居建材、电子、汽车等行业得到广泛应用。
氧化工艺-01
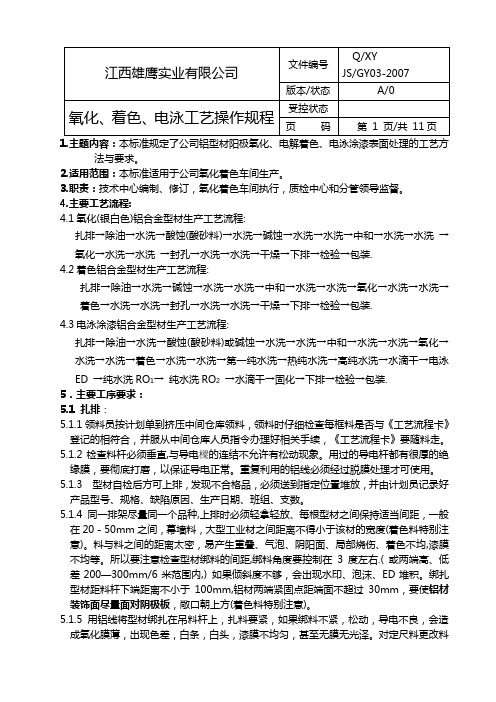
1.主题内容:本标准规定了公司铝型材阳极氧化、电解着色、电泳涂漆表面处理的工艺方法与要求。
2.适用范围:本标准适用于公司氧化着色车间生产。
3.职责:技术中心编制、修订,氧化着色车间执行,质检中心和分管领导监督。
4.主要工艺流程:4.1氧化(银白色)铝合金型材生产工艺流程:扎排→除油→水洗→酸蚀(酸砂料)→水洗→碱蚀→水洗→水洗→中和→水洗→水洗→氧化→水洗→水洗→封孔→水洗→水洗→干燥→下排→检验→包装.4.2着色铝合金型材生产工艺流程:扎排→除油→水洗→碱蚀→水洗→水洗→中和→水洗→水洗→氧化→水洗→水洗→着色→水洗→水洗→封孔→水洗→水洗→干燥→下排→检验→包装.4.3电泳涂漆铝合金型材生产工艺流程:扎排→除油→水洗→酸蚀(酸砂料)或碱蚀→水洗→水洗→中和→水洗→水洗→氧化→水洗→水洗→着色→水洗→水洗→第一纯水洗→热纯水洗→高纯水洗→水滴干→电泳ED →纯水洗RO1→纯水洗RO2→水滴干→固化→下排→检验→包装.5.主要工序要求:5.1 扎排:5.1.1领料员按计划单到挤压中间仓库领料,领料时仔细检查每框料是否与《工艺流程卡》登记的相符合,并服从中间仓库人员指令办理好相关手续,《工艺流程卡》要随料走。
5.1.2检查料杆必须垂直,与导电樑的连结不允许有松动现象。
用过的导电杆都有很厚的绝缘膜,要彻底打磨,以保证导电正常。
重复利用的铝线必须经过脱膜处理才可使用。
5.1.3 型材自检后方可上排,发现不合格品,必须送到指定位臵堆放,并由计划员记录好产品型号、规格、缺陷原因、生产日期、班组、支数。
5.1.4 同一排架尽量同一个品种,上排时必须轻拿轻放、每根型材之间保持适当间距,一般在20-50mm之间,幕墙料,大型工业材之间距离不得小于该材的宽度(着色料特别注意)。
料与料之间的距离太密,易产生重叠、气泡、阴阳面、局部烧伤、着色不均,漆膜不均等。
所以要注意检查型材绑料的间距,绑料角度要控制在3度左右.( 或两端高、低差200—300mm/6米范围内,) 如果倾斜度不够,会出现水印、泡沫、ED堆积。
- 1、下载文档前请自行甄别文档内容的完整性,平台不提供额外的编辑、内容补充、找答案等附加服务。
- 2、"仅部分预览"的文档,不可在线预览部分如存在完整性等问题,可反馈申请退款(可完整预览的文档不适用该条件!)。
- 3、如文档侵犯您的权益,请联系客服反馈,我们会尽快为您处理(人工客服工作时间:9:00-18:30)。
氧化车间生产工艺操作规程阳极氧化、电泳涂漆工艺操作规程本规程适用于铝合金型材的阳极氧化、电解着色和电泳涂漆生产工艺。
1 生产工艺流程1.1 阳极氧化、电解着色工艺流程备料及装挂—脱脂—水洗—水洗—碱洗—水洗—水洗—中和—水洗—水洗—阳极氧化—水洗—水洗—电解着色—水洗—水洗—封孔—滴干—卸料—检验—包装—入库1.2 电泳涂漆工艺流程备料及装挂—脱脂—水洗—水洗—碱洗—水洗—水洗—中和—水洗—水洗—阳极氧化—水洗—水洗—电解着色—水洗—纯水洗—热纯水洗—纯水洗—阳极电泳—水洗1—水洗2—滴干—固化—自然冷却—卸料—检验—包装—入库2 阳极氧化、电解着色工艺规程2.1 备料及装料2.1.1按生产计划要求,准备好检验合格的型材。
2.1.2在装挂前,应检查料挂的导电杆与导电梁上螺杆连接是否紧固,导电杆是否弯曲。
2.1.3装挂前,应用锉刀或其它方法去除吊杆上与型材接触面的阳极氧化膜以及漆膜,确保良好的导电性。
2.1.4 装挂时,应按照工艺卡片规定的支数挂料。
2.1.5 装挂时,应尽量把相同断面或相近形状尺寸的型材装在同一挂上,型材与型材之间应保持均匀的间距(着色型材一般为30~35mm,非着色型材为20~25mm)和合适的倾角(> 5℃),型材绑线位置距端头应<50mm。
2.1.6装挂时,型材重要的装饰面应朝向邻近阴极。
2.1.7型材装挂必须牢固,不得窜动。
2.1.8 装挂时,应轻拿轻放,防止型材磕碰伤。
2.1.9 装挂完毕后应仔细检查,型材之间不应相互接触,挂在吊杆最上面的型材在处理时不能露出液面。
2.2 脱脂在酸液中使铝型材表面的油污和天然氧化膜等脏物与铝基体的结合力松弛,且趋于一致,便于碱洗时去除速度均一。
脱脂采用硫酸(工业纯H2SO4,GB/T534)溶液。
为降低成本,可以使用氧化槽排放的硫酸。
槽液成分及工艺制度如下:硫酸:150~180g/L温度:室温时间:1~3min 生产合金元素含量较高的6061 合金型材,或在使用废料较多的情况下,为防止铝材出现黑斑,可在硫酸中加入10~20g/L 硝酸操作时,将型材从装料台吊起放置到脱脂槽内,处理时间到后,将其吊出滴干,然后放入水洗槽中进行两次水洗。
对于砂面型材,水洗后进入酸蚀槽进行磨砂处理。
非砂面型材直接进入碱洗槽。
2.3 酸蚀磨砂处理采用酸性砂面,其槽液成分及工艺制度如下:氟化氢氨:35~55g/L酸蚀添加剂:5~7g/L温度:35~45℃时间:3~6min操作时,将型材从水洗槽中吊起滴干后放入酸蚀槽中,处理时间到后,立即吊起放入其后的水洗槽经过两次水洗后进行碱洗。
2.4 碱洗(碱腐蚀)在碱(NaOH,GB209)溶液中蚀洗有两方面的作用:一方面,将型材表面的油污及天然氧化膜清除掉,使基体金属表面暴露出来,以利于阳极氧化时表面生成质地优良的氧化膜;另一方面,使有轻微粗糙的表面得到轻度抛光。
槽液成分及工艺制度见表1。
表1 碱洗槽液成分及制度操作时,将型材从水洗槽吊起滴干后放置到碱洗槽中,处理时间到后,吊起立即放入其后的水洗槽经过两次水洗后进行中和处理。
2.5 中和碱洗后的型材表面的黑色挂灰(系合金元素的氧化物),不能溶于碱溶液,也不能水洗干净,但在硫酸溶液中可以洗净,获得光亮的金属表面。
同时,也有中和型材表面残留碱液的作用。
对于含有铜等元素的6061合金,在中和槽中添加约10~20g/L 硝酸(工业纯HNO3,GB/T337)可获得较好的处理效果。
槽液成分及工艺制度如下:硫酸:140~160g/L硝酸:10~20g/L游离酸:120~180g/L温度:室温时间:1~2min操作时,将经过两次水洗后的型材,从水洗槽吊起滴干后放置到中和槽,处理时间到后将其吊出滴干。
然后,放入后面的水洗槽进行清洗,清洗后进入抛光槽进行抛光处理。
2.6 抛光把型材放入抛光剂浓度为4%~8% 的抛光槽中进行抛光处理1~3min。
抛光剂的主要成分是氢氟酸、络合剂、缓蚀剂和乳化剂。
抛光后的型材,立即放入后面的水洗槽进行清洗。
2.7 阳极氧化2.7.1表面预处理后会出现型材松动,在进入氧化槽前应再紧料一次,确保导电良好,避免出现色浅、色差等。
2.7.2 槽液成分及工艺制度硫酸:170±20g/L铝离子含量:<15g/L温度:20± 2℃时间:25~40min电流密度:110~150A/m2,常用120A/m2.7.3 每槽阳极氧化总面积为被处理型材外表面积之和。
对于空心型材,根据断面大小,每根型材阳极氧化面积应多加200~500mm 长度的内表面面积。
然后根据阳极氧化总面积和电流密度计算出总电流。
2.7.4 需要电解着色处理的型材,每一挂型材应是同一种规格,避免产生色差。
2.7.5 导电梁与导电座之间应接触良好,保证通电正常,接触温升不大于30℃。
2.7.6 送电进行氧化处理时应一次给足总电流,并自此时开始计算处理时。
送电时要防止出现电流的过大冲击,电压上升应取软启动,电压上升时间一般为10~15s。
2.7.7 阳极氧化处理时,应避免型材与阴极接触,防止短路烧坏制品及阴极。
2.7.8 为使槽液与进行阳极氧化的制品表面温度均匀,处理过程中,槽液除进行循环外,还须进行均匀的压缩空气搅拌。
2.7.9 每一槽处理过程中,在头、中、尾部三个测试点至少应测量溶液温度一次。
2.7.10在氧化进行过程中,因发生故障,停电时间不超过2min,通电后继续氧化,氧化时间可累计。
2.7.11因发生故障,制品在干净水槽中放置超过4h,则应重新预处理后才能阳极氧化。
2.7.12具体的氧化时间应根据氧化膜的厚度来确定。
阳极氧化膜的厚度与通电量成正比,即与电流密度和氧化处理时间成正比。
氧化膜厚度按下式计算:δ=KIt式中:δ——氧化膜厚度,μm;I——电流密度,A/dm2;t——氧化时间,min;K——系数,一般取0.3。
操作时,根据装料面积计算氧化电流通电。
氧化完毕,将型材吊出滴干,立即放入后面的水洗槽进行清洗。
2.8 电解着色生产香槟色着色型材时,采用锡镍盐着色工艺,其成分主要为硫酸亚锡和硫酸镍( NiSO4·6H2O,GB/T1287),槽液用纯水配制。
根据对着色后的型材颜色深浅要求不同,可采用不同的着色工艺制度。
2.8.1 槽液成分及工艺制度生产浅色和深色型材的工艺制度分别见表2 表2着色槽液成分及制度2.8.2 对于着色型材,在绑料时,一般凹槽向上,装饰面向上或相对电极。
绑料要有一定的斜度,以减少上下面的色差。
2.8.3 着色槽中超过挂料区的对电极,应撤除或用塑料板遮挡,以免周边颜色加深。
2.8.4 型材放入着色槽时,先不通电浸泡1~2min,有利于着色微粒进入孔底沉积,使颜色均匀不容易褪色。
2.8.5 由于浅色系的着色总时间较短,电压上升段的低电压时间过长,会造成型材凹槽颜色太浅。
因此,电压上升速度宜快(5~10s)。
2.8.6 游离硫酸浓度应高一些,以提高槽液导电性,使颜色分散性更好。
2.8.7 着色结束后,应迅速水洗。
转移速度慢会出现型材的深色或浅色带2.9 封孔2.9.1 槽液成分及工艺制度封孔的槽液成份及工艺制度如下:镍离子:1.0~1.3g/L氟离子:0.3~0.6g/LpH 值:5.5~6.5温度:25~28℃时间:10~20min2.9.2 阳极氧化后的型材应及时水洗干净,停留在氧化槽中时间过长会影响封孔质量;洗不干净会造成窜液污染,增加封孔槽的氟消耗。
2.9.3 用氢氟酸调氟的封孔槽,应以10%的稀溶液形式加入,添加之后应经过5~10min 才生产。
2.9.4 封孔之后应迅速进行水洗。
为提高封孔质量并加快干燥速度,冷封孔后,可在45~60℃的热水中洗10~15min。
2.10 水洗从碱槽或酸槽中出来的型材,在进入下一个处理槽之前都应进行两次水洗,清除型材表面上残留的残碱或残酸液。
每一次水洗的时间一般为1~2min。
2.11卸料、检验、包装、入库2.11.1表面处理结束,即可卸料。
卸料时,应轻拿轻放,防止型材之间相互刮檫,并按不同规格、品种、色号、长度、定单分别整齐堆放待检2.11.2按有关标准规定的项目进行检验。
2.11.3经检验合格的型材,按规定的支数叠好料后进行包装(氧化着色材每层中间应垫包装纸)。
包装时未封端头的一端不允许裸露,以免损伤型材表面。
2.11.4包装好的型材,按规定入库。
3 电泳涂漆工艺流程生产银白色或着色电泳涂漆型材的工艺,是将经过阳极氧化或电解着色的型材,放在水溶性丙烯酸漆的电泳槽中,铝材作为阳极,在直流电压为90~120V 下电泳,使得氧化膜表面沉积一层不溶性漆膜,再在170~200℃高温下烘烤固化。
电泳前必须经过一道纯水,二道热纯水,三道冷纯水的洗涤,充分洗干净型材表面、内孔和膜孔中残留的酸水和污物。
3.1 纯水洗槽液:纯水,电导率≤100μ S /cm ,PH≥4.5温度:常温时间:3~5min操作时,将从前道水洗槽中提出的型材放置进纯水槽中,处理时间到后再将其提出。
3.2 热纯水洗槽液:纯水,电导率≤50μ S /cm,PH≥4.5温度:70~80℃ 时间:3~8min操作时,将从前道纯水槽中提出的型材放置进热纯水槽中,处理时间到后再将其提出。
3.3 冷纯水洗槽液:纯水,电导率≤50μS /cm,PH≥5 温度:<30℃ 时间:3~5min操作时,将从前道热纯水槽中提出的型材放置进冷纯水槽中,处理时间到后再将其提出滴干。
3.4 电泳涂漆3.4.1 槽液成分及工艺参数槽液:固形份5.0~8.0% ,PH 7.5~8.5,IPA1~3%,电导率800~1200μS/cm,BC 1.0~1.8%电压:90~120v温度:23±3℃时间:1.5~3min3.4.2 型材进入电泳槽时必须保持较大的倾斜度,以利排除空气。
型材进入电泳槽后应放置在电极中央,确保与两边极板的距离相等,并静置1 分钟后才能通电电泳。
3.4.3 电泳时必须开启电泳槽循环泵和电泳回收装置。
3.4.4电泳槽液应根据PH 值或电导率的升高定期开启净化系统,确保电泳槽液符合工艺要求。
3.4.5 操作时,根据型材的种类和膜厚要求设定具体的通电电压和通电时间。
3.5水洗(RO1)槽液:固形分≤1.5%,PH 8.0~8.5,电导率≤200μS/cm,IPA1~3%,BC 1.0~1.8%温度:室温时间:3~5min操作时,将电泳槽通电完毕的型材提出放置在本水洗槽中,处理时间到后尽快提出。
3.6水洗(RO2)槽液:固形分<1.0%,PH 8.0~9.0,电导率≤100μs/cm,IPA 1~3%,BC 1~1.8%温度:室温时间:2~3min操作时,将上道水洗提出的型材放入本道水洗槽中,处理时间到后将其提出、滴干。